compression LOTUS ELISE 2005 Owners Manual
[x] Cancel search | Manufacturer: LOTUS, Model Year: 2005, Model line: ELISE, Model: LOTUS ELISE 2005Pages: 205, PDF Size: 4.51 MB
Page 95 of 205
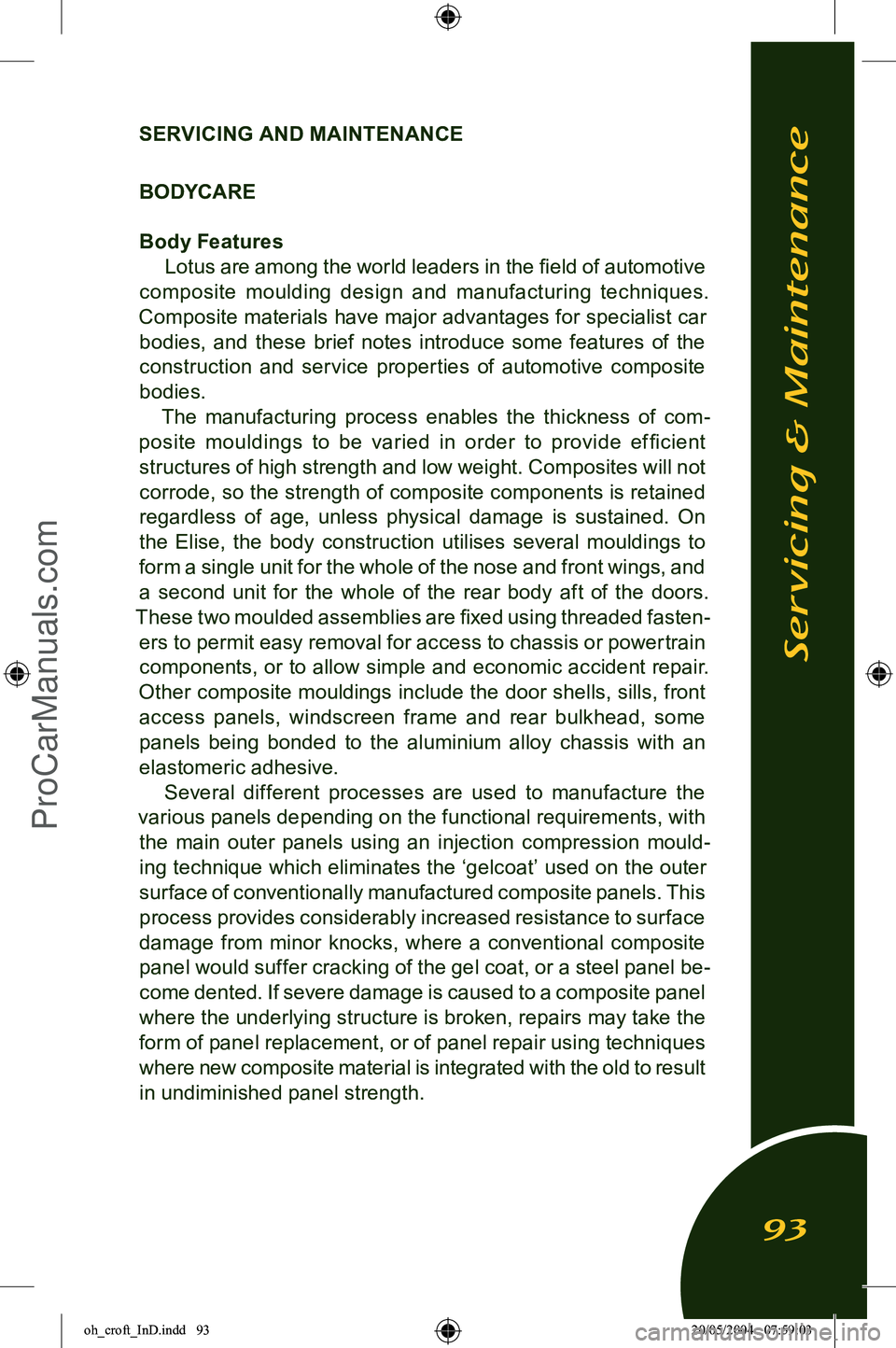
SERVICING AND MAINTENANCEBODYCARE
Body Features Lotus are among the world leaders in the field of automotive
composite moulding design and manufacturing techniques.
Composite materials have major advantages for specialist car bodies, and these brief notes introduce some features of the
construction and service properties of automotive composite bodies. The manufacturing process enables the thickness of com
-
posite mouldings to be varied in order to provide ef ficient structures of high strength and low weight. Composites will not
corrode, so the strength of composite components is retained regardless of age, unless physical damage is sustained. On
the Elise, the body construction utilises several mouldings to
form a single unit for the whole of the nose and front wings, and
a second unit for the whole of the rear body aft of the doors.
These two moulded assemblies are fixed using threaded fasten
-
ers to permit easy removal for access to chassis or powertrain
components, or to allow simple and economic accident repair.
Other composite mouldings include the door shells, sills, front access panels, windscreen frame and rear bulkhead, some panels being bonded to the aluminium alloy chassis with an
elastomeric adhesive.
Several different processes are used to manufacture the
various panels depending on the functional requirements, with the main outer panels using an injection compression mould
-
ing technique which eliminates the ‘gelcoat’ used on the outer
surface of conventionally manufactured composite panels. This
process provides considerably increased resistance to surface
damage from minor knocks, where a conventional composite panel would suffer cracking of the gel coat, or a steel panel be
-
come dented. If severe damage is caused to a composite panel
where the underlying structure is broken, repairs may take the
form of panel replacement, or of panel repair using techniques
where new composite material is integrated with the old to result in undiminished panel strength.
Servicing & Maintenance
93
oh_croft_InD.indd 9320/05/2004 07:59:03ProCarManuals.com
Page 160 of 205
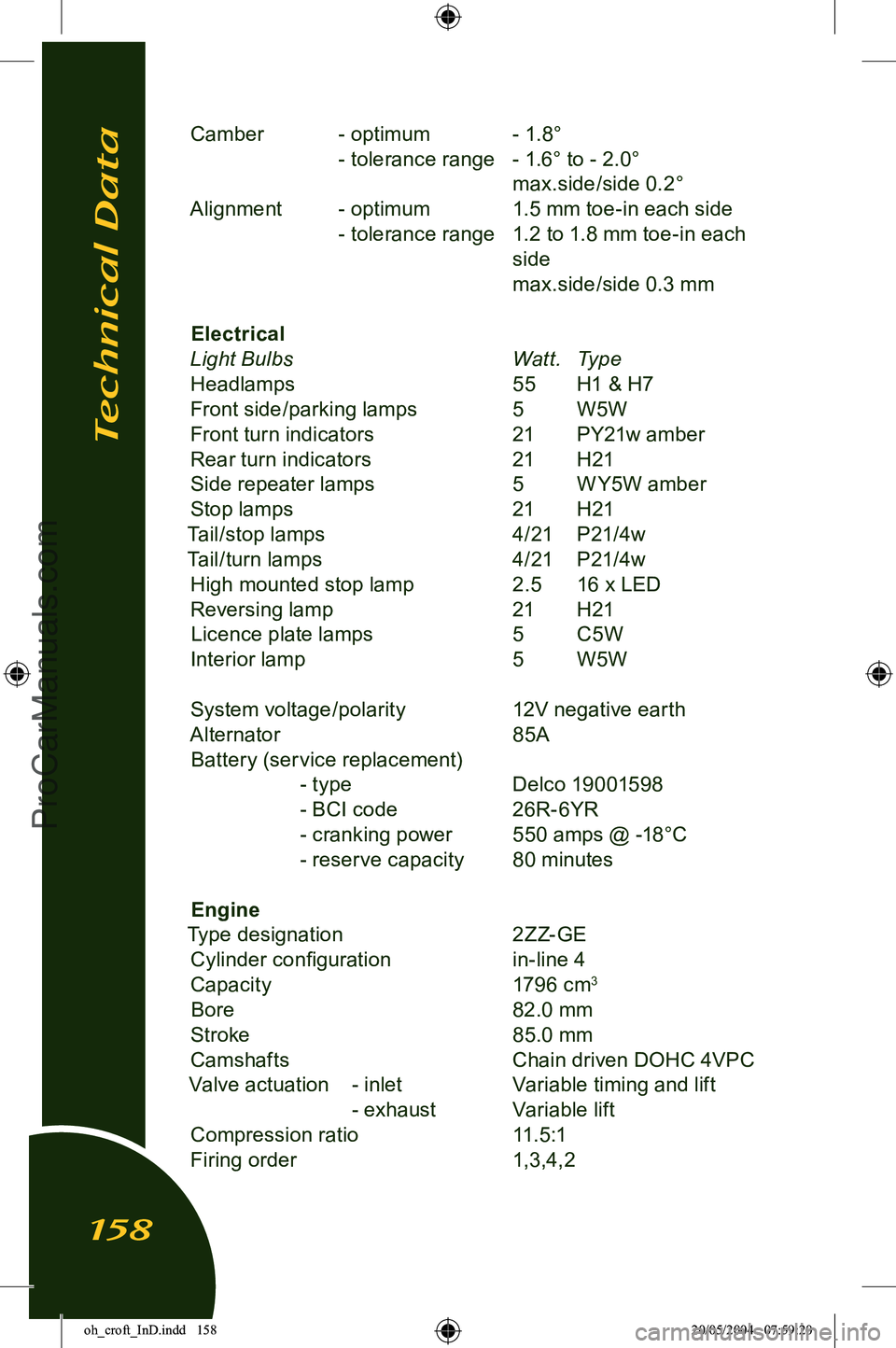
Camber - optimum - 1.8°
- tolerance range - 1.6° to - 2.0°
max.side/side 0.2°
Alignment - optimum 1.5 mm toe-in each side - tolerance range 1.2 to 1.8 mm toe-in each
side
max.side/side 0.3 mm
Electrical
Light Bulbs Watt. Type
Headlamps 55 H1 & H7
Front side/parking lamps 5 W5W
Front turn indicators 21 PY21w amber
Rear turn indicators 21 H21
Side repeater lamps 5 W Y5W amber
Stop lamps 21 H21
Tail/stop lamps 4/21 P21/4w
Tail/turn lamps 4/21 P21/4w
High mounted stop lamp 2.5 16 x LED
Reversing lamp 21 H21
Licence plate lamps 5 C5W
Interior lamp 5 W5W
System voltage/polarity 12V negative earth
Alternator 85A
Battery (service replacement)
- type Delco 19001598
- BCI code 26R- 6YR
- cranking power 550 amps @ -18°C
- reserve capacity 80 minutes
Engine
Type designation 2ZZ-GE
Cylinder configuration in-line 4
Capacity 1796 cm
3
Bore 82.0 mm
Stroke 85.0 mm
Camshafts Chain driven DOHC 4VPC
Valve actuation - inlet Variable timing and lift
- exhaust Variable lift
Compression ratio 11.5:1
Firing order 1,3,4,2
Technical Data
158
oh_croft_InD.indd 15820/05/2004 07:59:20ProCarManuals.com