stop start LAND ROVER DISCOVERY 1995 Workshop Manual
[x] Cancel search | Manufacturer: LAND ROVER, Model Year: 1995, Model line: DISCOVERY, Model: LAND ROVER DISCOVERY 1995Pages: 873, PDF Size: 12.89 MB
Page 116 of 873
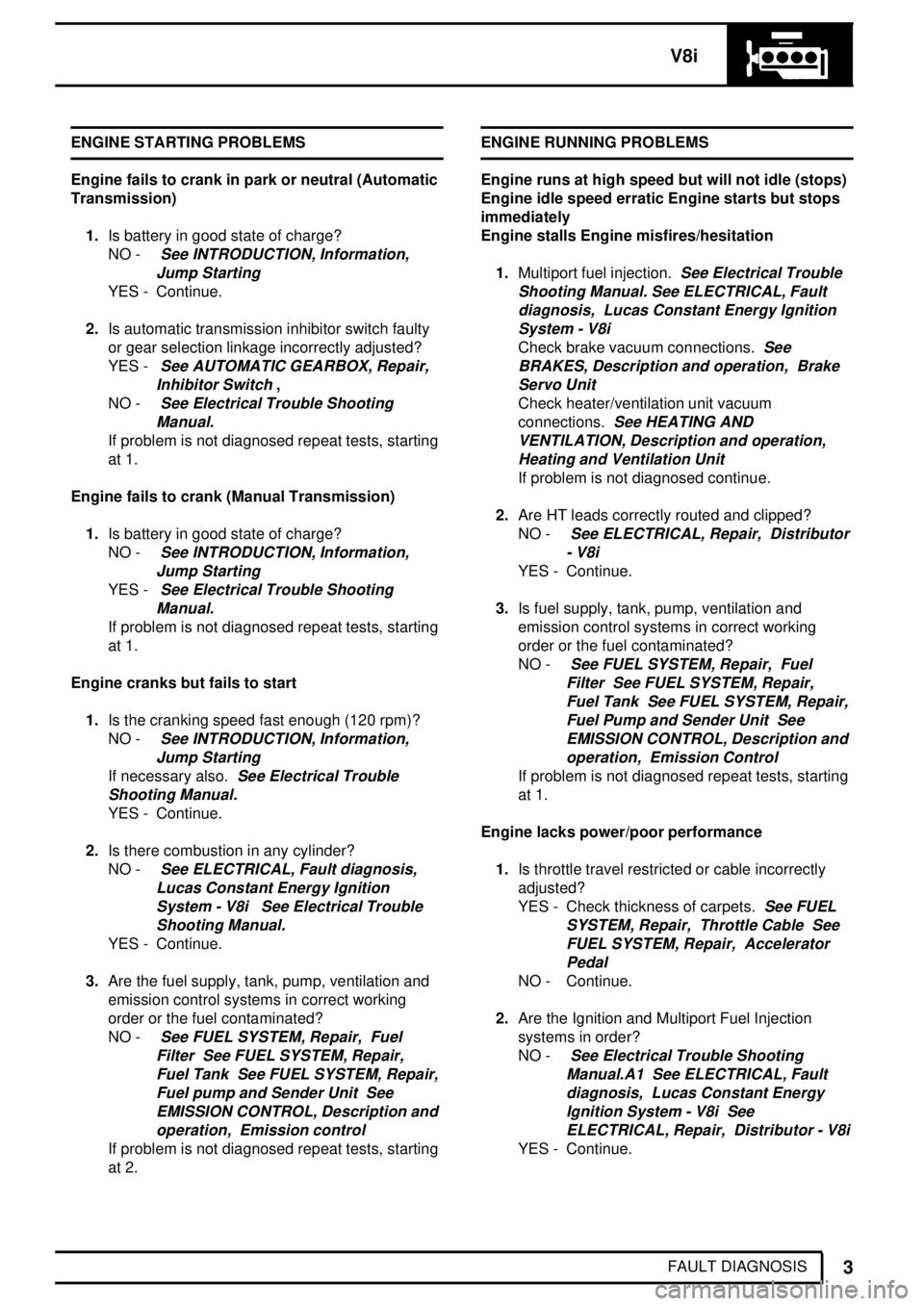
V8i
3
FAULT DIAGNOSIS ENGINE STARTING PROBLEMS
Engine fails to crank in park or neutral (Automatic
Transmission)
1.Is battery in good state of charge?
NO -
See INTRODUCTION, Information,
Jump Starting
YES - Continue.
2.Is automatic transmission inhibitor switch faulty
or gear selection linkage incorrectly adjusted?
YES -
See AUTOMATIC GEARBOX, Repair,
Inhibitor Switch
,
NO -
See Electrical Trouble Shooting
Manual.
If problem is not diagnosed repeat tests, starting
at 1.
Engine fails to crank (Manual Transmission)
1.Is battery in good state of charge?
NO -
See INTRODUCTION, Information,
Jump Starting
YES -See Electrical Trouble Shooting
Manual.
If problem is not diagnosed repeat tests, starting
at 1.
Engine cranks but fails to start
1.Is the cranking speed fast enough (120 rpm)?
NO -
See INTRODUCTION, Information,
Jump Starting
If necessary also.See Electrical Trouble
Shooting Manual.
YES - Continue.
2.Is there combustion in any cylinder?
NO -
See ELECTRICAL, Fault diagnosis,
Lucas Constant Energy Ignition
System - V8i See Electrical Trouble
Shooting Manual.
YES - Continue.
3.Are the fuel supply, tank, pump, ventilation and
emission control systems in correct working
order or the fuel contaminated?
NO -
See FUEL SYSTEM, Repair, Fuel
Filter See FUEL SYSTEM, Repair,
Fuel Tank See FUEL SYSTEM, Repair,
Fuel pump and Sender Unit See
EMISSION CONTROL, Description and
operation, Emission control
If problem is not diagnosed repeat tests, starting
at 2.ENGINE RUNNING PROBLEMS
Engine runs at high speed but will not idle (stops)
Engine idle speed erratic Engine starts but stops
immediately
Engine stalls Engine misfires/hesitation
1.Multiport fuel injection.
See Electrical Trouble
Shooting Manual. See ELECTRICAL, Fault
diagnosis, Lucas Constant Energy Ignition
System - V8i
Check brake vacuum connections.See
BRAKES, Description and operation, Brake
Servo Unit
Check heater/ventilation unit vacuum
connections.
See HEATING AND
VENTILATION, Description and operation,
Heating and Ventilation Unit
If problem is not diagnosed continue.
2.Are HT leads correctly routed and clipped?
NO -
See ELECTRICAL, Repair, Distributor
- V8i
YES - Continue.
3.Is fuel supply, tank, pump, ventilation and
emission control systems in correct working
order or the fuel contaminated?
NO -
See FUEL SYSTEM, Repair, Fuel
Filter See FUEL SYSTEM, Repair,
Fuel Tank See FUEL SYSTEM, Repair,
Fuel Pump and Sender Unit See
EMISSION CONTROL, Description and
operation, Emission Control
If problem is not diagnosed repeat tests, starting
at 1.
Engine lacks power/poor performance
1.Is throttle travel restricted or cable incorrectly
adjusted?
YES - Check thickness of carpets.
See FUEL
SYSTEM, Repair, Throttle Cable See
FUEL SYSTEM, Repair, Accelerator
Pedal
NO - Continue.
2.Are the Ignition and Multiport Fuel Injection
systems in order?
NO -
See Electrical Trouble Shooting
Manual.A1 See ELECTRICAL, Fault
diagnosis, Lucas Constant Energy
Ignition System - V8i See
ELECTRICAL, Repair, Distributor - V8i
YES - Continue.
Page 245 of 873
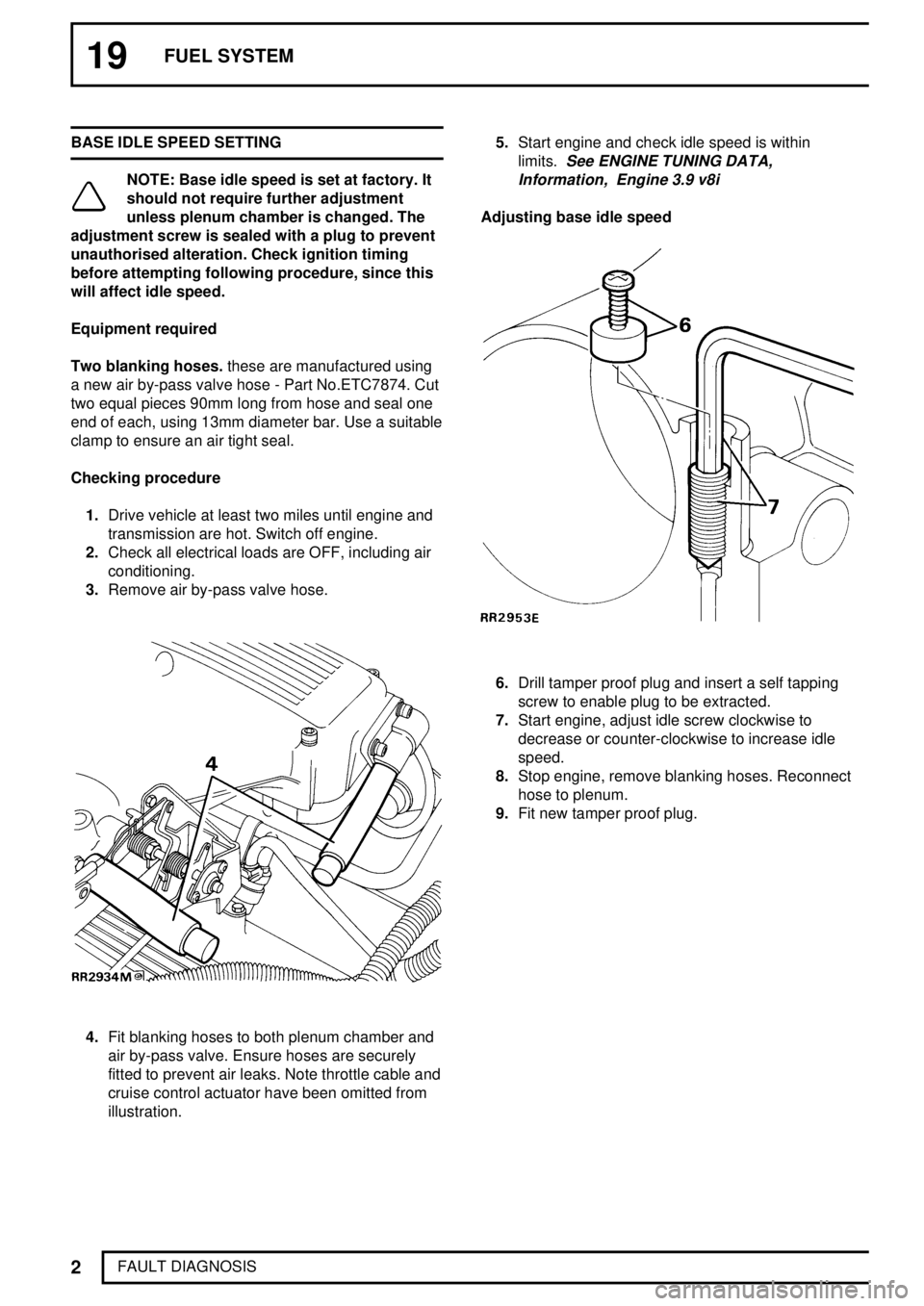
19FUEL SYSTEM
2
FAULT DIAGNOSIS BASE IDLE SPEED SETTING
NOTE: Base idle speed is set at factory. It
should not require further adjustment
unless plenum chamber is changed. The
adjustment screw is sealed with a plug to prevent
unauthorised alteration. Check ignition timing
before attempting following procedure, since this
will affect idle speed.
Equipment required
Two blanking hoses.these are manufactured using
a new air by-pass valve hose - Part No.ETC7874. Cut
two equal pieces 90mm long from hose and seal one
end of each, using 13mm diameter bar. Use a suitable
clamp to ensure an air tight seal.
Checking procedure
1.Drive vehicle at least two miles until engine and
transmission are hot. Switch off engine.
2.Check all electrical loads are OFF, including air
conditioning.
3.Remove air by-pass valve hose.
4.Fit blanking hoses to both plenum chamber and
air by-pass valve. Ensure hoses are securely
fitted to prevent air leaks. Note throttle cable and
cruise control actuator have been omitted from
illustration.5.Start engine and check idle speed is within
limits.
See ENGINE TUNING DATA,
Information, Engine 3.9 v8i
Adjusting base idle speed
6.Drill tamper proof plug and insert a self tapping
screw to enable plug to be extracted.
7.Start engine, adjust idle screw clockwise to
decrease or counter-clockwise to increase idle
speed.
8.Stop engine, remove blanking hoses. Reconnect
hose to plenum.
9.Fit new tamper proof plug.
Page 512 of 873
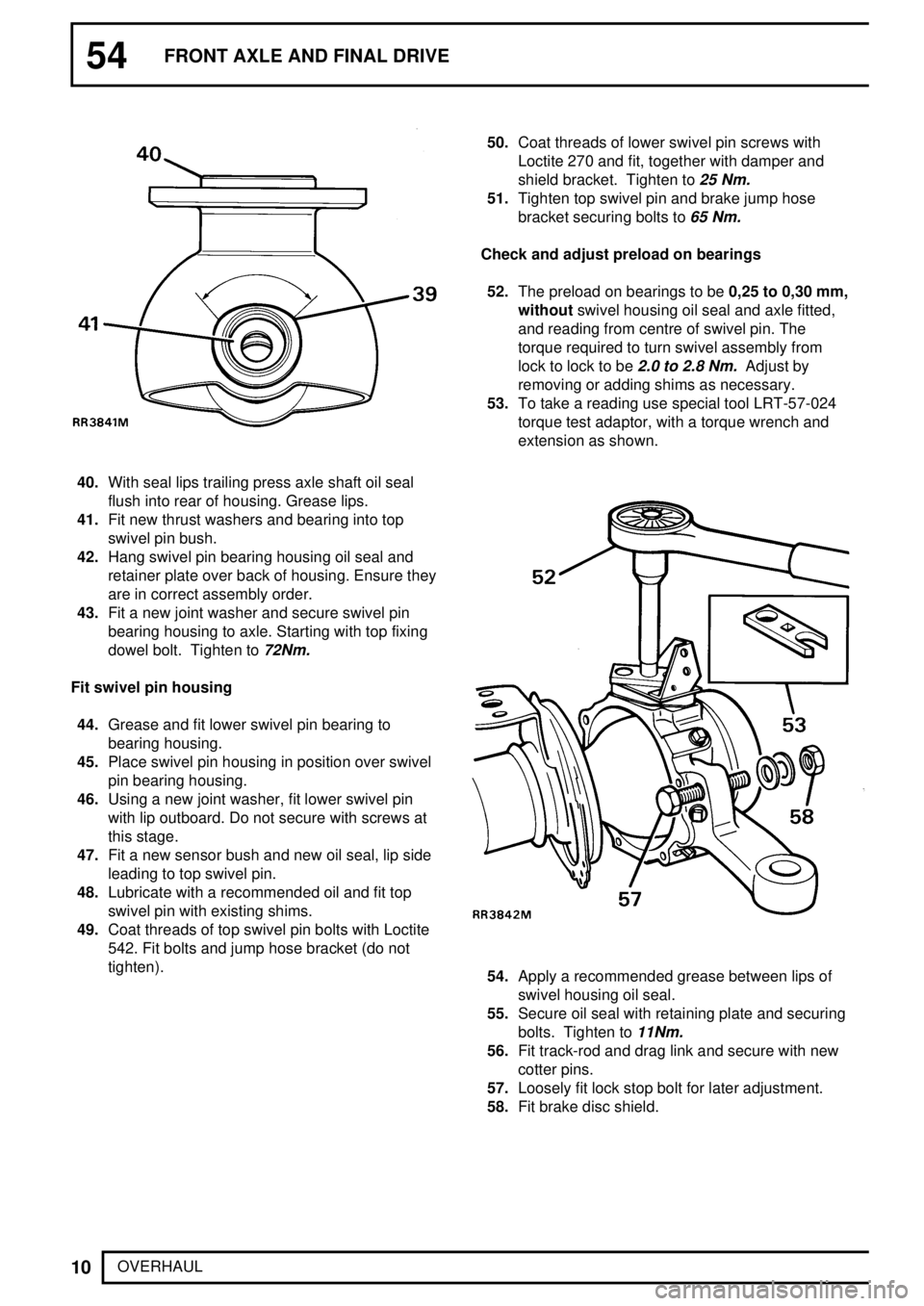
54FRONT AXLE AND FINAL DRIVE
10
OVERHAUL
40.With seal lips trailing press axle shaft oil seal
flush into rear of housing. Grease lips.
41.Fit new thrust washers and bearing into top
swivel pin bush.
42.Hang swivel pin bearing housing oil seal and
retainer plate over back of housing. Ensure they
are in correct assembly order.
43.Fit a new joint washer and secure swivel pin
bearing housing to axle. Starting with top fixing
dowel bolt. Tighten to
72Nm.
Fit swivel pin housing
44.Grease and fit lower swivel pin bearing to
bearing housing.
45.Place swivel pin housing in position over swivel
pin bearing housing.
46.Using a new joint washer, fit lower swivel pin
with lip outboard. Do not secure with screws at
this stage.
47.Fit a new sensor bush and new oil seal, lip side
leading to top swivel pin.
48.Lubricate with a recommended oil and fit top
swivel pin with existing shims.
49.Coat threads of top swivel pin bolts with Loctite
542. Fit bolts and jump hose bracket (do not
tighten).50.Coat threads of lower swivel pin screws with
Loctite 270 and fit, together with damper and
shield bracket. Tighten to
25 Nm.
51.Tighten top swivel pin and brake jump hose
bracket securing bolts to
65 Nm.
Check and adjust preload on bearings
52.The preload on bearings to be0,25 to 0,30 mm,
withoutswivel housing oil seal and axle fitted,
and reading from centre of swivel pin. The
torque required to turn swivel assembly from
lock to lock to be
2.0 to 2.8 Nm.Adjust by
removing or adding shims as necessary.
53.To take a reading use special tool LRT-57-024
torque test adaptor, with a torque wrench and
extension as shown.
54.Apply a recommended grease between lips of
swivel housing oil seal.
55.Secure oil seal with retaining plate and securing
bolts. Tighten to
11Nm.
56.Fit track-rod and drag link and secure with new
cotter pins.
57.Loosely fit lock stop bolt for later adjustment.
58.Fit brake disc shield.
Page 546 of 873
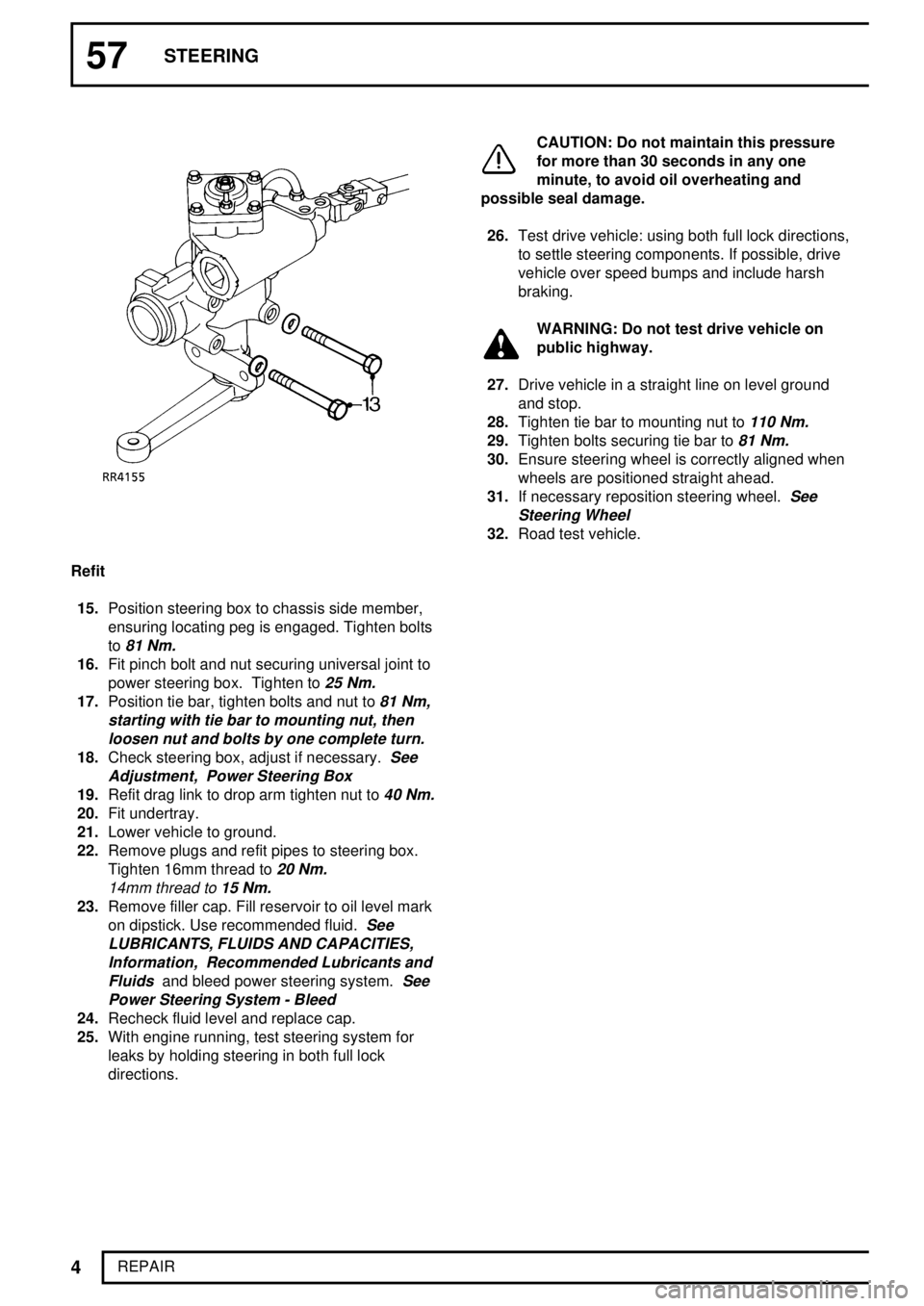
57STEERING
4
REPAIR
Refit
15.Position steering box to chassis side member,
ensuring locating peg is engaged. Tighten bolts
to
81 Nm.
16.Fit pinch bolt and nut securing universal joint to
power steering box. Tighten to
25 Nm.
17.Position tie bar, tighten bolts and nut to81 Nm,
starting with tie bar to mounting nut, then
loosen nut and bolts by one complete turn.
18.Check steering box, adjust if necessary.See
Adjustment, Power Steering Box
19.Refit drag link to drop arm tighten nut to40 Nm.
20.Fit undertray.
21.Lower vehicle to ground.
22.Remove plugs and refit pipes to steering box.
Tighten 16mm thread to
20 Nm.
14mm thread to15 Nm.
23.Remove filler cap. Fill reservoir to oil level mark
on dipstick. Use recommended fluid.
See
LUBRICANTS, FLUIDS AND CAPACITIES,
Information, Recommended Lubricants and
Fluids
and bleed power steering system.See
Power Steering System - Bleed
24.Recheck fluid level and replace cap.
25.With engine running, test steering system for
leaks by holding steering in both full lock
directions.
CAUTION: Do not maintain this pressure
for more than 30 seconds in any one
minute, to avoid oil overheating and
possible seal damage.
26.Test drive vehicle: using both full lock directions,
to settle steering components. If possible, drive
vehicle over speed bumps and include harsh
braking.
WARNING: Do not test drive vehicle on
public highway.
27.Drive vehicle in a straight line on level ground
and stop.
28.Tighten tie bar to mounting nut to
110 Nm.
29.Tighten bolts securing tie bar to81 Nm.
30.Ensure steering wheel is correctly aligned when
wheels are positioned straight ahead.
31.If necessary reposition steering wheel.
See
Steering Wheel
32.Road test vehicle.
Page 595 of 873
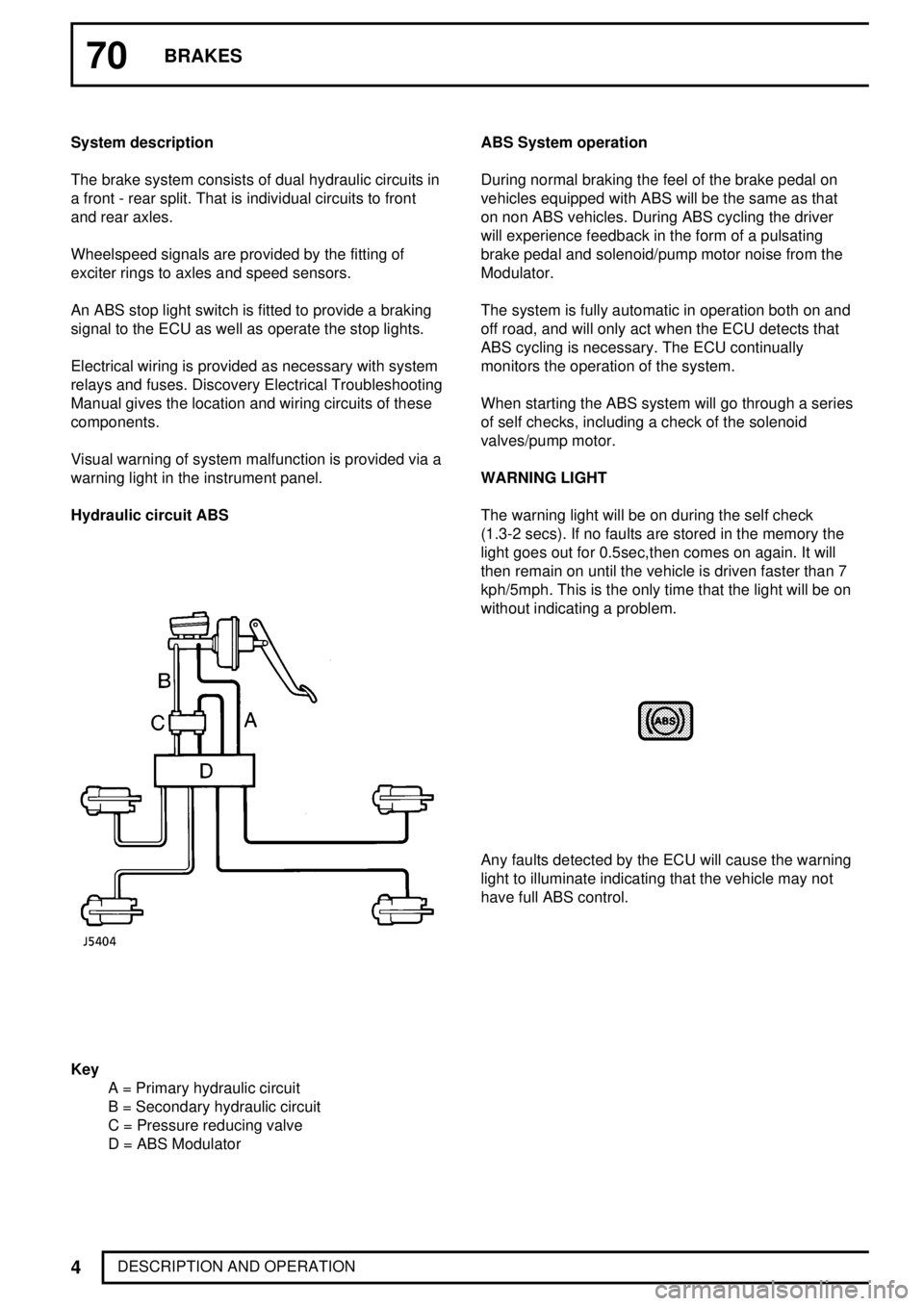
70BRAKES
4
DESCRIPTION AND OPERATION System description
The brake system consists of dual hydraulic circuits in
a front - rear split. That is individual circuits to front
and rear axles.
Wheelspeed signals are provided by the fitting of
exciter rings to axles and speed sensors.
An ABS stop light switch is fitted to provide a braking
signal to the ECU as well as operate the stop lights.
Electrical wiring is provided as necessary with system
relays and fuses. Discovery Electrical Troubleshooting
Manual gives the location and wiring circuits of these
components.
Visual warning of system malfunction is provided via a
warning light in the instrument panel.
Hydraulic circuit ABS
Key
A = Primary hydraulic circuit
B = Secondary hydraulic circuit
C = Pressure reducing valve
D = ABS ModulatorABS System operation
During normal braking the feel of the brake pedal on
vehicles equipped with ABS will be the same as that
on non ABS vehicles. During ABS cycling the driver
will experience feedback in the form of a pulsating
brake pedal and solenoid/pump motor noise from the
Modulator.
The system is fully automatic in operation both on and
off road, and will only act when the ECU detects that
ABS cycling is necessary. The ECU continually
monitors the operation of the system.
When starting the ABS system will go through a series
of self checks, including a check of the solenoid
valves/pump motor.
WARNING LIGHT
The warning light will be on during the self check
(1.3-2 secs). If no faults are stored in the memory the
light goes out for 0.5sec,then comes on again. It will
then remain on until the vehicle is driven faster than 7
kph/5mph. This is the only time that the light will be on
without indicating a problem.
Any faults detected by the ECU will cause the warning
light to illuminate indicating that the vehicle may not
have full ABS control.
Page 764 of 873
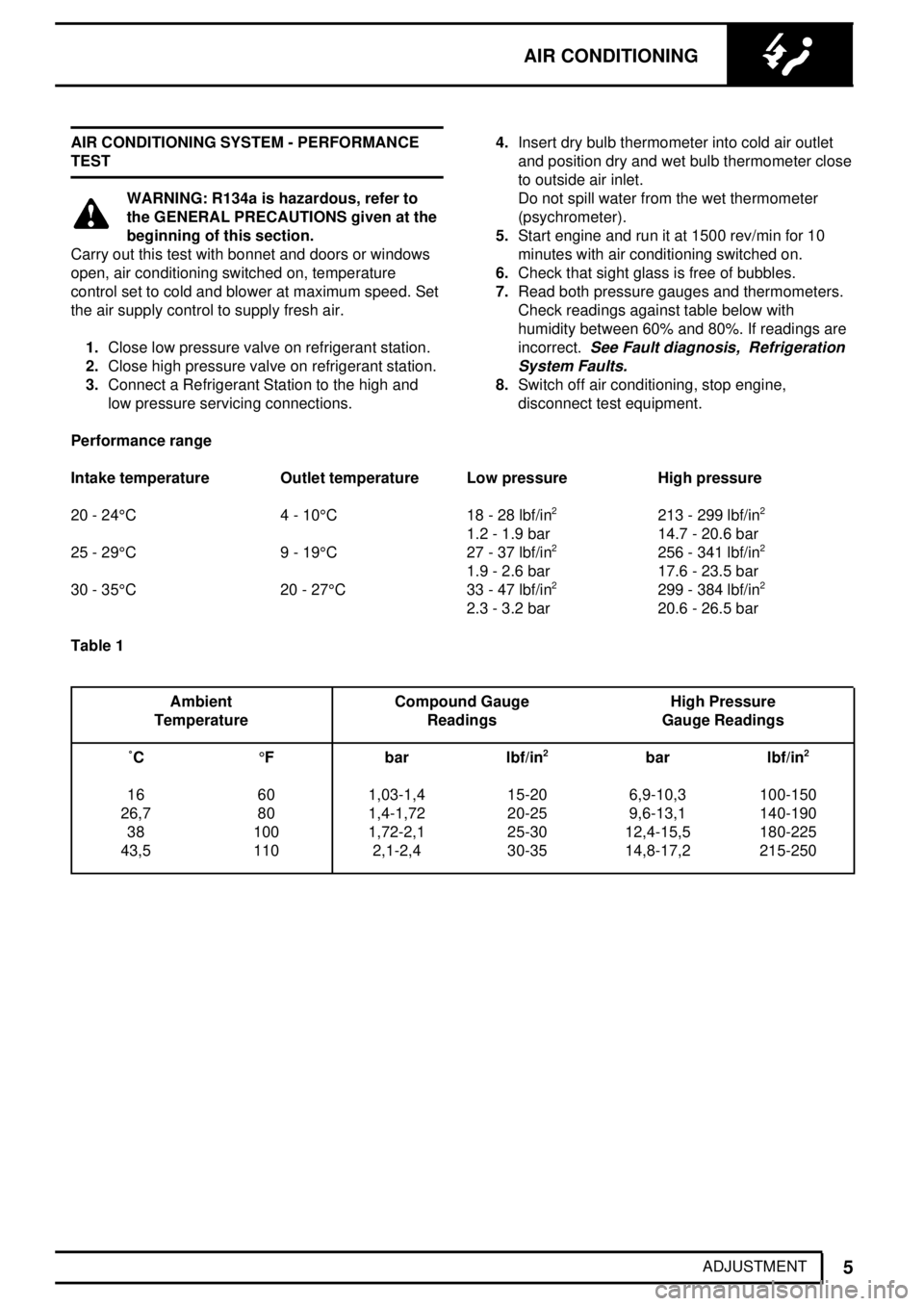
AIR CONDITIONING
5
ADJUSTMENT AIR CONDITIONING SYSTEM - PERFORMANCE
TEST
WARNING: R134a is hazardous, refer to
the GENERAL PRECAUTIONS given at the
beginning of this section.
Carry out this test with bonnet and doors or windows
open, air conditioning switched on, temperature
control set to cold and blower at maximum speed. Set
the air supply control to supply fresh air.
1.Close low pressure valve on refrigerant station.
2.Close high pressure valve on refrigerant station.
3.Connect a Refrigerant Station to the high and
low pressure servicing connections.4.Insert dry bulb thermometer into cold air outlet
and position dry and wet bulb thermometer close
to outside air inlet.
Do not spill water from the wet thermometer
(psychrometer).
5.Start engine and run it at 1500 rev/min for 10
minutes with air conditioning switched on.
6.Check that sight glass is free of bubbles.
7.Read both pressure gauges and thermometers.
Check readings against table below with
humidity between 60% and 80%. If readings are
incorrect.
See Fault diagnosis, Refrigeration
System Faults.
8.Switch off air conditioning, stop engine,
disconnect test equipment.
Performance range
Intake temperature Outlet temperature Low pressure High pressure
20 - 24°C4-10°C 18 - 28 lbf/in
2213 - 299 lbf/in2
1.2 - 1.9 bar 14.7 - 20.6 bar
25 - 29°C9-19°C 27 - 37 lbf/in2256 - 341 lbf/in2
1.9 - 2.6 bar 17.6 - 23.5 bar
30 - 35°C20-27°C 33 - 47 lbf/in2299 - 384 lbf/in2
2.3 - 3.2 bar 20.6 - 26.5 bar
Table 1
Ambient Compound Gauge High Pressure
Temperature Readings Gauge Readings
ÊC°F bar lbf/in
2bar lbf/in2
16 60 1,03-1,4 15-20 6,9-10,3 100-150
26,7 80 1,4-1,72 20-25 9,6-13,1 140-190
38 100 1,72-2,1 25-30 12,4-15,5 180-225
43,5 110 2,1-2,4 30-35 14,8-17,2 215-250
Page 765 of 873
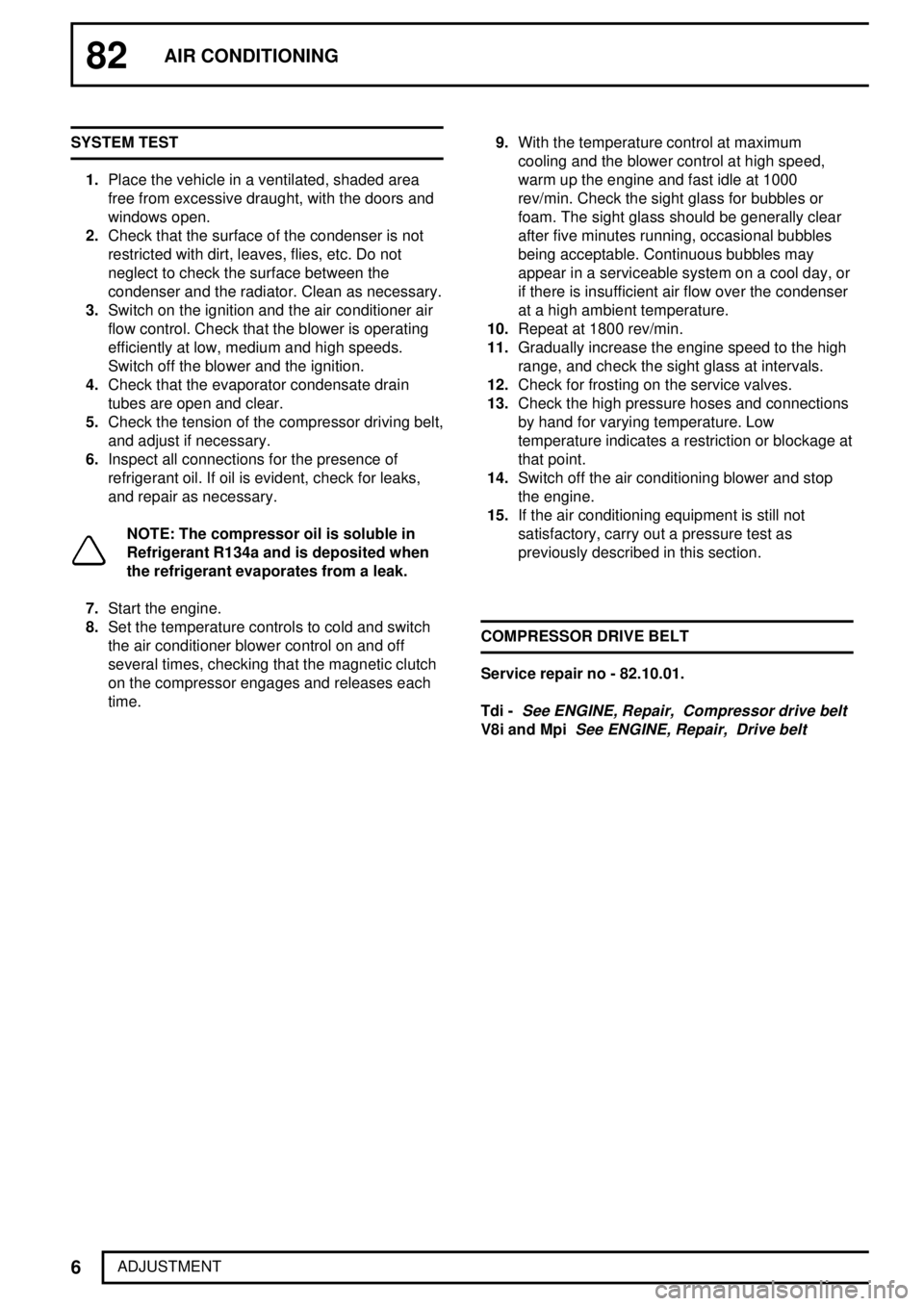
82AIR CONDITIONING
6
ADJUSTMENT SYSTEM TEST
1.Place the vehicle in a ventilated, shaded area
free from excessive draught, with the doors and
windows open.
2.Check that the surface of the condenser is not
restricted with dirt, leaves, flies, etc. Do not
neglect to check the surface between the
condenser and the radiator. Clean as necessary.
3.Switch on the ignition and the air conditioner air
flow control. Check that the blower is operating
efficiently at low, medium and high speeds.
Switch off the blower and the ignition.
4.Check that the evaporator condensate drain
tubes are open and clear.
5.Check the tension of the compressor driving belt,
and adjust if necessary.
6.Inspect all connections for the presence of
refrigerant oil. If oil is evident, check for leaks,
and repair as necessary.
NOTE: The compressor oil is soluble in
Refrigerant R134a and is deposited when
the refrigerant evaporates from a leak.
7.Start the engine.
8.Set the temperature controls to cold and switch
the air conditioner blower control on and off
several times, checking that the magnetic clutch
on the compressor engages and releases each
time.9.With the temperature control at maximum
cooling and the blower control at high speed,
warm up the engine and fast idle at 1000
rev/min. Check the sight glass for bubbles or
foam. The sight glass should be generally clear
after five minutes running, occasional bubbles
being acceptable. Continuous bubbles may
appear in a serviceable system on a cool day, or
if there is insufficient air flow over the condenser
at a high ambient temperature.
10.Repeat at 1800 rev/min.
11.Gradually increase the engine speed to the high
range, and check the sight glass at intervals.
12.Check for frosting on the service valves.
13.Check the high pressure hoses and connections
by hand for varying temperature. Low
temperature indicates a restriction or blockage at
that point.
14.Switch off the air conditioning blower and stop
the engine.
15.If the air conditioning equipment is still not
satisfactory, carry out a pressure test as
previously described in this section.
COMPRESSOR DRIVE BELT
Service repair no - 82.10.01.
Tdi -
See ENGINE, Repair, Compressor drive belt
V8i and MpiSee ENGINE, Repair, Drive belt
Page 821 of 873
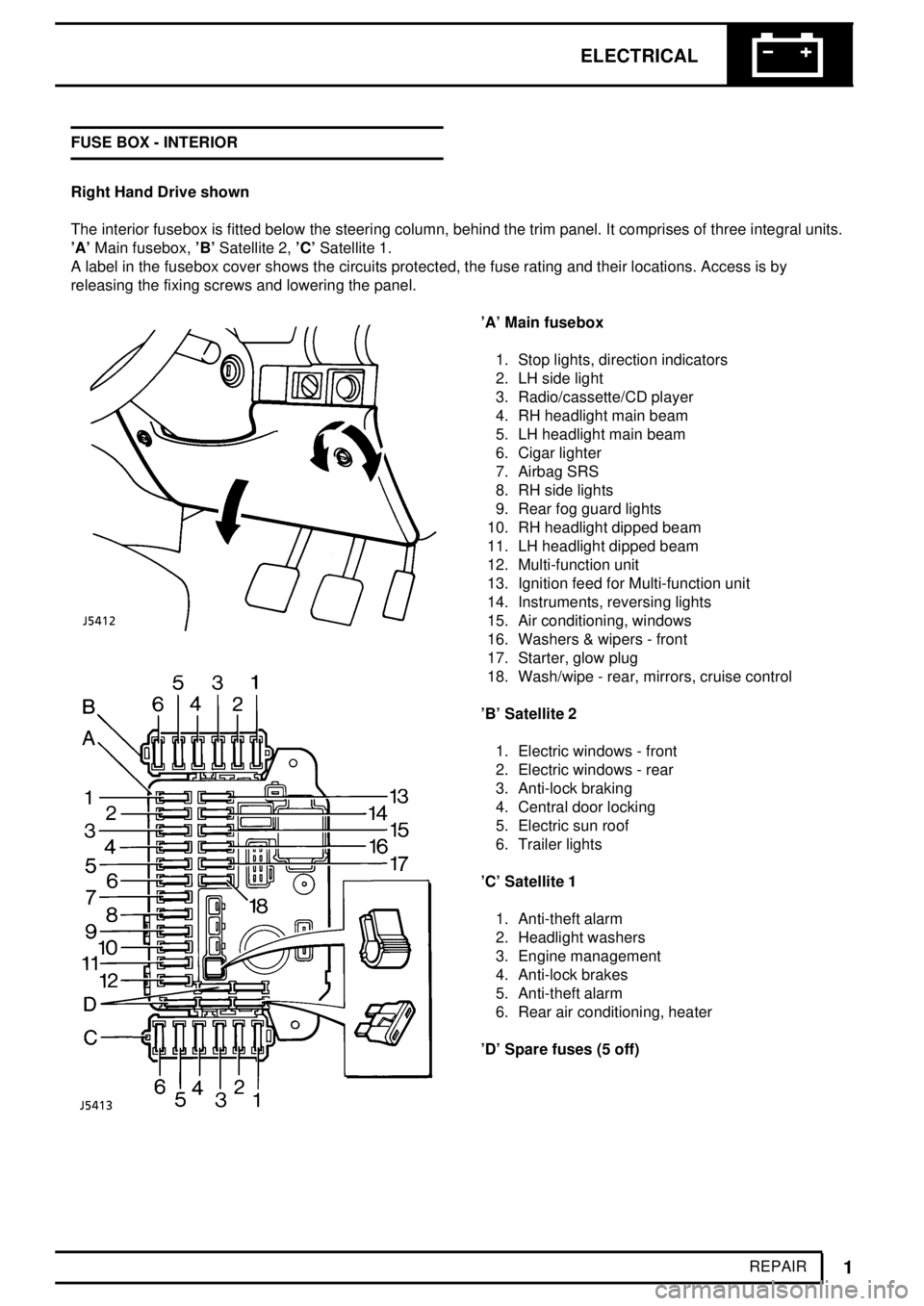
ELECTRICAL
1
REPAIR FUSE BOX - INTERIOR
Right Hand Drive shown
The interior fusebox is fitted below the steering column, behind the trim panel. It comprises of three integral units.
'A'Main fusebox,'B'Satellite 2,'C'Satellite 1.
A label in the fusebox cover shows the circuits protected, the fuse rating and their locations. Access is by
releasing the fixing screws and lowering the panel.
'A' Main fusebox
1. Stop lights, direction indicators
2. LH side light
3. Radio/cassette/CD player
4. RH headlight main beam
5. LH headlight main beam
6. Cigar lighter
7. Airbag SRS
8. RH side lights
9. Rear fog guard lights
10. RH headlight dipped beam
11. LH headlight dipped beam
12. Multi-function unit
13. Ignition feed for Multi-function unit
14. Instruments, reversing lights
15. Air conditioning, windows
16. Washers & wipers - front
17. Starter, glow plug
18. Wash/wipe - rear, mirrors, cruise control
'B' Satellite 2
1. Electric windows - front
2. Electric windows - rear
3. Anti-lock braking
4. Central door locking
5. Electric sun roof
6. Trailer lights
'C' Satellite 1
1. Anti-theft alarm
2. Headlight washers
3. Engine management
4. Anti-lock brakes
5. Anti-theft alarm
6. Rear air conditioning, heater
'D' Spare fuses (5 off)