wheel torque RENAULT SCENIC 2010 J95 / 3.G Petrol Injection S3000 Injection Workshop Manual
[x] Cancel search | Manufacturer: RENAULT, Model Year: 2010, Model line: SCENIC, Model: RENAULT SCENIC 2010 J95 / 3.GPages: 230, PDF Size: 0.92 MB
Page 29 of 230
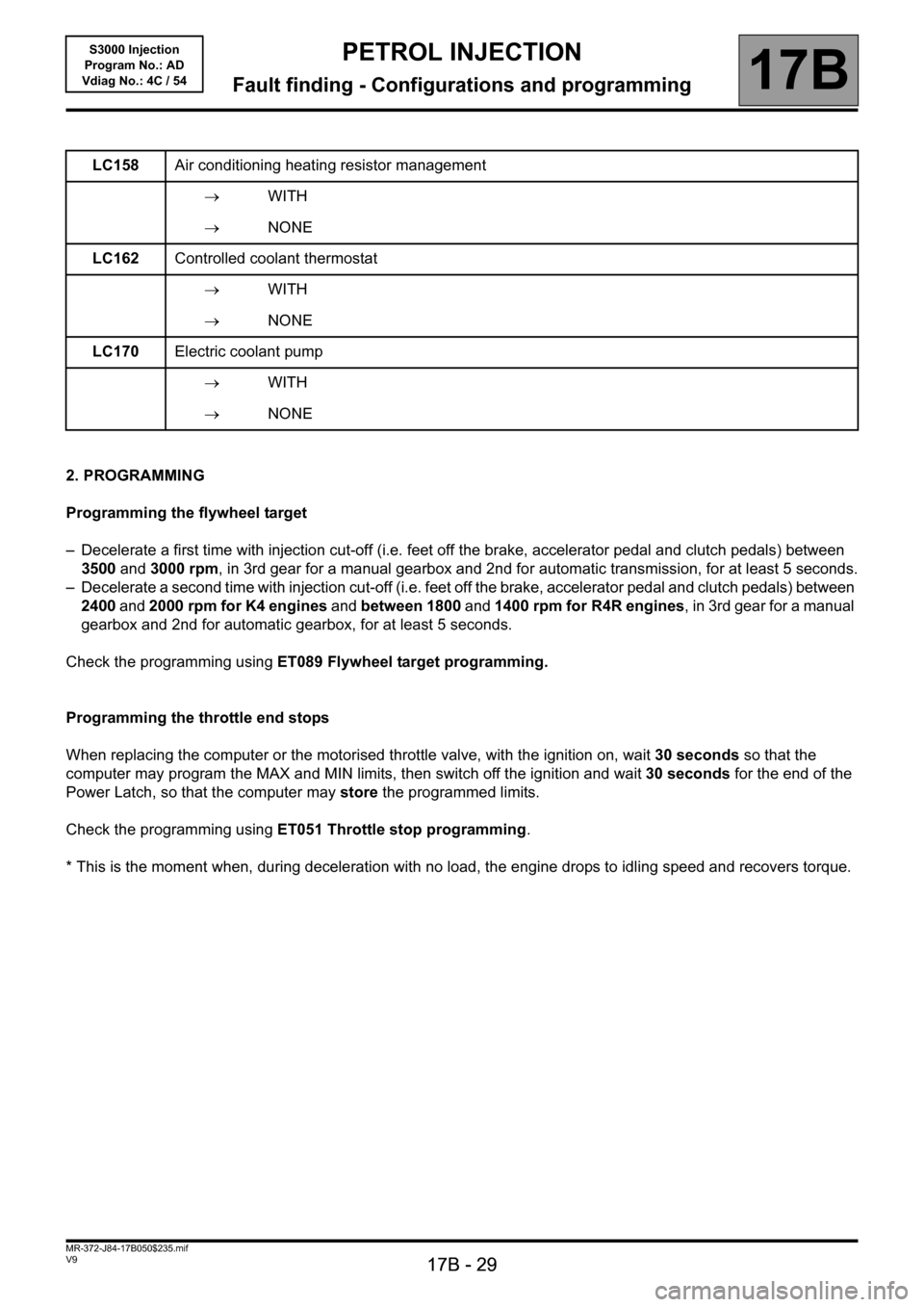
PETROL INJECTION
Fault finding - Configurations and programming17B
17B - 29
17B
17B - 29V9 MR-372-J84-17B050$235.mif
S3000 Injection
Program No.: AD
Vdiag No.: 4C / 54
2. PROGRAMMING
Programming the flywheel target
– Decelerate a first time with injection cut-off (i.e. feet off the brake, accelerator pedal and clutch pedals) between
3500 and 3000 rpm, in 3rd gear for a manual gearbox and 2nd for automatic transmission, for at least 5 seconds.
– Decelerate a second time with injection cut-off (i.e. feet off the brake, accelerator pedal and clutch pedals) between
2400 and 2000 rpm for K4 engines and between 1800 and 1400 rpm for R4R engines, in 3rd gear for a manual
gearbox and 2nd for automatic gearbox, for at least 5 seconds.
Check the programming using ET089 Flywheel target programming.
Programming the throttle end stops
When replacing the computer or the motorised throttle valve, with the ignition on, wait 30 seconds so that the
computer may program the MAX and MIN limits, then switch off the ignition and wait 30 seconds for the end of the
Power Latch, so that the computer may store the programmed limits.
Check the programming using ET051 Throttle stop programming.
* This is the moment when, during deceleration with no load, the engine drops to idling speed and recovers torque. LC158Air conditioning heating resistor management
→WITH
→NONE
LC162Controlled coolant thermostat
→WITH
→NONE
LC170Electric coolant pump
→WITH
→NONE
Page 88 of 230
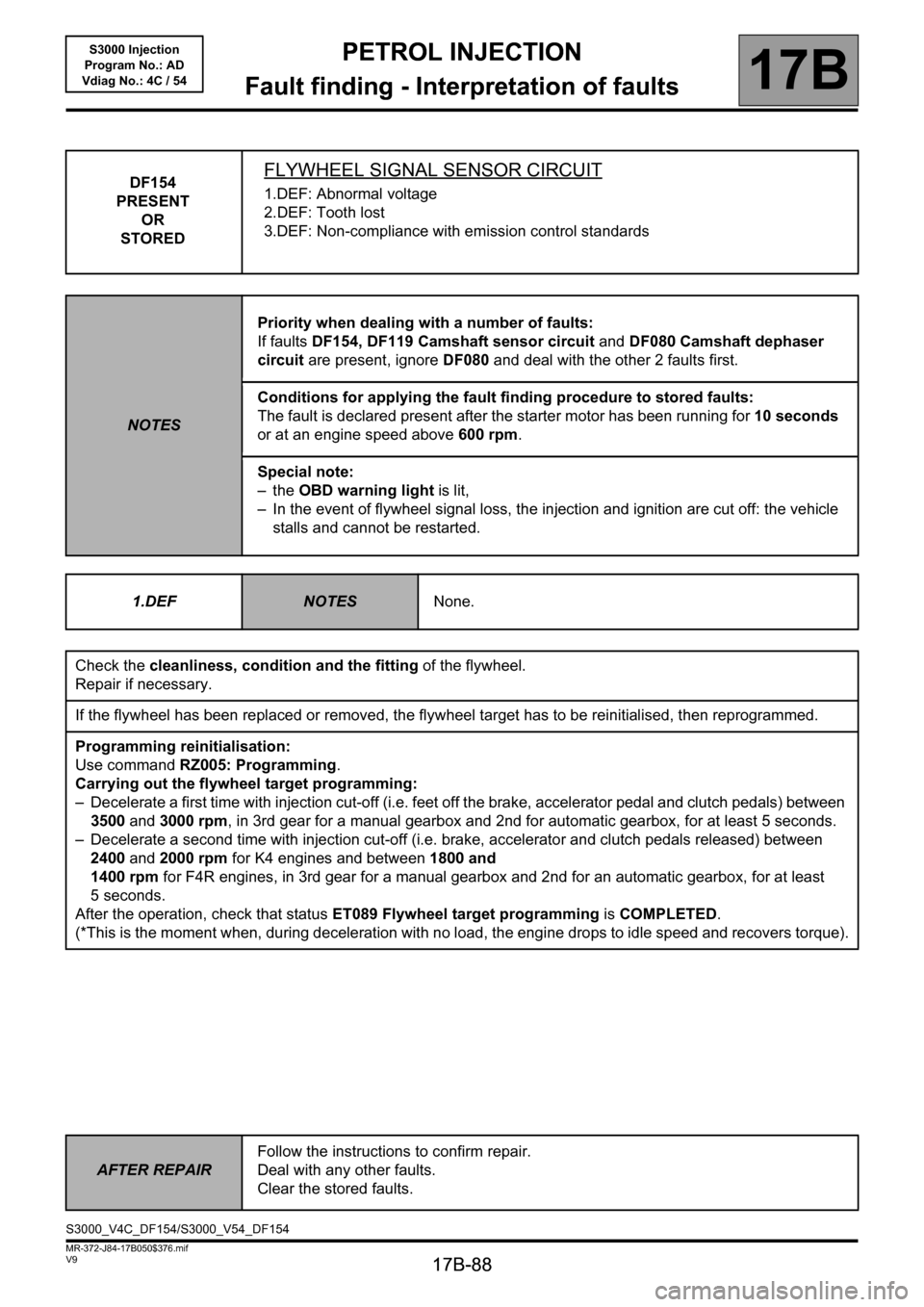
PETROL INJECTION
Fault finding - Interpretation of faults
17B
17B-88
PETROL INJECTION
Fault finding - Interpretation of faults
17B
17B-88V9 MR-372-J84-17B050$376.mif
S3000 Injection
Program No.: AD
Vdiag No.: 4C / 54
DF154
PRESENT
OR
STOREDFLYWHEEL SIGNAL SENSOR CIRCUIT
1.DEF: Abnormal voltage
2.DEF: Tooth lost
3.DEF: Non-compliance with emission control standards
NOTESPriority when dealing with a number of faults:
If faults DF154, DF119 Camshaft sensor circuit and DF080 Camshaft dephaser
circuit are present, ignore DF080 and deal with the other 2 faults first.
Conditions for applying the fault finding procedure to stored faults:
The fault is declared present after the starter motor has been running for 10 seconds
or at an engine speed above 600 rpm.
Special note:
–the OBD warning light is lit,
– In the event of flywheel signal loss, the injection and ignition are cut off: the vehicle
stalls and cannot be restarted.
1.DEF
NOTESNone.
Check the cleanliness, condition and the fitting of the flywheel.
Repair if necessary.
If the flywheel has been replaced or removed, the flywheel target has to be reinitialised, then reprogrammed.
Programming reinitialisation:
Use command RZ005: Programming.
Carrying out the flywheel target programming:
– Decelerate a first time with injection cut-off (i.e. feet off the brake, accelerator pedal and clutch pedals) between
3500 and 3000 rpm, in 3rd gear for a manual gearbox and 2nd for automatic gearbox, for at least 5 seconds.
– Decelerate a second time with injection cut-off (i.e. brake, accelerator and clutch pedals released) between
2400and 2000 rpm for K4 engines and between 1800 and
1400 rpm for F4R engines, in 3rd gear for a manual gearbox and 2nd for an automatic gearbox, for at least
5 seconds.
After the operation, check that status ET089 Flywheel target programming is COMPLETED.
(*This is the moment when, during deceleration with no load, the engine drops to idle speed and recovers torque).
AFTER REPAIRFollow the instructions to confirm repair.
Deal with any other faults.
Clear the stored faults.
S3000_V4C_DF154/S3000_V54_DF154
Page 89 of 230
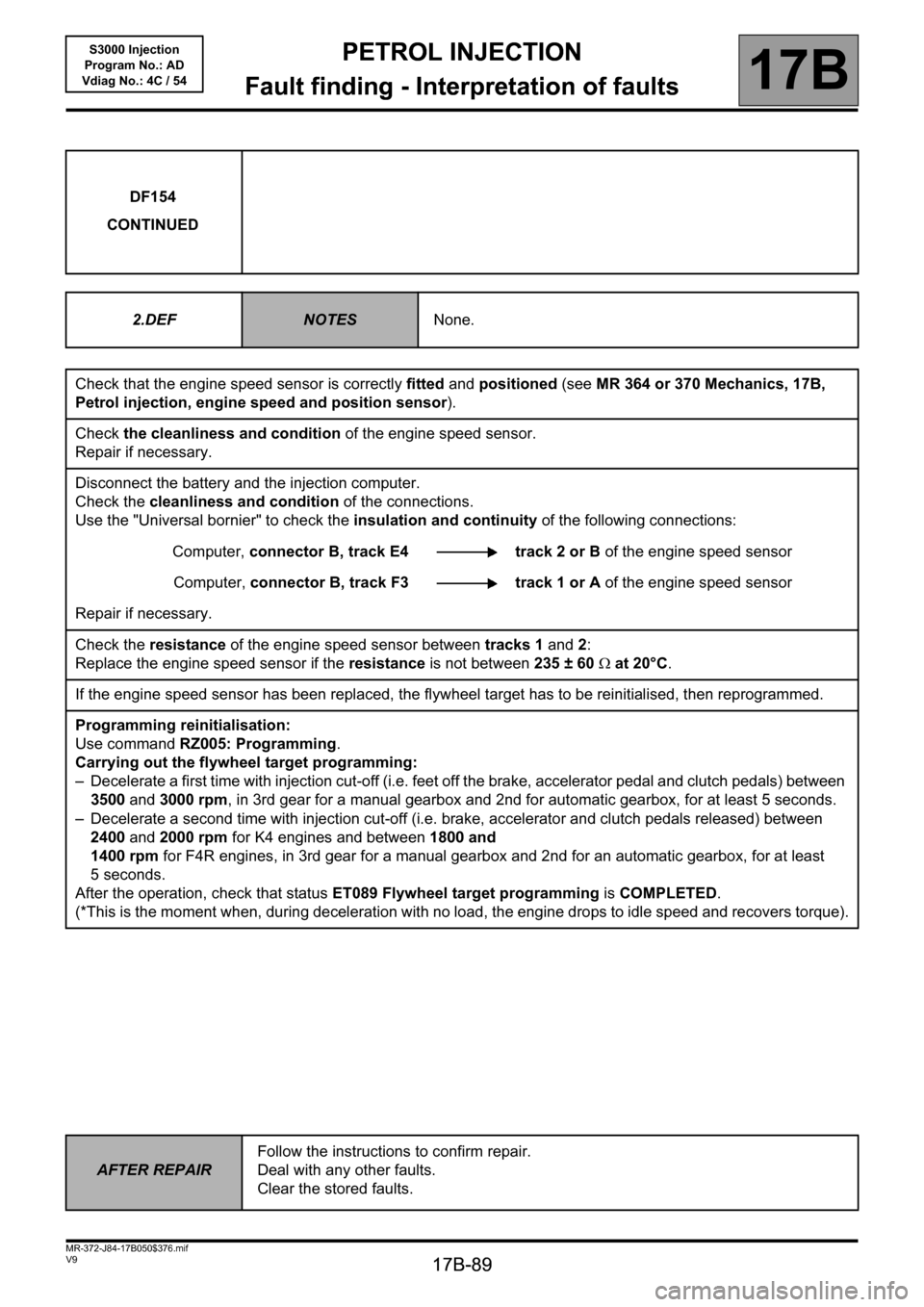
PETROL INJECTION
Fault finding - Interpretation of faults
17B
17B-89
PETROL INJECTION
Fault finding - Interpretation of faults
17B
17B-89V9 MR-372-J84-17B050$376.mif
S3000 Injection
Program No.: AD
Vdiag No.: 4C / 54
DF154
CONTINUED
2.DEF
NOTESNone.
Check that the engine speed sensor is correctly fitted and positioned (see MR 364 or 370 Mechanics, 17B,
Petrol injection, engine speed and position sensor).
Check the cleanliness and condition of the engine speed sensor.
Repair if necessary.
Disconnect the battery and the injection computer.
Check the cleanliness and condition of the connections.
Use the "Universal bornier" to check the insulation and continuity of the following connections:
Computer, connector B, track E4 track 2 or B of the engine speed sensor
Computer, connector B, track F3 track 1 or A of the engine speed sensor
Repair if necessary.
Check the resistance of the engine speed sensor between tracks 1 and 2:
Replace the engine speed sensor if the resistance is not between 235 ± 60Ω at 20°C.
If the engine speed sensor has been replaced, the flywheel target has to be reinitialised, then reprogrammed.
Programming reinitialisation:
Use command RZ005: Programming.
Carrying out the flywheel target programming:
– Decelerate a first time with injection cut-off (i.e. feet off the brake, accelerator pedal and clutch pedals) between
3500 and 3000 rpm, in 3rd gear for a manual gearbox and 2nd for automatic gearbox, for at least 5 seconds.
– Decelerate a second time with injection cut-off (i.e. brake, accelerator and clutch pedals released) between
2400and 2000 rpm for K4 engines and between 1800 and
1400 rpm for F4R engines, in 3rd gear for a manual gearbox and 2nd for an automatic gearbox, for at least
5 seconds.
After the operation, check that status ET089 Flywheel target programming is COMPLETED.
(*This is the moment when, during deceleration with no load, the engine drops to idle speed and recovers torque).
AFTER REPAIRFollow the instructions to confirm repair.
Deal with any other faults.
Clear the stored faults.
Page 106 of 230
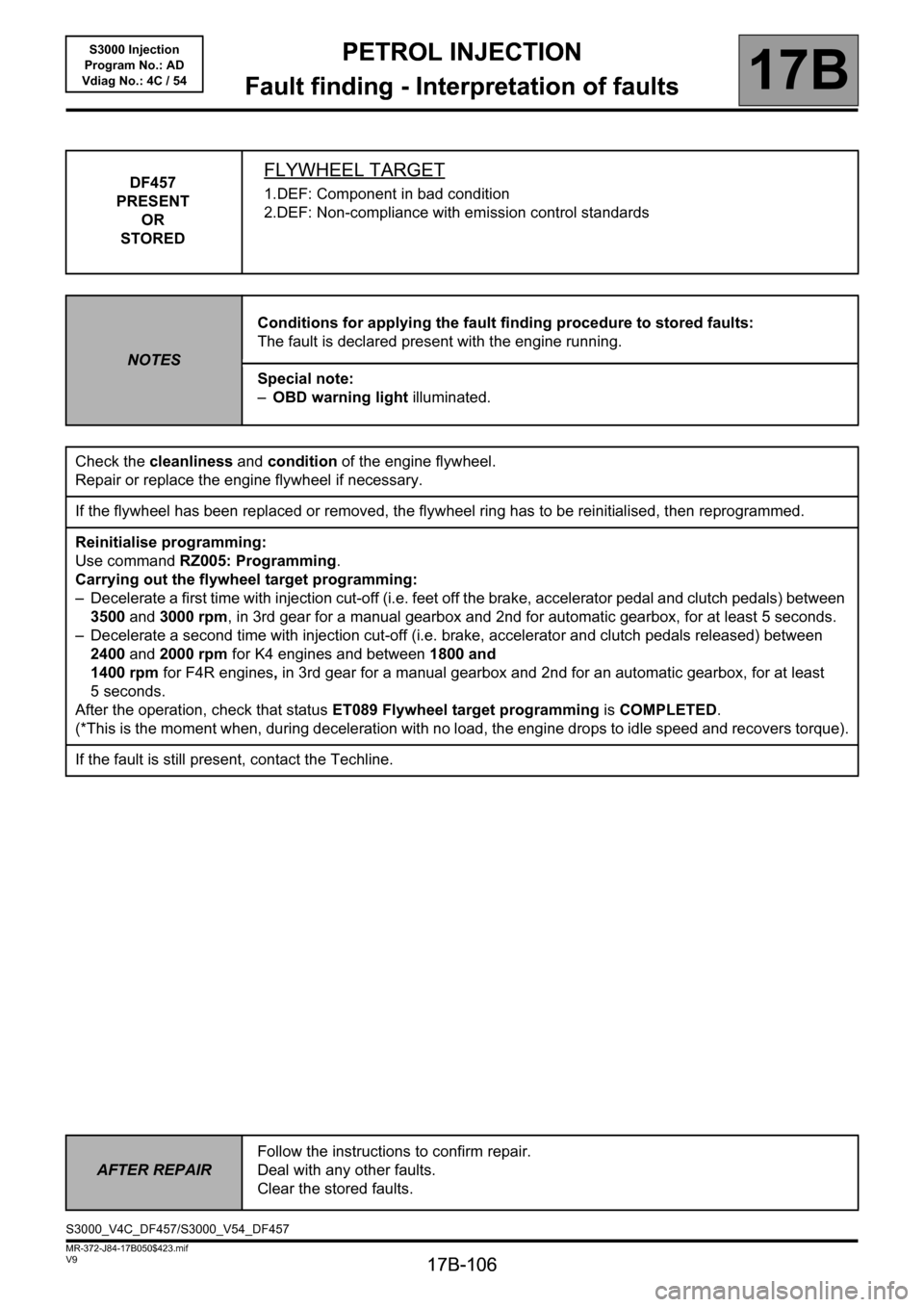
PETROL INJECTION
Fault finding - Interpretation of faults
17B
17B-106
PETROL INJECTION
Fault finding - Interpretation of faults
17B
17B-106V9 MR-372-J84-17B050$423.mif
S3000 Injection
Program No.: AD
Vdiag No.: 4C / 54
DF457
PRESENT
OR
STOREDFLYWHEEL TARGET
1.DEF: Component in bad condition
2.DEF: Non-compliance with emission control standards
NOTESConditions for applying the fault finding procedure to stored faults:
The fault is declared present with the engine running.
Special note:
–OBD warning light illuminated.
Check the cleanliness and condition of the engine flywheel.
Repair or replace the engine flywheel if necessary.
If the flywheel has been replaced or removed, the flywheel ring has to be reinitialised, then reprogrammed.
Reinitialise programming:
Use command RZ005: Programming.
Carrying out the flywheel target programming:
– Decelerate a first time with injection cut-off (i.e. feet off the brake, accelerator pedal and clutch pedals) between
3500 and 3000 rpm, in 3rd gear for a manual gearbox and 2nd for automatic gearbox, for at least 5 seconds.
– Decelerate a second time with injection cut-off (i.e. brake, accelerator and clutch pedals released) between
2400and 2000 rpm for K4 engines and between 1800 and
1400 rpm for F4R engines, in 3rd gear for a manual gearbox and 2nd for an automatic gearbox, for at least
5 seconds.
After the operation, check that status ET089 Flywheel target programming is COMPLETED.
(*This is the moment when, during deceleration with no load, the engine drops to idle speed and recovers torque).
If the fault is still present, contact the Techline.
AFTER REPAIRFollow the instructions to confirm repair.
Deal with any other faults.
Clear the stored faults.
S3000_V4C_DF457/S3000_V54_DF457
Page 179 of 230
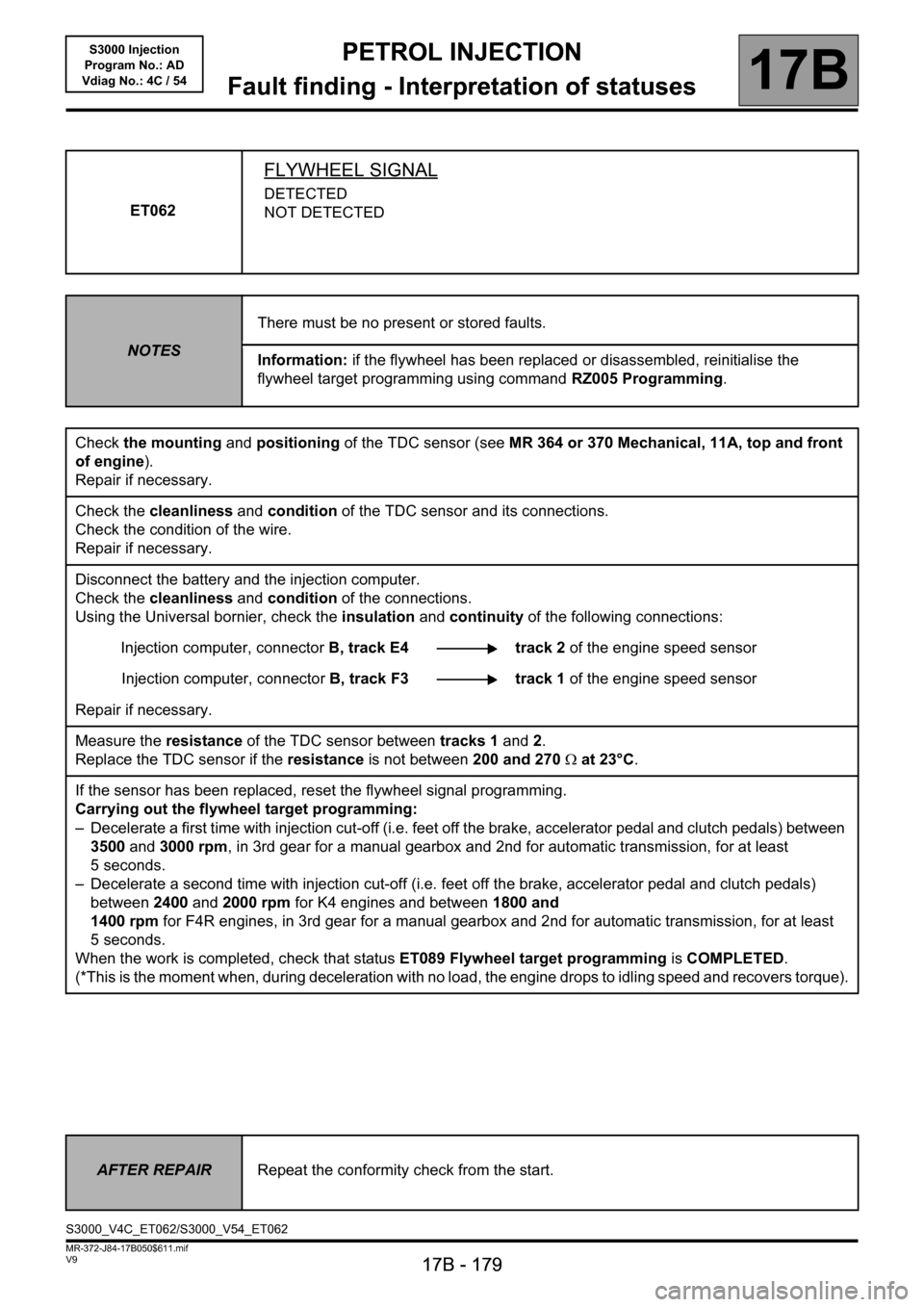
PETROL INJECTION
Fault finding - Interpretation of statuses
17B
17B - 179
PETROL INJECTION
Fault finding - Interpretation of statuses
17B
17B - 179V9 MR-372-J84-17B050$611.mif
S3000 Injection
Program No.: AD
Vdiag No.: 4C / 54
ET062
FLYWHEEL SIGNAL
DETECTED
NOT DETECTED
NOTESThere must be no present or stored faults.
Information: if the flywheel has been replaced or disassembled, reinitialise the
flywheel target programming using command RZ005 Programming.
Check the mounting and positioning of the TDC sensor (see MR 364 or 370 Mechanical, 11A, top and front
of engine).
Repair if necessary.
Check the cleanliness and condition of the TDC sensor and its connections.
Check the condition of the wire.
Repair if necessary.
Disconnect the battery and the injection computer.
Check the cleanliness and condition of the connections.
Using the Universal bornier, check the insulation and continuity of the following connections:
Injection computer, connectorB, track E4 track 2 of the engine speed sensor
Injection computer, connectorB, track F3 track 1 of the engine speed sensor
Repair if necessary.
Measure the resistance of the TDC sensor between tracks 1 and 2.
Replace the TDC sensor if the resistance is not between 200 and 270Ω at 23°C.
If the sensor has been replaced, reset the flywheel signal programming.
Carrying out the flywheel target programming:
– Decelerate a first time with injection cut-off (i.e. feet off the brake, accelerator pedal and clutch pedals) between
3500 and 3000 rpm, in 3rd gear for a manual gearbox and 2nd for automatic transmission, for at least
5 seconds.
– Decelerate a second time with injection cut-off (i.e. feet off the brake, accelerator pedal and clutch pedals)
between 2400 and 2000 rpm for K4 engines and between 1800 and
1400 rpm for F4R engines, in 3rd gear for a manual gearbox and 2nd for automatic transmission, for at least
5 seconds.
When the work is completed, check that status ET089 Flywheel target programming is COMPLETED.
(*This is the moment when, during deceleration with no load, the engine drops to idling speed and recovers torque).
AFTER REPAIRRepeat the conformity check from the start.
S3000_V4C_ET062/S3000_V54_ET062