sensor RENAULT ESPACE 2000 J66 / 3.G Technical Note 3426A Workshop Manual
[x] Cancel search | Manufacturer: RENAULT, Model Year: 2000, Model line: ESPACE, Model: RENAULT ESPACE 2000 J66 / 3.GPages: 52, PDF Size: 0.98 MB
Page 24 of 52
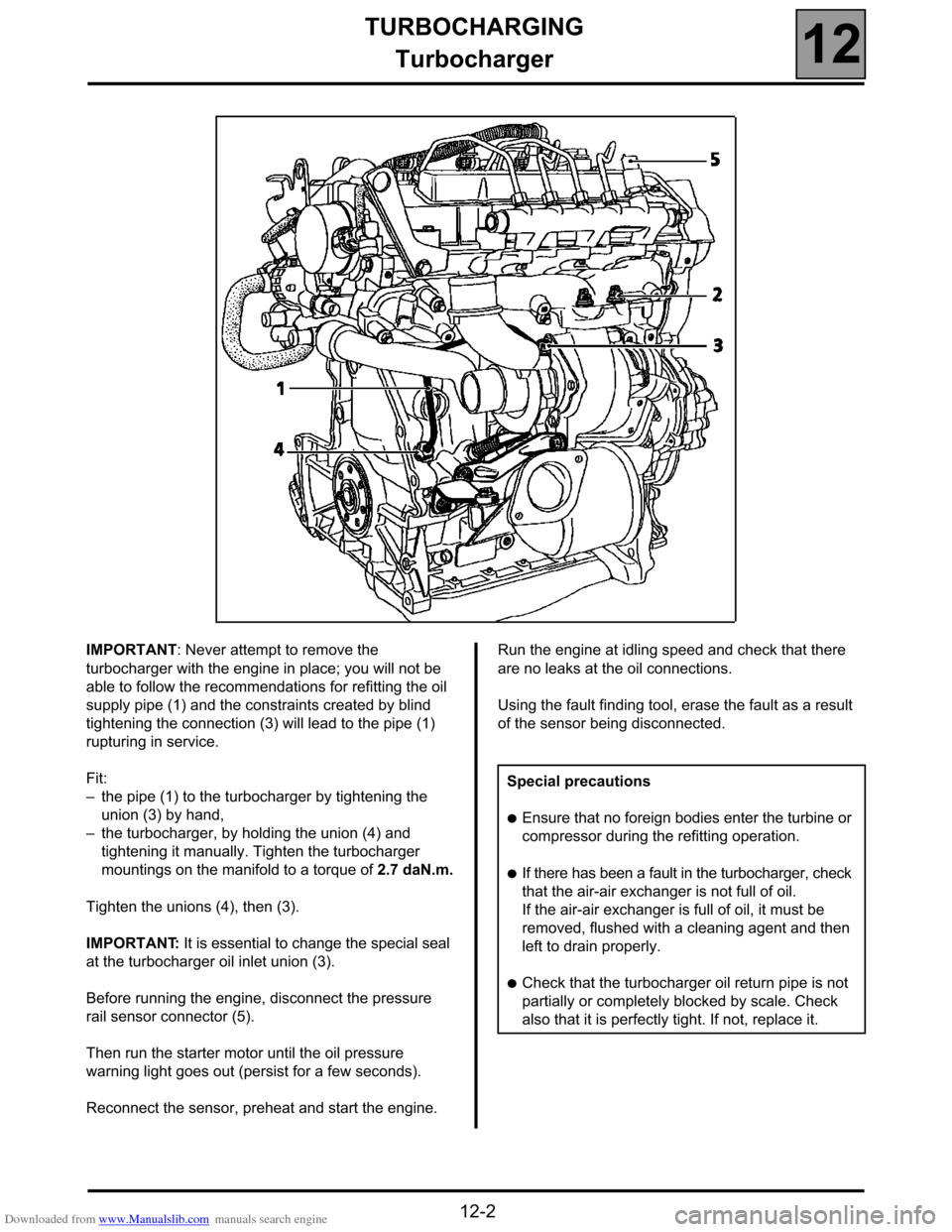
Downloaded from www.Manualslib.com manuals search engine TURBOCHARGING
Turbocharger
12
12-2
IMPORTANT: Never attempt to remove the
turbocharger with the engine in place; you will not be
able to follow the recommendations for refitting the oil
supply pipe (1) and the constraints created by blind
tightening the connection (3) will lead to the pipe (1)
rupturing in service.
Fit:
–the pipe (1) to the turbocharger by tightening the
union (3) by hand,
–the turbocharger, by holding the union (4) and
tightening it manually. Tighten the turbocharger
mountings on the manifold to a torque of 2.7 daN.m.
Tighten the unions (4), then (3).
IMPORTANT: It is essential to change the special seal
at the turbocharger oil inlet union (3).
Before running the engine, disconnect the pressure
rail sensor connector (5).
Then run the starter motor until the oil pressure
warning light goes out (persist for a few seconds).
Reconnect the sensor, preheat and start the engine.Run the engine at idling speed and check that there
are no leaks at the oil connections.
Using the fault finding tool, erase the fault as a result
of the sensor being disconnected.
Special precautions
●Ensure that no foreign bodies enter the turbine or
compressor during the refitting operation.
●If there has been a fault in the turbocharger, check
that the air-air exchanger is not full of oil.
If the air-air exchanger is full of oil, it must be
removed, flushed with a cleaning agent and then
left to drain properly.
●Check that the turbocharger oil return pipe is not
partially or completely blocked by scale. Check
also that it is perfectly tight. If not, replace it.
Page 45 of 52
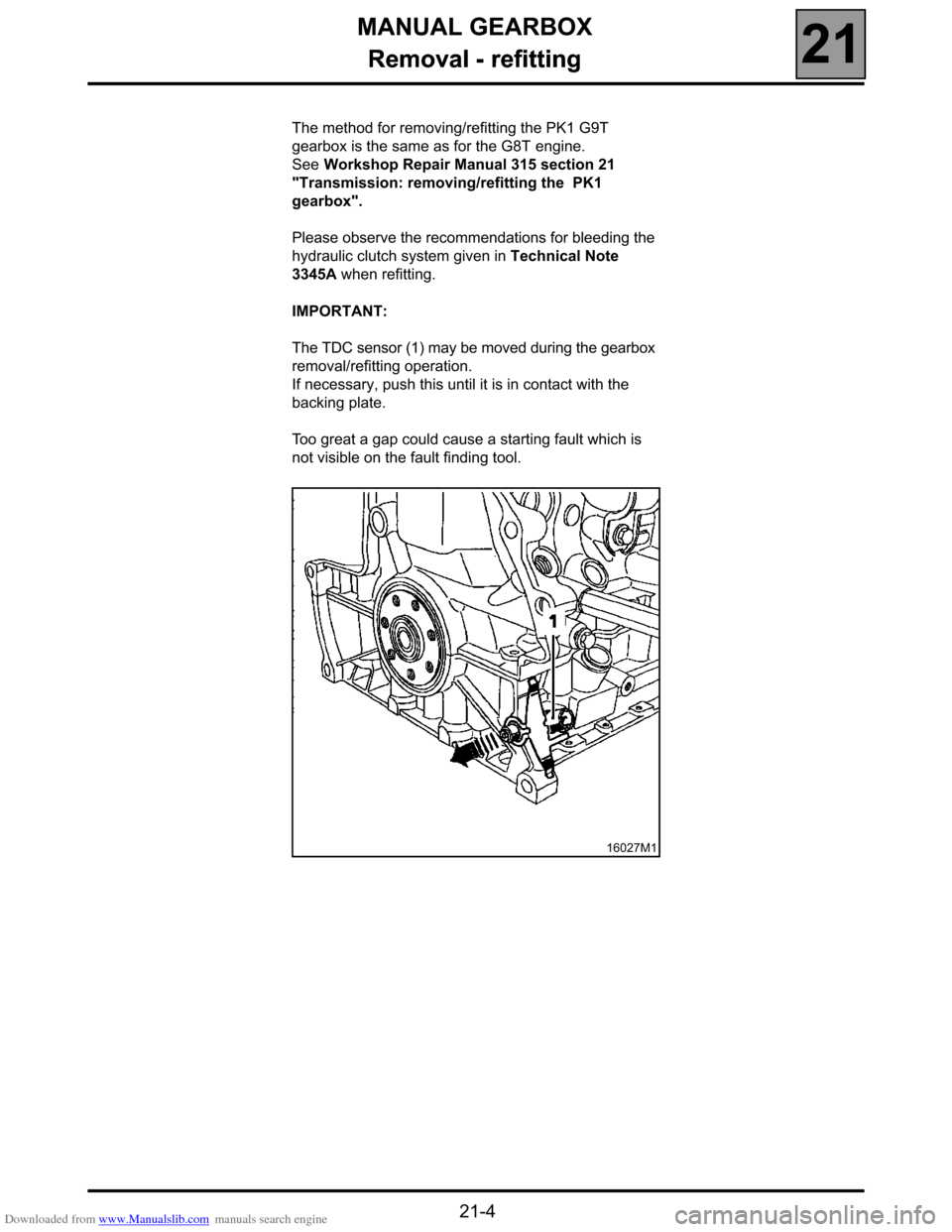
Downloaded from www.Manualslib.com manuals search engine MANUAL GEARBOX
Removal - refitting
21
21-4
Removal - refitting
The method for removing/refitting the PK1 G9T
gearbox is the same as for the G8T engine.
See Workshop Repair Manual 315 section 21
"Transmission: removing/refitting the PK1
gearbox".
Please observe the recommendations for bleeding the
hydraulic clutch system given in Technical Note
3345A when refitting.
IMPORTANT:
The TDC sensor (1) may be moved during the gearbox
removal/refitting operation.
If necessary, push this until it is in contact with the
backing plate.
Too great a gap could cause a starting fault which is
not visible on the fault finding tool.
16027M1
Page 47 of 52
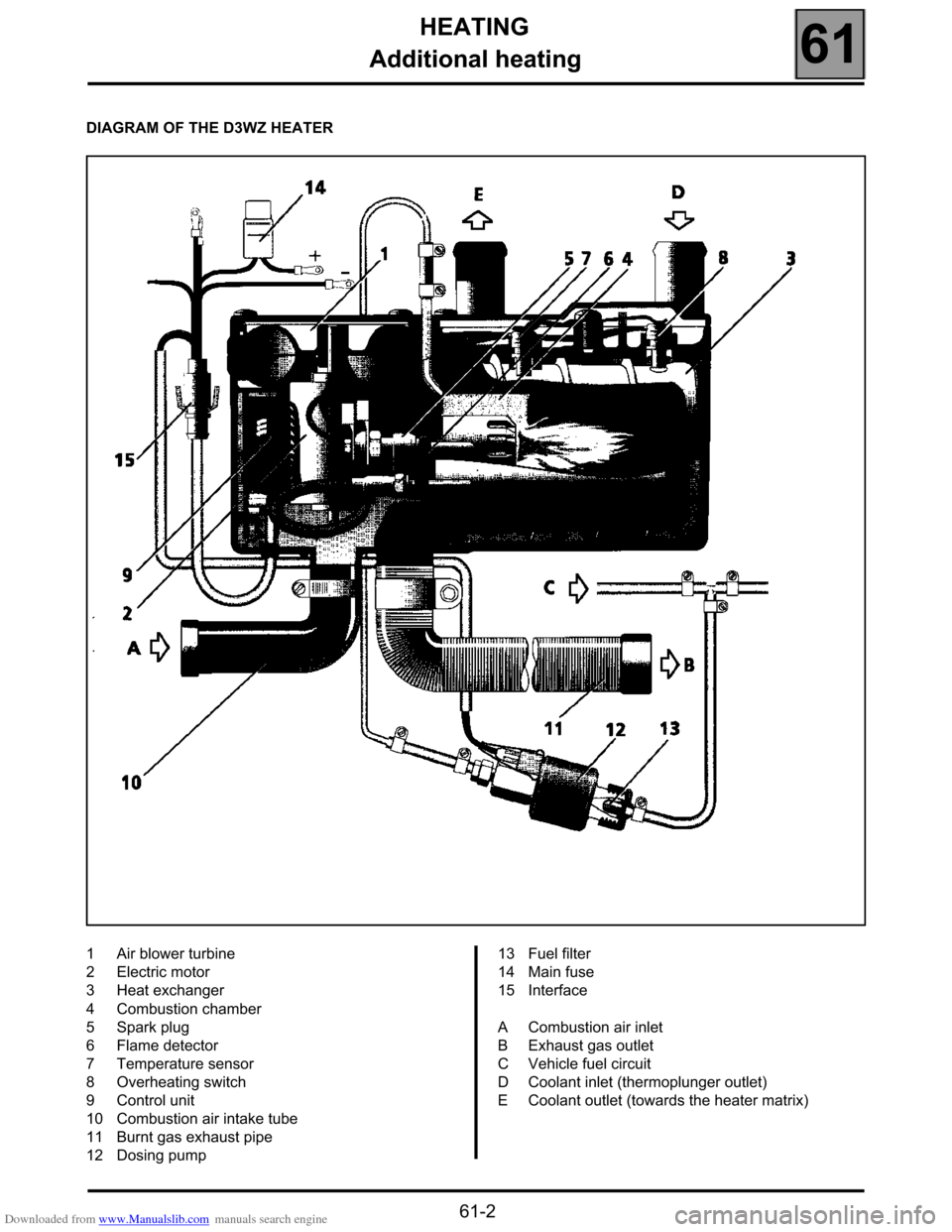
Downloaded from www.Manualslib.com manuals search engine HEATING
Additional heating
61
61-2
DIAGRAM OF THE D3WZ HEATER
1Air blower turbine
2Electric motor
3Heat exchanger
4Combustion chamber
5Spark plug
6Flame detector
7Temperature sensor
8Overheating switch
9Control unit
10 Combustion air intake tube
11 Burnt gas exhaust pipe
12 Dosing pump 13 Fuel filter
14 Main fuse
15 Interface
ACombustion air inlet
BExhaust gas outlet
CVehicle fuel circuit
DCoolant inlet (thermoplunger outlet)
ECoolant outlet (towards the heater matrix)
Page 48 of 52
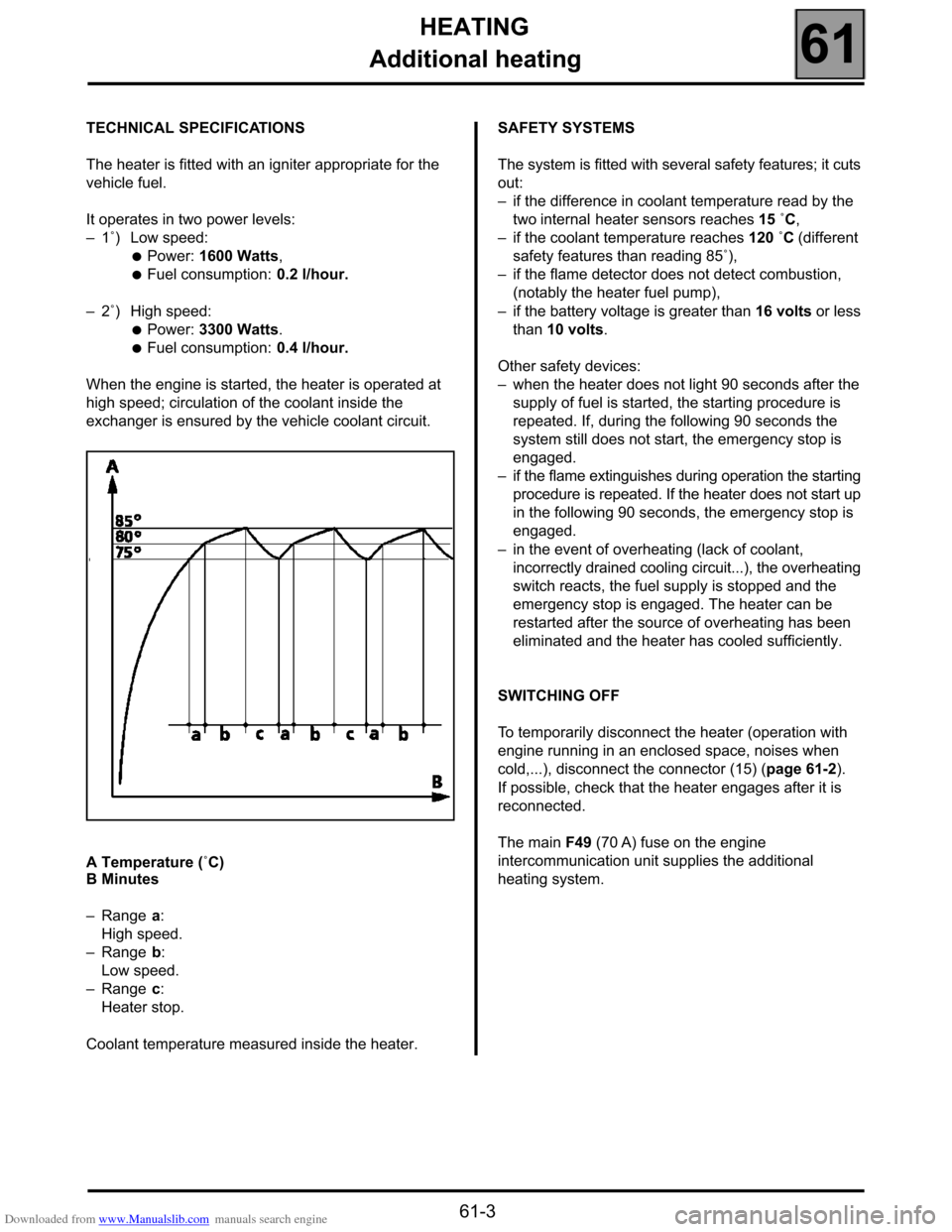
Downloaded from www.Manualslib.com manuals search engine HEATING
Additional heating
61
61-3
TECHNICAL SPECIFICATIONS
The heater is fitted with an igniter appropriate for the
vehicle fuel.
It operates in two power levels:
–1˚) Low speed:
●Power: 1600 Watts,
●Fuel consumption: 0.2 l/hour.
–2˚) High speed:
●Power: 3300 Watts.
●Fuel consumption: 0.4 l/hour.
When the engine is started, the heater is operated at
high speed; circulation of the coolant inside the
exchanger is ensured by the vehicle coolant circuit.
A Temperature (˚C)
B Minutes
–Range a:
High speed.
–Range b:
Low speed.
–Range c:
Heater stop.
Coolant temperature measured inside the heater.SAFETY SYSTEMS
The system is fitted with several safety features; it cuts
out:
–if the difference in coolant temperature read by the
two internal heater sensors reaches 15 ˚C,
–if the coolant temperature reaches 120 ˚C (different
safety features than reading 85˚),
–if the flame detector does not detect combustion,
(notably the heater fuel pump),
–if the battery voltage is greater than 16 volts or less
than 10 volts.
Other safety devices:
–when the heater does not light 90 seconds after the
supply of fuel is started, the starting procedure is
repeated. If, during the following 90 seconds the
system still does not start, the emergency stop is
engaged.
–if the flame extinguishes during operation the starting
procedure is repeated. If the heater does not start up
in the following 90 seconds, the emergency stop is
engaged.
–in the event of overheating (lack of coolant,
incorrectly drained cooling circuit...), the overheating
switch reacts, the fuel supply is stopped and the
emergency stop is engaged. The heater can be
restarted after the source of overheating has been
eliminated and the heater has cooled sufficiently.
SWITCHING OFF
To temporarily disconnect the heater (operation with
engine running in an enclosed space, noises when
cold,...), disconnect the connector (15) (page 61-2).
If possible, check that the heater engages after it is
reconnected.
The main F49 (70 A) fuse on the engine
intercommunication unit supplies the additional
heating system.
Page 51 of 52
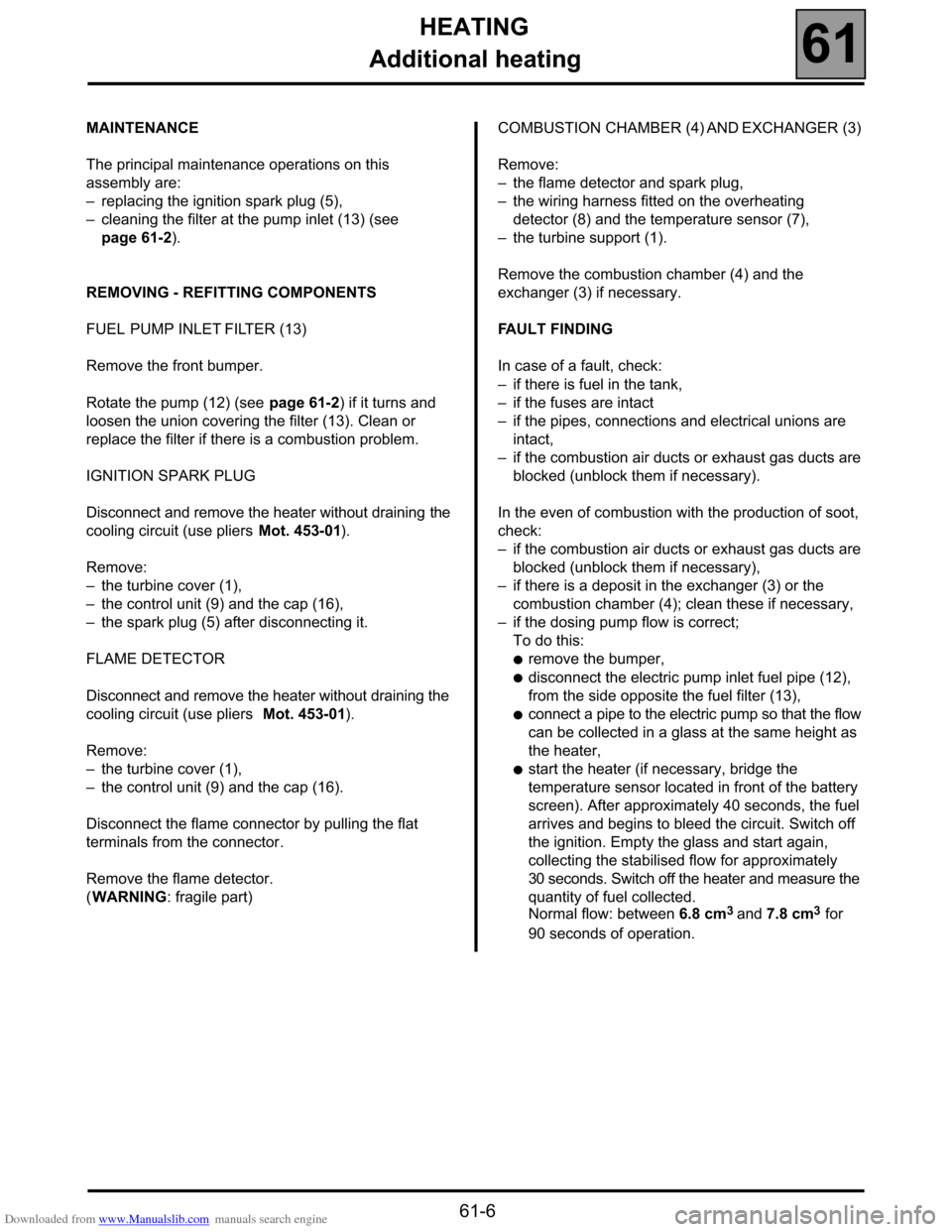
Downloaded from www.Manualslib.com manuals search engine HEATING
Additional heating
61
61-6
MAINTENANCE
The principal maintenance operations on this
assembly are:
–replacing the ignition spark plug (5),
–cleaning the filter at the pump inlet (13) (see
page 61-2).
REMOVING - REFITTING COMPONENTS
FUEL PUMP INLET FILTER (13)
Remove the front bumper.
Rotate the pump (12) (see page 61-2) if it turns and
loosen the union covering the filter (13). Clean or
replace the filter if there is a combustion problem.
IGNITION SPARK PLUG
Disconnect and remove the heater without draining the
cooling circuit (use pliers Mot. 453-01).
Remove:
–the turbine cover (1),
–the control unit (9) and the cap (16),
–the spark plug (5) after disconnecting it.
FLAME DETECTOR
Disconnect and remove the heater without draining the
cooling circuit (use pliers Mot. 453-01).
Remove:
–the turbine cover (1),
–the control unit (9) and the cap (16).
Disconnect the flame connector by pulling the flat
terminals from the connector.
Remove the flame detector.
(WARNING: fragile part)COMBUSTION CHAMBER (4) AND EXCHANGER (3)
Remove:
–the flame detector and spark plug,
–the wiring harness fitted on the overheating
detector (8) and the temperature sensor (7),
–the turbine support (1).
Remove the combustion chamber (4) and the
exchanger (3) if necessary.
FAULT FINDING
In case of a fault, check:
–if there is fuel in the tank,
–if the fuses are intact
–if the pipes, connections and electrical unions are
intact,
–if the combustion air ducts or exhaust gas ducts are
blocked (unblock them if necessary).
In the even of combustion with the production of soot,
check:
–if the combustion air ducts or exhaust gas ducts are
blocked (unblock them if necessary),
–if there is a deposit in the exchanger (3) or the
combustion chamber (4); clean these if necessary,
–if the dosing pump flow is correct;
To do this:
●remove the bumper,
●disconnect the electric pump inlet fuel pipe (12),
from the side opposite the fuel filter (13),
●connect a pipe to the electric pump so that the flow
can be collected in a glass at the same height as
the heater,
●start the heater (if necessary, bridge the
temperature sensor located in front of the battery
screen). After approximately 40 seconds, the fuel
arrives and begins to bleed the circuit. Switch off
the ignition. Empty the glass and start again,
collecting the stabilised flow for approximately
30 seconds. Switch off the heater and measure the
quantity of fuel collected.
Normal flow: between 6.8 cm
3 and 7.8 cm3 for
90 seconds of operation.
Page 52 of 52
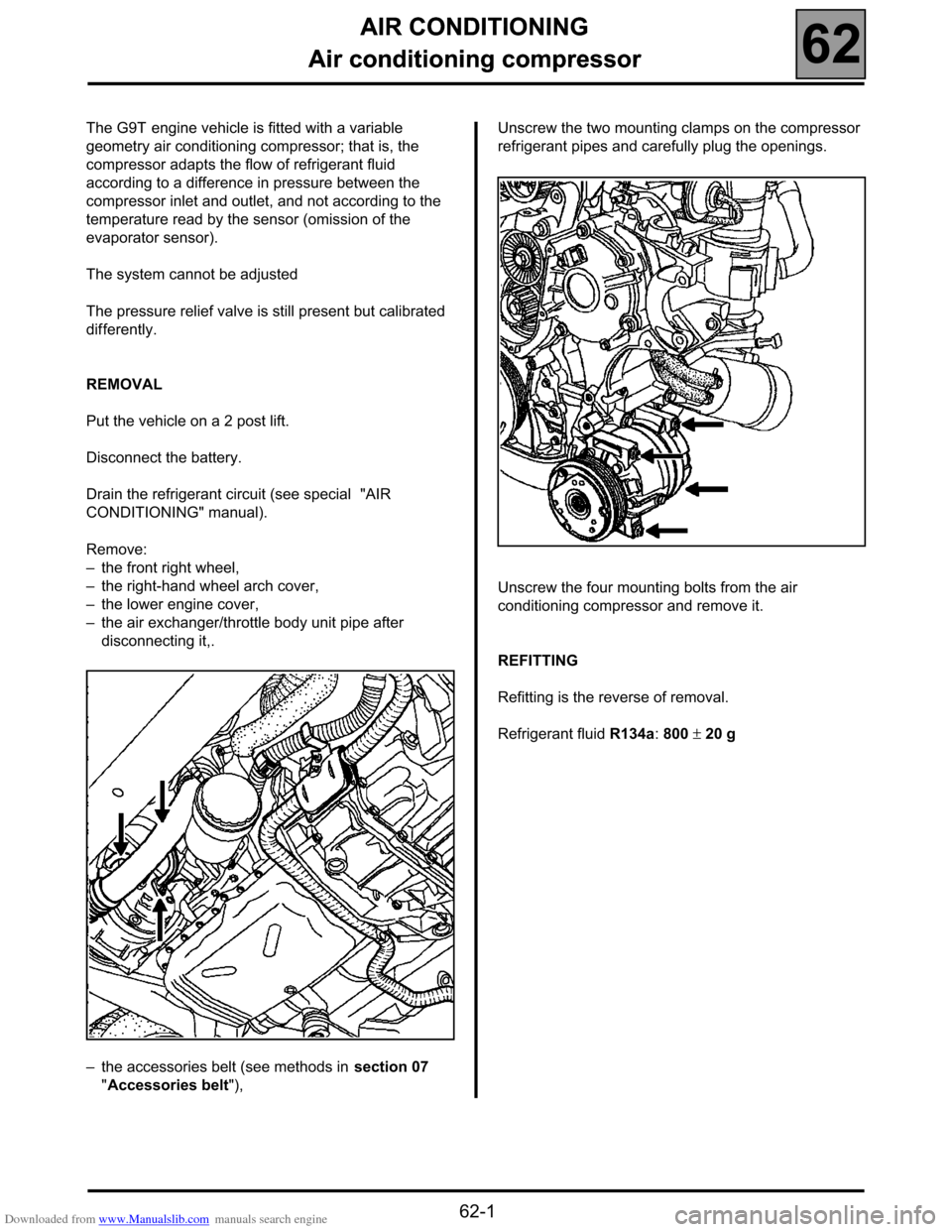
Downloaded from www.Manualslib.com manuals search engine AIR CONDITIONING
Air conditioning compressor
62
62-1
662AIR CONDITIONING
Air conditioning compressor
The G9T engine vehicle is fitted with a variable
geometry air conditioning compressor; that is, the
compressor adapts the flow of refrigerant fluid
according to a difference in pressure between the
compressor inlet and outlet, and not according to the
temperature read by the sensor (omission of the
evaporator sensor).
The system cannot be adjusted
The pressure relief valve is still present but calibrated
differently.
REMOVAL
Put the vehicle on a 2 post lift.
Disconnect the battery.
Drain the refrigerant circuit (see special "AIR
CONDITIONING" manual).
Remove:
–the front right wheel,
–the right-hand wheel arch cover,
–the lower engine cover,
–the air exchanger/throttle body unit pipe after
disconnecting it,.
–the accessories belt (see methods in section 07
"Accessories belt"),Unscrew the two mounting clamps on the compressor
refrigerant pipes and carefully plug the openings.
Unscrew the four mounting bolts from the air
conditioning compressor and remove it.
REFITTING
Refitting is the reverse of removal.
Refrigerant fluid R134a: 800 ± 20 g