load capacity LAND ROVER DISCOVERY 2002 Workshop Manual
[x] Cancel search | Manufacturer: LAND ROVER, Model Year: 2002, Model line: DISCOVERY, Model: LAND ROVER DISCOVERY 2002Pages: 1672, PDF Size: 46.1 MB
Page 37 of 1672
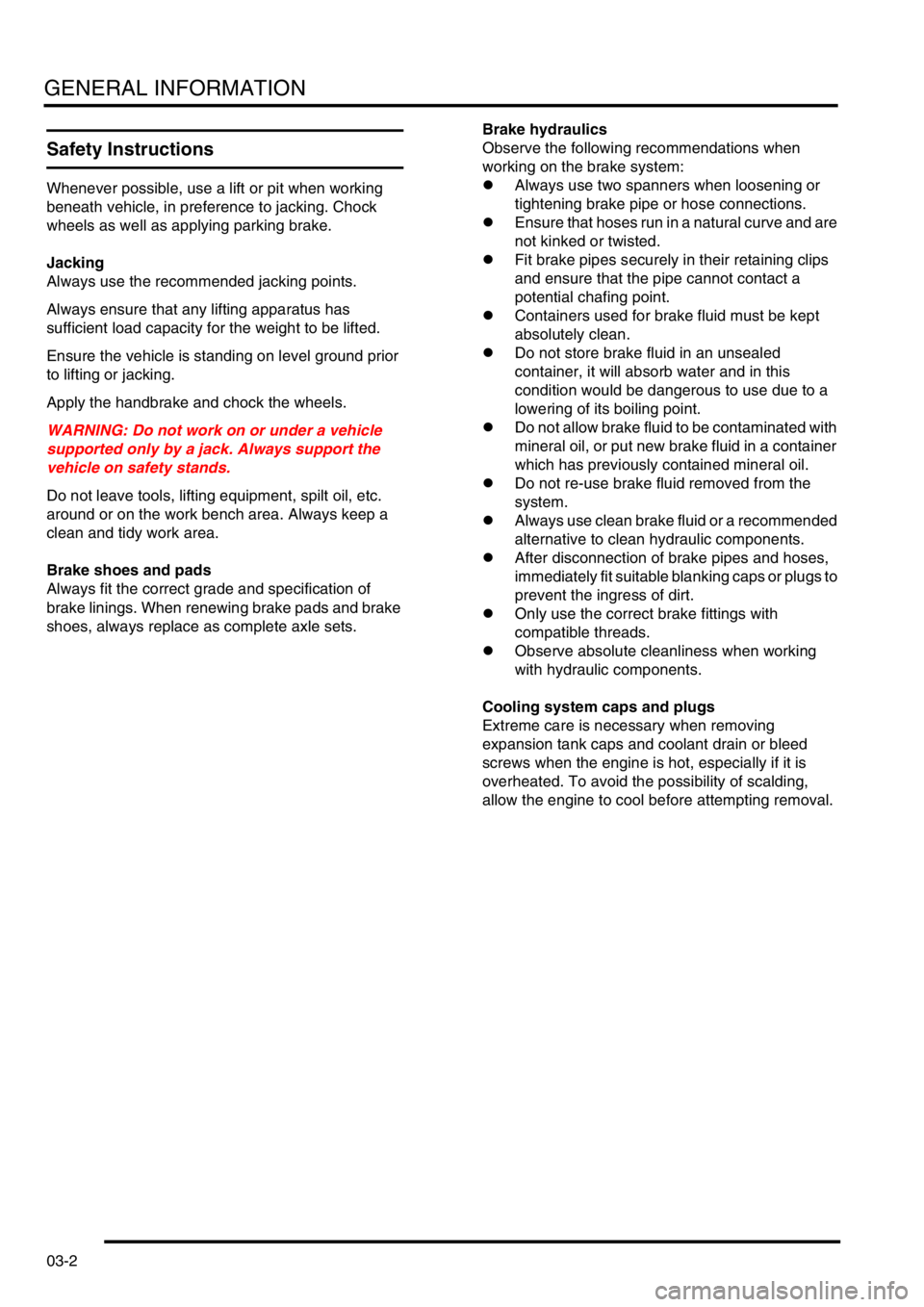
GENERAL INFORMATION
03-2
Safety Instructions
Whenever possible, use a lift or pit when working
beneath vehicle, in preference to jacking. Chock
wheels as well as applying parking brake.
Jacking
Always use the recommended jacking points.
Always ensure that any lifting apparatus has
sufficient load capacity for the weight to be lifted.
Ensure the vehicle is standing on level ground prior
to lifting or jacking.
Apply the handbrake and chock the wheels.
WARNING: Do not work on or under a vehicle
supported only by a jack. Always support the
vehicle on safety stands.
Do not leave tools, lifting equipment, spilt oil, etc.
around or on the work bench area. Always keep a
clean and tidy work area.
Brake shoes and pads
Always fit the correct grade and specification of
brake linings. When renewing brake pads and brake
shoes, always replace as complete axle sets.Brake hydraulics
Observe the following recommendations when
working on the brake system:
lAlways use two spanners when loosening or
tightening brake pipe or hose connections.
lEnsure that hoses run in a natural curve and are
not kinked or twisted.
lFit brake pipes securely in their retaining clips
and ensure that the pipe cannot contact a
potential chafing point.
lContainers used for brake fluid must be kept
absolutely clean.
lDo not store brake fluid in an unsealed
container, it will absorb water and in this
condition would be dangerous to use due to a
lowering of its boiling point.
lDo not allow brake fluid to be contaminated with
mineral oil, or put new brake fluid in a container
which has previously contained mineral oil.
lDo not re-use brake fluid removed from the
system.
lAlways use clean brake fluid or a recommended
alternative to clean hydraulic components.
lAfter disconnection of brake pipes and hoses,
immediately fit suitable blanking caps or plugs to
prevent the ingress of dirt.
lOnly use the correct brake fittings with
compatible threads.
lObserve absolute cleanliness when working
with hydraulic components.
Cooling system caps and plugs
Extreme care is necessary when removing
expansion tank caps and coolant drain or bleed
screws when the engine is hot, especially if it is
overheated. To avoid the possibility of scalding,
allow the engine to cool before attempting removal.
Page 102 of 1672
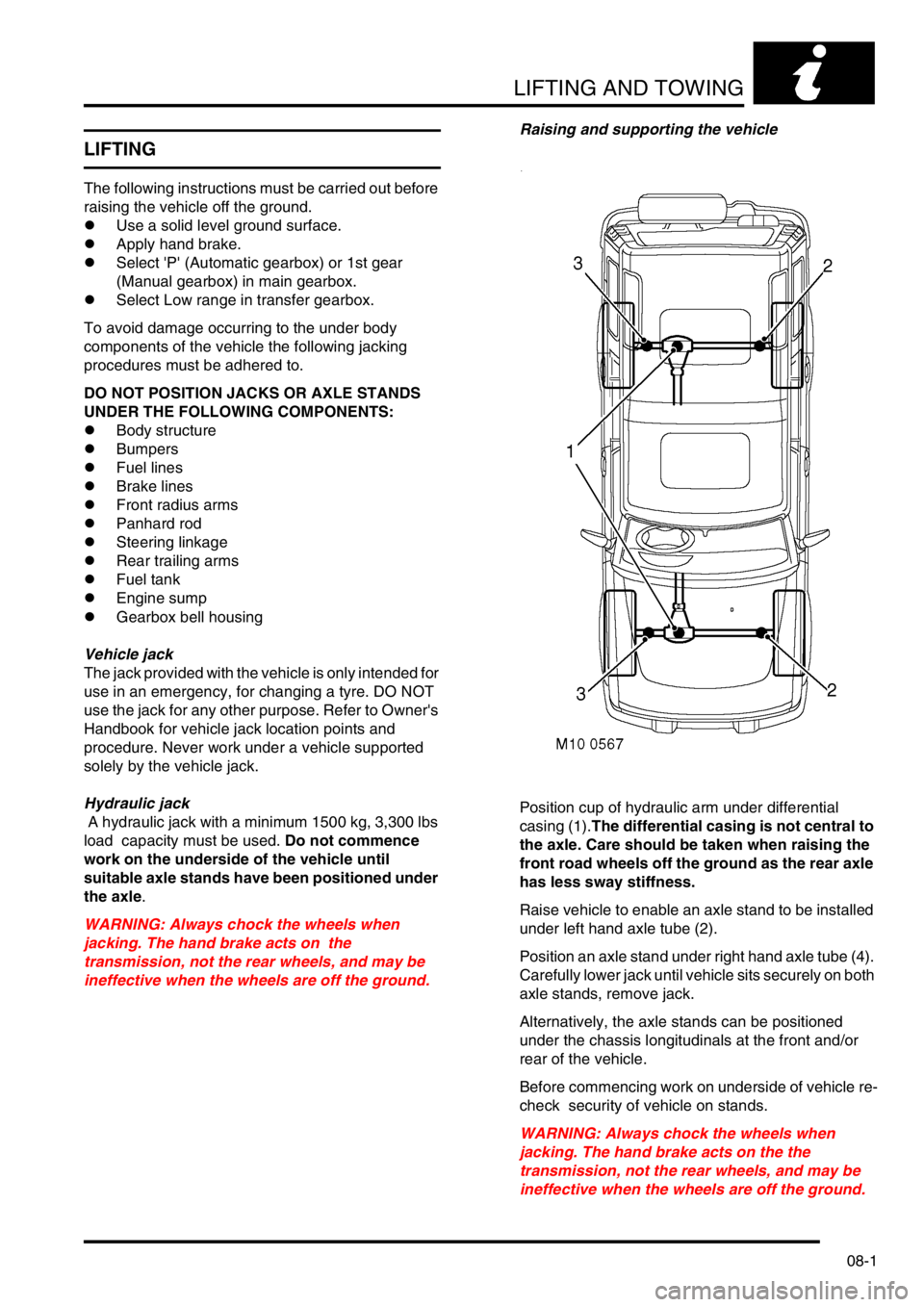
LIFTING AND TOWING
08-1
LIFTING AND TOWING
LIFTING
The following instructions must be carried out before
raising the vehicle off the ground.
lUse a solid level ground surface.
lApply hand brake.
lSelect 'P' (Automatic gearbox) or 1st gear
(Manual gearbox) in main gearbox.
lSelect Low range in transfer gearbox.
To avoid damage occurring to the under body
components of the vehicle the following jacking
procedures must be adhered to.
DO NOT POSITION JACKS OR AXLE STANDS
UNDER THE FOLLOWING COMPONENTS:
lBody structure
lBumpers
lFuel lines
lBrake lines
lFront radius arms
lPanhard rod
lSteering linkage
lRear trailing arms
lFuel tank
lEngine sump
lGearbox bell housing
Vehicle jack
The jack provided with the vehicle is only intended for
use in an emergency, for changing a tyre. DO NOT
use the jack for any other purpose. Refer to Owner's
Handbook for vehicle jack location points and
procedure. Never work under a vehicle supported
solely by the vehicle jack.
Hydraulic jack
A hydraulic jack with a minimum 1500 kg, 3,300 lbs
load capacity must be used. Do not commence
work on the underside of the vehicle until
suitable axle stands have been positioned under
the axle.
WARNING: Always chock the wheels when
jacking. The hand brake acts on the
transmission, not the rear wheels, and may be
ineffective when the wheels are off the ground.Raising and supporting the vehicle
Position cup of hydraulic arm under differential
casing (1).The differential casing is not central to
the axle. Care should be taken when raising the
front road wheels off the ground as the rear axle
has less sway stiffness.
Raise vehicle to enable an axle stand to be installed
under left hand axle tube (2).
Position an axle stand under right hand axle tube (4).
Carefully lower jack until vehicle sits securely on both
axle stands, remove jack.
Alternatively, the axle stands can be positioned
under the chassis longitudinals at the front and/or
rear of the vehicle.
Before commencing work on underside of vehicle re-
check security of vehicle on stands.
WARNING: Always chock the wheels when
jacking. The hand brake acts on the the
transmission, not the rear wheels, and may be
ineffective when the wheels are off the ground.
Page 570 of 1672
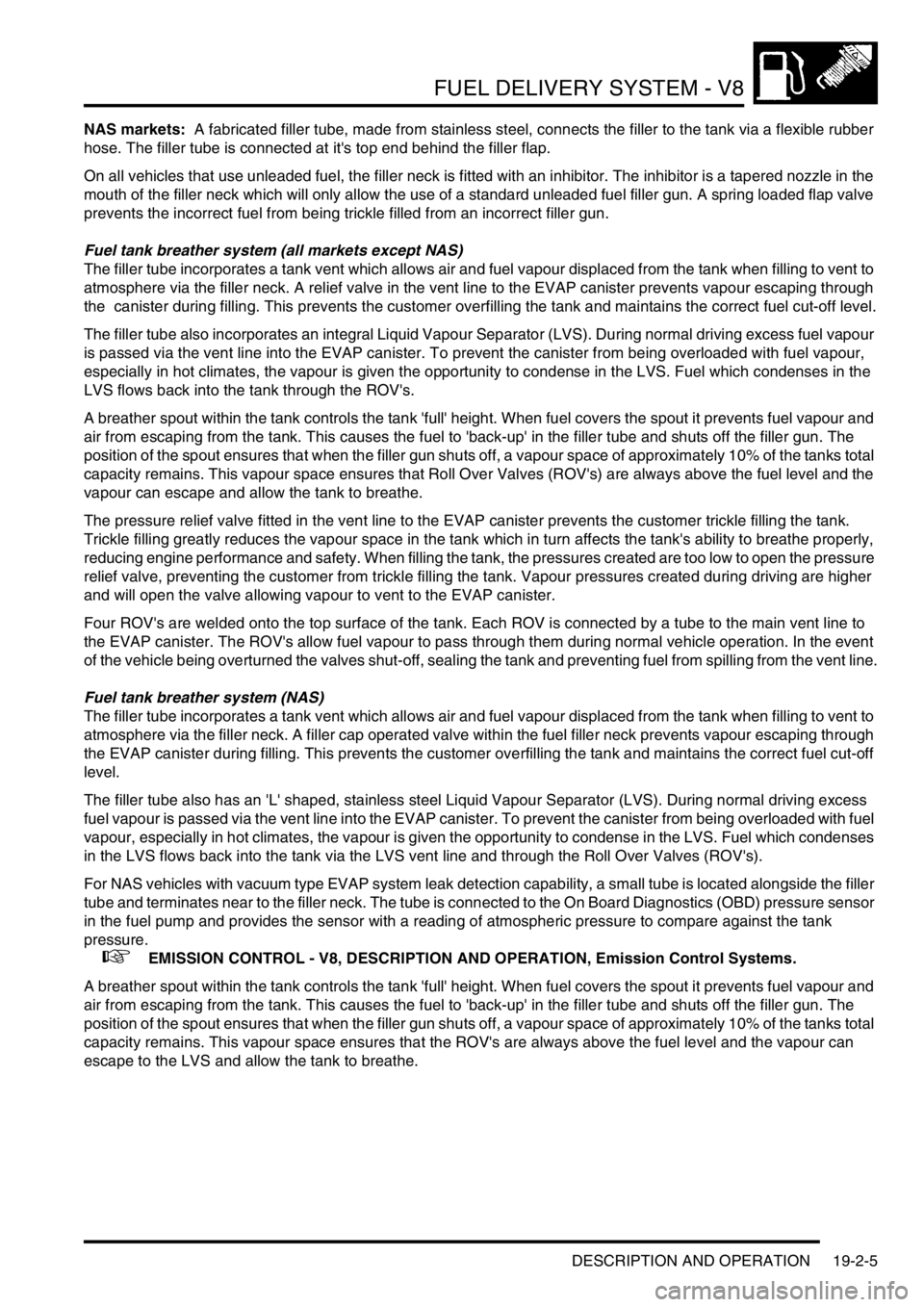
FUEL DELIVERY SYSTEM - V8
DESCRIPTION AND OPERATION 19-2-5
NAS markets: A fabricated filler tube, made from stainless steel, connects the filler to the tank via a flexible rubber
hose. The filler tube is connected at it's top end behind the filler flap.
On all vehicles that use unleaded fuel, the filler neck is fitted with an inhibitor. The inhibitor is a tapered nozzle in the
mouth of the filler neck which will only allow the use of a standard unleaded fuel filler gun. A spring loaded flap valve
prevents the incorrect fuel from being trickle filled from an incorrect filler gun.
Fuel tank breather system (all markets except NAS)
The filler tube incorporates a tank vent which allows air and fuel vapour displaced from the tank when filling to vent to
atmosphere via the filler neck. A relief valve in the vent line to the EVAP canister prevents vapour escaping through
the canister during filling. This prevents the customer overfilling the tank and maintains the correct fuel cut-off level.
The filler tube also incorporates an integral Liquid Vapour Separator (LVS). During normal driving excess fuel vapour
is passed via the vent line into the EVAP canister. To prevent the canister from being overloaded with fuel vapour,
especially in hot climates, the vapour is given the opportunity to condense in the LVS. Fuel which condenses in the
LVS flows back into the tank through the ROV's.
A breather spout within the tank controls the tank 'full' height. When fuel covers the spout it prevents fuel vapour and
air from escaping from the tank. This causes the fuel to 'back-up' in the filler tube and shuts off the filler gun. The
position of the spout ensures that when the filler gun shuts off, a vapour space of approximately 10% of the tanks total
capacity remains. This vapour space ensures that Roll Over Valves (ROV's) are always above the fuel level and the
vapour can escape and allow the tank to breathe.
The pressure relief valve fitted in the vent line to the EVAP canister prevents the customer trickle filling the tank.
Trickle filling greatly reduces the vapour space in the tank which in turn affects the tank's ability to breathe properly,
reducing engine performance and safety. When filling the tank, the pressures created are too low to open the pressure
relief valve, preventing the customer from trickle filling the tank. Vapour pressures created during driving are higher
and will open the valve allowing vapour to vent to the EVAP canister.
Four ROV's are welded onto the top surface of the tank. Each ROV is connected by a tube to the main vent line to
the EVAP canister. The ROV's allow fuel vapour to pass through them during normal vehicle operation. In the event
of the vehicle being overturned the valves shut-off, sealing the tank and preventing fuel from spilling from the vent line.
Fuel tank breather system (NAS)
The filler tube incorporates a tank vent which allows air and fuel vapour displaced from the tank when filling to vent to
atmosphere via the filler neck. A filler cap operated valve within the fuel filler neck prevents vapour escaping through
the EVAP canister during filling. This prevents the customer overfilling the tank and maintains the correct fuel cut-off
level.
The filler tube also has an 'L' shaped, stainless steel Liquid Vapour Separator (LVS). During normal driving excess
fuel vapour is passed via the vent line into the EVAP canister. To prevent the canister from being overloaded with fuel
vapour, especially in hot climates, the vapour is given the opportunity to condense in the LVS. Fuel which condenses
in the LVS flows back into the tank via the LVS vent line and through the Roll Over Valves (ROV's).
For NAS vehicles with vacuum type EVAP system leak detection capability, a small tube is located alongside the filler
tube and terminates near to the filler neck. The tube is connected to the On Board Diagnostics (OBD) pressure sensor
in the fuel pump and provides the sensor with a reading of atmospheric pressure to compare against the tank
pressure.
+ EMISSION CONTROL - V8, DESCRIPTION AND OPERATION, Emission Control Systems.
A breather spout within the tank controls the tank 'full' height. When fuel covers the spout it prevents fuel vapour and
air from escaping from the tank. This causes the fuel to 'back-up' in the filler tube and shuts off the filler gun. The
position of the spout ensures that when the filler gun shuts off, a vapour space of approximately 10% of the tanks total
capacity remains. This vapour space ensures that the ROV's are always above the fuel level and the vapour can
escape to the LVS and allow the tank to breathe.
Page 746 of 1672
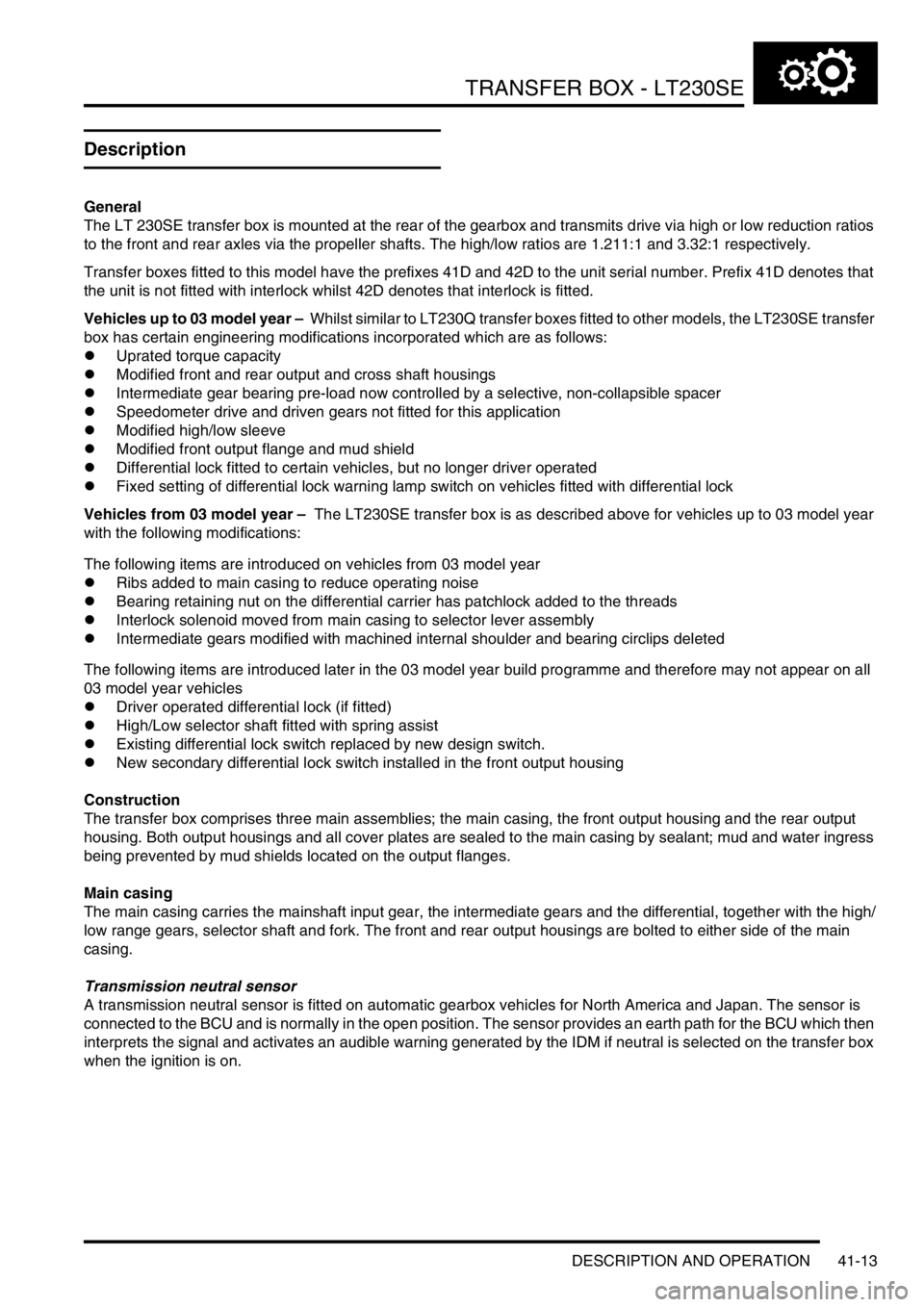
TRANSFER BOX - LT230SE
DESCRIPTION AND OPERATION 41-13
Description
General
The LT 230SE transfer box is mounted at the rear of the gearbox and transmits drive via high or low reduction ratios
to the front and rear axles via the propeller shafts. The high/low ratios are 1.211:1 and 3.32:1 respectively.
Transfer boxes fitted to this model have the prefixes 41D and 42D to the unit serial number. Prefix 41D denotes that
the unit is not fitted with interlock whilst 42D denotes that interlock is fitted.
Vehicles up to 03 model year – Whilst similar to LT230Q transfer boxes fitted to other models, the LT230SE transfer
box has certain engineering modifications incorporated which are as follows:
lUprated torque capacity
lModified front and rear output and cross shaft housings
lIntermediate gear bearing pre-load now controlled by a selective, non-collapsible spacer
lSpeedometer drive and driven gears not fitted for this application
lModified high/low sleeve
lModified front output flange and mud shield
lDifferential lock fitted to certain vehicles, but no longer driver operated
lFixed setting of differential lock warning lamp switch on vehicles fitted with differential lock
Vehicles from 03 model year – The LT230SE transfer box is as described above for vehicles up to 03 model year
with the following modifications:
The following items are introduced on vehicles from 03 model year
lRibs added to main casing to reduce operating noise
lBearing retaining nut on the differential carrier has patchlock added to the threads
lInterlock solenoid moved from main casing to selector lever assembly
lIntermediate gears modified with machined internal shoulder and bearing circlips deleted
The following items are introduced later in the 03 model year build programme and therefore may not appear on all
03 model year vehicles
lDriver operated differential lock (if fitted)
lHigh/Low selector shaft fitted with spring assist
lExisting differential lock switch replaced by new design switch.
lNew secondary differential lock switch installed in the front output housing
Construction
The transfer box comprises three main assemblies; the main casing, the front output housing and the rear output
housing. Both output housings and all cover plates are sealed to the main casing by sealant; mud and water ingress
being prevented by mud shields located on the output flanges.
Main casing
The main casing carries the mainshaft input gear, the intermediate gears and the differential, together with the high/
low range gears, selector shaft and fork. The front and rear output housings are bolted to either side of the main
casing.
Transmission neutral sensor
A transmission neutral sensor is fitted on automatic gearbox vehicles for North America and Japan. The sensor is
connected to the BCU and is normally in the open position. The sensor provides an earth path for the BCU which then
interprets the signal and activates an audible warning generated by the IDM if neutral is selected on the transfer box
when the ignition is on.