filler SSANGYONG MUSSO 1998 Workshop Owner's Manual
[x] Cancel search | Manufacturer: SSANGYONG, Model Year: 1998, Model line: MUSSO, Model: SSANGYONG MUSSO 1998Pages: 1463, PDF Size: 19.88 MB
Page 733 of 1463
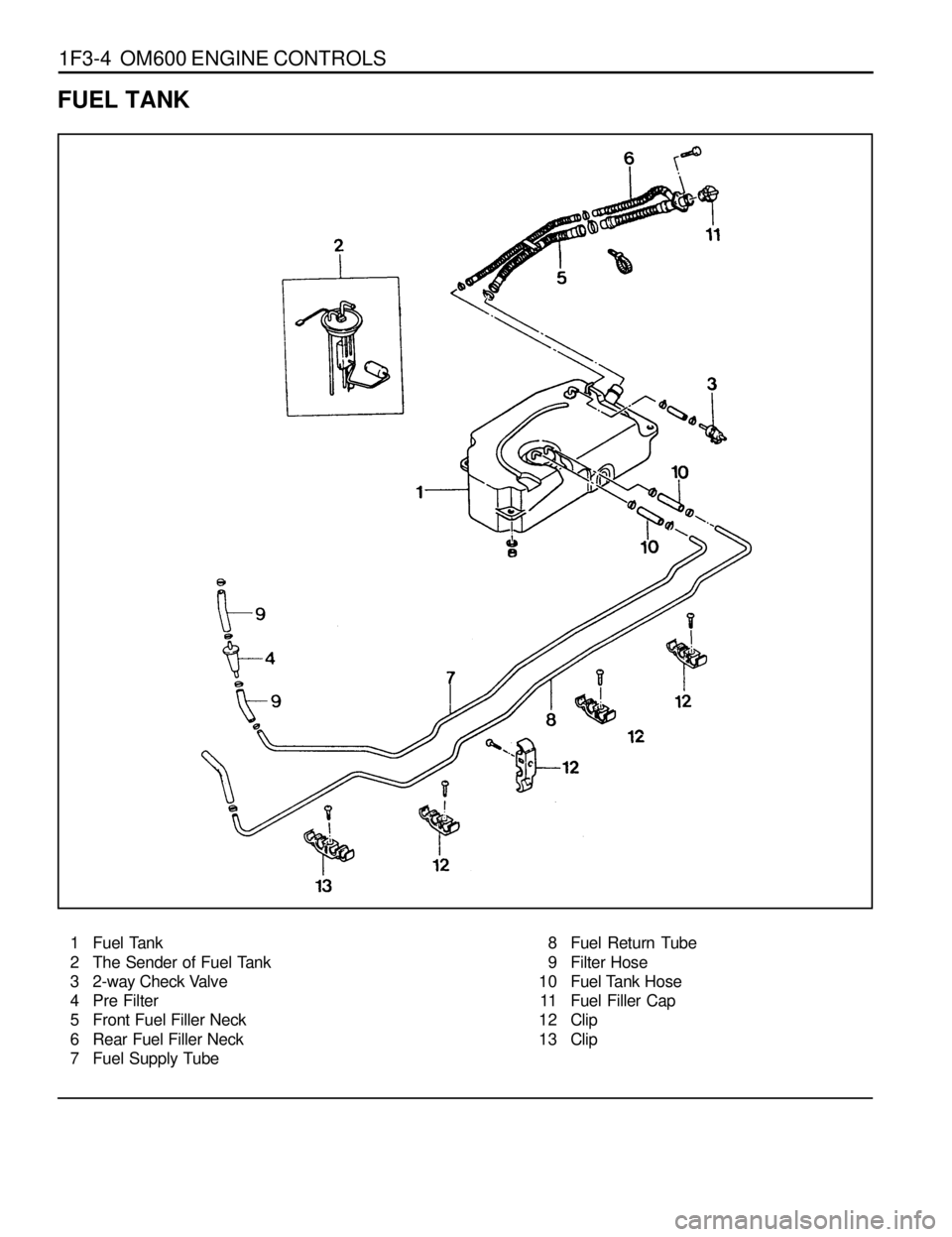
1F3-4 OM600 ENGINE CONTROLS
FUEL TANK
1 Fuel Tank
2 The Sender of Fuel Tank
3 2-way Check Valve
4 Pre Filter
5 Front Fuel Filler Neck
6 Rear Fuel Filler Neck
7 Fuel Supply Tube8 Fuel Return Tube
9 Filter Hose
10 Fuel Tank Hose
11 Fuel Filler Cap
1 2 Clip
1 3 Clip
Page 885 of 1463
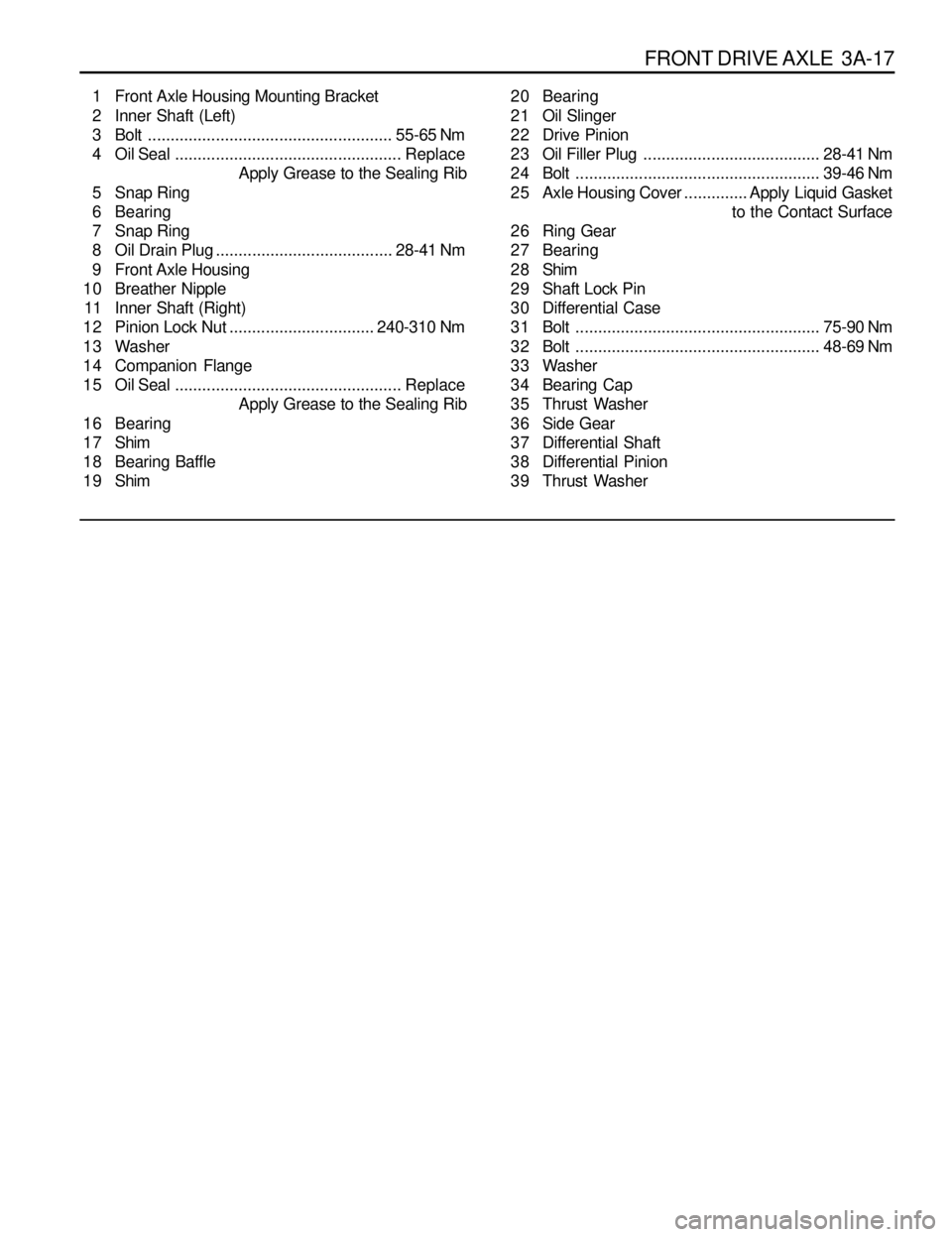
FRONT DRIVE AXLE 3A-17
1 Front Axle Housing Mounting Bracket
2 Inner Shaft (Left)
3 Bolt......................................................55-65 Nm
4 Oil Seal.................................................. Replace
Apply Grease to the Sealing Rib
5 Snap Ring
6 Bearing
7 Snap Ring
8 Oil Drain Plug.......................................28-41 Nm
9 Front Axle Housing
10 Breather Nipple
11 Inner Shaft (Right)
12 Pinion Lock Nut................................240-310 Nm
13 Washer
14 Companion Flange
15 Oil Seal.................................................. Replace
Apply Grease to the Sealing Rib
16 Bearing
1 7 Shim
18 Bearing Baffle
1 9 Shim20 Bearing
21 Oil Slinger
22 Drive Pinion
23 Oil Filler Plug.......................................28-41 Nm
2 4 Bolt......................................................39-46 Nm
25 Axle Housing Cover..............Apply Liquid Gasket
to the Contact Surface
26 Ring Gear
27 Bearing
2 8 Shim
29 Shaft Lock Pin
30 Differential Case
3 1 Bolt......................................................75-90 Nm
3 2 Bolt......................................................48-69 Nm
33 Washer
34 Bearing Cap
35 Thrust Washer
36 Side Gear
37 Differential Shaft
38 Differential Pinion
39 Thrust Washer
Page 900 of 1463

3D-2 REAR DRIVE AXLE
FASTENER TIGHTENING SPECIFICATIONS
Application
Inner Bracket Mounting Nut
Propeller Shaft to Rear Axle Input Shaft
Lower Arm Mounting Nut
Lower Shock Absorber to Axle Housing
Upper Arm Mounting Nut
Stabilizer Bar Mounting Bolt
Lateral Rod Mounting Nut
Drive Pinion Lock Nut
Oil Drain Plug
Ring Gear Mounting Bolt
Oil Filler PlugN
· ·· ·
·m
50 - 65
70 - 80
150 - 180
50 - 65
150 - 180
30 - 45
150 - 180
240 - 310
28 - 42
75 - 90
28 - 42
4.55
4.55
4.55
4.27
5.86
3.73
3.73
4.89
1.9 L
SEA 80W/90, API GL - 5 M/T
A/T (MB)
M/T
A/T (MB)
A/T (BTRA)
M/T
A/T (MB)
A/T (BTRA)
Oil Capacity
Oil Specification
ApplicationDescription
GENERAL SPECIFICATIONS(CONT'D)
E20
E23
E32 Reduction Ratio
Page 909 of 1463
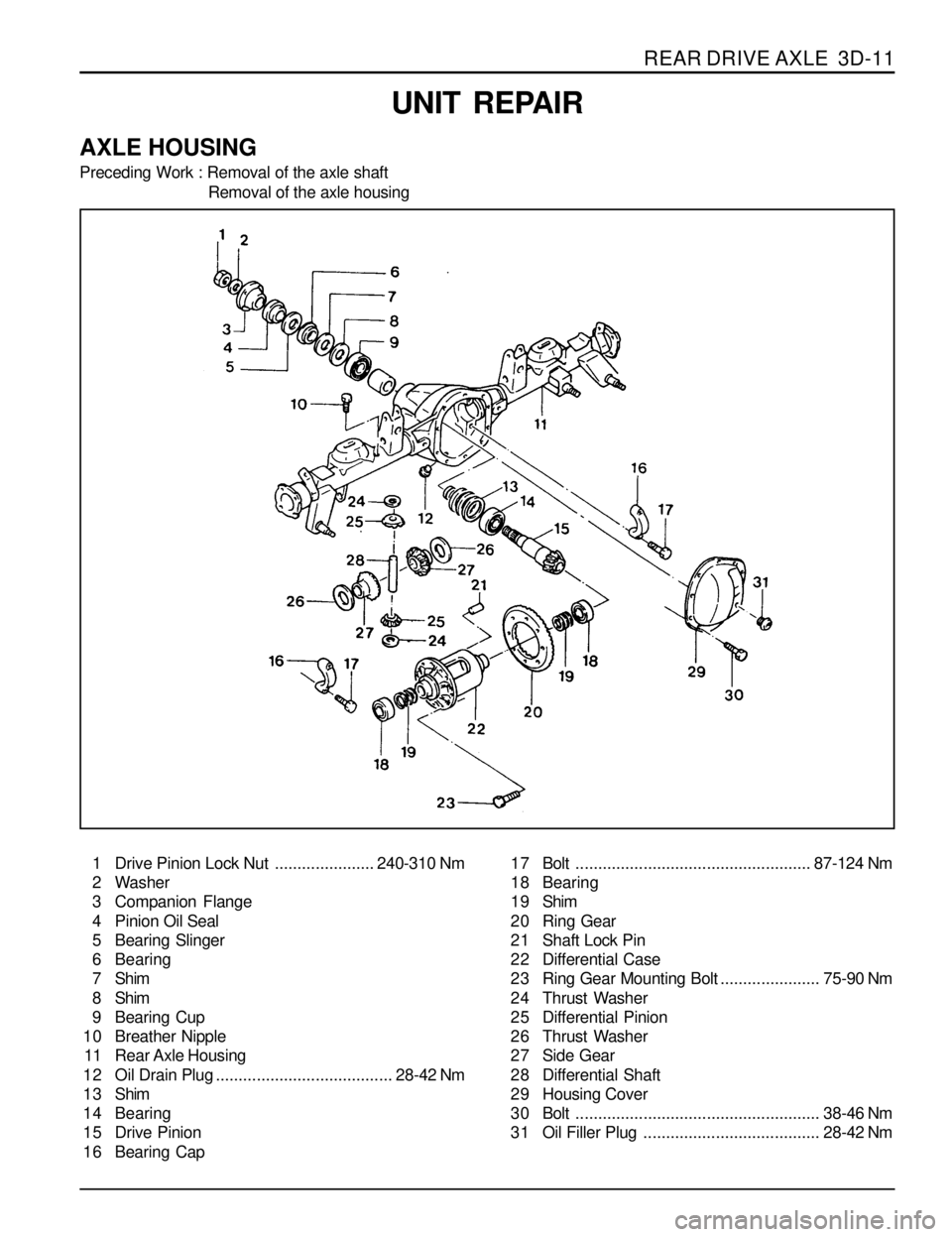
REAR DRIVE AXLE 3D-11
UNIT REPAIR
AXLE HOUSING
Preceding Work : Removal of the axle shaft
Removal of the axle housing
1 Drive Pinion Lock Nut......................240-310 Nm
2 Washer
3 Companion Flange
4 Pinion Oil Seal
5 Bearing Slinger
6 Bearing
7 Shim
8 Shim
9 Bearing Cup
10 Breather Nipple
11 Rear Axle Housing
12 Oil Drain Plug.......................................28-42 Nm
1 3 Shim
14 Bearing
15 Drive Pinion
16 Bearing Cap1 7 Bolt....................................................87-124 Nm
18 Bearing
1 9 Shim
20 Ring Gear
21 Shaft Lock Pin
22 Differential Case
23 Ring Gear Mounting Bolt......................75-90 Nm
24 Thrust Washer
25 Differential Pinion
26 Thrust Washer
27 Side Gear
28 Differential Shaft
29 Housing Cover
3 0 Bolt......................................................38-46 Nm
31 Oil Filler Plug.......................................28-42 Nm
Page 1056 of 1463
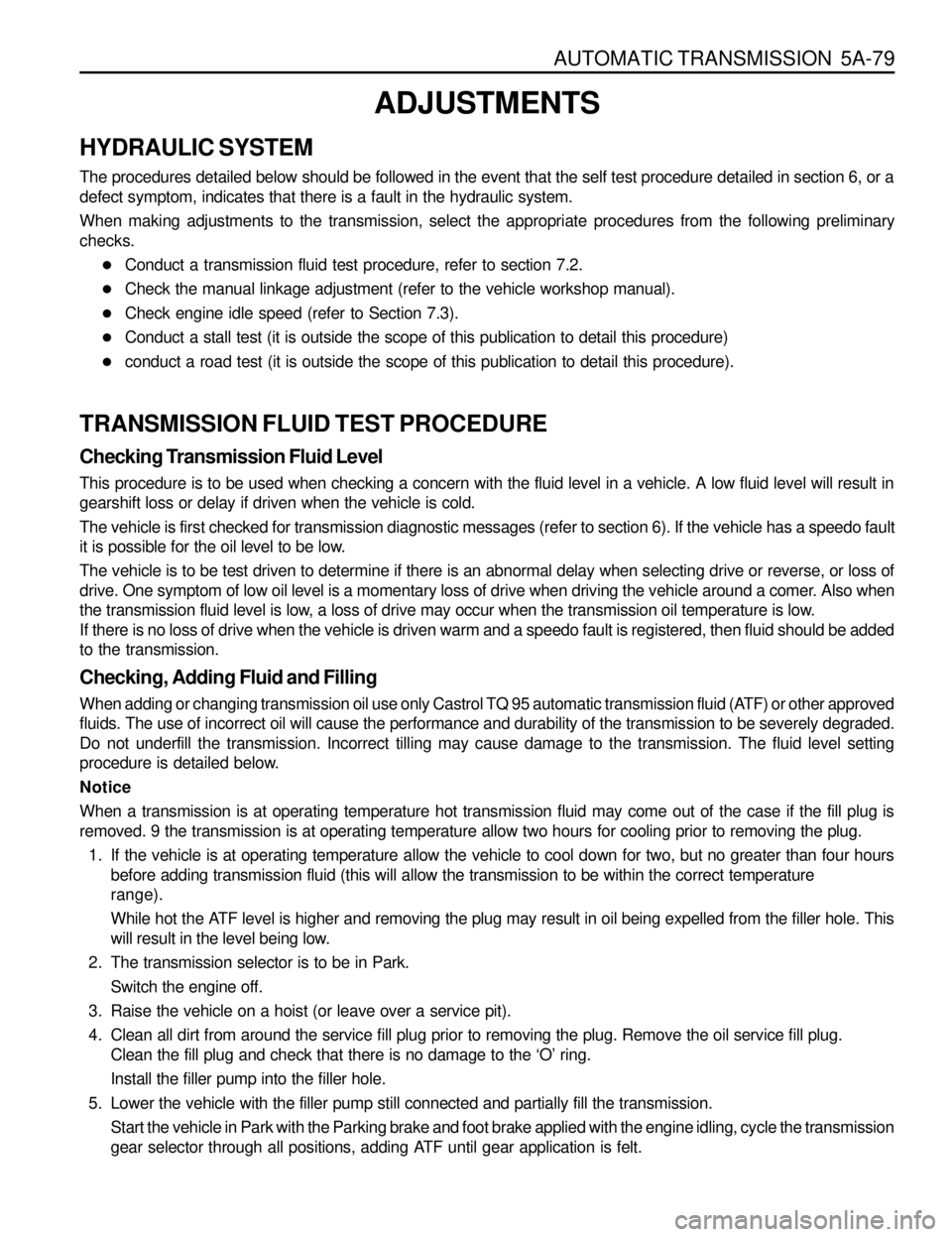
AUTOMATIC TRANSMISSION 5A-79
ADJUSTMENTS
HYDRAULIC SYSTEM
The procedures detailed below should be followed in the event that the self test procedure detailed in section 6, or a
defect symptom, indicates that there is a fault in the hydraulic system.
When making adjustments to the transmission, select the appropriate procedures from the following preliminary
checks.
lConduct a transmission fluid test procedure, refer to section 7.2.
lCheck the manual linkage adjustment (refer to the vehicle workshop manual).
lCheck engine idle speed (refer to Section 7.3).
lConduct a stall test (it is outside the scope of this publication to detail this procedure)
lconduct a road test (it is outside the scope of this publication to detail this procedure).
TRANSMISSION FLUID TEST PROCEDURE
Checking Transmission Fluid Level
This procedure is to be used when checking a concern with the fluid level in a vehicle. A low fluid level will result in
gearshift loss or delay if driven when the vehicle is cold.
The vehicle is first checked for transmission diagnostic messages (refer to section 6). If the vehicle has a speedo fault
it is possible for the oil level to be low.
The vehicle is to be test driven to determine if there is an abnormal delay when selecting drive or reverse, or loss of
drive. One symptom of low oil level is a momentary loss of drive when driving the vehicle around a comer. Also when
the transmission fluid level is low, a loss of drive may occur when the transmission oil temperature is low.
If there is no loss of drive when the vehicle is driven warm and a speedo fault is registered, then fluid should be added
to the transmission.
Checking, Adding Fluid and Filling
When adding or changing transmission oil use only Castrol TQ 95 automatic transmission fluid (ATF) or other approved
fluids. The use of incorrect oil will cause the performance and durability of the transmission to be severely degraded.
Do not underfill the transmission. Incorrect tilling may cause damage to the transmission. The fluid level setting
procedure is detailed below.
Notice
When a transmission is at operating temperature hot transmission fluid may come out of the case if the fill plug is
removed. 9 the transmission is at operating temperature allow two hours for cooling prior to removing the plug.
1. If the vehicle is at operating temperature allow the vehicle to cool down for two, but no greater than four hours
before adding transmission fluid (this will allow the transmission to be within the correct temperature
range).
While hot the ATF level is higher and removing the plug may result in oil being expelled from the filler hole. This
will result in the level being low.
2. The transmission selector is to be in Park.
Switch the engine off.
3. Raise the vehicle on a hoist (or leave over a service pit).
4. Clean all dirt from around the service fill plug prior to removing the plug. Remove the oil service fill plug.
Clean the fill plug and check that there is no damage to the ‘O’ ring.
Install the filler pump into the filler hole.
5. Lower the vehicle with the filler pump still connected and partially fill the transmission.
Start the vehicle in Park with the Parking brake and foot brake applied with the engine idling, cycle the transmission
gear selector through all positions, adding ATF until gear application is felt.
Page 1057 of 1463
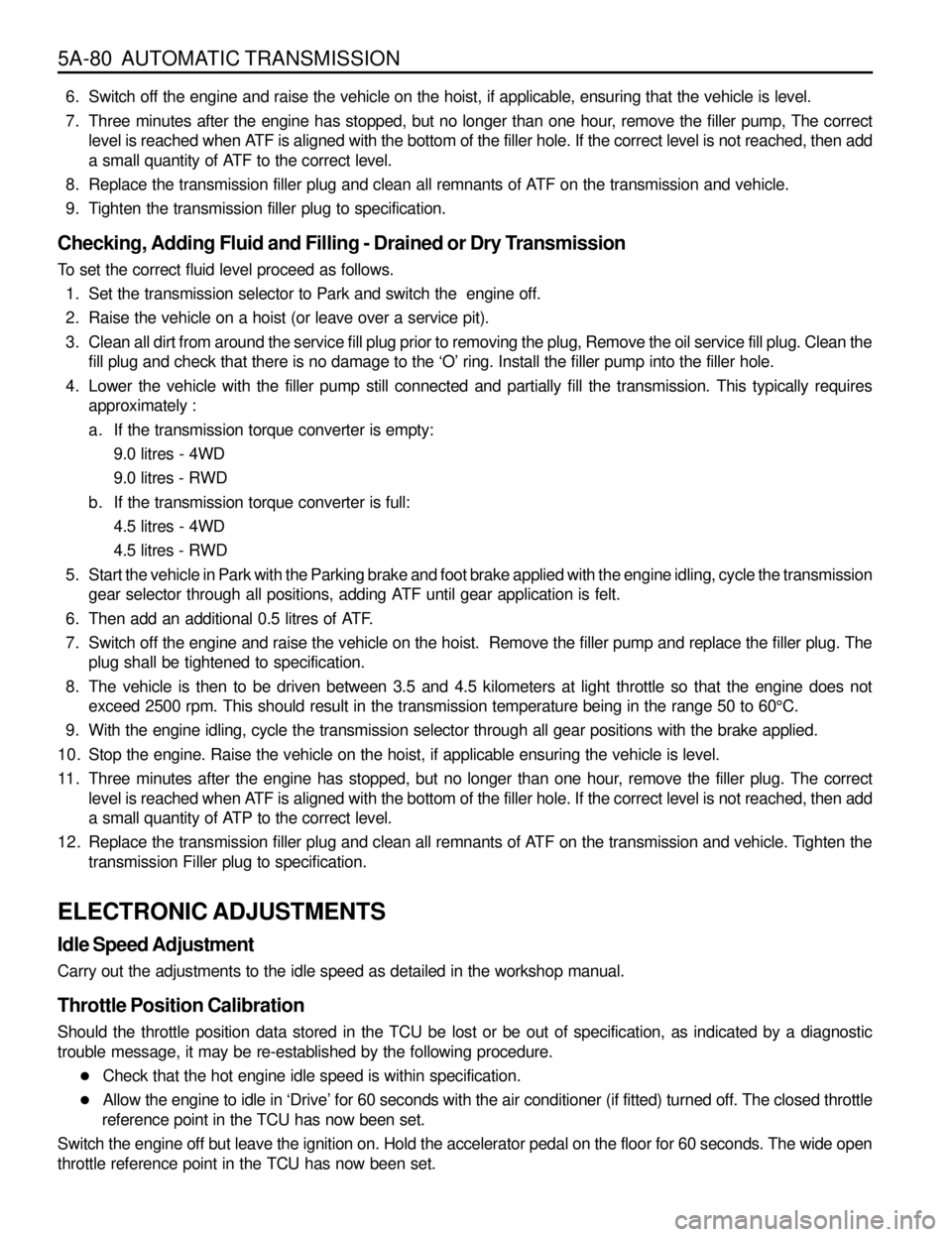
5A-80 AUTOMATIC TRANSMISSION
6. Switch off the engine and raise the vehicle on the hoist, if applicable, ensuring that the vehicle is level.
7. Three minutes after the engine has stopped, but no longer than one hour, remove the filler pump, The correct
level is reached when ATF is aligned with the bottom of the filler hole. If the correct level is not reached, then add
a small quantity of ATF to the correct level.
8. Replace the transmission filler plug and clean all remnants of ATF on the transmission and vehicle.
9. Tighten the transmission filler plug to specification.
Checking, Adding Fluid and Filling - Drained or Dry Transmission
To set the correct fluid level proceed as follows.
1. Set the transmission selector to Park and switch the engine off.
2. Raise the vehicle on a hoist (or leave over a service pit).
3. Clean all dirt from around the service fill plug prior to removing the plug, Remove the oil service fill plug. Clean the
fill plug and check that there is no damage to the ‘O’ ring. Install the filler pump into the filler hole.
4. Lower the vehicle with the filler pump still connected and partially fill the transmission. This typically requires
approximately :
a. If the transmission torque converter is empty:
9.0 litres - 4WD
9.0 litres - RWD
b. If the transmission torque converter is full:
4.5 litres - 4WD
4.5 litres - RWD
5. Start the vehicle in Park with the Parking brake and foot brake applied with the engine idling, cycle the transmission
gear selector through all positions, adding ATF until gear application is felt.
6. Then add an additional 0.5 litres of ATF.
7. Switch off the engine and raise the vehicle on the hoist. Remove the filler pump and replace the filler plug. The
plug shall be tightened to specification.
8. The vehicle is then to be driven between 3.5 and 4.5 kilometers at light throttle so that the engine does not
exceed 2500 rpm. This should result in the transmission temperature being in the range 50 to 60°C.
9. With the engine idling, cycle the transmission selector through all gear positions with the brake applied.
10. Stop the engine. Raise the vehicle on the hoist, if applicable ensuring the vehicle is level.
11. Three minutes after the engine has stopped, but no longer than one hour, remove the filler plug. The correct
level is reached when ATF is aligned with the bottom of the filler hole. If the correct level is not reached, then add
a small quantity of ATP to the correct level.
12. Replace the transmission filler plug and clean all remnants of ATF on the transmission and vehicle. Tighten the
transmission Filler plug to specification.
ELECTRONIC ADJUSTMENTS
Idle Speed Adjustment
Carry out the adjustments to the idle speed as detailed in the workshop manual.
Throttle Position Calibration
Should the throttle position data stored in the TCU be lost or be out of specification, as indicated by a diagnostic
trouble message, it may be re-established by the following procedure.
lCheck that the hot engine idle speed is within specification.
lAllow the engine to idle in ‘Drive’ for 60 seconds with the air conditioner (if fitted) turned off. The closed throttle
reference point in the TCU has now been set.
Switch the engine off but leave the ignition on. Hold the accelerator pedal on the floor for 60 seconds. The wide open
throttle reference point in the TCU has now been set.
Page 1104 of 1463
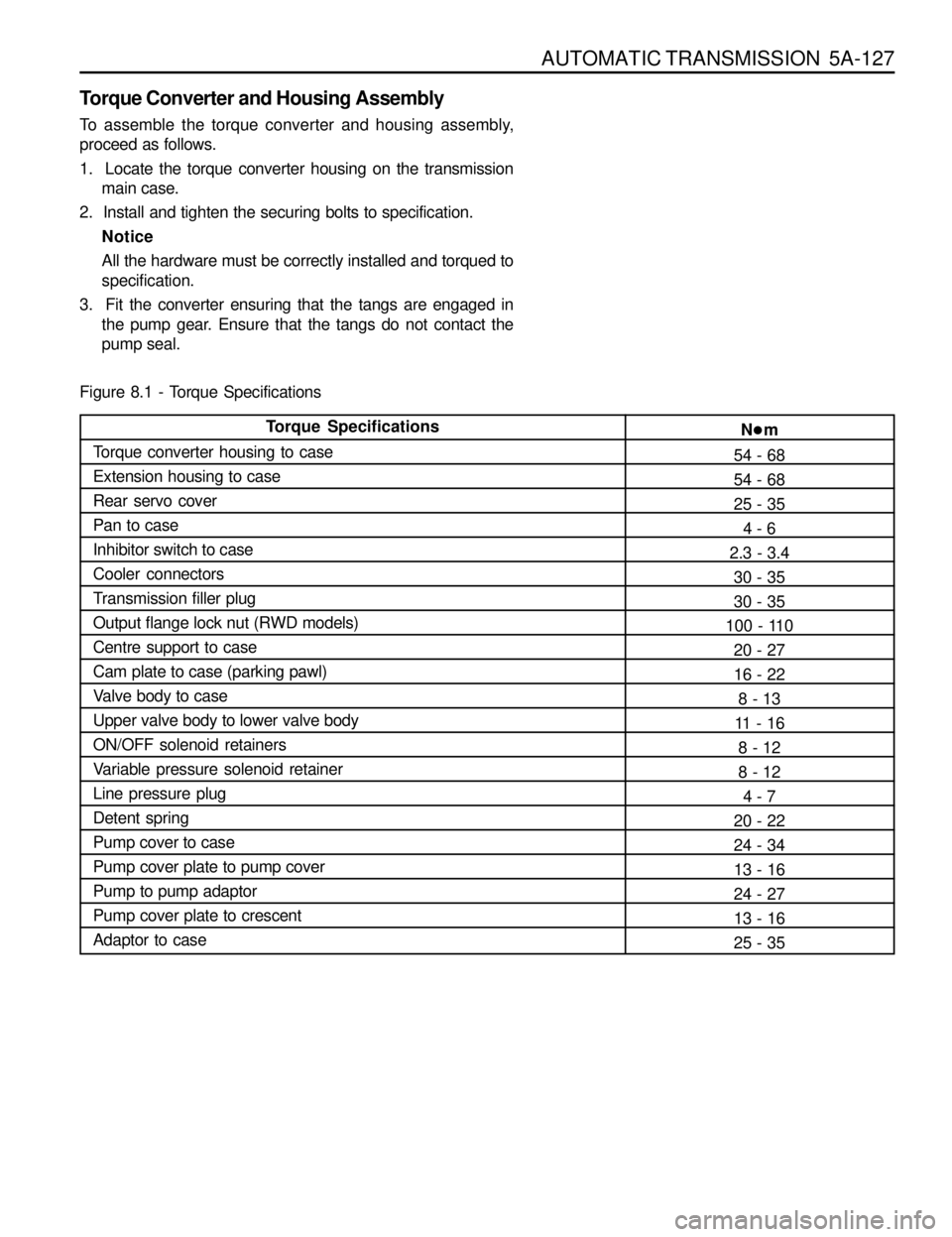
AUTOMATIC TRANSMISSION 5A-127
Torque Converter and Housing Assembly
To assemble the torque converter and housing assembly,
proceed as follows.
1. Locate the torque converter housing on the transmission
main case.
2. Install and tighten the securing bolts to specification.
Notice
All the hardware must be correctly installed and torqued to
specification.
3. Fit the converter ensuring that the tangs are engaged in
the pump gear. Ensure that the tangs do not contact the
pump seal.
Figure 8.1 - Torque Specifications
Torque Specifications
Torque converter housing to case
Extension housing to case
Rear servo cover
Pan to case
Inhibitor switch to case
Cooler connectors
Transmission filler plug
Output flange lock nut (RWD models)
Centre support to case
Cam plate to case (parking pawl)
Valve body to case
Upper valve body to lower valve body
ON/OFF solenoid retainers
Variable pressure solenoid retainer
Line pressure plug
Detent spring
Pump cover to case
Pump cover plate to pump cover
Pump to pump adaptor
Pump cover plate to crescent
Adaptor to caseNlm
54 - 68
54 - 68
25 - 35
4 - 6
2.3 - 3.4
30 - 35
30 - 35
100 - 110
20 - 27
16 - 22
8 - 13
11 - 16
8 - 12
8 - 12
4 - 7
20 - 22
24 - 34
13 - 16
24 - 27
13 - 16
25 - 35
Page 1109 of 1463
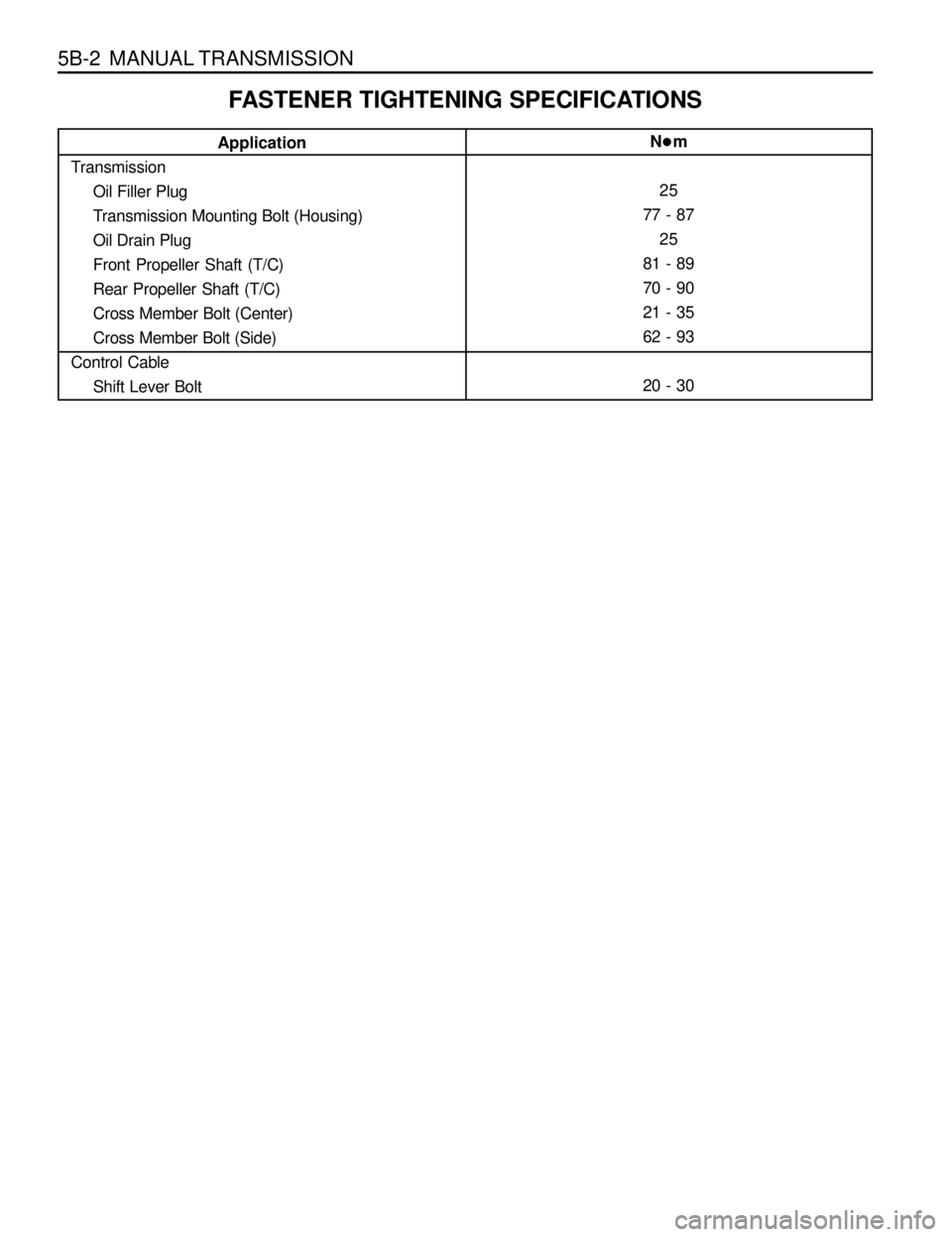
5B-2 MANUAL TRANSMISSION
FASTENER TIGHTENING SPECIFICATIONS
Application
Transmission
Oil Filler Plug
Transmission Mounting Bolt (Housing)
Oil Drain Plug
Front Propeller Shaft (T/C)
Rear Propeller Shaft (T/C)
Cross Member Bolt (Center)
Cross Member Bolt (Side)
Control Cable
Shift Lever BoltNlm
25
77 - 87
25
81 - 89
70 - 90
21 - 35
62 - 93
20 - 30
Page 1117 of 1463
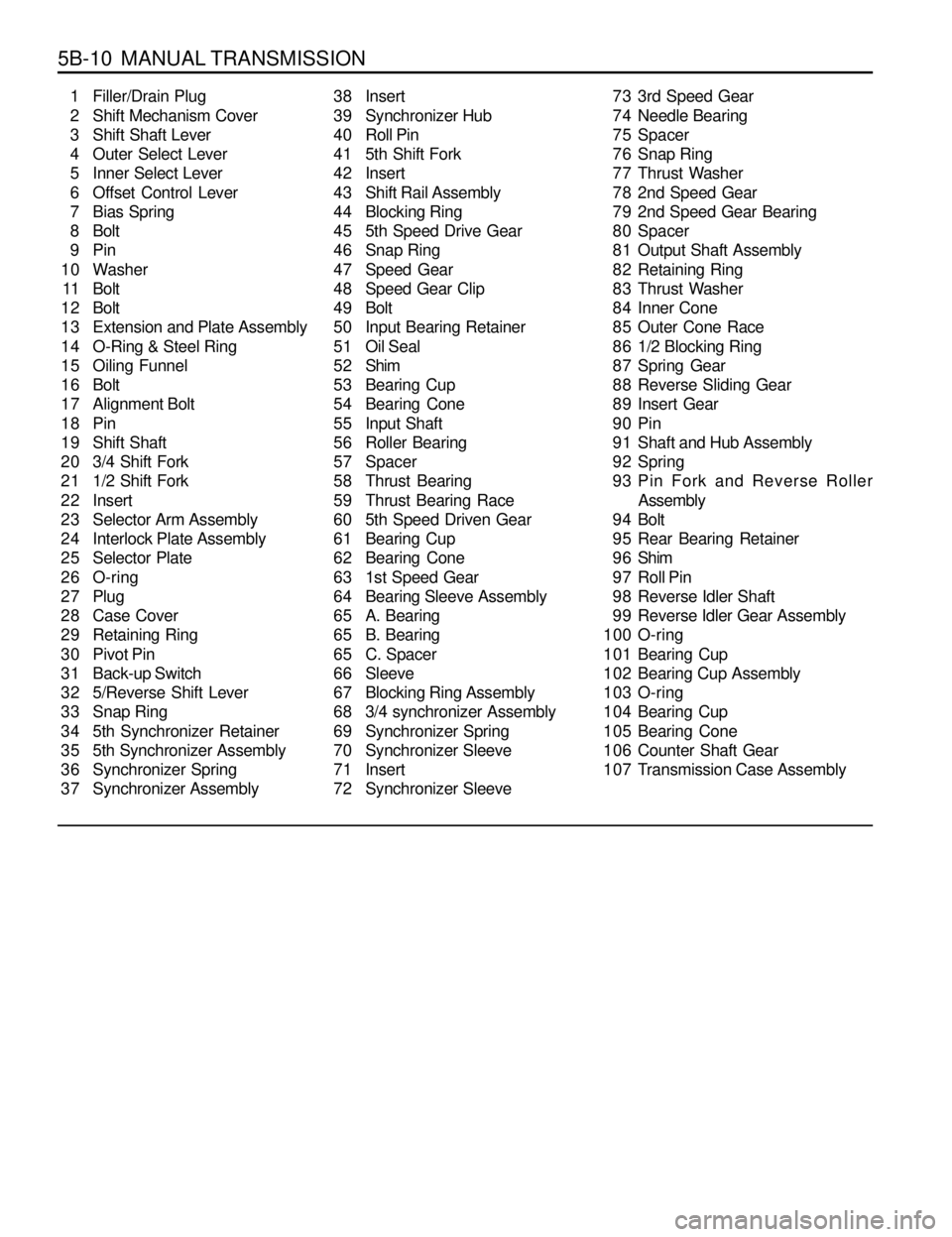
5B-10 MANUAL TRANSMISSION
1 Filler/Drain Plug
2 Shift Mechanism Cover
3 Shift Shaft Lever
4 Outer Select Lever
5 Inner Select Lever
6 Offset Control Lever
7 Bias Spring
8 Bolt
9 Pin
10 Washer
11 Bolt
1 2 Bolt
13 Extension and Plate Assembly
14 O-Ring & Steel Ring
15 Oiling Funnel
1 6 Bolt
17 Alignment Bolt
18 Pin
19 Shift Shaft
20 3/4 Shift Fork
21 1/2 Shift Fork
22 Insert
23 Selector Arm Assembly
24 Interlock Plate Assembly
25 Selector Plate
26 O-ring
2 7 Plug
28 Case Cover
29 Retaining Ring
30 Pivot Pin
31 Back-up Switch
32 5/Reverse Shift Lever
33 Snap Ring
34 5th Synchronizer Retainer
35 5th Synchronizer Assembly
36 Synchronizer Spring
37 Synchronizer Assembly38 Insert
39 Synchronizer Hub
40 Roll Pin
41 5th Shift Fork
42 Insert
43 Shift Rail Assembly
44 Blocking Ring
45 5th Speed Drive Gear
46 Snap Ring
47 Speed Gear
48 Speed Gear Clip
4 9 Bolt
50 Input Bearing Retainer
51 Oil Seal
5 2 Shim
53 Bearing Cup
54 Bearing Cone
55 Input Shaft
56 Roller Bearing
57 Spacer
58 Thrust Bearing
59 Thrust Bearing Race
60 5th Speed Driven Gear
61 Bearing Cup
62 Bearing Cone
63 1st Speed Gear
64 Bearing Sleeve Assembly
65 A. Bearing
65 B. Bearing
65 C. Spacer
66 Sleeve
67 Blocking Ring Assembly
68 3/4 synchronizer Assembly
69 Synchronizer Spring
70 Synchronizer Sleeve
71 Insert
72 Synchronizer Sleeve73 3rd Speed Gear
74 Needle Bearing
75 Spacer
76 Snap Ring
77 Thrust Washer
78 2nd Speed Gear
79 2nd Speed Gear Bearing
80 Spacer
81 Output Shaft Assembly
82 Retaining Ring
83 Thrust Washer
84 Inner Cone
85 Outer Cone Race
86 1/2 Blocking Ring
87 Spring Gear
88 Reverse Sliding Gear
89 Insert Gear
90 Pin
91 Shaft and Hub Assembly
92 Spring
93 Pin Fork and Reverse Roller
Assembly
9 4 Bolt
95 Rear Bearing Retainer
9 6 Shim
97 Roll Pin
98 Reverse Idler Shaft
99 Reverse Idler Gear Assembly
100 O-ring
101 Bearing Cup
102 Bearing Cup Assembly
103 O-ring
104 Bearing Cup
105 Bearing Cone
106 Counter Shaft Gear
107 Transmission Case Assembly
Page 1121 of 1463
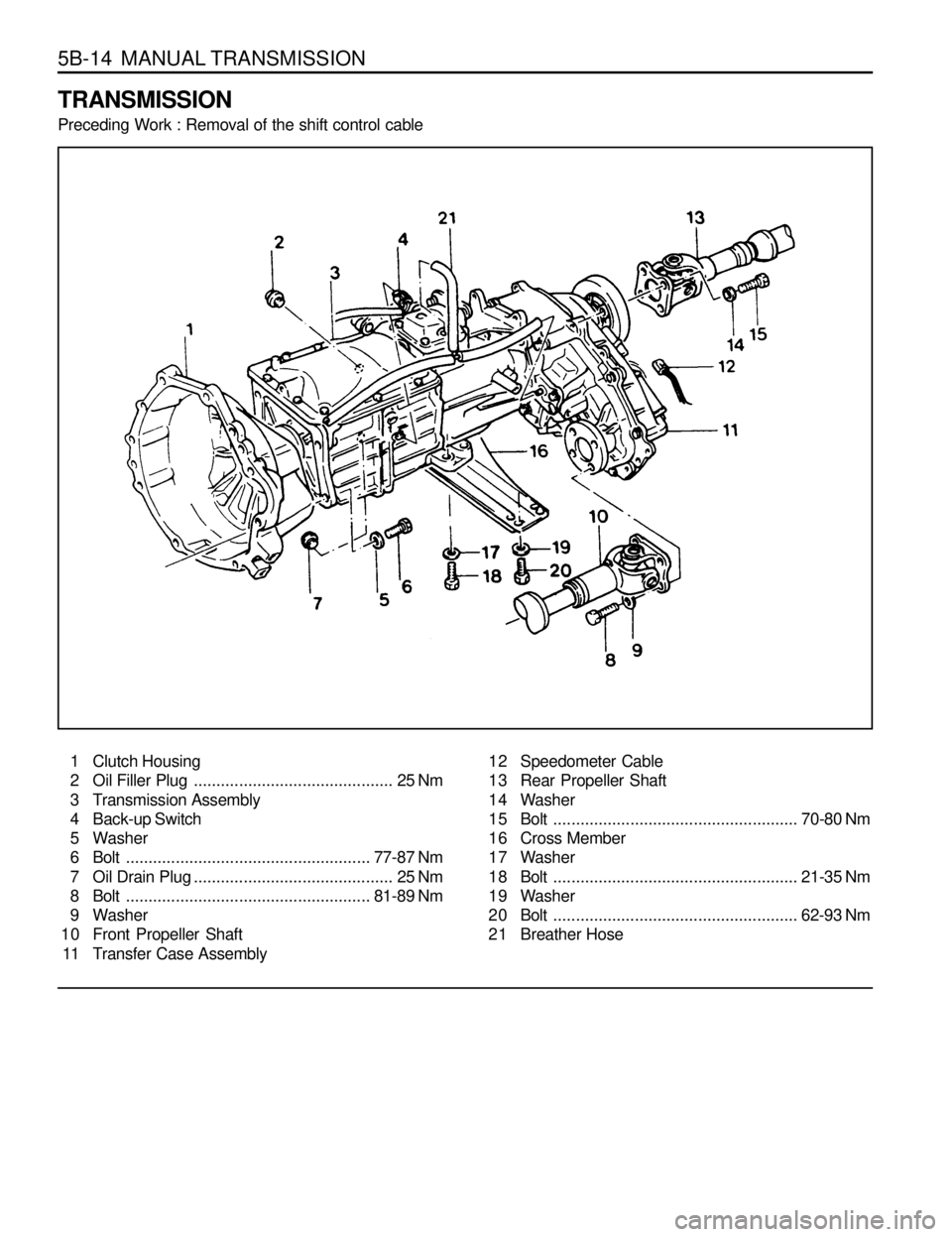
5B-14 MANUAL TRANSMISSION
TRANSMISSION
Preceding Work : Removal of the shift control cable
1 Clutch Housing
2 Oil Filler Plug............................................ 25 Nm
3 Transmission Assembly
4 Back-up Switch
5 Washer
6 Bolt......................................................77-87 Nm
7 Oil Drain Plug............................................ 25 Nm
8 Bolt......................................................81-89 Nm
9 Washer
10 Front Propeller Shaft
11 Transfer Case Assembly12 Speedometer Cable
13 Rear Propeller Shaft
14 Washer
1 5 Bolt......................................................70-80 Nm
16 Cross Member
17 Washer
1 8 Bolt......................................................21-35 Nm
19 Washer
2 0 Bolt......................................................62-93 Nm
21 Breather Hose