transmission LAND ROVER DISCOVERY 2002 Workshop Manual
[x] Cancel search | Manufacturer: LAND ROVER, Model Year: 2002, Model line: DISCOVERY, Model: LAND ROVER DISCOVERY 2002Pages: 1672, PDF Size: 46.1 MB
Page 16 of 1672
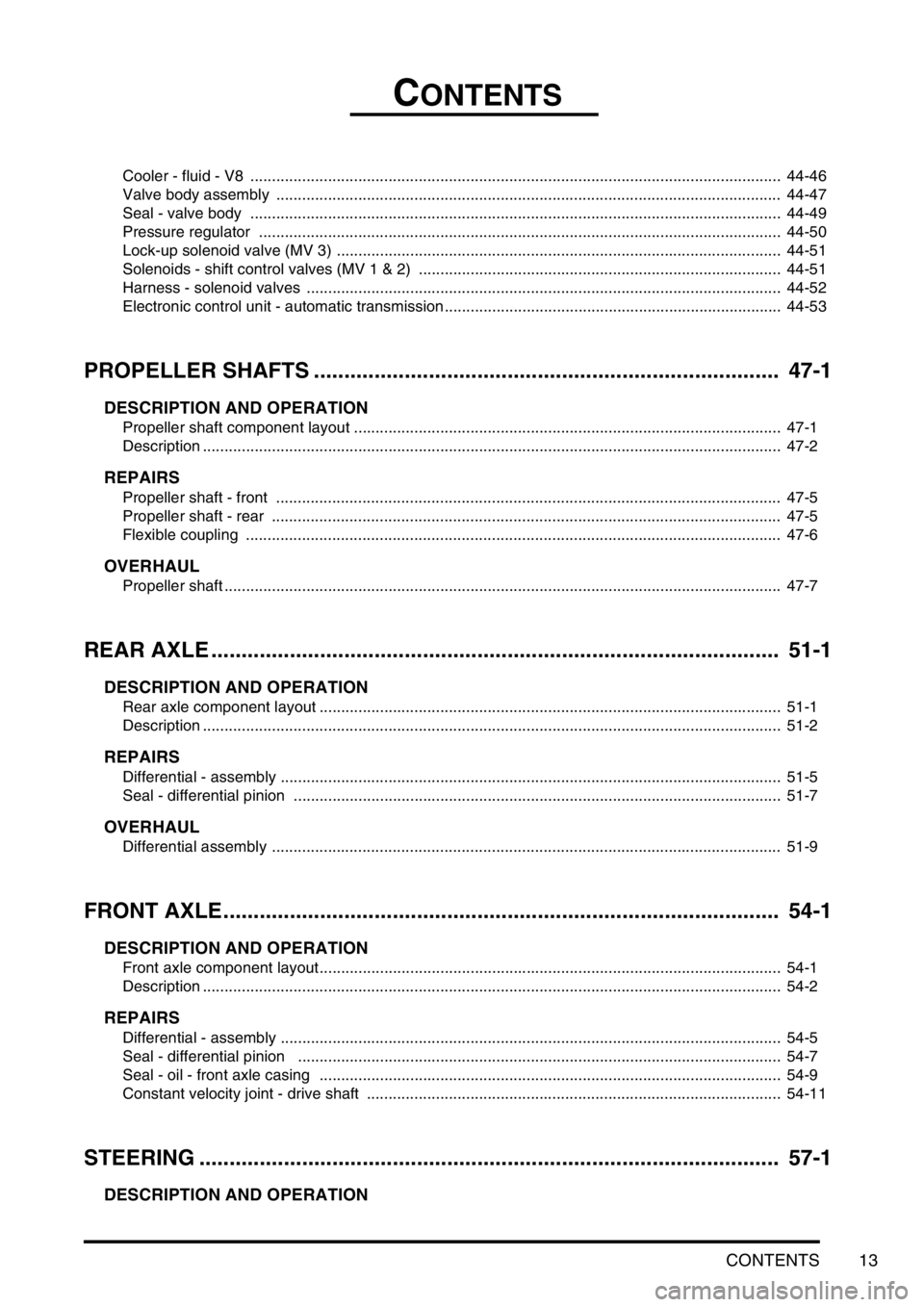
CONTENTS
CONTENTS 13
Cooler - fluid - V8 ........................................................................................................................... 44-46
Valve body assembly ..................................................................................................................... 44-47
Seal - valve body ........................................................................................................................... 44-49
Pressure regulator ......................................................................................................................... 44-50
Lock-up solenoid valve (MV 3) ....................................................................................................... 44-51
Solenoids - shift control valves (MV 1 & 2) .................................................................................... 44-51
Harness - solenoid valves .............................................................................................................. 44-52
Electronic control unit - automatic transmission .............................................................................. 44-53
PROPELLER SHAFTS ............................................................................. 47-1
DESCRIPTION AND OPERATION
Propeller shaft component layout ................................................................................................... 47-1
Description ...................................................................................................................................... 47-2
REPAIRS
Propeller shaft - front ..................................................................................................................... 47-5
Propeller shaft - rear ...................................................................................................................... 47-5
Flexible coupling ............................................................................................................................ 47-6
OVERHAUL
Propeller shaft ................................................................................................................................. 47-7
REAR AXLE .............................................................................................. 51-1
DESCRIPTION AND OPERATION
Rear axle component layout ........................................................................................................... 51-1
Description ...................................................................................................................................... 51-2
REPAIRS
Differential - assembly .................................................................................................................... 51-5
Seal - differential pinion ................................................................................................................. 51-7
OVERHAUL
Differential assembly ...................................................................................................................... 51-9
FRONT AXLE............................................................................................ 54-1
DESCRIPTION AND OPERATION
Front axle component layout........................................................................................................... 54-1
Description ...................................................................................................................................... 54-2
REPAIRS
Differential - assembly .................................................................................................................... 54-5
Seal - differential pinion ................................................................................................................ 54-7
Seal - oil - front axle casing ........................................................................................................... 54-9
Constant velocity joint - drive shaft ................................................................................................ 54-11
STEERING ................................................................................................ 57-1
DESCRIPTION AND OPERATION
Page 32 of 1672
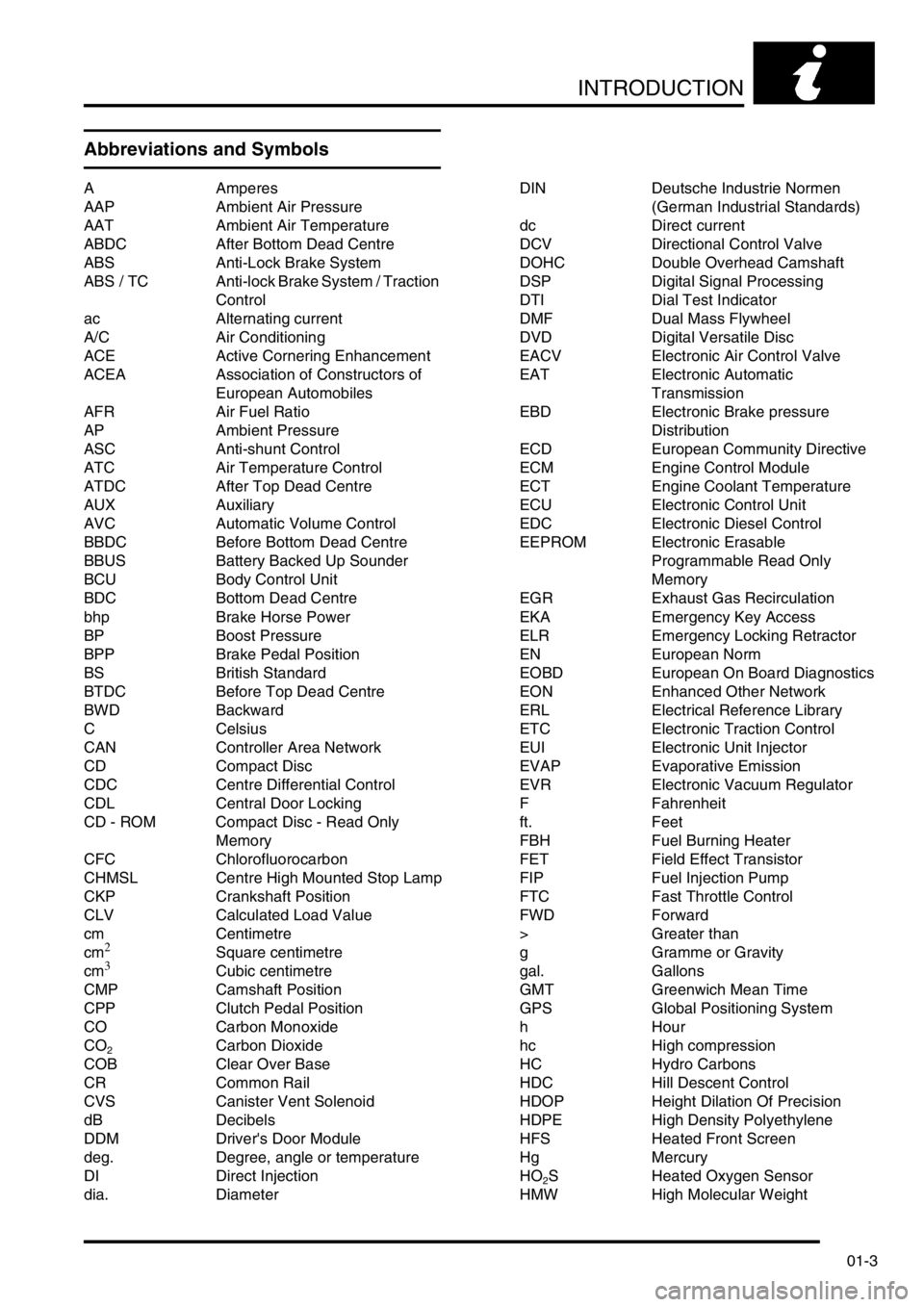
INTRODUCTION
01-3
Abbreviations and Symbols
A Amperes
AAP Ambient Air Pressure
AAT Ambient Air Temperature
ABDC After Bottom Dead Centre
ABS Anti-Lock Brake System
ABS / TC Anti-lock Brake System / Traction
Control
ac Alternating current
A/C Air Conditioning
ACE Active Cornering Enhancement
ACEA Association of Constructors of
European Automobiles
AFR Air Fuel Ratio
AP Ambient Pressure
ASC Anti-shunt Control
ATC Air Temperature Control
ATDC After Top Dead Centre
AUX Auxiliary
AVC Automatic Volume Control
BBDC Before Bottom Dead Centre
BBUS Battery Backed Up Sounder
BCU Body Control Unit
BDC Bottom Dead Centre
bhp Brake Horse Power
BP Boost Pressure
BPP Brake Pedal Position
BS British Standard
BTDC Before Top Dead Centre
BWD Backward
C Celsius
CAN Controller Area Network
CD Compact Disc
CDC Centre Differential Control
CDL Central Door Locking
CD - ROM Compact Disc - Read Only
Memory
CFC Chlorofluorocarbon
CHMSL Centre High Mounted Stop Lamp
CKP Crankshaft Position
CLV Calculated Load Value
cm Centimetre
cm
2Square centimetre
cm3Cubic centimetre
CMP Camshaft Position
CPP Clutch Pedal Position
CO Carbon Monoxide
CO
2Carbon Dioxide
COB Clear Over Base
CR Common Rail
CVS Canister Vent Solenoid
dB Decibels
DDM Driver's Door Module
deg. Degree, angle or temperature
DI Direct Injection
dia. DiameterDIN Deutsche Industrie Normen
(German Industrial Standards)
dc Direct current
DCV Directional Control Valve
DOHC Double Overhead Camshaft
DSP Digital Signal Processing
DTI Dial Test Indicator
DMF Dual Mass Flywheel
DVD Digital Versatile Disc
EACV Electronic Air Control Valve
EAT Electronic Automatic
Transmission
EBD Electronic Brake pressure
Distribution
ECD European Community Directive
ECM Engine Control Module
ECT Engine Coolant Temperature
ECU Electronic Control Unit
EDC Electronic Diesel Control
EEPROM Electronic Erasable
Programmable Read Only
Memory
EGR Exhaust Gas Recirculation
EKA Emergency Key Access
ELR Emergency Locking Retractor
EN European Norm
EOBD European On Board Diagnostics
EON Enhanced Other Network
ERL Electrical Reference Library
ETC Electronic Traction Control
EUI Electronic Unit Injector
EVAP Evaporative Emission
EVR Electronic Vacuum Regulator
F Fahrenheit
ft. Feet
FBH Fuel Burning Heater
FET Field Effect Transistor
FIP Fuel Injection Pump
FTC Fast Throttle Control
FWD Forward
> Greater than
g Gramme or Gravity
gal. Gallons
GMT Greenwich Mean Time
GPS Global Positioning System
hHour
hc High compression
HC Hydro Carbons
HDC Hill Descent Control
HDOP Height Dilation Of Precision
HDPE High Density Polyethylene
HFS Heated Front Screen
Hg Mercury
HO
2S Heated Oxygen Sensor
HMW High Molecular Weight
Page 62 of 1672
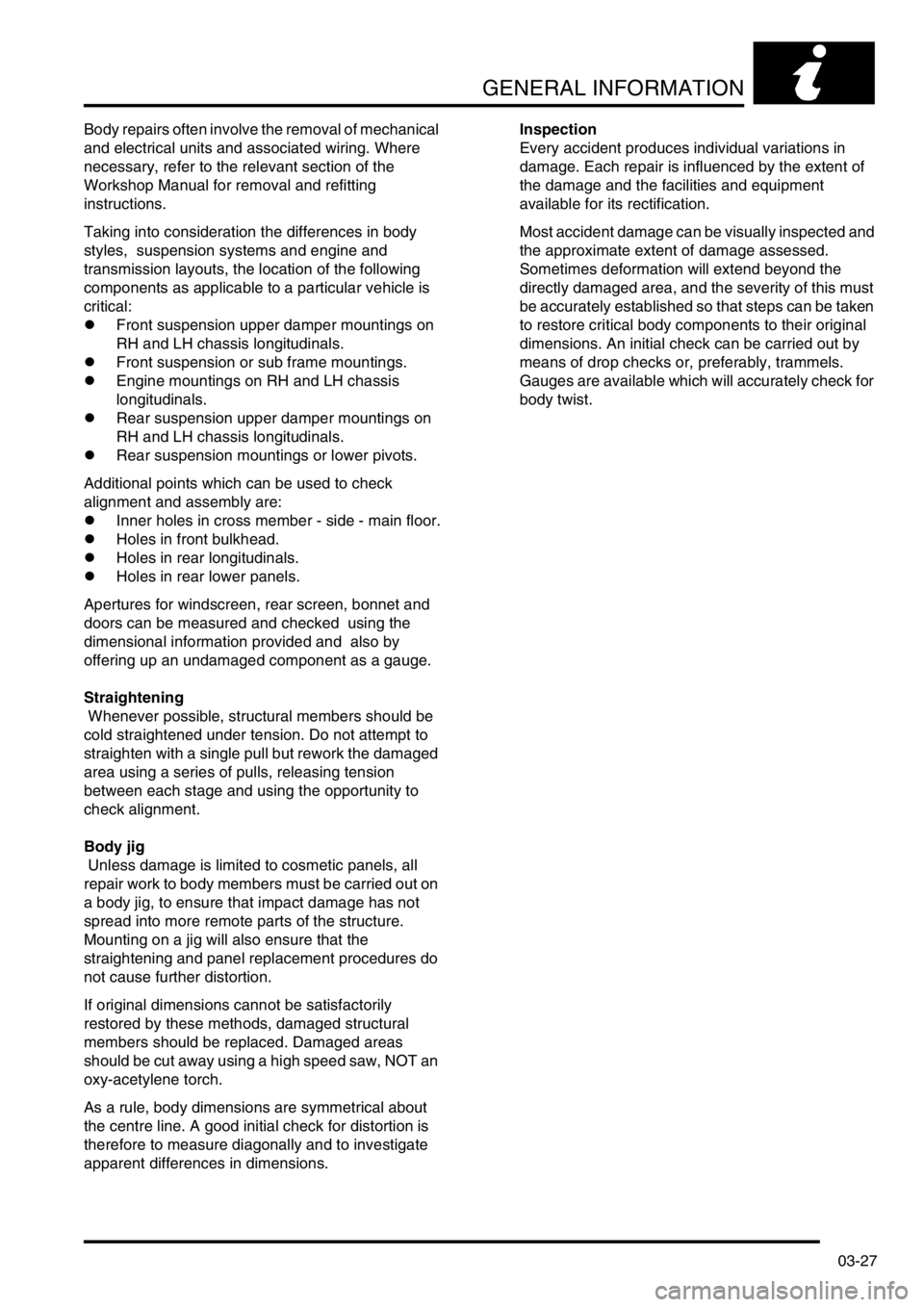
GENERAL INFORMATION
03-27
Body repairs often involve the removal of mechanical
and electrical units and associated wiring. Where
necessary, refer to the relevant section of the
Workshop Manual for removal and refitting
instructions.
Taking into consideration the differences in body
styles, suspension systems and engine and
transmission layouts, the location of the following
components as applicable to a particular vehicle is
critical:
lFront suspension upper damper mountings on
RH and LH chassis longitudinals.
lFront suspension or sub frame mountings.
lEngine mountings on RH and LH chassis
longitudinals.
lRear suspension upper damper mountings on
RH and LH chassis longitudinals.
lRear suspension mountings or lower pivots.
Additional points which can be used to check
alignment and assembly are:
lInner holes in cross member - side - main floor.
lHoles in front bulkhead.
lHoles in rear longitudinals.
lHoles in rear lower panels.
Apertures for windscreen, rear screen, bonnet and
doors can be measured and checked using the
dimensional information provided and also by
offering up an undamaged component as a gauge.
Straightening
Whenever possible, structural members should be
cold straightened under tension. Do not attempt to
straighten with a single pull but rework the damaged
area using a series of pulls, releasing tension
between each stage and using the opportunity to
check alignment.
Body jig
Unless damage is limited to cosmetic panels, all
repair work to body members must be carried out on
a body jig, to ensure that impact damage has not
spread into more remote parts of the structure.
Mounting on a jig will also ensure that the
straightening and panel replacement procedures do
not cause further distortion.
If original dimensions cannot be satisfactorily
restored by these methods, damaged structural
members should be replaced. Damaged areas
should be cut away using a high speed saw, NOT an
oxy-acetylene torch.
As a rule, body dimensions are symmetrical about
the centre line. A good initial check for distortion is
therefore to measure diagonally and to investigate
apparent differences in dimensions.Inspection
Every accident produces individual variations in
damage. Each repair is influenced by the extent of
the damage and the facilities and equipment
available for its rectification.
Most accident damage can be visually inspected and
the approximate extent of damage assessed.
Sometimes deformation will extend beyond the
directly damaged area, and the severity of this must
be accurately established so that steps can be taken
to restore critical body components to their original
dimensions. An initial check can be carried out by
means of drop checks or, preferably, trammels.
Gauges are available which will accurately check for
body twist.
Page 83 of 1672
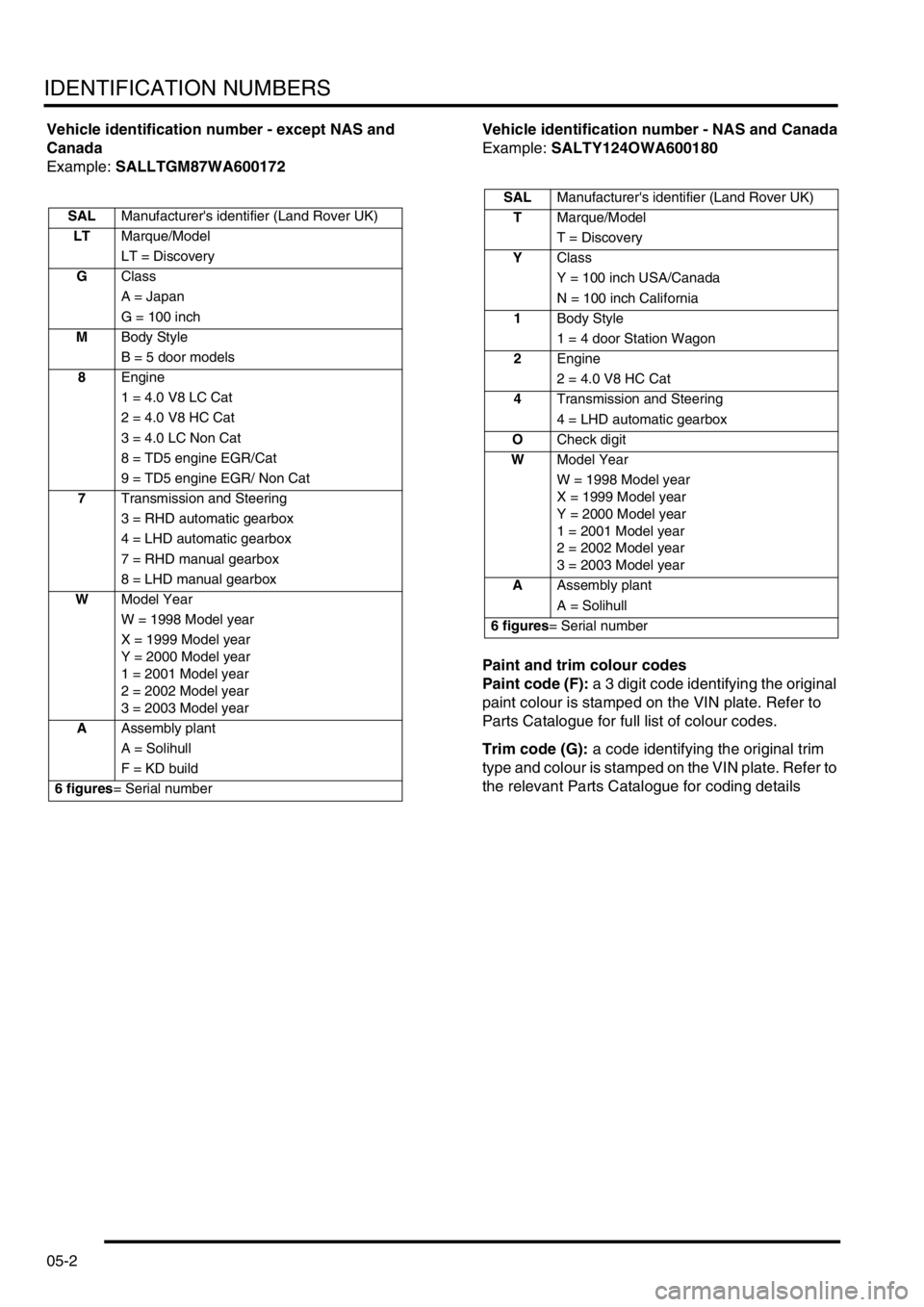
IDENTIFICATION NUMBERS
05-2
Vehicle identification number - except NAS and
Canada
Example: SALLTGM87WA600172Vehicle identification number - NAS and Canada
Example: SALTY124OWA600180
Paint and trim colour codes
Paint code (F): a 3 digit code identifying the original
paint colour is stamped on the VIN plate. Refer to
Parts Catalogue for full list of colour codes.
Trim code (G): a code identifying the original trim
type and colour is stamped on the VIN plate. Refer to
the relevant Parts Catalogue for coding details
SALManufacturer's identifier (Land Rover UK)
LTMarque/Model
LT = Discovery
GClass
A = Japan
G = 100 inch
MBody Style
B = 5 door models
8Engine
1 = 4.0 V8 LC Cat
2 = 4.0 V8 HC Cat
3 = 4.0 LC Non Cat
8 = TD5 engine EGR/Cat
9 = TD5 engine EGR/ Non Cat
7Transmission and Steering
3 = RHD automatic gearbox
4 = LHD automatic gearbox
7 = RHD manual gearbox
8 = LHD manual gearbox
WModel Year
W = 1998 Model year
X = 1999 Model year
Y = 2000 Model year
1 = 2001 Model year
2 = 2002 Model year
3 = 2003 Model year
AAssembly plant
A = Solihull
F = KD build
6 figures= Serial number
SALManufacturer's identifier (Land Rover UK)
TMarque/Model
T = Discovery
YClass
Y = 100 inch USA/Canada
N = 100 inch California
1Body Style
1 = 4 door Station Wagon
2Engine
2 = 4.0 V8 HC Cat
4Transmission and Steering
4 = LHD automatic gearbox
OCheck digit
WModel Year
W = 1998 Model year
X = 1999 Model year
Y = 2000 Model year
1 = 2001 Model year
2 = 2002 Model year
3 = 2003 Model year
AAssembly plant
A = Solihull
6 figures= Serial number
Page 87 of 1672
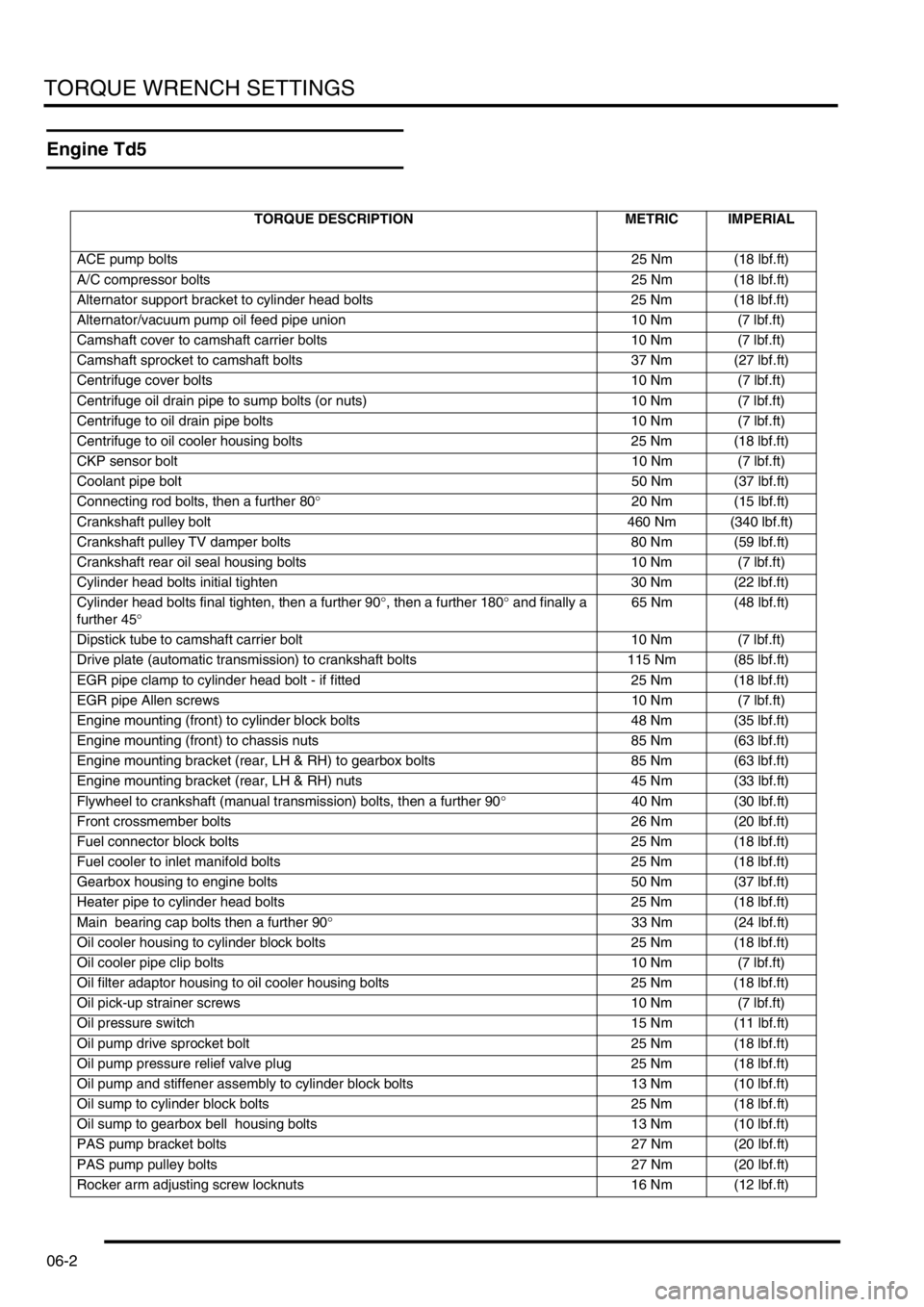
TORQUE WRENCH SETTINGS
06-2
Engine Td5
TORQUE DESCRIPTION METRIC IMPERIAL
ACE pump bolts25 Nm (18 lbf.ft)
A/C compressor bolts 25 Nm (18 lbf.ft)
Alternator support bracket to cylinder head bolts 25 Nm (18 lbf.ft)
Alternator/vacuum pump oil feed pipe union 10 Nm (7 lbf.ft)
Camshaft cover to camshaft carrier bolts 10 Nm (7 lbf.ft)
Camshaft sprocket to camshaft bolts 37 Nm (27 lbf.ft)
Centrifuge cover bolts 10 Nm (7 lbf.ft)
Centrifuge oil drain pipe to sump bolts (or nuts) 10 Nm (7 lbf.ft)
Centrifuge to oil drain pipe bolts 10 Nm (7 lbf.ft)
Centrifuge to oil cooler housing bolts 25 Nm (18 lbf.ft)
CKP sensor bolt10 Nm (7 lbf.ft)
Coolant pipe bolt50 Nm (37 lbf.ft)
Connecting rod bolts, then a further 80°20 Nm (15 lbf.ft)
Crankshaft pulley bolt 460 Nm (340 lbf.ft)
Crankshaft pulley TV damper bolts 80 Nm (59 lbf.ft)
Crankshaft rear oil seal housing bolts 10 Nm (7 lbf.ft)
Cylinder head bolts initial tighten 30 Nm (22 lbf.ft)
Cylinder head bolts final tighten, then a further 90°, then a further 180° and finally a
further 45°65 Nm (48 lbf.ft)
Dipstick tube to camshaft carrier bolt 10 Nm (7 lbf.ft)
Drive plate (automatic transmission) to crankshaft bolts 115 Nm (85 lbf.ft)
EGR pipe clamp to cylinder head bolt - if fitted 25 Nm (18 lbf.ft)
EGR pipe Allen screws 10 Nm (7 lbf.ft)
Engine mounting (front) to cylinder block bolts 48 Nm (35 lbf.ft)
Engine mounting (front) to chassis nuts 85 Nm (63 lbf.ft)
Engine mounting bracket (rear, LH & RH) to gearbox bolts 85 Nm (63 lbf.ft)
Engine mounting bracket (rear, LH & RH) nuts 45 Nm (33 lbf.ft)
Flywheel to crankshaft (manual transmission) bolts, then a further 90°40 Nm (30 lbf.ft)
Front crossmember bolts 26 Nm (20 lbf.ft)
Fuel connector block bolts 25 Nm (18 lbf.ft)
Fuel cooler to inlet manifold bolts 25 Nm (18 lbf.ft)
Gearbox housing to engine bolts 50 Nm (37 lbf.ft)
Heater pipe to cylinder head bolts 25 Nm (18 lbf.ft)
Main bearing cap bolts then a further 90°33 Nm (24 lbf.ft)
Oil cooler housing to cylinder block bolts 25 Nm (18 lbf.ft)
Oil cooler pipe clip bolts 10 Nm (7 lbf.ft)
Oil filter adaptor housing to oil cooler housing bolts 25 Nm (18 lbf.ft)
Oil pick-up strainer screws 10 Nm (7 lbf.ft)
Oil pressure switch 15 Nm (11 lbf.ft)
Oil pump drive sprocket bolt 25 Nm (18 lbf.ft)
Oil pump pressure relief valve plug 25 Nm (18 lbf.ft)
Oil pump and stiffener assembly to cylinder block bolts 13 Nm (10 lbf.ft)
Oil sump to cylinder block bolts 25 Nm (18 lbf.ft)
Oil sump to gearbox bell housing bolts 13 Nm (10 lbf.ft)
PAS pump bracket bolts 27 Nm (20 lbf.ft)
PAS pump pulley bolts 27 Nm (20 lbf.ft)
Rocker arm adjusting screw locknuts 16 Nm (12 lbf.ft)
Page 88 of 1672
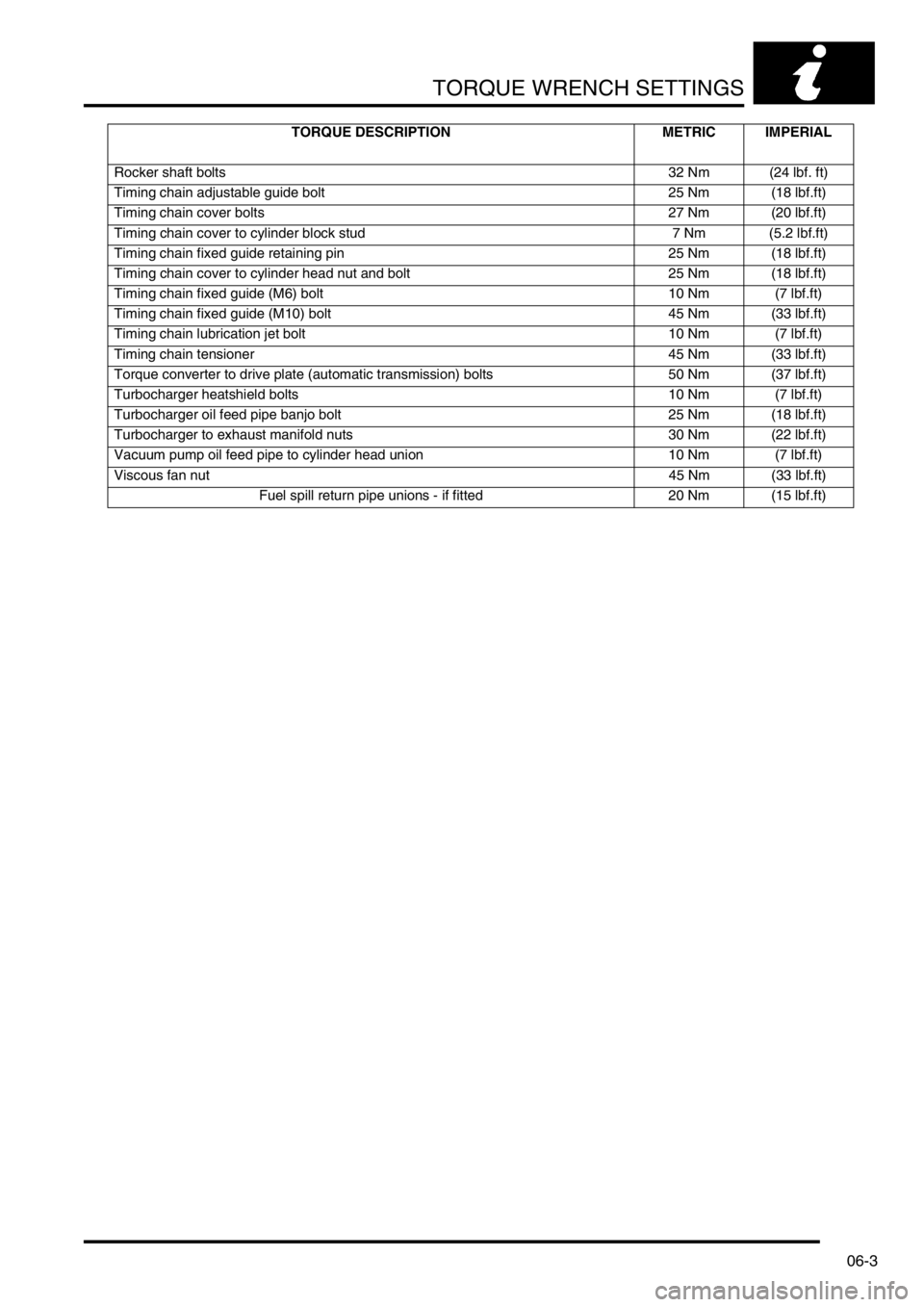
TORQUE WRENCH SETTINGS
06-3
Rocker shaft bolts 32 Nm (24 lbf. ft)
Timing chain adjustable guide bolt 25 Nm (18 lbf.ft)
Timing chain cover bolts 27 Nm (20 lbf.ft)
Timing chain cover to cylinder block stud 7 Nm (5.2 lbf.ft)
Timing chain fixed guide retaining pin 25 Nm (18 lbf.ft)
Timing chain cover to cylinder head nut and bolt 25 Nm (18 lbf.ft)
Timing chain fixed guide (M6) bolt 10 Nm (7 lbf.ft)
Timing chain fixed guide (M10) bolt 45 Nm (33 lbf.ft)
Timing chain lubrication jet bolt 10 Nm (7 lbf.ft)
Timing chain tensioner 45 Nm (33 lbf.ft)
Torque converter to drive plate (automatic transmission) bolts 50 Nm (37 lbf.ft)
Turbocharger heatshield bolts 10 Nm (7 lbf.ft)
Turbocharger oil feed pipe banjo bolt 25 Nm (18 lbf.ft)
Turbocharger to exhaust manifold nuts 30 Nm (22 lbf.ft)
Vacuum pump oil feed pipe to cylinder head union 10 Nm (7 lbf.ft)
Viscous fan nut45 Nm (33 lbf.ft)
Fuel spill return pipe unions - if fitted 20 Nm (15 lbf.ft)TORQUE DESCRIPTION METRIC IMPERIAL
Page 102 of 1672
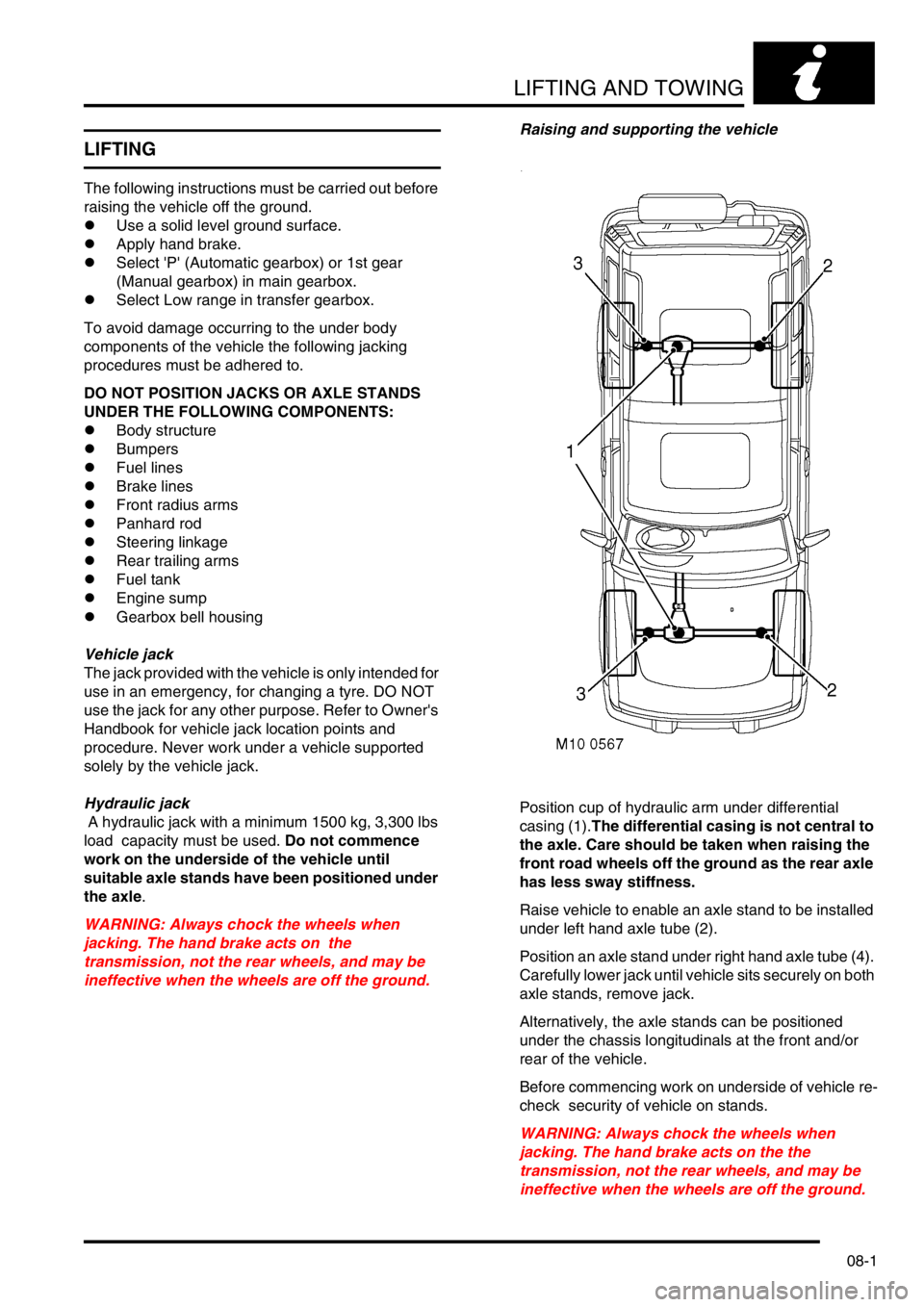
LIFTING AND TOWING
08-1
LIFTING AND TOWING
LIFTING
The following instructions must be carried out before
raising the vehicle off the ground.
lUse a solid level ground surface.
lApply hand brake.
lSelect 'P' (Automatic gearbox) or 1st gear
(Manual gearbox) in main gearbox.
lSelect Low range in transfer gearbox.
To avoid damage occurring to the under body
components of the vehicle the following jacking
procedures must be adhered to.
DO NOT POSITION JACKS OR AXLE STANDS
UNDER THE FOLLOWING COMPONENTS:
lBody structure
lBumpers
lFuel lines
lBrake lines
lFront radius arms
lPanhard rod
lSteering linkage
lRear trailing arms
lFuel tank
lEngine sump
lGearbox bell housing
Vehicle jack
The jack provided with the vehicle is only intended for
use in an emergency, for changing a tyre. DO NOT
use the jack for any other purpose. Refer to Owner's
Handbook for vehicle jack location points and
procedure. Never work under a vehicle supported
solely by the vehicle jack.
Hydraulic jack
A hydraulic jack with a minimum 1500 kg, 3,300 lbs
load capacity must be used. Do not commence
work on the underside of the vehicle until
suitable axle stands have been positioned under
the axle.
WARNING: Always chock the wheels when
jacking. The hand brake acts on the
transmission, not the rear wheels, and may be
ineffective when the wheels are off the ground.Raising and supporting the vehicle
Position cup of hydraulic arm under differential
casing (1).The differential casing is not central to
the axle. Care should be taken when raising the
front road wheels off the ground as the rear axle
has less sway stiffness.
Raise vehicle to enable an axle stand to be installed
under left hand axle tube (2).
Position an axle stand under right hand axle tube (4).
Carefully lower jack until vehicle sits securely on both
axle stands, remove jack.
Alternatively, the axle stands can be positioned
under the chassis longitudinals at the front and/or
rear of the vehicle.
Before commencing work on underside of vehicle re-
check security of vehicle on stands.
WARNING: Always chock the wheels when
jacking. The hand brake acts on the the
transmission, not the rear wheels, and may be
ineffective when the wheels are off the ground.
Page 347 of 1672
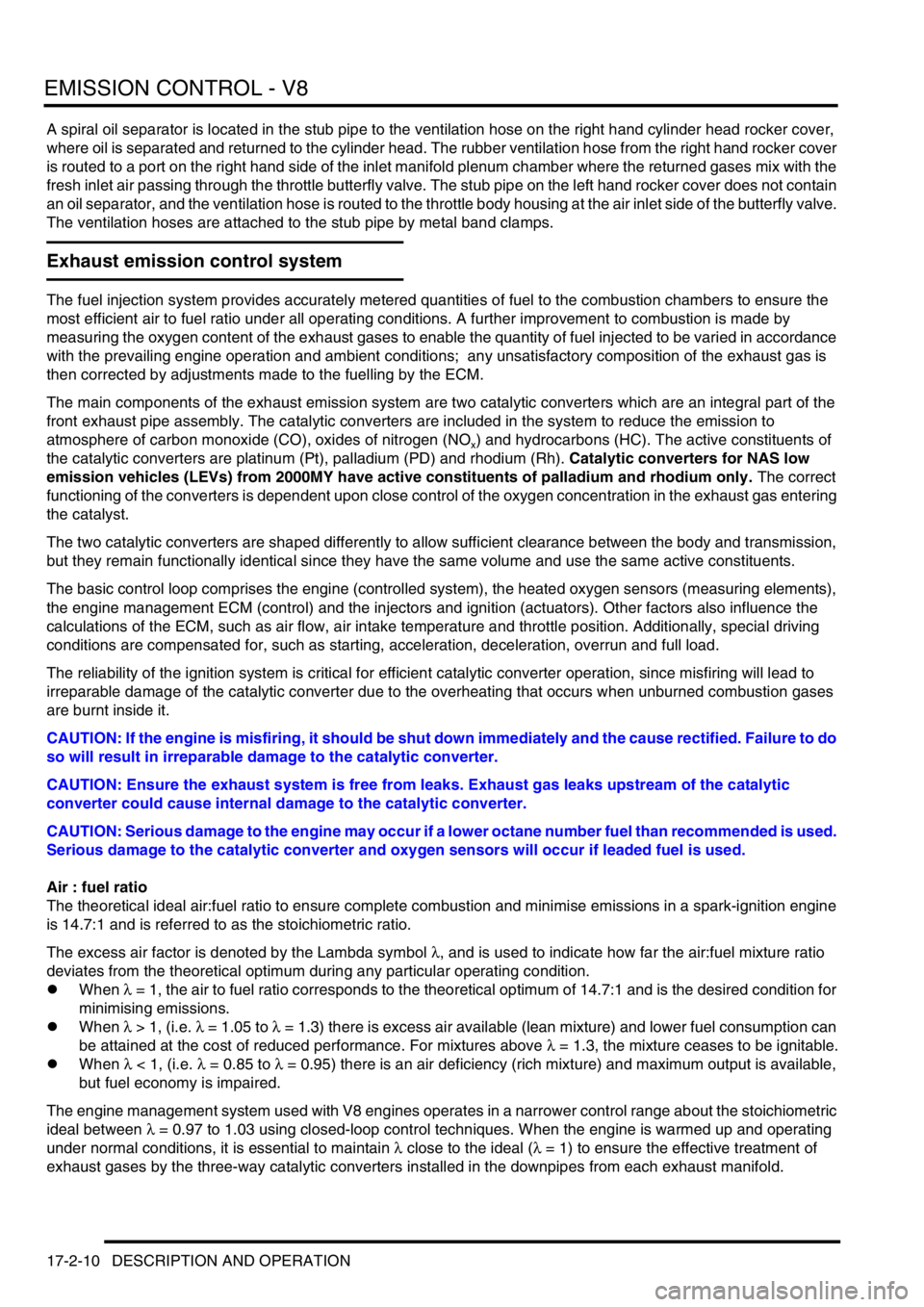
EMISSION CONTROL - V8
17-2-10 DESCRIPTION AND OPERATION
A spiral oil separator is located in the stub pipe to the ventilation hose on the right hand cylinder head rocker cover,
where oil is separated and returned to the cylinder head. The rubber ventilation hose from the right hand rocker cover
is routed to a port on the right hand side of the inlet manifold plenum chamber where the returned gases mix with the
fresh inlet air passing through the throttle butterfly valve. The stub pipe on the left hand rocker cover does not contain
an oil separator, and the ventilation hose is routed to the throttle body housing at the air inlet side of the butterfly valve.
The ventilation hoses are attached to the stub pipe by metal band clamps.
Exhaust emission control system
The fuel injection system provides accurately metered quantities of fuel to the combustion chambers to ensure the
most efficient air to fuel ratio under all operating conditions. A further improvement to combustion is made by
measuring the oxygen content of the exhaust gases to enable the quantity of fuel injected to be varied in accordance
with the prevailing engine operation and ambient conditions; any unsatisfactory composition of the exhaust gas is
then corrected by adjustments made to the fuelling by the ECM.
The main components of the exhaust emission system are two catalytic converters which are an integral part of the
front exhaust pipe assembly. The catalytic converters are included in the system to reduce the emission to
atmosphere of carbon monoxide (CO), oxides of nitrogen (NO
x) and hydrocarbons (HC). The active constituents of
the catalytic converters are platinum (Pt), palladium (PD) and rhodium (Rh). Catalytic converters for NAS low
emission vehicles (LEVs) from 2000MY have active constituents of palladium and rhodium only. The correct
functioning of the converters is dependent upon close control of the oxygen concentration in the exhaust gas entering
the catalyst.
The two catalytic converters are shaped differently to allow sufficient clearance between the body and transmission,
but they remain functionally identical since they have the same volume and use the same active constituents.
The basic control loop comprises the engine (controlled system), the heated oxygen sensors (measuring elements),
the engine management ECM (control) and the injectors and ignition (actuators). Other factors also influence the
calculations of the ECM, such as air flow, air intake temperature and throttle position. Additionally, special driving
conditions are compensated for, such as starting, acceleration, deceleration, overrun and full load.
The reliability of the ignition system is critical for efficient catalytic converter operation, since misfiring will lead to
irreparable damage of the catalytic converter due to the overheating that occurs when unburned combustion gases
are burnt inside it.
CAUTION: If the engine is misfiring, it should be shut down immediately and the cause rectified. Failure to do
so will result in irreparable damage to the catalytic converter.
CAUTION: Ensure the exhaust system is free from leaks. Exhaust gas leaks upstream of the catalytic
converter could cause internal damage to the catalytic converter.
CAUTION: Serious damage to the engine may occur if a lower octane number fuel than recommended is used.
Serious damage to the catalytic converter and oxygen sensors will occur if leaded fuel is used.
Air : fuel ratio
The theoretical ideal air:fuel ratio to ensure complete combustion and minimise emissions in a spark-ignition engine
is 14.7:1 and is referred to as the stoichiometric ratio.
The excess air factor is denoted by the Lambda symbol
λ, and is used to indicate how far the air:fuel mixture ratio
deviates from the theoretical optimum during any particular operating condition.
lWhen
λ = 1, the air to fuel ratio corresponds to the theoretical optimum of 14.7:1 and is the desired condition for
minimising emissions.
lWhen
λ > 1, (i.e. λ = 1.05 to λ = 1.3) there is excess air available (lean mixture) and lower fuel consumption can
be attained at the cost of reduced performance. For mixtures above
λ = 1.3, the mixture ceases to be ignitable.
lWhen
λ < 1, (i.e. λ = 0.85 to λ = 0.95) there is an air deficiency (rich mixture) and maximum output is available,
but fuel economy is impaired.
The engine management system used with V8 engines operates in a narrower control range about the stoichiometric
ideal between
λ = 0.97 to 1.03 using closed-loop control techniques. When the engine is warmed up and operating
under normal conditions, it is essential to maintain
λ close to the ideal (λ = 1) to ensure the effective treatment of
exhaust gases by the three-way catalytic converters installed in the downpipes from each exhaust manifold.
Page 355 of 1672
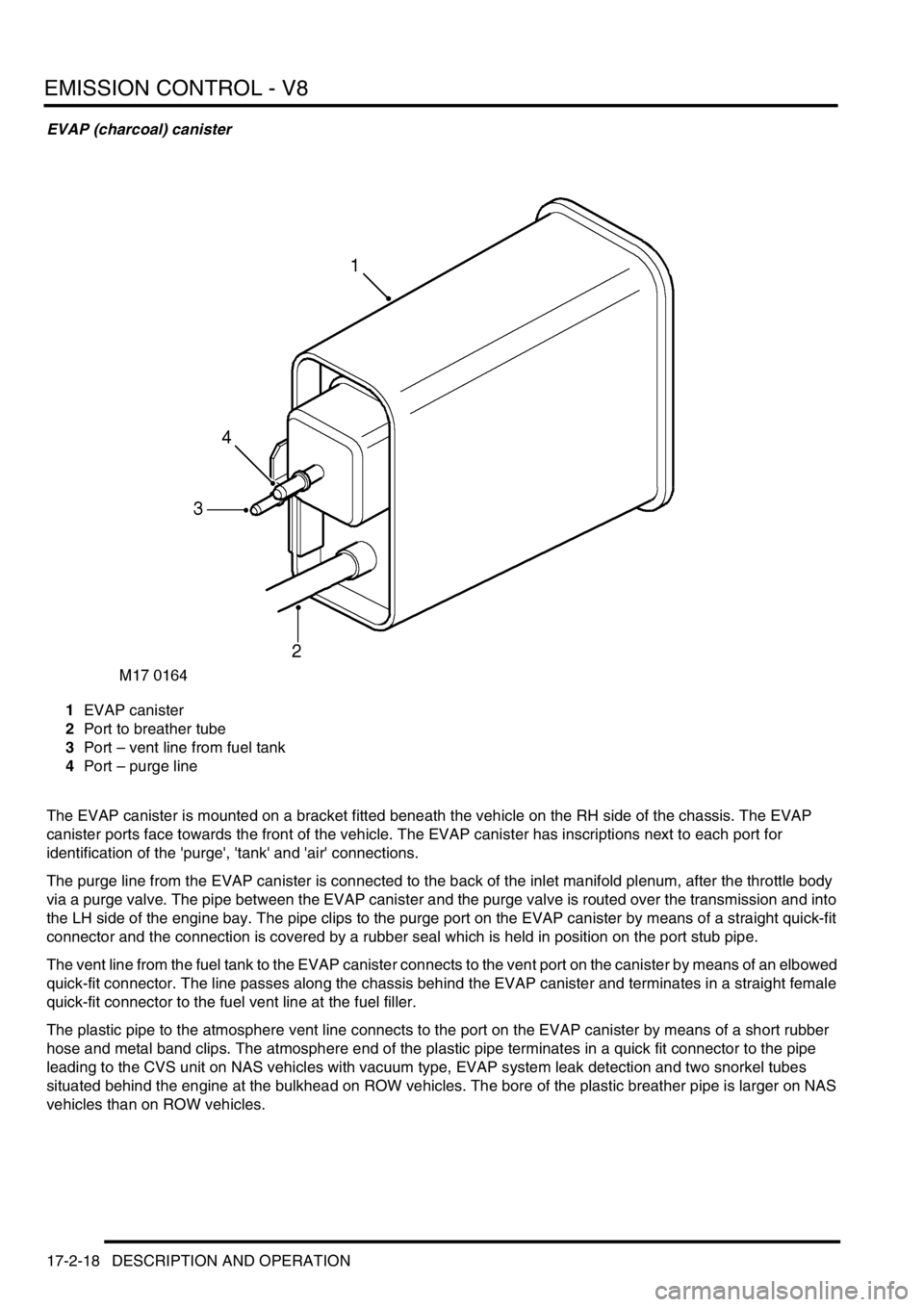
EMISSION CONTROL - V8
17-2-18 DESCRIPTION AND OPERATION
EVAP (charcoal) canister
1EVAP canister
2Port to breather tube
3Port – vent line from fuel tank
4Port – purge line
The EVAP canister is mounted on a bracket fitted beneath the vehicle on the RH side of the chassis. The EVAP
canister ports face towards the front of the vehicle. The EVAP canister has inscriptions next to each port for
identification of the 'purge', 'tank' and 'air' connections.
The purge line from the EVAP canister is connected to the back of the inlet manifold plenum, after the throttle body
via a purge valve. The pipe between the EVAP canister and the purge valve is routed over the transmission and into
the LH side of the engine bay. The pipe clips to the purge port on the EVAP canister by means of a straight quick-fit
connector and the connection is covered by a rubber seal which is held in position on the port stub pipe.
The vent line from the fuel tank to the EVAP canister connects to the vent port on the canister by means of an elbowed
quick-fit connector. The line passes along the chassis behind the EVAP canister and terminates in a straight female
quick-fit connector to the fuel vent line at the fuel filler.
The plastic pipe to the atmosphere vent line connects to the port on the EVAP canister by means of a short rubber
hose and metal band clips. The atmosphere end of the plastic pipe terminates in a quick fit connector to the pipe
leading to the CVS unit on NAS vehicles with vacuum type, EVAP system leak detection and two snorkel tubes
situated behind the engine at the bulkhead on ROW vehicles. The bore of the plastic breather pipe is larger on NAS
vehicles than on ROW vehicles.
Page 398 of 1672

ENGINE MANAGEMENT SYSTEM - TD5
DESCRIPTION AND OPERATION 18-1-5
1Mass air flow sensor
2Ambient air pressure sensor
3Manifold absolute pressure/ inlet air
temperature sensor
4Engine coolant temperature sensor
5Crankshaft speed and position sensor
6Throttle position sensor
7Fuel temperature sensor
8Brake pedal switch
9Clutch switch
10High/ Low ratio switch
11Main relay
12Malfunction indicator lamp
13Fuel pump relay
14Glow plug warning lamp
15Glow plugs16Electronic unit injectors
17Turbocharger wastegate modulator
18EGR modulator
19Diagnostic connector
20Engine control module
21Cruise control master switch
22Cruise control SET+ switch
23Cruise control RES switch
24Air conditioning clutch relay
25Air conditioning cooling fan relay
26Electronic automatic transmission ECU
27Self levelling and anti-lock brakes ECU
28Instrument cluster
29Body control unit