display LAND ROVER DISCOVERY 1995 Workshop Manual
[x] Cancel search | Manufacturer: LAND ROVER, Model Year: 1995, Model line: DISCOVERY, Model: LAND ROVER DISCOVERY 1995Pages: 873, PDF Size: 12.89 MB
Page 13 of 873
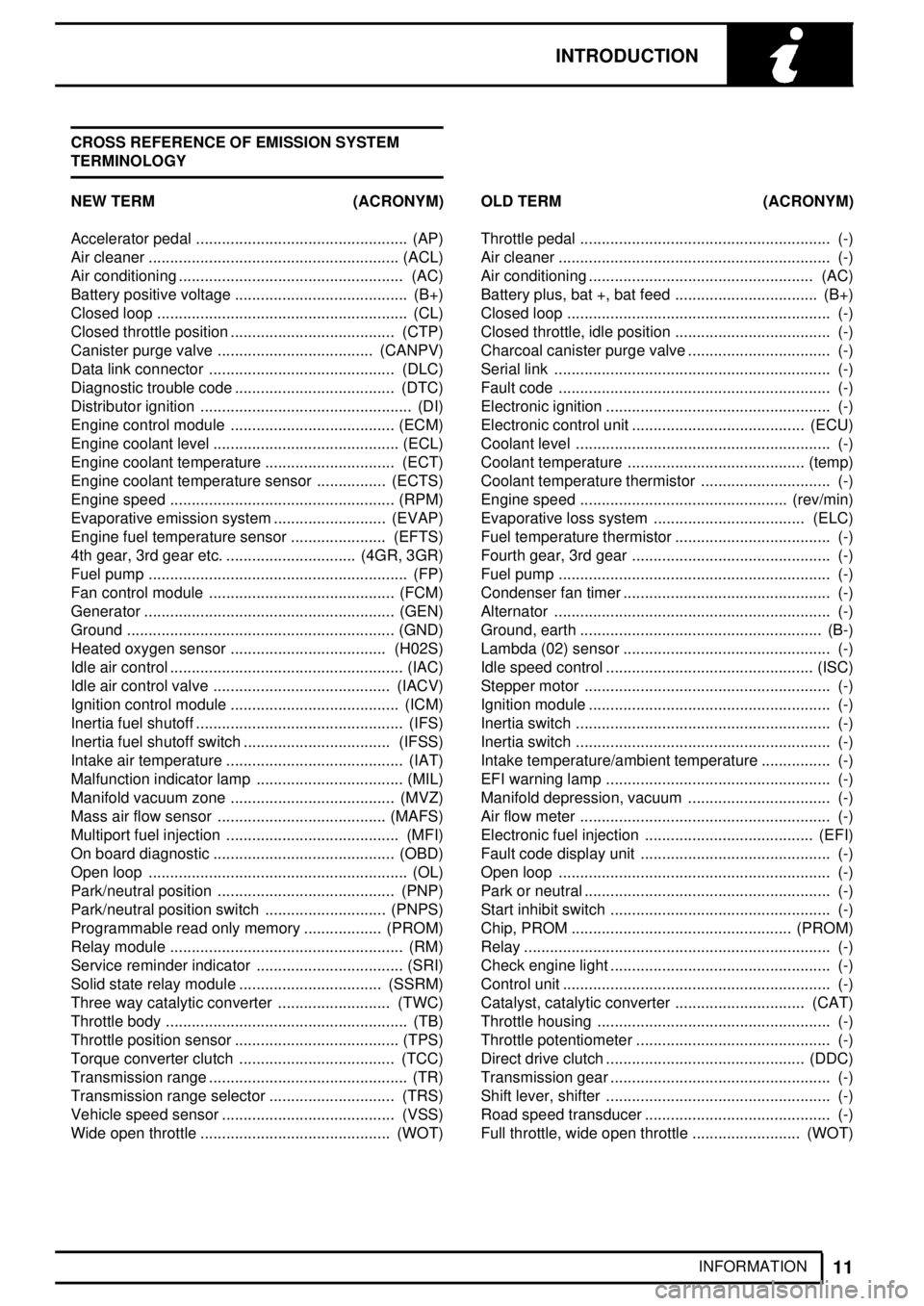
INTRODUCTION
11
INFORMATION CROSS REFERENCE OF EMISSION SYSTEM
TERMINOLOGY
NEW TERM (ACRONYM)
Accelerator pedal (AP).................................................
Air cleaner (ACL)..........................................................
Air conditioning (AC)....................................................
Battery positive voltage (B+)........................................
Closed loop (CL)..........................................................
Closed throttle position (CTP)......................................
Canister purge valve (CANPV)....................................
Data link connector (DLC)...........................................
Diagnostic trouble code (DTC).....................................
Distributor ignition (DI).................................................
Engine control module (ECM)......................................
Engine coolant level (ECL)...........................................
Engine coolant temperature (ECT)..............................
Engine coolant temperature sensor (ECTS)................
Engine speed (RPM)....................................................
Evaporative emission system (EVAP)..........................
Engine fuel temperature sensor (EFTS)......................
4th gear, 3rd gear etc. (4GR, 3GR)..............................
Fuel pump (FP)............................................................
Fan control module (FCM)...........................................
Generator (GEN)..........................................................
Ground (GND)..............................................................
Heated oxygen sensor (H02S)....................................
Idle air control (IAC)......................................................
Idle air control valve (IACV).........................................
Ignition control module (ICM).......................................
Inertia fuel shutoff (IFS)................................................
Inertia fuel shutoff switch (IFSS)..................................
Intake air temperature (IAT).........................................
Malfunction indicator lamp (MIL)..................................
Manifold vacuum zone (MVZ)......................................
Mass air flow sensor (MAFS).......................................
Multiport fuel injection (MFI)........................................
On board diagnostic (OBD)..........................................
Open loop (OL)............................................................
Park/neutral position (PNP).........................................
Park/neutral position switch (PNPS)............................
Programmable read only memory (PROM)..................
Relay module (RM)......................................................
Service reminder indicator (SRI)..................................
Solid state relay module (SSRM).................................
Three way catalytic converter (TWC)..........................
Throttle body (TB)........................................................
Throttle position sensor (TPS)......................................
Torque converter clutch (TCC)....................................
Transmission range (TR)..............................................
Transmission range selector (TRS).............................
Vehicle speed sensor (VSS)........................................
Wide open throttle (WOT)............................................OLD TERM (ACRONYM)
Throttle pedal (-)..........................................................
Air cleaner (-)...............................................................
Air conditioning (AC)....................................................
Battery plus, bat +, bat feed (B+).................................
Closed loop (-).............................................................
Closed throttle, idle position (-)....................................
Charcoal canister purge valve (-).................................
Serial link (-)................................................................
Fault code (-)...............................................................
Electronic ignition (-)....................................................
Electronic control unit (ECU)........................................
Coolant level (-)...........................................................
Coolant temperature (temp).........................................
Coolant temperature thermistor (-)..............................
Engine speed (rev/min)................................................
Evaporative loss system (ELC)...................................
Fuel temperature thermistor (-)....................................
Fourth gear, 3rd gear (-)..............................................
Fuel pump (-)...............................................................
Condenser fan timer (-)................................................
Alternator (-)................................................................
Ground, earth (B-)........................................................
Lambda (02) sensor (-)................................................
Idle speed control (ISC)................................................
Stepper motor (-).........................................................
Ignition module (-)........................................................
Inertia switch (-)...........................................................
Inertia switch (-)...........................................................
Intake temperature/ambient temperature (-)................
EFI warning lamp (-)....................................................
Manifold depression, vacuum (-).................................
Air flow meter (-)..........................................................
Electronic fuel injection (EFI).......................................
Fault code display unit (-)............................................
Open loop (-)...............................................................
Park or neutral (-).........................................................
Start inhibit switch (-)...................................................
Chip, PROM (PROM)...................................................
Relay (-).......................................................................
Check engine light (-)...................................................
Control unit (-)..............................................................
Catalyst, catalytic converter (CAT)..............................
Throttle housing (-)......................................................
Throttle potentiometer (-).............................................
Direct drive clutch (DDC)..............................................
Transmission gear (-)...................................................
Shift lever, shifter (-)....................................................
Road speed transducer (-)...........................................
Full throttle, wide open throttle (WOT).........................
Page 195 of 873
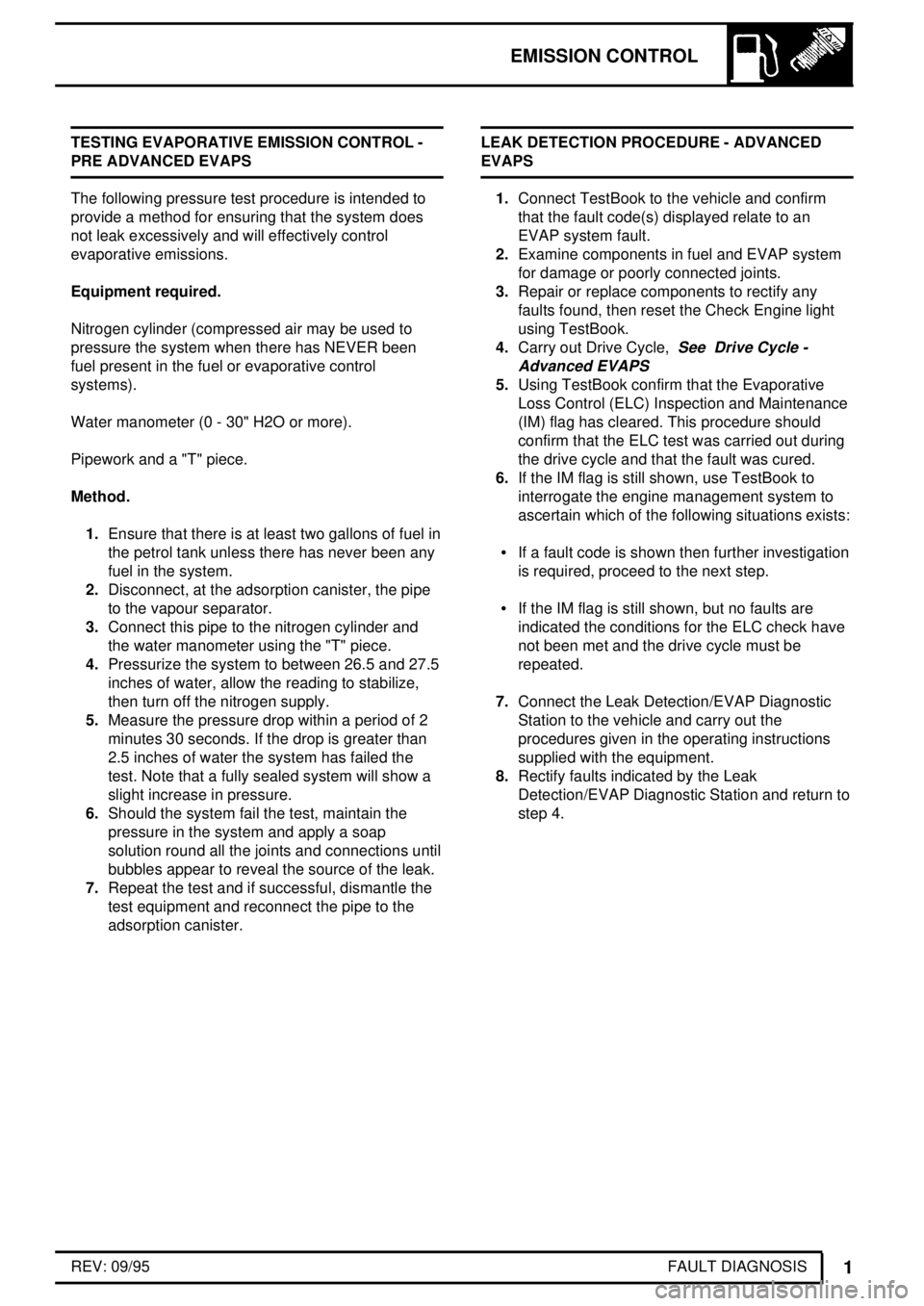
EMISSION CONTROL
1
FAULT DIAGNOSIS REV: 09/95 TESTING EVAPORATIVE EMISSION CONTROL -
PRE ADVANCED EVAPS
The following pressure test procedure is intended to
provide a method for ensuring that the system does
not leak excessively and will effectively control
evaporative emissions.
Equipment required.
Nitrogen cylinder (compressed air may be used to
pressure the system when there has NEVER been
fuel present in the fuel or evaporative control
systems).
Water manometer (0 - 30" H2O or more).
Pipework and a "T" piece.
Method.
1.Ensure that there is at least two gallons of fuel in
the petrol tank unless there has never been any
fuel in the system.
2.Disconnect, at the adsorption canister, the pipe
to the vapour separator.
3.Connect this pipe to the nitrogen cylinder and
the water manometer using the "T" piece.
4.Pressurize the system to between 26.5 and 27.5
inches of water, allow the reading to stabilize,
then turn off the nitrogen supply.
5.Measure the pressure drop within a period of 2
minutes 30 seconds. If the drop is greater than
2.5 inches of water the system has failed the
test. Note that a fully sealed system will show a
slight increase in pressure.
6.Should the system fail the test, maintain the
pressure in the system and apply a soap
solution round all the joints and connections until
bubbles appear to reveal the source of the leak.
7.Repeat the test and if successful, dismantle the
test equipment and reconnect the pipe to the
adsorption canister.LEAK DETECTION PROCEDURE - ADVANCED
EVAPS
1.Connect TestBook to the vehicle and confirm
that the fault code(s) displayed relate to an
EVAP system fault.
2.Examine components in fuel and EVAP system
for damage or poorly connected joints.
3.Repair or replace components to rectify any
faults found, then reset the Check Engine light
using TestBook.
4.Carry out Drive Cycle,
See Drive Cycle -
Advanced EVAPS
5.Using TestBook confirm that the Evaporative
Loss Control (ELC) Inspection and Maintenance
(IM) flag has cleared. This procedure should
confirm that the ELC test was carried out during
the drive cycle and that the fault was cured.
6.If the IM flag is still shown, use TestBook to
interrogate the engine management system to
ascertain which of the following situations exists:
·If a fault code is shown then further investigation
is required, proceed to the next step.
·If the IM flag is still shown, but no faults are
indicated the conditions for the ELC check have
not been met and the drive cycle must be
repeated.
7.Connect the Leak Detection/EVAP Diagnostic
Station to the vehicle and carry out the
procedures given in the operating instructions
supplied with the equipment.
8.Rectify faults indicated by the Leak
Detection/EVAP Diagnostic Station and return to
step 4.
Page 390 of 873
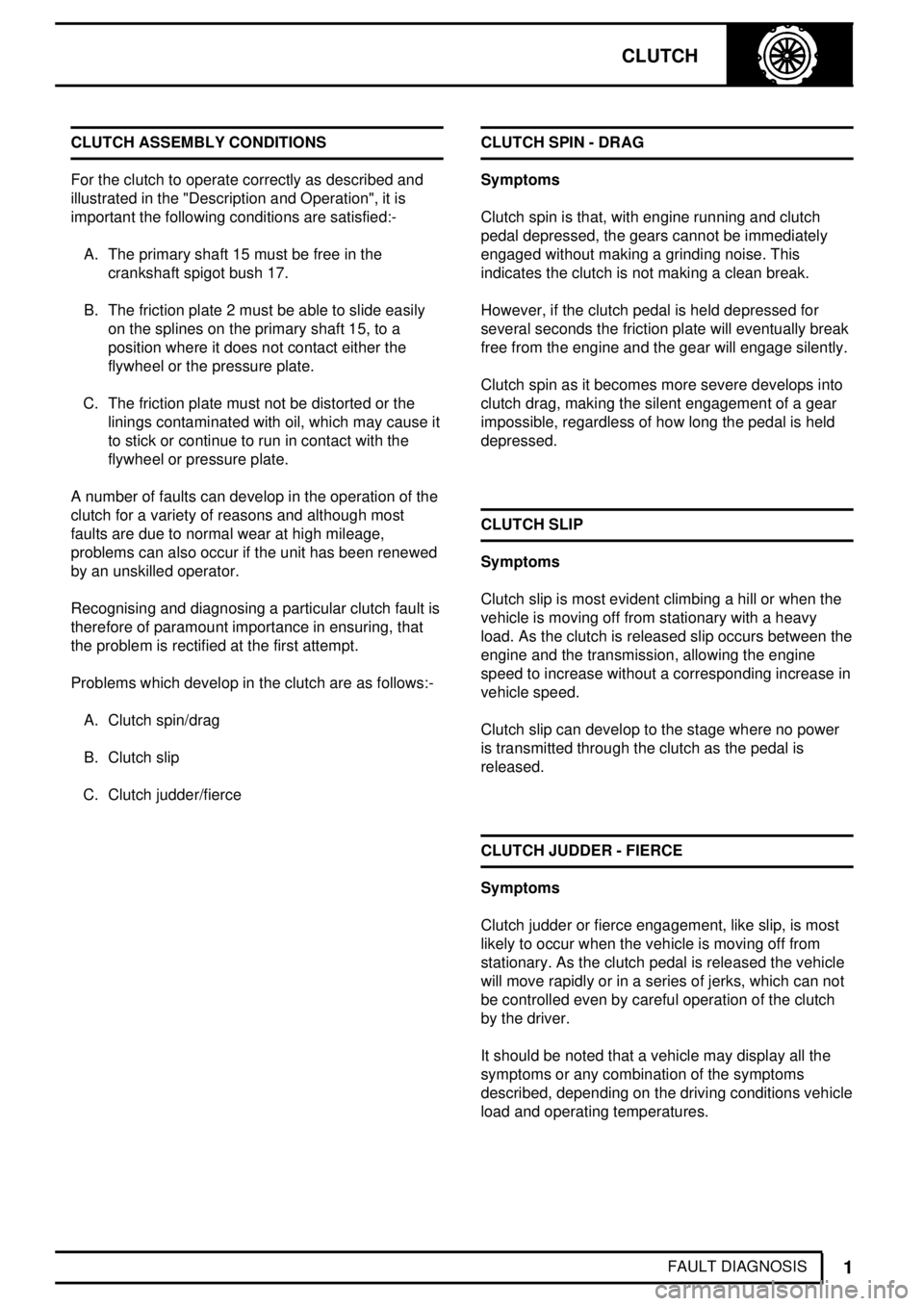
CLUTCH
1
FAULT DIAGNOSIS CLUTCH ASSEMBLY CONDITIONS
For the clutch to operate correctly as described and
illustrated in the "Description and Operation", it is
important the following conditions are satisfied:-
A. The primary shaft 15 must be free in the
crankshaft spigot bush 17.
B. The friction plate 2 must be able to slide easily
on the splines on the primary shaft 15, to a
position where it does not contact either the
flywheel or the pressure plate.
C. The friction plate must not be distorted or the
linings contaminated with oil, which may cause it
to stick or continue to run in contact with the
flywheel or pressure plate.
A number of faults can develop in the operation of the
clutch for a variety of reasons and although most
faults are due to normal wear at high mileage,
problems can also occur if the unit has been renewed
by an unskilled operator.
Recognising and diagnosing a particular clutch fault is
therefore of paramount importance in ensuring, that
the problem is rectified at the first attempt.
Problems which develop in the clutch are as follows:-
A. Clutch spin/drag
B. Clutch slip
C. Clutch judder/fierceCLUTCH SPIN - DRAG
Symptoms
Clutch spin is that, with engine running and clutch
pedal depressed, the gears cannot be immediately
engaged without making a grinding noise. This
indicates the clutch is not making a clean break.
However, if the clutch pedal is held depressed for
several seconds the friction plate will eventually break
free from the engine and the gear will engage silently.
Clutch spin as it becomes more severe develops into
clutch drag, making the silent engagement of a gear
impossible, regardless of how long the pedal is held
depressed.
CLUTCH SLIP
Symptoms
Clutch slip is most evident climbing a hill or when the
vehicle is moving off from stationary with a heavy
load. As the clutch is released slip occurs between the
engine and the transmission, allowing the engine
speed to increase without a corresponding increase in
vehicle speed.
Clutch slip can develop to the stage where no power
is transmitted through the clutch as the pedal is
released.
CLUTCH JUDDER - FIERCE
Symptoms
Clutch judder or fierce engagement, like slip, is most
likely to occur when the vehicle is moving off from
stationary. As the clutch pedal is released the vehicle
will move rapidly or in a series of jerks, which can not
be controlled even by careful operation of the clutch
by the driver.
It should be noted that a vehicle may display all the
symptoms or any combination of the symptoms
described, depending on the driving conditions vehicle
load and operating temperatures.
Page 538 of 873
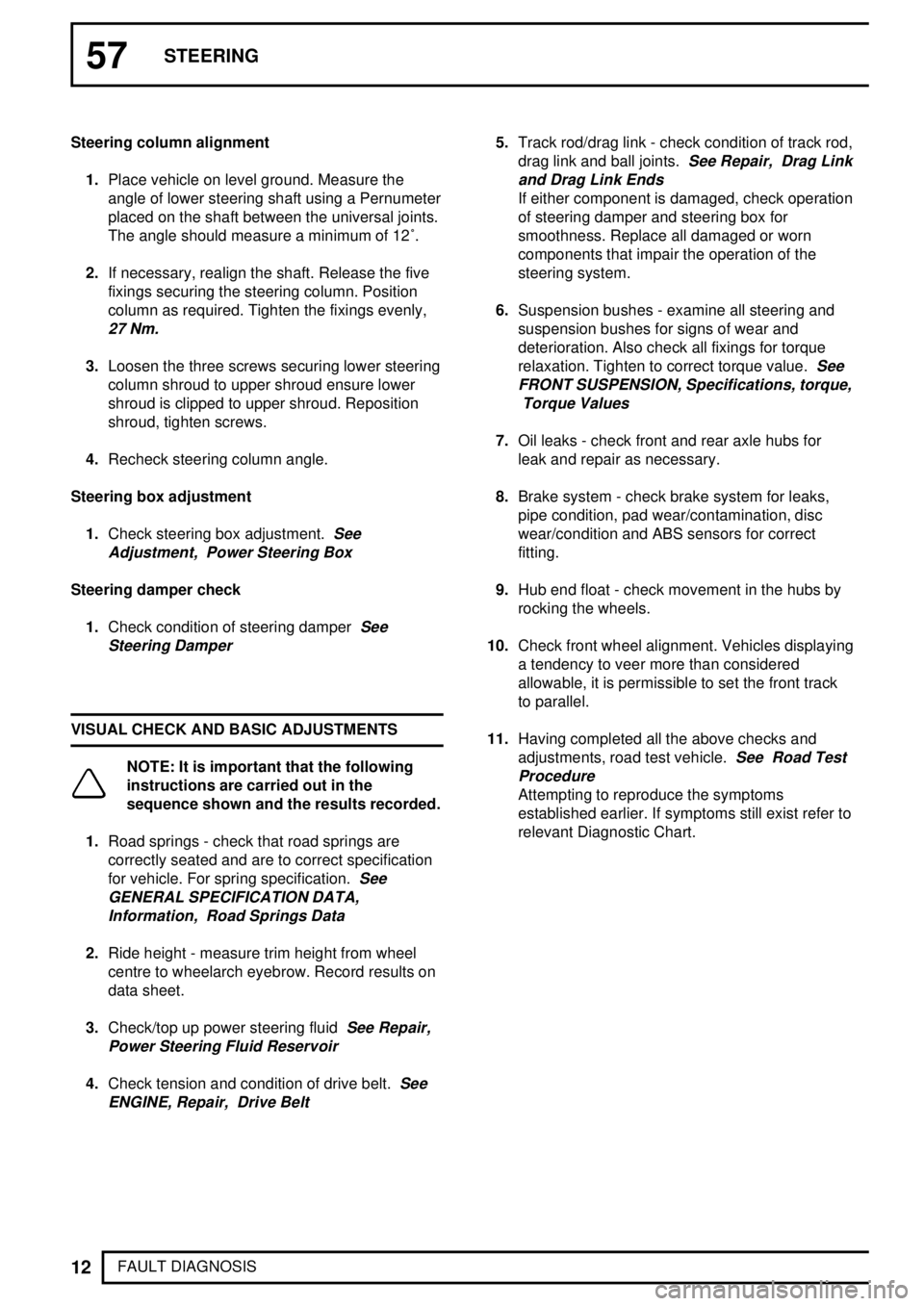
57STEERING
12
FAULT DIAGNOSIS Steering column alignment
1.Place vehicle on level ground. Measure the
angle of lower steering shaft using a Pernumeter
placed on the shaft between the universal joints.
The angle should measure a minimum of 12Ê.
2.If necessary, realign the shaft. Release the five
fixings securing the steering column. Position
column as required. Tighten the fixings evenly,
27 Nm.
3.Loosen the three screws securing lower steering
column shroud to upper shroud ensure lower
shroud is clipped to upper shroud. Reposition
shroud, tighten screws.
4.Recheck steering column angle.
Steering box adjustment
1.Check steering box adjustment.
See
Adjustment, Power Steering Box
Steering damper check
1.Check condition of steering damper
See
Steering Damper
VISUAL CHECK AND BASIC ADJUSTMENTS
NOTE: It is important that the following
instructions are carried out in the
sequence shown and the results recorded.
1.Road springs - check that road springs are
correctly seated and are to correct specification
for vehicle. For spring specification.
See
GENERAL SPECIFICATION DATA,
Information, Road Springs Data
2.Ride height - measure trim height from wheel
centre to wheelarch eyebrow. Record results on
data sheet.
3.Check/top up power steering fluid
See Repair,
Power Steering Fluid Reservoir
4.Check tension and condition of drive belt.See
ENGINE, Repair, Drive Belt
5.Track rod/drag link - check condition of track rod,
drag link and ball joints.
See Repair, Drag Link
and Drag Link Ends
If either component is damaged, check operation
of steering damper and steering box for
smoothness. Replace all damaged or worn
components that impair the operation of the
steering system.
6.Suspension bushes - examine all steering and
suspension bushes for signs of wear and
deterioration. Also check all fixings for torque
relaxation. Tighten to correct torque value.
See
FRONT SUSPENSION, Specifications, torque,
Torque Values
7.Oil leaks - check front and rear axle hubs for
leak and repair as necessary.
8.Brake system - check brake system for leaks,
pipe condition, pad wear/contamination, disc
wear/condition and ABS sensors for correct
fitting.
9.Hub end float - check movement in the hubs by
rocking the wheels.
10.Check front wheel alignment. Vehicles displaying
a tendency to veer more than considered
allowable, it is permissible to set the front track
to parallel.
11.Having completed all the above checks and
adjustments, road test vehicle.
See Road Test
Procedure
Attempting to reproduce the symptoms
established earlier. If symptoms still exist refer to
relevant Diagnostic Chart.
Page 713 of 873
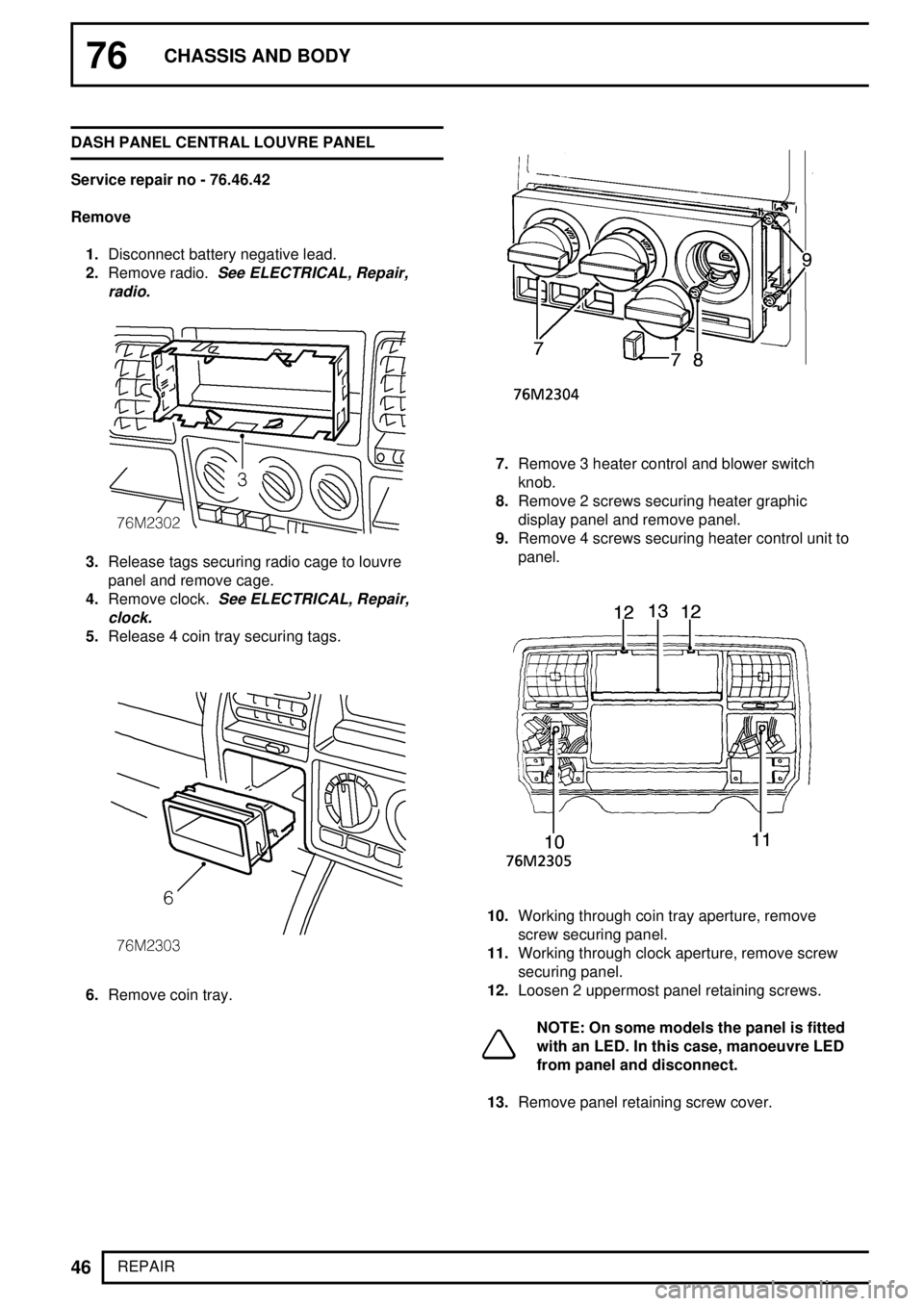
76CHASSIS AND BODY
46
REPAIR DASH PANEL CENTRAL LOUVRE PANEL
Service repair no - 76.46.42
Remove
1.Disconnect battery negative lead.
2.Remove radio.
See ELECTRICAL, Repair,
radio.
3.Release tags securing radio cage to louvre
panel and remove cage.
4.Remove clock.
See ELECTRICAL, Repair,
clock.
5.Release 4 coin tray securing tags.
6.Remove coin tray.
7.Remove 3 heater control and blower switch
knob.
8.Remove 2 screws securing heater graphic
display panel and remove panel.
9.Remove 4 screws securing heater control unit to
panel.
10.Working through coin tray aperture, remove
screw securing panel.
11.Working through clock aperture, remove screw
securing panel.
12.Loosen 2 uppermost panel retaining screws.
NOTE: On some models the panel is fitted
with an LED. In this case, manoeuvre LED
from panel and disconnect.
13.Remove panel retaining screw cover.
Page 714 of 873
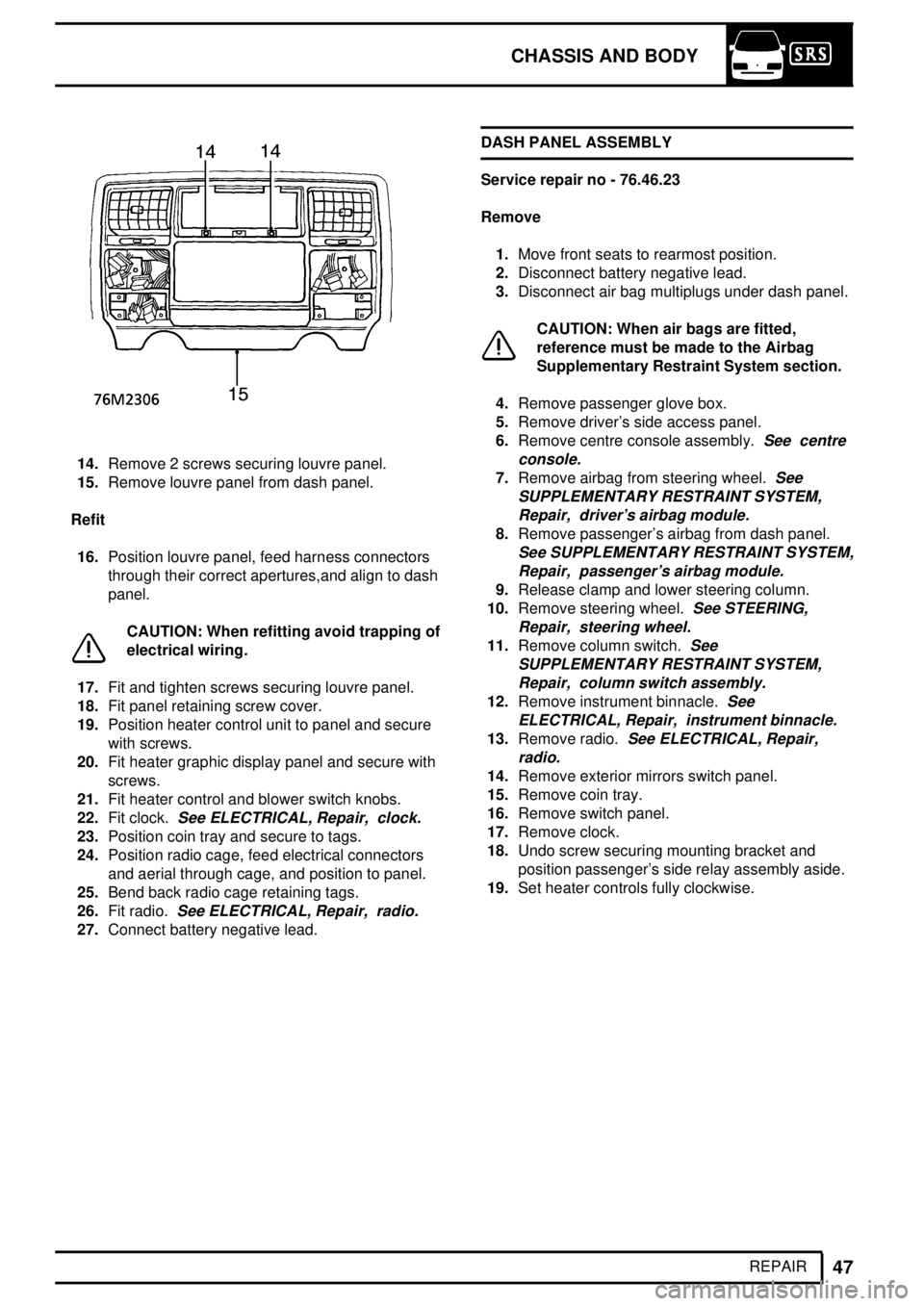
CHASSIS AND BODY
47
REPAIR
14.Remove 2 screws securing louvre panel.
15.Remove louvre panel from dash panel.
Refit
16.Position louvre panel, feed harness connectors
through their correct apertures,and align to dash
panel.
CAUTION: When refitting avoid trapping of
electrical wiring.
17.Fit and tighten screws securing louvre panel.
18.Fit panel retaining screw cover.
19.Position heater control unit to panel and secure
with screws.
20.Fit heater graphic display panel and secure with
screws.
21.Fit heater control and blower switch knobs.
22.Fit clock.
See ELECTRICAL, Repair, clock.
23.Position coin tray and secure to tags.
24.Position radio cage, feed electrical connectors
and aerial through cage, and position to panel.
25.Bend back radio cage retaining tags.
26.Fit radio.
See ELECTRICAL, Repair, radio.
27.Connect battery negative lead.DASH PANEL ASSEMBLY
Service repair no - 76.46.23
Remove
1.Move front seats to rearmost position.
2.Disconnect battery negative lead.
3.Disconnect air bag multiplugs under dash panel.
CAUTION: When air bags are fitted,
reference must be made to the Airbag
Supplementary Restraint System section.
4.Remove passenger glove box.
5.Remove driver's side access panel.
6.Remove centre console assembly.
See centre
console.
7.Remove airbag from steering wheel.See
SUPPLEMENTARY RESTRAINT SYSTEM,
Repair, driver's airbag module.
8.Remove passenger's airbag from dash panel.
See SUPPLEMENTARY RESTRAINT SYSTEM,
Repair, passenger's airbag module.
9.Release clamp and lower steering column.
10.Remove steering wheel.
See STEERING,
Repair, steering wheel.
11.Remove column switch.See
SUPPLEMENTARY RESTRAINT SYSTEM,
Repair, column switch assembly.
12.Remove instrument binnacle.See
ELECTRICAL, Repair, instrument binnacle.
13.Remove radio.See ELECTRICAL, Repair,
radio.
14.Remove exterior mirrors switch panel.
15.Remove coin tray.
16.Remove switch panel.
17.Remove clock.
18.Undo screw securing mounting bracket and
position passenger's side relay assembly aside.
19.Set heater controls fully clockwise.
Page 787 of 873
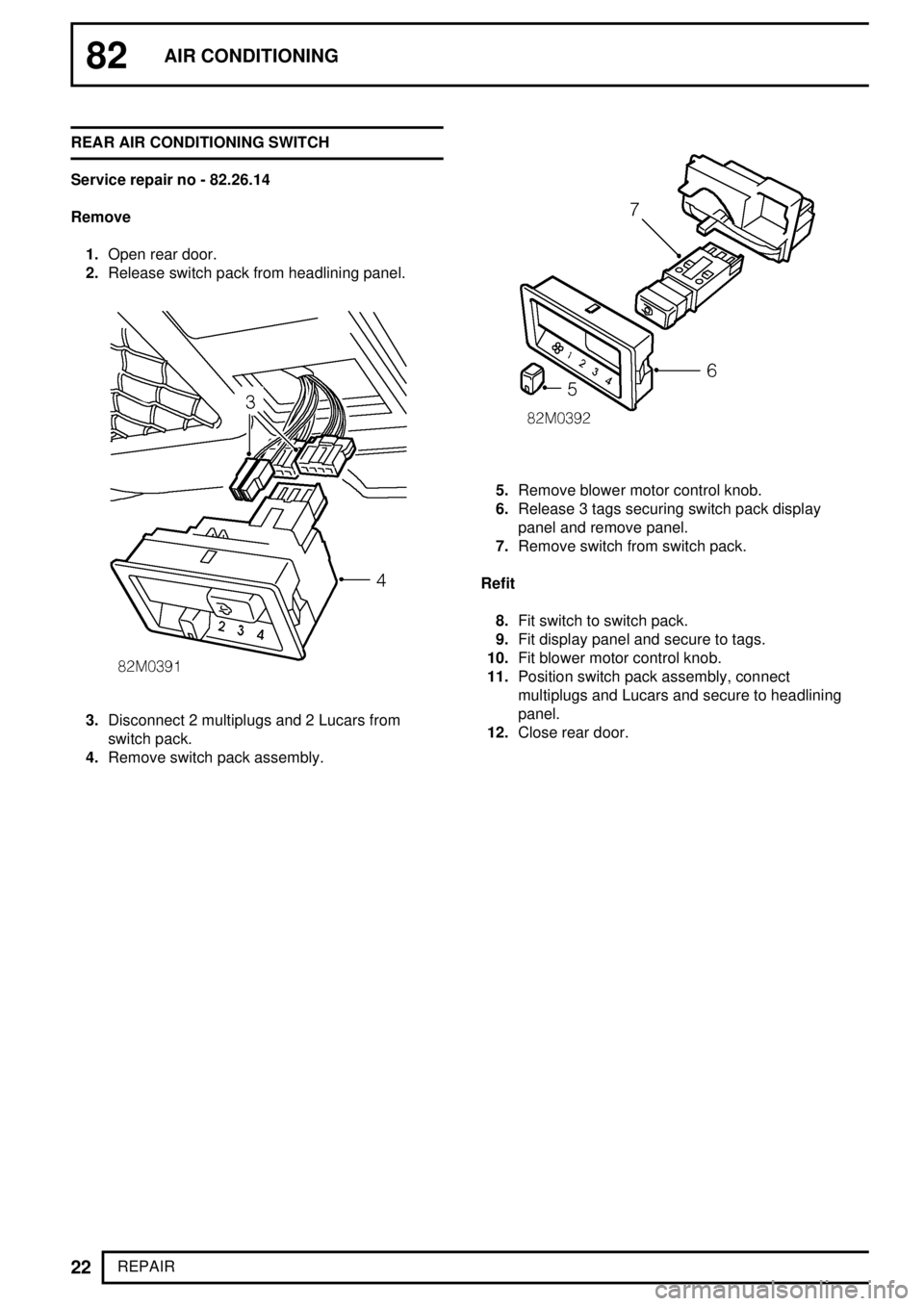
82AIR CONDITIONING
22
REPAIR REAR AIR CONDITIONING SWITCH
Service repair no - 82.26.14
Remove
1.Open rear door.
2.Release switch pack from headlining panel.
3.Disconnect 2 multiplugs and 2 Lucars from
switch pack.
4.Remove switch pack assembly.
5.Remove blower motor control knob.
6.Release 3 tags securing switch pack display
panel and remove panel.
7.Remove switch from switch pack.
Refit
8.Fit switch to switch pack.
9.Fit display panel and secure to tags.
10.Fit blower motor control knob.
11.Position switch pack assembly, connect
multiplugs and Lucars and secure to headlining
panel.
12.Close rear door.
Page 788 of 873
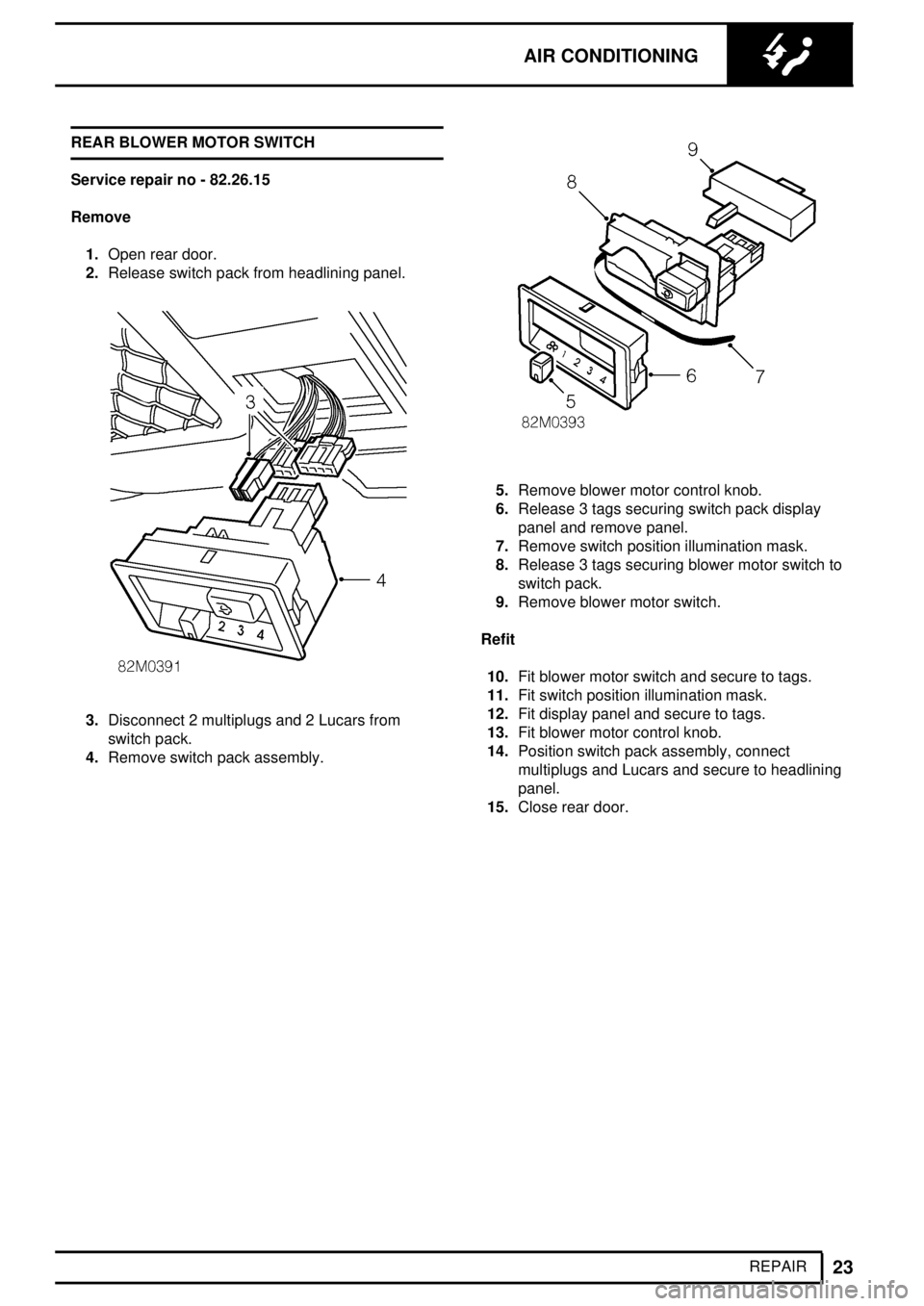
AIR CONDITIONING
23
REPAIR REAR BLOWER MOTOR SWITCH
Service repair no - 82.26.15
Remove
1.Open rear door.
2.Release switch pack from headlining panel.
3.Disconnect 2 multiplugs and 2 Lucars from
switch pack.
4.Remove switch pack assembly.
5.Remove blower motor control knob.
6.Release 3 tags securing switch pack display
panel and remove panel.
7.Remove switch position illumination mask.
8.Release 3 tags securing blower motor switch to
switch pack.
9.Remove blower motor switch.
Refit
10.Fit blower motor switch and secure to tags.
11.Fit switch position illumination mask.
12.Fit display panel and secure to tags.
13.Fit blower motor control knob.
14.Position switch pack assembly, connect
multiplugs and Lucars and secure to headlining
panel.
15.Close rear door.