check engine light YAMAHA WR 250F 2016 Owners Manual
[x] Cancel search | Manufacturer: YAMAHA, Model Year: 2016, Model line: WR 250F, Model: YAMAHA WR 250F 2016Pages: 428, PDF Size: 14.13 MB
Page 18 of 428
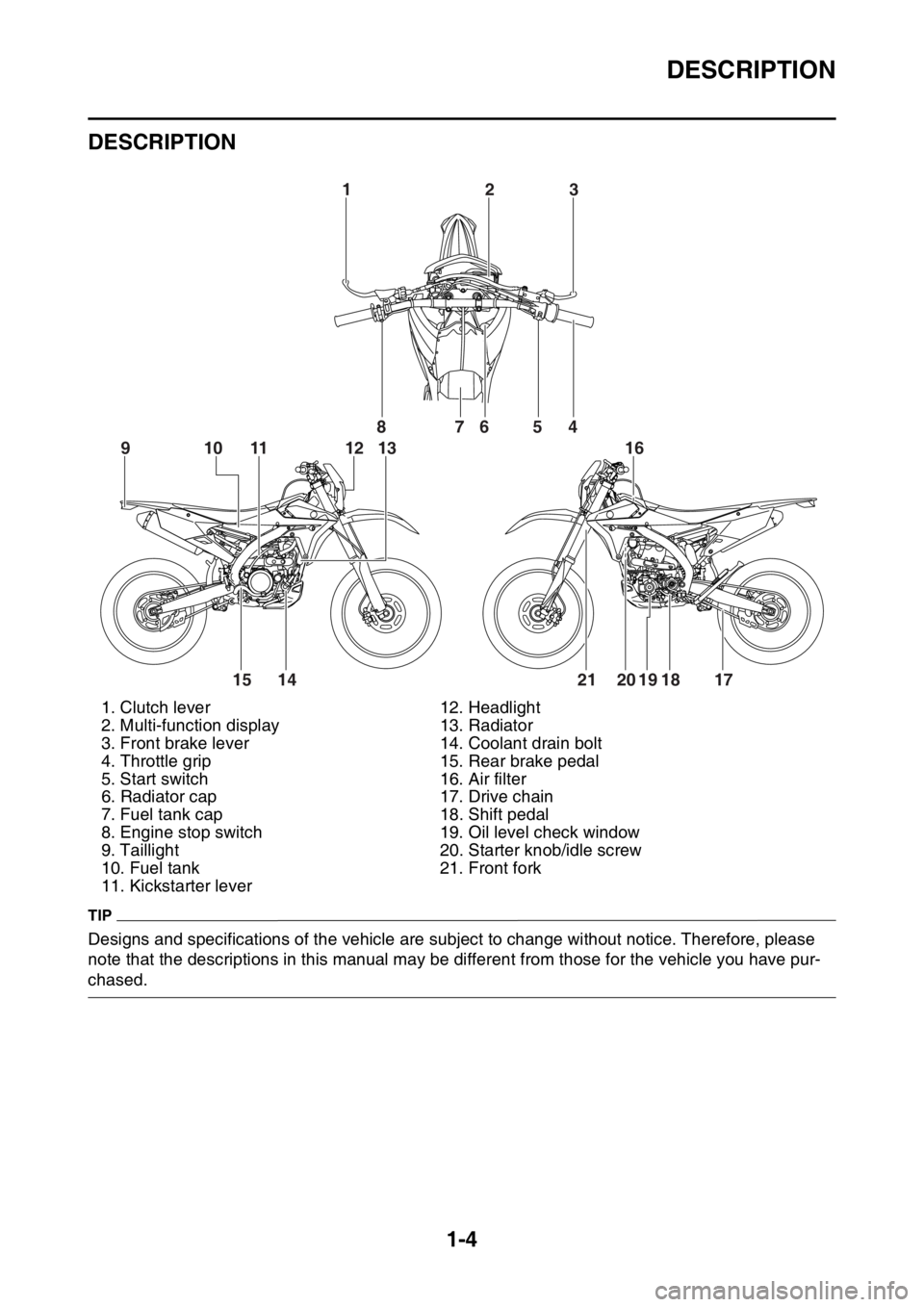
DESCRIPTION
1-4
EAS2GB7009
DESCRIPTION
TIP
Designs and specifications of the vehicle are subject to change without notice. Therefore, please
note that the descriptions in this manual may be different from those for the vehicle you have pur-
chased.1. Clutch lever 12. Headlight
2. Multi-function display 13. Radiator
3. Front brake lever 14. Coolant drain bolt
4. Throttle grip 15. Rear brake pedal
5. Start switch 16. Air filter
6. Radiator cap 17. Drive chain
7. Fuel tank cap 18. Shift pedal
8. Engine stop switch 19. Oil level check window
9. Taillight 20. Starter knob/idle screw
10. Fuel tank 21. Front fork
11. Kickstarter lever
32 1
8
10
91112 1376
54
15 14 21 20 19 18 1716
Page 33 of 428
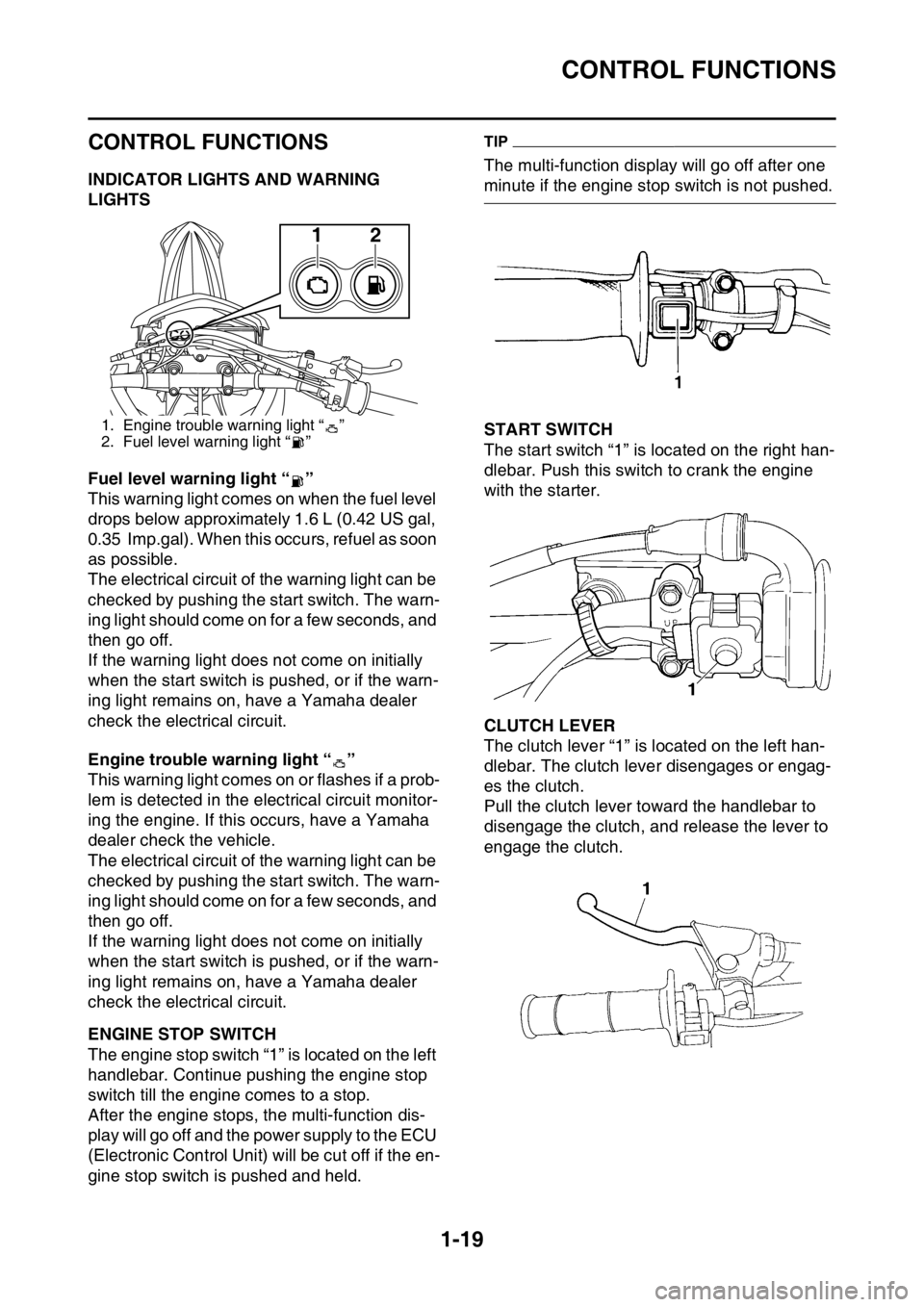
CONTROL FUNCTIONS
1-19
EAS2GB7029
CONTROL FUNCTIONS
EAS2GB7030INDICATOR LIGHTS AND WARNING
LIGHTS
Fuel level warning light “ ”
This warning light comes on when the fuel level
drops below approximately 1.6 L (0.42 US gal,
0.35 Imp.gal). When this occurs, refuel as soon
as possible.
The electrical circuit of the warning light can be
checked by pushing the start switch. The warn-
ing light should come on for a few seconds, and
then go off.
If the warning light does not come on initially
when the start switch is pushed, or if the warn-
ing light remains on, have a Yamaha dealer
check the electrical circuit.
Engine trouble warning light “ ”
This warning light comes on or flashes if a prob-
lem is detected in the electrical circuit monitor-
ing the engine. If this occurs, have a Yamaha
dealer check the vehicle.
The electrical circuit of the warning light can be
checked by pushing the start switch. The warn-
ing light should come on for a few seconds, and
then go off.
If the warning light does not come on initially
when the start switch is pushed, or if the warn-
ing light remains on, have a Yamaha dealer
check the electrical circuit.
EAS2GB7031ENGINE STOP SWITCH
The engine stop switch “1” is located on the left
handlebar. Continue pushing the engine stop
switch till the engine comes to a stop.
After the engine stops, the multi-function dis-
play will go off and the power supply to the ECU
(Electronic Control Unit) will be cut off if the en-
gine stop switch is pushed and held.
TIP
The multi-function display will go off after one
minute if the engine stop switch is not pushed.
EAS2GB7032START SWITCH
The start switch “1” is located on the right han-
dlebar. Push this switch to crank the engine
with the starter.
EAS2GB7033CLUTCH LEVER
The clutch lever “1” is located on the left han-
dlebar. The clutch lever disengages or engag-
es the clutch.
Pull the clutch lever toward the handlebar to
disengage the clutch, and release the lever to
engage the clutch.
1. Engine trouble warning light “ ”
2. Fuel level warning light “ ”
12
Page 103 of 428
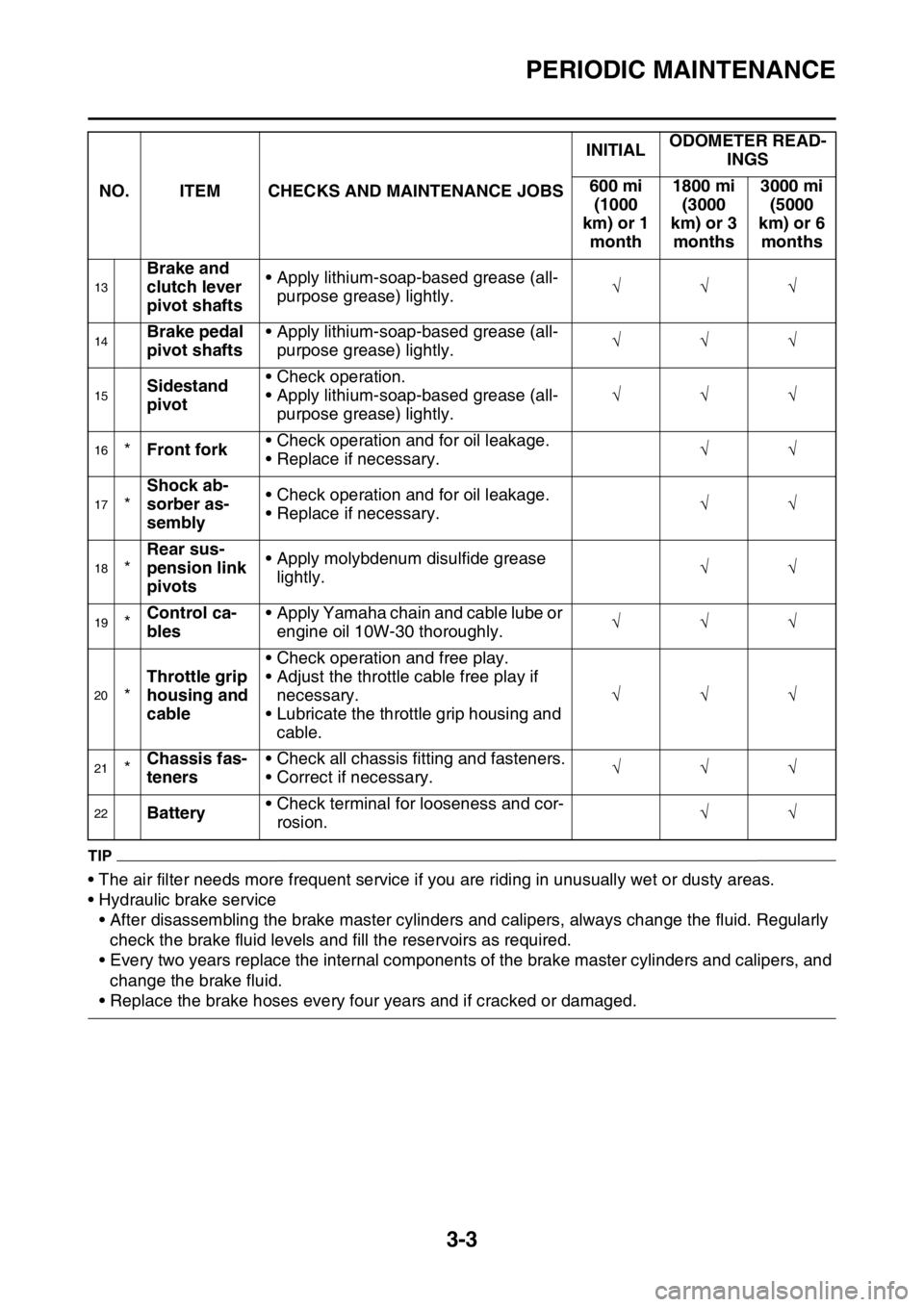
PERIODIC MAINTENANCE
3-3
TIP
• The air filter needs more frequent service if you are riding in unusually wet or dusty areas.
• Hydraulic brake service
• After disassembling the brake master cylinders and calipers, always change the fluid. Regularly
check the brake fluid levels and fill the reservoirs as required.
• Every two years replace the internal components of the brake master cylinders and calipers, and
change the brake fluid.
• Replace the brake hoses every four years and if cracked or damaged.
13
Brake and
clutch lever
pivot shafts• Apply lithium-soap-based grease (all-
purpose grease) lightly.
14Brake pedal
pivot shafts• Apply lithium-soap-based grease (all-
purpose grease) lightly.
15Sidestand
pivot• Check operation.
• Apply lithium-soap-based grease (all-
purpose grease) lightly.
16*Front fork• Check operation and for oil leakage.
• Replace if necessary.
17*Shock ab-
sorber as-
sembly• Check operation and for oil leakage.
• Replace if necessary.
18*Rear sus-
pension link
pivots• Apply molybdenum disulfide grease
lightly.
19*Control ca-
bles• Apply Yamaha chain and cable lube or
engine oil 10W-30 thoroughly.
20*Throttle grip
housing and
cable• Check operation and free play.
• Adjust the throttle cable free play if
necessary.
• Lubricate the throttle grip housing and
cable.
21*Chassis fas-
teners• Check all chassis fitting and fasteners.
• Correct if necessary.
22Battery• Check terminal for looseness and cor-
rosion. NO. ITEM CHECKS AND MAINTENANCE JOBSINITIALODOMETER READ-
INGS
600 mi
(1000
km) or 1
month1800 mi
(3000
km) or 3
months3000 mi
(5000
km) or 6
months
Page 118 of 428
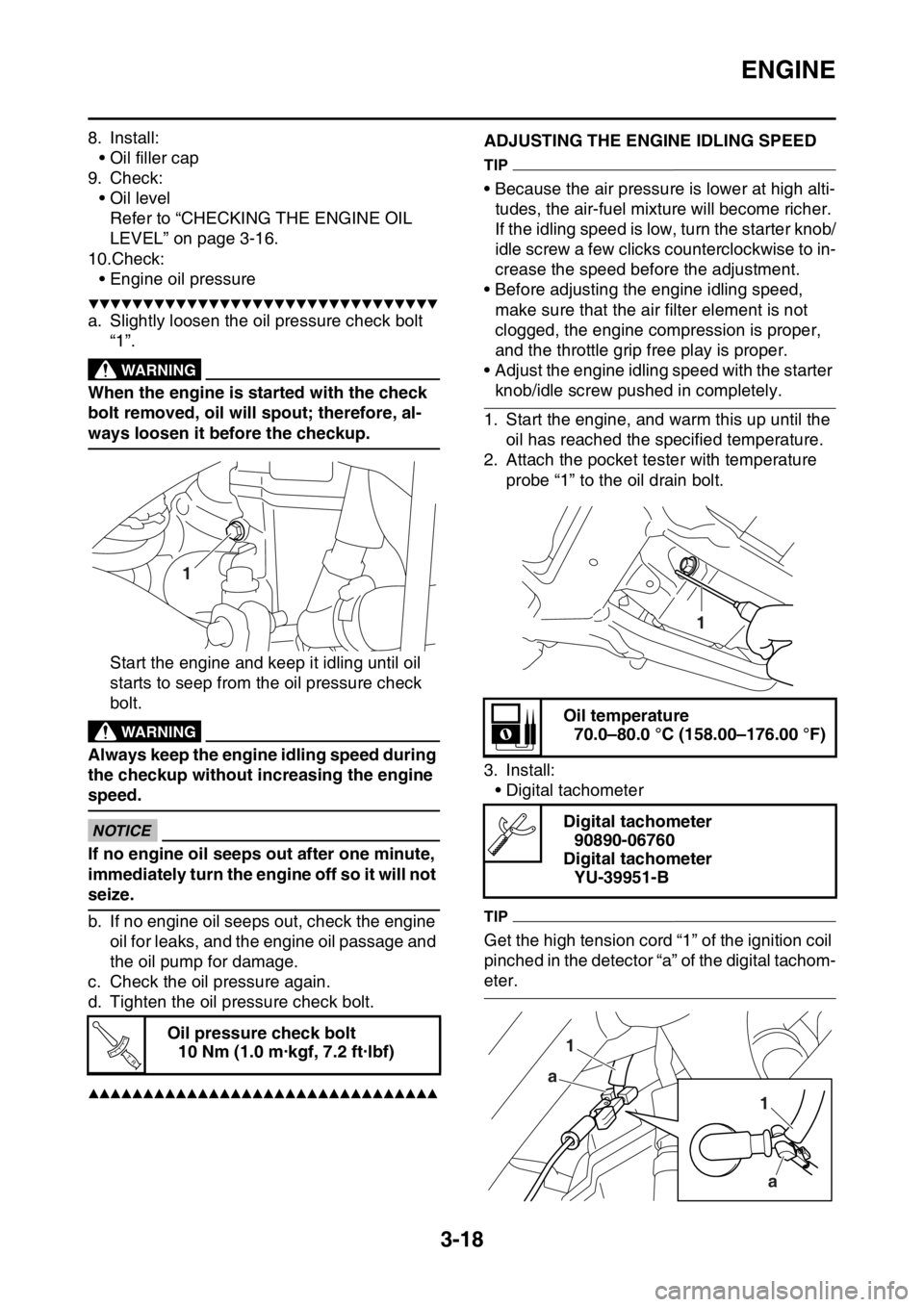
ENGINE
3-18
8. Install:
• Oil filler cap
9. Check:
• Oil level
Refer to “CHECKING THE ENGINE OIL
LEVEL” on page 3-16.
10.Check:
• Engine oil pressure
▼▼▼▼▼▼▼▼▼▼▼▼▼▼▼▼▼▼▼▼▼▼▼▼▼▼▼▼▼▼▼▼
a. Slightly loosen the oil pressure check bolt
“1”.
EWA
WARNING
When the engine is started with the check
bolt removed, oil will spout; therefore, al-
ways loosen it before the checkup.
Start the engine and keep it idling until oil
starts to seep from the oil pressure check
bolt.
EWA
WARNING
Always keep the engine idling speed during
the checkup without increasing the engine
speed.
ECA
NOTICE
If no engine oil seeps out after one minute,
immediately turn the engine off so it will not
seize.
b. If no engine oil seeps out, check the engine
oil for leaks, and the engine oil passage and
the oil pump for damage.
c. Check the oil pressure again.
d. Tighten the oil pressure check bolt.
▲▲▲▲▲▲▲▲▲▲▲▲▲▲▲▲▲▲▲▲▲▲▲▲▲▲▲▲▲▲▲▲
EAS2GB7098ADJUSTING THE ENGINE IDLING SPEED
TIP
• Because the air pressure is lower at high alti-
tudes, the air-fuel mixture will become richer.
If the idling speed is low, turn the starter knob/
idle screw a few clicks counterclockwise to in-
crease the speed before the adjustment.
• Before adjusting the engine idling speed,
make sure that the air filter element is not
clogged, the engine compression is proper,
and the throttle grip free play is proper.
• Adjust the engine idling speed with the starter
knob/idle screw pushed in completely.
1. Start the engine, and warm this up until the
oil has reached the specified temperature.
2. Attach the pocket tester with temperature
probe “1” to the oil drain bolt.
3. Install:
• Digital tachometer
TIP
Get the high tension cord “1” of the ignition coil
pinched in the detector “a” of the digital tachom-
eter.
Oil pressure check bolt
10 Nm (1.0 m·kgf, 7.2 ft·lbf)
1
T R..
Oil temperature
70.0–80.0 °C (158.00–176.00 °F)
Digital tachometer
90890-06760
Digital tachometer
YU-39951-B
1
1 1
a a
Page 140 of 428
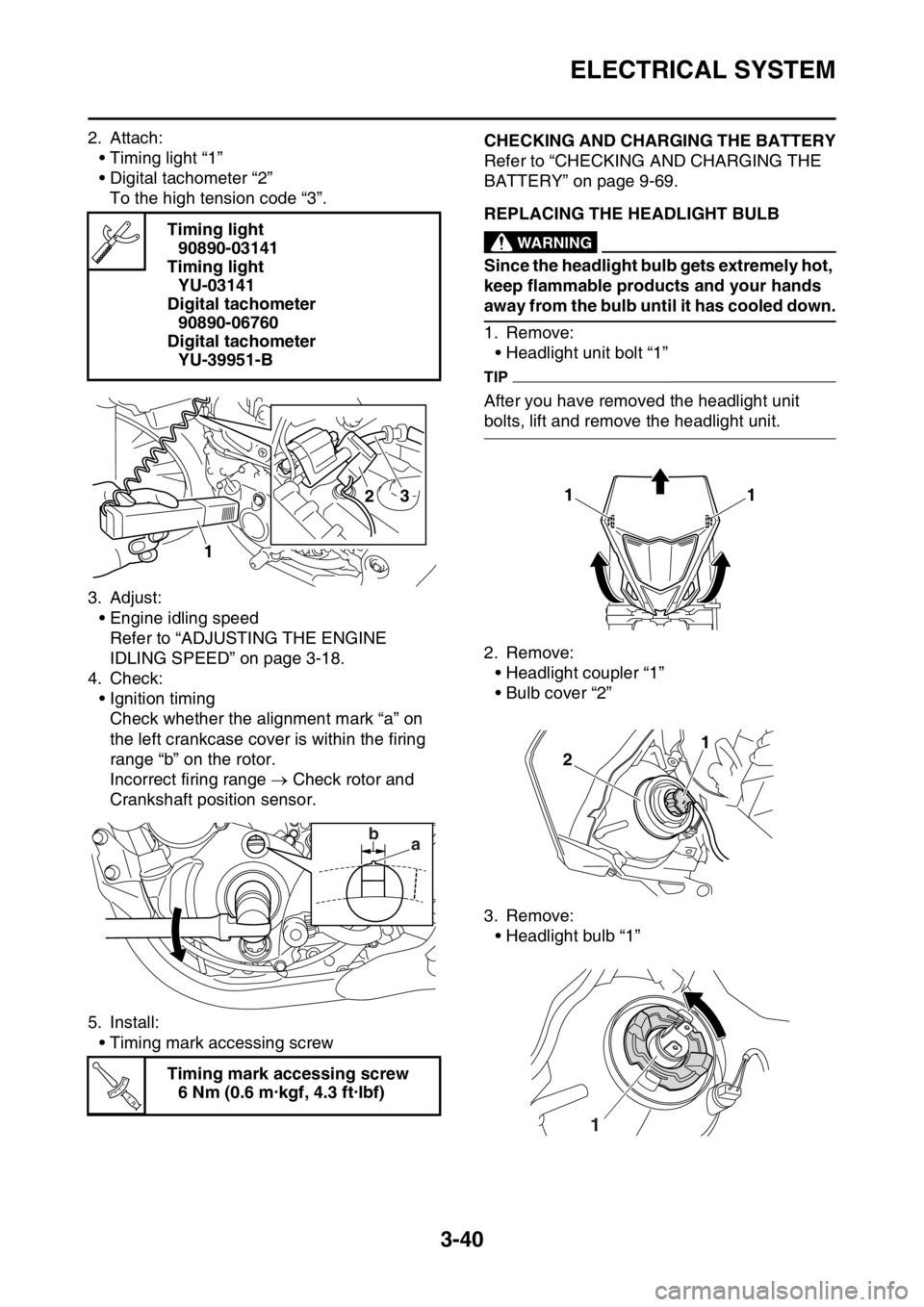
ELECTRICAL SYSTEM
3-40
2. Attach:
• Timing light “1”
• Digital tachometer “2”
To the high tension code “3”.
3. Adjust:
• Engine idling speed
Refer to “ADJUSTING THE ENGINE
IDLING SPEED” on page 3-18.
4. Check:
• Ignition timing
Check whether the alignment mark “a” on
the left crankcase cover is within the firing
range “b” on the rotor.
Incorrect firing range Check rotor and
Crankshaft position sensor.
5. Install:
• Timing mark accessing screwEAS2GB7133CHECKING AND CHARGING THE BATTERY
Refer to “CHECKING AND CHARGING THE
BATTERY” on page 9-69.
EAS2GB7134REPLACING THE HEADLIGHT BULBEWA
WARNING
Since the headlight bulb gets extremely hot,
keep flammable products and your hands
away from the bulb until it has cooled down.
1. Remove:
• Headlight unit bolt “1”
TIP
After you have removed the headlight unit
bolts, lift and remove the headlight unit.
2. Remove:
• Headlight coupler “1”
• Bulb cover “2”
3. Remove:
• Headlight bulb “1” Timing light
90890-03141
Timing light
YU-03141
Digital tachometer
90890-06760
Digital tachometer
YU-39951-B
Timing mark accessing screw
6 Nm (0.6 m·kgf, 4.3 ft·lbf)
2
1
3
ba
T R..
11
1
2
1
Page 300 of 428
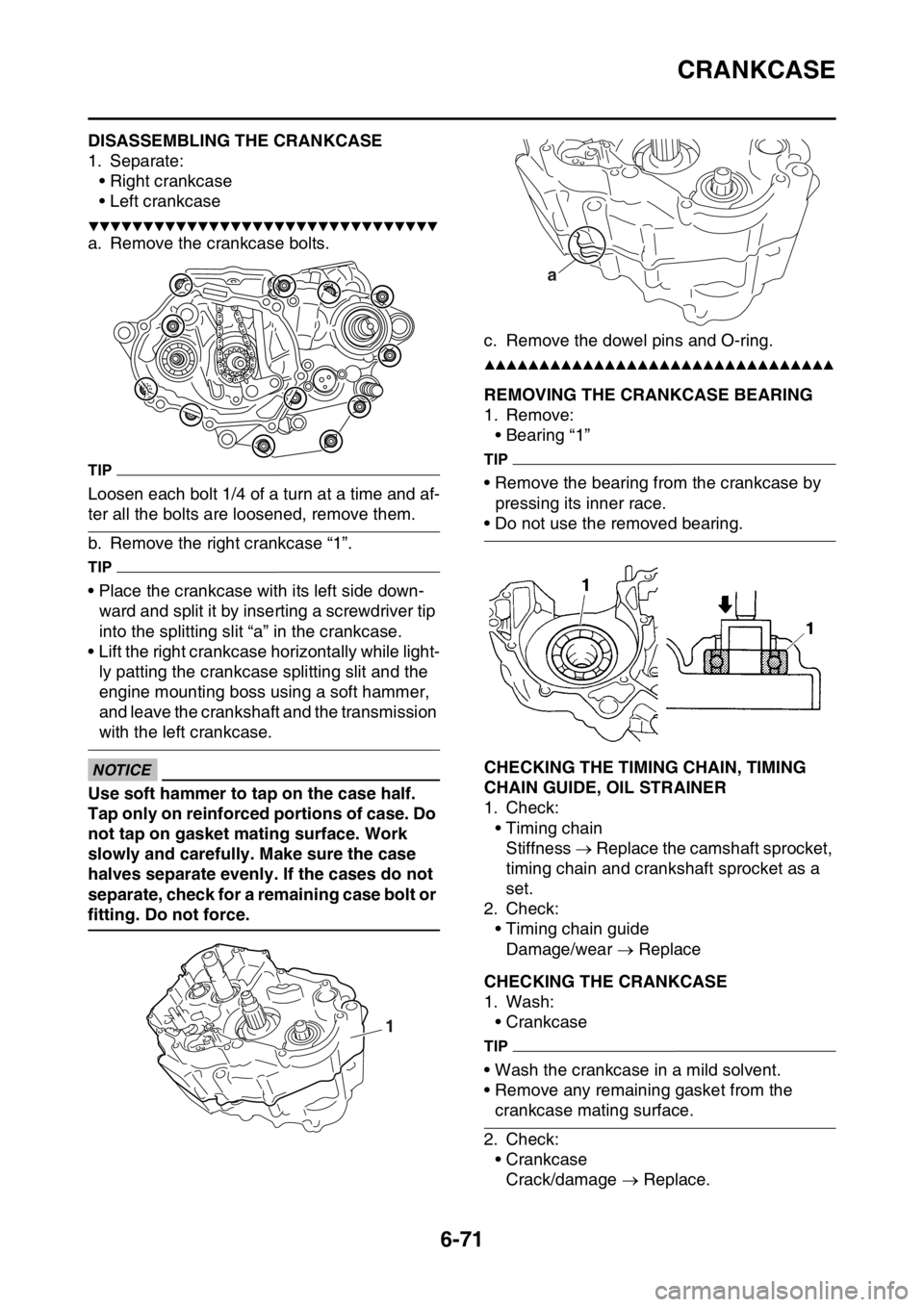
CRANKCASE
6-71
EAS2GB7311DISASSEMBLING THE CRANKCASE
1. Separate:
• Right crankcase
• Left crankcase
▼▼▼▼▼▼▼▼▼▼▼▼▼▼▼▼▼▼▼▼▼▼▼▼▼▼▼▼▼▼▼▼
a. Remove the crankcase bolts.
TIP
Loosen each bolt 1/4 of a turn at a time and af-
ter all the bolts are loosened, remove them.
b. Remove the right crankcase “1”.
TIP
• Place the crankcase with its left side down-
ward and split it by inserting a screwdriver tip
into the splitting slit “a” in the crankcase.
• Lift the right crankcase horizontally while light-
ly patting the crankcase splitting slit and the
engine mounting boss using a soft hammer,
and leave the crankshaft and the transmission
with the left crankcase.
ECA
NOTICE
Use soft hammer to tap on the case half.
Tap only on reinforced portions of case. Do
not tap on gasket mating surface. Work
slowly and carefully. Make sure the case
halves separate evenly. If the cases do not
separate, check for a remaining case bolt or
fitting. Do not force.c. Remove the dowel pins and O-ring.
▲▲▲▲▲▲▲▲▲▲▲▲▲▲▲▲▲▲▲▲▲▲▲▲▲▲▲▲▲▲▲▲
EAS2GB7312REMOVING THE CRANKCASE BEARING
1. Remove:
• Bearing “1”
TIP
• Remove the bearing from the crankcase by
pressing its inner race.
• Do not use the removed bearing.
EAS2GB7313CHECKING THE TIMING CHAIN, TIMING
CHAIN GUIDE, OIL STRAINER
1. Check:
• Timing chain
Stiffness Replace the camshaft sprocket,
timing chain and crankshaft sprocket as a
set.
2. Check:
• Timing chain guide
Damage/wear Replace
EAS2GB7314CHECKING THE CRANKCASE
1. Wash:
• Crankcase
TIP
• Wash the crankcase in a mild solvent.
• Remove any remaining gasket from the
crankcase mating surface.
2. Check:
• Crankcase
Crack/damage Replace.
1
a
Page 309 of 428
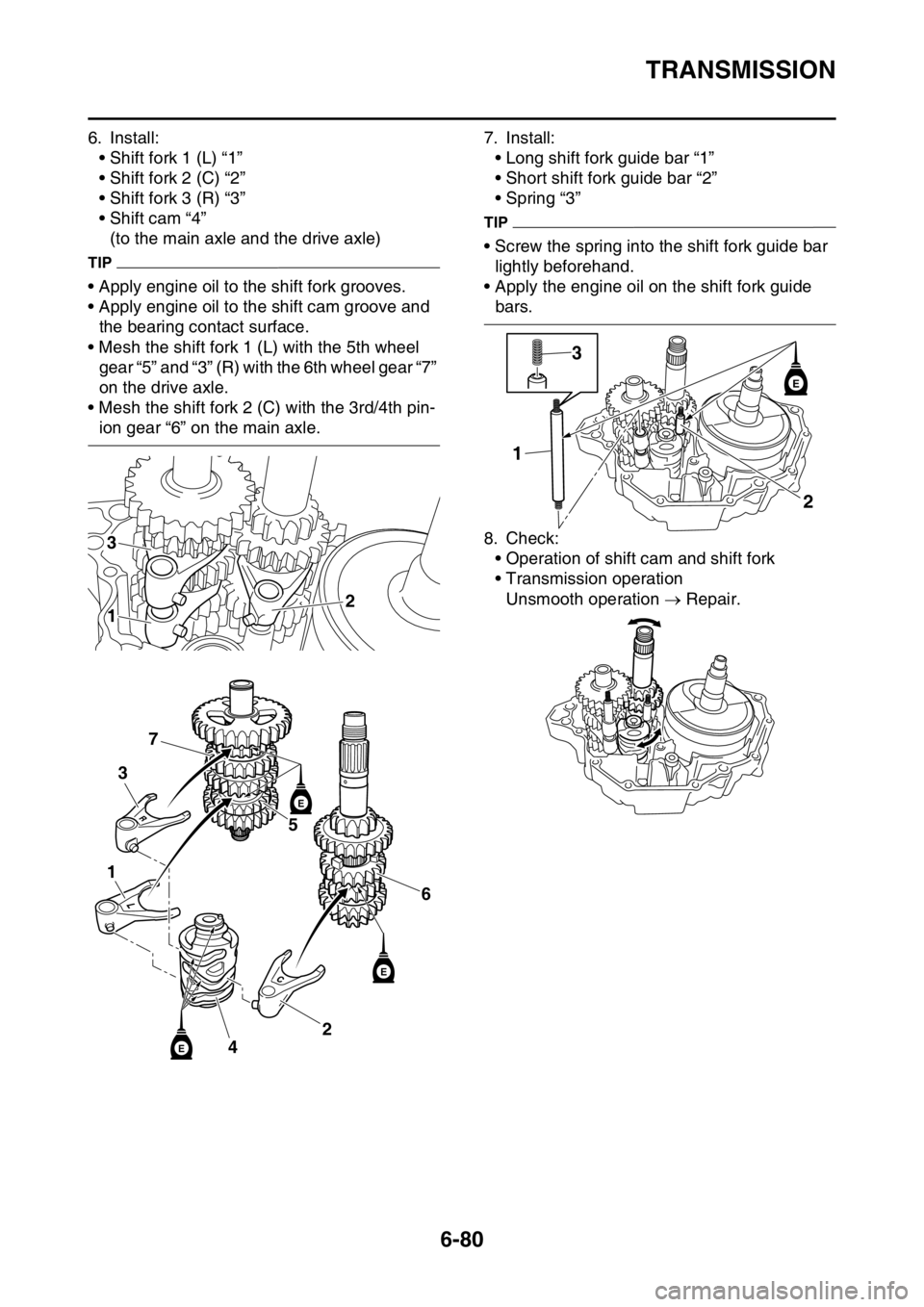
TRANSMISSION
6-80
6. Install:
• Shift fork 1 (L) “1”
• Shift fork 2 (C) “2”
• Shift fork 3 (R) “3”
• Shift cam “4”
(to the main axle and the drive axle)
TIP
• Apply engine oil to the shift fork grooves.
• Apply engine oil to the shift cam groove and
the bearing contact surface.
• Mesh the shift fork 1 (L) with the 5th wheel
gear “5” and “3” (R) with the 6th wheel gear “7”
on the drive axle.
• Mesh the shift fork 2 (C) with the 3rd/4th pin-
ion gear “6” on the main axle.7. Install:
• Long shift fork guide bar “1”
• Short shift fork guide bar “2”
• Spring “3”
TIP
• Screw the spring into the shift fork guide bar
lightly beforehand.
• Apply the engine oil on the shift fork guide
bars.
8. Check:
• Operation of shift cam and shift fork
• Transmission operation
Unsmooth operation Repair.
3
12
6
2
4
5
3
7
1
E
E
E
2 13
E
Page 362 of 428

FUEL INJECTION SYSTEM
9-30
EAS2GB7374ECU SELF-DIAGNOSTIC FUNCTION
The ECU is equipped with a self-diagnostic function in order to ensure that the fuel injection system
is operating normally. If this function detects a malfunction in the system, it immediately operates the
engine under substitute characteristics and illuminates the engine trouble warning light to alert the
rider that a malfunction has occurred in the system. Once a malfunction has been detected, a fault
code number is stored in the memory of the ECU.
• To inform the rider that the fuel injection system is not functioning, the engine trouble warning light
flashes while the start switch is being pushed to start the engine.
• If a malfunction is detected in the system by the self-diagnostic function, the ECU provides an ap-
propriate substitute characteristic operation, and alerts the rider of the detected malfunction by illu-
minating the engine trouble warning light.
Engine trouble warning light indication and fuel injection system operation
* The warning light flashes when any one of the following conditions is present and the start switch
is pushed:
Checking the engine trouble warning light
The engine trouble warning light comes on for around 2 seconds when pushing the start switch to
turn on the meter light and the engine trouble warning light comes on while the start switch is being
pushed.Warning light indica-
tionECU operationFuel injection opera-
tionVehicle operation
Flashing* Warning provided
when unable to start
engineOperation stopped Cannot be operated
Remains on Malfunction detected Operated with substi-
tute characteristics in
accordance with the
description of the mal-
functionCan or cannot be oper-
ated depending on the
fault code
12: Crankshaft position sensor 41: Lean angle sensor
(open or short circuit)
30: Lean angle sensor
(latch up detected)50: ECU internal malfunction
(faulty ECU memory)
33: Ignition coil
(Malfunction detected in the primary wire
of the ignition coil)
a. The meter light does not come on.
b. The meter light comes on.
c. Light OFF
d. Light ON for 2 seconds
ab
cdc
Page 363 of 428
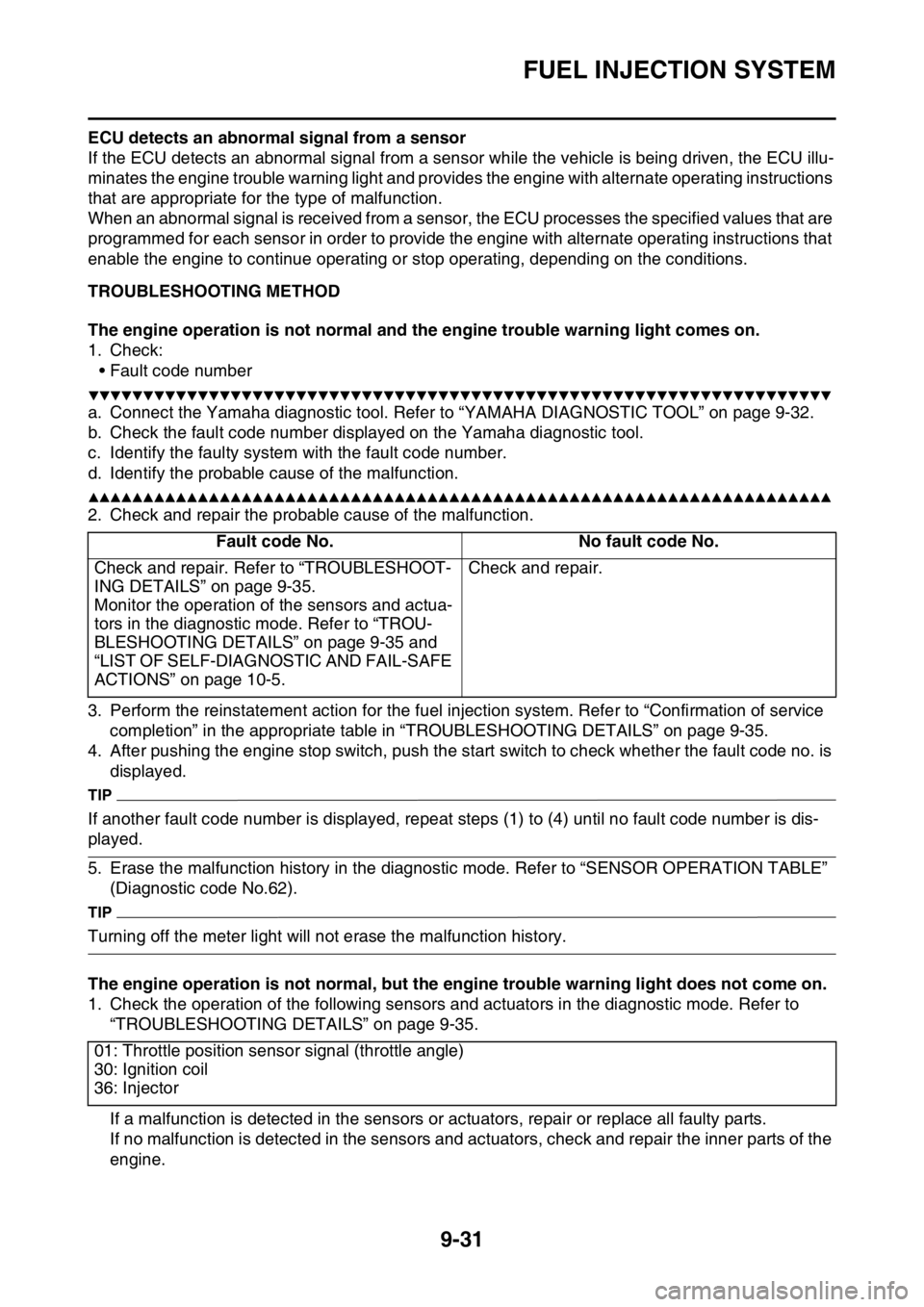
FUEL INJECTION SYSTEM
9-31
ECU detects an abnormal signal from a sensor
If the ECU detects an abnormal signal from a sensor while the vehicle is being driven, the ECU illu-
minates the engine trouble warning light and provides the engine with alternate operating instructions
that are appropriate for the type of malfunction.
When an abnormal signal is received from a sensor, the ECU processes the specified values that are
programmed for each sensor in order to provide the engine with alternate operating instructions that
enable the engine to continue operating or stop operating, depending on the conditions.
EAS2GB7375TROUBLESHOOTING METHOD
The engine operation is not normal and the engine trouble warning light comes on.
1. Check:
• Fault code number
▼▼▼▼▼▼▼▼▼▼▼▼▼▼▼▼▼▼▼▼▼▼▼▼▼▼▼▼▼▼▼▼▼▼▼▼▼▼▼▼▼▼▼▼▼▼▼▼▼▼▼▼▼▼▼▼▼▼▼▼▼▼▼▼▼▼▼▼
a. Connect the Yamaha diagnostic tool. Refer to “YAMAHA DIAGNOSTIC TOOL” on page 9-32.
b. Check the fault code number displayed on the Yamaha diagnostic tool.
c. Identify the faulty system with the fault code number.
d. Identify the probable cause of the malfunction.
▲▲▲▲▲▲▲▲▲▲▲▲▲▲▲▲▲▲▲▲▲▲▲▲▲▲▲▲▲▲▲▲▲▲▲▲▲▲▲▲▲▲▲▲▲▲▲▲▲▲▲▲▲▲▲▲▲▲▲▲▲▲▲▲▲▲▲▲
2. Check and repair the probable cause of the malfunction.
3. Perform the reinstatement action for the fuel injection system. Refer to “Confirmation of service
completion” in the appropriate table in “TROUBLESHOOTING DETAILS” on page 9-35.
4. After pushing the engine stop switch, push the start switch to check whether the fault code no. is
displayed.
TIP
If another fault code number is displayed, repeat steps (1) to (4) until no fault code number is dis-
played.
5. Erase the malfunction history in the diagnostic mode. Refer to “SENSOR OPERATION TABLE”
(Diagnostic code No.62).
TIP
Turning off the meter light will not erase the malfunction history.
The engine operation is not normal, but the engine trouble warning light does not come on.
1. Check the operation of the following sensors and actuators in the diagnostic mode. Refer to
“TROUBLESHOOTING DETAILS” on page 9-35.
If a malfunction is detected in the sensors or actuators, repair or replace all faulty parts.
If no malfunction is detected in the sensors and actuators, check and repair the inner parts of the
engine.Fault code No. No fault code No.
Check and repair. Refer to “TROUBLESHOOT-
ING DETAILS” on page 9-35.
Monitor the operation of the sensors and actua-
tors in the diagnostic mode. Refer to “TROU-
BLESHOOTING DETAILS” on page 9-35 and
“LIST OF SELF-DIAGNOSTIC AND FAIL-SAFE
ACTIONS” on page 10-5.Check and repair.
01: Throttle position sensor signal (throttle angle)
30: Ignition coil
36: Injector
Page 367 of 428
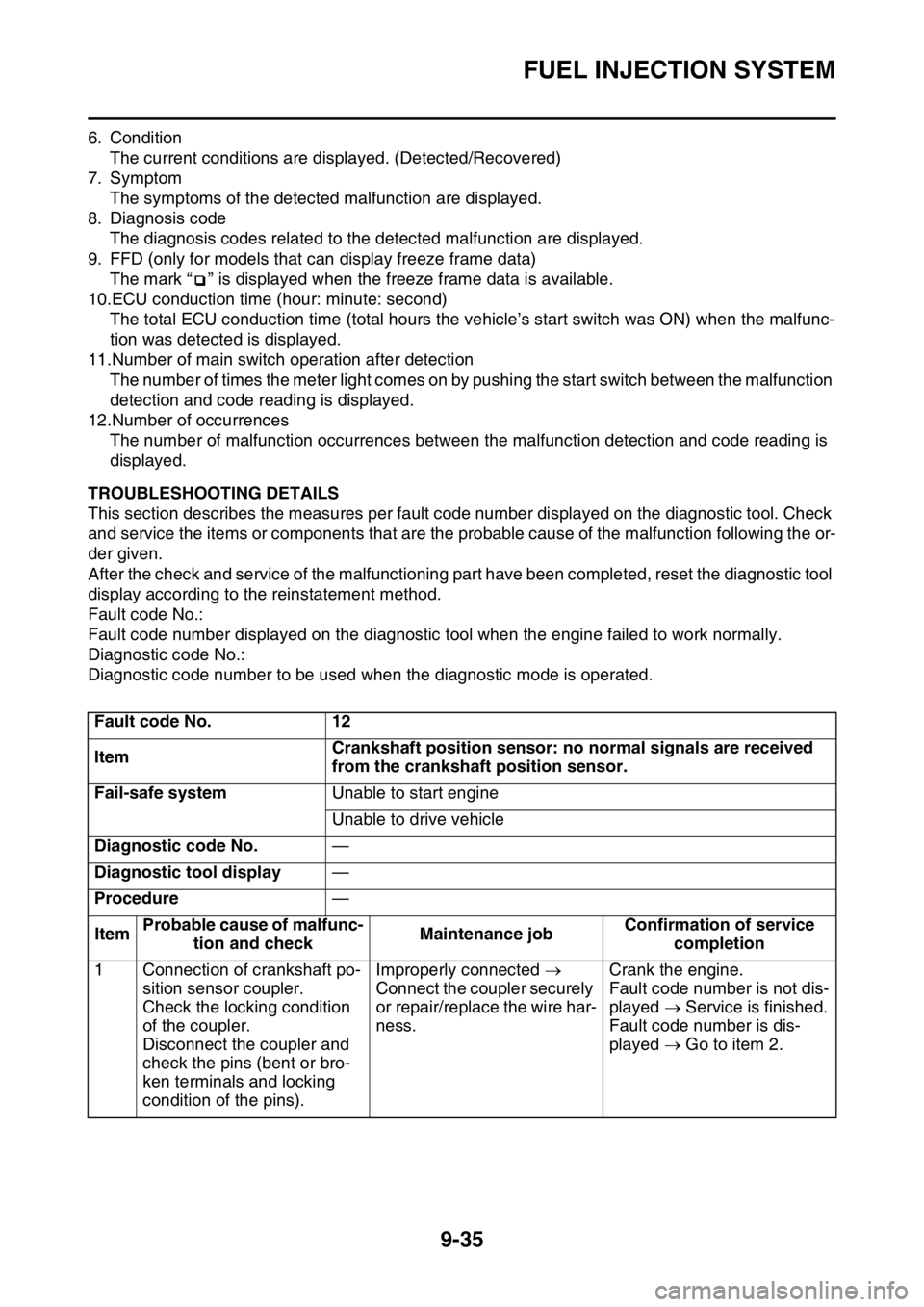
FUEL INJECTION SYSTEM
9-35
6. Condition
The current conditions are displayed. (Detected/Recovered)
7. Symptom
The symptoms of the detected malfunction are displayed.
8. Diagnosis code
The diagnosis codes related to the detected malfunction are displayed.
9. FFD (only for models that can display freeze frame data)
The mark “ ” is displayed when the freeze frame data is available.
10.ECU conduction time (hour: minute: second)
The total ECU conduction time (total hours the vehicle’s start switch was ON) when the malfunc-
tion was detected is displayed.
11.Number of main switch operation after detection
The number of times the meter light comes on by pushing the start switch between the malfunction
detection and code reading is displayed.
12.Number of occurrences
The number of malfunction occurrences between the malfunction detection and code reading is
displayed.
EAS2GB7377TROUBLESHOOTING DETAILS
This section describes the measures per fault code number displayed on the diagnostic tool. Check
and service the items or components that are the probable cause of the malfunction following the or-
der given.
After the check and service of the malfunctioning part have been completed, reset the diagnostic tool
display according to the reinstatement method.
Fault code No.:
Fault code number displayed on the diagnostic tool when the engine failed to work normally.
Diagnostic code No.:
Diagnostic code number to be used when the diagnostic mode is operated.
Fault code No. 12
ItemCrankshaft position sensor: no normal signals are received
from the crankshaft position sensor.
Fail-safe systemUnable to start engine
Unable to drive vehicle
Diagnostic code No.—
Diagnostic tool display—
Procedure—
ItemProbable cause of malfunc-
tion and checkMaintenance jobConfirmation of service
completion
1 Connection of crankshaft po-
sition sensor coupler.
Check the locking condition
of the coupler.
Disconnect the coupler and
check the pins (bent or bro-
ken terminals and locking
condition of the pins).Improperly connected
Connect the coupler securely
or repair/replace the wire har-
ness.Crank the engine.
Fault code number is not dis-
played Service is finished.
Fault code number is dis-
played Go to item 2.