valve SUZUKI SWIFT 2000 1.G SF310 Service Workshop Manual
[x] Cancel search | Manufacturer: SUZUKI, Model Year: 2000, Model line: SWIFT, Model: SUZUKI SWIFT 2000 1.GPages: 557, PDF Size: 14.35 MB
Page 466 of 557
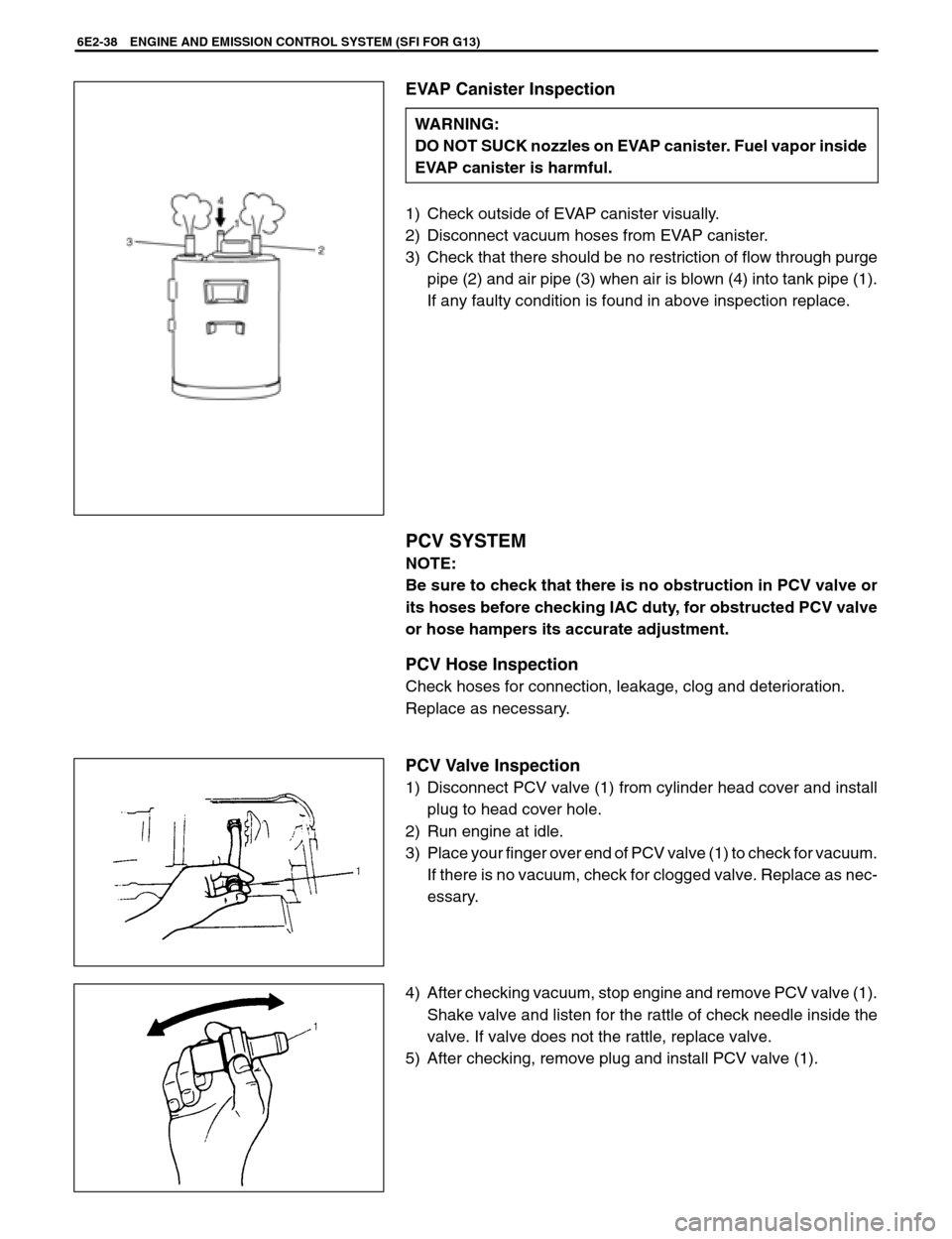
6E2-38 ENGINE AND EMISSION CONTROL SYSTEM (SFI FOR G13)
EVAP Canister Inspection
WARNING:
DO NOT SUCK nozzles on EVAP canister. Fuel vapor inside
EVAP canister is harmful.
1) Check outside of EVAP canister visually.
2) Disconnect vacuum hoses from EVAP canister.
3) Check that there should be no restriction of flow through purge
pipe (2) and air pipe (3) when air is blown (4) into tank pipe (1).
If any faulty condition is found in above inspection replace.
PCV SYSTEM
NOTE:
Be sure to check that there is no obstruction in PCV valve or
its hoses before checking IAC duty, for obstructed PCV valve
or hose hampers its accurate adjustment.
PCV Hose Inspection
Check hoses for connection, leakage, clog and deterioration.
Replace as necessary.
PCV Valve Inspection
1) Disconnect PCV valve (1) from cylinder head cover and install
plug to head cover hole.
2) Run engine at idle.
3) Place your finger over end of PCV valve (1) to check for vacuum.
If there is no vacuum, check for clogged valve. Replace as nec-
essary.
4) After checking vacuum, stop engine and remove PCV valve (1).
Shake valve and listen for the rattle of check needle inside the
valve. If valve does not the rattle, replace valve.
5) After checking, remove plug and install PCV valve (1).
Page 467 of 557
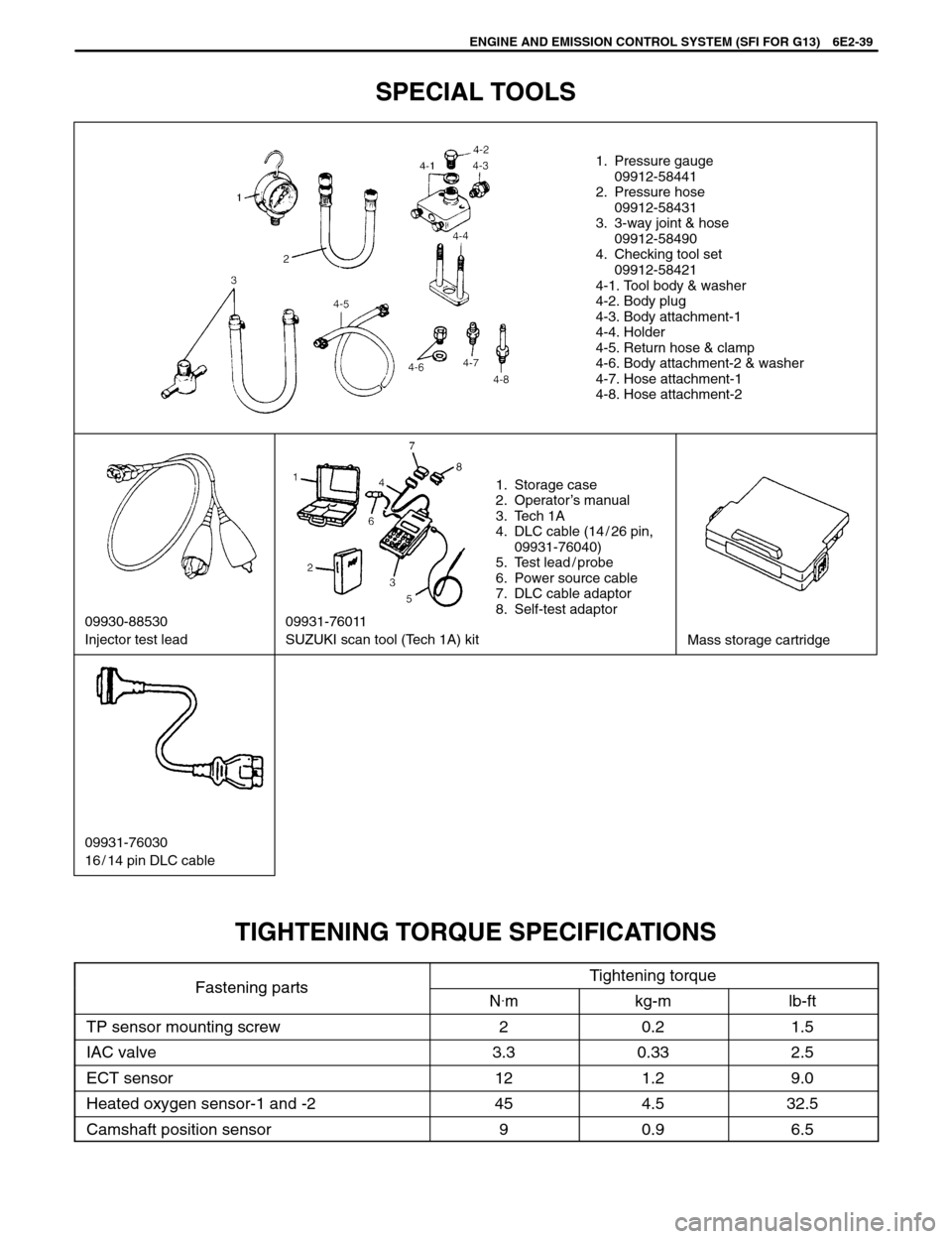
ENGINE AND EMISSION CONTROL SYSTEM (SFI FOR G13) 6E2-39
09930-88530
Injector test lead09931-76011
SUZUKI scan tool (Tech 1A) kit
Mass storage cartridge
09931-76030
16 / 14 pin DLC cable1. Pressure gauge
09912-58441
2. Pressure hose
09912-58431
3. 3-way joint & hose
09912-58490
4. Checking tool set
09912-58421
4-1. Tool body & washer
4-2. Body plug
4-3. Body attachment-1
4-4. Holder
4-5. Return hose & clamp
4-6. Body attachment-2 & washer
4-7. Hose attachment-1
4-8. Hose attachment-2
1. Storage case
2. Operator’s manual
3. Tech 1A
4. DLC cable (14 / 26 pin,
09931-76040)
5. Test lead / probe
6. Power source cable
7. DLC cable adaptor
8. Self-test adaptor
SPECIAL TOOLS
TIGHTENING TORQUE SPECIFICATIONS
FasteningpartsTightening torqueFastening artsN.mkg-mlb-ft
TP sensor mounting screw20.21.5
IAC valve3.30.332.5
ECT sensor121.29.0
Heated oxygen sensor-1 and -2454.532.5
Camshaft position sensor90.96.5
Page 492 of 557
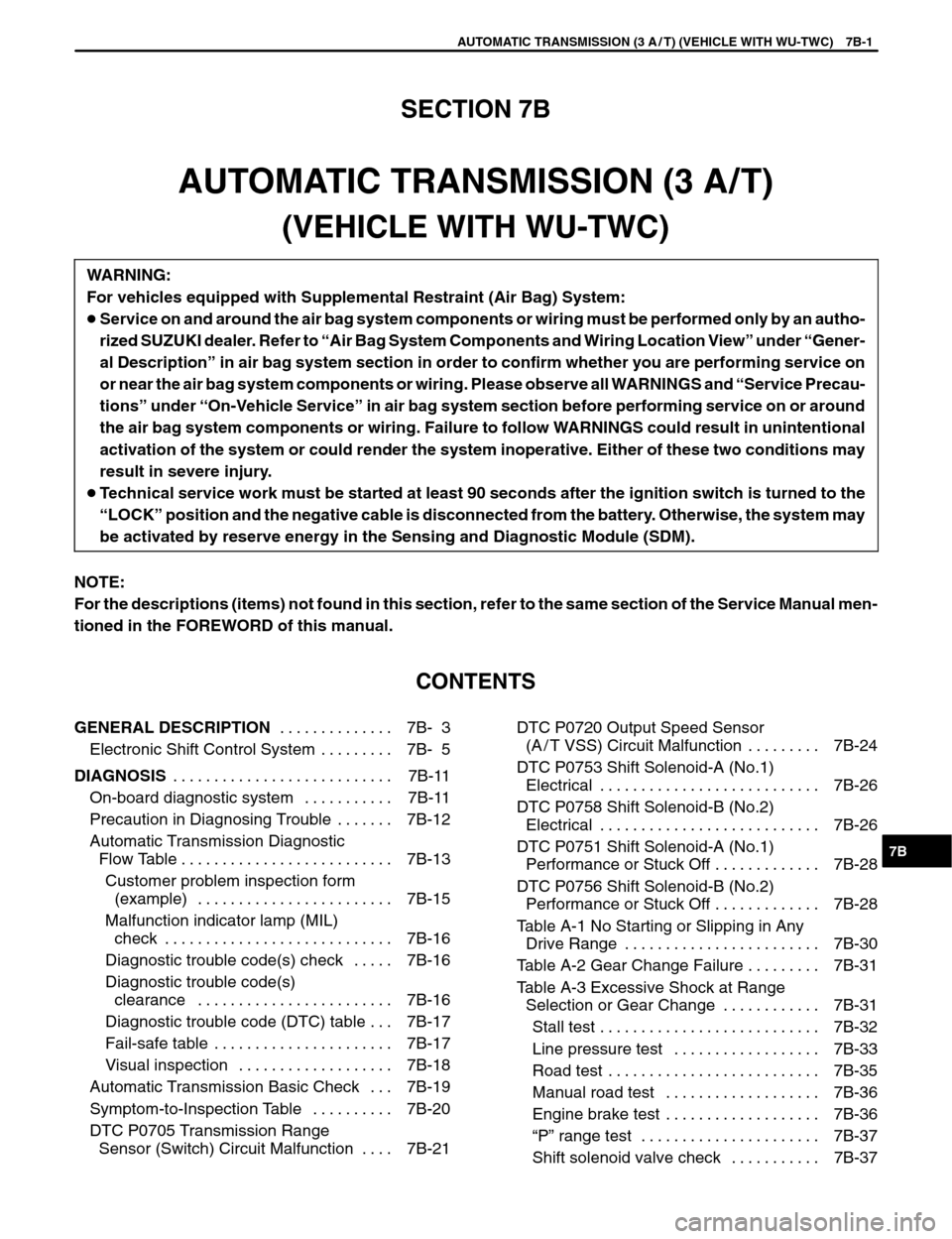
7B
AUTOMATIC TRANSMISSION (3 A / T) (VEHICLE WITH WU-TWC) 7B-1
GENERAL DESCRIPTION7B- 3 . . . . . . . . . . . . . .
Electronic Shift Control System 7B- 5. . . . . . . . .
DIAGNOSIS7B-11 . . . . . . . . . . . . . . . . . . . . . . . . . . .
On-board diagnostic system 7B-11. . . . . . . . . . .
Precaution in Diagnosing Trouble 7B-12. . . . . . .
Automatic Transmission Diagnostic
Flow Table 7B-13. . . . . . . . . . . . . . . . . . . . . . . . . .
Customer problem inspection form
(example) 7B-15. . . . . . . . . . . . . . . . . . . . . . . .
Malfunction indicator lamp (MIL)
check 7B-16. . . . . . . . . . . . . . . . . . . . . . . . . . . .
Diagnostic trouble code(s) check 7B-16. . . . .
Diagnostic trouble code(s)
clearance 7B-16. . . . . . . . . . . . . . . . . . . . . . . .
Diagnostic trouble code (DTC) table 7B-17. . .
Fail-safe table 7B-17. . . . . . . . . . . . . . . . . . . . . .
Visual inspection 7B-18. . . . . . . . . . . . . . . . . . .
Automatic Transmission Basic Check 7B-19. . .
Symptom-to-Inspection Table 7B-20. . . . . . . . . .
DTC P0705 Transmission Range
Sensor (Switch) Circuit Malfunction 7B-21. . . . DTC P0720 Output Speed Sensor
(A / T VSS) Circuit Malfunction 7B-24. . . . . . . . .
DTC P0753 Shift Solenoid-A (No.1)
Electrical 7B-26. . . . . . . . . . . . . . . . . . . . . . . . . . .
DTC P0758 Shift Solenoid-B (No.2)
Electrical 7B-26. . . . . . . . . . . . . . . . . . . . . . . . . . .
DTC P0751 Shift Solenoid-A (No.1)
Performance or Stuck Off 7B-28. . . . . . . . . . . . .
DTC P0756 Shift Solenoid-B (No.2)
Performance or Stuck Off 7B-28. . . . . . . . . . . . .
Table A-1 No Starting or Slipping in Any
Drive Range 7B-30. . . . . . . . . . . . . . . . . . . . . . . .
Table A-2 Gear Change Failure 7B-31. . . . . . . . .
Table A-3 Excessive Shock at Range
Selection or Gear Change 7B-31. . . . . . . . . . . .
Stall test 7B-32. . . . . . . . . . . . . . . . . . . . . . . . . . .
Line pressure test 7B-33. . . . . . . . . . . . . . . . . .
Road test 7B-35. . . . . . . . . . . . . . . . . . . . . . . . . .
Manual road test 7B-36. . . . . . . . . . . . . . . . . . .
Engine brake test 7B-36. . . . . . . . . . . . . . . . . . .
“P” range test 7B-37. . . . . . . . . . . . . . . . . . . . . .
Shift solenoid valve check 7B-37. . . . . . . . . . .
SECTION 7B
AUTOMATIC TRANSMISSION (3 A/T)
(VEHICLE WITH WU-TWC)
WARNING:
For vehicles equipped with Supplemental Restraint (Air Bag) System:
Service on and around the air bag system components or wiring must be performed only by an autho-
rized SUZUKI dealer. Refer to “Air Bag System Components and Wiring Location View” under “Gener-
al Description” in air bag system section in order to confirm whether you are performing service on
or near the air bag system components or wiring. Please observe all WARNINGS and “Service Precau-
tions” under “On-Vehicle Service” in air bag system section before performing service on or around
the air bag system components or wiring. Failure to follow WARNINGS could result in unintentional
activation of the system or could render the system inoperative. Either of these two conditions may
result in severe injury.
Technical service work must be started at least 90 seconds after the ignition switch is turned to the
“LOCK” position and the negative cable is disconnected from the battery. Otherwise, the system may
be activated by reserve energy in the Sensing and Diagnostic Module (SDM).
NOTE:
For the descriptions (items) not found in this section, refer to the same section of the Service Manual men-
tioned in the FOREWORD of this manual.
CONTENTS
Page 493 of 557
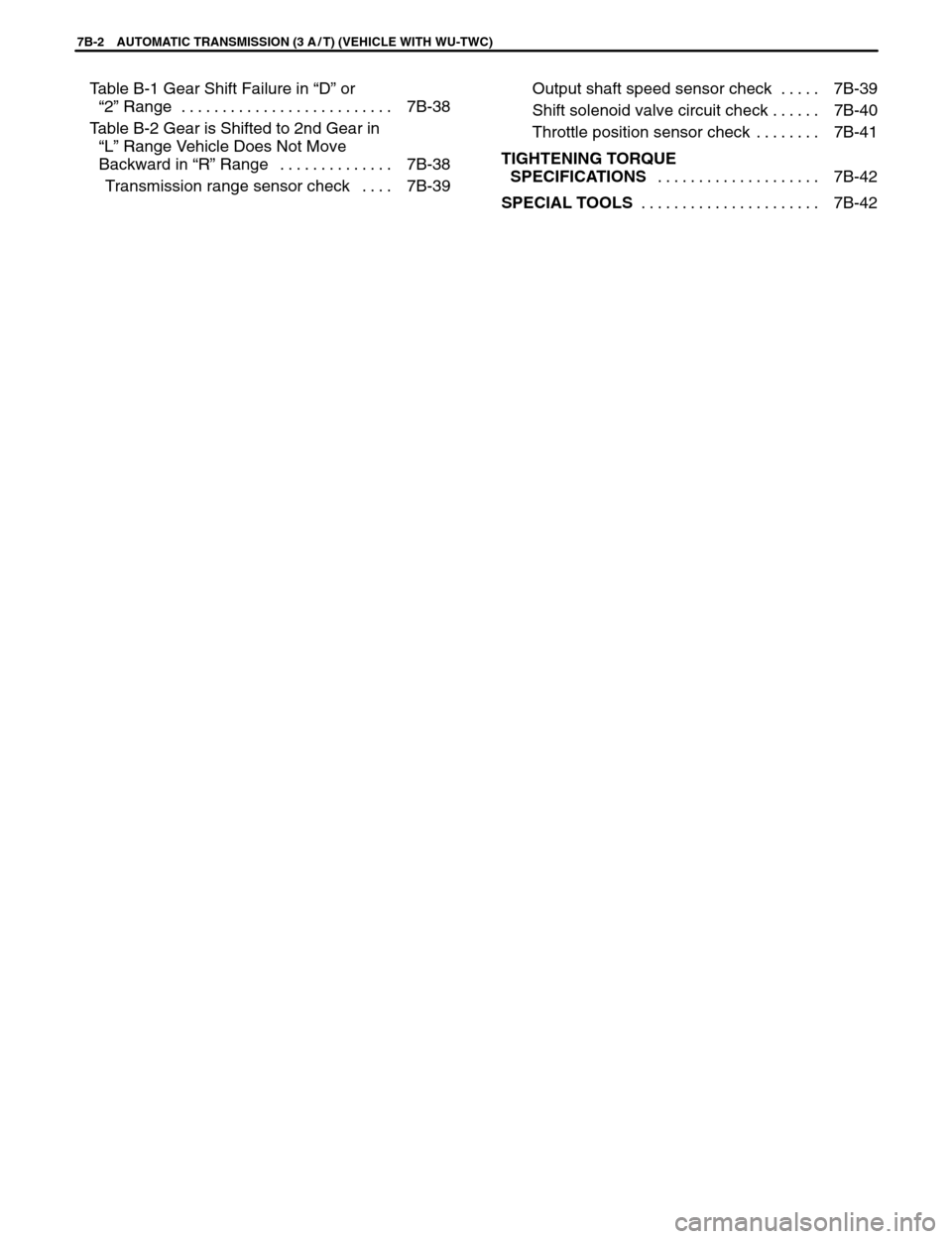
7B-2 AUTOMATIC TRANSMISSION (3 A / T) (VEHICLE WITH WU-TWC)
Table B-1 Gear Shift Failure in “D” or
“2” Range 7B-38. . . . . . . . . . . . . . . . . . . . . . . . . .
Table B-2 Gear is Shifted to 2nd Gear in
“L” Range Vehicle Does Not Move
Backward in “R” Range 7B-38. . . . . . . . . . . . . .
Transmission range sensor check 7B-39. . . . Output shaft speed sensor check 7B-39. . . . .
Shift solenoid valve circuit check 7B-40. . . . . .
Throttle position sensor check 7B-41. . . . . . . .
TIGHTENING TORQUE
SPECIFICATIONS7B-42 . . . . . . . . . . . . . . . . . . . .
SPECIAL TOOLS7B-42 . . . . . . . . . . . . . . . . . . . . . .
Page 494 of 557
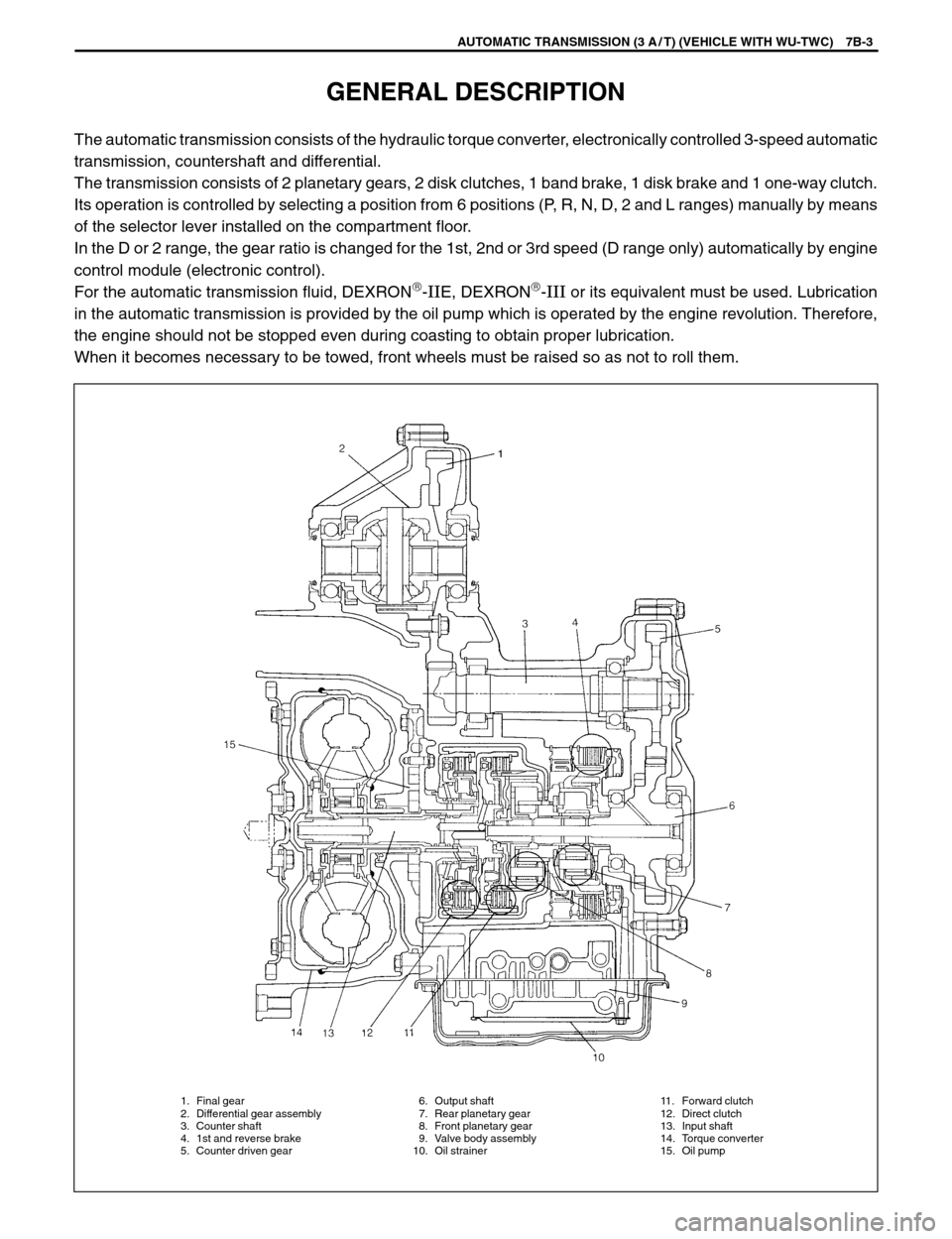
1. Final gear
2. Differential gear assembly
3. Counter shaft
4. 1st and reverse brake
5. Counter driven gear11. Forward clutch
12. Direct clutch
13. Input shaft
14. Torque converter
15. Oil pump 6. Output shaft
7. Rear planetary gear
8. Front planetary gear
9. Valve body assembly
10. Oil strainer
AUTOMATIC TRANSMISSION (3 A / T) (VEHICLE WITH WU-TWC) 7B-3
GENERAL DESCRIPTION
The automatic transmission consists of the hydraulic torque converter, electronically controlled 3-speed automatic
transmission, countershaft and differential.
The transmission consists of 2 planetary gears, 2 disk clutches, 1 band brake, 1 disk brake and 1 one-way clutch.
Its operation is controlled by selecting a position from 6 positions (P, R, N, D, 2 and L ranges) manually by means
of the selector lever installed on the compartment floor.
In the D or 2 range, the gear ratio is changed for the 1st, 2nd or 3rd speed (D range only) automatically by engine
control module (electronic control).
For the automatic transmission fluid, DEXRON
-E, DEXRON- or its equivalent must be used. Lubrication
in the automatic transmission is provided by the oil pump which is operated by the engine revolution. Therefore,
the engine should not be stopped even during coasting to obtain proper lubrication.
When it becomes necessary to be towed, front wheels must be raised so as not to roll them.
Page 496 of 557
![SUZUKI SWIFT 2000 1.G SF310 Service Workshop Manual [G10 Engine Model]
1. PCM
2. Camshaft position (CMP) sensor
3. Throttle position (TP) sensor
4. Engine coolant temperature (ECT) sensor
5. Transmission range sensor (shift switch)
6. Output shaft spee SUZUKI SWIFT 2000 1.G SF310 Service Workshop Manual [G10 Engine Model]
1. PCM
2. Camshaft position (CMP) sensor
3. Throttle position (TP) sensor
4. Engine coolant temperature (ECT) sensor
5. Transmission range sensor (shift switch)
6. Output shaft spee](/img/20/7602/w960_7602-495.png)
[G10 Engine Model]
1. PCM
2. Camshaft position (CMP) sensor
3. Throttle position (TP) sensor
4. Engine coolant temperature (ECT) sensor
5. Transmission range sensor (shift switch)
6. Output shaft speed sensor (A / T VSS)7. Malfunction indicator lamp (MIL)
8. Data link connector (DLC)
9. Shift solenoid-A
(No.1, Direct clutch solenoid valve)
10. Shift solenoid-B
(No.2, 2nd brake solenoid valve)11. Ignition switch
12. Main relay
13. Inhibitor switch
14. To starter
15. Terminal arrangement of PCM coupler
(Viewed from harness side)
AUTOMATIC TRANSMISSION (3 A / T) (VEHICLE WITH WU-TWC) 7B-5
ELECTRONIC SHIFT CONTROL SYSTEM
Page 497 of 557
![SUZUKI SWIFT 2000 1.G SF310 Service Workshop Manual 7B-6 AUTOMATIC TRANSMISSION (3 A / T) (VEHICLE WITH WU-TWC)
[G13 Engine Model]
1. PCM
2. Camshaft position (CMP) sensor
3. Throttle position (TP) sensor
4. Engine coolant temperature (ECT) sensor
5. T SUZUKI SWIFT 2000 1.G SF310 Service Workshop Manual 7B-6 AUTOMATIC TRANSMISSION (3 A / T) (VEHICLE WITH WU-TWC)
[G13 Engine Model]
1. PCM
2. Camshaft position (CMP) sensor
3. Throttle position (TP) sensor
4. Engine coolant temperature (ECT) sensor
5. T](/img/20/7602/w960_7602-496.png)
7B-6 AUTOMATIC TRANSMISSION (3 A / T) (VEHICLE WITH WU-TWC)
[G13 Engine Model]
1. PCM
2. Camshaft position (CMP) sensor
3. Throttle position (TP) sensor
4. Engine coolant temperature (ECT) sensor
5. Transmission range sensor (shift switch)
6. Output shaft speed sensor (A / T VSS)7. Malfunction indicator lamp (MIL)
8. Data link connector (DLC)
9. Shift solenoid-A
(No.1, Direct clutch solenoid valve)
10. Shift solenoid-B
(No.2, 2nd brake solenoid valve)11. Ignition switch
12. Main relay
13. Inhibitor switch
14. To starter
15. Terminal arrangement of PCM coupler
(Viewed from harness side)
Page 498 of 557
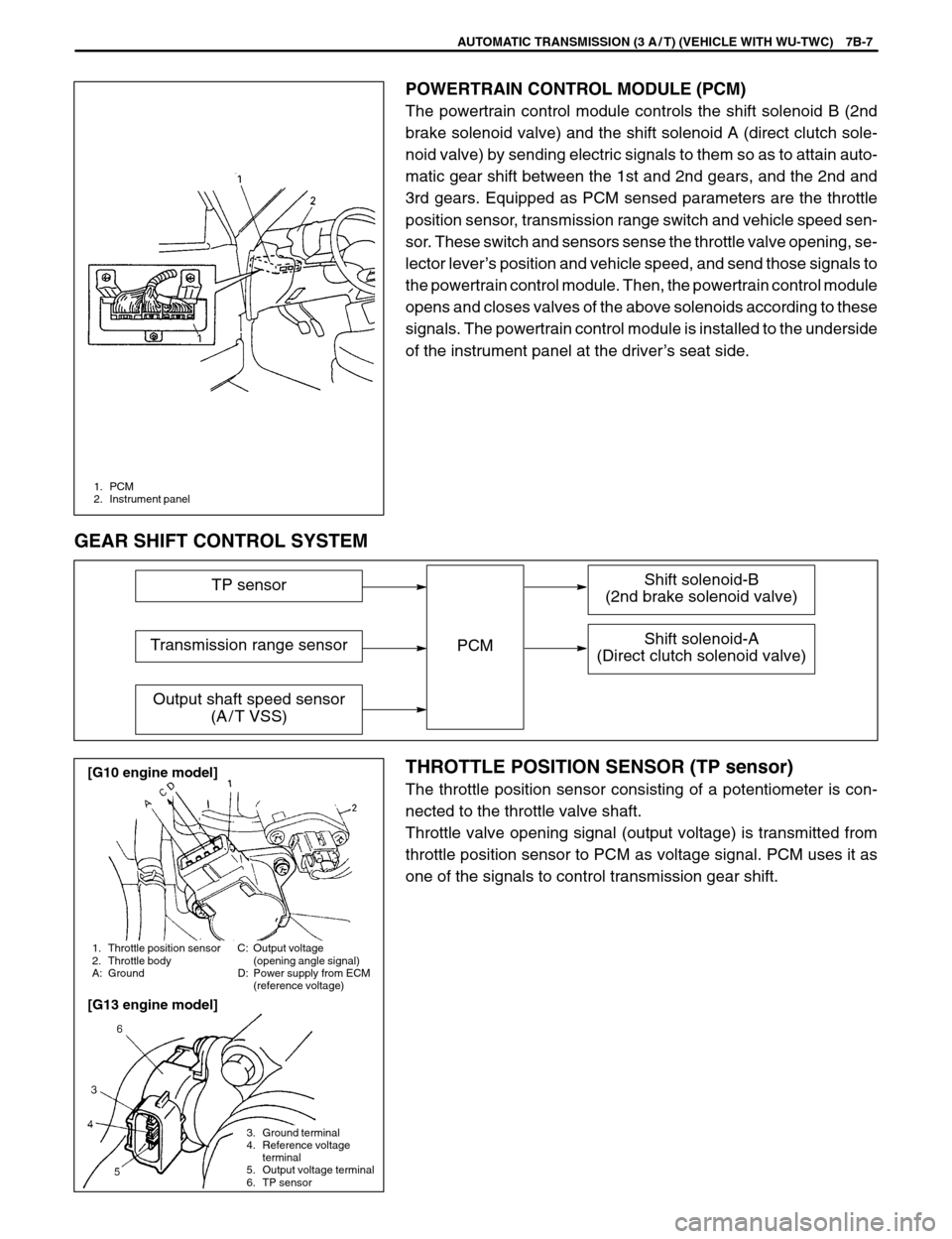
1. PCM
2. Instrument panel
TP sensor
Transmission range sensor
Output shaft speed sensor
(A / T VSS)
Shift solenoid-B
(2nd brake solenoid valve)
Shift solenoid-A
(Direct clutch solenoid valve)PCM
1. Throttle position sensor
2. Throttle body
A: Ground
3. Ground terminal
4. Reference voltage
terminal
5. Output voltage terminal
6. TP sensor
C: Output voltage
(opening angle signal)
D: Power supply from ECM
(reference voltage)
[G10 engine model]
[G13 engine model]
AUTOMATIC TRANSMISSION (3 A / T) (VEHICLE WITH WU-TWC) 7B-7
POWERTRAIN CONTROL MODULE (PCM)
The powertrain control module controls the shift solenoid B (2nd
brake solenoid valve) and the shift solenoid A (direct clutch sole-
noid valve) by sending electric signals to them so as to attain auto-
matic gear shift between the 1st and 2nd gears, and the 2nd and
3rd gears. Equipped as PCM sensed parameters are the throttle
position sensor, transmission range switch and vehicle speed sen-
sor. These switch and sensors sense the throttle valve opening, se-
lector lever’s position and vehicle speed, and send those signals to
the powertrain control module. Then, the powertrain control module
opens and closes valves of the above solenoids according to these
signals. The powertrain control module is installed to the underside
of the instrument panel at the driver’s seat side.
GEAR SHIFT CONTROL SYSTEM
THROTTLE POSITION SENSOR (TP sensor)
The throttle position sensor consisting of a potentiometer is con-
nected to the throttle valve shaft.
Throttle valve opening signal (output voltage) is transmitted from
throttle position sensor to PCM as voltage signal. PCM uses it as
one of the signals to control transmission gear shift.
Page 499 of 557
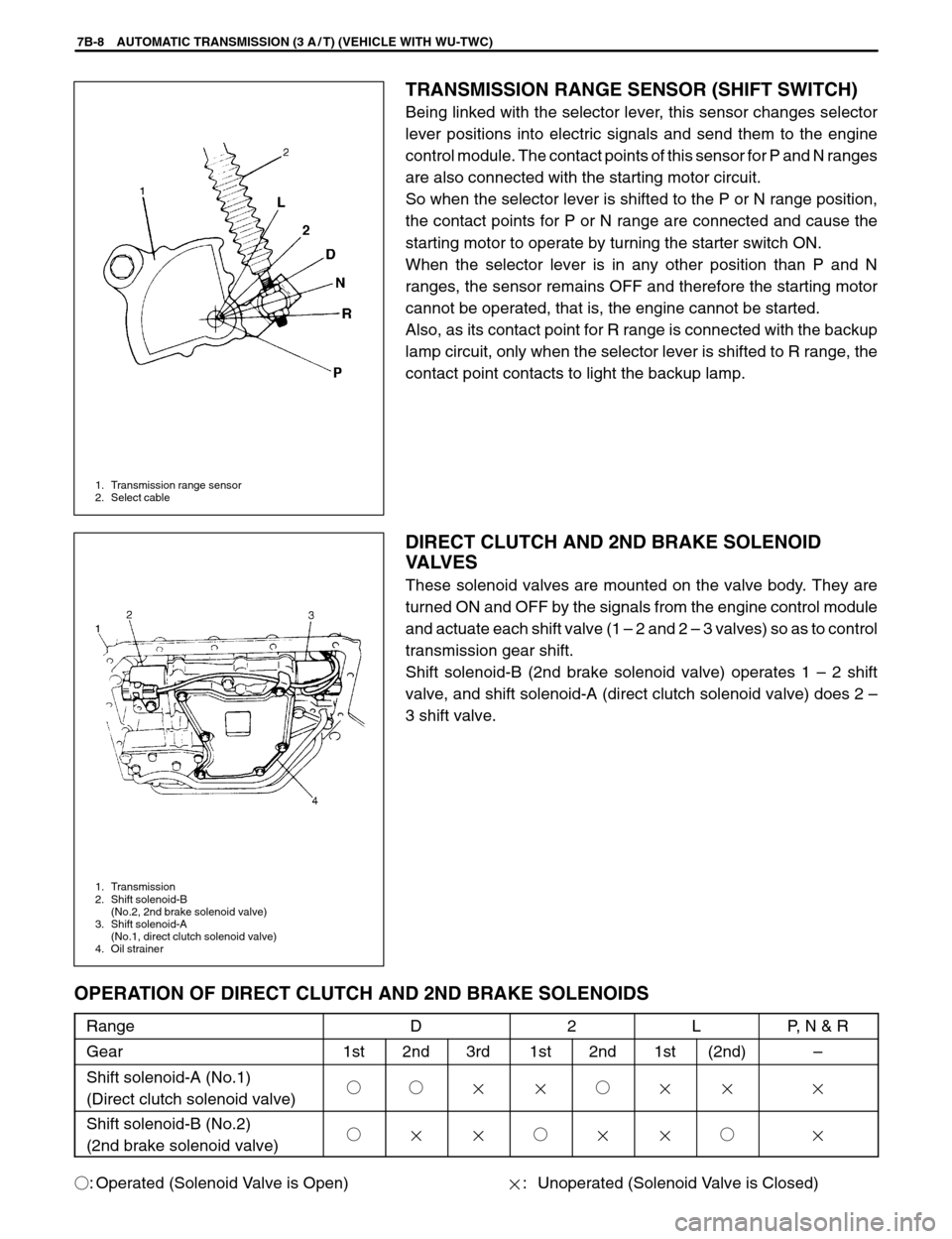
1. Transmission range sensor
2. Select cable
1. Transmission
2. Shift solenoid-B
(No.2, 2nd brake solenoid valve)
3. Shift solenoid-A
(No.1, direct clutch solenoid valve)
4. Oil strainer
7B-8 AUTOMATIC TRANSMISSION (3 A / T) (VEHICLE WITH WU-TWC)
TRANSMISSION RANGE SENSOR (SHIFT SWITCH)
Being linked with the selector lever, this sensor changes selector
lever positions into electric signals and send them to the engine
control module. The contact points of this sensor for P and N ranges
are also connected with the starting motor circuit.
So when the selector lever is shifted to the P or N range position,
the contact points for P or N range are connected and cause the
starting motor to operate by turning the starter switch ON.
When the selector lever is in any other position than P and N
ranges, the sensor remains OFF and therefore the starting motor
cannot be operated, that is, the engine cannot be started.
Also, as its contact point for R range is connected with the backup
lamp circuit, only when the selector lever is shifted to R range, the
contact point contacts to light the backup lamp.
DIRECT CLUTCH AND 2ND BRAKE SOLENOID
VALVES
These solenoid valves are mounted on the valve body. They are
turned ON and OFF by the signals from the engine control module
and actuate each shift valve (1 – 2 and 2 – 3 valves) so as to control
transmission gear shift.
Shift solenoid-B (2nd brake solenoid valve) operates 1 – 2 shift
valve, and shift solenoid-A (direct clutch solenoid valve) does 2 –
3 shift valve.
OPERATION OF DIRECT CLUTCH AND 2ND BRAKE SOLENOIDS
RangeD2LP, N & R
Gear1st2nd3rd1st2nd1st(2nd)–
Shift solenoid-A (No.1)
(Direct clutch solenoid valve)
Shift solenoid-B (No.2)
(2nd brake solenoid valve)
: Operated (Solenoid Valve is Open): Unoperated (Solenoid Valve is Closed)
Page 500 of 557
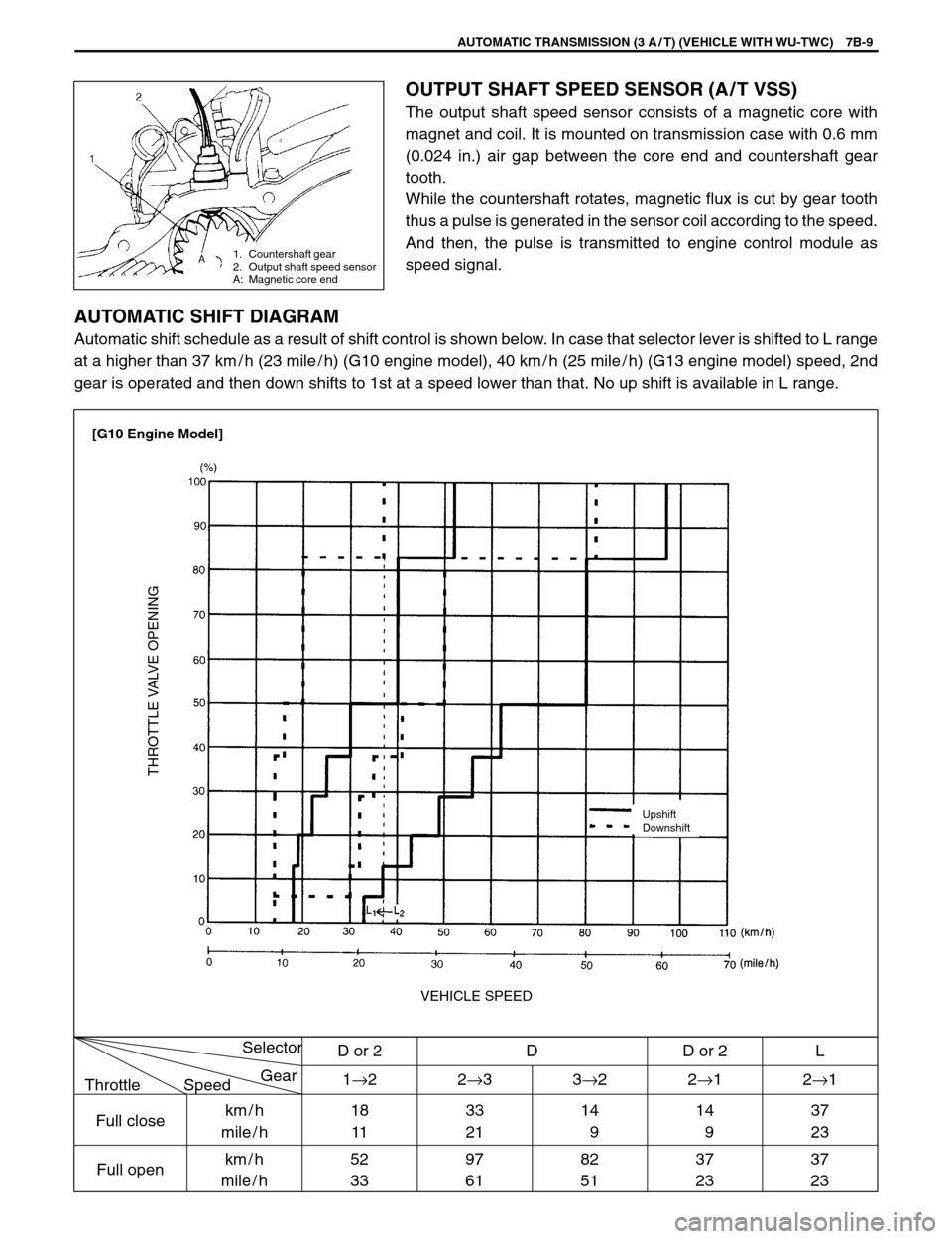
1. Countershaft gear
2. Output shaft speed sensor
A: Magnetic core end
D or 2
1→2
18
11
52
33D
2→3
33
21
97
613→2
14
9
82
51D or 2
2→1
14
9
37
23L
2→1
37
23
37
23 Full close
Full openkm / h
mile/h
km / h
mile/h Throttle SpeedGear Selector
VEHICLE SPEED
UpshiftDownshift
THROTTLE VALVE OPENING
[G10 Engine Model]
AUTOMATIC TRANSMISSION (3 A / T) (VEHICLE WITH WU-TWC) 7B-9
OUTPUT SHAFT SPEED SENSOR (A / T VSS)
The output shaft speed sensor consists of a magnetic core with
magnet and coil. It is mounted on transmission case with 0.6 mm
(0.024 in.) air gap between the core end and countershaft gear
tooth.
While the countershaft rotates, magnetic flux is cut by gear tooth
thus a pulse is generated in the sensor coil according to the speed.
And then, the pulse is transmitted to engine control module as
speed signal.
AUTOMATIC SHIFT DIAGRAM
Automatic shift schedule as a result of shift control is shown below. In case that selector lever is shifted to L range
at a higher than 37 km / h (23 mile / h) (G10 engine model), 40 km / h (25 mile / h) (G13 engine model) speed, 2nd
gear is operated and then down shifts to 1st at a speed lower than that. No up shift is available in L range.