4WD SSANGYONG MUSSO 1998 Workshop Repair Manual
[x] Cancel search | Manufacturer: SSANGYONG, Model Year: 1998, Model line: MUSSO, Model: SSANGYONG MUSSO 1998Pages: 1463, PDF Size: 19.88 MB
Page 15 of 1463
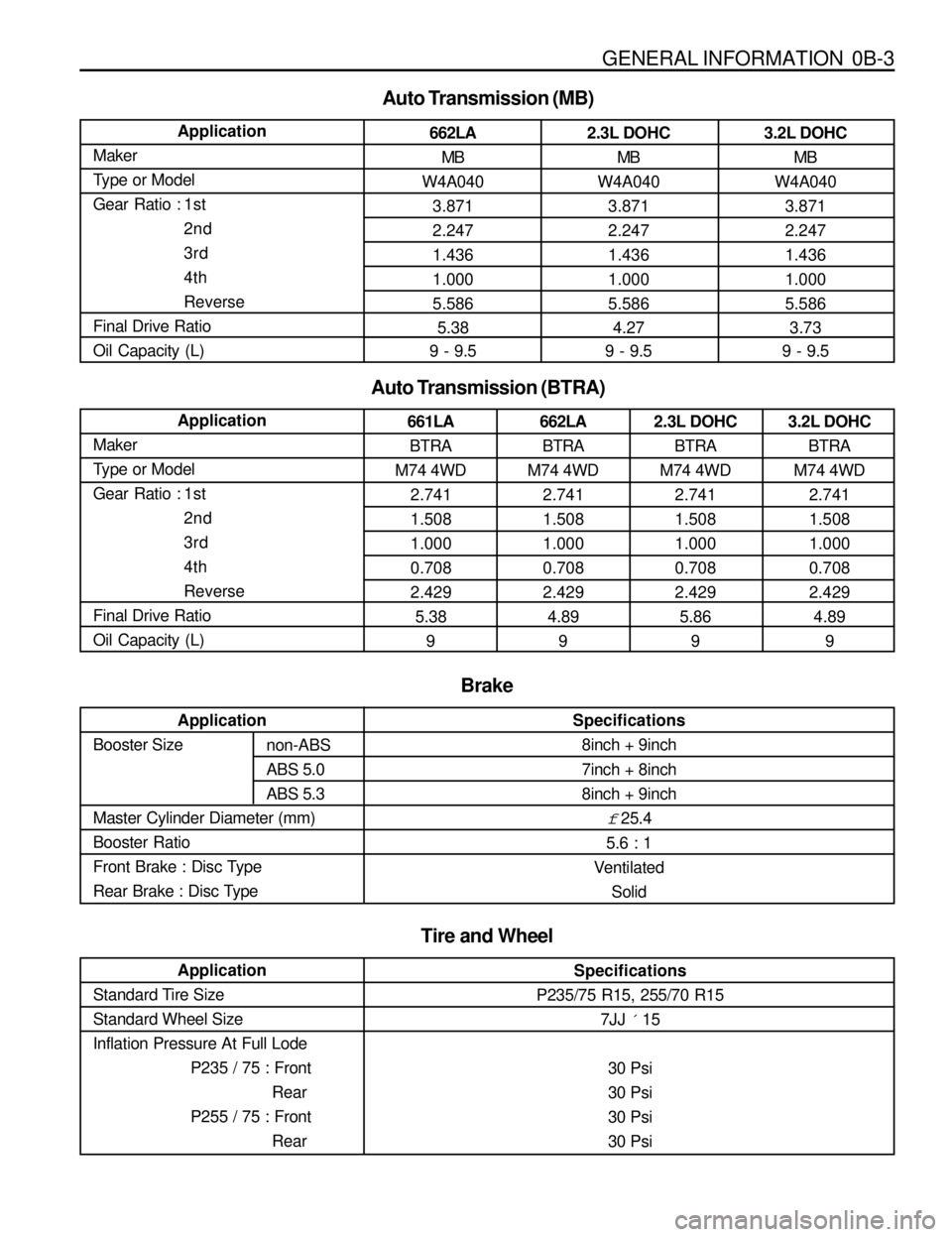
GENERAL INFORMATION 0B-3
662LA
MB
W4A040
3.871
2.247
1.436
1.000
5.586
5.38
9 - 9.5
Auto Transmission (MB)
Application
Maker
Type or Model
Gear Ratio : 1st
2nd
3rd
4th
Reverse
Final Drive Ratio
Oil Capacity (L)2.3L DOHC
MB
W4A040
3.871
2.247
1.436
1.000
5.586
4.27
9 - 9.53.2L DOHC
MB
W4A040
3.871
2.247
1.436
1.000
5.586
3.73
9 - 9.5
661LA
BTRA
M74 4WD
2.741
1.508
1.000
0.708
2.429
5.38
9
Auto Transmission (BTRA)
Application
Maker
Type or Model
Gear Ratio : 1st
2nd
3rd
4th
Reverse
Final Drive Ratio
Oil Capacity (L)662LA
BTRA
M74 4WD
2.741
1.508
1.000
0.708
2.429
4.89
92.3L DOHC
BTRA
M74 4WD
2.741
1.508
1.000
0.708
2.429
5.86
93.2L DOHC
BTRA
M74 4WD
2.741
1.508
1.000
0.708
2.429
4.89
9
Tire and Wheel
Specifications
P235/75 R15, 255/70 R15
7JJ ´ 15
30 Psi
30 Psi
30 Psi
30 Psi Application
Standard Tire Size
Standard Wheel Size
Inflation Pressure At Full Lode
P235 / 75 : Front
Rear
P255 / 75 : Front
Rear Application
Booster Size
Master Cylinder Diameter (mm)
Booster Ratio
Front Brake : Disc Type
Rear Brake : Disc Type
Specifications
8inch + 9inch
7inch + 8inch
8inch + 9inch
f 25.4
5.6 : 1
Ventilated
Solid
Brake
non-ABS
ABS 5.0
ABS 5.3
Page 982 of 1463
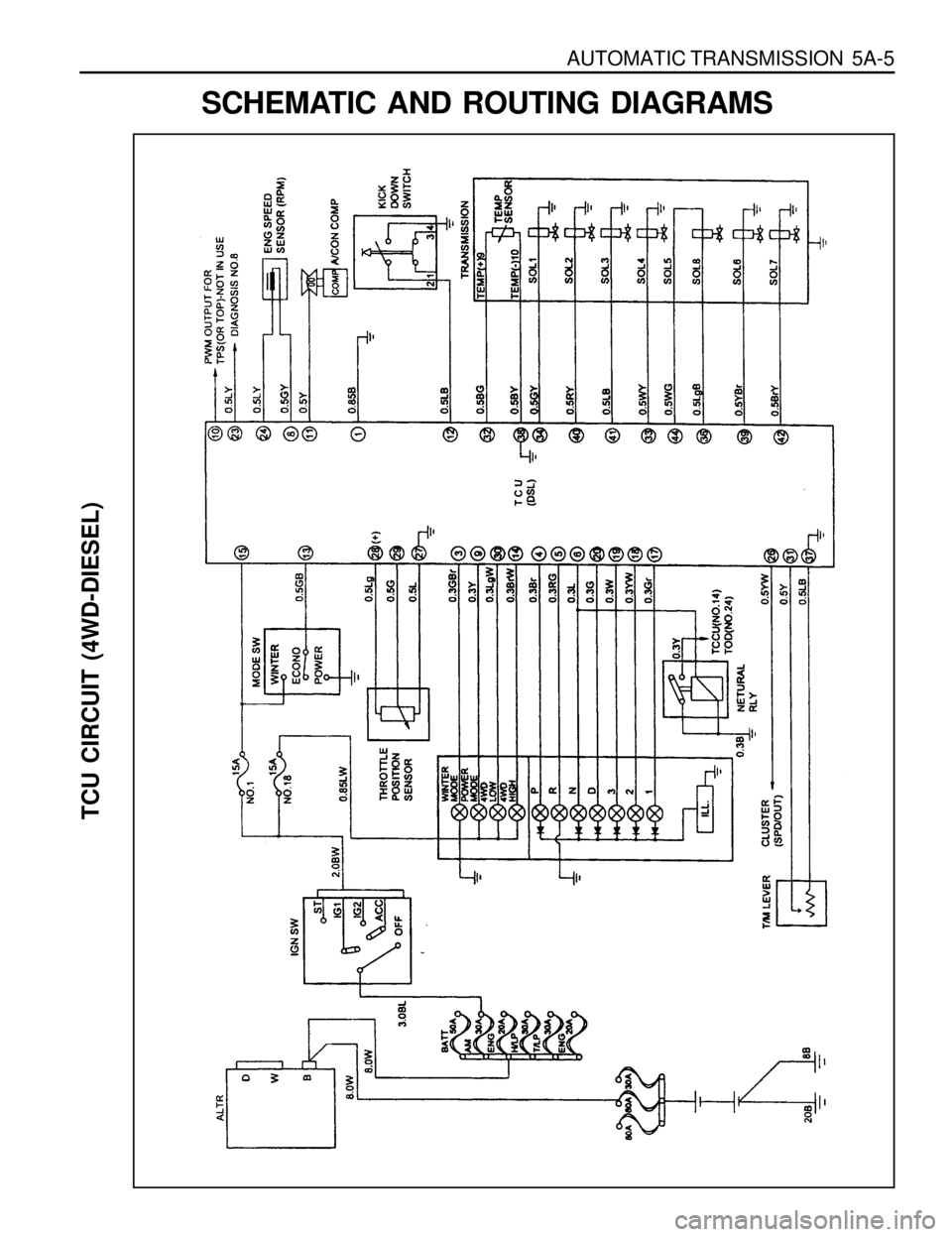
AUTOMATIC TRANSMISSION 5A-5
SCHEMATIC AND ROUTING DIAGRAMS
TCU CIRCUIT (4WD-DIESEL)
Page 983 of 1463
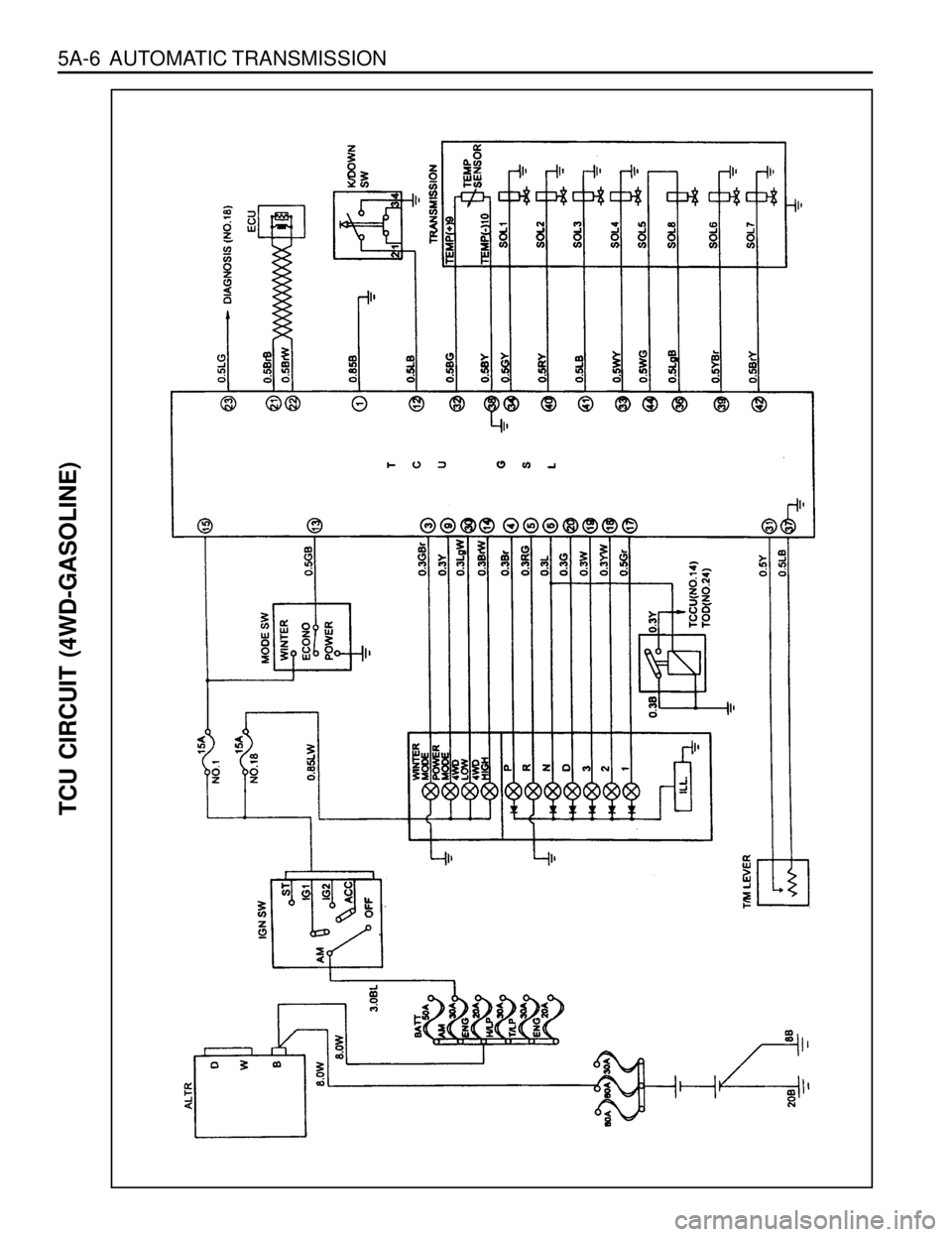
5A-6 AUTOMATIC TRANSMISSION
TCU CIRCUIT (4WD-GASOLINE)
Page 995 of 1463
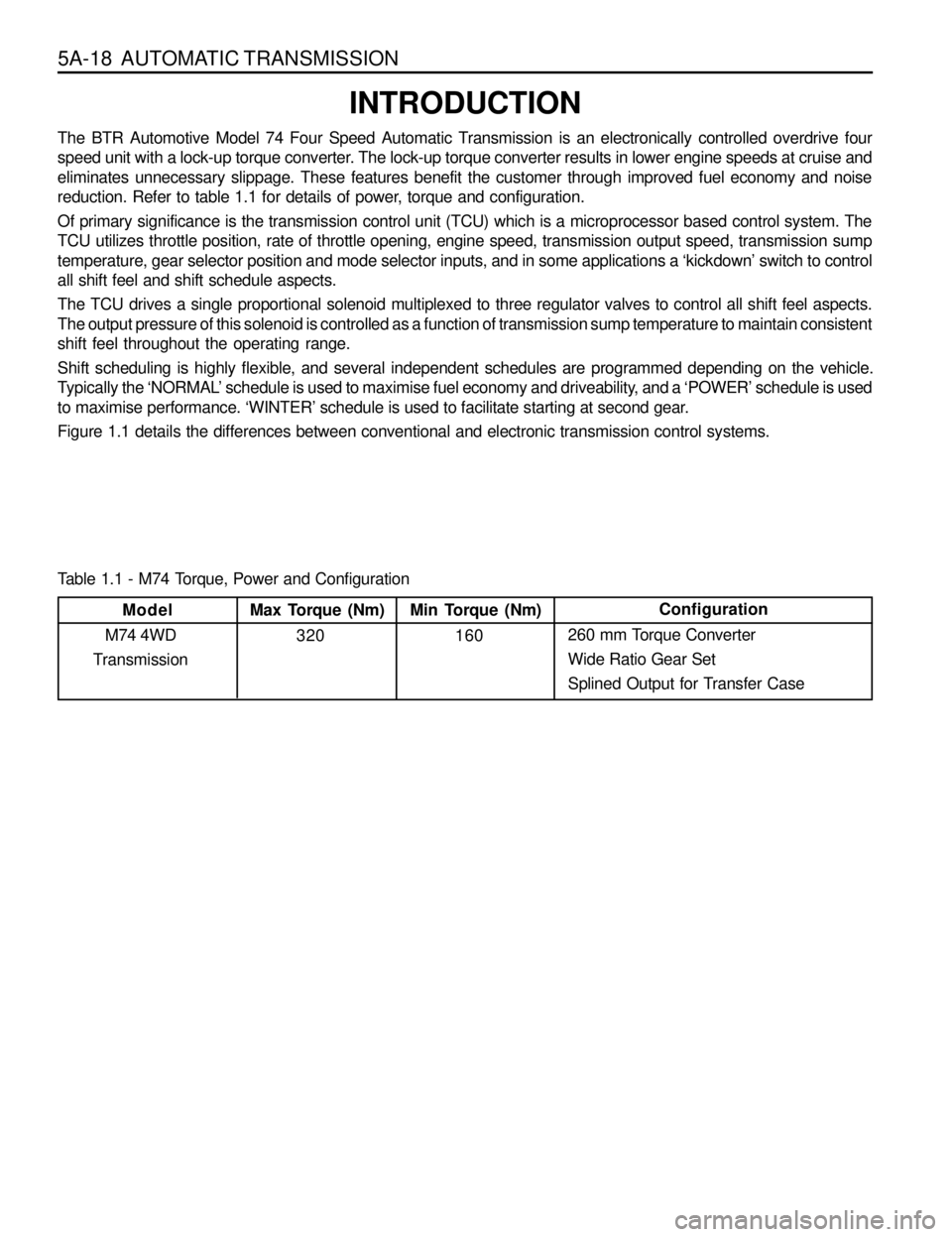
5A-18 AUTOMATIC TRANSMISSION
INTRODUCTION
The BTR Automotive Model 74 Four Speed Automatic Transmission is an electronically controlled overdrive four
speed unit with a lock-up torque converter. The lock-up torque converter results in lower engine speeds at cruise and
eliminates unnecessary slippage. These features benefit the customer through improved fuel economy and noise
reduction. Refer to table 1.1 for details of power, torque and configuration.
Of primary significance is the transmission control unit (TCU) which is a microprocessor based control system. The
TCU utilizes throttle position, rate of throttle opening, engine speed, transmission output speed, transmission sump
temperature, gear selector position and mode selector inputs, and in some applications a ‘kickdown’ switch to control
all shift feel and shift schedule aspects.
The TCU drives a single proportional solenoid multiplexed to three regulator valves to control all shift feel aspects.
The output pressure of this solenoid is controlled as a function of transmission sump temperature to maintain consistent
shift feel throughout the operating range.
Shift scheduling is highly flexible, and several independent schedules are programmed depending on the vehicle.
Typically the ‘NORMAL’ schedule is used to maximise fuel economy and driveability, and a ‘POWER’ schedule is used
to maximise performance. ‘WINTER’ schedule is used to facilitate starting at second gear.
Figure 1.1 details the differences between conventional and electronic transmission control systems.
Max Torque (Nm)
320Configuration
260 mm Torque Converter
Wide Ratio Gear Set
Splined Output for Transfer CaseMin Torque (Nm)
160 Model
M74 4WD
Transmission Table 1.1 - M74 Torque, Power and Configuration
Page 1001 of 1463
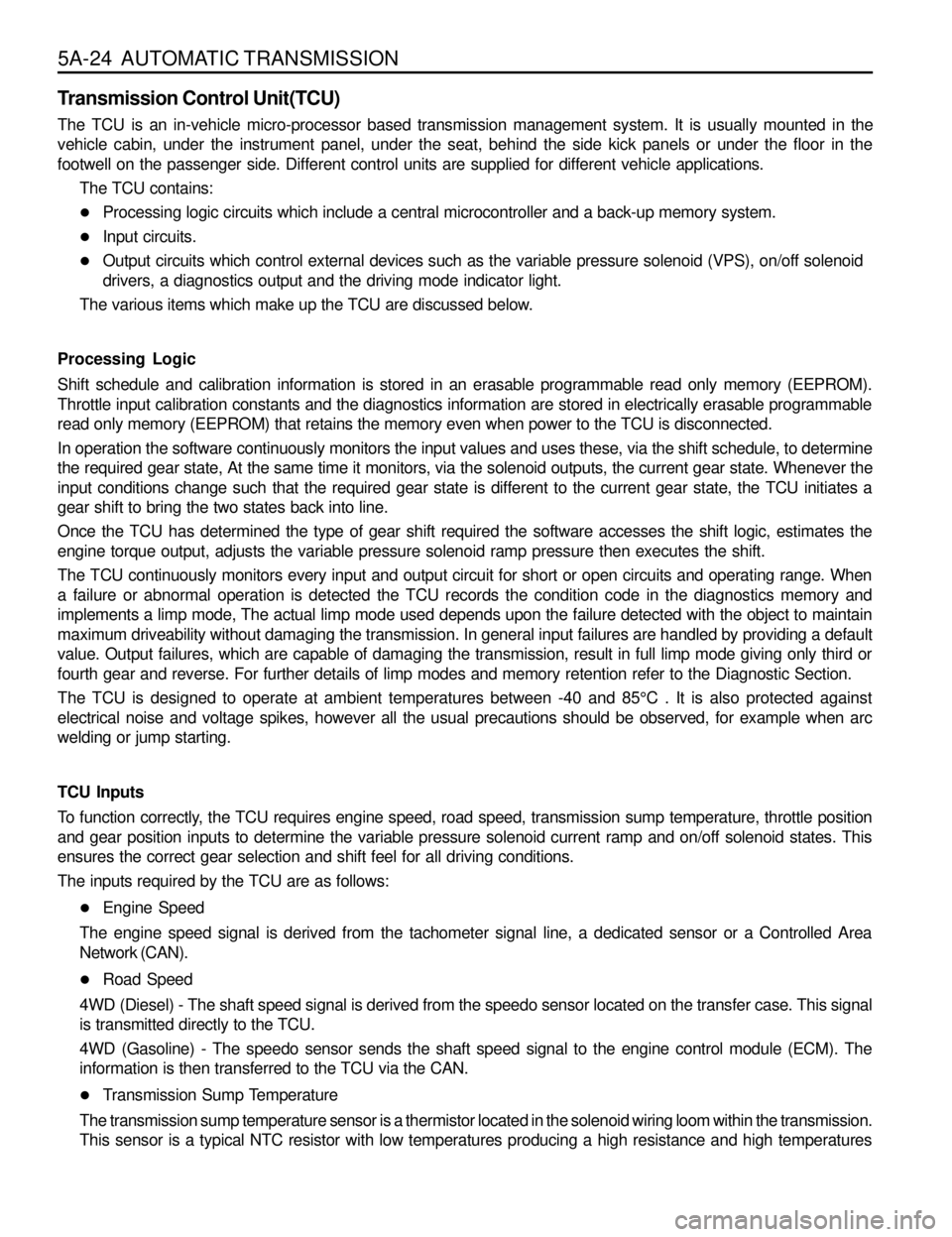
5A-24 AUTOMATIC TRANSMISSION
Transmission Control Unit(TCU)
The TCU is an in-vehicle micro-processor based transmission management system. It is usually mounted in the
vehicle cabin, under the instrument panel, under the seat, behind the side kick panels or under the floor in the
footwell on the passenger side. Different control units are supplied for different vehicle applications.
The TCU contains:
lProcessing logic circuits which include a central microcontroller and a back-up memory system.
lInput circuits.
lOutput circuits which control external devices such as the variable pressure solenoid (VPS), on/off solenoid
drivers, a diagnostics output and the driving mode indicator light.
The various items which make up the TCU are discussed below.
Processing Logic
Shift schedule and calibration information is stored in an erasable programmable read only memory (EEPROM).
Throttle input calibration constants and the diagnostics information are stored in electrically erasable programmable
read only memory (EEPROM) that retains the memory even when power to the TCU is disconnected.
In operation the software continuously monitors the input values and uses these, via the shift schedule, to determine
the required gear state, At the same time it monitors, via the solenoid outputs, the current gear state. Whenever the
input conditions change such that the required gear state is different to the current gear state, the TCU initiates a
gear shift to bring the two states back into line.
Once the TCU has determined the type of gear shift required the software accesses the shift logic, estimates the
engine torque output, adjusts the variable pressure solenoid ramp pressure then executes the shift.
The TCU continuously monitors every input and output circuit for short or open circuits and operating range. When
a failure or abnormal operation is detected the TCU records the condition code in the diagnostics memory and
implements a limp mode, The actual limp mode used depends upon the failure detected with the object to maintain
maximum driveability without damaging the transmission. In general input failures are handled by providing a default
value. Output failures, which are capable of damaging the transmission, result in full limp mode giving only third or
fourth gear and reverse. For further details of limp modes and memory retention refer to the Diagnostic Section.
The TCU is designed to operate at ambient temperatures between -40 and 85°C . It is also protected against
electrical noise and voltage spikes, however all the usual precautions should be observed, for example when arc
welding or jump starting.
TCU Inputs
To function correctly, the TCU requires engine speed, road speed, transmission sump temperature, throttle position
and gear position inputs to determine the variable pressure solenoid current ramp and on/off solenoid states. This
ensures the correct gear selection and shift feel for all driving conditions.
The inputs required by the TCU are as follows:
lEngine Speed
The engine speed signal is derived from the tachometer signal line, a dedicated sensor or a Controlled Area
Network (CAN).
lRoad Speed
4WD (Diesel) - The shaft speed signal is derived from the speedo sensor located on the transfer case. This signal
is transmitted directly to the TCU.
4WD (Gasoline) - The speedo sensor sends the shaft speed signal to the engine control module (ECM). The
information is then transferred to the TCU via the CAN.
lTransmission Sump Temperature
The transmission sump temperature sensor is a thermistor located in the solenoid wiring loom within the transmission.
This sensor is a typical NTC resistor with low temperatures producing a high resistance and high temperatures
Page 1025 of 1463
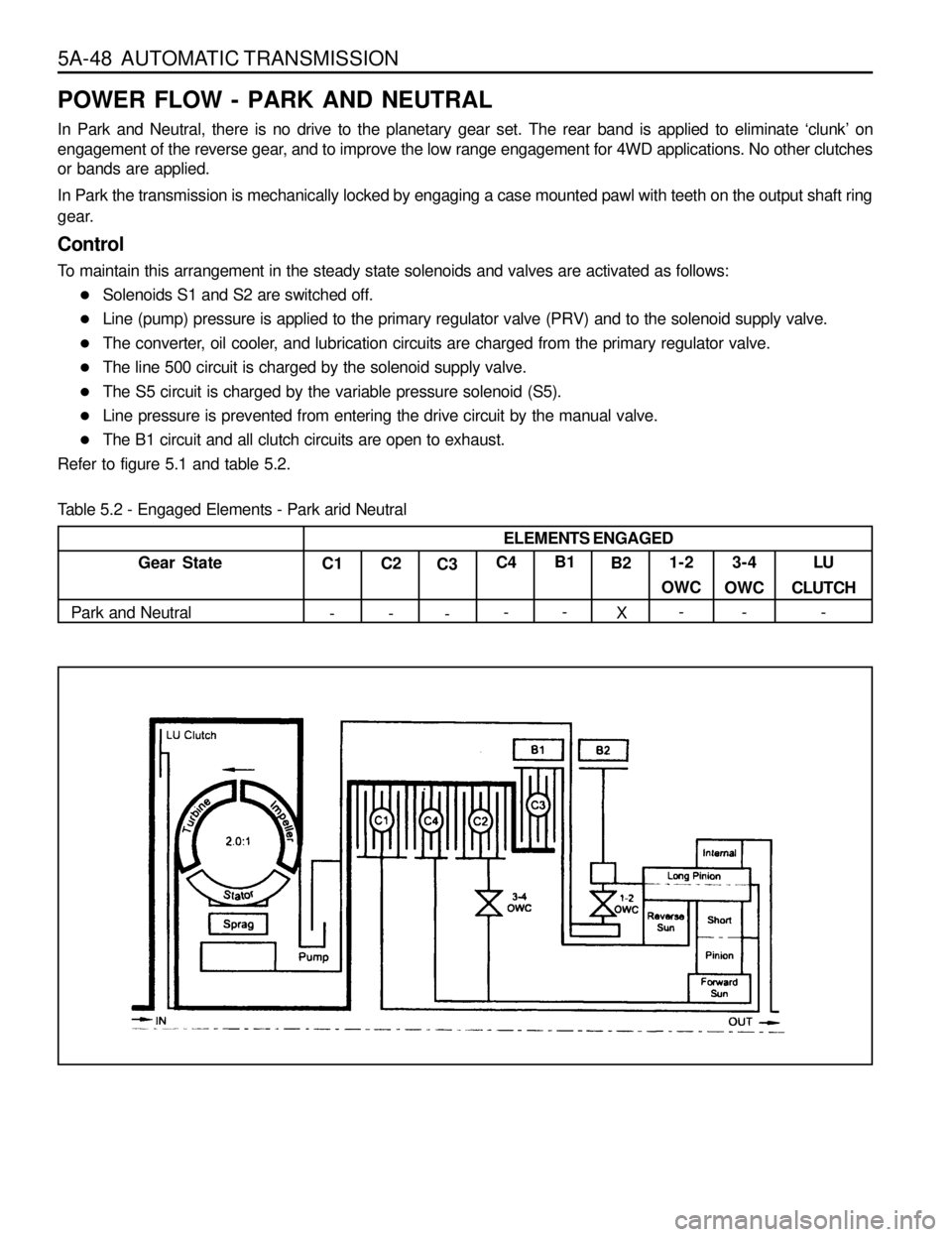
5A-48 AUTOMATIC TRANSMISSION
POWER FLOW - PARK AND NEUTRAL
In Park and Neutral, there is no drive to the planetary gear set. The rear band is applied to eliminate ‘clunk’ on
engagement of the reverse gear, and to improve the low range engagement for 4WD applications. No other clutches
or bands are applied.
In Park the transmission is mechanically locked by engaging a case mounted pawl with teeth on the output shaft ring
gear.
Control
To maintain this arrangement in the steady state solenoids and valves are activated as follows:
lSolenoids S1 and S2 are switched off.
lLine (pump) pressure is applied to the primary regulator valve (PRV) and to the solenoid supply valve.
lThe converter, oil cooler, and lubrication circuits are charged from the primary regulator valve.
lThe line 500 circuit is charged by the solenoid supply valve.
lThe S5 circuit is charged by the variable pressure solenoid (S5).
lLine pressure is prevented from entering the drive circuit by the manual valve.
lThe B1 circuit and all clutch circuits are open to exhaust.
Refer to figure 5.1 and table 5.2.
Table 5.2 - Engaged Elements - Park arid Neutral
Gear State
Park and NeutralC1
-C2
-C3
-C4
-B1
-B2
X1-2
OWC
-3-4
OWC
-LU
CLUTCH
- ELEMENTS ENGAGED
Page 1037 of 1463
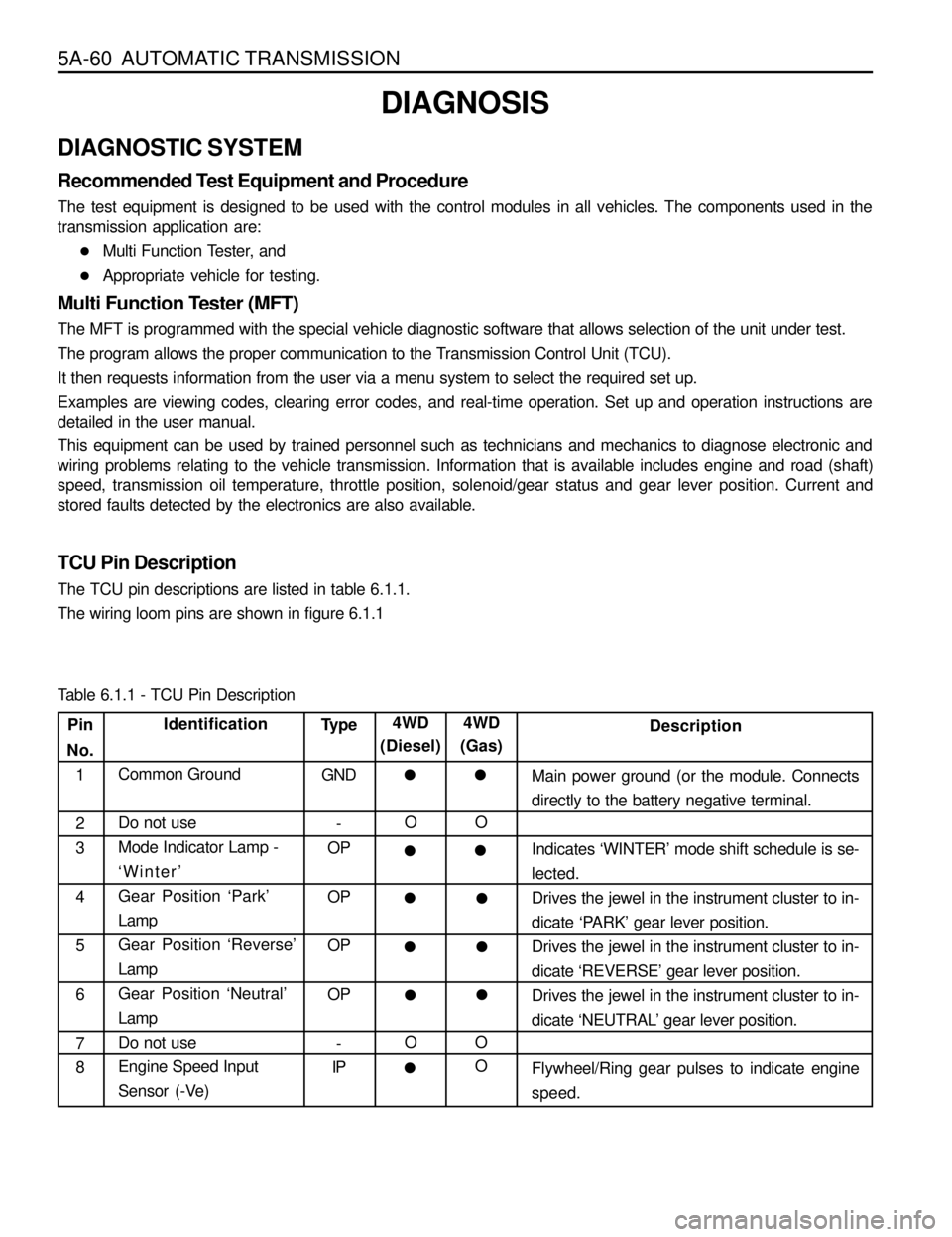
5A-60 AUTOMATIC TRANSMISSION
DIAGNOSIS
DIAGNOSTIC SYSTEM
Recommended Test Equipment and Procedure
The test equipment is designed to be used with the control modules in all vehicles. The components used in the
transmission application are:
lMulti Function Tester, and
lAppropriate vehicle for testing.
Multi Function Tester (MFT)
The MFT is programmed with the special vehicle diagnostic software that allows selection of the unit under test.
The program allows the proper communication to the Transmission Control Unit (TCU).
It then requests information from the user via a menu system to select the required set up.
Examples are viewing codes, clearing error codes, and real-time operation. Set up and operation instructions are
detailed in the user manual.
This equipment can be used by trained personnel such as technicians and mechanics to diagnose electronic and
wiring problems relating to the vehicle transmission. Information that is available includes engine and road (shaft)
speed, transmission oil temperature, throttle position, solenoid/gear status and gear lever position. Current and
stored faults detected by the electronics are also available.
TCU Pin Description
The TCU pin descriptions are listed in table 6.1.1.
The wiring loom pins are shown in figure 6.1.1
Pin
No.
1
2
3
4
5
6
7
8Identification
Common Ground
Do not use
Mode Indicator Lamp -
‘Winter’
Gear Position ‘Park’
Lamp
Gear Position ‘Reverse’
Lamp
Gear Position ‘Neutral’
Lamp
Do not use
Engine Speed Input
Sensor (-Ve)Type
GND
-
OP
OP
OP
OP
-
IPDescription
Main power ground (or the module. Connects
directly to the battery negative terminal.
Indicates ‘WINTER’ mode shift schedule is se-
lected.
Drives the jewel in the instrument cluster to in-
dicate ‘PARK’ gear lever position.
Drives the jewel in the instrument cluster to in-
dicate ‘REVERSE’ gear lever position.
Drives the jewel in the instrument cluster to in-
dicate ‘NEUTRAL’ gear lever position.
Flywheel/Ring gear pulses to indicate engine
speed. 4WD
(Diesel)
O
O
l
l l l
l
4WD
(Gas)
O
O
O
l
l l l
l
l
Table 6.1.1 - TCU Pin Description
Page 1038 of 1463
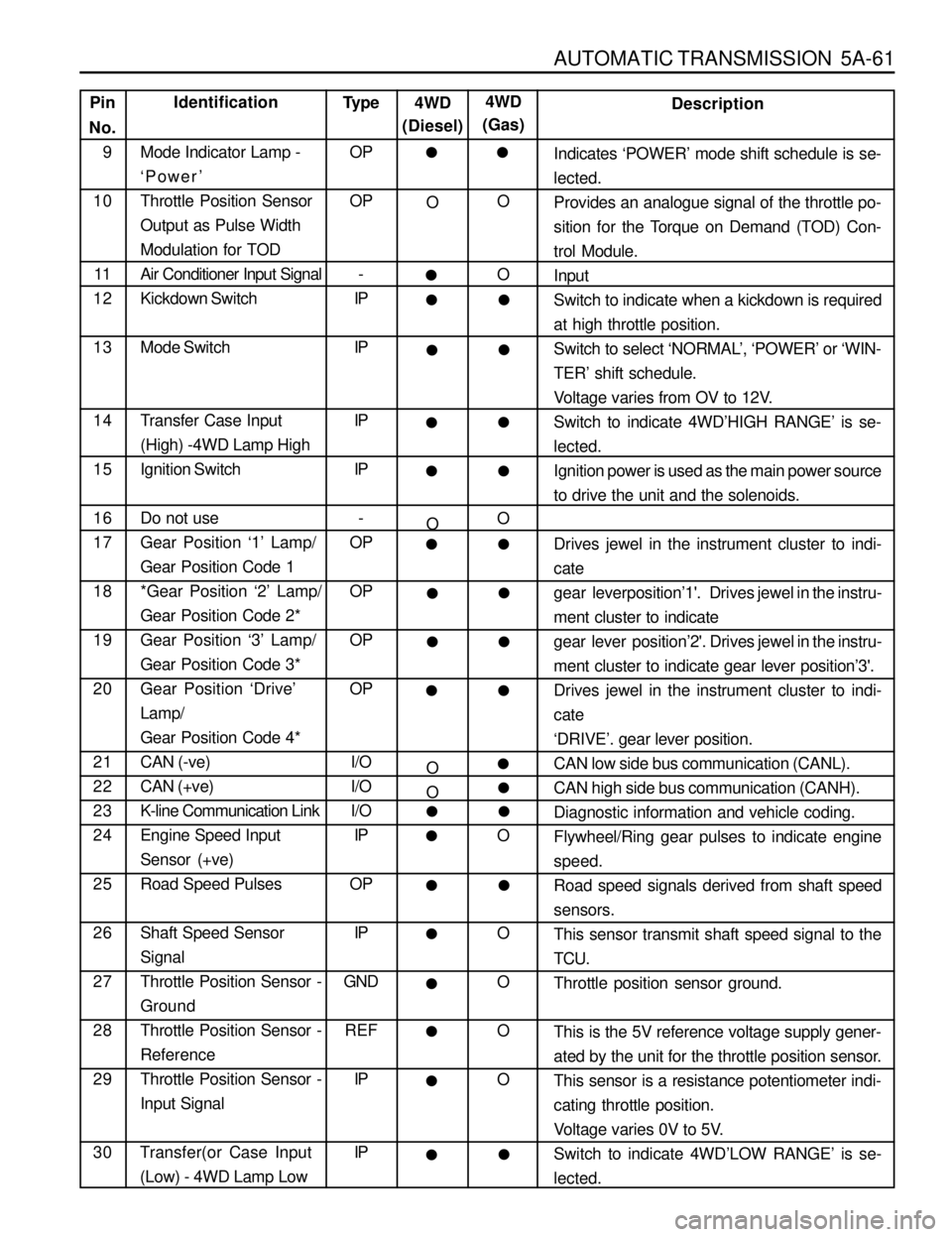
AUTOMATIC TRANSMISSION 5A-61
Pin
No.
9
10
11
12
13
14
15
16
17
18
19
20
21
22
23
24
25
26
27
28
29
30Identification
Mode Indicator Lamp -
‘Power’
Throttle Position Sensor
Output as Pulse Width
Modulation for TOD
Air Conditioner Input Signal
Kickdown Switch
Mode Switch
Transfer Case Input
(High) -4WD Lamp High
Ignition Switch
Do not use
Gear Position ‘1’ Lamp/
Gear Position Code 1
*Gear Position ‘2’ Lamp/
Gear Position Code 2*
Gear Position ‘3’ Lamp/
Gear Position Code 3*
Gear Position ‘Drive’
Lamp/
Gear Position Code 4*
CAN (-ve)
CAN (+ve)
K-line Communication Link
Engine Speed Input
Sensor (+ve)
Road Speed Pulses
Shaft Speed Sensor
Signal
Throttle Position Sensor -
Ground
Throttle Position Sensor -
Reference
Throttle Position Sensor -
Input Signal
Transfer(or Case Input
(Low) - 4WD Lamp LowType
OP
OP
-
IP
IP
IP
IP
-
OP
OP
OP
OP
I/O
I/O
I/O
IP
OP
IP
GND
REF
IP
IPDescription
Indicates ‘POWER’ mode shift schedule is se-
lected.
Provides an analogue signal of the throttle po-
sition for the Torque on Demand (TOD) Con-
trol Module.
Input
Switch to indicate when a kickdown is required
at high throttle position.
Switch to select ‘NORMAL’, ‘POWER’ or ‘WIN-
TER’ shift schedule.
Voltage varies from OV to 12V.
Switch to indicate 4WD’HIGH RANGE’ is se-
lected.
Ignition power is used as the main power source
to drive the unit and the solenoids.
Drives jewel in the instrument cluster to indi-
cate
gear leverposition’1'. Drives jewel in the instru-
ment cluster to indicate
gear lever position’2'. Drives jewel in the instru-
ment cluster to indicate gear lever position’3'.
Drives jewel in the instrument cluster to indi-
cate
‘DRIVE’. gear lever position.
CAN low side bus communication (CANL).
CAN high side bus communication (CANH).
Diagnostic information and vehicle coding.
Flywheel/Ring gear pulses to indicate engine
speed.
Road speed signals derived from shaft speed
sensors.
This sensor transmit shaft speed signal to the
TCU.
Throttle position sensor ground.
This is the 5V reference voltage supply gener-
ated by the unit for the throttle position sensor.
This sensor is a resistance potentiometer indi-
cating throttle position.
Voltage varies 0V to 5V.
Switch to indicate 4WD’LOW RANGE’ is se-
lected. 4WD
(Diesel)
O
O
O
O
l
l
l
4WD
(Gas)
O
O
O
O
O
O
O
O
l
l
l
ll
ll
ll
ll
ll
ll
l
l
ll
l
ll
l
l
l
l
ll l
Page 1039 of 1463
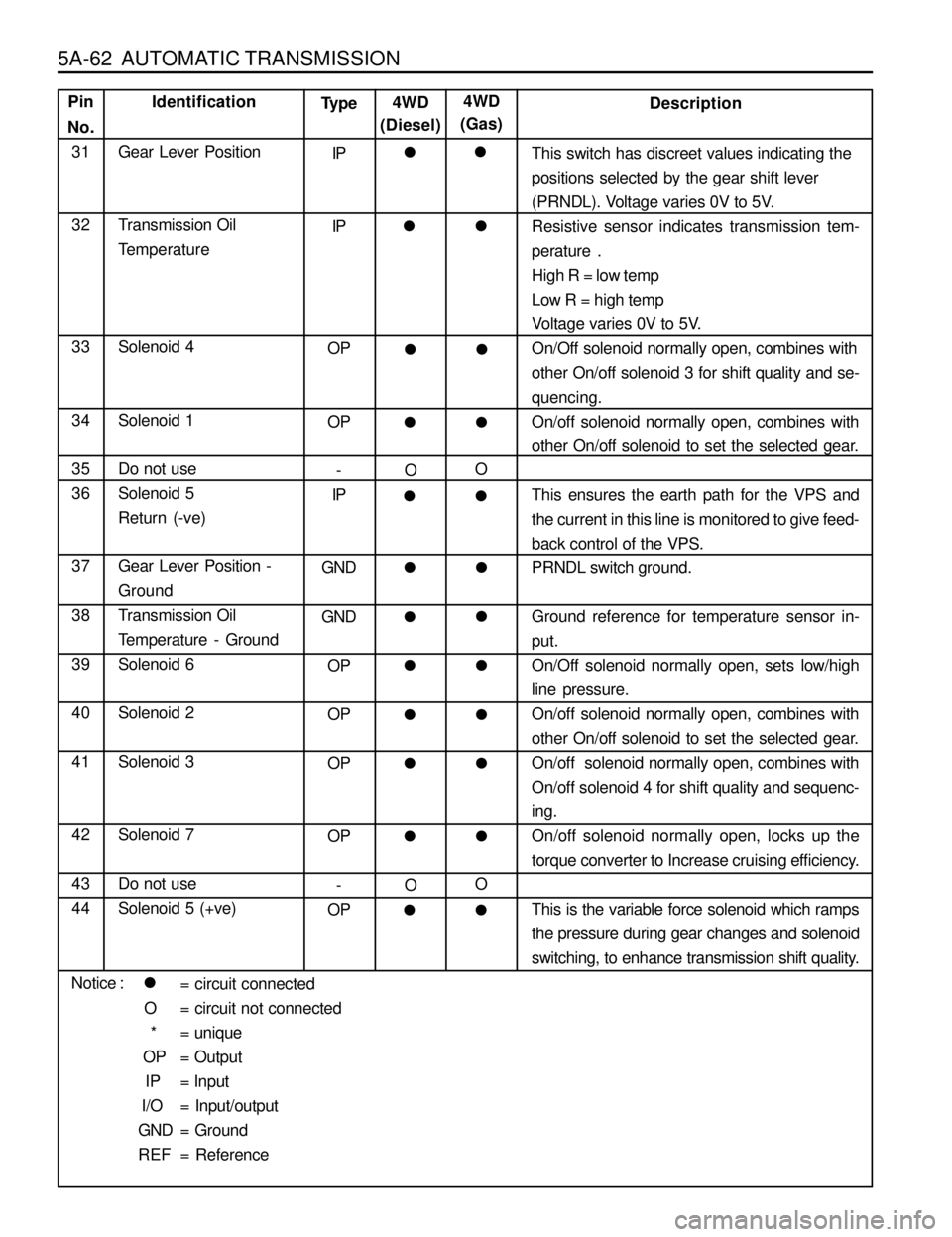
5A-62 AUTOMATIC TRANSMISSION
Identification
Gear Lever Position
Transmission Oil
Temperature
Solenoid 4
Solenoid 1
Do not use
Solenoid 5
Return (-ve)
Gear Lever Position -
Ground
Transmission Oil
Temperature - Ground
Solenoid 6
Solenoid 2
Solenoid 3
Solenoid 7
Do not use
Solenoid 5 (+ve)Type
IP
IP
OP
OP
-
IP
GND
GND
OP
OP
OP
OP
-
OPDescription
This switch has discreet values indicating the
positions selected by the gear shift lever
(PRNDL). Voltage varies 0V to 5V.
Resistive sensor indicates transmission tem-
perature .
High R = low temp
Low R = high temp
Voltage varies 0V to 5V.
On/Off solenoid normally open, combines with
other On/off solenoid 3 for shift quality and se-
quencing.
On/off solenoid normally open, combines with
other On/off solenoid to set the selected gear.
This ensures the earth path for the VPS and
the current in this line is monitored to give feed-
back control of the VPS.
PRNDL switch ground.
Ground reference for temperature sensor in-
put.
On/Off solenoid normally open, sets low/high
line pressure.
On/off solenoid normally open, combines with
other On/off solenoid to set the selected gear.
On/off solenoid normally open, combines with
On/off solenoid 4 for shift quality and sequenc-
ing.
On/off solenoid normally open, locks up the
torque converter to Increase cruising efficiency.
This is the variable force solenoid which ramps
the pressure during gear changes and solenoid
switching, to enhance transmission shift quality. 4WD
(Diesel)
O
O
l
l
4WD
(Gas)
O
O
l
l
ll
ll
ll
ll
Pin
No.
31
32
33
34
35
36
37
38
39
40
41
42
43
44
ll
ll
ll
ll
ll
ll
l= circuit connected
O = circuit not connected
* = unique
OP = Output
IP = Input
I/O = Input/output
GND = Ground
REF = Reference Notice :
Page 1057 of 1463
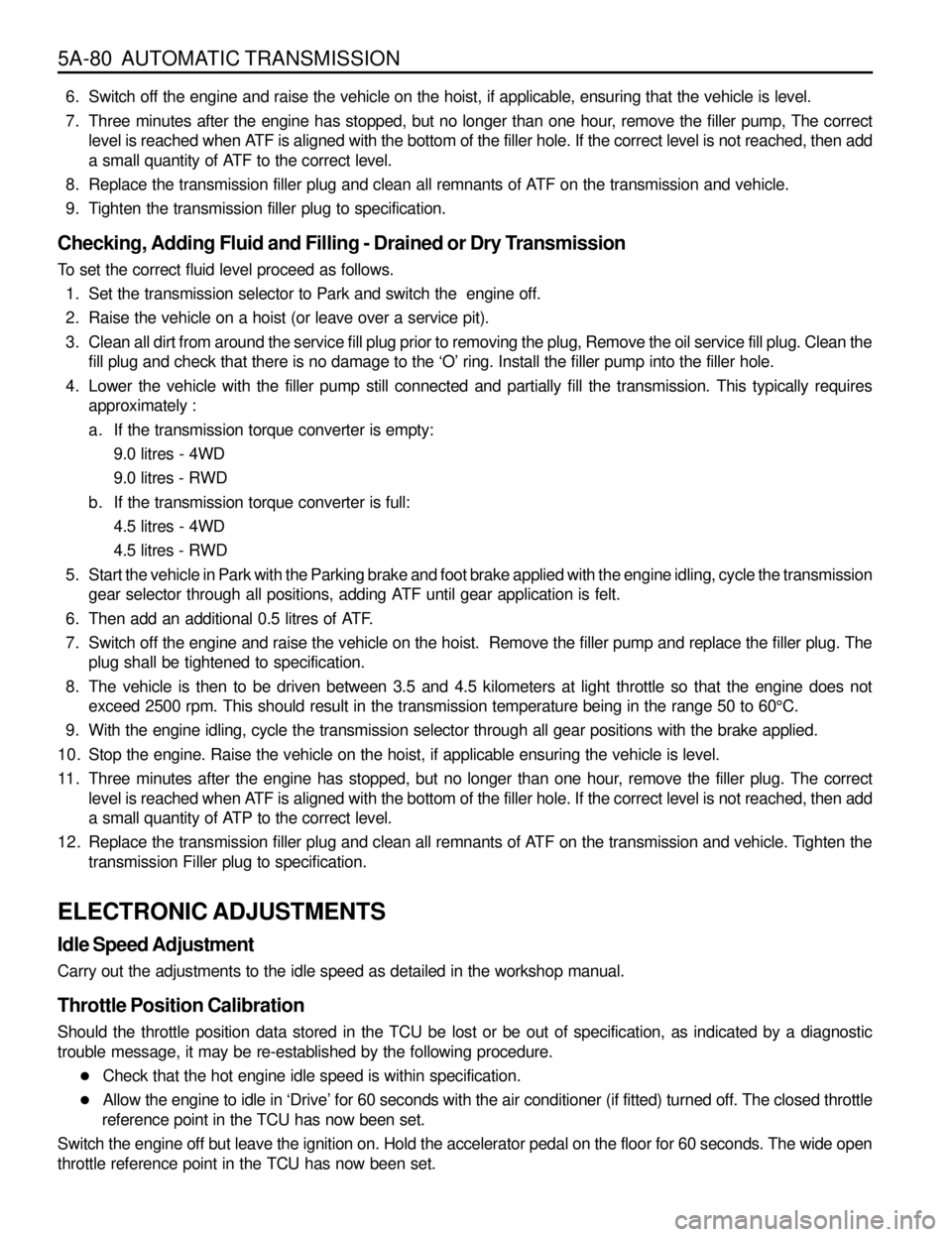
5A-80 AUTOMATIC TRANSMISSION
6. Switch off the engine and raise the vehicle on the hoist, if applicable, ensuring that the vehicle is level.
7. Three minutes after the engine has stopped, but no longer than one hour, remove the filler pump, The correct
level is reached when ATF is aligned with the bottom of the filler hole. If the correct level is not reached, then add
a small quantity of ATF to the correct level.
8. Replace the transmission filler plug and clean all remnants of ATF on the transmission and vehicle.
9. Tighten the transmission filler plug to specification.
Checking, Adding Fluid and Filling - Drained or Dry Transmission
To set the correct fluid level proceed as follows.
1. Set the transmission selector to Park and switch the engine off.
2. Raise the vehicle on a hoist (or leave over a service pit).
3. Clean all dirt from around the service fill plug prior to removing the plug, Remove the oil service fill plug. Clean the
fill plug and check that there is no damage to the ‘O’ ring. Install the filler pump into the filler hole.
4. Lower the vehicle with the filler pump still connected and partially fill the transmission. This typically requires
approximately :
a. If the transmission torque converter is empty:
9.0 litres - 4WD
9.0 litres - RWD
b. If the transmission torque converter is full:
4.5 litres - 4WD
4.5 litres - RWD
5. Start the vehicle in Park with the Parking brake and foot brake applied with the engine idling, cycle the transmission
gear selector through all positions, adding ATF until gear application is felt.
6. Then add an additional 0.5 litres of ATF.
7. Switch off the engine and raise the vehicle on the hoist. Remove the filler pump and replace the filler plug. The
plug shall be tightened to specification.
8. The vehicle is then to be driven between 3.5 and 4.5 kilometers at light throttle so that the engine does not
exceed 2500 rpm. This should result in the transmission temperature being in the range 50 to 60°C.
9. With the engine idling, cycle the transmission selector through all gear positions with the brake applied.
10. Stop the engine. Raise the vehicle on the hoist, if applicable ensuring the vehicle is level.
11. Three minutes after the engine has stopped, but no longer than one hour, remove the filler plug. The correct
level is reached when ATF is aligned with the bottom of the filler hole. If the correct level is not reached, then add
a small quantity of ATP to the correct level.
12. Replace the transmission filler plug and clean all remnants of ATF on the transmission and vehicle. Tighten the
transmission Filler plug to specification.
ELECTRONIC ADJUSTMENTS
Idle Speed Adjustment
Carry out the adjustments to the idle speed as detailed in the workshop manual.
Throttle Position Calibration
Should the throttle position data stored in the TCU be lost or be out of specification, as indicated by a diagnostic
trouble message, it may be re-established by the following procedure.
lCheck that the hot engine idle speed is within specification.
lAllow the engine to idle in ‘Drive’ for 60 seconds with the air conditioner (if fitted) turned off. The closed throttle
reference point in the TCU has now been set.
Switch the engine off but leave the ignition on. Hold the accelerator pedal on the floor for 60 seconds. The wide open
throttle reference point in the TCU has now been set.