Ac controller SUZUKI GRAND VITARA 2003 2.G Service User Guide
[x] Cancel search | Manufacturer: SUZUKI, Model Year: 2003, Model line: GRAND VITARA, Model: SUZUKI GRAND VITARA 2003 2.GPages: 801, PDF Size: 12.15 MB
Page 89 of 801
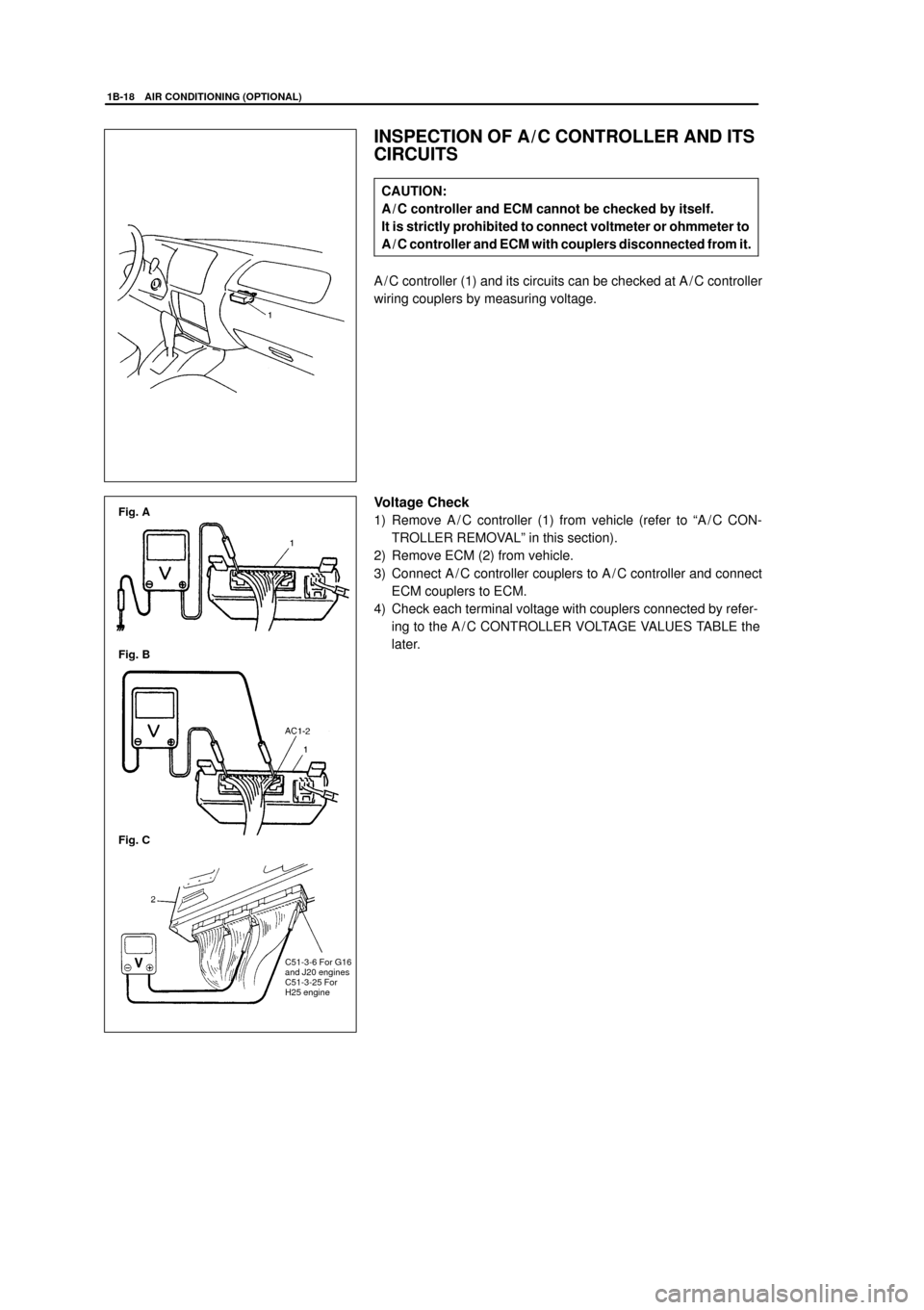
YH4
GRAND
VITARA
Fig. A
Fig. B
Fig. C
C51-3-6 For G16
and J20 engines
C51-3-25 For
H25 engine
1B-18 AIR CONDITIONING (OPTIONAL)
INSPECTION OF A / C CONTROLLER AND ITS
CIRCUITS
CAUTION:
A / C controller and ECM cannot be checked by itself.
It is strictly prohibited to connect voltmeter or ohmmeter to
A / C controller and ECM with couplers disconnected from it.
A / C controller (1) and its circuits can be checked at A / C controller
wiring couplers by measuring voltage.
Voltage Check
1) Remove A / C controller (1) from vehicle (refer to ªA / C CON-
TROLLER REMOVALº in this section).
2) Remove ECM (2) from vehicle.
3) Connect A / C controller couplers to A / C controller and connect
ECM couplers to ECM.
4) Check each terminal voltage with couplers connected by refer-
ing to the A / C CONTROLLER VOLTAGE VALUES TABLE the
later.
Page 90 of 801
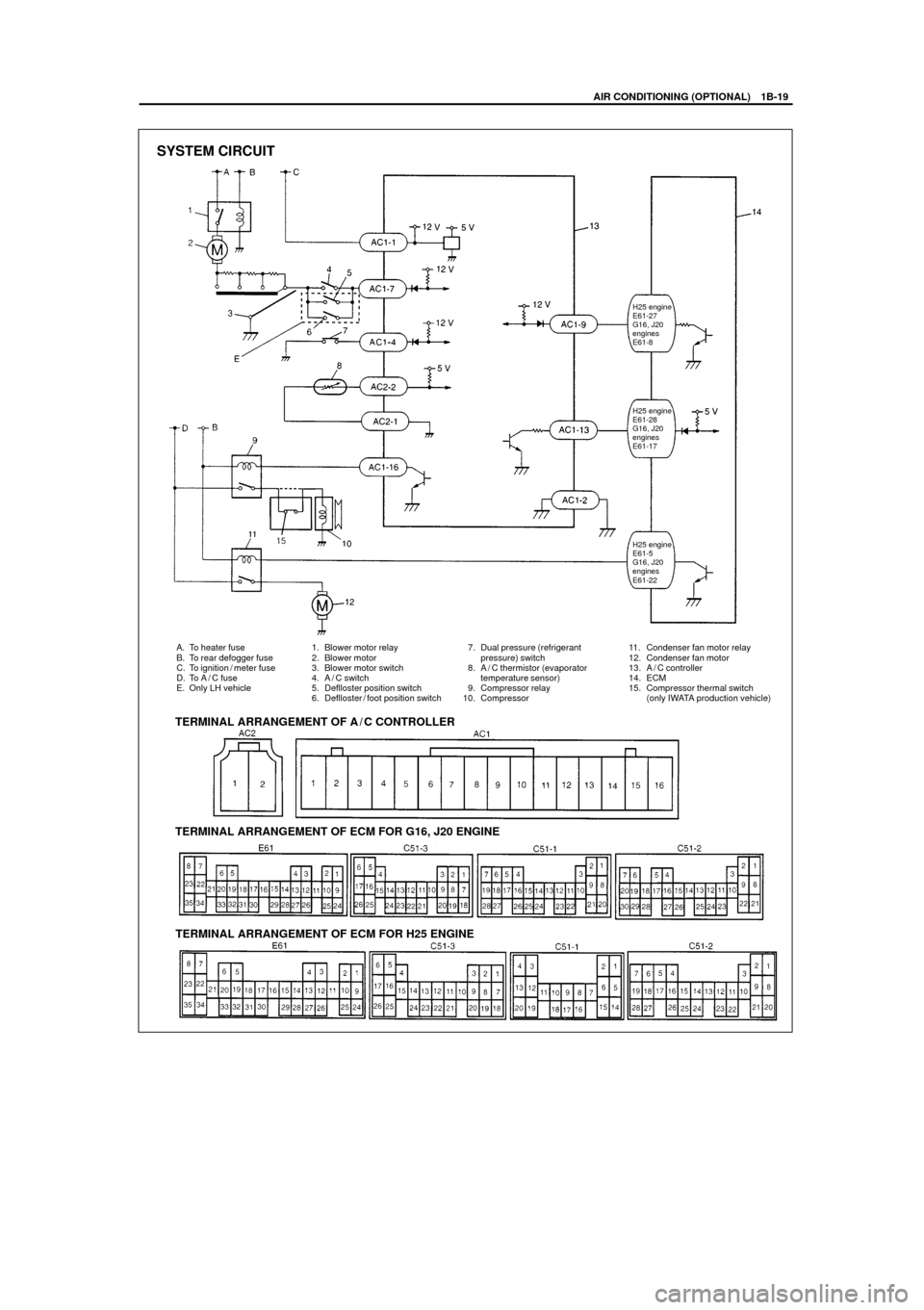
YH4
GRAND
VITARA
SYSTEM CIRCUIT
A. To heater fuse
B. To rear defogger fuse
C. To ignition / meter fuse
D. To A / C fuse
E. Only LH vehicle1. Blower motor relay
2. Blower motor
3. Blower motor switch
4. A / C switch
5. Deflloster position switch
6. Deflloster / foot position switch7. Dual pressure (refrigerant
pressure) switch
8. A / C thermistor (evaporator
temperature sensor)
9. Compressor relay
10. Compressor11. Condenser fan motor relay
12. Condenser fan motor
13. A / C controller
14. ECM
15. Compressor thermal switch
(only IWATA production vehicle)
TERMINAL ARRANGEMENT OF A / C CONTROLLER
TERMINAL ARRANGEMENT OF ECM FOR G16, J20 ENGINE
TERMINAL ARRANGEMENT OF ECM FOR H25 ENGINE
H25 engine
E61-27
G16, J20
engines
E61-8
H25 engine
E61-28
G16, J20
engines
E61-17
1919
19H25 engine
E61-5
G16, J20
engines
E61-22
AIR CONDITIONING (OPTIONAL) 1B-19
Page 91 of 801
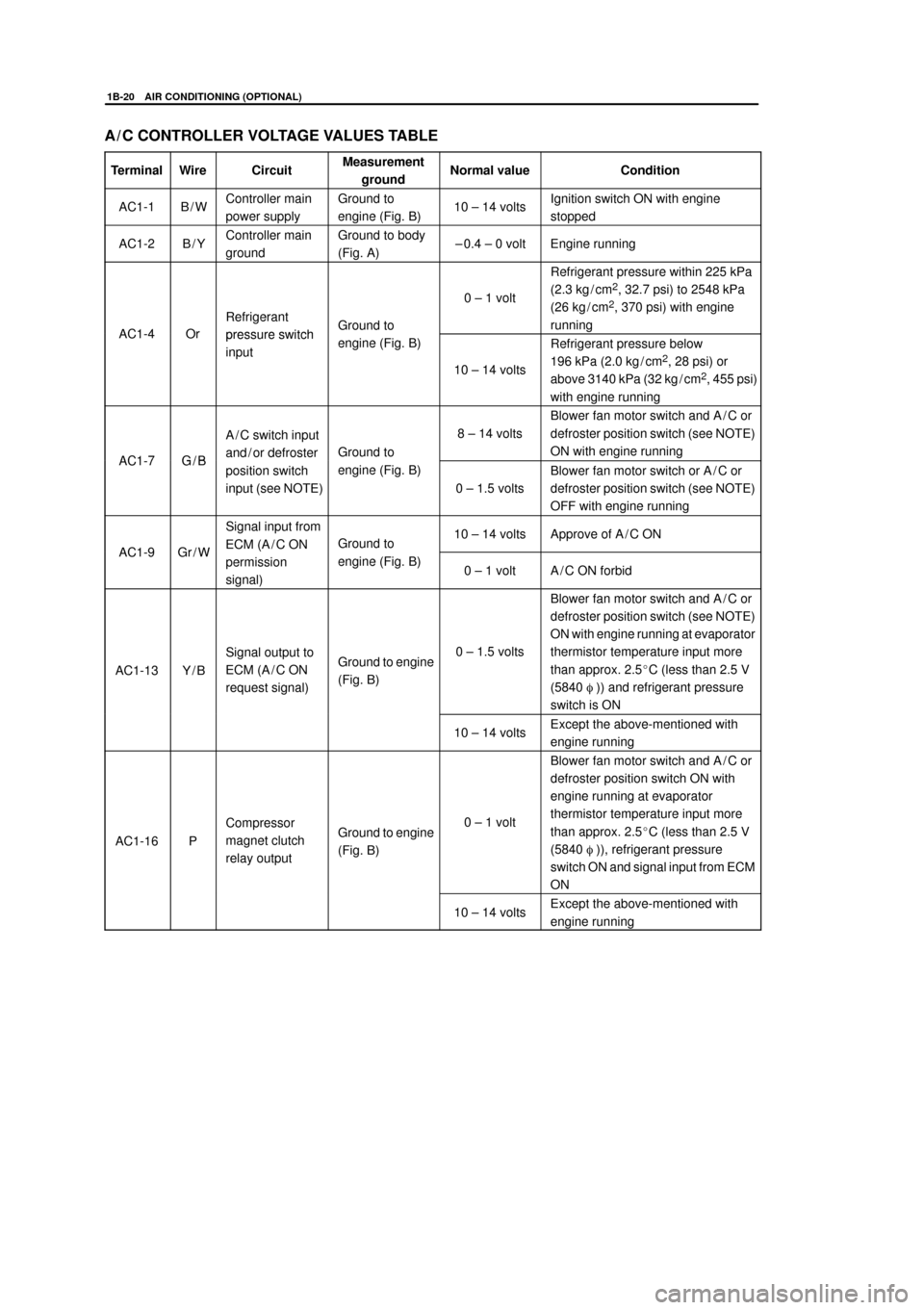
YH4
GRAND
VITARA
1B-20 AIR CONDITIONING (OPTIONAL)
A / C CONTROLLER VOLTAGE VALUES TABLE
TerminalWireCircuitMeasurement
groundNormal valueCondition
AC1-1B/WController main
power supplyGround to
engine (Fig. B)10 ± 14 voltsIgnition switch ON with engine
stopped
AC1-2B/YController main
groundGround to body
(Fig. A)± 0.4 ± 0 voltEngine running
AC1 4Or
Refrigerant
p
ressure switchGround to
0 ± 1 volt
Refrigerant pressure within 225 kPa
(2.3 kg / cm
2, 32.7 psi) to 2548 kPa
(26 kg / cm
2, 370 psi) with engine
running
AC1-4Orpressure switch
inputengine (Fig. B)
10 ± 14 volts
Refrigerant pressure below
196 kPa (2.0 kg / cm
2, 28 psi) or
above 3140 kPa (32 kg / cm
2, 455 psi)
with engine running
AC1 7G/B
A / C switch input
and / or defroster
Ground to
8 ± 14 volts
Blower fan motor switch and A / C or
defroster position switch (see NOTE)
ON with engine running
AC1-7G/Bposition switch
input (see NOTE)engine (Fig. B)
0 ± 1.5 volts
Blower fan motor switch or A / C or
defroster position switch (see NOTE)
OFF with engine running
AC1 9Gr/W
Signal input from
ECM (A / C ON
Ground to10 ± 14 voltsApprove of A / C ON
AC1-9Gr/W(
permission
signal)engine (Fig. B)0 ± 1 voltA / C ON forbid
AC1-13Y/B
Signal output to
ECM (A / C ON
request signal)Ground to engine
(Fig. B)0 ± 1.5 volts
Blower fan motor switch and A / C or
defroster position switch (see NOTE)
ON with engine running at evaporator
thermistor temperature input more
than approx. 2.5C (less than 2.5 V
(5840 )) and refrigerant pressure
switch is ON
10 ± 14 voltsExcept the above-mentioned with
engine running
AC1-16P
Compressor
magnet clutch
relay outputGround to engine
(Fig. B)0 ± 1 volt
Blower fan motor switch and A / C or
defroster position switch ON with
engine running at evaporator
thermistor temperature input more
than approx. 2.5C (less than 2.5 V
(5840 )), refrigerant pressure
switch ON and signal input from ECM
ON
10 ± 14 voltsExcept the above-mentioned with
engine running
Page 92 of 801
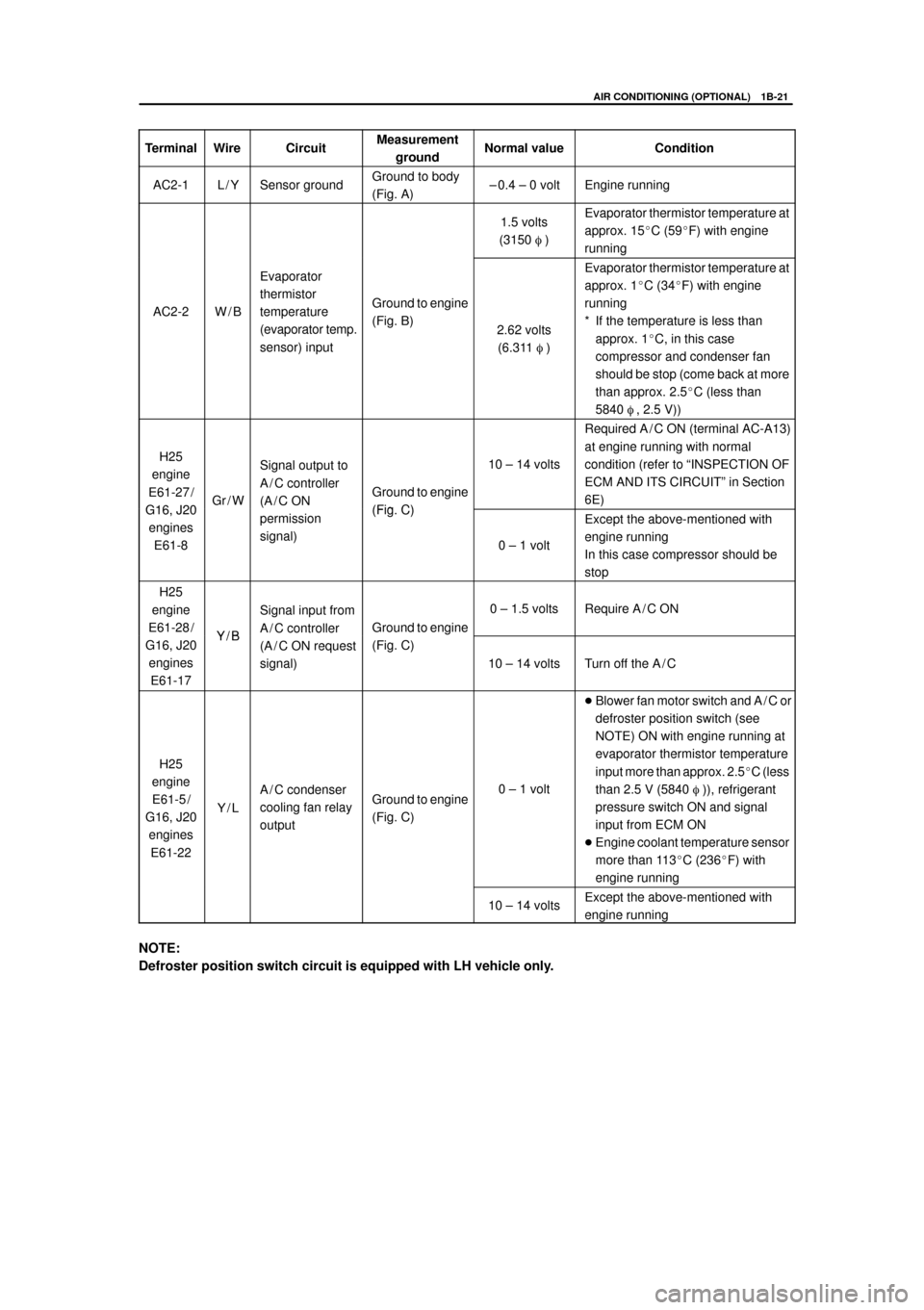
YH4
GRAND
VITARA
AIR CONDITIONING (OPTIONAL) 1B-21
TerminalWireCircuitMeasurement
groundNormal valueCondition
AC2-1L/YSensor groundGround to body
(Fig. A)± 0.4 ± 0 voltEngine running
1.5 volts
(3150 )Evaporator thermistor temperature at
approx. 15C (59F) with engine
running
AC2-2W/B
Evaporator
thermistor
temperature
(evaporator temp.
sensor) input
Ground to engine
(Fig. B)
2.62 volts
(6.311 )
Evaporator thermistor temperature at
approx. 1C (34F) with engine
running
* If the temperature is less than
approx. 1C, in this case
compressor and condenser fan
should be stop (come back at more
than approx. 2.5C (less than
5840 , 2.5 V))
H25
engine
E61-27 /
G16 J20Gr/W
Signal output to
A / C controller
(A / C ON
Ground to engine
(Fig C)
10 ± 14 volts
Required A / C ON (terminal AC-A13)
at engine running with normal
condition (refer to ªINSPECTION OF
ECM AND ITS CIRCUITº in Section
6E)
G16, J20
engines
E61-8
(
permission
signal)(Fig. C)
0 ± 1 volt
Except the above-mentioned with
engine running
In this case compressor should be
stop
H25
engine
E61-28 /
Y/B
Signal input from
A / C controller
Ground to engine
0 ± 1.5 voltsRequire A / C ON
G16, J20
engines
E61-17Y/B(A / C ON request
signal)
g
(Fig. C)
10 ± 14 voltsTurn off the A / C
H25
engine
E61-5 /
G16, J20
engines
E61-22
Y/L
A / C condenser
cooling fan relay
outputGround to engine
(Fig. C)0 ± 1 volt
Blower fan motor switch and A / C or
defroster position switch (see
NOTE) ON with engine running at
evaporator thermistor temperature
input more than approx. 2.5C (less
than 2.5 V (5840 )), refrigerant
pressure switch ON and signal
input from ECM ON
Engine coolant temperature sensor
more than 113C (236F) with
engine running
10 ± 14 voltsExcept the above-mentioned with
engine running
NOTE:
Defroster position switch circuit is equipped with LH vehicle only.
Page 117 of 801
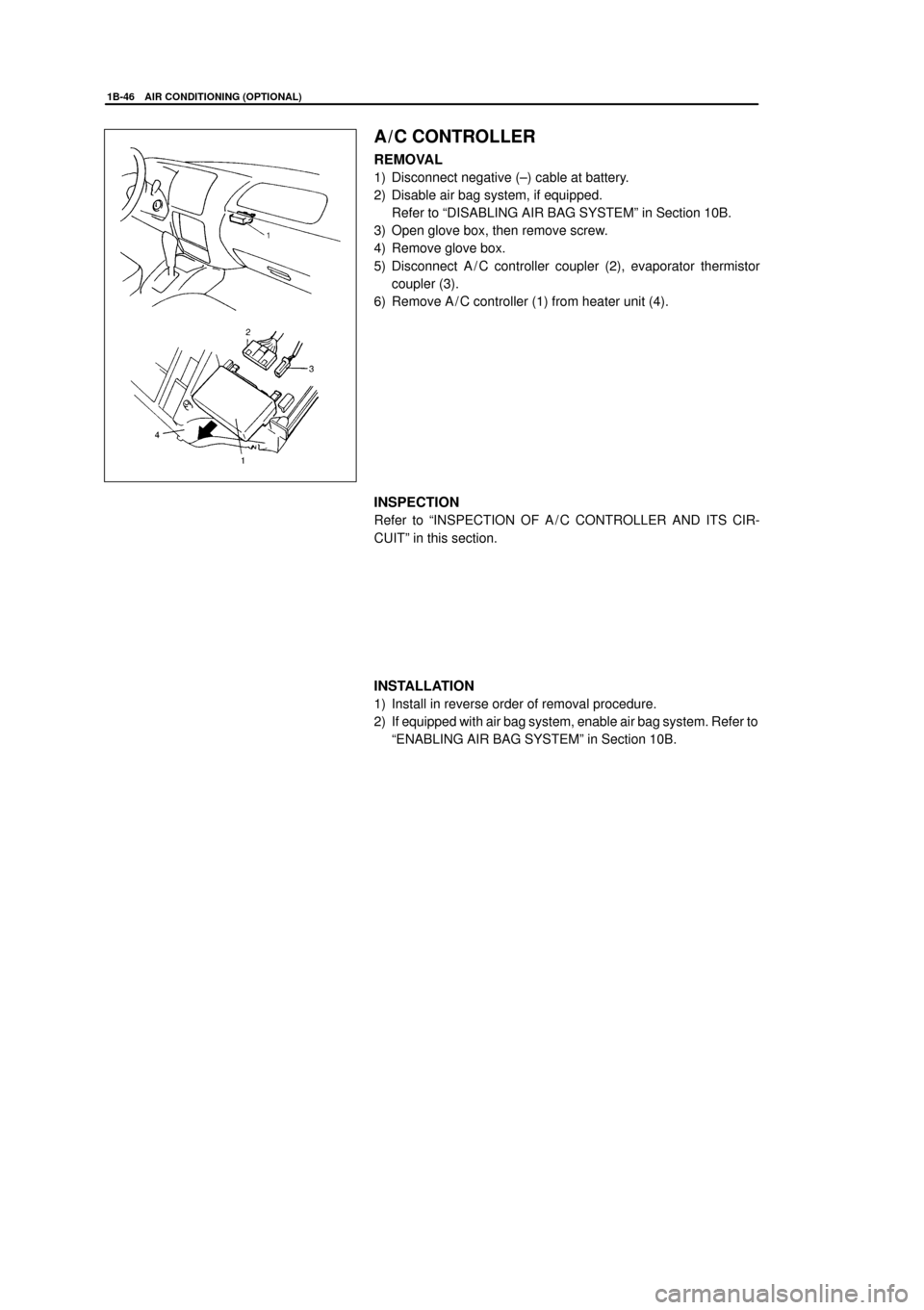
YH4
GRAND
VITARA
1B-46 AIR CONDITIONING (OPTIONAL)
A / C CONTROLLER
REMOVAL
1) Disconnect negative (±) cable at battery.
2) Disable air bag system, if equipped.
Refer to ªDISABLING AIR BAG SYSTEMº in Section 10B.
3) Open glove box, then remove screw.
4) Remove glove box.
5) Disconnect A / C controller coupler (2), evaporator thermistor
coupler (3).
6) Remove A / C controller (1) from heater unit (4).
INSPECTION
Refer to ªINSPECTION OF A / C CONTROLLER AND ITS CIR-
CUITº in this section.
INSTALLATION
1) Install in reverse order of removal procedure.
2) If equipped with air bag system, enable air bag system. Refer to
ªENABLING AIR BAG SYSTEMº in Section 10B.
Page 356 of 801
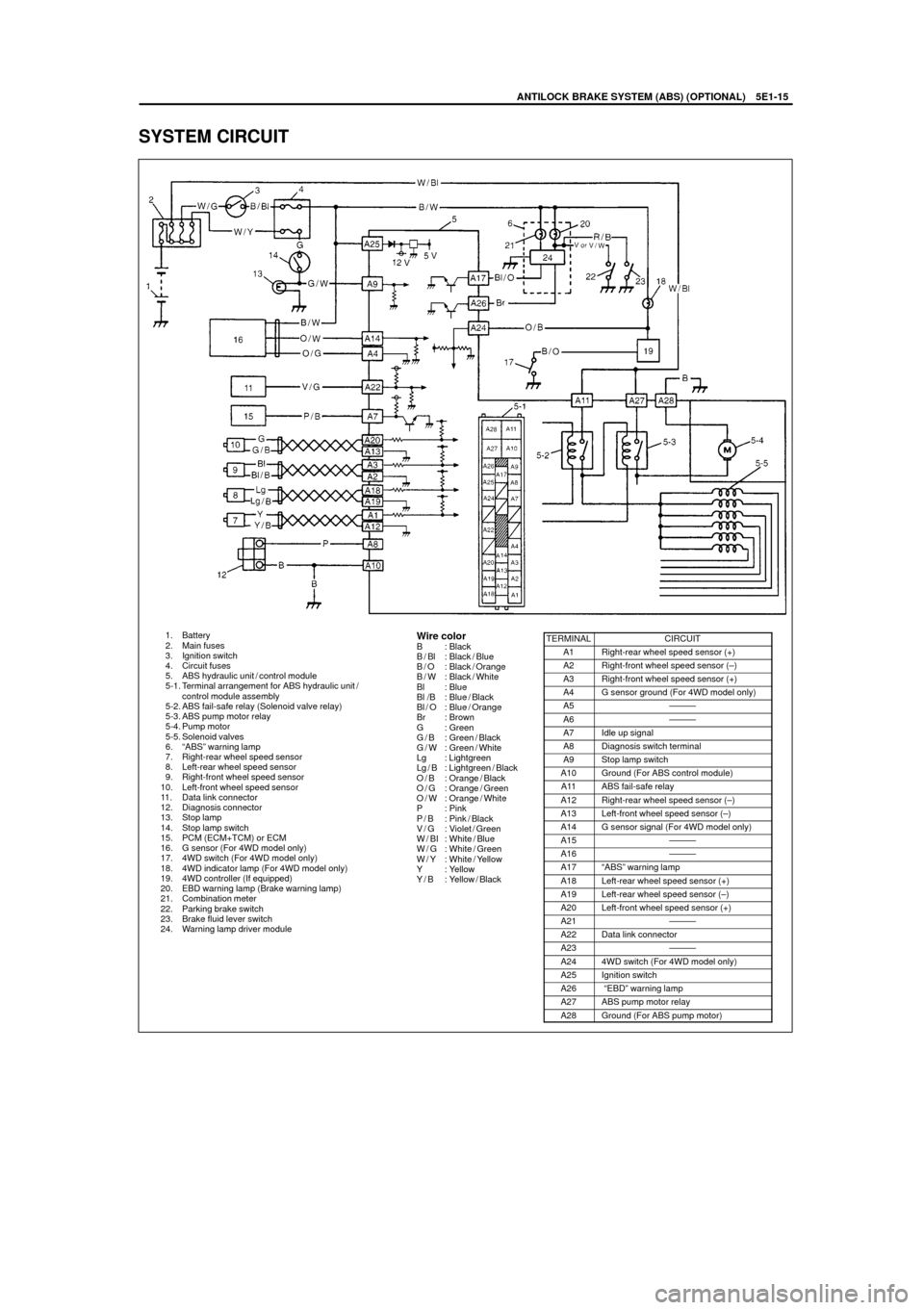
YH4
GRAND
VITARA
ANTILOCK BRAKE SYSTEM (ABS) (OPTIONAL) 5E1-15
1. Battery
2. Main fuses
3. Ignition switch
4. Circuit fuses
5. ABS hydraulic unit / control module
5-1. Terminal arrangement for ABS hydraulic unit /
control module assembly
5-2. ABS fail-safe relay (Solenoid valve relay)
5-3. ABS pump motor relay
5-4. Pump motor
5-5. Solenoid valves
6. ªABSº warning lamp
7. Right-rear wheel speed sensor
8. Left-rear wheel speed sensor
9. Right-front wheel speed sensor
10. Left-front wheel speed sensor
11. Data link connector
12. Diagnosis connector
13. Stop lamp
14. Stop lamp switch
15. PCM (ECM+TCM) or ECM
16. G sensor (For 4WD model only)
17. 4WD switch (For 4WD model only)
18. 4WD indicator lamp (For 4WD model only)
19. 4WD controller (If equipped)
20. EBD warning lamp (Brake warning lamp)
21. Combination meter
22. Parking brake switch
23. Brake fluid lever switch
24. Warning lamp driver moduleWire colorB : Black
B / Bl : Black / Blue
B / O : Black / Orange
B / W : Black / White
Bl : Blue
Bl /B : Blue / Black
Bl / O : Blue / Orange
Br : Brown
G : Green
G / B : Green / Black
G / W : Green / White
Lg : Lightgreen
Lg / B : Lightgreen / Black
O / B : Orange / Black
O / G : Orange / Green
O / W : Orange / White
P : Pink
P / B : Pink / Black
V / G : Violet / Green
W / BI : White / Blue
W / G : White / Green
W / Y : White / Yellow
Y : Yellow
Y / B : Yellow / Black
SYSTEM CIRCUIT
TERMINALCIRCUIT
A1Right-rear wheel speed sensor (+)
A2Right-front wheel speed sensor (±)
A3Right-front wheel speed sensor (+)
A4G sensor ground (For 4WD model only)
A5ÐÐÐ
A6ÐÐÐ
A7Idle up signal
A8Diagnosis switch terminal
A9Stop lamp switch
A10Ground (For ABS control module)
A11ABS fail-safe relay
A12Right-rear wheel speed sensor (±)
A13Left-front wheel speed sensor (±)
A14G sensor signal (For 4WD model only)
A15ÐÐÐ
A16ÐÐÐ
A17ªABSº warning lamp
A18Left-rear wheel speed sensor (+)
A19Left-rear wheel speed sensor (±)
A20Left-front wheel speed sensor (+)
A21ÐÐÐ
A22Data link connector
A23ÐÐÐ
A244WD switch (For 4WD model only)
A25Ignition switch
A26ªEBDº warning lamp
A27ABS pump motor relay
A28Ground (For ABS pump motor)
Page 504 of 801
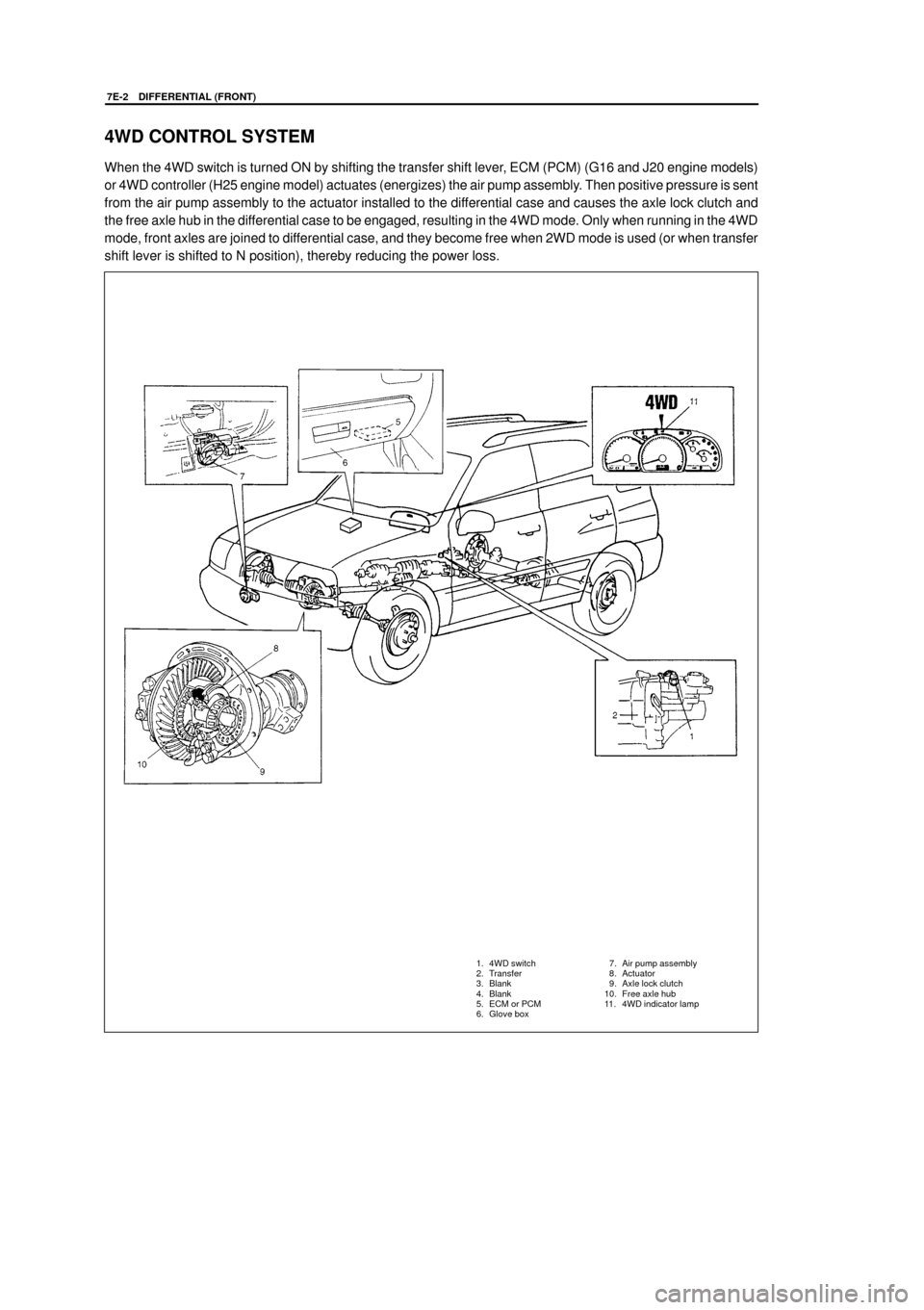
YH4
GRAND
VITARA
1. 4WD switch
2. Transfer
3. Blank
4. Blank
5. ECM or PCM
6. Glove box7. Air pump assembly
8. Actuator
9. Axle lock clutch
10. Free axle hub
11. 4WD indicator lamp
7E-2 DIFFERENTIAL (FRONT)
4WD CONTROL SYSTEM
When the 4WD switch is turned ON by shifting the transfer shift lever, ECM (PCM) (G16 and J20 engine models)
or 4WD controller (H25 engine model) actuates (energizes) the air pump assembly. Then positive pressure is sent
from the air pump assembly to the actuator installed to the differential case and causes the axle lock clutch and
the free axle hub in the differential case to be engaged, resulting in the 4WD mode. Only when running in the 4WD
mode, front axles are joined to differential case, and they become free when 2WD mode is used (or when transfer
shift lever is shifted to N position), thereby reducing the power loss.
Page 559 of 801
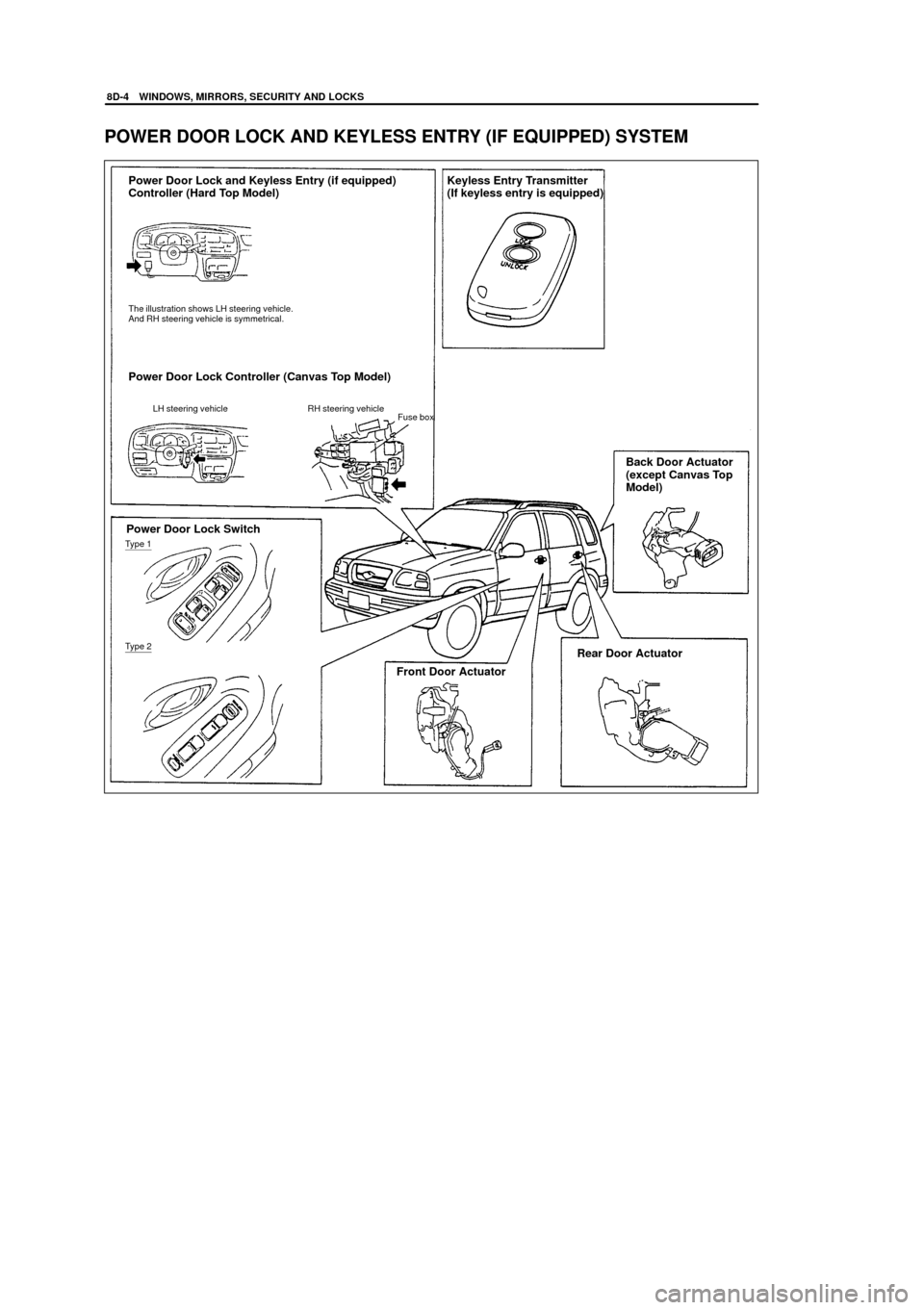
YH4
GRAND
VITARA
8D-4 WINDOWS, MIRRORS, SECURITY AND LOCKS
LH steering vehicleRH steering vehicle
Type 1
Type 2
Power Door Lock Controller (Canvas Top Model)
Power Door Lock SwitchBack Door Actuator
(except Canvas Top
Model)
Rear Door Actuator
Front Door Actuator
Fuse box
Power Door Lock and Keyless Entry (if equipped)
Controller (Hard Top Model)Keyless Entry Transmitter
(If keyless entry is equipped)
The illustration shows LH steering vehicle.
And RH steering vehicle is symmetrical.
POWER DOOR LOCK AND KEYLESS ENTRY (IF EQUIPPED) SYSTEM
Page 561 of 801
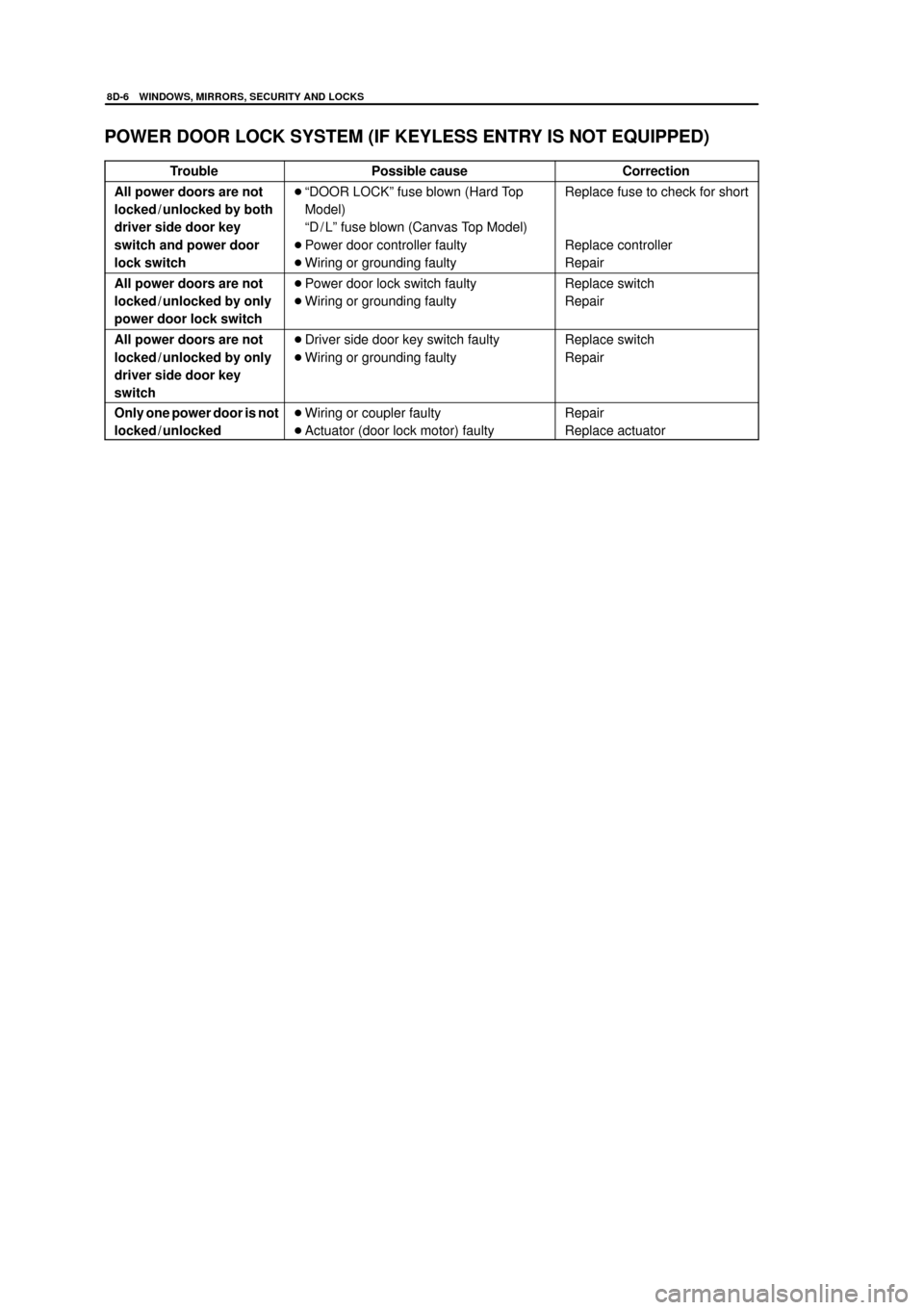
YH4
GRAND
VITARA
8D-6 WINDOWS, MIRRORS, SECURITY AND LOCKS
POWER DOOR LOCK SYSTEM (IF KEYLESS ENTRY IS NOT EQUIPPED)
TroublePossible causeCorrection
All power doors are not
locked / unlocked by both
driver side door key
switch and power door
lock switchªDOOR LOCKº fuse blown (Hard Top
Model)
ªD / Lº fuse blown (Canvas Top Model)
Power door controller faulty
Wiring or grounding faultyReplace fuse to check for short
Replace controller
Repair
All power doors are not
locked / unlocked by only
power door lock switchPower door lock switch faulty
Wiring or grounding faultyReplace switch
Repair
All power doors are not
locked / unlocked by only
driver side door key
switchDriver side door key switch faulty
Wiring or grounding faultyReplace switch
Repair
Only one power door is not
locked / unlockedWiring or coupler faulty
Actuator (door lock motor) faultyRepair
Replace actuator
Page 575 of 801
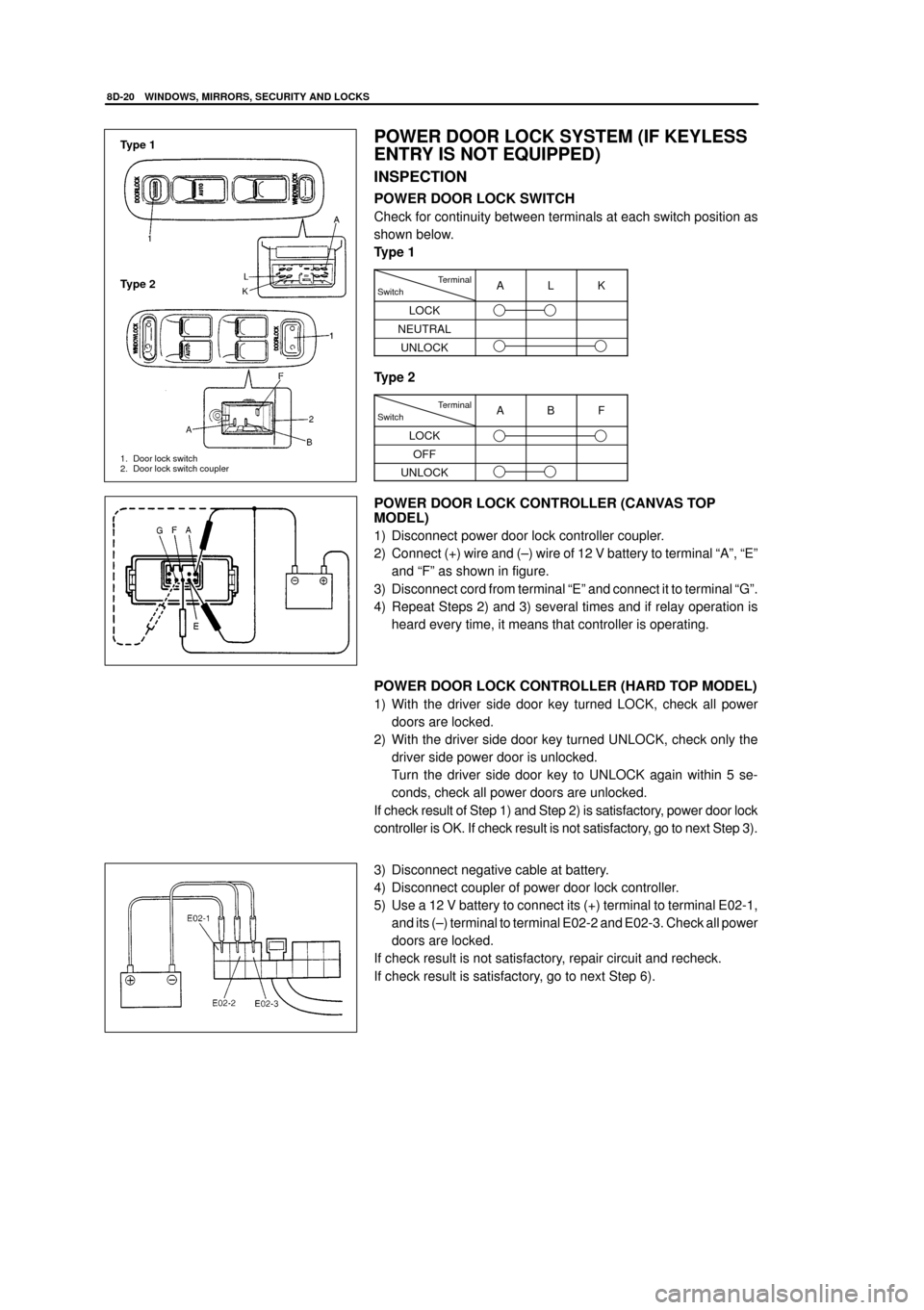
YH4
GRAND
VITARA
Terminal
Switch
Type 1
Type 2
1. Door lock switch
2. Door lock switch coupler
Terminal
Switch
8D-20 WINDOWS, MIRRORS, SECURITY AND LOCKS
POWER DOOR LOCK SYSTEM (IF KEYLESS
ENTRY IS NOT EQUIPPED)
INSPECTION
POWER DOOR LOCK SWITCH
Check for continuity between terminals at each switch position as
shown below.
Type 1
ALK
LOCK
NEUTRAL
UNLOCK
Type 2
ABF
LOCK
OFF
UNLOCK
POWER DOOR LOCK CONTROLLER (CANVAS TOP
MODEL)
1) Disconnect power door lock controller coupler.
2) Connect (+) wire and (±) wire of 12 V battery to terminal ªAº, ªEº
and ªFº as shown in figure.
3) Disconnect cord from terminal ªEº and connect it to terminal ªGº.
4) Repeat Steps 2) and 3) several times and if relay operation is
heard every time, it means that controller is operating.
POWER DOOR LOCK CONTROLLER (HARD TOP MODEL)
1) With the driver side door key turned LOCK, check all power
doors are locked.
2) With the driver side door key turned UNLOCK, check only the
driver side power door is unlocked.
Turn the driver side door key to UNLOCK again within 5 se-
conds, check all power doors are unlocked.
If check result of Step 1) and Step 2) is satisfactory, power door lock
controller is OK. If check result is not satisfactory, go to next Step 3).
3) Disconnect negative cable at battery.
4) Disconnect coupler of power door lock controller.
5) Use a 12 V battery to connect its (+) terminal to terminal E02-1,
and its (±) terminal to terminal E02-2 and E02-3. Check all power
doors are locked.
If check result is not satisfactory, repair circuit and recheck.
If check result is satisfactory, go to next Step 6).