engine oil ASTON MARTIN V8 VANTAGE 2010 Workshop Manual
[x] Cancel search | Manufacturer: ASTON MARTIN, Model Year: 2010, Model line: V8 VANTAGE, Model: ASTON MARTIN V8 VANTAGE 2010Pages: 947, PDF Size: 43.21 MB
Page 666 of 947
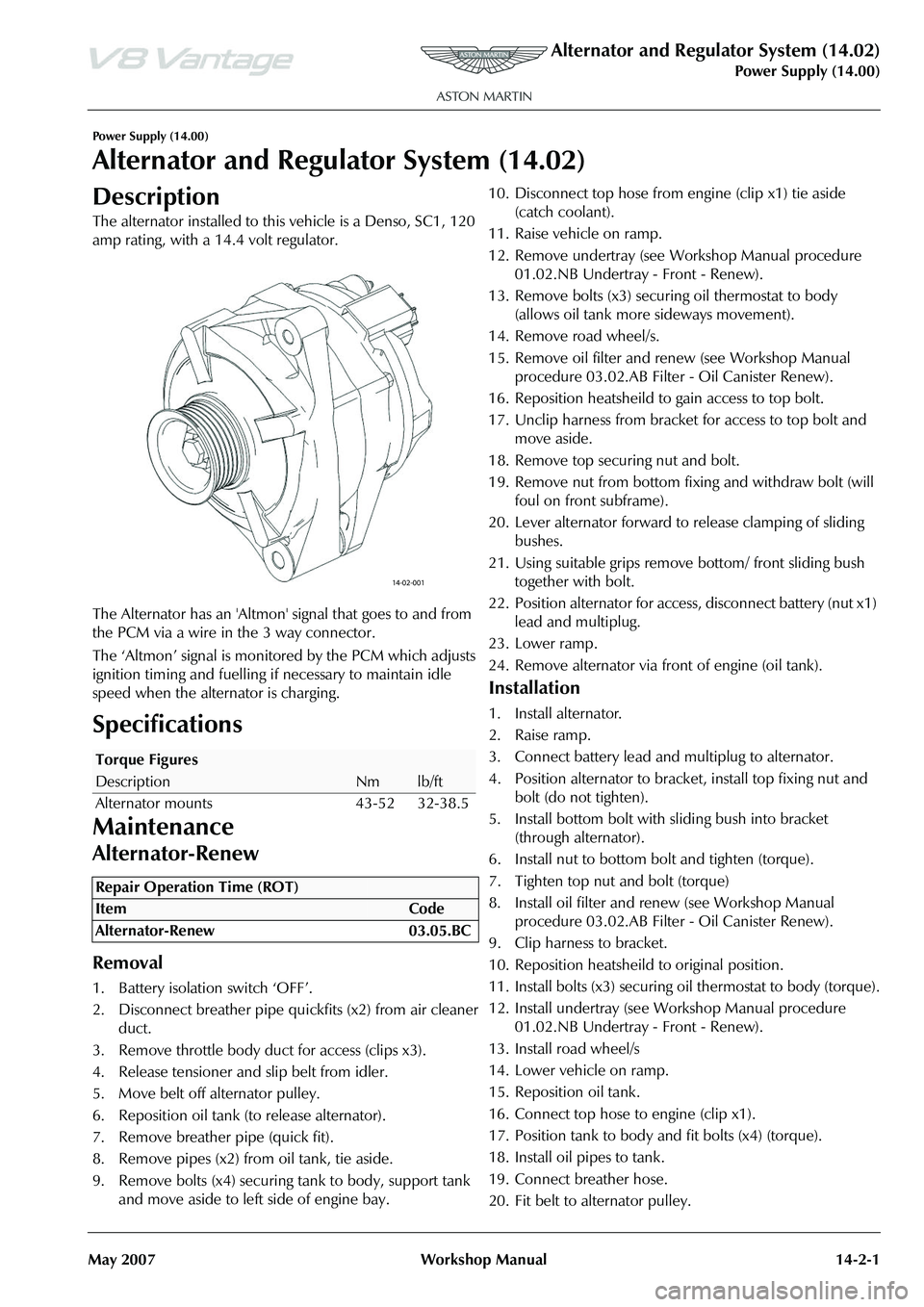
Alternator and Regulator System (14.02)
Power Supply (14.00)
May 2007 Workshop Manual 14-2-1
Power Supply (14.00)
Alternator and Regulator System (14.02)
Description
The alternator installed to this vehicle is a Denso, SC1, 120
amp rating, with a 14.4 volt regulator.
The Alternator has an 'Altmon' signal that goes to and from
the PCM via a wire in the 3 way connector.
The ‘Altmon’ signal is monitored by the PCM which adjusts
ignition timing and fuelling if necessary to maintain idle
speed when the alternator is charging.
Specifications
Maintenance
Alternator-Renew
Removal
1. Battery isolation switch ‘OFF’.
2. Disconnect breather pipe qu ickfits (x2) from air cleaner
duct.
3. Remove throttle body du ct for access (clips x3).
4. Release tensioner and slip belt from idler.
5. Move belt off alternator pulley.
6. Reposition oil tank (to release alternator).
7. Remove breather pipe (quick fit).
8. Remove pipes (x2) fr om oil tank, tie aside.
9. Remove bolts (x4) securing tank to body, support tank and move aside to left side of engine bay. 10. Disconnect top hose from engine (clip x1) tie aside
(catch coolant).
11. Raise vehicle on ramp.
12. Remove undertray (see Workshop Manual procedure 01.02.NB Undertray - Front - Renew).
13. Remove bolts (x3) securing oil thermostat to body (allows oil tank more sideways movement).
14. Remove road wheel/s.
15. Remove oil filter and renew (see Workshop Manual procedure 03.02.AB Filter - Oil Canister Renew).
16. Reposition heatsheild to gain access to top bolt.
17. Unclip harness from bracket for access to top bolt and move aside.
18. Remove top securing nut and bolt.
19. Remove nut from bottom fixing and withdraw bolt (will foul on front subframe).
20. Lever alternator forward to release clamping of sliding bushes.
21. Using suitable grips remove bottom/ front sliding bush together with bolt.
22. Position alternator for access, disconnect battery (nut x1) lead and multiplug.
23. Lower ramp.
24. Remove alternator via front of engine (oil tank).
Installation
1. Install alternator.
2. Raise ramp.
3. Connect battery lead and multiplug to alternator.
4. Position alternator to bracket, install top fixing nut and bolt (do not tighten).
5. Install bottom bolt with sliding bush into bracket (through alternator).
6. Install nut to bottom bolt and tighten (torque).
7. Tighten top nut and bolt (torque)
8. Install oil filter and re new (see Workshop Manual
procedure 03.02.AB Filter - Oil Canister Renew).
9. Clip harness to bracket.
10. Reposition heatsheild to original position.
11. Install bolts (x3) securing oil thermostat to body (torque).
12. Install undertray (see Workshop Manual procedure 01.02.NB Undertray - Front - Renew).
13. Install road wheel/s
14. Lower vehicle on ramp.
15. Reposition oil tank.
16. Connect top hose to engine (clip x1).
17. Position tank to body and fit bolts (x4) (torque).
18. Install oil pipes to tank.
19. Connect breather hose.
20. Fit belt to alternator pulley.
Torque Figures
DescriptionNmlb/ft
Alternator mounts 43-52 32-38.5
Repair Operation Time (ROT)
Page 712 of 947
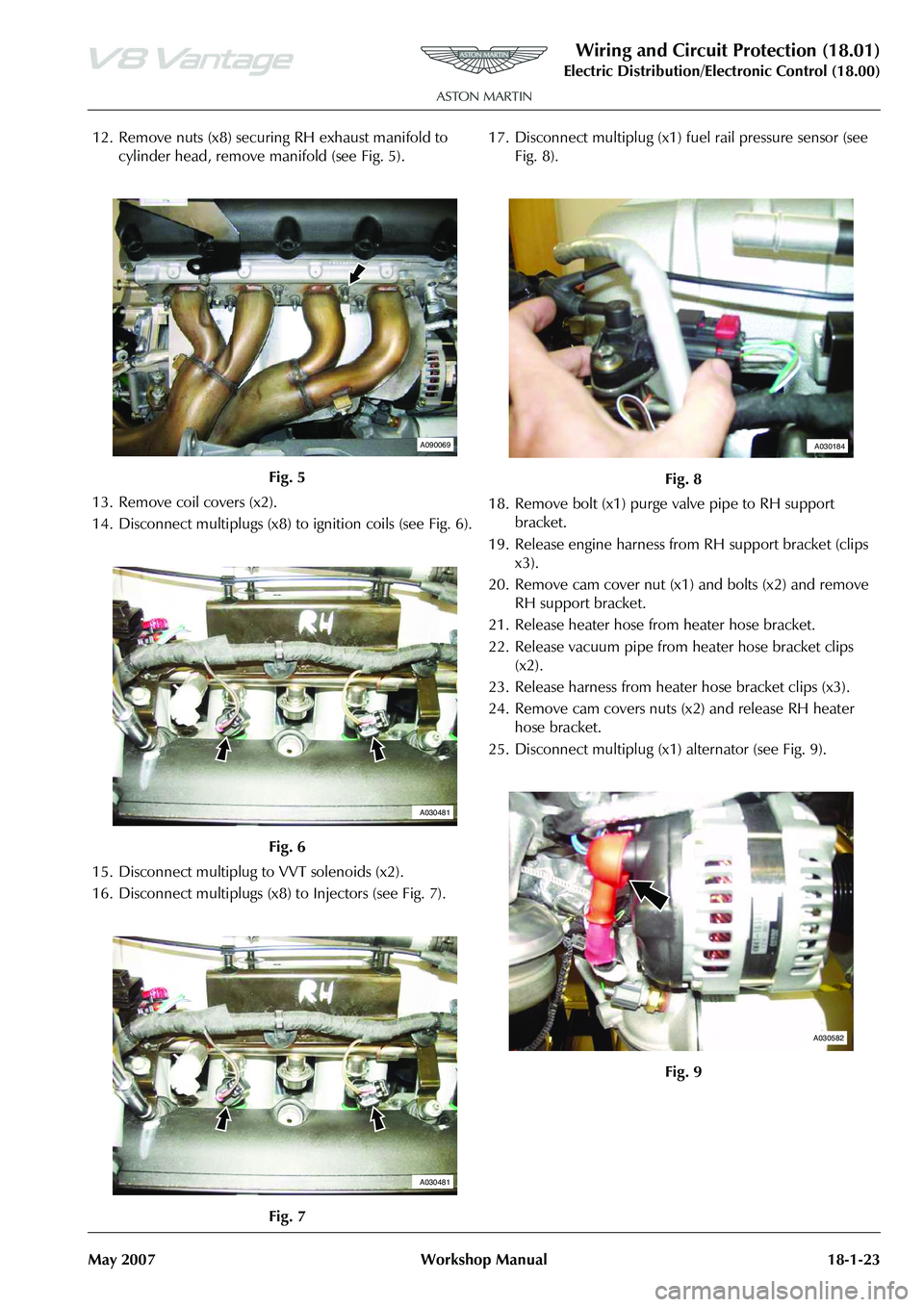
Wiring and Circuit Protection (18.01)
Electric Distribution/Electronic Control (18.00)
May 2007 Workshop Manual 18-1-23
12. Remove nuts (x8) securing RH exhaust manifold to cylinder head, remove ma nifold (see Fig. 5).
13. Remove coil covers (x2).
14. Disconnect multiplugs (x8) to ignition coils (see Fig. 6).
15. Disconnect multiplug to VVT solenoids (x2).
16. Disconnect multiplugs (x8) to Injectors (see Fig. 7).17. Disconnect multiplug (x1) fu
el rail pressure sensor (see
Fig. 8).
18. Remove bolt (x1) purge valve pipe to RH support bracket.
19. Release engine harness from RH support bracket (clips x3).
20. Remove cam cover nut (x1) and bolts (x2) and remove RH support bracket.
21. Release heater hose from heater hose bracket.
22. Release vacuum pipe from heater hose bracket clips (x2).
23. Release harness from heater hose bracket clips (x3).
24. Remove cam covers nuts (x2) and release RH heater hose bracket.
25. Disconnect multiplug (x1) alternator (see Fig. 9).
Fig. 5
Fig. 6
Fig. 7
$
$
$
Fig. 8
Fig. 9
$
$
Page 713 of 947
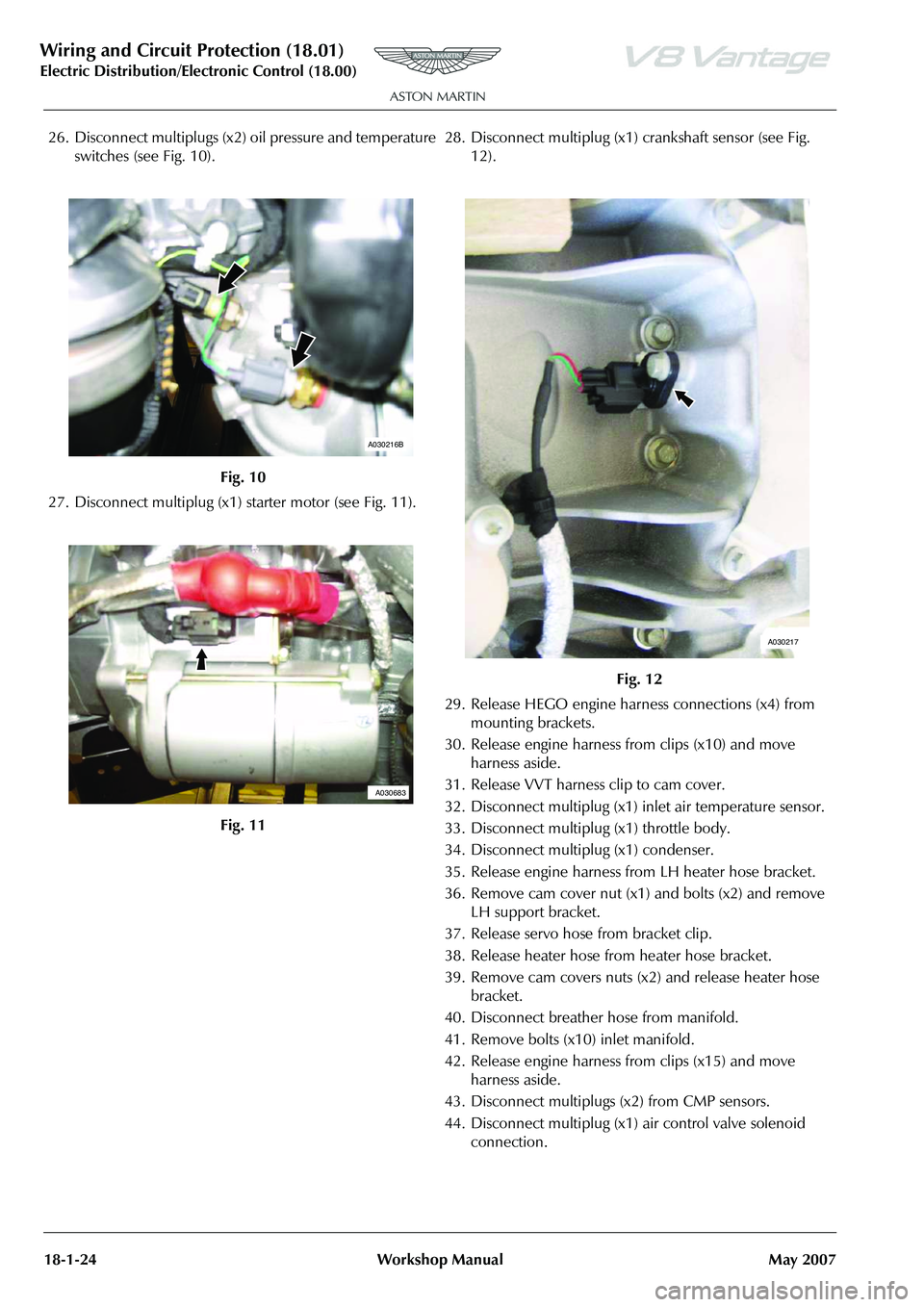
Wiring and Circuit Protection (18.01)
Electric Distribution/E lectronic Control (18.00)
18-1-24 Workshop Manual May 2007
26. Disconnect multiplugs (x2) oil pressure and temperature
switches (see Fig. 10).
27. Disconnect multiplug (x1) starter motor (see Fig. 11). 28. Disconnect multiplug (x1) cr
ankshaft sensor (see Fig.
12).
29. Release HEGO engine harn ess connections (x4) from
mounting brackets.
30. Release engine harness from clips (x10) and move harness aside.
31. Release VVT harness clip to cam cover.
32. Disconnect multiplug (x1) inlet air temperature sensor.
33. Disconnect multiplug (x1) throttle body.
34. Disconnect multiplug (x1) condenser.
35. Release engine harness from LH heater hose bracket.
36. Remove cam cover nut (x1) and bolts (x2) and remove
LH support bracket.
37. Release servo hose from bracket clip.
38. Release heater hose fr om heater hose bracket.
39. Remove cam covers nuts (x 2) and release heater hose
bracket.
40. Disconnect breather hose from manifold.
41. Remove bolts (x10) inlet manifold.
42. Release engine harness from clips (x15) and move harness aside.
43. Disconnect multiplugs (x2) from CMP sensors.
44. Disconnect multiplug (x1) air control valve solenoid
connection.
Fig. 10
Fig. 11
$ %
$
Fig. 12
$
Page 714 of 947
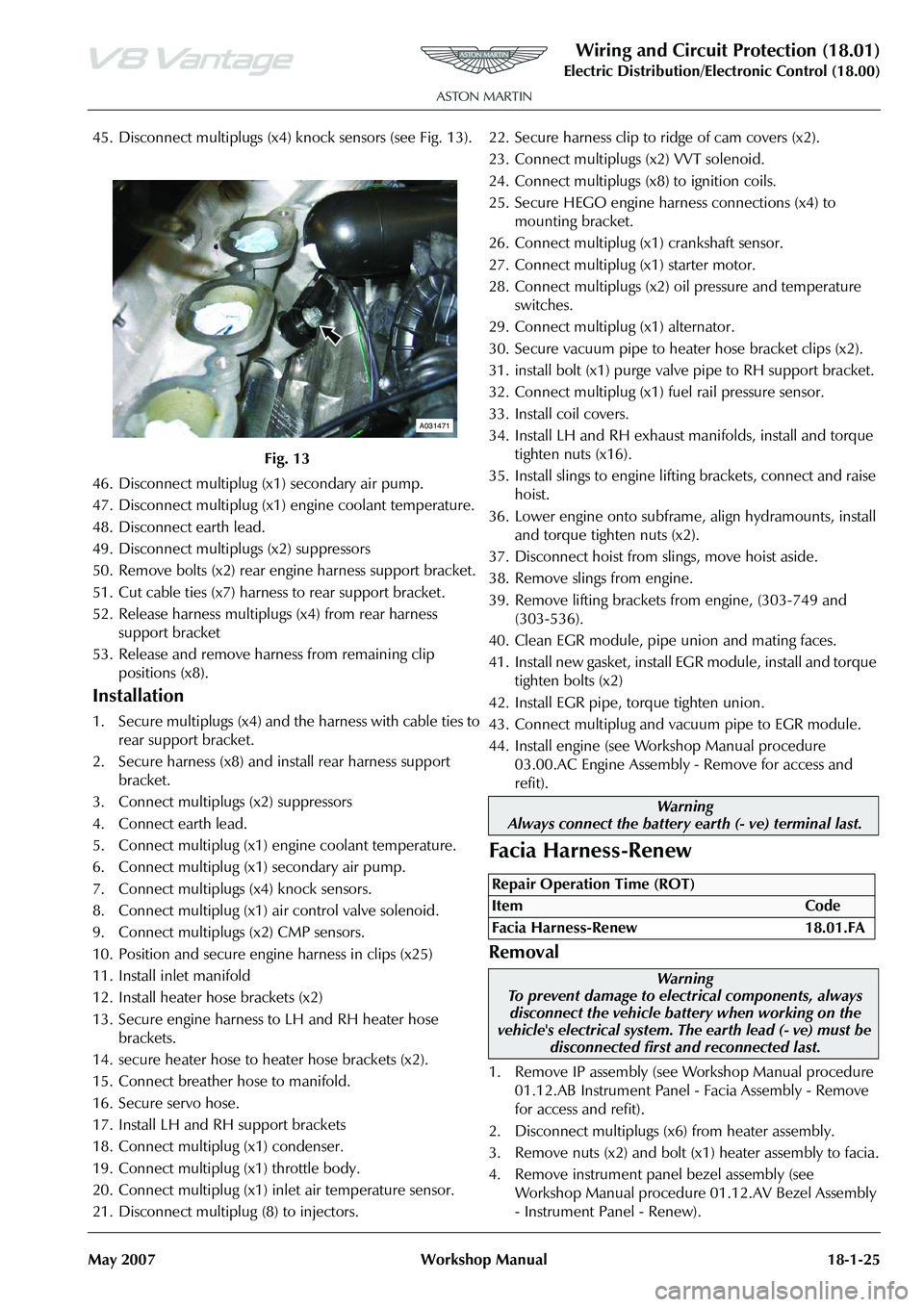
Wiring and Circuit Protection (18.01)
Electric Distribution/Electronic Control (18.00)
May 2007 Workshop Manual 18-1-25
45. Disconnect multiplugs (x4) knock sensors (see Fig. 13).
46. Disconnect multiplug (x 1) secondary air pump.
47. Disconnect multiplug (x1) engine coolant temperature.
48. Disconnect earth lead.
49. Disconnect multiplugs (x2) suppressors
50. Remove bolts (x2) rear engine harness support bracket.
51. Cut cable ties (x7) harn ess to rear support bracket.
52. Release harness multiplugs (x4) from rear harness support bracket
53. Release and remove harness from remaining clip positions (x8).
Installation
1. Secure multiplugs (x4) and the harness with cable ties to rear support bracket.
2. Secure harness (x8) and install rear harness support bracket.
3. Connect multiplugs (x2) suppressors
4. Connect earth lead.
5. Connect multiplug (x1) engine coolant temperature.
6. Connect multiplug (x1) secondary air pump.
7. Connect multiplugs (x4) knock sensors.
8. Connect multiplug (x1) air control valve solenoid.
9. Connect multiplugs (x2) CMP sensors.
10. Position and secure engine harness in clips (x25)
11. Install inlet manifold
12. Install heater hose brackets (x2)
13. Secure engine harness to LH and RH heater hose brackets.
14. secure heater hose to he ater hose brackets (x2).
15. Connect breather hose to manifold.
16. Secure servo hose.
17. Install LH and RH support brackets
18. Connect multiplug (x1) condenser.
19. Connect multiplug (x1) throttle body.
20. Connect multiplug (x1) in let air temperature sensor.
21. Disconnect multiplug (8) to injectors. 22. Secure harness clip to ridge of cam covers (x2).
23. Connect multiplugs (x2) VVT solenoid.
24. Connect multiplugs (x8) to ignition coils.
25. Secure HEGO engine harn
ess connections (x4) to
mounting bracket.
26. Connect multiplug (x1) crankshaft sensor.
27. Connect multiplug (x1) starter motor.
28. Connect multiplugs (x2) oil pressure and temperature switches.
29. Connect multiplug (x1) alternator.
30. Secure vacuum pipe to heater hose bracket clips (x2).
31. install bolt (x1) purge valv e pipe to RH support bracket.
32. Connect multiplug (x1) fuel rail pressure sensor.
33. Install coil covers.
34. Install LH and RH exhaust ma nifolds, install and torque
tighten nuts (x16).
35. Install slings to engine lifting brackets, connect and raise hoist.
36. Lower engine onto subframe, align hydramounts, install and torque tighten nuts (x2).
37. Disconnect hoist from slings, move hoist aside.
38. Remove slings from engine.
39. Remove lifting brackets from engine, (303-749 and (303-536).
40. Clean EGR module, pipe union and mating faces.
41. Install new gasket, install EGR module, install and torque tighten bolts (x2)
42. Install EGR pipe, torque tighten union.
43. Connect multiplug and vacuum pipe to EGR module.
44. Install engine (see Wo rkshop Manual procedure
03.00.AC Engine Assembly - Remove for access and
refit).
Facia Harness-Renew
Removal
1. Remove IP assembly (see Workshop Manual procedure
01.12.AB Instrument Panel - Facia Assembly - Remove
for access and refit).
2. Disconnect multiplugs (x 6) from heater assembly.
3. Remove nuts (x2) and bolt (x 1) heater assembly to facia.
4. Remove instrument panel bezel assembly (see Workshop Manual procedur e 01.12.AV Bezel Assembly
- Instrument Panel - Renew).
Fig. 13
$
Warning
Always connect the battery earth (- ve) terminal last.
Repair Operation Time (ROT)
Warning
To prevent damage to electrical components, always disconnect the vehicle battery when working on the
vehicle's electrical system. The earth lead (- ve) must be disconnected first an d reconnected last.
Page 735 of 947
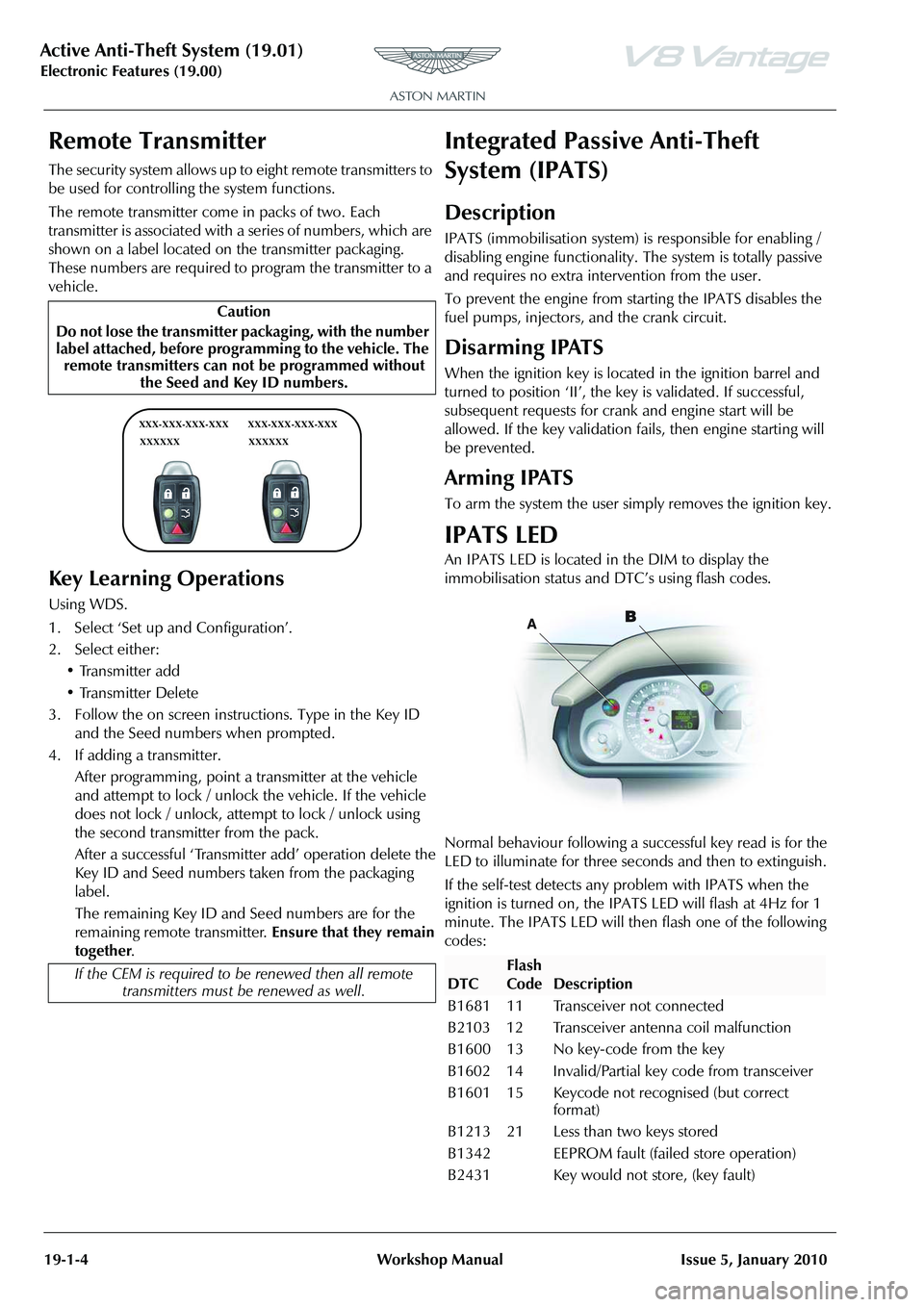
Active Anti-Theft System (19.01)
Electronic Features (19.00)19-1-4 Workshop ManualIssue 5, January 2010
Remote Transmitter
The security system allows up to eight remote transmitters to
be used for controlling the system functions.
The remote transmitter come in packs of two. Each
transmitter is associated with a
series of numbers, which are
shown on a label located on the transmitter packaging.
These numbers are required to program the transmitter to a
vehicle.
Key Learning Operations
Using WDS.
1. Select ‘Set up and Configuration’.
2. Select either:
• Transmitter add
• Transmitter Delete
3. Follow the on screen instructions. Type in the Key ID and the Seed numbers when prompted.
4. If adding a transmitter. After programming , point a transmitter at the vehicle
and attempt to lock / unlock the vehicle. If the vehicle
does not lock / unlock, attempt to lock / unlock using
the second transmitter from the pack.
After a successful ‘Transmitter add’ operation delete the
Key ID and Seed numbers taken from the packaging
label.
The remaining Key ID and Seed numbers are for the
remaining remote transmitter. Ensure that they remain
together .
Integrated Passive Anti-Theft
System (IPATS)
Description
IPATS (immobilisation system) is responsible for enabling /
disabling engine functionality. The system is totally passive
and requires no extra inte rvention from the user.
To prevent the engine from starting the IPATS disables the
fuel pumps, injectors, and the crank circuit.
Disarming IPATS
When the ignition key is located in the ignition barrel and
turned to position ‘II’, the key is validated. If successful,
subsequent requests for crank and engine start will be
allowed. If the key validation fa ils, then engine starting will
be prevented.
Arming IPATS
To arm the system the user simply removes the ignition key.
IPATS LED
An IPATS LED is located in the DIM to display the
immobilisation status and DTC’s using flash codes.
Normal behaviour following a su ccessful key read is for the
LED to illuminate for three seconds and then to extinguish.
If the self-test detects any problem with IPATS when the
ignition is turned on, the IPAT S LED will flash at 4Hz for 1
minute. The IPATS LED will then flash one of the following
codes:
Caution
Do not lose the transmitter packaging, with the number
label attached, before progra mming to the vehicle. The
remote transmitters can not be programmed without the Seed and Key ID numbers.
If the CEM is required to be renewed then all remote
transmitters must be renewed as well.
XXX-XXX-XXX-XXX
XXXXXX XXX-XXX-XXX-XXX
XXXXXX
DTC
Flash
Code
Description
B1681 11 Transceiver not connected
B2103 12 Transceiver antenna coil malfunction
B1600 13 No key-code from the key
B1602 14 Invalid/Partial key code from transceiver
B1601 15 Keycode not recognised (but correct format)
B1213 21 Less than two keys stored
B1342 EEPROM fault (failed store operation)
B2431 Key would not store, (key fault)
Page 742 of 947
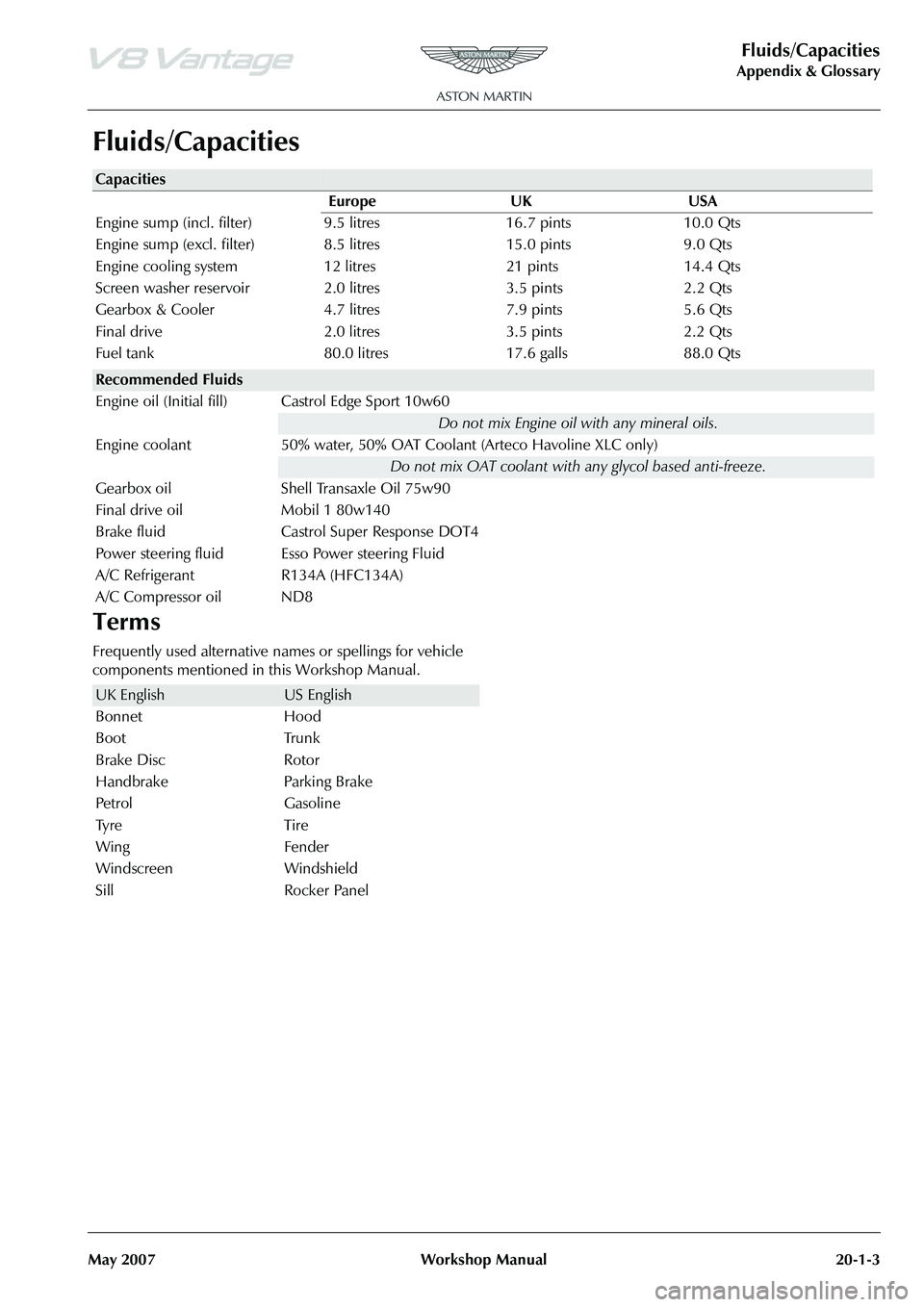
Fluids/Capacities
Appendix & Glossary
May 2007 Workshop Manual 20-1-3
Fluids/Capacities
Terms
Frequently used alternative names or spellings for vehicle
components mentioned in this Workshop Manual.
Capacities
Europe UK USA
Engine sump (incl. filter) 9 .5 litres 16.7 pints 10.0 Qts
Engine sump (excl. filter) 8 .5 litres 15.0 pints 9.0 Qts
Engine cooling system 12 litres 21 pints 14.4 Qts
Screen washer reservoir 2.0 litres 3.5 pints 2.2 Qts
Gearbox & Cooler 4.7 litres 7.9 pints 5.6 Qts
Final drive 2.0 litres 3.5 pints 2.2 Qts
Fuel tank 80.0 litres 17.6 galls 88.0 Qts
Recommended Fluids
Engine oil (Initial fill) Castrol Edge Sport 10w60
Do not mix Engine oil with any mineral oils.
Engine coolant 50% water, 50% OAT Coolant (Arteco Havoline XLC only)
Do not mix OAT coolant with any glycol based anti-freeze.
Gearbox oil Shell Transaxle Oil 75w90
Final drive oil Mobil 1 80w140
Brake fluid Castrol Super Response DOT4
Power steering fluid Esso Power steering Fluid
A/C Refrigerant R134A (HFC134A)
A/C Compressor oil ND8
UK EnglishUS English
Bonnet Hood
Boot Trunk
Brake Disc Rotor
Handbrake Parking Brake
Petrol Gasoline
Tyre Tire
Wing Fender
Windscreen Windshield
Sill Rocker Panel
Page 747 of 947
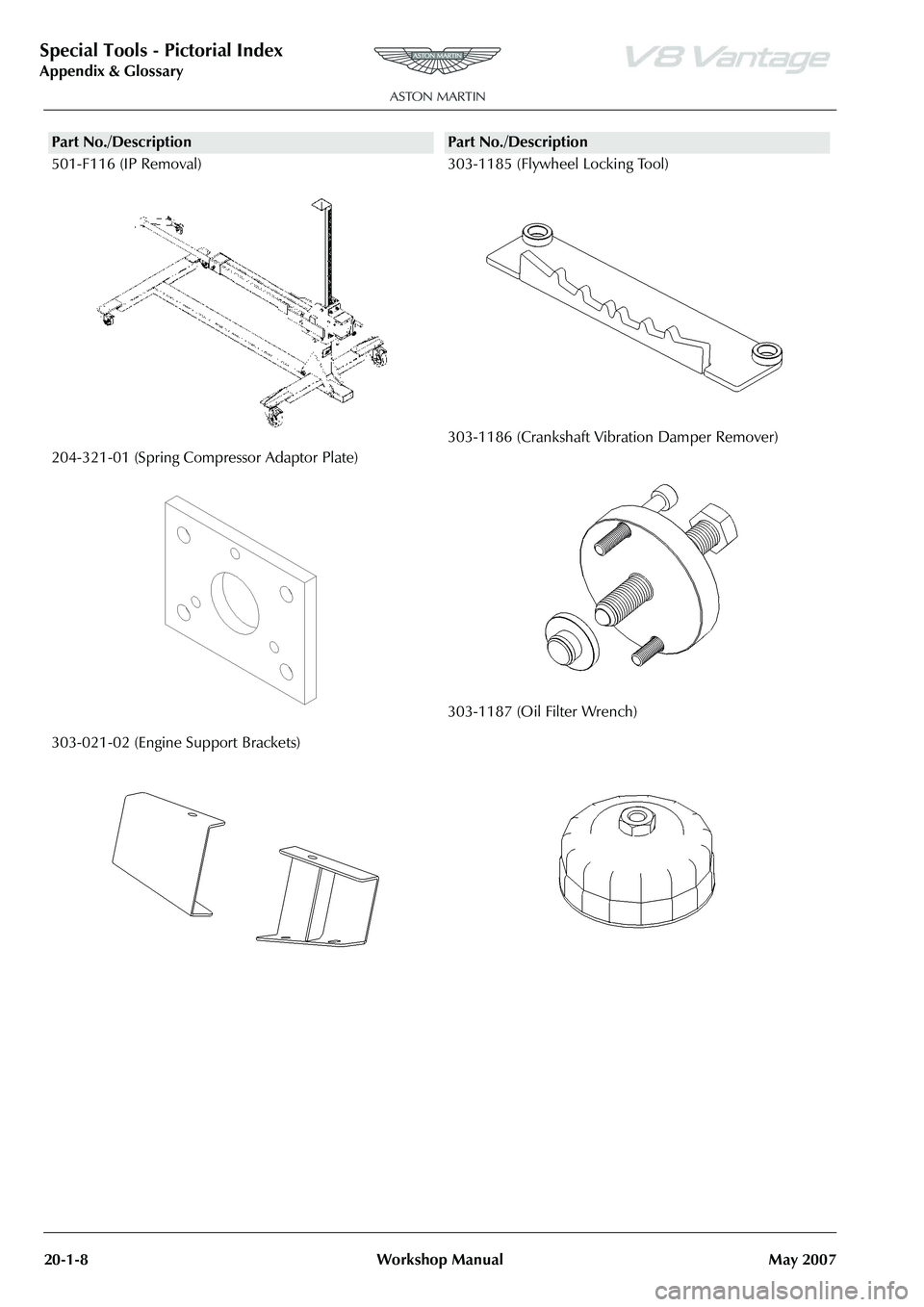
Special Tools - Pictorial Index
Appendix & Glossary20-1-8 Workshop Manual May 2007
501-F116 (IP Removal)
204-321-01 (Spring Compressor Adaptor Plate)
303-021-02 (Engine Support Brackets)
Part No./Description
303-1185 (Flywheel Locking Tool)
303-1186 (Crankshaft Vibration Damper Remover)
303-1187 (Oil Filter Wrench)
Part No./Description
Page 748 of 947
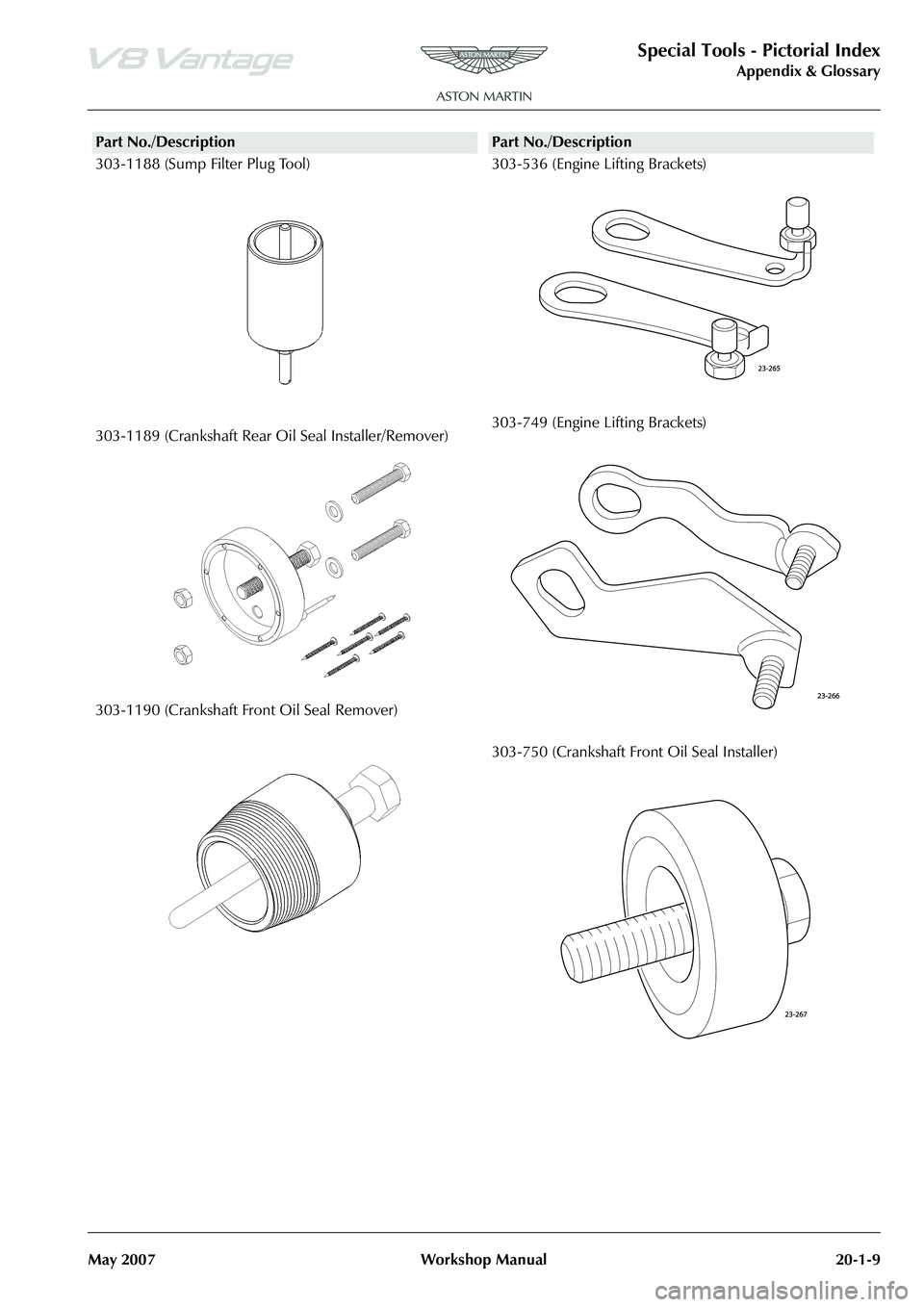
Special Tools - Pictorial Index
Appendix & Glossary
May 2007 Workshop Manual 20-1-9
303-1188 (Sump Filter Plug Tool)
303-1189 (Crankshaft Rear Oil Seal Installer/Remover)
303-1190 (Crankshaft Front Oil Seal Remover)
Part No./Description
303-536 (Engine Lifting Brackets)
303-749 (Engine Lifting Brackets)
303-750 (Crankshaft Front Oil Seal Installer)
Page 751 of 947
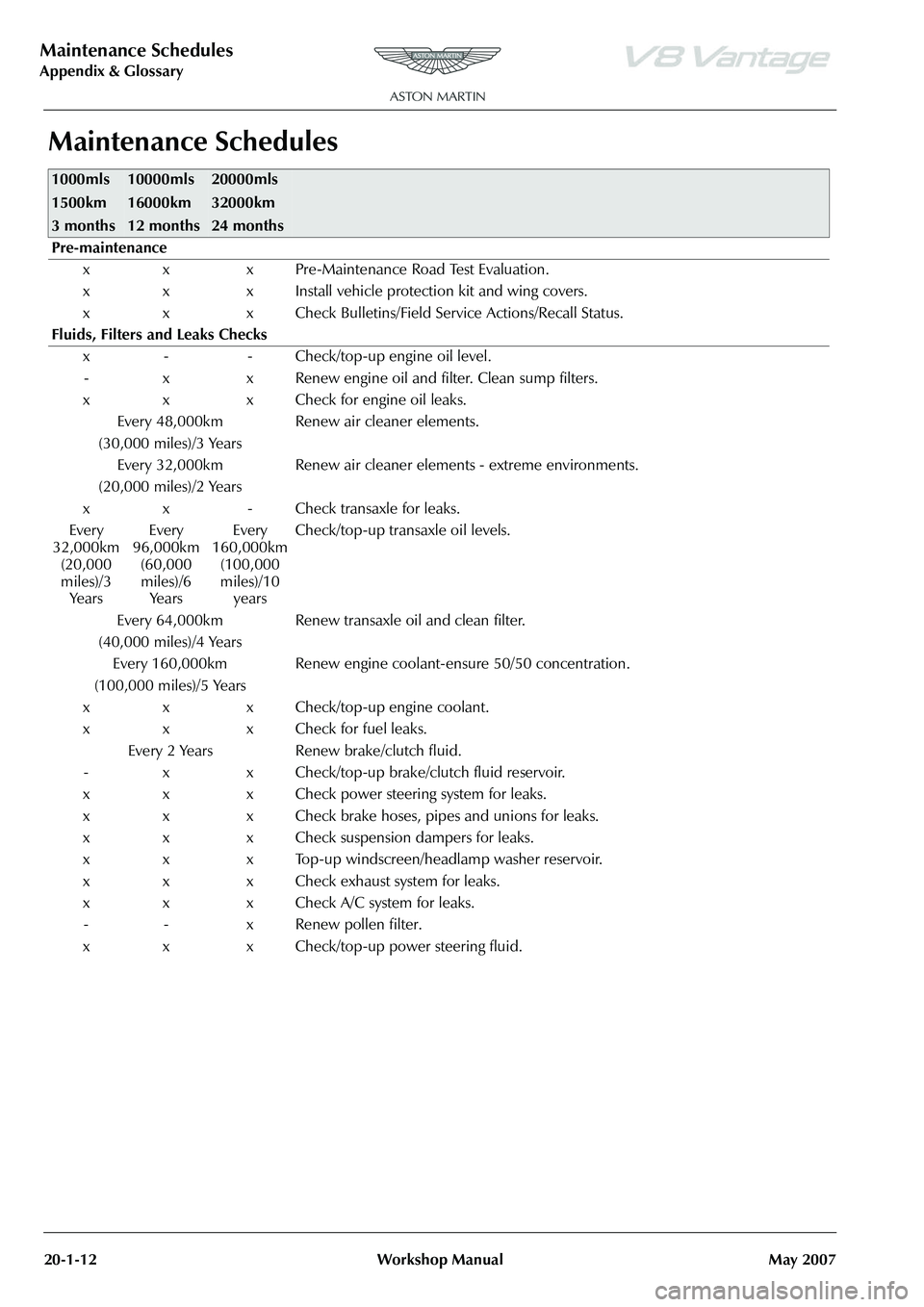
Maintenance Schedules
Appendix & Glossary20-1-12 Workshop Manual May 2007
Maintenance Schedules
1000mls
1500km
3 months10000mls
16000km
12 months20000mls
32000km
24 months
Pre-maintenance
x x x Pre-Maintenance Road Test Evaluation.
x x x Install vehicle protection kit and wing covers.
x x x Check Bulletins/Field Service Actions/Recall Status.
Fluids, Filters and Leaks Checks x - - Check/top-up engine oil level.- x x Renew engine oil and filter. Clean sump filters.
x x x Check for engine oil leaks. Every 48,000km
(30,000 miles)/3 Years Renew air cleaner elements.
Every 32,000km
(20,000 miles)/2 Years Renew air cleaner elements - extreme environments.
x x - Check transaxle for leaks.
Every
32,000km (20,000
miles)/3 Ye a r s Every
96,000km (60,000
miles)/6 Ye a r s Every
160,000km (100,000
miles)/10 years Check/top-up transaxle oil levels.
Every 64,000km
(40,000 miles)/4 Years Renew transaxle oil and clean filter.
Every 160,000km
(100,000 miles)/5 Years Renew engine coolant-ensure 50/50 concentration.
x x x Check/top-up engine coolant.
x x x Check for fuel leaks. Every 2 Years Renew brake/clutch fluid.
- x x Check/top-up brake/clutch fluid reservoir.
x x x Check power steering system for leaks.
x x x Check brake hoses, pipes and unions for leaks.
x x x Check suspension dampers for leaks.
x x x Top-up windscreen/headlamp washer reservoir.
x x x Check exhaust system for leaks.
x x x Check A/C system for leaks. - - x Renew pollen filter.
x x x Check/top-up power steering fluid.
Page 871 of 947
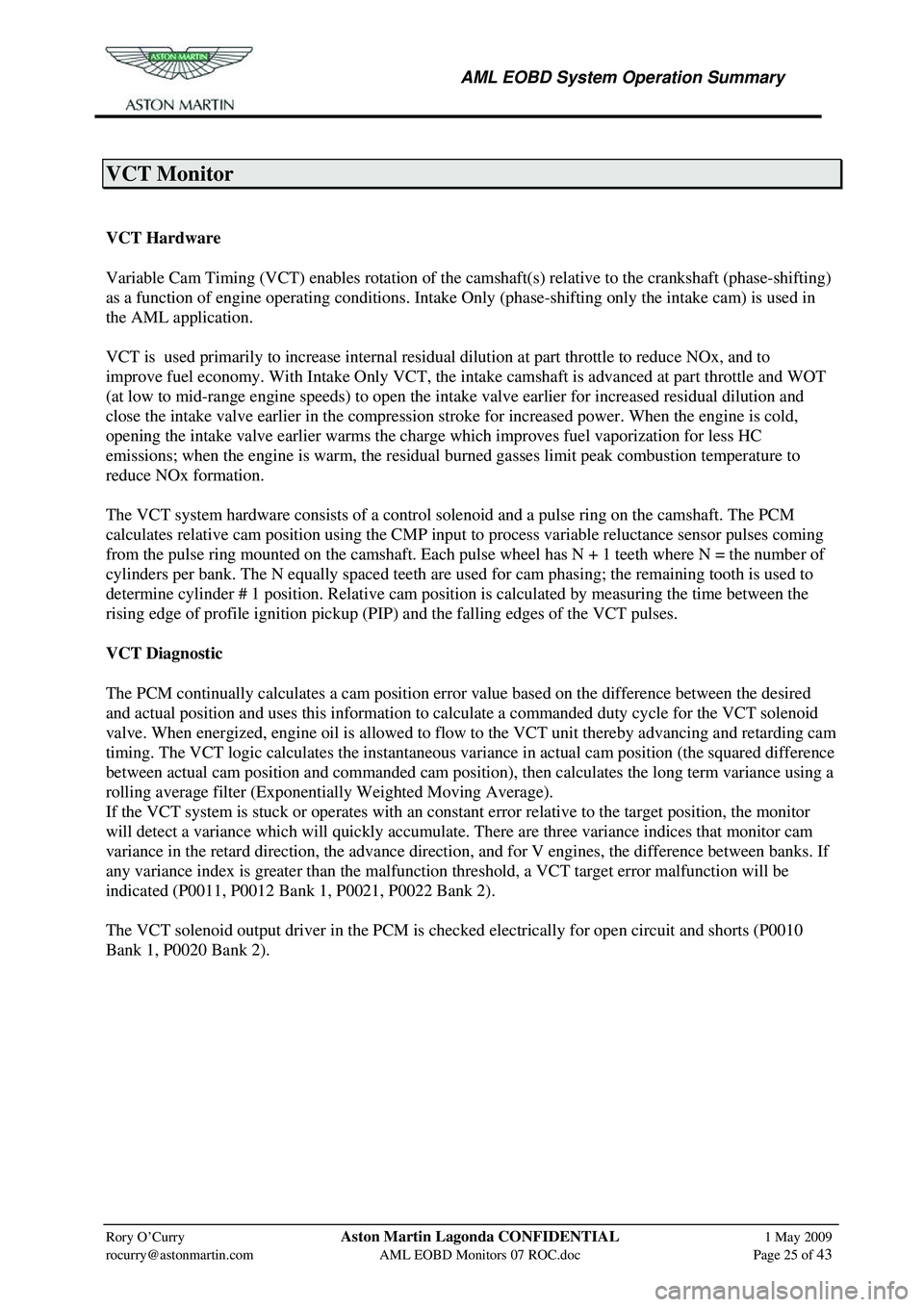
AML EOBD System Operation Summary
Rory O’Curry Aston Martin Lagonda CONFIDENTIAL 1 May 2009
[email protected] AML EOBD Monitors 07 ROC.doc Page 25 of 43
VCT Monitor
Variable Cam Timing System Monitor
VCT Hardware
Variable Cam Timing (VCT) enables rotation of the camshaft(s) relative to the crankshaft (phase-shifting)
as a function of engine operating conditions. Intake Only (phase-shifting only the intake cam) is used in
the AML application.
VCT is used primarily to increase internal residua l dilution at part throttle to reduce NOx, and to
improve fuel economy. With Intake Only VCT, the in take camshaft is advanced at part throttle and WOT
(at low to mid-range engine speeds) to open the in take valve earlier for increased residual dilution and
close the intake valve earlier in the compression stroke for increased power. When the engine is cold,
opening the intake valve earlier warms the charge which improves fuel vaporization for less HC
emissions; when the engine is warm, the residua l burned gasses limit peak combustion temperature to
reduce NOx formation.
The VCT system hardware consists of a contro l solenoid and a pulse ring on the camshaft. The PCM
calculates relative cam position using the CMP input to process variable reluctance sensor pulses coming
from the pulse ring mounted on the camshaft. Each pul se wheel has N + 1 teeth where N = the number of
cylinders per bank. The N equally spaced teeth are used for cam phasing; the remaining tooth is used to
determine cylinder # 1 position. Relative cam position is calculated by measuring the time between the
rising edge of profile ignition pickup (PIP ) and the falling edges of the VCT pulses.
VCT Diagnostic
The PCM continually calculates a cam position error value based on the difference between the desired
and actual position and uses this information to cal culate a commanded duty cycle for the VCT solenoid
valve. When energized, engine oil is allowed to flow to the VCT unit thereby advancing and retarding cam
timing. The VCT logic calculates the instantaneous va riance in actual cam position (the squared difference
between actual cam position and commanded cam position), then calculates the long term variance using a
rolling average filter (Exponentially Weighted Moving Average).
If the VCT system is stuck or operates with an consta nt error relative to the target position, the monitor
will detect a variance which will quickly accumulate. There are three variance indices that monitor cam
variance in the retard direction, the advance directi on, and for V engines, the difference between banks. If
any variance index is greater than the malfunction threshold, a VCT target error malfunction will be
indicated (P0011, P0012 Bank 1, P0021, P0022 Bank 2).
The VCT solenoid output driver in the PCM is check ed electrically for open circuit and shorts (P0010
Bank 1, P0020 Bank 2).
VCT Monitor Operation: