YAMAHA YZ250F 2011 Owners Manual
Manufacturer: YAMAHA, Model Year: 2011, Model line: YZ250F, Model: YAMAHA YZ250F 2011Pages: 196, PDF Size: 14.15 MB
Page 181 of 196
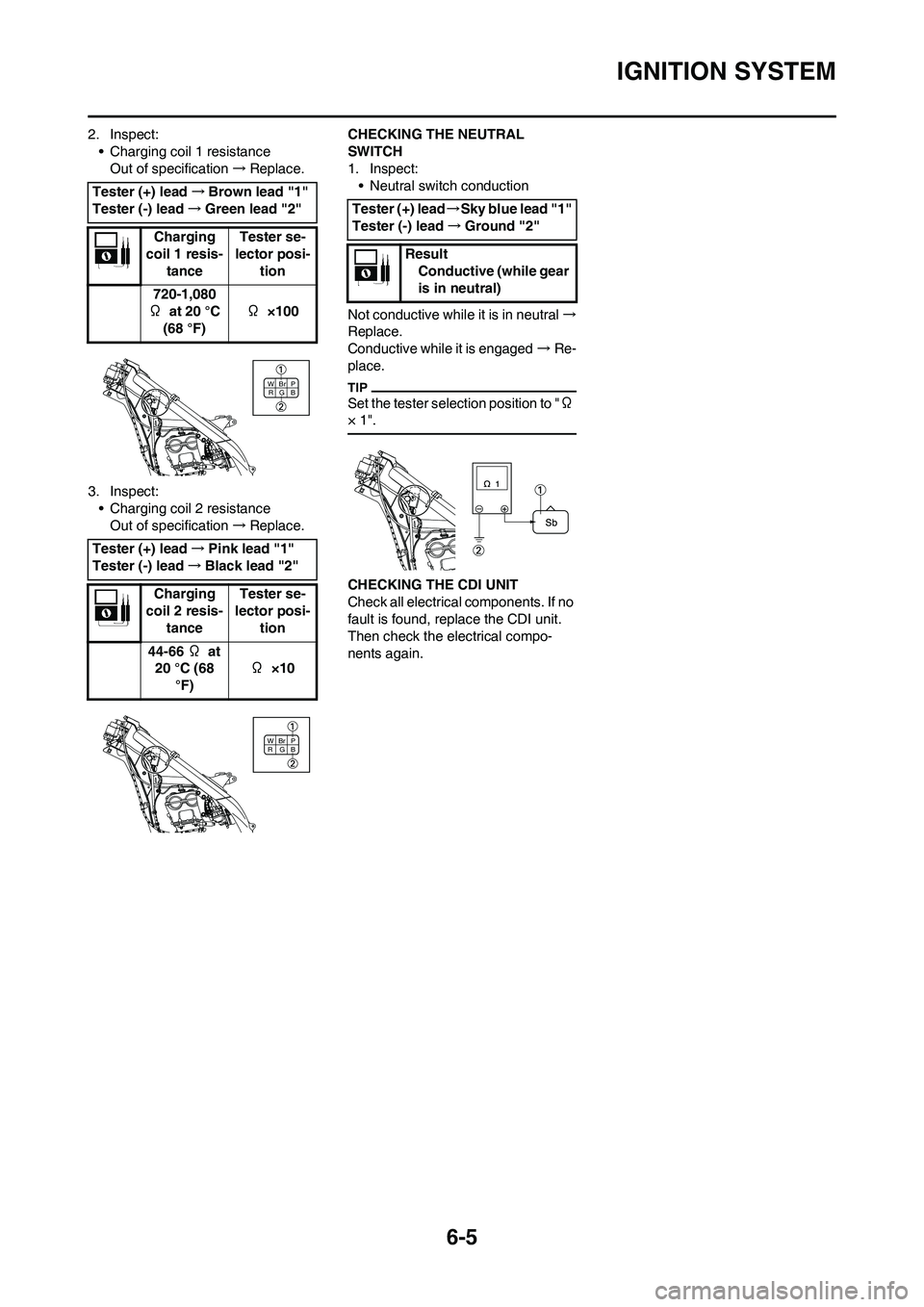
6-5
IGNITION SYSTEM
2. Inspect:
• Charging coil 1 resistance
Out of specification→Replace.
3. Inspect:
• Charging coil 2 resistance
Out of specification→Replace.CHECKING THE NEUTRAL
SWITCH
1. Inspect:
• Neutral switch conduction
Not conductive while it is in neutral→
Replace.
Conductive while it is engaged→Re-
place.
Set the tester selection position to "Ω
× 1".
CHECKING THE CDI UNIT
Check all electrical components. If no
fault is found, replace the CDI unit.
Then check the electrical compo-
nents again. Tester (+) lead→Brown lead "1"
Tester (-) lead→Green lead "2"
Charging
coil 1 resis-
tanceTester se-
lector posi-
tion
720-1,080
Ω at 20 °C
(68 °F)Ω ×100
Tester (+) lead→Pink lead "1"
Tester (-) lead→Black lead "2"
Charging
coil 2 resis-
tanceTester se-
lector posi-
tion
44-66 Ω at
20 °C (68
°F)Ω ×10
B WBr
GP
R
B WBr
GP
R
Tester (+) lead→Sky blue lead "1"
Tester (-) lead→Ground "2"
Result
Conductive (while gear
is in neutral)
Page 182 of 196
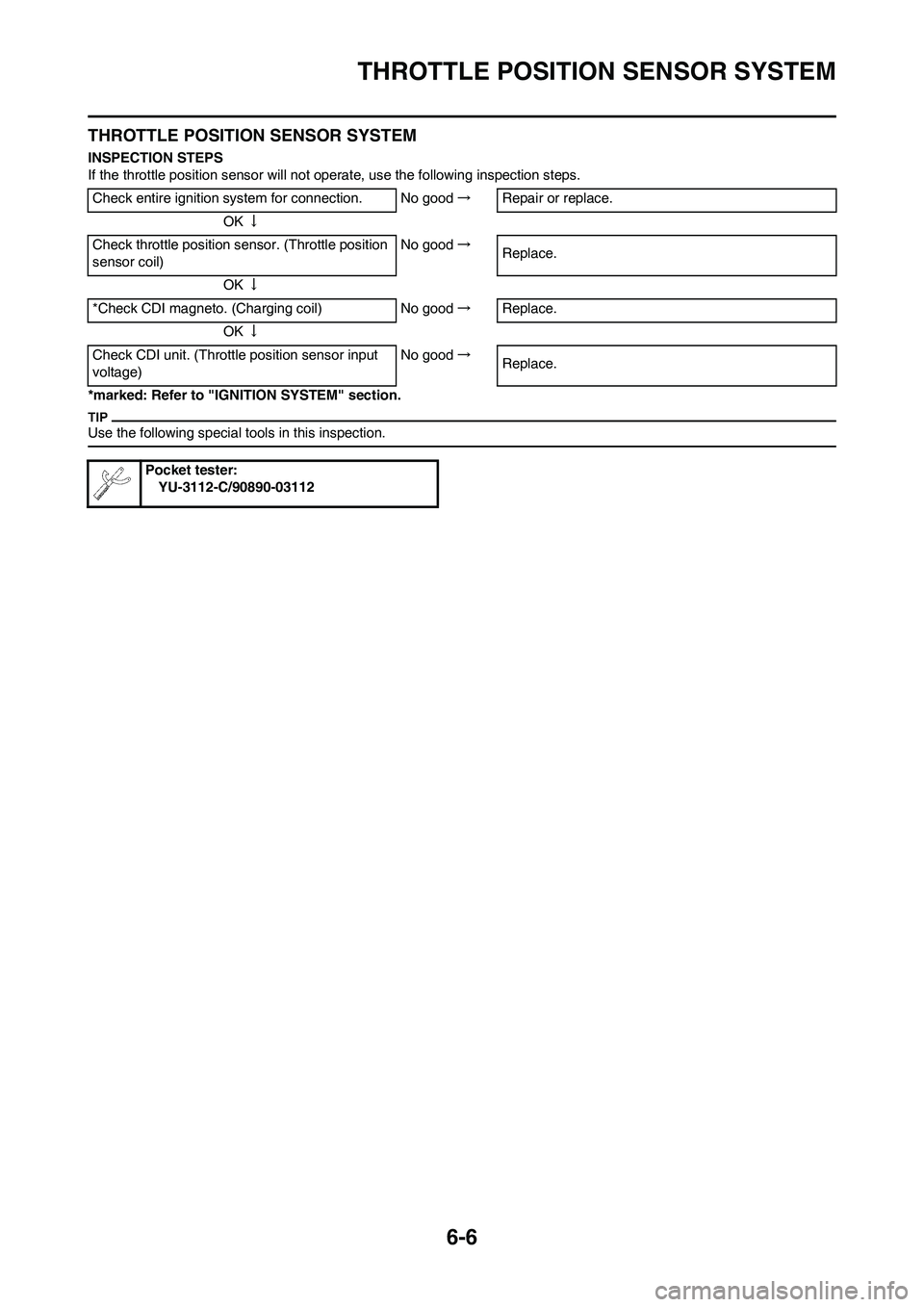
6-6
THROTTLE POSITION SENSOR SYSTEM
THROTTLE POSITION SENSOR SYSTEM
INSPECTION STEPS
If the throttle position sensor will not operate, use the following inspection steps.
*marked: Refer to "IGNITION SYSTEM" section.
Use the following special tools in this inspection.
Check entire ignition system for connection. No good→Repair or replace.
OK↓
Check throttle position sensor. (Throttle position
sensor coil)No good→
Replace.
OK↓
*Check CDI magneto. (Charging coil) No good→Replace.
OK↓
Check CDI unit. (Throttle position sensor input
voltage)No good→
Replace.
Pocket tester:
YU-3112-C/90890-03112
Page 183 of 196
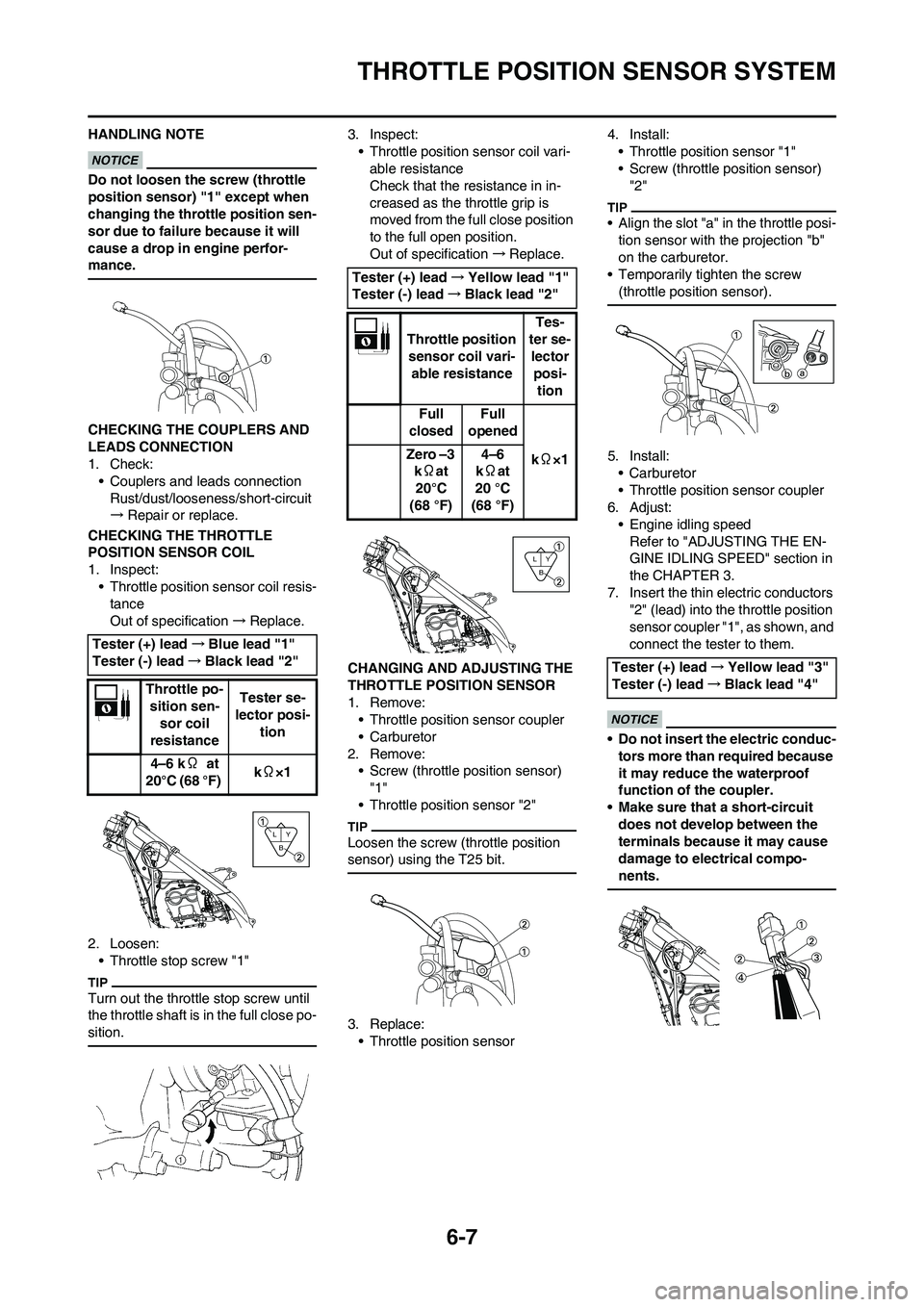
6-7
THROTTLE POSITION SENSOR SYSTEM
HANDLING NOTE
Do not loosen the screw (throttle
position sensor) "1" except when
changing the throttle position sen-
sor due to failure because it will
cause a drop in engine perfor-
mance.
CHECKING THE COUPLERS AND
LEADS CONNECTION
1. Check:
• Couplers and leads connection
Rust/dust/looseness/short-circuit
→Repair or replace.
CHECKING THE THROTTLE
POSITION SENSOR COIL
1. Inspect:
• Throttle position sensor coil resis-
tance
Out of specification→Replace.
2. Loosen:
• Throttle stop screw "1"
Turn out the throttle stop screw until
the throttle shaft is in the full close po-
sition.
3. Inspect:
• Throttle position sensor coil vari-
able resistance
Check that the resistance in in-
creased as the throttle grip is
moved from the full close position
to the full open position.
Out of specification→Replace.
CHANGING AND ADJUSTING THE
THROTTLE POSITION SENSOR
1. Remove:
• Throttle position sensor coupler
• Carburetor
2. Remove:
• Screw (throttle position sensor)
"1"
• Throttle position sensor "2"
Loosen the screw (throttle position
sensor) using the T25 bit.
3. Replace:
• Throttle position sensor4. Install:
• Throttle position sensor "1"
• Screw (throttle position sensor)
"2"
• Align the slot "a" in the throttle posi-
tion sensor with the projection "b"
on the carburetor.
• Temporarily tighten the screw
(throttle position sensor).
5. Install:
•Carburetor
• Throttle position sensor coupler
6. Adjust:
• Engine idling speed
Refer to "ADJUSTING THE EN-
GINE IDLING SPEED" section in
the CHAPTER 3.
7. Insert the thin electric conductors
"2" (lead) into the throttle position
sensor coupler "1", as shown, and
connect the tester to them.
• Do not insert the electric conduc-
tors more than required because
it may reduce the waterproof
function of the coupler.
• Make sure that a short-circuit
does not develop between the
terminals because it may cause
damage to electrical compo-
nents.
Tester (+) lead→Blue lead "1"
Tester (-) lead→Black lead "2"
Throttle po-
sition sen-
sor coil
resistanceTester se-
lector posi-
tion
4–6 kΩ at
20°C (68 °F) kΩ×1
Y
B L
Tester (+) lead→Yellow lead "1"
Tester (-) lead→Black lead "2"
Throttle position
sensor coil vari-
able resistanceTes-
ter se-
lector
posi-
tion
Full
closedFull
opened
kΩ×1 Zero –3
kΩat
20°C
(68 °F)4–6
kΩat
20 °C
(68 °F)
Y
B L
Tester (+) lead→Yellow lead "3"
Tester (-) lead→Black lead "4"
Page 184 of 196
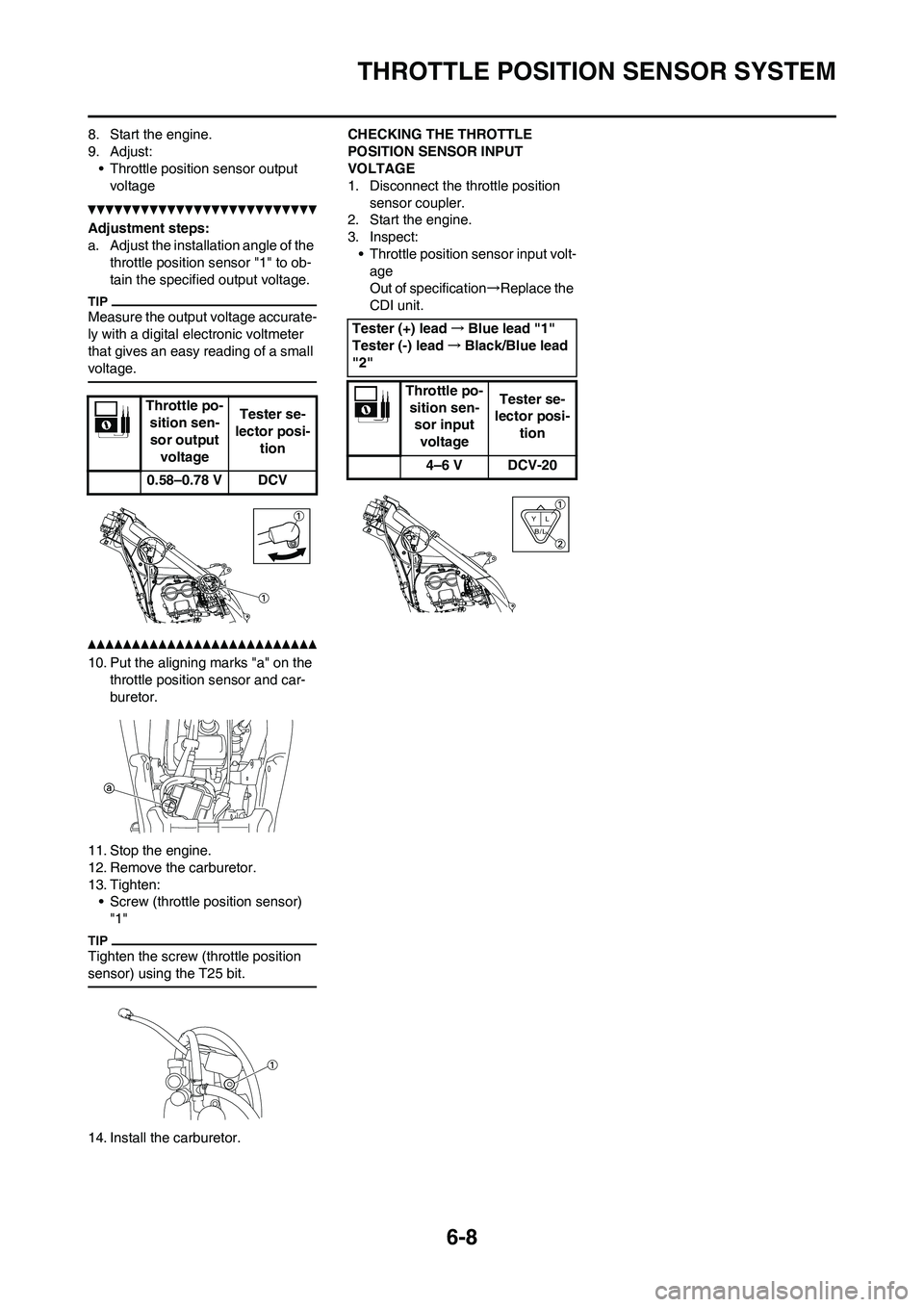
6-8
THROTTLE POSITION SENSOR SYSTEM
8. Start the engine.
9. Adjust:
• Throttle position sensor output
voltage
Adjustment steps:
a. Adjust the installation angle of the
throttle position sensor "1" to ob-
tain the specified output voltage.
Measure the output voltage accurate-
ly with a digital electronic voltmeter
that gives an easy reading of a small
voltage.
10. Put the aligning marks "a" on the
throttle position sensor and car-
buretor.
11. Stop the engine.
12. Remove the carburetor.
13. Tighten:
• Screw (throttle position sensor)
"1"
Tighten the screw (throttle position
sensor) using the T25 bit.
14. Install the carburetor.CHECKING THE THROTTLE
POSITION SENSOR INPUT
VOLTAGE
1. Disconnect the throttle position
sensor coupler.
2. Start the engine.
3. Inspect:
• Throttle position sensor input volt-
age
Out of specification→Replace the
CDI unit.
Throttle po-
sition sen-
sor output
voltageTester se-
lector posi-
tion
0.58–0.78 V DCV
Tester (+) lead→Blue lead "1"
Tester (-) lead→Black/Blue lead
"2"
Throttle po-
sition sen-
sor input
voltage Tester se-
lector posi-
tion
4–6 V DCV-20
L Y
B/L
Page 185 of 196
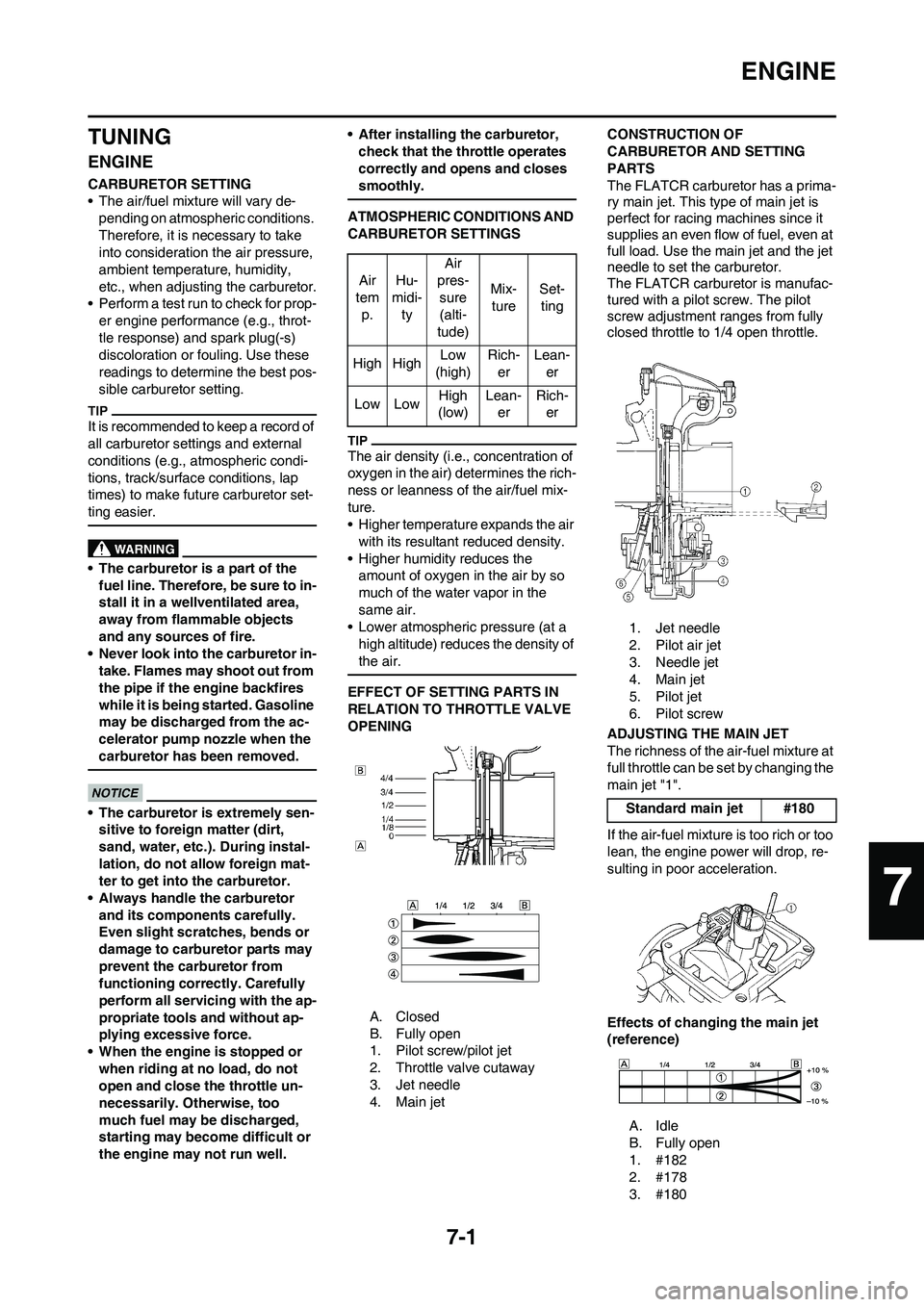
7-1
ENGINE
TUNING
ENGINE
CARBURETOR SETTING
• The air/fuel mixture will vary de-
pending on atmospheric conditions.
Therefore, it is necessary to take
into consideration the air pressure,
ambient temperature, humidity,
etc., when adjusting the carburetor.
• Perform a test run to check for prop-
er engine performance (e.g., throt-
tle response) and spark plug(-s)
discoloration or fouling. Use these
readings to determine the best pos-
sible carburetor setting.
It is recommended to keep a record of
all carburetor settings and external
conditions (e.g., atmospheric condi-
tions, track/surface conditions, lap
times) to make future carburetor set-
ting easier.
• The carburetor is a part of the
fuel line. Therefore, be sure to in-
stall it in a wellventilated area,
away from flammable objects
and any sources of fire.
• Never look into the carburetor in-
take. Flames may shoot out from
the pipe if the engine backfires
while it is being started. Gasoline
may be discharged from the ac-
celerator pump nozzle when the
carburetor has been removed.
• The carburetor is extremely sen-
sitive to foreign matter (dirt,
sand, water, etc.). During instal-
lation, do not allow foreign mat-
ter to get into the carburetor.
• Always handle the carburetor
and its components carefully.
Even slight scratches, bends or
damage to carburetor parts may
prevent the carburetor from
functioning correctly. Carefully
perform all servicing with the ap-
propriate tools and without ap-
plying excessive force.
• When the engine is stopped or
when riding at no load, do not
open and close the throttle un-
necessarily. Otherwise, too
much fuel may be discharged,
starting may become difficult or
the engine may not run well.• After installing the carburetor,
check that the throttle operates
correctly and opens and closes
smoothly.
ATMOSPHERIC CONDITIONS AND
CARBURETOR SETTINGS
The air density (i.e., concentration of
oxygen in the air) determines the rich-
ness or leanness of the air/fuel mix-
ture.
• Higher temperature expands the air
with its resultant reduced density.
• Higher humidity reduces the
amount of oxygen in the air by so
much of the water vapor in the
same air.
• Lower atmospheric pressure (at a
high altitude) reduces the density of
the air.
EFFECT OF SETTING PARTS IN
RELATION TO THROTTLE VALVE
OPENING
A. Closed
B. Fully open
1. Pilot screw/pilot jet
2. Throttle valve cutaway
3. Jet needle
4. Main jetCONSTRUCTION OF
CARBURETOR AND SETTING
PARTS
The FLATCR carburetor has a prima-
ry main jet. This type of main jet is
perfect for racing machines since it
supplies an even flow of fuel, even at
full load. Use the main jet and the jet
needle to set the carburetor.
The FLATCR carburetor is manufac-
tured with a pilot screw. The pilot
screw adjustment ranges from fully
closed throttle to 1/4 open throttle.
1. Jet needle
2. Pilot air jet
3. Needle jet
4. Main jet
5. Pilot jet
6. Pilot screw
ADJUSTING THE MAIN JET
The richness of the air-fuel mixture at
full throttle can be set by changing the
main jet "1".
If the air-fuel mixture is too rich or too
lean, the engine power will drop, re-
sulting in poor acceleration.
Effects of changing the main jet
(reference)
A. Idle
B. Fully open
1. #182
2. #178
3. #180 Air
tem
p.Hu-
midi-
tyAir
pres-
sure
(alti-
tude)Mix-
tureSet-
ting
High HighLow
(high)Rich-
erLean-
er
Low LowHigh
(low)Lean-
erRich-
er
Standard main jet #180
7
Page 186 of 196
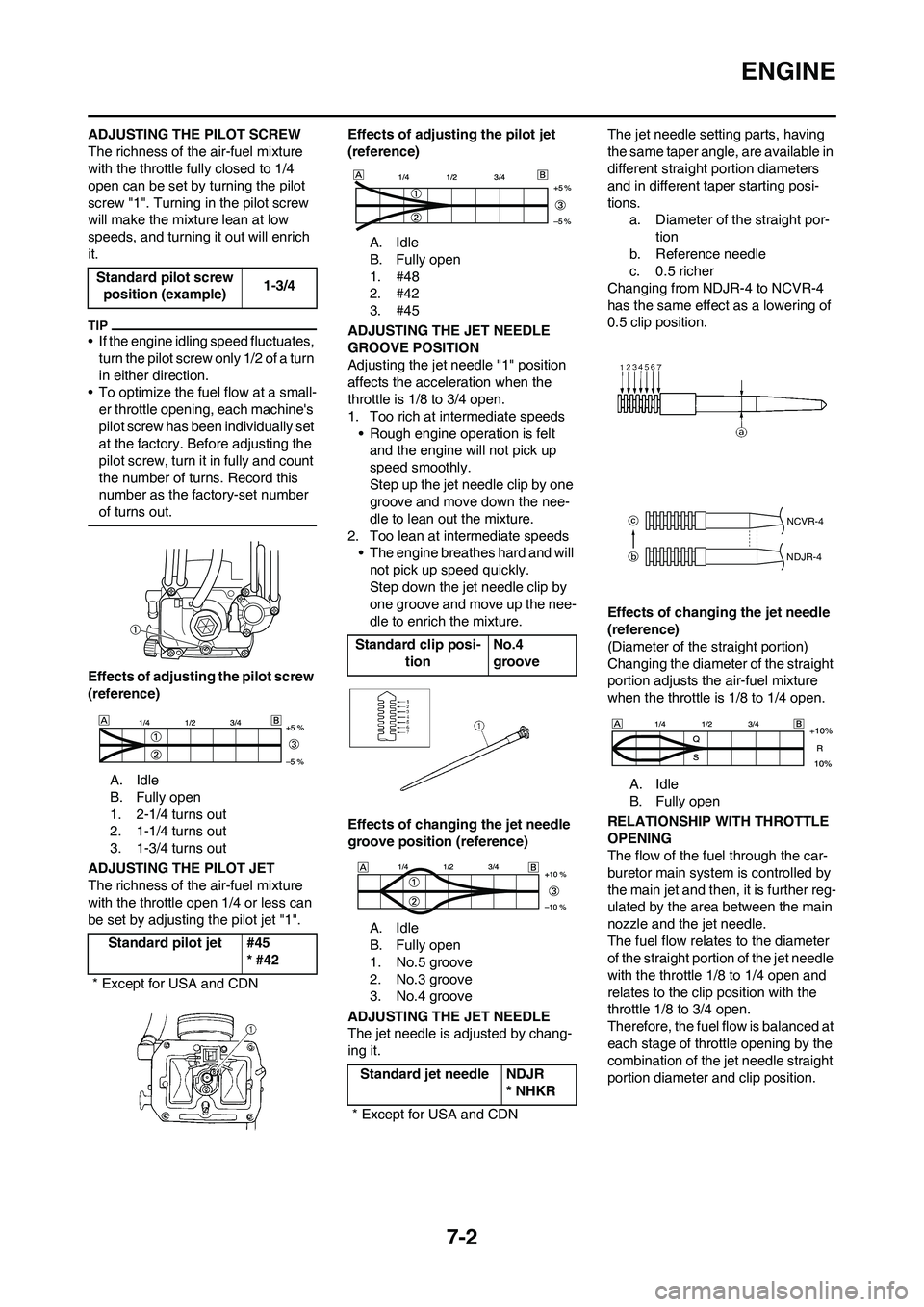
7-2
ENGINE
ADJUSTING THE PILOT SCREW
The richness of the air-fuel mixture
with the throttle fully closed to 1/4
open can be set by turning the pilot
screw "1". Turning in the pilot screw
will make the mixture lean at low
speeds, and turning it out will enrich
it.
• If the engine idling speed fluctuates, turn the pilot screw only 1/2 of a turn
in either direction.
• To optimize the fuel flow at a small- er throttle opening, each machine's
pilot screw has been individually set
at the factory. Before adjusting the
pilot screw, turn it in fully and count
the number of turns. Record this
number as the factory-set number
of turns out.
Effects of adjusting the pilot screw
(reference)
A. Idle
B. Fully open
1. 2-1/4 turns out
2. 1-1/4 turns out
3. 1-3/4 turns out
ADJUSTING THE PILOT JET
The richness of the air-fuel mixture
with the throttle open 1/4 or less can
be set by adjusting the pilot jet "1". Effects of adjusting the pilot jet
(reference)
A. Idle
B. Fully open
1. #48
2. #42
3. #45
ADJUSTING THE JET NEEDLE
GROOVE POSITION
Adjusting the jet needle "1" position
affects the acceleration when the
throttle is 1/8 to 3/4 open.
1. Too rich at intermediate speeds • Rough engine operation is felt and the engine will not pick up
speed smoothly.
Step up the jet needle clip by one
groove and move down the nee-
dle to lean out the mixture.
2. Too lean at intermediate speeds • The engine breathes hard and will not pick up speed quickly.
Step down the jet needle clip by
one groove and move up the nee-
dle to enrich the mixture.
Effects of changing the jet needle
groove position (reference) A. Idle
B. Fully open
1. No.5 groove
2. No.3 groove
3. No.4 groove
ADJUSTING THE JET NEEDLE
The jet needle is adjusted by chang-
ing it. The jet needle setting parts, having
the same taper angle, are available in
different straight portion diameters
and in different taper starting posi-
tions.
a. Diameter of t he straight por-
tion
b. Reference needle
c. 0.5 richer
Changing from NDJR-4 to NCVR-4
has the same effect as a lowering of
0.5 clip position.
Effects of changing the jet needle
(reference)
(Diameter of the straight portion)
Changing the diameter of the straight
portion adjusts the air-fuel mixture
when the throttle is 1/8 to 1/4 open.
A. Idle
B. Fully open
RELATIONSHIP WITH THROTTLE
OPENING
The flow of the fuel through the car-
buretor main system is controlled by
the main jet and then, it is further reg-
ulated by the area between the main
nozzle and the jet needle.
The fuel flow relates to the diameter
of the straight portion of the jet needle
with the throttle 1/8 to 1/4 open and
relates to the clip position with the
throttle 1/8 to 3/4 open.
Therefore, the fuel flow is balanced at
each stage of throttle opening by the
combination of the jet needle straight
portion diameter and clip position.
Standard pilot screw
position (example) 1-3/4
Standard pilot jet #45 * #42
* Except for USA and CDN
Standard clip posi- tion No.4
groove
Standard jet needle NDJR * NHKR
* Except for USA and CDN
NCVR-4
NDJR-4
Page 187 of 196
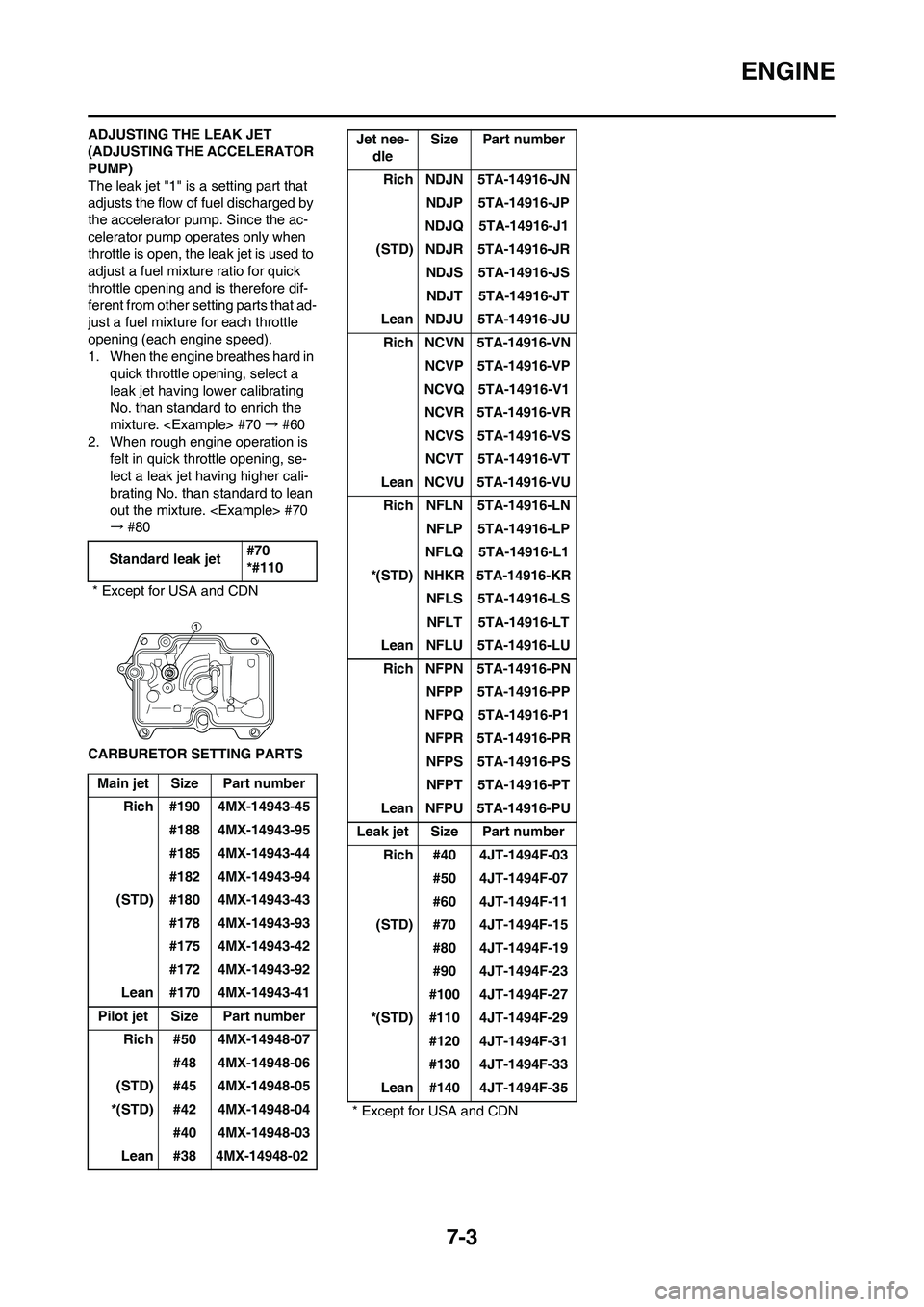
7-3
ENGINE
ADJUSTING THE LEAK JET
(ADJUSTING THE ACCELERATOR
PUMP)
The leak jet "1" is a setting part that
adjusts the flow of fuel discharged by
the accelerator pump. Since the ac-
celerator pump operates only when
throttle is open, the leak jet is used to
adjust a fuel mixture ratio for quick
throttle opening and is therefore dif-
ferent from other setting parts that ad-
just a fuel mixture for each throttle
opening (each engine speed).
1. When the engine breathes hard in
quick throttle opening, select a
leak jet having lower calibrating
No. than standard to enrich the
mixture.
2. When rough engine operation is
felt in quick throttle opening, se-
lect a leak jet having higher cali-
brating No. than standard to lean
out the mixture.
→#80
CARBURETOR SETTING PARTSStandard leak jet#70
*#110
* Except for USA and CDN
Main jet Size Part number
Rich #190 4MX-14943-45
#188 4MX-14943-95
#185 4MX-14943-44
#182 4MX-14943-94
(STD) #180 4MX-14943-43
#178 4MX-14943-93
#175 4MX-14943-42
#172 4MX-14943-92
Lean #170 4MX-14943-41
Pilot jet Size Part number
Rich #50 4MX-14948-07
#48 4MX-14948-06
(STD) #45 4MX-14948-05
*(STD) #42 4MX-14948-04
#40 4MX-14948-03
Lean #38 4MX-14948-02Jet nee-
dleSize Part number
Rich NDJN 5TA-14916-JN
NDJP 5TA-14916-JP
NDJQ 5TA-14916-J1
(STD) NDJR 5TA-14916-JR
NDJS 5TA-14916-JS
NDJT 5TA-14916-JT
Lean NDJU 5TA-14916-JU
Rich NCVN 5TA-14916-VN
NCVP 5TA-14916-VP
NCVQ 5TA-14916-V1
NCVR 5TA-14916-VR
NCVS 5TA-14916-VS
NCVT 5TA-14916-VT
Lean NCVU 5TA-14916-VU
Rich NFLN 5TA-14916-LN
NFLP 5TA-14916-LP
NFLQ 5TA-14916-L1
*(STD) NHKR 5TA-14916-KR
NFLS 5TA-14916-LS
NFLT 5TA-14916-LT
Lean NFLU 5TA-14916-LU
Rich NFPN 5TA-14916-PN
NFPP 5TA-14916-PP
NFPQ 5TA-14916-P1
NFPR 5TA-14916-PR
NFPS 5TA-14916-PS
NFPT 5TA-14916-PT
Lean NFPU 5TA-14916-PU
Leak jet Size Part number
Rich #40 4JT-1494F-03
#50 4JT-1494F-07
#60 4JT-1494F-11
(STD) #70 4JT-1494F-15
#80 4JT-1494F-19
#90 4JT-1494F-23
#100 4JT-1494F-27
*(STD) #110 4JT-1494F-29
#120 4JT-1494F-31
#130 4JT-1494F-33
Lean #140 4JT-1494F-35
* Except for USA and CDN
Page 188 of 196
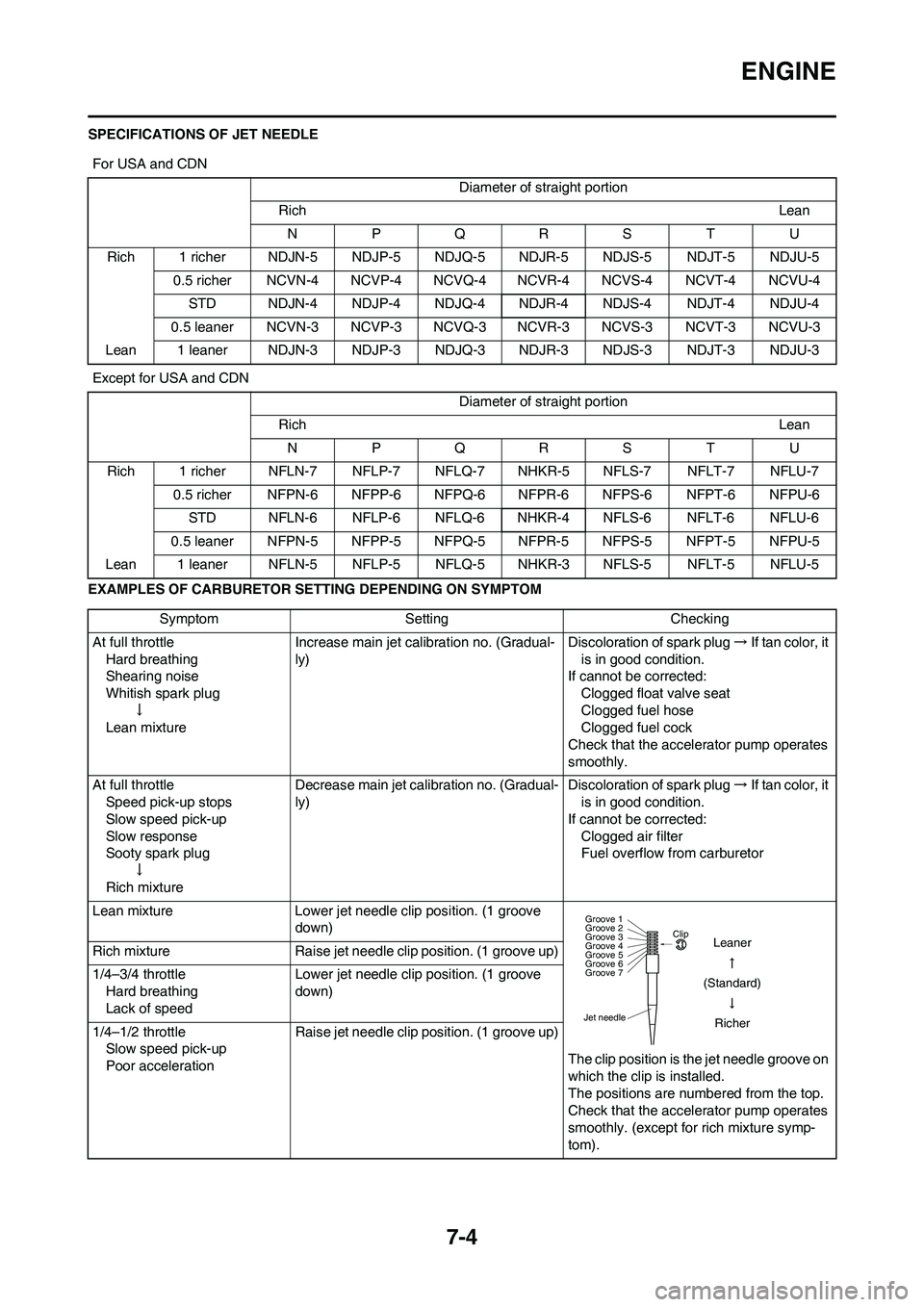
7-4
ENGINE
SPECIFICATIONS OF JET NEEDLE
EXAMPLES OF CARBURETOR SETTING DEPENDING ON SYMPTOMFor USA and CDN
Diameter of straight portion
RichLean
NPQRS TU
Rich 1 richer NDJN-5 NDJP-5 NDJQ-5 NDJR-5 NDJS-5 NDJT-5 NDJU-5
0.5 richer NCVN-4 NCVP-4 NCVQ-4 NCVR-4 NCVS-4 NCVT-4 NCVU-4
STD NDJN-4 NDJP-4 NDJQ-4 NDJR-4 NDJS-4 NDJT-4 NDJU-4
0.5 leaner NCVN-3 NCVP-3 NCVQ-3 NCVR-3 NCVS-3 NCVT-3 NCVU-3
Lean 1 leaner NDJN-3 NDJP-3 NDJQ-3 NDJR-3 NDJS-3 NDJT-3 NDJU-3
Except for USA and CDN
Diameter of straight portion
RichLean
NPQRS TU
Rich 1 richer NFLN-7 NFLP-7 NFLQ-7 NHKR-5 NFLS-7 NFLT-7 NFLU-7
0.5 richer NFPN-6 NFPP-6 NFPQ-6 NFPR-6 NFPS-6 NFPT-6 NFPU-6
STD NFLN-6 NFLP-6 NFLQ-6 NHKR-4 NFLS-6 NFLT-6 NFLU-6
0.5 leaner NFPN-5 NFPP-5 NFPQ-5 NFPR-5 NFPS-5 NFPT-5 NFPU-5
Lean 1 leaner NFLN-5 NFLP-5 NFLQ-5 NHKR-3 NFLS-5 NFLT-5 NFLU-5
Symptom Setting Checking
At full throttle
Hard breathing
Shearing noise
Whitish spark plug
↓
Lean mixtureIncrease main jet calibration no. (Gradual-
ly)Discoloration of spark plug→If tan color, it
is in good condition.
If cannot be corrected:
Clogged float valve seat
Clogged fuel hose
Clogged fuel cock
Check that the accelerator pump operates
smoothly.
At full throttle
Speed pick-up stops
Slow speed pick-up
Slow response
Sooty spark plug
↓
Rich mixtureDecrease main jet calibration no. (Gradual-
ly)Discoloration of spark plug→If tan color, it
is in good condition.
If cannot be corrected:
Clogged air filter
Fuel overflow from carburetor
Lean mixture Lower jet needle clip position. (1 groove
down)
The clip position is the jet needle groove on
which the clip is installed.
The positions are numbered from the top.
Check that the accelerator pump operates
smoothly. (except for rich mixture symp-
tom). Rich mixture Raise jet needle clip position. (1 groove up)
1/4–3/4 throttle
Hard breathing
Lack of speedLower jet needle clip position. (1 groove
down)
1/4–1/2 throttle
Slow speed pick-up
Poor accelerationRaise jet needle clip position. (1 groove up)
Jet needleClip
Groove 7 Groove 6
Groove 5
Groove 4
Groove 3
Groove 2
Groove 1
Leaner
(Standard)
Richer
Page 189 of 196
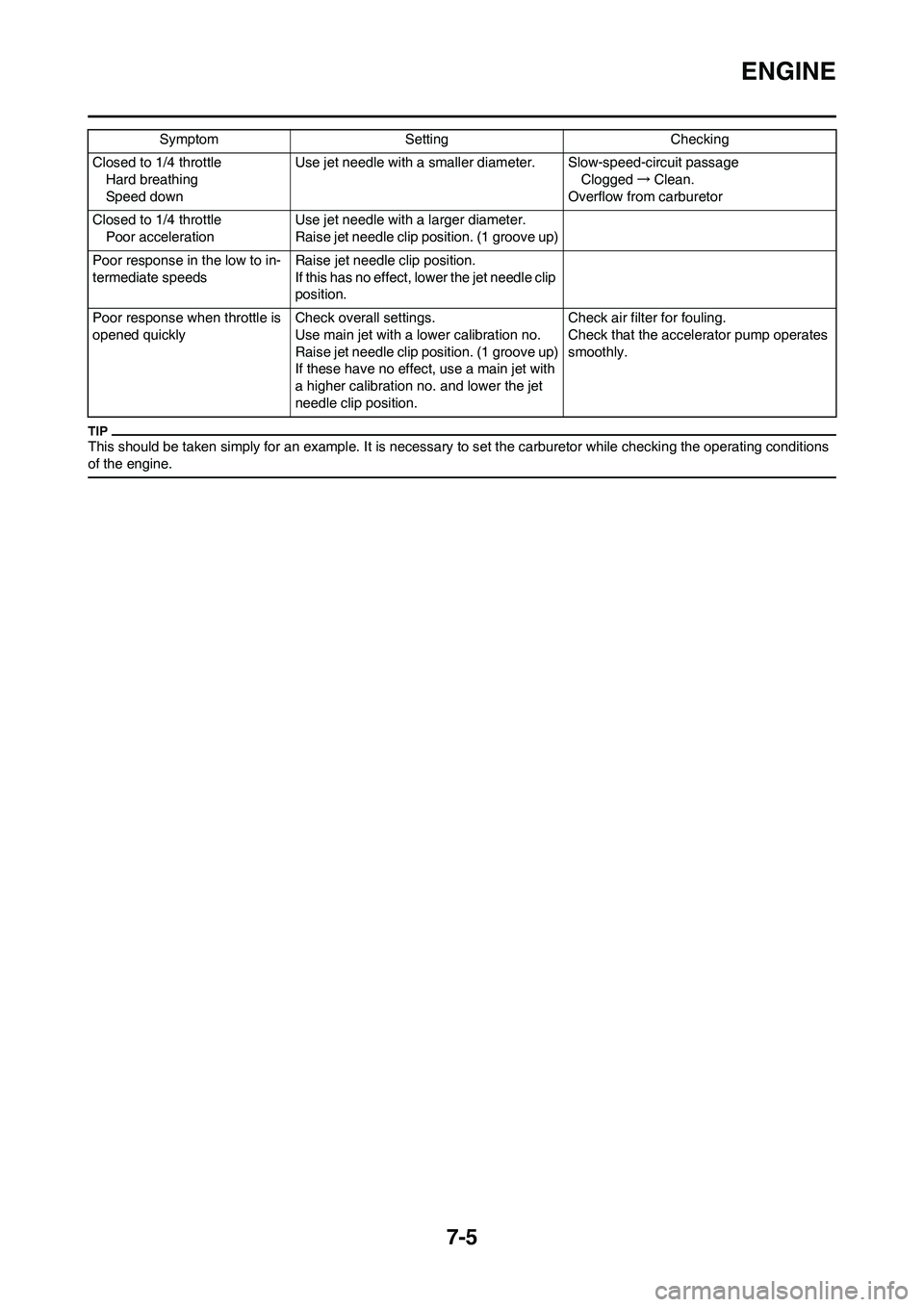
7-5
ENGINE
This should be taken simply for an example. It is necessary to set the carburetor while checking the operating conditions
of the engine.
Closed to 1/4 throttle
Hard breathing
Speed downUse jet needle with a smaller diameter. Slow-speed-circuit passage
Clogged→Clean.
Overflow from carburetor
Closed to 1/4 throttle
Poor accelerationUse jet needle with a larger diameter.
Raise jet needle clip position. (1 groove up)
Poor response in the low to in-
termediate speedsRaise jet needle clip position.
If this has no effect, lower the jet needle clip
position.
Poor response when throttle is
opened quicklyCheck overall settings.
Use main jet with a lower calibration no.
Raise jet needle clip position. (1 groove up)
If these have no effect, use a main jet with
a higher calibration no. and lower the jet
needle clip position.Check air filter for fouling.
Check that the accelerator pump operates
smoothly. Symptom Setting Checking
Page 190 of 196
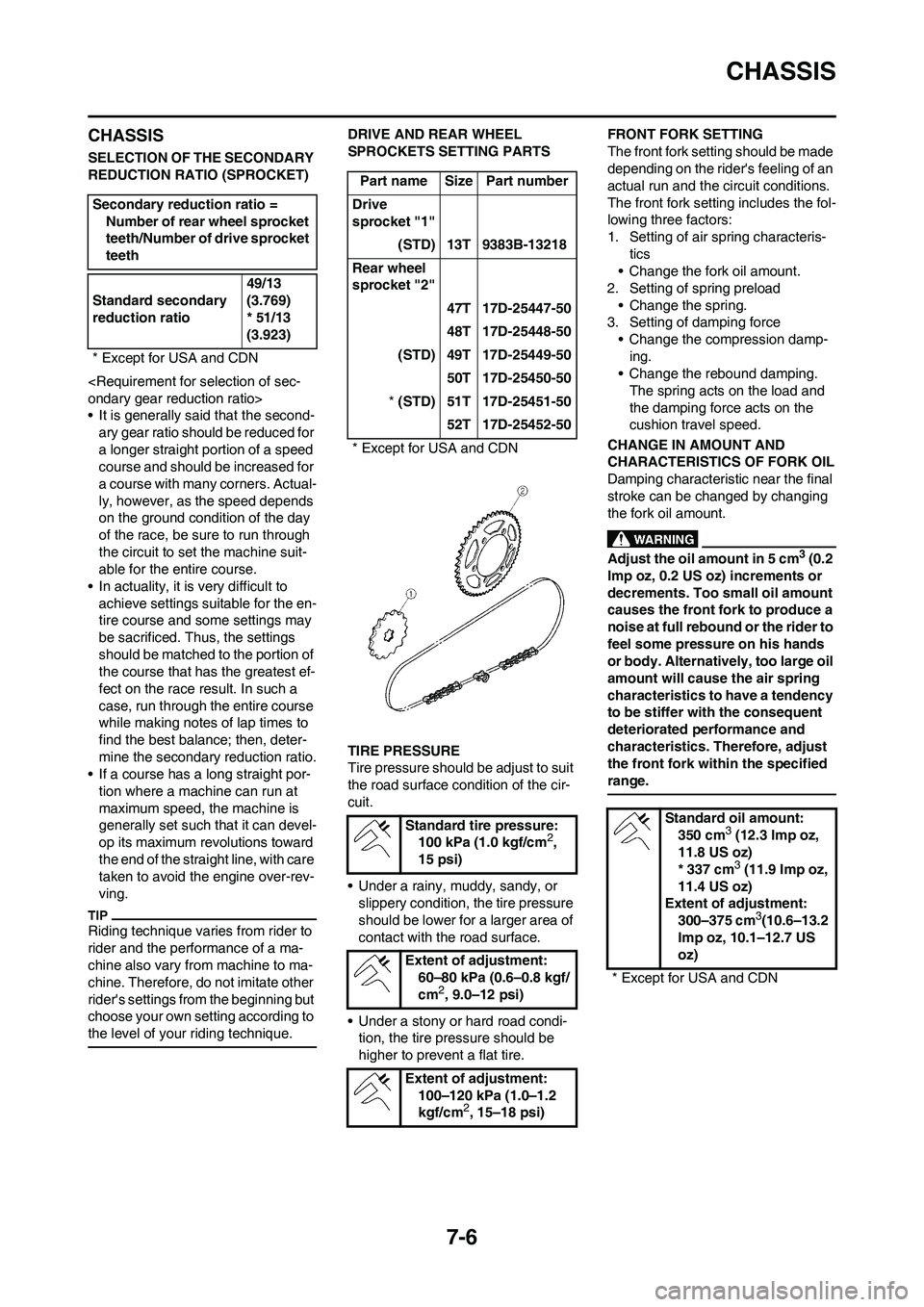
7-6
CHASSIS
CHASSIS
SELECTION OF THE SECONDARY
REDUCTION RATIO (SPROCKET)
• It is generally said that the second-
ary gear ratio should be reduced for
a longer straight portion of a speed
course and should be increased for
a course with many corners. Actual-
ly, however, as the speed depends
on the ground condition of the day
of the race, be sure to run through
the circuit to set the machine suit-
able for the entire course.
• In actuality, it is very difficult to
achieve settings suitable for the en-
tire course and some settings may
be sacrificed. Thus, the settings
should be matched to the portion of
the course that has the greatest ef-
fect on the race result. In such a
case, run through the entire course
while making notes of lap times to
find the best balance; then, deter-
mine the secondary reduction ratio.
• If a course has a long straight por-
tion where a machine can run at
maximum speed, the machine is
generally set such that it can devel-
op its maximum revolutions toward
the end of the straight line, with care
taken to avoid the engine over-rev-
ving.
Riding technique varies from rider to
rider and the performance of a ma-
chine also vary from machine to ma-
chine. Therefore, do not imitate other
rider's settings from the beginning but
choose your own setting according to
the level of your riding technique.
DRIVE AND REAR WHEEL
SPROCKETS SETTING PARTS
TIRE PRESSURE
Tire pressure should be adjust to suit
the road surface condition of the cir-
cuit.
• Under a rainy, muddy, sandy, or
slippery condition, the tire pressure
should be lower for a larger area of
contact with the road surface.
• Under a stony or hard road condi-
tion, the tire pressure should be
higher to prevent a flat tire.FRONT FORK SETTING
The front fork setting should be made
depending on the rider's feeling of an
actual run and the circuit conditions.
The front fork setting includes the fol-
lowing three factors:
1. Setting of air spring characteris-
tics
• Change the fork oil amount.
2. Setting of spring preload
• Change the spring.
3. Setting of damping force
• Change the compression damp-
ing.
• Change the rebound damping.
The spring acts on the load and
the damping force acts on the
cushion travel speed.
CHANGE IN AMOUNT AND
CHARACTERISTICS OF FORK OIL
Damping characteristic near the final
stroke can be changed by changing
the fork oil amount.
Adjust the oil amount in 5 cm3 (0.2
Imp oz, 0.2 US oz) increments or
decrements. Too small oil amount
causes the front fork to produce a
noise at full rebound or the rider to
feel some pressure on his hands
or body. Alternatively, too large oil
amount will cause the air spring
characteristics to have a tendency
to be stiffer with the consequent
deteriorated performance and
characteristics. Therefore, adjust
the front fork within the specified
range.
Secondary reduction ratio =
Number of rear wheel sprocket
teeth/Number of drive sprocket
teeth
Standard secondary
reduction ratio49/13
(3.769)
* 51/13
(3.923)
* Except for USA and CDN
Part name Size Part number
Drive
sprocket "1"
(STD) 13T 9383B-13218
Rear wheel
sprocket "2"
47T 17D-25447-50
48T 17D-25448-50
(STD) 49T 17D-25449-50
50T 17D-25450-50
* (STD) 51T 17D-25451-50
52T 17D-25452-50
* Except for USA and CDN
Standard tire pressure:
100 kPa (1.0 kgf/cm
2,
15 psi)
Extent of adjustment:
60–80 kPa (0.6–0.8 kgf/
cm
2, 9.0–12 psi)
Extent of adjustment:
100–120 kPa (1.0–1.2
kgf/cm
2, 15–18 psi)
Standard oil amount:
350 cm3 (12.3 Imp oz,
11.8 US oz)
* 337 cm
3 (11.9 Imp oz,
11.4 US oz)
Extent of adjustment:
300–375 cm
3(10.6–13.2
Imp oz, 10.1–12.7 US
oz)
* Except for USA and CDN