engine oil SSANGYONG NEW REXTON 2012 Owner's Manual
[x] Cancel search | Manufacturer: SSANGYONG, Model Year: 2012, Model line: NEW REXTON, Model: SSANGYONG NEW REXTON 2012Pages: 600, PDF Size: 73.29 MB
Page 316 of 600
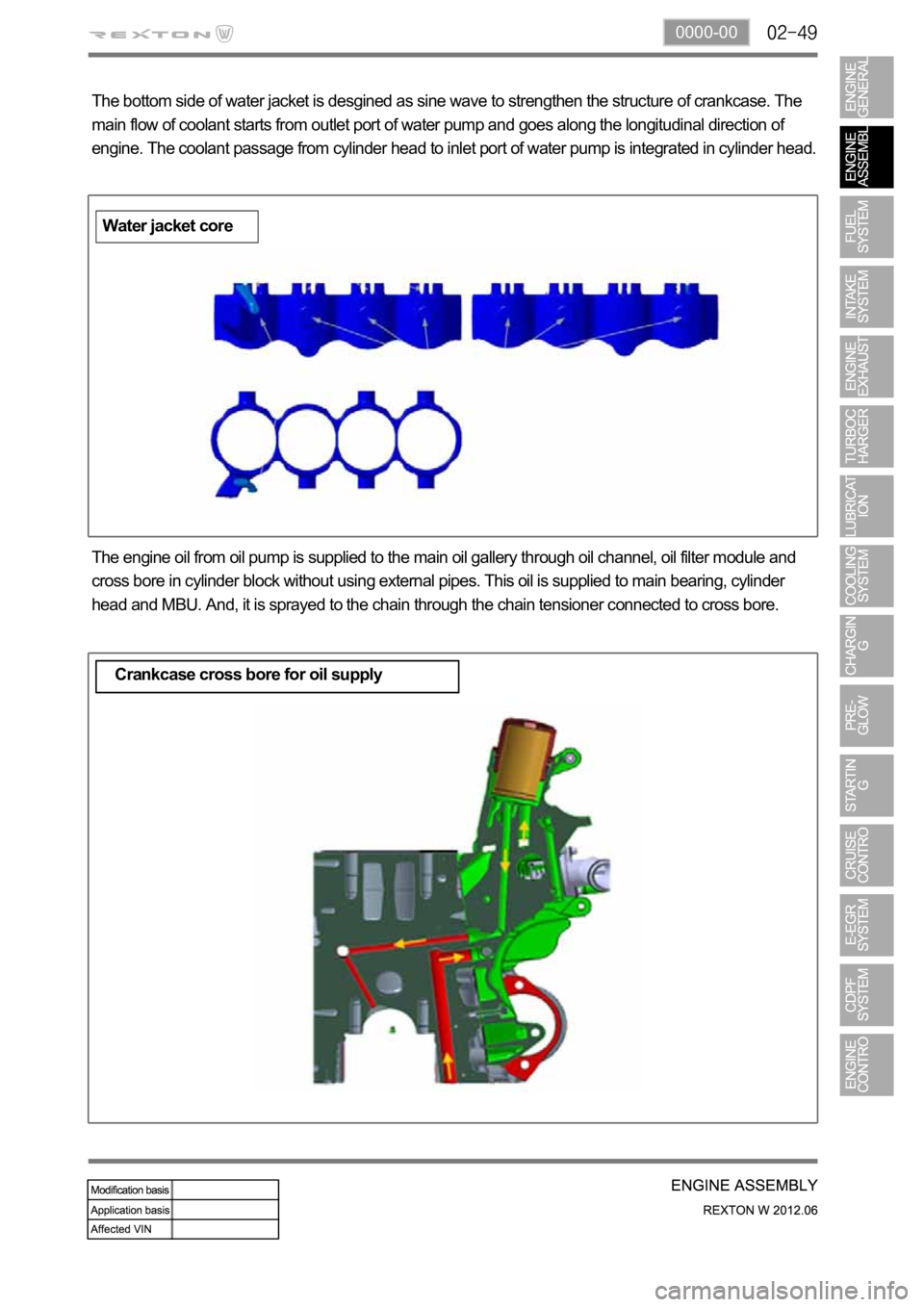
0000-00
The bottom side of water jacket is desgined as sine wave to strengthen the structure of crankcase. The
main flow of coolant starts from outlet port of water pump and goes along the longitudinal direction of
engine. The coolant passage from cylinder head to inlet port of water pump is integrated in cylinder head.
The engine oil from oil pump is supplied to the main oil gallery through oil channel, oil filter module and
cross bore in cylinder block without using external pipes. This oil is supplied to main bearing, cylinder
head and MBU. And, it is sprayed to the chain through the chain tensioner connected to cross bore.
Crankcase cross bore for oil supply
Water jacket core
Page 318 of 600
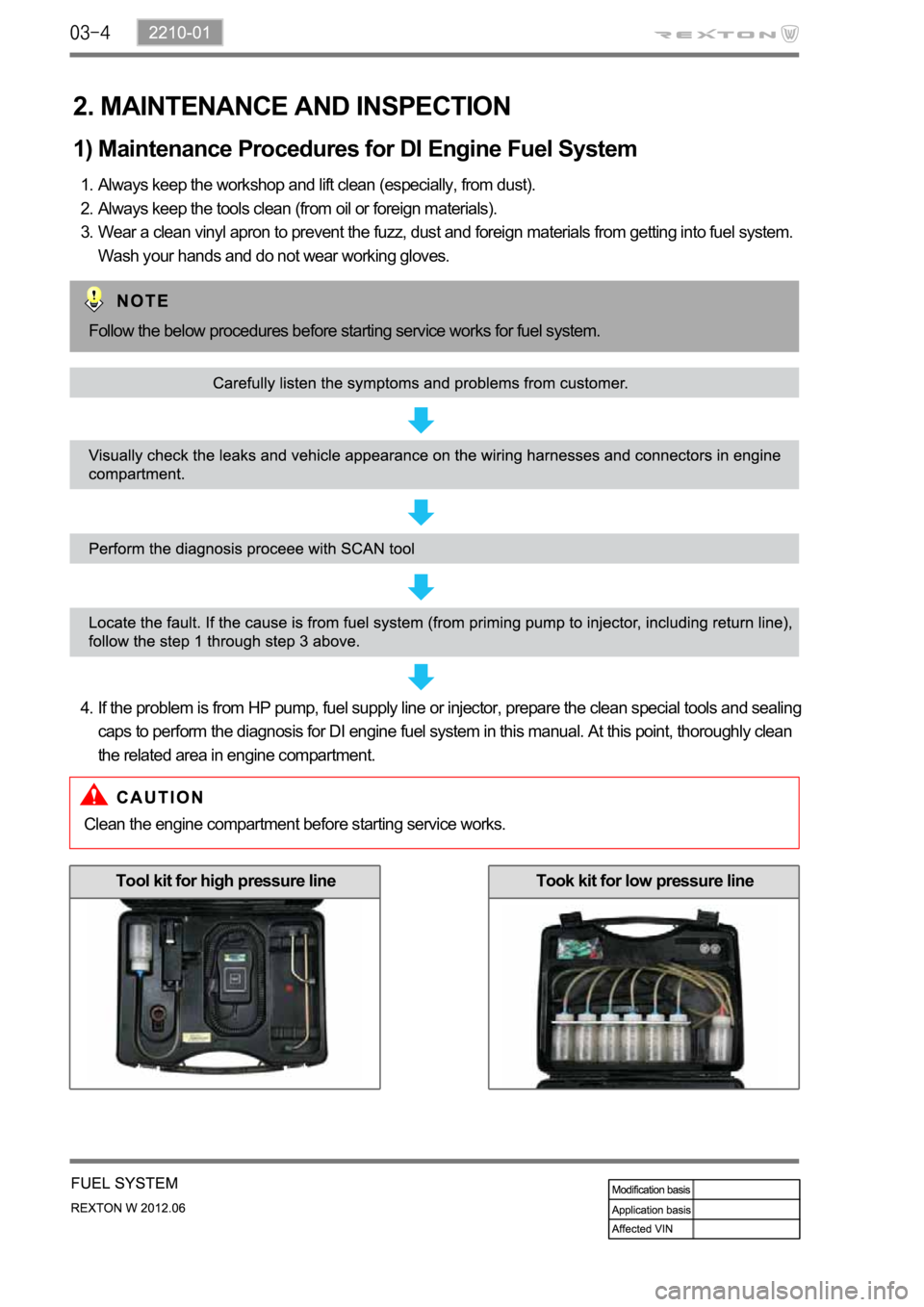
2. MAINTENANCE AND INSPECTION
1) Maintenance Procedures for DI Engine Fuel System
Always keep the workshop and lift clean (especially, from dust).
Always keep the tools clean (from oil or foreign materials).
Wear a clean vinyl apron to prevent the fuzz, dust and foreign materials from getting into fuel system.
Wash your hands and do not wear working gloves. 1.
2.
3.
Follow the below procedures before starting service works for fuel system.
If the problem is from HP pump, fuel supply line or injector, prepare the clean special tools and sealing
caps to perform the diagnosis for DI engine fuel system in this manual. At this point, thoroughly clean
the related area in engine compartment. 4.
Clean the engine compartment before starting service works.
Tool kit for high pressure lineTook kit for low pressure line
Page 334 of 600
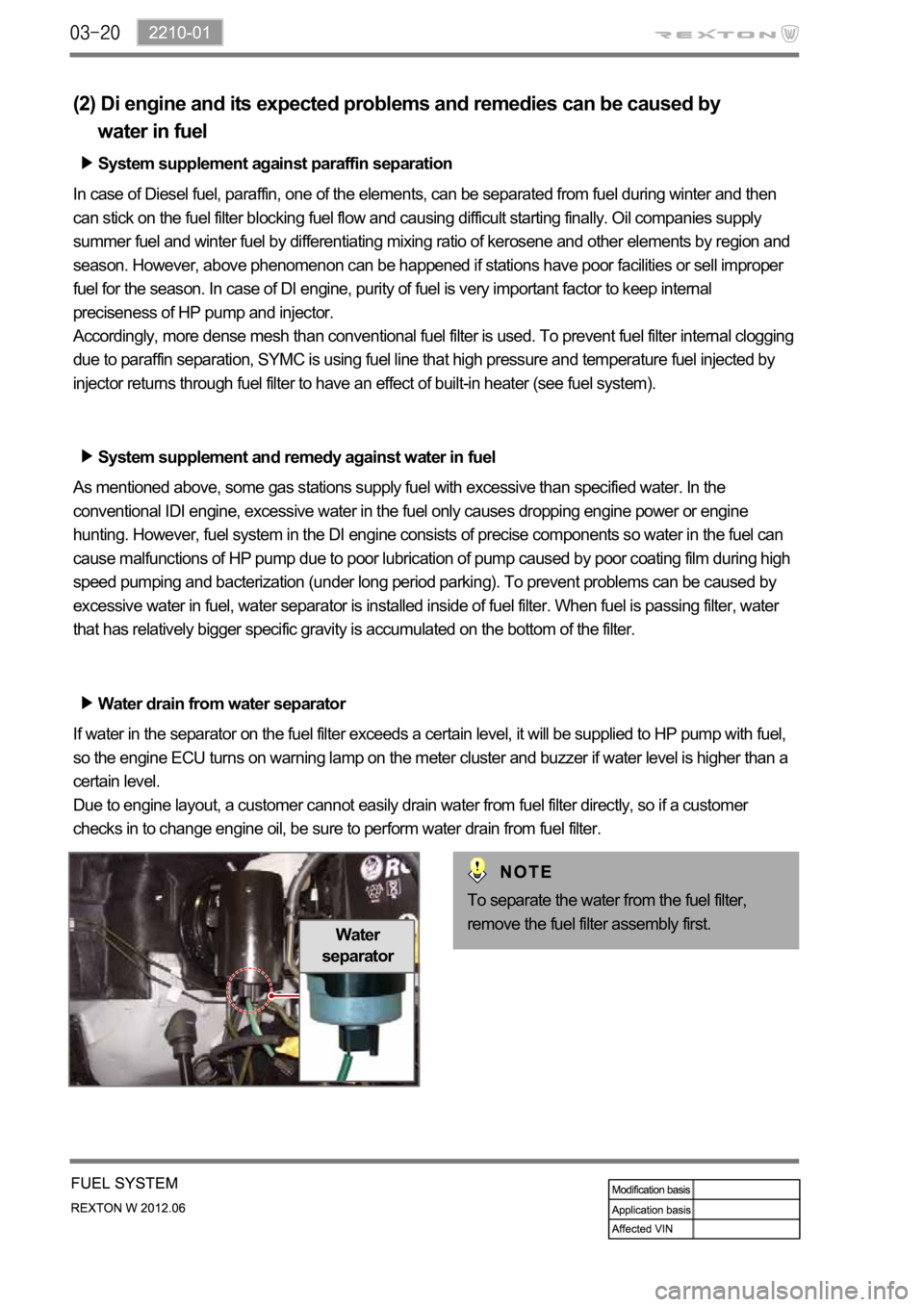
(2) Di engine and its expected problems and remedies can be caused by
water in fuel
System supplement against paraffin separation
In case of Diesel fuel, paraffin, one of the elements, can be separated from fuel during winter and then
can stick on the fuel filter blocking fuel flow and causing difficult starting finally. Oil companies supply
summer fuel and winter fuel by differentiating mixing ratio of kerosene and other elements by region and
season. However, above phenomenon can be happened if stations have poor facilities or sell improper
fuel for the season. In case of DI engine, purity of fuel is very important factor to keep internal
preciseness of HP pump and injector.
Accordingly, more dense mesh than conventional fuel filter is used. To prevent fuel filter internal clogging
due to paraffin separation, SYMC is using fuel line that high pressure and temperature fuel injected by
injector returns through fuel filter to have an effect of built-in heater (see fuel system).
System supplement and remedy against water in fuel
As mentioned above, some gas stations supply fuel with excessive than specified water. In the
conventional IDI engine, excessive water in the fuel only causes dropping engine power or engine
hunting. However, fuel system in the DI engine consists of precise components so water in the fuel can
cause malfunctions of HP pump due to poor lubrication of pump caused by poor coating film during high
speed pumping and bacterization (under long period parking). To prevent problems can be caused by
excessive water in fuel, water separator is installed inside of fuel filter. When fuel is passing filter, water
that has relatively bigger specific gravity is accumulated on the bottom of the filter.
Water drain from water separator
If water in the separator on the fuel filter exceeds a certain level, it will be supplied to HP pump with fuel,
so the engine ECU turns on warning lamp on the meter cluster and buzzer if water level is higher than a
certain level.
Due to engine layout, a customer cannot easily drain water from fuel filter directly, so if a customer
checks in to change engine oil, be sure to perform water drain from fuel filter.
Water
separator
To separate the water from the fuel filter,
remove the fuel filter assembly first.
Page 342 of 600
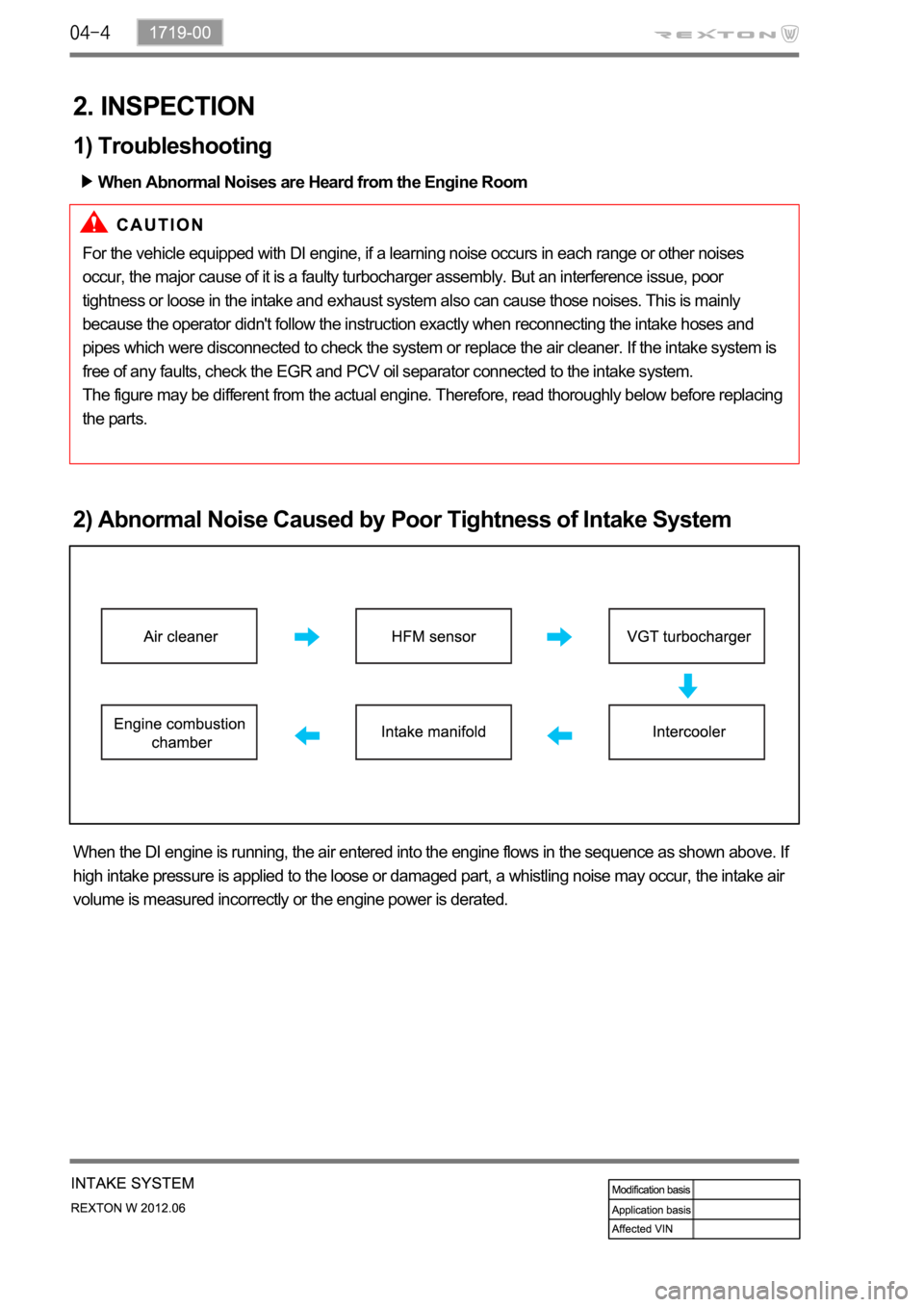
2. INSPECTION
1) Troubleshooting
When Abnormal Noises are Heard from the Engine Room
For the vehicle equipped with DI engine, if a learning noise occurs in each range or other noises
occur, the major cause of it is a faulty turbocharger assembly. But an interference issue, poor
tightness or loose in the intake and exhaust system also can cause those noises. This is mainly
because the operator didn't follow the instruction exactly when reconnecting the intake hoses and
pipes which were disconnected to check the system or replace the air cleaner. If the intake system is
free of any faults, check the EGR and PCV oil separator connected to the intake system.
The figure may be different from the actual engine. Therefore, read thoroughly below before replacing
the parts.
2) Abnormal Noise Caused by Poor Tightness of Intake System
When the DI engine is running, the air entered into the engine flows in the sequence as shown above. If
high intake pressure is applied to the loose or damaged part, a whistling noise may occur, the intake air
volume is measured incorrectly or the engine power is derated.
Page 343 of 600
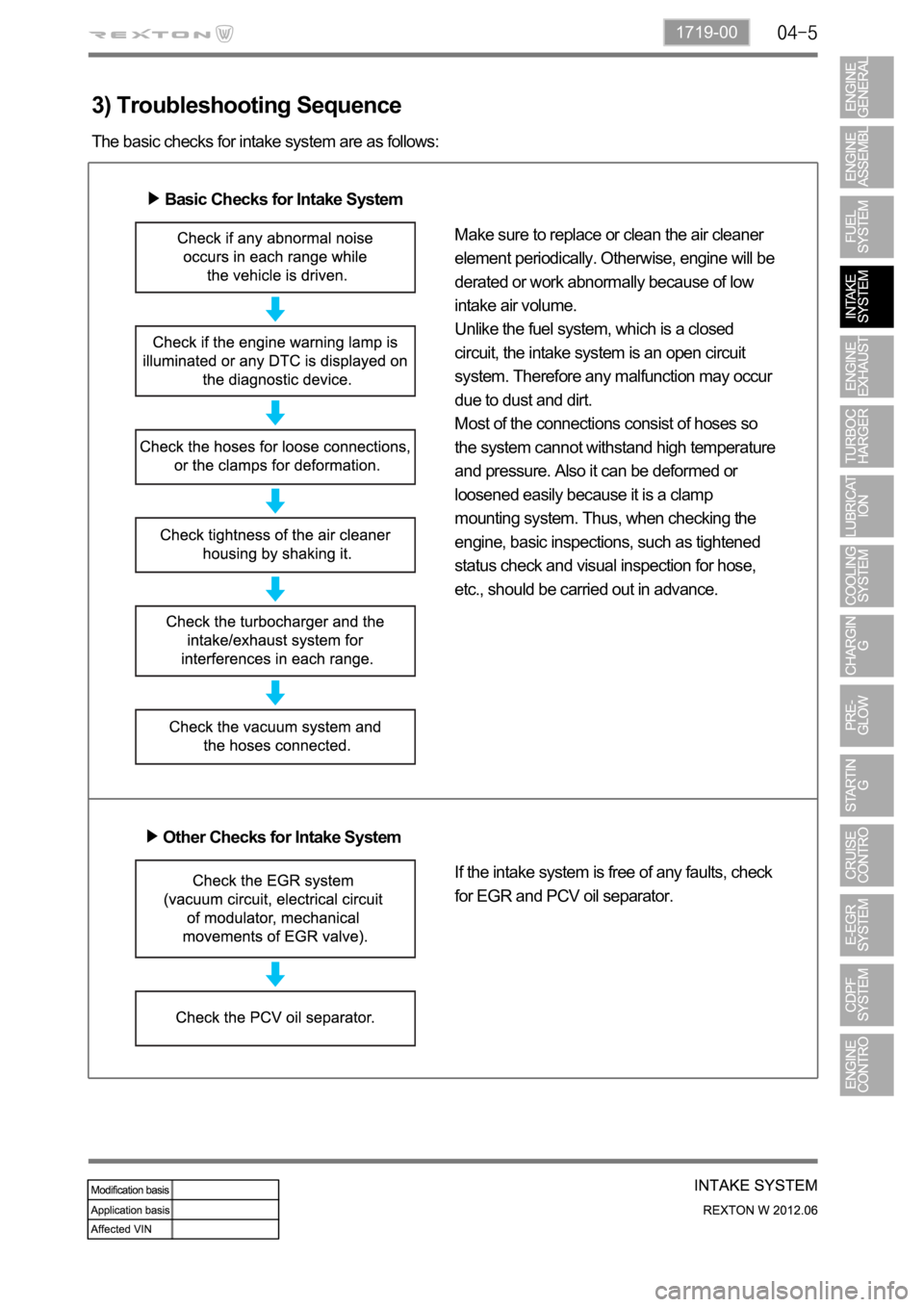
1719-00
3) Troubleshooting Sequence
The basic checks for intake system are as follows:
Basic Checks for Intake System
Make sure to replace or clean the air cleaner
element periodically. Otherwise, engine will be
derated or work abnormally because of low
intake air volume.
Unlike the fuel system, which is a closed
circuit, the intake system is an open circuit
system. Therefore any malfunction may occur
due to dust and dirt.
Most of the connections consist of hoses so
the system cannot withstand high temperature
and pressure. Also it can be deformed or
loosened easily because it is a clamp
mounting system. Thus, when checking the
engine, basic inspections, such as tightened
status check and visual inspection for hose,
etc., should be carried out in advance.
Other Checks for Intake System
If the intake system is free of any faults, check
for EGR and PCV oil separator.
Page 355 of 600

2. INSPECTION
1) Cautions During Driving
The following lists cautions to take during test drive and on the turbocharger vehicle, which must be
considered during the operation.
It's important not to drastically increase the engine rpm starting the engine. It could make rotation at
excessive speed even before the journal bearing is lubricated and when the turbocharger rotates in
poor oil supply condition, it could cause damage of bearing seizure within few seconds.
If the engine is running radically after replacing the engine oil or oil filter brings poor oil supply
condition. To avoid this, it's necessary to start off after idling the engine for about 1 minute allowing oil
to circulate to the turbocharger after the replacement.
When the engine is stopped abruptly after driving at high speed, the turbocharger continues to rotate
in condition where the oil pressure is at '0'. In such condition, an oil film between the journal bearing
and the housing shaft journal section gets broken and this causes abrasion of the journal bearing due
to the rapid contact. The repeat of such condition significantly reduces life of the turbocharger.
Therefore, the engine should be stopped possibly in the idle condition. 1.
2.
3.
After string for long period of time during winter season or in the low temperature condition where the
fluidity of engine oil declines, the engine, before being started, should be cranked to circulate oil and
must drive after checking the oil pressure is in normal condition by idling the engine for few minutes.
Page 356 of 600
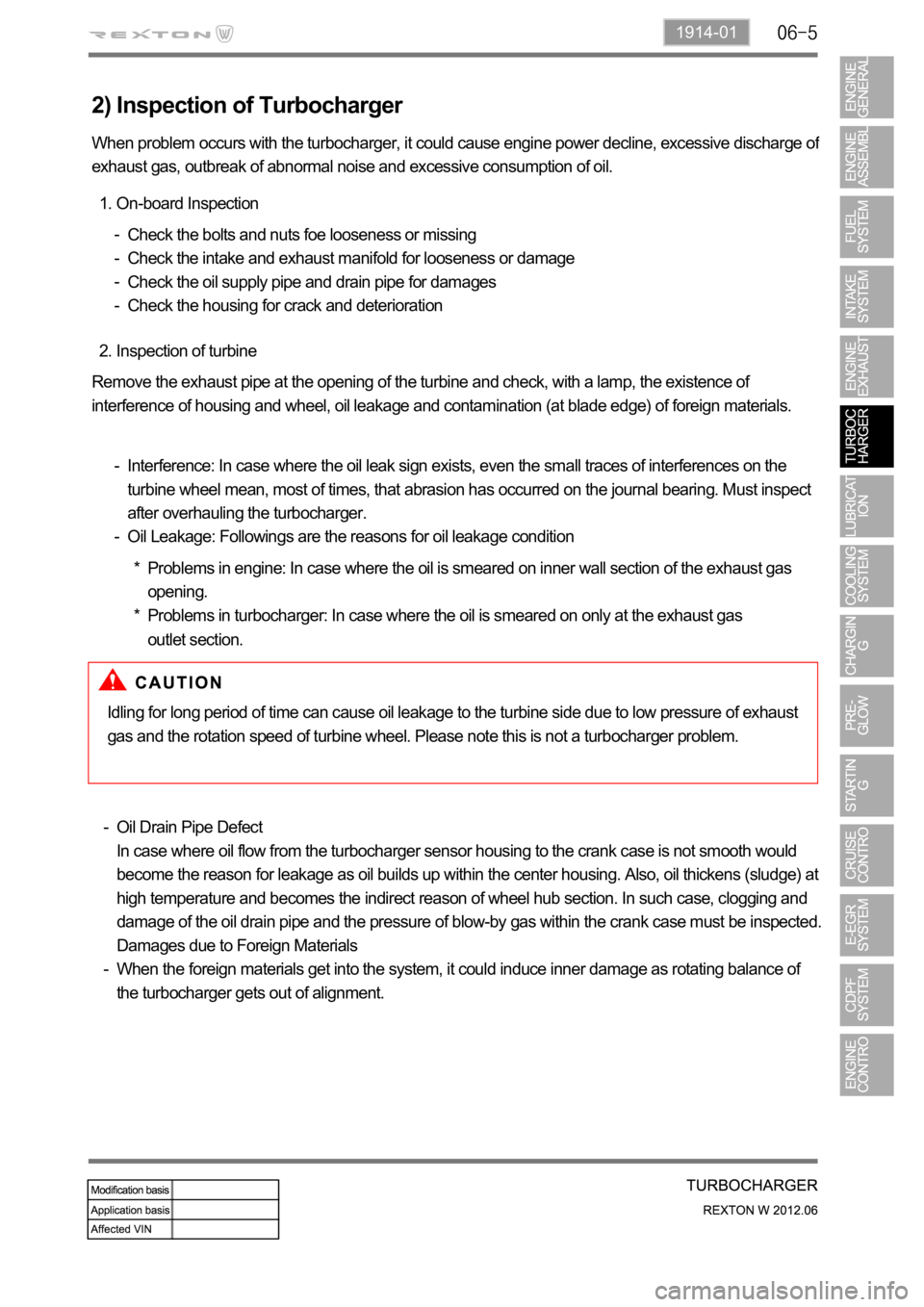
1914-01
2) Inspection of Turbocharger
When problem occurs with the turbocharger, it could cause engine power decline, excessive discharge of
exhaust gas, outbreak of abnormal noise and excessive consumption of oil.
On-board Inspection 1.
Check the bolts and nuts foe looseness or missing
Check the intake and exhaust manifold for looseness or damage
Check the oil supply pipe and drain pipe for damages
Check the housing for crack and deterioration -
-
-
-
Inspection of turbine 2.
Remove the exhaust pipe at the opening of the turbine and check, with a lamp, the existence of
interference of housing and wheel, oil leakage and contamination (at blade edge) of foreign materials.
Interference: In case where the oil leak sign exists, even the small traces of interferences on the
turbine wheel mean, most of times, that abrasion has occurred on the journal bearing. Must inspect
after overhauling the turbocharger.
Oil Leakage: Followings are the reasons for oil leakage condition -
-
Idling for long period of time can cause oil leakage to the turbine side due to low pressure of exhaust
gas and the rotation speed of turbine wheel. Please note this is not a turbocharger problem.
Oil Drain Pipe Defect
In case where oil flow from the turbocharger sensor housing to the crank case is not smooth would
become the reason for leakage as oil builds up within the center housing. Also, oil thickens (sludge) at
high temperature and becomes the indirect reason of wheel hub section. In such case, clogging and
damage of the oil drain pipe and the pressure of blow-by gas within the crank case must be inspected.
Damages due to Foreign Materials
When the foreign materials get into the system, it could induce inner damage as rotating balance of
the turbocharger gets out of alignment. -
-Problems in engine: In case where the oil is smeared on inner wall section of the exhaust gas
opening.
Problems in turbocharger: In case where the oil is smeared on only at the exhaust gas
outlet section. *
*
Page 357 of 600
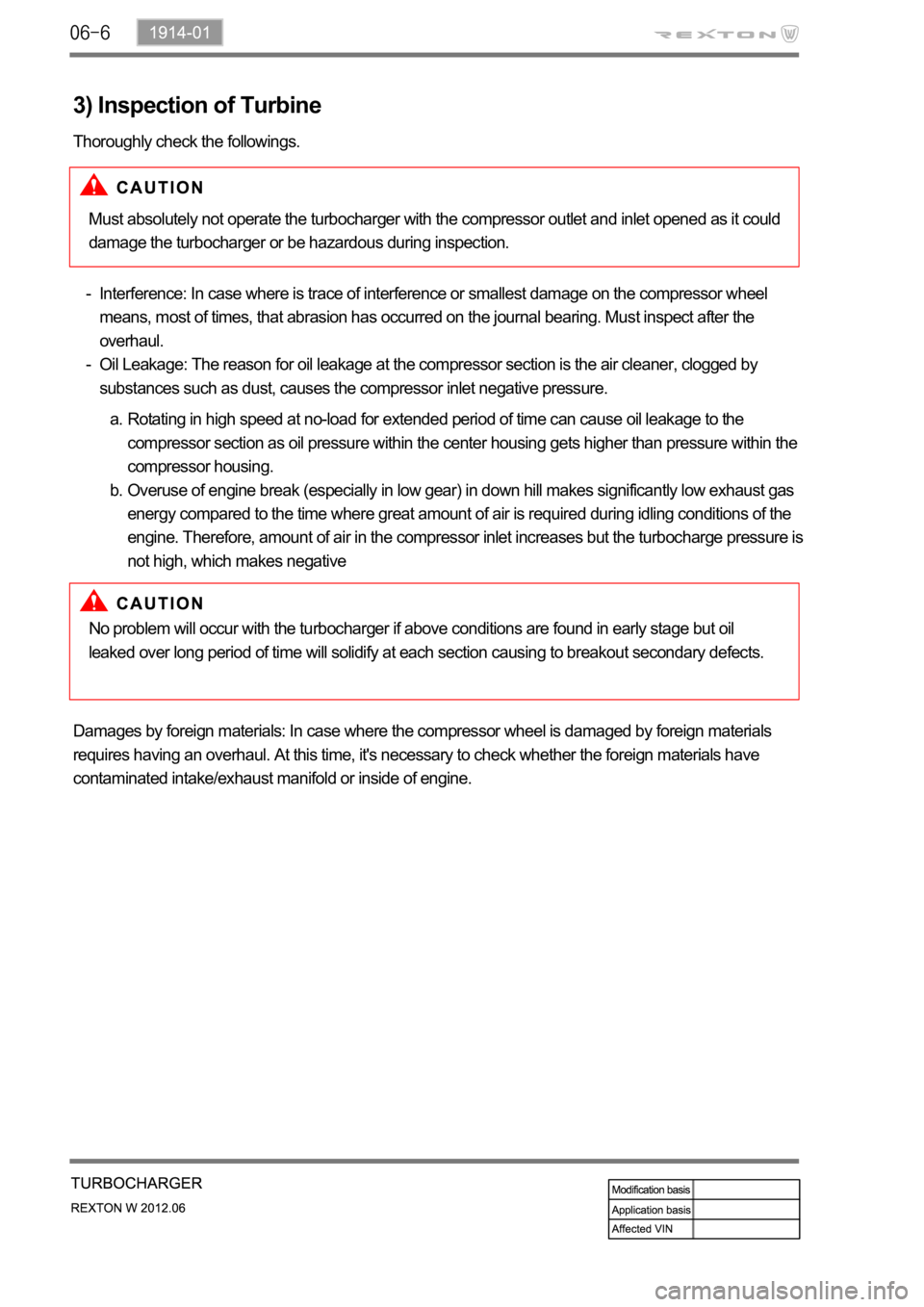
3) Inspection of Turbine
Thoroughly check the followings.
Must absolutely not operate the turbocharger with the compressor outlet and inlet opened as it could
damage the turbocharger or be hazardous during inspection.
Interference: In case where is trace of interference or smallest damage on the compressor wheel
means, most of times, that abrasion has occurred on the journal bearing. Must inspect after the
overhaul.
Oil Leakage: The reason for oil leakage at the compressor section is the air cleaner, clogged by
substances such as dust, causes the compressor inlet negative pressure. -
-
Rotating in high speed at no-load for extended period of time can cause oil leakage to the
compressor section as oil pressure within the center housing gets higher than pressure within the
compressor housing.
Overuse of engine break (especially in low gear) in down hill makes significantly low exhaust gas
energy compared to the time where great amount of air is required during idling conditions of the
engine. Therefore, amount of air in the compressor inlet increases but the turbocharge pressure is
not high, which makes negative a.
b.
No problem will occur with the turbocharger if above conditions are found in early stage but oil
leaked over long period of time will solidify at each section causing to breakout secondary defects.
Damages by foreign materials: In case where the compressor wheel is damaged by foreign materials
requires having an overhaul. At this time, it's necessary to check whether the foreign materials have
contaminated intake/exhaust manifold or inside of engine.
Page 362 of 600
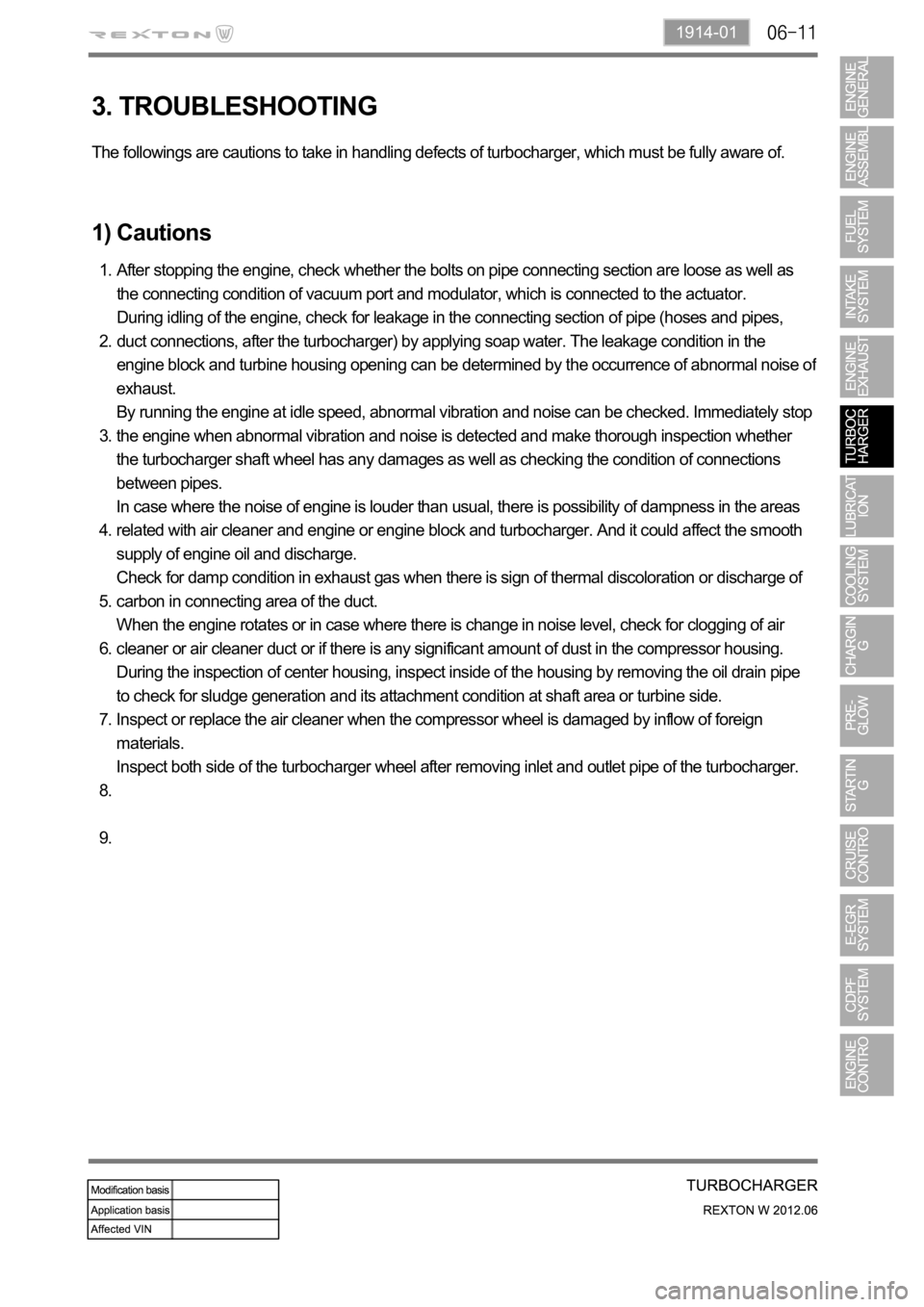
1914-01
3. TROUBLESHOOTING
The followings are cautions to take in handling defects of turbocharger, which must be fully aware of.
1) Cautions
After stopping the engine, check whether the bolts on pipe connecting section are loose as well as
the connecting condition of vacuum port and modulator, which is connected to the actuator.
During idling of the engine, check for leakage in the connecting section of pipe (hoses and pipes,
duct connections, after the turbocharger) by applying soap water. The leakage condition in the
engine block and turbine housing opening can be determined by the occurrence of abnormal noise o
f
exhaust.
By running the engine at idle speed, abnormal vibration and noise can be checked. Immediately stop
the engine when abnormal vibration and noise is detected and make thorough inspection whether
the turbocharger shaft wheel has any damages as well as checking the condition of connections
between pipes.
In case where the noise of engine is louder than usual, there is possibility of dampness in the areas
related with air cleaner and engine or engine block and turbocharger. And it could affect the smooth
supply of engine oil and discharge.
Check for damp condition in exhaust gas when there is sign of thermal discoloration or discharge of
carbon in connecting area of the duct.
When the engine rotates or in case where there is change in noise level, check for clogging of air
cleaner or air cleaner duct or if there is any significant amount of dust in the compressor housing.
During the inspection of center housing, inspect inside of the housing by removing the oil drain pipe
to check for sludge generation and its attachment condition at shaft area or turbine side.
Inspect or replace the air cleaner when the compressor wheel is damaged by inflow of foreign
materials.
Inspect both side of the turbocharger wheel after removing inlet and outlet pipe of the turbocharger. 1.
2.
3.
4.
5.
6.
7.
8.
9.
Page 374 of 600
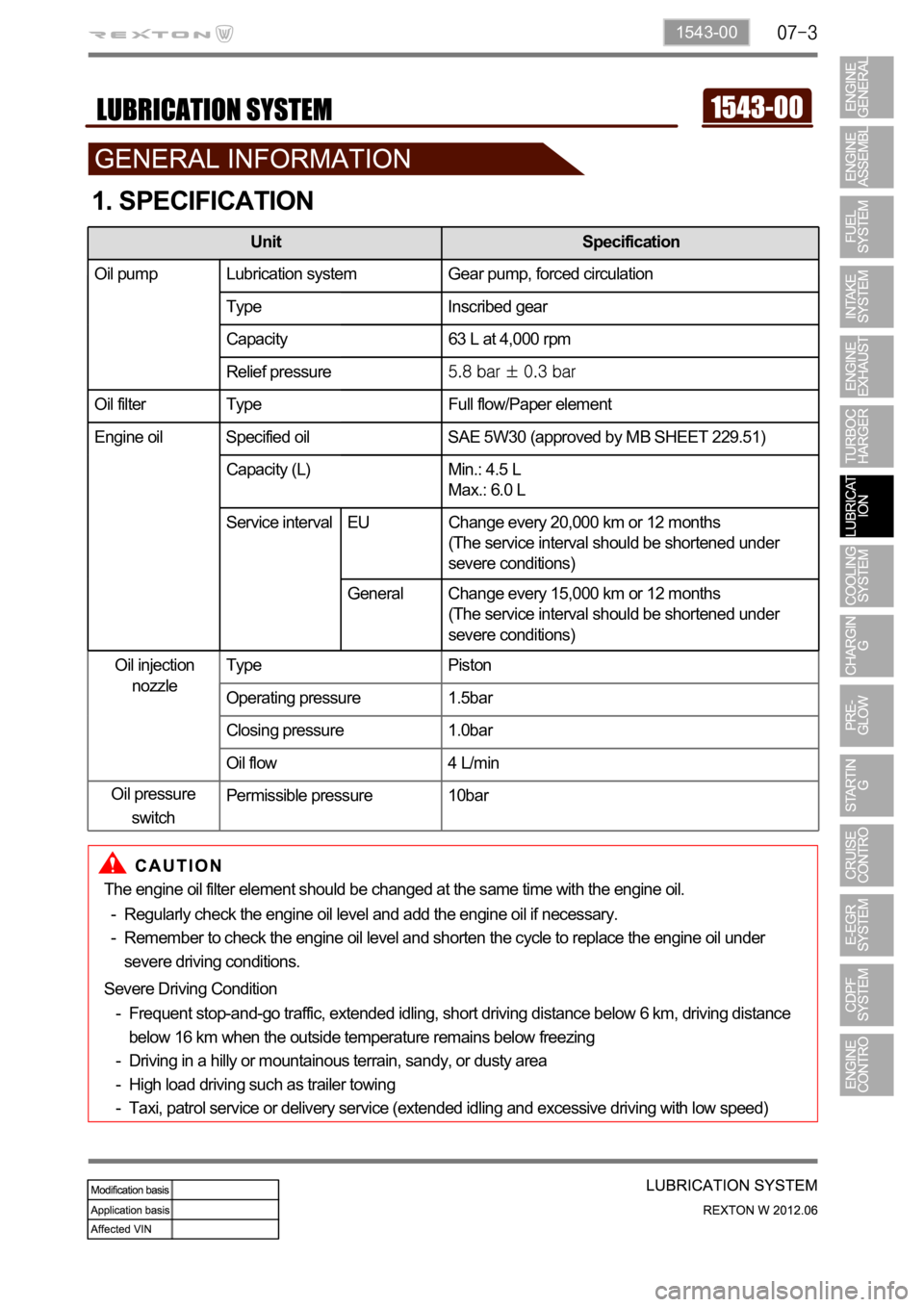
1543-00
1. SPECIFICATION
The engine oil filter element should be changed at the same time with the engine oil.
Regularly check the engine oil level and add the engine oil if necessary.
Remember to check the engine oil level and shorten the cycle to replace the engine oil under
severe driving conditions. -
-
Severe Driving Condition
Frequent stop-and-go traffic, extended idling, short driving distance below 6 km, driving distance
below 16 km when the outside temperature remains below freezing
Driving in a hilly or mountainous terrain, sandy, or dusty area
High load driving such as trailer towing
Taxi, patrol service or delivery service (extended idling and excessive driving with low speed) -
-
-
-
Unit Specification
Oil pump Lubrication system Gear pump, forced circulation
Type Inscribed gear
Capacity 63 L at 4,000 rpm
Relief pressure
Oil filter Type Full flow/Paper element
Engine oil Specified oil SAE 5W30 (approved by MB SHEET 229.51)
Capacity (L) Min.: 4.5 L
Max.: 6.0 L
Service interval Change every 15,000 km or 12 months (But, shorten
the service interval under severe condition)
Oil injection
nozzleType Piston
Operating pressure 1.5bar
Closing pressure 1.0bar
Oil flow 4 L/min
Permissible pressure 10bar
Unit Specification
Oil pump Lubrication system Gear pump, forced circulation
Type Inscribed gear
Capacity 63 L at 4,000 rpm
Relief pressure
Oil filter Type Full flow/Paper element
Engine oil Specified oil SAE 5W30 (approved by MB SHEET 229.51)
Capacity (L) Min.: 4.5 L
Max.: 6.0 L
Service interval EU Change every 20,000 km or 12 months
(The service interval should be shortened under
severe conditions)
General Change every 15,000 km or 12 months
(The service interval should be shortened under
severe conditions)
Oil pressure
switch