Valve SUZUKI SWIFT 2000 1.G SF310 Service Workshop Manual
[x] Cancel search | Manufacturer: SUZUKI, Model Year: 2000, Model line: SWIFT, Model: SUZUKI SWIFT 2000 1.GPages: 557, PDF Size: 14.35 MB
Page 425 of 557
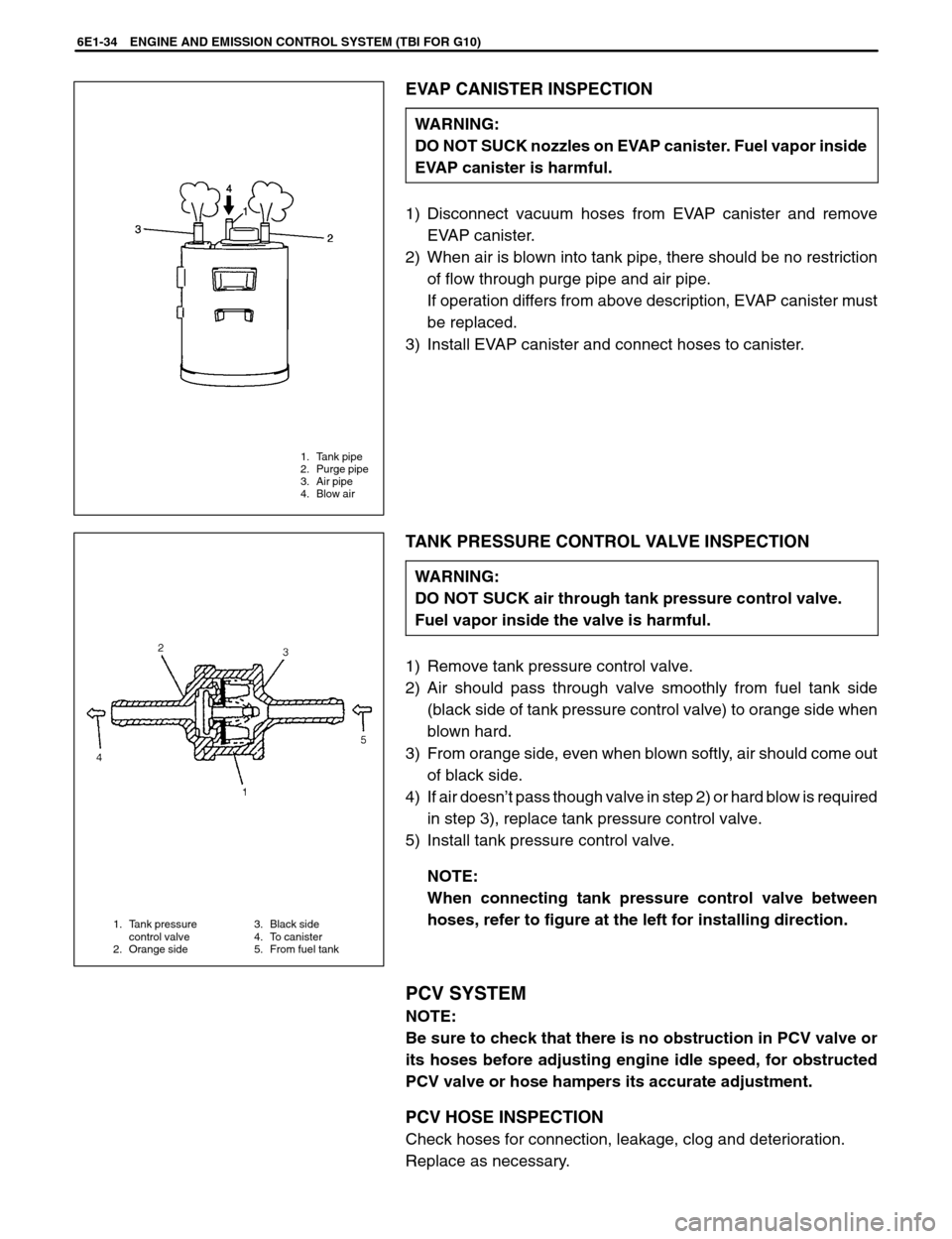
6E1-34 ENGINE AND EMISSION CONTROL SYSTEM (TBI FOR G10)
1. Tank pipe
2. Purge pipe
3. Air pipe
4. Blow air
1. Tank pressure
control valve
2. Orange side3. Black side
4. To canister
5. From fuel tank
EVAP CANISTER INSPECTION
WARNING:
DO NOT SUCK nozzles on EVAP canister. Fuel vapor inside
EVAP canister is harmful.
1) Disconnect vacuum hoses from EVAP canister and remove
EVAP canister.
2) When air is blown into tank pipe, there should be no restriction
of flow through purge pipe and air pipe.
If operation differs from above description, EVAP canister must
be replaced.
3) Install EVAP canister and connect hoses to canister.
TANK PRESSURE CONTROL VALVE INSPECTION
WARNING:
DO NOT SUCK air through tank pressure control valve.
Fuel vapor inside the valve is harmful.
1) Remove tank pressure control valve.
2) Air should pass through valve smoothly from fuel tank side
(black side of tank pressure control valve) to orange side when
blown hard.
3) From orange side, even when blown softly, air should come out
of black side.
4) If air doesn’t pass though valve in step 2) or hard blow is required
in step 3), replace tank pressure control valve.
5) Install tank pressure control valve.
NOTE:
When connecting tank pressure control valve between
hoses, refer to figure at the left for installing direction.
PCV SYSTEM
NOTE:
Be sure to check that there is no obstruction in PCV valve or
its hoses before adjusting engine idle speed, for obstructed
PCV valve or hose hampers its accurate adjustment.
PCV HOSE INSPECTION
Check hoses for connection, leakage, clog and deterioration.
Replace as necessary.
Page 426 of 557
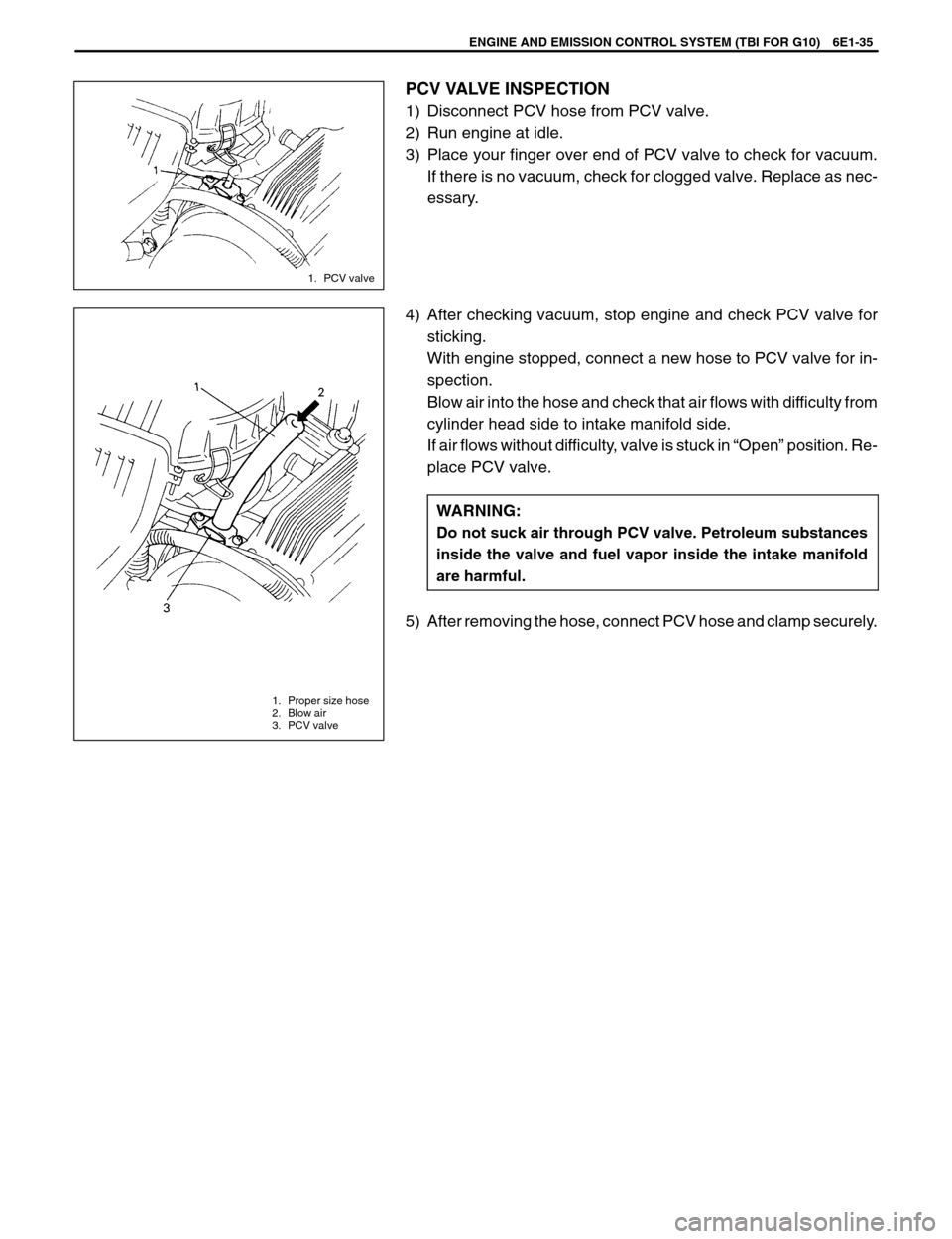
ENGINE AND EMISSION CONTROL SYSTEM (TBI FOR G10) 6E1-35
1. PCV valve
1. Proper size hose
2. Blow air
3. PCV valve
PCV VALVE INSPECTION
1) Disconnect PCV hose from PCV valve.
2) Run engine at idle.
3) Place your finger over end of PCV valve to check for vacuum.
If there is no vacuum, check for clogged valve. Replace as nec-
essary.
4) After checking vacuum, stop engine and check PCV valve for
sticking.
With engine stopped, connect a new hose to PCV valve for in-
spection.
Blow air into the hose and check that air flows with difficulty from
cylinder head side to intake manifold side.
If air flows without difficulty, valve is stuck in “Open” position. Re-
place PCV valve.
WARNING:
Do not suck air through PCV valve. Petroleum substances
inside the valve and fuel vapor inside the intake manifold
are harmful.
5) After removing the hose, connect PCV hose and clamp securely.
Page 429 of 557
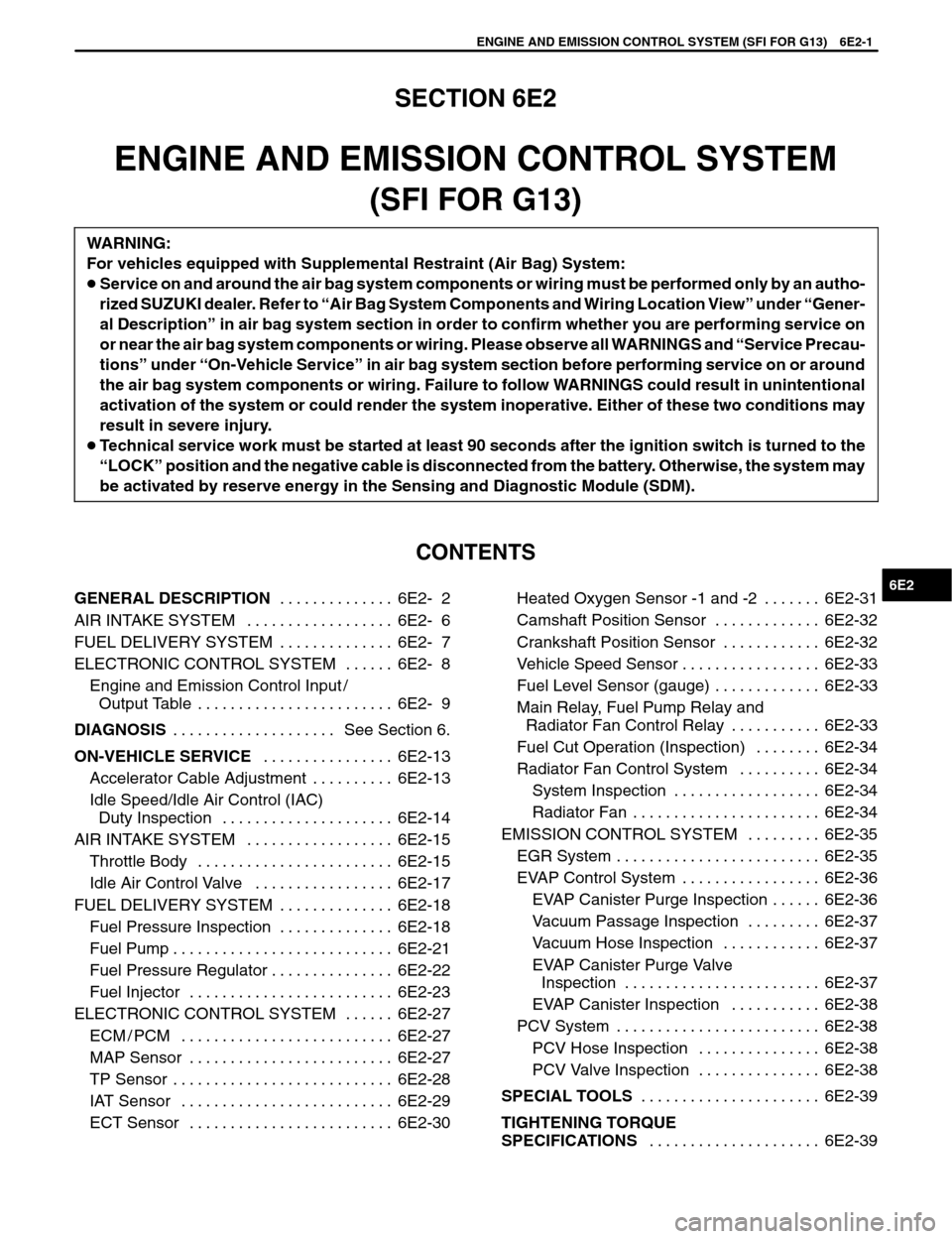
6E2
ENGINE AND EMISSION CONTROL SYSTEM (SFI FOR G13) 6E2-1
GENERAL DESCRIPTION6E2- 2 . . . . . . . . . . . . . .
AIR INTAKE SYSTEM 6E2- 6. . . . . . . . . . . . . . . . . .
FUEL DELIVERY SYSTEM 6E2- 7. . . . . . . . . . . . . .
ELECTRONIC CONTROL SYSTEM 6E2- 8. . . . . .
Engine and Emission Control Input /
Output Table 6E2- 9. . . . . . . . . . . . . . . . . . . . . . . .
DIAGNOSISSee Section 6. . . . . . . . . . . . . . . . . . . . .
ON-VEHICLE SERVICE6E2-13 . . . . . . . . . . . . . . . .
Accelerator Cable Adjustment 6E2-13. . . . . . . . . .
Idle Speed/Idle Air Control (IAC)
Duty Inspection 6E2-14. . . . . . . . . . . . . . . . . . . . .
AIR INTAKE SYSTEM 6E2-15. . . . . . . . . . . . . . . . . .
Throttle Body 6E2-15. . . . . . . . . . . . . . . . . . . . . . . .
Idle Air Control Valve 6E2-17. . . . . . . . . . . . . . . . .
FUEL DELIVERY SYSTEM 6E2-18. . . . . . . . . . . . . .
Fuel Pressure Inspection 6E2-18. . . . . . . . . . . . . .
Fuel Pump 6E2-21. . . . . . . . . . . . . . . . . . . . . . . . . . .
Fuel Pressure Regulator 6E2-22. . . . . . . . . . . . . . .
Fuel Injector 6E2-23. . . . . . . . . . . . . . . . . . . . . . . . .
ELECTRONIC CONTROL SYSTEM 6E2-27. . . . . .
ECM / PCM 6E2-27. . . . . . . . . . . . . . . . . . . . . . . . . .
MAP Sensor 6E2-27. . . . . . . . . . . . . . . . . . . . . . . . .
TP Sensor 6E2-28. . . . . . . . . . . . . . . . . . . . . . . . . . .
IAT Sensor 6E2-29. . . . . . . . . . . . . . . . . . . . . . . . . .
ECT Sensor 6E2-30. . . . . . . . . . . . . . . . . . . . . . . . . Heated Oxygen Sensor -1 and -2 6E2-31. . . . . . .
Camshaft Position Sensor 6E2-32. . . . . . . . . . . . .
Crankshaft Position Sensor 6E2-32. . . . . . . . . . . .
Vehicle Speed Sensor 6E2-33. . . . . . . . . . . . . . . . .
Fuel Level Sensor (gauge) 6E2-33. . . . . . . . . . . . .
Main Relay, Fuel Pump Relay and
Radiator Fan Control Relay 6E2-33. . . . . . . . . . .
Fuel Cut Operation (Inspection) 6E2-34. . . . . . . .
Radiator Fan Control System 6E2-34. . . . . . . . . .
System Inspection 6E2-34. . . . . . . . . . . . . . . . . .
Radiator Fan 6E2-34. . . . . . . . . . . . . . . . . . . . . . .
EMISSION CONTROL SYSTEM 6E2-35. . . . . . . . .
EGR System 6E2-35. . . . . . . . . . . . . . . . . . . . . . . . .
EVAP Control System 6E2-36. . . . . . . . . . . . . . . . .
EVAP Canister Purge Inspection 6E2-36. . . . . .
Vacuum Passage Inspection 6E2-37. . . . . . . . .
Vacuum Hose Inspection 6E2-37. . . . . . . . . . . .
EVAP Canister Purge Valve
Inspection 6E2-37. . . . . . . . . . . . . . . . . . . . . . . .
EVAP Canister Inspection 6E2-38. . . . . . . . . . .
PCV System 6E2-38. . . . . . . . . . . . . . . . . . . . . . . . .
PCV Hose Inspection 6E2-38. . . . . . . . . . . . . . .
PCV Valve Inspection 6E2-38. . . . . . . . . . . . . . .
SPECIAL TOOLS6E2-39 . . . . . . . . . . . . . . . . . . . . . .
TIGHTENING TORQUE
SPECIFICATIONS6E2-39 . . . . . . . . . . . . . . . . . . . . .
SECTION 6E2
ENGINE AND EMISSION CONTROL SYSTEM
(SFI FOR G13)
WARNING:
For vehicles equipped with Supplemental Restraint (Air Bag) System:
Service on and around the air bag system components or wiring must be performed only by an autho-
rized SUZUKI dealer. Refer to “Air Bag System Components and Wiring Location View” under “Gener-
al Description” in air bag system section in order to confirm whether you are performing service on
or near the air bag system components or wiring. Please observe all WARNINGS and “Service Precau-
tions” under “On-Vehicle Service” in air bag system section before performing service on or around
the air bag system components or wiring. Failure to follow WARNINGS could result in unintentional
activation of the system or could render the system inoperative. Either of these two conditions may
result in severe injury.
Technical service work must be started at least 90 seconds after the ignition switch is turned to the
“LOCK” position and the negative cable is disconnected from the battery. Otherwise, the system may
be activated by reserve energy in the Sensing and Diagnostic Module (SDM).
CONTENTS
Page 430 of 557
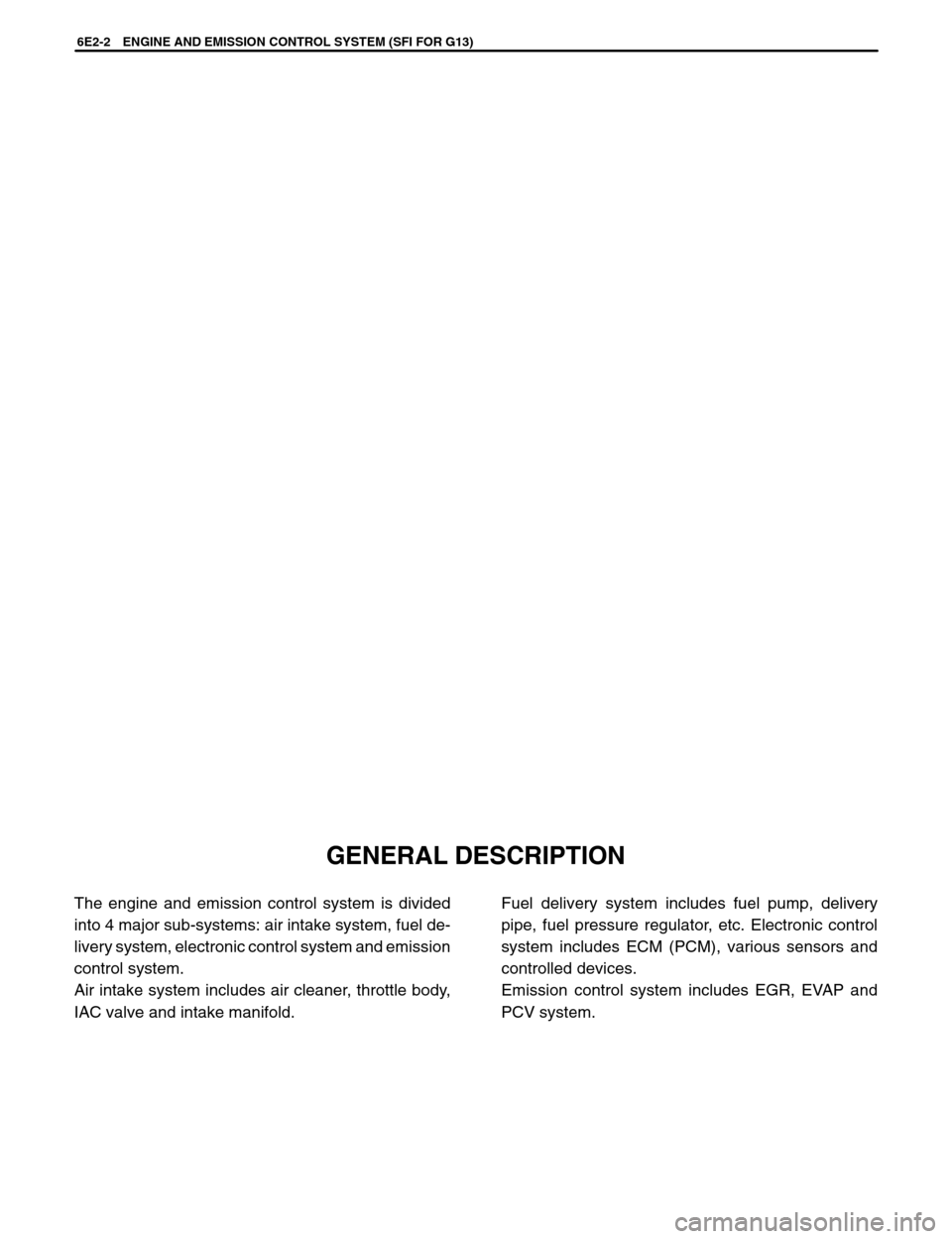
6E2-2 ENGINE AND EMISSION CONTROL SYSTEM (SFI FOR G13)
The engine and emission control system is divided
into 4 major sub-systems: air intake system, fuel de-
livery system, electronic control system and emission
control system.
Air intake system includes air cleaner, throttle body,
IAC valve and intake manifold.Fuel delivery system includes fuel pump, delivery
pipe, fuel pressure regulator, etc. Electronic control
system includes ECM (PCM), various sensors and
controlled devices.
Emission control system includes EGR, EVAP and
PCV system.
GENERAL DESCRIPTION
Page 434 of 557
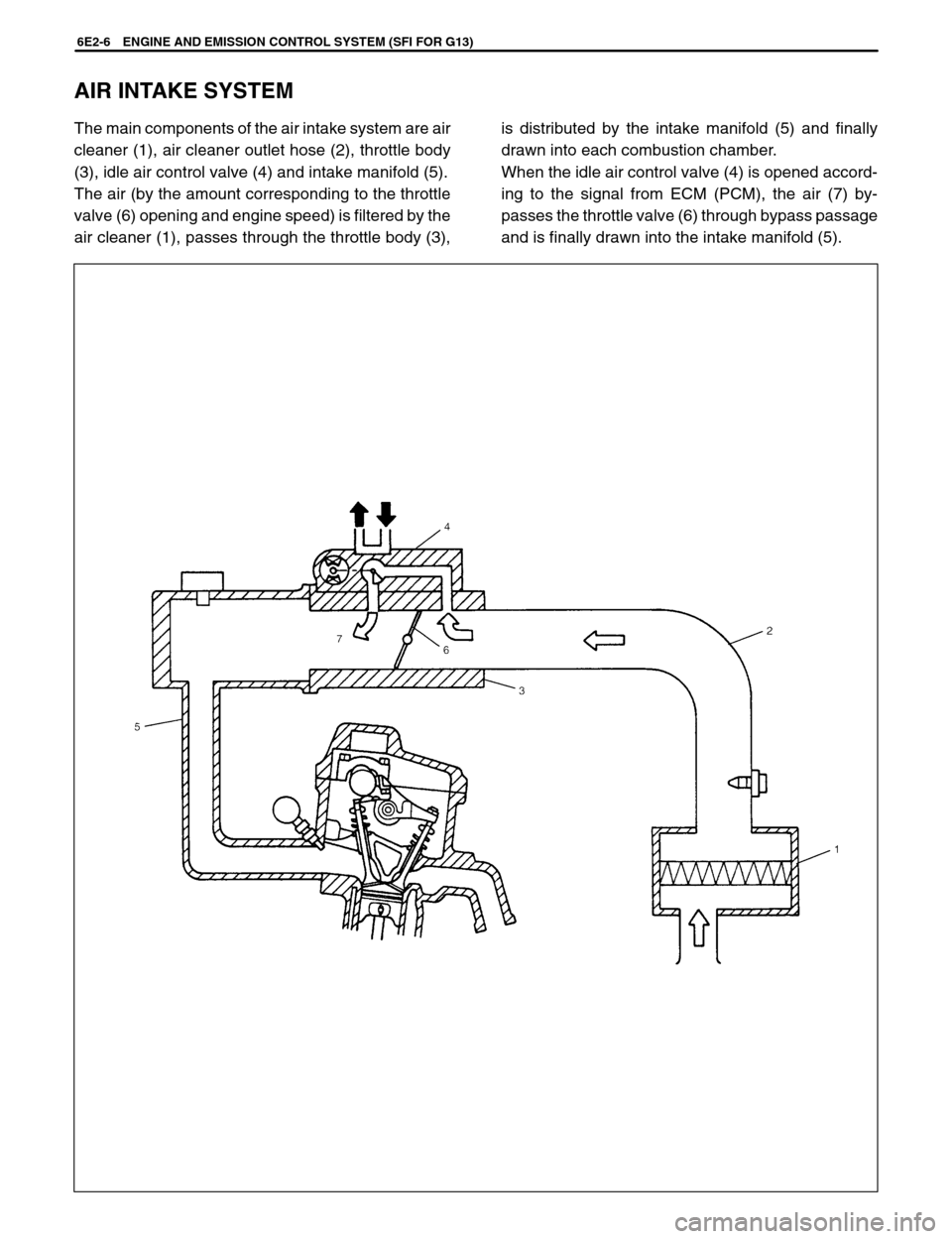
6E2-6 ENGINE AND EMISSION CONTROL SYSTEM (SFI FOR G13)
The main components of the air intake system are air
cleaner (1), air cleaner outlet hose (2), throttle body
(3), idle air control valve (4) and intake manifold (5).
The air (by the amount corresponding to the throttle
valve (6) opening and engine speed) is filtered by the
air cleaner (1), passes through the throttle body (3),is distributed by the intake manifold (5) and finally
drawn into each combustion chamber.
When the idle air control valve (4) is opened accord-
ing to the signal from ECM (PCM), the air (7) by-
passes the throttle valve (6) through bypass passage
and is finally drawn into the intake manifold (5).
AIR INTAKE SYSTEM
Page 435 of 557
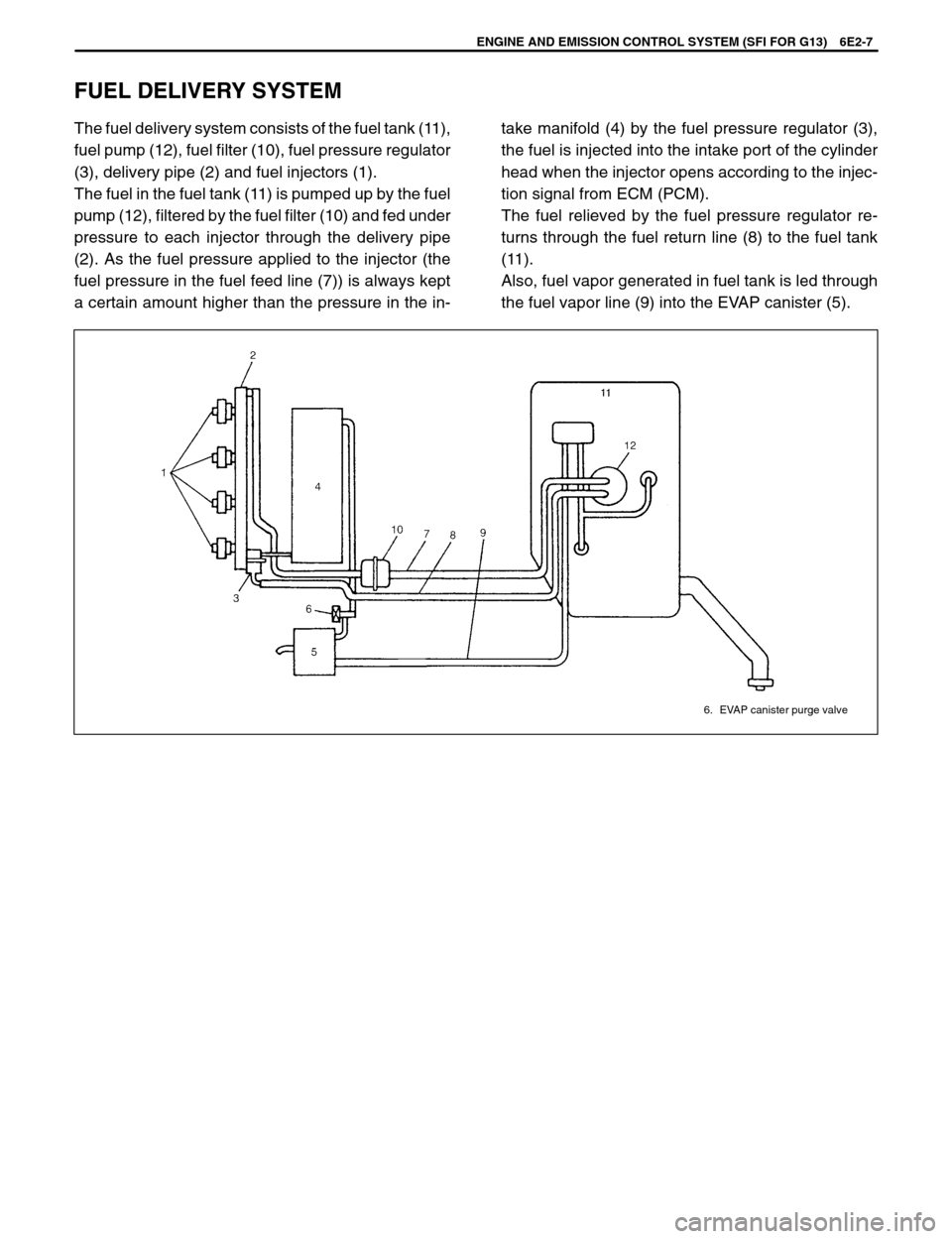
6. EVAP canister purge valve
ENGINE AND EMISSION CONTROL SYSTEM (SFI FOR G13) 6E2-7
The fuel delivery system consists of the fuel tank (11),
fuel pump (12), fuel filter (10), fuel pressure regulator
(3), delivery pipe (2) and fuel injectors (1).
The fuel in the fuel tank (11) is pumped up by the fuel
pump (12), filtered by the fuel filter (10) and fed under
pressure to each injector through the delivery pipe
(2). As the fuel pressure applied to the injector (the
fuel pressure in the fuel feed line (7)) is always kept
a certain amount higher than the pressure in the in-take manifold (4) by the fuel pressure regulator (3),
the fuel is injected into the intake port of the cylinder
head when the injector opens according to the injec-
tion signal from ECM (PCM).
The fuel relieved by the fuel pressure regulator re-
turns through the fuel return line (8) to the fuel tank
(11).
Also, fuel vapor generated in fuel tank is led through
the fuel vapor line (9) into the EVAP canister (5).
FUEL DELIVERY SYSTEM
Page 436 of 557

6E2-8 ENGINE AND EMISSION CONTROL SYSTEM (SFI FOR G13)
INFORMATION SENSORS
-1. MAP sensor
-2. TP sensor
-3. IAT sensor
-4. ECT sensor
-5. Heated oxygen sensor-1
5-1. Heated oxygen sensor-2
-6. VSS (A / T)
-7. Transmission range switch (A / T)
-8. Battery
-9. CMP sensor
-10. CKP sensor
-11. Fuel level sensor (gauge) (in fuel tank)
-12. PSP switch
-13. A / C control module (if equipped)
-14. VSS (speedometer) (M / T)OTHERS
A: ECM (PCM)
B: Main relay
C: EVAP canister
D: Data link connector CONTROL DEVICES
a: Fuel injector
b: EVAP canister purge valve
c: Fuel pump relay
d: EGR valve (step motor)
e: Malfunction indicator lamp
f: Ignition coil assembly
g: Radiator fan control relay
h: IAC valve
The electronic control system consists of 1) various
sensors which detect the state of engine and driving
conditions, 2) ECM (PCM) which controls various de-
vices according to the signals from the sensors and
3) various controlled devices.
Functionally, it is divided into nine sub systems:
Fuel injection control system
Idle speed control systemFuel pump control system
A / C control system (if equipped)
Radiator fan control system
EGR system
Evaporative emission control system
Oxygen sensor heater control system
Ignition control system
Also, with A / T model, PCM controls A / T.
ELECTRONIC CONTROL SYSTEM
Page 437 of 557
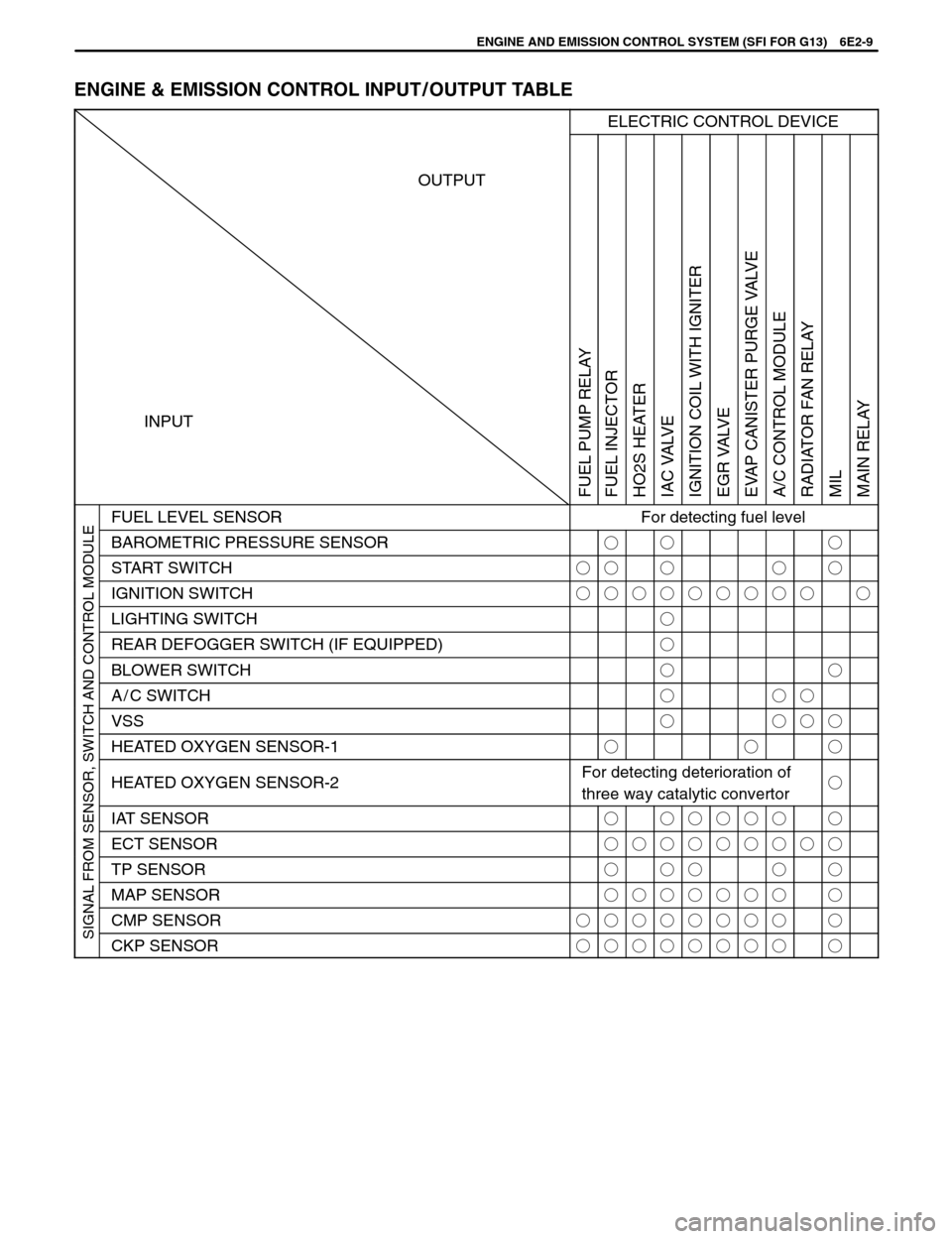
ENGINE AND EMISSION CONTROL SYSTEM (SFI FOR G13) 6E2-9
FUEL PUMP RELAY
FUEL INJECTOR
HO2S HEATER
IAC VALVE
IGNITION COIL WITH IGNITER
EGR VALVE
EVAP CANISTER PURGE VALVE
A/C CONTROL MODULE
RADIATOR FAN RELAY
MIL
MAIN RELAY
SIGNAL FROM SENSOR, SWITCH AND CONTROL MODULE
OUTPUT
INPUT
ENGINE & EMISSION CONTROL INPUT / OUTPUT TABLE
ELECTRIC CONTROL DEVICE
FUEL LEVEL SENSORFor detecting fuel level
BAROMETRIC PRESSURE SENSOR
START SWITCH
IGNITION SWITCH
LIGHTING SWITCH
REAR DEFOGGER SWITCH (IF EQUIPPED)
BLOWER SWITCH
A / C SWITCH
VSS
HEATED OXYGEN SENSOR-1
HEATED OXYGEN SENSOR-2For detecting deterioration of
three way catalytic convertor
IAT SENSOR
ECT SENSOR
TP SENSOR
MAP SENSOR
CMP SENSOR
CKP SENSOR
Page 440 of 557
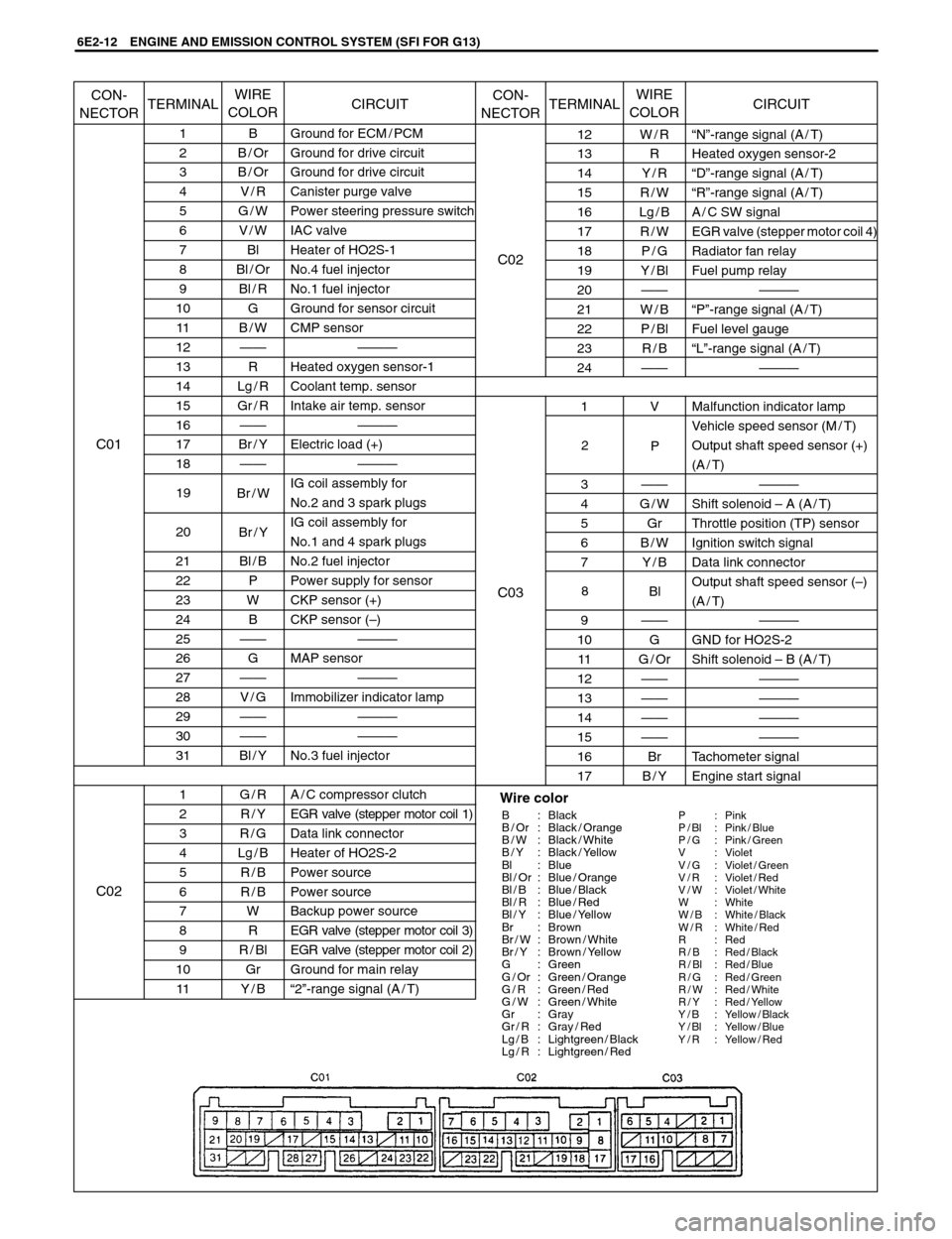
12 W / R “N”-range signal (A / T)
13 R Heated oxygen sensor-2
14 Y / R “D”-range signal (A / T)
15 R / W “R”-range signal (A / T)
16 Lg / B A / C SW signal
17 R / W EGR valve (stepper motor coil 4)
18 P / G Radiator fan relay
19 Y / Bl Fuel pump relay
20 —— ———
21 W / B “P”-range signal (A / T)
22 P / Bl Fuel level gauge
23 R / B “L”-range signal (A / T)
24 —— ———
1 V Malfunction indicator lamp
Vehicle speed sensor (M / T)
Output shaft speed sensor (+)
(A / T)
3 —— ———
4 G / W Shift solenoid – A (A / T)
5 Gr Throttle position (TP) sensor
6 B / W Ignition switch signal
7 Y / B Data link connector
Output shaft speed sensor (–)
(A / T)
9 —— ———
10 G GND for HO2S-2
11 G / Or Shift solenoid – B (A / T)
12 —— ———
13 —— ———
14 —— ———
15 —— ———
16 Br Tachometer signal
17 B / Y Engine start signal
CON-
NECTORTERMINALWIRE
COLORCIRCUITCON-
NECTORTERMINALWIRE
COLORCIRCUIT
20
Br / Y 19
Br / W
C02 C01C02
C03
Wire color
B : Black
B / Or : Black / Orange
B / W : Black / White
B / Y : Black / Yellow
Bl : Blue
Bl / Or : Blue / Orange
Bl / B : Blue / Black
Bl / R : Blue / Red
Bl / Y : Blue / Yellow
Br : Brown
Br / W : Brown / White
Br / Y : Brown / Yellow
G : Green
G / Or : Green / Orange
G / R : Green / Red
G / W : Green / White
Gr : Gray
Gr / R : Gray / Red
Lg / B : Lightgreen / Black
Lg / R : Lightgreen / RedP : Pink
P / Bl : Pink / Blue
P / G : Pink / Green
V : Violet
V / G : Violet / Green
V / R : Violet / Red
V / W : Violet / White
W : White
W / B : White / Black
W / R : White / Red
R : Red
R / B : Red / Black
R / Bl : Red / Blue
R / G : Red / Green
R / W : Red / White
R / Y : Red / Yellow
Y / B : Yellow / Black
Y / Bl : Yellow / Blue
Y / R : Yellow / Red
2
P
8
Bl
6E2-12 ENGINE AND EMISSION CONTROL SYSTEM (SFI FOR G13)
1 B Ground for ECM / PCM
2 B / Or Ground for drive circuit
3 B / Or Ground for drive circuit
4 V / R Canister purge valve
5 G / W Power steering pressure switch
6 V / W IAC valve
7 Bl Heater of HO2S-1
8 Bl / Or No.4 fuel injector
9 Bl / R No.1 fuel injector
10 G Ground for sensor circuit
11 B / W CMP sensor
12 —— ———
13 R Heated oxygen sensor-1
14 Lg / R Coolant temp. sensor
15 Gr / R Intake air temp. sensor
16 —— ———
17 Br / Y Electric load (+)
18 —— ———
IG coil assembly for
No.2 and 3 spark plugs
IG coil assembly for
No.1 and 4 spark plugs
21 Bl / B No.2 fuel injector
22 P Power supply for sensor
23 W CKP sensor (+)
24 B CKP sensor (–)
25 —— ———
26 G MAP sensor
27 —— ———
28 V / G Immobilizer indicator lamp
29 —— ———
30 —— ———
31 Bl / Y No.3 fuel injector
1 G / R A / C compressor clutch
2 R / Y EGR valve (stepper motor coil 1)
3 R / G Data link connector
4 Lg / B Heater of HO2S-2
5 R / B Power source
6 R / B Power source
7 W Backup power source
8 R EGR valve (stepper motor coil 3)
9 R / Bl EGR valve (stepper motor coil 2)
10 Gr Ground for main relay
11 Y / B “2”-range signal (A / T)
Page 441 of 557
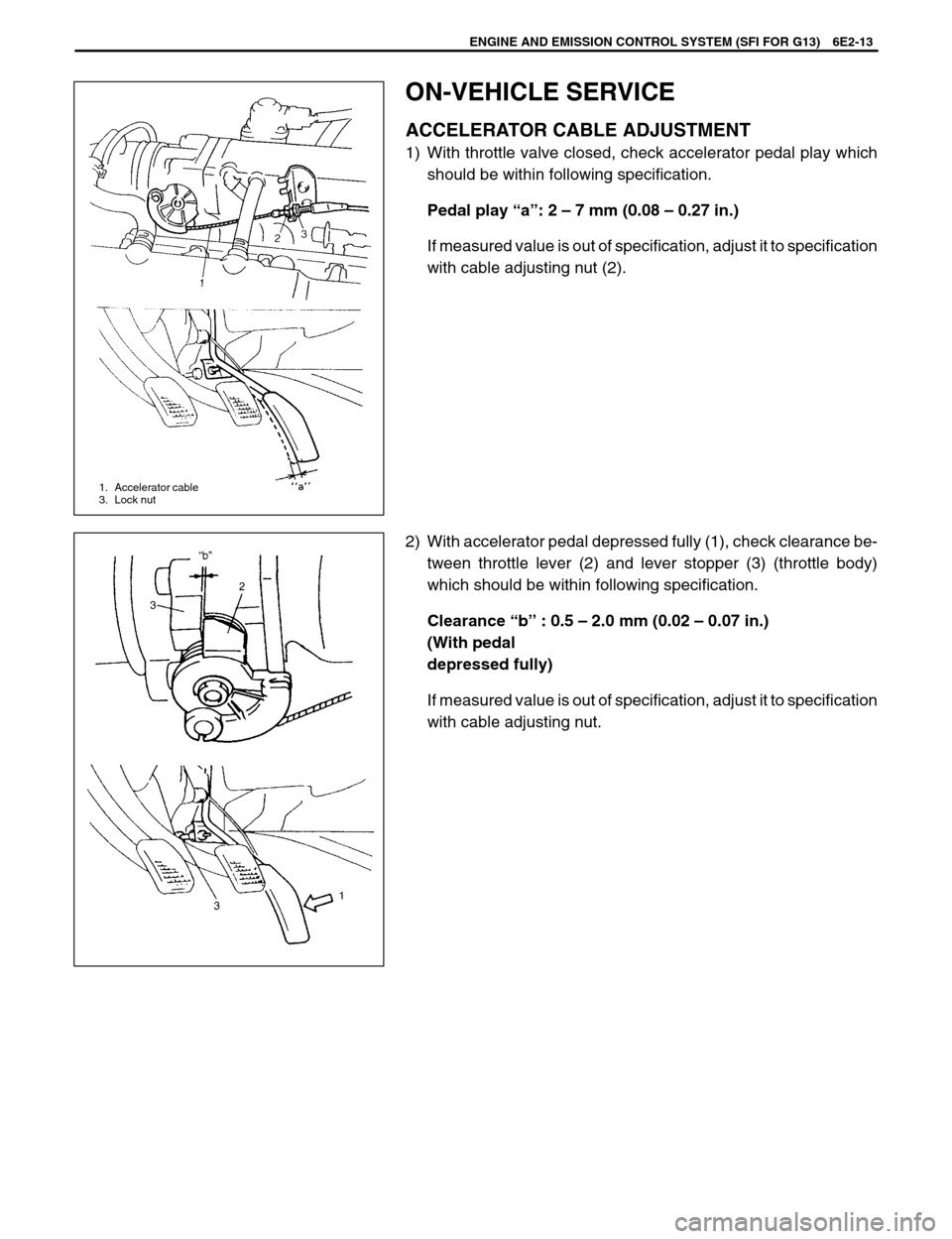
1. Accelerator cable
3. Lock nut
ENGINE AND EMISSION CONTROL SYSTEM (SFI FOR G13) 6E2-13
ON-VEHICLE SERVICE
ACCELERATOR CABLE ADJUSTMENT
1) With throttle valve closed, check accelerator pedal play which
should be within following specification.
Pedal play “a”: 2 – 7 mm (0.08 – 0.27 in.)
If measured value is out of specification, adjust it to specification
with cable adjusting nut (2).
2) With accelerator pedal depressed fully (1), check clearance be-
tween throttle lever (2) and lever stopper (3) (throttle body)
which should be within following specification.
Clearance “b” : 0.5 – 2.0 mm (0.02 – 0.07 in.)
(With pedal
depressed fully)
If measured value is out of specification, adjust it to specification
with cable adjusting nut.