weight SSANGYONG KORANDO 2012 Owner's Manual
[x] Cancel search | Manufacturer: SSANGYONG, Model Year: 2012, Model line: KORANDO, Model: SSANGYONG KORANDO 2012Pages: 1082, PDF Size: 96.1 MB
Page 913 of 1082
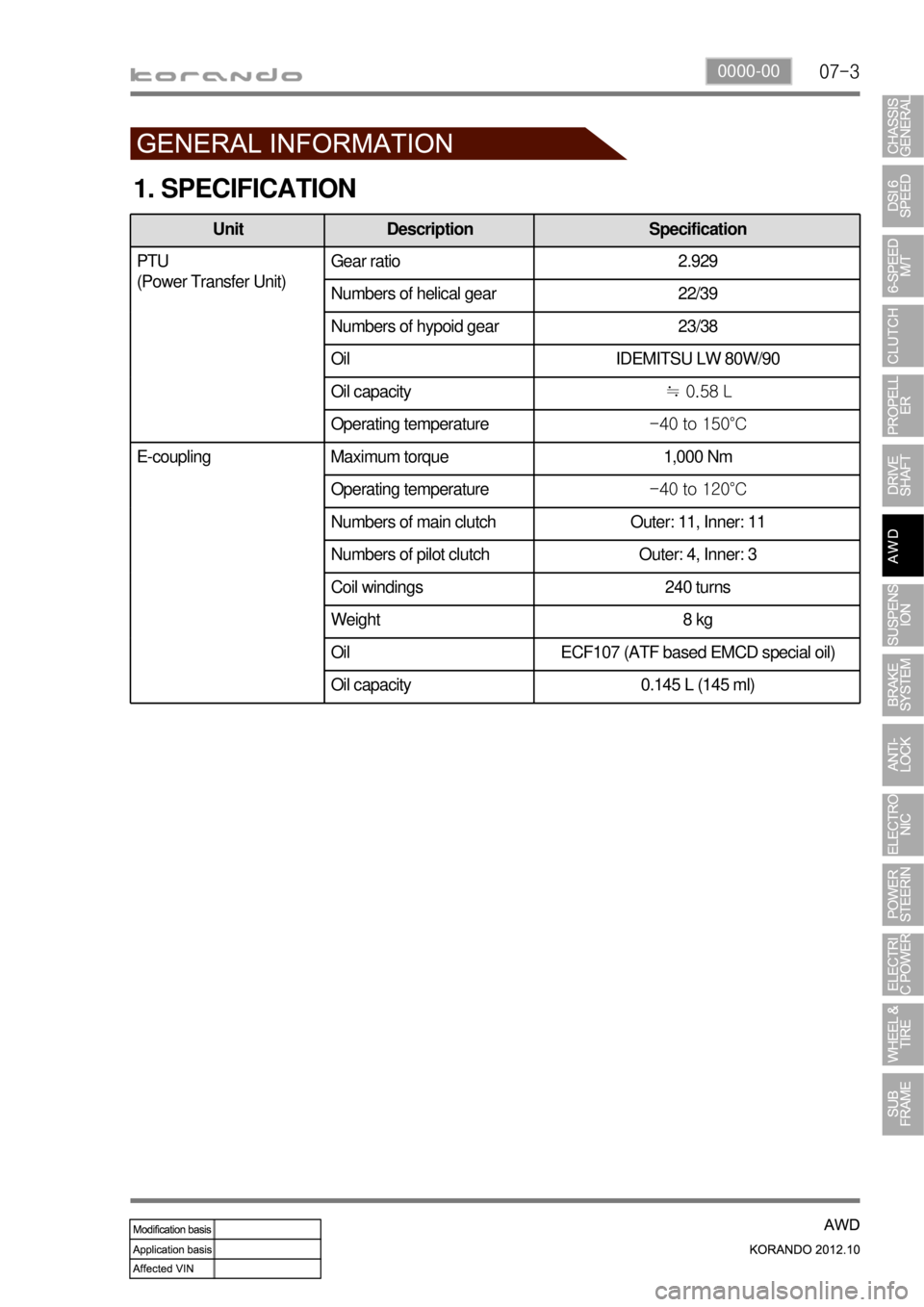
07-30000-00
1. SPECIFICATION
Unit Description Specification
PTU
(Power Transfer Unit)Gear ratio 2.929
Numbers of helical gear 22/39
Numbers of hypoid gear 23/38
Oil IDEMITSU LW 80W/90
Oil capacity≒ 0.58 L
Operating temperature-40 to 150°C
E-coupling Maximum torque 1,000 Nm
Operating temperature-40 to 120°C
Numbers of main clutch Outer: 11, Inner: 11
Numbers of pilot clutch Outer: 4, Inner: 3
Coil windings 240 turns
Weight 8 kg
Oil ECF107 (ATF based EMCD special oil)
Oil capacity 0.145 L (145 ml)
Page 921 of 1082
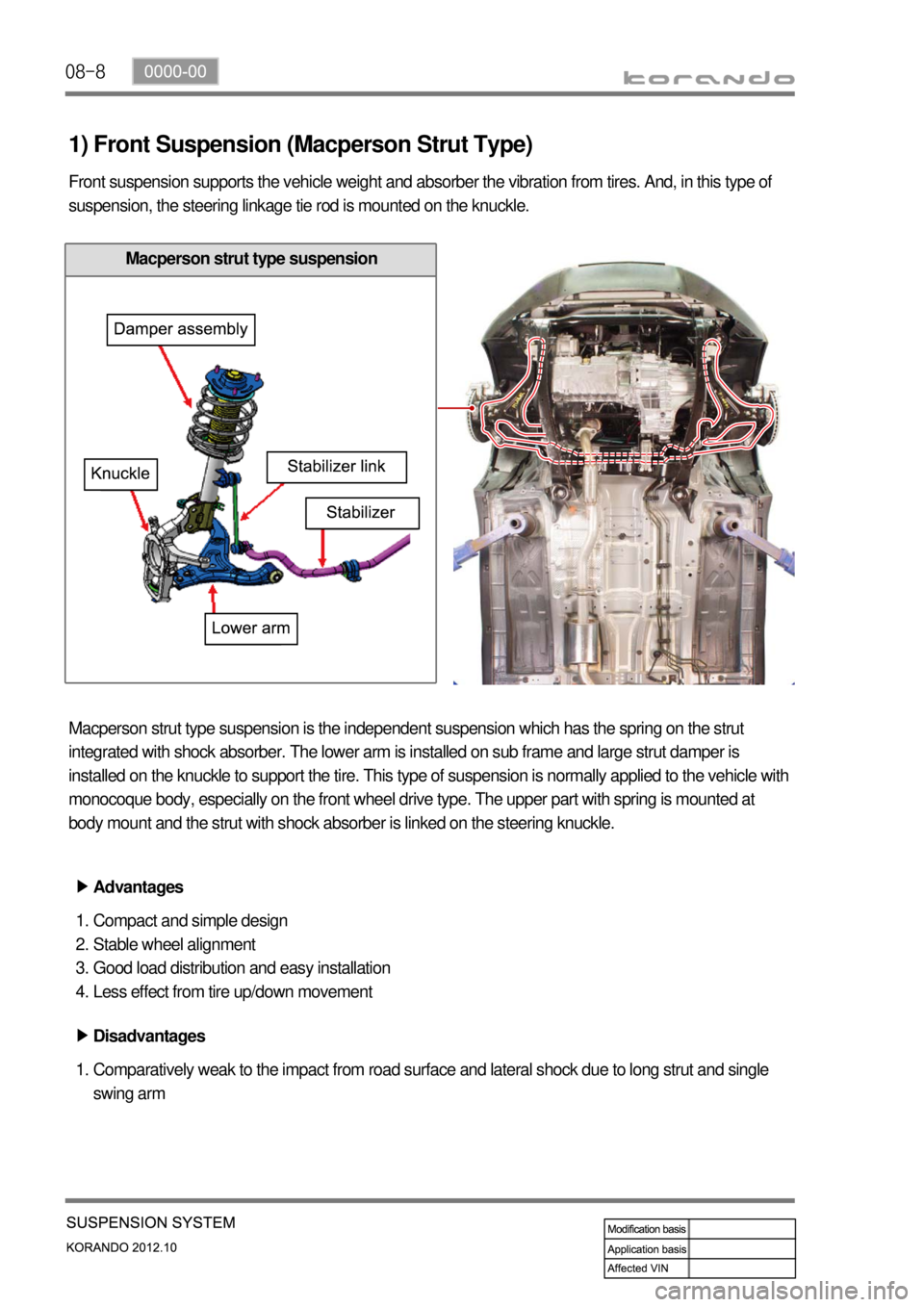
08-8
1) Front Suspension (Macperson Strut Type)
Front suspension supports the vehicle weight and absorber the vibration from tires. And, in this type of
suspension, the steering linkage tie rod is mounted on the knuckle.
Macperson strut type suspension is the independent suspension which has the spring on the strut
integrated with shock absorber. The lower arm is installed on sub frame and large strut damper is
installed on the knuckle to support the tire. This type of suspension is normally applied to the vehicle with
monocoque body, especially on the front wheel drive type. The upper part with spring is mounted at
body mount and the strut with shock absorber is linked on the steering knuckle.
Advantages â–¶
Compact and simple design
Stable wheel alignment
Good load distribution and easy installation
Less effect from tire up/down movement 1.
2.
3.
4.
Disadvantages â–¶
Comparatively weak to the impact from road surface and lateral shock due to long strut and single
swing arm 1.
Macperson strut type suspension
Page 922 of 1082
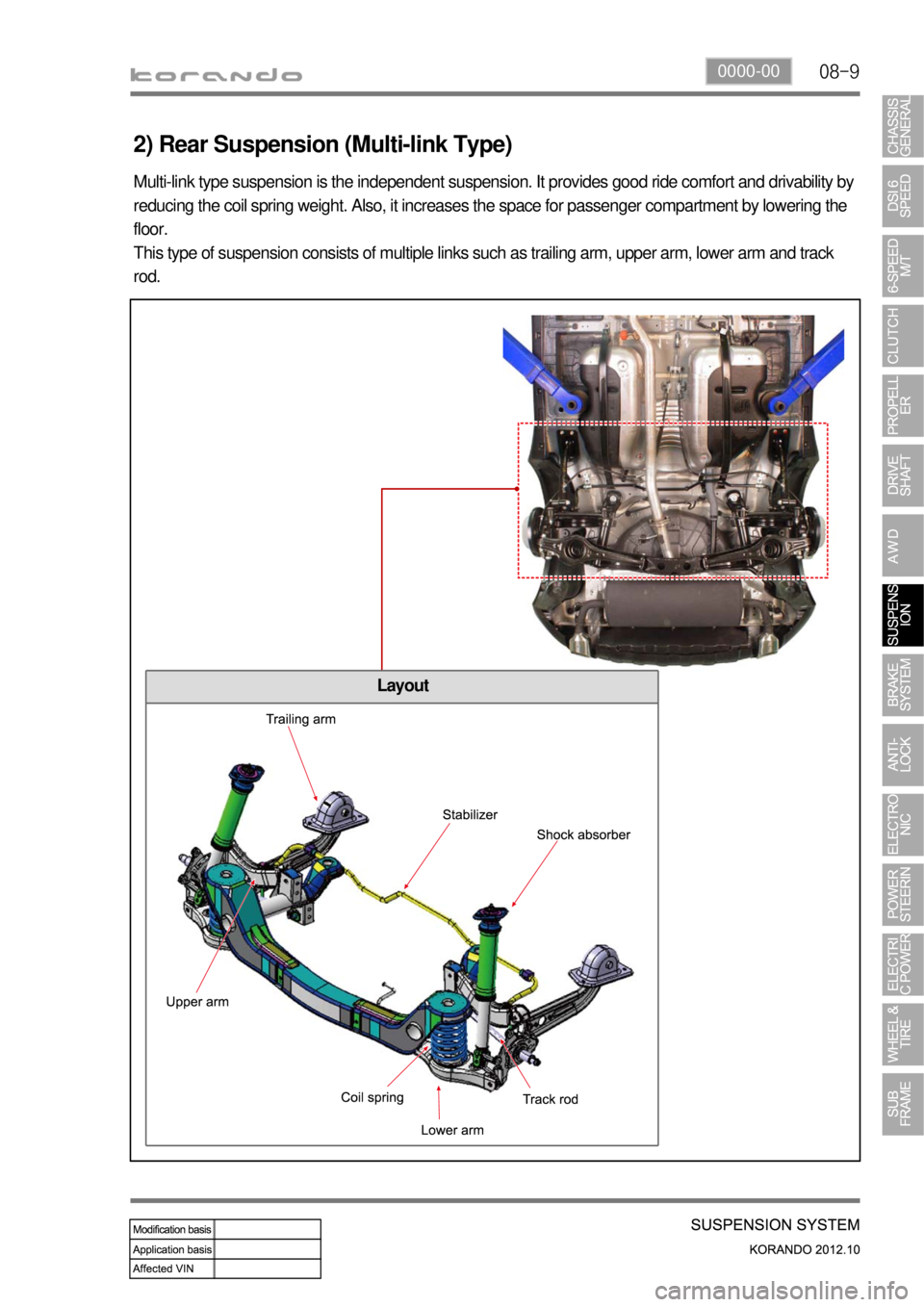
08-90000-00
2) Rear Suspension (Multi-link Type)
Multi-link type suspension is the independent suspension. It provides good ride comfort and drivability by
reducing the coil spring weight. Also, it increases the space for passenger compartment by lowering the
floor.
This type of suspension consists of multiple links such as trailing arm, upper arm, lower arm and track
rod.
Layout
Page 944 of 1082
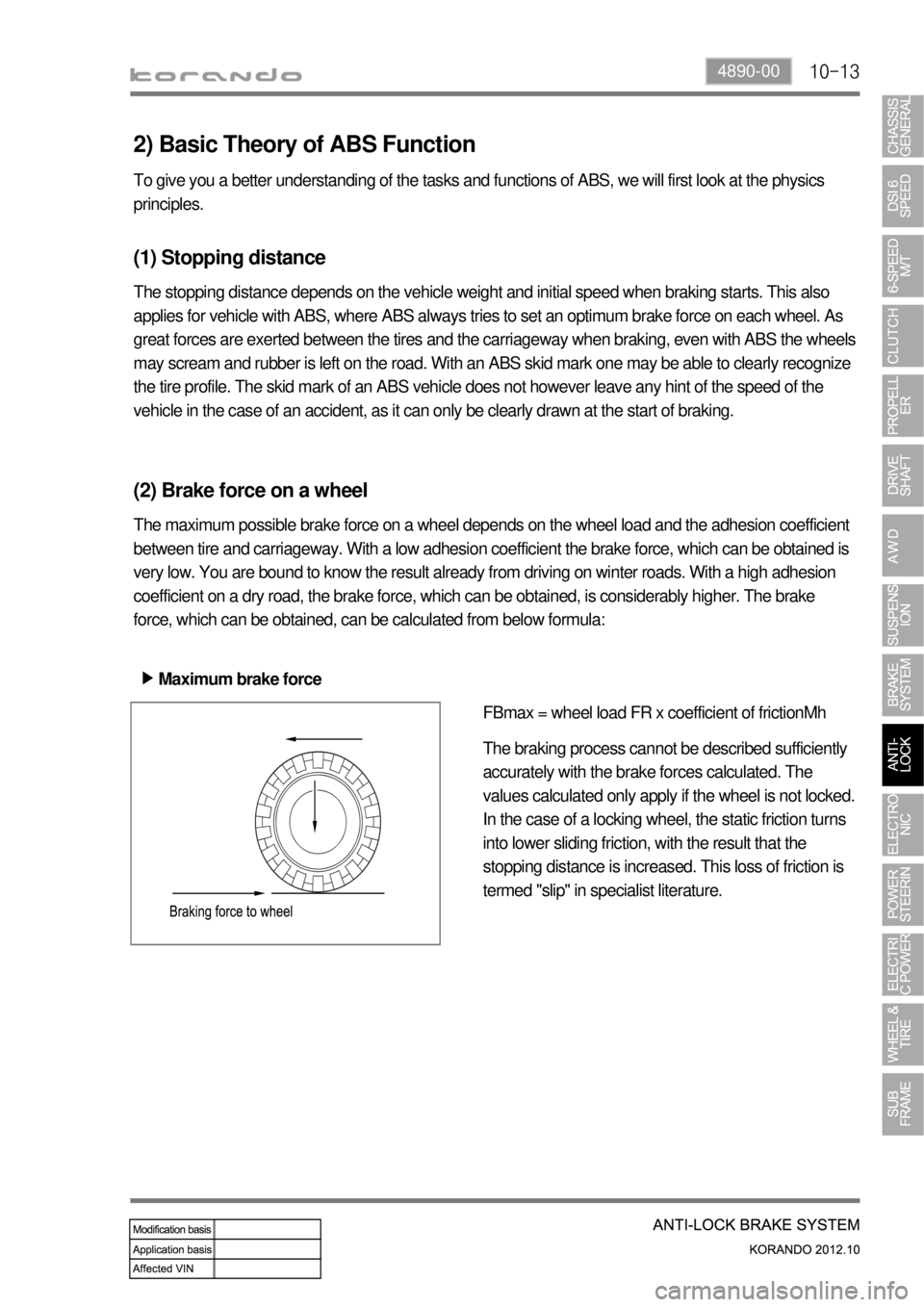
10-134890-00
2) Basic Theory of ABS Function
To give you a better understanding of the tasks and functions of ABS, we will first look at the physics
principles.
(1) Stopping distance
The stopping distance depends on the vehicle weight and initial speed when braking starts. This also
applies for vehicle with ABS, where ABS always tries to set an optimum brake force on each wheel. As
great forces are exerted between the tires and the carriageway when braking, even with ABS the wheels
may scream and rubber is left on the road. With an ABS skid mark one may be able to clearly recognize
the tire profile. The skid mark of an ABS vehicle does not however leave any hint of the speed of the
vehicle in the case of an accident, as it can only be clearly drawn at the start of braking.
(2) Brake force on a wheel
The maximum possible brake force on a wheel depends on the wheel load and the adhesion coefficient
between tire and carriageway. With a low adhesion coefficient the brake force, which can be obtained is
very low. You are bound to know the result already from driving on winter roads. With a high adhesion
coefficient on a dry road, the brake force, which can be obtained, is considerably higher. The brake
force, which can be obtained, can be calculated from below formula:
Maximum brake force â–¶
FBmax = wheel load FR x coefficient of frictionMh
The braking process cannot be described sufficiently
accurately with the brake forces calculated. The
values calculated only apply if the wheel is not locked.
In the case of a locking wheel, the static friction turns
into lower sliding friction, with the result that the
stopping distance is increased. This loss of friction is
termed "slip" in specialist literature.
Page 989 of 1082
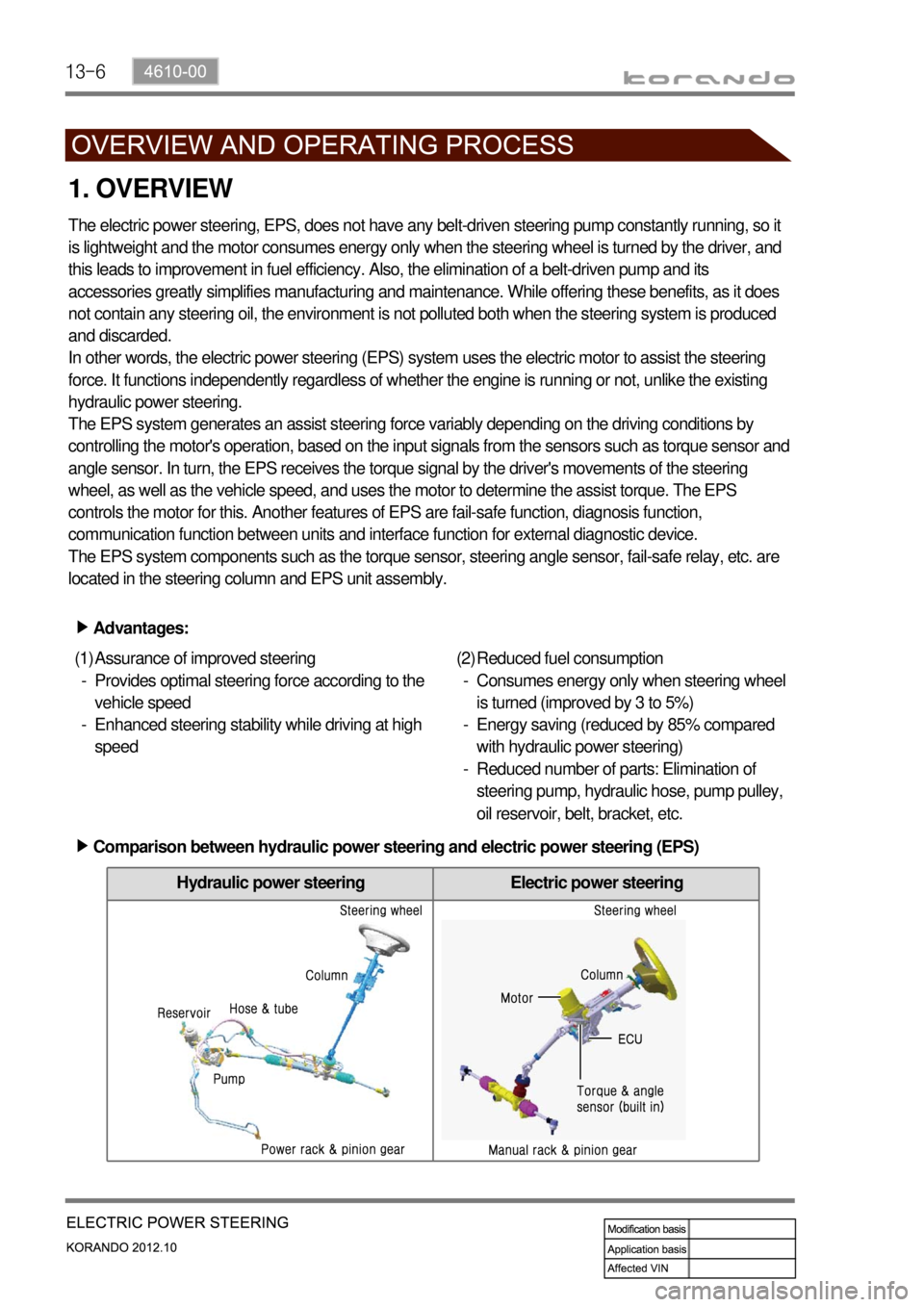
13-6
Hydraulic power steering Electric power steering
1. OVERVIEW
The electric power steering, EPS, does not have any belt-driven steering pump constantly running, so it
is lightweight and the motor consumes energy only when the steering wheel is turned by the driver, and
this leads to improvement in fuel efficiency. Also, the elimination of a belt-driven pump and its
accessories greatly simplifies manufacturing and maintenance. While offering these benefits, as it does
not contain any steering oil, the environment is not polluted both when the steering system is produced
and discarded.
In other words, the electric power steering (EPS) system uses the electric motor to assist the steering
force. It functions independently regardless of whether the engine is running or not, unlike the existing
hydraulic power steering.
The EPS system generates an assist steering force variably depending on the driving conditions by
controlling the motor's operation, based on the input signals from the sensors such as torque sensor and
angle sensor. In turn, the EPS receives the torque signal by the driver's movements of the steering
wheel, as well as the vehicle speed, and uses the motor to determine the assist torque. The EPS
controls the motor for this. Another features of EPS are fail-safe function, diagnosis function,
communication function between units and interface function for external diagnostic device.
The EPS system components such as the torque sensor, steering angle sensor, fail-safe relay, etc. are
located in the steering column and EPS unit assembly.
Advantages: â–¶
Assurance of improved steering
Provides optimal steering force according to the
vehicle speed
Enhanced steering stability while driving at high
speed (1)
-
-Reduced fuel consumption
Consumes energy only when steering wheel
is turned (improved by 3 to 5%)
Energy saving (reduced by 85% compared
with hydraulic power steering)
Reduced number of parts: Elimination of
steering pump, hydraulic hose, pump pulley,
oil reservoir, belt, bracket, etc. (2)
-
-
-
Comparison between hydraulic power steering and electric power steering (EPS) â–¶
Page 991 of 1082
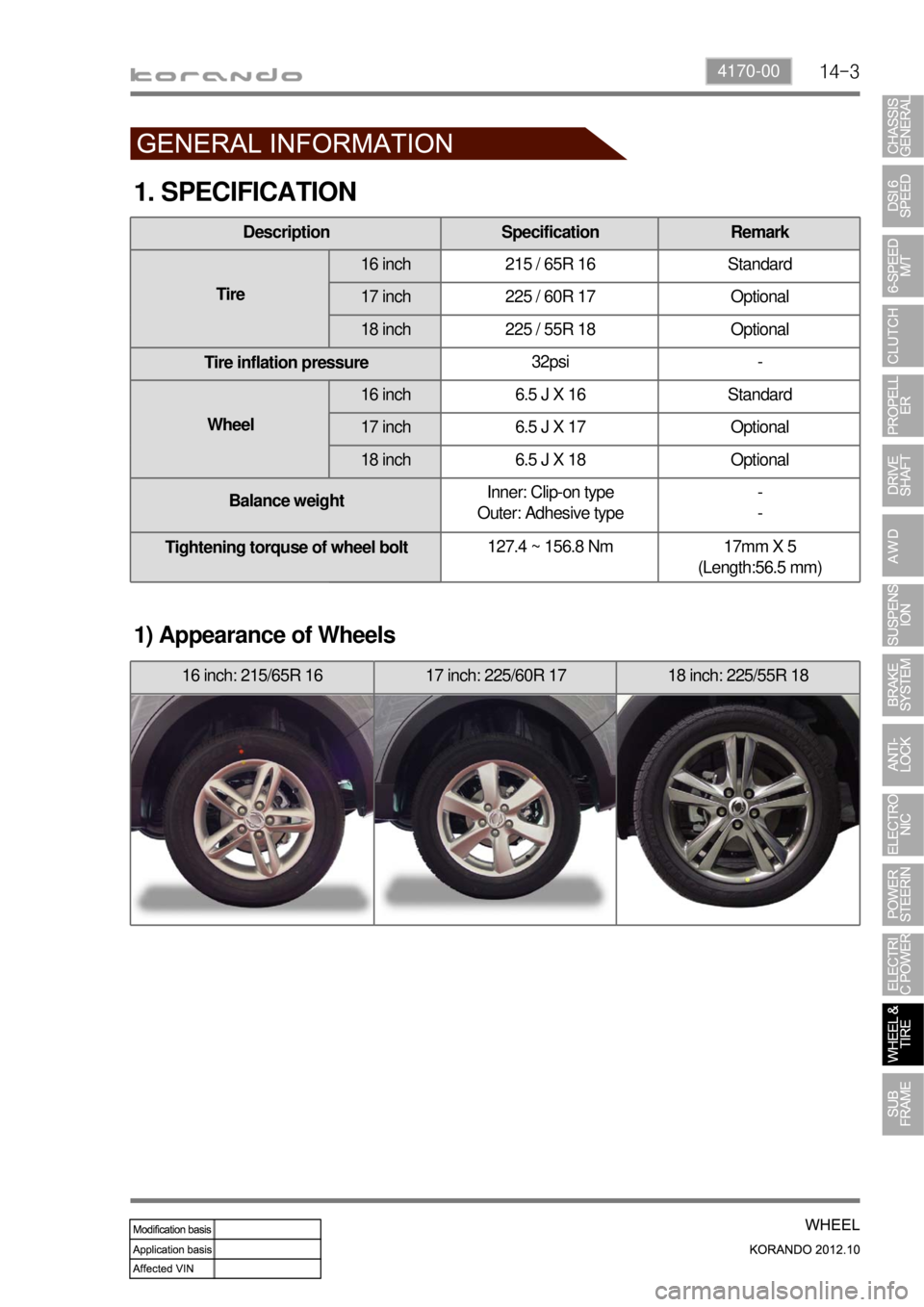
14-34170-00
1. SPECIFICATION
1) Appearance of Wheels
16 inch: 215/65R 16 17 inch: 225/60R 17 18 inch: 225/55R 18
Description Specification Remark
Tire16 inch 215 / 65R 16 Standard
17 inch 225 / 60R 17 Optional
18 inch 225 / 55R 18 Optional
Tire inflation pressure32psi -
Wheel16 inch 6.5 J X 16 Standard
17 inch 6.5 J X 17 Optional
18 inch 6.5 J X 18 Optional
Balance weightInner: Clip-on type
Outer: Adhesive type-
-
Tightening torquse of wheel bolt127.4 ~ 156.8 Nm 17mm X 5
(Length:56.5 mm)
Page 992 of 1082
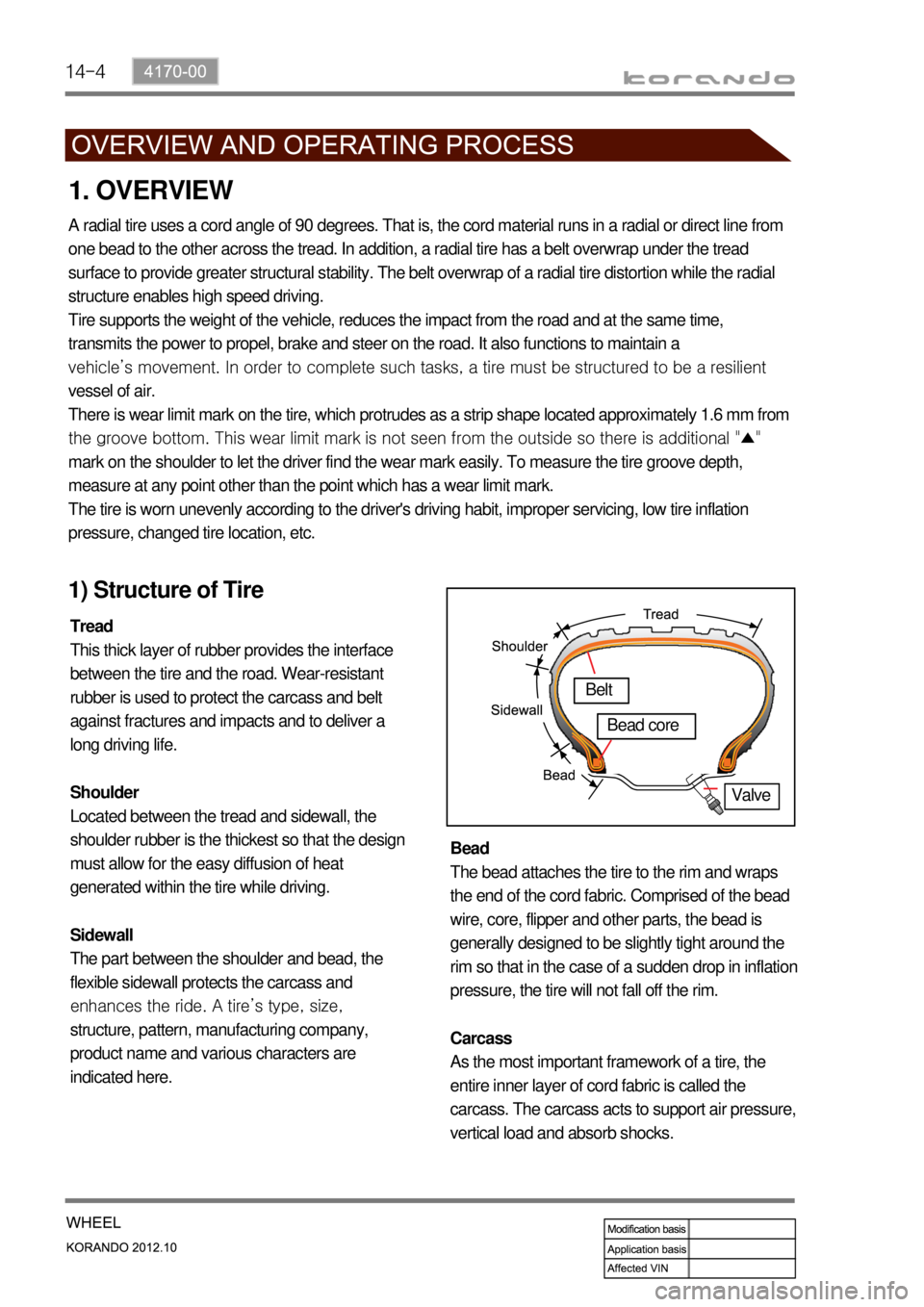
14-4
1. OVERVIEW
A radial tire uses a cord angle of 90 degrees. That is, the cord material runs in a radial or direct line from
one bead to the other across the tread. In addition, a radial tire has a belt overwrap under the tread
surface to provide greater structural stability. The belt overwrap of a radial tire distortion while the radial
structure enables high speed driving.
Tire supports the weight of the vehicle, reduces the impact from the road and at the same time,
transmits the power to propel, brake and steer on the road. It also functions to maintain a
<009d008c008f0090008a0093008c02c5009a004700940096009d008c0094008c0095009b0055004700700095004700960099008b008c00990047009b00960047008a0096009400970093008c009b008c0047009a009c008a008f0047009b0088009a009200
9a0053004700880047009b00900099008c00470094009c009a>t be structured to be a resilient
vessel of air.
There is wear limit mark on the tire, which protrudes as a strip shape located approximately 1.6 mm from
<009b008f008c0047008e009900960096009d008c004700890096009b009b0096009400550047007b008f0090009a0047009e008c0088009900470093009000940090009b0047009400880099009200470090009a004700950096009b0047009a008c008c00
950047008d0099009600940047009b008f008c00470096009c>tside so there is additional "â–²"
mark on the shoulder to let the driver find the wear mark easily. To measure the tire groove depth,
measure at any point other than the point which has a wear limit mark.
The tire is worn unevenly according to the driver's driving habit, improper servicing, low tire inflation
pressure, changed tire location, etc.
1) Structure of Tire
Tread
This thick layer of rubber provides the interface
between the tire and the road. Wear-resistant
rubber is used to protect the carcass and belt
against fractures and impacts and to deliver a
long driving life.
Shoulder
Located between the tread and sidewall, the
shoulder rubber is the thickest so that the design
must allow for the easy diffusion of heat
generated within the tire while driving.
Sidewall
The part between the shoulder and bead, the
flexible sidewall protects the carcass and
enhances the ride. A tire’s type, size,
structure, pattern, manufacturing company,
product name and various characters are
indicated here. Bead
The bead attaches the tire to the rim and wraps
the end of the cord fabric. Comprised of the bead
wire, core, flipper and other parts, the bead is
generally designed to be slightly tight around the
rim so that in the case of a sudden drop in inflation
pressure, the tire will not fall off the rim.
Carcass
As the most important framework of a tire, the
entire inner layer of cord fabric is called the
carcass. The carcass acts to support air pressure,
vertical load and absorb shocks.
Valve
Belt
Bead core
Page 996 of 1082
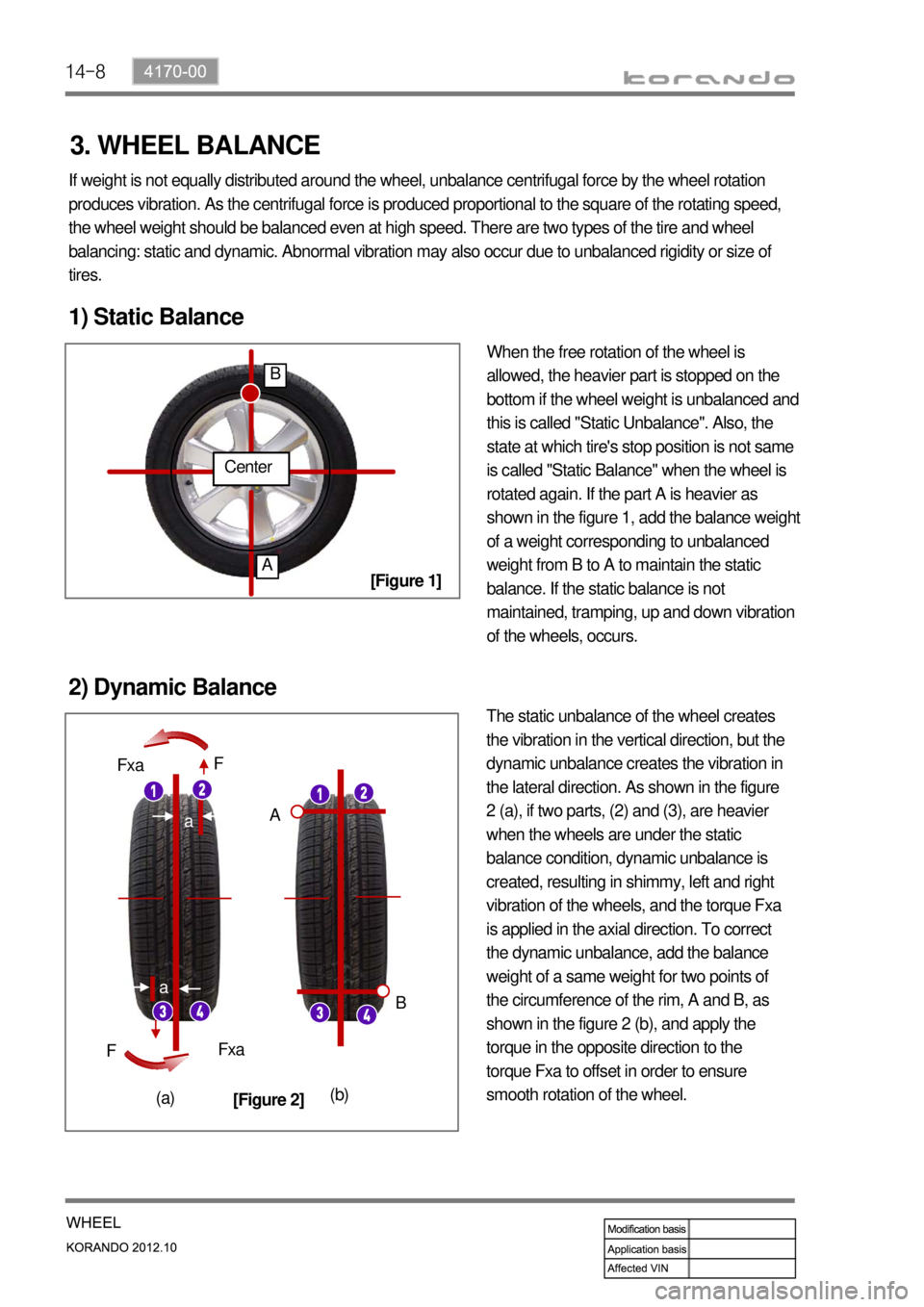
14-8
If weight is not equally distributed around the wheel, unbalance centrifugal force by the wheel rotation
produces vibration. As the centrifugal force is produced proportional to the square of the rotating speed,
the wheel weight should be balanced even at high speed. There are two types of the tire and wheel
balancing: static and dynamic. Abnormal vibration may also occur due to unbalanced rigidity or size of
tires.
1) Static Balance
When the free rotation of the wheel is
allowed, the heavier part is stopped on the
bottom if the wheel weight is unbalanced and
this is called "Static Unbalance". Also, the
state at which tire's stop position is not same
is called "Static Balance" when the wheel is
rotated again. If the part A is heavier as
shown in the figure 1, add the balance weight
of a weight corresponding to unbalanced
weight from B to A to maintain the static
balance. If the static balance is not
maintained, tramping, up and down vibration
of the wheels, occurs.
2) Dynamic Balance
The static unbalance of the wheel creates
the vibration in the vertical direction, but the
dynamic unbalance creates the vibration in
the lateral direction. As shown in the figure
2 (a), if two parts, (2) and (3), are heavier
when the wheels are under the static
balance condition, dynamic unbalance is
created, resulting in shimmy, left and right
vibration of the wheels, and the torque Fxa
is applied in the axial direction. To correct
the dynamic unbalance, add the balance
weight of a same weight for two points of
the circumference of the rim, A and B, as
shown in the figure 2 (b), and apply the
torque in the opposite direction to the
torque Fxa to offset in order to ensure
smooth rotation of the wheel.
Center
A
B
a
a
Fxa
Fxa F
F
A
B
(a)(b)
[Figure 1]
[Figure 2]
3. WHEEL BALANCE
Page 997 of 1082
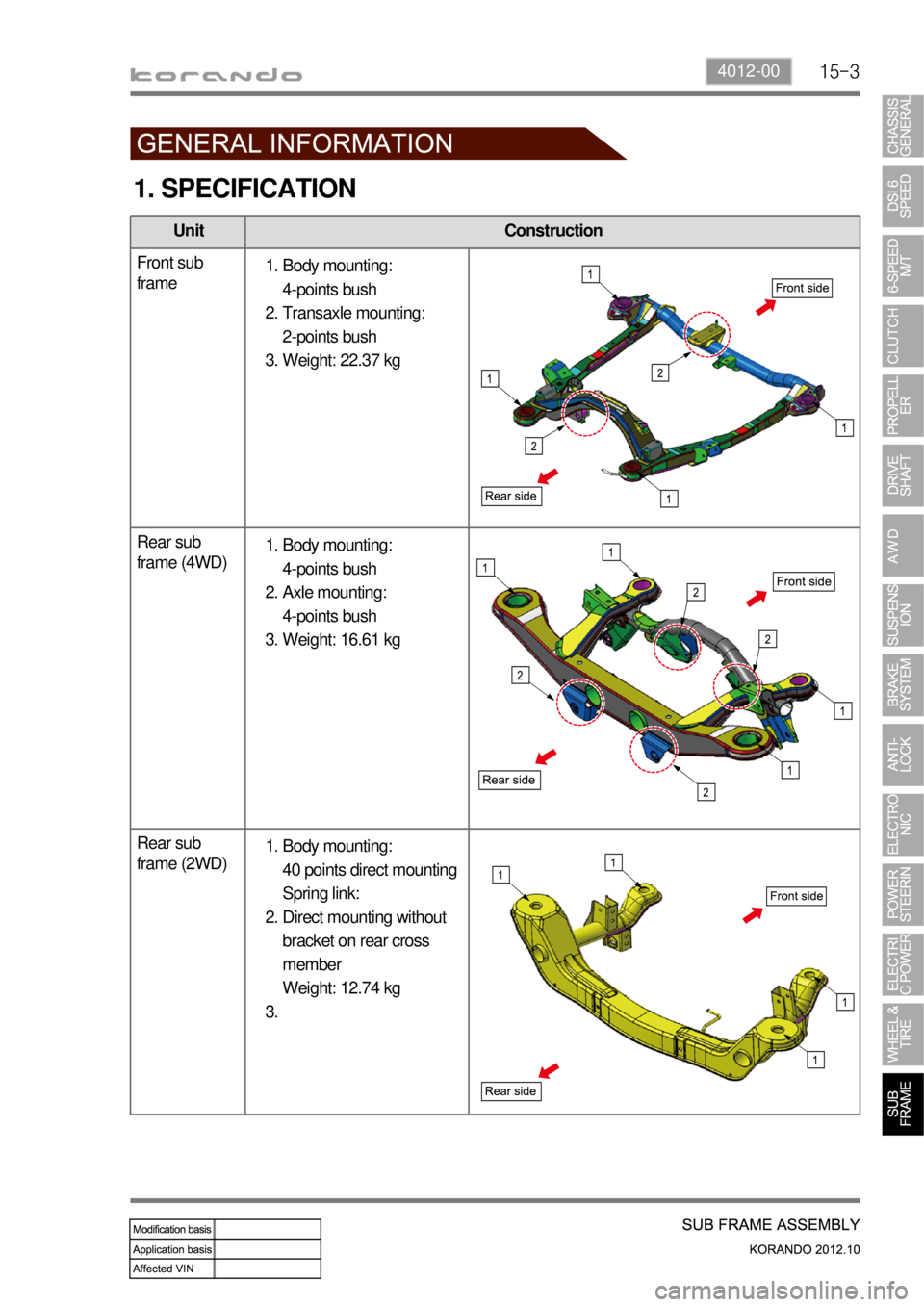
15-34012-00
1. SPECIFICATION
Unit Construction
Front sub
frame
Rear sub
frame (4WD)
Rear sub
frame (2WD)
Body mounting:
4-points bush
Transaxle mounting:
2-points bush
Weight: 22.37 kg 1.
2.
3.
Body mounting:
4-points bush
Axle mounting:
4-points bush
Weight: 16.61 kg 1.
2.
3.
Body mounting:
40 points direct mounting
Spring link:
Direct mounting without
bracket on rear cross
member
Weight: 12.74 kg 1.
2.
3.