Valve SUZUKI SWIFT 2000 1.G SF310 Service Owner's Manual
[x] Cancel search | Manufacturer: SUZUKI, Model Year: 2000, Model line: SWIFT, Model: SUZUKI SWIFT 2000 1.GPages: 557, PDF Size: 14.35 MB
Page 86 of 557
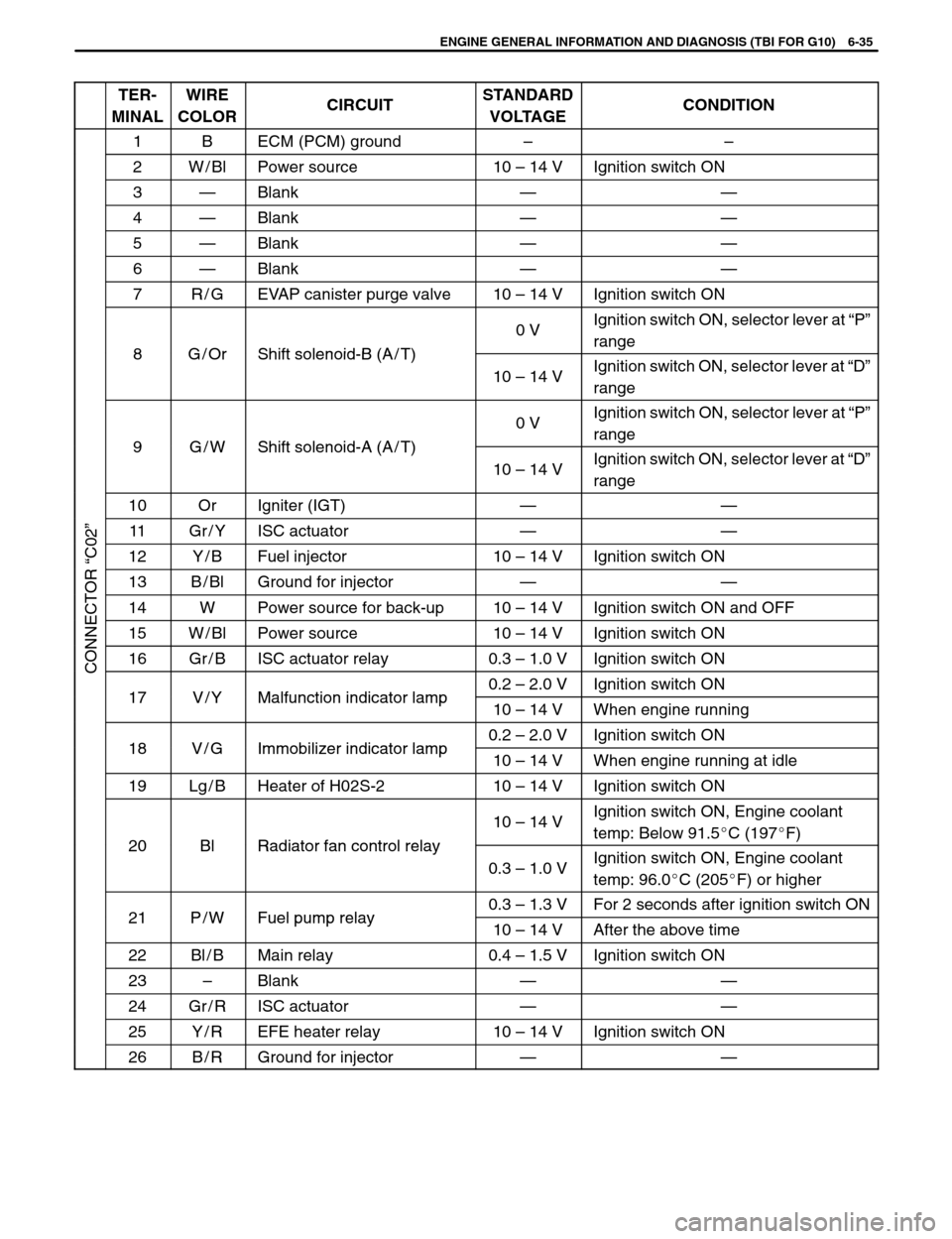
ENGINE GENERAL INFORMATION AND DIAGNOSIS (TBI FOR G10) 6-35
CONNECTOR “C02”
TER-
MINALWIRE
COLORCIRCUITSTANDARD
VOLTAGECONDITION
1BECM (PCM) ground––
2W/BlPower source10 – 14 VIgnition switch ON
3—Blank——
4—Blank——
5—Blank——
6—Blank——
7R/GEVAP canister purge valve10 – 14 VIgnition switch ON
8G/OrShift solenoid B (A / T)
0 VIgnition switch ON, selector lever at “P”
range
8G/OrShift solenoid-B (A / T)
10 – 14 VIgnition switch ON, selector lever at “D”
range
9G/WShift solenoid A (A / T)
0 VIgnition switch ON, selector lever at “P”
range
9G/WShift solenoid-A (A / T)
10 – 14 VIgnition switch ON, selector lever at “D”
range
10OrIgniter (IGT)——
11Gr / YISC actuator——
12Y/BFuel injector10 – 14 VIgnition switch ON
13B/BlGround for injector——
14WPower source for back-up10 – 14 VIgnition switch ON and OFF
15W/BlPower source10 – 14 VIgnition switch ON
16Gr / BISC actuator relay0.3 – 1.0 VIgnition switch ON
17V/YMalfunction indicator lamp0.2 – 2.0 VIgnition switch ON17V/YMalfunction indicator lamp10 – 14 VWhen engine running
18V/GImmobilizer indicator lamp0.2 – 2.0 VIgnition switch ON18V/GImmobilizer indicator lamp10 – 14 VWhen engine running at idle
19Lg / BHeater of H02S-210 – 14 VIgnition switch ON
20BlRadiator fan control relay
10 – 14 VIgnition switch ON, Engine coolant
temp: Below 91.5C (197F)
20BlRadiator fan control relay
0.3 – 1.0 VIgnition switch ON, Engine coolant
temp: 96.0C (205F) or higher
21P/WFuelpumprelay0.3 – 1.3 VFor 2 seconds after ignition switch ON21P/WFuel pump relay10 – 14 VAfter the above time
22Bl / BMain relay0.4 – 1.5 VIgnition switch ON
23–Blank——
24Gr / RISC actuator——
25Y/REFE heater relay10 – 14 VIgnition switch ON
26B/RGround for injector——
Page 87 of 557
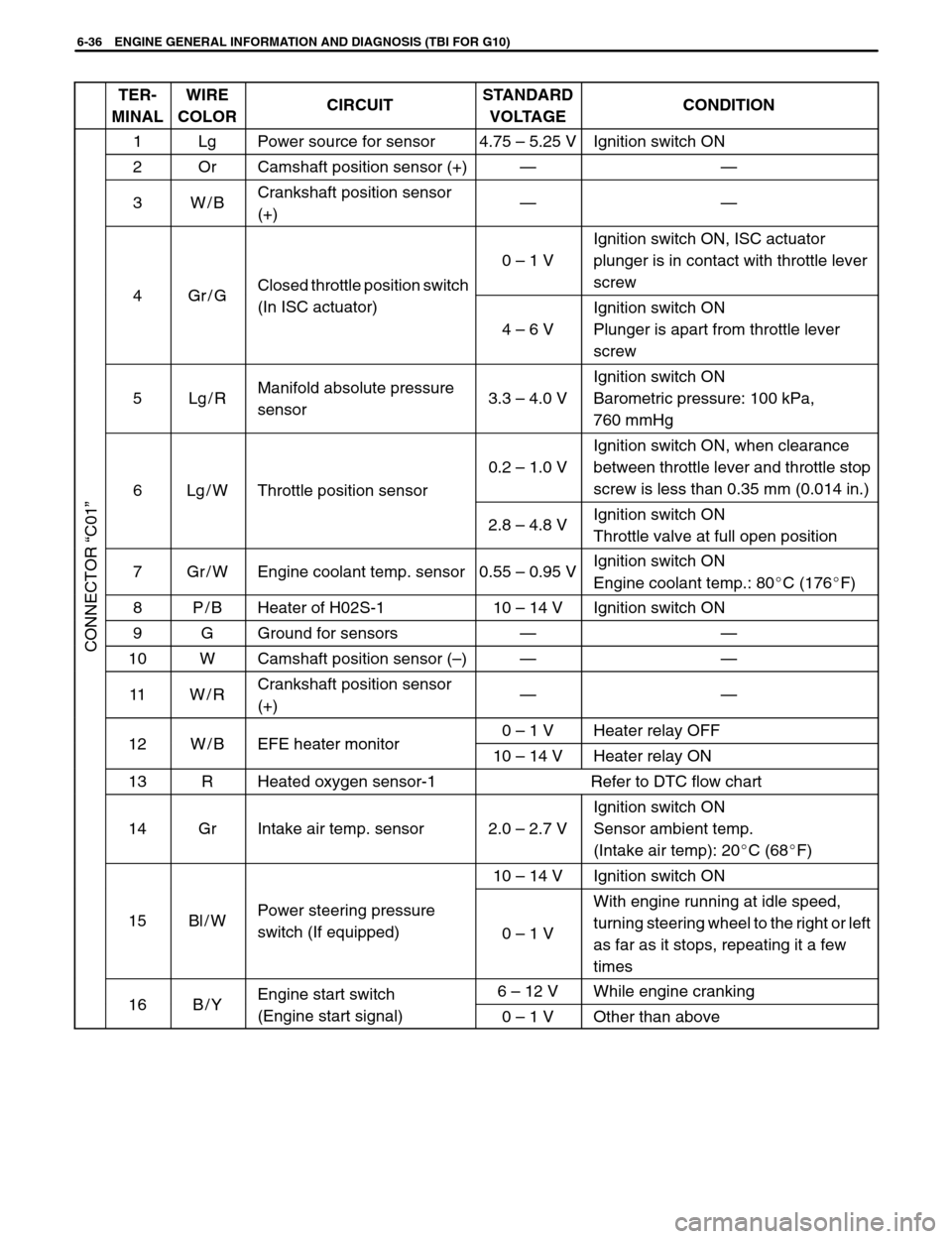
6-36 ENGINE GENERAL INFORMATION AND DIAGNOSIS (TBI FOR G10)
CONNECTOR “C01”
TER-
MINALWIRE
COLORCIRCUITSTANDARD
VOLTAGECONDITION
1LgPower source for sensor4.75 – 5.25 VIgnition switch ON
2OrCamshaft position sensor (+)——
3W/BCrankshaft position sensor
(+)——
4Gr / GClosed throttle position switch
0 – 1 V
Ignition switch ON, ISC actuator
plunger is in contact with throttle lever
screw
4Gr / G(In ISC actuator)
4 – 6 V
Ignition switch ON
Plunger is apart from throttle lever
screw
5Lg / RManifold absolute pressure
sensor3.3 – 4.0 V
Ignition switch ON
Barometric pressure: 100 kPa,
760 mmHg
6Lg / WThrottle position sensor
0.2 – 1.0 V
Ignition switch ON, when clearance
between throttle lever and throttle stop
screw is less than 0.35 mm (0.014 in.)
2.8 – 4.8 VIgnition switch ON
Throttle valve at full open position
7Gr / WEngine coolant temp. sensor0.55 – 0.95 VIgnition switch ON
Engine coolant temp.: 80C (176F)
8P/BHeater of H02S-110 – 14 VIgnition switch ON
9GGround for sensors——
10WCamshaft position sensor (–)——
11W/RCrankshaft position sensor
(+)——
12W/BEFE heater monitor0 – 1 VHeater relay OFF12W/BEFE heater monitor10 – 14 VHeater relay ON
13RHeated oxygen sensor-1Refer to DTC flow chart
14GrIntake air temp. sensor2.0 – 2.7 V
Ignition switch ON
Sensor ambient temp.
(Intake air temp): 20C (68F)
10 – 14 VIgnition switch ON
15Bl / WPower steering pressure
switch (If equipped)
0 – 1 V
With engine running at idle speed,
turning steering wheel to the right or left
as far as it stops, repeating it a few
times
16B/YEngine start switch6 – 12 VWhile engine cranking16B/Yg
(Engine start signal)0 – 1 VOther than above
Page 89 of 557
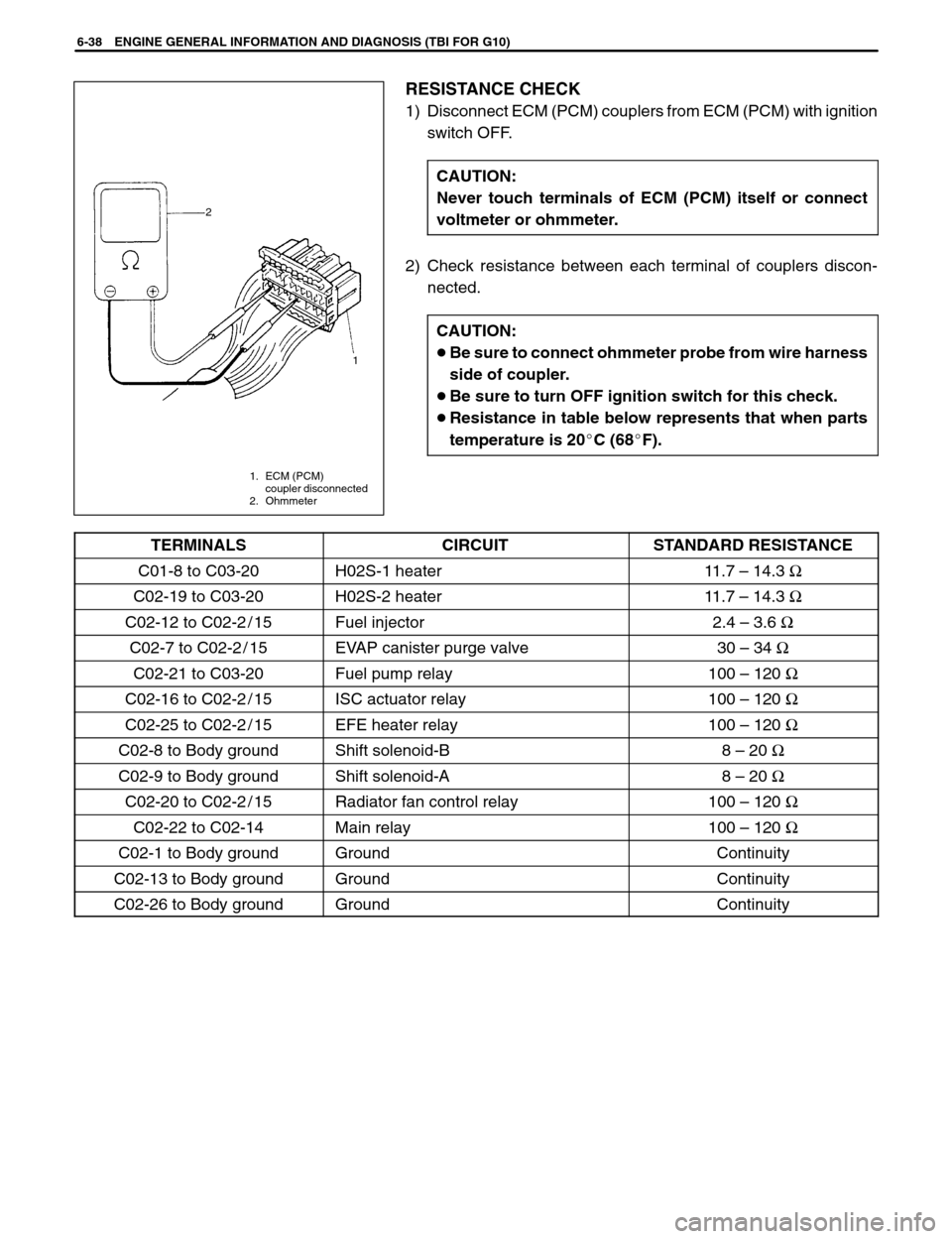
6-38 ENGINE GENERAL INFORMATION AND DIAGNOSIS (TBI FOR G10)
1 2
1. ECM (PCM)
coupler disconnected
2. Ohmmeter
RESISTANCE CHECK
1) Disconnect ECM (PCM) couplers from ECM (PCM) with ignition
switch OFF.
CAUTION:
Never touch terminals of ECM (PCM) itself or connect
voltmeter or ohmmeter.
2) Check resistance between each terminal of couplers discon-
nected.
CAUTION:
Be sure to connect ohmmeter probe from wire harness
side of coupler.
Be sure to turn OFF ignition switch for this check.
Resistance in table below represents that when parts
temperature is 20C (68F).
TERMINALSCIRCUITSTANDARD RESISTANCE
C01-8 to C03-20H02S-1 heater11.7 – 14.3 Ω
C02-19 to C03-20H02S-2 heater11.7 – 14.3 Ω
C02-12 to C02-2 / 15Fuel injector2.4 – 3.6 Ω
C02-7 to C02-2 / 15EVAP canister purge valve30 – 34 Ω
C02-21 to C03-20Fuel pump relay100 – 120 Ω
C02-16 to C02-2 / 15ISC actuator relay100 – 120 Ω
C02-25 to C02-2 / 15EFE heater relay100 – 120 Ω
C02-8 to Body groundShift solenoid-B8 – 20 Ω
C02-9 to Body groundShift solenoid-A8 – 20 Ω
C02-20 to C02-2 / 15Radiator fan control relay100 – 120 Ω
C02-22 to C02-14Main relay100 – 120 Ω
C02-1 to Body groundGroundContinuity
C02-13 to Body groundGroundContinuity
C02-26 to Body groundGroundContinuity
Page 90 of 557
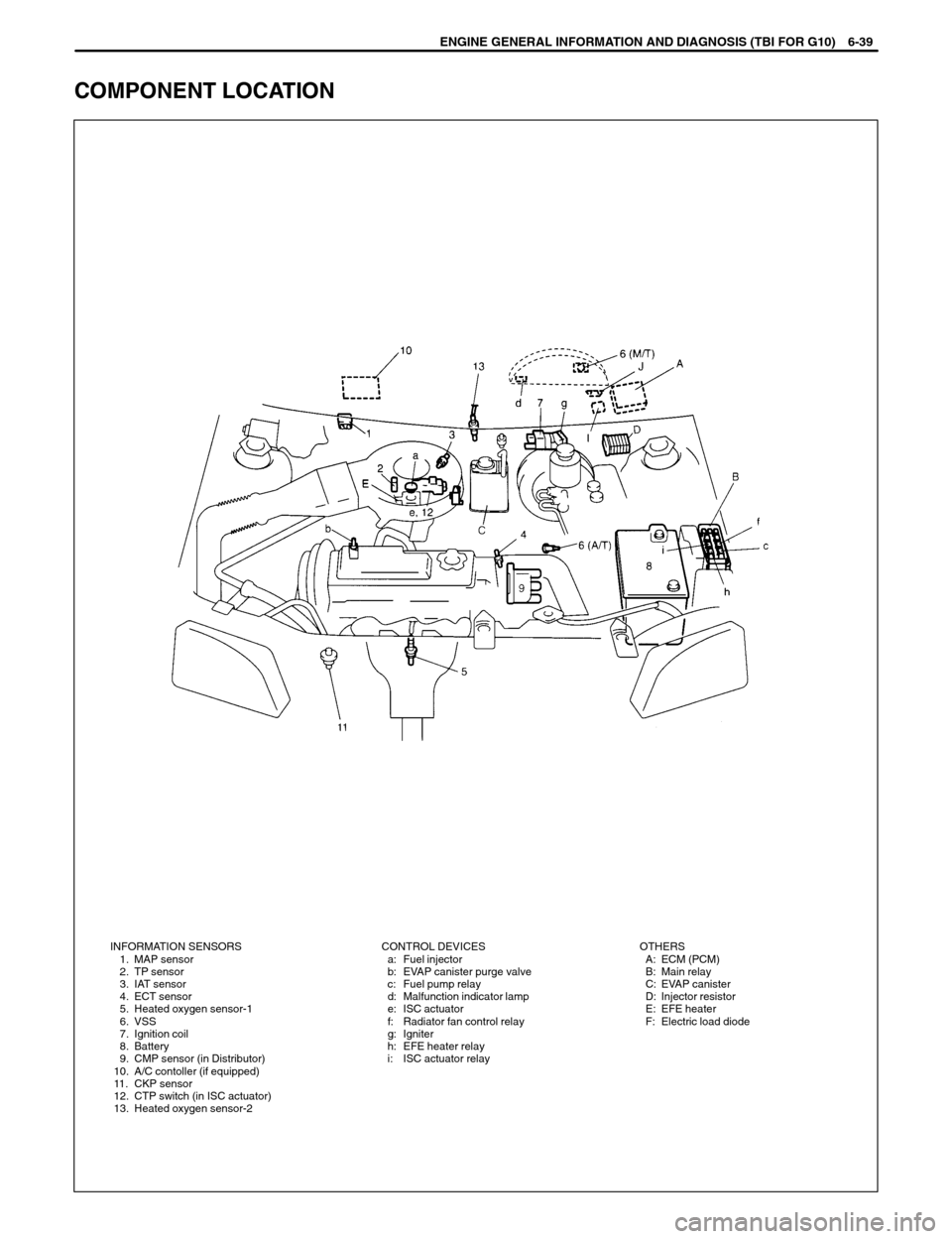
ENGINE GENERAL INFORMATION AND DIAGNOSIS (TBI FOR G10) 6-39
INFORMATION SENSORS
-1. MAP sensor
-2. TP sensor
-3. IAT sensor
-4. ECT sensor
-5. Heated oxygen sensor-1
-6. VSS
-7. Ignition coil
-8. Battery
-9. CMP sensor (in Distributor)
-10. A/C contoller (if equipped)
-11. CKP sensor
-12. CTP switch (in ISC actuator)
-13. Heated oxygen sensor-2OTHERS
A: ECM (PCM)
B: Main relay
C: EVAP canister
D: Injector resistor
E: EFE heater
F: Electric load diode CONTROL DEVICES
a: Fuel injector
b: EVAP canister purge valve
c: Fuel pump relay
d: Malfunction indicator lamp
e: ISC actuator
f: Radiator fan control relay
g: Igniter
h: EFE heater relay
i: ISC actuator relay
COMPONENT LOCATION
Page 102 of 557
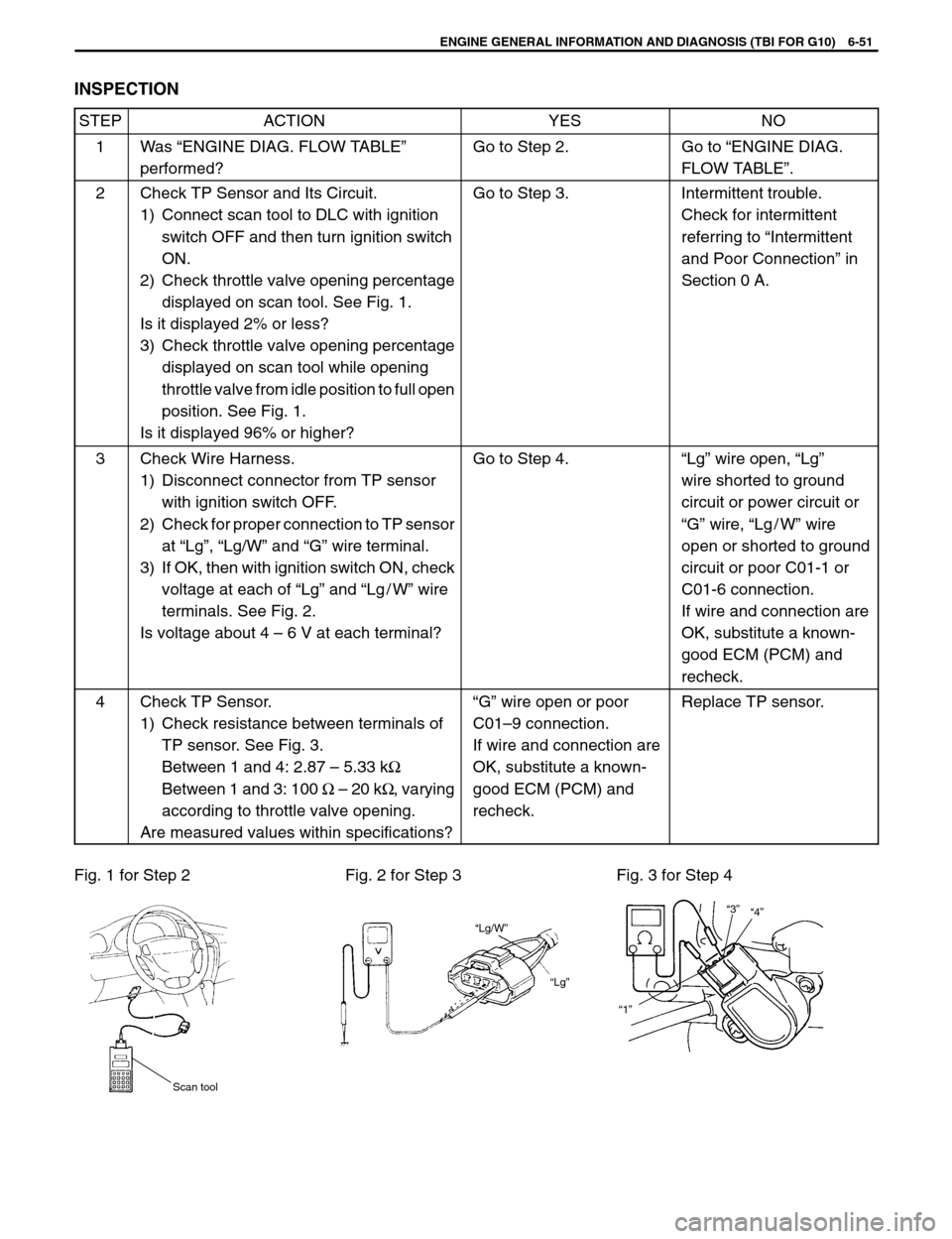
ENGINE GENERAL INFORMATION AND DIAGNOSIS (TBI FOR G10) 6-51
Fig. 1 for Step 2 Fig. 2 for Step 3 Fig. 3 for Step 4
Scan tool
“Lg” “Lg/W”
“3”“4”
“1”
INSPECTION
STEPACTIONYESNO
1Was “ENGINE DIAG. FLOW TABLE”
performed?Go to Step 2.Go to “ENGINE DIAG.
FLOW TABLE”.
2Check TP Sensor and Its Circuit.
1) Connect scan tool to DLC with ignition
switch OFF and then turn ignition switch
ON.
2) Check throttle valve opening percentage
displayed on scan tool. See Fig. 1.
Is it displayed 2% or less?
3) Check throttle valve opening percentage
displayed on scan tool while opening
throttle valve from idle position to full open
position. See Fig. 1.
Is it displayed 96% or higher?Go to Step 3.Intermittent trouble.
Check for intermittent
referring to “Intermittent
and Poor Connection” in
Section 0 A.
3Check Wire Harness.
1) Disconnect connector from TP sensor
with ignition switch OFF.
2) Check for proper connection to TP sensor
at “Lg”, “Lg/W” and “G” wire terminal.
3) If OK, then with ignition switch ON, check
voltage at each of “Lg” and “Lg / W” wire
terminals. See Fig. 2.
Is voltage about 4 – 6 V at each terminal?Go to Step 4.“Lg” wire open, “Lg”
wire shorted to ground
circuit or power circuit or
“G” wire, “Lg / W” wire
open or shorted to ground
circuit or poor C01-1 or
C01-6 connection.
If wire and connection are
OK, substitute a known-
good ECM (PCM) and
recheck.
4Check TP Sensor.
1) Check resistance between terminals of
TP sensor. See Fig. 3.
Between 1 and 4: 2.87 – 5.33 kΩ
Between 1 and 3: 100 Ω – 20 kΩ, varying
according to throttle valve opening.
Are measured values within specifications?“G” wire open or poor
C01–9 connection.
If wire and connection are
OK, substitute a known-
good ECM (PCM) and
recheck.Replace TP sensor.
Page 103 of 557
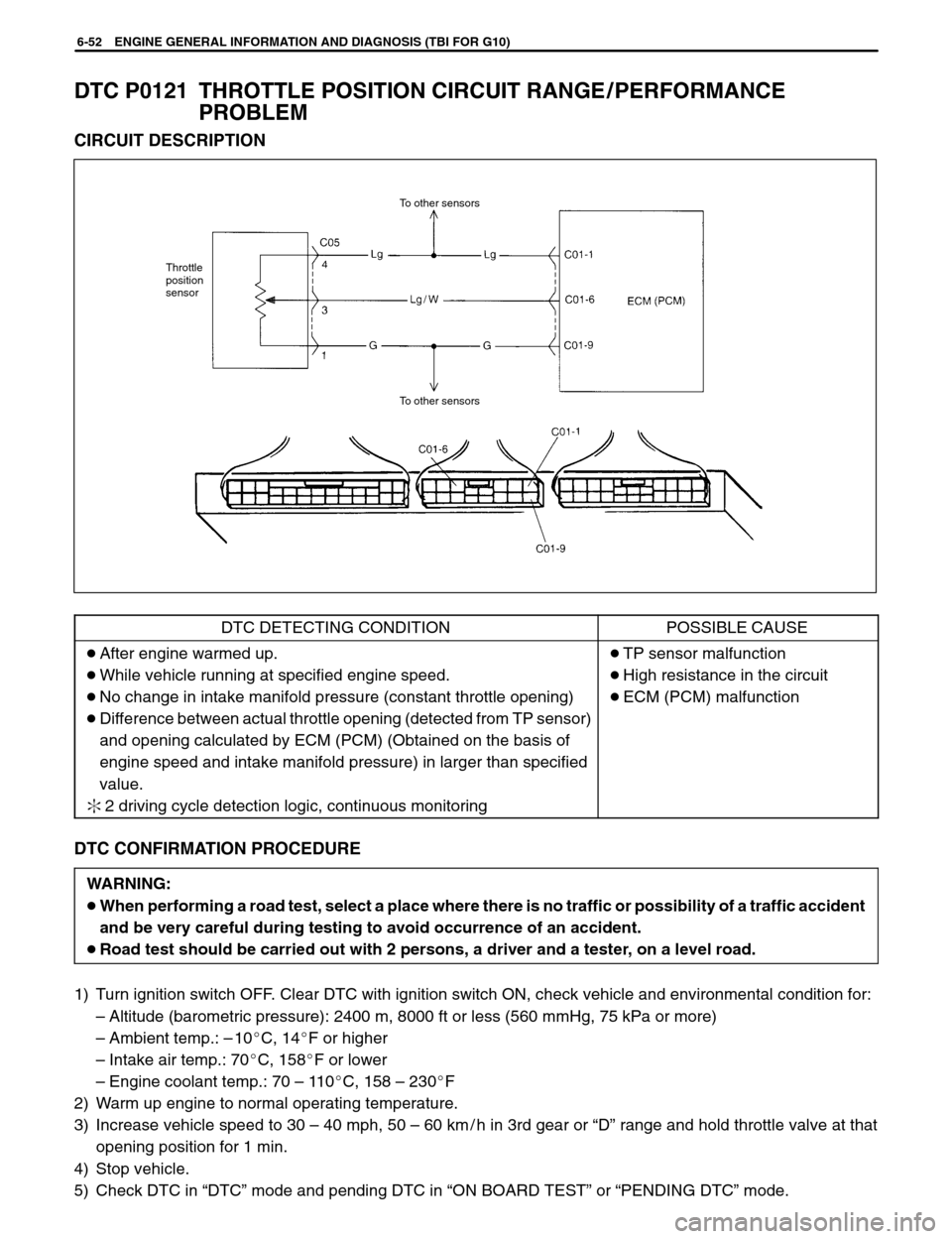
To other sensors Throttle
position
sensorTo other sensors
6-52 ENGINE GENERAL INFORMATION AND DIAGNOSIS (TBI FOR G10)
DTC P0121 THROTTLE POSITION CIRCUIT RANGE / PERFORMANCE
PROBLEM
CIRCUIT DESCRIPTION
DTC DETECTING CONDITIONPOSSIBLE CAUSE
After engine warmed up.
While vehicle running at specified engine speed.
No change in intake manifold pressure (constant throttle opening)
Difference between actual throttle opening (detected from TP sensor)
and opening calculated by ECM (PCM) (Obtained on the basis of
engine speed and intake manifold pressure) in larger than specified
value.
2 driving cycle detection logic, continuous monitoringTP sensor malfunction
High resistance in the circuit
ECM (PCM) malfunction
DTC CONFIRMATION PROCEDURE
WARNING:
When performing a road test, select a place where there is no traffic or possibility of a traffic accident
and be very careful during testing to avoid occurrence of an accident.
Road test should be carried out with 2 persons, a driver and a tester, on a level road.
1) Turn ignition switch OFF. Clear DTC with ignition switch ON, check vehicle and environmental condition for:
–Altitude (barometric pressure): 2400 m, 8000 ft or less (560 mmHg, 75 kPa or more)
–Ambient temp.: –10C, 14F or higher
–Intake air temp.: 70C, 158F or lower
–Engine coolant temp.: 70 – 11 0C, 158 – 230F
2) Warm up engine to normal operating temperature.
3) Increase vehicle speed to 30 – 40 mph, 50 – 60 km / h in 3rd gear or “D” range and hold throttle valve at that
opening position for 1 min.
4) Stop vehicle.
5) Check DTC in “DTC” mode and pending DTC in “ON BOARD TEST” or “PENDING DTC” mode.
Page 104 of 557
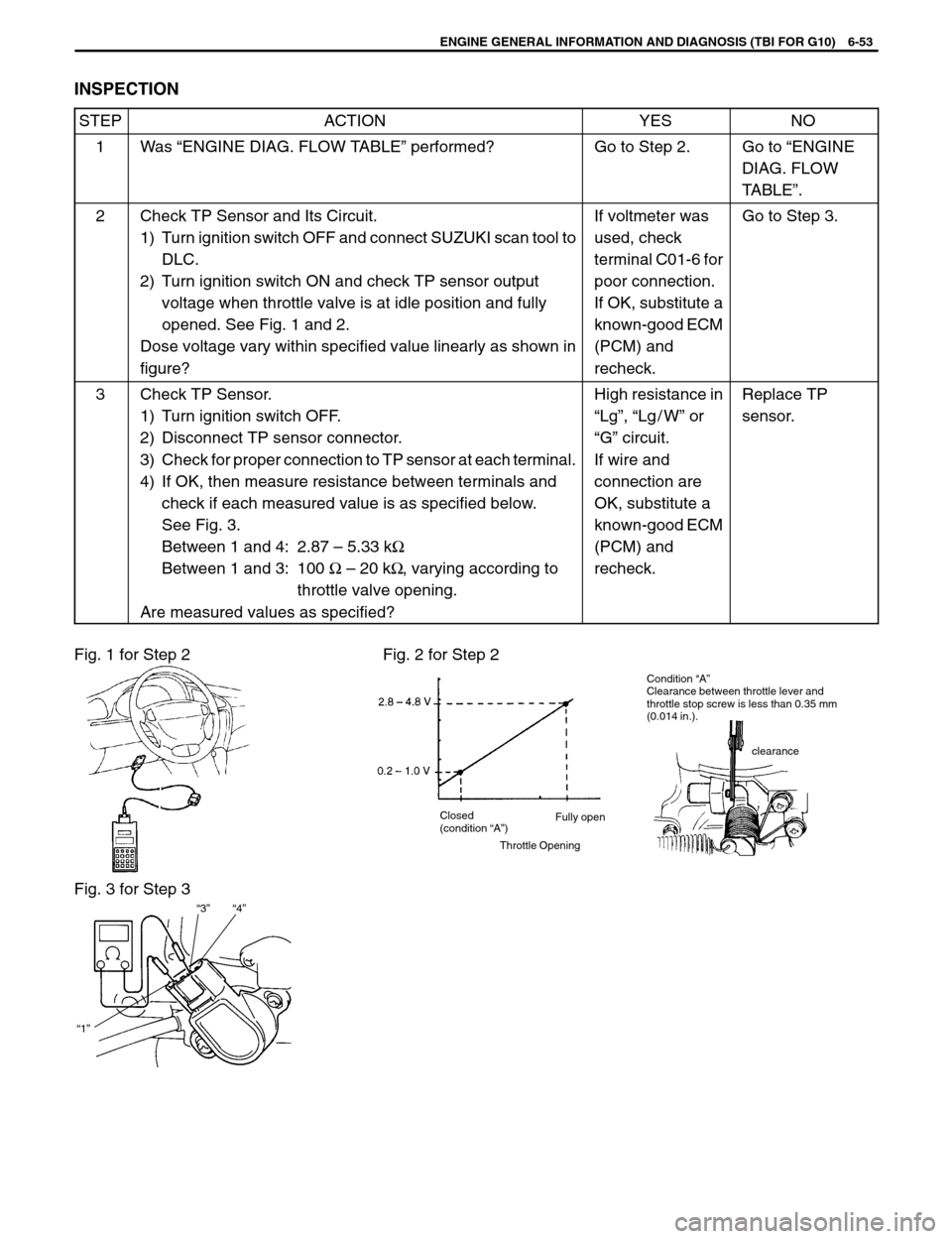
ENGINE GENERAL INFORMATION AND DIAGNOSIS (TBI FOR G10) 6-53
Fig. 1 for Step 2 Fig. 2 for Step 2
Fig. 3 for Step 3
Closed
(condition “A”)Fully open
Throttle Opening
Condition “A”
Clearance between throttle lever and
throttle stop screw is less than 0.35 mm
(0.014 in.).
clearance
“1”“3”“4”
INSPECTION
STEPACTIONYESNO
1Was “ENGINE DIAG. FLOW TABLE” performed?Go to Step 2.Go to “ENGINE
DIAG. FLOW
TABLE”.
2Check TP Sensor and Its Circuit.
1) Turn ignition switch OFF and connect SUZUKI scan tool to
DLC.
2) Turn ignition switch ON and check TP sensor output
voltage when throttle valve is at idle position and fully
opened. See Fig. 1 and 2.
Dose voltage vary within specified value linearly as shown in
figure?If voltmeter was
used, check
terminal C01-6 for
poor connection.
If OK, substitute a
known-good ECM
(PCM) and
recheck.Go to Step 3.
3Check TP Sensor.
1) Turn ignition switch OFF.
2) Disconnect TP sensor connector.
3) Check for proper connection to TP sensor at each terminal.
4) If OK, then measure resistance between terminals and
check if each measured value is as specified below.
See Fig. 3.
Between 1 and 4: 2.87 – 5.33 kΩ
Between 1 and 3: 100 Ω – 20 kΩ, varying according to
throttle valve opening.
Are measured values as specified?High resistance in
“Lg”, “Lg / W” or
“G” circuit.
If wire and
connection are
OK, substitute a
known-good ECM
(PCM) and
recheck.Replace TP
sensor.
Page 115 of 557
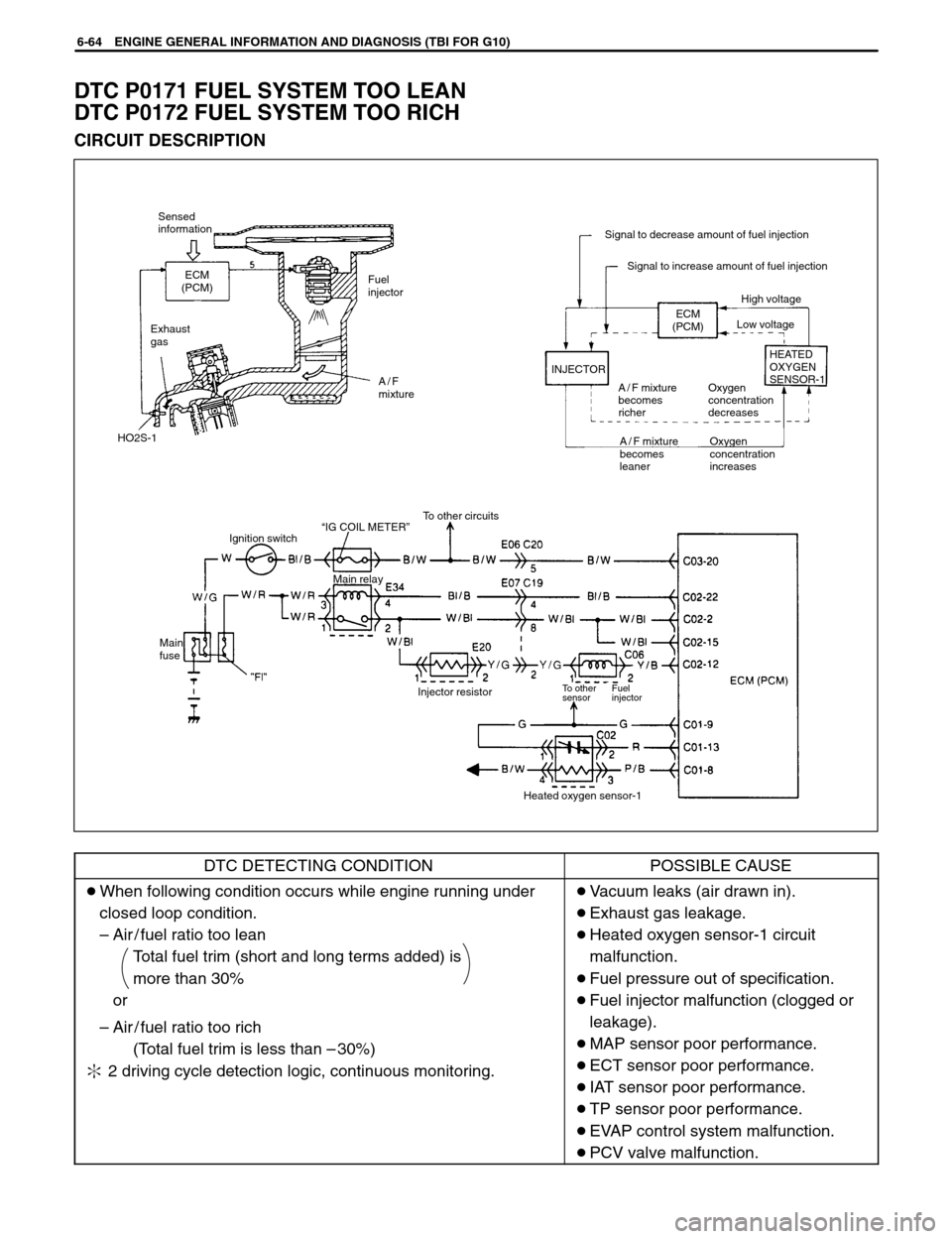
6-64 ENGINE GENERAL INFORMATION AND DIAGNOSIS (TBI FOR G10)
Sensed
information
Exhaust
gasFuel
injector
A/F
mixtureSignal to decrease amount of fuel injection
Signal to increase amount of fuel injection
High voltage
Low voltage
INJECTORHEATED
OXYGEN
SENSOR-1
A / F mixture
becomes
richerOxygen
concentration
decreases
A / F mixture
becomes
leanerOxygen
concentration
increases ECM
(PCM)
ECM
(PCM)
Main
fuseIgnition switch“IG COIL METER”
Main relayTo other circuits
Injector resistor
To other
sensorFuel
injector
Heated oxygen sensor-1
HO2S-1
DTC P0171 FUEL SYSTEM TOO LEAN
DTC P0172 FUEL SYSTEM TOO RICH
CIRCUIT DESCRIPTION
DTC DETECTING CONDITIONPOSSIBLE CAUSE
When following condition occurs while engine running under
closed loop condition.
–Air / fuel ratio too lean
Total fuel trim (short and long terms added) is
more than 30%
or
–Air / fuel ratio too rich
(Total fuel trim is less than –30%)
2 driving cycle detection logic, continuous monitoring.Vacuum leaks (air drawn in).
Exhaust gas leakage.
Heated oxygen sensor-1 circuit
malfunction.
Fuel pressure out of specification.
Fuel injector malfunction (clogged or
leakage).
MAP sensor poor performance.
ECT sensor poor performance.
IAT sensor poor performance.
TP sensor poor performance.
EVAP control system malfunction.
PCV valve malfunction.
Page 117 of 557
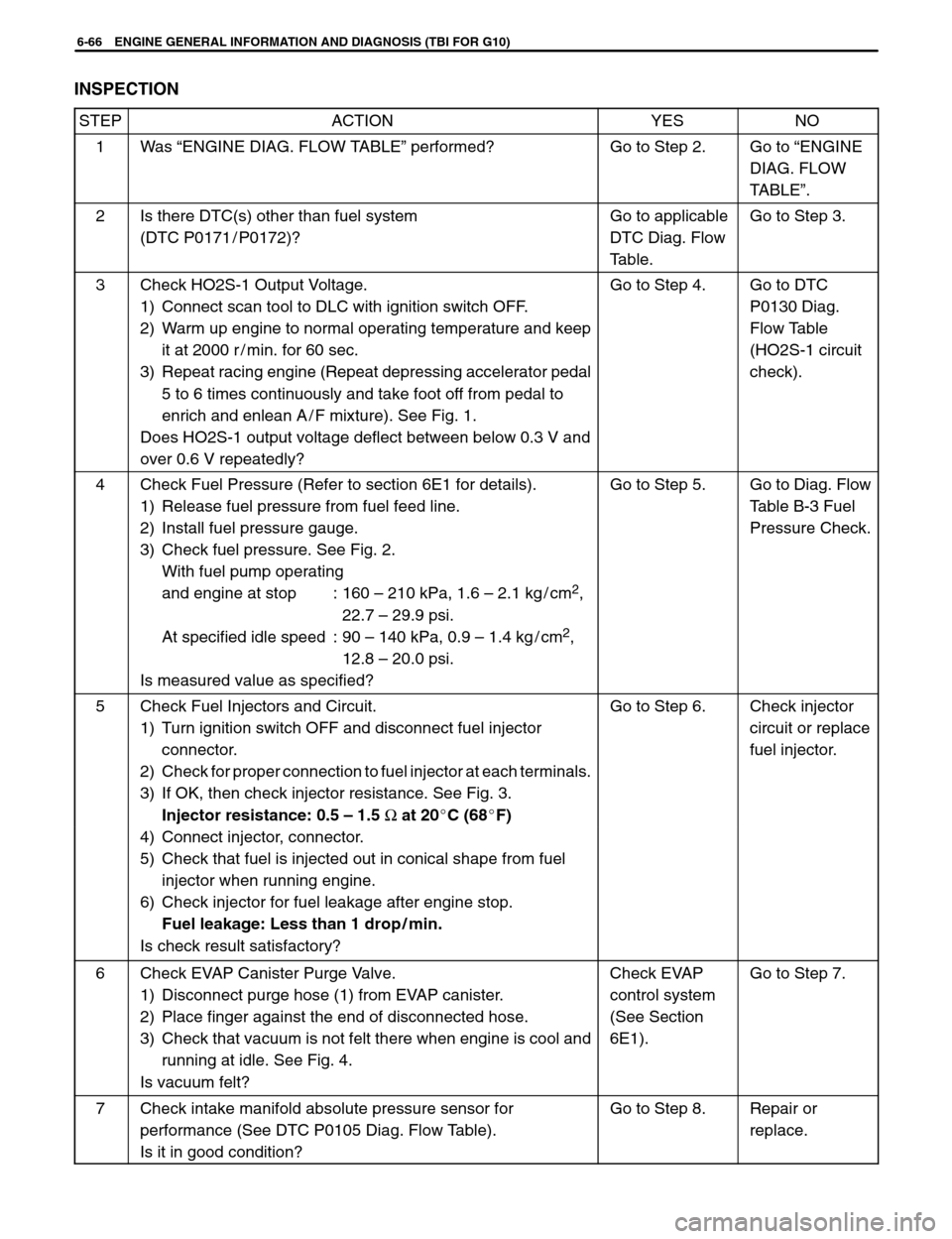
6-66 ENGINE GENERAL INFORMATION AND DIAGNOSIS (TBI FOR G10)
INSPECTION
STEPACTIONYESNO
1Was “ENGINE DIAG. FLOW TABLE” performed?Go to Step 2.Go to “ENGINE
DIAG. FLOW
TABLE”.
2Is there DTC(s) other than fuel system
(DTC P0171 / P0172)?Go to applicable
DTC Diag. Flow
Table.Go to Step 3.
3Check HO2S-1 Output Voltage.
1) Connect scan tool to DLC with ignition switch OFF.
2) Warm up engine to normal operating temperature and keep
it at 2000 r / min. for 60 sec.
3) Repeat racing engine (Repeat depressing accelerator pedal
5 to 6 times continuously and take foot off from pedal to
enrich and enlean A / F mixture). See Fig. 1.
Does HO2S-1 output voltage deflect between below 0.3 V and
over 0.6 V repeatedly?Go to Step 4.Go to DTC
P0130 Diag.
Flow Table
(HO2S-1 circuit
check).
4Check Fuel Pressure (Refer to section 6E1 for details).
1) Release fuel pressure from fuel feed line.
2) Install fuel pressure gauge.
3) Check fuel pressure. See Fig. 2.
With fuel pump operating
and engine at stop : 160 – 210 kPa, 1.6 – 2.1 kg / cm
2,
22.7 – 29.9 psi.
At specified idle speed : 90 – 140 kPa, 0.9 – 1.4 kg / cm
2,
12.8 – 20.0 psi.
Is measured value as specified?
Go to Step 5.Go to Diag. Flow
Table B-3 Fuel
Pressure Check.
5Check Fuel Injectors and Circuit.
1) Turn ignition switch OFF and disconnect fuel injector
connector.
2) Check for proper connection to fuel injector at each terminals.
3) If OK, then check injector resistance. See Fig. 3.
Injector resistance: 0.5 – 1.5 Ω at 20C (68F)Go to Step 6.Check injector
circuit or replace
fuel injector.
4) Connect injector, connector.
5) Check that fuel is injected out in conical shape from fuel
injector when running engine.
6) Check injector for fuel leakage after engine stop.
Fuel leakage: Less than 1 drop / min.
Is check result satisfactory?
6Check EVAP Canister Purge Valve.
1) Disconnect purge hose (1) from EVAP canister.
2) Place finger against the end of disconnected hose.
3) Check that vacuum is not felt there when engine is cool and
running at idle. See Fig. 4.
Is vacuum felt?Check EVAP
control system
(See Section
6E1).Go to Step 7.
7Check intake manifold absolute pressure sensor for
performance (See DTC P0105 Diag. Flow Table).
Is it in good condition?Go to Step 8.Repair or
replace.
Page 118 of 557
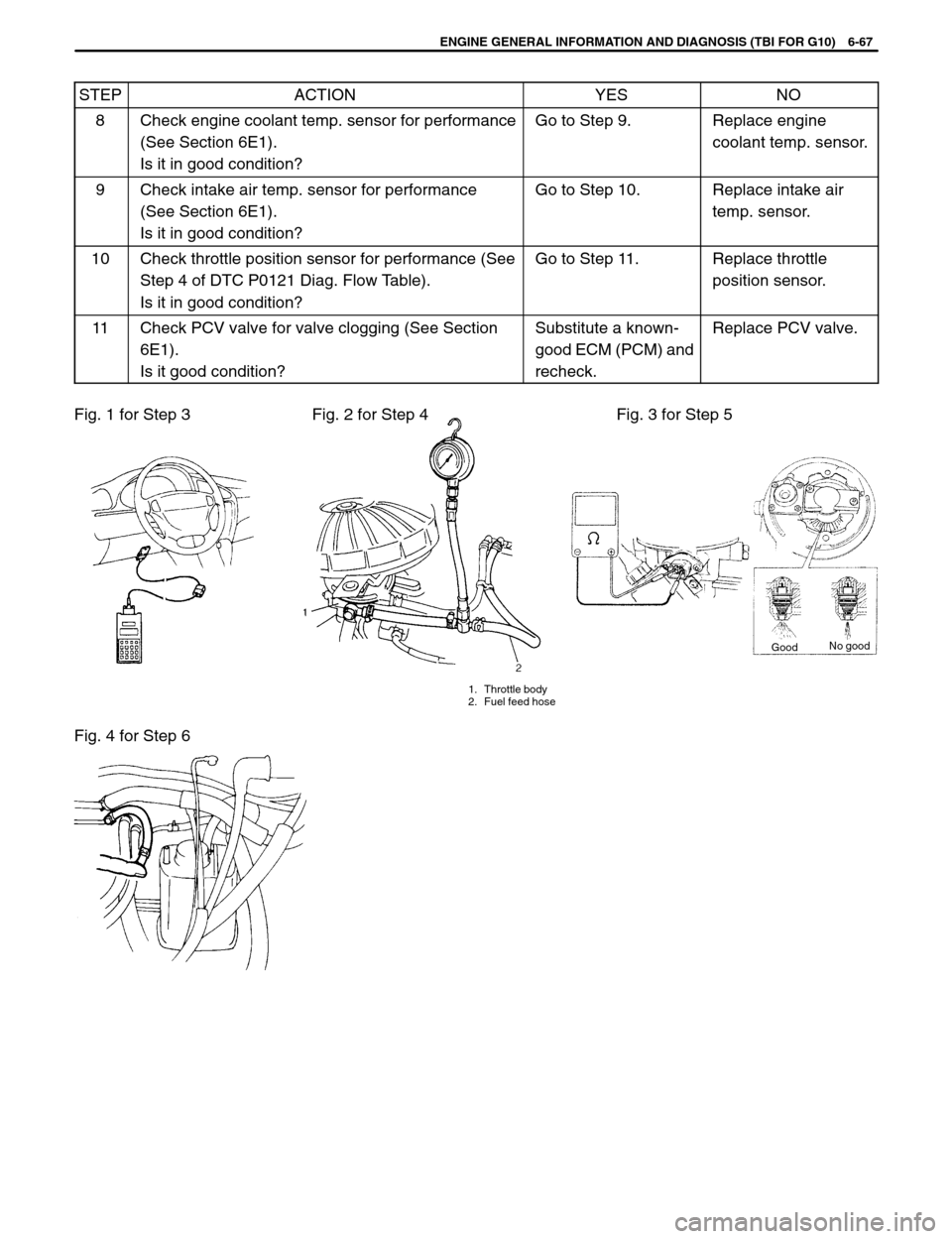
ENGINE GENERAL INFORMATION AND DIAGNOSIS (TBI FOR G10) 6-67
Fig. 1 for Step 3 Fig. 2 for Step 4 Fig. 3 for Step 5
Fig. 4 for Step 6
1. Throttle body
2. Fuel feed hose
GoodNo good
STEPACTIONYESNO
8Check engine coolant temp. sensor for performance
(See Section 6E1).
Is it in good condition?Go to Step 9.Replace engine
coolant temp. sensor.
9Check intake air temp. sensor for performance
(See Section 6E1).
Is it in good condition?Go to Step 10.Replace intake air
temp. sensor.
10Check throttle position sensor for performance (See
Step 4 of DTC P0121 Diag. Flow Table).
Is it in good condition?Go to Step 11.Replace throttle
position sensor.
11Check PCV valve for valve clogging (See Section
6E1).
Is it good condition?Substitute a known-
good ECM (PCM) and
recheck.Replace PCV valve.