engine YAMAHA TTR90 2002 Notices Demploi (in French)
[x] Cancel search | Manufacturer: YAMAHA, Model Year: 2002, Model line: TTR90, Model: YAMAHA TTR90 2002Pages: 288, PDF Size: 15.07 MB
Page 118 of 288
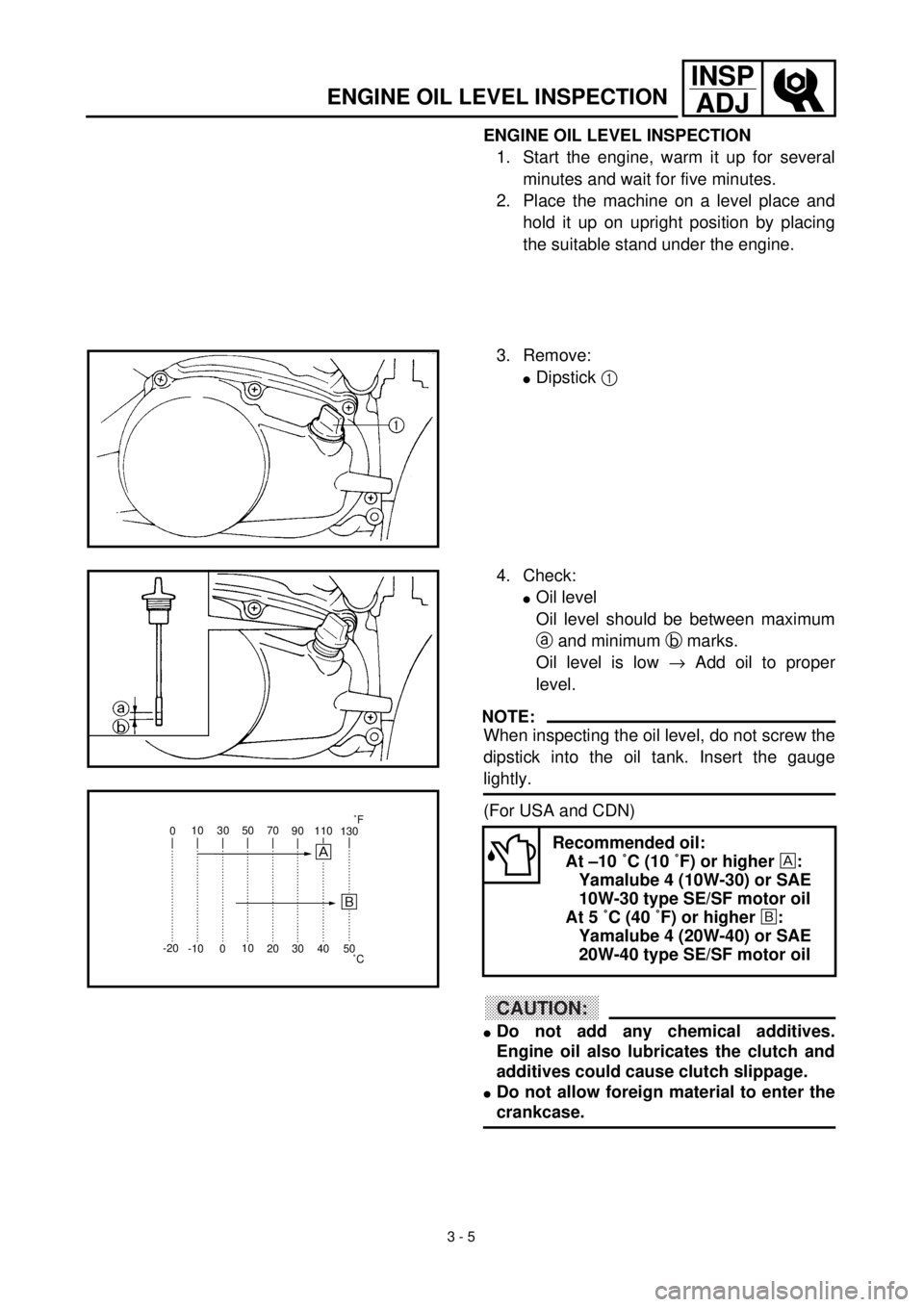
3 - 5
INSP
ADJ
ENGINE OIL LEVEL INSPECTION
1. Start the engine, warm it up for several
minutes and wait for five minutes.
2. Place the machine on a level place and
hold it up on upright position by placing
the suitable stand under the engine.
3. Remove:
lDipstick 1
4. Check:
lOil level
Oil level should be between maximum
a and minimum b marks.
Oil level is low ® Add oil to proper
level.
NOTE:
When inspecting the oil level, do not screw the
dipstick into the oil tank. Insert the gauge
lightly.
(For USA and CDN)
CAUTION:
lDo not add any chemical additives.
Engine oil also lubricates the clutch and
additives could cause clutch slippage.
lDo not allow foreign material to enter the
crankcase.
Recommended oil:
At –10 ˚C (10 ˚F) or higher :
Yamalube 4 (10W-30) or SAE
10W-30 type SE/SF motor oil
At 5 ˚C (40 ˚F) or higher õ:
Yamalube 4 (20W-40) or SAE
20W-40 type SE/SF motor oil010 30 50 70
90110
130
-20
-10010
20 30 40
50
õ
˚C˚F
ENGINE OIL LEVEL INSPECTION
Page 120 of 288
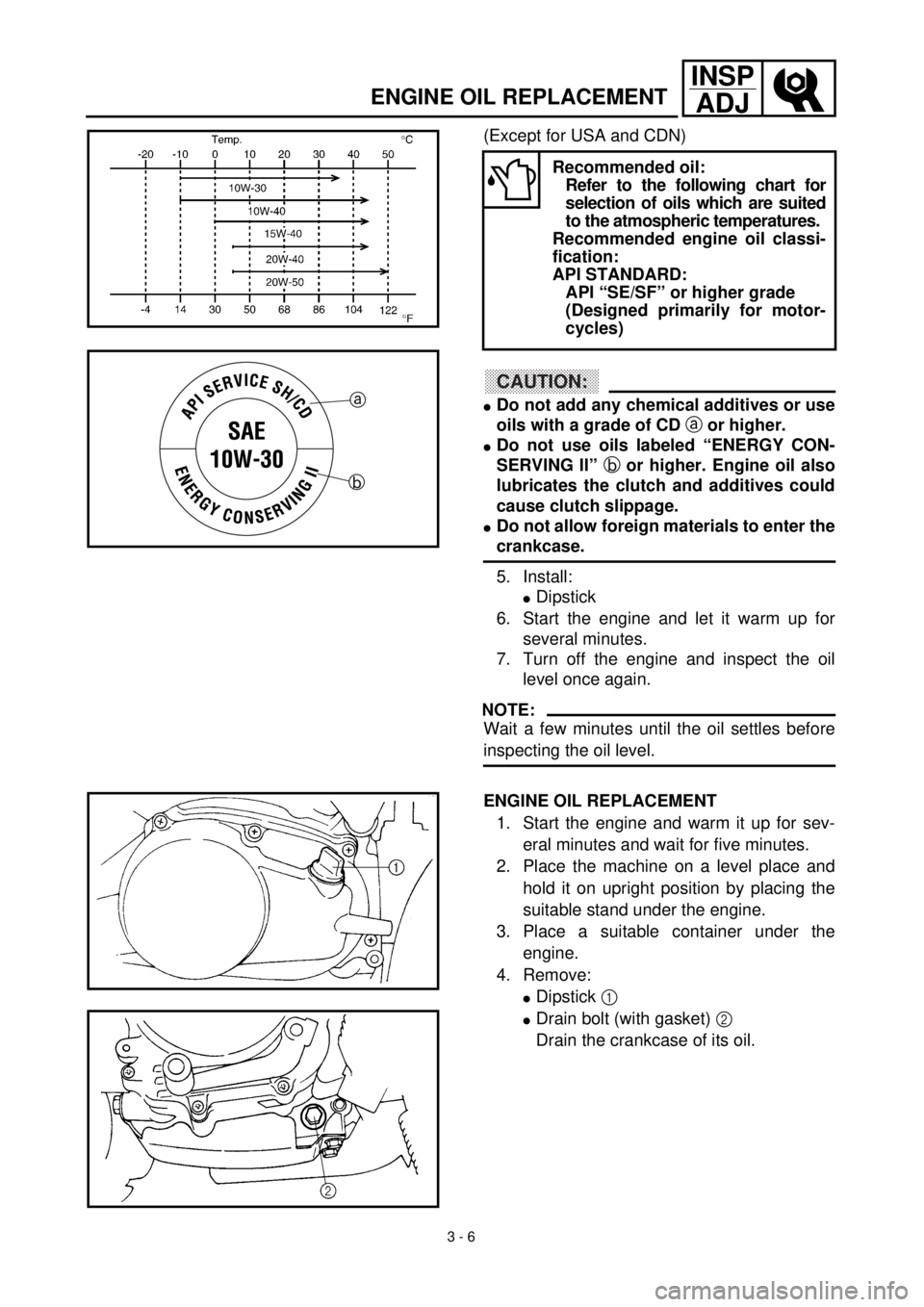
3 - 6
INSP
ADJ
ENGINE OIL REPLACEMENT
(Except for USA and CDN)
CAUTION:
lDo not add any chemical additives or use
oils with a grade of CD a or higher.
lDo not use oils labeled “ENERGY CON-
SERVING II” b or higher. Engine oil also
lubricates the clutch and additives could
cause clutch slippage.
lDo not allow foreign materials to enter the
crankcase.
5. Install:
lDipstick
6. Start the engine and let it warm up for
several minutes.
7. Turn off the engine and inspect the oil
level once again.
NOTE:
Wait a few minutes until the oil settles before
inspecting the oil level.
ENGINE OIL REPLACEMENT
1. Start the engine and warm it up for sev-
eral minutes and wait for five minutes.
2. Place the machine on a level place and
hold it on upright position by placing the
suitable stand under the engine.
3. Place a suitable container under the
engine.
4. Remove:
lDipstick 1
lDrain bolt (with gasket) 2
Drain the crankcase of its oil.
Recommended oil:
Refer to the following chart for
selection of oils which are suited
to the atmospheric temperatures.
Recommended engine oil classi-
fication:
API STANDARD:
API “SE/SF” or higher grade
(Designed primarily for motor-
cycles)
a
b
Page 122 of 288
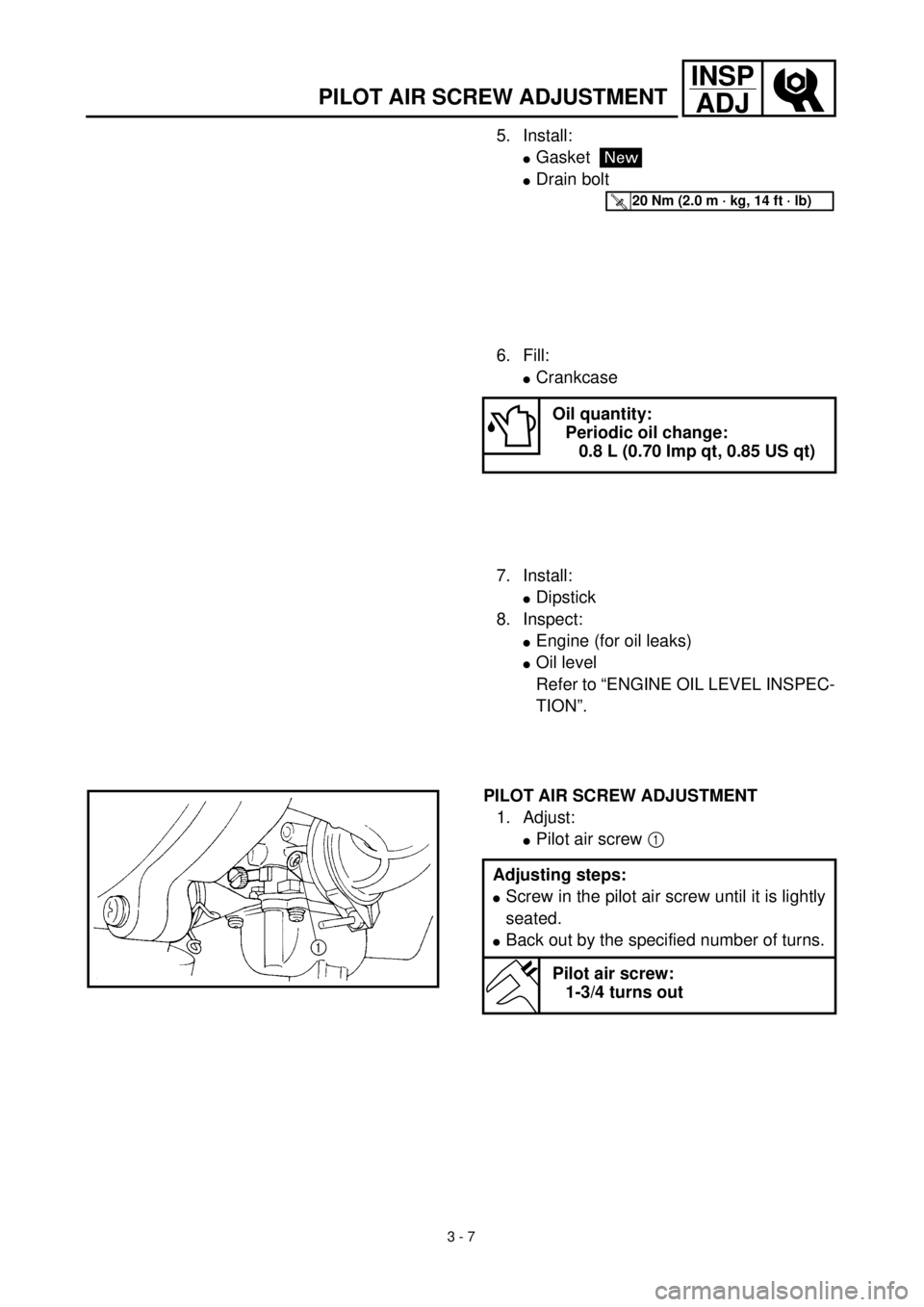
3 - 7
INSP
ADJ
PILOT AIR SCREW ADJUSTMENT
5. Install:
lGasket
lDrain bolt
New
T R..20 Nm (2.0 m · kg, 14 ft · lb)
6. Fill:
lCrankcase
Oil quantity:
Periodic oil change:
0.8 L (0.70 Imp qt, 0.85 US qt)
7. Install:
lDipstick
8. Inspect:
lEngine (for oil leaks)
lOil level
Refer to “ENGINE OIL LEVEL INSPEC-
TION”.
PILOT AIR SCREW ADJUSTMENT
1. Adjust:
lPilot air screw 1
Adjusting steps:
lScrew in the pilot air screw until it is lightly
seated.
lBack out by the specified number of turns.
Pilot air screw:
1-3/4 turns out
Page 124 of 288
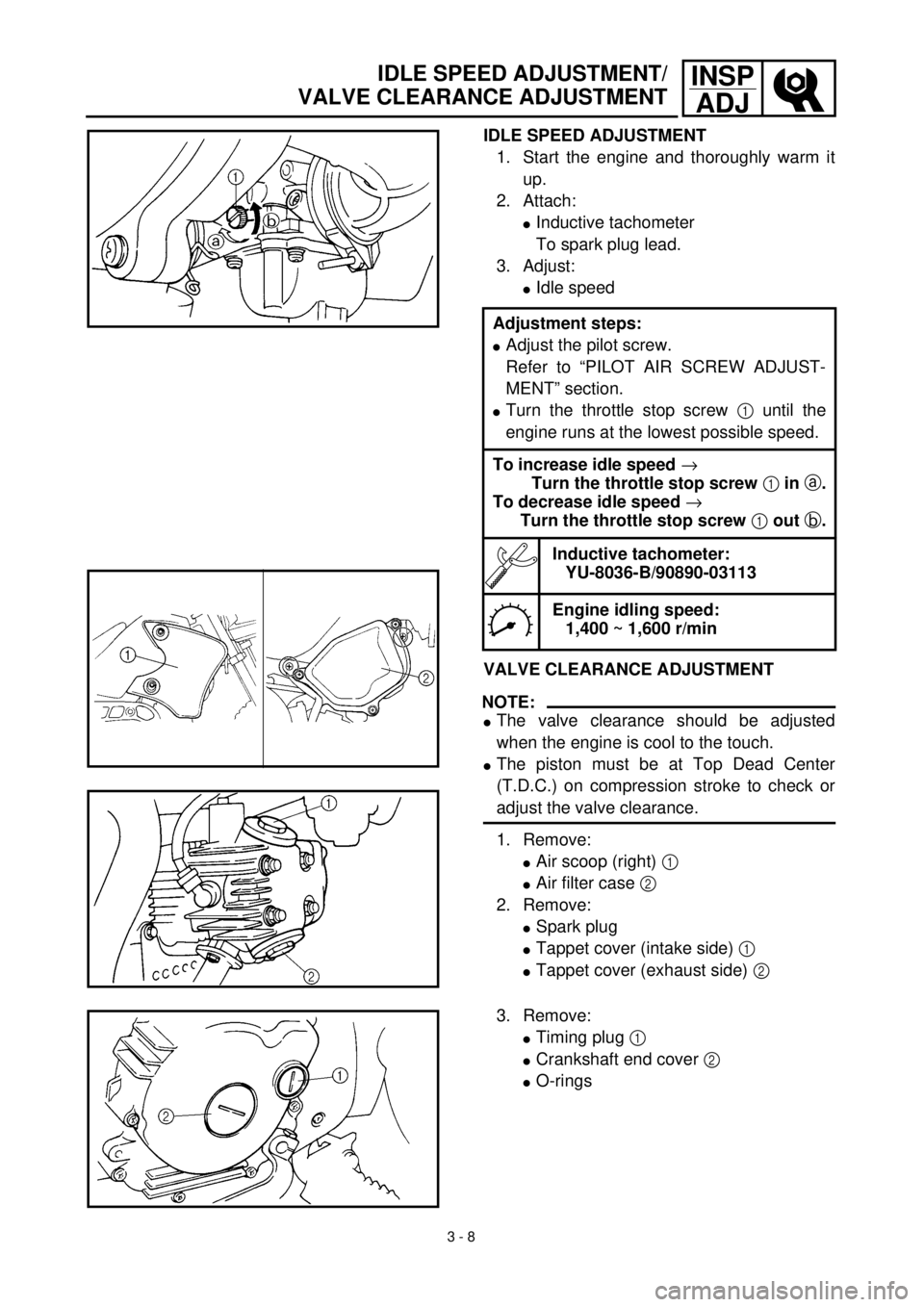
3 - 8
INSP
ADJIDLE SPEED ADJUSTMENT/
VALVE CLEARANCE ADJUSTMENT
IDLE SPEED ADJUSTMENT
1. Start the engine and thoroughly warm it
up.
2. Attach:
lInductive tachometer
To spark plug lead.
3. Adjust:
lIdle speed
VALVE CLEARANCE ADJUSTMENT
NOTE:
lThe valve clearance should be adjusted
when the engine is cool to the touch.
lThe piston must be at Top Dead Center
(T.D.C.) on compression stroke to check or
adjust the valve clearance.
1. Remove:
lAir scoop (right) 1
lAir filter case 2
2. Remove:
lSpark plug
lTappet cover (intake side) 1
lTappet cover (exhaust side) 2 Adjustment steps:
lAdjust the pilot screw.
Refer to “PILOT AIR SCREW ADJUST-
MENT” section.
lTurn the throttle stop screw 1 until the
engine runs at the lowest possible speed.
To increase idle speed ®
Turn the throttle stop screw 1 in a.
To decrease idle speed ®
Turn the throttle stop screw 1 out b.
Inductive tachometer:
YU-8036-B/90890-03113
Engine idling speed:
1,400 ~ 1,600 r/min
3. Remove:
lTiming plug 1
lCrankshaft end cover 2
lO-rings
Page 128 of 288
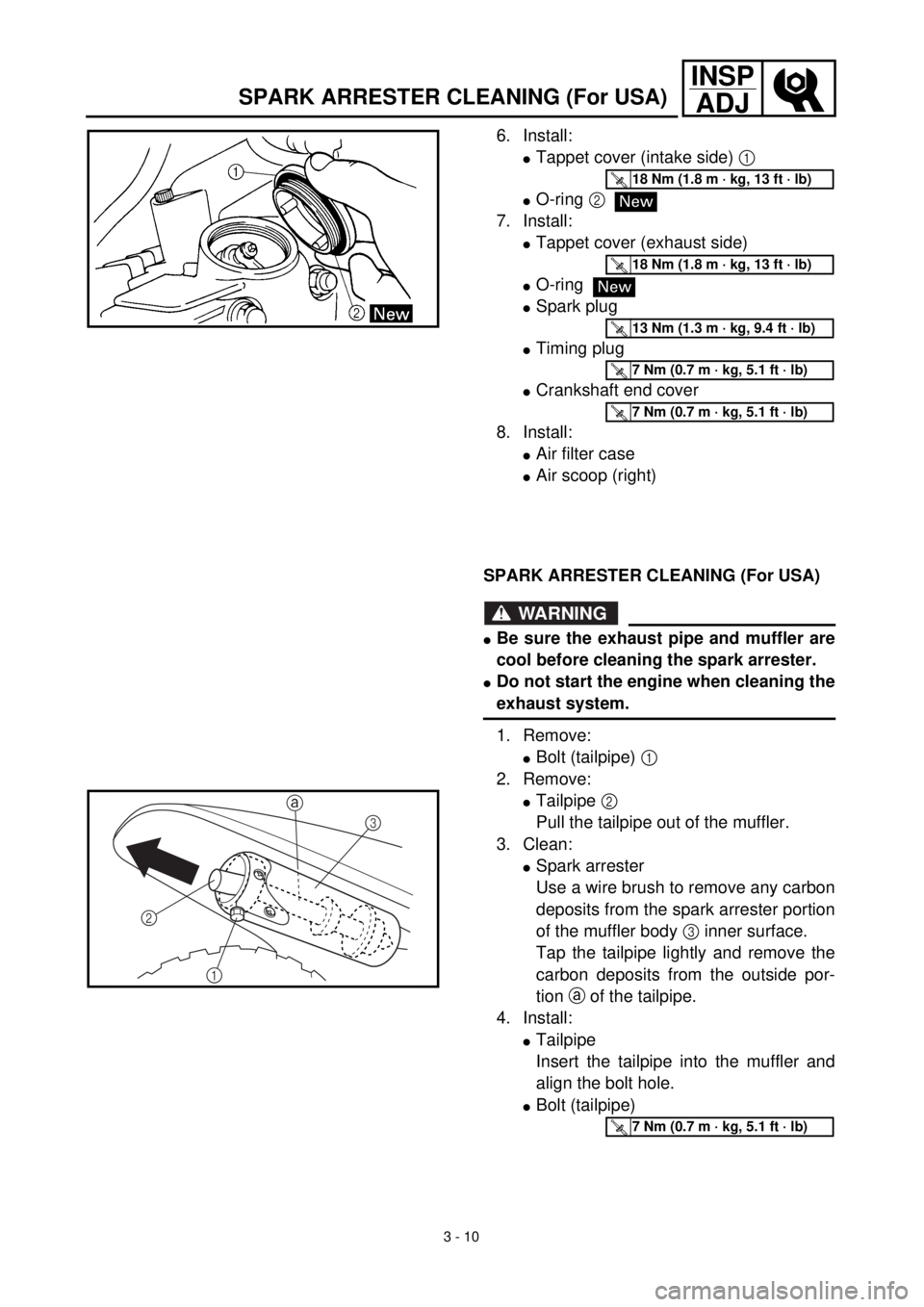
3 - 10
INSP
ADJ
SPARK ARRESTER CLEANING (For USA)
6. Install:
lTappet cover (intake side) 1
lO-ring 2
7. Install:
lTappet cover (exhaust side)
lO-ring
lSpark plug
lTiming plug
lCrankshaft end cover
8. Install:
lAir filter case
lAir scoop (right)
T R..18 Nm (1.8 m · kg, 13 ft · lb)
New
T R..18 Nm (1.8 m · kg, 13 ft · lb)
New
T R..13 Nm (1.3 m · kg, 9.4 ft · lb)
T R..7 Nm (0.7 m · kg, 5.1 ft · lb)
T R..7 Nm (0.7 m · kg, 5.1 ft · lb)
SPARK ARRESTER CLEANING (For USA)
WARNING
lBe sure the exhaust pipe and muffler are
cool before cleaning the spark arrester.
lDo not start the engine when cleaning the
exhaust system.
1. Remove:
lBolt (tailpipe) 1
2. Remove:
lTailpipe 2
Pull the tailpipe out of the muffler.
3. Clean:
lSpark arrester
Use a wire brush to remove any carbon
deposits from the spark arrester portion
of the muffler body 3 inner surface.
Tap the tailpipe lightly and remove the
carbon deposits from the outside por-
tion a of the tailpipe.
4. Install:
lTailpipe
Insert the tailpipe into the muffler and
align the bolt hole.
lBolt (tailpipe)
2
1
3
a
T R..7 Nm (0.7 m · kg, 5.1 ft · lb)
Page 132 of 288
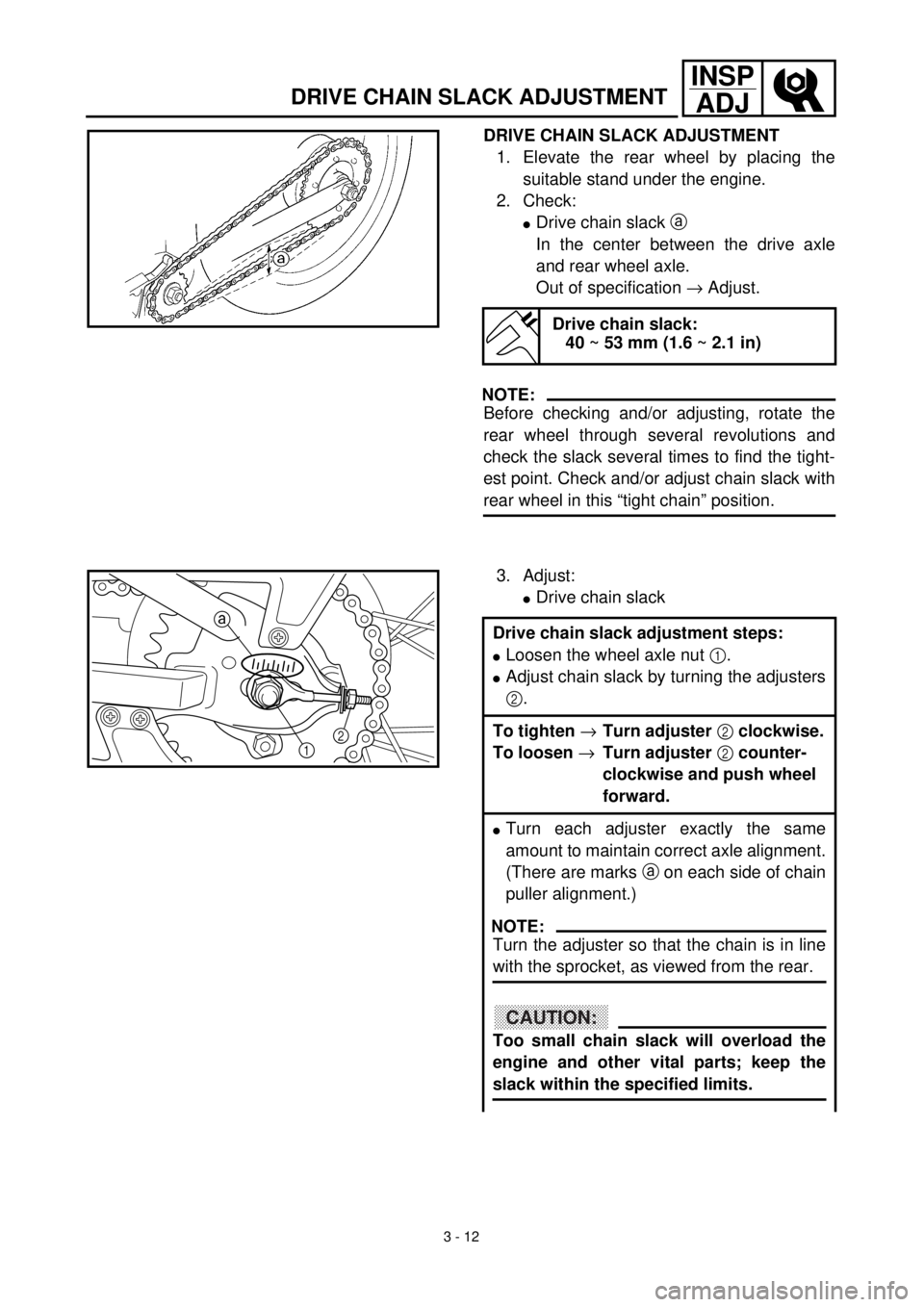
3 - 12
INSP
ADJ
DRIVE CHAIN SLACK ADJUSTMENT
DRIVE CHAIN SLACK ADJUSTMENT
1. Elevate the rear wheel by placing the
suitable stand under the engine.
2. Check:
lDrive chain slack a
In the center between the drive axle
and rear wheel axle.
Out of specification ® Adjust.
NOTE:
Before checking and/or adjusting, rotate the
rear wheel through several revolutions and
check the slack several times to find the tight-
est point. Check and/or adjust chain slack with
rear wheel in this “tight chain” position.
Drive chain slack:
40 ~ 53 mm (1.6 ~ 2.1 in)
3. Adjust:
lDrive chain slack
Drive chain slack adjustment steps:
lLoosen the wheel axle nut 1.
lAdjust chain slack by turning the adjusters
2.
To tighten ®Turn adjuster 2 clockwise.
To loosen ®Turn adjuster 2 counter-
clockwise and push wheel
forward.
lTurn each adjuster exactly the same
amount to maintain correct axle alignment.
(There are marks a on each side of chain
puller alignment.)
NOTE:
Turn the adjuster so that the chain is in line
with the sprocket, as viewed from the rear.
CAUTION:
Too small chain slack will overload the
engine and other vital parts; keep the
slack within the specified limits.
12 a
Page 134 of 288
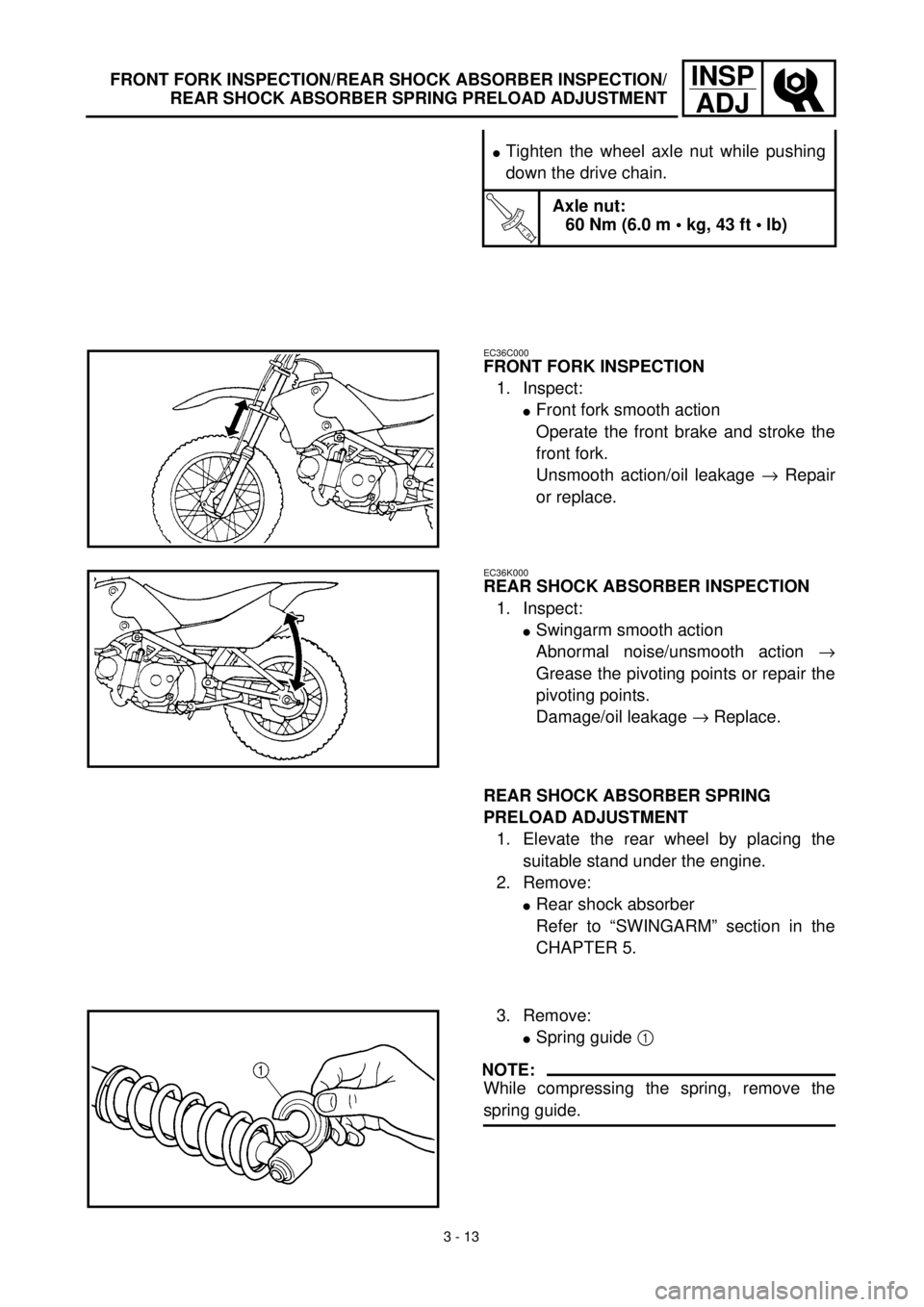
3 - 13
INSP
ADJFRONT FORK INSPECTION/REAR SHOCK ABSORBER INSPECTION/
REAR SHOCK ABSORBER SPRING PRELOAD ADJUSTMENT
lTighten the wheel axle nut while pushing
down the drive chain.
T R..
Axle nut:
60 Nm (6.0 m • kg, 43 ft • lb)
EC36C000
FRONT FORK INSPECTION
1. Inspect:
lFront fork smooth action
Operate the front brake and stroke the
front fork.
Unsmooth action/oil leakage ® Repair
or replace.
EC36K000
REAR SHOCK ABSORBER INSPECTION
1. Inspect:
lSwingarm smooth action
Abnormal noise/unsmooth action ®
Grease the pivoting points or repair the
pivoting points.
Damage/oil leakage ® Replace.
REAR SHOCK ABSORBER SPRING
PRELOAD ADJUSTMENT
1. Elevate the rear wheel by placing the
suitable stand under the engine.
2. Remove:
lRear shock absorber
Refer to “SWINGARM” section in the
CHAPTER 5.
3. Remove:
lSpring guide 1
NOTE:
While compressing the spring, remove the
spring guide.
Page 138 of 288
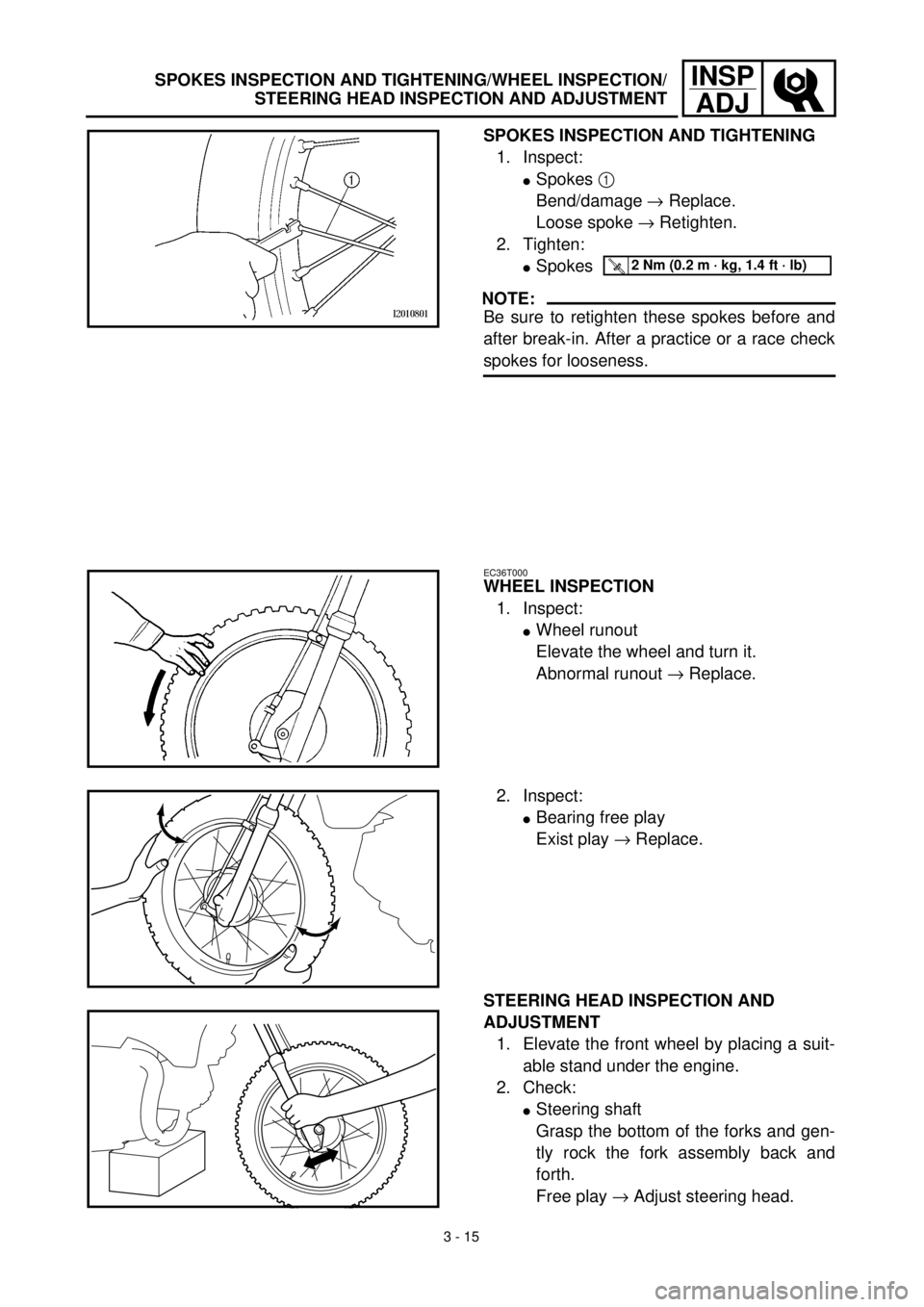
3 - 15
INSP
ADJSPOKES INSPECTION AND TIGHTENING/WHEEL INSPECTION/
STEERING HEAD INSPECTION AND ADJUSTMENT
SPOKES INSPECTION AND TIGHTENING
1. Inspect:
lSpokes 1
Bend/damage ® Replace.
Loose spoke ® Retighten.
2. Tighten:
lSpokes
NOTE:
Be sure to retighten these spokes before and
after break-in. After a practice or a race check
spokes for looseness.
T R..2 Nm (0.2 m · kg, 1.4 ft · lb)
EC36T000
WHEEL INSPECTION
1. Inspect:
lWheel runout
Elevate the wheel and turn it.
Abnormal runout ® Replace.
2. Inspect:
lBearing free play
Exist play ® Replace.
STEERING HEAD INSPECTION AND
ADJUSTMENT
1. Elevate the front wheel by placing a suit-
able stand under the engine.
2. Check:
lSteering shaft
Grasp the bottom of the forks and gen-
tly rock the fork assembly back and
forth.
Free play ® Adjust steering head.
Page 146 of 288
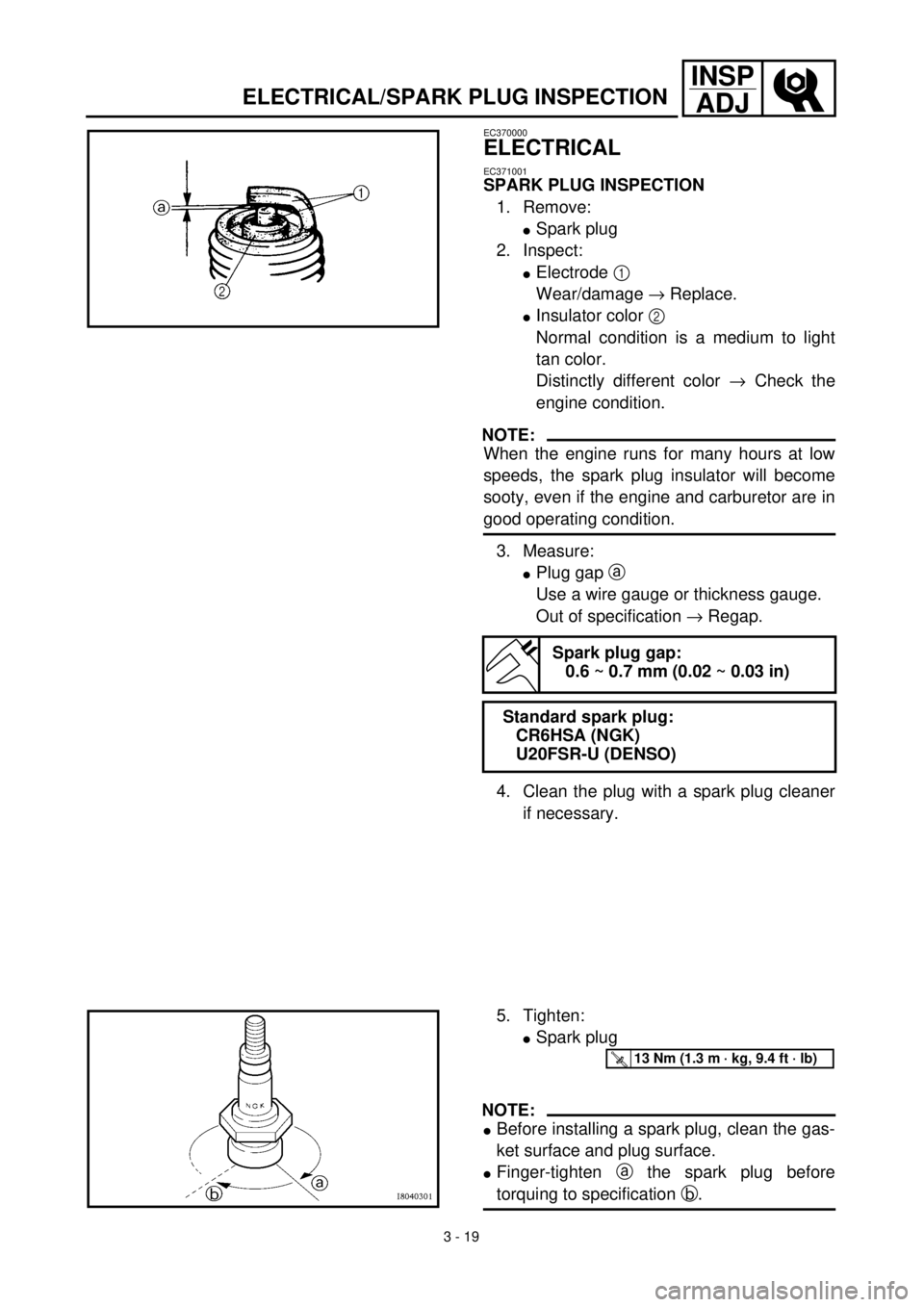
3 - 19
INSP
ADJ
ELECTRICAL/SPARK PLUG INSPECTION
EC370000
ELECTRICAL
EC371001
SPARK PLUG INSPECTION
1. Remove:
lSpark plug
2. Inspect:
lElectrode 1
Wear/damage ® Replace.
lInsulator color 2
Normal condition is a medium to light
tan color.
Distinctly different color ® Check the
engine condition.
NOTE:
When the engine runs for many hours at low
speeds, the spark plug insulator will become
sooty, even if the engine and carburetor are in
good operating condition.
3. Measure:
lPlug gap a
Use a wire gauge or thickness gauge.
Out of specification ® Regap.
4. Clean the plug with a spark plug cleaner
if necessary.
Spark plug gap:
0.6 ~ 0.7 mm (0.02 ~ 0.03 in)
Standard spark plug:
CR6HSA (NGK)
U20FSR-U (DENSO)
5. Tighten:
lSpark plug
NOTE:
lBefore installing a spark plug, clean the gas-
ket surface and plug surface.
lFinger-tighten a the spark plug before
torquing to specification b.
T R..13 Nm (1.3 m · kg, 9.4 ft · lb)
Page 148 of 288
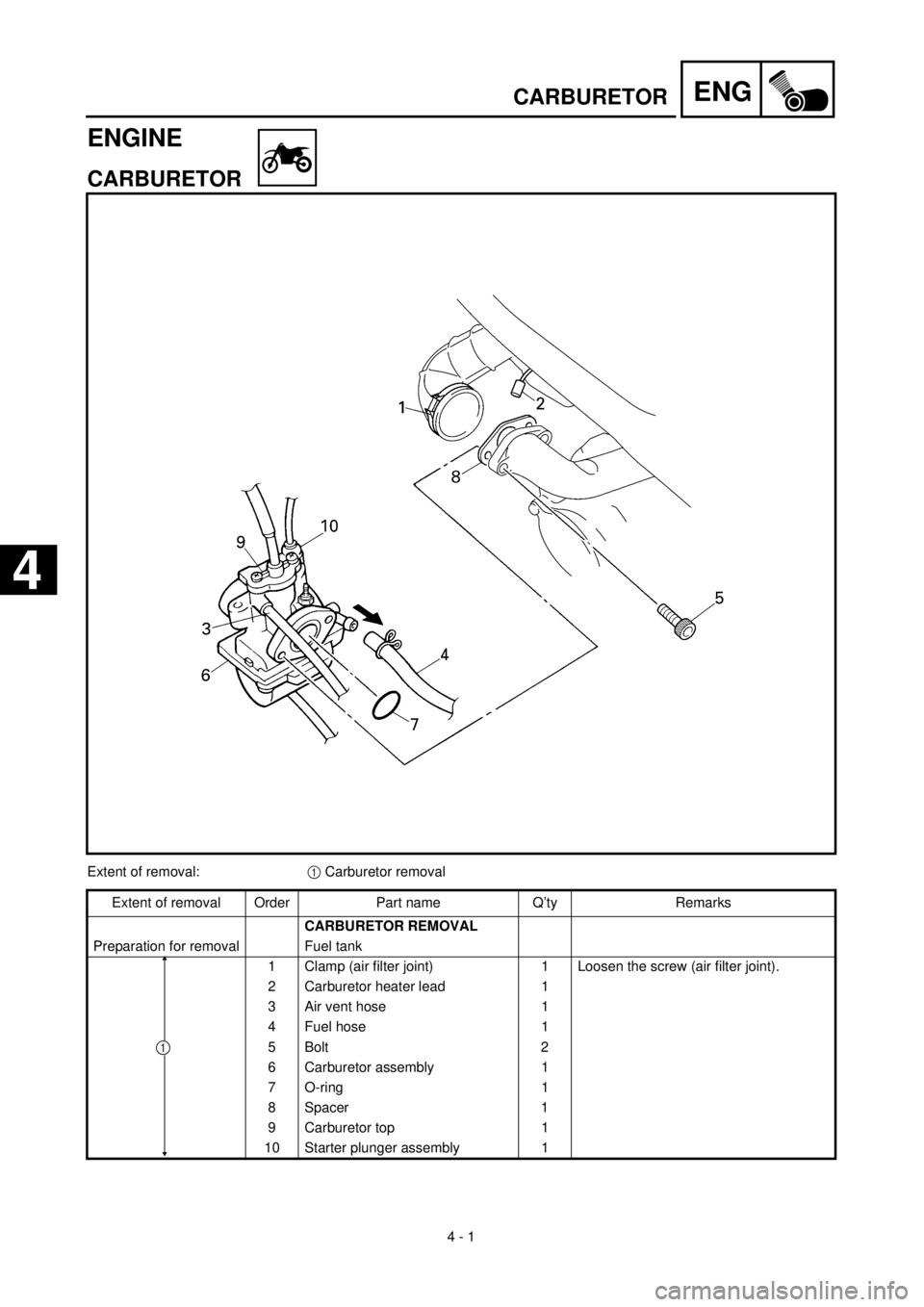
4 - 1
ENG
ENGINE
CARBURETOR
Extent of removal:1 Carburetor removal
Extent of removal Order Part name Q’ty Remarks
CARBURETOR REMOVAL
Preparation for removal Fuel tank
1 Clamp (air filter joint) 1 Loosen the screw (air filter joint).
2 Carburetor heater lead 1
3 Air vent hose 1
4 Fuel hose 1
5 Bolt 2
6 Carburetor assembly 1
7 O-ring 1
8 Spacer 1
9 Carburetor top 1
10 Starter plunger assembly 1
1
CARBURETOR
4