oil capacity ASTON MARTIN DB7 1997 Workshop Manual
[x] Cancel search | Manufacturer: ASTON MARTIN, Model Year: 1997, Model line: DB7, Model: ASTON MARTIN DB7 1997Pages: 421, PDF Size: 9.31 MB
Page 4 of 421
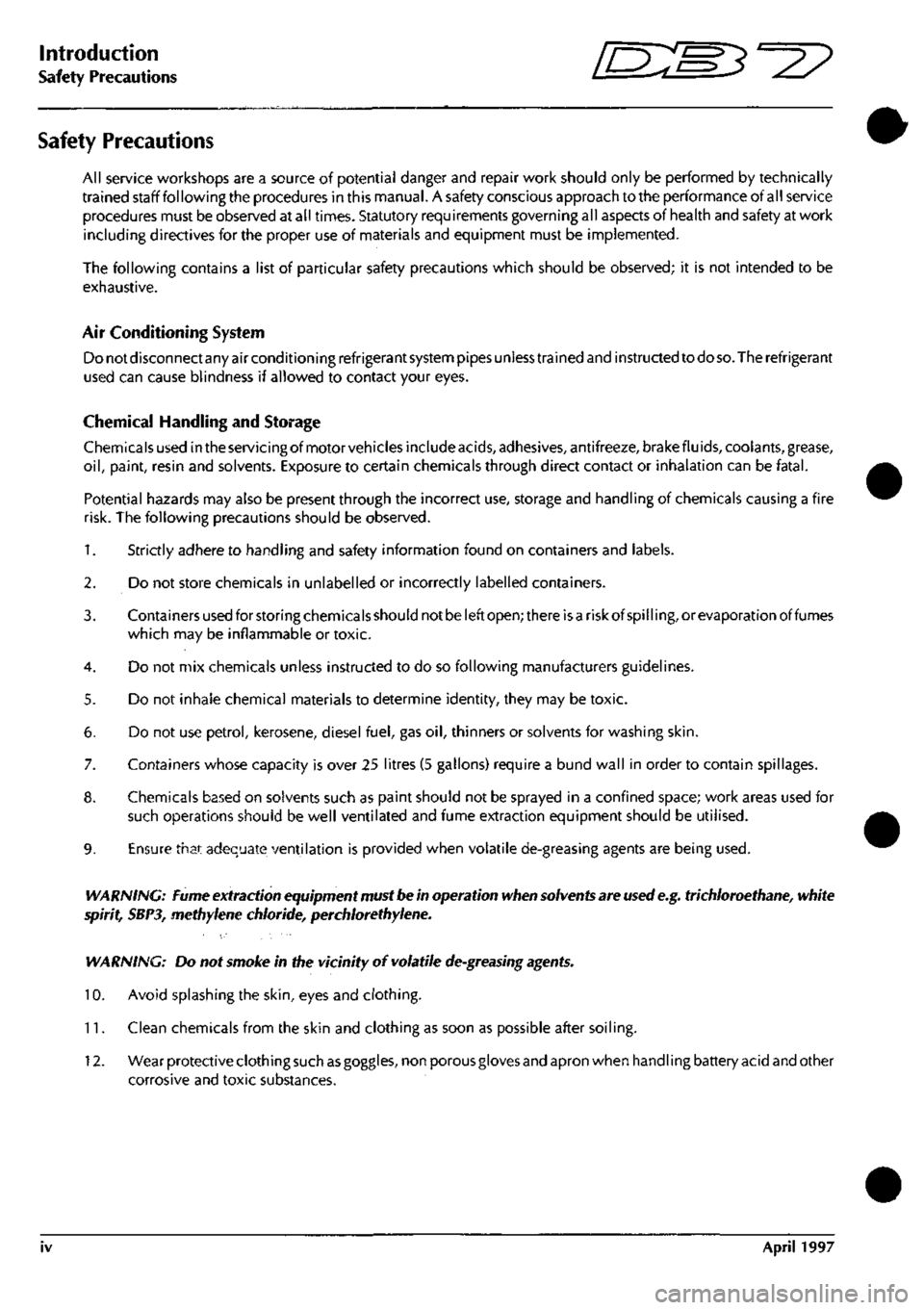
Introduction
/^r"^^^^^3^
'"'P ?
Safety Precautions L —^ ^^—^
Safety Precautions "
All service workshops are a source of potential danger and repair work should only be performed by technically
trained staff following the procedures in this manual. A safety conscious approach to the performance of all service
procedures must be observed at all times. Statutory requirements governing all aspects of health and safety at work
including directives for the proper use of materials and equipment must be implemented.
The following contains a list of particular safety precautions which should be observed; it is not intended to be
exhaustive.
Air Conditioning System
Do not disconnect any air conditioning refrigerant system pipes unless trained and instructed to do
so.
The refrigerant
used can cause blindness if allowed to contact your eyes.
Chemical Handling and Storage
Chemicalsusedintheservicingofmotorvehiclesincludeacids,adhesives, antifreeze, brake fluids, coolants, grease,
oil,
paint, resin and solvents. Exposure to certain chemicals through direct contact or inhalation can be
fatal.
Potential hazards may also be present through the incorrect use, storage and handling of chemicals causing a fire
risk. The following precautions should be observed.
1.
Strictly adhere to handling and safety information found on containers and labels.
2.
Do not store chemicals in unlabelled or incorrectly labelled containers.
3. Containers used for storing chemicals should not be left
open;
there is a risk of
spilling,
or evaporation of fumes
which may be inflammable or toxic.
4.
Do not mix chemicals unless instructed to do so following manufacturers guidelines.
5. Do not inhale chemical materials to determine identity, they may be toxic.
6. Do not use petrol, kerosene, diesel
fuel,
gas oil, thinners or solvents for washing
skin.
7. Containers whose capacity is over 25 litres (5 gallons) require a bund wall in order to contain spillages.
8. Chemicals based on solvents such as paint should not be sprayed in a confined space; work areas used for
such operations should be well ventilated and fume extraction equipment should be utilised.
9. Ensure that adequate ventilation is provided when volatile de-greasing agents are being used.
WARNING: Fume extraction equipment must be in operation when
solvents
are
used
e.g.
trichloroethane, white
spirit, SBP3, methylene chloride, perchlorethylene.
WARNING: Do not smoke in the vicinity of volatile de-greasing agents.
10.
Avoid splashing the
skin,
eyes and clothing.
11.
Clean chemicals from the skin and clothing as soon as possible after soiling.
12.
Wear protective clothing such as goggles, non porous gloves and apron when hand
I
ing battery acid and other
corrosive and toxic substances.
iv April 1997
Page 5 of 421
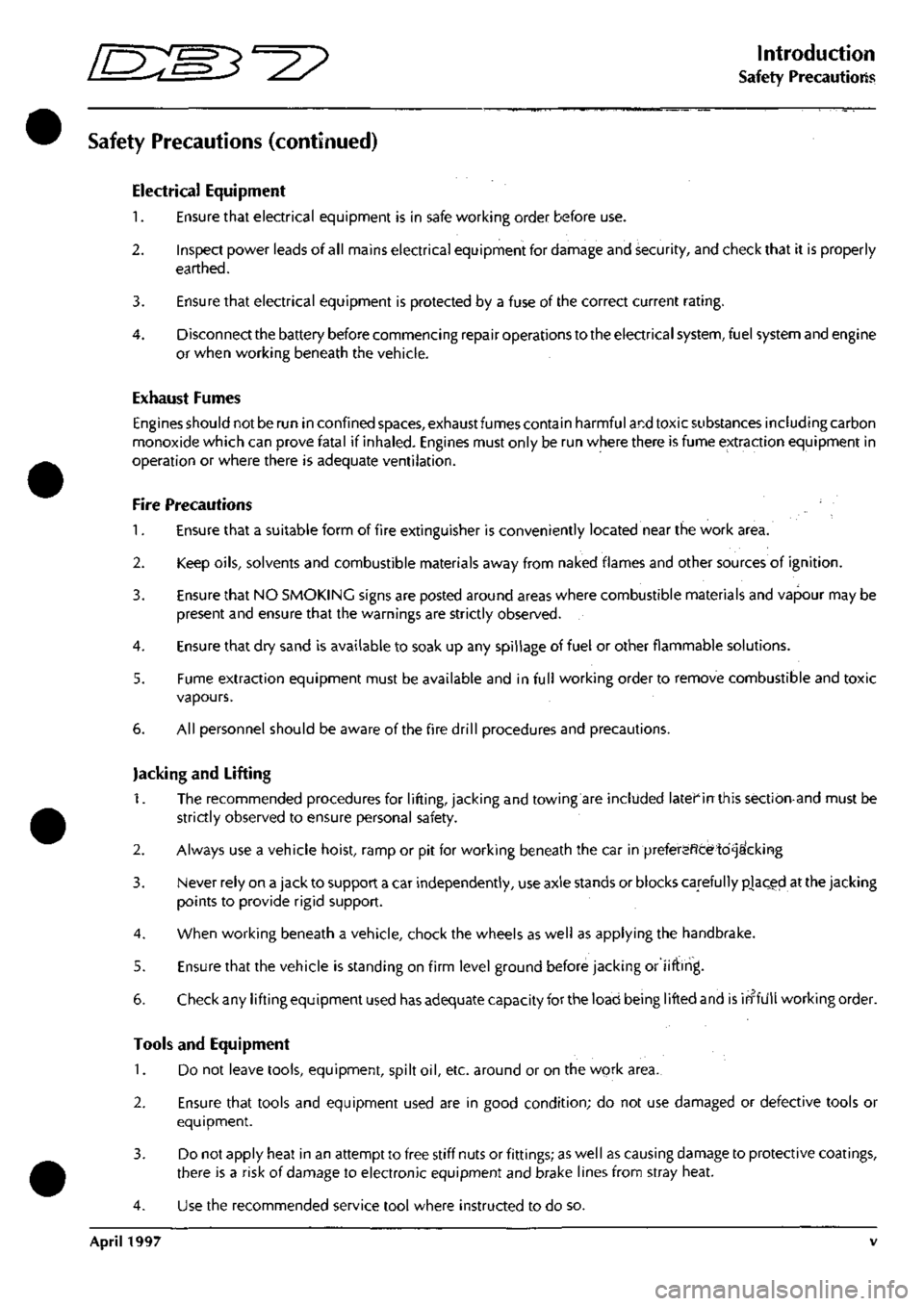
//—-^
^^^^5~^
' -^ ^ Introduction
Safety Precautions
Safety Precautions (continued)
Electrical Equipment
1.
Ensure that electrical equipment is in safe working order before use.
2.
Inspect power leads of all mains electrical equipment for damage and security, and check that it is properly
earthed.
3. Ensure that electrical equipment is protected by a fuse of the correct current rating.
4.
Disconnect the battery before commencing repair operations to the electrical system, fuel system and engine
or when working beneath the vehicle.
Exhaust Fumes
Engines should not be run in confined spaces, exhaust fumes contain harmful and toxic substances including carbon
monoxide which can prove fatal if inhaled. Engines must only be run where there is fume extraction equipment in
operation or where there is adequate ventilation.
Fire Precautions
1.
Ensure that a suitable form of fire extinguisher is conveniently located near the work area.
2.
Keep oils, solvents and combustible materials away from naked flames and other sources of ignition.
3. Ensure that NO SMOKING signs are posted around areas where combustible materials and vapour may be
present and ensure that the warnings are strictly observed.
4.
Ensure that dry sand is available to soak up any spillage of fuel or other flammable solutions.
5. Fume extraction equipment must be available and in full working order to remove combustible and toxic
vapours.
6. All personnel should be aware of the fire drill procedures and precautions.
Jacking and Lifting
1.
The recommended procedures for lifting, jacking and towing are included latefin this seetion-and must be
strictly observed to ensure personal safety.
2.
Always use a vehicle hoist, ramp or pit for working beneath the car in preferencetd^&^cking
3. Never rely on a jack to support a car independently, use axle stands or blocks carefully pJaQed at the jacking
points to provide rigid support.
4.
When working beneath a vehicle, chock the wheels as well as applying the handbrake.
5. Ensure that the vehicle is standing on firm level ground before jacking or lifting.
5. Check any lifting equipment used has adequate capacity for the load being lifted and is ih"fdll working order.
Tools and Equipment
1.
Do not leave tools, equipment, spilt oil, etc. around or on the work area.
2.
Ensure that tools and equipment used are in good condition; do not use damaged or defective tools or
equipment.
3. Do not apply heat in an attempt to free stiff nuts or fittings; as well as causing damage to protective coatings,
there is a risk of damage to electronic equipment and brake lines from stray heat.
4.
Use the recommended service tool where instructed to do so.
April 1997 v
Page 282 of 421
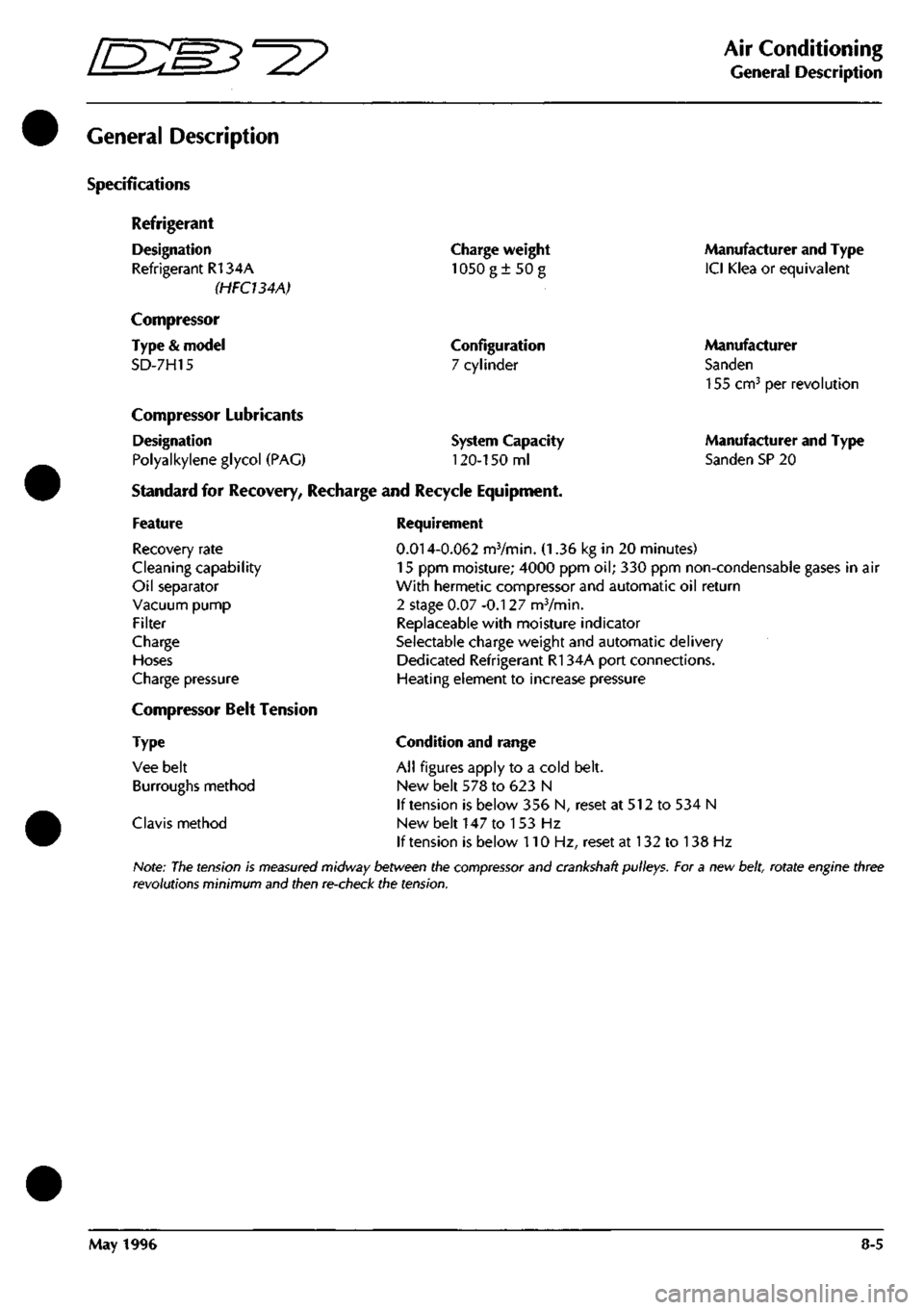
Em^^^?
Air Conditioning
General Description
General Description
Specifications
Refrigerant
Designation
Refrigerant R134A
(HFCUAA)
Compressor
Type
&
model
SD-7H15
Charge weight
1050g±50g
Configuration
7 cylinder
Compressor Lubricants
Designation
Polyalkylene glycol
(PAG)
Standard
for
Recovery, Recharge
and
Recycle Equipment,
System Capacity
120-150
ml
Manufacturer and Type
ICI Klea
or
equivalent
Manufacturer
Sanden
155 cm^
per
revolution
Manufacturer and Type
Sanden SP
20
Feature
Recovery rate
Cleaning capability
Oil separator
Vacuum pump
Filter
Charge
Hoses
Charge pressure
Compressor Belt Tension
Type
Vee belt
Burroughs method
Clavis method
Requirement
0.014-0.062
mVmin.
(1.36 kg in 20
minutes)
15
ppm
moisture; 4000
ppm oil; 330 ppm
non-condensable gases
in air
With hermetic compressor and automatic
oil
return
2 stage
0.07
-0.127 mVmin.
Replaceable with moisture indicator
Selectable charge weight and automatic delivery
Dedicated Refrigerant R134A port connections.
Heating element
to
increase pressure
Condition and range
All figures apply
to a
cold belt.
New belt
578 to 623 N
If tension
is
below
356 N,
reset
at 512 to 534 N
New belt
147 to 153 Hz
If tension
is
below
110 Hz,
reset
at 132 to 138 Hz
Note:
The
tension
is
measured
midway between the
compressor
and crankshaft pulleys. For a new
belt,
rotate engine three
revolutions minimum and then re-check the tension.
May 1996
8-5
Page 290 of 421
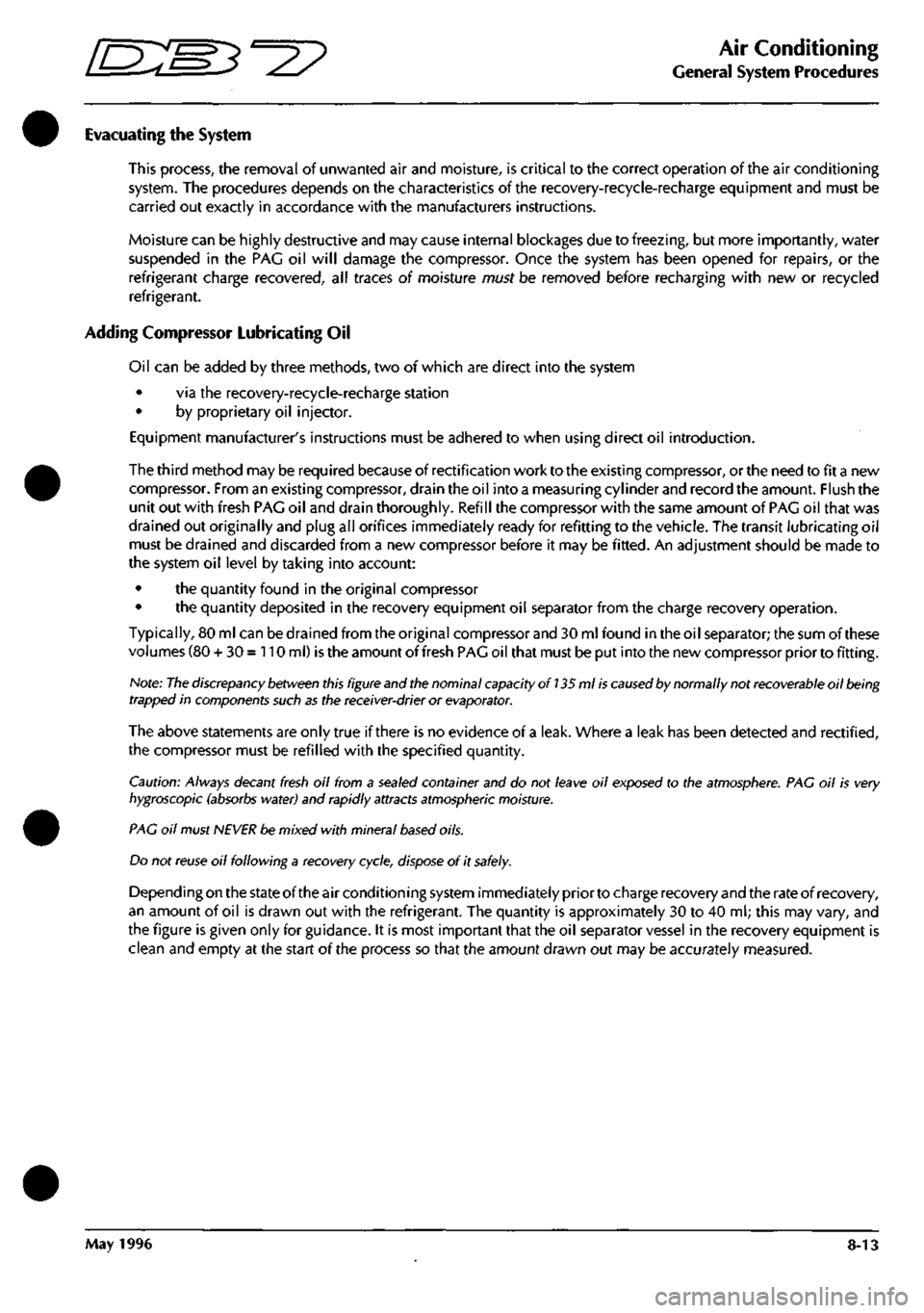
^2?
Air Conditioning
General System Procedures
Evacuating the System
This process, the removal of unwanted air and moisture, is critical to the correct operation of the air conditioning
system.
The procedures depends on the characteristics of the recovery-recycle-recharge equipment and must be
carried out exactly in accordance with the manufacturers instructions.
Moisture can be highly destructive and may cause internal blockages due to freezing, but more importantly, water
suspended in the PAG oil will damage the compressor. Once the system has been opened for repairs, or the
refrigerant charge recovered, all traces oi moisture must be removed before recharging with new or recycled
refrigerant.
Adding Compressor Lubricating Oil
Oil can be added by three methods, two of which are direct into the system
• via the recovery-recycle-recharge station
• by proprietary oil injector.
Equipment manufacturer's instructions must be adhered to when using direct oil introduction.
The third method may be required because of rectification work to the existing compressor, or the need to fit a new
compressor. From an existing compressor, drain the oil into a measuring cylinder and record the amount. Flush the
unit out with fresh PAG oil and drain thoroughly. Refill the compressor with the same amount of PAG oil that was
drained out originally and plug all orifices immediately ready for refitting to the vehicle. The transit lubricating oil
must be drained and discarded from a new compressor before it may be fitted. An adjustment should be made to
the system oil level by taking into account:
• the quantity found in the original compressor
• the quantity deposited in the recovery equipment oil separator from the charge recovery operation.
Typically, 80 ml can be drained from the original compressor and 30 ml found in the oil separator; the sum of these
volumes (80 + 30 = 110 ml) is the amount of fresh PAG oil that must be put into the new compressor prior to fitting.
Hote:
The
discrepancy
between
this
figure
and
the
nominal capacity of
135
ml is
caused
by normally not
recoverable
oil being
trapped in
components
such
as
the receiver-drier or
evaporator.
The above statements are only true if there is no evidence of a leak. Where a leak has been detected and rectified,
the compressor must be refilled with the specified quantity.
Caution: Always decant
fresh
oil from a sealed container and do not leave oil exposed to the
atmosphere.
PAG oil is very
hygroscopic
(absorbs
water) and rapidly
attracts
atmospheric moisture.
PAG oil must
NEVER
be mixed with mineral
based
oils.
Do not
reuse
oil following a recovery cycle,
dispose
of it
safely.
Depending on the state of the air conditioning system immediately prior to charge recovery and the rate of recovery,
an amount of oil is drawn out with the refrigerant. The quantity is approximately 30 to 40 mi; this may vary, and
the figure is given only for guidance. It is most important that the oil separator vessel in the recovery equipment is
clean and empty at the start of the process so that the amount drawn out may be accurately measured.
May 1996 8-13