lock SSANGYONG MUSSO 1998 Workshop User Guide
[x] Cancel search | Manufacturer: SSANGYONG, Model Year: 1998, Model line: MUSSO, Model: SSANGYONG MUSSO 1998Pages: 1463, PDF Size: 19.88 MB
Page 79 of 1463
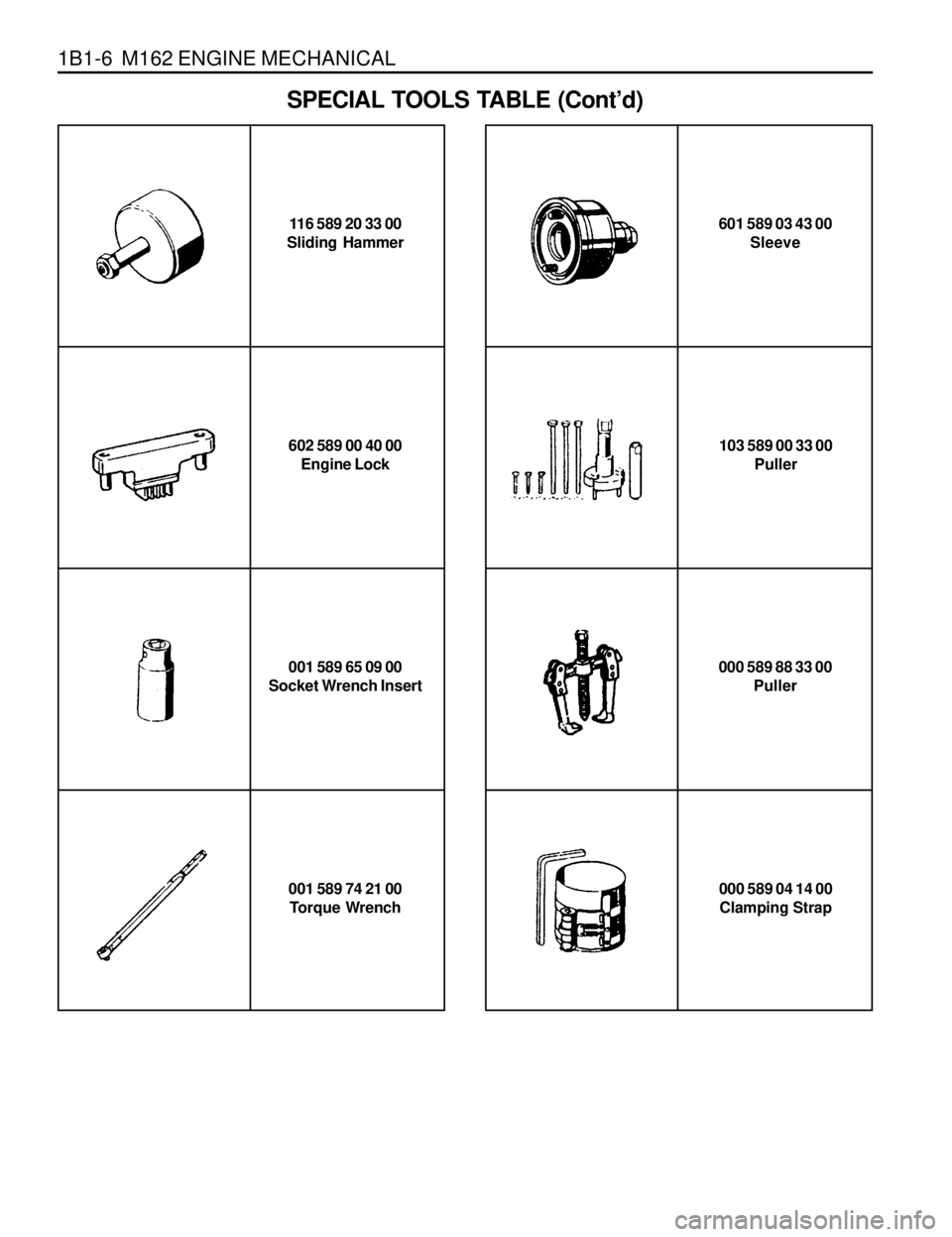
1B1-6 M162 ENGINE MECHANICAL
116 589 20 33 00
Sliding Hammer
602 589 00 40 00
Engine Lock103 589 00 33 00
Puller
SPECIAL TOOLS TABLE (Cont’d)
601 589 03 43 00
Sleeve
001 589 65 09 00
Socket Wrench Insert
001 589 74 21 00
Torque Wrench000 589 04 14 00
Clamping Strap 000 589 88 33 00
Puller
Page 83 of 1463
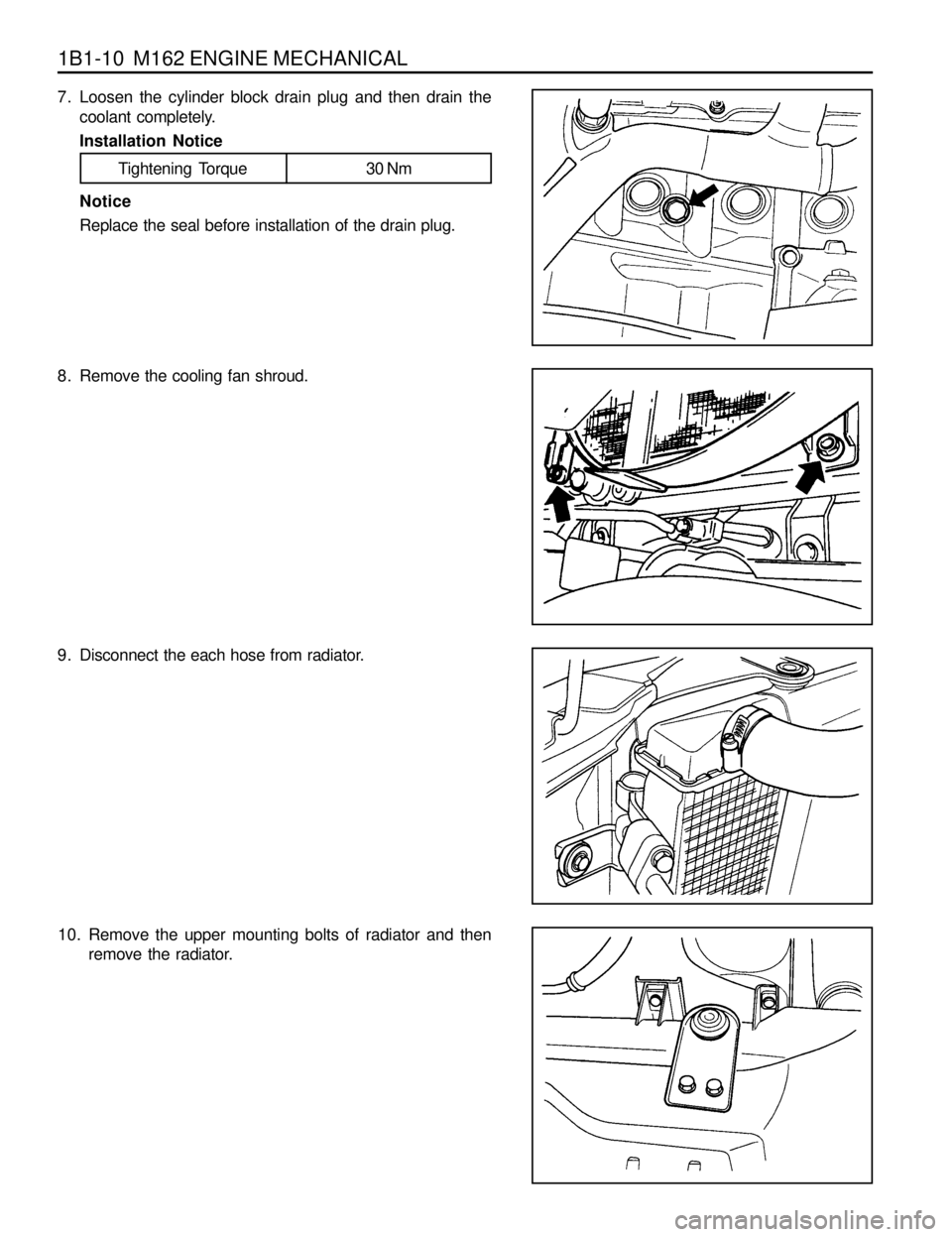
1B1-10 M162 ENGINE MECHANICAL
10. Remove the upper mounting bolts of radiator and then
remove the radiator.
7. Loosen the cylinder block drain plug and then drain the
coolant completely.
Installation Notice
Tightening Torque 30 Nm
Notice
Replace the seal before installation of the drain plug.
8. Remove the cooling fan shroud.
9. Disconnect the each hose from radiator.
Page 93 of 1463
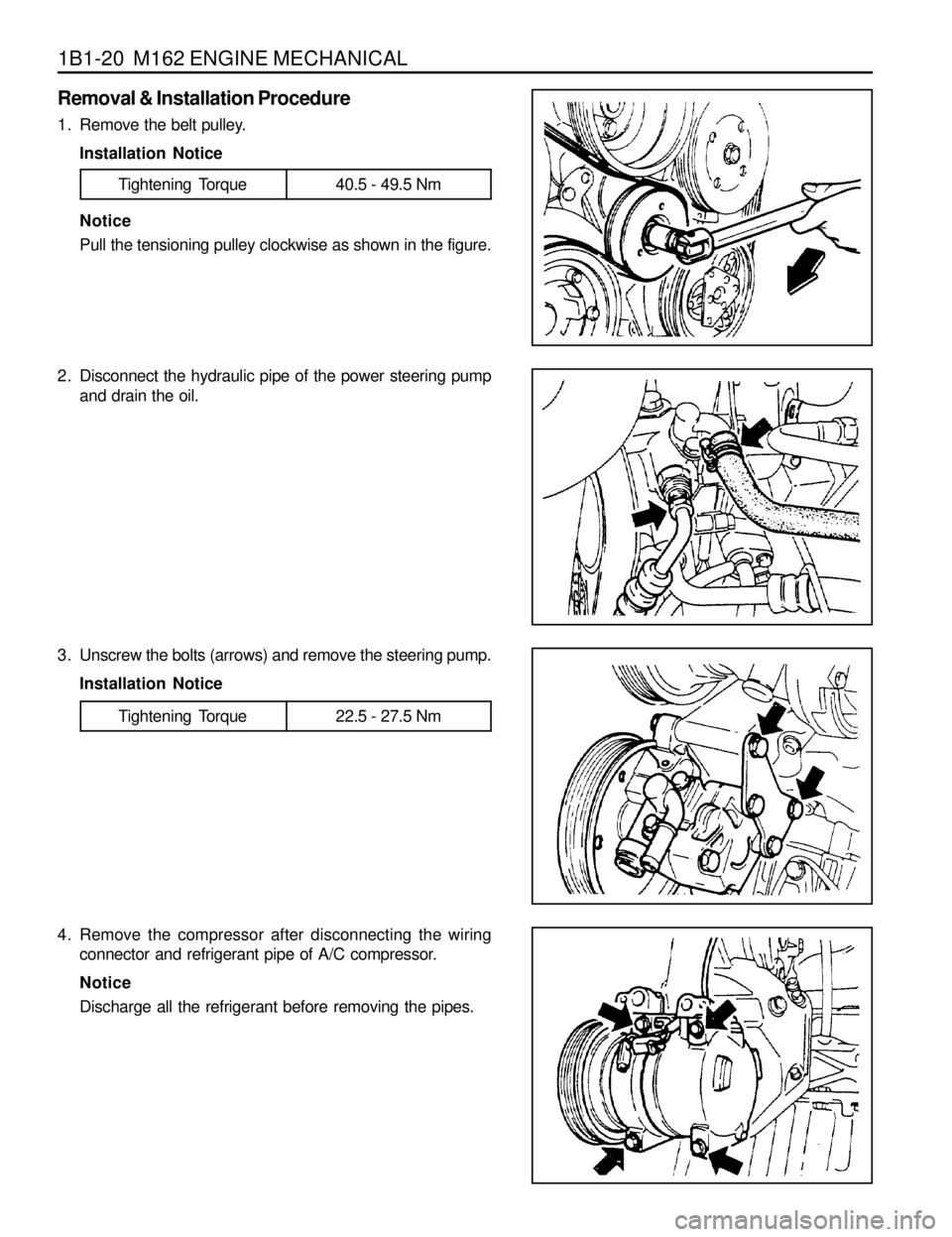
1B1-20 M162 ENGINE MECHANICAL
Removal & Installation Procedure
1. Remove the belt pulley.
Installation Notice
2. Disconnect the hydraulic pipe of the power steering pump
and drain the oil.
3. Unscrew the bolts (arrows) and remove the steering pump.
Installation Notice Notice
Pull the tensioning pulley clockwise as shown in the figure.
4. Remove the compressor after disconnecting the wiring
connector and refrigerant pipe of A/C compressor.
Notice
Discharge all the refrigerant before removing the pipes.
Tightening Torque 40.5 - 49.5 Nm
Tightening Torque 22.5 - 27.5 Nm
Page 98 of 1463
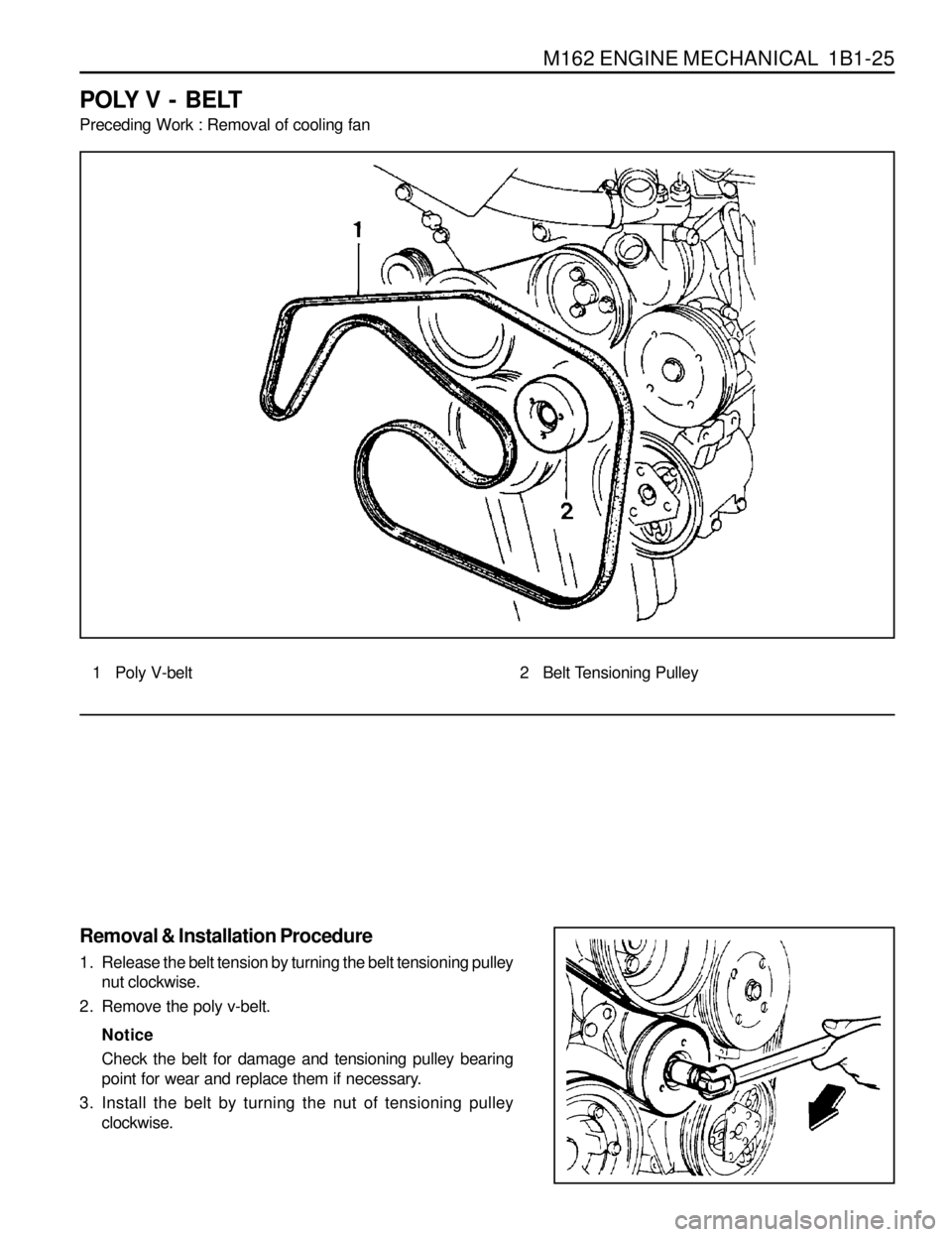
M162 ENGINE MECHANICAL 1B1-25
POLY V - BELT
Preceding Work : Removal of cooling fan
1 Poly V-belt
Removal & Installation Procedure
1. Release the belt tension by turning the belt tensioning pulley
nut clockwise.
2. Remove the poly v-belt.
Notice
Check the belt for damage and tensioning pulley bearing
point for wear and replace them if necessary.
3. Install the belt by turning the nut of tensioning pulley
clockwise.
2 Belt Tensioning Pulley
Page 100 of 1463
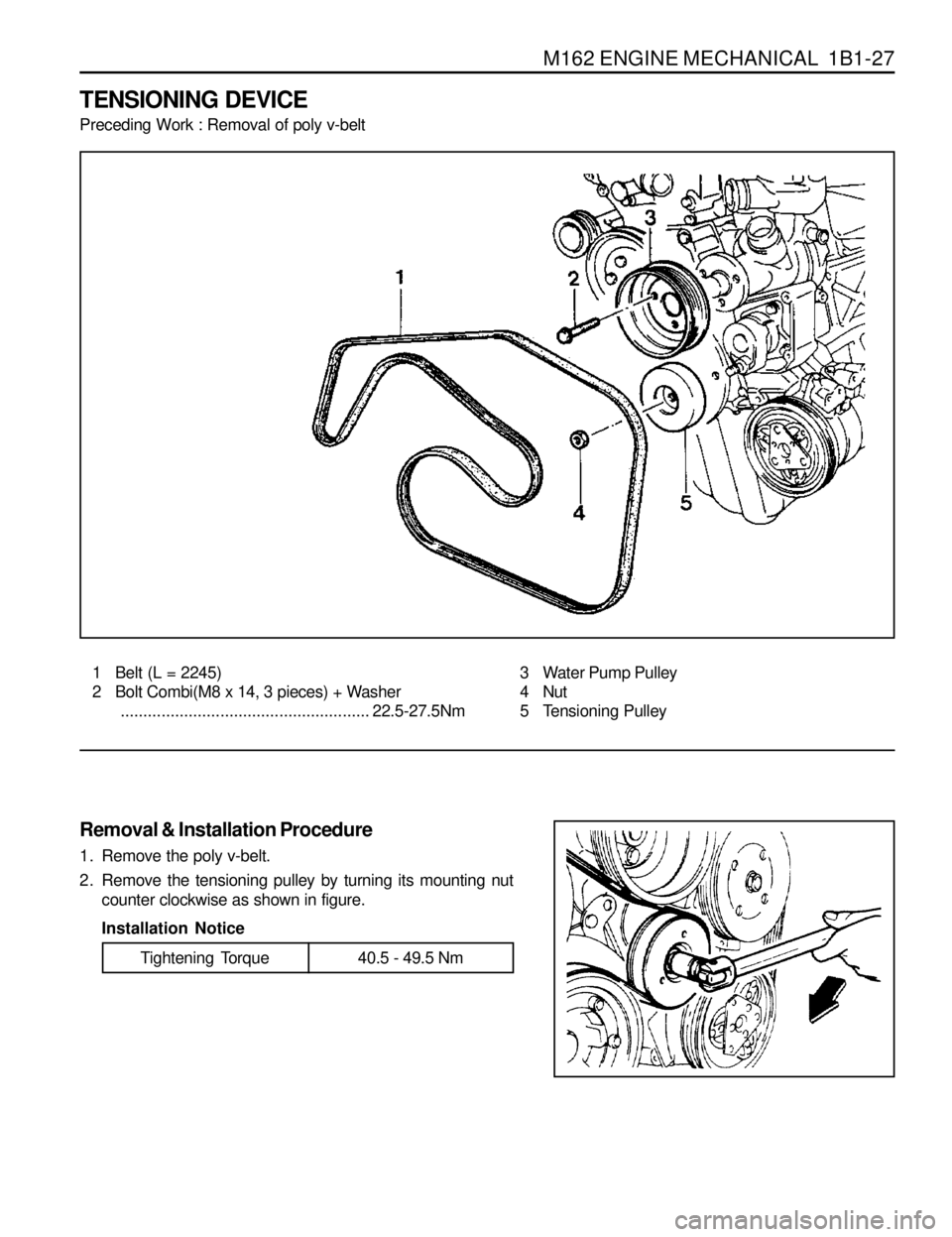
M162 ENGINE MECHANICAL 1B1-27
TENSIONING DEVICE
Preceding Work : Removal of poly v-belt
1 Belt (L = 2245)
2 Bolt Combi(M8 x 14, 3 pieces) + Washer
.......................................................22.5-27.5Nm
Removal & Installation Procedure
1. Remove the poly v-belt.
2. Remove the tensioning pulley by turning its mounting nut
counter clockwise as shown in figure.
Installation Notice3 Water Pump Pulley
4 Nut
5 Tensioning Pulley
Tightening Torque 40.5 - 49.5 Nm
Page 116 of 1463
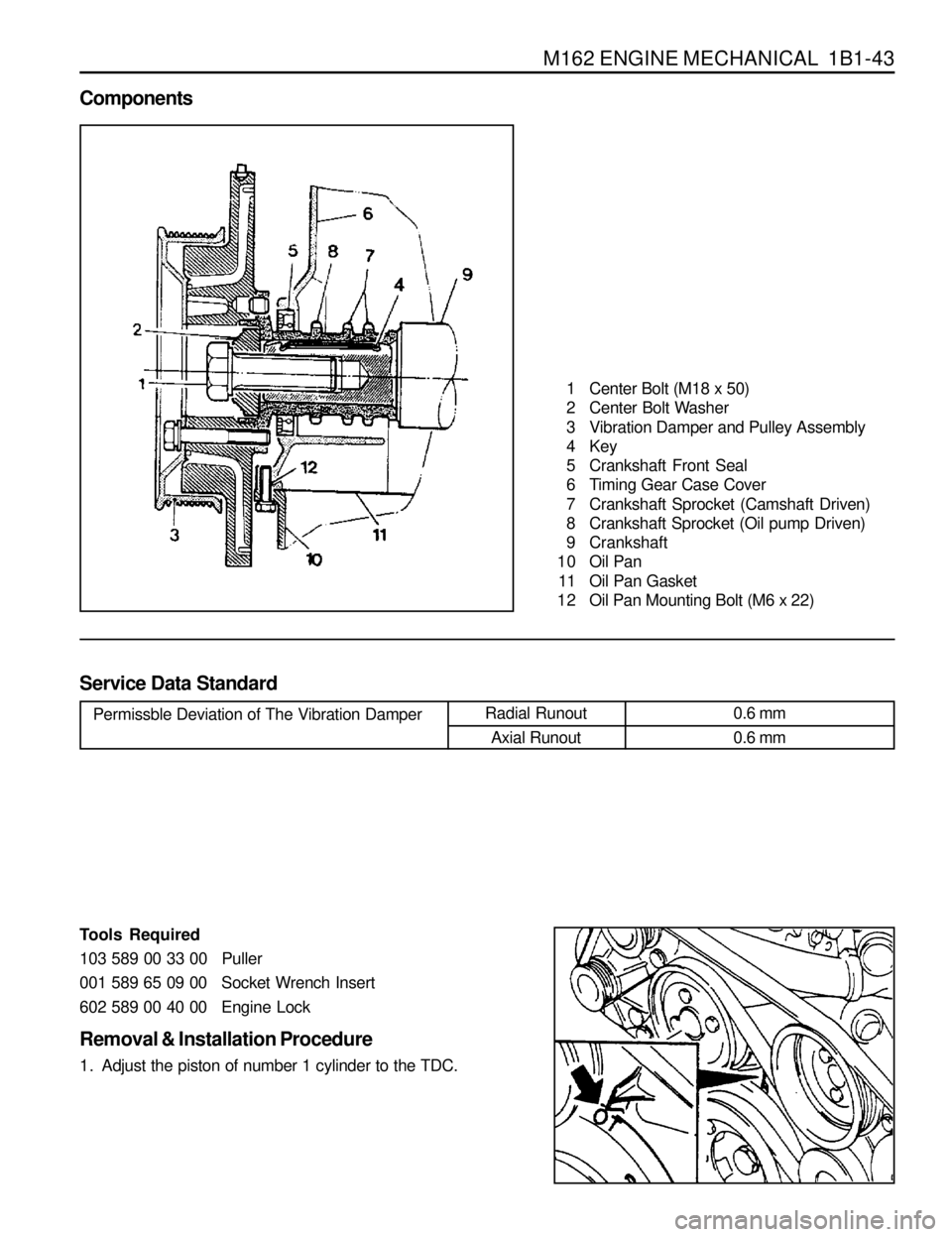
M162 ENGINE MECHANICAL 1B1-43
Components
1 Center Bolt (M18 x 50)
2 Center Bolt Washer
3 Vibration Damper and Pulley Assembly
4 Key
5 Crankshaft Front Seal
6 Timing Gear Case Cover
7 Crankshaft Sprocket (Camshaft Driven)
8 Crankshaft Sprocket (Oil pump Driven)
9 Crankshaft
10 Oil Pan
11 Oil Pan Gasket
12 Oil Pan Mounting Bolt (M6 x 22)
Service Data Standard
Permissble Deviation of The Vibration DamperRadial Runout
Axial Runout0.6 mm
0.6 mm
Tools Required
103 589 00 33 00 Puller
001 589 65 09 00 Socket Wrench Insert
602 589 00 40 00 Engine Lock
Removal & Installation Procedure
1. Adjust the piston of number 1 cylinder to the TDC.
Page 117 of 1463
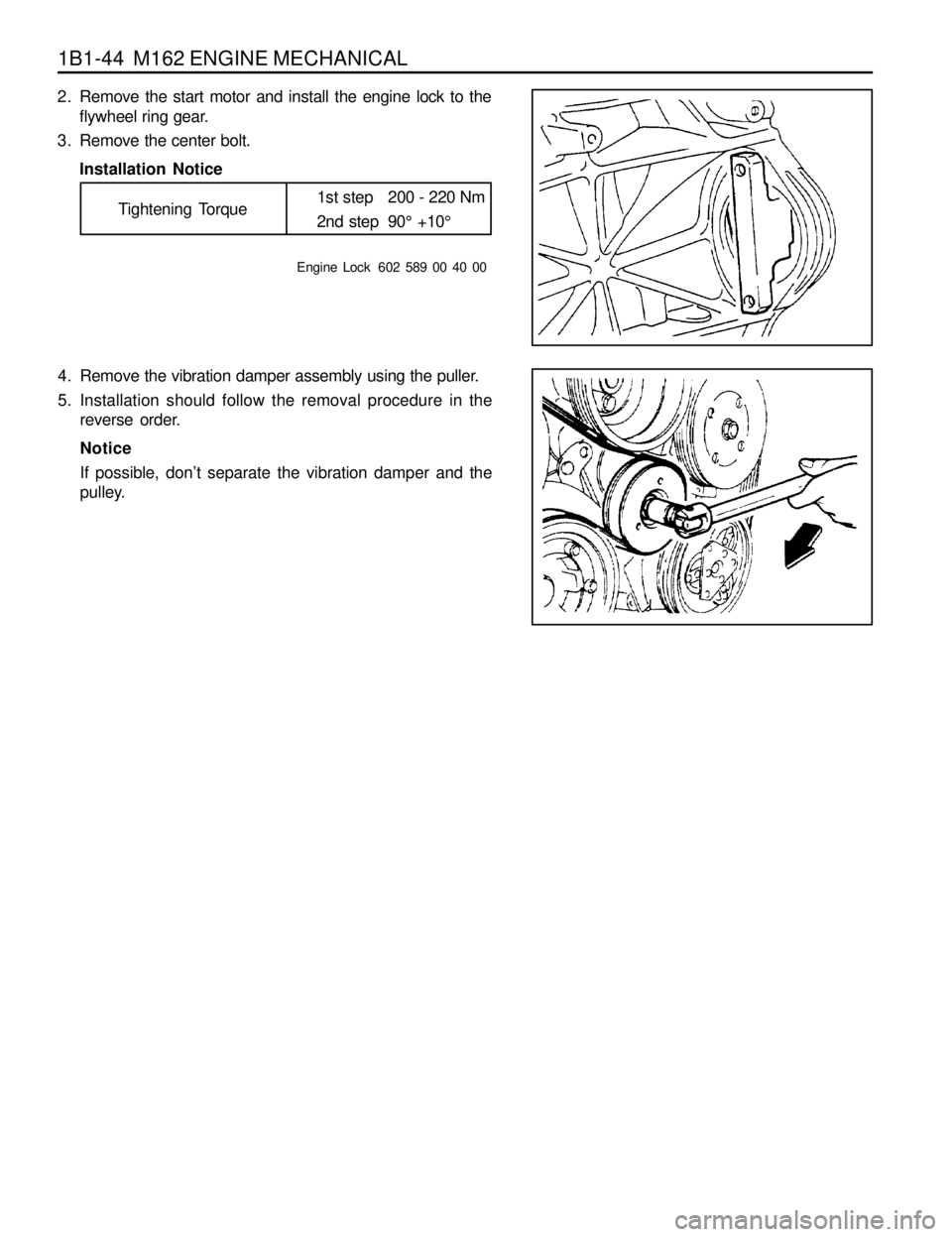
1B1-44 M162 ENGINE MECHANICAL
Engine Lock 602 589 00 40 00
2. Remove the start motor and install the engine lock to the
flywheel ring gear.
3. Remove the center bolt.
Installation Notice
Tightening Torque1st step 200 - 220 Nm
2nd step 90° +10°
4. Remove the vibration damper assembly using the puller.
5. Installation should follow the removal procedure in the
reverse order.
Notice
If possible, don’t separate the vibration damper and the
pulley.
Page 124 of 1463
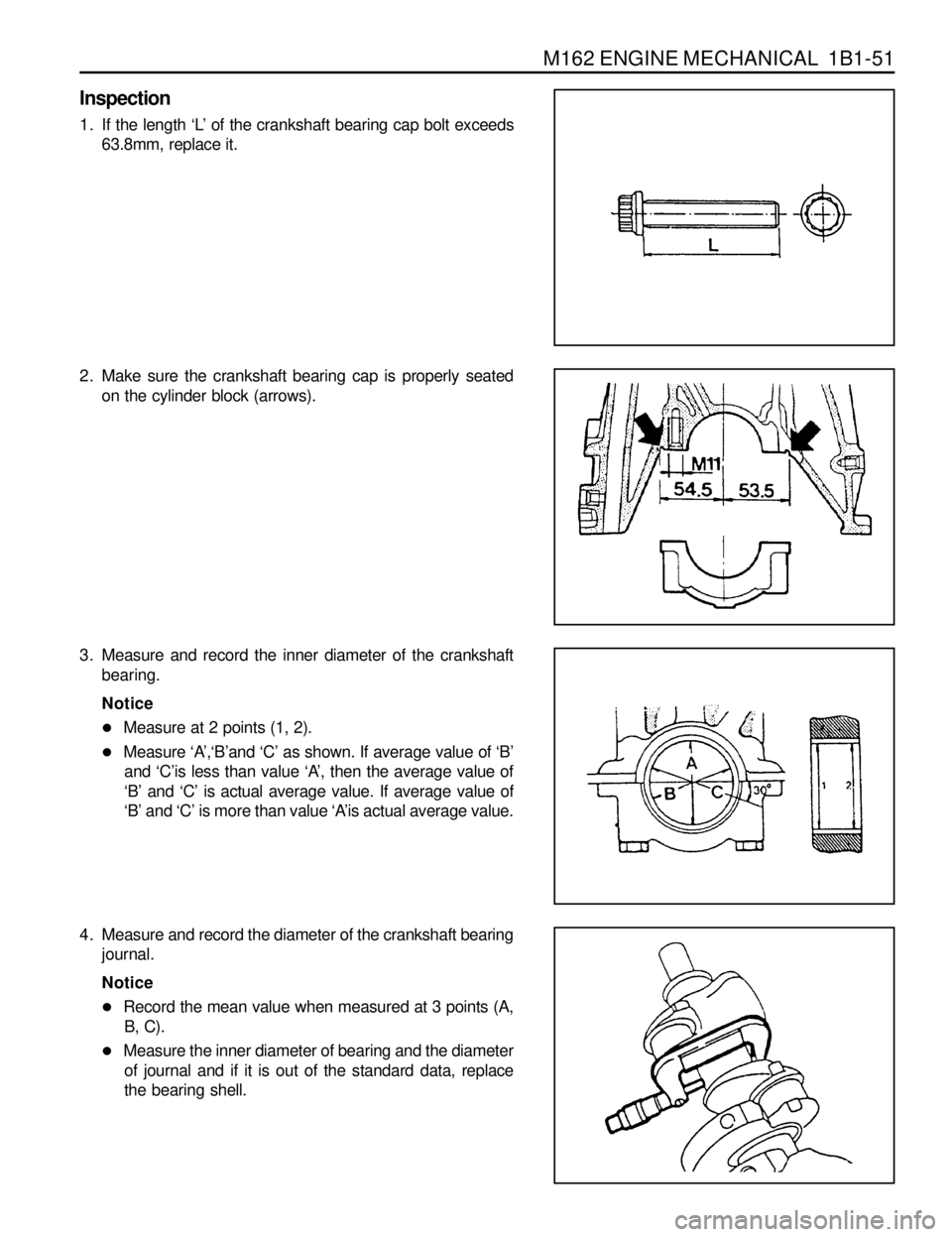
M162 ENGINE MECHANICAL 1B1-51
Inspection
1. If the length ‘L’ of the crankshaft bearing cap bolt exceeds
63.8mm, replace it.
2. Make sure the crankshaft bearing cap is properly seated
on the cylinder block (arrows).
3. Measure and record the inner diameter of the crankshaft
bearing.
Notice
lMeasure at 2 points (1, 2).
lMeasure ‘A’,‘B’and ‘C’ as shown. If average value of ‘B’
and ‘C’is less than value ‘A’, then the average value of
‘B’ and ‘C’ is actual average value. If average value of
‘B’ and ‘C’ is more than value ‘A’is actual average value.
4. Measure and record the diameter of the crankshaft bearing
journal.
Notice
lRecord the mean value when measured at 3 points (A,
B, C).
lMeasure the inner diameter of bearing and the diameter
of journal and if it is out of the standard data, replace
the bearing shell.
Page 134 of 1463
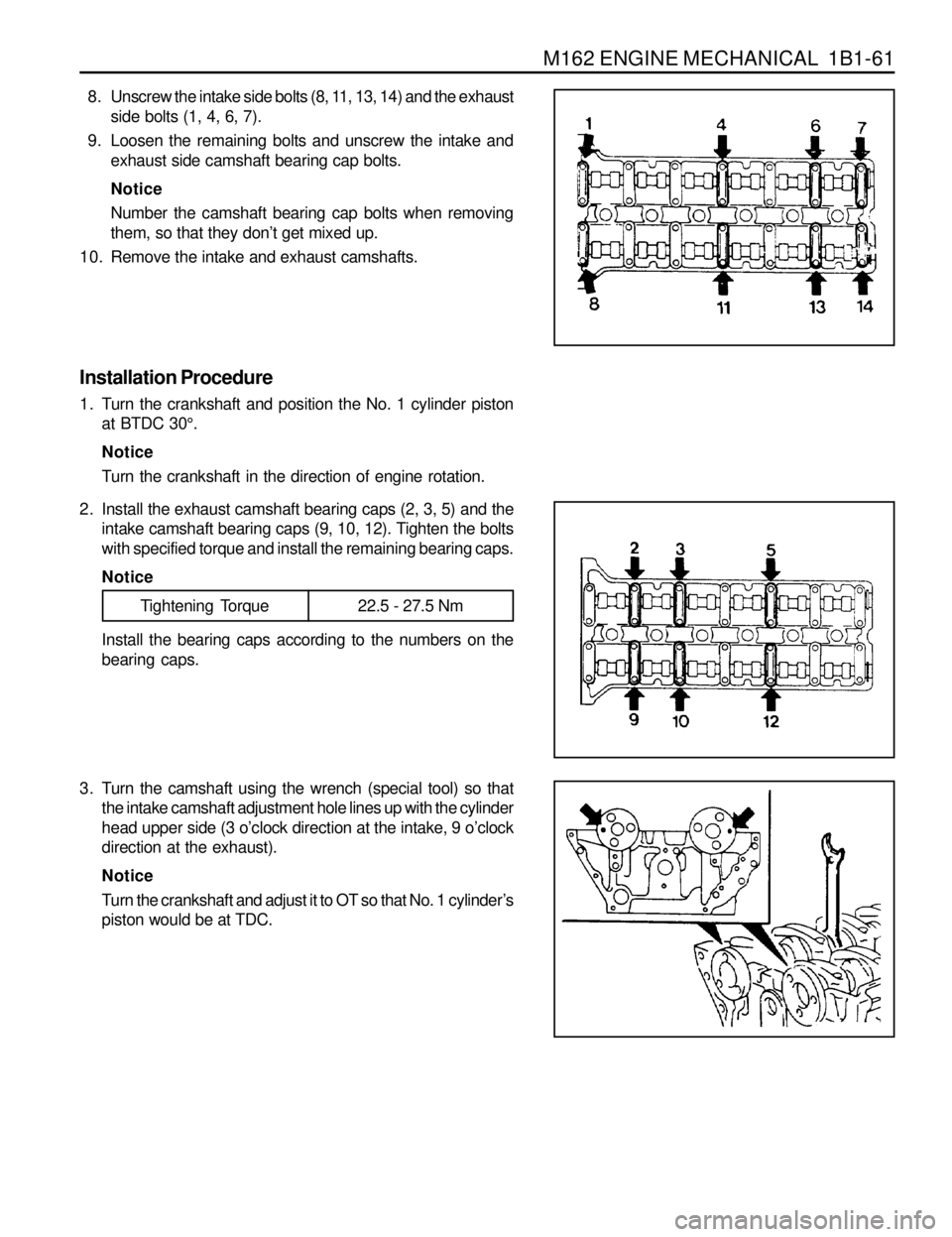
M162 ENGINE MECHANICAL 1B1-61
8 . Unscrew the intake side bolts (8, 11, 13, 14) and the exhaust
side bolts (1, 4, 6, 7).
9. Loosen the remaining bolts and unscrew the intake and
exhaust side camshaft bearing cap bolts.
Notice
Number the camshaft bearing cap bolts when removing
them, so that they don’t get mixed up.
10. Remove the intake and exhaust camshafts.
Installation Procedure
1. Turn the crankshaft and position the No. 1 cylinder piston
at BTDC 30°.
Notice
Turn the crankshaft in the direction of engine rotation.
3. Turn the camshaft using the wrench (special tool) so that
the intake camshaft adjustment hole lines up with the cylinder
head upper side (3 o’clock direction at the intake, 9 o’clock
direction at the exhaust).
Notice
Turn the crankshaft and adjust it to OT so that No. 1 cylinder’s
piston would be at TDC. Install the bearing caps according to the numbers on the
bearing caps.
Tightening Torque 22.5 - 27.5 Nm 2. Install the exhaust camshaft bearing caps (2, 3, 5) and the
intake camshaft bearing caps (9, 10, 12). Tighten the bolts
with specified torque and install the remaining bearing caps.
Notice
Page 138 of 1463
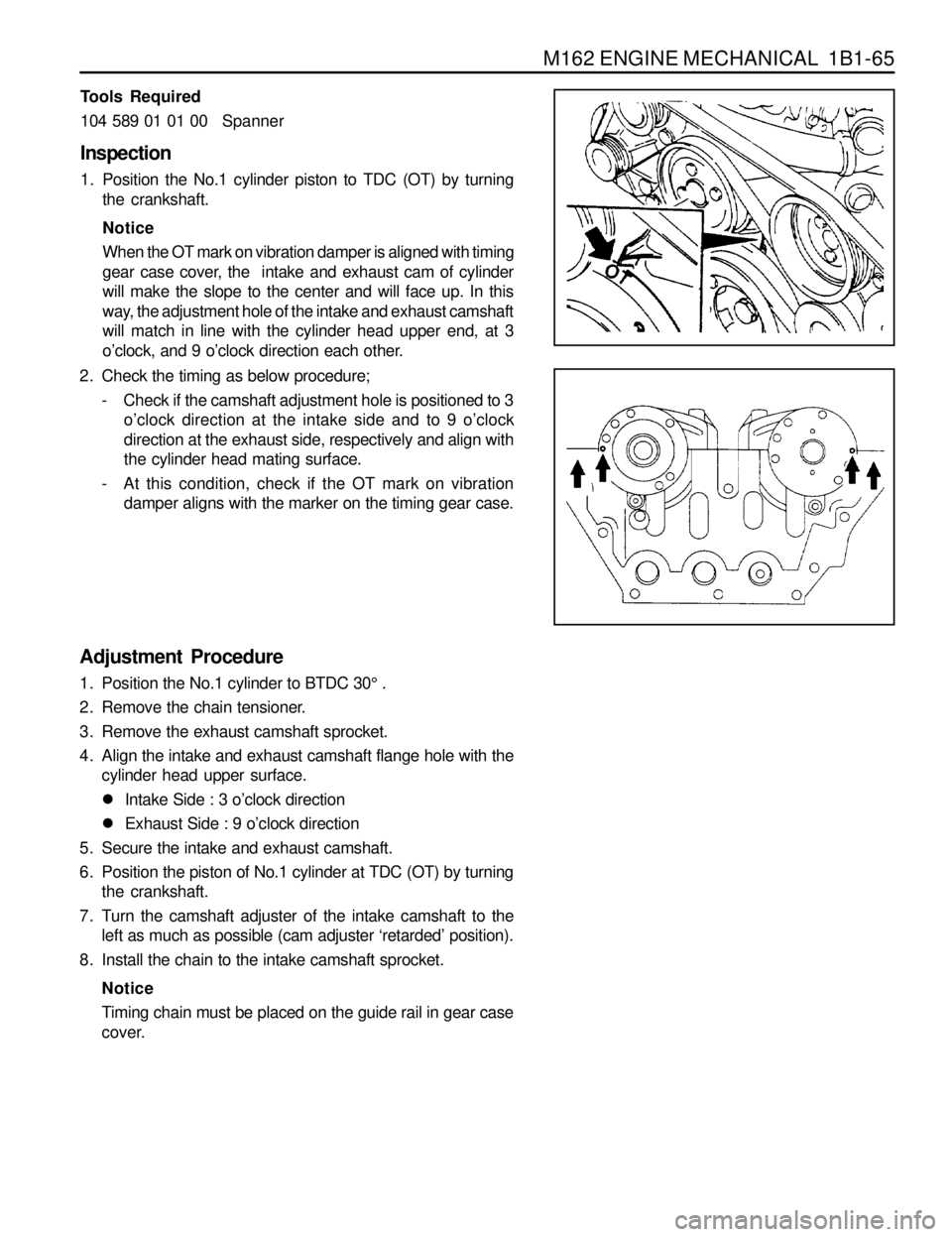
M162 ENGINE MECHANICAL 1B1-65
Adjustment Procedure
1. Position the No.1 cylinder to BTDC 30° .
2. Remove the chain tensioner.
3. Remove the exhaust camshaft sprocket.
4. Align the intake and exhaust camshaft flange hole with the
cylinder head upper surface.
lIntake Side : 3 o’clock direction
lExhaust Side : 9 o’clock direction
5. Secure the intake and exhaust camshaft.
6. Position the piston of No.1 cylinder at TDC (OT) by turning
the crankshaft.
7. Turn the camshaft adjuster of the intake camshaft to the
left as much as possible (cam adjuster ‘retarded’ position).
8. Install the chain to the intake camshaft sprocket.
Notice
Timing chain must be placed on the guide rail in gear case
cover. Tools Required
104 589 01 01 00Spanner
Inspection
1. Position the No.1 cylinder piston to TDC (OT) by turning
the crankshaft.
Notice
When the OT mark on vibration damper is aligned with timing
gear case cover, the intake and exhaust cam of cylinder
will make the slope to the center and will face up. In this
way, the adjustment hole of the intake and exhaust camshaft
will match in line with the cylinder head upper end, at 3
o’clock, and 9 o’clock direction each other.
2. Check the timing as below procedure;
- Check if the camshaft adjustment hole is positioned to 3
o’clock direction at the intake side and to 9 o’clock
direction at the exhaust side, respectively and align with
the cylinder head mating surface.
- At this condition, check if the OT mark on vibration
damper aligns with the marker on the timing gear case.