battery SUZUKI SWIFT 2000 1.G SF310 Service Repair Manual
[x] Cancel search | Manufacturer: SUZUKI, Model Year: 2000, Model line: SWIFT, Model: SUZUKI SWIFT 2000 1.GPages: 557, PDF Size: 14.35 MB
Page 319 of 557
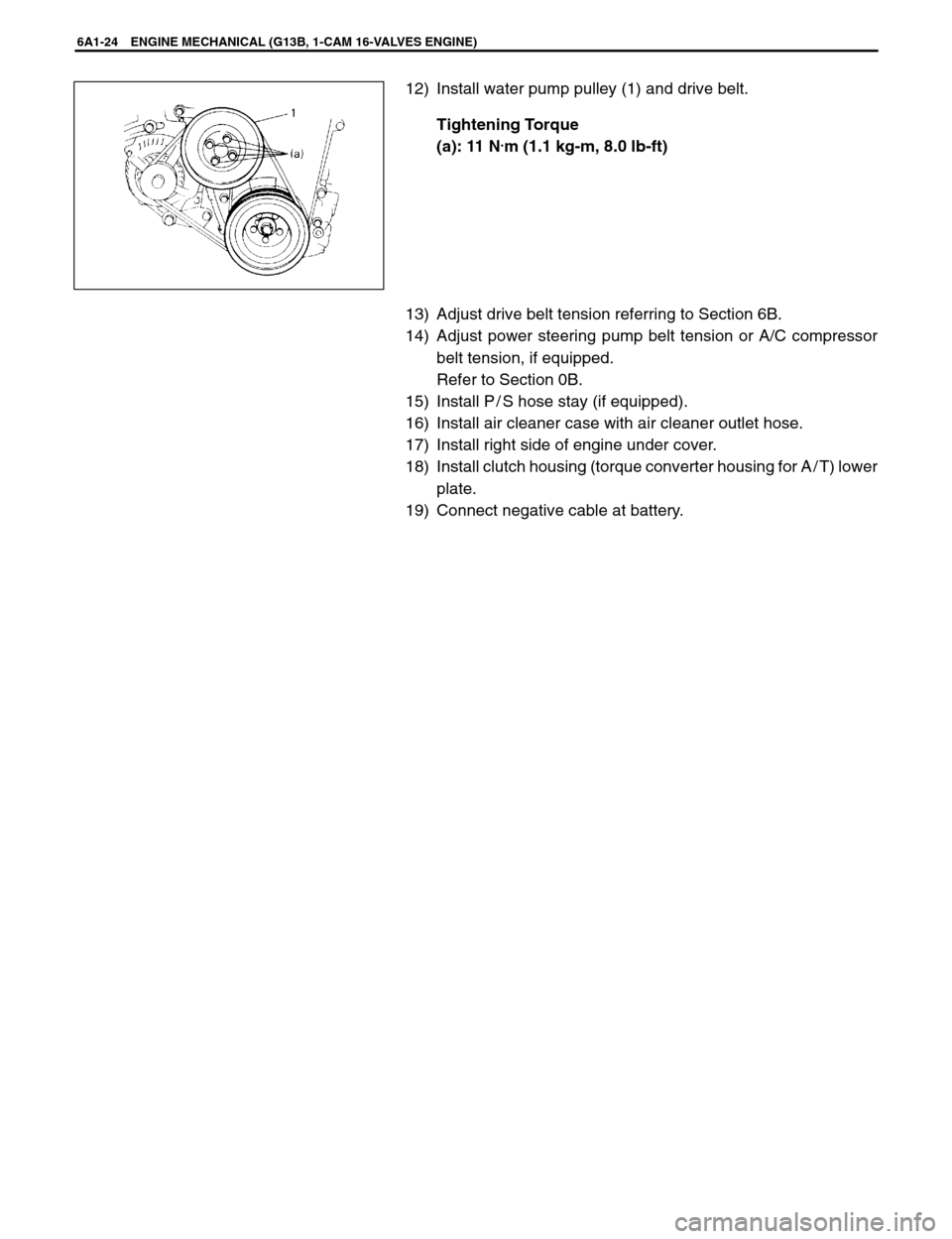
6A1-24 ENGINE MECHANICAL (G13B, 1-CAM 16-VALVES ENGINE)
12) Install water pump pulley (1) and drive belt.
Tightening Torque
(a): 11 N
.m (1.1 kg-m, 8.0 lb-ft)
13) Adjust drive belt tension referring to Section 6B.
14) Adjust power steering pump belt tension or A/C compressor
belt tension, if equipped.
Refer to Section 0B.
15) Install P / S hose stay (if equipped).
16) Install air cleaner case with air cleaner outlet hose.
17) Install right side of engine under cover.
18) Install clutch housing (torque converter housing for A / T) lower
plate.
19) Connect negative cable at battery.
Page 323 of 557
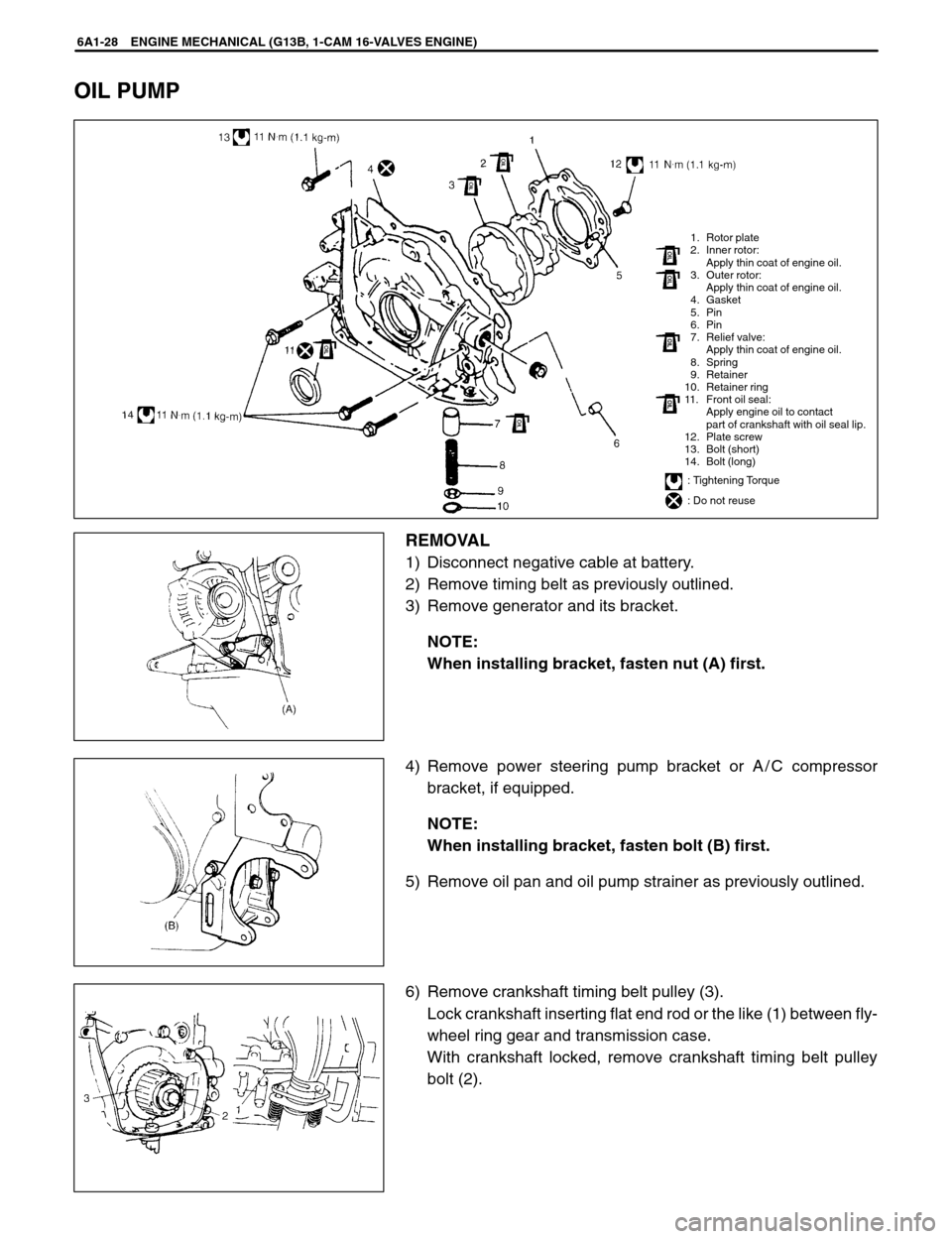
1. Rotor plate
2. Inner rotor:
Apply thin coat of engine oil.
3. Outer rotor:
Apply thin coat of engine oil.
4. Gasket
5. Pin
6. Pin
7. Relief valve:
Apply thin coat of engine oil.
8. Spring
9. Retainer
10. Retainer ring
11. Front oil seal:
Apply engine oil to contact
part of crankshaft with oil seal lip.
12. Plate screw
13. Bolt (short)
14. Bolt (long)
: Tightening Torque
: Do not reuse
6A1-28 ENGINE MECHANICAL (G13B, 1-CAM 16-VALVES ENGINE)
OIL PUMP
REMOVAL
1) Disconnect negative cable at battery.
2) Remove timing belt as previously outlined.
3) Remove generator and its bracket.
NOTE:
When installing bracket, fasten nut (A) first.
4) Remove power steering pump bracket or A / C compressor
bracket, if equipped.
NOTE:
When installing bracket, fasten bolt (B) first.
5) Remove oil pan and oil pump strainer as previously outlined.
6) Remove crankshaft timing belt pulley (3).
Lock crankshaft inserting flat end rod or the like (1) between fly-
wheel ring gear and transmission case.
With crankshaft locked, remove crankshaft timing belt pulley
bolt (2).
Page 327 of 557
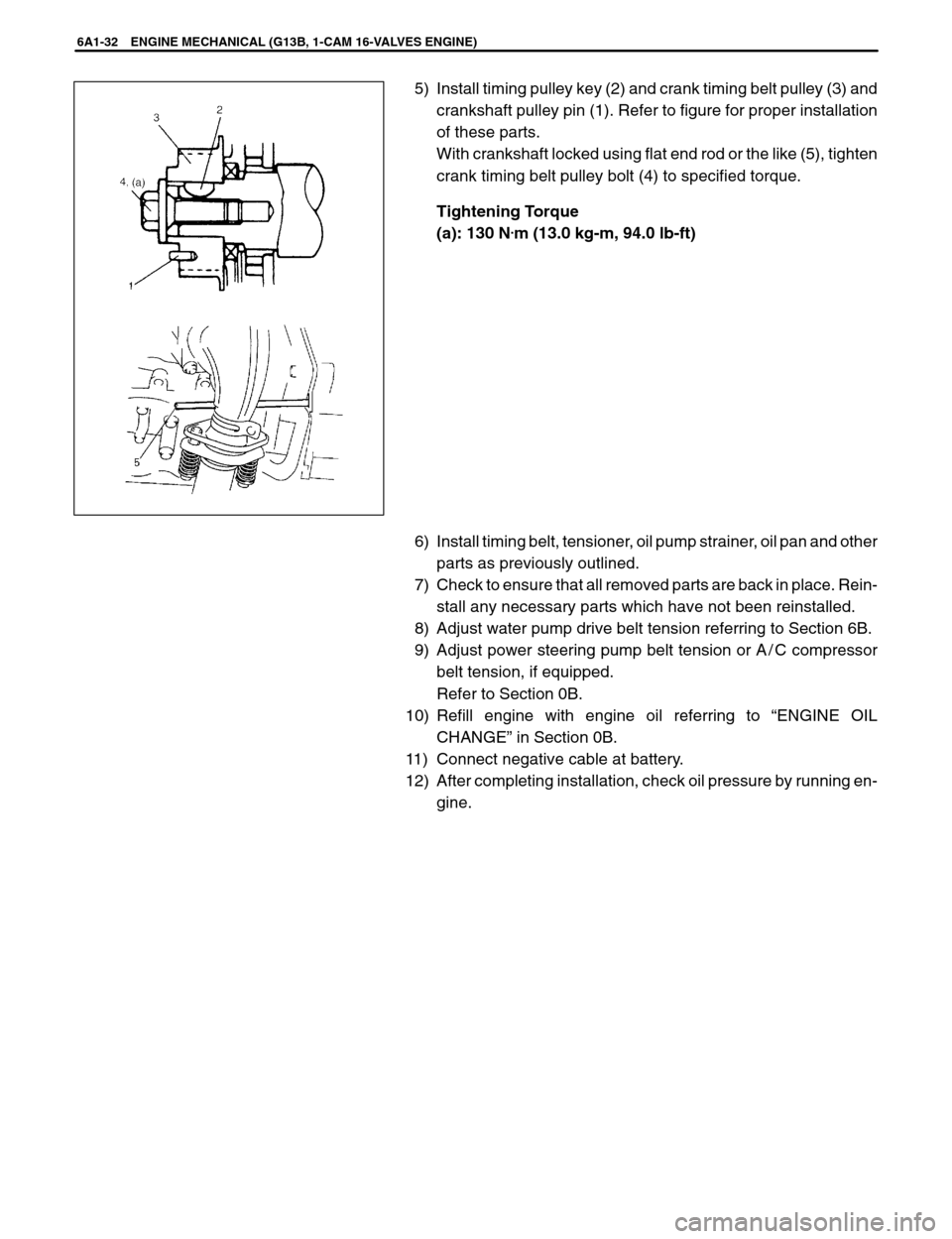
6A1-32 ENGINE MECHANICAL (G13B, 1-CAM 16-VALVES ENGINE)
5) Install timing pulley key (2) and crank timing belt pulley (3) and
crankshaft pulley pin (1). Refer to figure for proper installation
of these parts.
With crankshaft locked using flat end rod or the like (5), tighten
crank timing belt pulley bolt (4) to specified torque.
Tightening Torque
(a): 130 N
.m (13.0 kg-m, 94.0 lb-ft)
6) Install timing belt, tensioner, oil pump strainer, oil pan and other
parts as previously outlined.
7) Check to ensure that all removed parts are back in place. Rein-
stall any necessary parts which have not been reinstalled.
8) Adjust water pump drive belt tension referring to Section 6B.
9) Adjust power steering pump belt tension or A / C compressor
belt tension, if equipped.
Refer to Section 0B.
10) Refill engine with engine oil referring to “ENGINE OIL
CHANGE” in Section 0B.
11) Connect negative cable at battery.
12) After completing installation, check oil pressure by running en-
gine.
Page 328 of 557
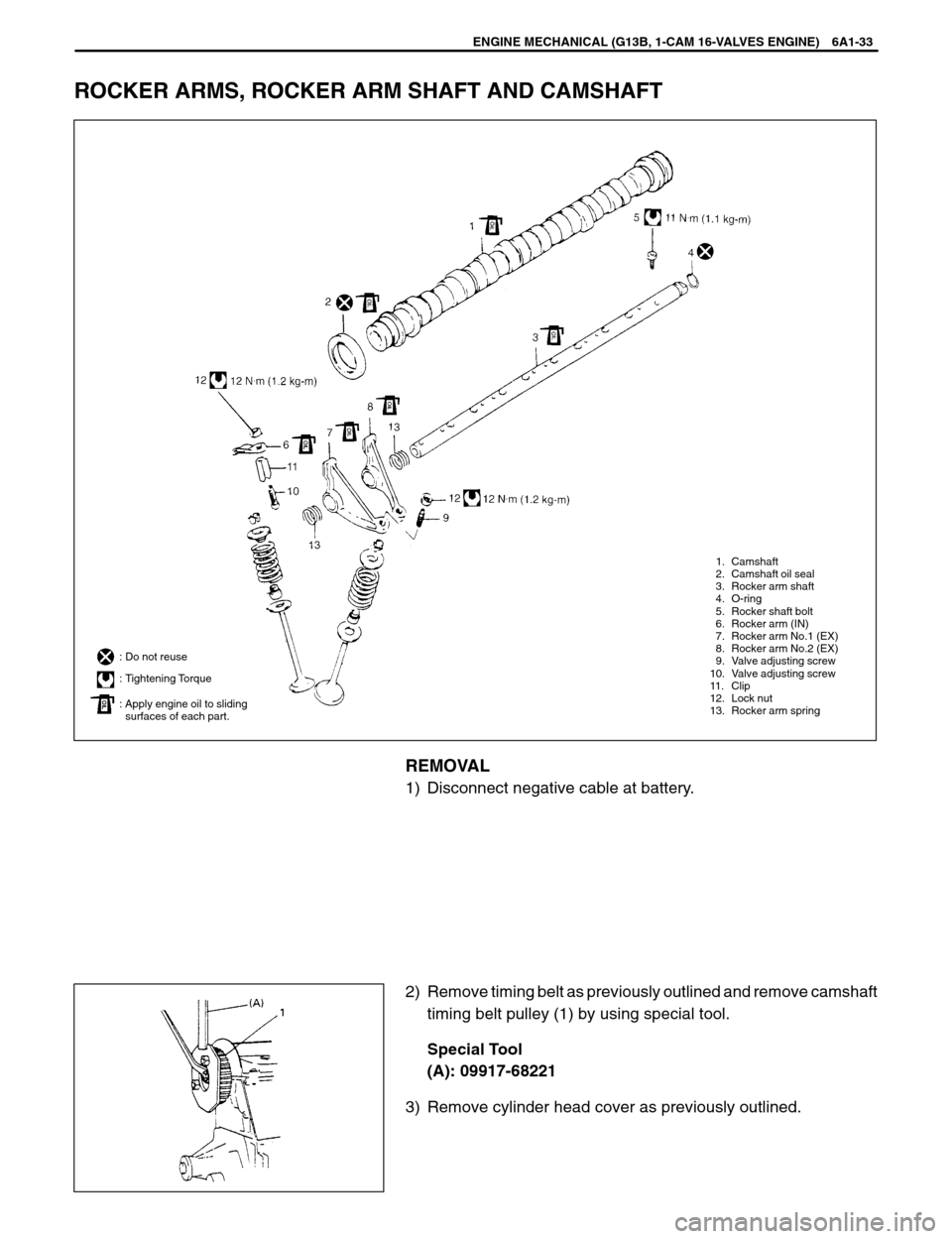
1. Camshaft
2. Camshaft oil seal
3. Rocker arm shaft
4. O-ring
5. Rocker shaft bolt
6. Rocker arm (IN)
7. Rocker arm No.1 (EX)
8. Rocker arm No.2 (EX)
9. Valve adjusting screw
10. Valve adjusting screw
11. Clip
12. Lock nut
13. Rocker arm spring
: Tightening Torque : Do not reuse
: Apply engine oil to sliding
: surfaces of each part.
ENGINE MECHANICAL (G13B, 1-CAM 16-VALVES ENGINE) 6A1-33
ROCKER ARMS, ROCKER ARM SHAFT AND CAMSHAFT
REMOVAL
1) Disconnect negative cable at battery.
2) Remove timing belt as previously outlined and remove camshaft
timing belt pulley (1) by using special tool.
Special Tool
(A): 09917-68221
3) Remove cylinder head cover as previously outlined.
Page 330 of 557
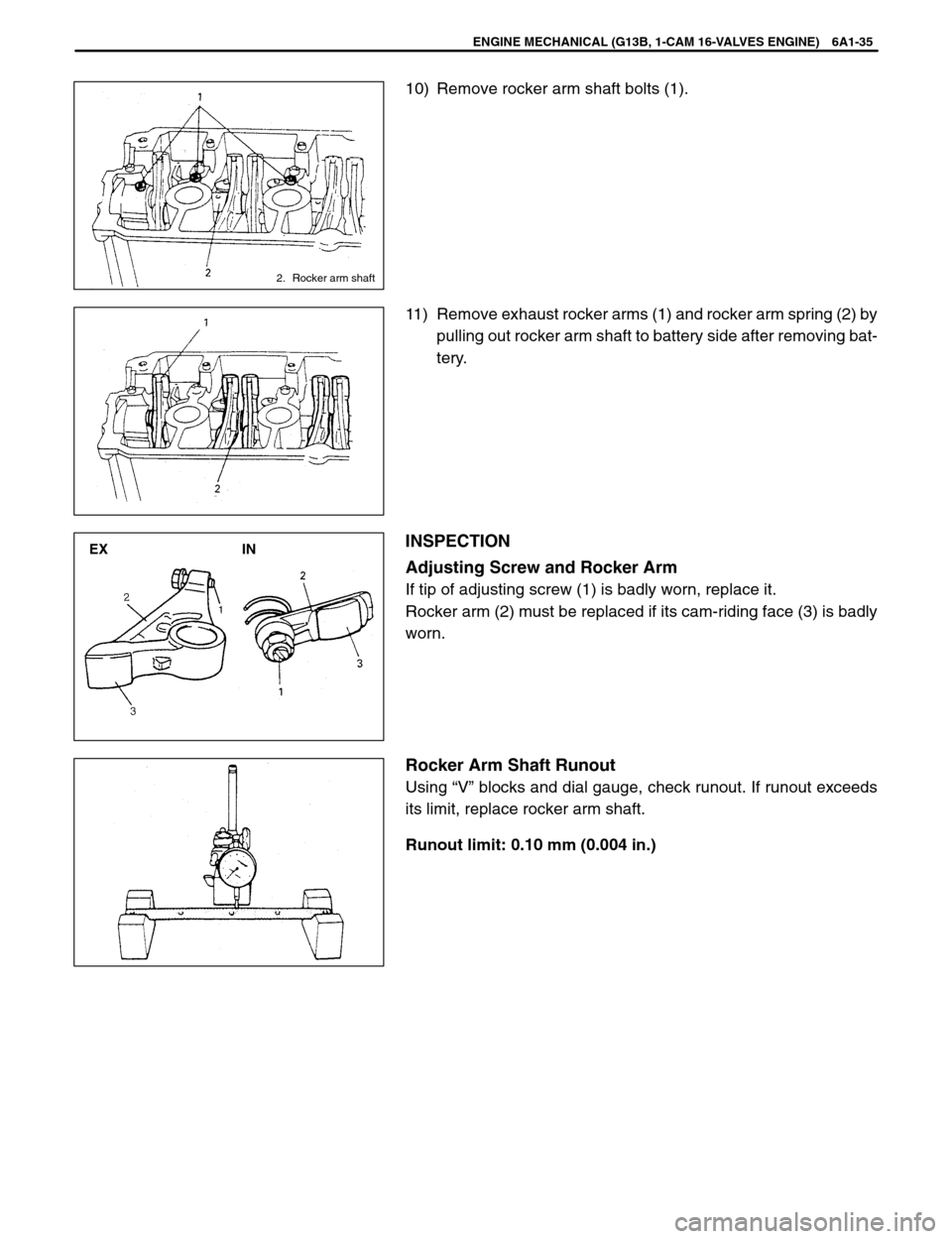
EX IN
2. Rocker arm shaft
ENGINE MECHANICAL (G13B, 1-CAM 16-VALVES ENGINE) 6A1-35
10) Remove rocker arm shaft bolts (1).
11) Remove exhaust rocker arms (1) and rocker arm spring (2) by
pulling out rocker arm shaft to battery side after removing bat-
tery.
INSPECTION
Adjusting Screw and Rocker Arm
If tip of adjusting screw (1) is badly worn, replace it.
Rocker arm (2) must be replaced if its cam-riding face (3) is badly
worn.
Rocker Arm Shaft Runout
Using “V” blocks and dial gauge, check runout. If runout exceeds
its limit, replace rocker arm shaft.
Runout limit: 0.10 mm (0.004 in.)
Page 335 of 557
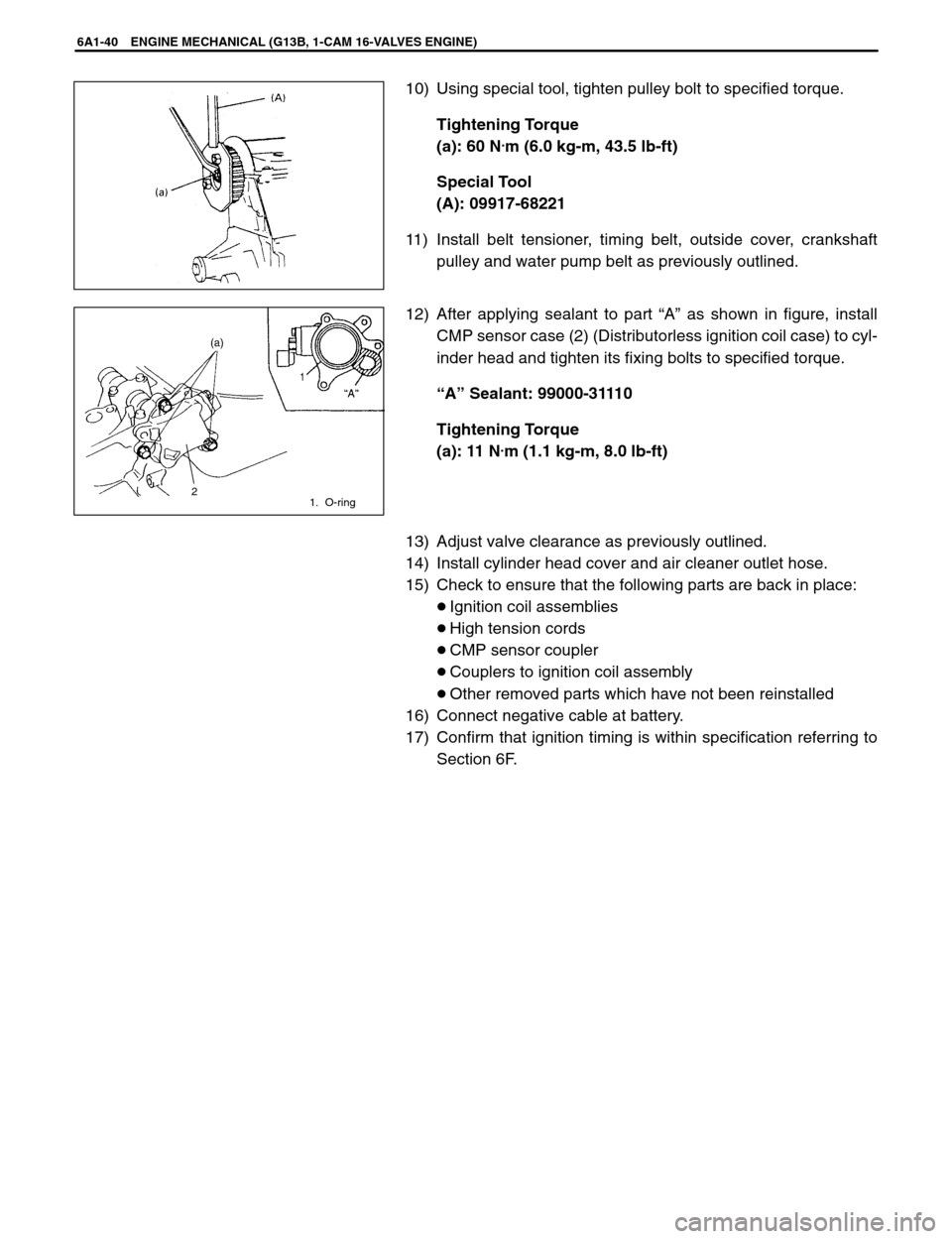
6A1-40 ENGINE MECHANICAL (G13B, 1-CAM 16-VALVES ENGINE)
1. O-ring2
10) Using special tool, tighten pulley bolt to specified torque.
Tightening Torque
(a): 60 N
.m (6.0 kg-m, 43.5 lb-ft)
Special Tool
(A): 09917-68221
11) Install belt tensioner, timing belt, outside cover, crankshaft
pulley and water pump belt as previously outlined.
12) After applying sealant to part “A” as shown in figure, install
CMP sensor case (2) (Distributorless ignition coil case) to cyl-
inder head and tighten its fixing bolts to specified torque.
“A” Sealant: 99000-31110
Tightening Torque
(a): 11 N
.m (1.1 kg-m, 8.0 lb-ft)
13) Adjust valve clearance as previously outlined.
14) Install cylinder head cover and air cleaner outlet hose.
15) Check to ensure that the following parts are back in place:
Ignition coil assemblies
High tension cords
CMP sensor coupler
Couplers to ignition coil assembly
Other removed parts which have not been reinstalled
16) Connect negative cable at battery.
17) Confirm that ignition timing is within specification referring to
Section 6F.
Page 336 of 557
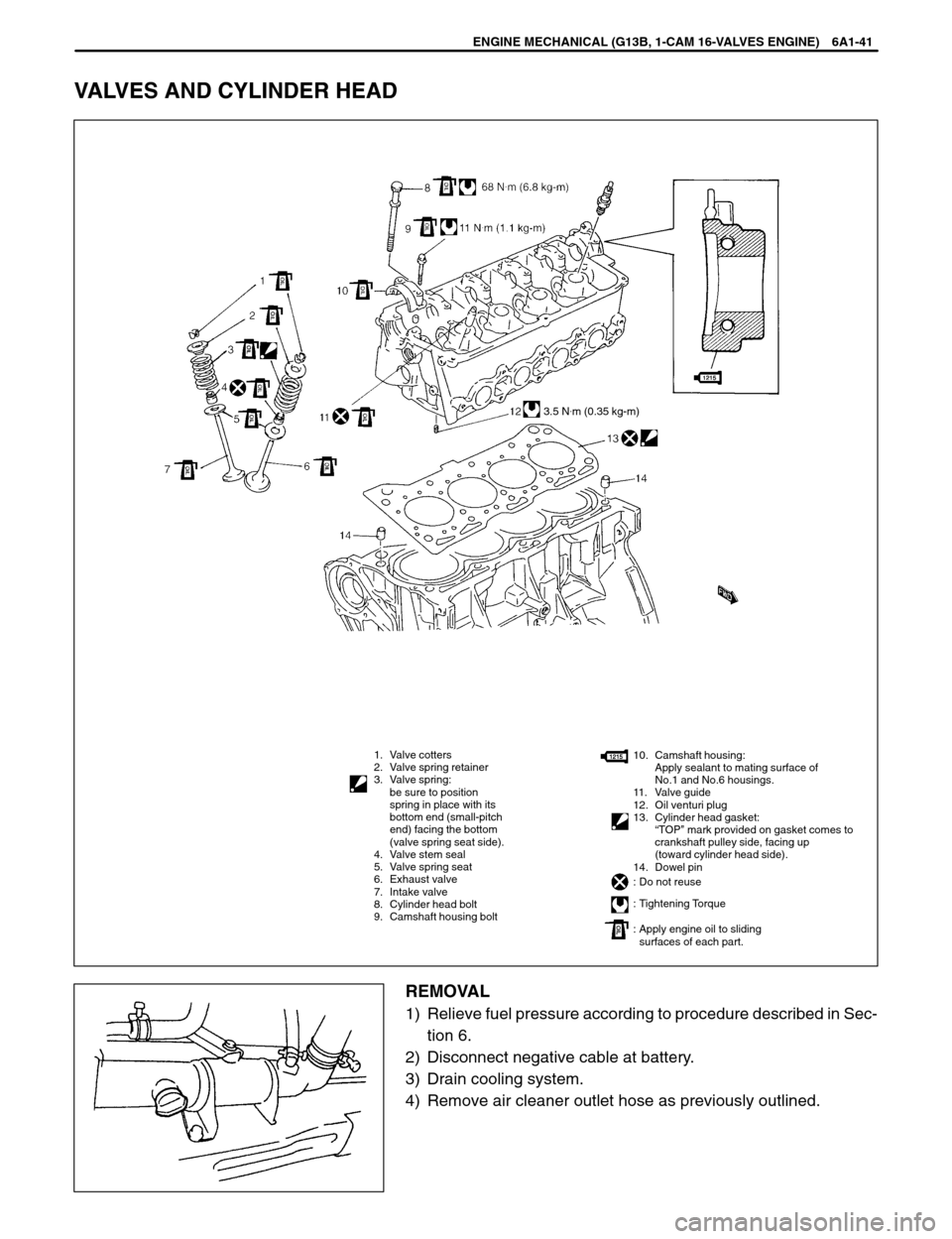
: Do not reuse
1. Valve cotters
2. Valve spring retainer
3. Valve spring:
be sure to position
spring in place with its
bottom end (small-pitch
end) facing the bottom
(valve spring seat side).
4. Valve stem seal
5. Valve spring seat
6. Exhaust valve
7. Intake valve
8. Cylinder head bolt
9. Camshaft housing bolt10. Camshaft housing:
Apply sealant to mating surface of
No.1 and No.6 housings.
11. Valve guide
12. Oil venturi plug
13. Cylinder head gasket:
“TOP” mark provided on gasket comes to
crankshaft pulley side, facing up
(toward cylinder head side).
14. Dowel pin
: Tightening Torque
: Apply engine oil to sliding
: surfaces of each part.
3.5 N.m (0.35 kg-m)
ENGINE MECHANICAL (G13B, 1-CAM 16-VALVES ENGINE) 6A1-41
VALVES AND CYLINDER HEAD
REMOVAL
1) Relieve fuel pressure according to procedure described in Sec-
tion 6.
2) Disconnect negative cable at battery.
3) Drain cooling system.
4) Remove air cleaner outlet hose as previously outlined.
Page 348 of 557
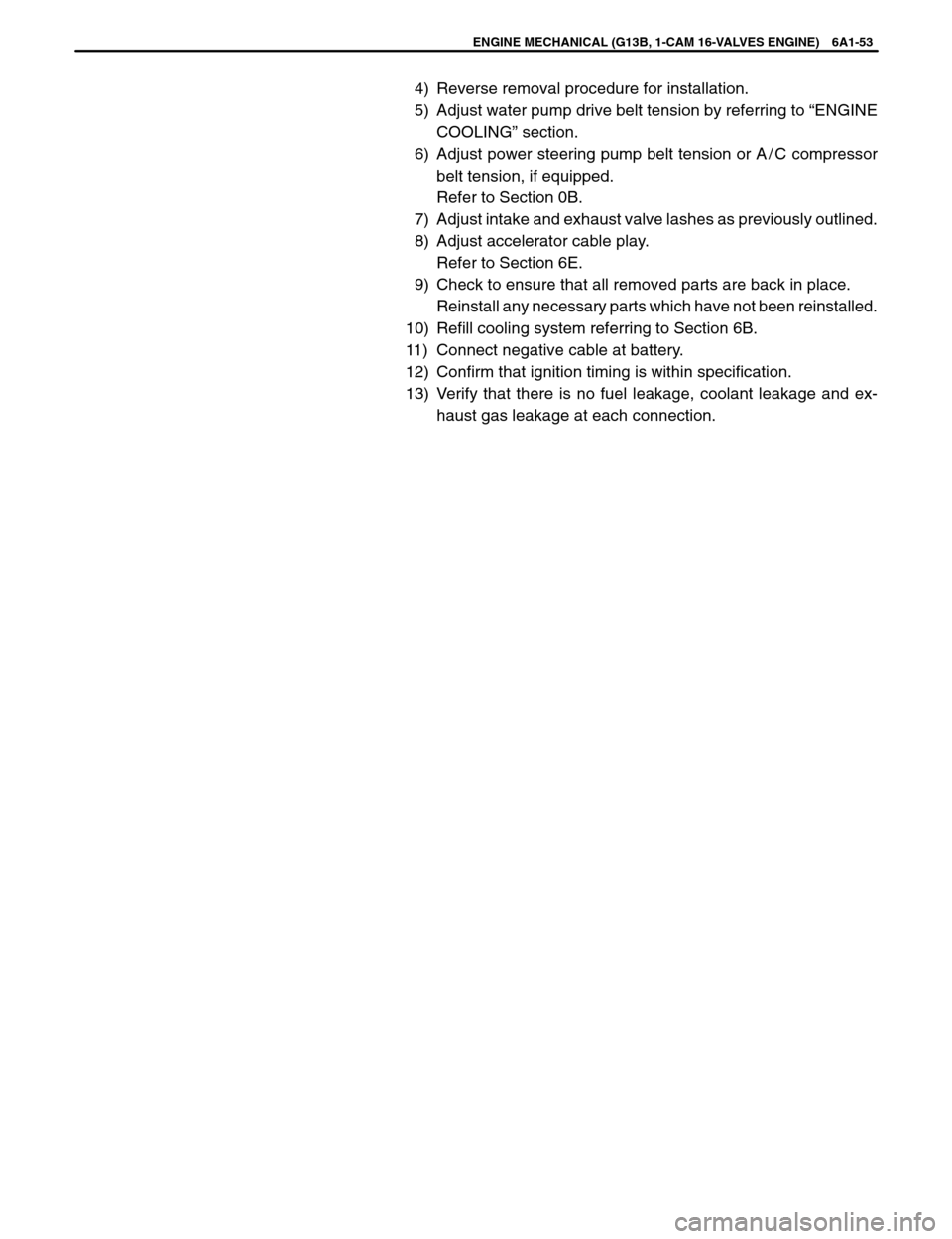
ENGINE MECHANICAL (G13B, 1-CAM 16-VALVES ENGINE) 6A1-53
4) Reverse removal procedure for installation.
5) Adjust water pump drive belt tension by referring to “ENGINE
COOLING” section.
6) Adjust power steering pump belt tension or A / C compressor
belt tension, if equipped.
Refer to Section 0B.
7) Adjust intake and exhaust valve lashes as previously outlined.
8) Adjust accelerator cable play.
Refer to Section 6E.
9) Check to ensure that all removed parts are back in place.
Reinstall any necessary parts which have not been reinstalled.
10) Refill cooling system referring to Section 6B.
11) Connect negative cable at battery.
12) Confirm that ignition timing is within specification.
13) Verify that there is no fuel leakage, coolant leakage and ex-
haust gas leakage at each connection.
Page 358 of 557
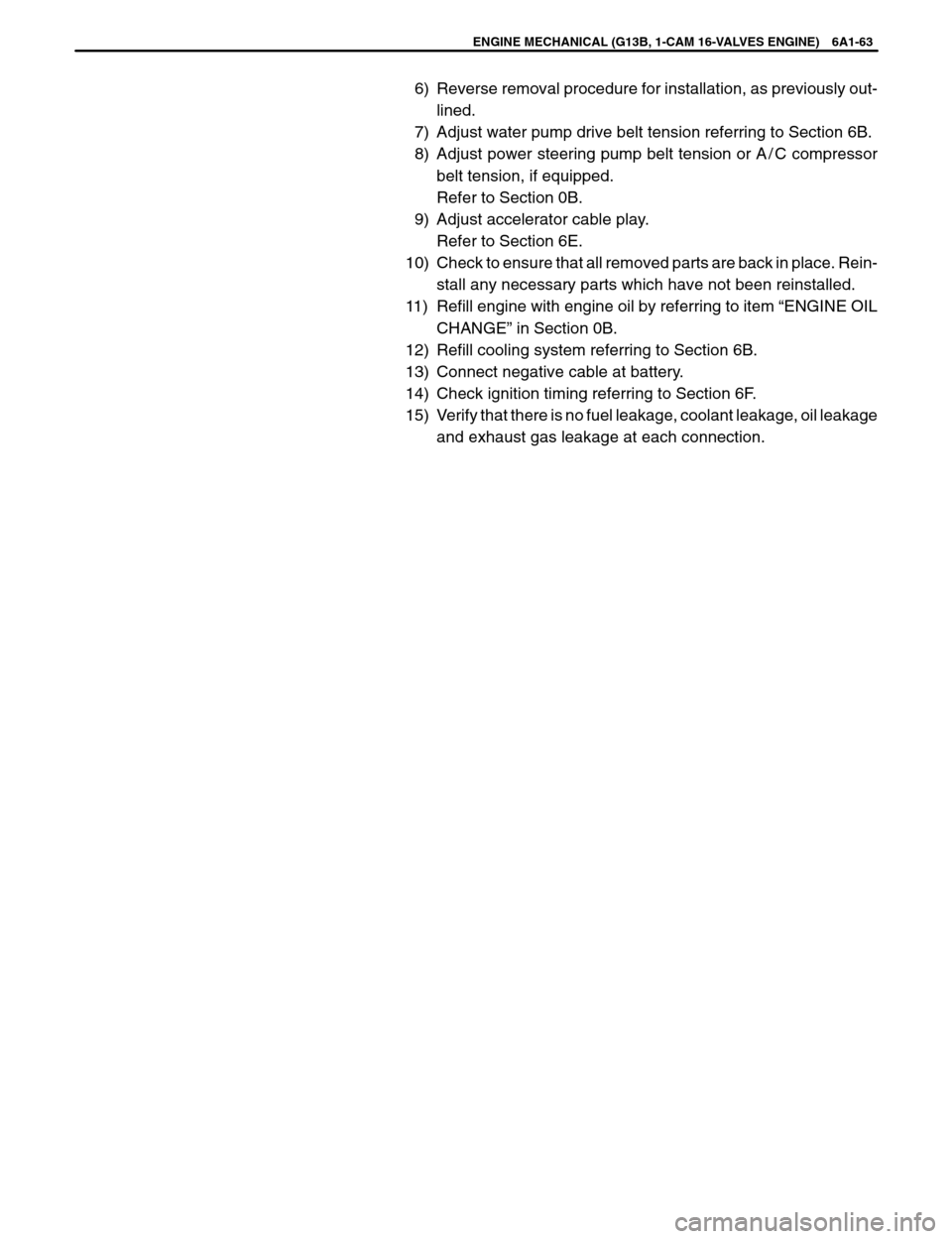
ENGINE MECHANICAL (G13B, 1-CAM 16-VALVES ENGINE) 6A1-63
6) Reverse removal procedure for installation, as previously out-
lined.
7) Adjust water pump drive belt tension referring to Section 6B.
8) Adjust power steering pump belt tension or A / C compressor
belt tension, if equipped.
Refer to Section 0B.
9) Adjust accelerator cable play.
Refer to Section 6E.
10) Check to ensure that all removed parts are back in place. Rein-
stall any necessary parts which have not been reinstalled.
11) Refill engine with engine oil by referring to item “ENGINE OIL
CHANGE” in Section 0B.
12) Refill cooling system referring to Section 6B.
13) Connect negative cable at battery.
14) Check ignition timing referring to Section 6F.
15) Verify that there is no fuel leakage, coolant leakage, oil leakage
and exhaust gas leakage at each connection.
Page 359 of 557
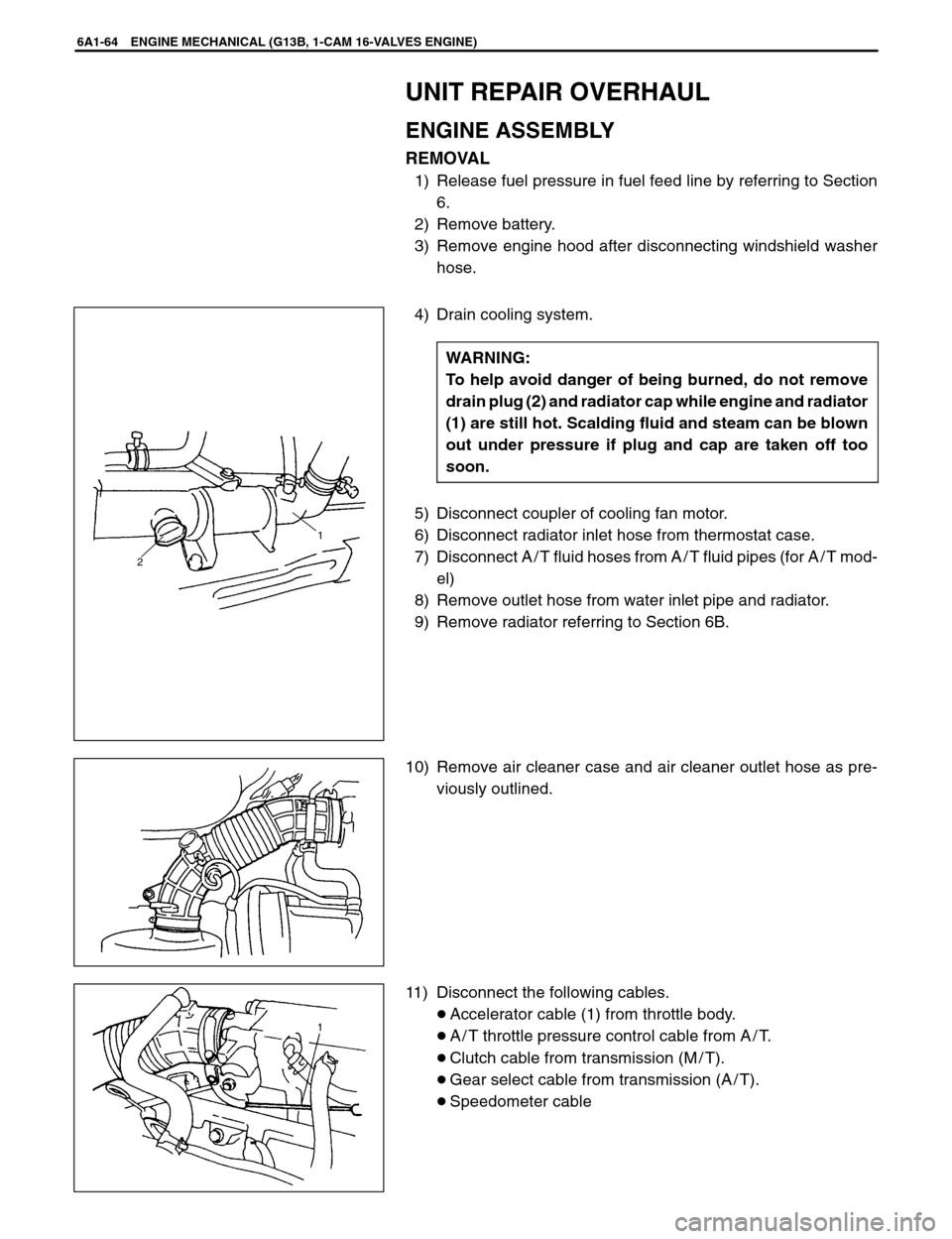
1
2
6A1-64 ENGINE MECHANICAL (G13B, 1-CAM 16-VALVES ENGINE)
UNIT REPAIR OVERHAUL
ENGINE ASSEMBLY
REMOVAL
1) Release fuel pressure in fuel feed line by referring to Section
6.
2) Remove battery.
3) Remove engine hood after disconnecting windshield washer
hose.
4) Drain cooling system.
WARNING:
To help avoid danger of being burned, do not remove
drain plug (2) and radiator cap while engine and radiator
(1) are still hot. Scalding fluid and steam can be blown
out under pressure if plug and cap are taken off too
soon.
5) Disconnect coupler of cooling fan motor.
6) Disconnect radiator inlet hose from thermostat case.
7) Disconnect A / T fluid hoses from A / T fluid pipes (for A / T mod-
el)
8) Remove outlet hose from water inlet pipe and radiator.
9) Remove radiator referring to Section 6B.
10) Remove air cleaner case and air cleaner outlet hose as pre-
viously outlined.
11) Disconnect the following cables.
Accelerator cable (1) from throttle body.
A / T throttle pressure control cable from A / T.
Clutch cable from transmission (M / T).
Gear select cable from transmission (A / T).
Speedometer cable