ignition RENAULT TWINGO RS 2009 2.G Electrical Equipment - Petrol Injection Workshop Manual
[x] Cancel search | Manufacturer: RENAULT, Model Year: 2009, Model line: TWINGO RS, Model: RENAULT TWINGO RS 2009 2.GPages: 348
Page 3 of 348
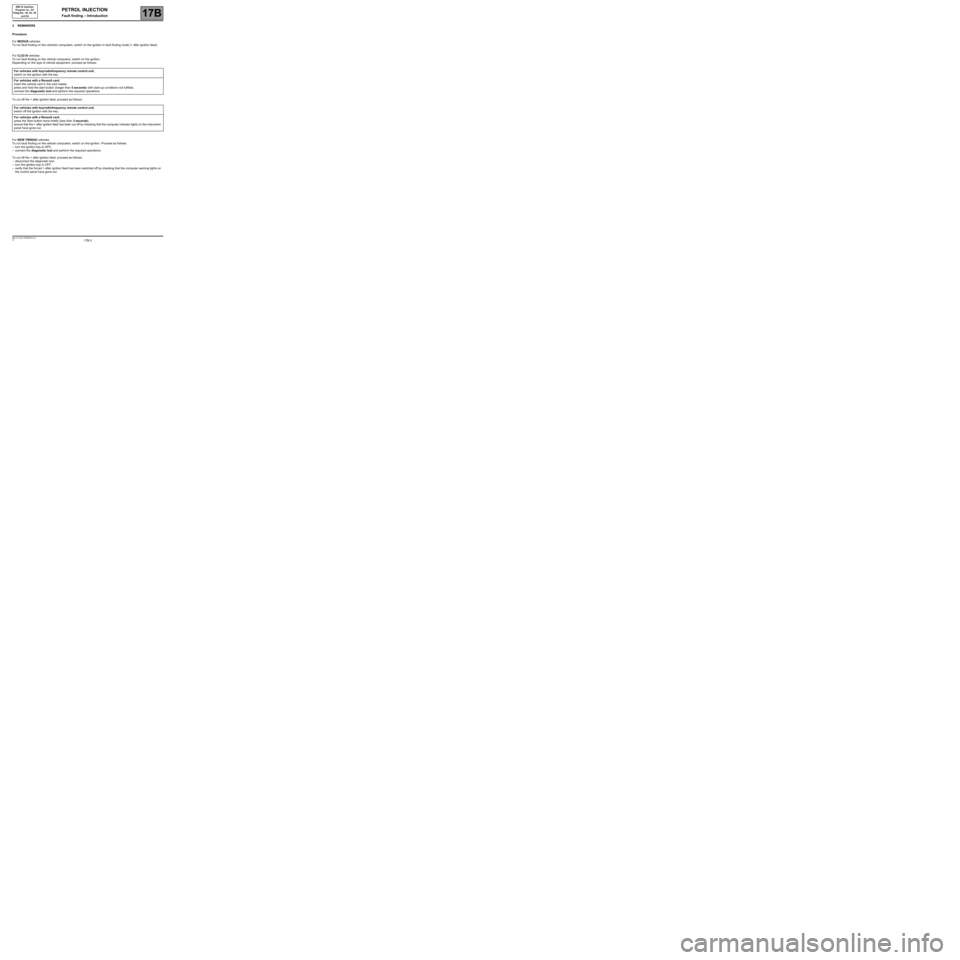
17B-3V7 MR-413-X44-17B000$010.mif
PETROL INJECTION
Fault finding – Introduction17B
SIM 32 Injection
Program no.: D3
Vdiag No.: 44, 4C, 50
and 54
3. REMINDERS
Procedure
For MODUS vehicles:
To run fault finding on the vehicle's computers, switch on the ignition in fault finding mode (+ after ignition feed).
For CLIO III vehicles:
To run fault finding on the vehicle computers, switch on the ignition.
Depending on the type of vehicle equipment, proceed as follows:
To cut off the + after ignition feed, proceed as follows:
For NEW TWINGO vehicles:
To run fault finding on the vehicle computers, switch on the ignition. Proceed as follows:
–turn the ignition key to APC,
–connect the diagnostic tool and perform the required operations.
To cut off the + after ignition feed, proceed as follows:
–disconnect the diagnostic tool,
–turn the ignition key to OFF,
–verify that the forced + after ignition feed has been switched off by checking that the computer warning lights on
the control panel have gone out. For vehicles with key/radiofrequency remote control unit,
switch on the ignition with the key.
For vehicles with a Renault card,
insert the vehicle card in the card reader.
press and hold the start button (longer than 5 seconds) with start-up conditions not fulfilled,
connect the diagnostic tool and perform the required operations.
For vehicles with key/radiofrequency remote control unit,
switch off the ignition with the key.
For vehicles with a Renault card,
press the Start button twice briefly (less than 3 seconds),
ensure that the + after ignition feed has been cut off by checking that the computer indicator lights on the instrument
panel have gone out.
Page 4 of 348
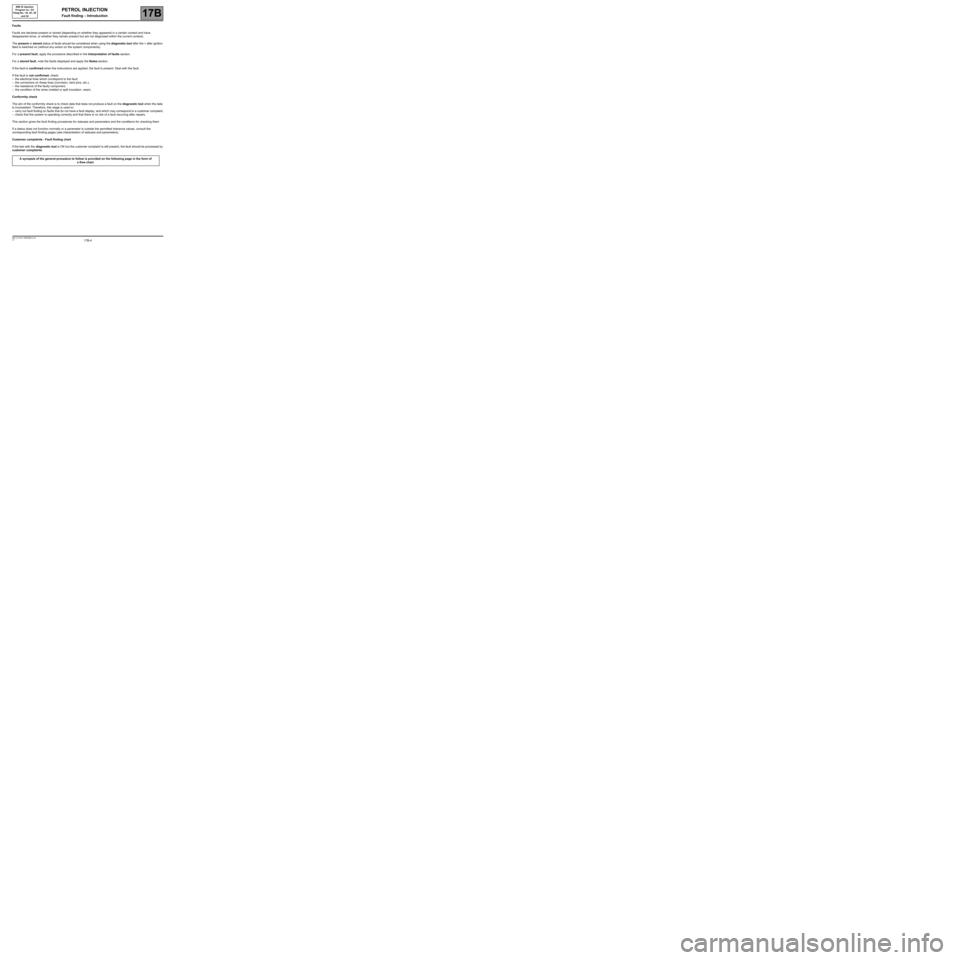
17B-4V7 MR-413-X44-17B000$010.mif
PETROL INJECTION
Fault finding – Introduction17B
SIM 32 Injection
Program no.: D3
Vdiag No.: 44, 4C, 50
and 54
Faults
Faults are declared present or stored (depending on whether they appeared in a certain context and have
disappeared since, or whether they remain present but are not diagnosed within the current context).
The present or stored status of faults should be considered when using the diagnostic tool after the + after ignition
feed is switched on (without any action on the system components).
For a present fault, apply the procedure described in the Interpretation of faults section.
For a stored fault, note the faults displayed and apply the Notes section.
If the fault is confirmed when the instructions are applied, the fault is present. Deal with the fault.
If the fault is not confirmed, check:
–the electrical lines which correspond to the fault,
–the connectors on these lines (corrosion, bent pins, etc.),
–the resistance of the faulty component,
–the condition of the wires (melted or split insulation, wear).
Conformity check
The aim of the conformity check is to check data that does not produce a fault on the diagnostic tool when the data
is inconsistent. Therefore, this stage is used to:
–carry out fault finding on faults that do not have a fault display, and which may correspond to a customer complaint,
–check that the system is operating correctly and that there is no risk of a fault recurring after repairs.
This section gives the fault finding procedures for statuses and parameters and the conditions for checking them
If a status does not function normally or a parameter is outside the permitted tolerance values, consult the
corresponding fault finding pages (see interpretation of statuses and parameters).
Customer complaints - Fault finding chart
If the test with the diagnostic tool is OK but the customer complaint is still present, the fault should be processed by
customer complaints.
A synopsis of the general procedure to follow is provided on the following page in the form of
a flow chart.
Page 10 of 348
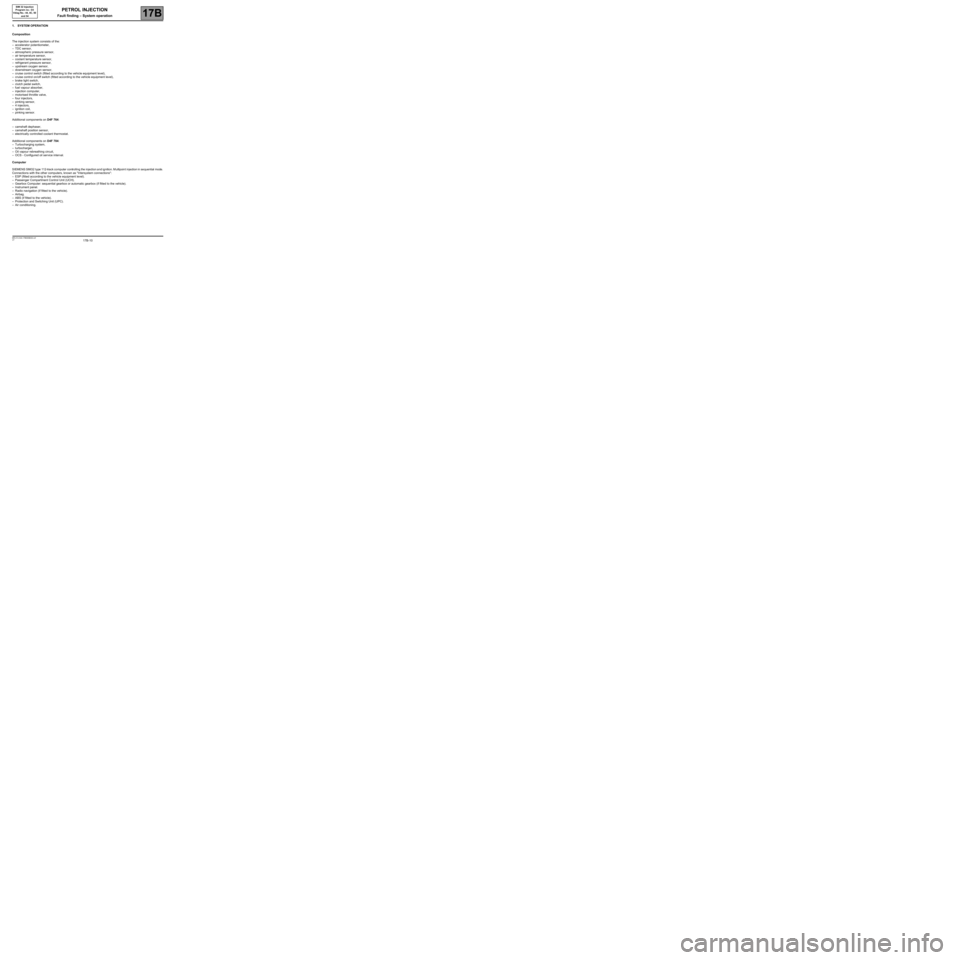
17B-10V7 MR-413-X44-17B000$030.mif
17B
SIM 32 Injection
Program no.: D3
Vdiag No.: 44, 4C, 50
and 54
1. SYSTEM OPERATION
Composition
The injection system consists of the:
–accelerator potentiometer,
–TDC sensor,
–atmospheric pressure sensor,
–air temperature sensor,
–coolant temperature sensor,
–refrigerant pressure sensor,
–upstream oxygen sensor,
–downstream oxygen sensor,
–cruise control switch (fitted according to the vehicle equipment level),
–cruise control on/off switch (fitted according to the vehicle equipment level),
–brake light switch,
–clutch pedal switch,
–fuel vapour absorber,
–injection computer,
–motorised throttle valve,
–four injectors,
–pinking sensor,
–4 injectors,
–ignition coil,
–pinking sensor.
Additional components on D4F 764:
–camshaft dephaser,
–camshaft position sensor,
–electrically controlled coolant thermostat.
Additional components on D4F 784:
–Turbocharging system,
–turbocharger,
–Oil vapour rebreathing circuit,
–OCS - Configured oil service interval.
Computer
SIEMENSSIM32type112-track co mputer controlling the injection a nd ignition. M ultipoint injection in se quential mode.
Connections with the other computers, known as "Intersystem connections":
–ESP (fitted according to the vehicle equipment level).
–Passenger Compartment Control Unit (UCH).
–Gearbox Computer: sequential gearbox or automatic gearbox (if fitted to the vehicle).
–Instrument panel.
–Radio navigation (if fitted to the vehicle).
–Airbag.
–ABS (if fitted to the vehicle).
–Protection and Switching Unit (UPC).
–Air conditioning.
PETROL INJECTION
Fault finding – System operation
Page 11 of 348
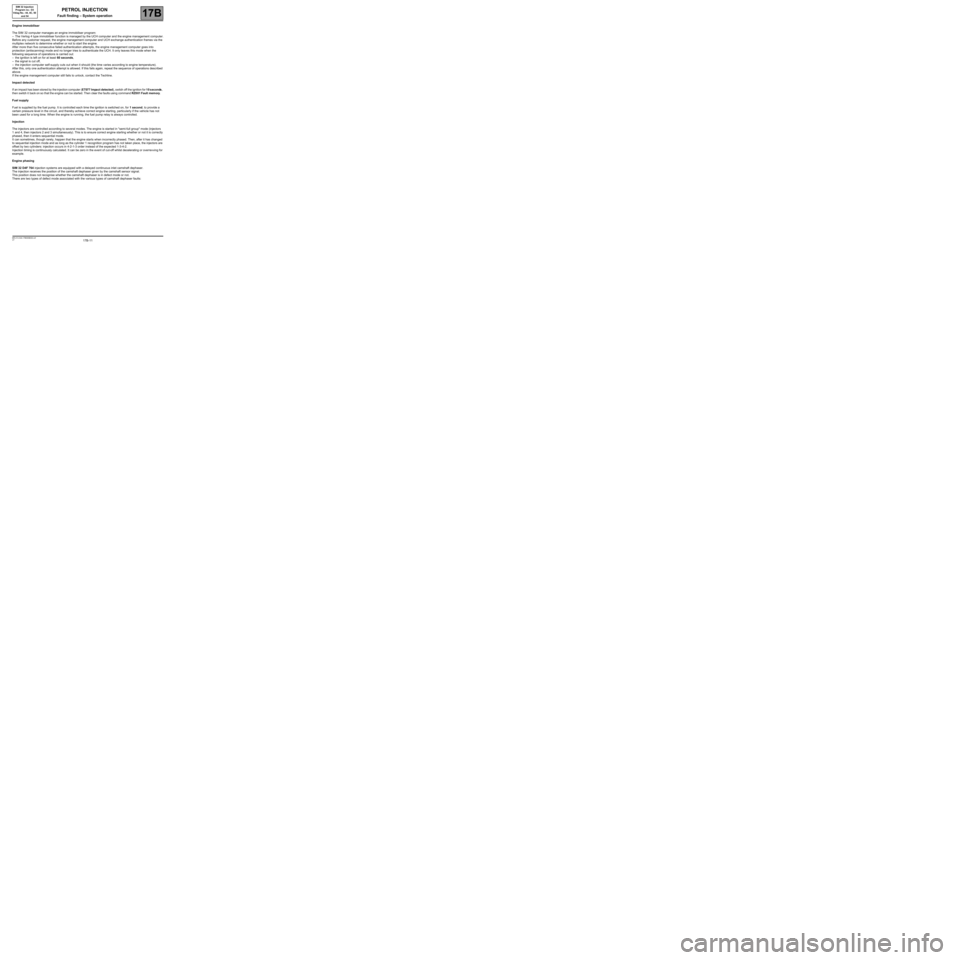
17B-11V7 MR-413-X44-17B000$030.mif
PETROL INJECTION
Fault finding – System operation17B
SIM 32 Injection
Program no.: D3
Vdiag No.: 44, 4C, 50
and 54
Engine immobiliser
The SIM 32 computer manages an engine immobiliser program:
–The Verlog 4 type immobiliser function is managed by the UCH computer and the engine management computer.
Before any customer request, the engine management computer and UCH exchange authentication frames via the
multiplex network to determine whether or not to start the engine.
After more than five consecutive failed authentication attempts, the engine management computer goes into
protection (antiscanning) mode and no longer tries to authenticate the UCH. It only leaves this mode when the
following sequence of operations is carried out:
–the ignition is left on for at least 60 seconds,
–the signal is cut off,
–the injection computer self-supply cuts out when it should (the time varies according to engine temperature).
After this, only one authentication attempt is allowed. If this fails again, repeat the sequence of operations described
above.
If the engine management computer still fails to unlock, contact the Techline.
Impact detected
If an impacthas been stored by the injection computer (ET077 Impactdetected), switch off the ignition for10 seconds,
thenswitch it back on so that the e ngine can b e started. Then clear the faults using commandRZ0 01 Fault memory.
Fuel supply
Fuel is supplied by the fuel pump. It is controlled each time the ignition is switched on, for 1 second, to provide a
certain pressure level in the circuit, and thereby achieve correct engine starting, particularly if the vehicle has not
been used for a long time. When the engine is running, the fuel pump relay is always controlled.
Injection
The injectors are controlled according to several modes. The engine is started in "semi-full group" mode (injectors
1 and 4, then injectors 2 and 3 simultaneously). This is to ensure correct engine starting whether or not it is correctly
phased, then it enters sequential mode.
It can sometimes, though rarely, happen that the engine starts when incorrectly phased. Then, after it has changed
to sequential injection mode and as long as the cylinder 1 recognition program has not taken place, the injectors are
offset by two cylinders: injection occurs in 4-2-1-3 order instead of the expected 1-3-4-2.
Injection timing is continuously calculated. It can be zero in the event of cut-off whilst decelerating or overrevving for
example.
Engine phasing
SIM 32 D4F 764 injection systems are equipped with a delayed continuous inlet camshaft dephaser.
The injection receives the position of the camshaft dephaser given by the camshaft sensor signal.
This position does not recognise whether the camshaft dephaser is in defect mode or not.
There are two types of defect mode associated with the various types of camshaft dephaser faults:
Page 13 of 348
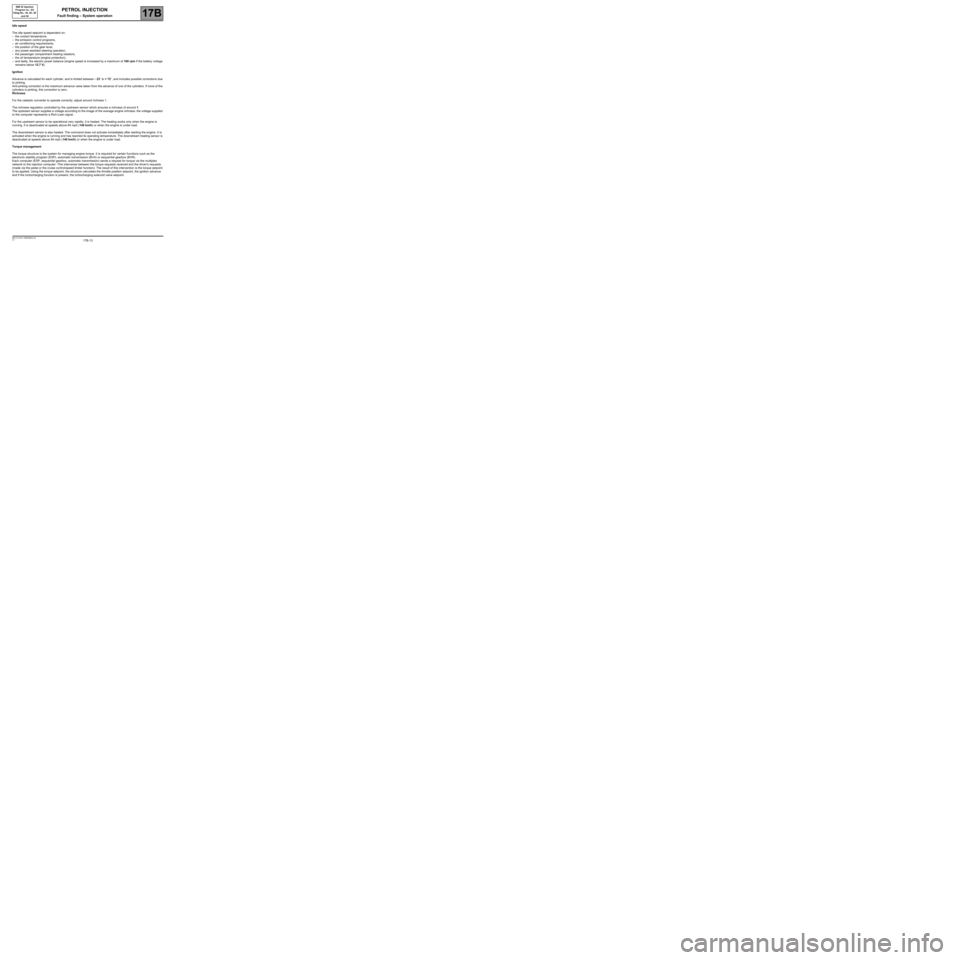
17B-13V7 MR-413-X44-17B000$030.mif
PETROL INJECTION
Fault finding – System operation17B
SIM 32 Injection
Program no.: D3
Vdiag No.: 44, 4C, 50
and 54
Idle speed
The idle speed setpoint is dependent on:
–the coolant temperature,
–the emission control programs,
–air conditioning requirements,
–the position of the gear lever,
–any power-assisted steering operation,
–the passenger compartment heating resistors,
–the oil temperature (engine protection),
–and lastly, the electric power balance (engine speed is increased by a maximum of 160 rpm if the battery voltage
remains below 12.7 V).
Ignition
Advance is calculated for each cylinder, and is limited between - 23Ëš to + 72Ëš, and includes possible corrections due
to pinking.
Anti-pinking correction is the maximum advance value taken from the advance of one of the cylinders. If none of the
cylinders is pinking, this correction is zero.
Richness
For the catalytic converter to operate correctly, adjust around richness 1.
The richness regulation controlled by the upstream sensor which ensures a richness of around 1.
The upstream sensor supplies a voltage according to the image of the average engine richness: the voltage supplied
to the computer represents a Rich-Lean signal.
For the upstream sensor to be operational very rapidly, it is heated. The heating works only when the engine is
running. It is deactivated at speeds above 84 mph (140 km/h) or when the engine is under load.
The downstream sensor is also heated. The command does not activate immediately after starting the engine. It is
activated when the engine is running and has reached its operating temperature. The downstream heating sensor is
deactivated at speeds above 84 mph (140 km/h) or when the engine is under load.
Torque management
The torque structure is the system for managing engine torque. It is required for certain functions such as the
electronic stability program (ESP), automatic transmission (BVA) or sequential gearbox (BVR).
Each computer (ESP, sequential gearbox, automatic transmission) sends a request for torque via the multiplex
network to the injection computer. This intervenes between the torque requests received and the driver's requests
(made via the pedal or the cruise control/speed limiter function). The result of this intervention is the torque setpoint
to be applied. Using the torque setpoint, the structure calculates the throttle position setpoint, the ignition advance
and if the turbocharging function is present, the turbocharging solenoid valve setpoint.
Page 14 of 348
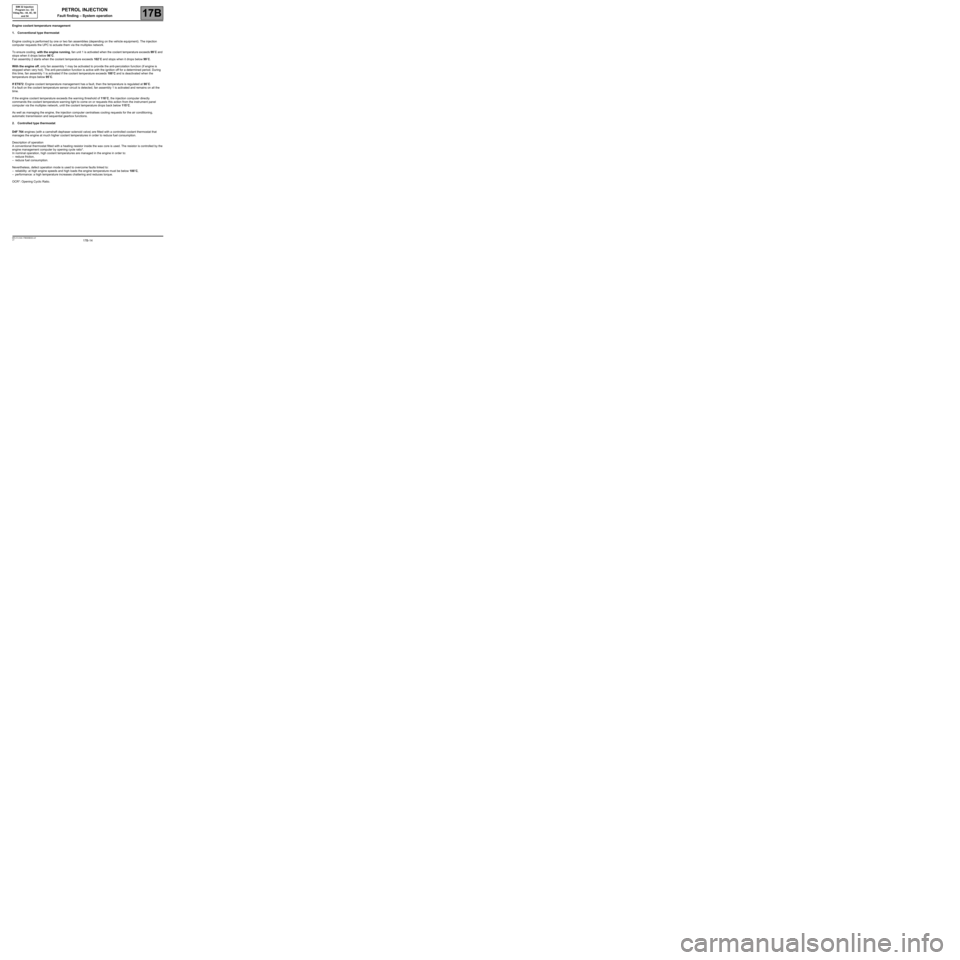
17B-14V7 MR-413-X44-17B000$030.mif
PETROL INJECTION
Fault finding – System operation17B
SIM 32 Injection
Program no.: D3
Vdiag No.: 44, 4C, 50
and 54
Engine coolant temperature management
1. Conventional type thermostat
Engine cooling is performed by one or two fan assemblies (depending on the vehicle equipment). The injection
computer requests the UPC to actuate them via the multiplex network.
To ensure cooling, with the engine running, fan unit 1 is activated when the coolant temperature exceeds 99ËšC and
stops when it drops below 96ËšC.
Fan assembly 2 starts when the coolant temperature exceeds 102ËšC and stops when it drops below 99ËšC.
With the engine off, only fan assembly 1 may be activated to provide the anti-percolation function (if engine is
stopped when very hot). The anti-percolation function is active with the ignition off for a determined period. During
this time, fan assembly 1 is activated if the coolant temperature exceeds 100ËšC and is deactivated when the
temperature drops below 95ËšC.
If ET672: Engine coolant temperature management has a fault, then the temperature is regulated at 90ËšC.
If a fault on the coolant temperature sensor circuit is detected, fan assembly 1 is activated and remains on all the
time.
If the engine coolant temperature exceeds the warning threshold of 118ËšC, the injection computer directly
commands the coolant temperature warning light to come on or requests this action from the instrument panel
computer via the multiplex network, until the coolant temperature drops back below 115ËšC.
As well as managing the engine, the injection computer centralises cooling requests for the air conditioning,
automatic transmission and sequential gearbox functions.
2. Controlled type thermostat
D4F 764 engines (with a camshaft dephaser solenoid valve) are fitted with a controlled coolant thermostat that
manages the engine at much higher coolant temperatures in order to reduce fuel consumption.
Description of operation
A conventional thermostat fitted with a heating resistor inside the wax core is used. The resistor is controlled by the
engine management computer by opening cycle ratio*.
In nominal operation, high coolant temperatures are managed in the engine in order to:
–reduce friction,
–reduce fuel consumption.
Nevertheless, defect operation mode is used to overcome faults linked to:
–reliability: at high engine speeds and high loads the engine temperature must be below 100˚C,
–performance: a high temperature increases chattering and reduces torque.
OCR*: Opening Cyclic Ratio.
Page 19 of 348
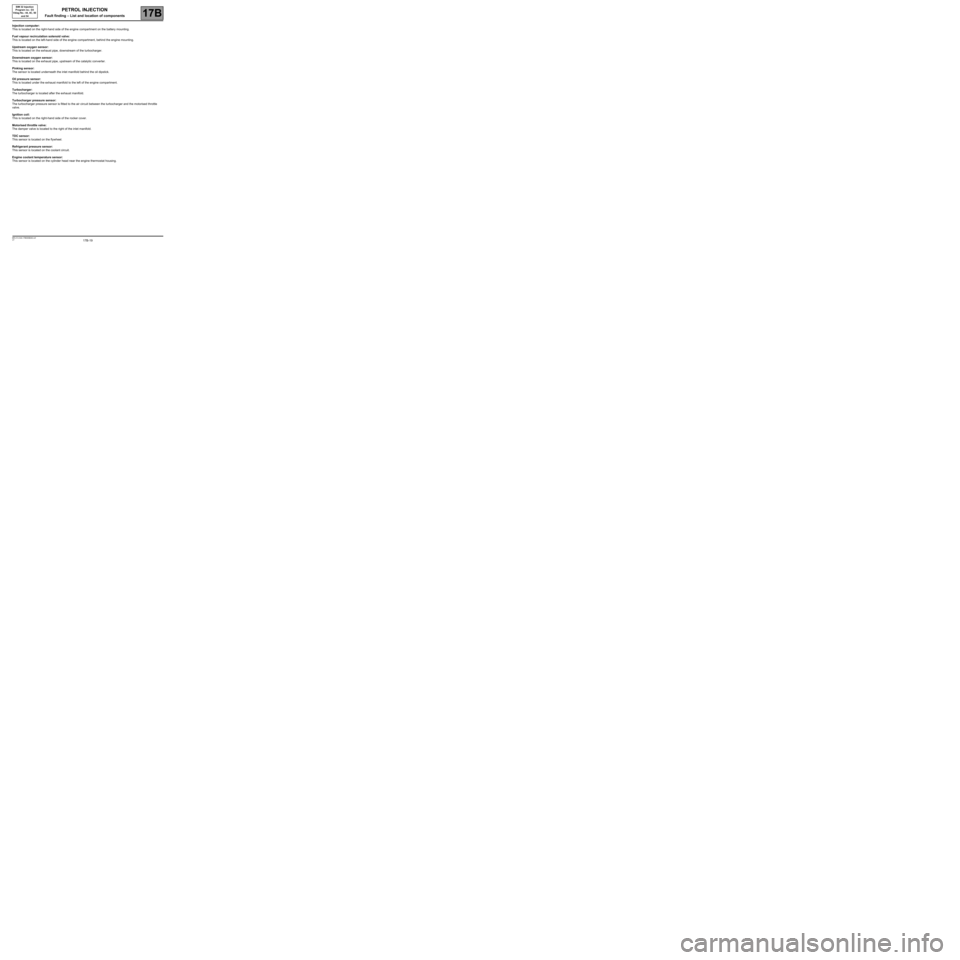
17B-19V7 MR-413-X44-17B000$040.mif
17B
SIM 32 Injection
Program no.: D3
Vdiag No.: 44, 4C, 50
and 54
Injection computer:
This is located on the right-hand side of the engine compartment on the battery mounting.
Fuel vapour recirculation solenoid valve:
This is located on the left-hand side of the engine compartment, behind the engine mounting.
Upstream oxygen sensor:
This is located on the exhaust pipe, downstream of the turbocharger.
Downstream oxygen sensor:
This is located on the exhaust pipe, upstream of the catalytic converter.
Pinking sensor:
The sensor is located underneath the inlet manifold behind the oil dipstick.
Oil pressure sensor:
This is located under the exhaust manifold to the left of the engine compartment.
Turbocharger:
The turbocharger is located after the exhaust manifold.
Turbocharger pressure sensor:
The turbocharger pressure sensor is fitted to the air circuit between the turbocharger and the motorised throttle
valve.
Ignition coil:
This is located on the right-hand side of the rocker cover.
Motorised throttle valve:
The damper valve is located to the right of the inlet manifold.
TDC sensor:
This sensor is located on the flywheel.
Refrigerant pressure sensor:
This sensor is located on the coolant circuit.
Engine coolant temperature sensor:
This sensor is located on the cylinder head near the engine thermostat housing.
PETROL INJECTION
Fault finding – List and location of components
Page 21 of 348
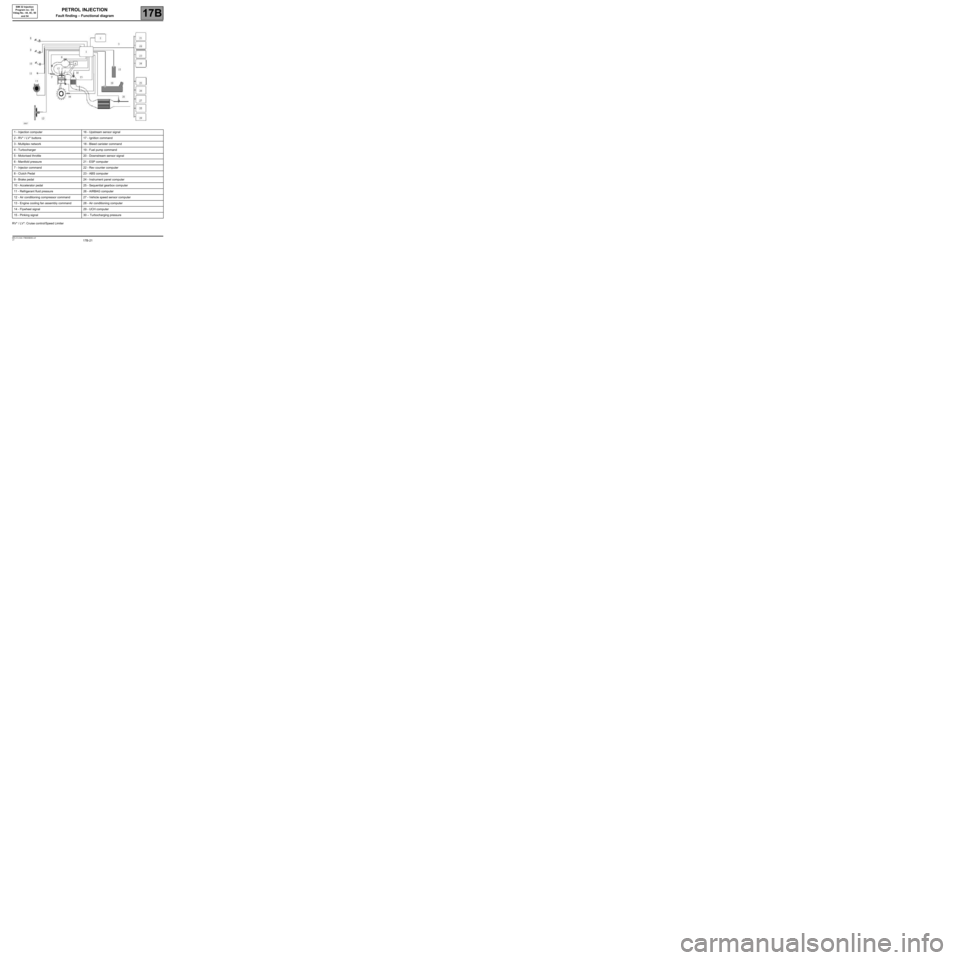
17B-21V7 MR-413-X44-17B000$050.mif
17B
SIM 32 Injection
Program no.: D3
Vdiag No.: 44, 4C, 50
and 54
RV* / LV*: Cruise control/Speed Limiter1 - Injection computer 16 - Upstream sensor signal
2 - RV* / LV* buttons 17 - Ignition command
3 - Multiplex network 18 - Bleed canister command
4 - Turbocharger 19 - Fuel pump command
5 - Motorised throttle 20 - Downstream sensor signal
6 - Manifold pressure 21 - ESP computer
7 - Injector command 22 - Rev counter computer
8 - Clutch Pedal 23 - ABS computer
9 - Brake pedal 24 - Instrument panel computer
10 - Accelerator pedal 25 - Sequential gearbox computer
11 - Refrigerant fluid pressure 26 - AIRBAG computer
12 - Air conditioning compressor command 27 - Vehicle speed sensor computer
13 - Engine cooling fan assembly command 28 - Air conditioning computer
14 - Flywheel signal 29 - UCH computer
15 - Pinking signal 30 – Turbocharging pressure
PETROL INJECTION
Fault finding – Functional diagram
Page 22 of 348
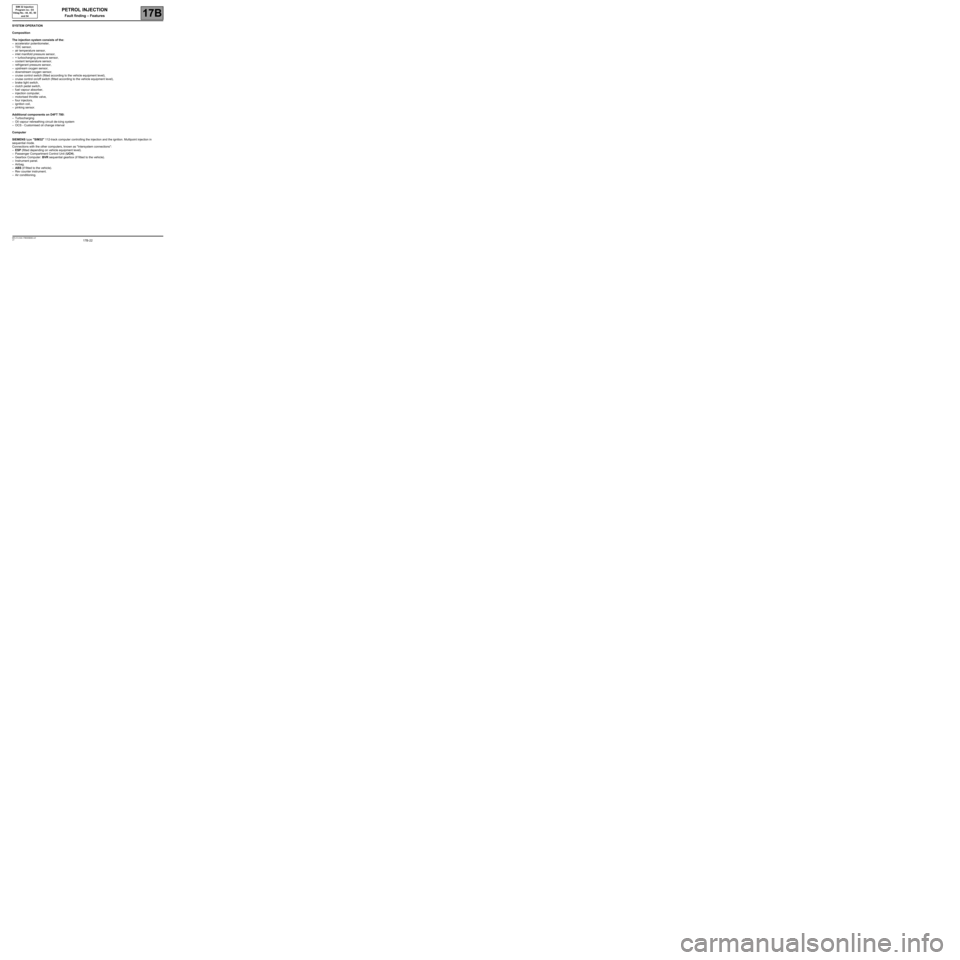
17B-22V7 MR-413-X44-17B000$060.mif
17B
SIM 32 Injection
Program no.: D3
Vdiag No.: 44, 4C, 50
and 54
SYSTEM OPERATION
Composition
The injection system consists of the:
–accelerator potentiometer,
–TDC sensor,
–air temperature sensor,
–inlet manifold pressure sensor,
–+ turbocharging pressure sensor,
–coolant temperature sensor,
–refrigerant pressure sensor,
–upstream oxygen sensor,
–downstream oxygen sensor,
–cruise control switch (fitted according to the vehicle equipment level),
–cruise control on/off switch (fitted according to the vehicle equipment level),
–brake light switch,
–clutch pedal switch,
–fuel vapour absorber,
–injection computer,
–motorised throttle valve,
–four injectors,
–ignition coil,
–pinking sensor.
Additional components on D4FT 780:
–Turbocharging
–Oil vapour rebreathing circuit de-icing system
–OCS - Customised oil change interval
Computer
SIEMENS type "SIM32" 112-track computer controlling the injection and the ignition. Multipoint injection in
sequential mode.
Connections with the other computers, known as "Intersystem connections":
–ESP (fitted depending on vehicle equipment level).
–Passenger Compartment Control Unit (UCH).
–Gearbox Computer: BVR sequential gearbox (if fitted to the vehicle).
–Instrument panel.
–Airbag.
–ABS (if fitted to the vehicle).
–Rev counter instrument.
–Air conditioning.
PETROL INJECTION
Fault finding – Features
Page 23 of 348
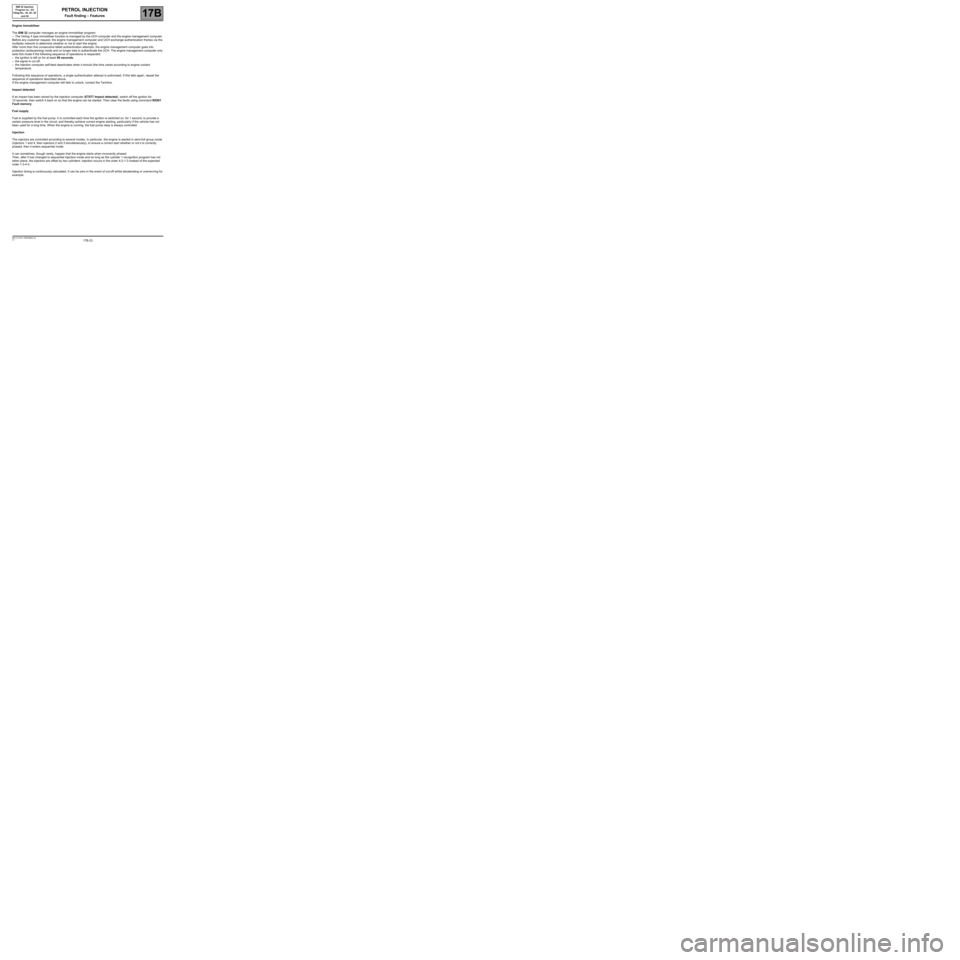
17B-23V7 MR-413-X44-17B000$060.mif
PETROL INJECTION
Fault finding – Features17B
SIM 32 Injection
Program no.: D3
Vdiag No.: 44, 4C, 50
and 54
Engine immobiliser
The SIM 32 computer manages an engine immobiliser program:
–The Verlog 4 type immobiliser function is managed by the UCH computer and the engine management computer.
Before any customer request, the engine management computer and UCH exchange authentication frames via the
multiplex network to determine whether or not to start the engine.
After more than five consecutive failed authentication attempts, the engine management computer goes into
protection (antiscanning) mode and no longer tries to authenticate the UCH. The engine management computer only
exits this mode if the following sequence of operations is respected:
–the ignition is left on for at least 60 seconds,
–the signal is cut off,
–the injection computer self-feed deactivates when it should (the time varies according to engine coolant
temperature.
Following this sequence of operations, a single authentication attempt is authorised. If this fails again, repeat the
sequence of operations described above.
If the engine management computer still fails to unlock, contact the Techline.
Impact detected
If an impact has been stored by the injection computer (ET077 Impact detected), switch off the ignition for
10 seconds, then switch it back on so that the engine can be started. Then clear the faults using command RZ001
Fault memory.
Fuel supply
Fuel is supplied by the fuel pump. It is controlled each time the ignition is switched on, for 1 second, to provide a
certain pressure level in the circuit, and thereby achieve correct engine starting, particularly if the vehicle has not
been used for a long time. When the engine is running, the fuel pump relay is always controlled.
Injection
The injectors are controlled according to several modes. In particular, the engine is started in semi-full group mode
(injectors 1 and 4, then injectors 2 and 3 simultaneously), to ensure a correct start whether or not it is correctly
phased, then it enters sequential mode.
It can sometimes, though rarely, happen that the engine starts when incorrectly phased.
Then, after it has changed to sequential injection mode and as long as the cylinder 1 recognition program has not
taken place, the injectors are offset by two cylinders: injection occurs in the order 4-2-1-3 instead of the expected
order 1-3-4-2.
Injection timing is continuously calculated. It can be zero in the event of cut-off whilst decelerating or overrevving for
example.