brake sensor SSANGYONG TURISMO 2013 Service Manual
[x] Cancel search | Manufacturer: SSANGYONG, Model Year: 2013, Model line: TURISMO, Model: SSANGYONG TURISMO 2013Pages: 796, PDF Size: 78.99 MB
Page 167 of 796
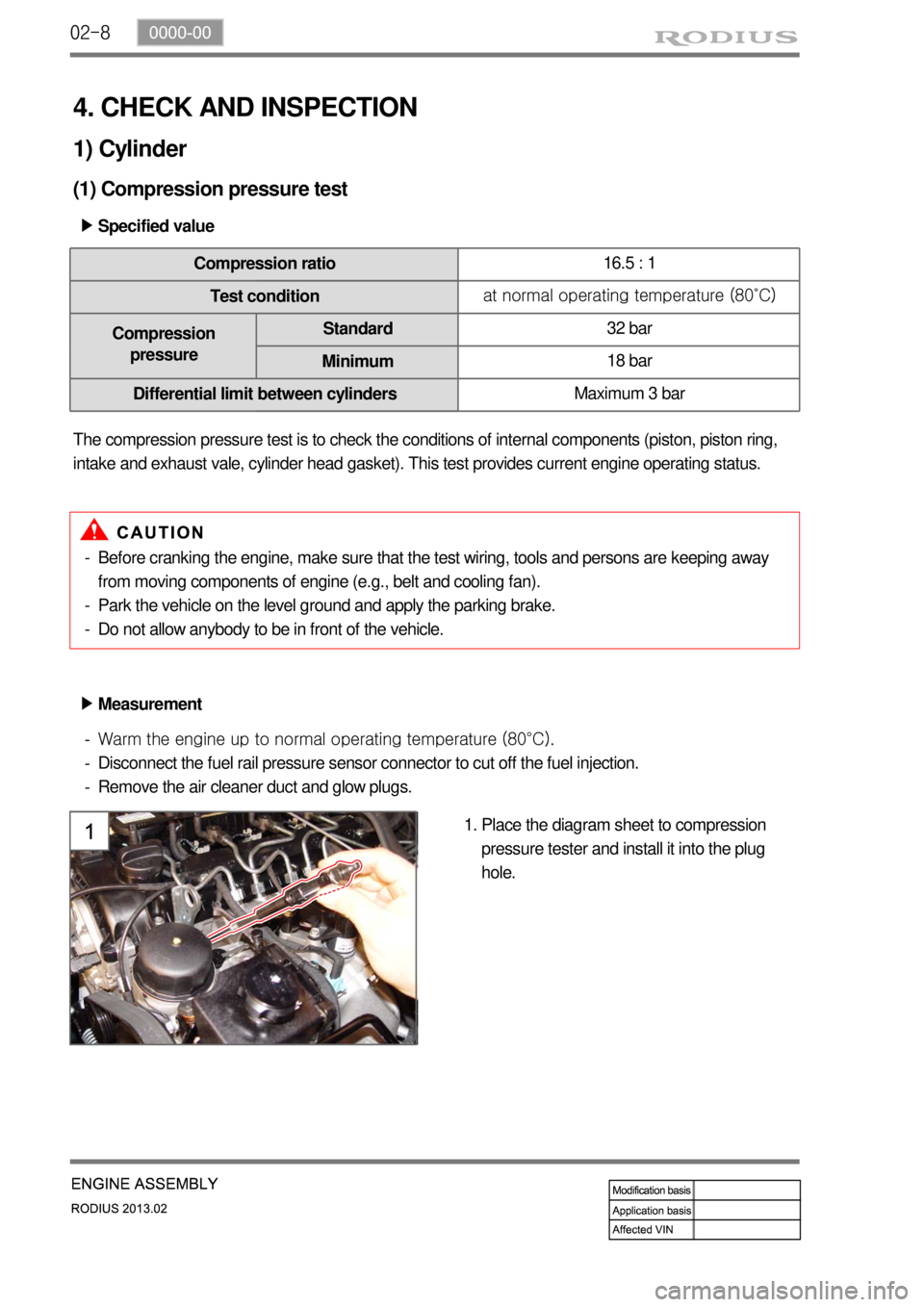
02-8
4. CHECK AND INSPECTION
1) Cylinder
(1) Compression pressure test
Specified value ▶
Compression ratio16.5 : 1
Test conditionat normal operating temperature (80˚C)
Compression
pressureStandard32 bar
Minimum18 bar
Differential limit between cylindersMaximum 3 bar
The compression pressure test is to check the conditions of internal components (piston, piston ring,
intake and exhaust vale, cylinder head gasket). This test provides current engine operating status.
Measurement ▶
Warm the engine up to normal operating temperature (80°C).
Disconnect the fuel rail pressure sensor connector to cut off the fuel injection.
Remove the air cleaner duct and glow plugs. -
-
-
Place the diagram sheet to compression
pressure tester and install it into the plug
hole. 1. Before cranking the engine, make sure that the test wiring, tools and persons are keeping away
from moving components of engine (e.g., belt and cooling fan).
Park the vehicle on the level ground and apply the parking brake.
Do not allow anybody to be in front of the vehicle. -
-
-
Page 331 of 796
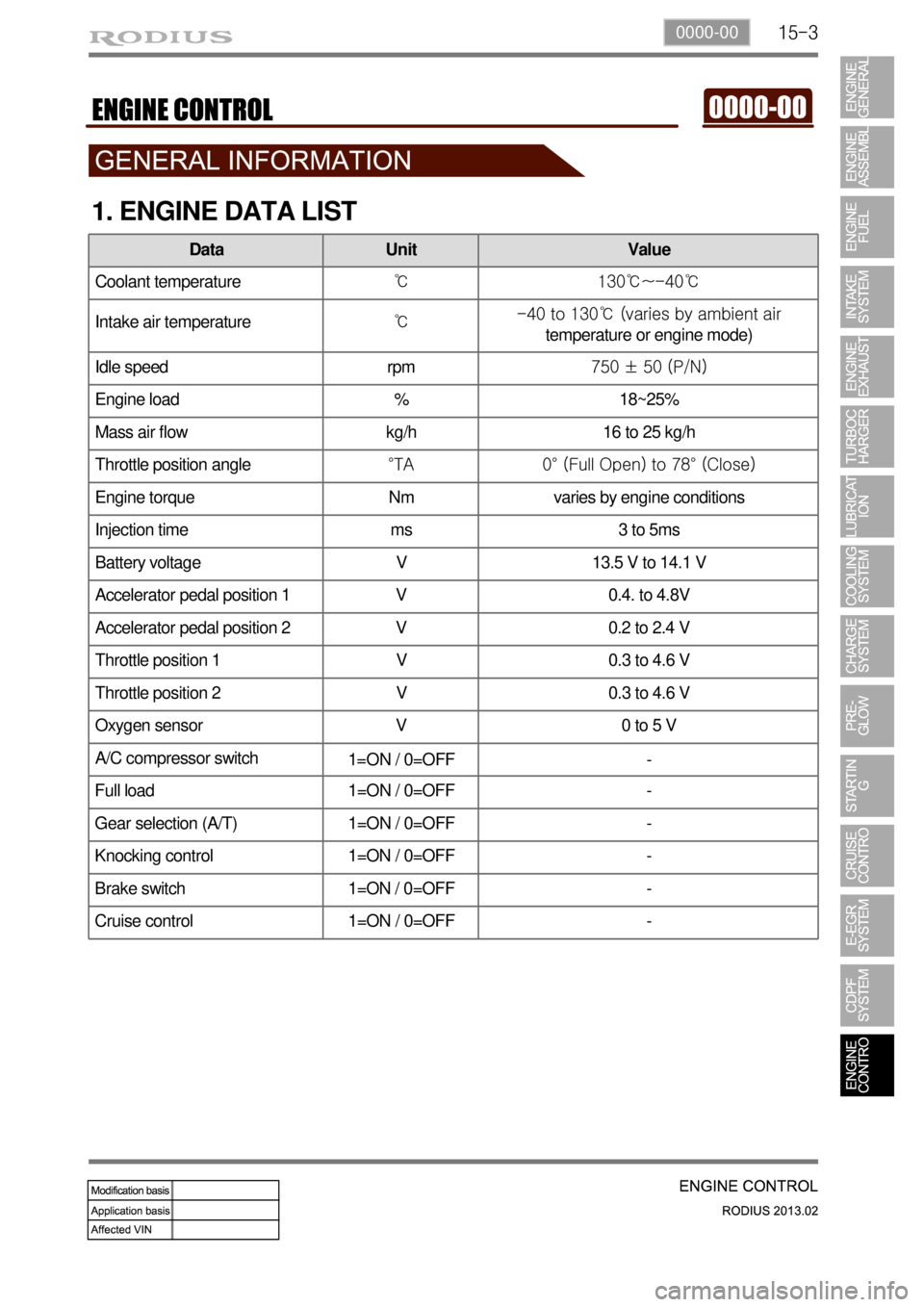
15-30000-00
1. ENGINE DATA LIST
Data Unit Value
Coolant temperature℃ 130℃~-40℃
Intake air temperature℃ -40 to 130℃ (varies by ambient air
temperature or engine mode)
Idle speed rpm 750 ± 50 (P/N)
Engine load % 18~25%
Mass air flow kg/h 16 to 25 kg/h
Throttle position angle°TA 0° (Full Open) to 78° (Close)
Engine torque Nm varies by engine conditions
Injection time ms 3 to 5ms
Battery voltage V 13.5 V to 14.1 V
Accelerator pedal position 1 V 0.4. to 4.8V
Accelerator pedal position 2 V 0.2 to 2.4 V
Throttle position 1 V 0.3 to 4.6 V
Throttle position 2 V 0.3 to 4.6 V
Oxygen sensor V 0 to 5 V
A/C compressor switch
1=ON / 0=OFF -
Full load 1=ON / 0=OFF -
Gear selection (A/T) 1=ON / 0=OFF -
Knocking control 1=ON / 0=OFF -
Brake switch 1=ON / 0=OFF -
Cruise control 1=ON / 0=OFF -
Page 337 of 796
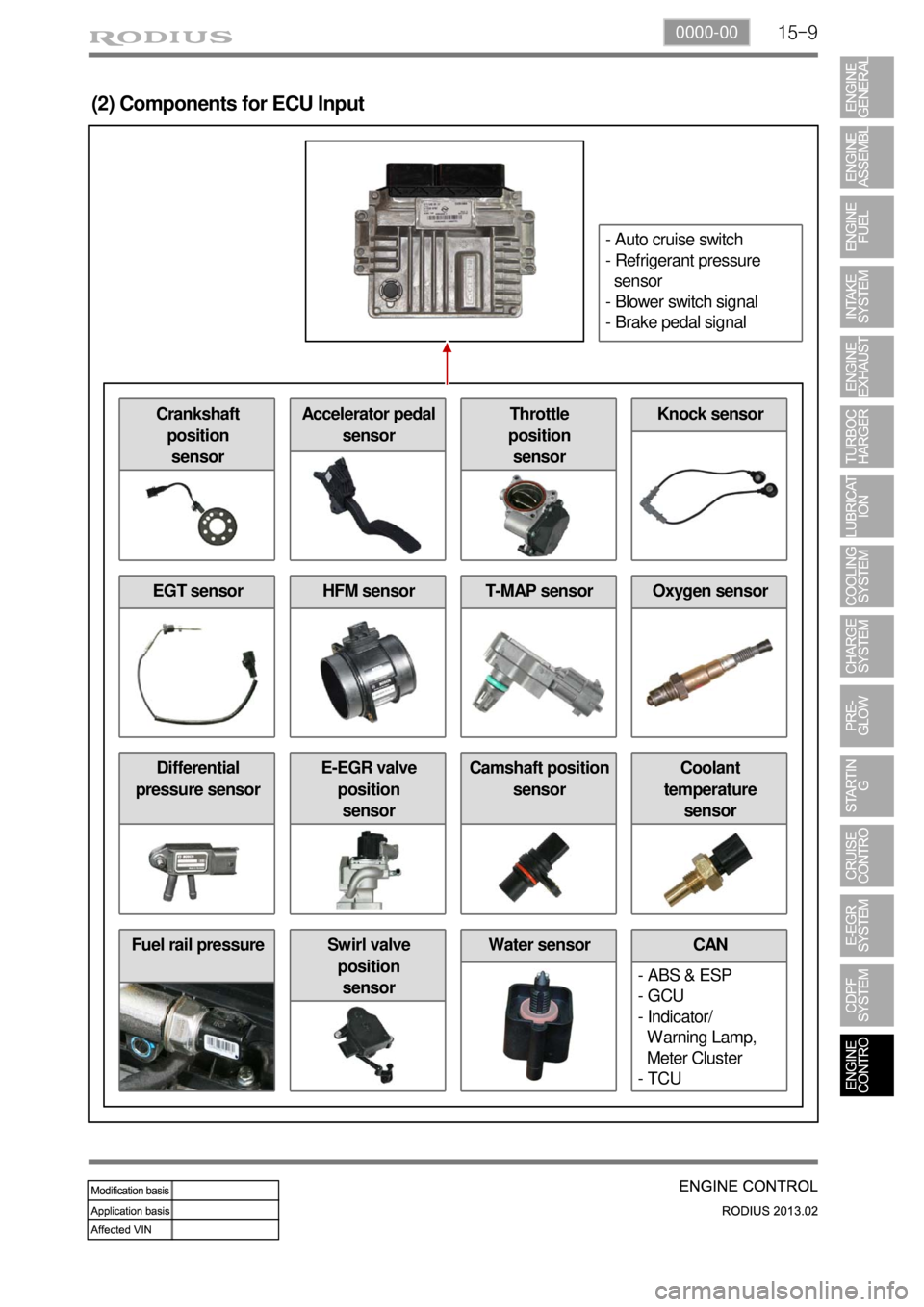
15-90000-00
Fuel rail pressure Water sensor
(2) Components for ECU Input
CAN
- ABS & ESP
- GCU
- Indicator/
Warning Lamp,
Meter Cluster
- TCUSwirl valve
position
sensor
Differential
pressure sensorE-EGR valve
position
sensorCamshaft position
sensorCoolant
temperature
sensor
EGT sensorHFM sensorOxygen sensorT-MAP sensor
Crankshaft
position
sensorAccelerator pedal
sensorThrottle
position
sensorKnock sensor
- Auto cruise switch
- Refrigerant pressure
sensor
- Blower switch signal
- Brake pedal signal
Page 339 of 796
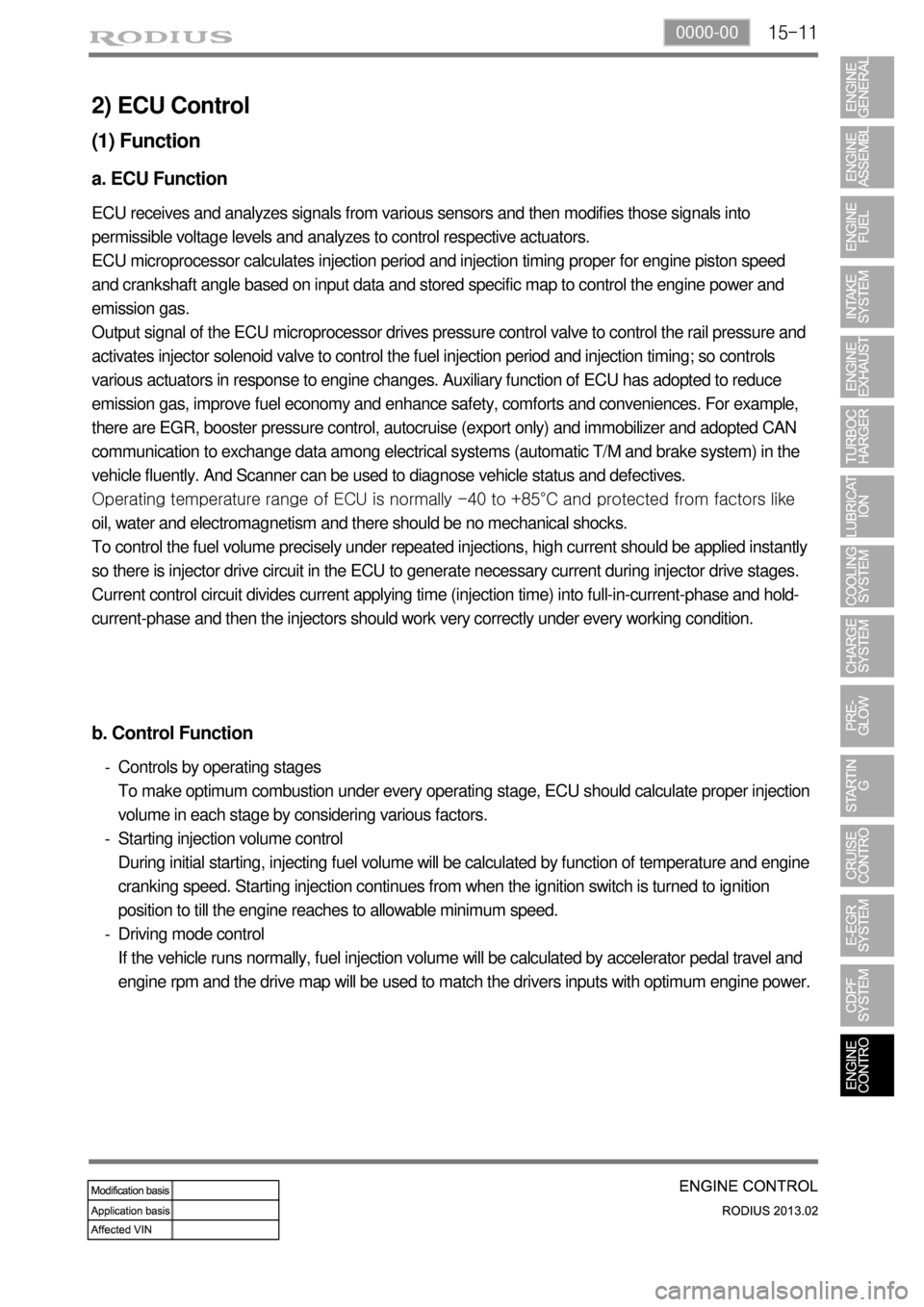
15-110000-00
2) ECU Control
(1) Function
a. ECU Function
ECU receives and analyzes signals from various sensors and then modifies those signals into
permissible voltage levels and analyzes to control respective actuators.
ECU microprocessor calculates injection period and injection timing proper for engine piston speed
and crankshaft angle based on input data and stored specific map to control the engine power and
emission gas.
Output signal of the ECU microprocessor drives pressure control valve to control the rail pressure and
activates injector solenoid valve to control the fuel injection period and injection timing; so controls
various actuators in response to engine changes. Auxiliary function of ECU has adopted to reduce
emission gas, improve fuel economy and enhance safety, comforts and conveniences. For example,
there are EGR, booster pressure control, autocruise (export only) and immobilizer and adopted CAN
communication to exchange data among electrical systems (automatic T/M and brake system) in the
vehicle fluently. And Scanner can be used to diagnose vehicle status and defectives.
Operating temperature range of ECU is normally -40 to +85°C and protected from factors like
oil, water and electromagnetism and there should be no mechanical shocks.
To control the fuel volume precisely under repeated injections, high current should be applied instantly
so there is injector drive circuit in the ECU to generate necessary current during injector drive stages.
Current control circuit divides current applying time (injection time) into full-in-current-phase and hold-
current-phase and then the injectors should work very correctly under every working condition.
b. Control Function
Controls by operating stages
To make optimum combustion under every operating stage, ECU should calculate proper injection
volume in each stage by considering various factors.
Starting injection volume control
During initial starting, injecting fuel volume will be calculated by function of temperature and engine
cranking speed. Starting injection continues from when the ignition switch is turned to ignition
position to till the engine reaches to allowable minimum speed.
Driving mode control
If the vehicle runs normally, fuel injection volume will be calculated by accelerator pedal travel and
engine rpm and the drive map will be used to match the drivers inputs with optimum engine power. -
-
-
Page 554 of 796
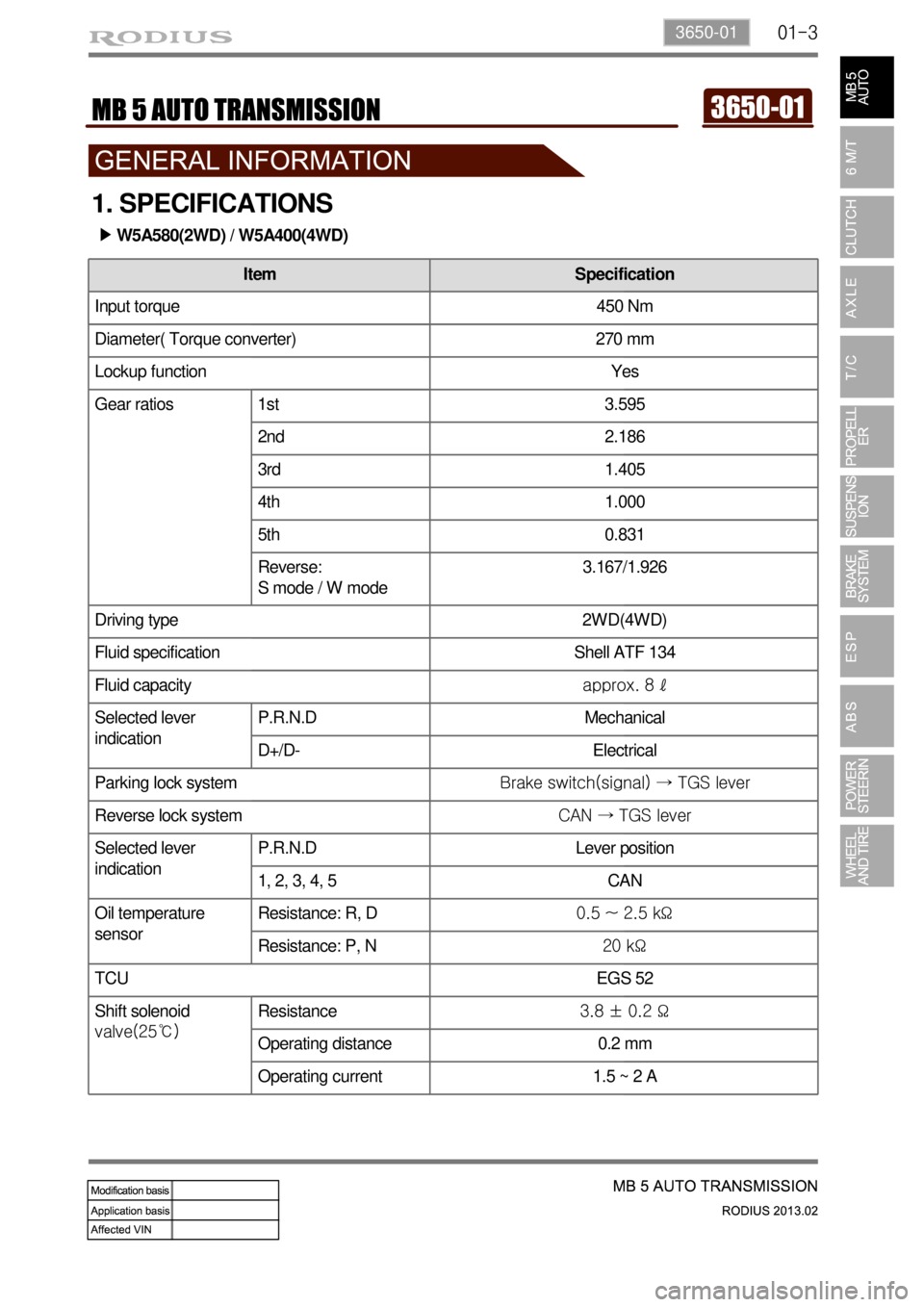
01-33650-01
Diameter( Torque converter) 270 mm
Lockup function Yes
Gear ratios 1st 3.595
2nd 2.186
3rd 1.405
4th 1.000
5th 0.831
Reverse:
S mode / W mode3.167/1.926
Driving type 2WD(4WD)
Fluid specification Shell ATF 134
Fluid capacityapprox. 8 ℓ
Selected lever
indicationP.R.N.D Mechanical
D+/D- Electrical
Parking lock systemBrake switch(signal) → TGS lever
Reverse lock systemCAN → TGS lever
Selected lever
indicationP.R.N.D Lever position
1, 2, 3, 4, 5 CAN
Oil temperature
sensorResistance: R, D0.5 ~ 2.5 kΩ
Resistance: P, N20 kΩ
TCU EGS 52
Shift solenoid
valve(25℃)Resistance3.8 ± 0.2 Ω
Operating distance 0.2 mm
Operating current 1.5 ~ 2 A
Item Specification
Input torque 450 Nm
1. SPECIFICATIONS
W5A580(2WD) / W5A400(4WD) ▶
Page 555 of 796
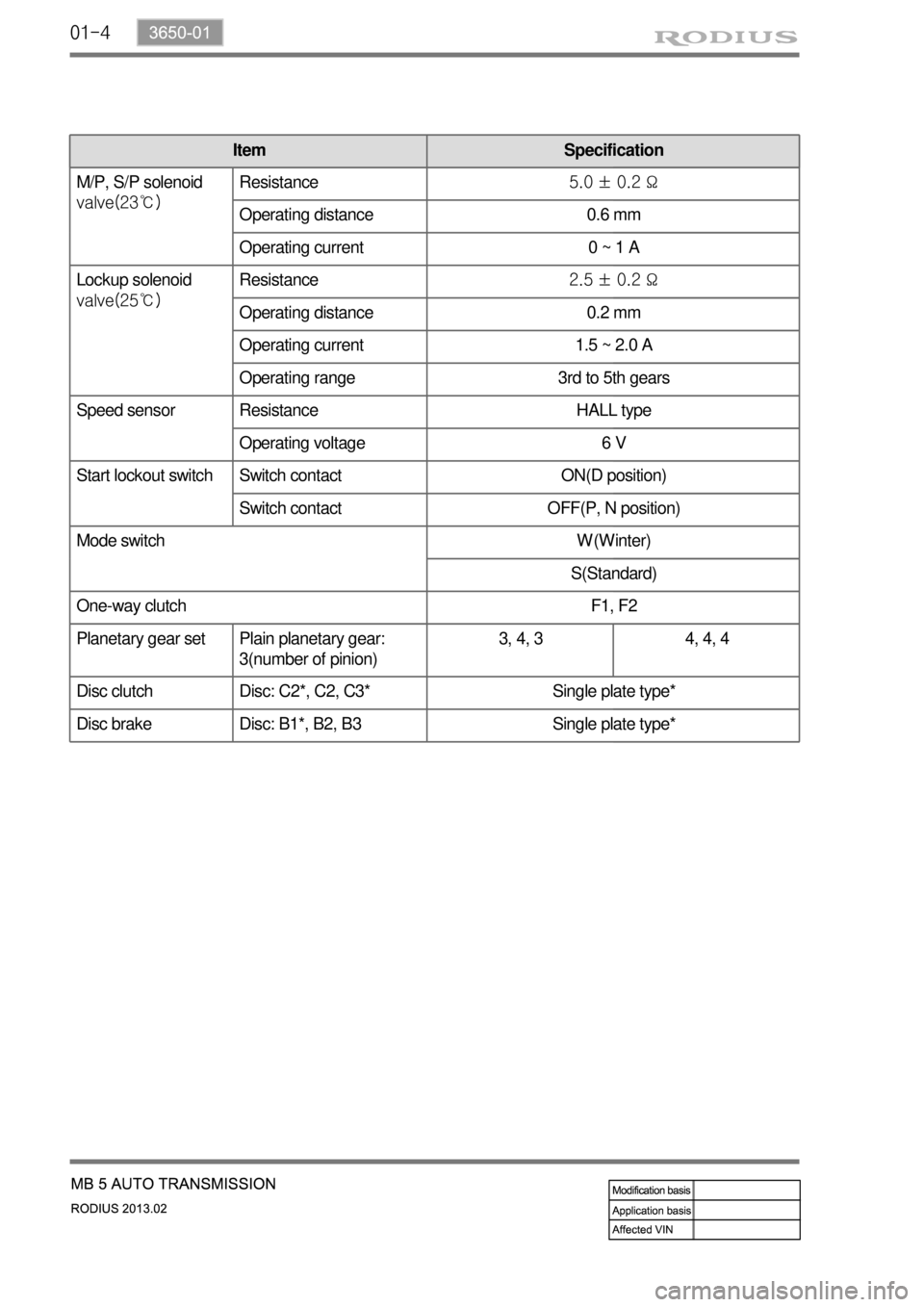
01-4
Item W5A330(300) W5A580(400)
M/P, S/P solenoid
valve(23℃)Resistance5.0 ± 0.2 Ω
Operating distance 0.6 mm
Operating current 0 ~ 1 A
Lockup solenoid
valve(25℃)Resistance2.5 ± 0.2 Ω
Operating distance 0.2 mm
Operating current 1.5 ~ 2.0 A
Operating range 3rd to 5th gears
Speed sensor Resistance HALL type
Operating voltage 6 V
Start lockout switch Switch contact ON(D position)
Switch contact OFF(P, N position)
Mode switch W(Winter)
S(Standard)
One-way clutch F1, F2
Planetary gear set Plain planetary gear:
3(number of pinion)3, 4, 3 4, 4, 4
Disc clutch Disc: C2*, C2, C3* Single plate type*
Disc brake Disc: B1*, B2, B3 Single plate type*
Item Specification
Page 559 of 796
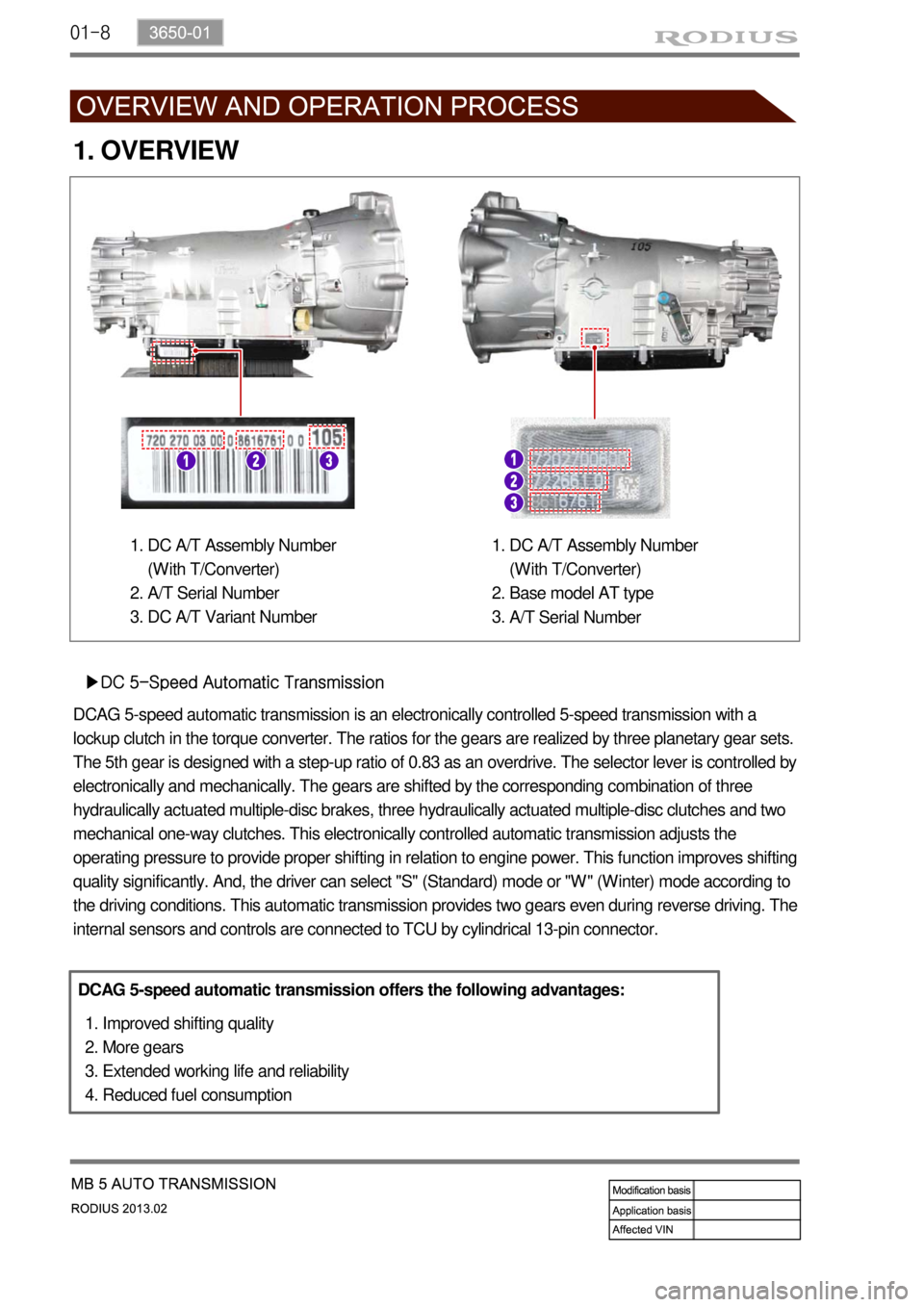
01-8
1. OVERVIEW
▶DC 5-Speed Automatic Transmission
DCAG 5-speed automatic transmission is an electronically controlled 5-speed transmission with a
lockup clutch in the torque converter. The ratios for the gears are realized by three planetary gear sets.
The 5th gear is designed with a step-up ratio of 0.83 as an overdrive. The selector lever is controlled by
electronically and mechanically. The gears are shifted by the corresponding combination of three
hydraulically actuated multiple-disc brakes, three hydraulically actuated multiple-disc clutches and two
mechanical one-way clutches. This electronically controlled automatic transmission adjusts the
operating pressure to provide proper shifting in relation to engine power. This function improves shifting
quality significantly. And, the driver can select "S" (Standard) mode or "W" (Winter) mode according to
the driving conditions. This automatic transmission provides two gears even during reverse driving. The
internal sensors and controls are connected to TCU by cylindrical 13-pin connector.
DCAG 5-speed automatic transmission offers the following advantages:
Improved shifting quality
More gears
Extended working life and reliability
Reduced fuel consumption 1.
2.
3.
4.
DC A/T Assembly Number
(With T/Converter)
A/T Serial Number
DC A/T Variant Number 1.
2.
3.DC A/T Assembly Number
(With T/Converter)
Base model AT type
A/T Serial Number 1.
2.
3.
Page 630 of 796
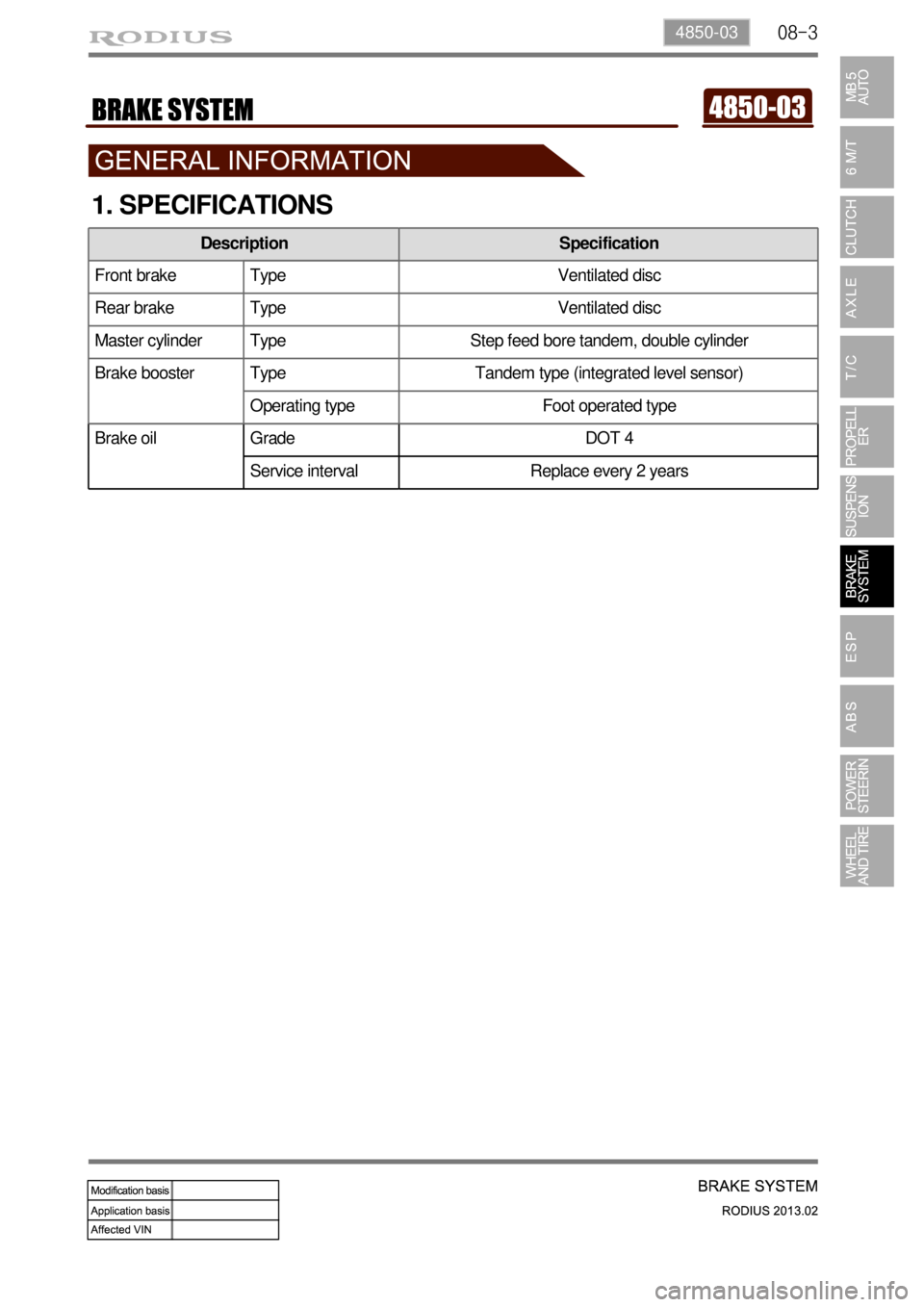
08-34850-03
Brake oil Grade DOT 4
Service interval Replace every 2 years
1. SPECIFICATIONS
Description Specification
Front brake Type Ventilated disc
Rear brake Type Ventilated disc
Master cylinder Type Step feed bore tandem, double cylinder
Brake booster Type Tandem type (integrated level sensor)
Operating type Foot operated type
Page 651 of 796
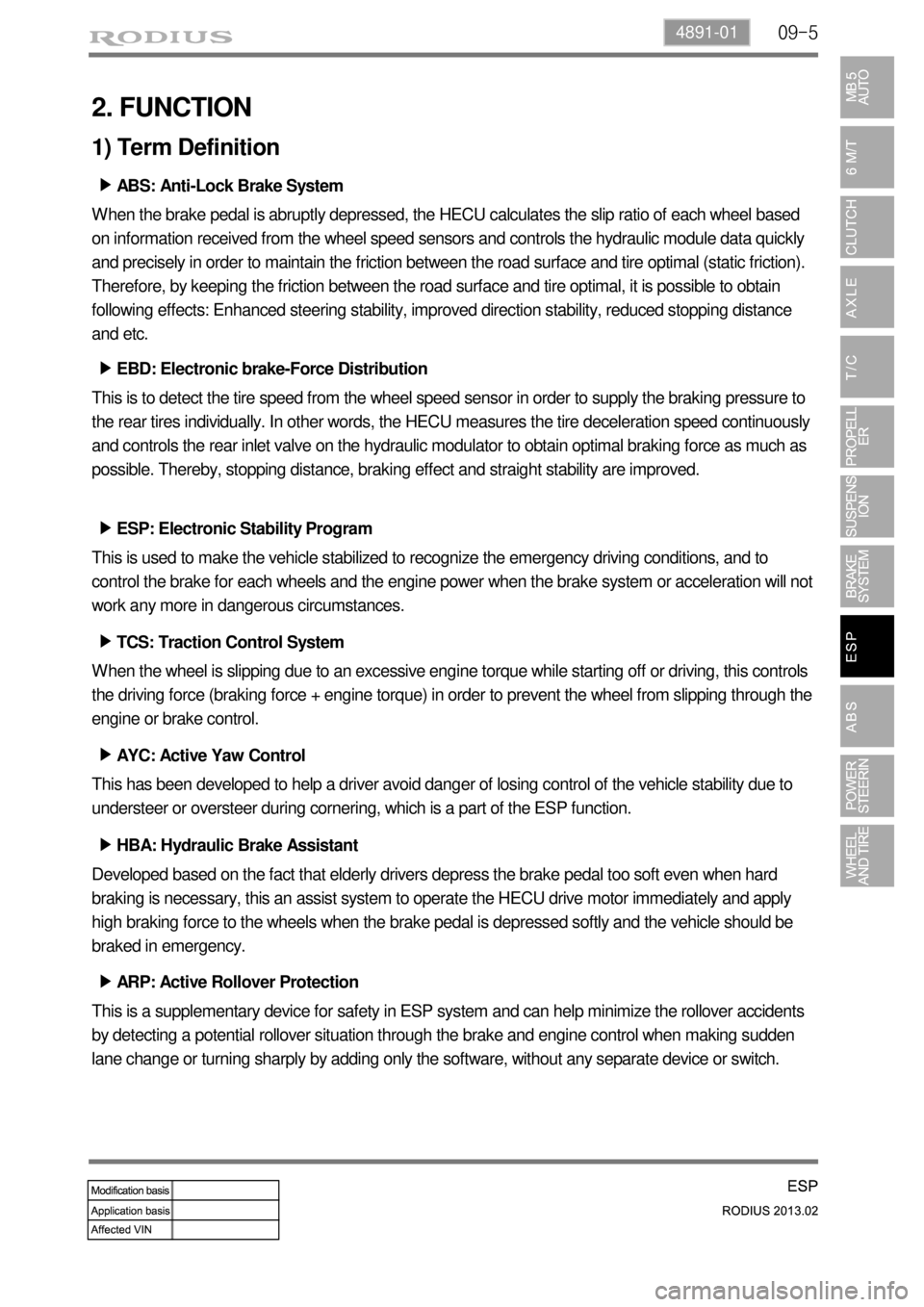
09-54891-01
2. FUNCTION
1) Term Definition
ABS: Anti-Lock Brake System ▶
When the brake pedal is abruptly depressed, the HECU calculates the slip ratio of each wheel based
on information received from the wheel speed sensors and controls the hydraulic module data quickly
and precisely in order to maintain the friction between the road surface and tire optimal (static friction).
Therefore, by keeping the friction between the road surface and tire optimal, it is possible to obtain
following effects: Enhanced steering stability, improved direction stability, reduced stopping distance
and etc.
EBD: Electronic brake-Force Distribution ▶
This is to detect the tire speed from the wheel speed sensor in order to supply the braking pressure to
the rear tires individually. In other words, the HECU measures the tire deceleration speed continuously
and controls the rear inlet valve on the hydraulic modulator to obtain optimal braking force as much as
possible. Thereby, stopping distance, braking effect and straight stability are improved.
ESP: Electronic Stability Program ▶
This is used to make the vehicle stabilized to recognize the emergency driving conditions, and to
control the brake for each wheels and the engine power when the brake system or acceleration will not
work any more in dangerous circumstances.
TCS: Traction Control System ▶
When the wheel is slipping due to an excessive engine torque while starting off or driving, this controls
the driving force (braking force + engine torque) in order to prevent the wheel from slipping through the
engine or brake control.
AYC: Active Yaw Control ▶
This has been developed to help a driver avoid danger of losing control of the vehicle stability due to
understeer or oversteer during cornering, which is a part of the ESP function.
HBA: Hydraulic Brake Assistant ▶
Developed based on the fact that elderly drivers depress the brake pedal too soft even when hard
braking is necessary, this an assist system to operate the HECU drive motor immediately and apply
high braking force to the wheels when the brake pedal is depressed softly and the vehicle should be
braked in emergency.
ARP: Active Rollover Protection ▶
This is a supplementary device for safety in ESP system and can help minimize the rollover accidents
by detecting a potential rollover situation through the brake and engine control when making sudden
lane change or turning sharply by adding only the software, without any separate device or switch.
Page 655 of 796
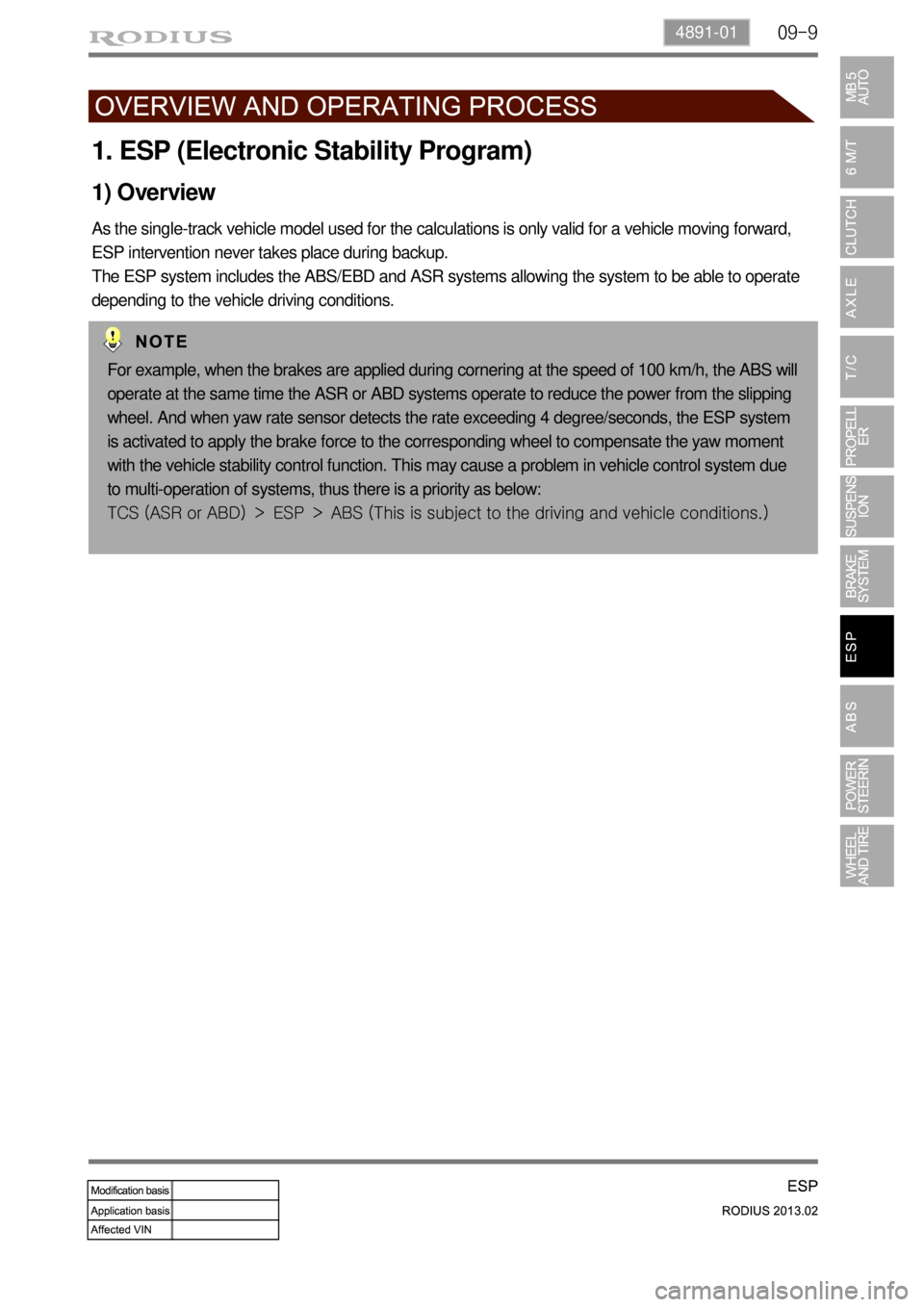
09-94891-01
1. ESP (Electronic Stability Program)
As the single-track vehicle model used for the calculations is only valid for a vehicle moving forward,
ESP intervention never takes place during backup.
The ESP system includes the ABS/EBD and ASR systems allowing the system to be able to operate
depending to the vehicle driving conditions.
1) Overview
For example, when the brakes are applied during cornering at the speed of 100 km/h, the ABS will
operate at the same time the ASR or ABD systems operate to reduce the power from the slipping
wheel. And when yaw rate sensor detects the rate exceeding 4 degree/seconds, the ESP system
is activated to apply the brake force to the corresponding wheel to compensate the yaw moment
with the vehicle stability control function. This may cause a problem in vehicle control system due
to multi-operation of systems, thus there is a priority as below:
TCS (ASR or ABD) > ESP > ABS (This is subject to the driving and vehicle conditions.)