wheel MITSUBISHI LANCER EVOLUTION IX 2005 Workshop Manual
[x] Cancel search | Manufacturer: MITSUBISHI, Model Year: 2005, Model line: LANCER EVOLUTION IX, Model: MITSUBISHI LANCER EVOLUTION IX 2005Pages: 364, PDF Size: 14.38 MB
Page 3 of 364
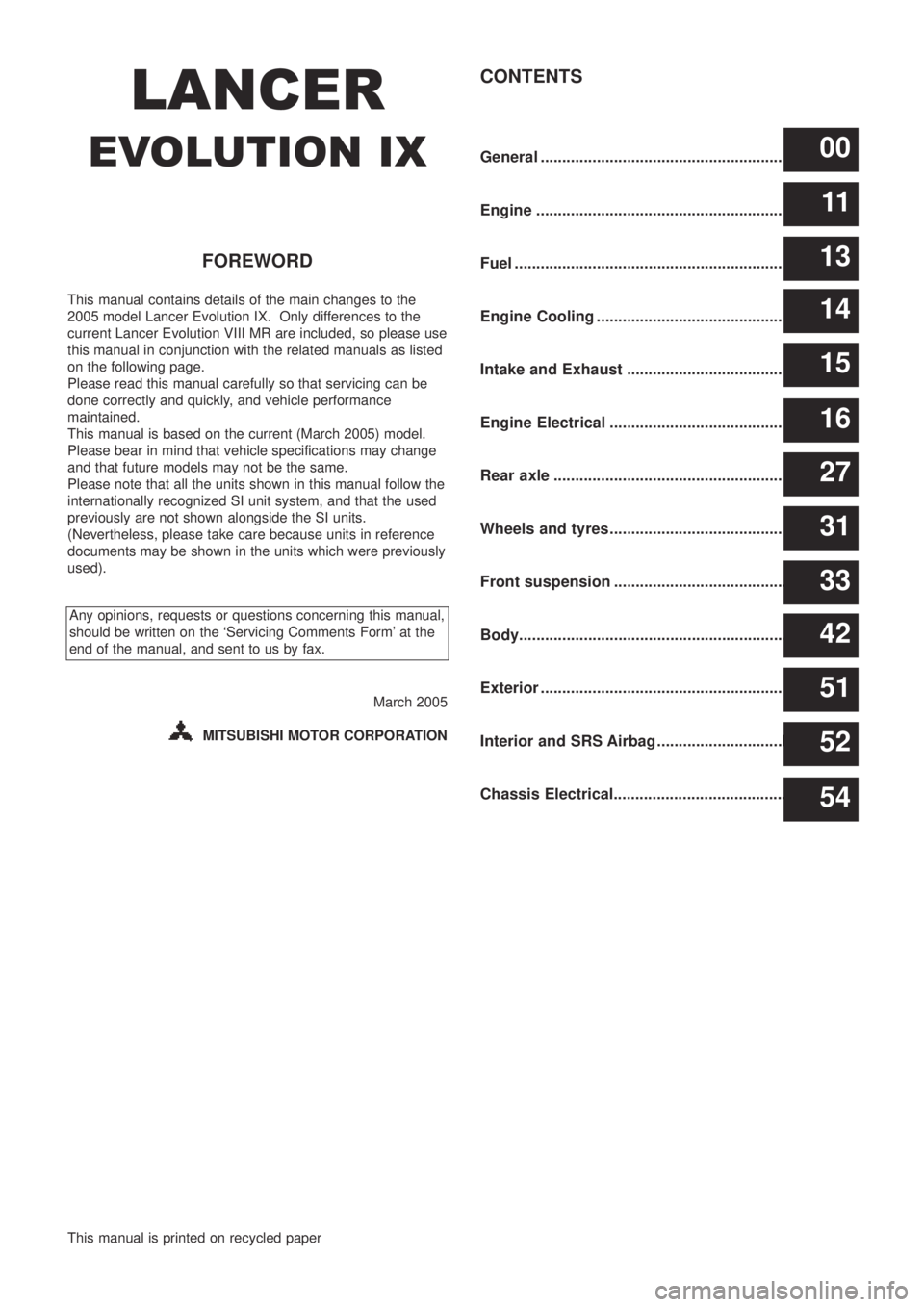
LANCER
EVOLUTION IX
FOREWORD
This manual contains details of the main changes to the
2005 model Lancer Evolution IX. Only differences to the
current Lancer Evolution VIII MR are included, so please use
this manual in conjunction with the related manuals as listed
on the following page.
Please read this manual carefully so that servicing can be
done correctly and quickly, and vehicle performance
maintained.
This manual is based on the current (March 2005) model.
Please bear in mind that vehicle specifications may change
and that future models may not be the same.
Please note that all the units shown in this manual follow the
internationally recognized SI unit system, and that the used
previously are not shown alongside the SI units.
(Nevertheless, please take care because units in reference
documents may be shown in the units which were previously
used). March 2005
MITSUBISHI MOTOR CORPORATION
CONTENTS
General ........................................................
Engine .........................................................
Fuel ..............................................................
Engine Cooling ...........................................
Intake and Exhaust ....................................
Engine Electrical ........................................
Rear axle .....................................................
Wheels and tyres ........................................
Front suspension ...............................................Body
Body.......................................................................
Exterior ........................................................
Interior and SRS Airbag .............................N
Chassis Electrical.........................................
This manual is printed on recycled paper
00
11
13
14
15
16
27
31
33
42
51
52
54
Any opinions, requests or questions concerning this manual,
should be written on the ‘Servicing Comments Form’ at the
end of the manual, and sent to us by fax.
Page 91 of 364
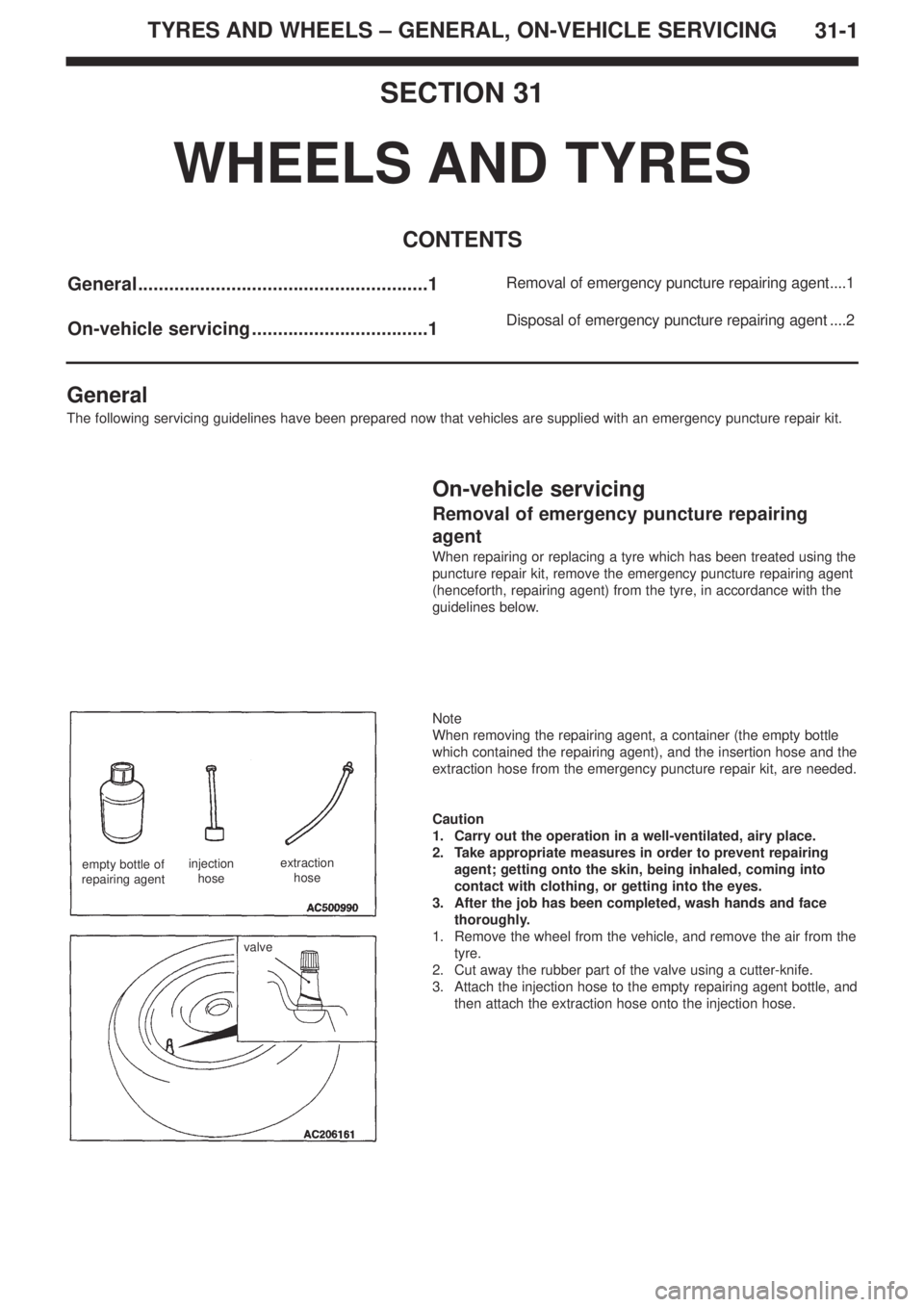
TYRES AND WHEELS – GENERAL, ON-VEHICLE SERVICING
31-1
SECTION 31
WHEELS AND TYRES
CONTENTS
General........................................................1
On-vehicle servicing ..................................1Removal of emergency puncture repairing agent ....1
Disposal of emergency puncture repairing agent ....2
General
The following servicing guidelines have been prepared now that vehicles are supplied with an emergency puncture repair kit.
On-vehicle servicing
Removal of emergency puncture repairing
agent
When repairing or replacing a tyre which has been treated using the
puncture repair kit, remove the emergency puncture repairing agent
(henceforth, repairing agent) from the tyre, in accordance with the
guidelines below.
Note
When removing the repairing agent, a container (the empty bottle
which contained the repairing agent), and the insertion hose and the
extraction hose from the emergency puncture repair kit, are needed.
Caution
1. Carry out the operation in a well-ventilated, airy place.
2. Take appropriate measures in order to prevent repairing
agent; getting onto the skin, being inhaled, coming into
contact with clothing, or getting into the eyes.
3. After the job has been completed, wash hands and face
thoroughly.
1. Remove the wheel from the vehicle, and remove the air from the
tyre.
2. Cut away the rubber part of the valve using a cutter-knife.
3. Attach the injection hose to the empty repairing agent bottle, and
then attach the extraction hose onto the injection hose.
empty bottle of
repairing agentinjection
hoseextraction
hose
valve
Page 92 of 364
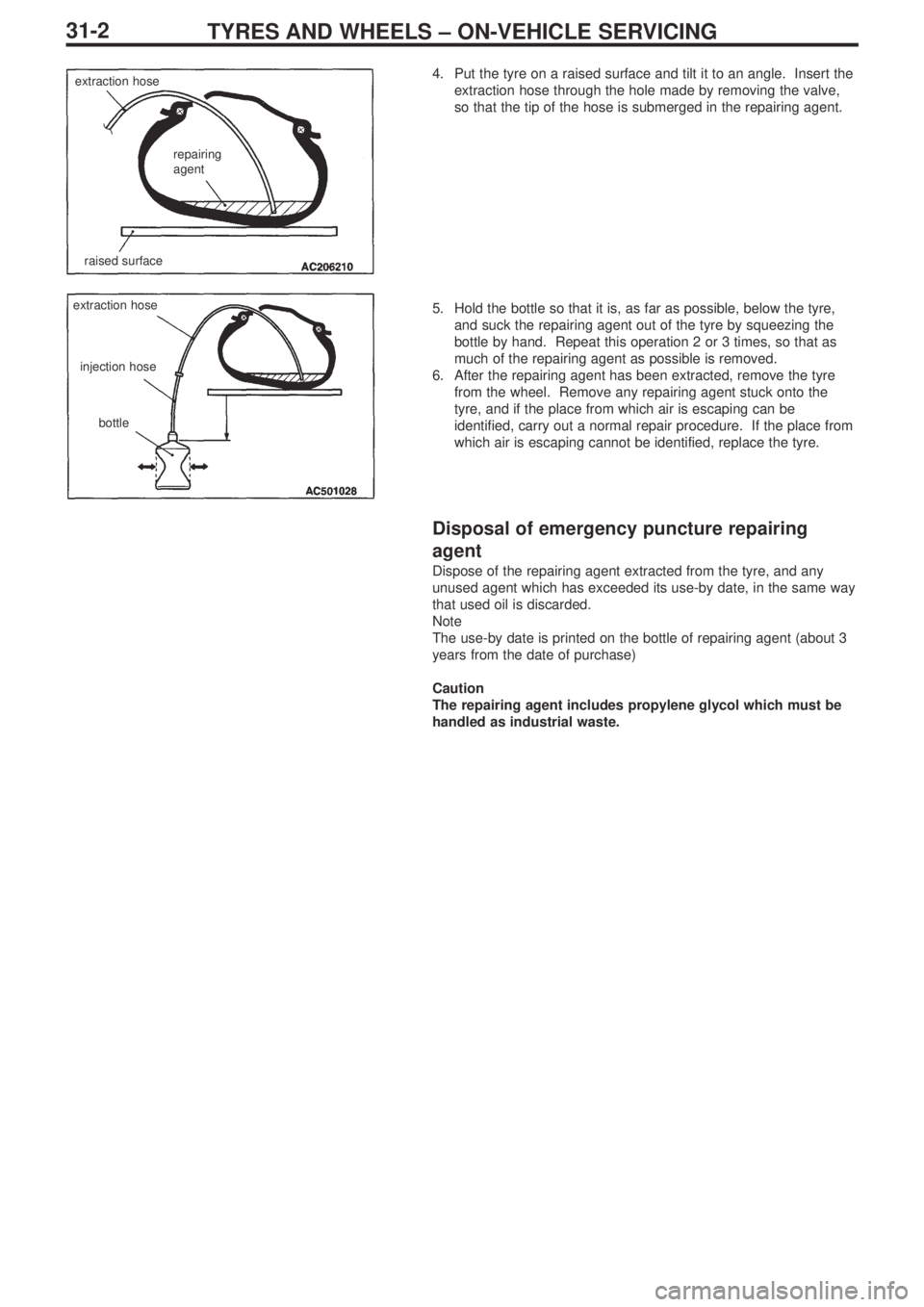
TYRES AND WHEELS – ON-VEHICLE SERVICING31-2
4. Put the tyre on a raised surface and tilt it to an angle. Insert the
extraction hose through the hole made by removing the valve,
so that the tip of the hose is submerged in the repairing agent.
5. Hold the bottle so that it is, as far as possible, below the tyre,
and suck the repairing agent out of the tyre by squeezing the
bottle by hand. Repeat this operation 2 or 3 times, so that as
much of the repairing agent as possible is removed.
6. After the repairing agent has been extracted, remove the tyre
from the wheel. Remove any repairing agent stuck onto the
tyre, and if the place from which air is escaping can be
identified, carry out a normal repair procedure. If the place from
which air is escaping cannot be identified, replace the tyre.
Disposal of emergency puncture repairing
agent
Dispose of the repairing agent extracted from the tyre, and any
unused agent which has exceeded its use-by date, in the same way
that used oil is discarded.
Note
The use-by date is printed on the bottle of repairing agent (about 3
years from the date of purchase)
Caution
The repairing agent includes propylene glycol which must be
handled as industrial waste.
extraction hose
raised surface
repairing
agent
extraction hose
injection hose
bottle
Page 114 of 364
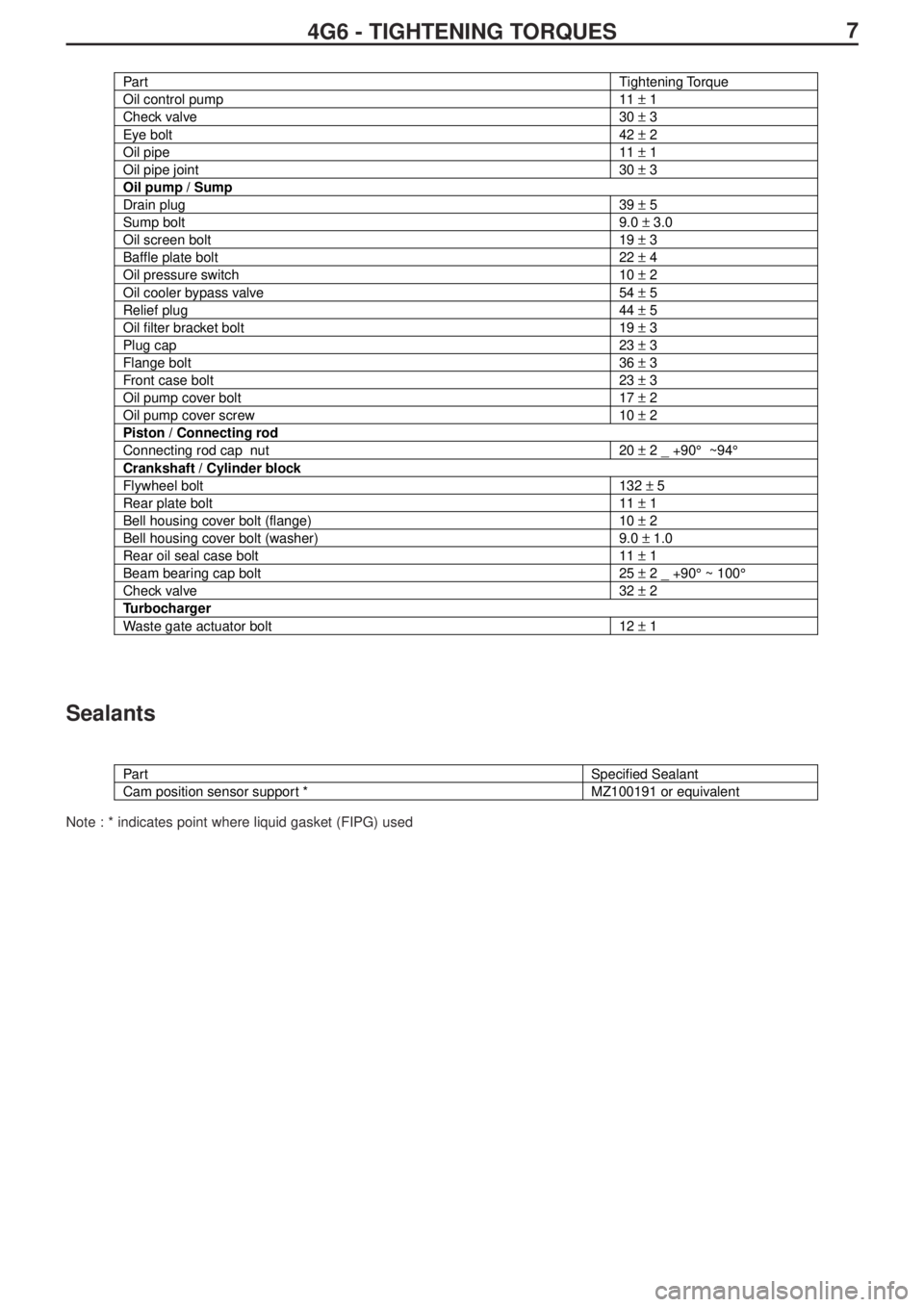
74G6 - TIGHTENING TORQUES
Par tTightening Torque
Oil control pump11 ± 1
Check valve30 ± 3
Eye bolt42 ± 2
Oil pipe11 ± 1
Oil pipe joint30 ± 3
Oil pump / Sump
Drain plug39 ± 5
Sump bolt9.0 ± 3.0
Oil screen bolt19 ± 3
Baffle plate bolt22 ± 4
Oil pressure switch10 ± 2
Oil cooler bypass valve54 ± 5
Relief plug44 ± 5
Oil filter bracket bolt19 ± 3
Plug cap23 ± 3
Flange bolt36 ± 3
Front case bolt23 ± 3
Oil pump cover bolt17 ± 2
Oil pump cover screw10 ± 2
Piston / Connecting rod
Connecting rod cap nut20 ± 2 _ +90° ~94°
Crankshaft / Cylinder block
Flywheel bolt132 ± 5
Rear plate bolt11 ± 1
Bell housing cover bolt (flange)10 ± 2
Bell housing cover bolt (washer)9.0 ± 1.0
Rear oil seal case bolt11 ± 1
Beam bearing cap bolt25 ± 2 _ +90° ~ 100°
Check valve32 ± 2
Turbocharger
Waste gate actuator bolt12 ± 1
Sealants
Par tSpecified Sealant
Cam position sensor support *MZ100191 or equivalent
Note : * indicates point where liquid gasket (FIPG) used
Page 132 of 364
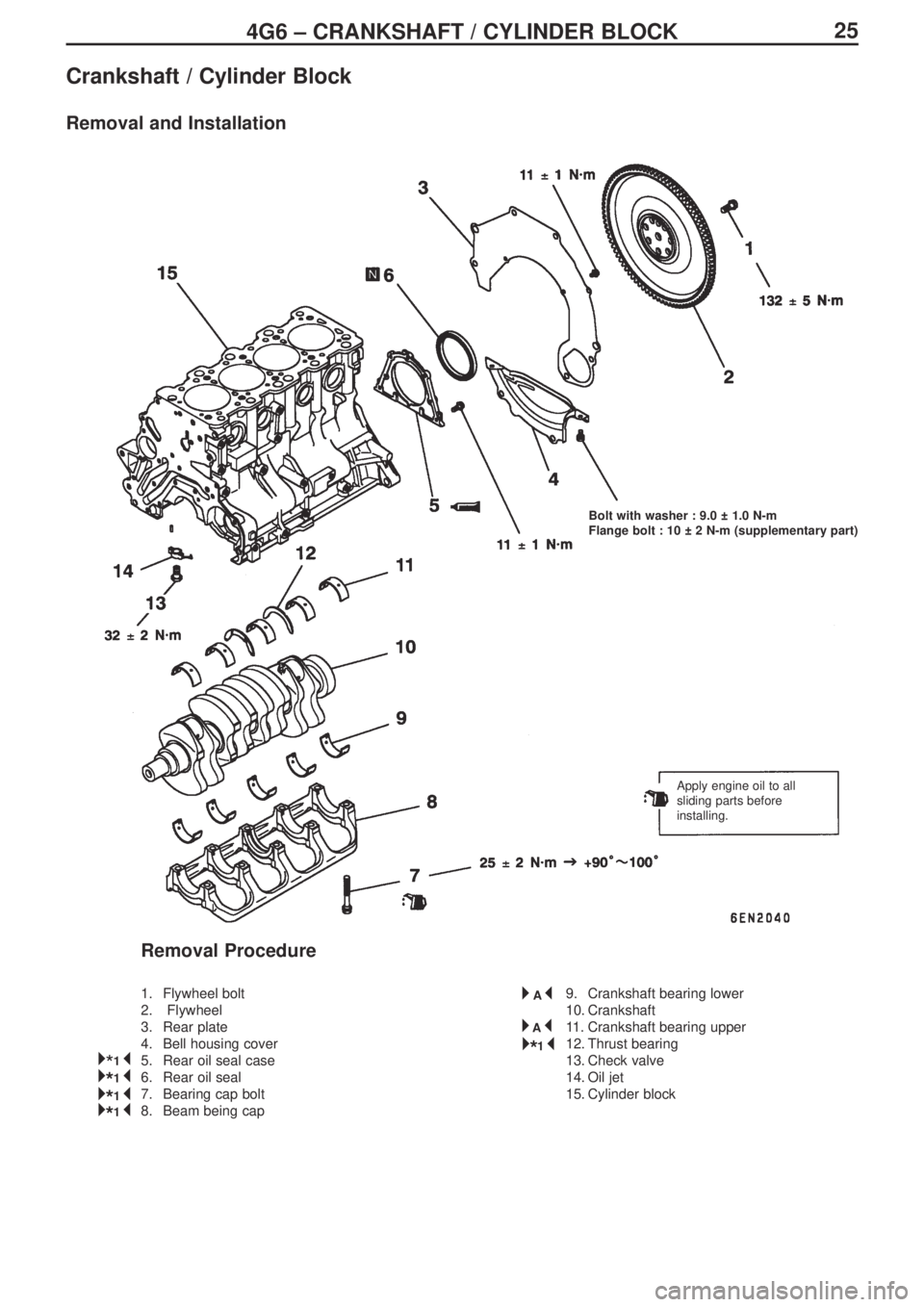
254G6 – CRANKSHAFT / CYLINDER BLOCK
Crankshaft / Cylinder Block
Removal and Installation
Removal Procedure
1. Flywheel bolt
2. Flywheel
3. Rear plate
4. Bell housing cover
5. Rear oil seal case
6. Rear oil seal
7. Bearing cap bolt
8. Beam being cap9. Crankshaft bearing lower
10. Crankshaft
11.Crankshaft bearing upper
12. Thrust bearing
13. Check valve
14. Oil jet
15. Cylinder block
Apply engine oil to all
sliding parts before
installing. Bolt with washer : 9.0 ± 1.0 N-m
Flange bolt : 10 ± 2 N-m (supplementary part)
A*
A*
* 1*
* 1*
* 1*
* 1*
*1*
Page 164 of 364
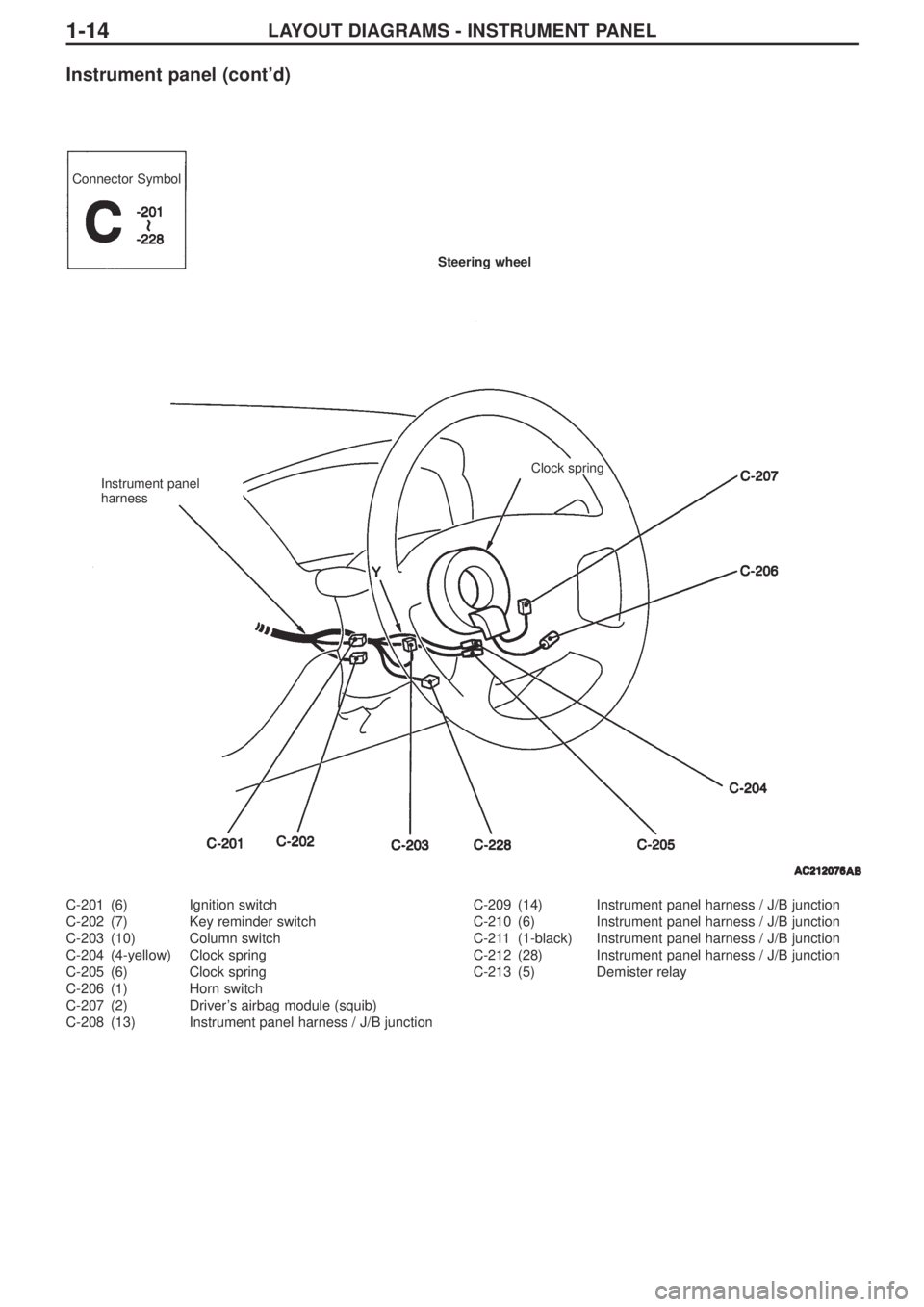
LAYOUT DIAGRAMS - INSTRUMENT PANEL1-14
C-201 (6) Ignition switch
C-202 (7) Key reminder switch
C-203 (10) Column switch
C-204 (4-yellow) Clock spring
C-205 (6) Clock spring
C-206 (1) Horn switch
C-207 (2) Driver’s airbag module (squib)
C-208 (13) Instrument panel harness / J/B junctionC-209 (14) Instrument panel harness / J/B junction
C-210 (6) Instrument panel harness / J/B junction
C-211 (1-black) Instrument panel harness / J/B junction
C-212 (28) Instrument panel harness / J/B junction
C-213 (5) Demister relay
Instrument panel (cont’d)
Connector Symbol
Steering wheel
Clock spring
Instrument panel
harness