stop start YAMAHA WR 450F 2010 User Guide
[x] Cancel search | Manufacturer: YAMAHA, Model Year: 2010, Model line: WR 450F, Model: YAMAHA WR 450F 2010Pages: 230, PDF Size: 13.87 MB
Page 59 of 230
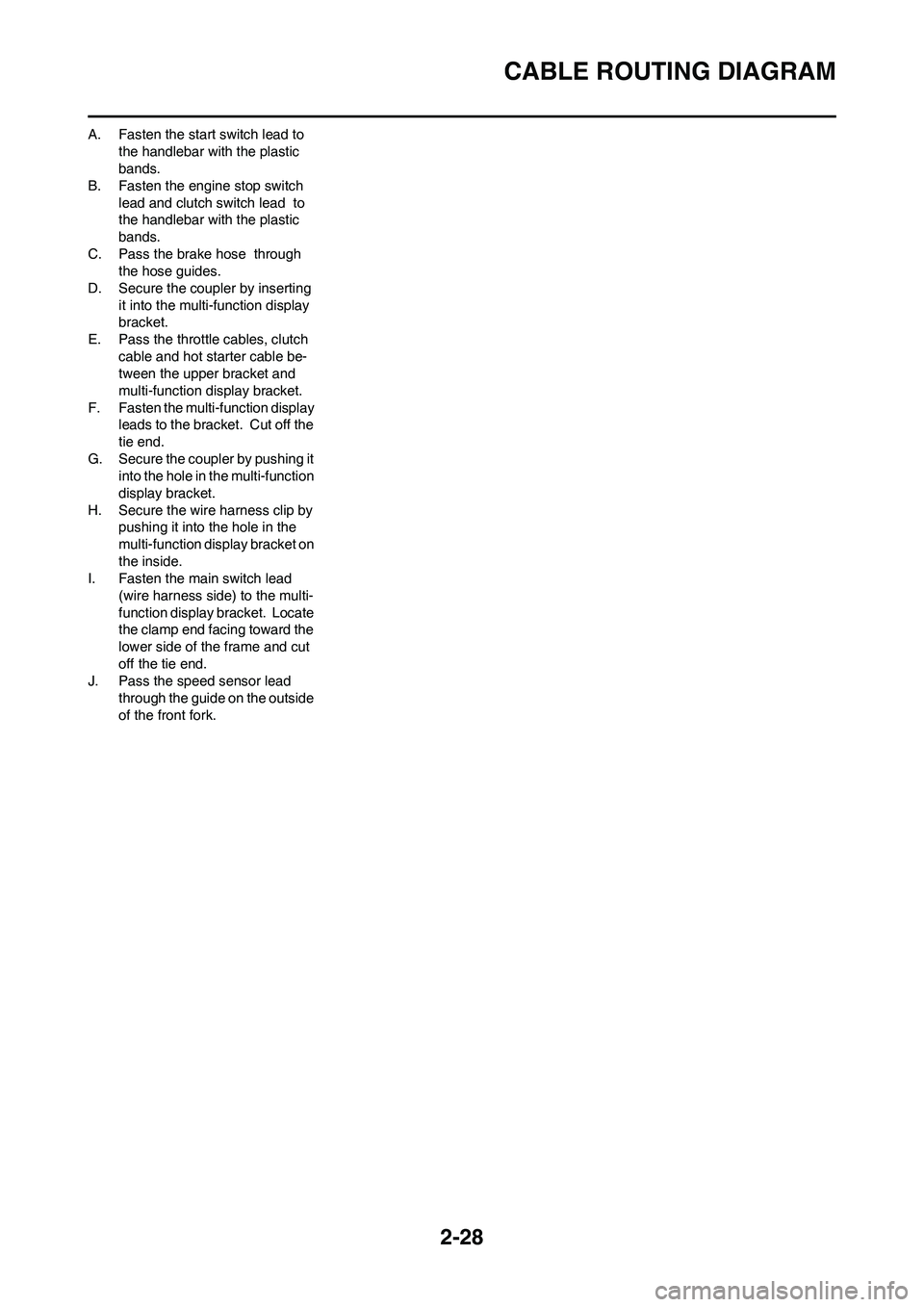
2-28
CABLE ROUTING DIAGRAM
A. Fasten the start switch lead to
the handlebar with the plastic
bands.
B. Fasten the engine stop switch
lead and clutch switch lead to
the handlebar with the plastic
bands.
C. Pass the brake hose through
the hose guides.
D. Secure the coupler by inserting
it into the multi-function display
bracket.
E. Pass the throttle cables, clutch
cable and hot starter cable be-
tween the upper bracket and
multi-function display bracket.
F. Fasten the multi-function display
leads to the bracket. Cut off the
tie end.
G. Secure the coupler by pushing it
into the hole in the multi-function
display bracket.
H. Secure the wire harness clip by
pushing it into the hole in the
multi-function display bracket on
the inside.
I. Fasten the main switch lead
(wire harness side) to the multi-
function display bracket. Locate
the clamp end facing toward the
lower side of the frame and cut
off the tie end.
J. Pass the speed sensor lead
through the guide on the outside
of the front fork.
Page 73 of 230
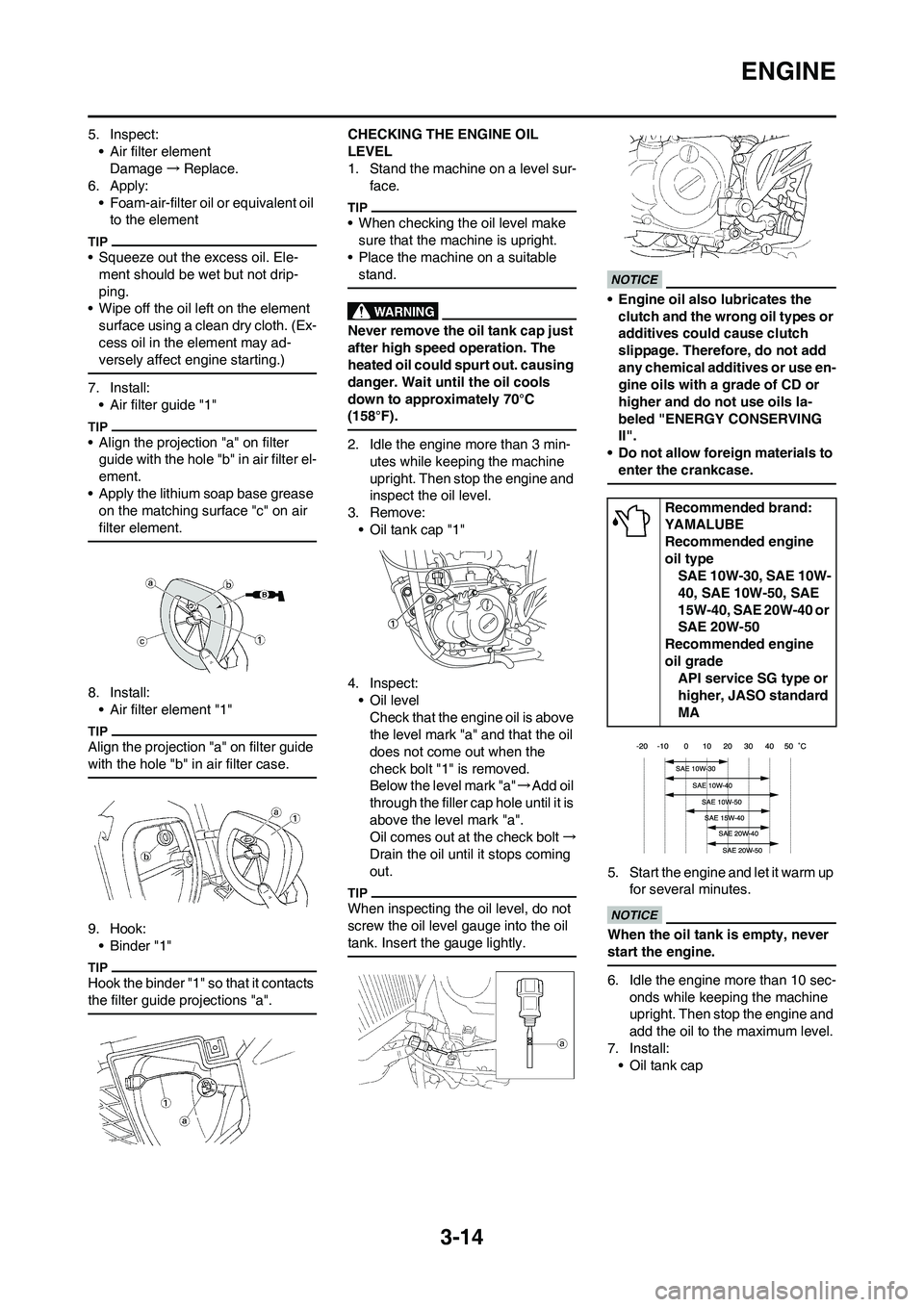
3-14
ENGINE
5. Inspect:
• Air filter element
Damage→Replace.
6. Apply:
• Foam-air-filter oil or equivalent oil
to the element
• Squeeze out the excess oil. Ele-
ment should be wet but not drip-
ping.
• Wipe off the oil left on the element
surface using a clean dry cloth. (Ex-
cess oil in the element may ad-
versely affect engine starting.)
7. Install:
• Air filter guide "1"
• Align the projection "a" on filter
guide with the hole "b" in air filter el-
ement.
• Apply the lithium soap base grease
on the matching surface "c" on air
filter element.
8. Install:
• Air filter element "1"
Align the projection "a" on filter guide
with the hole "b" in air filter case.
9. Hook:
•Binder "1"
Hook the binder "1" so that it contacts
the filter guide projections "a".
CHECKING THE ENGINE OIL
LEVEL
1. Stand the machine on a level sur-
face.
• When checking the oil level make
sure that the machine is upright.
• Place the machine on a suitable
stand.
Never remove the oil tank cap just
after high speed operation. The
heated oil could spurt out. causing
danger. Wait until the oil cools
down to approximately 70°C
(158°F).
2. Idle the engine more than 3 min-
utes while keeping the machine
upright. Then stop the engine and
inspect the oil level.
3. Remove:
• Oil tank cap "1"
4. Inspect:
• Oil level
Check that the engine oil is above
the level mark "a" and that the oil
does not come out when the
check bolt "1" is removed.
Below the level mark "a"→Add oil
through the filler cap hole until it is
above the level mark "a".
Oil comes out at the check bolt→
Drain the oil until it stops coming
out.
When inspecting the oil level, do not
screw the oil level gauge into the oil
tank. Insert the gauge lightly.
• Engine oil also lubricates the
clutch and the wrong oil types or
additives could cause clutch
slippage. Therefore, do not add
any chemical additives or use en-
gine oils with a grade of CD or
higher and do not use oils la-
beled "ENERGY CONSERVING
II".
• Do not allow foreign materials to
enter the crankcase.
5. Start the engine and let it warm up
for several minutes.
When the oil tank is empty, never
start the engine.
6. Idle the engine more than 10 sec-
onds while keeping the machine
upright. Then stop the engine and
add the oil to the maximum level.
7. Install:
• Oil tank cap
Recommended brand:
YAMALUBE
Recommended engine
oil type
SAE 10W-30, SAE 10W-
40, SAE 10W-50, SAE
15W-40, SAE 20W-40 or
SAE 20W-50
Recommended engine
oil grade
API service SG type or
higher, JASO standard
MA
Page 74 of 230
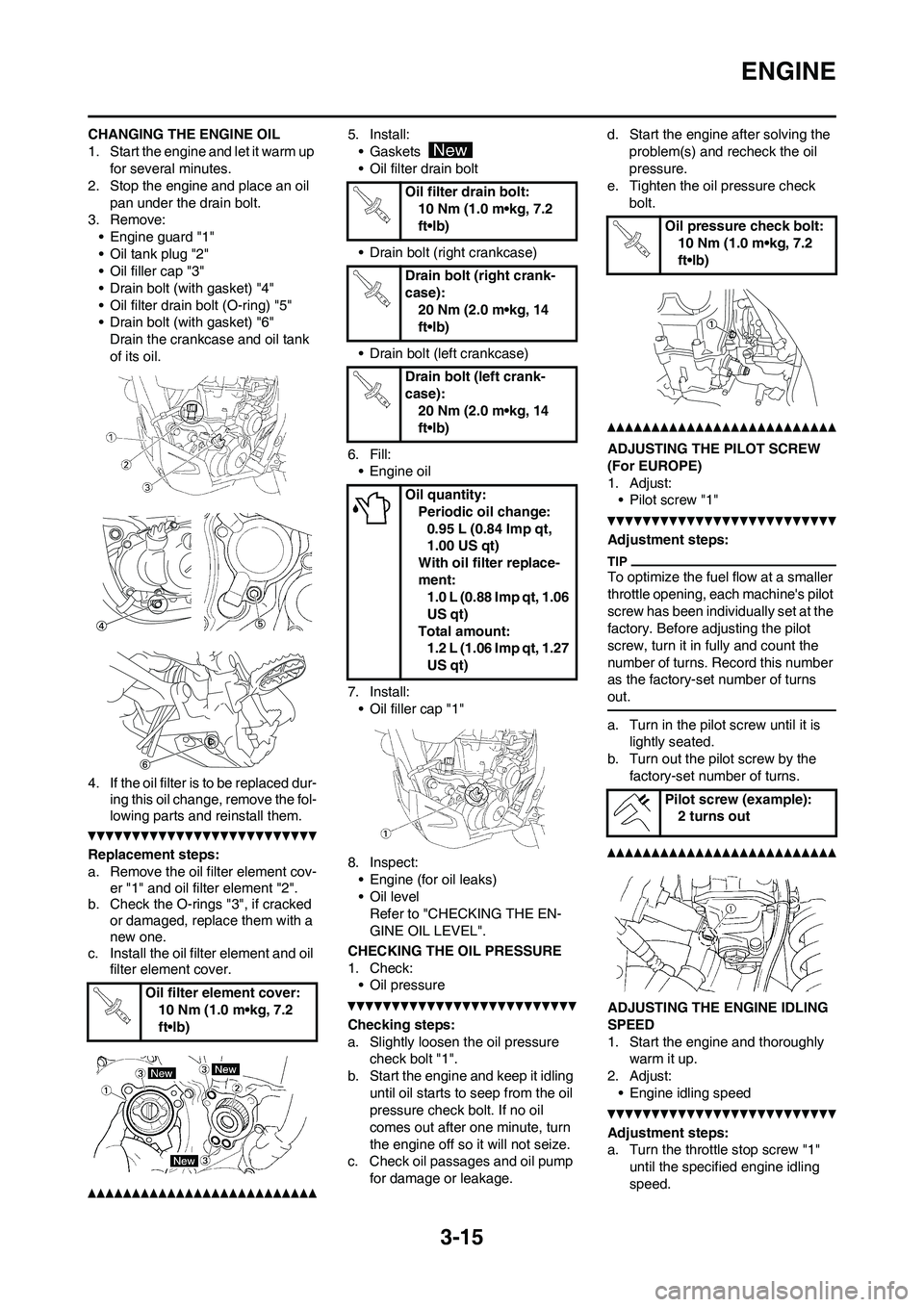
3-15
ENGINE
CHANGING THE ENGINE OIL
1. Start the engine and let it warm up
for several minutes.
2. Stop the engine and place an oil
pan under the drain bolt.
3. Remove:
• Engine guard "1"
• Oil tank plug "2"
• Oil filler cap "3"
• Drain bolt (with gasket) "4"
• Oil filter drain bolt (O-ring) "5"
• Drain bolt (with gasket) "6"
Drain the crankcase and oil tank
of its oil.
4. If the oil filter is to be replaced dur-
ing this oil change, remove the fol-
lowing parts and reinstall them.
Replacement steps:
a. Remove the oil filter element cov-
er "1" and oil filter element "2".
b. Check the O-rings "3", if cracked
or damaged, replace them with a
new one.
c. Install the oil filter element and oil
filter element cover.
5. Install:
• Gaskets
• Oil filter drain bolt
• Drain bolt (right crankcase)
• Drain bolt (left crankcase)
6. Fill:
• Engine oil
7. Install:
• Oil filler cap "1"
8. Inspect:
• Engine (for oil leaks)
• Oil level
Refer to "CHECKING THE EN-
GINE OIL LEVEL".
CHECKING THE OIL PRESSURE
1. Check:
• Oil pressure
Checking steps:
a. Slightly loosen the oil pressure
check bolt "1".
b. Start the engine and keep it idling
until oil starts to seep from the oil
pressure check bolt. If no oil
comes out after one minute, turn
the engine off so it will not seize.
c. Check oil passages and oil pump
for damage or leakage.d. Start the engine after solving the
problem(s) and recheck the oil
pressure.
e. Tighten the oil pressure check
bolt.
ADJUSTING THE PILOT SCREW
(For EUROPE)
1. Adjust:
• Pilot screw "1"
Adjustment steps:
To optimize the fuel flow at a smaller
throttle opening, each machine's pilot
screw has been individually set at the
factory. Before adjusting the pilot
screw, turn it in fully and count the
number of turns. Record this number
as the factory-set number of turns
out.
a. Turn in the pilot screw until it is
lightly seated.
b. Turn out the pilot screw by the
factory-set number of turns.
ADJUSTING THE ENGINE IDLING
SPEED
1. Start the engine and thoroughly
warm it up.
2. Adjust:
• Engine idling speed
Adjustment steps:
a. Turn the throttle stop screw "1"
until the specified engine idling
speed. Oil filter element cover:
10 Nm (1.0 m•kg, 7.2
ft•lb)
Oil filter drain bolt:
10 Nm (1.0 m•kg, 7.2
ft•lb)
Drain bolt (right crank-
case):
20 Nm (2.0 m•kg, 14
ft•lb)
Drain bolt (left crank-
case):
20 Nm (2.0 m•kg, 14
ft•lb)
Oil quantity:
Periodic oil change:
0.95 L (0.84 Imp qt,
1.00 US qt)
With oil filter replace-
ment:
1.0 L (0.88 Imp qt, 1.06
US qt)
Total amount:
1.2 L (1.06 Imp qt, 1.27
US qt)
Oil pressure check bolt:
10 Nm (1.0 m•kg, 7.2
ft•lb)
Pilot screw (example):
2 turns out
Page 94 of 230
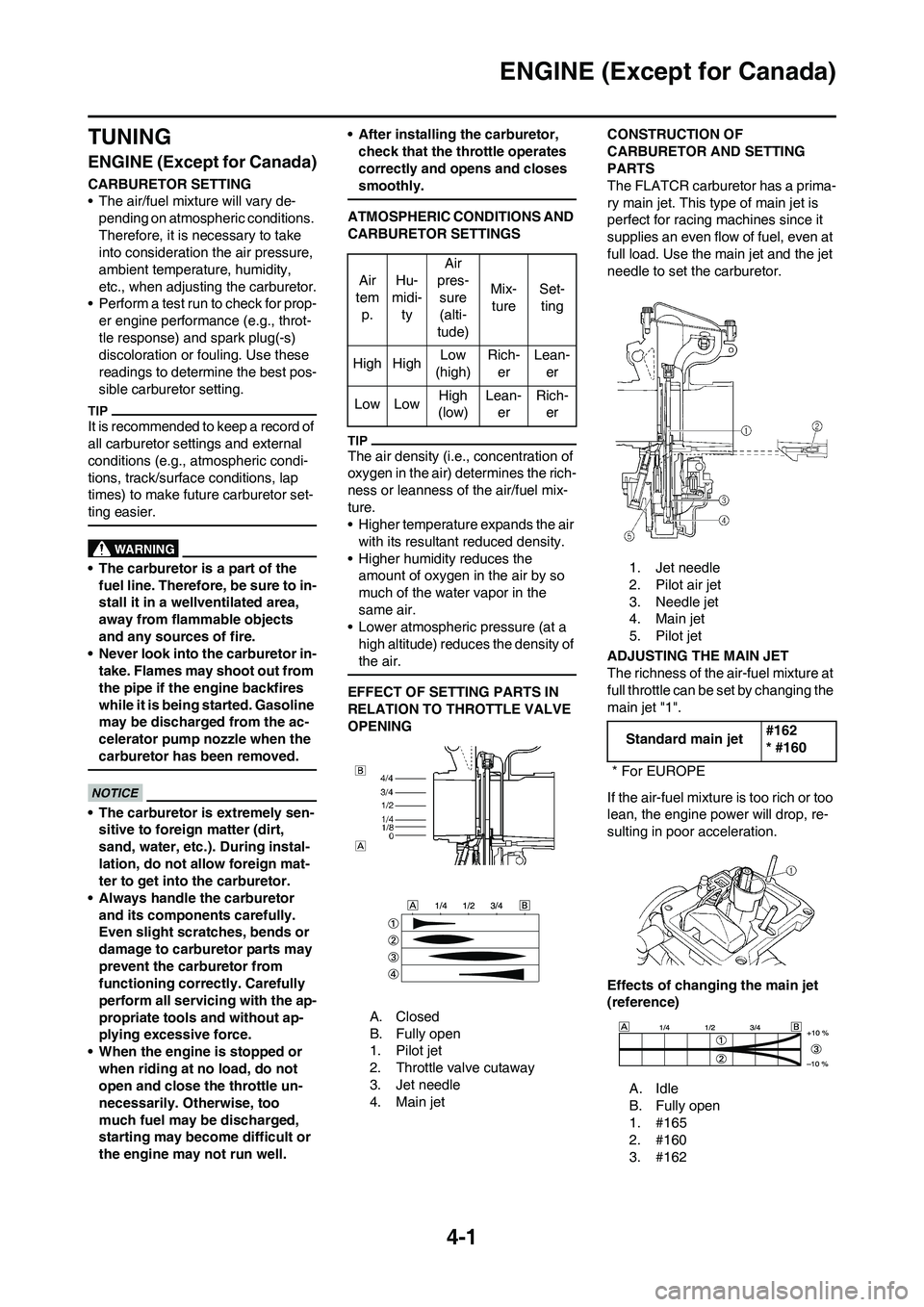
4-1
ENGINE (Except for Canada)
TUNING
ENGINE (Except for Canada)
CARBURETOR SETTING
• The air/fuel mixture will vary de-pending on atmospheric conditions.
Therefore, it is necessary to take
into consideration the air pressure,
ambient temperature, humidity,
etc., when adjusting the carburetor.
• Perform a test run to check for prop- er engine performance (e.g., throt-
tle response) and spark plug(-s)
discoloration or fouling. Use these
readings to determine the best pos-
sible carburetor setting.
It is recommended to keep a record of
all carburetor settings and external
conditions (e.g., atmospheric condi-
tions, track/surface conditions, lap
times) to make future carburetor set-
ting easier.
• The carburetor is a part of the fuel line. Therefore, be sure to in-
stall it in a wellventilated area,
away from flammable objects
and any sources of fire.
• Never look into the carburetor in- take. Flames may shoot out from
the pipe if the engine backfires
while it is being started. Gasoline
may be discharged from the ac-
celerator pump nozzle when the
carburetor has been removed.
• The carburetor is extremely sen-sitive to foreign matter (dirt,
sand, water, etc.). During instal-
lation, do not al low foreign mat-
ter to get into the carburetor.
• Always handle the carburetor and its components carefully.
Even slight scratches, bends or
damage to carburetor parts may
prevent the carburetor from
functioning correctly. Carefully
perform all servicing with the ap-
propriate tools and without ap-
plying excessive force.
• When the engine is stopped or when riding at no load, do not
open and close the throttle un-
necessarily. Otherwise, too
much fuel may be discharged,
starting may become difficult or
the engine may not run well. • After installing the carburetor,
check that the throttle operates
correctly and opens and closes
smoothly.
ATMOSPHERIC CONDITIONS AND
CARBURETOR SETTINGS
The air density (i.e., concentration of
oxygen in the air) determines the rich-
ness or leanness of the air/fuel mix-
ture.
• Higher temperature expands the air with its resultant reduced density.
• Higher humidity reduces the amount of oxygen in the air by so
much of the water vapor in the
same air.
• Lower atmospheric pressure (at a
high altitude) reduces the density of
the air.
EFFECT OF SETTING PARTS IN
RELATION TO THROTTLE VALVE
OPENING
A. Closed
B. Fully open
1. Pilot jet
2. Throttle valve cutaway
3. Jet needle
4. Main jet CONSTRUCTION OF
CARBURETOR AND SETTING
PARTS
The FLATCR carburetor has a prima-
ry main jet. This type of main jet is
perfect for racing machines since it
supplies an even flow of fuel, even at
full load. Use the main jet and the jet
needle to set the carburetor.
1. Jet needle
2. Pilot air jet
3. Needle jet
4. Main jet
5. Pilot jet
ADJUSTING THE MAIN JET
The richness of the air-fuel mixture at
full throttle can be set by changing the
main jet "1".
If the air-fuel mixture is too rich or too
lean, the engine power will drop, re-
sulting in poor acceleration.
Effects of changing the main jet
(reference)
A. Idle
B. Fully open
1. #165
2. #160
3. #162
Air
tem p. Hu-
midi- ty Air
pres- sure
(alti-
tude) Mix-
ture Set-
ting
High High Low
(high) Rich-
er Lean-
er
Low Low High
(low) Lean-
er Rich-
er
Standard main jet #162
* #160
* For EUROPE
Page 112 of 230
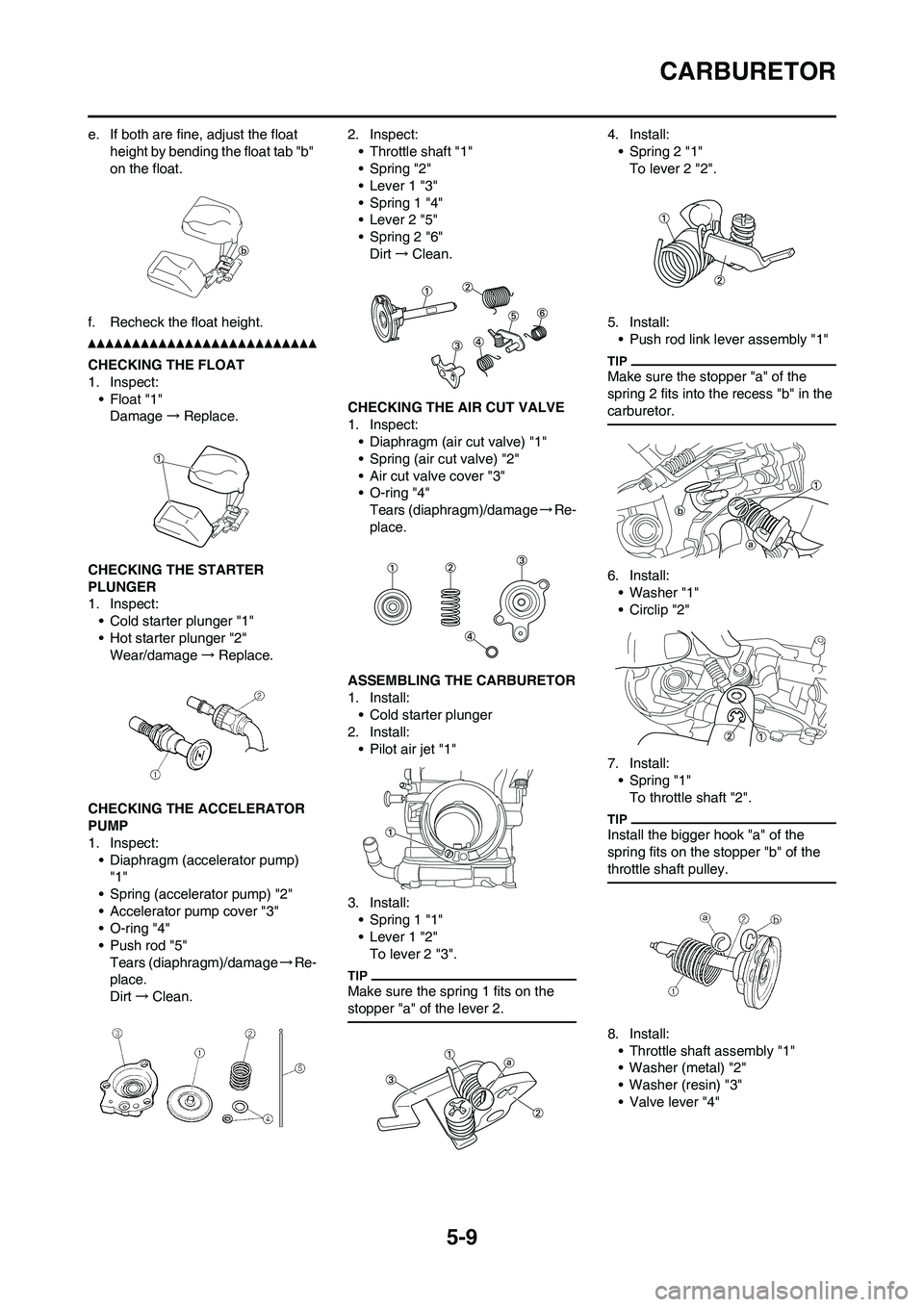
5-9
CARBURETOR
e. If both are fine, adjust the float
height by bending the float tab "b"
on the float.
f. Recheck the float height.
CHECKING THE FLOAT
1. Inspect:
• Float "1"
Damage→Replace.
CHECKING THE STARTER
PLUNGER
1. Inspect:
• Cold starter plunger "1"
• Hot starter plunger "2"
Wear/damage→Replace.
CHECKING THE ACCELERATOR
PUMP
1. Inspect:
• Diaphragm (accelerator pump)
"1"
• Spring (accelerator pump) "2"
• Accelerator pump cover "3"
• O-ring "4"
• Push rod "5"
Tears (diaphragm)/damage→Re-
place.
Dirt→Clean.2. Inspect:
• Throttle shaft "1"
• Spring "2"
• Lever 1 "3"
• Spring 1 "4"
• Lever 2 "5"
• Spring 2 "6"
Dirt→Clean.
CHECKING THE AIR CUT VALVE
1. Inspect:
• Diaphragm (air cut valve) "1"
• Spring (air cut valve) "2"
• Air cut valve cover "3"
• O-ring "4"
Tears (diaphragm)/damage→Re-
place.
ASSEMBLING THE CARBURETOR
1. Install:
• Cold starter plunger
2. Install:
•Pilot air jet "1"
3. Install:
• Spring 1 "1"
• Lever 1 "2"
To lever 2 "3".
Make sure the spring 1 fits on the
stopper "a" of the lever 2.
4. Install:
• Spring 2 "1"
To lever 2 "2".
5. Install:
• Push rod link lever assembly "1"
Make sure the stopper "a" of the
spring 2 fits into the recess "b" in the
carburetor.
6. Install:
• Washer "1"
• Circlip "2"
7. Install:
• Spring "1"
To throttle shaft "2".
Install the bigger hook "a" of the
spring fits on the stopper "b" of the
throttle shaft pulley.
8. Install:
• Throttle shaft assembly "1"
• Washer (metal) "2"
• Washer (resin) "3"
• Valve lever "4"
Page 113 of 230
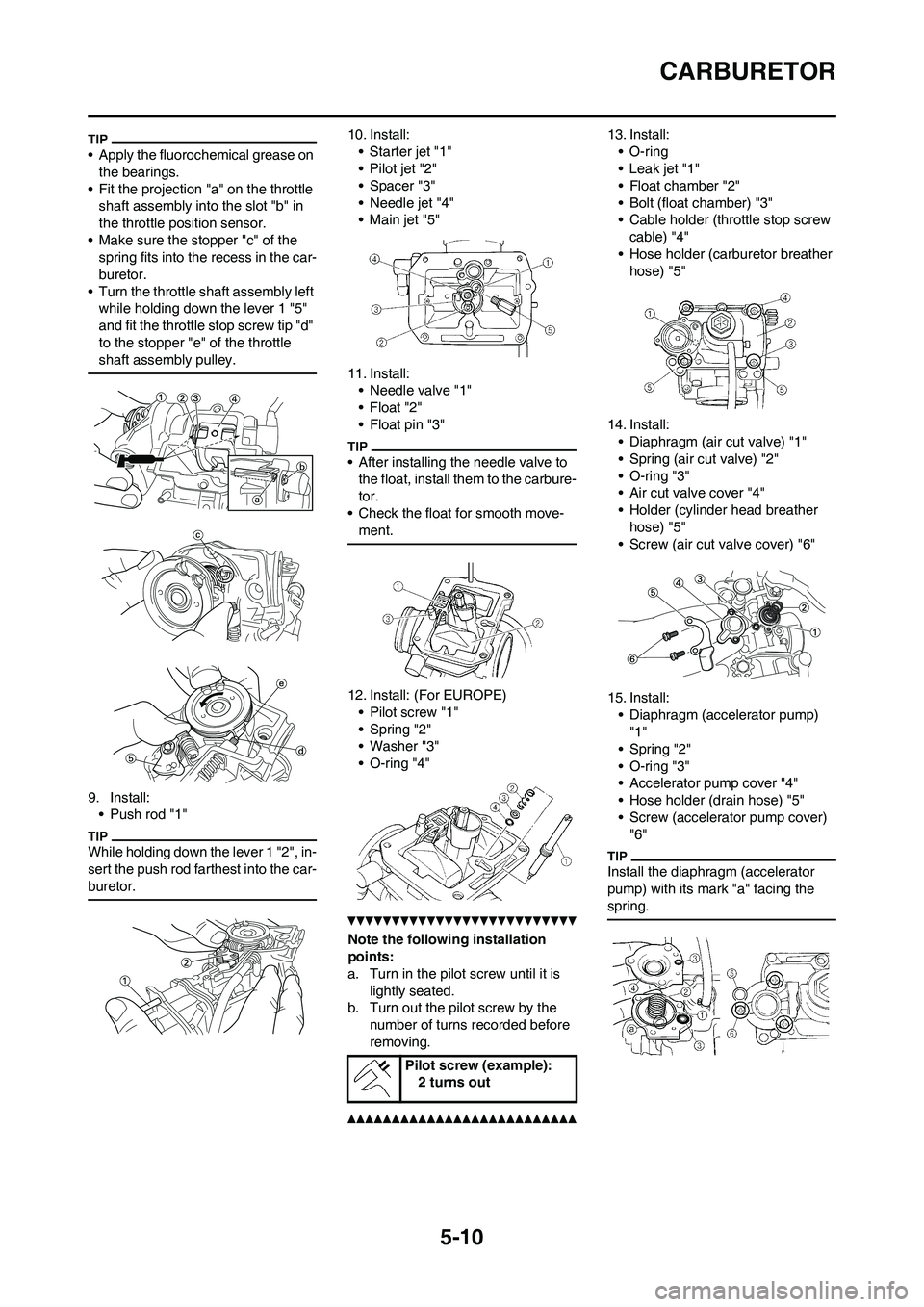
5-10
CARBURETOR
• Apply the fluorochemical grease on
the bearings.
• Fit the projection "a" on the throttle
shaft assembly into the slot "b" in
the throttle position sensor.
• Make sure the stopper "c" of the
spring fits into the recess in the car-
buretor.
• Turn the throttle shaft assembly left
while holding down the lever 1 "5"
and fit the throttle stop screw tip "d"
to the stopper "e" of the throttle
shaft assembly pulley.
9. Install:
• Push rod "1"
While holding down the lever 1 "2", in-
sert the push rod farthest into the car-
buretor.
10. Install:
• Starter jet "1"
• Pilot jet "2"
• Spacer "3"
• Needle jet "4"
•Main jet "5"
11. Install:
• Needle valve "1"
•Float "2"
• Float pin "3"
• After installing the needle valve to
the float, install them to the carbure-
tor.
• Check the float for smooth move-
ment.
12. Install: (For EUROPE)
• Pilot screw "1"
• Spring "2"
• Washer "3"
• O-ring "4"
Note the following installation
points:
a. Turn in the pilot screw until it is
lightly seated.
b. Turn out the pilot screw by the
number of turns recorded before
removing.
13. Install:
• O-ring
• Leak jet "1"
• Float chamber "2"
• Bolt (float chamber) "3"
• Cable holder (throttle stop screw
cable) "4"
• Hose holder (carburetor breather
hose) "5"
14. Install:
• Diaphragm (air cut valve) "1"
• Spring (air cut valve) "2"
• O-ring "3"
• Air cut valve cover "4"
• Holder (cylinder head breather
hose) "5"
• Screw (air cut valve cover) "6"
15. Install:
• Diaphragm (accelerator pump)
"1"
• Spring "2"
• O-ring "3"
• Accelerator pump cover "4"
• Hose holder (drain hose) "5"
• Screw (accelerator pump cover)
"6"
Install the diaphragm (accelerator
pump) with its mark "a" facing the
spring.
Pilot screw (example):
2 turns out
Page 149 of 230
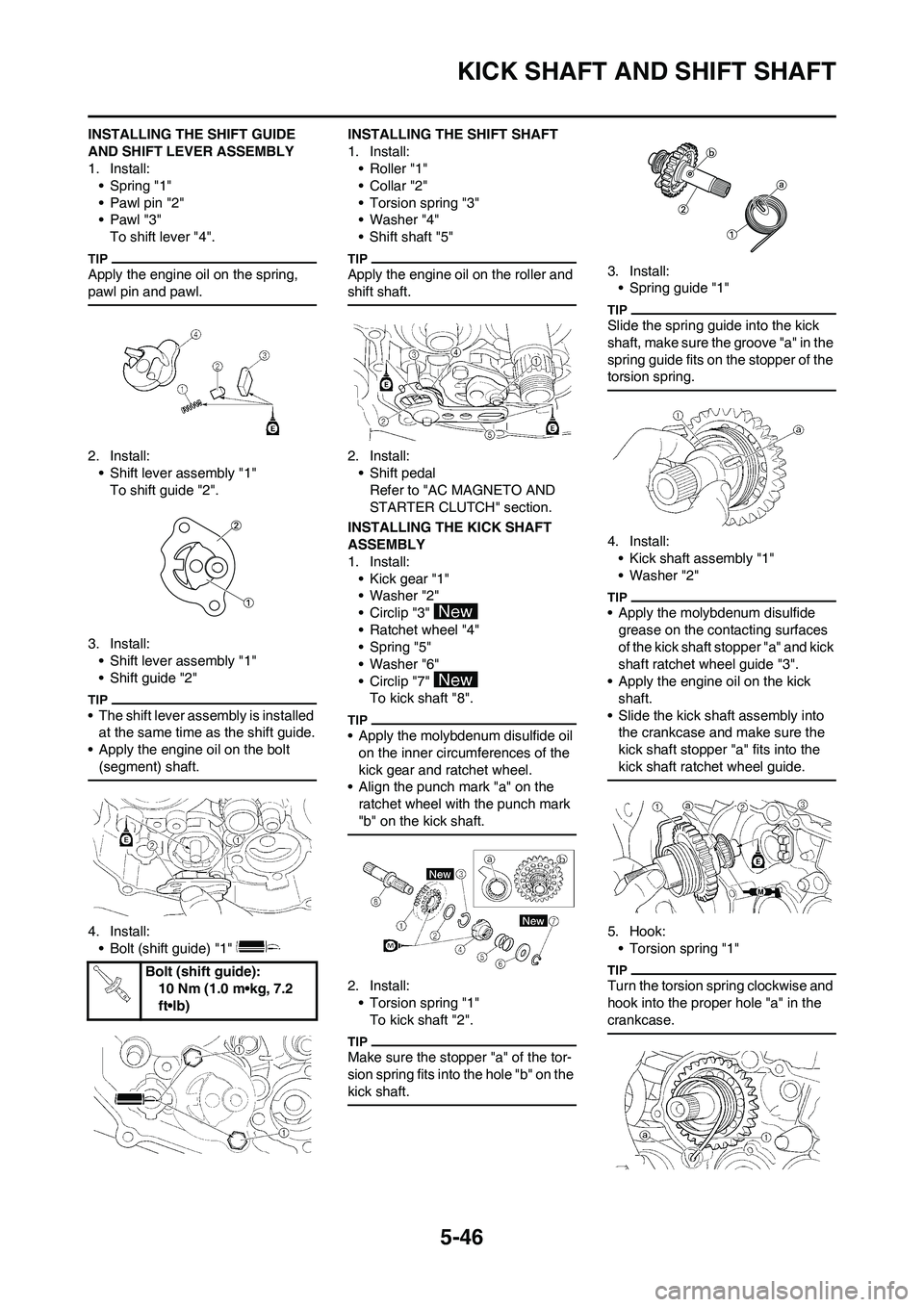
5-46
KICK SHAFT AND SHIFT SHAFT
INSTALLING THE SHIFT GUIDE
AND SHIFT LEVER ASSEMBLY
1. Install:
• Spring "1"
• Pawl pin "2"
•Pawl "3"
To shift lever "4".
Apply the engine oil on the spring,
pawl pin and pawl.
2. Install:
• Shift lever assembly "1"
To shift guide "2".
3. Install:
• Shift lever assembly "1"
• Shift guide "2"
• The shift lever assembly is installed
at the same time as the shift guide.
• Apply the engine oil on the bolt
(segment) shaft.
4. Install:
• Bolt (shift guide) "1" INSTALLING THE SHIFT SHAFT
1. Install:
• Roller "1"
• Collar "2"
• Torsion spring "3"
• Washer "4"
• Shift shaft "5"
Apply the engine oil on the roller and
shift shaft.
2. Install:
• Shift pedal
Refer to "AC MAGNETO AND
STARTER CLUTCH" section.
INSTALLING THE KICK SHAFT
ASSEMBLY
1. Install:
• Kick gear "1"
• Washer "2"
• Circlip "3"
• Ratchet wheel "4"
• Spring "5"
• Washer "6"
• Circlip "7"
To kick shaft "8".
• Apply the molybdenum disulfide oil
on the inner circumferences of the
kick gear and ratchet wheel.
• Align the punch mark "a" on the
ratchet wheel with the punch mark
"b" on the kick shaft.
2. Install:
• Torsion spring "1"
To kick shaft "2".
Make sure the stopper "a" of the tor-
sion spring fits into the hole "b" on the
kick shaft.
3. Install:
• Spring guide "1"
Slide the spring guide into the kick
shaft, make sure the groove "a" in the
spring guide fits on the stopper of the
torsion spring.
4. Install:
• Kick shaft assembly "1"
• Washer "2"
• Apply the molybdenum disulfide
grease on the contacting surfaces
of the kick shaft stopper "a" and kick
shaft ratchet wheel guide "3".
• Apply the engine oil on the kick
shaft.
• Slide the kick shaft assembly into
the crankcase and make sure the
kick shaft stopper "a" fits into the
kick shaft ratchet wheel guide.
5. Hook:
• Torsion spring "1"
Turn the torsion spring clockwise and
hook into the proper hole "a" in the
crankcase.Bolt (shift guide):
10 Nm (1.0 m•kg, 7.2
ft•lb)
Page 191 of 230
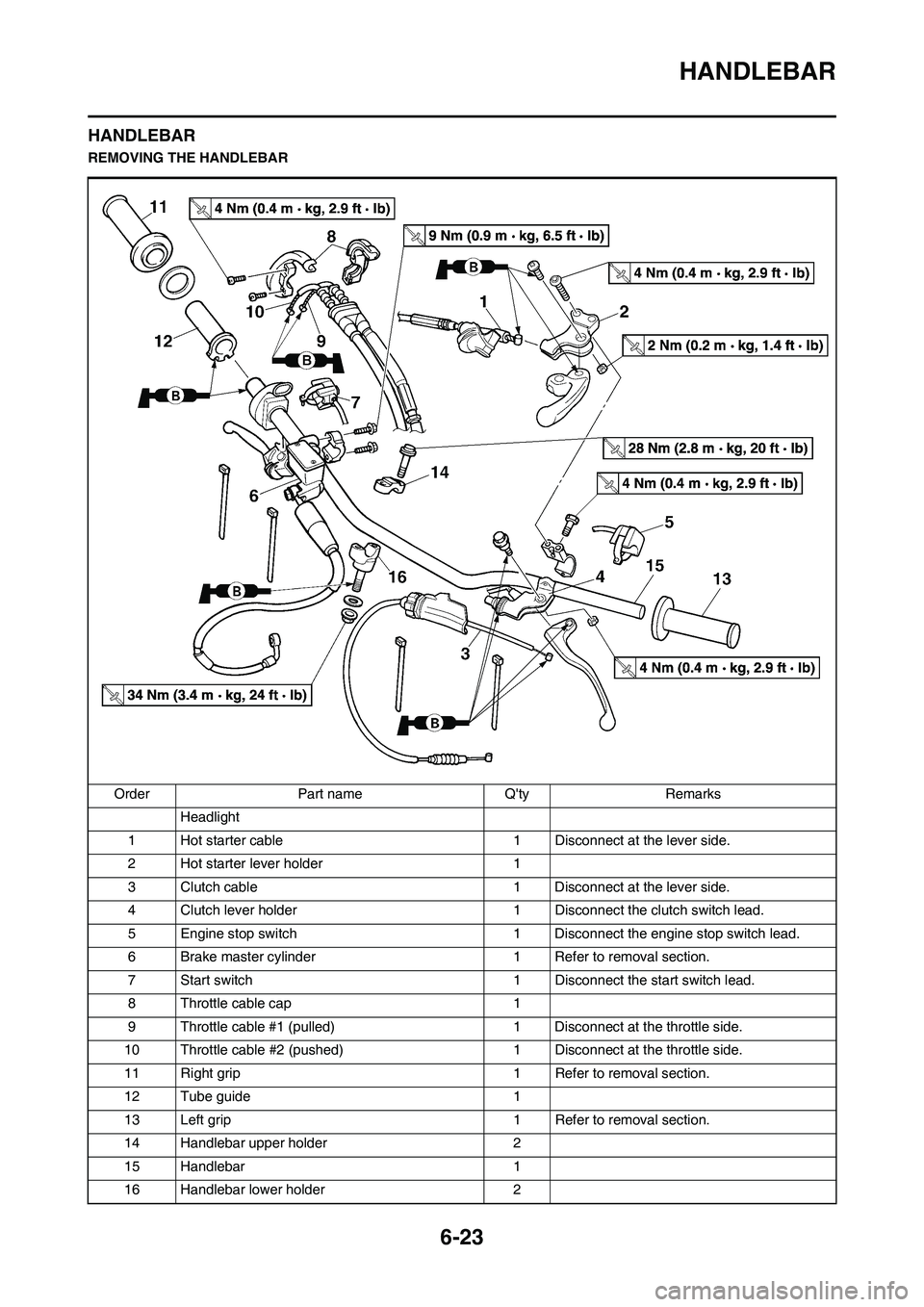
6-23
HANDLEBAR
HANDLEBAR
REMOVING THE HANDLEBAR
Order Part name Q'ty Remarks
Headlight
1 Hot starter cable 1 Disconnect at the lever side.
2 Hot starter lever holder 1
3 Clutch cable 1 Disconnect at the lever side.
4 Clutch lever holder 1 Disconnect the clutch switch lead.
5 Engine stop switch 1 Disconnect the engine stop switch lead.
6 Brake master cylinder 1 Refer to removal section.
7 Start switch 1 Disconnect the start switch lead.
8 Throttle cable cap 1
9 Throttle cable #1 (pulled) 1 Disconnect at the throttle side.
10 Throttle cable #2 (pushed) 1 Disconnect at the throttle side.
11 Right grip 1 Refer to removal section.
12 Tube guide 1
13 Left grip 1 Refer to removal section.
14 Handlebar upper holder 2
15 Handlebar 1
16 Handlebar lower holder 2
Page 193 of 230
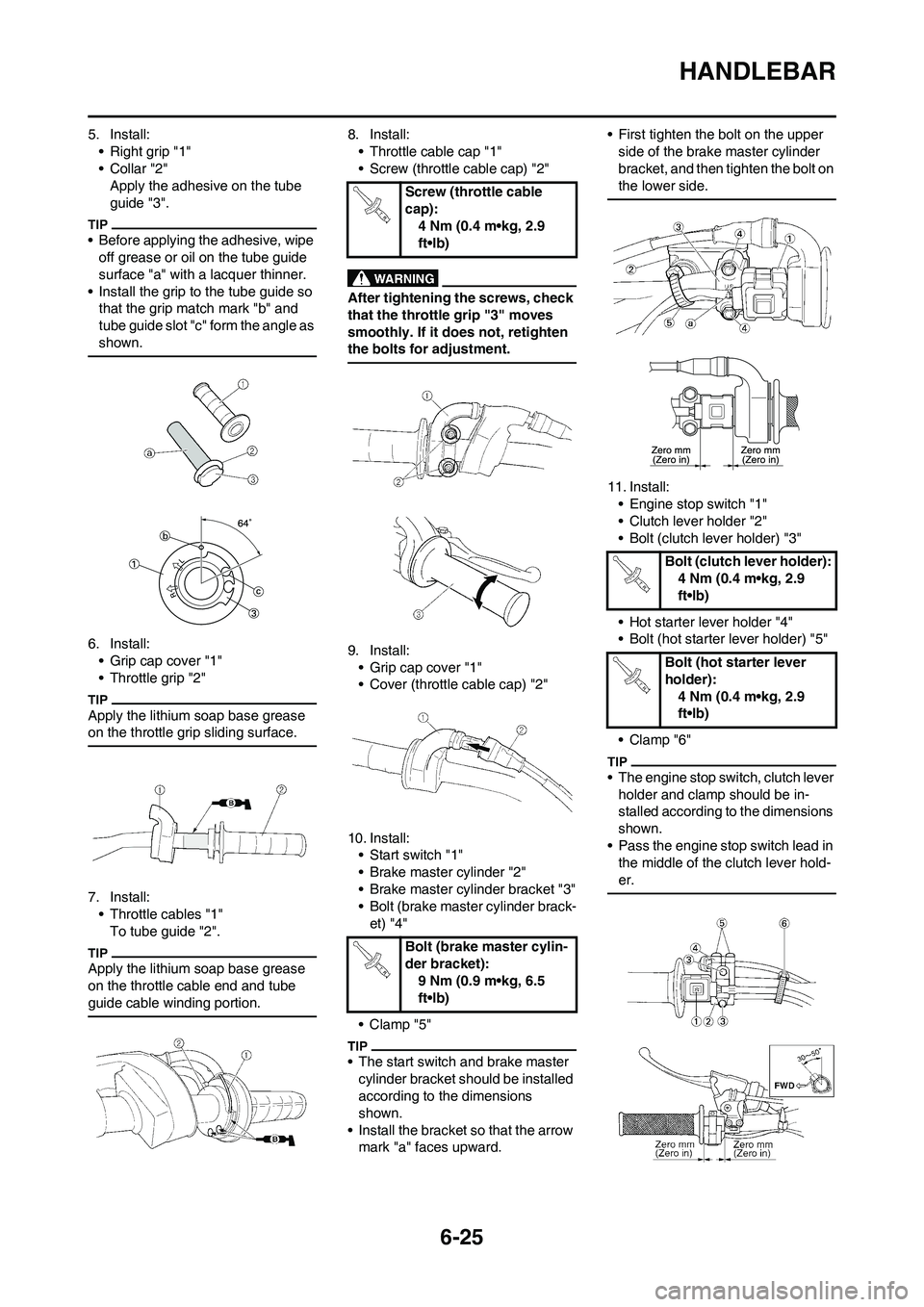
6-25
HANDLEBAR
5. Install:
• Right grip "1"
•Collar "2"
Apply the adhesive on the tube
guide "3".
• Before applying the adhesive, wipe
off grease or oil on the tube guide
surface "a" with a lacquer thinner.
• Install the grip to the tube guide so
that the grip match mark "b" and
tube guide slot "c" form the angle as
shown.
6. Install:
• Grip cap cover "1"
• Throttle grip "2"
Apply the lithium soap base grease
on the throttle grip sliding surface.
7. Install:
• Throttle cables "1"
To tube guide "2".
Apply the lithium soap base grease
on the throttle cable end and tube
guide cable winding portion.
8. Install:
• Throttle cable cap "1"
• Screw (throttle cable cap) "2"
After tightening the screws, check
that the throttle grip "3" moves
smoothly. If it does not, retighten
the bolts for adjustment.
9. Install:
• Grip cap cover "1"
• Cover (throttle cable cap) "2"
10. Install:
• Start switch "1"
• Brake master cylinder "2"
• Brake master cylinder bracket "3"
• Bolt (brake master cylinder brack-
et) "4"
•Clamp "5"
• The start switch and brake master
cylinder bracket should be installed
according to the dimensions
shown.
• Install the bracket so that the arrow
mark "a" faces upward.• First tighten the bolt on the upper
side of the brake master cylinder
bracket, and then tighten the bolt on
the lower side.
11. Install:
• Engine stop switch "1"
• Clutch lever holder "2"
• Bolt (clutch lever holder) "3"
• Hot starter lever holder "4"
• Bolt (hot starter lever holder) "5"
• Clamp "6"
• The engine stop switch, clutch lever
holder and clamp should be in-
stalled according to the dimensions
shown.
• Pass the engine stop switch lead in
the middle of the clutch lever hold-
er.
Screw (throttle cable
cap):
4 Nm (0.4 m•kg, 2.9
ft•lb)
Bolt (brake master cylin-
der bracket):
9 Nm (0.9 m•kg, 6.5
ft•lb)
Bolt (clutch lever holder):
4 Nm (0.4 m•kg, 2.9
ft•lb)
Bolt (hot starter lever
holder):
4 Nm (0.4 m•kg, 2.9
ft•lb)
Page 209 of 230
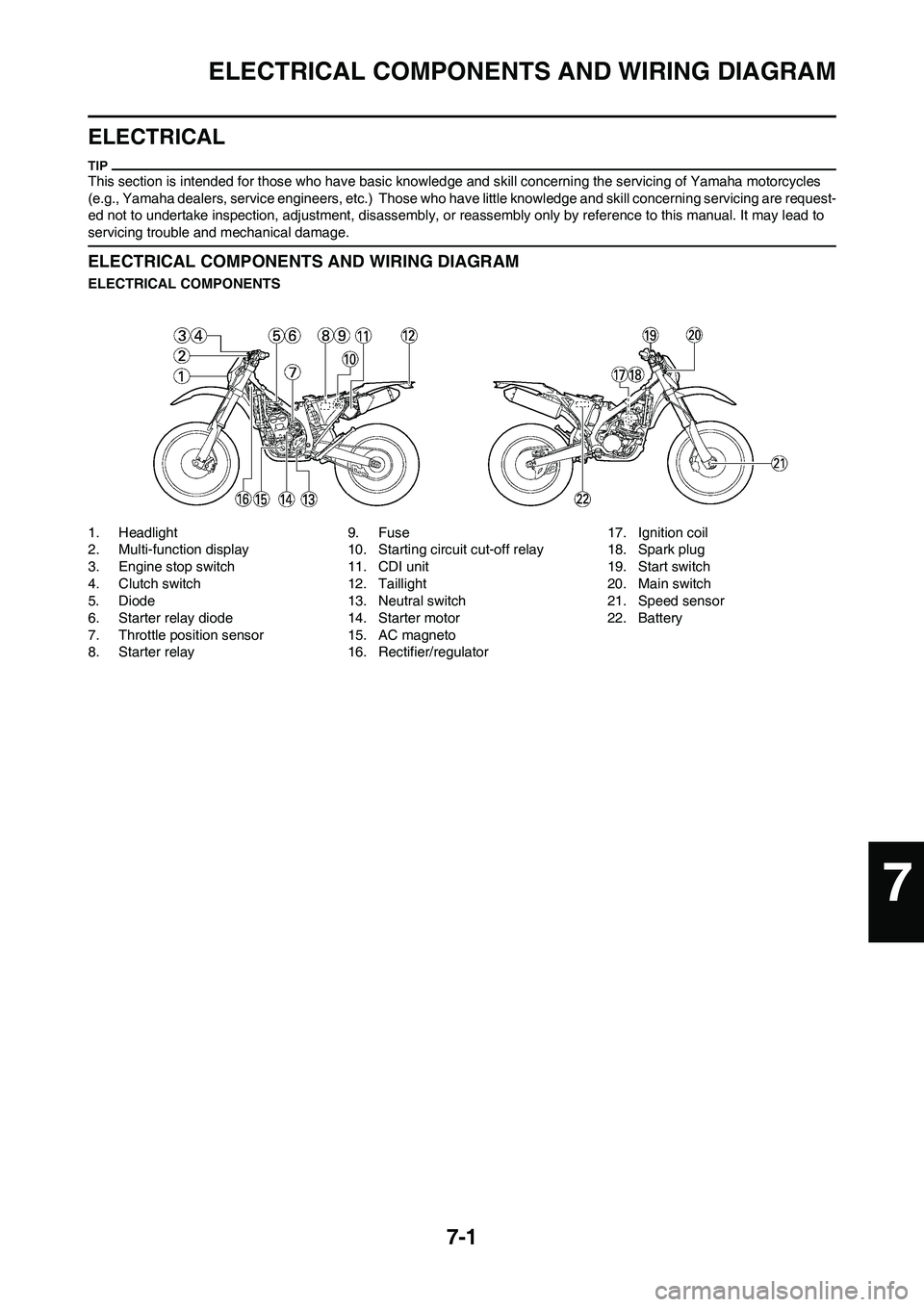
7-1
ELECTRICAL COMPONENTS AND WIRING DIAGRAM
ELECTRICAL
This section is intended for those who have basic knowledge and skill concerning the servicing of Yamaha motorcycles
(e.g., Yamaha dealers, service engineers, etc.) Those who have little knowledge and skill concerning servicing are request-
ed not to undertake inspection, adjustment, disassembly, or reassembly only by reference to this manual. It may lead to
servicing trouble and mechanical damage.
ELECTRICAL COMPONENTS AND WIRING DIAGRAM
ELECTRICAL COMPONENTS
1. Headlight
2. Multi-function display
3. Engine stop switch
4. Clutch switch
5. Diode
6. Starter relay diode
7. Throttle position sensor
8. Starter relay9. Fuse
10. Starting circuit cut-off relay
11. CDI unit
12. Taillight
13. Neutral switch
14. Starter motor
15. AC magneto
16. Rectifier/regulator17. Ignition coil
18. Spark plug
19. Start switch
20. Main switch
21. Speed sensor
22. Battery
7