check engine YAMAHA WR 426F 2002 Owners Manual
[x] Cancel search | Manufacturer: YAMAHA, Model Year: 2002, Model line: WR 426F, Model: YAMAHA WR 426F 2002Pages: 776, PDF Size: 41.64 MB
Page 20 of 776
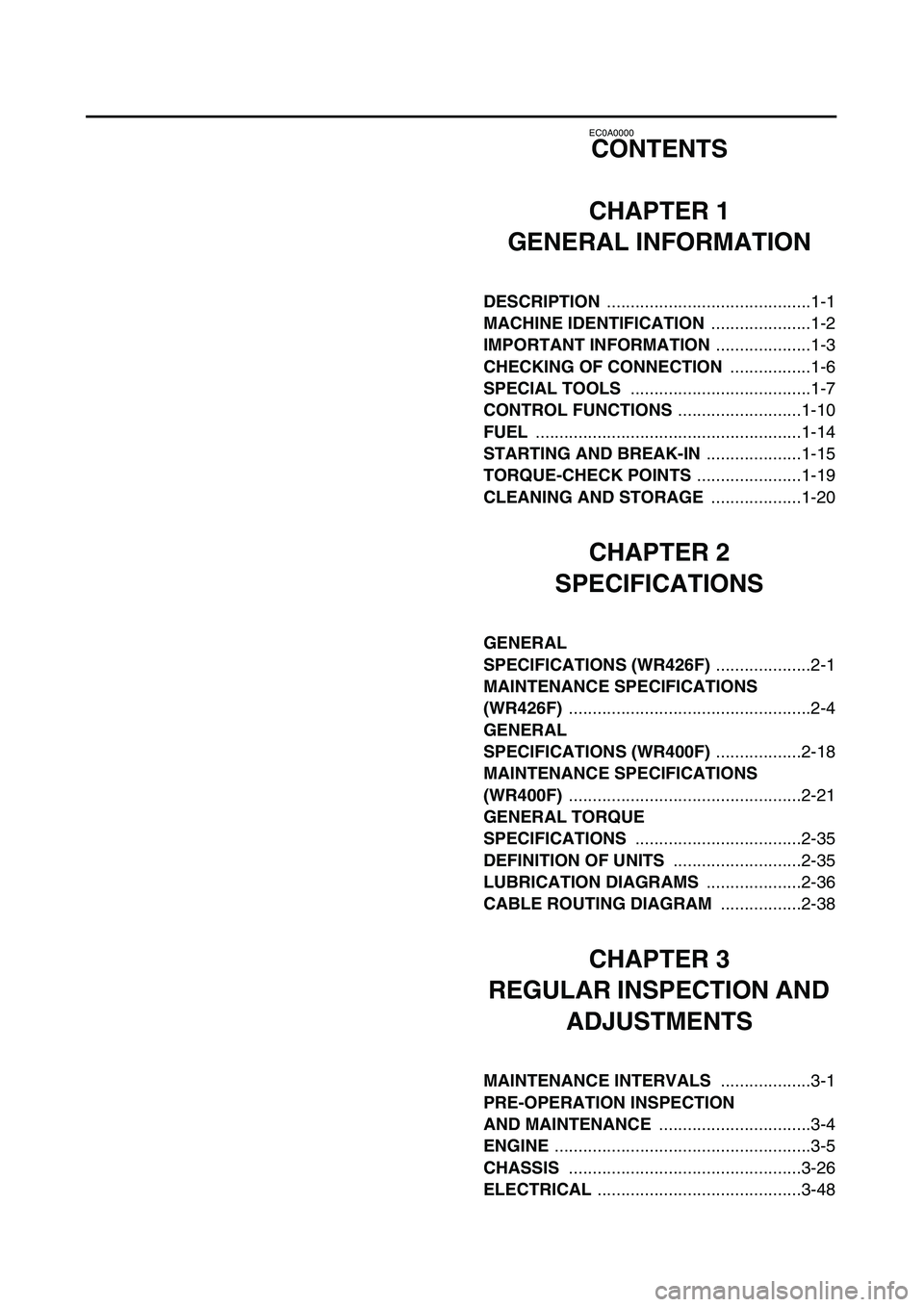
EC0A0000
CONTENTS
CHAPTER 1
GENERAL INFORMATION
DESCRIPTION
...........................................1-1
MACHINE IDENTIFICATION
.....................1-2
IMPORTANT INFORMATION
....................1-3
CHECKING OF CONNECTION
.................1-6
SPECIAL TOOLS
......................................1-7
CONTROL FUNCTIONS
..........................1-10
FUEL
........................................................1-14
STARTING AND BREAK-IN
....................1-15
TORQUE-CHECK POINTS
......................1-19
CLEANING AND STORAGE
...................1-20
CHAPTER 2
SPECIFICATIONS
GENERAL
SPECIFICATIONS (WR426F)
....................2-1
MAINTENANCE SPECIFICATIONS
(WR426F)
...................................................2-4
GENERAL
SPECIFICATIONS (WR400F)
..................2-18
MAINTENANCE SPECIFICATIONS
(WR400F)
.................................................2-21
GENERAL TORQUE
SPECIFICATIONS
...................................2-35
DEFINITION OF UNITS
...........................2-35
LUBRICATION DIAGRAMS
....................2-36
CABLE ROUTING DIAGRAM
.................2-38
CHAPTER 3
REGULAR INSPECTION AND
ADJUSTMENTS
MAINTENANCE INTERVALS
...................3-1
PRE-OPERATION INSPECTION
AND MAINTENANCE
................................3-4
ENGINE
......................................................3-5
CHASSIS
.................................................3-26
ELECTRICAL
...........................................3-48
Page 39 of 776
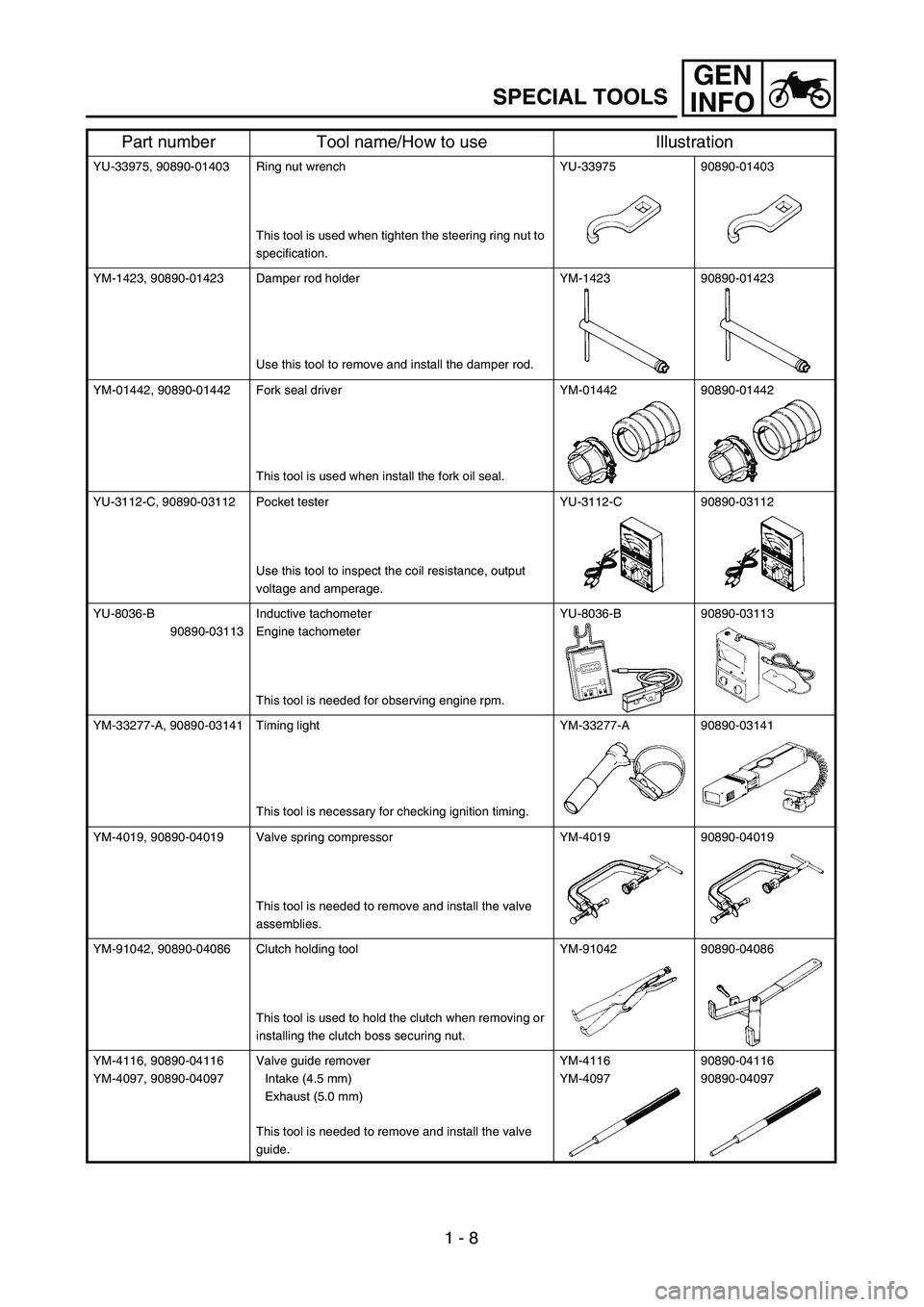
1 - 8
GEN
INFO
SPECIAL TOOLS
YU-33975, 90890-01403 Ring nut wrench
This tool is used when tighten the steering ring nut to
specification.YU-33975 90890-01403
YM-1423, 90890-01423 Damper rod holder
Use this tool to remove and install the damper rod.YM-1423 90890-01423
YM-01442, 90890-01442 Fork seal driver
This tool is used when install the fork oil seal.YM-01442 90890-01442
YU-3112-C, 90890-03112 Pocket tester
Use this tool to inspect the coil resistance, output
voltage and amperage.YU-3112-C 90890-03112
YU-8036-B
90890-03113Inductive tachometer
Engine tachometer
This tool is needed for observing engine rpm.YU-8036-B 90890-03113
YM-33277-A, 90890-03141 Timing light
This tool is necessary for checking ignition timing.YM-33277-A 90890-03141
YM-4019, 90890-04019 Valve spring compressor
This tool is needed to remove and install the valve
assemblies.YM-4019 90890-04019
YM-91042, 90890-04086 Clutch holding tool
This tool is used to hold the clutch when removing or
installing the clutch boss securing nut.YM-91042 90890-04086
YM-4116, 90890-04116
YM-4097, 90890-04097Valve guide remover
Intake (4.5 mm)
Exhaust (5.0 mm)
This tool is needed to remove and install the valve
guide.YM-4116
YM-409790890-04116
90890-04097
Part number Tool name/How to use Illustration
Page 60 of 776
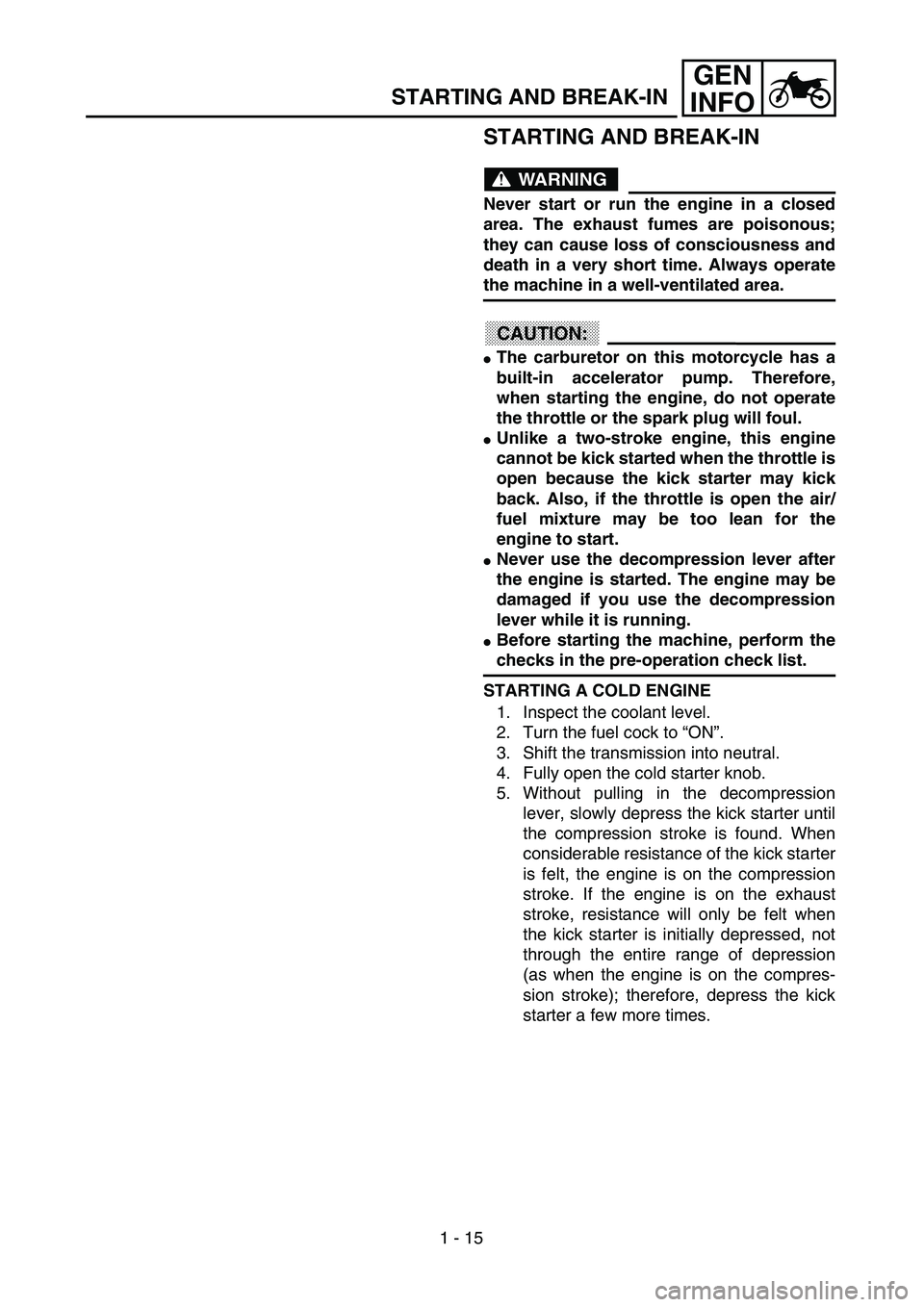
1 - 15
GEN
INFO
STARTING AND BREAK-IN
STARTING AND BREAK-IN
WARNING
Never start or run the engine in a closed
area. The exhaust fumes are poisonous;
they can cause loss of consciousness and
death in a very short time. Always operate
the machine in a well-ventilated area.
CAUTION:
The carburetor on this motorcycle has a
built-in accelerator pump. Therefore,
when starting the engine, do not operate
the throttle or the spark plug will foul.
Unlike a two-stroke engine, this engine
cannot be kick started when the throttle is
open because the kick starter may kick
back. Also, if the throttle is open the air/
fuel mixture may be too lean for the
engine to start.
Never use the decompression lever after
the engine is started. The engine may be
damaged if you use the decompression
lever while it is running.
Before starting the machine, perform the
checks in the pre-operation check list.
STARTING A COLD ENGINE
1. Inspect the coolant level.
2. Turn the fuel cock to “ON”.
3. Shift the transmission into neutral.
4. Fully open the cold starter knob.
5. Without pulling in the decompression
lever, slowly depress the kick starter until
the compression stroke is found. When
considerable resistance of the kick starter
is felt, the engine is on the compression
stroke. If the engine is on the exhaust
stroke, resistance will only be felt when
the kick starter is initially depressed, not
through the entire range of depression
(as when the engine is on the compres-
sion stroke); therefore, depress the kick
starter a few more times.
Page 66 of 776
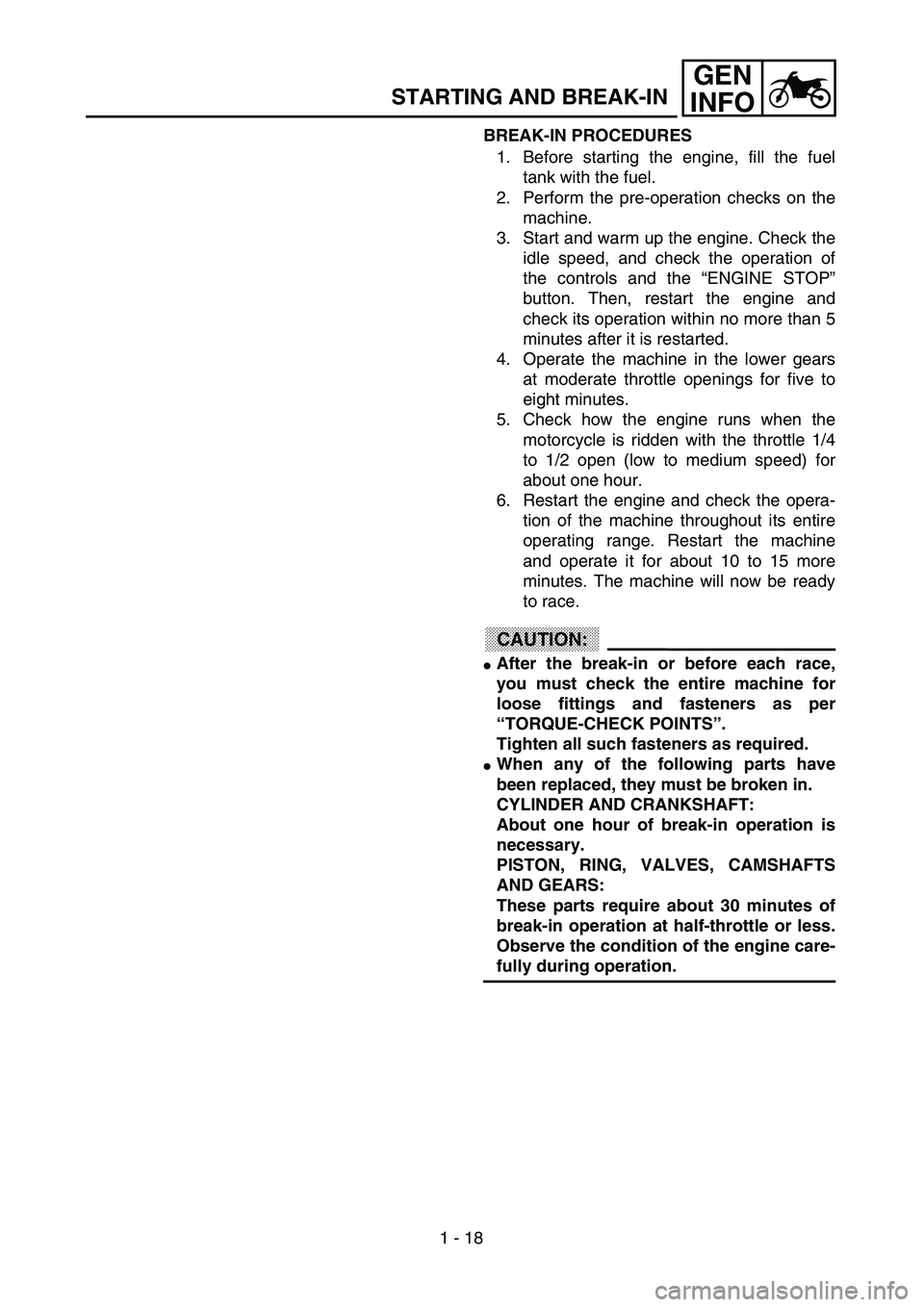
1 - 18
GEN
INFO
BREAK-IN PROCEDURES
1. Before starting the engine, fill the fuel
tank with the fuel.
2. Perform the pre-operation checks on the
machine.
3. Start and warm up the engine. Check the
idle speed, and check the operation of
the controls and the “ENGINE STOP”
button. Then, restart the engine and
check its operation within no more than 5
minutes after it is restarted.
4. Operate the machine in the lower gears
at moderate throttle openings for five to
eight minutes.
5. Check how the engine runs when the
motorcycle is ridden with the throttle 1/4
to 1/2 open (low to medium speed) for
about one hour.
6. Restart the engine and check the opera-
tion of the machine throughout its entire
operating range. Restart the machine
and operate it for about 10 to 15 more
minutes. The machine will now be ready
to race.
CAUTION:
After the break-in or before each race,
you must check the entire machine for
loose fittings and fasteners as per
“TORQUE-CHECK POINTS”.
Tighten all such fasteners as required.
When any of the following parts have
been replaced, they must be broken in.
CYLINDER AND CRANKSHAFT:
About one hour of break-in operation is
necessary.
PISTON, RING, VALVES, CAMSHAFTS
AND GEARS:
These parts require about 30 minutes of
break-in operation at half-throttle or less.
Observe the condition of the engine care-
fully during operation.
STARTING AND BREAK-IN
Page 68 of 776
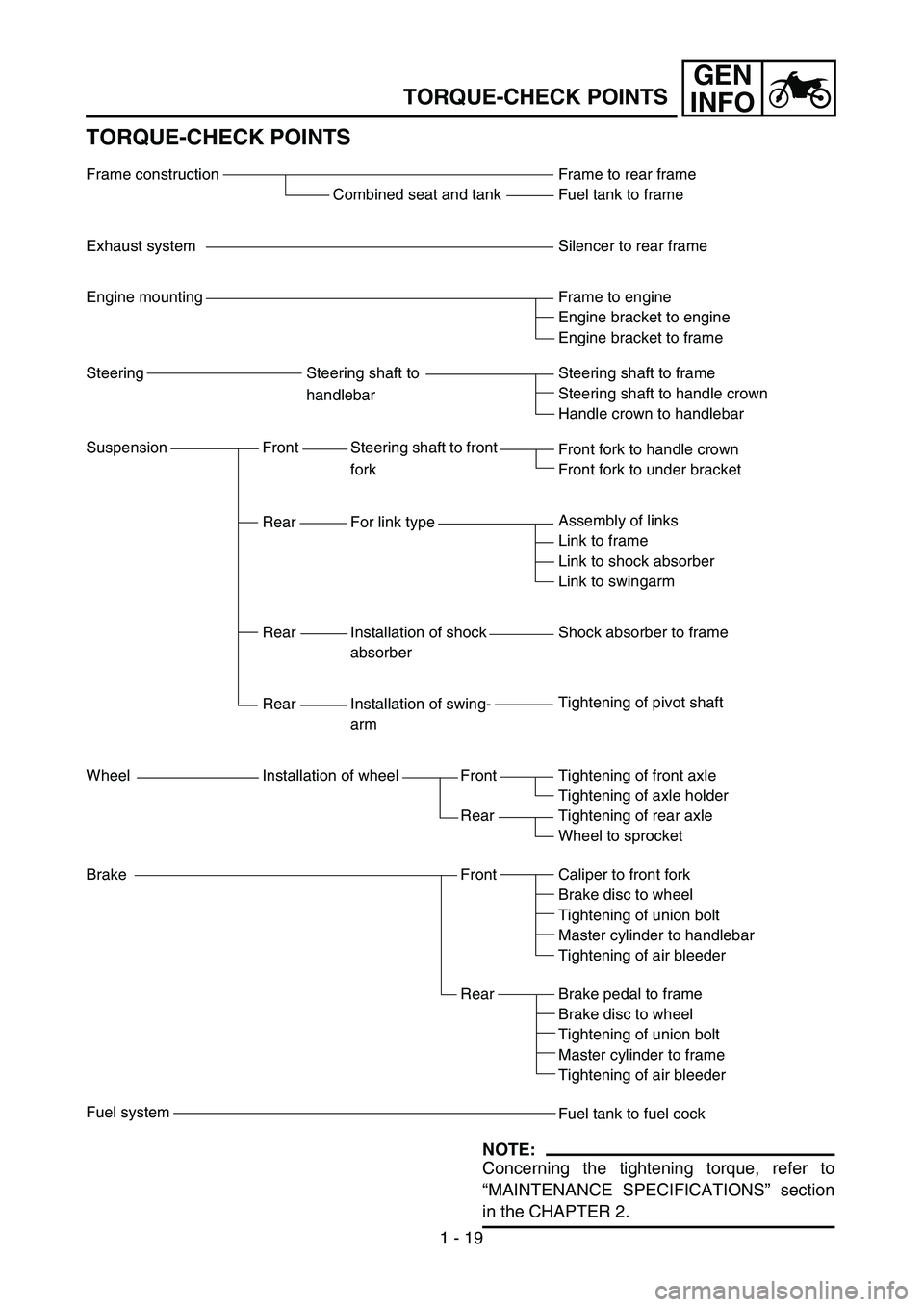
1 - 19
GEN
INFO
TORQUE-CHECK POINTS
TORQUE-CHECK POINTS
Frame construction
Combined seat and tank
Exhaust system
Engine mounting
Steering Steering shaft to
handlebar
Suspension Front Steering shaft to front
fork
Rear For link type
Rear Installation of shock
absorber
Rear Installation of swing-
arm
Wheel Installation of wheel Front
Rear
Brake Front
Rear
Fuel systemFrame to rear frame
Fuel tank to frame
Silencer to rear frame
Frame to engine
Engine bracket to engine
Engine bracket to frame
Steering shaft to frame
Steering shaft to handle crown
Handle crown to handlebar
Front fork to handle crown
Front fork to under bracket
Assembly of links
Link to frame
Link to shock absorber
Link to swingarm
Shock absorber to frame
Tightening of pivot shaft
Tightening of front axle
Tightening of axle holder
Tightening of rear axle
Wheel to sprocket
Caliper to front fork
Brake disc to wheel
Tightening of union bolt
Master cylinder to handlebar
Tightening of air bleeder
Brake pedal to frame
Brake disc to wheel
Tightening of union bolt
Master cylinder to frame
Tightening of air bleeder
Fuel tank to fuel cock
NOTE:
Concerning the tightening torque, refer to
“MAINTENANCE SPECIFICATIONS” section
in the CHAPTER 2.
Page 91 of 776
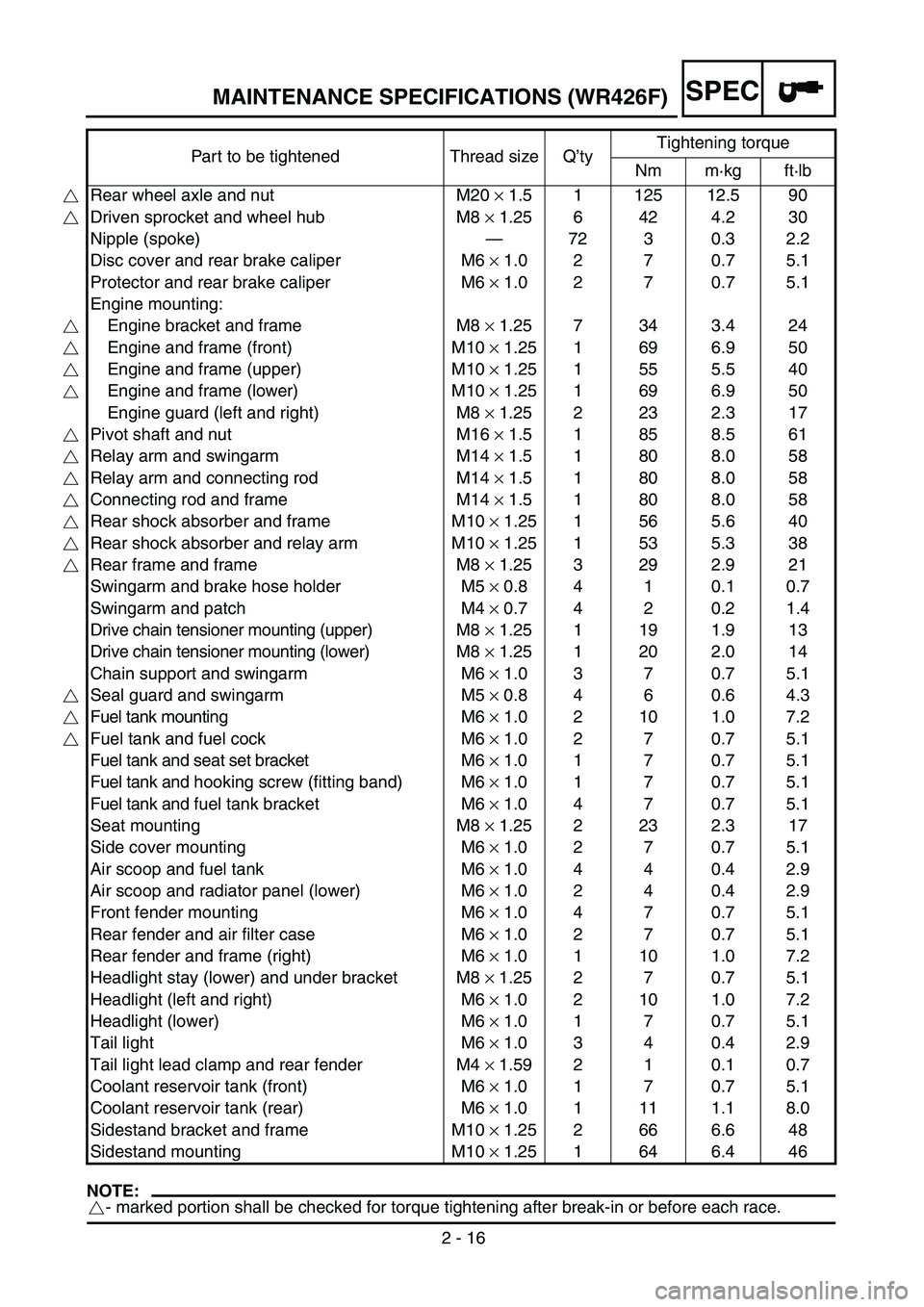
2 - 16
SPECMAINTENANCE SPECIFICATIONS (WR426F)
NOTE:
- marked portion shall be checked for torque tightening after break-in or before each race.Part to be tightened Thread size Q’tyTightening torque
Nm m·kg ft·lb
Rear wheel axle and nut M20 × 1.5 1 125 12.5 90
Driven sprocket and wheel hub M8 × 1.25 6 42 4.2 30
Nipple (spoke)—72 3 0.3 2.2
Disc cover and rear brake caliper M6 × 1.0 2 7 0.7 5.1
Protector and rear brake caliper M6 × 1.0 2 7 0.7 5.1
Engine mounting:
Engine bracket and frame M8 × 1.25 7 34 3.4 24
Engine and frame (front) M10 × 1.25 1 69 6.9 50
Engine and frame (upper) M10 × 1.25 1 55 5.5 40
Engine and frame (lower) M10 × 1.25 1 69 6.9 50
Engine guard (left and right) M8 × 1.25 2 23 2.3 17
Pivot shaft and nut M16 × 1.5 1 85 8.5 61
Relay arm and swingarm M14 × 1.5 1 80 8.0 58
Relay arm and connecting rod M14 × 1.5 1 80 8.0 58
Connecting rod and frame M14 × 1.5 1 80 8.0 58
Rear shock absorber and frame M10 × 1.25 1 56 5.6 40
Rear shock absorber and relay arm M10 × 1.25 1 53 5.3 38
Rear frame and frame M8 × 1.25 3 29 2.9 21
Swingarm and brake hose holder M5 × 0.8 4 1 0.1 0.7
Swingarm and patch M4 × 0.7 4 2 0.2 1.4
Drive chain tensioner mounting (upper) M8 × 1.25 1 19 1.9 13
Drive chain tensioner mounting (lower) M8 × 1.25 1 20 2.0 14
Chain support and swingarm M6 × 1.0 3 7 0.7 5.1
Seal guard and swingarm M5 × 0.8 4 6 0.6 4.3
Fuel tank mounting M6 × 1.0 2 10 1.0 7.2
Fuel tank and fuel cock M6 × 1.0 2 7 0.7 5.1
Fuel tank and seat set bracket M6 × 1.0 1 7 0.7 5.1
Fuel tank and hooking screw (fitting band) M6 × 1.0 1 7 0.7 5.1
Fuel tank and fuel tank bracket M6 × 1.0 4 7 0.7 5.1
Seat mounting M8 × 1.25 2 23 2.3 17
Side cover mounting M6 × 1.0 2 7 0.7 5.1
Air scoop and fuel tank M6 × 1.0 4 4 0.4 2.9
Air scoop and radiator panel (lower) M6 × 1.0 2 4 0.4 2.9
Front fender mounting M6 × 1.0 4 7 0.7 5.1
Rear fender and air filter case M6 × 1.0 2 7 0.7 5.1
Rear fender and frame (right) M6 × 1.0 1 10 1.0 7.2
Headlight stay (lower) and under bracket M8 × 1.25 2 7 0.7 5.1
Headlight (left and right) M6 × 1.0 2 10 1.0 7.2
Headlight (lower) M6 × 1.0 1 7 0.7 5.1
Tail light M6 × 1.0 3 4 0.4 2.9
Tail light lead clamp and rear fender M4 × 1.59 2 1 0.1 0.7
Coolant reservoir tank (front) M6 × 1.0 1 7 0.7 5.1
Coolant reservoir tank (rear) M6 × 1.0 1 11 1.1 8.0
Sidestand bracket and frame M10 × 1.25 2 66 6.6 48
Sidestand mounting M10 × 1.25 1 64 6.4 46
Page 108 of 776
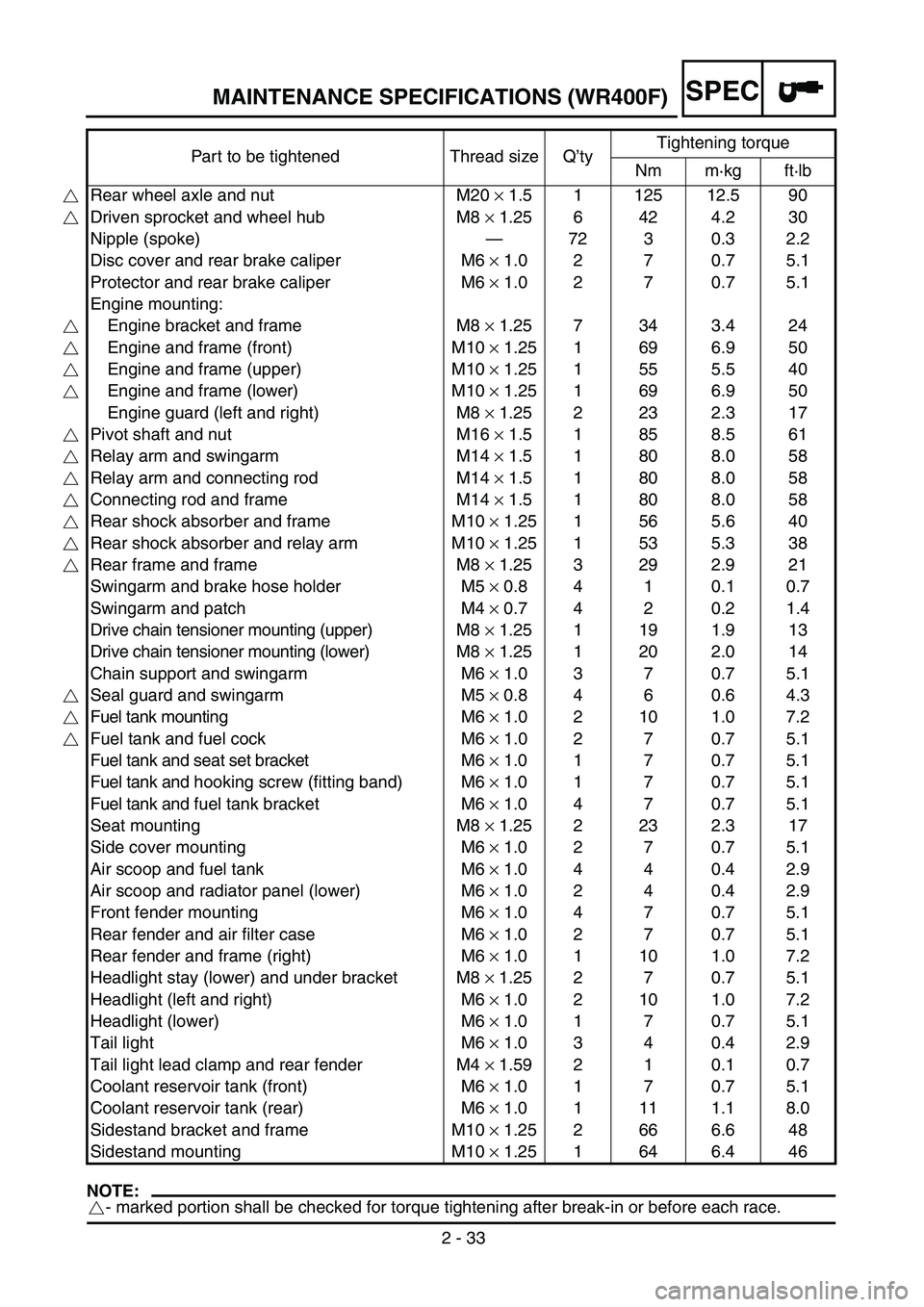
2 - 33
SPECMAINTENANCE SPECIFICATIONS (WR400F)
NOTE:
- marked portion shall be checked for torque tightening after break-in or before each race.Part to be tightened Thread size Q’tyTightening torque
Nm m·kg ft·lb
Rear wheel axle and nut M20 × 1.5 1 125 12.5 90
Driven sprocket and wheel hub M8 × 1.25 6 42 4.2 30
Nipple (spoke)—72 3 0.3 2.2
Disc cover and rear brake caliper M6 × 1.0 2 7 0.7 5.1
Protector and rear brake caliper M6 × 1.0 2 7 0.7 5.1
Engine mounting:
Engine bracket and frame M8 × 1.25 7 34 3.4 24
Engine and frame (front) M10 × 1.25 1 69 6.9 50
Engine and frame (upper) M10 × 1.25 1 55 5.5 40
Engine and frame (lower) M10 × 1.25 1 69 6.9 50
Engine guard (left and right) M8 × 1.25 2 23 2.3 17
Pivot shaft and nut M16 × 1.5 1 85 8.5 61
Relay arm and swingarm M14 × 1.5 1 80 8.0 58
Relay arm and connecting rod M14 × 1.5 1 80 8.0 58
Connecting rod and frame M14 × 1.5 1 80 8.0 58
Rear shock absorber and frame M10 × 1.25 1 56 5.6 40
Rear shock absorber and relay arm M10 × 1.25 1 53 5.3 38
Rear frame and frame M8 × 1.25 3 29 2.9 21
Swingarm and brake hose holder M5 × 0.8 4 1 0.1 0.7
Swingarm and patch M4 × 0.7 4 2 0.2 1.4
Drive chain tensioner mounting (upper) M8 × 1.25 1 19 1.9 13
Drive chain tensioner mounting (lower) M8 × 1.25 1 20 2.0 14
Chain support and swingarm M6 × 1.0 3 7 0.7 5.1
Seal guard and swingarm M5 × 0.8 4 6 0.6 4.3
Fuel tank mounting M6 × 1.0 2 10 1.0 7.2
Fuel tank and fuel cock M6 × 1.0 2 7 0.7 5.1
Fuel tank and seat set bracket M6 × 1.0 1 7 0.7 5.1
Fuel tank and hooking screw (fitting band) M6 × 1.0 1 7 0.7 5.1
Fuel tank and fuel tank bracket M6 × 1.0 4 7 0.7 5.1
Seat mounting M8 × 1.25 2 23 2.3 17
Side cover mounting M6 × 1.0 2 7 0.7 5.1
Air scoop and fuel tank M6 × 1.0 4 4 0.4 2.9
Air scoop and radiator panel (lower) M6 × 1.0 2 4 0.4 2.9
Front fender mounting M6 × 1.0 4 7 0.7 5.1
Rear fender and air filter case M6 × 1.0 2 7 0.7 5.1
Rear fender and frame (right) M6 × 1.0 1 10 1.0 7.2
Headlight stay (lower) and under bracket M8 × 1.25 2 7 0.7 5.1
Headlight (left and right) M6 × 1.0 2 10 1.0 7.2
Headlight (lower) M6 × 1.0 1 7 0.7 5.1
Tail light M6 × 1.0 3 4 0.4 2.9
Tail light lead clamp and rear fender M4 × 1.59 2 1 0.1 0.7
Coolant reservoir tank (front) M6 × 1.0 1 7 0.7 5.1
Coolant reservoir tank (rear) M6 × 1.0 1 11 1.1 8.0
Sidestand bracket and frame M10 × 1.25 2 66 6.6 48
Sidestand mounting M10 × 1.25 1 64 6.4 46
Page 232 of 776
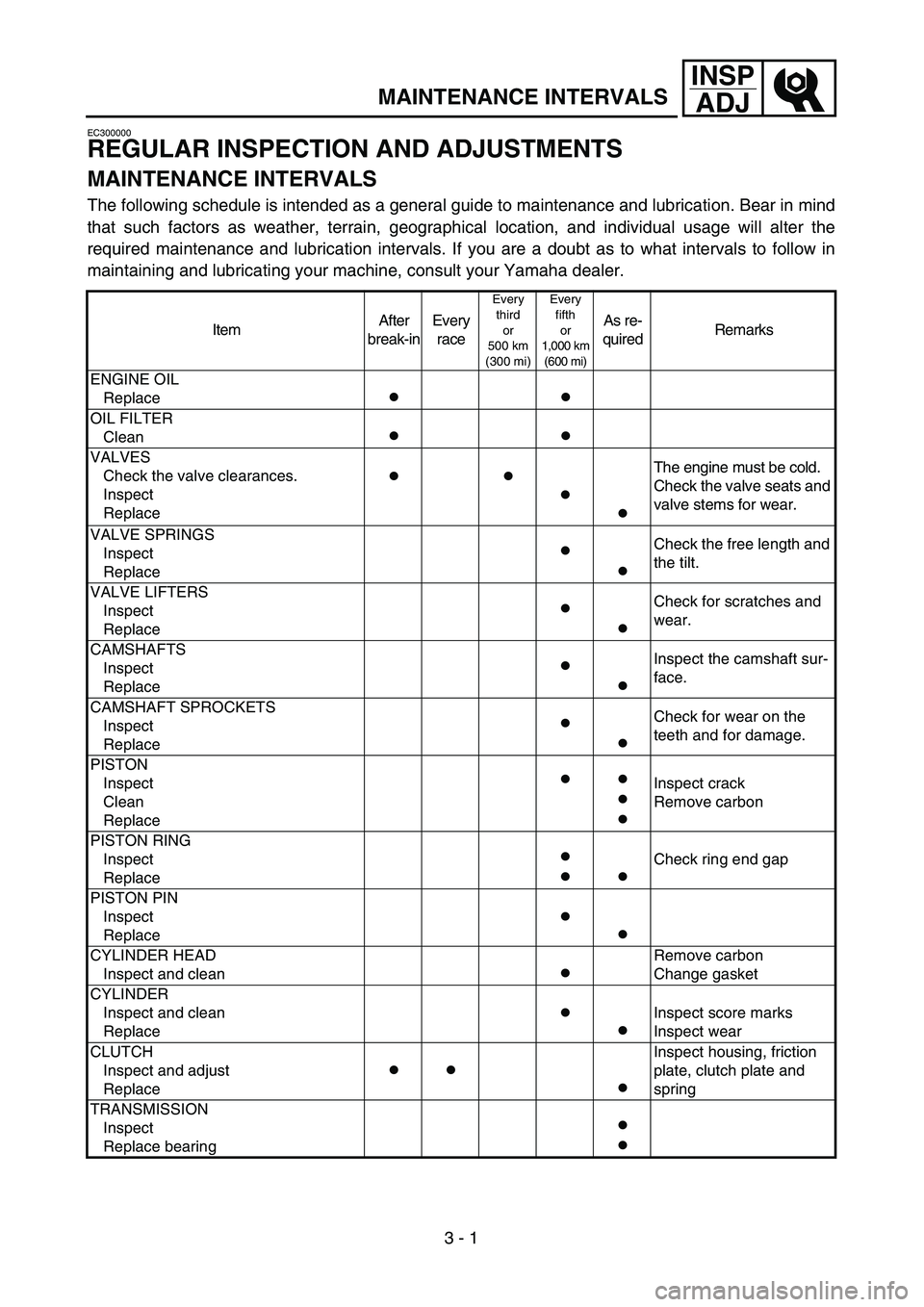
3 - 1
INSP
ADJ
MAINTENANCE INTERVALS
EC300000
REGULAR INSPECTION AND ADJUSTMENTS
MAINTENANCE INTERVALS
The following schedule is intended as a general guide to maintenance and lubrication. Bear in mind
that such factors as weather, terrain, geographical location, and individual usage will alter the
required maintenance and lubrication intervals. If you are a doubt as to what intervals to follow in
maintaining and lubricating your machine, consult your Yamaha dealer.
ItemAfter
break-inEvery
race
Every
third
or
500 km
(300 mi)Every
fifth
or
1,000 km
(600 mi)
As re-
quiredRemarks
ENGINE OIL
Replace
●●
OIL FILTER
Clean
●●
VALVES
Check the valve clearances.
Inspect
Replace
●●
●
●The engine must be cold.
Check the valve seats and
valve stems for wear.
VALVE SPRINGS
Inspect
Replace
●
●Check the free length and
the tilt.
VALVE LIFTERS
Inspect
Replace
●
●Check for scratches and
wear.
CAMSHAFTS
Inspect
Replace
●
●Inspect the camshaft sur-
face.
CAMSHAFT SPROCKETS
Inspect
Replace
●
●Check for wear on the
teeth and for damage.
PISTON
Inspect
Clean
Replace
●●
●
●Inspect crack
Remove carbon
PISTON RING
Inspect
Replace
●
●●Check ring end gap
PISTON PIN
Inspect
Replace
●
●
CYLINDER HEAD
Inspect and clean
●
Remove carbon
Change gasket
CYLINDER
Inspect and clean
Replace
●
●Inspect score marks
Inspect wear
CLUTCH
Inspect and adjust
Replace
●●
●
Inspect housing, friction
plate, clutch plate and
spring
TRANSMISSION
Inspect
Replace bearing
●
●
Page 244 of 776
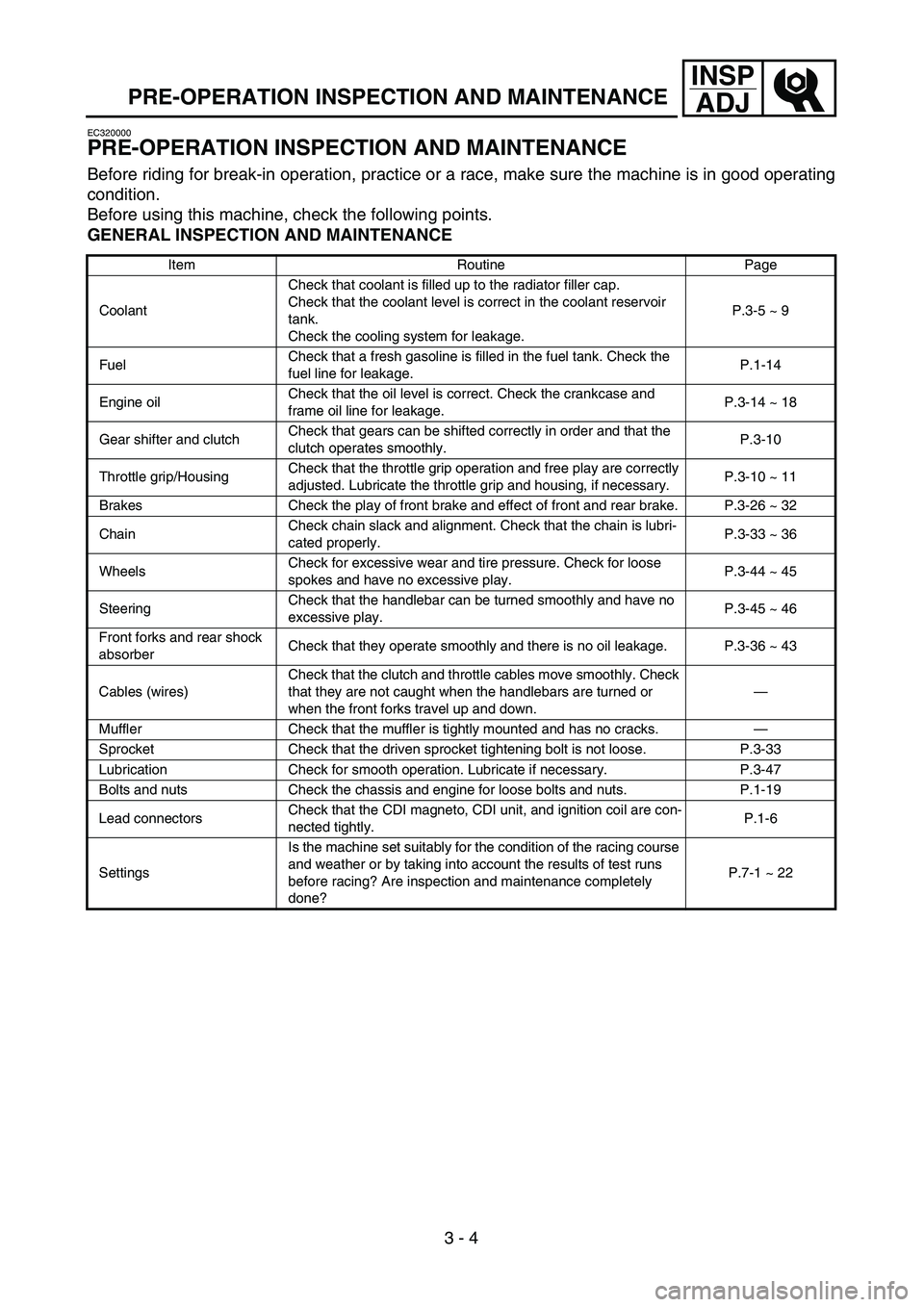
3 - 4
INSP
ADJ
PRE-OPERATION INSPECTION AND MAINTENANCE
EC320000
PRE-OPERATION INSPECTION AND MAINTENANCE
Before riding for break-in operation, practice or a race, make sure the machine is in good operating
condition.
Before using this machine, check the following points.
GENERAL INSPECTION AND MAINTENANCE
Item Routine Page
CoolantCheck that coolant is filled up to the radiator filler cap.
Check that the coolant level is correct in the coolant reservoir
tank.
Check the cooling system for leakage.P.3-5 ~ 9
FuelCheck that a fresh gasoline is filled in the fuel tank. Check the
fuel line for leakage.P.1-14
Engine oilCheck that the oil level is correct. Check the crankcase and
frame oil line for leakage.P.3-14 ~ 18
Gear shifter and clutchCheck that gears can be shifted correctly in order and that the
clutch operates smoothly.P.3-10
Throttle grip/HousingCheck that the throttle grip operation and free play are correctly
adjusted. Lubricate the throttle grip and housing, if necessary.P.3-10 ~ 11
Brakes Check the play of front brake and effect of front and rear brake. P.3-26 ~ 32
ChainCheck chain slack and alignment. Check that the chain is lubri-
cated properly.P.3-33 ~ 36
WheelsCheck for excessive wear and tire pressure. Check for loose
spokes and have no excessive play.P.3-44 ~ 45
SteeringCheck that the handlebar can be turned smoothly and have no
excessive play.P.3-45 ~ 46
Front forks and rear shock
absorberCheck that they operate smoothly and there is no oil leakage. P.3-36 ~ 43
Cables (wires)Check that the clutch and throttle cables move smoothly. Check
that they are not caught when the handlebars are turned or
when the front forks travel up and down.—
Muffler Check that the muffler is tightly mounted and has no cracks.—
Sprocket Check that the driven sprocket tightening bolt is not loose. P.3-33
Lubrication Check for smooth operation. Lubricate if necessary. P.3-47
Bolts and nuts Check the chassis and engine for loose bolts and nuts. P.1-19
Lead connectorsCheck that the CDI magneto, CDI unit, and ignition coil are con-
nected tightly.P.1-6
SettingsIs the machine set suitably for the condition of the racing course
and weather or by taking into account the results of test runs
before racing? Are inspection and maintenance completely
done?P.7-1 ~ 22
Page 248 of 776
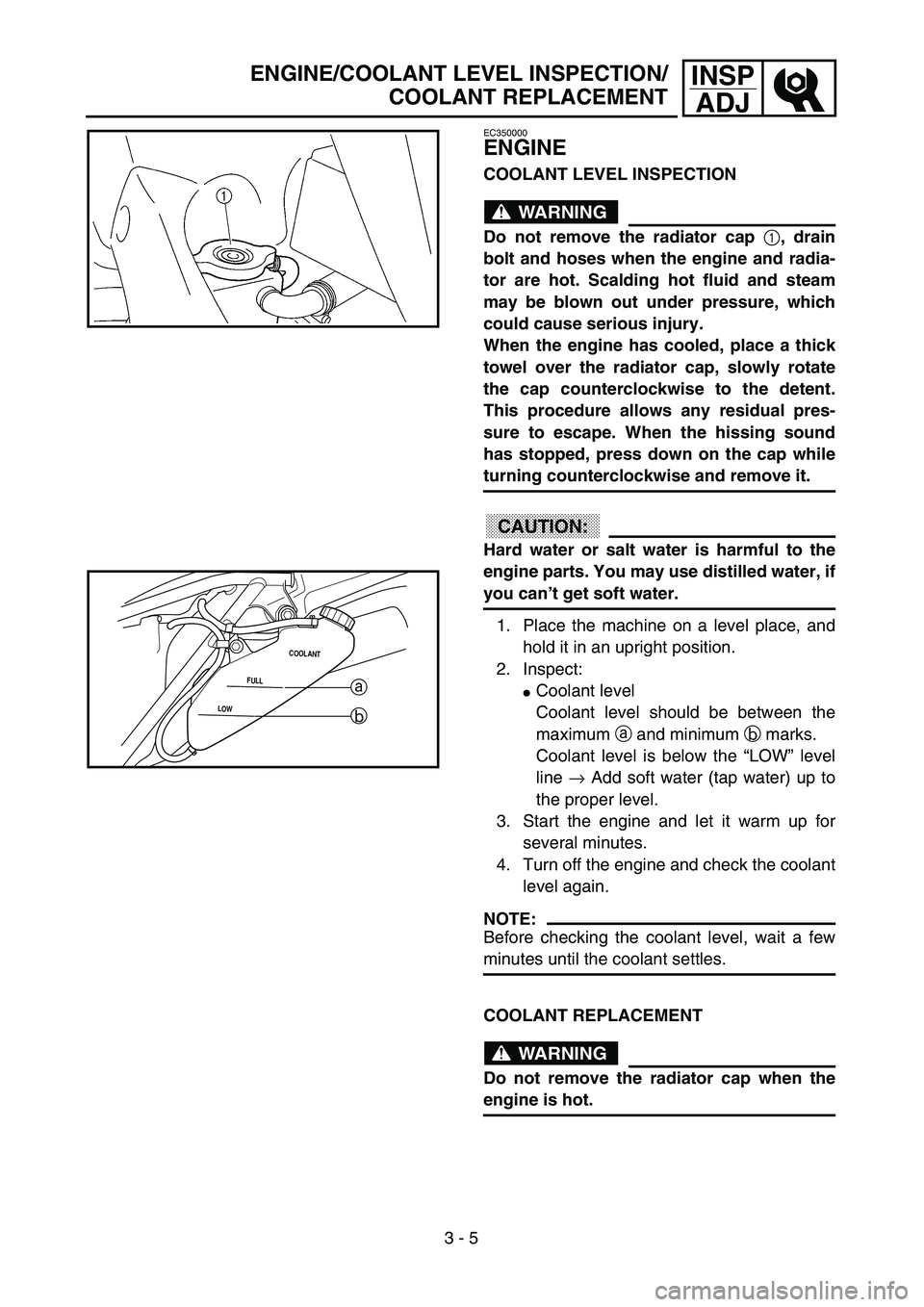
3 - 5
INSP
ADJ
EC350000
ENGINE
COOLANT LEVEL INSPECTION
WARNING
Do not remove the radiator cap 1, drain
bolt and hoses when the engine and radia-
tor are hot. Scalding hot fluid and steam
may be blown out under pressure, which
could cause serious injury.
When the engine has cooled, place a thick
towel over the radiator cap, slowly rotate
the cap counterclockwise to the detent.
This procedure allows any residual pres-
sure to escape. When the hissing sound
has stopped, press down on the cap while
turning counterclockwise and remove it.
CAUTION:
Hard water or salt water is harmful to the
engine parts. You may use distilled water, if
you can’t get soft water.
1. Place the machine on a level place, and
hold it in an upright position.
2. Inspect:
Coolant level
Coolant level should be between the
maximum a and minimum b marks.
Coolant level is below the “LOW” level
line → Add soft water (tap water) up to
the proper level.
3. Start the engine and let it warm up for
several minutes.
4. Turn off the engine and check the coolant
level again.
NOTE:
Before checking the coolant level, wait a few
minutes until the coolant settles.
LOWFULLCOOLANT
a
b
COOLANT REPLACEMENT
WARNING
Do not remove the radiator cap when the
engine is hot.
ENGINE/COOLANT LEVEL INSPECTION/
COOLANT REPLACEMENT