compression ratio LAND ROVER DEFENDER 1999 Workshop Manual
[x] Cancel search | Manufacturer: LAND ROVER, Model Year: 1999, Model line: DEFENDER, Model: LAND ROVER DEFENDER 1999Pages: 667, PDF Size: 8.76 MB
Page 24 of 667
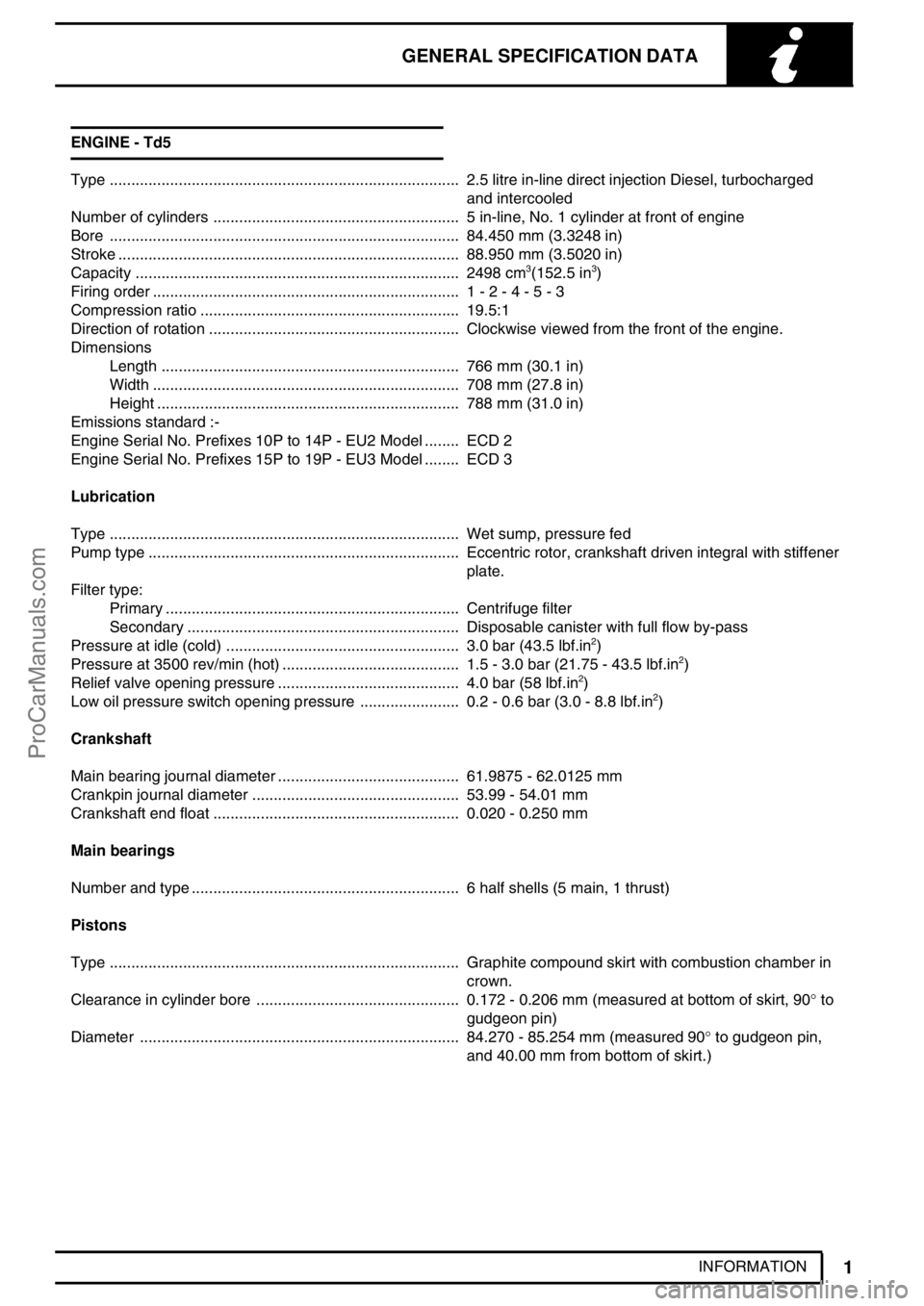
GENERAL SPECIFICATION DATA
1
INFORMATION ENGINE - Td5
Type 2.5 litre in-line direct injection Diesel, turbocharged.................................................................................
and intercooled
Number of cylinders 5 in-line, No. 1 cylinder at front of engine.........................................................
Bore 84.450 mm (3.3248 in).................................................................................
Stroke 88.950 mm (3.5020 in)...............................................................................
Capacity 2498 cm
3(152.5 in3) ...........................................................................
Firing order 1 - 2 - 4 - 5 - 3.......................................................................
Compression ratio 19.5:1............................................................
Direction of rotation Clockwise viewed from the front of the engine...........................................................
Dimensions
Length 766 mm (30.1 in).....................................................................
Width 708 mm (27.8 in).......................................................................
Height 788 mm (31.0 in)......................................................................
Emissions standard :-
Engine Serial No. Prefixes 10P to 14P - EU2 Model ECD 2........
Engine Serial No. Prefixes 15P to 19P - EU3 Model ECD 3........
Lubrication
Type Wet sump, pressure fed.................................................................................
Pump type Eccentric rotor, crankshaft driven integral with stiffener........................................................................
plate.
Filter type:
Primary Centrifuge filter....................................................................
Secondary Disposable canister with full flow by-pass...............................................................
Pressure at idle (cold) 3.0 bar (43.5 lbf.in
2) ......................................................
Pressure at 3500 rev/min (hot) 1.5 - 3.0 bar (21.75 - 43.5 lbf.in2) .........................................
Relief valve opening pressure 4.0 bar (58 lbf.in2) ..........................................
Low oil pressure switch opening pressure 0.2 - 0.6 bar (3.0 - 8.8 lbf.in2) .......................
Crankshaft
Main bearing journal diameter 61.9875 - 62.0125 mm..........................................
Crankpin journal diameter 53.99 - 54.01 mm................................................
Crankshaft end float 0.020 - 0.250 mm.........................................................
Main bearings
Number and type 6 half shells (5 main, 1 thrust)..............................................................
Pistons
Type Graphite compound skirt with combustion chamber in.................................................................................
crown.
Clearance in cylinder bore 0.172 - 0.206 mm (measured at bottom of skirt, 90°to ...............................................
gudgeon pin)
Diameter 84.270 - 85.254 mm (measured 90°to gudgeon pin, ..........................................................................
and 40.00 mm from bottom of skirt.)
ProCarManuals.com
Page 100 of 667
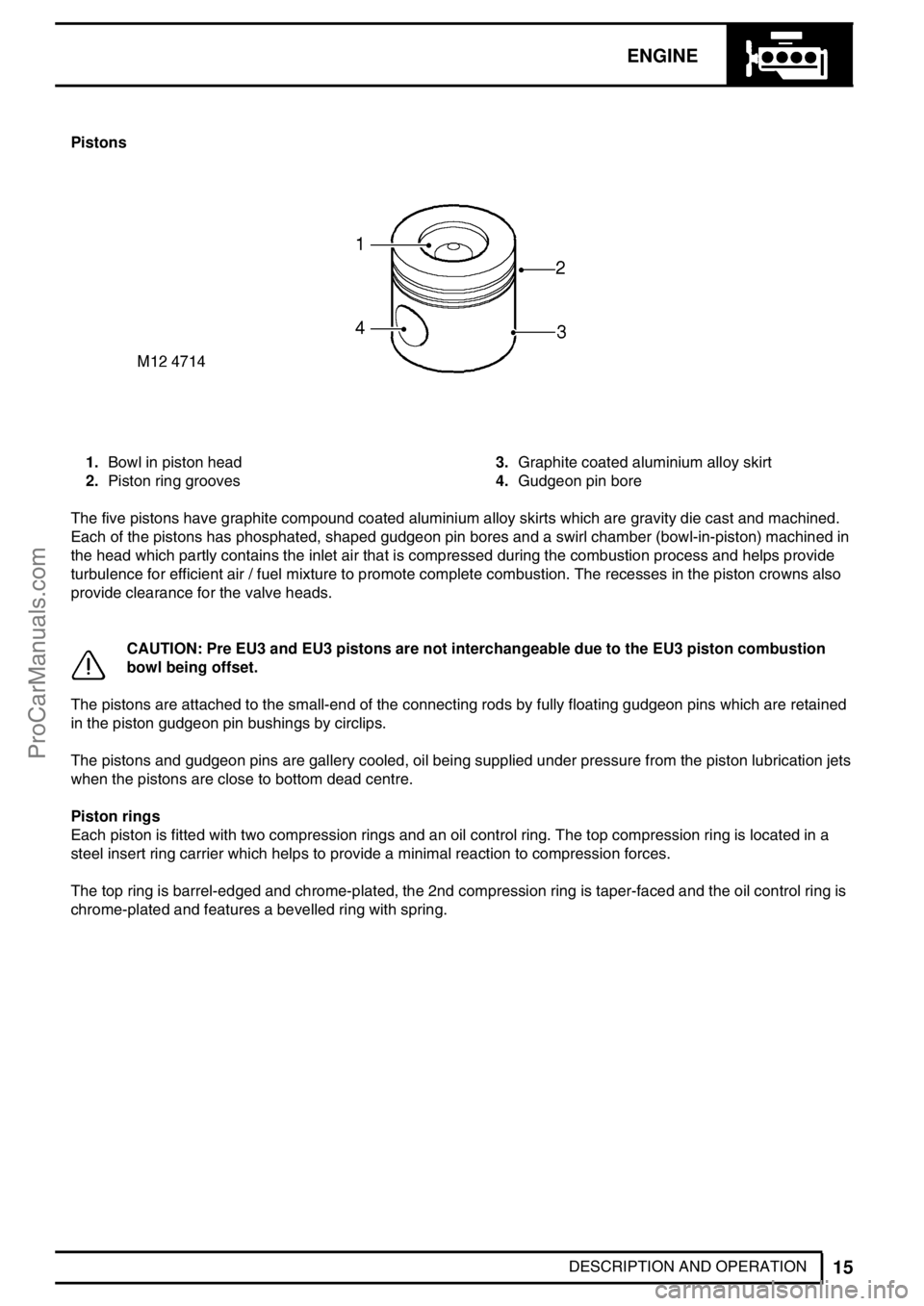
ENGINE
15
DESCRIPTION AND OPERATION Pistons
1.Bowl in piston head
2.Piston ring grooves3.Graphite coated aluminium alloy skirt
4.Gudgeon pin bore
The five pistons have graphite compound coated aluminium alloy skirts which are gravity die cast and machined.
Each of the pistons has phosphated, shaped gudgeon pin bores and a swirl chamber (bowl-in-piston) machined in
the head which partly contains the inlet air that is compressed during the combustion process and helps provide
turbulence for efficient air / fuel mixture to promote complete combustion. The recesses in the piston crowns also
provide clearance for the valve heads.
CAUTION: Pre EU3 and EU3 pistons are not interchangeable due to the EU3 piston combustion
bowl being offset.
The pistons are attached to the small-end of the connecting rods by fully floating gudgeon pins which are retained
in the piston gudgeon pin bushings by circlips.
The pistons and gudgeon pins are gallery cooled, oil being supplied under pressure from the piston lubrication jets
when the pistons are close to bottom dead centre.
Piston rings
Each piston is fitted with two compression rings and an oil control ring. The top compression ring is located in a
steel insert ring carrier which helps to provide a minimal reaction to compression forces.
The top ring is barrel-edged and chrome-plated, the 2nd compression ring is taper-faced and the oil control ring is
chrome-plated and features a bevelled ring with spring.
ProCarManuals.com
Page 107 of 667
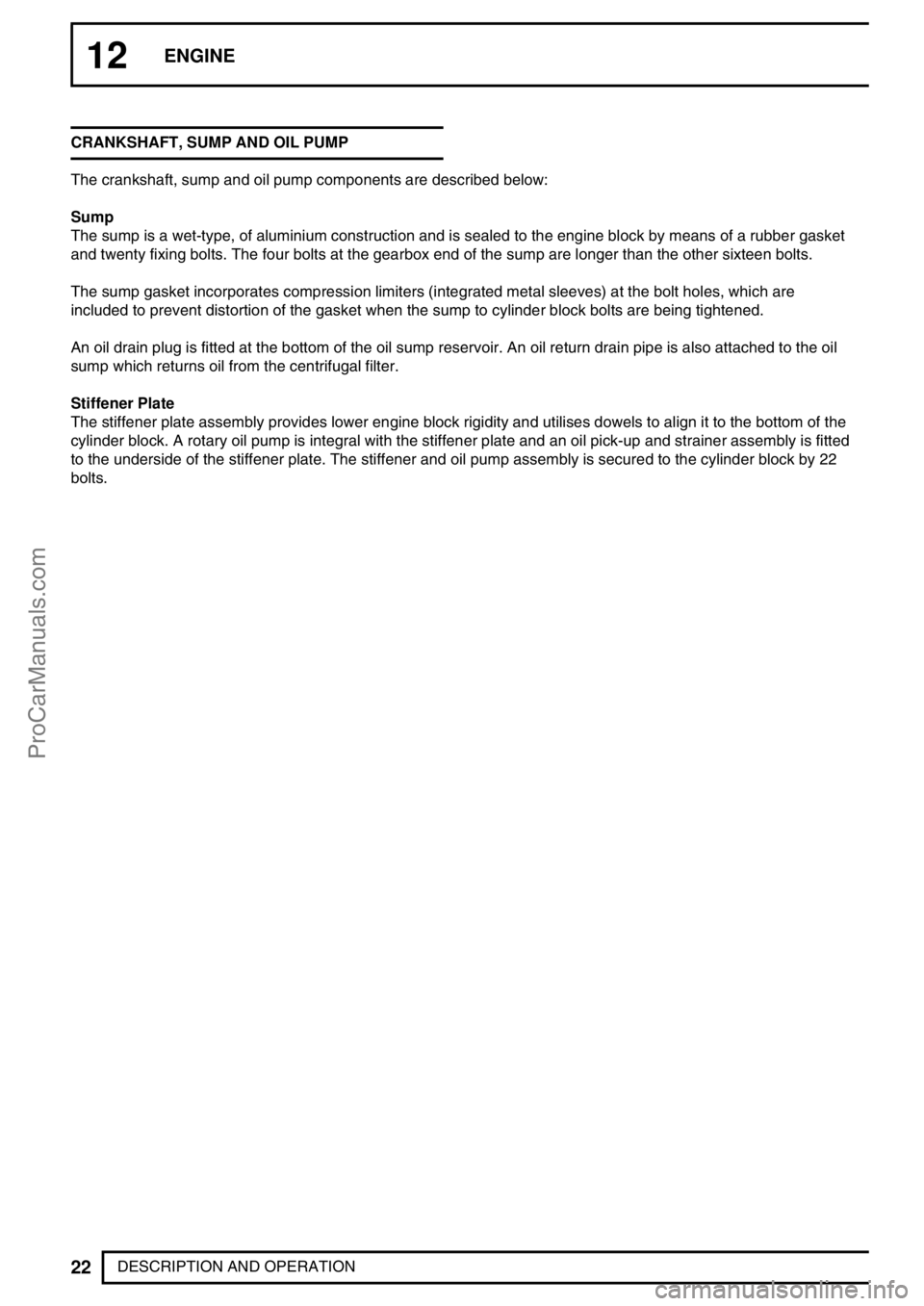
12ENGINE
22
DESCRIPTION AND OPERATION CRANKSHAFT, SUMP AND OIL PUMP
The crankshaft, sump and oil pump components are described below:
Sump
The sump is a wet-type, of aluminium construction and is sealed to the engine block by means of a rubber gasket
and twenty fixing bolts. The four bolts at the gearbox end of the sump are longer than the other sixteen bolts.
The sump gasket incorporates compression limiters (integrated metal sleeves) at the bolt holes, which are
included to prevent distortion of the gasket when the sump to cylinder block bolts are being tightened.
An oil drain plug is fitted at the bottom of the oil sump reservoir. An oil return drain pipe is also attached to the oil
sump which returns oil from the centrifugal filter.
Stiffener Plate
The stiffener plate assembly provides lower engine block rigidity and utilises dowels to align it to the bottom of the
cylinder block. A rotary oil pump is integral with the stiffener plate and an oil pick-up and strainer assembly is fitted
to the underside of the stiffener plate. The stiffener and oil pump assembly is secured to the cylinder block by 22
bolts.
ProCarManuals.com
Page 249 of 667
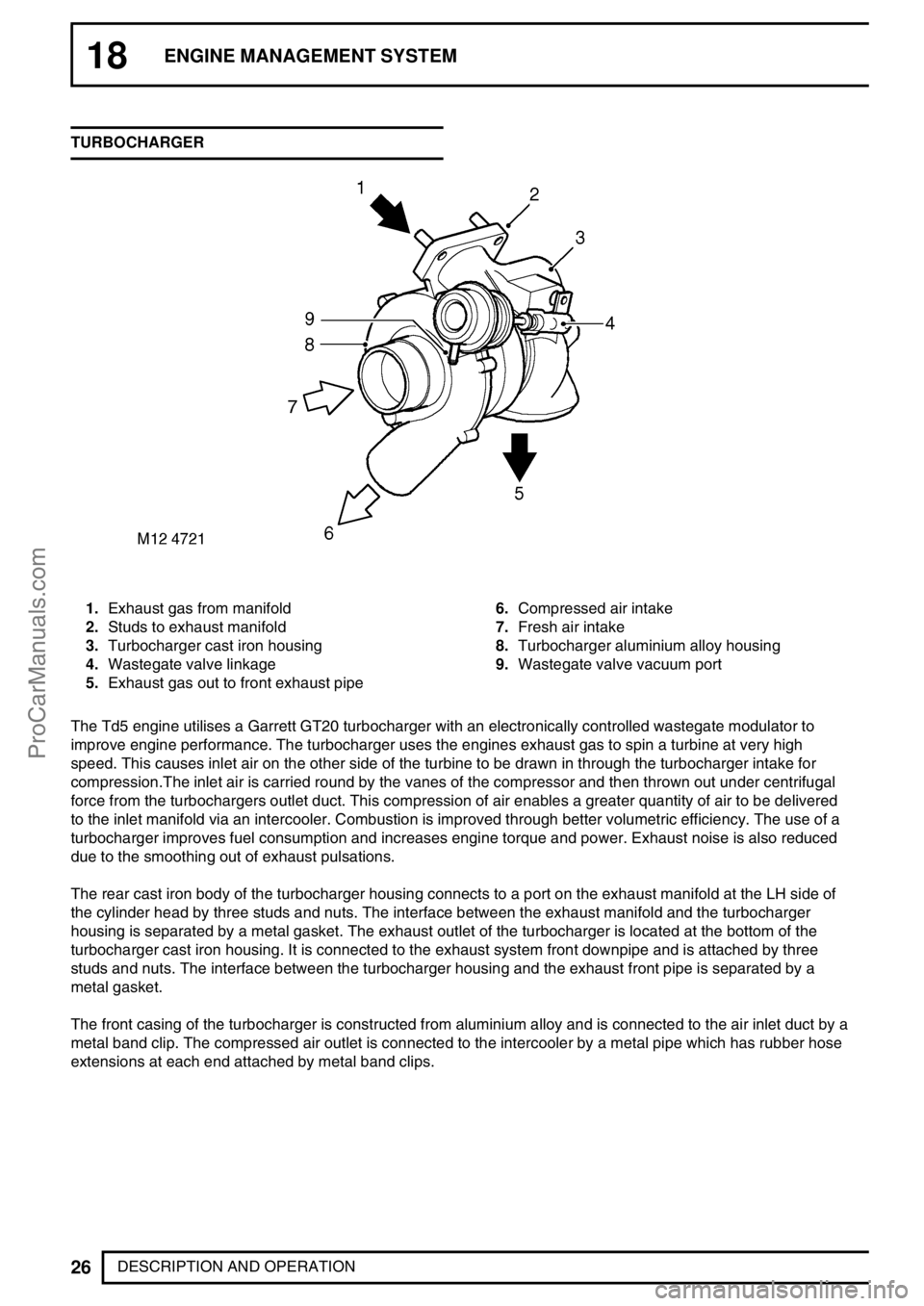
18ENGINE MANAGEMENT SYSTEM
26
DESCRIPTION AND OPERATION TURBOCHARGER
1.Exhaust gas from manifold
2.Studs to exhaust manifold
3.Turbocharger cast iron housing
4.Wastegate valve linkage
5.Exhaust gas out to front exhaust pipe6.Compressed air intake
7.Fresh air intake
8.Turbocharger aluminium alloy housing
9.Wastegate valve vacuum port
The Td5 engine utilises a Garrett GT20 turbocharger with an electronically controlled wastegate modulator to
improve engine performance. The turbocharger uses the engines exhaust gas to spin a turbine at very high
speed. This causes inlet air on the other side of the turbine to be drawn in through the turbocharger intake for
compression.The inlet air is carried round by the vanes of the compressor and then thrown out under centrifugal
force from the turbochargers outlet duct. This compression of air enables a greater quantity of air to be delivered
to the inlet manifold via an intercooler. Combustion is improved through better volumetric efficiency. The use of a
turbocharger improves fuel consumption and increases engine torque and power. Exhaust noise is also reduced
due to the smoothing out of exhaust pulsations.
The rear cast iron body of the turbocharger housing connects to a port on the exhaust manifold at the LH side of
the cylinder head by three studs and nuts. The interface between the exhaust manifold and the turbocharger
housing is separated by a metal gasket. The exhaust outlet of the turbocharger is located at the bottom of the
turbocharger cast iron housing. It is connected to the exhaust system front downpipe and is attached by three
studs and nuts. The interface between the turbocharger housing and the exhaust front pipe is separated by a
metal gasket.
The front casing of the turbocharger is constructed from aluminium alloy and is connected to the air inlet duct by a
metal band clip. The compressed air outlet is connected to the intercooler by a metal pipe which has rubber hose
extensions at each end attached by metal band clips.
ProCarManuals.com
Page 263 of 667
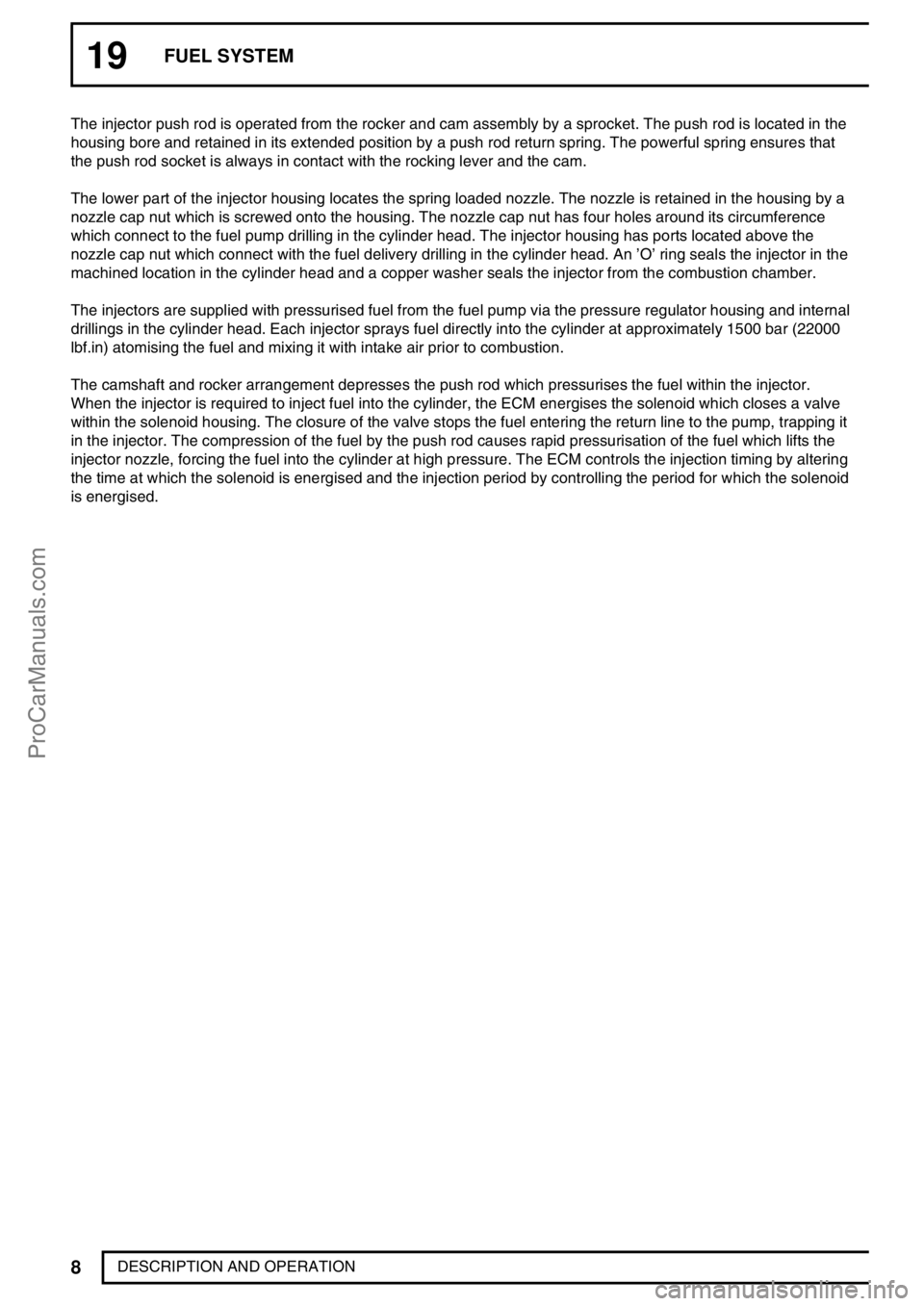
19FUEL SYSTEM
8
DESCRIPTION AND OPERATION The injector push rod is operated from the rocker and cam assembly by a sprocket. The push rod is located in the
housing bore and retained in its extended position by a push rod return spring. The powerful spring ensures that
the push rod socket is always in contact with the rocking lever and the cam.
The lower part of the injector housing locates the spring loaded nozzle. The nozzle is retained in the housing by a
nozzle cap nut which is screwed onto the housing. The nozzle cap nut has four holes around its circumference
which connect to the fuel pump drilling in the cylinder head. The injector housing has ports located above the
nozzle cap nut which connect with the fuel delivery drilling in the cylinder head. An’O’ring seals the injector in the
machined location in the cylinder head and a copper washer seals the injector from the combustion chamber.
The injectors are supplied with pressurised fuel from the fuel pump via the pressure regulator housing and internal
drillings in the cylinder head. Each injector sprays fuel directly into the cylinder at approximately 1500 bar (22000
lbf.in) atomising the fuel and mixing it with intake air prior to combustion.
The camshaft and rocker arrangement depresses the push rod which pressurises the fuel within the injector.
When the injector is required to inject fuel into the cylinder, the ECM energises the solenoid which closes a valve
within the solenoid housing. The closure of the valve stops the fuel entering the return line to the pump, trapping it
in the injector. The compression of the fuel by the push rod causes rapid pressurisation of the fuel which lifts the
injector nozzle, forcing the fuel into the cylinder at high pressure. The ECM controls the injection timing by altering
the time at which the solenoid is energised and the injection period by controlling the period for which the solenoid
is energised.
ProCarManuals.com
Page 331 of 667
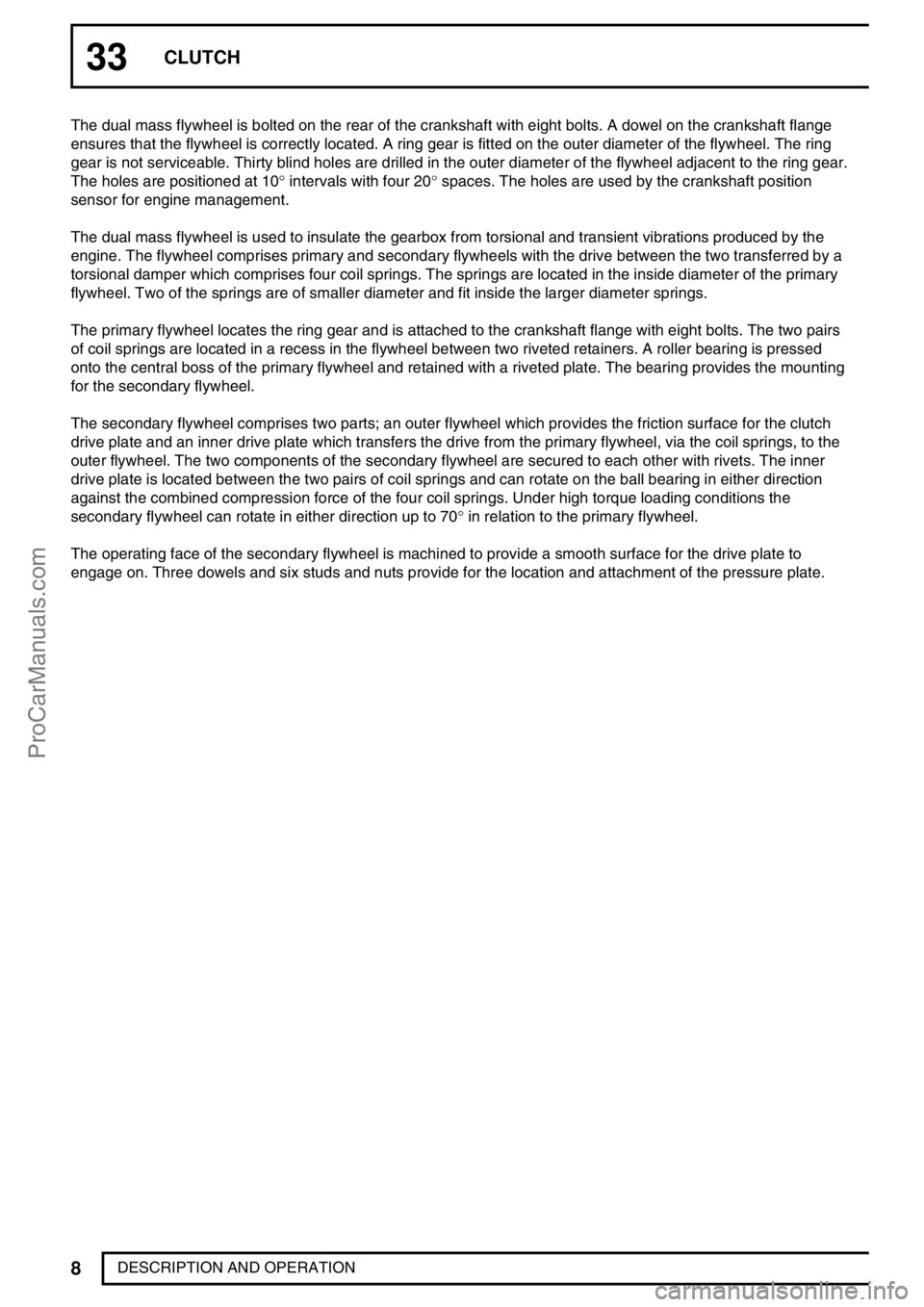
33CLUTCH
8
DESCRIPTION AND OPERATION The dual mass flywheel is bolted on the rear of the crankshaft with eight bolts. A dowel on the crankshaft flange
ensures that the flywheel is correctly located. A ring gear is fitted on the outer diameter of the flywheel. The ring
gear is not serviceable. Thirty blind holes are drilled in the outer diameter of the flywheel adjacent to the ring gear.
The holes are positioned at 10°intervals with four 20°spaces. The holes are used by the crankshaft position
sensor for engine management.
The dual mass flywheel is used to insulate the gearbox from torsional and transient vibrations produced by the
engine. The flywheel comprises primary and secondary flywheels with the drive between the two transferred by a
torsional damper which comprises four coil springs. The springs are located in the inside diameter of the primary
flywheel. Two of the springs are of smaller diameter and fit inside the larger diameter springs.
The primary flywheel locates the ring gear and is attached to the crankshaft flange with eight bolts. The two pairs
of coil springs are located in a recess in the flywheel between two riveted retainers. A roller bearing is pressed
onto the central boss of the primary flywheel and retained with a riveted plate. The bearing provides the mounting
for the secondary flywheel.
The secondary flywheel comprises two parts; an outer flywheel which provides the friction surface for the clutch
drive plate and an inner drive plate which transfers the drive from the primary flywheel, via the coil springs, to the
outer flywheel. The two components of the secondary flywheel are secured to each other with rivets. The inner
drive plate is located between the two pairs of coil springs and can rotate on the ball bearing in either direction
against the combined compression force of the four coil springs. Under high torque loading conditions the
secondary flywheel can rotate in either direction up to 70°in relation to the primary flywheel.
The operating face of the secondary flywheel is machined to provide a smooth surface for the drive plate to
engage on. Three dowels and six studs and nuts provide for the location and attachment of the pressure plate.
ProCarManuals.com