ignition SUZUKI SWIFT 2000 1.G SF310 Service Manual PDF
[x] Cancel search | Manufacturer: SUZUKI, Model Year: 2000, Model line: SWIFT, Model: SUZUKI SWIFT 2000 1.GPages: 557, PDF Size: 14.35 MB
Page 143 of 557
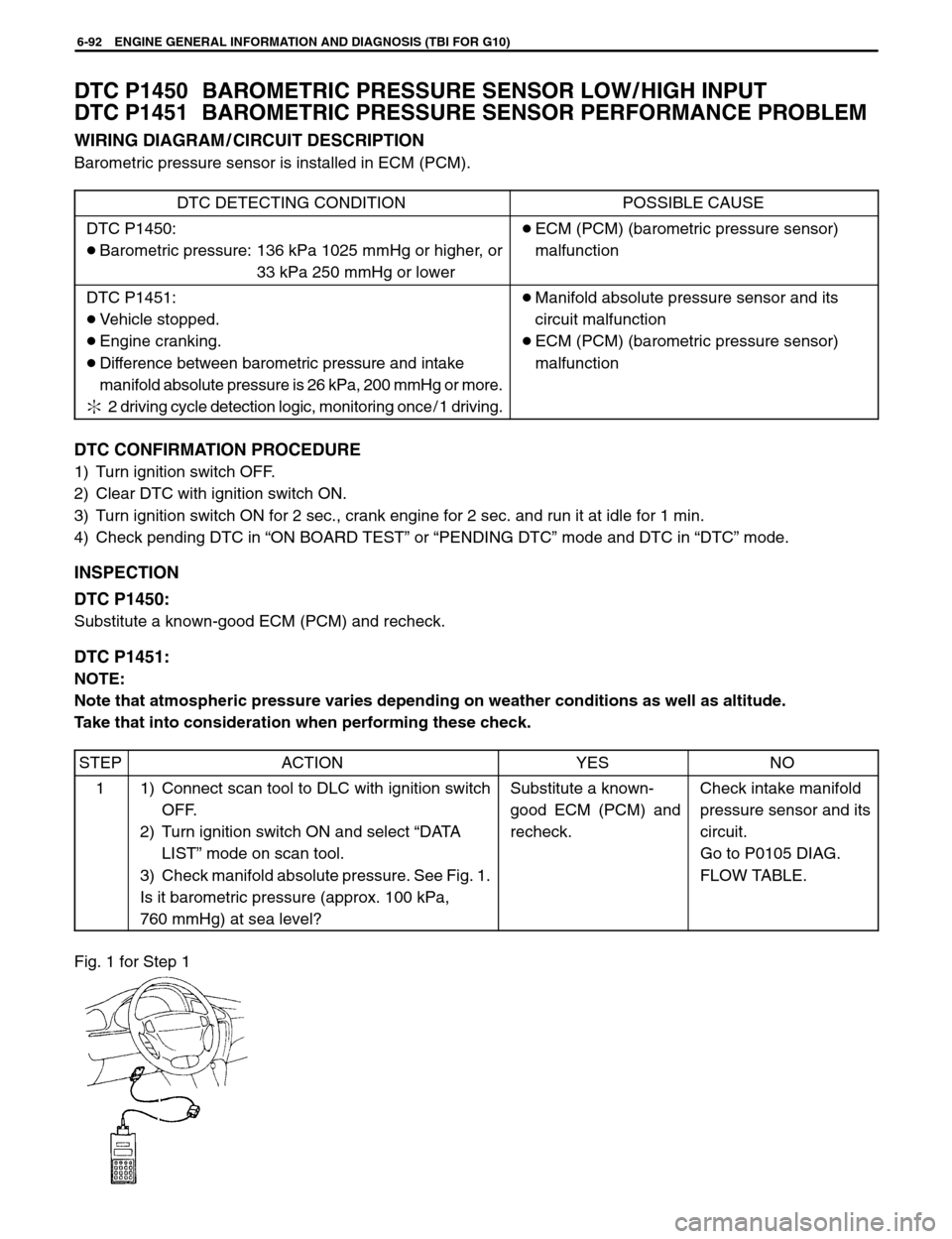
6-92 ENGINE GENERAL INFORMATION AND DIAGNOSIS (TBI FOR G10)
Fig. 1 for Step 1
DTC P1450 BAROMETRIC PRESSURE SENSOR LOW / HIGH INPUT
DTC P1451 BAROMETRIC PRESSURE SENSOR PERFORMANCE PROBLEM
WIRING DIAGRAM / CIRCUIT DESCRIPTION
Barometric pressure sensor is installed in ECM (PCM).
DTC DETECTING CONDITION
POSSIBLE CAUSE
DTC P1450:
Barometric pressure: 136 kPa 1025 mmHg or higher, or
33 kPa 250 mmHg or lowerECM (PCM) (barometric pressure sensor)
malfunction
DTC P1451:
Vehicle stopped.
Engine cranking.
Difference between barometric pressure and intake
manifold absolute pressure is 26 kPa, 200 mmHg or more.
2 driving cycle detection logic, monitoring once / 1 driving.Manifold absolute pressure sensor and its
circuit malfunction
ECM (PCM) (barometric pressure sensor)
malfunction
DTC CONFIRMATION PROCEDURE
1) Turn ignition switch OFF.
2) Clear DTC with ignition switch ON.
3) Turn ignition switch ON for 2 sec., crank engine for 2 sec. and run it at idle for 1 min.
4) Check pending DTC in “ON BOARD TEST” or “PENDING DTC” mode and DTC in “DTC” mode.
INSPECTION
DTC P1450:
Substitute a known-good ECM (PCM) and recheck.
DTC P1451:
NOTE:
Note that atmospheric pressure varies depending on weather conditions as well as altitude.
Take that into consideration when performing these check.
STEP
ACTIONYESNO
11) Connect scan tool to DLC with ignition switch
OFF.
2) Turn ignition switch ON and select “DATA
LIST” mode on scan tool.
3) Check manifold absolute pressure. See Fig. 1.
Is it barometric pressure (approx. 100 kPa,
760 mmHg) at sea level?Substitute a known-
good ECM (PCM) and
recheck.Check intake manifold
pressure sensor and its
circuit.
Go to P0105 DIAG.
FLOW TABLE.
Page 144 of 557
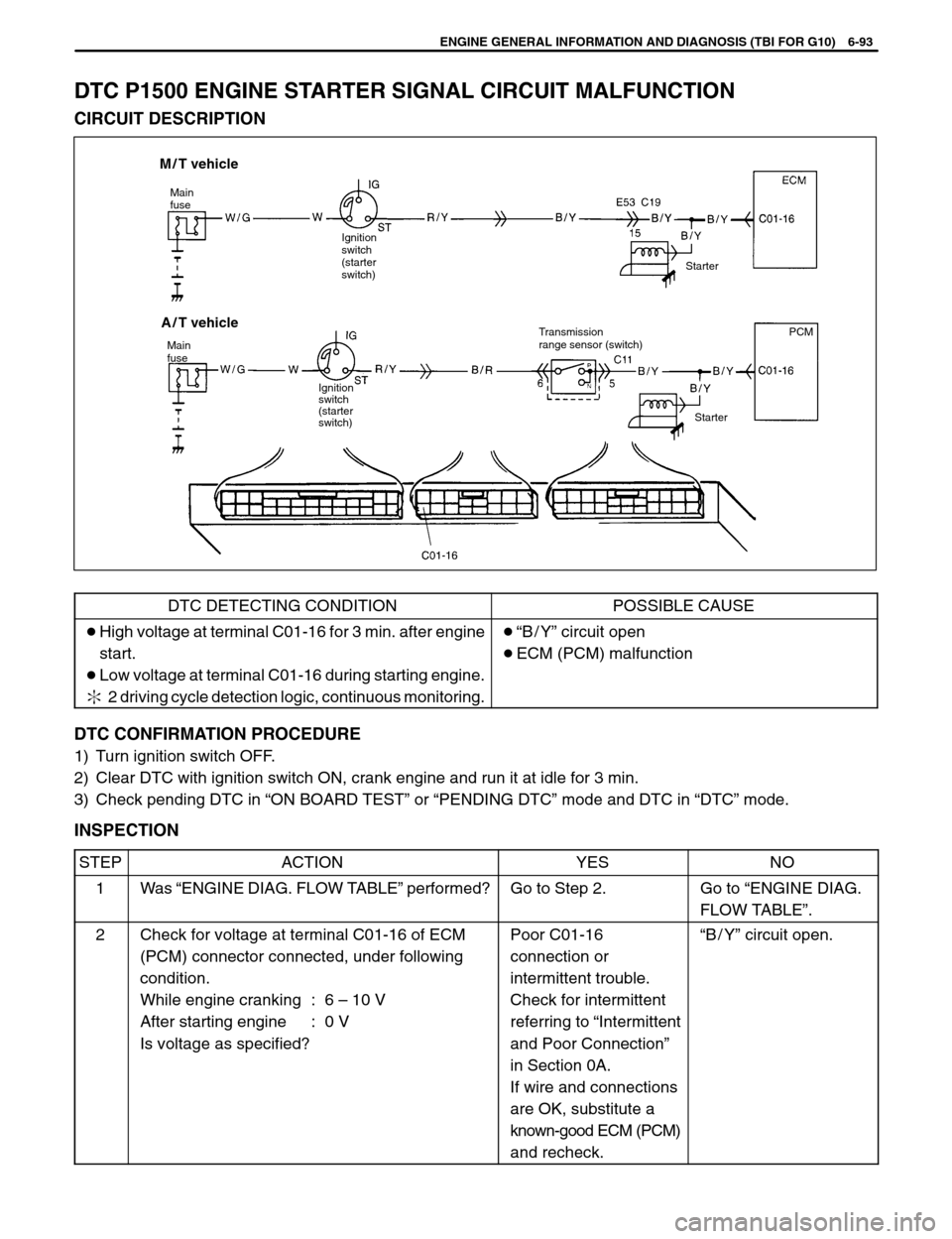
Main
fuse
M / T vehicle
Ignition
switch
(starter
switch)Starter
A / T vehicle
Main
fuse
Ignition
switch
(starter
switch)Transmission
range sensor (switch)
StarterPCM
ENGINE GENERAL INFORMATION AND DIAGNOSIS (TBI FOR G10) 6-93
DTC P1500 ENGINE STARTER SIGNAL CIRCUIT MALFUNCTION
CIRCUIT DESCRIPTION
DTC DETECTING CONDITIONPOSSIBLE CAUSE
High voltage at terminal C01-16 for 3 min. after engine
start.
Low voltage at terminal C01-16 during starting engine.
2 driving cycle detection logic, continuous monitoring.“B/Y” circuit open
ECM (PCM) malfunction
DTC CONFIRMATION PROCEDURE
1) Turn ignition switch OFF.
2) Clear DTC with ignition switch ON, crank engine and run it at idle for 3 min.
3) Check pending DTC in “ON BOARD TEST” or “PENDING DTC” mode and DTC in “DTC” mode.
INSPECTION
STEPACTIONYESNO
1Was “ENGINE DIAG. FLOW TABLE” performed?Go to Step 2.Go to “ENGINE DIAG.
FLOW TABLE”.
2Check for voltage at terminal C01-16 of ECM
(PCM) connector connected, under following
condition.
While engine cranking : 6 – 10 V
After starting engine : 0 V
Is voltage as specified?Poor C01-16
connection or
intermittent trouble.
Check for intermittent
referring to “Intermittent
and Poor Connection”
in Section 0A.
If wire and connections
are OK, substitute a
known-good ECM (PCM)
and recheck.“B/Y” circuit open.
Page 145 of 557
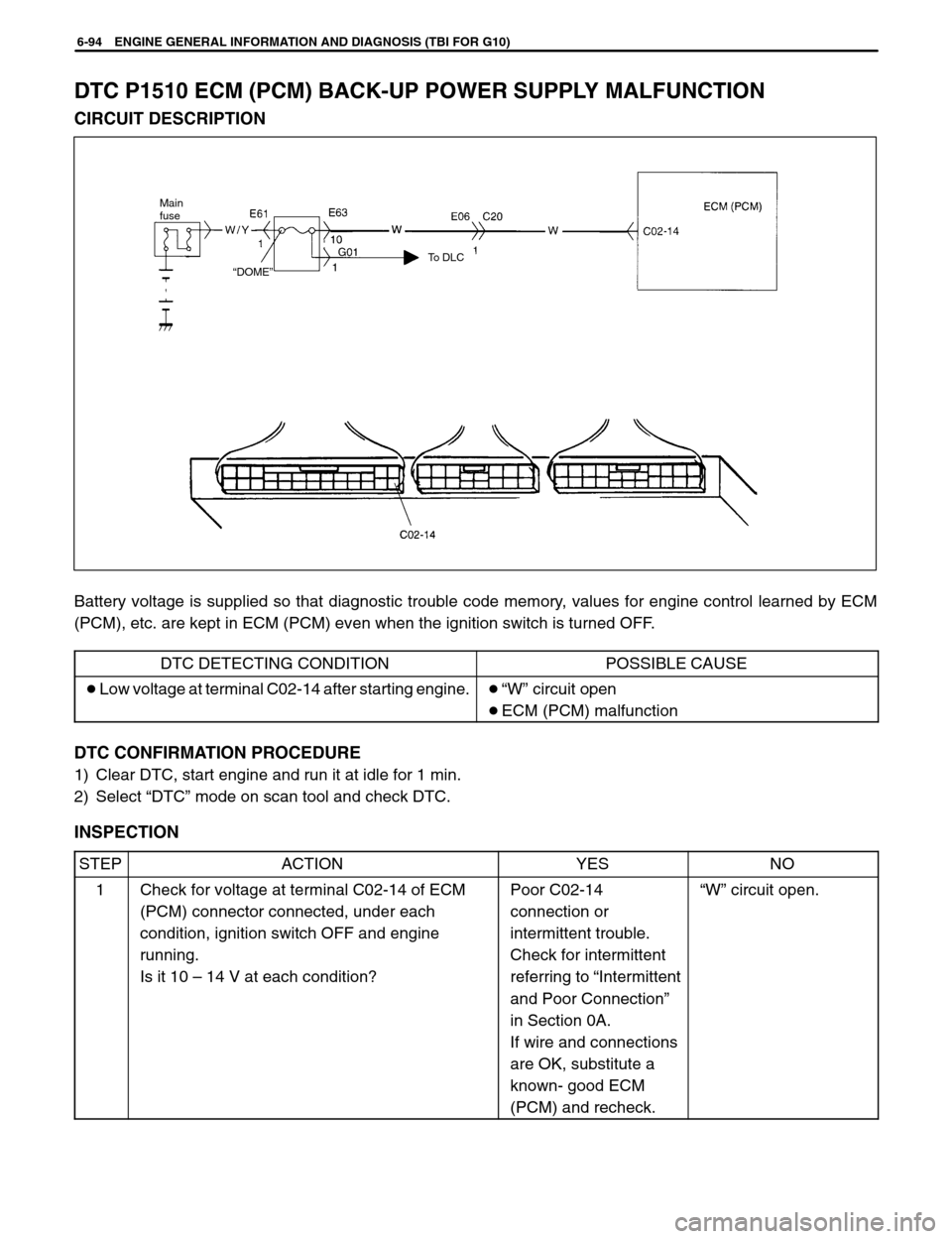
To DLC
“DOME” Main
fuse
6-94 ENGINE GENERAL INFORMATION AND DIAGNOSIS (TBI FOR G10)
DTC P1510 ECM (PCM) BACK-UP POWER SUPPLY MALFUNCTION
CIRCUIT DESCRIPTION
Battery voltage is supplied so that diagnostic trouble code memory, values for engine control learned by ECM
(PCM), etc. are kept in ECM (PCM) even when the ignition switch is turned OFF.
DTC DETECTING CONDITION
POSSIBLE CAUSE
Low voltage at terminal C02-14 after starting engine.“W” circuit open
ECM (PCM) malfunction
DTC CONFIRMATION PROCEDURE
1) Clear DTC, start engine and run it at idle for 1 min.
2) Select “DTC” mode on scan tool and check DTC.
INSPECTION
STEPACTIONYESNO
1Check for voltage at terminal C02-14 of ECM
(PCM) connector connected, under each
condition, ignition switch OFF and engine
running.
Is it 10 – 14 V at each condition?Poor C02-14
connection or
intermittent trouble.
Check for intermittent
referring to “Intermittent
and Poor Connection”
in Section 0A.
If wire and connections
are OK, substitute a
known- good ECM
(PCM) and recheck.“W” circuit open.
Page 147 of 557
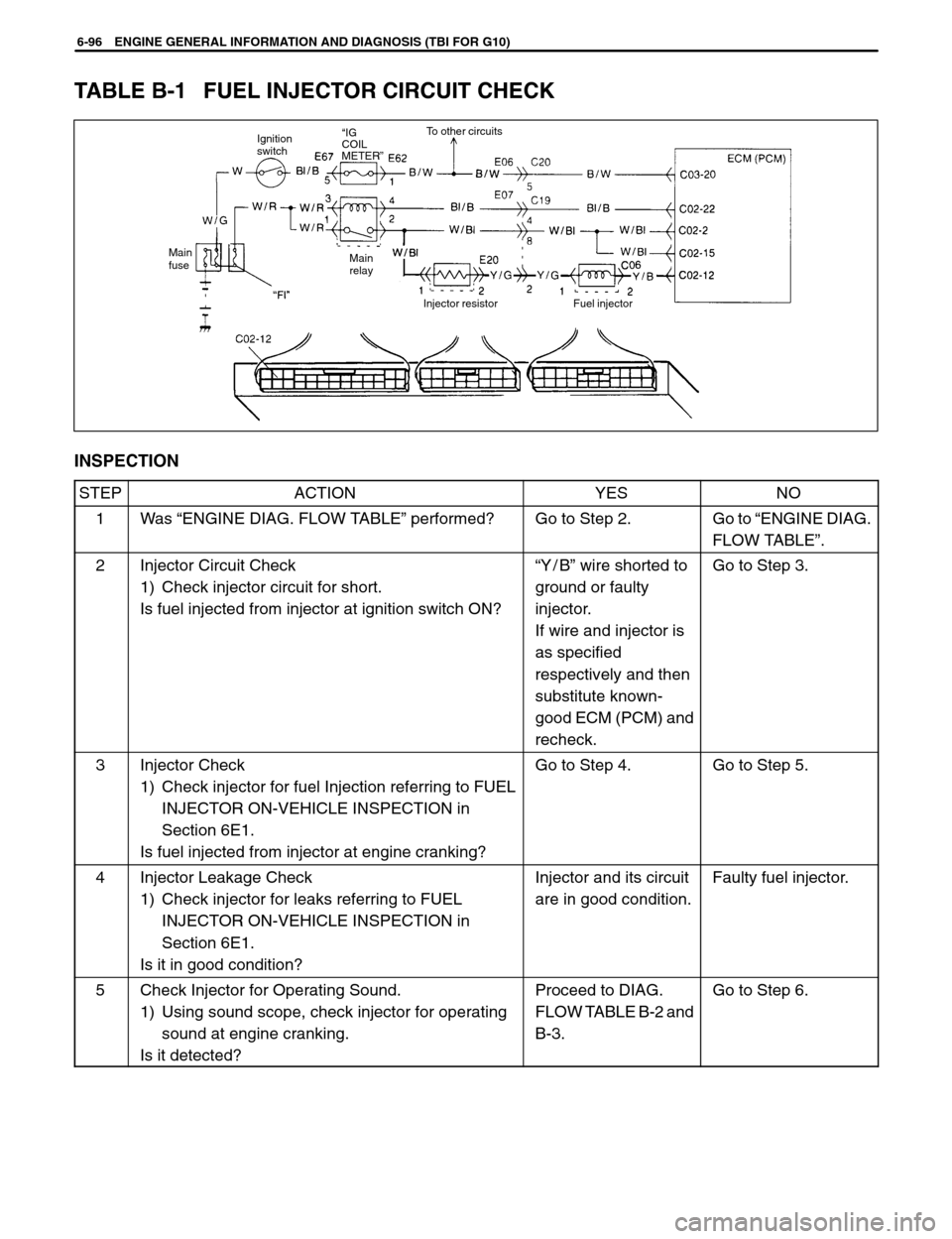
“IG
COIL
METER”
Main
fuseIgnition
switch
Main
relayTo other circuits
Injector resistor Fuel injector
6-96 ENGINE GENERAL INFORMATION AND DIAGNOSIS (TBI FOR G10)
TABLE B-1 FUEL INJECTOR CIRCUIT CHECK
INSPECTION
STEPACTIONYESNO
1Was “ENGINE DIAG. FLOW TABLE” performed?Go to Step 2.Go to “ENGINE DIAG.
FLOW TABLE”.
2Injector Circuit Check
1) Check injector circuit for short.
Is fuel injected from injector at ignition switch ON?“Y/B” wire shorted to
ground or faulty
injector.
If wire and injector is
as specified
respectively and then
substitute known-
good ECM (PCM) and
recheck.Go to Step 3.
3Injector Check
1) Check injector for fuel Injection referring to FUEL
INJECTOR ON-VEHICLE INSPECTION in
Section 6E1.
Is fuel injected from injector at engine cranking?Go to Step 4.Go to Step 5.
4Injector Leakage Check
1) Check injector for leaks referring to FUEL
INJECTOR ON-VEHICLE INSPECTION in
Section 6E1.
Is it in good condition?Injector and its circuit
are in good condition.Faulty fuel injector.
5Check Injector for Operating Sound.
1) Using sound scope, check injector for operating
sound at engine cranking.
Is it detected?Proceed to DIAG.
FLOW TABLE B-2 and
B-3.Go to Step 6.
Page 148 of 557
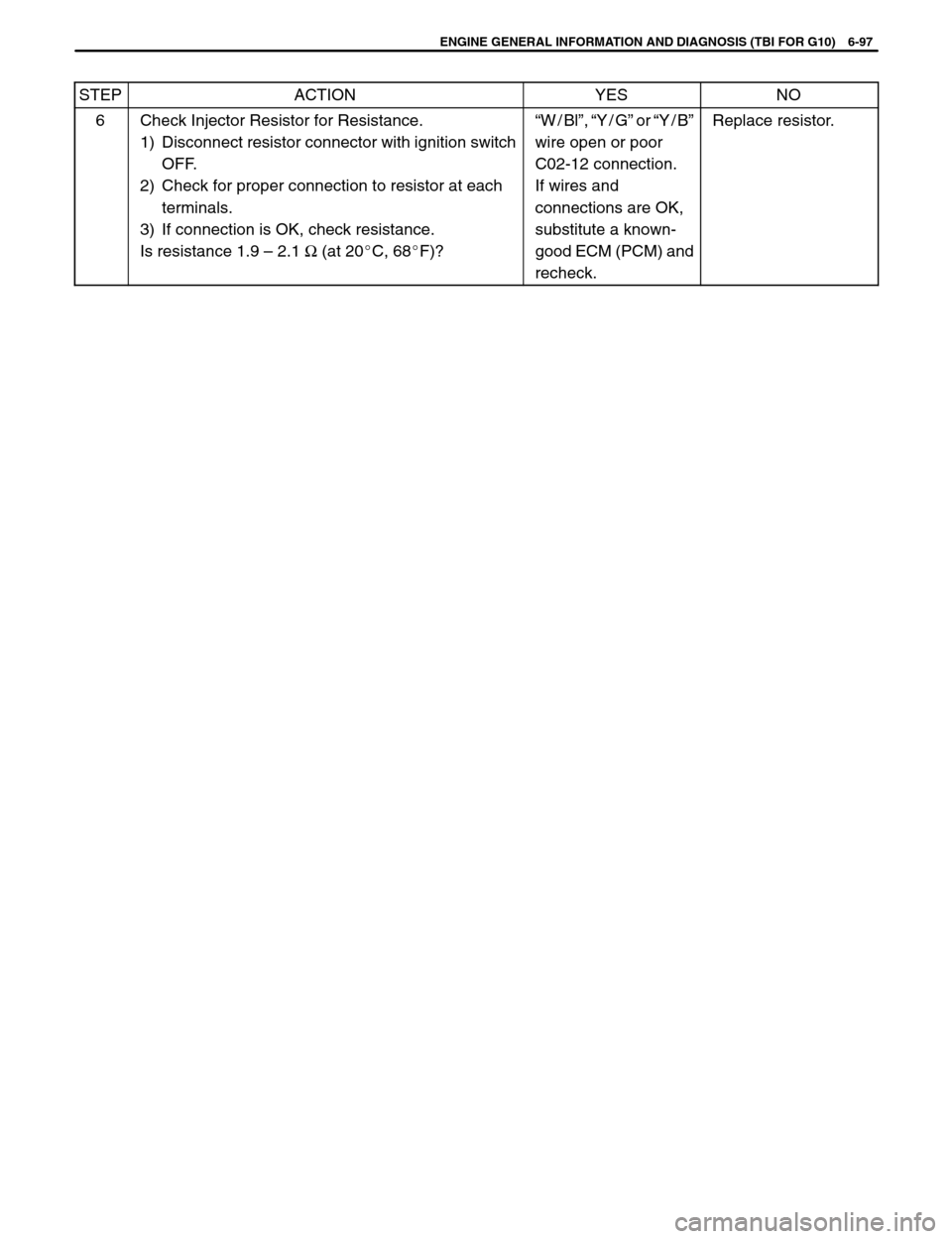
ENGINE GENERAL INFORMATION AND DIAGNOSIS (TBI FOR G10) 6-97
STEPACTIONYESNO
6Check Injector Resistor for Resistance.
1) Disconnect resistor connector with ignition switch
OFF.
2) Check for proper connection to resistor at each
terminals.
3) If connection is OK, check resistance.
Is resistance 1.9 – 2.1 Ω (at 20C, 68F)?“W/Bl”, “Y/G” or “Y/B”
wire open or poor
C02-12 connection.
If wires and
connections are OK,
substitute a known-
good ECM (PCM) and
recheck.Replace resistor.
Page 149 of 557
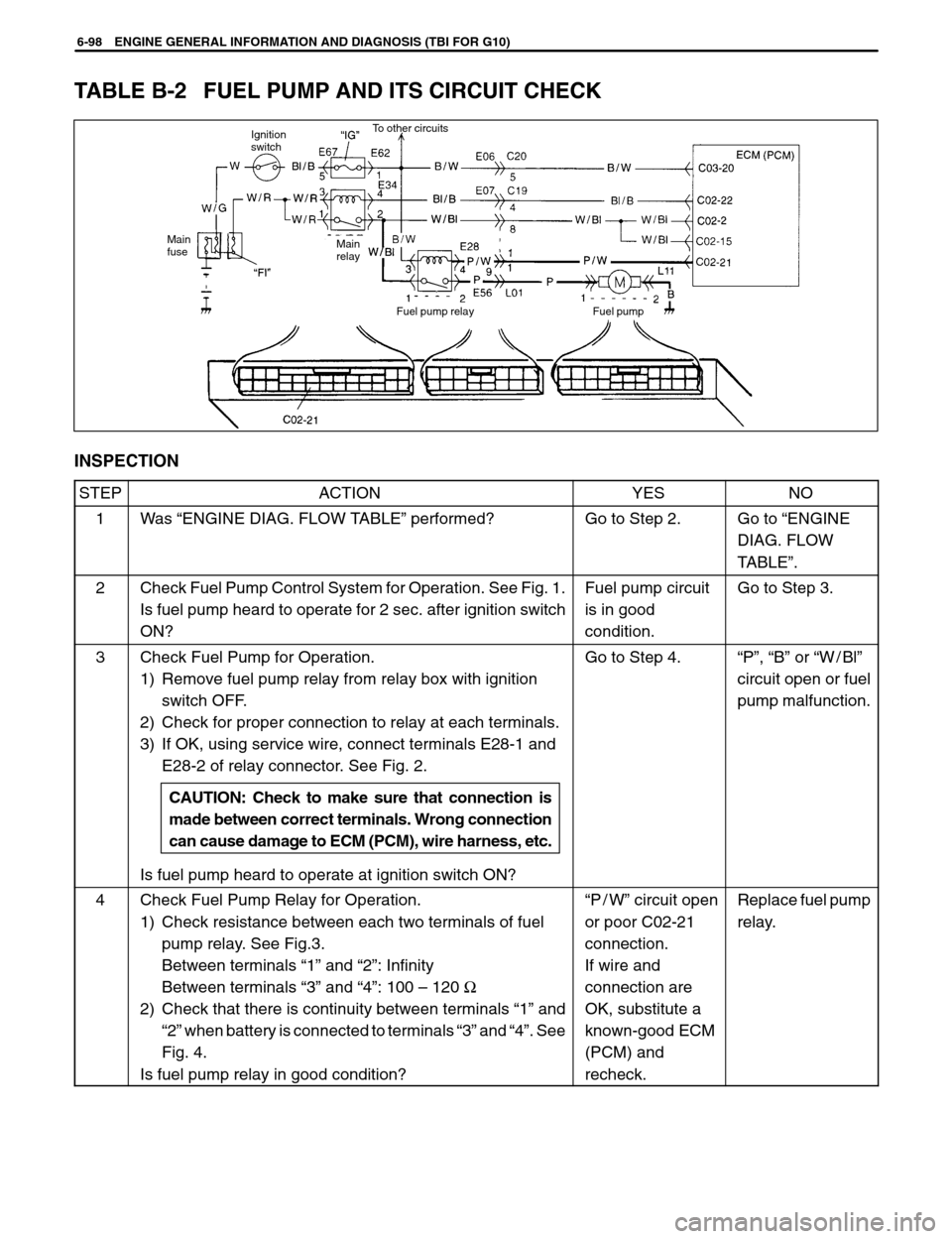
6-98 ENGINE GENERAL INFORMATION AND DIAGNOSIS (TBI FOR G10)
Main
fuseIgnition
switchTo other circuits
Main
relay
Fuel pump relay
Fuel pump
CAUTION: Check to make sure that connection is
made between correct terminals. Wrong connection
can cause damage to ECM (PCM), wire harness, etc.
TABLE B-2 FUEL PUMP AND ITS CIRCUIT CHECK
INSPECTION
STEPACTIONYESNO
1Was “ENGINE DIAG. FLOW TABLE” performed?Go to Step 2.Go to “ENGINE
DIAG. FLOW
TABLE”.
2Check Fuel Pump Control System for Operation. See Fig. 1.
Is fuel pump heard to operate for 2 sec. after ignition switch
ON?Fuel pump circuit
is in good
condition.Go to Step 3.
3Check Fuel Pump for Operation.
1) Remove fuel pump relay from relay box with ignition
switch OFF.
2) Check for proper connection to relay at each terminals.
3) If OK, using service wire, connect terminals E28-1 and
E28-2 of relay connector. See Fig. 2.
Is fuel pump heard to operate at ignition switch ON?Go to Step 4.“P”, “B” or “W/Bl”
circuit open or fuel
pump malfunction.
4Check Fuel Pump Relay for Operation.
1) Check resistance between each two terminals of fuel
pump relay. See Fig.3.
Between terminals “1” and “2”: Infinity
Between terminals “3” and “4”: 100 – 120 Ω
2) Check that there is continuity between terminals “1” and
“2” when battery is connected to terminals “3” and “4”. See
Fig. 4.
Is fuel pump relay in good condition?“P/W” circuit open
or poor C02-21
connection.
If wire and
connection are
OK, substitute a
known-good ECM
(PCM) and
recheck.Replace fuel pump
relay.
Page 151 of 557
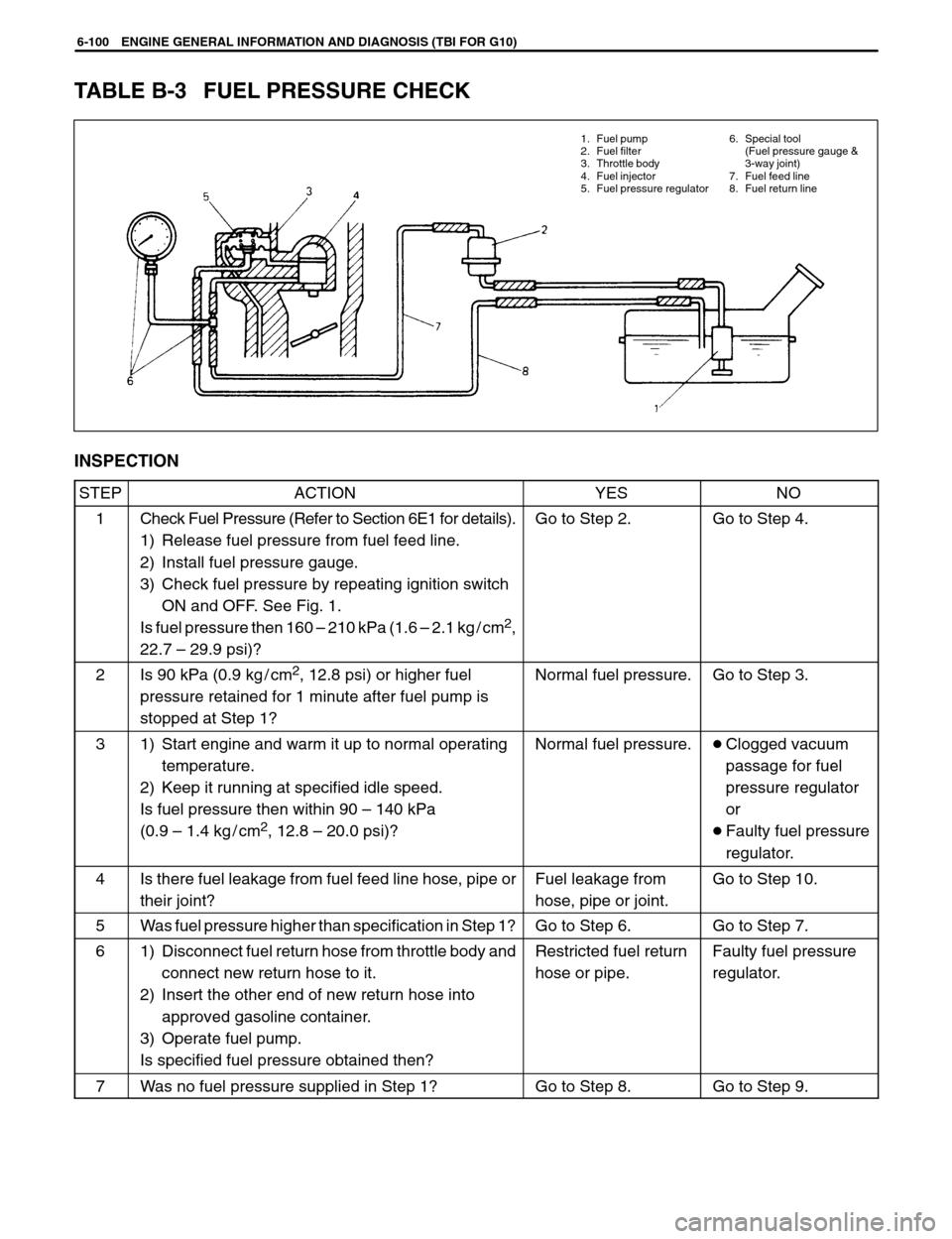
1. Fuel pump
2. Fuel filter
3. Throttle body
4. Fuel injector
5. Fuel pressure regulator6. Special tool
(Fuel pressure gauge &
3-way joint)
7. Fuel feed line
8. Fuel return line
6-100 ENGINE GENERAL INFORMATION AND DIAGNOSIS (TBI FOR G10)
TABLE B-3 FUEL PRESSURE CHECK
INSPECTION
STEPACTIONYESNO
1Check Fuel Pressure (Refer to Section 6E1 for details).
1) Release fuel pressure from fuel feed line.
2) Install fuel pressure gauge.
3) Check fuel pressure by repeating ignition switch
ON and OFF. See Fig. 1.
Is fuel pressure then 160 – 210 kPa (1.6 – 2.1 kg / cm
2,
22.7 – 29.9 psi)?
Go to Step 2.Go to Step 4.
2Is 90 kPa (0.9 kg / cm2, 12.8 psi) or higher fuel
pressure retained for 1 minute after fuel pump is
stopped at Step 1?Normal fuel pressure.Go to Step 3.
31) Start engine and warm it up to normal operating
temperature.
2) Keep it running at specified idle speed.
Is fuel pressure then within 90 – 140 kPa
(0.9 – 1.4 kg / cm
2, 12.8 – 20.0 psi)?
Normal fuel pressure.Clogged vacuum
passage for fuel
pressure regulator
or
Faulty fuel pressure
regulator.
4Is there fuel leakage from fuel feed line hose, pipe or
their joint?Fuel leakage from
hose, pipe or joint.Go to Step 10.
5Was fuel pressure higher than specification in Step 1?Go to Step 6.Go to Step 7.
61) Disconnect fuel return hose from throttle body and
connect new return hose to it.
2) Insert the other end of new return hose into
approved gasoline container.
3) Operate fuel pump.
Is specified fuel pressure obtained then?Restricted fuel return
hose or pipe.Faulty fuel pressure
regulator.
7Was no fuel pressure supplied in Step 1?Go to Step 8.Go to Step 9.
Page 154 of 557
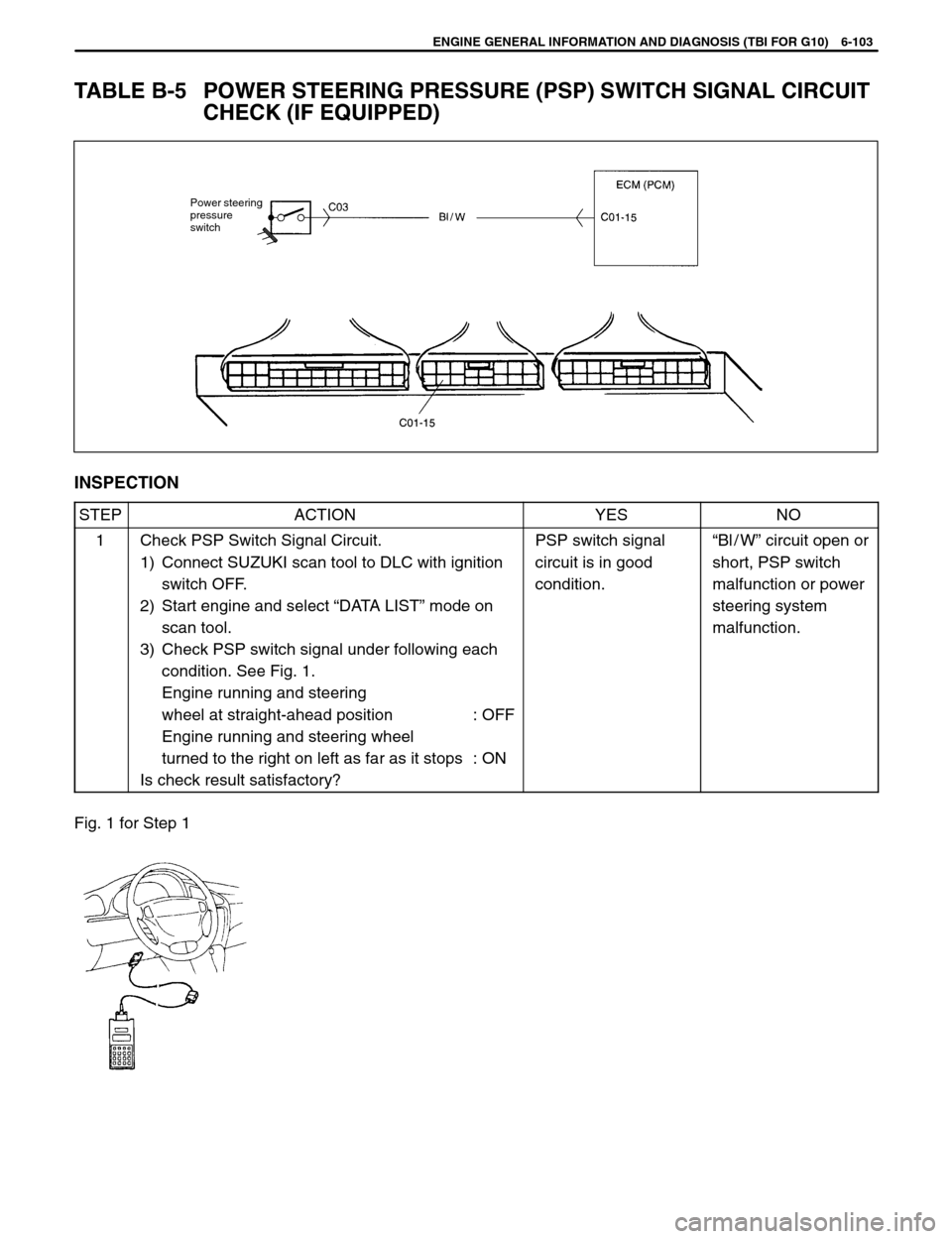
Power steering
pressure
switch
ENGINE GENERAL INFORMATION AND DIAGNOSIS (TBI FOR G10) 6-103
TABLE B-5 POWER STEERING PRESSURE (PSP) SWITCH SIGNAL CIRCUIT
CHECK (IF EQUIPPED)
INSPECTION
STEPACTIONYESNO
1Check PSP Switch Signal Circuit.
1) Connect SUZUKI scan tool to DLC with ignition
switch OFF.
2) Start engine and select “DATA LIST” mode on
scan tool.
3) Check PSP switch signal under following each
condition. See Fig. 1.
Engine running and steering
wheel at straight-ahead position : OFF
Engine running and steering wheel
turned to the right on left as far as it stops : ON
Is check result satisfactory?PSP switch signal
circuit is in good
condition.“Bl / W” circuit open or
short, PSP switch
malfunction or power
steering system
malfunction.
Fig. 1 for Step 1
Page 157 of 557
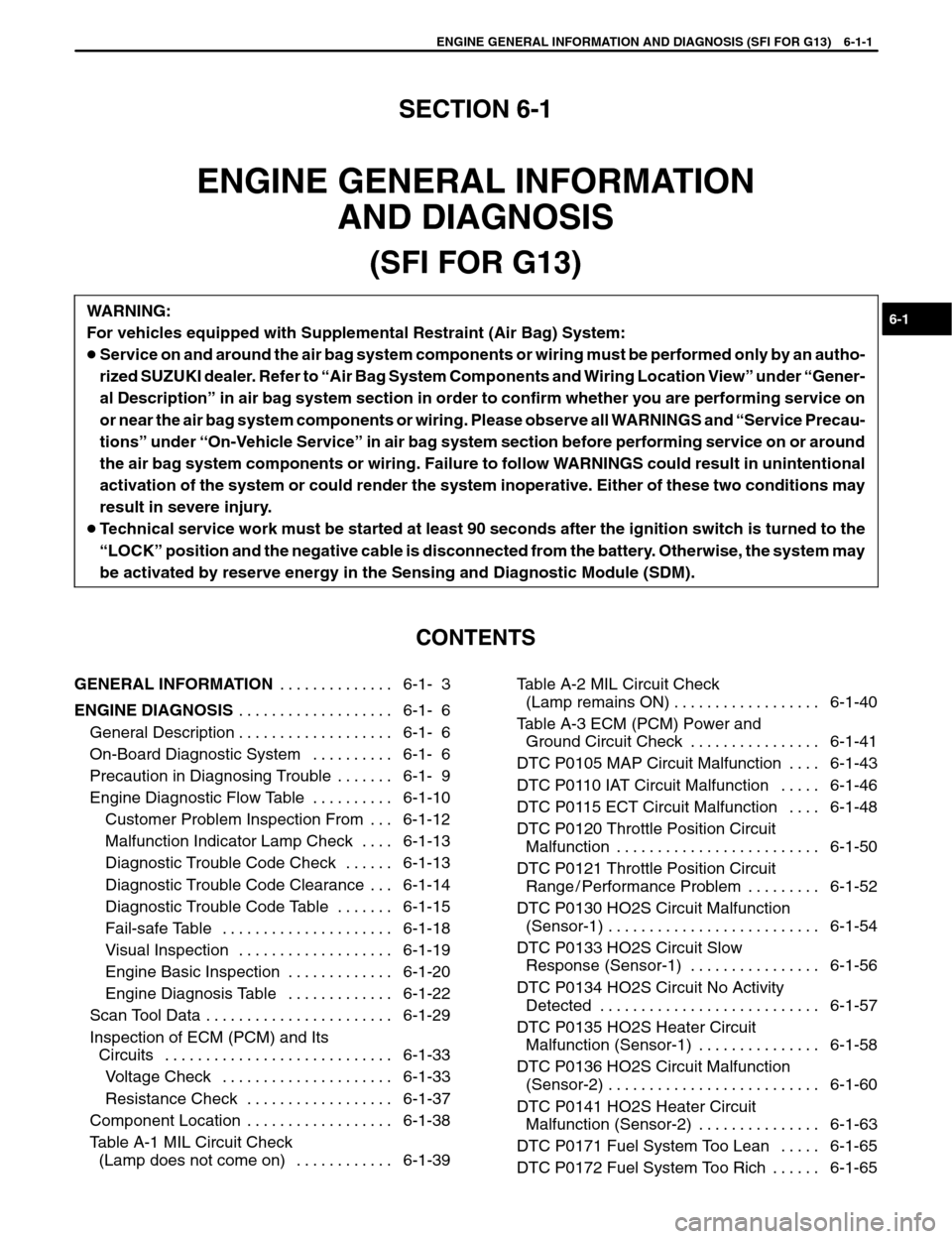
6-1
ENGINE GENERAL INFORMATION AND DIAGNOSIS (SFI FOR G13) 6-1-1
GENERAL INFORMATION6-1- 3 . . . . . . . . . . . . . .
ENGINE DIAGNOSIS6-1- 6 . . . . . . . . . . . . . . . . . . .
General Description 6-1- 6. . . . . . . . . . . . . . . . . . .
On-Board Diagnostic System 6-1- 6. . . . . . . . . .
Precaution in Diagnosing Trouble 6-1- 9. . . . . . .
Engine Diagnostic Flow Table 6-1-10. . . . . . . . . .
Customer Problem Inspection From 6-1-12. . .
Malfunction Indicator Lamp Check 6-1-13. . . .
Diagnostic Trouble Code Check 6-1-13. . . . . .
Diagnostic Trouble Code Clearance 6-1-14. . .
Diagnostic Trouble Code Table 6-1-15. . . . . . .
Fail-safe Table 6-1-18. . . . . . . . . . . . . . . . . . . . .
Visual Inspection 6-1-19. . . . . . . . . . . . . . . . . . .
Engine Basic Inspection 6-1-20. . . . . . . . . . . . .
Engine Diagnosis Table 6-1-22. . . . . . . . . . . . .
Scan Tool Data 6-1-29. . . . . . . . . . . . . . . . . . . . . . .
Inspection of ECM (PCM) and Its
Circuits 6-1-33. . . . . . . . . . . . . . . . . . . . . . . . . . . .
Voltage Check 6-1-33. . . . . . . . . . . . . . . . . . . . .
Resistance Check 6-1-37. . . . . . . . . . . . . . . . . .
Component Location 6-1-38. . . . . . . . . . . . . . . . . .
Table A-1 MIL Circuit Check
(Lamp does not come on) 6-1-39. . . . . . . . . . . . Table A-2 MIL Circuit Check
(Lamp remains ON) 6-1-40. . . . . . . . . . . . . . . . . .
Table A-3 ECM (PCM) Power and
Ground Circuit Check 6-1-41. . . . . . . . . . . . . . . .
DTC P0105 MAP Circuit Malfunction 6-1-43. . . .
DTC P0110 IAT Circuit Malfunction 6-1-46. . . . .
DTC P0115 ECT Circuit Malfunction 6-1-48. . . .
DTC P0120 Throttle Position Circuit
Malfunction 6-1-50. . . . . . . . . . . . . . . . . . . . . . . . .
DTC P0121 Throttle Position Circuit
Range / Performance Problem 6-1-52. . . . . . . . .
DTC P0130 HO2S Circuit Malfunction
(Sensor-1) 6-1-54. . . . . . . . . . . . . . . . . . . . . . . . . .
DTC P0133 HO2S Circuit Slow
Response (Sensor-1) 6-1-56. . . . . . . . . . . . . . . .
DTC P0134 HO2S Circuit No Activity
Detected 6-1-57. . . . . . . . . . . . . . . . . . . . . . . . . . .
DTC P0135 HO2S Heater Circuit
Malfunction (Sensor-1) 6-1-58. . . . . . . . . . . . . . .
DTC P0136 HO2S Circuit Malfunction
(Sensor-2) 6-1-60. . . . . . . . . . . . . . . . . . . . . . . . . .
DTC P0141 HO2S Heater Circuit
Malfunction (Sensor-2) 6-1-63. . . . . . . . . . . . . . .
DTC P0171 Fuel System Too Lean 6-1-65. . . . .
DTC P0172 Fuel System Too Rich 6-1-65. . . . . .
SECTION 6-1
ENGINE GENERAL INFORMATION
AND DIAGNOSIS
(SFI FOR G13)
WARNING:
For vehicles equipped with Supplemental Restraint (Air Bag) System:
Service on and around the air bag system components or wiring must be performed only by an autho-
rized SUZUKI dealer. Refer to “Air Bag System Components and Wiring Location View” under “Gener-
al Description” in air bag system section in order to confirm whether you are performing service on
or near the air bag system components or wiring. Please observe all WARNINGS and “Service Precau-
tions” under “On-Vehicle Service” in air bag system section before performing service on or around
the air bag system components or wiring. Failure to follow WARNINGS could result in unintentional
activation of the system or could render the system inoperative. Either of these two conditions may
result in severe injury.
Technical service work must be started at least 90 seconds after the ignition switch is turned to the
“LOCK” position and the negative cable is disconnected from the battery. Otherwise, the system may
be activated by reserve energy in the Sensing and Diagnostic Module (SDM).
CONTENTS
Page 161 of 557
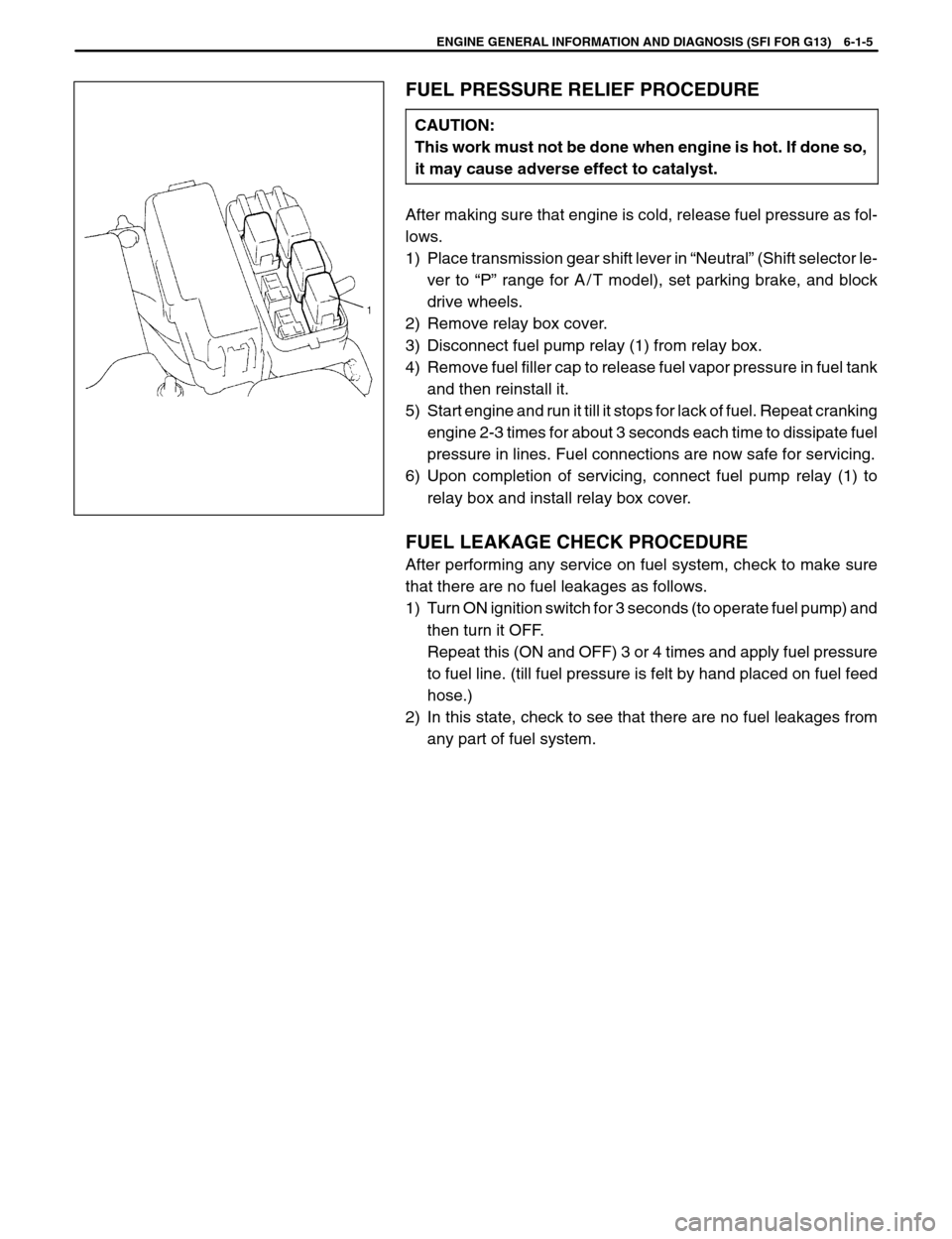
ENGINE GENERAL INFORMATION AND DIAGNOSIS (SFI FOR G13) 6-1-5
FUEL PRESSURE RELIEF PROCEDURE
CAUTION:
This work must not be done when engine is hot. If done so,
it may cause adverse effect to catalyst.
After making sure that engine is cold, release fuel pressure as fol-
lows.
1) Place transmission gear shift lever in “Neutral” (Shift selector le-
ver to “P” range for A / T model), set parking brake, and block
drive wheels.
2) Remove relay box cover.
3) Disconnect fuel pump relay (1) from relay box.
4) Remove fuel filler cap to release fuel vapor pressure in fuel tank
and then reinstall it.
5) Start engine and run it till it stops for lack of fuel. Repeat cranking
engine 2-3 times for about 3 seconds each time to dissipate fuel
pressure in lines. Fuel connections are now safe for servicing.
6) Upon completion of servicing, connect fuel pump relay (1) to
relay box and install relay box cover.
FUEL LEAKAGE CHECK PROCEDURE
After performing any service on fuel system, check to make sure
that there are no fuel leakages as follows.
1) Turn ON ignition switch for 3 seconds (to operate fuel pump) and
then turn it OFF.
Repeat this (ON and OFF) 3 or 4 times and apply fuel pressure
to fuel line. (till fuel pressure is felt by hand placed on fuel feed
hose.)
2) In this state, check to see that there are no fuel leakages from
any part of fuel system.