oil type ASTON MARTIN DB7 1997 Workshop Manual
[x] Cancel search | Manufacturer: ASTON MARTIN, Model Year: 1997, Model line: DB7, Model: ASTON MARTIN DB7 1997Pages: 421, PDF Size: 9.31 MB
Page 276 of 421
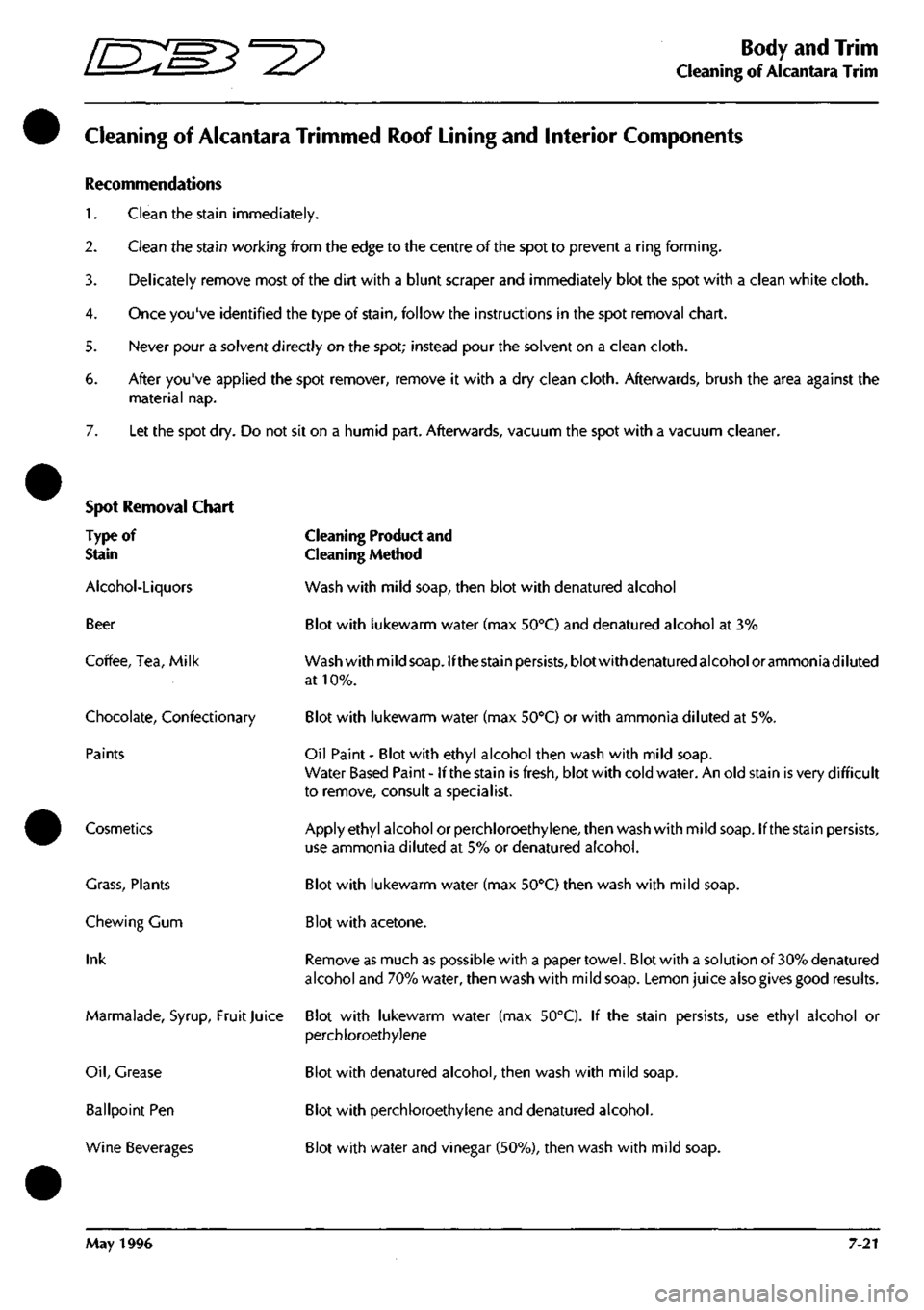
"^7
Body and Trim
Cleaning of Alcantara Trim
Cleaning of Alcantara Trimmed Roof Lining and Interior Components
Recommendations
1.
Clean the stain immediately.
Clean the stain working from the edge to the centre of the spot to prevent a ring forming.
Delicately remove most of the dirt with a blunt scraper and immediately blot the spot with a clean white cloth.
Once you've identified the type of stain, follow the instructions in the spot removal chart.
Never pour a solvent directly on the spot; instead pour the solvent on a clean cloth.
After you've applied the spot remover, remove it with a dry clean cloth. Afterwards, brush the area against the
material nap.
7. Let the spot dry. Do not sit on a humid part. Afterwards, vacuum the spot with a vacuum cleaner.
Spot Removal Chart
Type of
Stain
Alcohol-Liquors
Beer
Coffee, Tea, Milk
Chocolate, Confectionary
Paints
Cosmetics
Grass, Plants
Chewing Gum
Ink
Marmalade, Syrup, Fruit Juice
Oil,
Grease
Ballpoint Pen
Wine Beverages
Cleaning Product and
Cleaning Method
Wash with mild soap, then blot with denatured alcohol
Blot with lukewarm water (max 50°C) and denatured alcohol at 3%
Washwithmildsoap. If the stain persists, blot with denatured alcohol or ammonia diluted
at 10%.
Blot with lukewarm water (max 50°C) or with ammonia diluted at 5%.
Oil Paint - Blot with ethyl alcohol then wash with mild soap.
Water Based Paint - If the stain is fresh, blot with cold water. An old stain is very difficult
to remove, consult a specialist.
Apply ethyl alcohol or perchloroethylene, then wash with mild soap. If the stain persists,
use ammonia diluted at 5% or denatured alcohol.
Blot with lukewarm water (max 50°C) then wash with mild soap.
Blot with acetone.
Remove as much as possible with a paper towel. Blot with a solution of 30% denatured
alcohol and 70% water, then wash with mild soap. Lemon juice also gives good results.
Blot with lukewarm water (max 50°C). If the stain persists, use ethyl alcohol or
perchloroethylene
Blot with denatured alcohol, then wash with mild soap.
Blot with perchloroethylene and denatured alcohol.
Blot with water and vinegar (50%), then wash with mild soap.
May 1996 7-21
Page 282 of 421
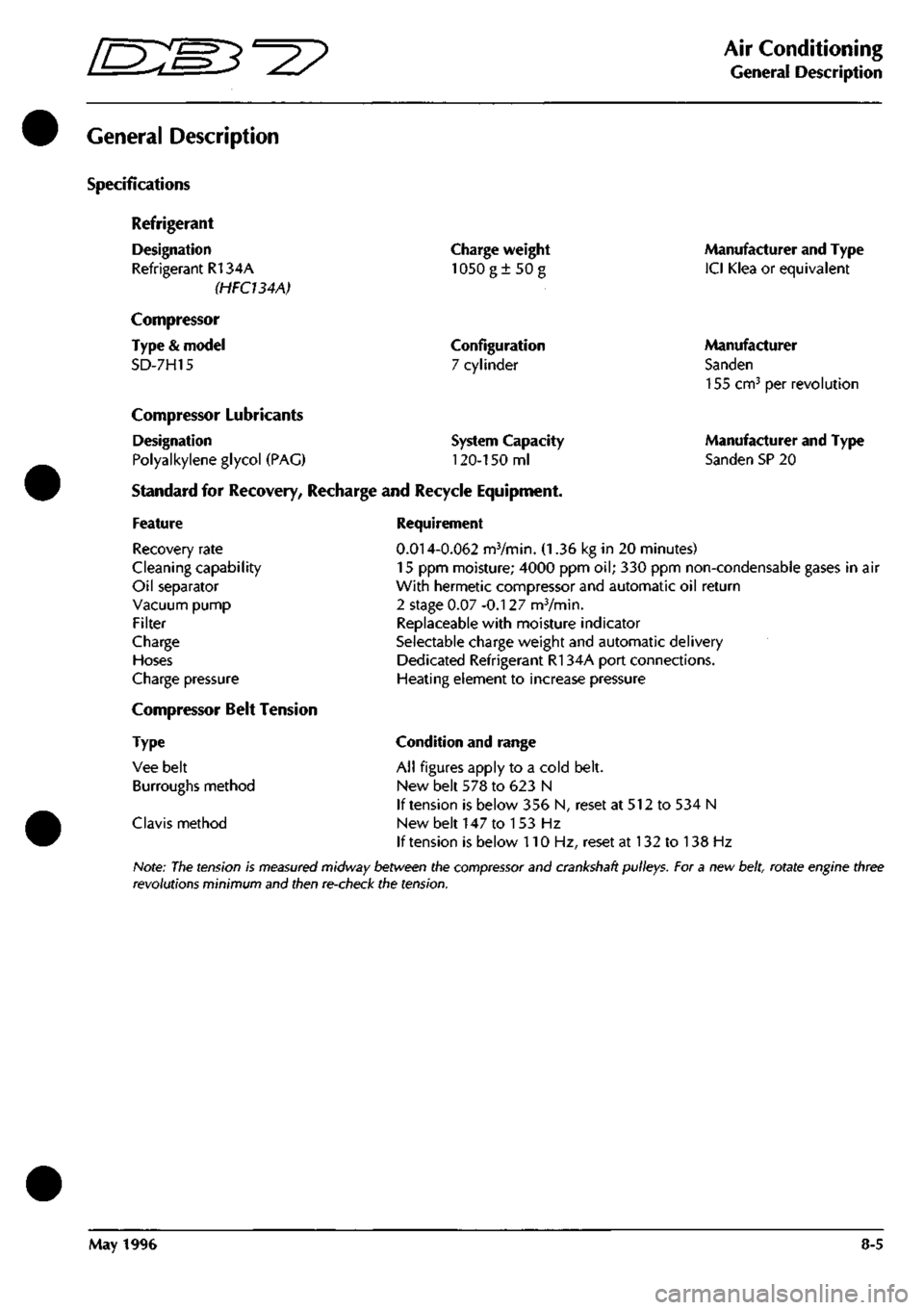
Em^^^?
Air Conditioning
General Description
General Description
Specifications
Refrigerant
Designation
Refrigerant R134A
(HFCUAA)
Compressor
Type
&
model
SD-7H15
Charge weight
1050g±50g
Configuration
7 cylinder
Compressor Lubricants
Designation
Polyalkylene glycol
(PAG)
Standard
for
Recovery, Recharge
and
Recycle Equipment,
System Capacity
120-150
ml
Manufacturer and Type
ICI Klea
or
equivalent
Manufacturer
Sanden
155 cm^
per
revolution
Manufacturer and Type
Sanden SP
20
Feature
Recovery rate
Cleaning capability
Oil separator
Vacuum pump
Filter
Charge
Hoses
Charge pressure
Compressor Belt Tension
Type
Vee belt
Burroughs method
Clavis method
Requirement
0.014-0.062
mVmin.
(1.36 kg in 20
minutes)
15
ppm
moisture; 4000
ppm oil; 330 ppm
non-condensable gases
in air
With hermetic compressor and automatic
oil
return
2 stage
0.07
-0.127 mVmin.
Replaceable with moisture indicator
Selectable charge weight and automatic delivery
Dedicated Refrigerant R134A port connections.
Heating element
to
increase pressure
Condition and range
All figures apply
to a
cold belt.
New belt
578 to 623 N
If tension
is
below
356 N,
reset
at 512 to 534 N
New belt
147 to 153 Hz
If tension
is
below
110 Hz,
reset
at 132 to 138 Hz
Note:
The
tension
is
measured
midway between the
compressor
and crankshaft pulleys. For a new
belt,
rotate engine three
revolutions minimum and then re-check the tension.
May 1996
8-5
Page 289 of 421
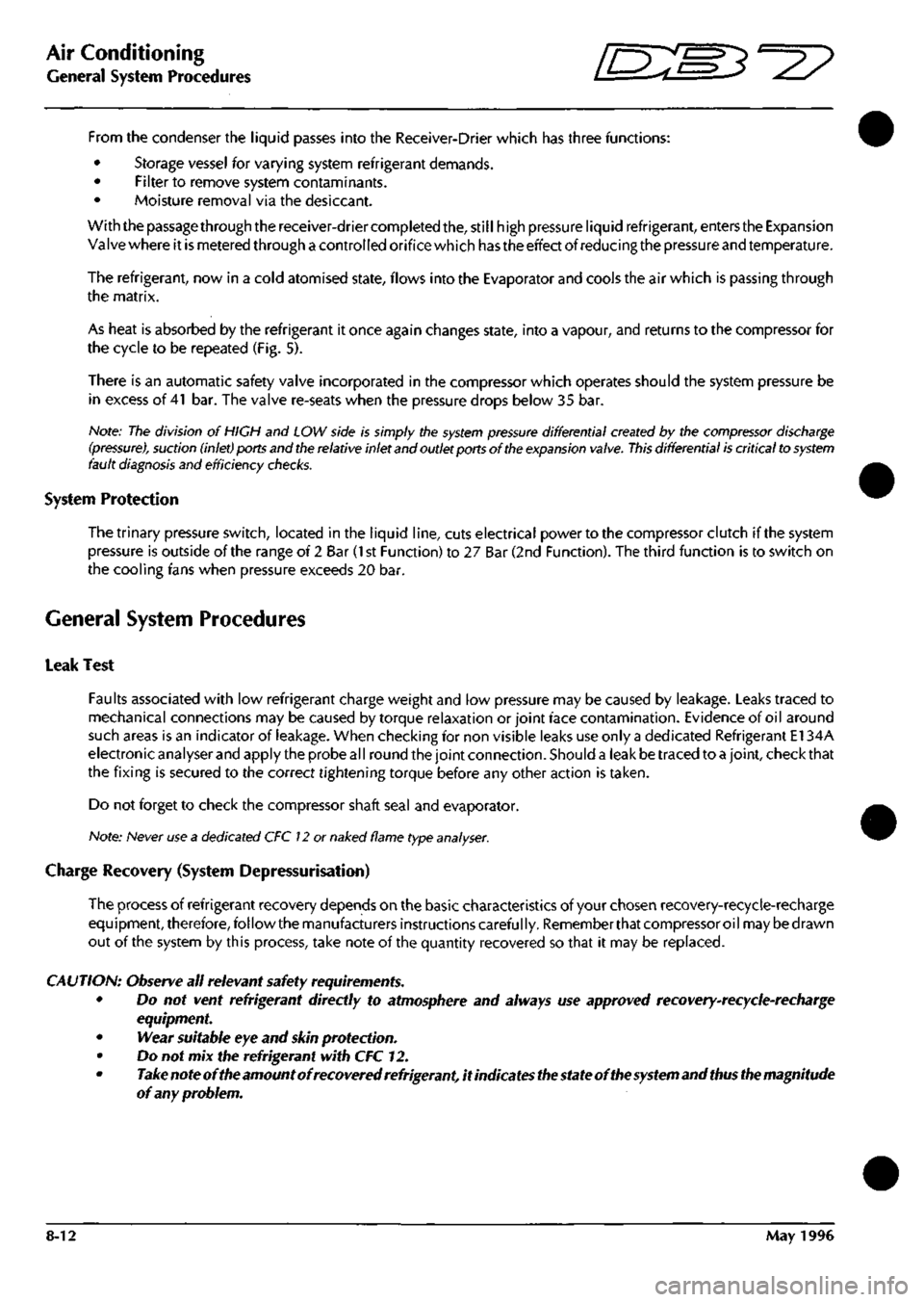
Air Conditioning //~-->> ^/zz:^^ • ^ ^
General Svstem Procedures ' —"^ ^ '^ General System Procedures
From the condenser the liquid passes into the Receiver-Drier which has three functions:
• Storage vessel for varying system refrigerant demands.
• Filter to remove system contaminants.
• Moisture removal via the desiccant.
With the passage through the receiver-drier completed the, still high pressure liquid refrigerant, enters the Expansion
Valve where it is metered through a controlled orifice which has the effect of reducing the pressure and temperature.
The refrigerant, now in a cold atomised state, flows into the Evaporator and cools the air which is passing through
the matrix.
As heat is absorbed by the refrigerant it once again changes state, into a vapour, and returns to the compressor for
the cycle to be repeated (Fig. 5).
There is an automatic safety valve incorporated in the compressor which operates should the system pressure be
in excess of
41
bar. The valve re-seats when the pressure drops below 35 bar.
Note: The division of HIGH and LOW side is simply the
system pressure
differential created by the
compressor
discharge
(pressure),
suction
(inlet)
ports and
the
relative inlet and outlet
ports
of the
expansion
valve.
This
differential is critical to
system
fault
diagnosis
and efficiency checks.
System Protection
The trinary pressure switch, located in the liquid line, cuts electrical power to the compressor clutch if the system
pressure is outside of the range of 2 Bar
(1
st Function) to 27 Bar (2nd Function). The third function is to switch on
the cooling fans when pressure exceeds 20 bar.
General System Procedures
Leak Test
Faults associated with low refrigerant charge weight and low pressure may be caused by leakage. Leaks traced to
mechanical connections may be caused by torque relaxation or joint face contamination. Evidence of oil around
such areas is an indicator of leakage. When checking for non visible leaks use only a dedicated Refrigerant El 34A
electronic analyser and apply the probe all round the joint connection. Should a leak be traced to a joint, check that
the fixing is secured to the correct tightening torque before any other action is taken.
Do not forget to check the compressor shaft seal and evaporator.
Note: Never
use
a dedicated
CFC 12
or
naiced
flame type
analyser.
Charge Recovery (System Depressurisation)
The process of refrigerant recovery depends on the basic characteristics of your chosen recovery-recycle-recharge
equipment, therefore, follow the manufacturers instructions carefully. Remember that compressor oil may be drawn
out of the system by this process, take note of the quantity recovered so that it may be replaced.
CAUTION: Observe all relevant safety requirements.
• Do not vent refrigerant directly to atmosphere and always use approved recovery-recycle-recharge
equipment.
• Wear suitable eye and skin protection.
• Do not mix the refrigerant with CFC 12.
• Take note of the amount of recovered refrigerant, it indica
tes the
state of the
system
and
thus the
magnitude
of any problem.
8-12 May 1996