air filter SUZUKI SWIFT 2000 1.G SF310 Service Workshop Manual
[x] Cancel search | Manufacturer: SUZUKI, Model Year: 2000, Model line: SWIFT, Model: SUZUKI SWIFT 2000 1.GPages: 557, PDF Size: 14.35 MB
Page 10 of 557
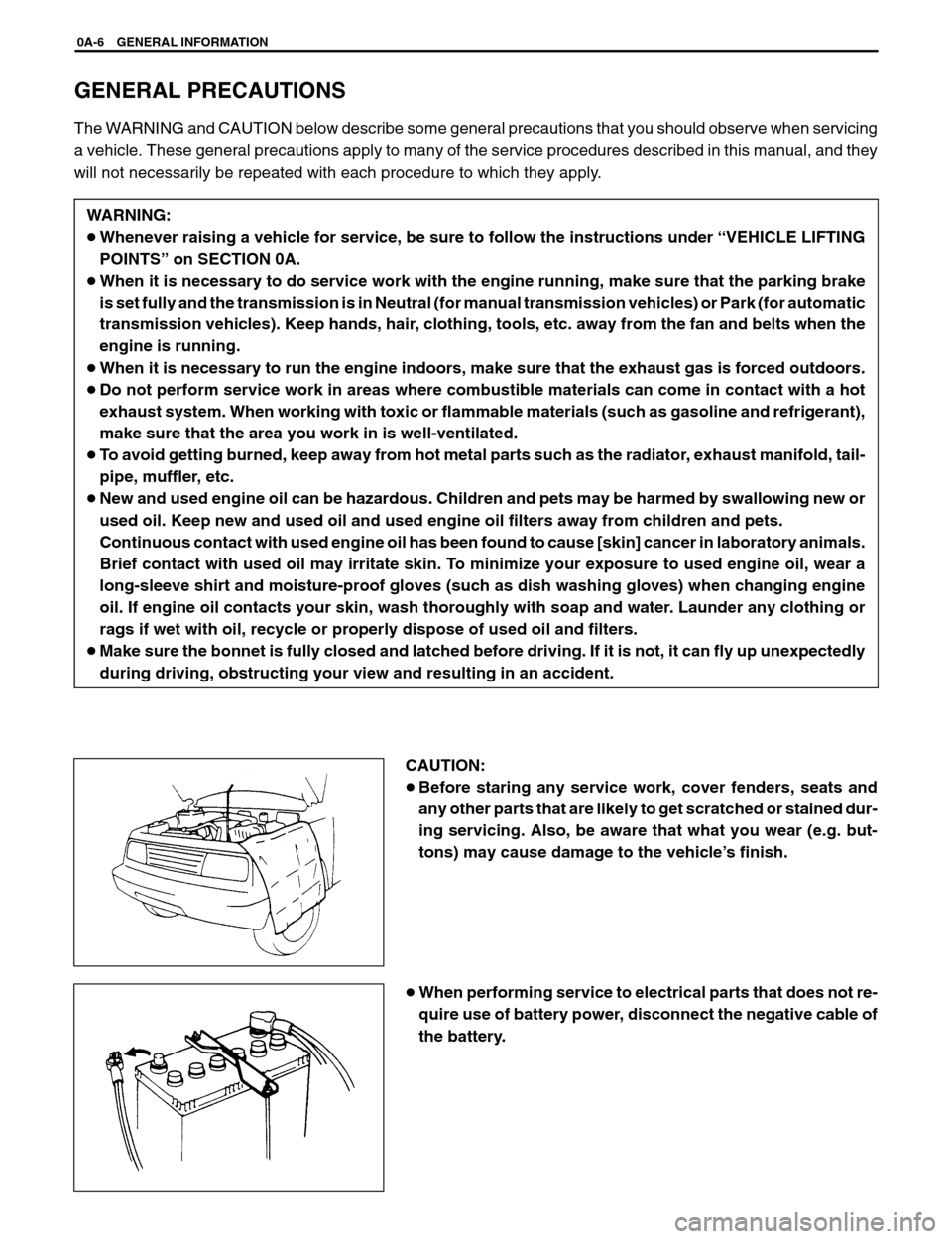
0A-6 GENERAL INFORMATION
GENERAL PRECAUTIONS
The WARNING and CAUTION below describe some general precautions that you should observe when servicing
a vehicle. These general precautions apply to many of the service procedures described in this manual, and they
will not necessarily be repeated with each procedure to which they apply.
WARNING:
Whenever raising a vehicle for service, be sure to follow the instructions under “VEHICLE LIFTING
POINTS” on SECTION 0A.
When it is necessary to do service work with the engine running, make sure that the parking brake
is set fully and the transmission is in Neutral (for manual transmission vehicles) or Park (for automatic
transmission vehicles). Keep hands, hair, clothing, tools, etc. away from the fan and belts when the
engine is running.
When it is necessary to run the engine indoors, make sure that the exhaust gas is forced outdoors.
Do not perform service work in areas where combustible materials can come in contact with a hot
exhaust system. When working with toxic or flammable materials (such as gasoline and refrigerant),
make sure that the area you work in is well-ventilated.
To avoid getting burned, keep away from hot metal parts such as the radiator, exhaust manifold, tail-
pipe, muffler, etc.
New and used engine oil can be hazardous. Children and pets may be harmed by swallowing new or
used oil. Keep new and used oil and used engine oil filters away from children and pets.
Continuous contact with used engine oil has been found to cause [skin] cancer in laboratory animals.
Brief contact with used oil may irritate skin. To minimize your exposure to used engine oil, wear a
long-sleeve shirt and moisture-proof gloves (such as dish washing gloves) when changing engine
oil. If engine oil contacts your skin, wash thoroughly with soap and water. Launder any clothing or
rags if wet with oil, recycle or properly dispose of used oil and filters.
Make sure the bonnet is fully closed and latched before driving. If it is not, it can fly up unexpectedly
during driving, obstructing your view and resulting in an accident.
CAUTION:
Before staring any service work, cover fenders, seats and
any other parts that are likely to get scratched or stained dur-
ing servicing. Also, be aware that what you wear (e.g. but-
tons) may cause damage to the vehicle’s finish.
When performing service to electrical parts that does not re-
quire use of battery power, disconnect the negative cable of
the battery.
Page 32 of 557
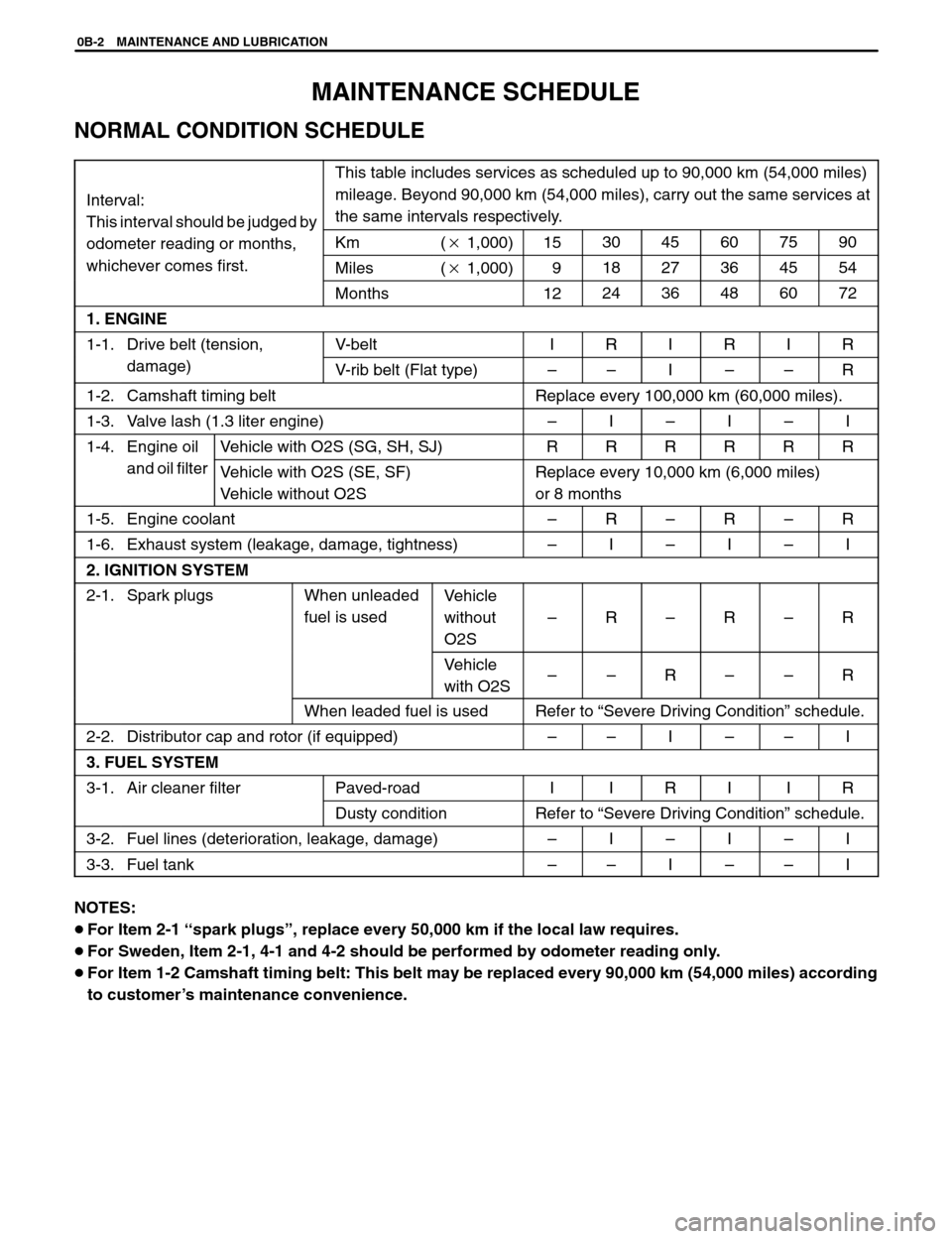
0B-2 MAINTENANCE AND LUBRICATION
MAINTENANCE SCHEDULE
NORMAL CONDITION SCHEDULE
Interval:
This interval should be
judged by
This table includes services as scheduled up to 90,000 km (54,000 miles)
mileage. Beyond 90,000 km (54,000 miles), carry out the same services at
the same intervals respectively.
jg y
odometer reading or months,Km( 1,000)153045607590
whichever comes first.Miles( 1,000)91827364554
Months122436486072
1. ENGINE
1-1.Drive belt (tension,V-beltIRIRIR
damage)
V-rib belt (Flat type)––I––R
1-2.Camshaft timing beltReplace every 100,000 km (60,000 miles).
1-3.Valve lash (1.3 liter engine)–I–I–I
1-4.Engine oilVehicle with O2S (SG, SH, SJ)RRRRRR
and oil filter
Vehicle with O2S (SE, SF)
Vehicle without O2SReplace every 10,000 km (6,000 miles)
or 8 months
1-5.Engine coolant–R–R–R
1-6.Exhaust system (leakage, damage, tightness)–I–I–I
2. IGNITION SYSTEM
2-1.Spark plugsWhen unleaded
fuel is usedVehicle
without
O2S
–R–R–R
Vehicle
with O2S––R––R
When leaded fuel is usedRefer to “Severe Driving Condition” schedule.
2-2.Distributor cap and rotor (if equipped)––I––I
3. FUEL SYSTEM
3-1.Air cleaner filterPaved-roadIIRIIR
Dusty conditionRefer to “Severe Driving Condition” schedule.
3-2.Fuel lines (deterioration, leakage, damage)–I–I–I
3-3.Fuel tank––I––I
NOTES:
For Item 2-1 “spark plugs”, replace every 50,000 km if the local law requires.
For Sweden, Item 2-1, 4-1 and 4-2 should be performed by odometer reading only.
For Item 1-2 Camshaft timing belt: This belt may be replaced every 90,000 km (54,000 miles) according
to customer’s maintenance convenience.
Page 34 of 557
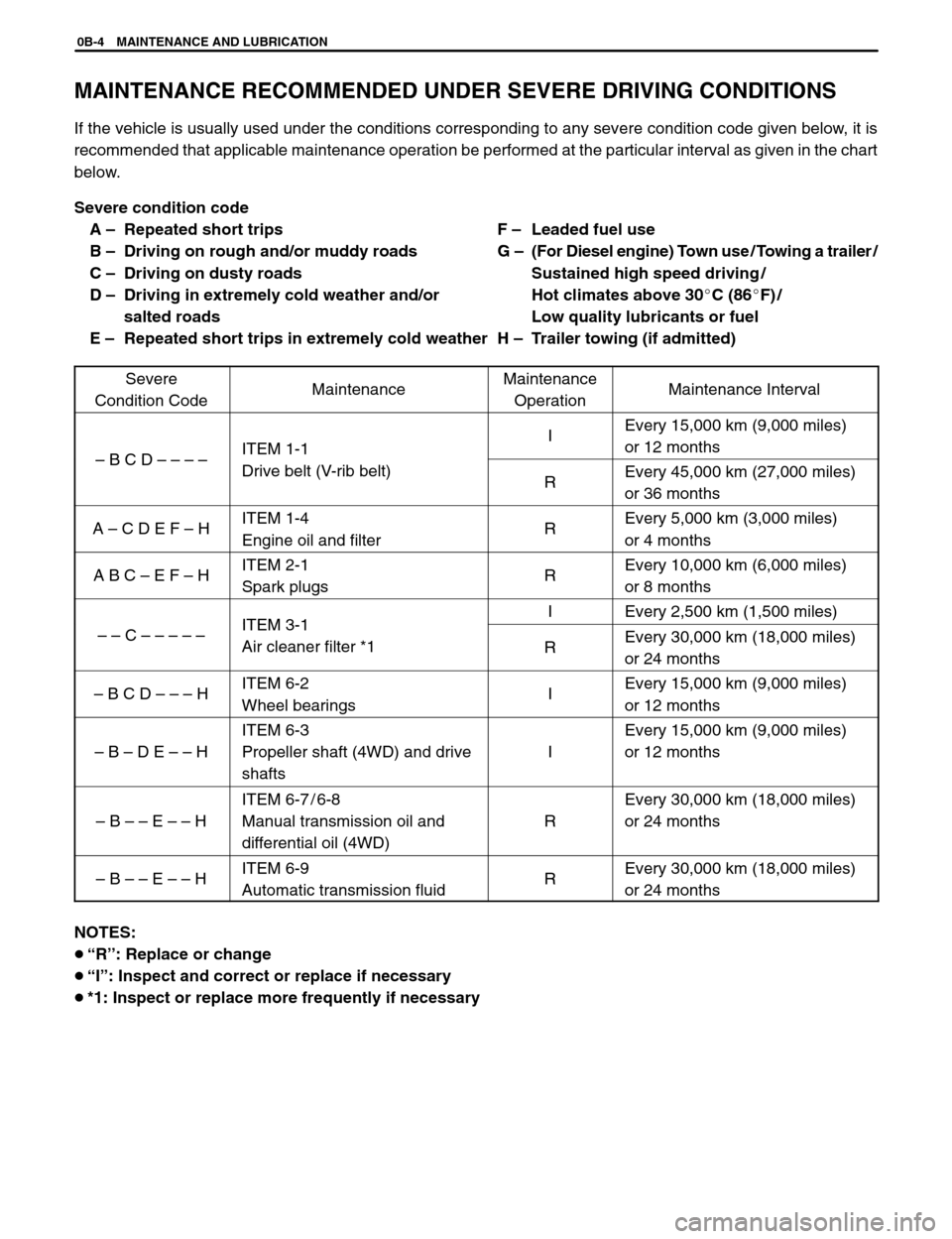
0B-4 MAINTENANCE AND LUBRICATION
MAINTENANCE RECOMMENDED UNDER SEVERE DRIVING CONDITIONS
If the vehicle is usually used under the conditions corresponding to any severe condition code given below, it is
recommended that applicable maintenance operation be performed at the particular interval as given in the chart
below.
Severe condition code
A –Repeated short trips F –Leaded fuel use
B –Driving on rough and/or muddy roads G –(For Diesel engine) Town use / Towing a trailer /
C –Driving on dusty roads Sustained high speed driving /
D –Driving in extremely cold weather and/or Hot climates above 30C (86F) /
salted roads Low quality lubricants or fuel
E –Repeated short trips in extremely cold weather H –Trailer towing (if admitted)
Severe
Condition Code
MaintenanceMaintenance
OperationMaintenance Interval
BCDITEM 1-1IEvery 15,000 km (9,000 miles)
or 12 months
– B C D – – – –Drive belt (V-rib belt)REvery 45,000 km (27,000 miles)
or 36 months
A – C D E F – HITEM 1-4
Engine oil and filterREvery 5,000 km (3,000 miles)
or 4 months
A B C – E F – HITEM 2-1
Spark plugsREvery 10,000 km (6,000 miles)
or 8 months
ITEM 3 1IEvery 2,500 km (1,500 miles)
– – C – – – – –ITEM 3-1
Air cleaner filter *1REvery 30,000 km (18,000 miles)
or 24 months
– B C D – – – HITEM 6-2
Wheel bearingsIEvery 15,000 km (9,000 miles)
or 12 months
– B – D E – – H
ITEM 6-3
Propeller shaft (4WD) and drive
shafts
I
Every 15,000 km (9,000 miles)
or 12 months
– B – – E – – H
ITEM 6-7 / 6-8
Manual transmission oil and
differential oil (4WD)
R
Every 30,000 km (18,000 miles)
or 24 months
– B – – E – – HITEM 6-9
Automatic transmission fluidREvery 30,000 km (18,000 miles)
or 24 months
NOTES:
“R”: Replace or change
“I”: Inspect and correct or replace if necessary
*1: Inspect or replace more frequently if necessary
Page 40 of 557
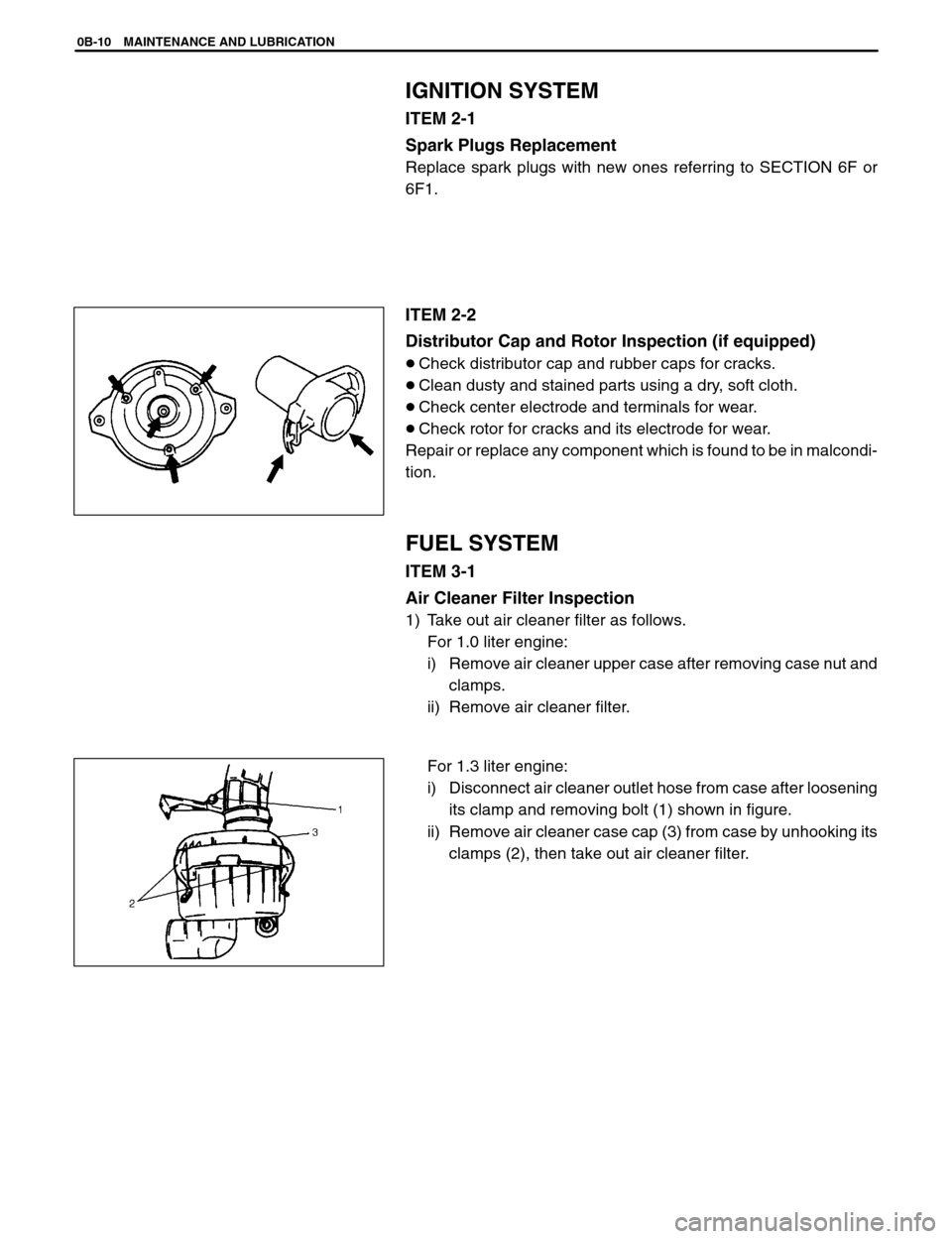
0B-10 MAINTENANCE AND LUBRICATION
IGNITION SYSTEM
ITEM 2-1
Spark Plugs Replacement
Replace spark plugs with new ones referring to SECTION 6F or
6F1.
ITEM 2-2
Distributor Cap and Rotor Inspection (if equipped)
Check distributor cap and rubber caps for cracks.
Clean dusty and stained parts using a dry, soft cloth.
Check center electrode and terminals for wear.
Check rotor for cracks and its electrode for wear.
Repair or replace any component which is found to be in malcondi-
tion.
FUEL SYSTEM
ITEM 3-1
Air Cleaner Filter Inspection
1) Take out air cleaner filter as follows.
For 1.0 liter engine:
i) Remove air cleaner upper case after removing case nut and
clamps.
ii) Remove air cleaner filter.
For 1.3 liter engine:
i) Disconnect air cleaner outlet hose from case after loosening
its clamp and removing bolt (1) shown in figure.
ii) Remove air cleaner case cap (3) from case by unhooking its
clamps (2), then take out air cleaner filter.
Page 41 of 557
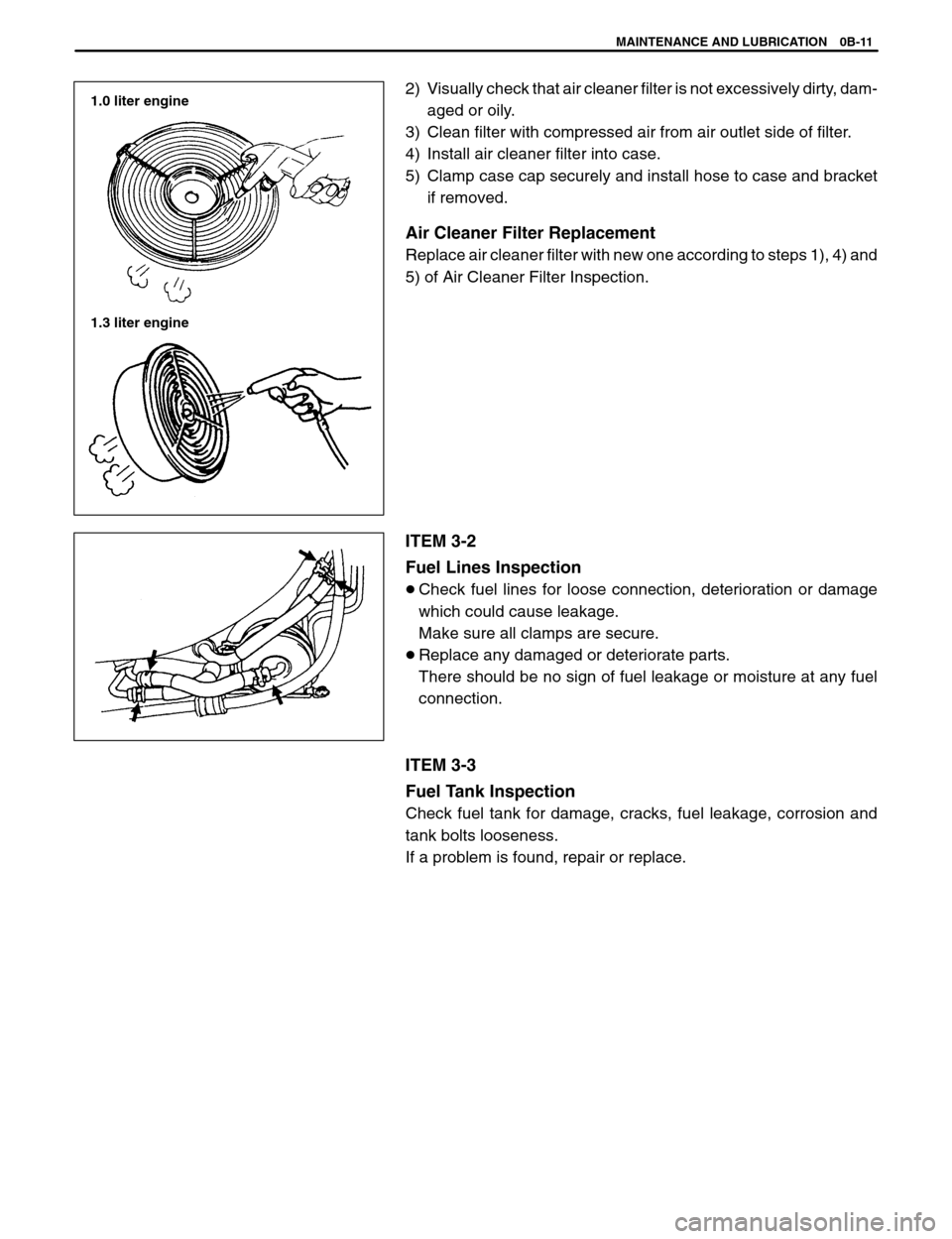
1.0 liter engine
1.3 liter engine
MAINTENANCE AND LUBRICATION 0B-11
2) Visually check that air cleaner filter is not excessively dirty, dam-
aged or oily.
3) Clean filter with compressed air from air outlet side of filter.
4) Install air cleaner filter into case.
5) Clamp case cap securely and install hose to case and bracket
if removed.
Air Cleaner Filter Replacement
Replace air cleaner filter with new one according to steps 1), 4) and
5) of Air Cleaner Filter Inspection.
ITEM 3-2
Fuel Lines Inspection
Check fuel lines for loose connection, deterioration or damage
which could cause leakage.
Make sure all clamps are secure.
Replace any damaged or deteriorate parts.
There should be no sign of fuel leakage or moisture at any fuel
connection.
ITEM 3-3
Fuel Tank Inspection
Check fuel tank for damage, cracks, fuel leakage, corrosion and
tank bolts looseness.
If a problem is found, repair or replace.
Page 76 of 557
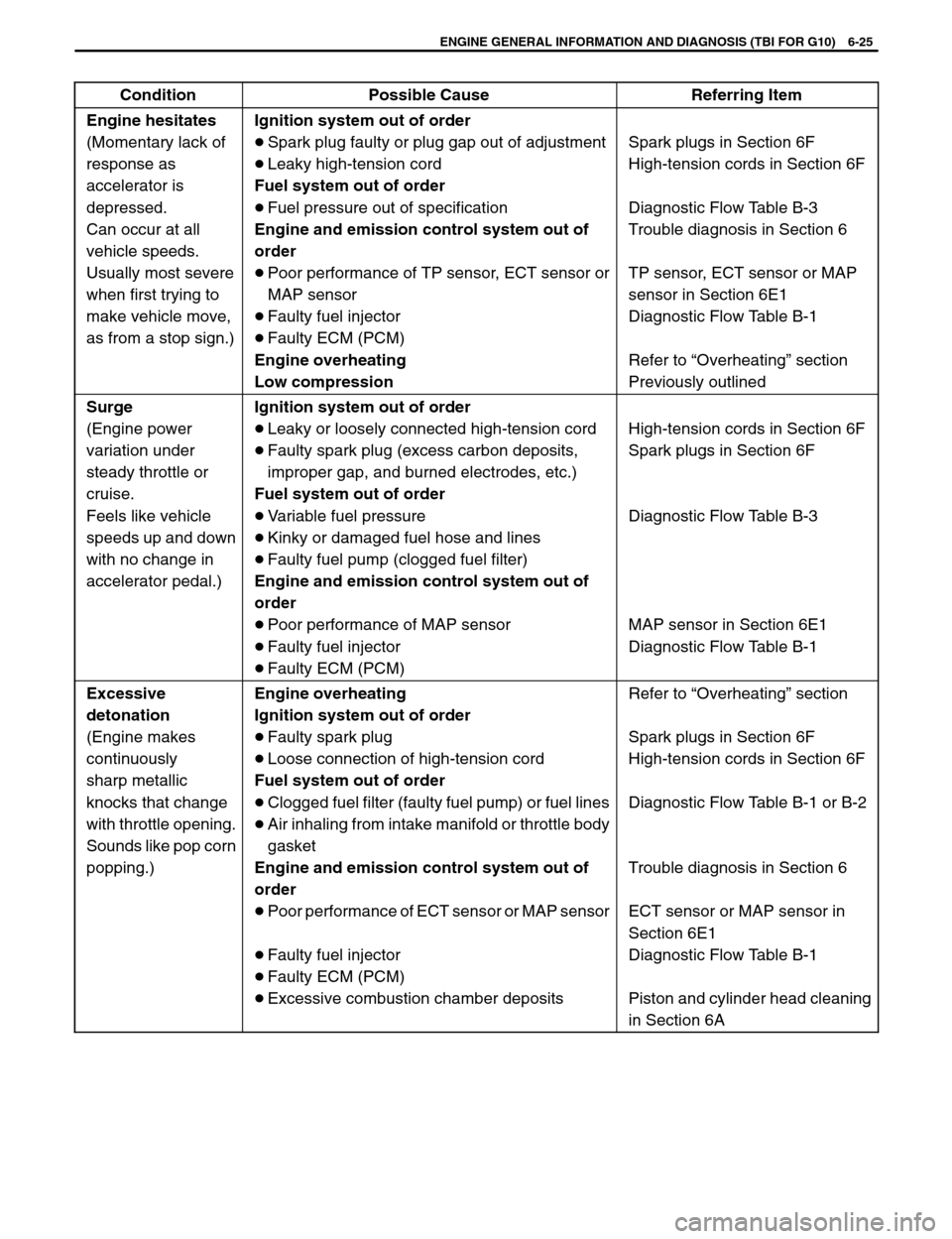
ENGINE GENERAL INFORMATION AND DIAGNOSIS (TBI FOR G10) 6-25
ConditionPossible CauseReferring Item
Engine hesitates
(Momentary lack of
response as
accelerator is
depressed.
Can occur at all
vehicle speeds.
Usually most severe
when first trying to
make vehicle move,
as from a stop sign.)Ignition system out of order
Spark plug faulty or plug gap out of adjustment
Leaky high-tension cord
Fuel system out of order
Fuel pressure out of specification
Engine and emission control system out of
order
Poor performance of TP sensor, ECT sensor or
MAP sensor
Faulty fuel injector
Faulty ECM (PCM)
Engine overheating
Low compression
Spark plugs in Section 6F
High-tension cords in Section 6F
Diagnostic Flow Table B-3
Trouble diagnosis in Section 6
TP sensor, ECT sensor or MAP
sensor in Section 6E1
Diagnostic Flow Table B-1
Refer to “Overheating” section
Previously outlined
Surge
(Engine power
variation under
steady throttle or
cruise.
Feels like vehicle
speeds up and down
with no change in
accelerator pedal.)Ignition system out of order
Leaky or loosely connected high-tension cord
Faulty spark plug (excess carbon deposits,
improper gap, and burned electrodes, etc.)
Fuel system out of order
Variable fuel pressure
Kinky or damaged fuel hose and lines
Faulty fuel pump (clogged fuel filter)
Engine and emission control system out of
order
Poor performance of MAP sensor
Faulty fuel injector
Faulty ECM (PCM)
High-tension cords in Section 6F
Spark plugs in Section 6F
Diagnostic Flow Table B-3
MAP sensor in Section 6E1
Diagnostic Flow Table B-1
Excessive
detonation
(Engine makes
continuously
sharp metallic
knocks that change
with throttle opening.
Sounds like pop corn
popping.)Engine overheating
Ignition system out of order
Faulty spark plug
Loose connection of high-tension cord
Fuel system out of order
Clogged fuel filter (faulty fuel pump) or fuel lines
Air inhaling from intake manifold or throttle body
gasket
Engine and emission control system out of
order
Poor performance of ECT sensor or MAP sensor
Faulty fuel injector
Faulty ECM (PCM)
Excessive combustion chamber depositsRefer to “Overheating” section
Spark plugs in Section 6F
High-tension cords in Section 6F
Diagnostic Flow Table B-1 or B-2
Trouble diagnosis in Section 6
ECT sensor or MAP sensor in
Section 6E1
Diagnostic Flow Table B-1
Piston and cylinder head cleaning
in Section 6A
Page 181 of 557
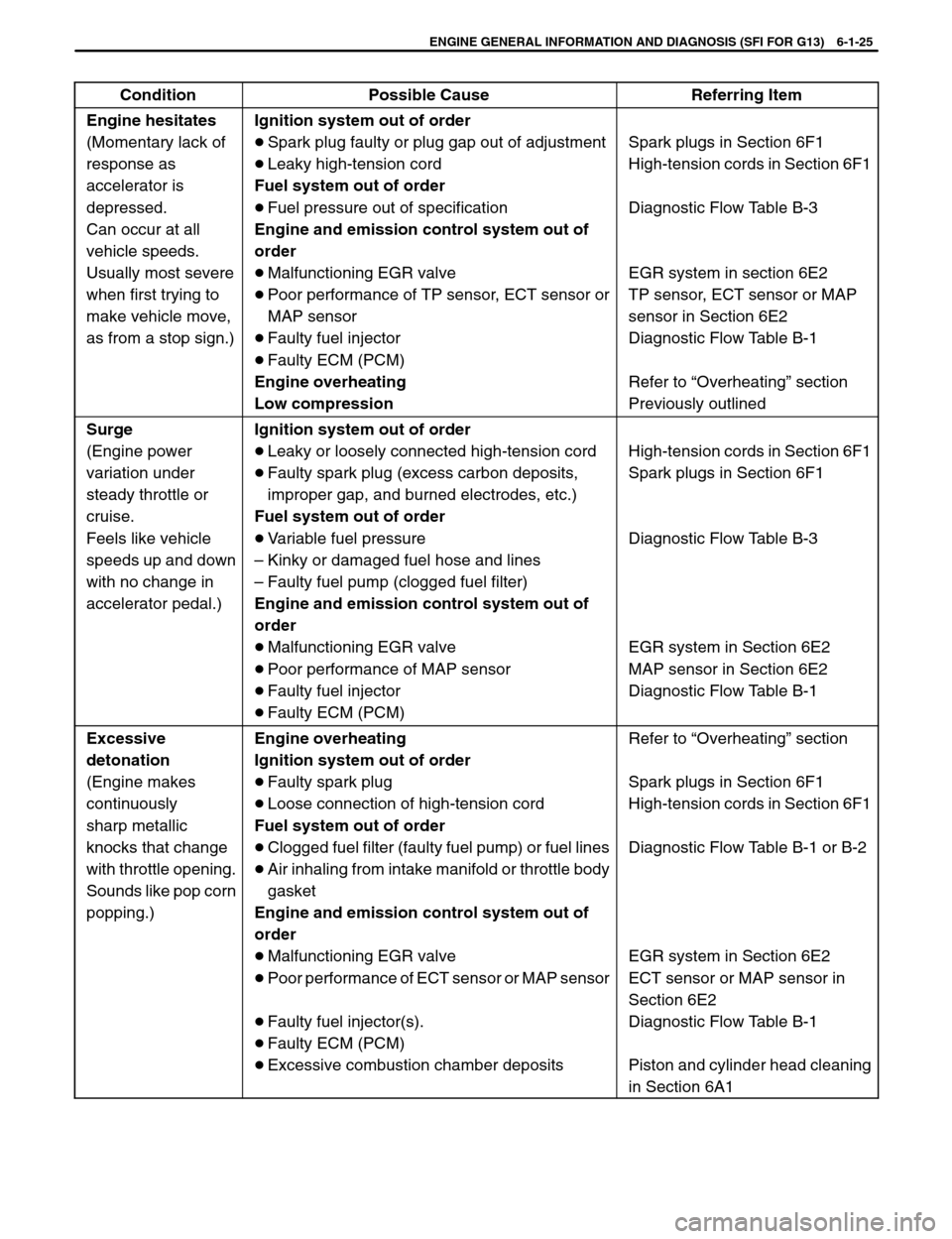
ENGINE GENERAL INFORMATION AND DIAGNOSIS (SFI FOR G13) 6-1-25
ConditionPossible CauseReferring Item
Engine hesitates
(Momentary lack of
response as
accelerator is
depressed.
Can occur at all
vehicle speeds.
Usually most severe
when first trying to
make vehicle move,
as from a stop sign.)Ignition system out of order
Spark plug faulty or plug gap out of adjustment
Leaky high-tension cord
Fuel system out of order
Fuel pressure out of specification
Engine and emission control system out of
order
Malfunctioning EGR valve
Poor performance of TP sensor, ECT sensor or
MAP sensor
Faulty fuel injector
Faulty ECM (PCM)
Engine overheating
Low compression
Spark plugs in Section 6F1
High-tension cords in Section 6F1
Diagnostic Flow Table B-3
EGR system in section 6E2
TP sensor, ECT sensor or MAP
sensor in Section 6E2
Diagnostic Flow Table B-1
Refer to “Overheating” section
Previously outlined
Surge
(Engine power
variation under
steady throttle or
cruise.
Feels like vehicle
speeds up and down
with no change in
accelerator pedal.)Ignition system out of order
Leaky or loosely connected high-tension cord
Faulty spark plug (excess carbon deposits,
improper gap, and burned electrodes, etc.)
Fuel system out of order
Variable fuel pressure
–Kinky or damaged fuel hose and lines
–Faulty fuel pump (clogged fuel filter)
Engine and emission control system out of
order
Malfunctioning EGR valve
Poor performance of MAP sensor
Faulty fuel injector
Faulty ECM (PCM)
High-tension cords in Section 6F1
Spark plugs in Section 6F1
Diagnostic Flow Table B-3
EGR system in Section 6E2
MAP sensor in Section 6E2
Diagnostic Flow Table B-1
Excessive
detonation
(Engine makes
continuously
sharp metallic
knocks that change
with throttle opening.
Sounds like pop corn
popping.)Engine overheating
Ignition system out of order
Faulty spark plug
Loose connection of high-tension cord
Fuel system out of order
Clogged fuel filter (faulty fuel pump) or fuel lines
Air inhaling from intake manifold or throttle body
gasket
Engine and emission control system out of
order
Malfunctioning EGR valve
Poor performance of ECT sensor or MAP sensor
Faulty fuel injector(s).
Faulty ECM (PCM)
Excessive combustion chamber depositsRefer to “Overheating” section
Spark plugs in Section 6F1
High-tension cords in Section 6F1
Diagnostic Flow Table B-1 or B-2
EGR system in Section 6E2
ECT sensor or MAP sensor in
Section 6E2
Diagnostic Flow Table B-1
Piston and cylinder head cleaning
in Section 6A1
Page 266 of 557
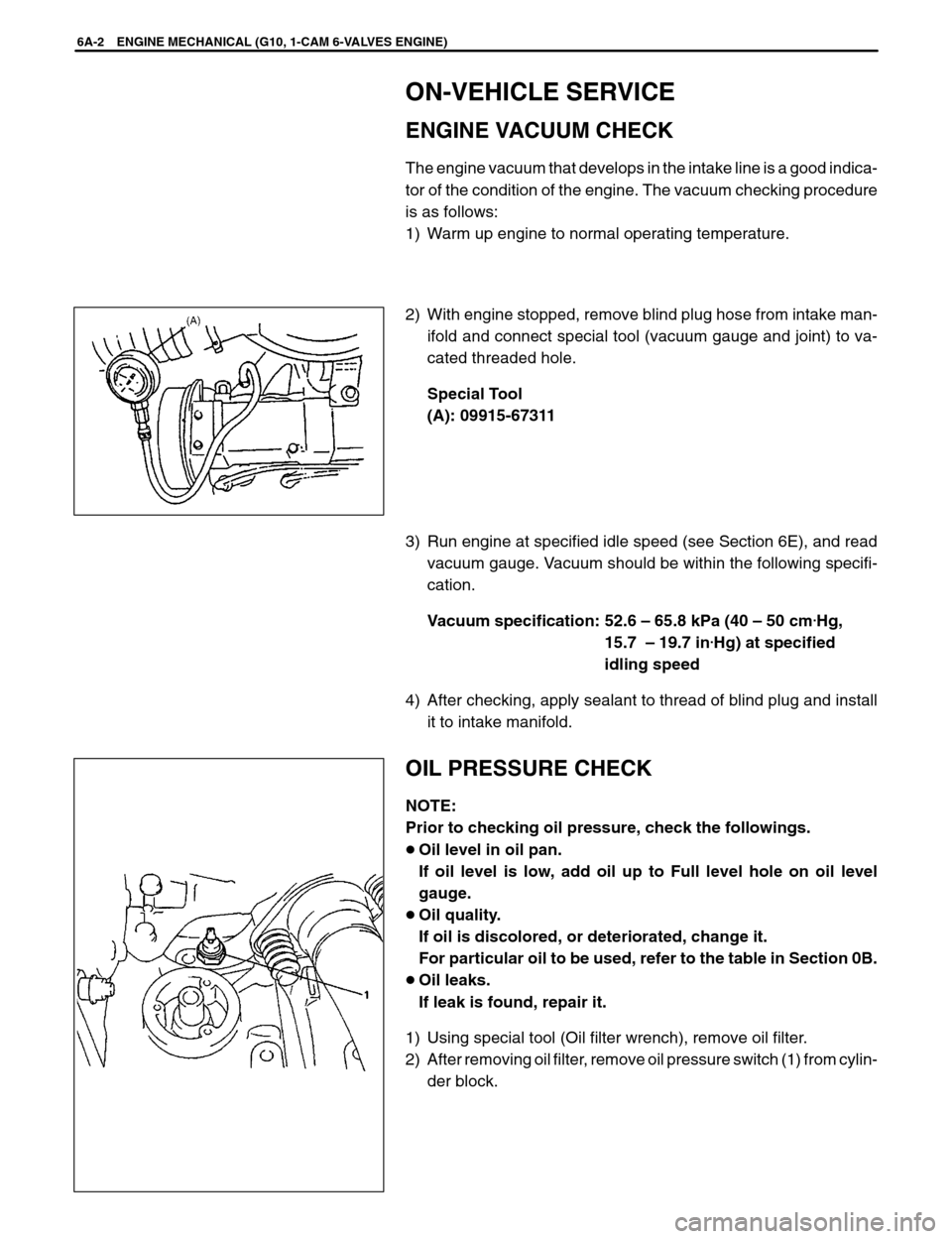
6A-2 ENGINE MECHANICAL (G10, 1-CAM 6-VALVES ENGINE)
ON-VEHICLE SERVICE
ENGINE VACUUM CHECK
The engine vacuum that develops in the intake line is a good indica-
tor of the condition of the engine. The vacuum checking procedure
is as follows:
1) Warm up engine to normal operating temperature.
2) With engine stopped, remove blind plug hose from intake man-
ifold and connect special tool (vacuum gauge and joint) to va-
cated threaded hole.
Special Tool
(A): 09915-67311
3) Run engine at specified idle speed (see Section 6E), and read
vacuum gauge. Vacuum should be within the following specifi-
cation.
Vacuum specification: 52.6 – 65.8 kPa (40 – 50 cm
.Hg,
15.7 – 19.7 in
.Hg) at specified
idling speed
4) After checking, apply sealant to thread of blind plug and install
it to intake manifold.
OIL PRESSURE CHECK
NOTE:
Prior to checking oil pressure, check the followings.
Oil level in oil pan.
If oil level is low, add oil up to Full level hole on oil level
gauge.
Oil quality.
If oil is discolored, or deteriorated, change it.
For particular oil to be used, refer to the table in Section 0B.
Oil leaks.
If leak is found, repair it.
1) Using special tool (Oil filter wrench), remove oil filter.
2) After removing oil filter, remove oil pressure switch (1) from cylin-
der block.
Page 395 of 557
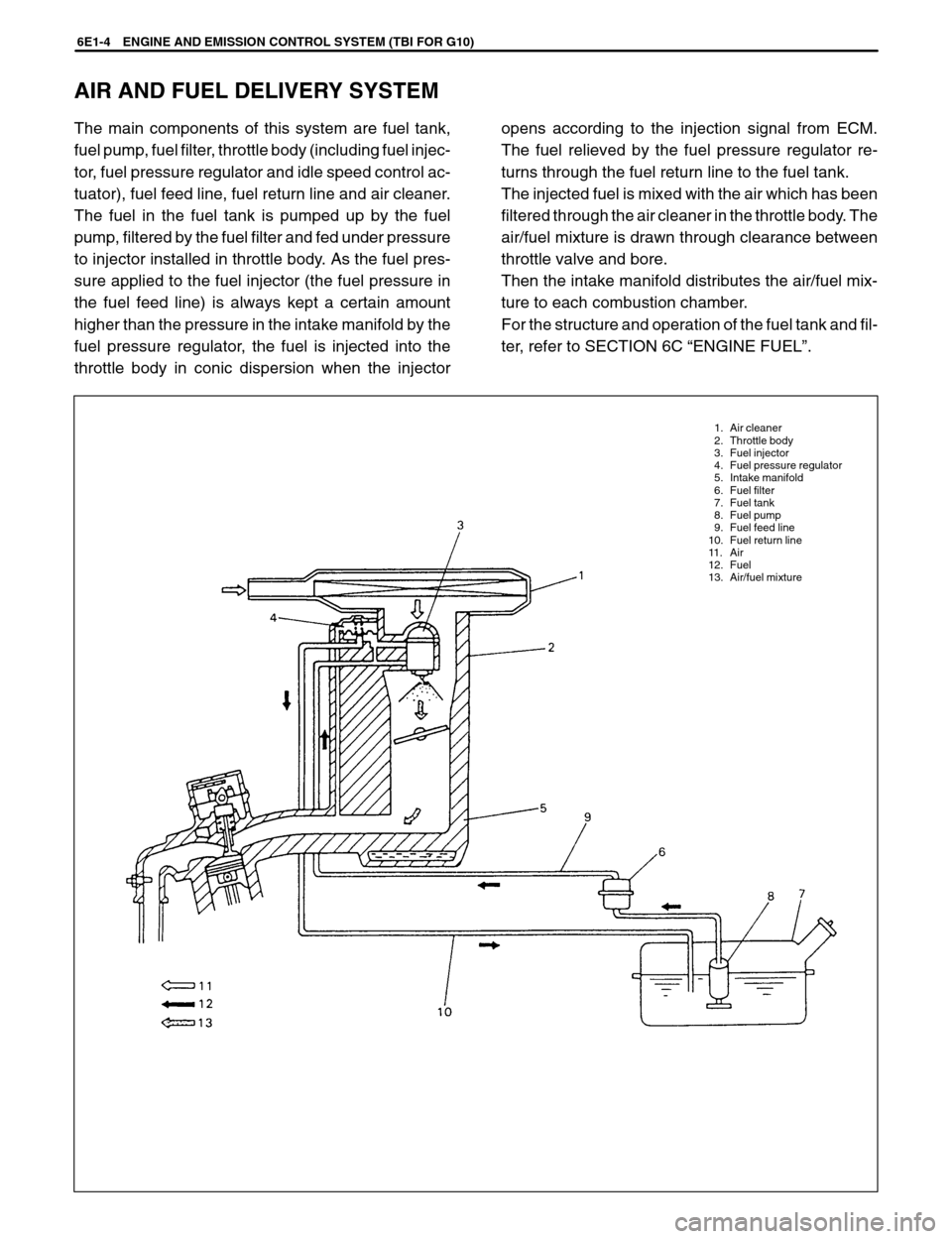
1. Air cleaner
2. Throttle body
3. Fuel injector
4. Fuel pressure regulator
5. Intake manifold
6. Fuel filter
7. Fuel tank
8. Fuel pump
9. Fuel feed line
10. Fuel return line
11. Air
12. Fuel
13. Air/fuel mixture
6E1-4 ENGINE AND EMISSION CONTROL SYSTEM (TBI FOR G10)
The main components of this system are fuel tank,
fuel pump, fuel filter, throttle body (including fuel injec-
tor, fuel pressure regulator and idle speed control ac-
tuator), fuel feed line, fuel return line and air cleaner.
The fuel in the fuel tank is pumped up by the fuel
pump, filtered by the fuel filter and fed under pressure
to injector installed in throttle body. As the fuel pres-
sure applied to the fuel injector (the fuel pressure in
the fuel feed line) is always kept a certain amount
higher than the pressure in the intake manifold by the
fuel pressure regulator, the fuel is injected into the
throttle body in conic dispersion when the injectoropens according to the injection signal from ECM.
The fuel relieved by the fuel pressure regulator re-
turns through the fuel return line to the fuel tank.
The injected fuel is mixed with the air which has been
filtered through the air cleaner in the throttle body. The
air/fuel mixture is drawn through clearance between
throttle valve and bore.
Then the intake manifold distributes the air/fuel mix-
ture to each combustion chamber.
For the structure and operation of the fuel tank and fil-
ter, refer to SECTION 6C “ENGINE FUEL”.
AIR AND FUEL DELIVERY SYSTEM
Page 407 of 557
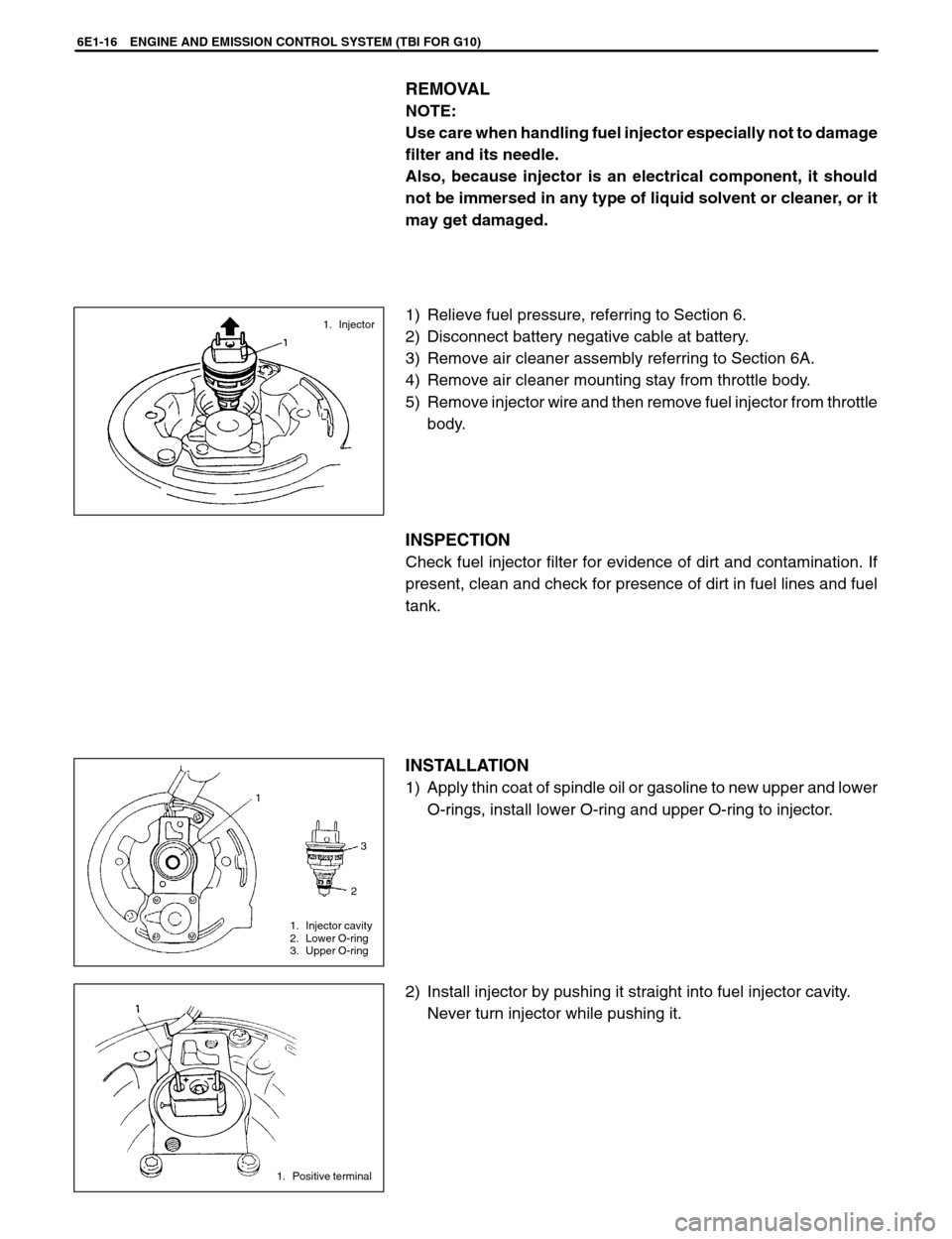
6E1-16 ENGINE AND EMISSION CONTROL SYSTEM (TBI FOR G10)
1. Injector
1
3
2
1. Injector cavity
2. Lower O-ring
3. Upper O-ring
1. Positive terminal
REMOVAL
NOTE:
Use care when handling fuel injector especially not to damage
filter and its needle.
Also, because injector is an electrical component, it should
not be immersed in any type of liquid solvent or cleaner, or it
may get damaged.
1) Relieve fuel pressure, referring to Section 6.
2) Disconnect battery negative cable at battery.
3) Remove air cleaner assembly referring to Section 6A.
4) Remove air cleaner mounting stay from throttle body.
5) Remove injector wire and then remove fuel injector from throttle
body.
INSPECTION
Check fuel injector filter for evidence of dirt and contamination. If
present, clean and check for presence of dirt in fuel lines and fuel
tank.
INSTALLATION
1) Apply thin coat of spindle oil or gasoline to new upper and lower
O-rings, install lower O-ring and upper O-ring to injector.
2) Install injector by pushing it straight into fuel injector cavity.
Never turn injector while pushing it.