set clock MITSUBISHI MONTERO 1998 Service Manual
[x] Cancel search | Manufacturer: MITSUBISHI, Model Year: 1998, Model line: MONTERO, Model: MITSUBISHI MONTERO 1998Pages: 1501, PDF Size: 25.81 MB
Page 85 of 1501
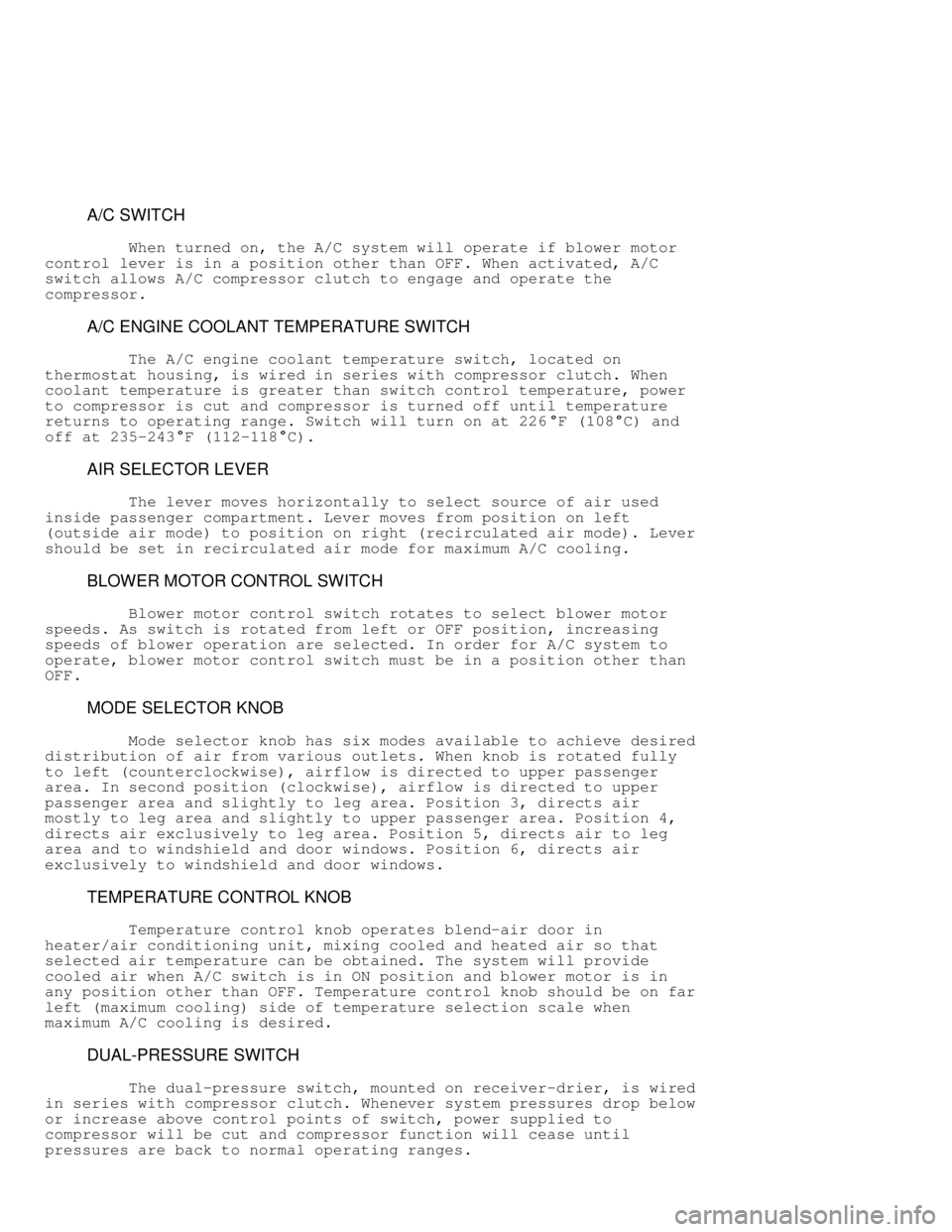
A/C SWITCH
When turned on, the A/C system will operate if blower motor
control lever is in a position other than OFF. When activated, A/C
switch allows A/C compressor clutch to engage and operate the
compressor.
A/C ENGINE COOLANT TEMPERATURE SWITCH
The A/C engine coolant temperature switch, located on
thermostat housing, is wired in series with compressor clutch. When
coolant temperature is greater than switch control temperature, power
to compressor is cut and compressor is turned off until temperature
returns to operating range. Switch will turn on at 226
F (108C) and
off at 235-243F (112-118C).
AIR SELECTOR LEVER
The lever moves horizontally to select source of air used
inside passenger compartment. Lever moves from position on left
(outside air mode) to position on right (recirculated air mode). Lev\
er
should be set in recirculated air mode for maximum A/C cooling.
BLOWER MOTOR CONTROL SWITCH
Blower motor control switch rotates to select blower motor
speeds. As switch is rotated from left or OFF position, increasing
speeds of blower operation are selected. In order for A/C system to
operate, blower motor control switch must be in a position other than
OFF.
MODE SELECTOR KNOB
Mode selector knob has six modes available to achieve desired
distribution of air from various outlets. When knob is rotated fully
to left (counterclockwise), airflow is directed to upper passenger
area. In second position (clockwise), airflow is directed to upper
passenger area and slightly to leg area. Position 3, directs air
mostly to leg area and slightly to upper passenger area. Position 4,
directs air exclusively to leg area. Position 5, directs air to leg
area and to windshield and door windows. Position 6, directs air
exclusively to windshield and door windows.
TEMPERATURE CONTROL KNOB
Temperature control knob operates blend-air door in
heater/air conditioning unit, mixing cooled and heated air so that
selected air temperature can be obtained. The system will provide
cooled air when A/C switch is in ON position and blower motor is in
any position other than OFF. Temperature control knob should be on far
left (maximum cooling) side of temperature selection scale when
maximum A/C cooling is desired.
DUAL-PRESSURE SWITCH
The dual-pressure switch, mounted on receiver-drier, is wired
in series with compressor clutch. Whenever system pressures drop below
or increase above control points of switch, power supplied to
compressor will be cut and compressor function will cease until
pressures are back to normal operating ranges.
Page 109 of 1501
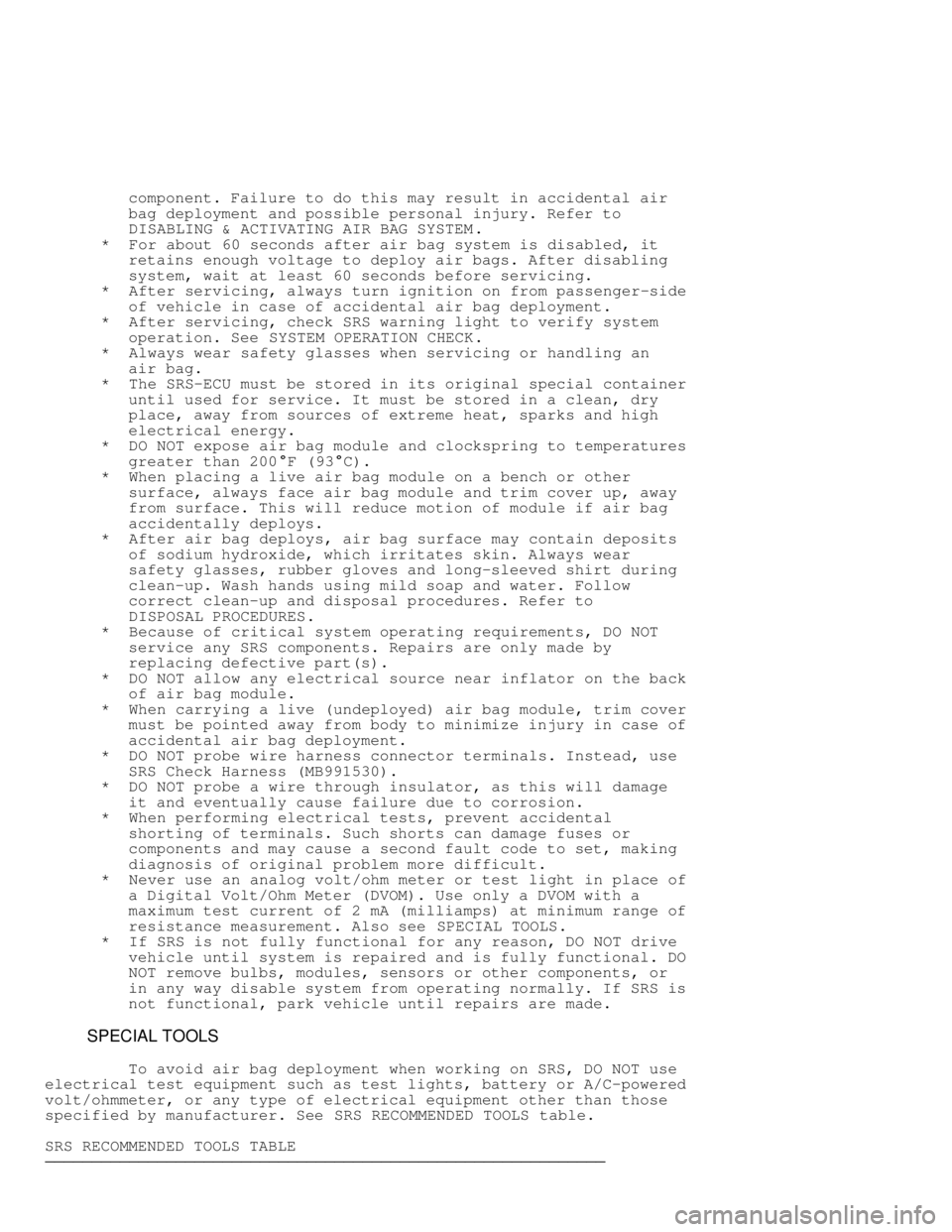
component. Failure to do this may result in accidental air
bag deployment and possible personal injury. Refer to
DISABLING & ACTIVATING AIR BAG SYSTEM .
* For about 60 seconds after air bag system is disabled, it
retains enough voltage to deploy air bags. After disabling
system, wait at least 60 seconds before servicing.
* After servicing, always turn ignition on from passenger-side
of vehicle in case of accidental air bag deployment.
* After servicing, check SRS warning light to verify system
operation. See SYSTEM OPERATION CHECK.
* Always wear safety glasses when servicing or handling an
air bag.
* The SRS-ECU must be stored in its original special container
until used for service. It must be stored in a clean, dry
place, away from sources of extreme heat, sparks and high
electrical energy.
* DO NOT expose air bag module and clockspring to temperatures
greater than 200
F (93 C).
* When placing a live air bag module on a bench or other
surface, always face air bag module and trim cover up, away
from surface. This will reduce motion of module if air bag
accidentally deploys.
* After air bag deploys, air bag surface may contain deposits
of sodium hydroxide, which irritates skin. Always wear
safety glasses, rubber gloves and long-sleeved shirt during
clean-up. Wash hands using mild soap and water. Follow
correct clean-up and disposal procedures. Refer to
DISPOSAL PROCEDURES .
* Because of critical system operating requirements, DO NOT
service any SRS components. Repairs are only made by
replacing defective part(s).
* DO NOT allow any electrical source near inflator on the back
of air bag module.
* When carrying a live (undeployed) air bag module, trim cover
must be pointed away from body to minimize injury in case of
accidental air bag deployment.
* DO NOT probe wire harness connector terminals. Instead, use
SRS Check Harness (MB991530).
* DO NOT probe a wire through insulator, as this will damage
it and eventually cause failure due to corrosion.
* When performing electrical tests, prevent accidental
shorting of terminals. Such shorts can damage fuses or
components and may cause a second fault code to set, making
diagnosis of original problem more difficult.
* Never use an analog volt/ohm meter or test light in place of
a Digital Volt/Ohm Meter (DVOM). Use only a DVOM with a
maximum test current of 2 mA (milliamps) at minimum range of
resistance measurement. Also see SPECIAL TOOLS.
* If SRS is not fully functional for any reason, DO NOT drive
vehicle until system is repaired and is fully functional. DO
NOT remove bulbs, modules, sensors or other components, or
in any way disable system from operating normally. If SRS is
not functional, park vehicle until repairs are made.
SPECIAL TOOLS
To avoid air bag deployment when working on SRS, DO NOT use
electrical test equipment such as test lights, battery or A/C-powered
volt/ohmmeter, or any type of electrical equipment other than those
specified by manufacturer. See SRS RECOMMENDED TOOLS table.
SRS RECOMMENDED TOOLS TABLE
\
\
\
\
\
\
Page 111 of 1501
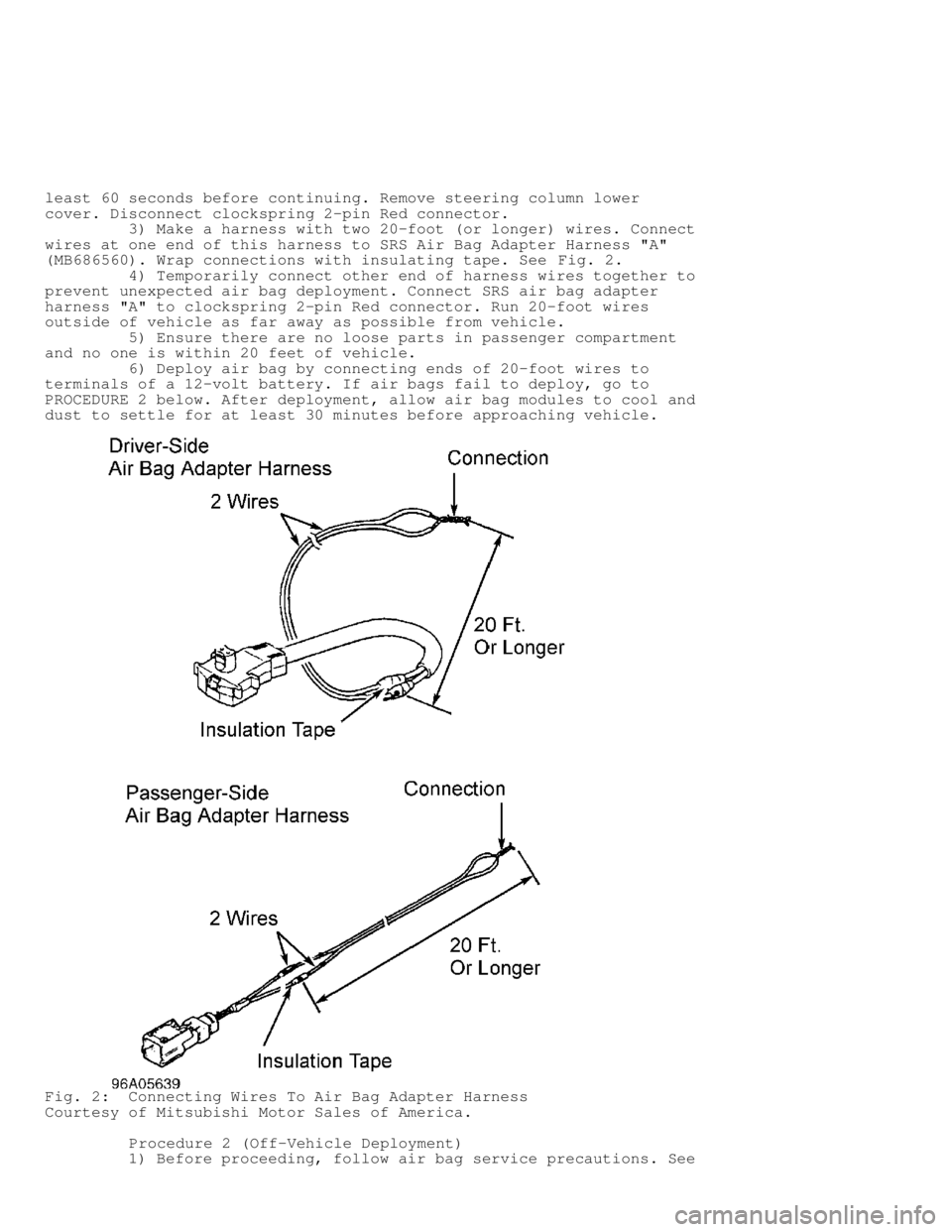
least 60 seconds before continuing. Remove steering column lower
cover. Disconnect clockspring 2-pin Red connector.
3) Make a harness with two 20-foot (or longer) wires. Connec\
t
wires at one end of this harness to SRS Air Bag Adapter Harness "A"
(MB686560). Wrap connections with insulating tape. See Fig. 2.
4) Temporarily connect other end of harness wires together to
prevent unexpected air bag deployment. Connect SRS air bag adapter
harness "A" to clockspring 2-pin Red connector. Run 20-foot wires
outside of vehicle as far away as possible from vehicle.
5) Ensure there are no loose parts in passenger compartment
and no one is within 20 feet of vehicle.
6) Deploy air bag by connecting ends of 20-foot wires to
terminals of a 12-volt battery. If air bags fail to deploy, go to
PROCEDURE 2 below. After deployment, allow air bag modules to cool and
dust to settle for at least 30 minutes before approaching vehicle.
Fig. 2: Connecting Wires To Air Bag Adapter Harness
Courtesy of Mitsubishi Motor Sales of America.
Procedure 2 (Off-Vehicle Deployment)
1) Before proceeding, follow air bag service precautions. See
Page 112 of 1501
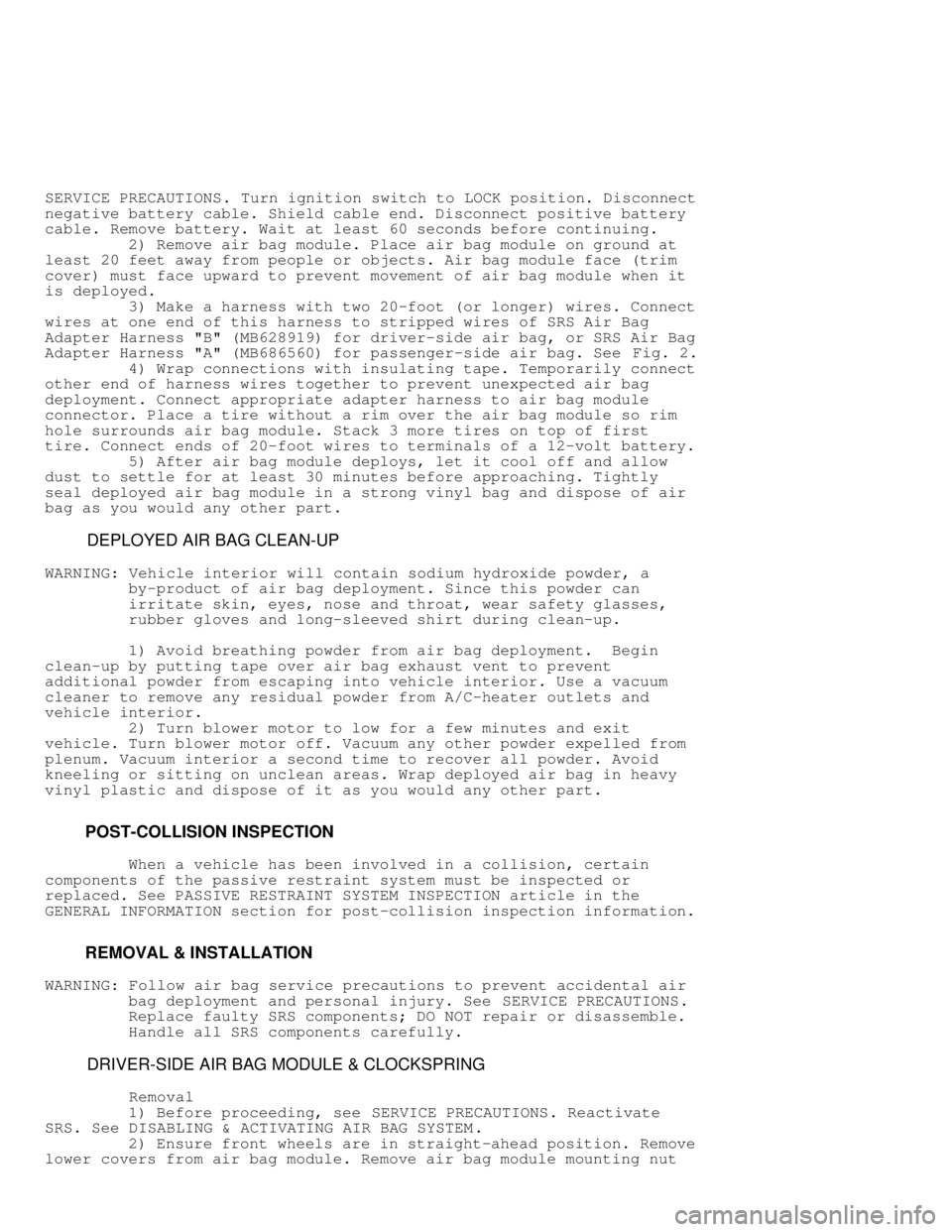
SERVICE PRECAUTIONS. Turn ignition switch to LOCK position. Disconnect
negative battery cable. Shield cable end. Disconnect positive battery
cable. Remove battery. Wait at least 60 seconds before continuing.
2) Remove air bag module. Place air bag module on ground at
least 20 feet away from people or objects. Air bag module face (trim
cover) must face upward to prevent movement of air bag module when it
is deployed.
3) Make a harness with two 20-foot (or longer) wires. Connec\
t
wires at one end of this harness to stripped wires of SRS Air Bag
Adapter Harness "B" (MB628919) for driver-side air bag, or SRS Air Bag\
Adapter Harness "A" (MB686560) for passenger-side air bag. See Fig. 2.
4) Wrap connections with insulating tape. Temporarily connect
other end of harness wires together to prevent unexpected air bag
deployment. Connect appropriate adapter harness to air bag module
connector. Place a tire without a rim over the air bag module so rim
hole surrounds air bag module. Stack 3 more tires on top of first
tire. Connect ends of 20-foot wires to terminals of a 12-volt battery.
5) After air bag module deploys, let it cool off and allow
dust to settle for at least 30 minutes before approaching. Tightly
seal deployed air bag module in a strong vinyl bag and dispose of air
bag as you would any other part.
DEPLOYED AIR BAG CLEAN-UP
WARNING: Vehicle interior will contain sodium hydroxide powder, a
by-product of air bag deployment. Since this powder can
irritate skin, eyes, nose and throat, wear safety glasses,
rubber gloves and long-sleeved shirt during clean-up.
1) Avoid breathing powder from air bag deployment. Begin
clean-up by putting tape over air bag exhaust vent to prevent
additional powder from escaping into vehicle interior. Use a vacuum
cleaner to remove any residual powder from A/C-heater outlets and
vehicle interior.
2) Turn blower motor to low for a few minutes and exit
vehicle. Turn blower motor off. Vacuum any other powder expelled from
plenum. Vacuum interior a second time to recover all powder. Avoid
kneeling or sitting on unclean areas. Wrap deployed air bag in heavy
vinyl plastic and dispose of it as you would any other part.
POST-COLLISION INSPECTION
When a vehicle has been involved in a collision, certain
components of the passive restraint system must be inspected or
replaced. See PASSIVE RESTRAINT SYSTEM INSPECTION article in the
GENERAL INFORMATION section for post-collision inspection information.
REMOVAL & INSTALLATION
WARNING: Follow air bag service precautions to prevent accidental air
bag deployment and personal injury. See SERVICE PRECAUTIONS.
Replace faulty SRS components; DO NOT repair or disassemble.
Handle all SRS components carefully.
DRIVER-SIDE AIR BAG MODULE & CLOCKSPRING
Removal
1) Before proceeding, see SERVICE PRECAUTIONS. Reactivate
SRS. See DISABLING & ACTIVATING AIR BAG SYSTEM .
2) Ensure front wheels are in straight-ahead position. Remove
lower covers from air bag module. Remove air bag module mounting nut
Page 120 of 1501
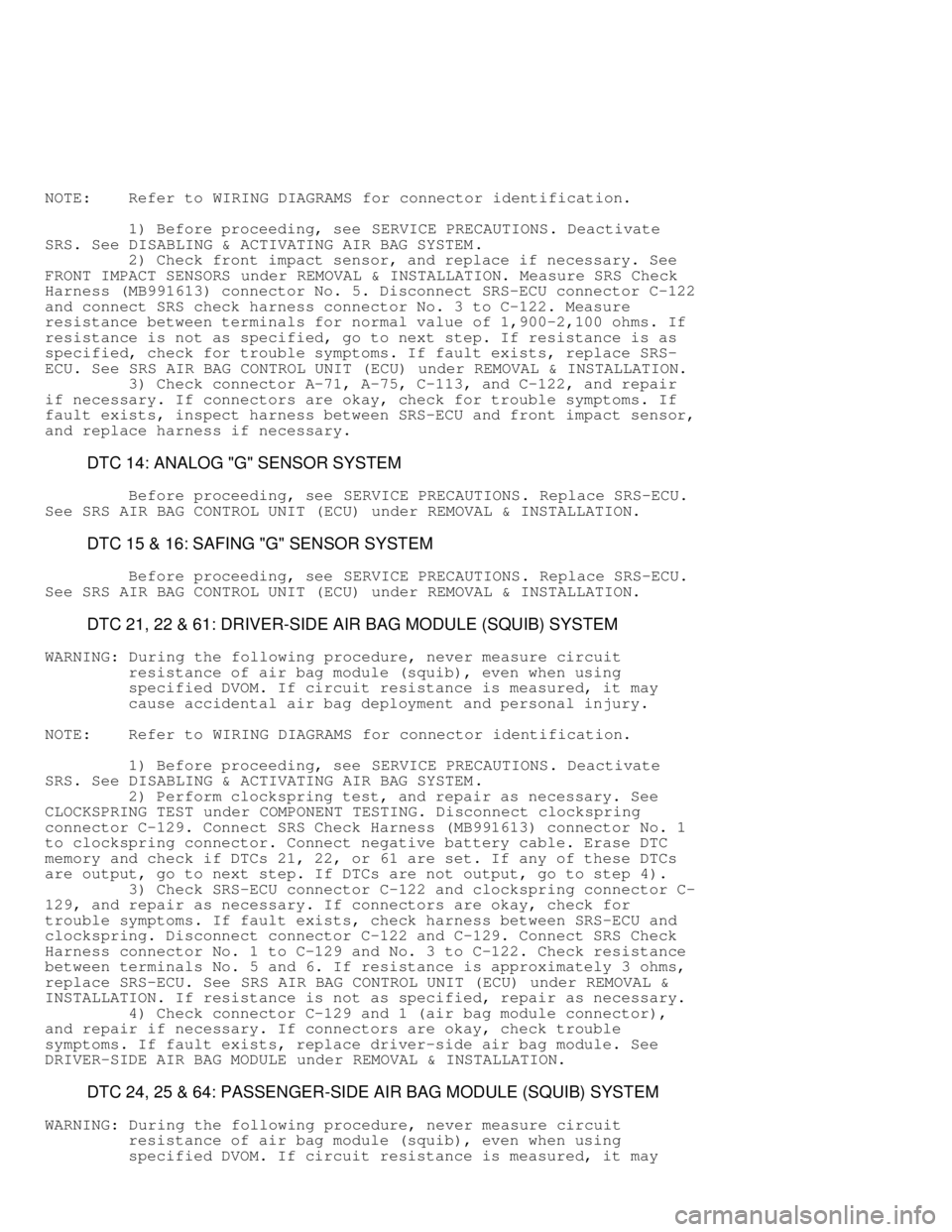
NOTE: Refer to WIRING DIAGRAMS for connector identification.
1) Before proceeding, see SERVICE PRECAUTIONS. Deactivate
SRS. See DISABLING & ACTIVATING AIR BAG SYSTEM .
2) Check front impact sensor, and replace if necessary. See
FRONT IMPACT SENSORS under REMOVAL & INSTALLATION. Measure SRS Check
Harness (MB991613) connector No. 5. Disconnect SRS-ECU connector C-122\
and connect SRS check harness connector No. 3 to C-122. Measure
resistance between terminals for normal value of 1,900-2,100 ohms. If
resistance is not as specified, go to next step. If resistance is as
specified, check for trouble symptoms. If fault exists, replace SRS-
ECU. See SRS AIR BAG CONTROL UNIT (ECU) under REMOVAL & INSTALLATION.
3) Check connector A-71, A-75, C-113, and C-122, and repair
if necessary. If connectors are okay, check for trouble symptoms. If
fault exists, inspect harness between SRS-ECU and front impact sensor,
and replace harness if necessary.
DTC 14: ANALOG "G" SENSOR SYSTEM
Before proceeding, see SERVICE PRECAUTIONS. Replace SRS-ECU.
See SRS AIR BAG CONTROL UNIT (ECU) under REMOVAL & INSTALLATION.
DTC 15 & 16: SAFING "G" SENSOR SYSTEM
Before proceeding, see SERVICE PRECAUTIONS. Replace SRS-ECU.
See SRS AIR BAG CONTROL UNIT (ECU) under REMOVAL & INSTALLATION.
DTC 21, 22 & 61: DRIVER-SIDE AIR BAG MODULE (SQUIB) SYSTEM
WARNING: During the following procedure, never measure circuit
resistance of air bag module (squib), even when using
specified DVOM. If circuit resistance is measured, it may
cause accidental air bag deployment and personal injury.
NOTE: Refer to WIRING DIAGRAMS for connector identification.
1) Before proceeding, see SERVICE PRECAUTIONS. Deactivate
SRS. See DISABLING & ACTIVATING AIR BAG SYSTEM .
2) Perform clockspring test, and repair as necessary. See
CLOCKSPRING TEST under COMPONENT TESTING. Disconnect clockspring
connector C-129. Connect SRS Check Harness (MB991613) connector No. 1
to clockspring connector. Connect negative battery cable. Erase DTC
memory and check if DTCs 21, 22, or 61 are set. If any of these DTCs
are output, go to next step. If DTCs are not output, go to step 4).
3) Check SRS-ECU connector C-122 and clockspring connector C-
129, and repair as necessary. If connectors are okay, check for
trouble symptoms. If fault exists, check harness between SRS-ECU and
clockspring. Disconnect connector C-122 and C-129. Connect SRS Check
Harness connector No. 1 to C-129 and No. 3 to C-122. Check resistance
between terminals No. 5 and 6. If resistance is approximately 3 ohms,
replace SRS-ECU. See SRS AIR BAG CONTROL UNIT (ECU) under REMOVAL &
INSTALLATION. If resistance is not as specified, repair as necessary.
4) Check connector C-129 and 1 (air bag module connector),
and repair if necessary. If connectors are okay, check trouble
symptoms. If fault exists, replace driver-side air bag module. See
DRIVER-SIDE AIR BAG MODULE under REMOVAL & INSTALLATION.
DTC 24, 25 & 64: PASSENGER-SIDE AIR BAG MODULE (SQUIB) SYSTEM
WARNING: During the following procedure, never measure circuit
resistance of air bag module (squib), even when using
specified DVOM. If circuit resistance is measured, it may
Page 179 of 1501
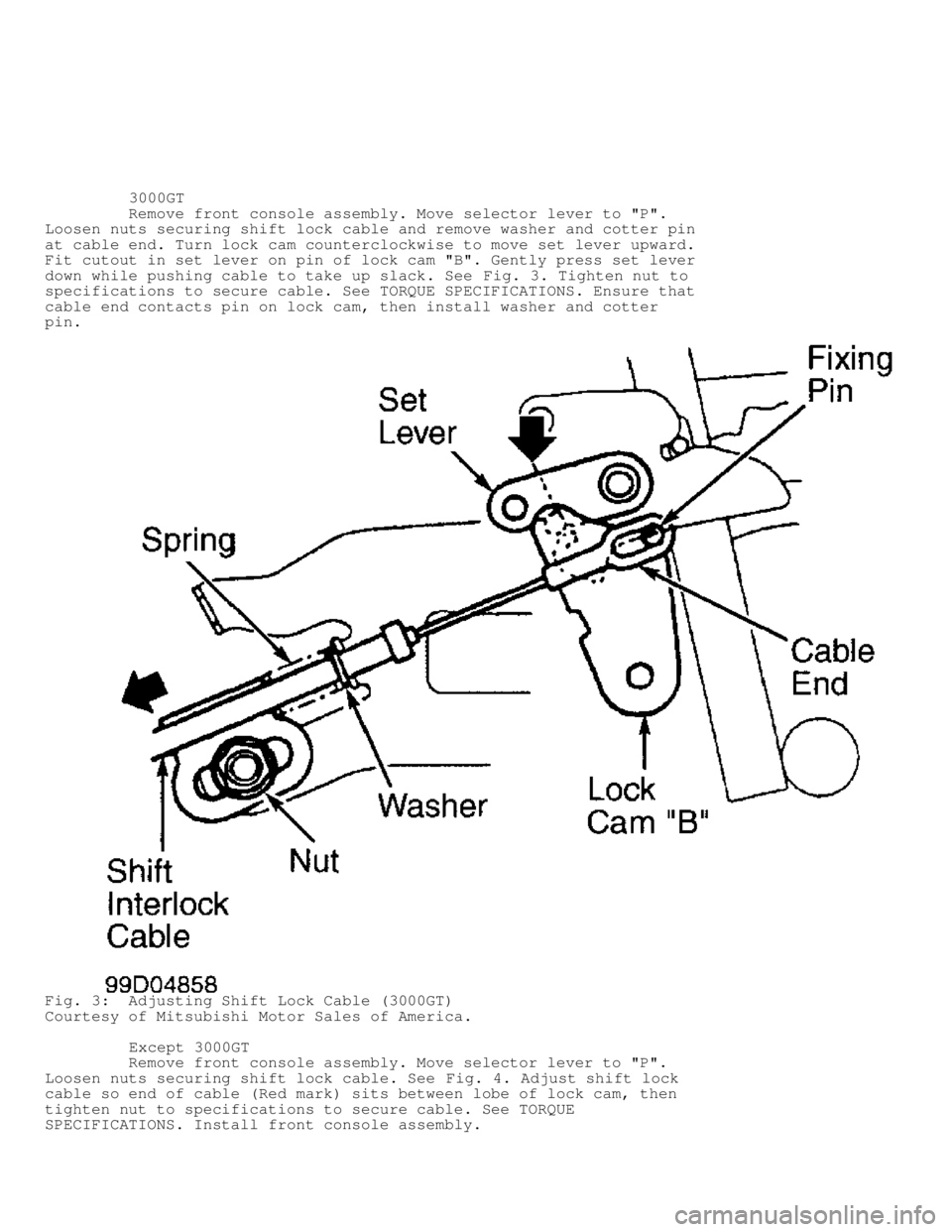
3000GT
Remove front console assembly. Move selector lever to "P".
Loosen nuts securing shift lock cable and remove washer and cotter pin
at cable end. Turn lock cam counterclockwise to move set lever upward.
Fit cutout in set lever on pin of lock cam "B". Gently press set lever
down while pushing cable to take up slack. See Fig. 3. Tighten nut to
specifications to secure cable. See TORQUE SPECIFICATIONS. Ensure that
cable end contacts pin on lock cam, then install washer and cotter
pin.
Fig. 3: Adjusting Shift Lock Cable (3000GT)
Courtesy of Mitsubishi Motor Sales of America.
Except 3000GT
Remove front console assembly. Move selector lever to "P".
Loosen nuts securing shift lock cable. See Fig. 4. Adjust shift lock
cable so end of cable (Red mark) sits between lobe of lock cam, then
tighten nut to specifications to secure cable. See TORQUE
SPECIFICATIONS. Install front console assembly.
Page 339 of 1501
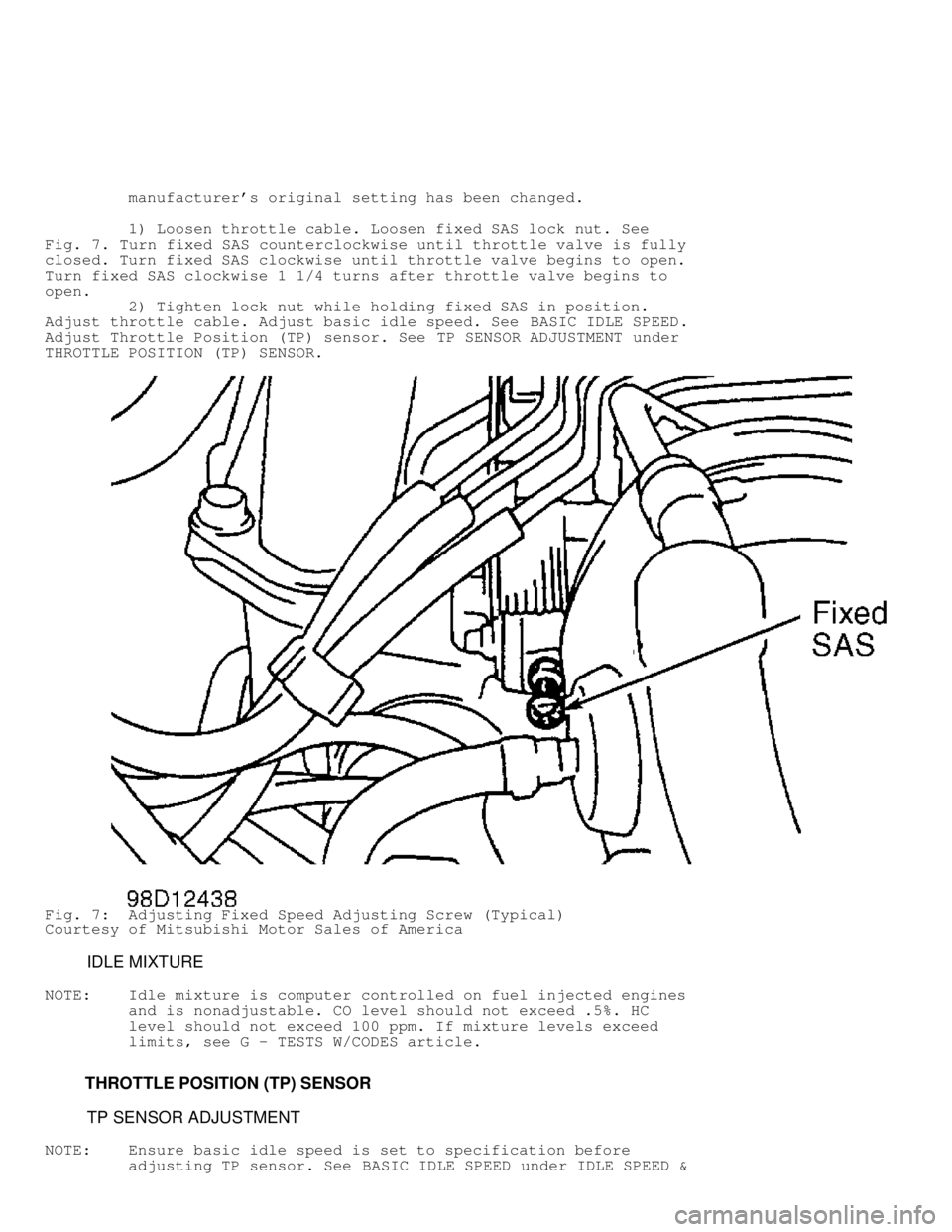
manufacturer's original setting has been changed.
1) Loosen throttle cable. Loosen fixed SAS lock nut. See
Fig. 7. Turn fixed SAS counterclockwise until throttle valve is fully
closed. Turn fixed SAS clockwise until throttle valve begins to open.
Turn fixed SAS clockwise 1 1/4 turns after throttle valve begins to
open.
2) Tighten lock nut while holding fixed SAS in position.
Adjust throttle cable. Adjust basic idle speed. See BASIC IDLE SPEED.
Adjust Throttle Position (TP) sensor. See TP SENSOR ADJUSTMENT under
THROTTLE POSITION (TP) SENSOR.
Fig. 7: Adjusting Fixed Speed Adjusting Screw (Typical)
Courtesy of Mitsubishi Motor Sales of America
IDLE MIXTURE
NOTE: Idle mixture is computer controlled on fuel injected engines
and is nonadjustable. CO level should not exceed .5%. HC
level should not exceed 100 ppm. If mixture levels exceed
limits, see G - TESTS W/CODES article.
THROTTLE POSITION (TP) SENSOR
TP SENSOR ADJUSTMENT
NOTE: Ensure basic idle speed is set to specification before
adjusting TP sensor. See BASIC IDLE SPEED under IDLE SPEED &
Page 806 of 1501
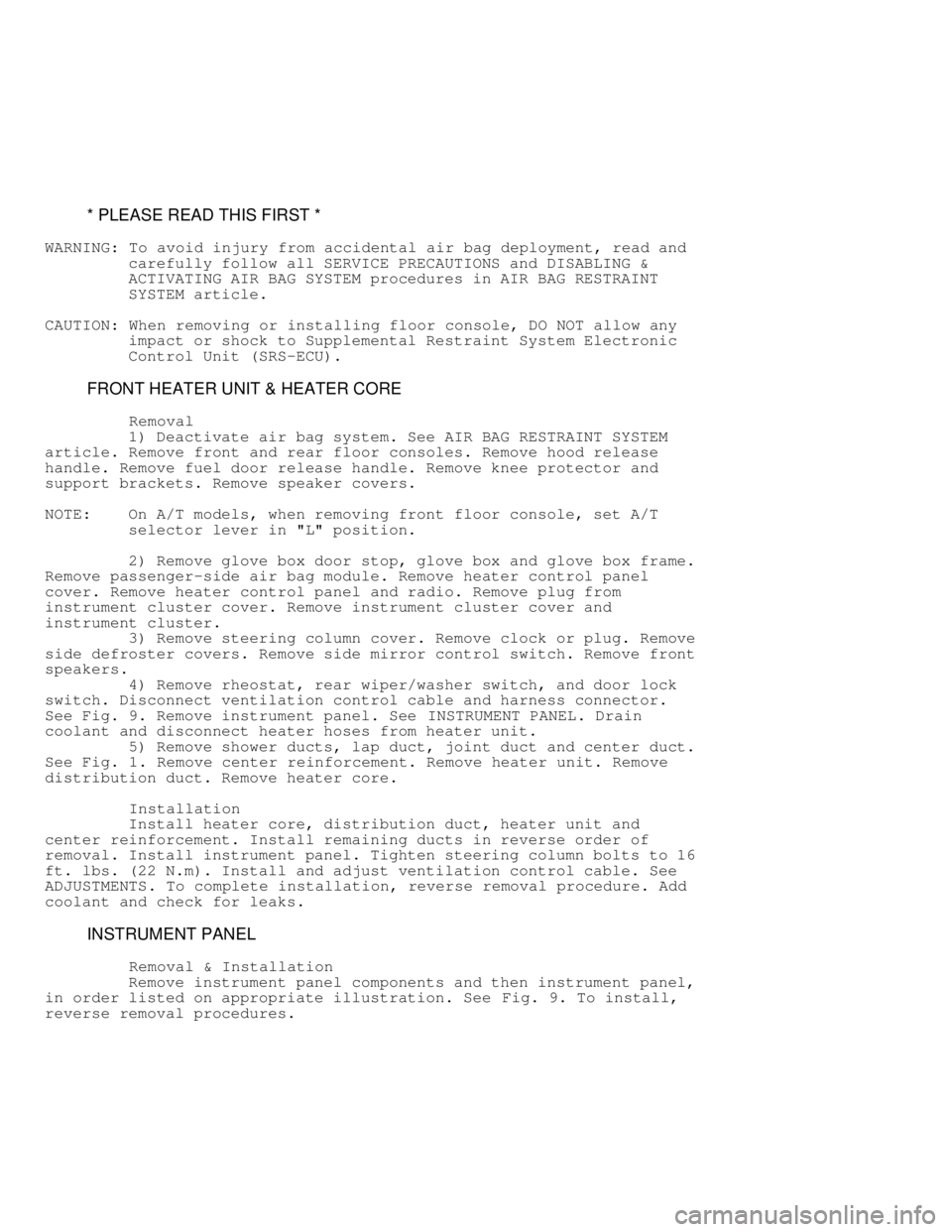
* PLEASE READ THIS FIRST *
WARNING: To avoid injury from accidental air bag deployment, read and
carefully follow all SERVICE PRECAUTIONS and DISABLING &
ACTIVATING AIR BAG SYSTEM procedures in AIR BAG RESTRAINT
SYSTEM article.
CAUTION: When removing or installing floor console, DO NOT allow any
impact or shock to Supplemental Restraint System Electronic
Control Unit (SRS-ECU).
FRONT HEATER UNIT & HEATER CORE
Removal
1) Deactivate air bag system. See AIR BAG RESTRAINT SYSTEM
article. Remove front and rear floor consoles. Remove hood release
handle. Remove fuel door release handle. Remove knee protector and
support brackets. Remove speaker covers.
NOTE: On A/T models, when removing front floor console, set A/T
selector lever in "L" position.
2) Remove glove box door stop, glove box and glove box frame.
Remove passenger-side air bag module. Remove heater control panel
cover. Remove heater control panel and radio. Remove plug from
instrument cluster cover. Remove instrument cluster cover and
instrument cluster.
3) Remove steering column cover. Remove clock or plug. Remove
side defroster covers. Remove side mirror control switch. Remove front
speakers.
4) Remove rheostat, rear wiper/washer switch, and door lock
switch. Disconnect ventilation control cable and harness connector.
See Fig. 9. Remove instrument panel. See INSTRUMENT PANEL. Drain
coolant and disconnect heater hoses from heater unit.
5) Remove shower ducts, lap duct, joint duct and center duct.
See Fig. 1 . Remove center reinforcement. Remove heater unit. Remove
distribution duct. Remove heater core.
Installation
Install heater core, distribution duct, heater unit and
center reinforcement. Install remaining ducts in reverse order of
removal. Install instrument panel. Tighten steering column bolts to 16
ft. lbs. (22 N.m). Install and adjust ventilation control cable. See
ADJUSTMENTS . To complete installation, reverse removal procedure. Add
coolant and check for leaks.
INSTRUMENT PANEL
Removal & Installation
Remove instrument panel components and then instrument panel,
in order listed on appropriate illustration. See Fig. 9. To install,
reverse removal procedures.
Page 1160 of 1501
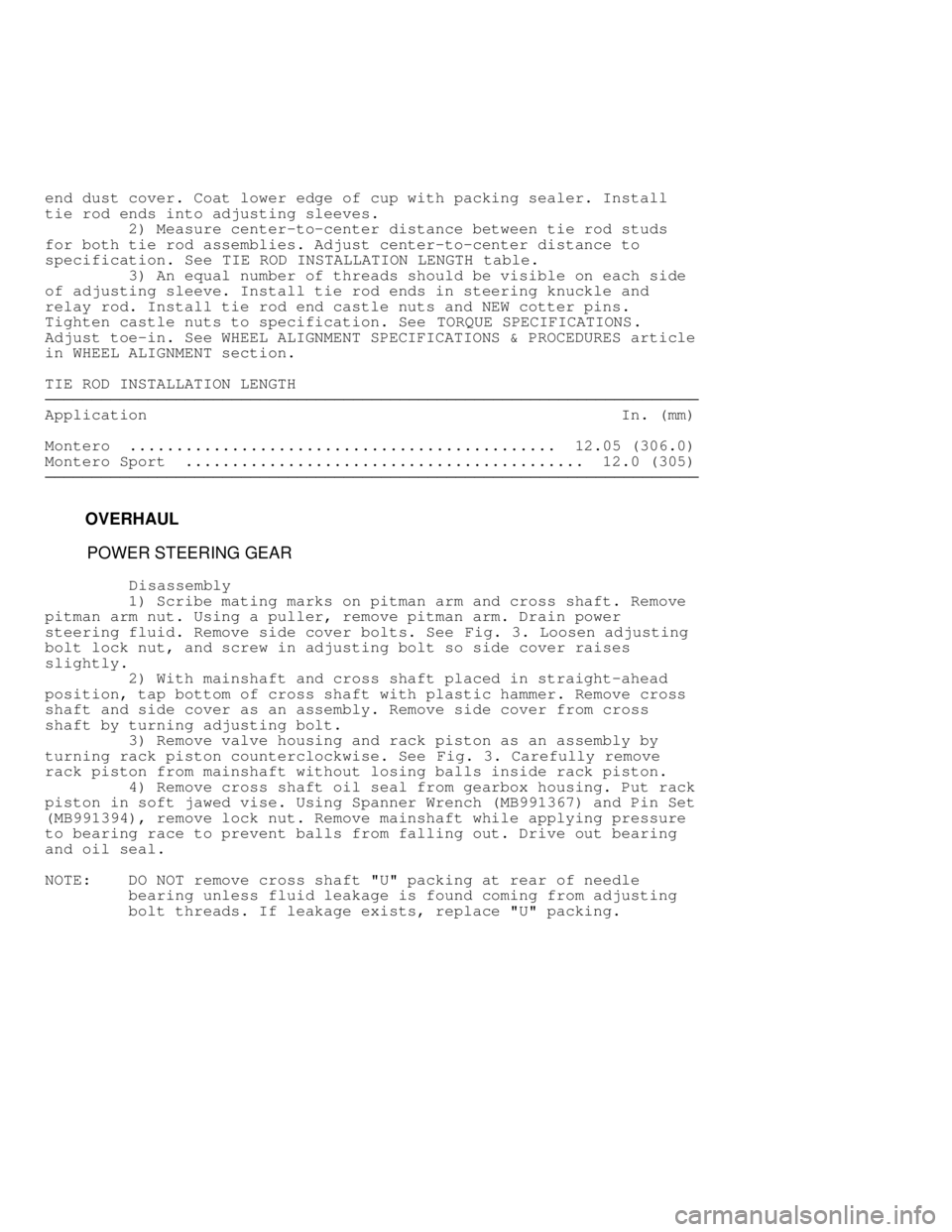
end dust cover. Coat lower edge of cup with packing sealer. Install
tie rod ends into adjusting sleeves.
2) Measure center-to-center distance between tie rod studs
for both tie rod assemblies. Adjust center-to-center distance to
specification. See TIE ROD INSTALLATION LENGTH table.
3) An equal number of threads should be visible on each side
of adjusting sleeve. Install tie rod ends in steering knuckle and
relay rod. Install tie rod end castle nuts and NEW cotter pins.
Tighten castle nuts to specification. See TORQUE SPECIFICATIONS.
Adjust toe-in. See WHEEL ALIGNMENT SPECIFICATIONS & PROCEDURES article
in WHEEL ALIGNMENT section.
TIE ROD INSTALLATION LENGTH
\
\
\
\
\
\
\
Application In. (mm)\
Montero .............................................. 12.05 (306.0)\
Montero Sport ........................................... 12.0 (305)\
\
\
\
\
\
\
\
OVERHAUL
POWER STEERING GEAR
Disassembly
1) Scribe mating marks on pitman arm and cross shaft. Remove
pitman arm nut. Using a puller, remove pitman arm. Drain power
steering fluid. Remove side cover bolts. See Fig. 3. Loosen adjusting
bolt lock nut, and screw in adjusting bolt so side cover raises
slightly.
2) With mainshaft and cross shaft placed in straight-ahead
position, tap bottom of cross shaft with plastic hammer. Remove cross
shaft and side cover as an assembly. Remove side cover from cross
shaft by turning adjusting bolt.
3) Remove valve housing and rack piston as an assembly by
turning rack piston counterclockwise. See Fig. 3. Carefully remove
rack piston from mainshaft without losing balls inside rack piston.
4) Remove cross shaft oil seal from gearbox housing. Put rack
piston in soft jawed vise. Using Spanner Wrench (MB991367) and Pin Set\
(MB991394), remove lock nut. Remove mainshaft while applying pressure
to bearing race to prevent balls from falling out. Drive out bearing
and oil seal.
NOTE: DO NOT remove cross shaft "U" packing at rear of needle
bearing unless fluid leakage is found coming from adjusting
bolt threads. If leakage exists, replace "U" packing.