service schedule JEEP LIBERTY 2002 KJ / 1.G Workshop Manual
[x] Cancel search | Manufacturer: JEEP, Model Year: 2002, Model line: LIBERTY, Model: JEEP LIBERTY 2002 KJ / 1.GPages: 1803, PDF Size: 62.3 MB
Page 13 of 1803
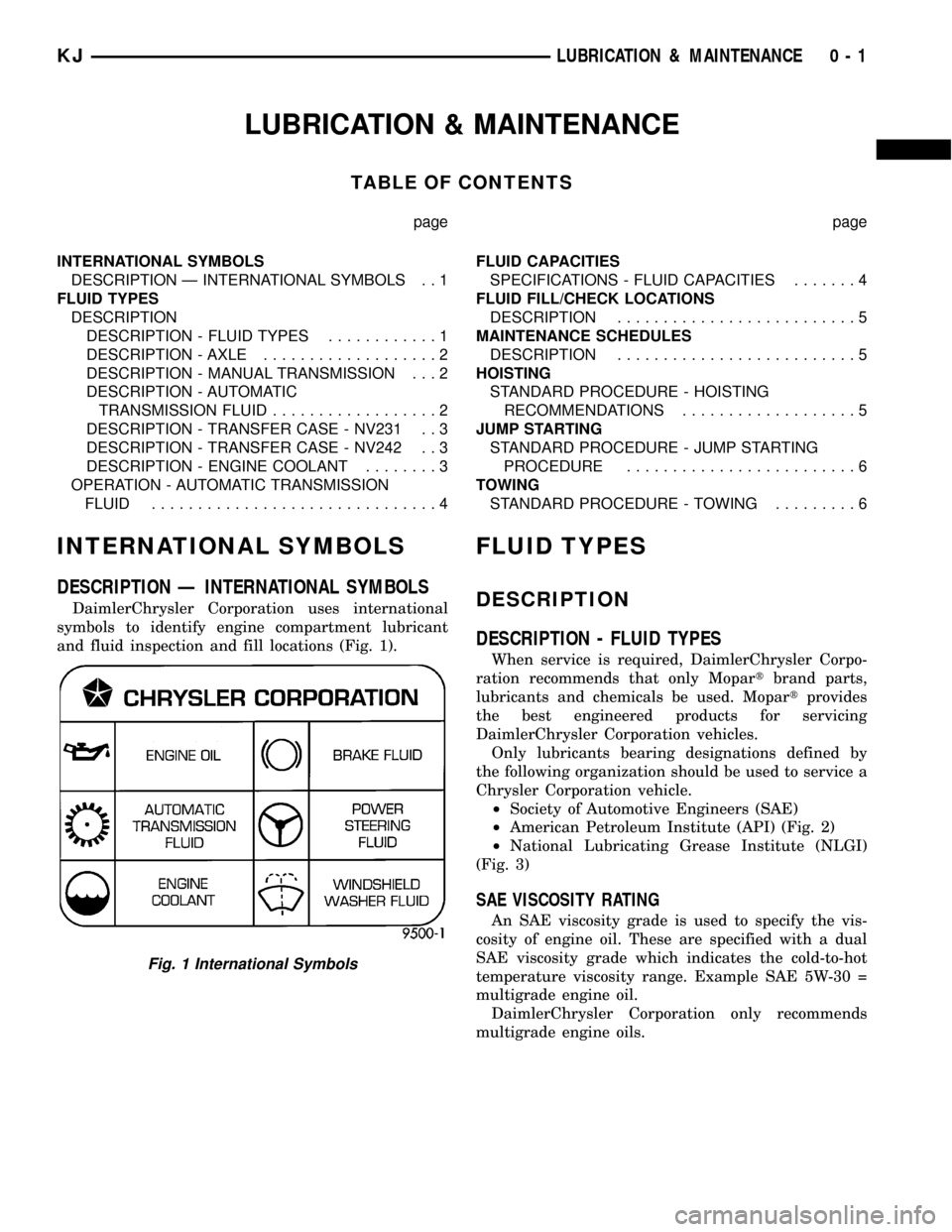
LUBRICATION & MAINTENANCE
TABLE OF CONTENTS
page page
INTERNATIONAL SYMBOLS
DESCRIPTION Ð INTERNATIONAL SYMBOLS . . 1
FLUID TYPES
DESCRIPTION
DESCRIPTION - FLUID TYPES............1
DESCRIPTION - AXLE...................2
DESCRIPTION - MANUAL TRANSMISSION . . . 2
DESCRIPTION - AUTOMATIC
TRANSMISSION FLUID..................2
DESCRIPTION - TRANSFER CASE - NV231 . . 3
DESCRIPTION - TRANSFER CASE - NV242 . . 3
DESCRIPTION - ENGINE COOLANT........3
OPERATION - AUTOMATIC TRANSMISSION
FLUID...............................4FLUID CAPACITIES
SPECIFICATIONS - FLUID CAPACITIES.......4
FLUID FILL/CHECK LOCATIONS
DESCRIPTION..........................5
MAINTENANCE SCHEDULES
DESCRIPTION..........................5
HOISTING
STANDARD PROCEDURE - HOISTING
RECOMMENDATIONS...................5
JUMP STARTING
STANDARD PROCEDURE - JUMP STARTING
PROCEDURE.........................6
TOWING
STANDARD PROCEDURE - TOWING.........6
INTERNATIONAL SYMBOLS
DESCRIPTION Ð INTERNATIONAL SYMBOLS
DaimlerChrysler Corporation uses international
symbols to identify engine compartment lubricant
and fluid inspection and fill locations (Fig. 1).
FLUID TYPES
DESCRIPTION
DESCRIPTION - FLUID TYPES
When service is required, DaimlerChrysler Corpo-
ration recommends that only Mopartbrand parts,
lubricants and chemicals be used. Mopartprovides
the best engineered products for servicing
DaimlerChrysler Corporation vehicles.
Only lubricants bearing designations defined by
the following organization should be used to service a
Chrysler Corporation vehicle.
²Society of Automotive Engineers (SAE)
²American Petroleum Institute (API) (Fig. 2)
²National Lubricating Grease Institute (NLGI)
(Fig. 3)
SAE VISCOSITY RATING
An SAE viscosity grade is used to specify the vis-
cosity of engine oil. These are specified with a dual
SAE viscosity grade which indicates the cold-to-hot
temperature viscosity range. Example SAE 5W-30 =
multigrade engine oil.
DaimlerChrysler Corporation only recommends
multigrade engine oils.
Fig. 1 International Symbols
KJLUBRICATION & MAINTENANCE 0 - 1
Page 14 of 1803
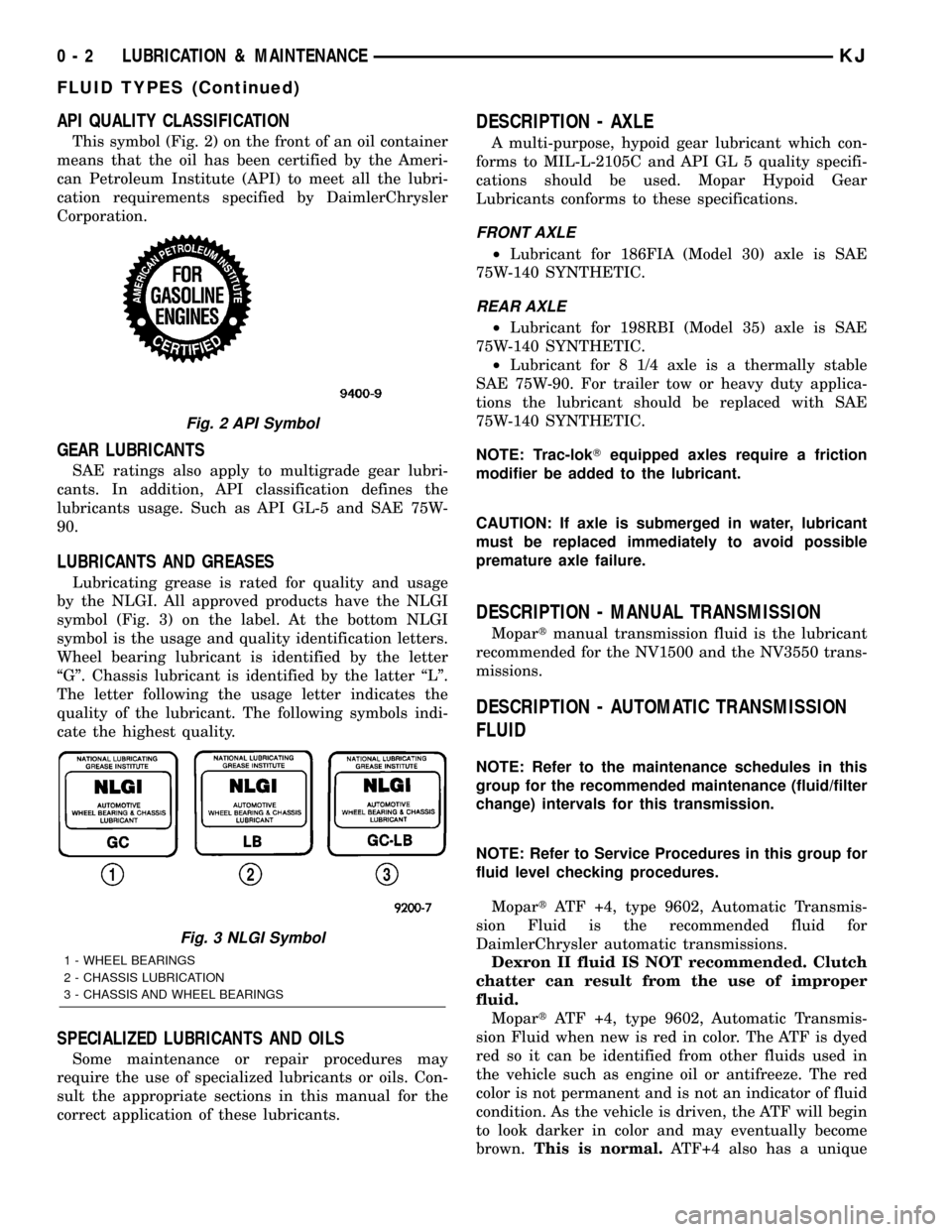
API QUALITY CLASSIFICATION
This symbol (Fig. 2) on the front of an oil container
means that the oil has been certified by the Ameri-
can Petroleum Institute (API) to meet all the lubri-
cation requirements specified by DaimlerChrysler
Corporation.
GEAR LUBRICANTS
SAE ratings also apply to multigrade gear lubri-
cants. In addition, API classification defines the
lubricants usage. Such as API GL-5 and SAE 75W-
90.
LUBRICANTS AND GREASES
Lubricating grease is rated for quality and usage
by the NLGI. All approved products have the NLGI
symbol (Fig. 3) on the label. At the bottom NLGI
symbol is the usage and quality identification letters.
Wheel bearing lubricant is identified by the letter
ªGº. Chassis lubricant is identified by the latter ªLº.
The letter following the usage letter indicates the
quality of the lubricant. The following symbols indi-
cate the highest quality.
SPECIALIZED LUBRICANTS AND OILS
Some maintenance or repair procedures may
require the use of specialized lubricants or oils. Con-
sult the appropriate sections in this manual for the
correct application of these lubricants.
DESCRIPTION - AXLE
A multi-purpose, hypoid gear lubricant which con-
forms to MIL-L-2105C and API GL 5 quality specifi-
cations should be used. Mopar Hypoid Gear
Lubricants conforms to these specifications.
FRONT AXLE
²Lubricant for 186FIA (Model 30) axle is SAE
75W-140 SYNTHETIC.
REAR AXLE
²Lubricant for 198RBI (Model 35) axle is SAE
75W-140 SYNTHETIC.
²Lubricant for 8 1/4 axle is a thermally stable
SAE 75W-90. For trailer tow or heavy duty applica-
tions the lubricant should be replaced with SAE
75W-140 SYNTHETIC.
NOTE: Trac-lokTequipped axles require a friction
modifier be added to the lubricant.
CAUTION: If axle is submerged in water, lubricant
must be replaced immediately to avoid possible
premature axle failure.
DESCRIPTION - MANUAL TRANSMISSION
Mopartmanual transmission fluid is the lubricant
recommended for the NV1500 and the NV3550 trans-
missions.
DESCRIPTION - AUTOMATIC TRANSMISSION
FLUID
NOTE: Refer to the maintenance schedules in this
group for the recommended maintenance (fluid/filter
change) intervals for this transmission.
NOTE: Refer to Service Procedures in this group for
fluid level checking procedures.
MopartATF +4, type 9602, Automatic Transmis-
sion Fluid is the recommended fluid for
DaimlerChrysler automatic transmissions.
Dexron II fluid IS NOT recommended. Clutch
chatter can result from the use of improper
fluid.
MopartATF +4, type 9602, Automatic Transmis-
sion Fluid when new is red in color. The ATF is dyed
red so it can be identified from other fluids used in
the vehicle such as engine oil or antifreeze. The red
color is not permanent and is not an indicator of fluid
condition. As the vehicle is driven, the ATF will begin
to look darker in color and may eventually become
brown.This is normal.ATF+4 also has a unique
Fig. 2 API Symbol
Fig. 3 NLGI Symbol
1 - WHEEL BEARINGS
2 - CHASSIS LUBRICATION
3 - CHASSIS AND WHEEL BEARINGS
0 - 2 LUBRICATION & MAINTENANCEKJ
FLUID TYPES (Continued)
Page 17 of 1803
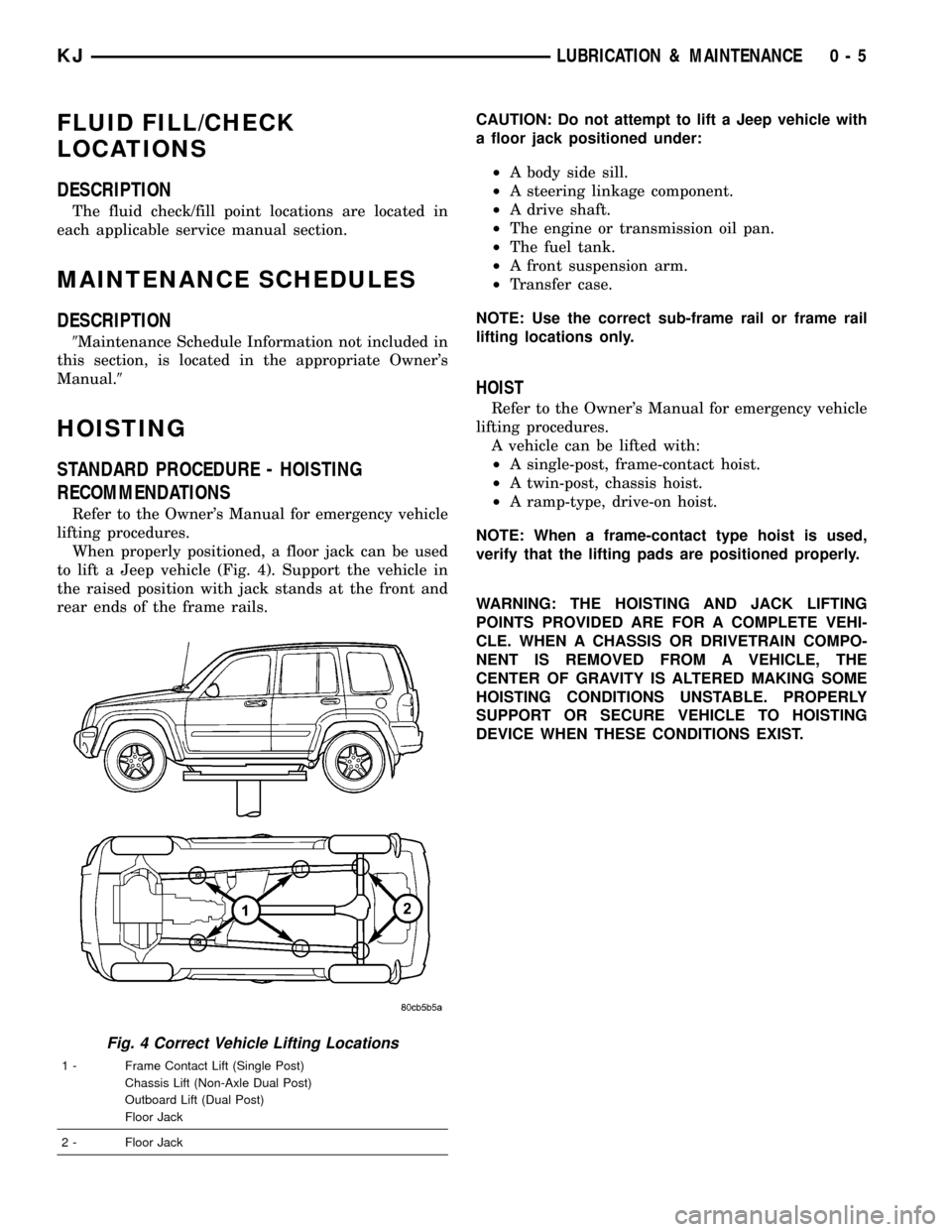
FLUID FILL/CHECK
LOCATIONS
DESCRIPTION
The fluid check/fill point locations are located in
each applicable service manual section.
MAINTENANCE SCHEDULES
DESCRIPTION
9Maintenance Schedule Information not included in
this section, is located in the appropriate Owner's
Manual.9
HOISTING
STANDARD PROCEDURE - HOISTING
RECOMMENDATIONS
Refer to the Owner's Manual for emergency vehicle
lifting procedures.
When properly positioned, a floor jack can be used
to lift a Jeep vehicle (Fig. 4). Support the vehicle in
the raised position with jack stands at the front and
rear ends of the frame rails.CAUTION: Do not attempt to lift a Jeep vehicle with
a floor jack positioned under:
²A body side sill.
²A steering linkage component.
²A drive shaft.
²The engine or transmission oil pan.
²The fuel tank.
²A front suspension arm.
²Transfer case.
NOTE: Use the correct sub-frame rail or frame rail
lifting locations only.
HOIST
Refer to the Owner's Manual for emergency vehicle
lifting procedures.
A vehicle can be lifted with:
²A single-post, frame-contact hoist.
²A twin-post, chassis hoist.
²A ramp-type, drive-on hoist.
NOTE: When a frame-contact type hoist is used,
verify that the lifting pads are positioned properly.
WARNING: THE HOISTING AND JACK LIFTING
POINTS PROVIDED ARE FOR A COMPLETE VEHI-
CLE. WHEN A CHASSIS OR DRIVETRAIN COMPO-
NENT IS REMOVED FROM A VEHICLE, THE
CENTER OF GRAVITY IS ALTERED MAKING SOME
HOISTING CONDITIONS UNSTABLE. PROPERLY
SUPPORT OR SECURE VEHICLE TO HOISTING
DEVICE WHEN THESE CONDITIONS EXIST.
Fig. 4 Correct Vehicle Lifting Locations
1 - Frame Contact Lift (Single Post)
Chassis Lift (Non-Axle Dual Post)
Outboard Lift (Dual Post)
Floor Jack
2 - Floor Jack
KJLUBRICATION & MAINTENANCE 0 - 5
Page 325 of 1803
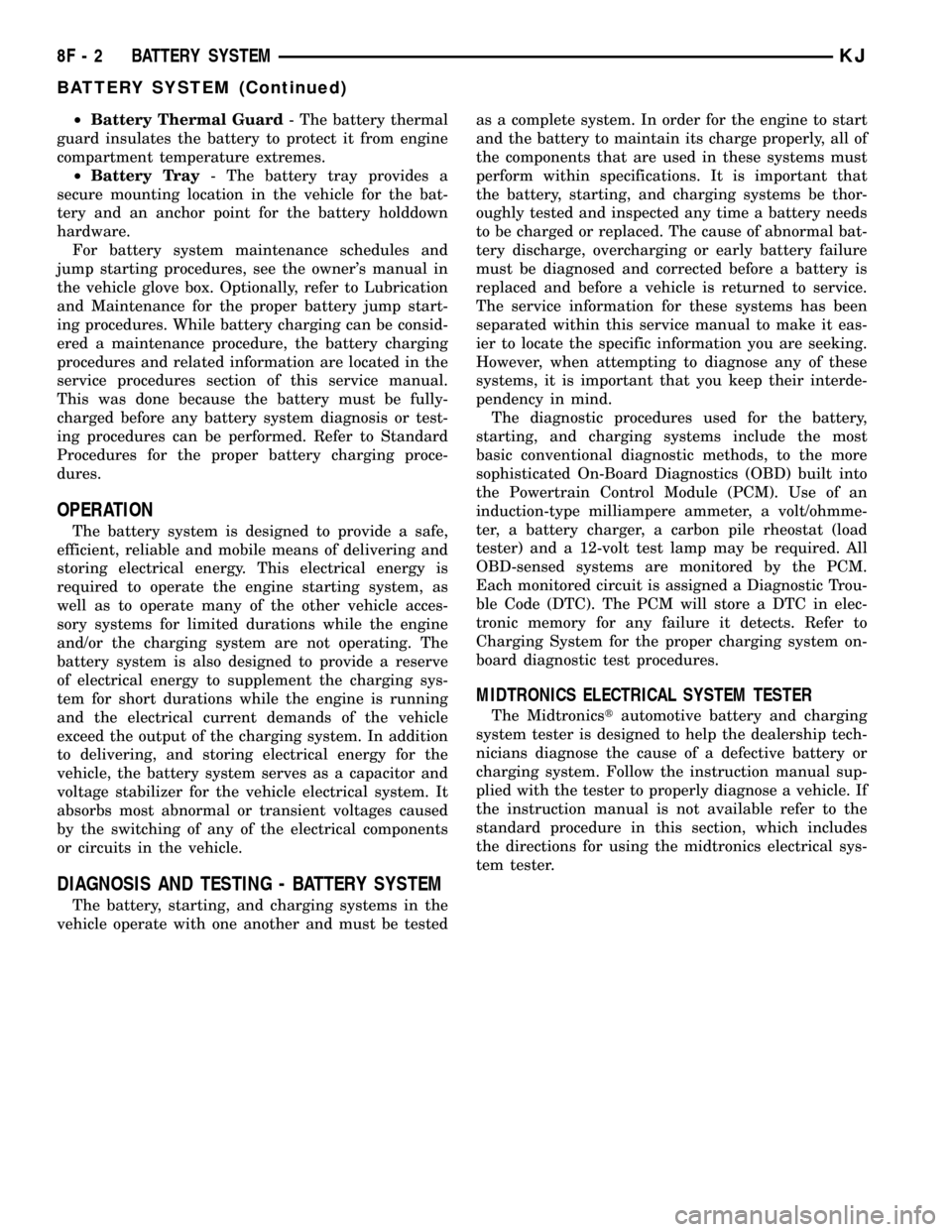
²Battery Thermal Guard- The battery thermal
guard insulates the battery to protect it from engine
compartment temperature extremes.
²Battery Tray- The battery tray provides a
secure mounting location in the vehicle for the bat-
tery and an anchor point for the battery holddown
hardware.
For battery system maintenance schedules and
jump starting procedures, see the owner's manual in
the vehicle glove box. Optionally, refer to Lubrication
and Maintenance for the proper battery jump start-
ing procedures. While battery charging can be consid-
ered a maintenance procedure, the battery charging
procedures and related information are located in the
service procedures section of this service manual.
This was done because the battery must be fully-
charged before any battery system diagnosis or test-
ing procedures can be performed. Refer to Standard
Procedures for the proper battery charging proce-
dures.
OPERATION
The battery system is designed to provide a safe,
efficient, reliable and mobile means of delivering and
storing electrical energy. This electrical energy is
required to operate the engine starting system, as
well as to operate many of the other vehicle acces-
sory systems for limited durations while the engine
and/or the charging system are not operating. The
battery system is also designed to provide a reserve
of electrical energy to supplement the charging sys-
tem for short durations while the engine is running
and the electrical current demands of the vehicle
exceed the output of the charging system. In addition
to delivering, and storing electrical energy for the
vehicle, the battery system serves as a capacitor and
voltage stabilizer for the vehicle electrical system. It
absorbs most abnormal or transient voltages caused
by the switching of any of the electrical components
or circuits in the vehicle.
DIAGNOSIS AND TESTING - BATTERY SYSTEM
The battery, starting, and charging systems in the
vehicle operate with one another and must be testedas a complete system. In order for the engine to start
and the battery to maintain its charge properly, all of
the components that are used in these systems must
perform within specifications. It is important that
the battery, starting, and charging systems be thor-
oughly tested and inspected any time a battery needs
to be charged or replaced. The cause of abnormal bat-
tery discharge, overcharging or early battery failure
must be diagnosed and corrected before a battery is
replaced and before a vehicle is returned to service.
The service information for these systems has been
separated within this service manual to make it eas-
ier to locate the specific information you are seeking.
However, when attempting to diagnose any of these
systems, it is important that you keep their interde-
pendency in mind.
The diagnostic procedures used for the battery,
starting, and charging systems include the most
basic conventional diagnostic methods, to the more
sophisticated On-Board Diagnostics (OBD) built into
the Powertrain Control Module (PCM). Use of an
induction-type milliampere ammeter, a volt/ohmme-
ter, a battery charger, a carbon pile rheostat (load
tester) and a 12-volt test lamp may be required. All
OBD-sensed systems are monitored by the PCM.
Each monitored circuit is assigned a Diagnostic Trou-
ble Code (DTC). The PCM will store a DTC in elec-
tronic memory for any failure it detects. Refer to
Charging System for the proper charging system on-
board diagnostic test procedures.
MIDTRONICS ELECTRICAL SYSTEM TESTER
The Midtronicstautomotive battery and charging
system tester is designed to help the dealership tech-
nicians diagnose the cause of a defective battery or
charging system. Follow the instruction manual sup-
plied with the tester to properly diagnose a vehicle. If
the instruction manual is not available refer to the
standard procedure in this section, which includes
the directions for using the midtronics electrical sys-
tem tester.
8F - 2 BATTERY SYSTEMKJ
BATTERY SYSTEM (Continued)
Page 328 of 1803
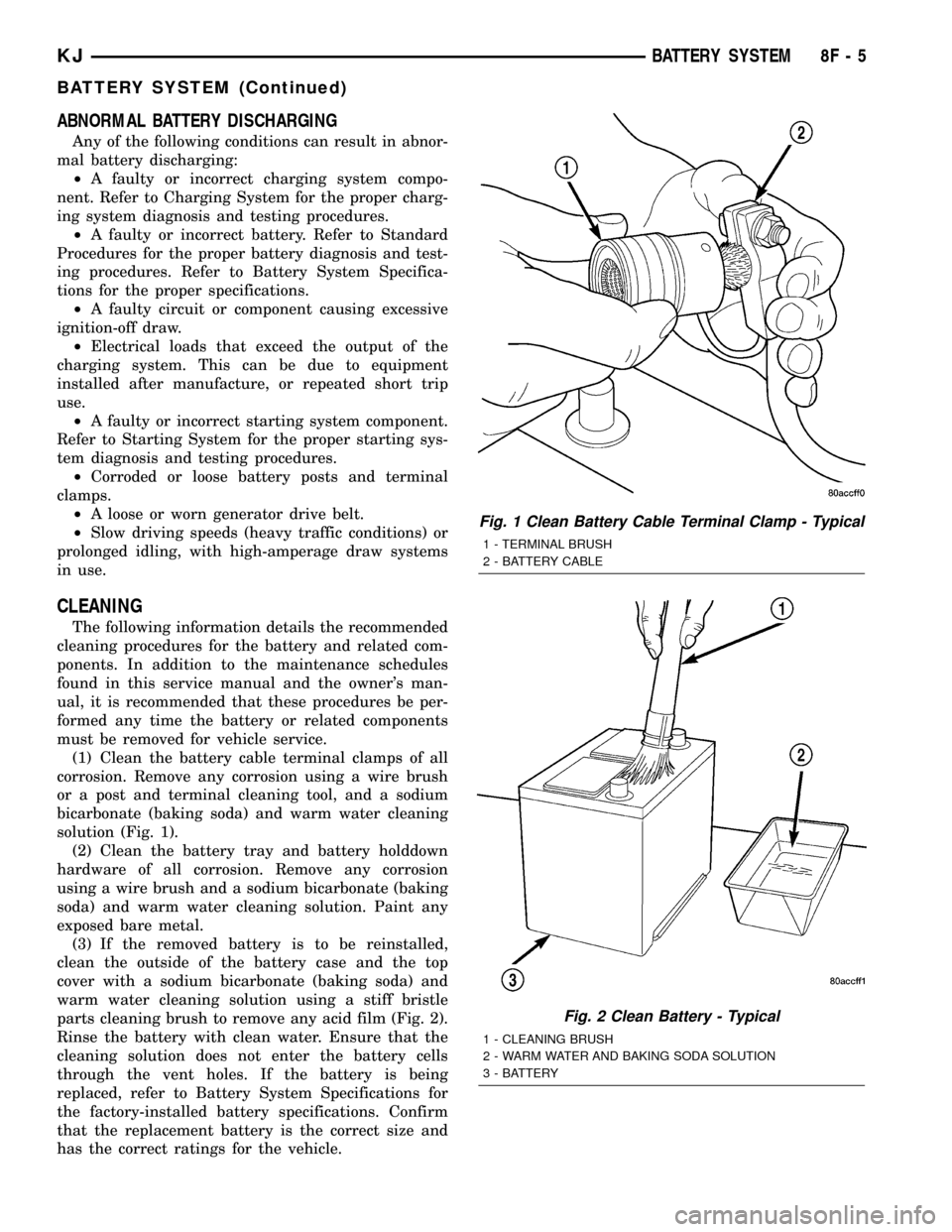
ABNORMAL BATTERY DISCHARGING
Any of the following conditions can result in abnor-
mal battery discharging:
²A faulty or incorrect charging system compo-
nent. Refer to Charging System for the proper charg-
ing system diagnosis and testing procedures.
²A faulty or incorrect battery. Refer to Standard
Procedures for the proper battery diagnosis and test-
ing procedures. Refer to Battery System Specifica-
tions for the proper specifications.
²A faulty circuit or component causing excessive
ignition-off draw.
²Electrical loads that exceed the output of the
charging system. This can be due to equipment
installed after manufacture, or repeated short trip
use.
²A faulty or incorrect starting system component.
Refer to Starting System for the proper starting sys-
tem diagnosis and testing procedures.
²Corroded or loose battery posts and terminal
clamps.
²A loose or worn generator drive belt.
²Slow driving speeds (heavy traffic conditions) or
prolonged idling, with high-amperage draw systems
in use.
CLEANING
The following information details the recommended
cleaning procedures for the battery and related com-
ponents. In addition to the maintenance schedules
found in this service manual and the owner's man-
ual, it is recommended that these procedures be per-
formed any time the battery or related components
must be removed for vehicle service.
(1) Clean the battery cable terminal clamps of all
corrosion. Remove any corrosion using a wire brush
or a post and terminal cleaning tool, and a sodium
bicarbonate (baking soda) and warm water cleaning
solution (Fig. 1).
(2) Clean the battery tray and battery holddown
hardware of all corrosion. Remove any corrosion
using a wire brush and a sodium bicarbonate (baking
soda) and warm water cleaning solution. Paint any
exposed bare metal.
(3) If the removed battery is to be reinstalled,
clean the outside of the battery case and the top
cover with a sodium bicarbonate (baking soda) and
warm water cleaning solution using a stiff bristle
parts cleaning brush to remove any acid film (Fig. 2).
Rinse the battery with clean water. Ensure that the
cleaning solution does not enter the battery cells
through the vent holes. If the battery is being
replaced, refer to Battery System Specifications for
the factory-installed battery specifications. Confirm
that the replacement battery is the correct size and
has the correct ratings for the vehicle.
Fig. 1 Clean Battery Cable Terminal Clamp - Typical
1 - TERMINAL BRUSH
2 - BATTERY CABLE
Fig. 2 Clean Battery - Typical
1 - CLEANING BRUSH
2 - WARM WATER AND BAKING SODA SOLUTION
3 - BATTERY
KJBATTERY SYSTEM 8F - 5
BATTERY SYSTEM (Continued)
Page 1761 of 1803
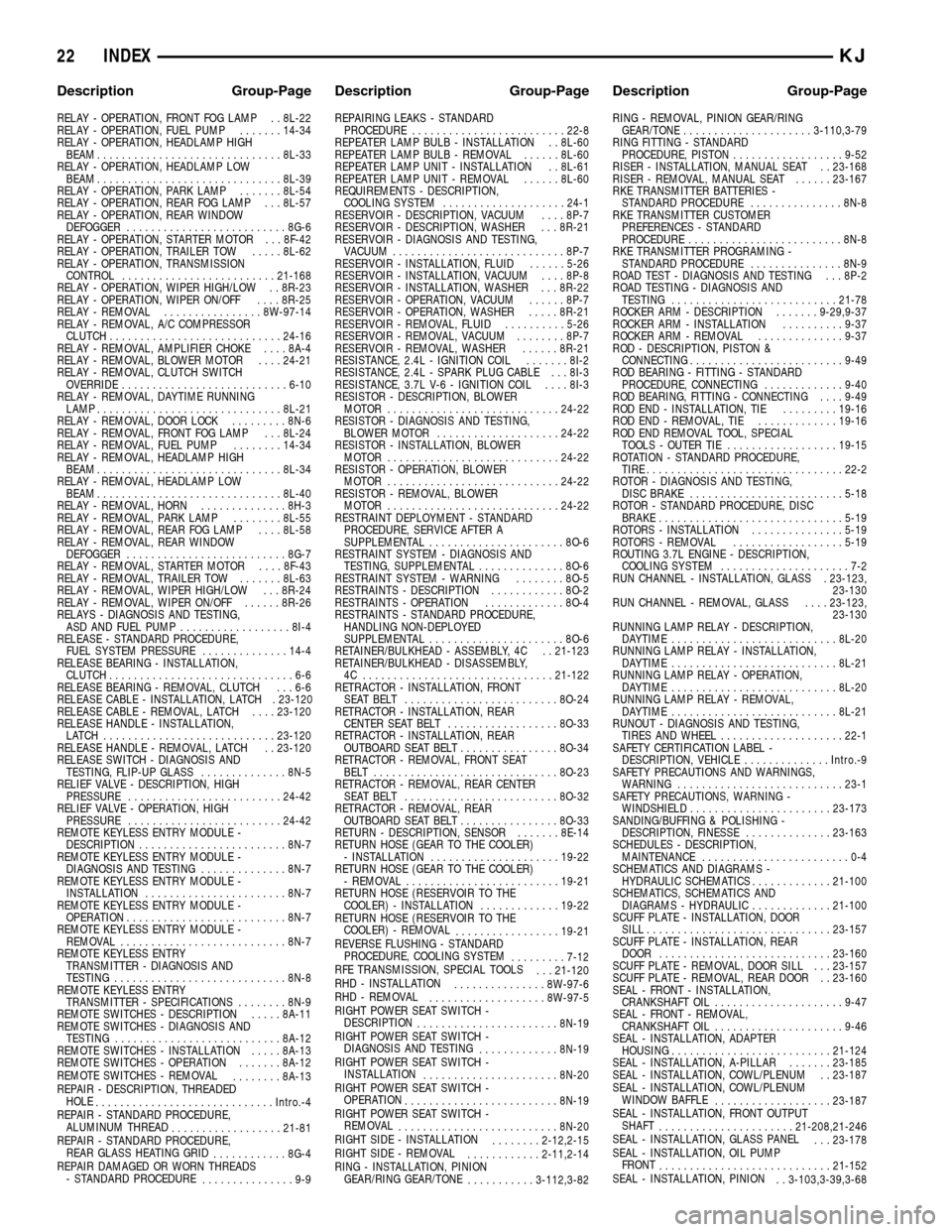
RELAY - OPERATION, FRONT FOG LAMP . . 8L-22
RELAY - OPERATION, FUEL PUMP.......14-34
RELAY - OPERATION, HEADLAMP HIGH
BEAM..............................8L-33
RELAY - OPERATION, HEADLAMP LOW
BEAM..............................8L-39
RELAY - OPERATION, PARK LAMP.......8L-54
RELAY - OPERATION, REAR FOG LAMP . . . 8L-57
RELAY - OPERATION, REAR WINDOW
DEFOGGER..........................8G-6
RELAY - OPERATION, STARTER MOTOR . . . 8F-42
RELAY - OPERATION, TRAILER TOW.....8L-62
RELAY - OPERATION, TRANSMISSION
CONTROL.........................21-168
RELAY - OPERATION, WIPER HIGH/LOW . . 8R-23
RELAY - OPERATION, WIPER ON/OFF....8R-25
RELAY - REMOVAL................8W-97-14
RELAY - REMOVAL, A/C COMPRESSOR
CLUTCH............................24-16
RELAY - REMOVAL, AMPLIFIER CHOKE....8A-4
RELAY - REMOVAL, BLOWER MOTOR....24-21
RELAY - REMOVAL, CLUTCH SWITCH
OVERRIDE...........................6-10
RELAY - REMOVAL, DAYTIME RUNNING
LAMP..............................8L-21
RELAY - REMOVAL, DOOR LOCK.........8N-6
RELAY - REMOVAL, FRONT FOG LAMP . . . 8L-24
RELAY - REMOVAL, FUEL PUMP........14-34
RELAY - REMOVAL, HEADLAMP HIGH
BEAM..............................8L-34
RELAY - REMOVAL, HEADLAMP LOW
BEAM..............................8L-40
RELAY - REMOVAL, HORN..............8H-3
RELAY - REMOVAL, PARK LAMP........8L-55
RELAY - REMOVAL, REAR FOG LAMP....8L-58
RELAY - REMOVAL, REAR WINDOW
DEFOGGER..........................8G-7
RELAY - REMOVAL, STARTER MOTOR....8F-43
RELAY - REMOVAL, TRAILER TOW.......8L-63
RELAY - REMOVAL, WIPER HIGH/LOW . . . 8R-24
RELAY - REMOVAL, WIPER ON/OFF......8R-26
RELAYS - DIAGNOSIS AND TESTING,
ASD AND FUEL PUMP..................8I-4
RELEASE - STANDARD PROCEDURE,
FUEL SYSTEM PRESSURE..............14-4
RELEASE BEARING - INSTALLATION,
CLUTCH..............................6-6
RELEASE BEARING - REMOVAL, CLUTCH . . . 6-6
RELEASE CABLE - INSTALLATION, LATCH . 23-120
RELEASE CABLE - REMOVAL, LATCH....23-120
RELEASE HANDLE - INSTALLATION,
LATCH ............................23-120
RELEASE HANDLE - REMOVAL, LATCH . . 23-120
RELEASE SWITCH - DIAGNOSIS AND
TESTING, FLIP-UP GLASS..............8N-5
RELIEF VALVE - DESCRIPTION, HIGH
PRESSURE.........................24-42
RELIEF VALVE - OPERATION, HIGH
PRESSURE.........................24-42
REMOTE KEYLESS ENTRY MODULE -
DESCRIPTION........................8N-7
REMOTE KEYLESS ENTRY MODULE -
DIAGNOSIS AND TESTING..............8N-7
REMOTE KEYLESS ENTRY MODULE -
INSTALLATION.......................8N-7
REMOTE KEYLESS ENTRY MODULE -
OPERATION..........................8N-7
REMOTE KEYLESS ENTRY MODULE -
REMOVAL...........................8N-7
REMOTE KEYLESS ENTRY
TRANSMITTER - DIAGNOSIS AND
TESTING............................8N-8
REMOTE KEYLESS ENTRY
TRANSMITTER - SPECIFICATIONS........8N-9
REMOTE SWITCHES - DESCRIPTION.....8A-11
REMOTE SWITCHES - DIAGNOSIS AND
TESTING...........................8A-12
REMOTE SWITCHES - INSTALLATION.....8A-13
REMOTE SWITCHES - OPERATION.......8A-12
REMOTE SWITCHES - REMOVAL
........8A-13
REPAIR - DESCRIPTION, THREADED
HOLE
.............................Intro.-4
REPAIR - STANDARD PROCEDURE,
ALUMINUM THREAD
..................21-81
REPAIR - STANDARD PROCEDURE,
REAR GLASS HEATING GRID
............8G-4
REPAIR DAMAGED OR WORN THREADS
- STANDARD PROCEDURE
...............9-9REPAIRING LEAKS - STANDARD
PROCEDURE.........................22-8
REPEATER LAMP BULB - INSTALLATION . . 8L-60
REPEATER LAMP BULB - REMOVAL......8L-60
REPEATER LAMP UNIT - INSTALLATION . . 8L-61
REPEATER LAMP UNIT - REMOVAL......8L-60
REQUIREMENTS - DESCRIPTION,
COOLING SYSTEM....................24-1
RESERVOIR - DESCRIPTION, VACUUM....8P-7
RESERVOIR - DESCRIPTION, WASHER . . . 8R-21
RESERVOIR - DIAGNOSIS AND TESTING,
VACUUM............................8P-7
RESERVOIR - INSTALLATION, FLUID......5-26
RESERVOIR - INSTALLATION, VACUUM....8P-8
RESERVOIR - INSTALLATION, WASHER . . . 8R-22
RESERVOIR - OPERATION, VACUUM......8P-7
RESERVOIR - OPERATION, WASHER.....8R-21
RESERVOIR - REMOVAL, FLUID..........5-26
RESERVOIR - REMOVAL, VACUUM........8P-7
RESERVOIR - REMOVAL, WASHER......8R-21
RESISTANCE, 2.4L - IGNITION COIL.......8I-2
RESISTANCE, 2.4L - SPARK PLUG CABLE . . . 8I-3
RESISTANCE, 3.7L V-6 - IGNITION COIL....8I-3
RESISTOR - DESCRIPTION, BLOWER
MOTOR............................24-22
RESISTOR - DIAGNOSIS AND TESTING,
BLOWER MOTOR....................24-22
RESISTOR - INSTALLATION, BLOWER
MOTOR............................24-22
RESISTOR - OPERATION, BLOWER
MOTOR............................24-22
RESISTOR - REMOVAL, BLOWER
MOTOR............................24-22
RESTRAINT DEPLOYMENT - STANDARD
PROCEDURE, SERVICE AFTER A
SUPPLEMENTAL......................8O-6
RESTRAINT SYSTEM - DIAGNOSIS AND
TESTING, SUPPLEMENTAL..............8O-6
RESTRAINT SYSTEM - WARNING........8O-5
RESTRAINTS - DESCRIPTION............8O-2
RESTRAINTS - OPERATION.............8O-4
RESTRAINTS - STANDARD PROCEDURE,
HANDLING NON-DEPLOYED
SUPPLEMENTAL......................8O-6
RETAINER/BULKHEAD - ASSEMBLY, 4C . . 21-123
RETAINER/BULKHEAD - DISASSEMBLY,
4C ...............................21-122
RETRACTOR - INSTALLATION, FRONT
SEAT BELT .........................8O-24
RETRACTOR - INSTALLATION, REAR
CENTER SEAT BELT..................8O-33
RETRACTOR - INSTALLATION, REAR
OUTBOARD SEAT BELT................8O-34
RETRACTOR - REMOVAL, FRONT SEAT
BELT ..............................8O-23
RETRACTOR - REMOVAL, REAR CENTER
SEAT BELT .........................8O-32
RETRACTOR - REMOVAL, REAR
OUTBOARD SEAT BELT................8O-33
RETURN - DESCRIPTION, SENSOR.......8E-14
RETURN HOSE (GEAR TO THE COOLER)
- INSTALLATION.....................19-22
RETURN HOSE (GEAR TO THE COOLER)
- REMOVAL.........................19-21
RETURN HOSE (RESERVOIR TO THE
COOLER) - INSTALLATION.............19-22
RETURN HOSE (RESERVOIR TO THE
COOLER) - REMOVAL
.................19-21
REVERSE FLUSHING - STANDARD
PROCEDURE, COOLING SYSTEM
.........7-12
RFE TRANSMISSION, SPECIAL TOOLS
. . . 21-120
RHD - INSTALLATION
...............8W-97-6
RHD - REMOVAL
...................8W-97-5
RIGHT POWER SEAT SWITCH -
DESCRIPTION
.......................8N-19
RIGHT POWER SEAT SWITCH -
DIAGNOSIS AND TESTING
.............8N-19
RIGHT POWER SEAT SWITCH -
INSTALLATION
......................8N-20
RIGHT POWER SEAT SWITCH -
OPERATION
.........................8N-19
RIGHT POWER SEAT SWITCH -
REMOVAL
..........................8N-20
RIGHT SIDE - INSTALLATION
........2-12,2-15
RIGHT SIDE - REMOVAL
............2-11,2-14
RING - INSTALLATION, PINION
GEAR/RING GEAR/TONE
...........3-112,3-82RING - REMOVAL, PINION GEAR/RING
GEAR/TONE.....................3-110,3-79
RING FITTING - STANDARD
PROCEDURE, PISTON..................9-52
RISER - INSTALLATION, MANUAL SEAT . . 23-168
RISER - REMOVAL, MANUAL SEAT......23-167
RKE TRANSMITTER BATTERIES -
STANDARD PROCEDURE...............8N-8
RKE TRANSMITTER CUSTOMER
PREFERENCES - STANDARD
PROCEDURE.........................8N-8
RKE TRANSMITTER PROGRAMING -
STANDARD PROCEDURE...............8N-9
ROAD TEST - DIAGNOSIS AND TESTING . . . 8P-2
ROAD TESTING - DIAGNOSIS AND
TESTING...........................21-78
ROCKER ARM - DESCRIPTION.......9-29,9-37
ROCKER ARM - INSTALLATION..........9-37
ROCKER ARM - REMOVAL..............9-37
ROD - DESCRIPTION, PISTON &
CONNECTING.........................9-49
ROD BEARING - FITTING - STANDARD
PROCEDURE, CONNECTING.............9-40
ROD BEARING, FITTING - CONNECTING....9-49
ROD END - INSTALLATION, TIE.........19-16
ROD END - REMOVAL, TIE.............19-16
ROD END REMOVAL TOOL, SPECIAL
TOOLS - OUTER TIE..................19-15
ROTATION - STANDARD PROCEDURE,
TIRE................................22-2
ROTOR - DIAGNOSIS AND TESTING,
DISC BRAKE.........................5-18
ROTOR - STANDARD PROCEDURE, DISC
BRAKE..............................5-19
ROTORS - INSTALLATION...............5-19
ROTORS - REMOVAL..................5-19
ROUTING 3.7L ENGINE - DESCRIPTION,
COOLING SYSTEM.....................7-2
RUN CHANNEL - INSTALLATION, GLASS . 23-123,
23-130
RUN CHANNEL - REMOVAL, GLASS....23-123,
23-130
RUNNING LAMP RELAY - DESCRIPTION,
DAYTIME...........................8L-20
RUNNING LAMP RELAY - INSTALLATION,
DAYTIME...........................8L-21
RUNNING LAMP RELAY - OPERATION,
DAYTIME...........................8L-20
RUNNING LAMP RELAY - REMOVAL,
DAYTIME...........................8L-21
RUNOUT - DIAGNOSIS AND TESTING,
TIRES AND WHEEL....................22-1
SAFETY CERTIFICATION LABEL -
DESCRIPTION, VEHICLE..............Intro.-9
SAFETY PRECAUTIONS AND WARNINGS,
WARNING...........................23-1
SAFETY PRECAUTIONS, WARNING -
WINDSHIELD.......................23-173
SANDING/BUFFING & POLISHING -
DESCRIPTION, FINESSE..............23-163
SCHEDULES - DESCRIPTION,
MAINTENANCE........................0-4
SCHEMATICS AND DIAGRAMS -
HYDRAULIC SCHEMATICS.............21-100
SCHEMATICS, SCHEMATICS AND
DIAGRAMS - HYDRAULIC.............21-100
SCUFF PLATE - INSTALLATION, DOOR
SILL..............................23-157
SCUFF PLATE - INSTALLATION, REAR
DOOR............................23-160
SCUFF PLATE - REMOVAL, DOOR SILL . . . 23-157
SCUFF PLATE - REMOVAL, REAR DOOR . . 23-160
SEAL - FRONT - INSTALLATION,
CRANKSHAFT OIL.....................9-47
SEAL - FRONT - REMOVAL,
CRANKSHAFT OIL.....................9-46
SEAL - INSTALLATION, ADAPTER
HOUSING..........................21-124
SEAL - INSTALLATION, A-PILLAR.......23-185
SEAL - INSTALLATION, COWL/PLENUM . . 23-187
SEAL - INSTALLATION, COWL/PLENUM
WINDOW BAFFLE
...................23-187
SEAL - INSTALLATION, FRONT OUTPUT
SHAFT
......................21-208,21-246
SEAL - INSTALLATION, GLASS PANEL
. . . 23-178
SEAL - INSTALLATION, OIL PUMP
FRONT
............................21-152
SEAL - INSTALLATION, PINION
. . 3-103,3-39,3-68
22 INDEXKJ
Description Group-Page Description Group-Page Description Group-Page