stop start LAND ROVER DISCOVERY 1999 User Guide
[x] Cancel search | Manufacturer: LAND ROVER, Model Year: 1999, Model line: DISCOVERY, Model: LAND ROVER DISCOVERY 1999Pages: 1529, PDF Size: 34.8 MB
Page 717 of 1529
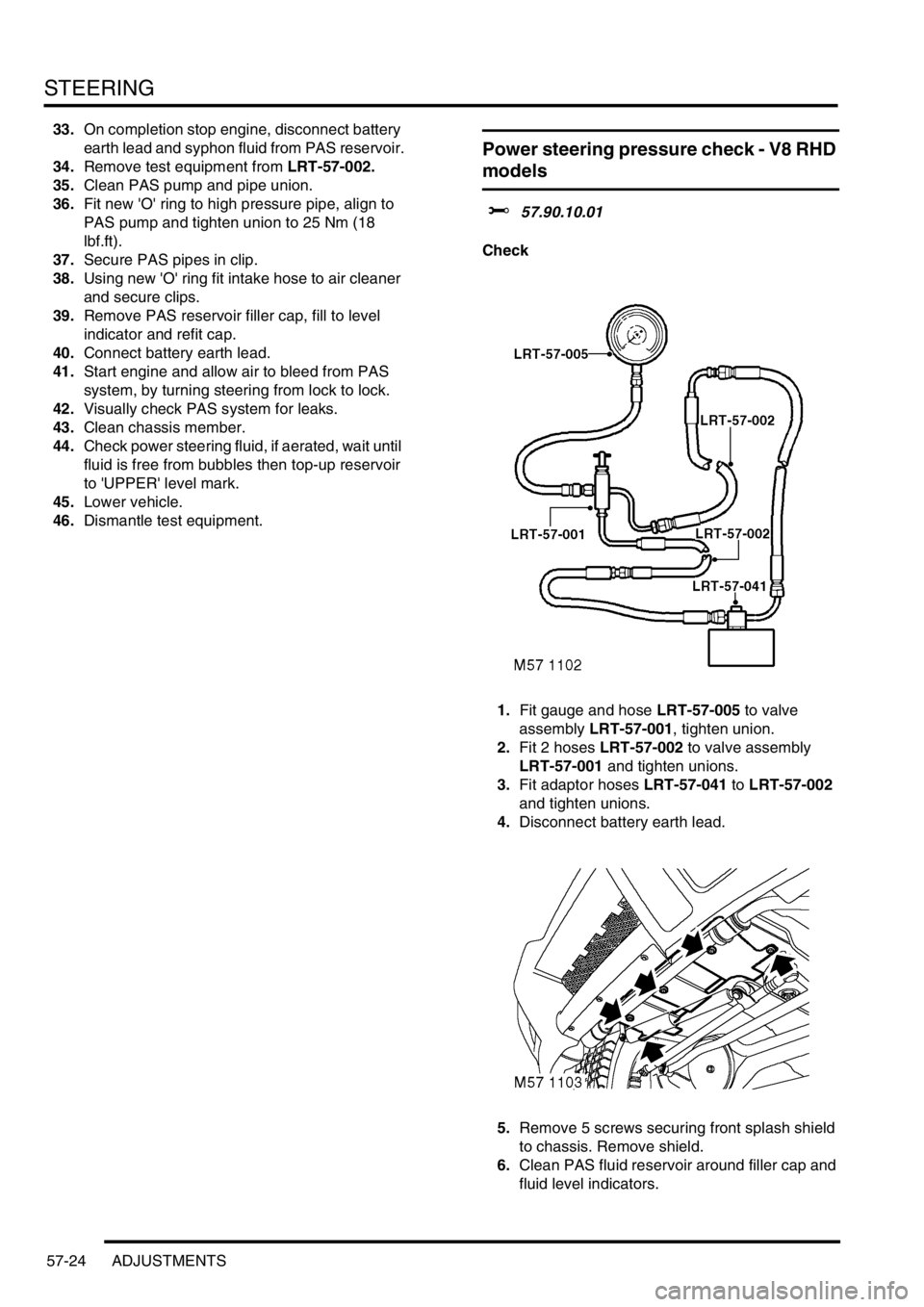
STEERING
57-24 ADJUSTMENTS
33.On completion stop engine, disconnect battery
earth lead and syphon fluid from PAS reservoir.
34.Remove test equipment from LRT-57-002.
35.Clean PAS pump and pipe union.
36.Fit new 'O' ring to high pressure pipe, align to
PAS pump and tighten union to 25 Nm (18
lbf.ft).
37.Secure PAS pipes in clip.
38.Using new 'O' ring fit intake hose to air cleaner
and secure clips.
39.Remove PAS reservoir filler cap, fill to level
indicator and refit cap.
40.Connect battery earth lead.
41.Start engine and allow air to bleed from PAS
system, by turning steering from lock to lock.
42.Visually check PAS system for leaks.
43.Clean chassis member.
44.Check power steering fluid, if aerated, wait until
fluid is free from bubbles then top-up reservoir
to 'UPPER' level mark.
45.Lower vehicle.
46.Dismantle test equipment.
Power steering pressure check - V8 RHD
models
$% 57.90.10.01
Check
1.Fit gauge and hose LRT-57-005 to valve
assembly LRT-57-001, tighten union.
2.Fit 2 hoses LRT-57-002 to valve assembly
LRT-57-001 and tighten unions.
3.Fit adaptor hoses LRT-57-041 to LRT-57-002
and tighten unions.
4.Disconnect battery earth lead.
5.Remove 5 screws securing front splash shield
to chassis. Remove shield.
6.Clean PAS fluid reservoir around filler cap and
fluid level indicators.
Page 718 of 1529
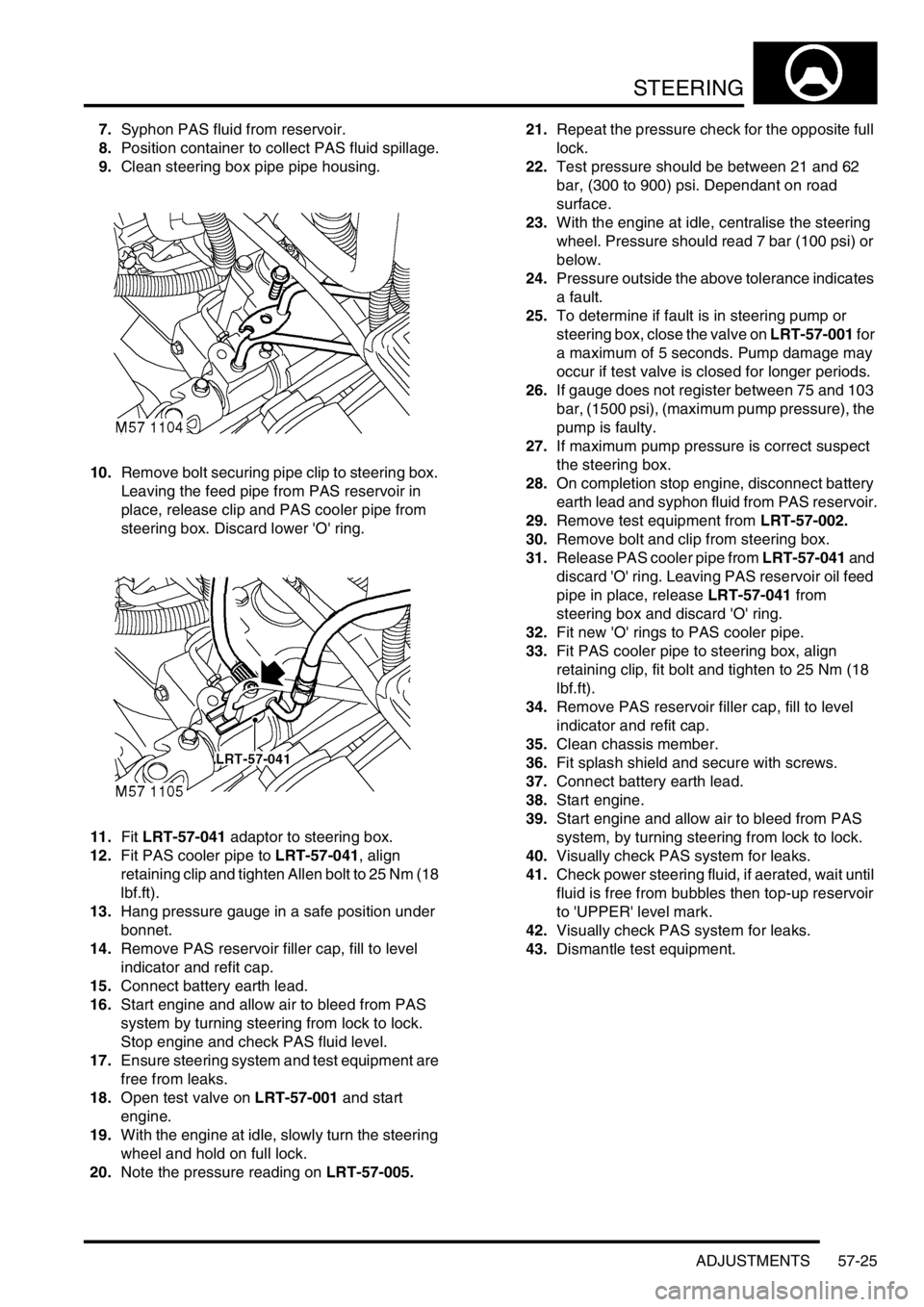
STEERING
ADJUSTMENTS 57-25
7.Syphon PAS fluid from reservoir.
8.Position container to collect PAS fluid spillage.
9.Clean steering box pipe pipe housing.
10.Remove bolt securing pipe clip to steering box.
Leaving the feed pipe from PAS reservoir in
place, release clip and PAS cooler pipe from
steering box. Discard lower 'O' ring.
11.Fit LRT-57-041 adaptor to steering box.
12.Fit PAS cooler pipe to LRT-57-041, align
retaining clip and tighten Allen bolt to 25 Nm (18
lbf.ft).
13.Hang pressure gauge in a safe position under
bonnet.
14.Remove PAS reservoir filler cap, fill to level
indicator and refit cap.
15.Connect battery earth lead.
16.Start engine and allow air to bleed from PAS
system by turning steering from lock to lock.
Stop engine and check PAS fluid level.
17.Ensure steering system and test equipment are
free from leaks.
18.Open test valve on LRT-57-001 and start
engine.
19.With the engine at idle, slowly turn the steering
wheel and hold on full lock.
20.Note the pressure reading on LRT-57-005.21.Repeat the pressure check for the opposite full
lock.
22.Test pressure should be between 21 and 62
bar, (300 to 900) psi. Dependant on road
surface.
23.With the engine at idle, centralise the steering
wheel. Pressure should read 7 bar (100 psi) or
below.
24.Pressure outside the above tolerance indicates
a fault.
25.To determine if fault is in steering pump or
steering box, close the valve on LRT-57-001 for
a maximum of 5 seconds. Pump damage may
occur if test valve is closed for longer periods.
26.If gauge does not register between 75 and 103
bar, (1500 psi), (maximum pump pressure), the
pump is faulty.
27.If maximum pump pressure is correct suspect
the steering box.
28.On completion stop engine, disconnect battery
earth lead and syphon fluid from PAS reservoir.
29.Remove test equipment from LRT-57-002.
30.Remove bolt and clip from steering box.
31.Release PAS cooler pipe from LRT-57-041 and
discard 'O' ring. Leaving PAS reservoir oil feed
pipe in place, release LRT-57-041 from
steering box and discard 'O' ring.
32.Fit new 'O' rings to PAS cooler pipe.
33.Fit PAS cooler pipe to steering box, align
retaining clip, fit bolt and tighten to 25 Nm (18
lbf.ft).
34.Remove PAS reservoir filler cap, fill to level
indicator and refit cap.
35.Clean chassis member.
36.Fit splash shield and secure with screws.
37.Connect battery earth lead.
38.Start engine.
39.Start engine and allow air to bleed from PAS
system, by turning steering from lock to lock.
40.Visually check PAS system for leaks.
41.Check power steering fluid, if aerated, wait until
fluid is free from bubbles then top-up reservoir
to 'UPPER' level mark.
42.Visually check PAS system for leaks.
43.Dismantle test equipment.
Page 831 of 1529
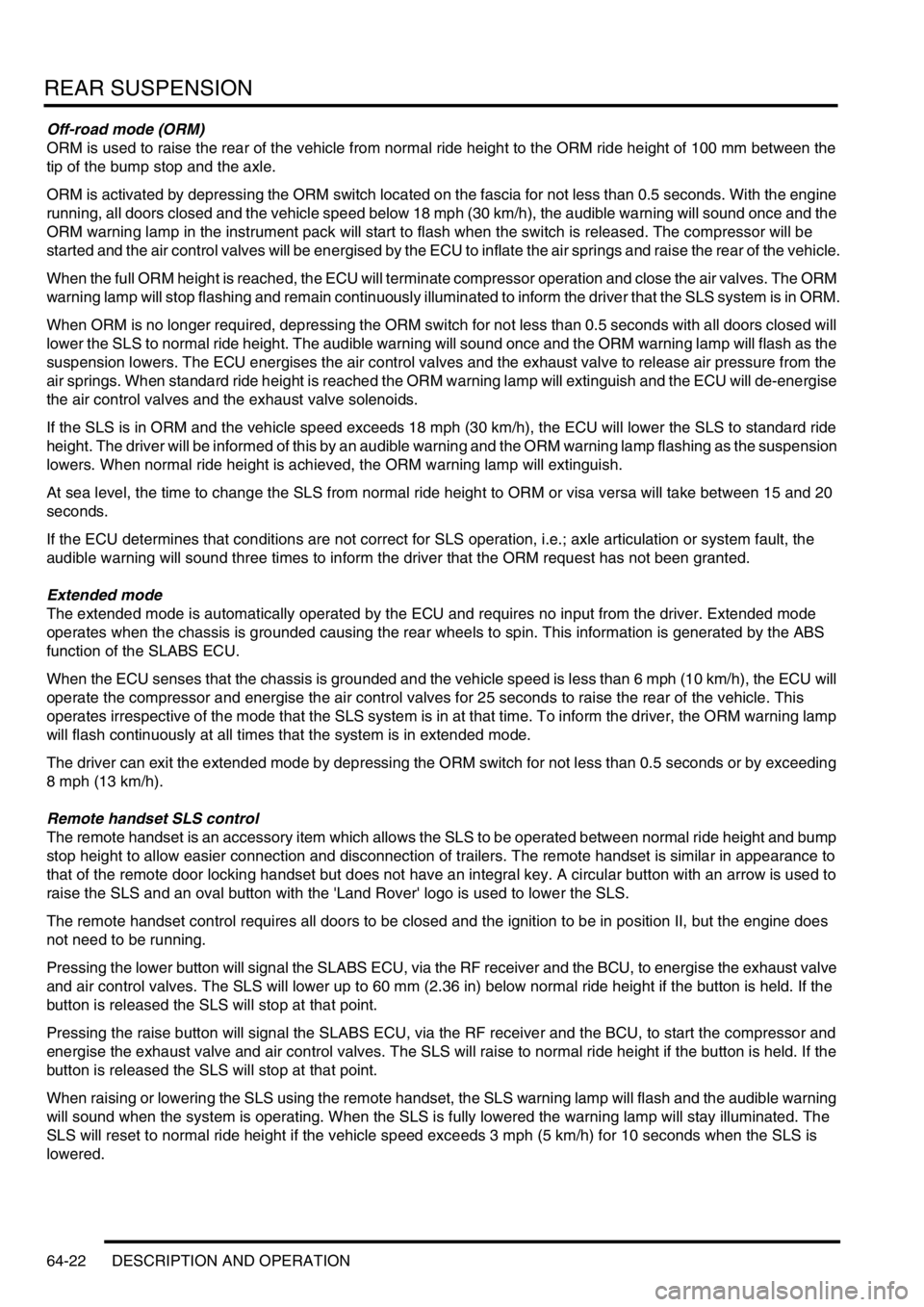
REAR SUSPENSION
64-22 DESCRIPTION AND OPERATION
Off-road mode (ORM)
ORM is used to raise the rear of the vehicle from normal ride height to the ORM ride height of 100 mm between the
tip of the bump stop and the axle.
ORM is activated by depressing the ORM switch located on the fascia for not less than 0.5 seconds. With the engine
running, all doors closed and the vehicle speed below 18 mph (30 km/h), the audible warning will sound once and the
ORM warning lamp in the instrument pack will start to flash when the switch is released. The compressor will be
started and the air control valves will be energised by the ECU to inflate the air springs and raise the rear of the vehicle.
When the full ORM height is reached, the ECU will terminate compressor operation and close the air valves. The ORM
warning lamp will stop flashing and remain continuously illuminated to inform the driver that the SLS system is in ORM.
When ORM is no longer required, depressing the ORM switch for not less than 0.5 seconds with all doors closed will
lower the SLS to normal ride height. The audible warning will sound once and the ORM warning lamp will flash as the
suspension lowers. The ECU energises the air control valves and the exhaust valve to release air pressure from the
air springs. When standard ride height is reached the ORM warning lamp will extinguish and the ECU will de-energise
the air control valves and the exhaust valve solenoids.
If the SLS is in ORM and the vehicle speed exceeds 18 mph (30 km/h), the ECU will lower the SLS to standard ride
height. The driver will be informed of this by an audible warning and the ORM warning lamp flashing as the suspension
lowers. When normal ride height is achieved, the ORM warning lamp will extinguish.
At sea level, the time to change the SLS from normal ride height to ORM or visa versa will take between 15 and 20
seconds.
If the ECU determines that conditions are not correct for SLS operation, i.e.; axle articulation or system fault, the
audible warning will sound three times to inform the driver that the ORM request has not been granted.
Extended mode
The extended mode is automatically operated by the ECU and requires no input from the driver. Extended mode
operates when the chassis is grounded causing the rear wheels to spin. This information is generated by the ABS
function of the SLABS ECU.
When the ECU senses that the chassis is grounded and the vehicle speed is less than 6 mph (10 km/h), the ECU will
operate the compressor and energise the air control valves for 25 seconds to raise the rear of the vehicle. This
operates irrespective of the mode that the SLS system is in at that time. To inform the driver, the ORM warning lamp
will flash continuously at all times that the system is in extended mode.
The driver can exit the extended mode by depressing the ORM switch for not less than 0.5 seconds or by exceeding
8 mph (13 km/h).
Remote handset SLS control
The remote handset is an accessory item which allows the SLS to be operated between normal ride height and bump
stop height to allow easier connection and disconnection of trailers. The remote handset is similar in appearance to
that of the remote door locking handset but does not have an integral key. A circular button with an arrow is used to
raise the SLS and an oval button with the 'Land Rover' logo is used to lower the SLS.
The remote handset control requires all doors to be closed and the ignition to be in position II, but the engine does
not need to be running.
Pressing the lower button will signal the SLABS ECU, via the RF receiver and the BCU, to energise the exhaust valve
and air control valves. The SLS will lower up to 60 mm (2.36 in) below normal ride height if the button is held. If the
button is released the SLS will stop at that point.
Pressing the raise button will signal the SLABS ECU, via the RF receiver and the BCU, to start the compressor and
energise the exhaust valve and air control valves. The SLS will raise to normal ride height if the button is held. If the
button is released the SLS will stop at that point.
When raising or lowering the SLS using the remote handset, the SLS warning lamp will flash and the audible warning
will sound when the system is operating. When the SLS is fully lowered the warning lamp will stay illuminated. The
SLS will reset to normal ride height if the vehicle speed exceeds 3 mph (5 km/h) for 10 seconds when the SLS is
lowered.
Page 832 of 1529
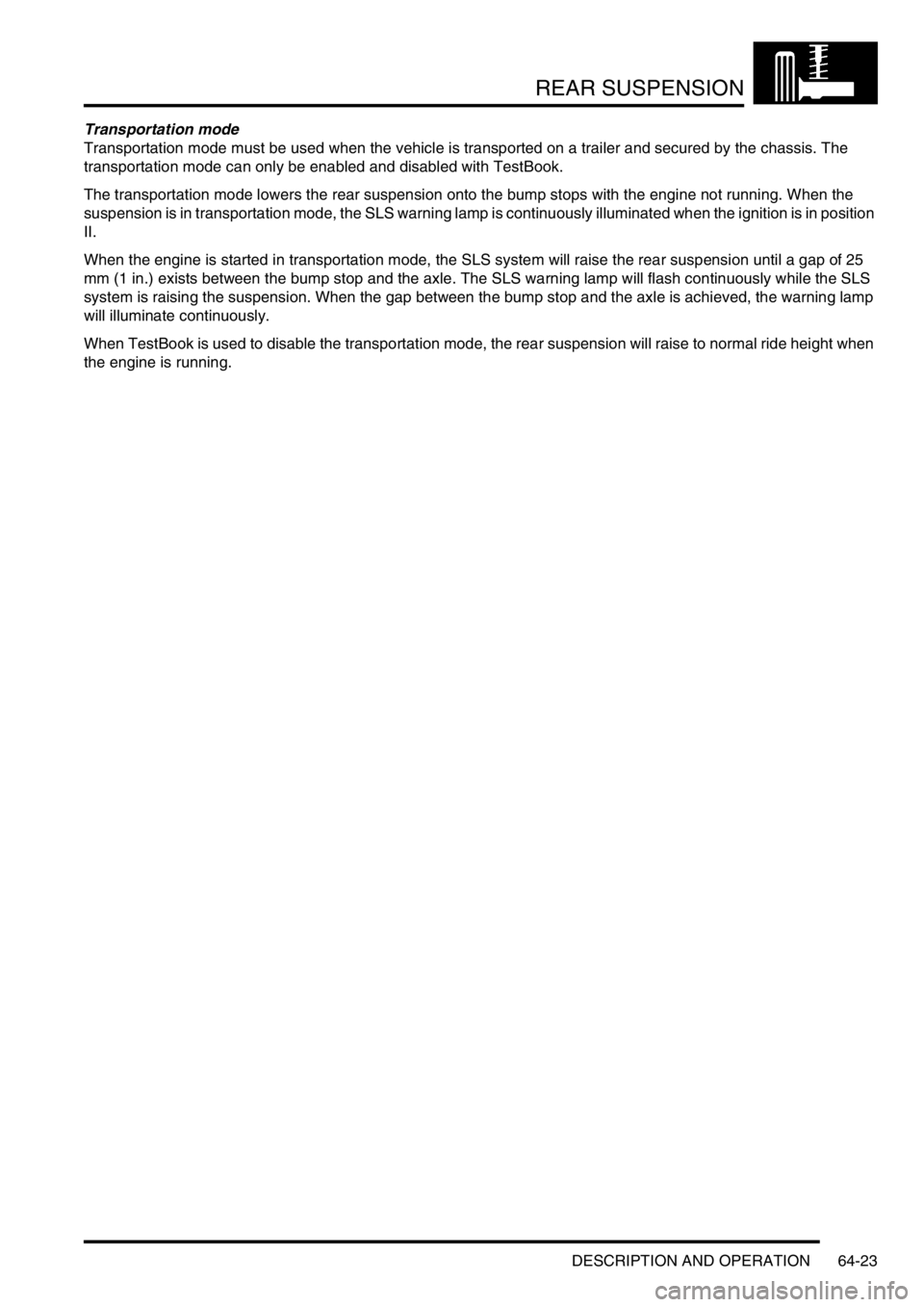
REAR SUSPENSION
DESCRIPTION AND OPERATION 64-23
Transportation mode
Transportation mode must be used when the vehicle is transported on a trailer and secured by the chassis. The
transportation mode can only be enabled and disabled with TestBook.
The transportation mode lowers the rear suspension onto the bump stops with the engine not running. When the
suspension is in transportation mode, the SLS warning lamp is continuously illuminated when the ignition is in position
II.
When the engine is started in transportation mode, the SLS system will raise the rear suspension until a gap of 25
mm (1 in.) exists between the bump stop and the axle. The SLS warning lamp will flash continuously while the SLS
system is raising the suspension. When the gap between the bump stop and the axle is achieved, the warning lamp
will illuminate continuously.
When TestBook is used to disable the transportation mode, the rear suspension will raise to normal ride height when
the engine is running.
Page 1171 of 1529
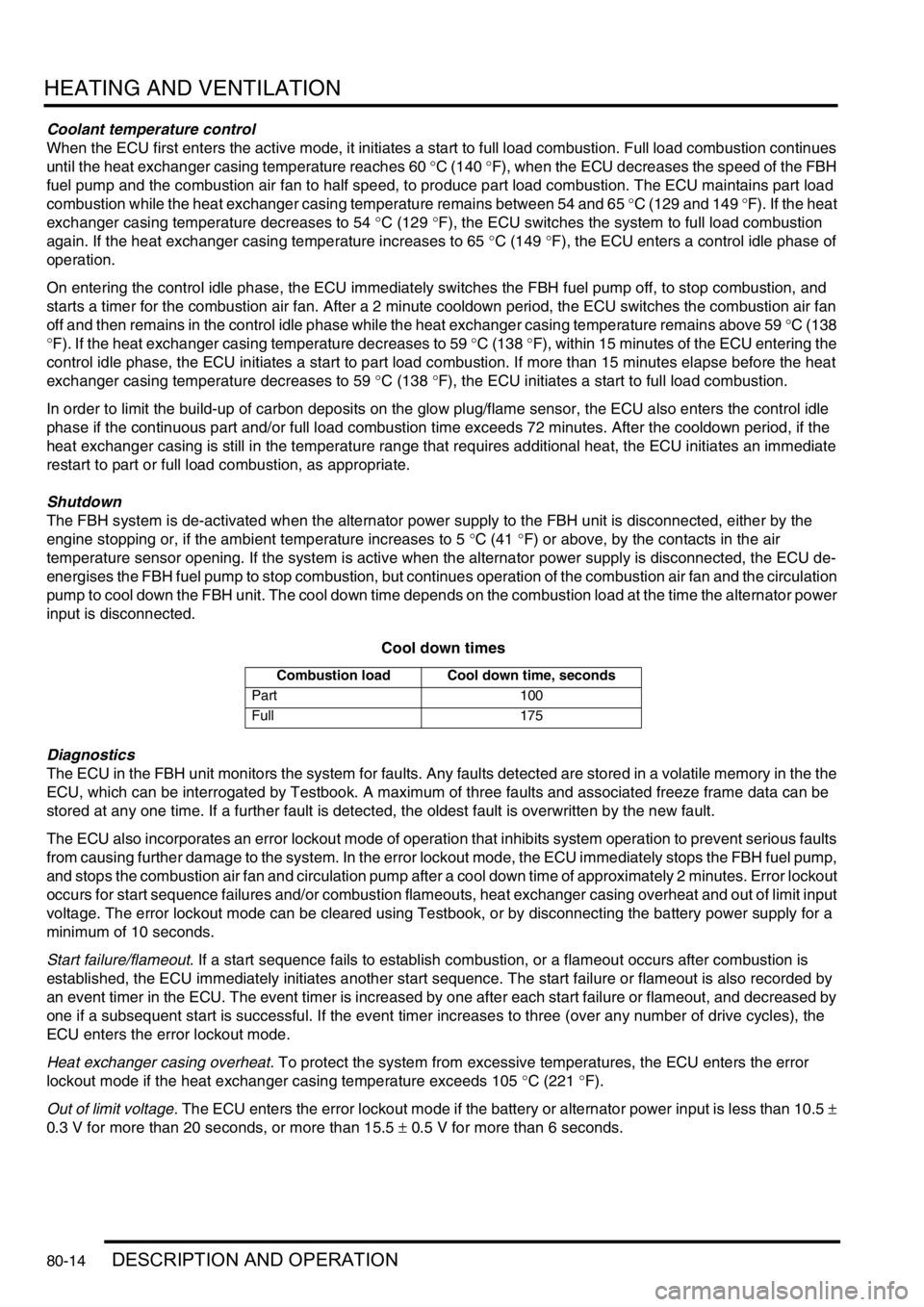
HEATING AND VENTILATION
80-14DESCRIPTION AND OPERATION
Coolant temperature control
When the ECU first enters the active mode, it initiates a start to full load combustion. Full load combustion continues
until the heat exchanger casing temperature reaches 60 °C (140 °F), when the ECU decreases the speed of the FBH
fuel pump and the combustion air fan to half speed, to produce part load combustion. The ECU maintains part load
combustion while the heat exchanger casing temperature remains between 54 and 65 °C (129 and 149 °F). If the heat
exchanger casing temperature decreases to 54 °C (129 °F), the ECU switches the system to full load combustion
again. If the heat exchanger casing temperature increases to 65 °C (149 °F), the ECU enters a control idle phase of
operation.
On entering the control idle phase, the ECU immediately switches the FBH fuel pump off, to stop combustion, and
starts a timer for the combustion air fan. After a 2 minute cooldown period, the ECU switches the combustion air fan
off and then remains in the control idle phase while the heat exchanger casing temperature remains above 59 °C (138
°F). If the heat exchanger casing temperature decreases to 59 °C (138 °F), within 15 minutes of the ECU entering the
control idle phase, the ECU initiates a start to part load combustion. If more than 15 minutes elapse before the heat
exchanger casing temperature decreases to 59 °C (138 °F), the ECU initiates a start to full load combustion.
In order to limit the build-up of carbon deposits on the glow plug/flame sensor, the ECU also enters the control idle
phase if the continuous part and/or full load combustion time exceeds 72 minutes. After the cooldown period, if the
heat exchanger casing is still in the temperature range that requires additional heat, the ECU initiates an immediate
restart to part or full load combustion, as appropriate.
Shutdown
The FBH system is de-activated when the alternator power supply to the FBH unit is disconnected, either by the
engine stopping or, if the ambient temperature increases to 5 °C (41 °F) or above, by the contacts in the air
temperature sensor opening. If the system is active when the alternator power supply is disconnected, the ECU de-
energises the FBH fuel pump to stop combustion, but continues operation of the combustion air fan and the circulation
pump to cool down the FBH unit. The cool down time depends on the combustion load at the time the alternator power
input is disconnected.
Cool down times
Diagnostics
The ECU in the FBH unit monitors the system for faults. Any faults detected are stored in a volatile memory in the the
ECU, which can be interrogated by Testbook. A maximum of three faults and associated freeze frame data can be
stored at any one time. If a further fault is detected, the oldest fault is overwritten by the new fault.
The ECU also incorporates an error lockout mode of operation that inhibits system operation to prevent serious faults
from causing further damage to the system. In the error lockout mode, the ECU immediately stops the FBH fuel pump,
and stops the combustion air fan and circulation pump after a cool down time of approximately 2 minutes. Error lockout
occurs for start sequence failures and/or combustion flameouts, heat exchanger casing overheat and out of limit input
voltage. The error lockout mode can be cleared using Testbook, or by disconnecting the battery power supply for a
minimum of 10 seconds.
Start failure/flameout. If a start sequence fails to establish combustion, or a flameout occurs after combustion is
established, the ECU immediately initiates another start sequence. The start failure or flameout is also recorded by
an event timer in the ECU. The event timer is increased by one after each start failure or flameout, and decreased by
one if a subsequent start is successful. If the event timer increases to three (over any number of drive cycles), the
ECU enters the error lockout mode.
Heat exchanger casing overheat. To protect the system from excessive temperatures, the ECU enters the error
lockout mode if the heat exchanger casing temperature exceeds 105 °C (221 °F).
Out of limit voltage. The ECU enters the error lockout mode if the battery or alternator power input is less than 10.5 ±
0.3 V for more than 20 seconds, or more than 15.5 ± 0.5 V for more than 6 seconds.
Combustion load Cool down time, seconds
Part 100
Full 175
Page 1254 of 1529
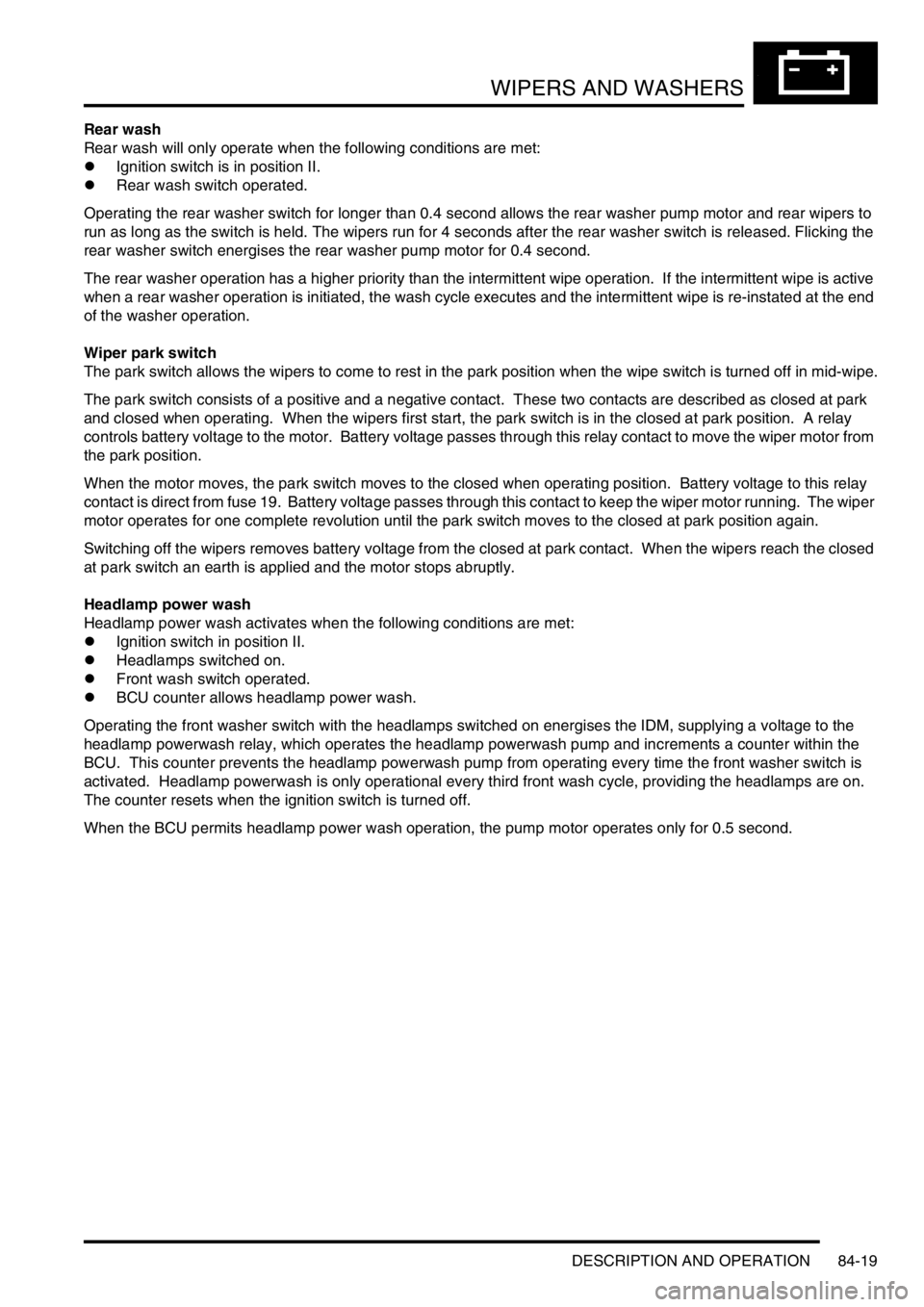
WIPERS AND WASHERS
DESCRIPTION AND OPERATION 84-19
Rear wash
Rear wash will only operate when the following conditions are met:
lIgnition switch is in position II.
lRear wash switch operated.
Operating the rear washer switch for longer than 0.4 second allows the rear washer pump motor and rear wipers to
run as long as the switch is held. The wipers run for 4 seconds after the rear washer switch is released. Flicking the
rear washer switch energises the rear washer pump motor for 0.4 second.
The rear washer operation has a higher priority than the intermittent wipe operation. If the intermittent wipe is active
when a rear washer operation is initiated, the wash cycle executes and the intermittent wipe is re-instated at the end
of the washer operation.
Wiper park switch
The park switch allows the wipers to come to rest in the park position when the wipe switch is turned off in mid-wipe.
The park switch consists of a positive and a negative contact. These two contacts are described as closed at park
and closed when operating. When the wipers first start, the park switch is in the closed at park position. A relay
controls battery voltage to the motor. Battery voltage passes through this relay contact to move the wiper motor from
the park position.
When the motor moves, the park switch moves to the closed when operating position. Battery voltage to this relay
contact is direct from fuse 19. Battery voltage passes through this contact to keep the wiper motor running. The wiper
motor operates for one complete revolution until the park switch moves to the closed at park position again.
Switching off the wipers removes battery voltage from the closed at park contact. When the wipers reach the closed
at park switch an earth is applied and the motor stops abruptly.
Headlamp power wash
Headlamp power wash activates when the following conditions are met:
lIgnition switch in position II.
lHeadlamps switched on.
lFront wash switch operated.
lBCU counter allows headlamp power wash.
Operating the front washer switch with the headlamps switched on energises the IDM, supplying a voltage to the
headlamp powerwash relay, which operates the headlamp powerwash pump and increments a counter within the
BCU. This counter prevents the headlamp powerwash pump from operating every time the front washer switch is
activated. Headlamp powerwash is only operational every third front wash cycle, providing the headlamps are on.
The counter resets when the ignition switch is turned off.
When the BCU permits headlamp power wash operation, the pump motor operates only for 0.5 second.
Page 1306 of 1529
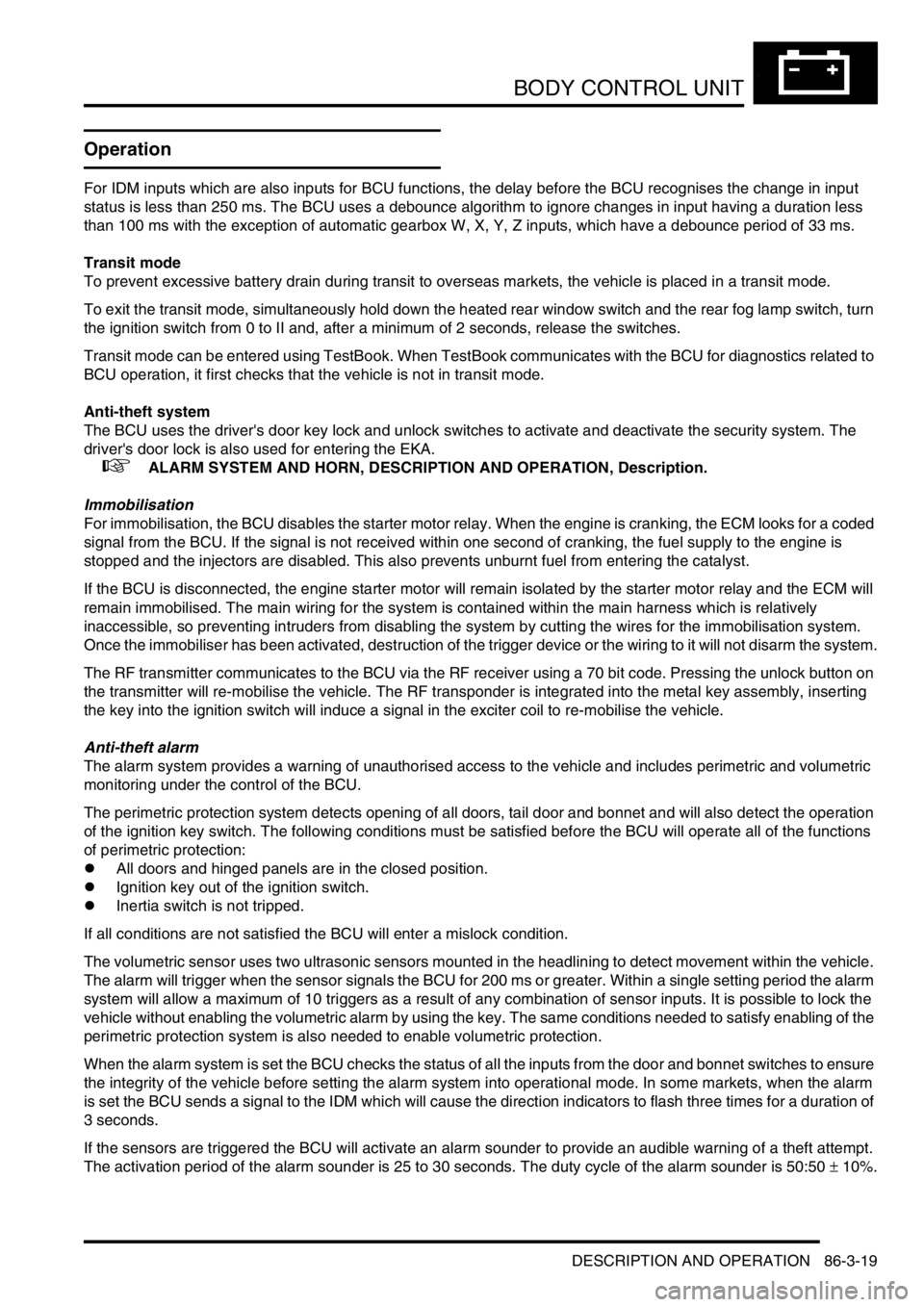
BODY CONTROL UNIT
DESCRIPTION AND OPERATION 86-3-19
Operation
For IDM inputs which are also inputs for BCU functions, the delay before the BCU recognises the change in input
status is less than 250 ms. The BCU uses a debounce algorithm to ignore changes in input having a duration less
than 100 ms with the exception of automatic gearbox W, X, Y, Z inputs, which have a debounce period of 33 ms.
Transit mode
To prevent excessive battery drain during transit to overseas markets, the vehicle is placed in a transit mode.
To exit the transit mode, simultaneously hold down the heated rear window switch and the rear fog lamp switch, turn
the ignition switch from 0 to II and, after a minimum of 2 seconds, release the switches.
Transit mode can be entered using TestBook. When TestBook communicates with the BCU for diagnostics related to
BCU operation, it first checks that the vehicle is not in transit mode.
Anti-theft system
The BCU uses the driver's door key lock and unlock switches to activate and deactivate the security system. The
driver's door lock is also used for entering the EKA.
+ ALARM SYSTEM AND HORN, DESCRIPTION AND OPERATION, Description.
Immobilisation
For immobilisation, the BCU disables the starter motor relay. When the engine is cranking, the ECM looks for a coded
signal from the BCU. If the signal is not received within one second of cranking, the fuel supply to the engine is
stopped and the injectors are disabled. This also prevents unburnt fuel from entering the catalyst.
If the BCU is disconnected, the engine starter motor will remain isolated by the starter motor relay and the ECM will
remain immobilised. The main wiring for the system is contained within the main harness which is relatively
inaccessible, so preventing intruders from disabling the system by cutting the wires for the immobilisation system.
Once the immobiliser has been activated, destruction of the trigger device or the wiring to it will not disarm the system.
The RF transmitter communicates to the BCU via the RF receiver using a 70 bit code. Pressing the unlock button on
the transmitter will re-mobilise the vehicle. The RF transponder is integrated into the metal key assembly, inserting
the key into the ignition switch will induce a signal in the exciter coil to re-mobilise the vehicle.
Anti-theft alarm
The alarm system provides a warning of unauthorised access to the vehicle and includes perimetric and volumetric
monitoring under the control of the BCU.
The perimetric protection system detects opening of all doors, tail door and bonnet and will also detect the operation
of the ignition key switch. The following conditions must be satisfied before the BCU will operate all of the functions
of perimetric protection:
lAll doors and hinged panels are in the closed position.
lIgnition key out of the ignition switch.
lInertia switch is not tripped.
If all conditions are not satisfied the BCU will enter a mislock condition.
The volumetric sensor uses two ultrasonic sensors mounted in the headlining to detect movement within the vehicle.
The alarm will trigger when the sensor signals the BCU for 200 ms or greater. Within a single setting period the alarm
system will allow a maximum of 10 triggers as a result of any combination of sensor inputs. It is possible to lock the
vehicle without enabling the volumetric alarm by using the key. The same conditions needed to satisfy enabling of the
perimetric protection system is also needed to enable volumetric protection.
When the alarm system is set the BCU checks the status of all the inputs from the door and bonnet switches to ensure
the integrity of the vehicle before setting the alarm system into operational mode. In some markets, when the alarm
is set the BCU sends a signal to the IDM which will cause the direction indicators to flash three times for a duration of
3 seconds.
If the sensors are triggered the BCU will activate an alarm sounder to provide an audible warning of a theft attempt.
The activation period of the alarm sounder is 25 to 30 seconds. The duty cycle of the alarm sounder is 50:50 ± 10%.
Page 1309 of 1529
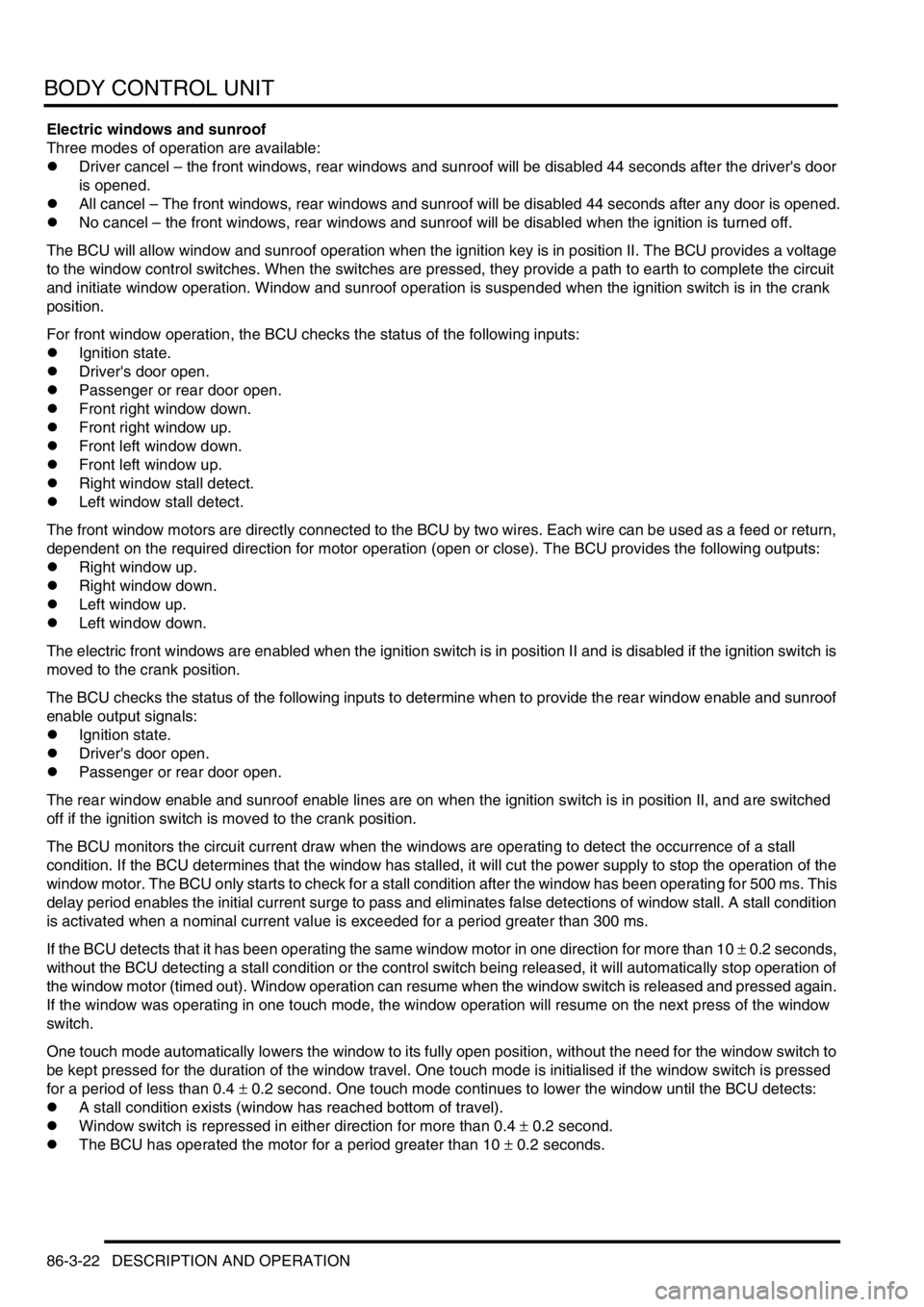
BODY CONTROL UNIT
86-3-22 DESCRIPTION AND OPERATION
Electric windows and sunroof
Three modes of operation are available:
lDriver cancel – the front windows, rear windows and sunroof will be disabled 44 seconds after the driver's door
is opened.
lAll cancel – The front windows, rear windows and sunroof will be disabled 44 seconds after any door is opened.
lNo cancel – the front windows, rear windows and sunroof will be disabled when the ignition is turned off.
The BCU will allow window and sunroof operation when the ignition key is in position II. The BCU provides a voltage
to the window control switches. When the switches are pressed, they provide a path to earth to complete the circuit
and initiate window operation. Window and sunroof operation is suspended when the ignition switch is in the crank
position.
For front window operation, the BCU checks the status of the following inputs:
lIgnition state.
lDriver's door open.
lPassenger or rear door open.
lFront right window down.
lFront right window up.
lFront left window down.
lFront left window up.
lRight window stall detect.
lLeft window stall detect.
The front window motors are directly connected to the BCU by two wires. Each wire can be used as a feed or return,
dependent on the required direction for motor operation (open or close). The BCU provides the following outputs:
lRight window up.
lRight window down.
lLeft window up.
lLeft window down.
The electric front windows are enabled when the ignition switch is in position II and is disabled if the ignition switch is
moved to the crank position.
The BCU checks the status of the following inputs to determine when to provide the rear window enable and sunroof
enable output signals:
lIgnition state.
lDriver's door open.
lPassenger or rear door open.
The rear window enable and sunroof enable lines are on when the ignition switch is in position II, and are switched
off if the ignition switch is moved to the crank position.
The BCU monitors the circuit current draw when the windows are operating to detect the occurrence of a stall
condition. If the BCU determines that the window has stalled, it will cut the power supply to stop the operation of the
window motor. The BCU only starts to check for a stall condition after the window has been operating for 500 ms. This
delay period enables the initial current surge to pass and eliminates false detections of window stall. A stall condition
is activated when a nominal current value is exceeded for a period greater than 300 ms.
If the BCU detects that it has been operating the same window motor in one direction for more than 10 ± 0.2 seconds,
without the BCU detecting a stall condition or the control switch being released, it will automatically stop operation of
the window motor (timed out). Window operation can resume when the window switch is released and pressed again.
If the window was operating in one touch mode, the window operation will resume on the next press of the window
switch.
One touch mode automatically lowers the window to its fully open position, without the need for the window switch to
be kept pressed for the duration of the window travel. One touch mode is initialised if the window switch is pressed
for a period of less than 0.4 ± 0.2 second. One touch mode continues to lower the window until the BCU detects:
lA stall condition exists (window has reached bottom of travel).
lWindow switch is repressed in either direction for more than 0.4 ± 0.2 second.
lThe BCU has operated the motor for a period greater than 10 ± 0.2 seconds.
Page 1318 of 1529
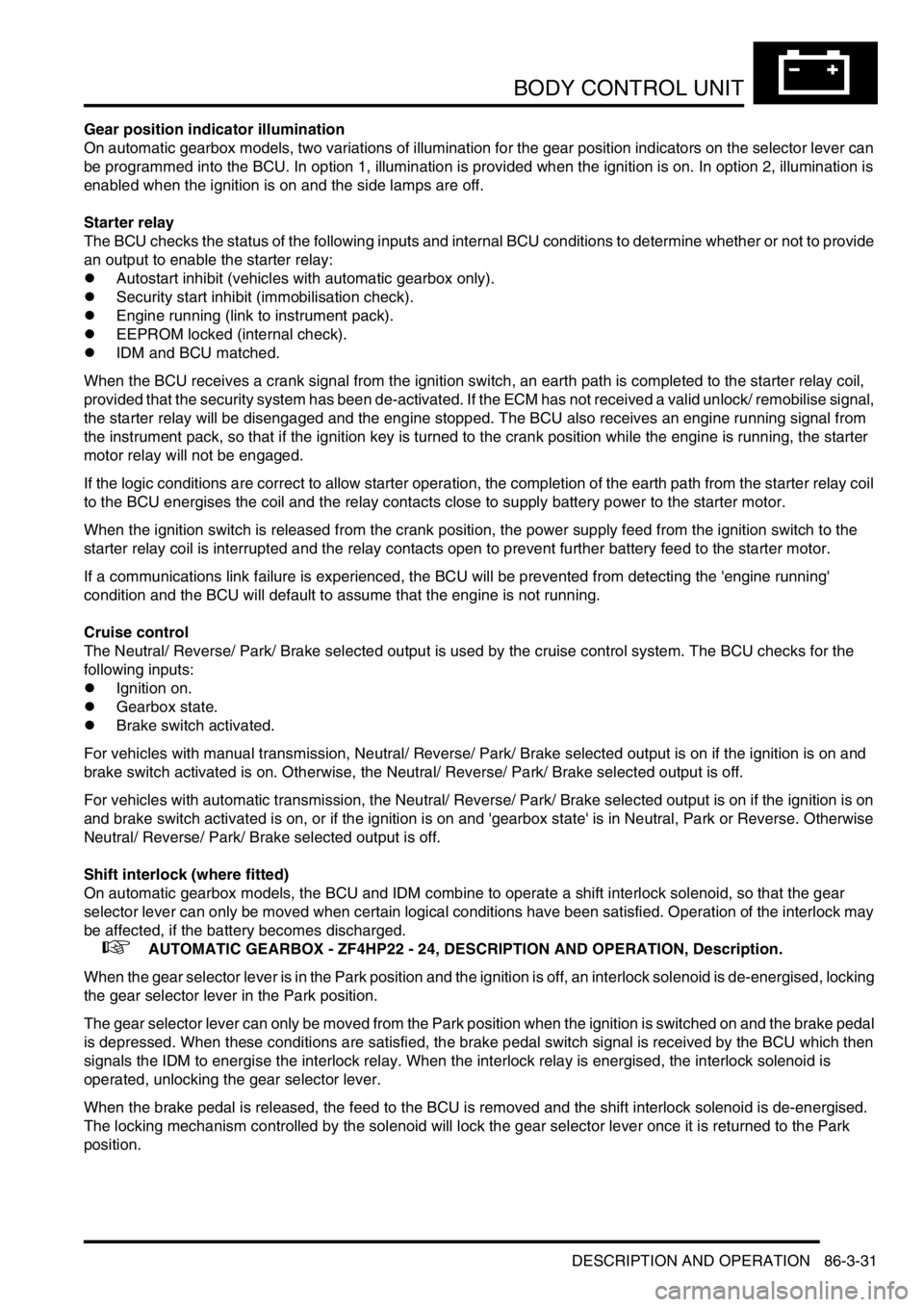
BODY CONTROL UNIT
DESCRIPTION AND OPERATION 86-3-31
Gear position indicator illumination
On automatic gearbox models, two variations of illumination for the gear position indicators on the selector lever can
be programmed into the BCU. In option 1, illumination is provided when the ignition is on. In option 2, illumination is
enabled when the ignition is on and the side lamps are off.
Starter relay
The BCU checks the status of the following inputs and internal BCU conditions to determine whether or not to provide
an output to enable the starter relay:
lAutostart inhibit (vehicles with automatic gearbox only).
lSecurity start inhibit (immobilisation check).
lEngine running (link to instrument pack).
lEEPROM locked (internal check).
lIDM and BCU matched.
When the BCU receives a crank signal from the ignition switch, an earth path is completed to the starter relay coil,
provided that the security system has been de-activated. If the ECM has not received a valid unlock/ remobilise signal,
the starter relay will be disengaged and the engine stopped. The BCU also receives an engine running signal from
the instrument pack, so that if the ignition key is turned to the crank position while the engine is running, the starter
motor relay will not be engaged.
If the logic conditions are correct to allow starter operation, the completion of the earth path from the starter relay coil
to the BCU energises the coil and the relay contacts close to supply battery power to the starter motor.
When the ignition switch is released from the crank position, the power supply feed from the ignition switch to the
starter relay coil is interrupted and the relay contacts open to prevent further battery feed to the starter motor.
If a communications link failure is experienced, the BCU will be prevented from detecting the 'engine running'
condition and the BCU will default to assume that the engine is not running.
Cruise control
The Neutral/ Reverse/ Park/ Brake selected output is used by the cruise control system. The BCU checks for the
following inputs:
lIgnition on.
lGearbox state.
lBrake switch activated.
For vehicles with manual transmission, Neutral/ Reverse/ Park/ Brake selected output is on if the ignition is on and
brake switch activated is on. Otherwise, the Neutral/ Reverse/ Park/ Brake selected output is off.
For vehicles with automatic transmission, the Neutral/ Reverse/ Park/ Brake selected output is on if the ignition is on
and brake switch activated is on, or if the ignition is on and 'gearbox state' is in Neutral, Park or Reverse. Otherwise
Neutral/ Reverse/ Park/ Brake selected output is off.
Shift interlock (where fitted)
On automatic gearbox models, the BCU and IDM combine to operate a shift interlock solenoid, so that the gear
selector lever can only be moved when certain logical conditions have been satisfied. Operation of the interlock may
be affected, if the battery becomes discharged.
+ AUTOMATIC GEARBOX - ZF4HP22 - 24, DESCRIPTION AND OPERATION, Description.
When the gear selector lever is in the Park position and the ignition is off, an interlock solenoid is de-energised, locking
the gear selector lever in the Park position.
The gear selector lever can only be moved from the Park position when the ignition is switched on and the brake pedal
is depressed. When these conditions are satisfied, the brake pedal switch signal is received by the BCU which then
signals the IDM to energise the interlock relay. When the interlock relay is energised, the interlock solenoid is
operated, unlocking the gear selector lever.
When the brake pedal is released, the feed to the BCU is removed and the shift interlock solenoid is de-energised.
The locking mechanism controlled by the solenoid will lock the gear selector lever once it is returned to the Park
position.
Page 1344 of 1529

ALARM SYSTEM AND HORN
DESCRIPTION AND OPERATION 86-4-21
Passive immobilisation
Passive immobilisation prevents the vehicle from being started unless the authorised key is used to start the vehicle.
There are only two configurations for passive immobilisation:
lpassive immobilisation not active
lpassive immobilisation active
When the ignition is switched off, the vehicle remains mobilised for up to a maximum of 5 minutes. If however the
driver's door is opened, after 2 minutes 30 seconds, the vehicle remains in a mobilised state for a further 30 seconds.
When the timer in the BCU has expired, the vehicle is immobilised.
Once the ignition is switched on, the BCU transmits a coded signal to the ECM. If the coded signal does not
correspond to the programmed code in the ECM, the ECM is inhibited and the BCU inhibits the starting circuit.
In order for passive immobilisation to occur, the following conditions must be met:
lDriver's door closed.
lFuel cut-off switch not tripped.
lKey not inserted in ignition.
Passive remobilisation
Whenever the vehicle is immobilised, passive remobilisation of the engine occurs when the ignition is switched on,
allowing the vehicle to be started.
There are three configurations for passive remobilisation:
lPassive immobilisation not active.
lPassive immobilisation active.
lEKA with super locking on receiving good passive remobilisation exciter coil signal.
The BCU controls the passive remobilisation exciter coil (located around the ignition barrel) to generate a magnetic
field which causes the handset to transmit a remobilisation signal. The BCU receives the signal and allows the vehicle
to be started. If a valid signal from the handset is not received within one minute of the ignition being switched to
position II, the BCU stops the passive coil from generating the magnetic field.
Emergency key access
If the handset fails to operate, the engine can be remobilised by using the key to enter a unique four digit Emergency
Key Access (EKA) code.
There are three configurations for emergency key access:
lEKA not active (no immobiliser fitted).
lEKA active.
lEKA with super locking on receiving good passive remobilisation exciter coil signal.