jacking VAUXHALL ADAM 2017 Owner's Manual
[x] Cancel search | Manufacturer: VAUXHALL, Model Year: 2017, Model line: ADAM, Model: VAUXHALL ADAM 2017Pages: 241, PDF Size: 7.33 MB
Page 198 of 241
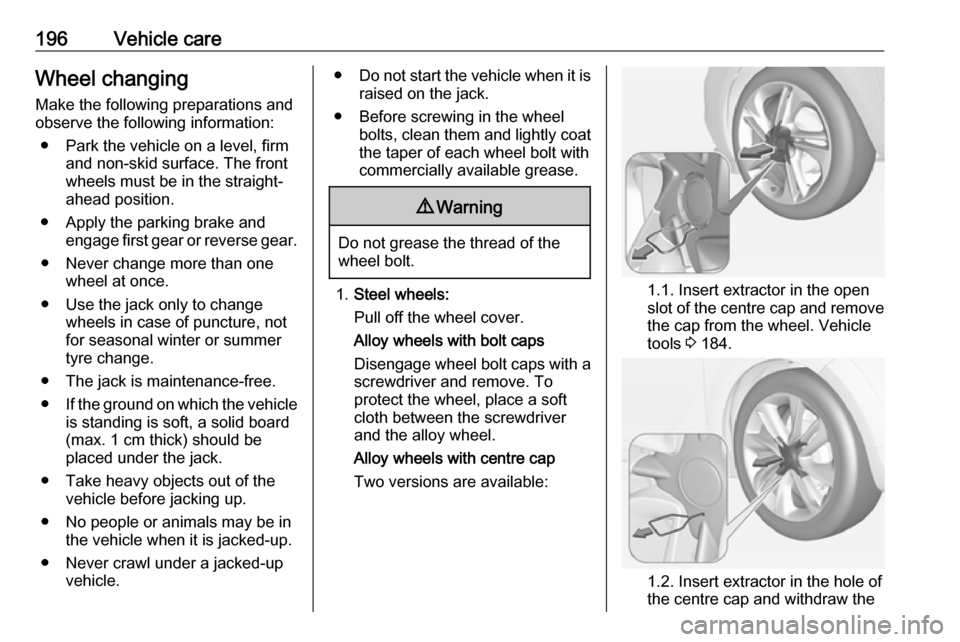
196Vehicle careWheel changingMake the following preparations and
observe the following information:
● Park the vehicle on a level, firm and non-skid surface. The front
wheels must be in the straight-
ahead position.
● Apply the parking brake and engage first gear or reverse gear.
● Never change more than one wheel at once.
● Use the jack only to change wheels in case of puncture, not
for seasonal winter or summer
tyre change.
● The jack is maintenance-free. ● If the ground on which the vehicle
is standing is soft, a solid board
(max. 1 cm thick) should be
placed under the jack.
● Take heavy objects out of the vehicle before jacking up.
● No people or animals may be in the vehicle when it is jacked-up.
● Never crawl under a jacked-up vehicle.●Do not start the vehicle when it is
raised on the jack.
● Before screwing in the wheel bolts, clean them and lightly coat
the taper of each wheel bolt with
commercially available grease.9 Warning
Do not grease the thread of the
wheel bolt.
1. Steel wheels:
Pull off the wheel cover.
Alloy wheels with bolt caps Disengage wheel bolt caps with a
screwdriver and remove. To
protect the wheel, place a soft
cloth between the screwdriver
and the alloy wheel.
Alloy wheels with centre cap
Two versions are available:1.1. Insert extractor in the open
slot of the centre cap and remove the cap from the wheel. Vehicle
tools 3 184.
1.2. Insert extractor in the hole of
the centre cap and withdraw the
Page 199 of 241
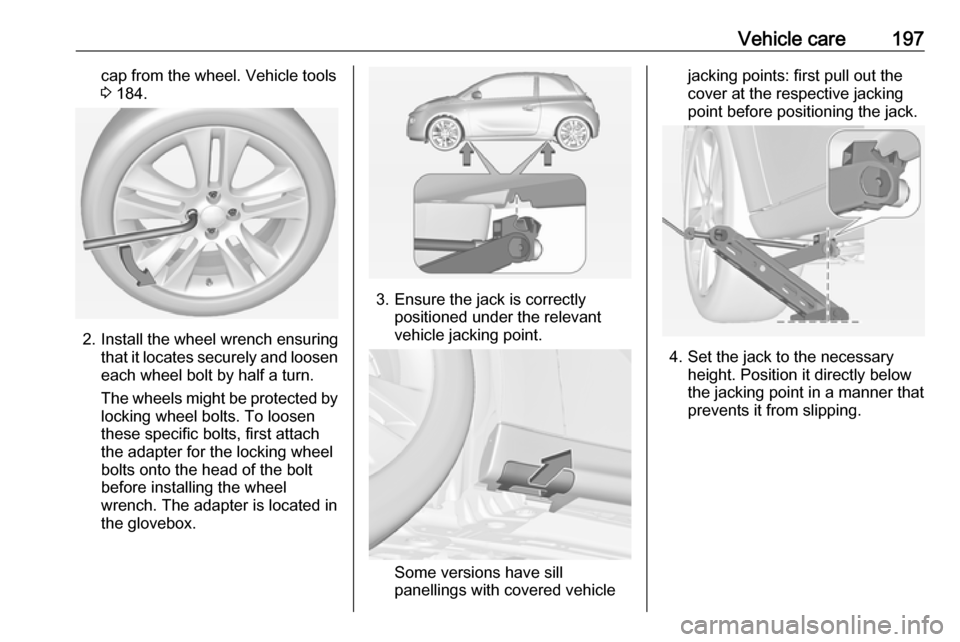
Vehicle care197cap from the wheel. Vehicle tools
3 184.
2. Install the wheel wrench ensuring
that it locates securely and loosen
each wheel bolt by half a turn.
The wheels might be protected by
locking wheel bolts. To loosen
these specific bolts, first attach
the adapter for the locking wheel
bolts onto the head of the bolt
before installing the wheel
wrench. The adapter is located in
the glovebox.
3. Ensure the jack is correctly positioned under the relevant
vehicle jacking point.
Some versions have sill
panellings with covered vehicle
jacking points: first pull out the
cover at the respective jacking
point before positioning the jack.
4. Set the jack to the necessary height. Position it directly below
the jacking point in a manner that
prevents it from slipping.
Page 200 of 241
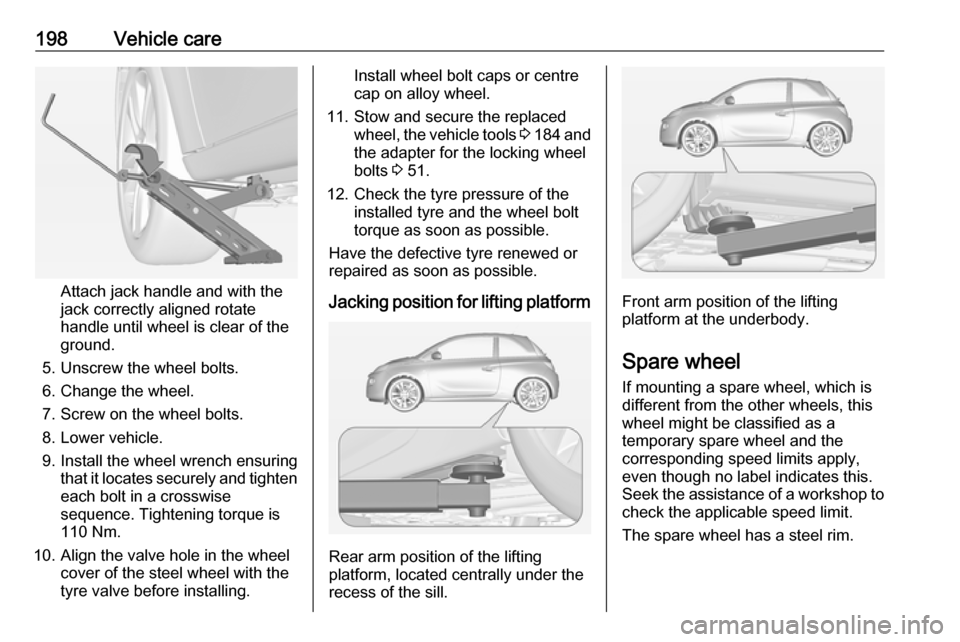
198Vehicle care
Attach jack handle and with the
jack correctly aligned rotate handle until wheel is clear of theground.
5. Unscrew the wheel bolts.
6. Change the wheel.
7. Screw on the wheel bolts.
8. Lower vehicle.
9. Install the wheel wrench ensuring that it locates securely and tighten
each bolt in a crosswise
sequence. Tightening torque is
110 Nm.
10. Align the valve hole in the wheel cover of the steel wheel with the
tyre valve before installing.
Install wheel bolt caps or centre
cap on alloy wheel.
11. Stow and secure the replaced wheel, the vehicle tools 3 184 and
the adapter for the locking wheel
bolts 3 51.
12. Check the tyre pressure of the installed tyre and the wheel bolt
torque as soon as possible.
Have the defective tyre renewed or
repaired as soon as possible.
Jacking position for lifting platform
Rear arm position of the lifting
platform, located centrally under the
recess of the sill.
Front arm position of the lifting platform at the underbody.
Spare wheel If mounting a spare wheel, which is
different from the other wheels, this
wheel might be classified as a
temporary spare wheel and the
corresponding speed limits apply,
even though no label indicates this.
Seek the assistance of a workshop to
check the applicable speed limit.
The spare wheel has a steel rim.
Page 231 of 241
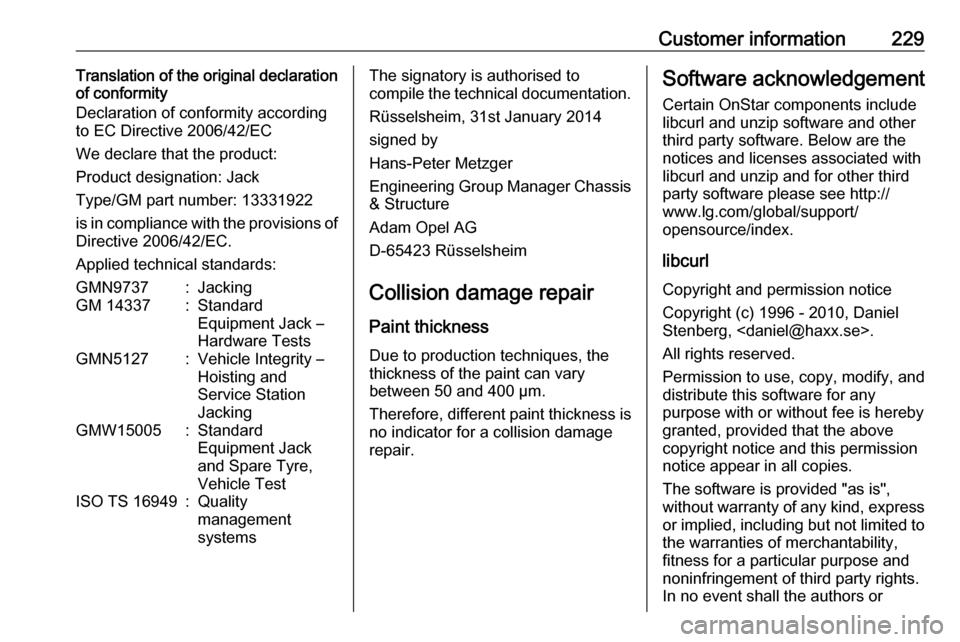
Customer information229Translation of the original declaration
of conformity
Declaration of conformity according
to EC Directive 2006/42/EC
We declare that the product:
Product designation: Jack
Type/GM part number: 13331922
is in compliance with the provisions of
Directive 2006/42/EC.
Applied technical standards:GMN9737:JackingGM 14337:Standard
Equipment Jack –
Hardware TestsGMN5127:Vehicle Integrity –
Hoisting and
Service Station
JackingGMW15005:Standard
Equipment Jack
and Spare Tyre,
Vehicle TestISO TS 16949:Quality
management
systemsThe signatory is authorised to
compile the technical documentation.
Rüsselsheim, 31st January 2014
signed by
Hans-Peter Metzger
Engineering Group Manager Chassis & Structure
Adam Opel AG
D-65423 Rüsselsheim
Collision damage repair
Paint thickness Due to production techniques, the
thickness of the paint can vary
between 50 and 400 µm.
Therefore, different paint thickness is
no indicator for a collision damage
repair.Software acknowledgement
Certain OnStar components include
libcurl and unzip software and other
third party software. Below are the
notices and licenses associated with
libcurl and unzip and for other third
party software please see http://
www.lg.com/global/support/
opensource/index.
libcurl Copyright and permission notice
Copyright (c) 1996 - 2010, Daniel
Stenberg,
All rights reserved.
Permission to use, copy, modify, and
distribute this software for any
purpose with or without fee is hereby
granted, provided that the above
copyright notice and this permission
notice appear in all copies.
The software is provided "as is",
without warranty of any kind, express
or implied, including but not limited to the warranties of merchantability,
fitness for a particular purpose and
noninfringement of third party rights.
In no event shall the authors or