ASD relay wiring JEEP LIBERTY 2002 KJ / 1.G Workshop Manual
[x] Cancel search | Manufacturer: JEEP, Model Year: 2002, Model line: LIBERTY, Model: JEEP LIBERTY 2002 KJ / 1.GPages: 1803, PDF Size: 62.3 MB
Page 345 of 1803
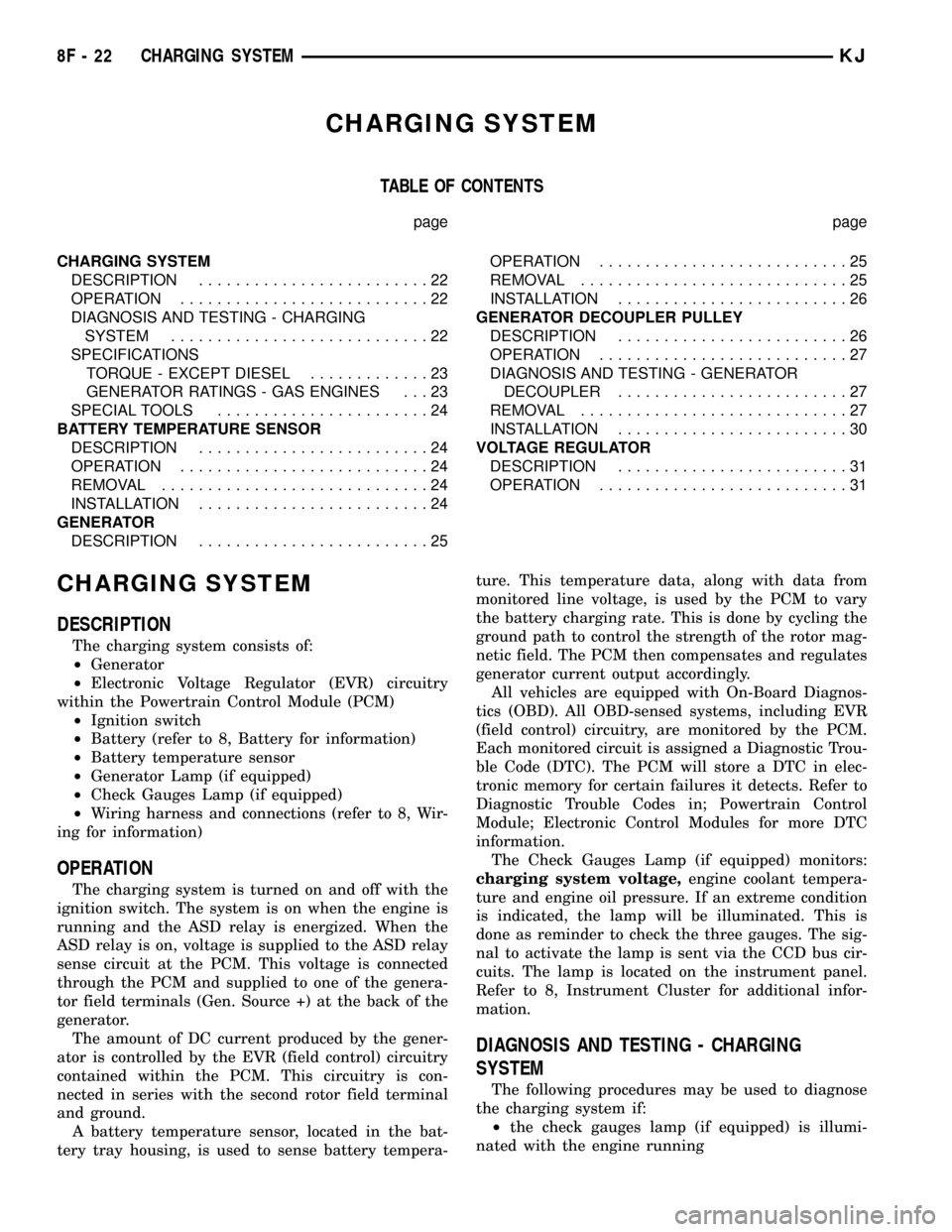
CHARGING SYSTEM
TABLE OF CONTENTS
page page
CHARGING SYSTEM
DESCRIPTION.........................22
OPERATION...........................22
DIAGNOSIS AND TESTING - CHARGING
SYSTEM............................22
SPECIFICATIONS
TORQUE - EXCEPT DIESEL.............23
GENERATOR RATINGS - GAS ENGINES . . . 23
SPECIAL TOOLS.......................24
BATTERY TEMPERATURE SENSOR
DESCRIPTION.........................24
OPERATION...........................24
REMOVAL.............................24
INSTALLATION.........................24
GENERATOR
DESCRIPTION.........................25OPERATION...........................25
REMOVAL.............................25
INSTALLATION.........................26
GENERATOR DECOUPLER PULLEY
DESCRIPTION.........................26
OPERATION...........................27
DIAGNOSIS AND TESTING - GENERATOR
DECOUPLER.........................27
REMOVAL.............................27
INSTALLATION.........................30
VOLTAGE REGULATOR
DESCRIPTION.........................31
OPERATION...........................31
CHARGING SYSTEM
DESCRIPTION
The charging system consists of:
²Generator
²Electronic Voltage Regulator (EVR) circuitry
within the Powertrain Control Module (PCM)
²Ignition switch
²Battery (refer to 8, Battery for information)
²Battery temperature sensor
²Generator Lamp (if equipped)
²Check Gauges Lamp (if equipped)
²Wiring harness and connections (refer to 8, Wir-
ing for information)
OPERATION
The charging system is turned on and off with the
ignition switch. The system is on when the engine is
running and the ASD relay is energized. When the
ASD relay is on, voltage is supplied to the ASD relay
sense circuit at the PCM. This voltage is connected
through the PCM and supplied to one of the genera-
tor field terminals (Gen. Source +) at the back of the
generator.
The amount of DC current produced by the gener-
ator is controlled by the EVR (field control) circuitry
contained within the PCM. This circuitry is con-
nected in series with the second rotor field terminal
and ground.
A battery temperature sensor, located in the bat-
tery tray housing, is used to sense battery tempera-ture. This temperature data, along with data from
monitored line voltage, is used by the PCM to vary
the battery charging rate. This is done by cycling the
ground path to control the strength of the rotor mag-
netic field. The PCM then compensates and regulates
generator current output accordingly.
All vehicles are equipped with On-Board Diagnos-
tics (OBD). All OBD-sensed systems, including EVR
(field control) circuitry, are monitored by the PCM.
Each monitored circuit is assigned a Diagnostic Trou-
ble Code (DTC). The PCM will store a DTC in elec-
tronic memory for certain failures it detects. Refer to
Diagnostic Trouble Codes in; Powertrain Control
Module; Electronic Control Modules for more DTC
information.
The Check Gauges Lamp (if equipped) monitors:
charging system voltage,engine coolant tempera-
ture and engine oil pressure. If an extreme condition
is indicated, the lamp will be illuminated. This is
done as reminder to check the three gauges. The sig-
nal to activate the lamp is sent via the CCD bus cir-
cuits. The lamp is located on the instrument panel.
Refer to 8, Instrument Cluster for additional infor-
mation.
DIAGNOSIS AND TESTING - CHARGING
SYSTEM
The following procedures may be used to diagnose
the charging system if:
²the check gauges lamp (if equipped) is illumi-
nated with the engine running
8F - 22 CHARGING SYSTEMKJ
Page 358 of 1803
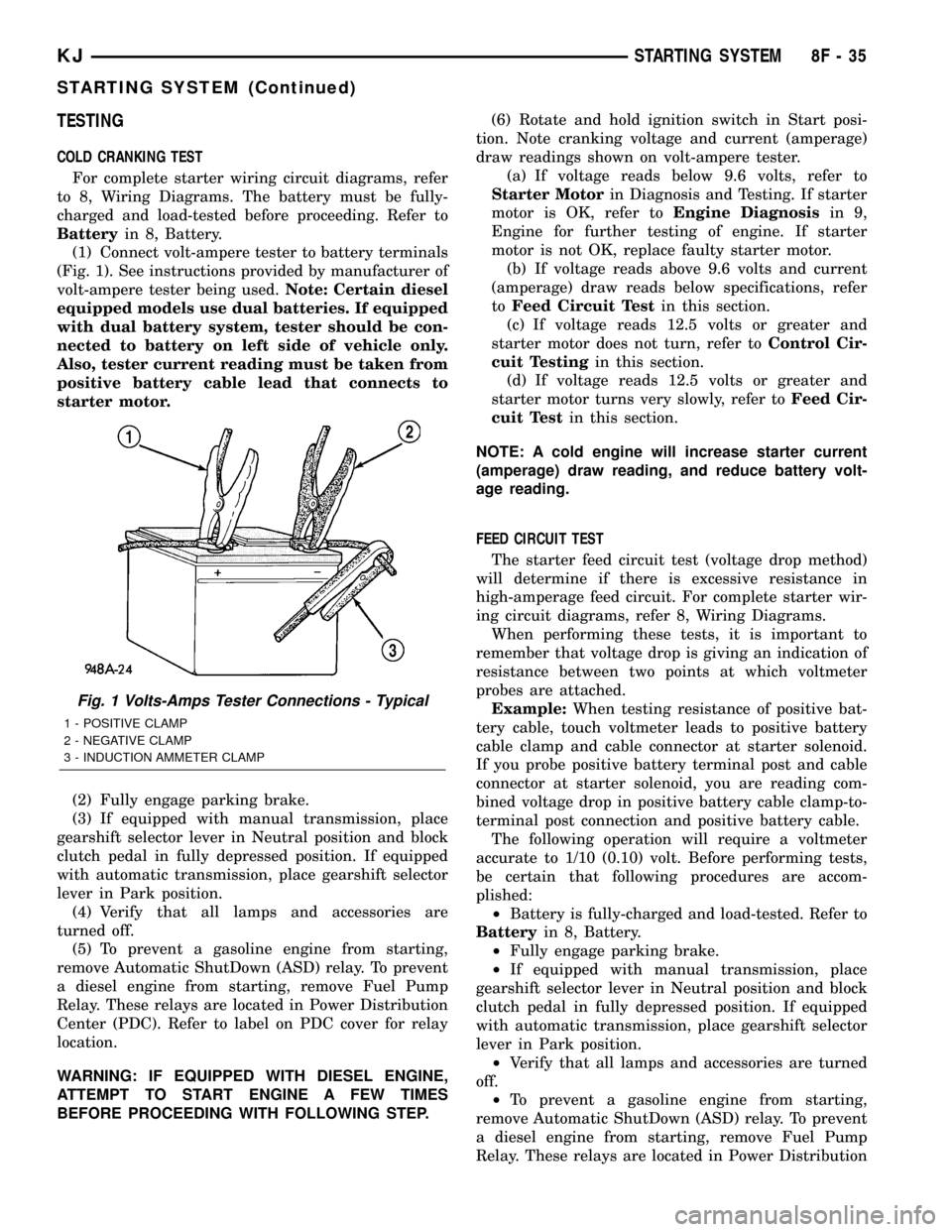
TESTING
COLD CRANKING TEST
For complete starter wiring circuit diagrams, refer
to 8, Wiring Diagrams. The battery must be fully-
charged and load-tested before proceeding. Refer to
Batteryin 8, Battery.
(1) Connect volt-ampere tester to battery terminals
(Fig. 1). See instructions provided by manufacturer of
volt-ampere tester being used.Note: Certain diesel
equipped models use dual batteries. If equipped
with dual battery system, tester should be con-
nected to battery on left side of vehicle only.
Also, tester current reading must be taken from
positive battery cable lead that connects to
starter motor.
(2) Fully engage parking brake.
(3) If equipped with manual transmission, place
gearshift selector lever in Neutral position and block
clutch pedal in fully depressed position. If equipped
with automatic transmission, place gearshift selector
lever in Park position.
(4) Verify that all lamps and accessories are
turned off.
(5) To prevent a gasoline engine from starting,
remove Automatic ShutDown (ASD) relay. To prevent
a diesel engine from starting, remove Fuel Pump
Relay. These relays are located in Power Distribution
Center (PDC). Refer to label on PDC cover for relay
location.
WARNING: IF EQUIPPED WITH DIESEL ENGINE,
ATTEMPT TO START ENGINE A FEW TIMES
BEFORE PROCEEDING WITH FOLLOWING STEP.(6) Rotate and hold ignition switch in Start posi-
tion. Note cranking voltage and current (amperage)
draw readings shown on volt-ampere tester.
(a) If voltage reads below 9.6 volts, refer to
Starter Motorin Diagnosis and Testing. If starter
motor is OK, refer toEngine Diagnosisin 9,
Engine for further testing of engine. If starter
motor is not OK, replace faulty starter motor.
(b) If voltage reads above 9.6 volts and current
(amperage) draw reads below specifications, refer
toFeed Circuit Testin this section.
(c) If voltage reads 12.5 volts or greater and
starter motor does not turn, refer toControl Cir-
cuit Testingin this section.
(d) If voltage reads 12.5 volts or greater and
starter motor turns very slowly, refer toFeed Cir-
cuit Testin this section.
NOTE: A cold engine will increase starter current
(amperage) draw reading, and reduce battery volt-
age reading.
FEED CIRCUIT TEST
The starter feed circuit test (voltage drop method)
will determine if there is excessive resistance in
high-amperage feed circuit. For complete starter wir-
ing circuit diagrams, refer 8, Wiring Diagrams.
When performing these tests, it is important to
remember that voltage drop is giving an indication of
resistance between two points at which voltmeter
probes are attached.
Example:When testing resistance of positive bat-
tery cable, touch voltmeter leads to positive battery
cable clamp and cable connector at starter solenoid.
If you probe positive battery terminal post and cable
connector at starter solenoid, you are reading com-
bined voltage drop in positive battery cable clamp-to-
terminal post connection and positive battery cable.
The following operation will require a voltmeter
accurate to 1/10 (0.10) volt. Before performing tests,
be certain that following procedures are accom-
plished:
²Battery is fully-charged and load-tested. Refer to
Batteryin 8, Battery.
²Fully engage parking brake.
²If equipped with manual transmission, place
gearshift selector lever in Neutral position and block
clutch pedal in fully depressed position. If equipped
with automatic transmission, place gearshift selector
lever in Park position.
²Verify that all lamps and accessories are turned
off.
²To prevent a gasoline engine from starting,
remove Automatic ShutDown (ASD) relay. To prevent
a diesel engine from starting, remove Fuel Pump
Relay. These relays are located in Power Distribution
Fig. 1 Volts-Amps Tester Connections - Typical
1 - POSITIVE CLAMP
2 - NEGATIVE CLAMP
3 - INDUCTION AMMETER CLAMP
KJSTARTING SYSTEM 8F - 35
STARTING SYSTEM (Continued)
Page 392 of 1803
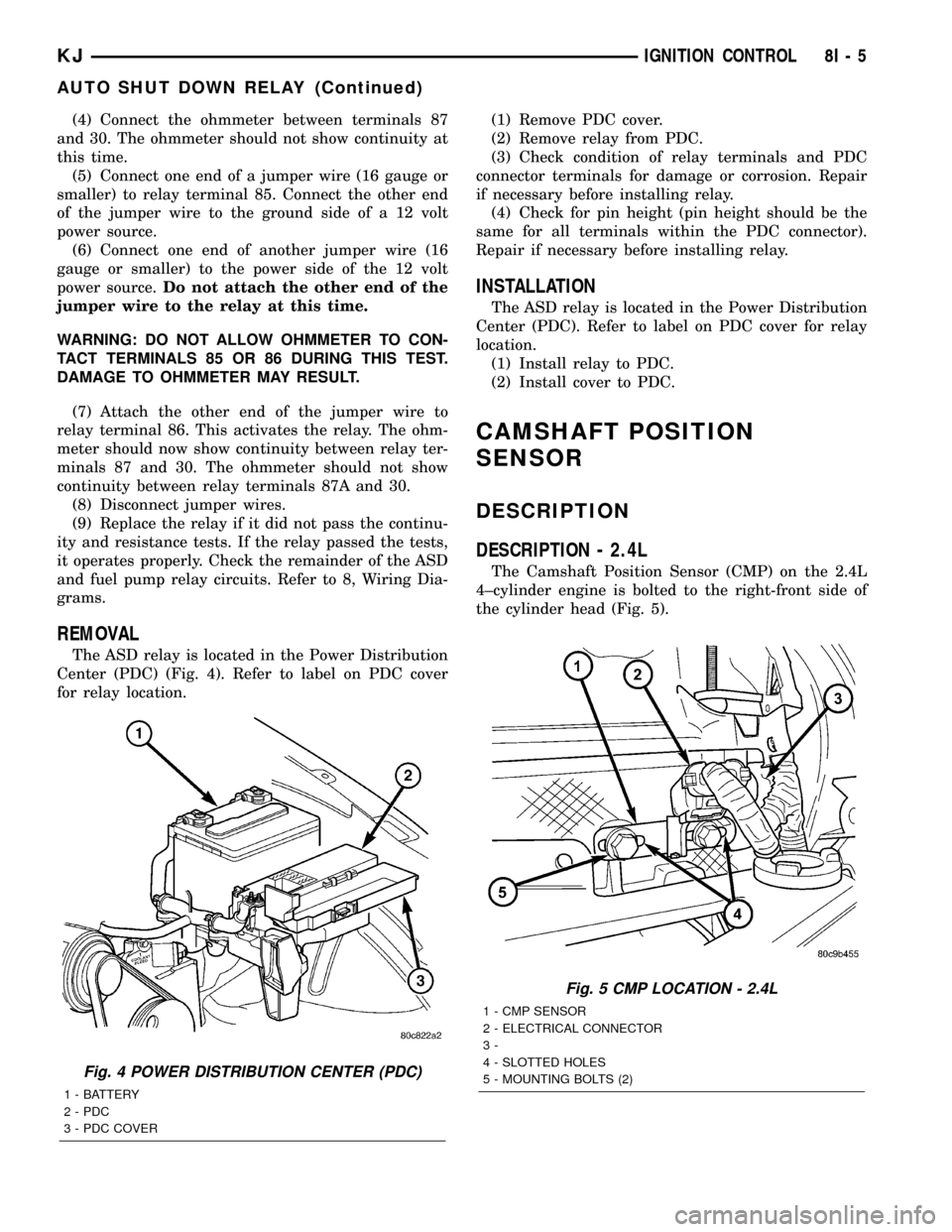
(4) Connect the ohmmeter between terminals 87
and 30. The ohmmeter should not show continuity at
this time.
(5) Connect one end of a jumper wire (16 gauge or
smaller) to relay terminal 85. Connect the other end
of the jumper wire to the ground side of a 12 volt
power source.
(6) Connect one end of another jumper wire (16
gauge or smaller) to the power side of the 12 volt
power source.Do not attach the other end of the
jumper wire to the relay at this time.
WARNING: DO NOT ALLOW OHMMETER TO CON-
TACT TERMINALS 85 OR 86 DURING THIS TEST.
DAMAGE TO OHMMETER MAY RESULT.
(7) Attach the other end of the jumper wire to
relay terminal 86. This activates the relay. The ohm-
meter should now show continuity between relay ter-
minals 87 and 30. The ohmmeter should not show
continuity between relay terminals 87A and 30.
(8) Disconnect jumper wires.
(9) Replace the relay if it did not pass the continu-
ity and resistance tests. If the relay passed the tests,
it operates properly. Check the remainder of the ASD
and fuel pump relay circuits. Refer to 8, Wiring Dia-
grams.
REMOVAL
The ASD relay is located in the Power Distribution
Center (PDC) (Fig. 4). Refer to label on PDC cover
for relay location.(1) Remove PDC cover.
(2) Remove relay from PDC.
(3) Check condition of relay terminals and PDC
connector terminals for damage or corrosion. Repair
if necessary before installing relay.
(4) Check for pin height (pin height should be the
same for all terminals within the PDC connector).
Repair if necessary before installing relay.
INSTALLATION
The ASD relay is located in the Power Distribution
Center (PDC). Refer to label on PDC cover for relay
location.
(1) Install relay to PDC.
(2) Install cover to PDC.
CAMSHAFT POSITION
SENSOR
DESCRIPTION
DESCRIPTION - 2.4L
The Camshaft Position Sensor (CMP) on the 2.4L
4±cylinder engine is bolted to the right-front side of
the cylinder head (Fig. 5).
Fig. 4 POWER DISTRIBUTION CENTER (PDC)
1 - BATTERY
2 - PDC
3 - PDC COVER
Fig. 5 CMP LOCATION - 2.4L
1 - CMP SENSOR
2 - ELECTRICAL CONNECTOR
3-
4 - SLOTTED HOLES
5 - MOUNTING BOLTS (2)
KJIGNITION CONTROL 8I - 5
AUTO SHUT DOWN RELAY (Continued)
Page 1415 of 1803
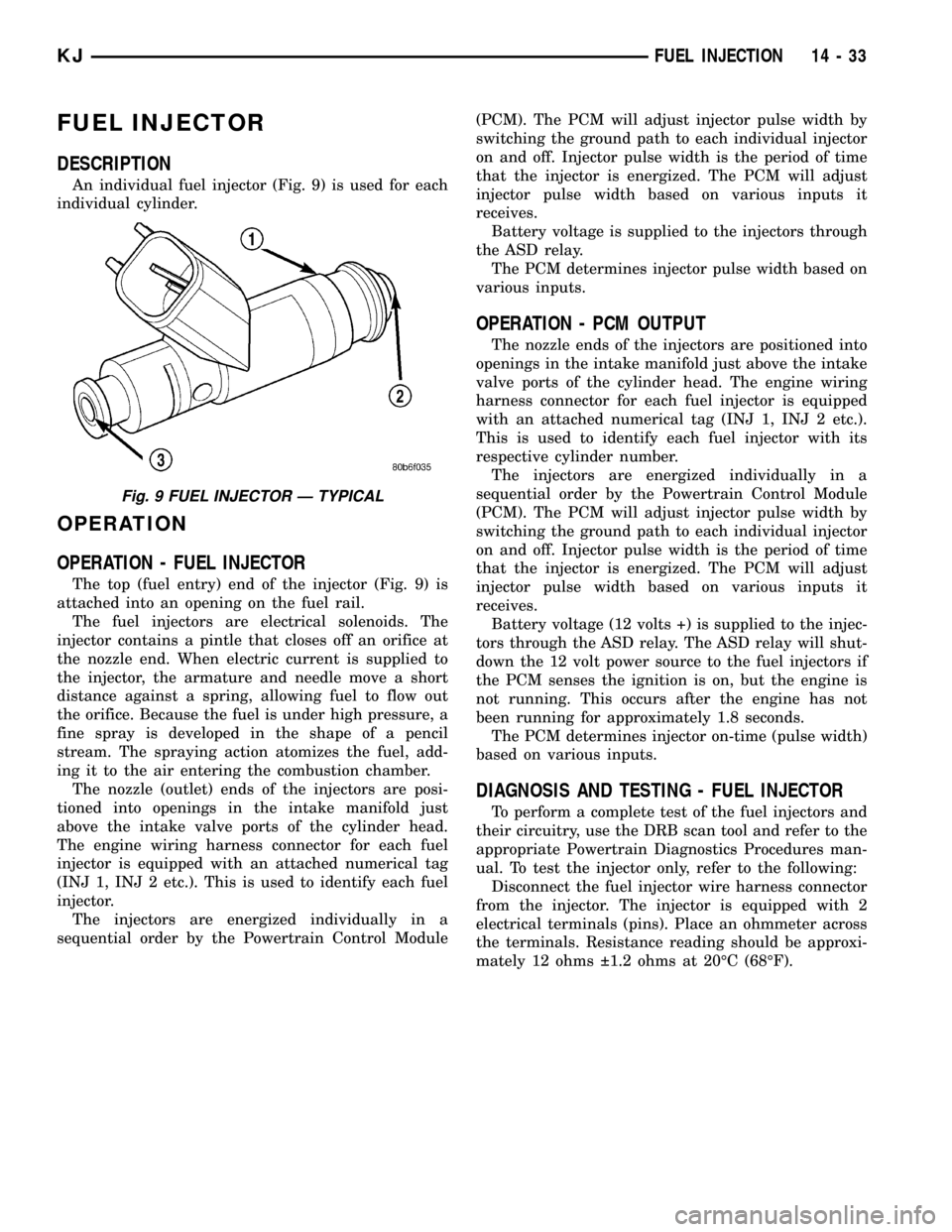
FUEL INJECTOR
DESCRIPTION
An individual fuel injector (Fig. 9) is used for each
individual cylinder.
OPERATION
OPERATION - FUEL INJECTOR
The top (fuel entry) end of the injector (Fig. 9) is
attached into an opening on the fuel rail.
The fuel injectors are electrical solenoids. The
injector contains a pintle that closes off an orifice at
the nozzle end. When electric current is supplied to
the injector, the armature and needle move a short
distance against a spring, allowing fuel to flow out
the orifice. Because the fuel is under high pressure, a
fine spray is developed in the shape of a pencil
stream. The spraying action atomizes the fuel, add-
ing it to the air entering the combustion chamber.
The nozzle (outlet) ends of the injectors are posi-
tioned into openings in the intake manifold just
above the intake valve ports of the cylinder head.
The engine wiring harness connector for each fuel
injector is equipped with an attached numerical tag
(INJ 1, INJ 2 etc.). This is used to identify each fuel
injector.
The injectors are energized individually in a
sequential order by the Powertrain Control Module(PCM). The PCM will adjust injector pulse width by
switching the ground path to each individual injector
on and off. Injector pulse width is the period of time
that the injector is energized. The PCM will adjust
injector pulse width based on various inputs it
receives.
Battery voltage is supplied to the injectors through
the ASD relay.
The PCM determines injector pulse width based on
various inputs.
OPERATION - PCM OUTPUT
The nozzle ends of the injectors are positioned into
openings in the intake manifold just above the intake
valve ports of the cylinder head. The engine wiring
harness connector for each fuel injector is equipped
with an attached numerical tag (INJ 1, INJ 2 etc.).
This is used to identify each fuel injector with its
respective cylinder number.
The injectors are energized individually in a
sequential order by the Powertrain Control Module
(PCM). The PCM will adjust injector pulse width by
switching the ground path to each individual injector
on and off. Injector pulse width is the period of time
that the injector is energized. The PCM will adjust
injector pulse width based on various inputs it
receives.
Battery voltage (12 volts +) is supplied to the injec-
tors through the ASD relay. The ASD relay will shut-
down the 12 volt power source to the fuel injectors if
the PCM senses the ignition is on, but the engine is
not running. This occurs after the engine has not
been running for approximately 1.8 seconds.
The PCM determines injector on-time (pulse width)
based on various inputs.
DIAGNOSIS AND TESTING - FUEL INJECTOR
To perform a complete test of the fuel injectors and
their circuitry, use the DRB scan tool and refer to the
appropriate Powertrain Diagnostics Procedures man-
ual. To test the injector only, refer to the following:
Disconnect the fuel injector wire harness connector
from the injector. The injector is equipped with 2
electrical terminals (pins). Place an ohmmeter across
the terminals. Resistance reading should be approxi-
mately 12 ohms 1.2 ohms at 20ÉC (68ÉF).
Fig. 9 FUEL INJECTOR Ð TYPICAL
KJFUEL INJECTION 14 - 33
Page 1750 of 1803
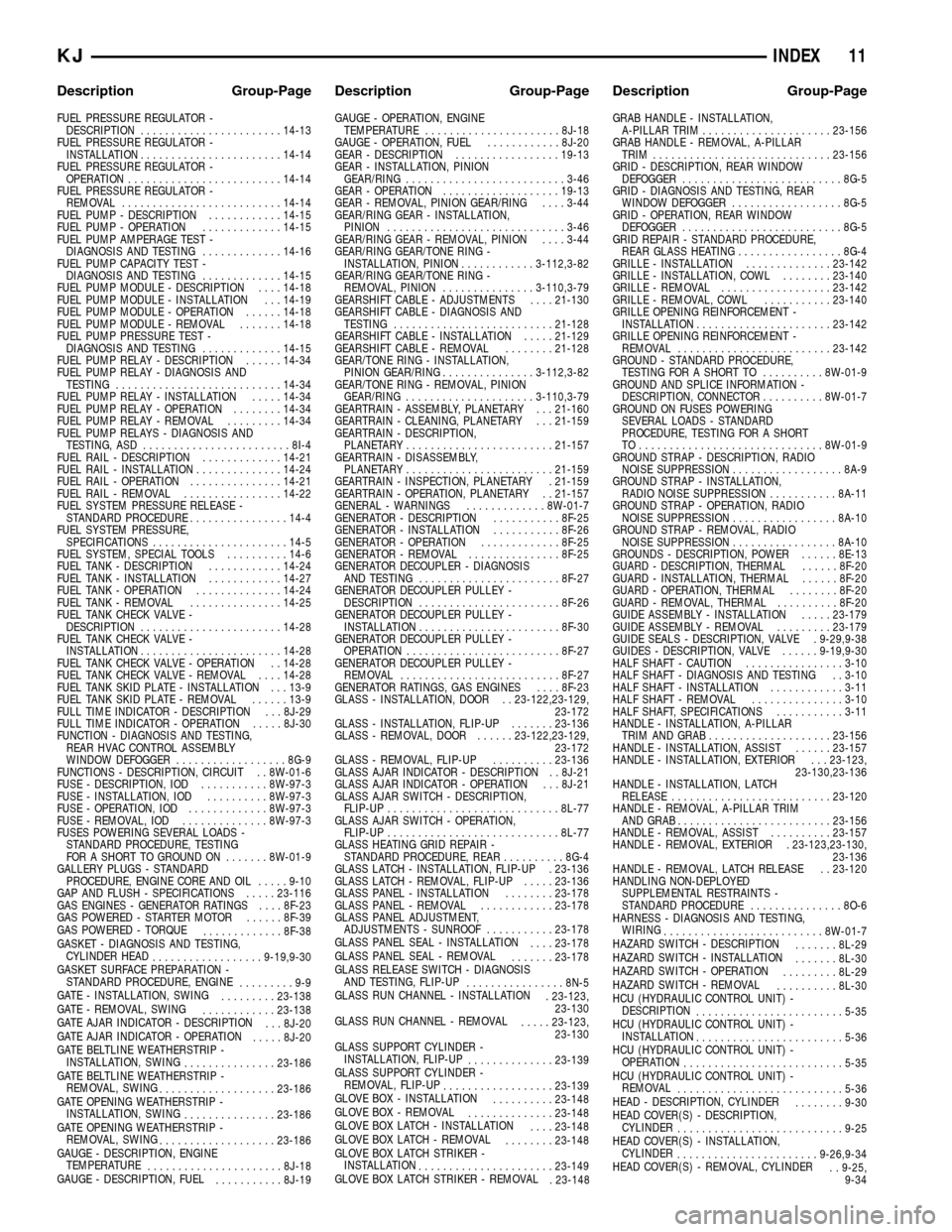
FUEL PRESSURE REGULATOR -
DESCRIPTION.......................14-13
FUEL PRESSURE REGULATOR -
INSTALLATION.......................14-14
FUEL PRESSURE REGULATOR -
OPERATION.........................14-14
FUEL PRESSURE REGULATOR -
REMOVAL..........................14-14
FUEL PUMP - DESCRIPTION............14-15
FUEL PUMP - OPERATION.............14-15
FUEL PUMP AMPERAGE TEST -
DIAGNOSIS AND TESTING.............14-16
FUEL PUMP CAPACITY TEST -
DIAGNOSIS AND TESTING.............14-15
FUEL PUMP MODULE - DESCRIPTION....14-18
FUEL PUMP MODULE - INSTALLATION . . . 14-19
FUEL PUMP MODULE - OPERATION......14-18
FUEL PUMP MODULE - REMOVAL.......14-18
FUEL PUMP PRESSURE TEST -
DIAGNOSIS AND TESTING.............14-15
FUEL PUMP RELAY - DESCRIPTION......14-34
FUEL PUMP RELAY - DIAGNOSIS AND
TESTING...........................14-34
FUEL PUMP RELAY - INSTALLATION.....14-34
FUEL PUMP RELAY - OPERATION........14-34
FUEL PUMP RELAY - REMOVAL.........14-34
FUEL PUMP RELAYS - DIAGNOSIS AND
TESTING, ASD........................8I-4
FUEL RAIL - DESCRIPTION.............14-21
FUEL RAIL - INSTALLATION..............14-24
FUEL RAIL - OPERATION...............14-21
FUEL RAIL - REMOVAL................14-22
FUEL SYSTEM PRESSURE RELEASE -
STANDARD PROCEDURE................14-4
FUEL SYSTEM PRESSURE,
SPECIFICATIONS......................14-5
FUEL SYSTEM, SPECIAL TOOLS..........14-6
FUEL TANK - DESCRIPTION............14-24
FUEL TANK - INSTALLATION............14-27
FUEL TANK - OPERATION..............14-24
FUEL TANK - REMOVAL...............14-25
FUEL TANK CHECK VALVE -
DESCRIPTION.......................14-28
FUEL TANK CHECK VALVE -
INSTALLATION.......................14-28
FUEL TANK CHECK VALVE - OPERATION . . 14-28
FUEL TANK CHECK VALVE - REMOVAL....14-28
FUEL TANK SKID PLATE - INSTALLATION . . . 13-9
FUEL TANK SKID PLATE - REMOVAL......13-9
FULL TIME INDICATOR - DESCRIPTION . . . 8J-29
FULL TIME INDICATOR - OPERATION.....8J-30
FUNCTION - DIAGNOSIS AND TESTING,
REAR HVAC CONTROL ASSEMBLY
WINDOW DEFOGGER..................8G-9
FUNCTIONS - DESCRIPTION, CIRCUIT . . 8W-01-6
FUSE - DESCRIPTION, IOD...........8W-97-3
FUSE - INSTALLATION, IOD..........8W-97-3
FUSE - OPERATION, IOD.............8W-97-3
FUSE - REMOVAL, IOD..............8W-97-3
FUSES POWERING SEVERAL LOADS -
STANDARD PROCEDURE, TESTING
FOR A SHORT TO GROUND ON.......8W-01-9
GALLERY PLUGS - STANDARD
PROCEDURE, ENGINE CORE AND OIL.....9-10
GAP AND FLUSH - SPECIFICATIONS.....23-116
GAS ENGINES - GENERATOR RATINGS....8F-23
GAS POWERED - STARTER MOTOR......8F-39
GAS POWERED - TORQUE
.............8F-38
GASKET - DIAGNOSIS AND TESTING,
CYLINDER HEAD
..................9-19,9-30
GASKET SURFACE PREPARATION -
STANDARD PROCEDURE, ENGINE
.........9-9
GATE - INSTALLATION, SWING
.........23-138
GATE - REMOVAL, SWING
............23-138
GATE AJAR INDICATOR - DESCRIPTION
. . . 8J-20
GATE AJAR INDICATOR - OPERATION
.....8J-20
GATE BELTLINE WEATHERSTRIP -
INSTALLATION, SWING
...............23-186
GATE BELTLINE WEATHERSTRIP -
REMOVAL, SWING
...................23-186
GATE OPENING WEATHERSTRIP -
INSTALLATION, SWING
...............23-186
GATE OPENING WEATHERSTRIP -
REMOVAL, SWING
...................23-186
GAUGE - DESCRIPTION, ENGINE
TEMPERATURE
......................8J-18
GAUGE - DESCRIPTION, FUEL
...........8J-19GAUGE - OPERATION, ENGINE
TEMPERATURE......................8J-18
GAUGE - OPERATION, FUEL............8J-20
GEAR - DESCRIPTION.................19-13
GEAR - INSTALLATION, PINION
GEAR/RING..........................3-46
GEAR - OPERATION...................19-13
GEAR - REMOVAL, PINION GEAR/RING....3-44
GEAR/RING GEAR - INSTALLATION,
PINION.............................3-46
GEAR/RING GEAR - REMOVAL, PINION....3-44
GEAR/RING GEAR/TONE RING -
INSTALLATION, PINION............3-112,3-82
GEAR/RING GEAR/TONE RING -
REMOVAL, PINION...............3-110,3-79
GEARSHIFT CABLE - ADJUSTMENTS....21-130
GEARSHIFT CABLE - DIAGNOSIS AND
TESTING..........................21-128
GEARSHIFT CABLE - INSTALLATION.....21-129
GEARSHIFT CABLE - REMOVAL........21-128
GEAR/TONE RING - INSTALLATION,
PINION GEAR/RING...............3-112,3-82
GEAR/TONE RING - REMOVAL, PINION
GEAR/RING.....................3-110,3-79
GEARTRAIN - ASSEMBLY, PLANETARY . . . 21-160
GEARTRAIN - CLEANING, PLANETARY . . . 21-159
GEARTRAIN - DESCRIPTION,
PLANETARY........................21-157
GEARTRAIN - DISASSEMBLY,
PLANETARY........................21-159
GEARTRAIN - INSPECTION, PLANETARY . 21-159
GEARTRAIN - OPERATION, PLANETARY . . 21-157
GENERAL - WARNINGS.............8W-01-7
GENERATOR - DESCRIPTION...........8F-25
GENERATOR - INSTALLATION...........8F-26
GENERATOR - OPERATION.............8F-25
GENERATOR - REMOVAL...............8F-25
GENERATOR DECOUPLER - DIAGNOSIS
AND TESTING.......................8F-27
GENERATOR DECOUPLER PULLEY -
DESCRIPTION.......................8F-26
GENERATOR DECOUPLER PULLEY -
INSTALLATION.......................8F-30
GENERATOR DECOUPLER PULLEY -
OPERATION.........................8F-27
GENERATOR DECOUPLER PULLEY -
REMOVAL..........................8F-27
GENERATOR RATINGS, GAS ENGINES....8F-23
GLASS - INSTALLATION, DOOR . . 23-122,23-129,
23-172
GLASS - INSTALLATION, FLIP-UP.......23-136
GLASS - REMOVAL, DOOR......23-122,23-129,
23-172
GLASS - REMOVAL, FLIP-UP..........23-136
GLASS AJAR INDICATOR - DESCRIPTION . . 8J-21
GLASS AJAR INDICATOR - OPERATION . . . 8J-21
GLASS AJAR SWITCH - DESCRIPTION,
FLIP-UP............................8L-77
GLASS AJAR SWITCH - OPERATION,
FLIP-UP............................8L-77
GLASS HEATING GRID REPAIR -
STANDARD PROCEDURE, REAR..........8G-4
GLASS LATCH - INSTALLATION, FLIP-UP . 23-136
GLASS LATCH - REMOVAL, FLIP-UP.....23-136
GLASS PANEL - INSTALLATION........23-178
GLASS PANEL - REMOVAL............23-178
GLASS PANEL ADJUSTMENT,
ADJUSTMENTS - SUNROOF...........23-178
GLASS PANEL SEAL - INSTALLATION
....23-178
GLASS PANEL SEAL - REMOVAL
.......23-178
GLASS RELEASE SWITCH - DIAGNOSIS
AND TESTING, FLIP-UP
................8N-5
GLASS RUN CHANNEL - INSTALLATION
. 23-123,
23-130
GLASS RUN CHANNEL - REMOVAL
.....23-123,
23-130
GLASS SUPPORT CYLINDER -
INSTALLATION, FLIP-UP
..............23-139
GLASS SUPPORT CYLINDER -
REMOVAL, FLIP-UP
..................23-139
GLOVE BOX - INSTALLATION
..........23-148
GLOVE BOX - REMOVAL
..............23-148
GLOVE BOX LATCH - INSTALLATION
....23-148
GLOVE BOX LATCH - REMOVAL
........23-148
GLOVE BOX LATCH STRIKER -
INSTALLATION
......................23-149
GLOVE BOX LATCH STRIKER - REMOVAL
. 23-148GRAB HANDLE - INSTALLATION,
A-PILLAR TRIM.....................23-156
GRAB HANDLE - REMOVAL, A-PILLAR
TRIM.............................23-156
GRID - DESCRIPTION, REAR WINDOW
DEFOGGER..........................8G-5
GRID - DIAGNOSIS AND TESTING, REAR
WINDOW DEFOGGER..................8G-5
GRID - OPERATION, REAR WINDOW
DEFOGGER..........................8G-5
GRID REPAIR - STANDARD PROCEDURE,
REAR GLASS HEATING.................8G-4
GRILLE - INSTALLATION..............23-142
GRILLE - INSTALLATION, COWL........23-140
GRILLE - REMOVAL..................23-142
GRILLE - REMOVAL, COWL...........23-140
GRILLE OPENING REINFORCEMENT -
INSTALLATION......................23-142
GRILLE OPENING REINFORCEMENT -
REMOVAL.........................23-142
GROUND - STANDARD PROCEDURE,
TESTING FOR A SHORT TO..........8W-01-9
GROUND AND SPLICE INFORMATION -
DESCRIPTION, CONNECTOR..........8W-01-7
GROUND ON FUSES POWERING
SEVERAL LOADS - STANDARD
PROCEDURE, TESTING FOR A SHORT
TO..............................8W-01-9
GROUND STRAP - DESCRIPTION, RADIO
NOISE SUPPRESSION..................8A-9
GROUND STRAP - INSTALLATION,
RADIO NOISE SUPPRESSION...........8A-11
GROUND STRAP - OPERATION, RADIO
NOISE SUPPRESSION.................8A-10
GROUND STRAP - REMOVAL, RADIO
NOISE SUPPRESSION.................8A-10
GROUNDS - DESCRIPTION, POWER......8E-13
GUARD - DESCRIPTION, THERMAL......8F-20
GUARD - INSTALLATION, THERMAL......8F-20
GUARD - OPERATION, THERMAL........8F-20
GUARD - REMOVAL, THERMAL..........8F-20
GUIDE ASSEMBLY - INSTALLATION.....23-179
GUIDE ASSEMBLY - REMOVAL.........23-179
GUIDE SEALS - DESCRIPTION, VALVE . 9-29,9-38
GUIDES - DESCRIPTION, VALVE......9-19,9-30
HALF SHAFT - CAUTION................3-10
HALF SHAFT - DIAGNOSIS AND TESTING . . 3-10
HALF SHAFT - INSTALLATION............3-11
HALF SHAFT - REMOVAL...............3-10
HALF SHAFT, SPECIFICATIONS...........3-11
HANDLE - INSTALLATION, A-PILLAR
TRIM AND GRAB....................23-156
HANDLE - INSTALLATION, ASSIST......23-157
HANDLE - INSTALLATION, EXTERIOR . . . 23-123,
23-130,23-136
HANDLE - INSTALLATION, LATCH
RELEASE..........................23-120
HANDLE - REMOVAL, A-PILLAR TRIM
AND GRAB.........................23-156
HANDLE - REMOVAL, ASSIST..........23-157
HANDLE - REMOVAL, EXTERIOR . 23-123,23-130,
23-136
HANDLE - REMOVAL, LATCH RELEASE . . 23-120
HANDLING NON-DEPLOYED
SUPPLEMENTAL RESTRAINTS -
STANDARD PROCEDURE...............8O-6
HARNESS - DIAGNOSIS AND TESTING,
WIRING
..........................8W-01-7
HAZARD SWITCH - DESCRIPTION
.......8L-29
HAZARD SWITCH - INSTALLATION
.......8L-30
HAZARD SWITCH - OPERATION
.........8L-29
HAZARD SWITCH - REMOVAL
..........8L-30
HCU (HYDRAULIC CONTROL UNIT) -
DESCRIPTION
........................5-35
HCU (HYDRAULIC CONTROL UNIT) -
INSTALLATION
........................5-36
HCU (HYDRAULIC CONTROL UNIT) -
OPERATION
..........................5-35
HCU (HYDRAULIC CONTROL UNIT) -
REMOVAL
...........................5-36
HEAD - DESCRIPTION, CYLINDER
........9-30
HEAD COVER(S) - DESCRIPTION,
CYLINDER
...........................9-25
HEAD COVER(S) - INSTALLATION,
CYLINDER
.......................9-26,9-34
HEAD COVER(S) - REMOVAL, CYLINDER
. . 9-25,
9-34
KJINDEX 11
Description Group-Page Description Group-Page Description Group-Page