check engine ASTON MARTIN V8 VANTAGE 2010 Manual PDF
[x] Cancel search | Manufacturer: ASTON MARTIN, Model Year: 2010, Model line: V8 VANTAGE, Model: ASTON MARTIN V8 VANTAGE 2010Pages: 947, PDF Size: 43.21 MB
Page 921 of 947
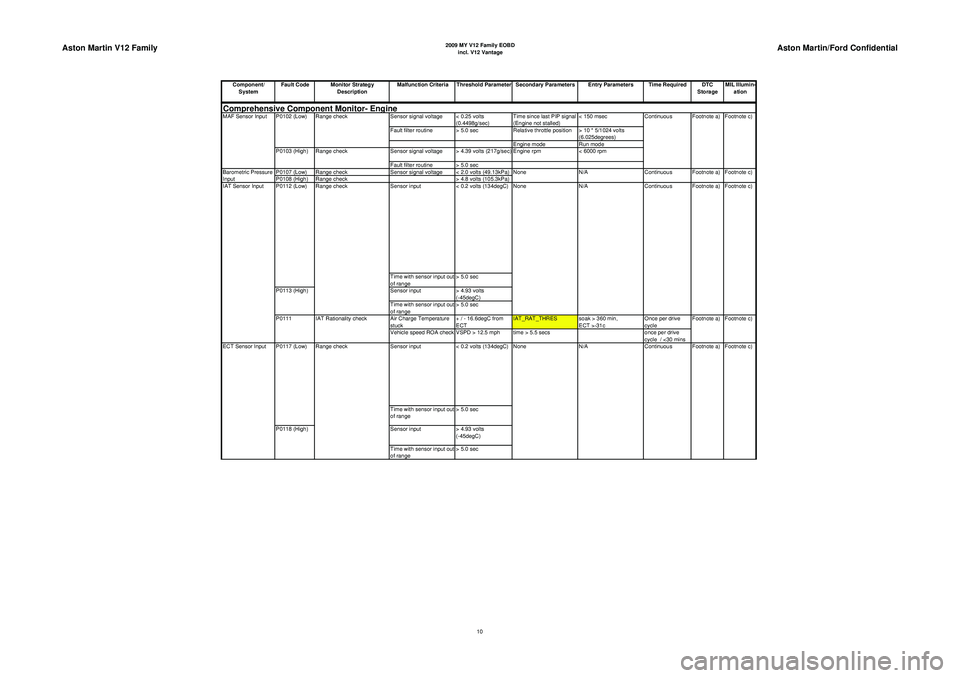
Aston Martin V12 Family
2009 MY V12 Family EOBDincl. V12 Vantage
Aston Martin/Ford Confidential
Component/ System Fault Code Monitor Strategy
Description Malfunction Criteria Threshold Parameter Secondary Parameters Entry Parameters Time Required DTC
StorageMIL Illumin-
ation
Sensor signal voltage < 0.25 volts (0.4498g/sec)Time since last PIP signal
(Engine not stalled) < 150 msec
Fault filter routine > 5.0 sec Relative throttle position > 10 * 5/1024 volts
(6.025degrees)
Engine mode Run mode
Sensor signal voltage > 4.39 volts (217g/sec) Engine rpm < 6000 rpm
Fault filter routine > 5.0 sec
P0107 (Low) Range check Sensor signal voltage < 2.0 volts (49.13kPa)
P0108 (High) Range check > 4.8 volts (105.3kPa) Sensor input < 0.2 volts (134degC)
Time with sensor input out
of range> 5.0 sec
Sensor input > 4.93 volts (-45degC)
Time with sensor input out
of range > 5.0 sec
Air Charge Temperature
stuck + / - 16.6degC from
ECT IAT_RAT_THRES soak > 360 min,
ECT >-31cOnce per drive
cycle
Vehicle speed ROA check VSPD > 12.5 mph time > 5.5 secs once per drive
cycle / <30 mins
Sensor input < 0.2 volts (134degC)
Time with sensor input out
of range > 5.0 sec
Sensor input > 4.93 volts
(-45degC)
Time with sensor input out
of range > 5.0 sec Footnote a) Footnote c)
None N/A Continuous
Com
prehensive Com
ponent Monitor- En
gine
MAF Sensor Input P0102 (Low)
P0103 (High)Range check
Range check Continuous
Footnote a) Footnote c)
IAT Sensor Input P0112 (Low)
P0113 (High)
P0111Range check
NoneN/A
Barometric Pressure
Input
Continuous Footnote a) Footnote c)
IAT Rationality check Footnote a) Footnote c)
Footnote a)
ECT Sensor Input P0117 (Low)
P0118 (High)Range check
Footnote c)
None N/A Continuous
10
Page 922 of 947
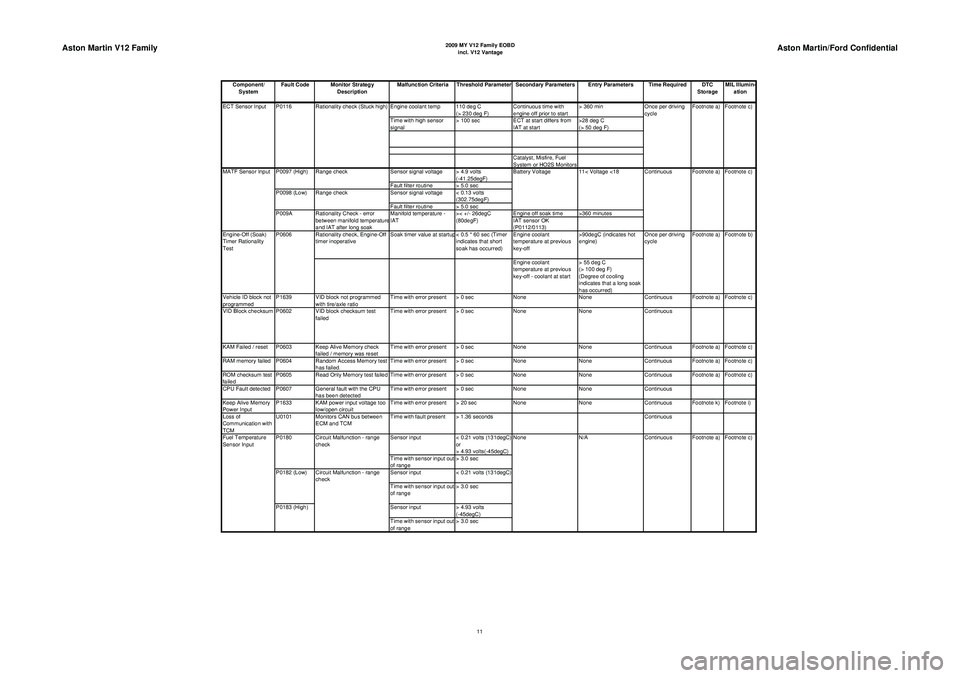
Aston Martin V12 Family
2009 MY V12 Family EOBDincl. V12 Vantage
Aston Martin/Ford Confidential
Component/ System Fault Code Monitor Strategy
Description Malfunction Criteria Threshold Parameter Secondary Parameters Entry Parameters Time Required DTC
StorageMIL Illumin-
ation
Engine coolant temp 110 deg C (> 230 deg F)Continuous time with
engine off prior to start > 360 min
Time with high sensor
signal > 100 sec
ECT at start differs from
IAT at start >28 deg C
(> 50 deg F)
Catalyst, Misfire, Fuel
System or HO2S Monitors
Sensor signal voltage > 4.9 volts (-41.25degF)
Fault filter routine > 5.0 sec
Sensor signal voltage < 0.13 volts (302.75degF)
Fault filter routine > 5.0 sec Engine off soak time >360 minutes
IAT sensor OK
(P0112/0113)
Rationality check, Engine-Off
timer inoperative Soak timer value at startup < 0.5 * 60 sec (Timer
indicates that short
soak has occurred)Engine coolant
temperature at previous
key-off >90degC (indicates hot
engine)
Engine coolant
temperature at previous
key-off - coolant at start > 55 deg C
(> 100 deg F)
(Degree of cooling
indicates that a long soak
has occurred)
Vehicle ID block not
programmed P1639 VID block not programmed
with tire/axle ratio Time with error present > 0 sec
NoneNoneContinuous Footnote a) Footnote c)
VID Block checksum P0602 VID block checksum test failedTime with error present > 0 sec
NoneNoneContinuous
KAM Failed / reset P0603 Keep Alive Memory check failed / memory was resetTime with error present > 0 sec
NoneNoneContinuous Footnote a) Footnote c)
RAM memory failed P0604 Random Access Memory test has failed.Time with error present > 0 sec
NoneNoneContinuous Footnote a) Footnote c)
ROM checksum test
failed P0605 Read Only Memory test failed Time with error present > 0 sec
NoneNoneContinuous Footnote a) Footnote c)
CPU Fault detected P0607 General fault with the CPU has been detectedTime with error present > 0 sec
NoneNoneContinuous
Keep Alive Memory
Power Input P1633 KAM power input voltage too
low/open circuit Time with error present > 20 sec
NoneNoneContinuous Footnote k) Footnote i)
Loss of
Communication with
TCM U0101 Monitors CAN bus between
ECM and TCM Time with fault present > 1.36 seconds
Continuous
Sensor input < 0.21 volts (131degC)
or
> 4.93 volts(-45degC)
Time with sensor input out
of range > 3.0 sec
Sensor input < 0.21 volts (131degC)
Time with sensor input out
of range > 3.0 sec
Sensor input > 4.93 volts
(-45degC)
Time with sensor input out
of range > 3.0 sec 11< Voltage <18 Continuous Footnote a) Footnote c)
MATF Sensor Input P0097 (High) Range check Battery Voltage
P0098 (Low) Range check
P009A Rationality Check - error between manifold temperature
and IAT after long soak Manifold temperature -
IAT
>< +/- 26degC
(80degF)
ECT Sensor Input P0116 Rationality check (Stuck high)
Once per driving
cycleFootnote a) Footnote c)
Engine-Off (Soak)
Timer Rationality
Test P0606
Once per driving
cycleFootnote a) Footnote b)
Fuel Temperature
Sensor Input P0180
P0182 (Low)
P0183 (High)Circuit Malfunction - range
check
Circuit Malfunction - range
check
None
N/A Continuous Footnote a) Footnote c)
11
Page 923 of 947
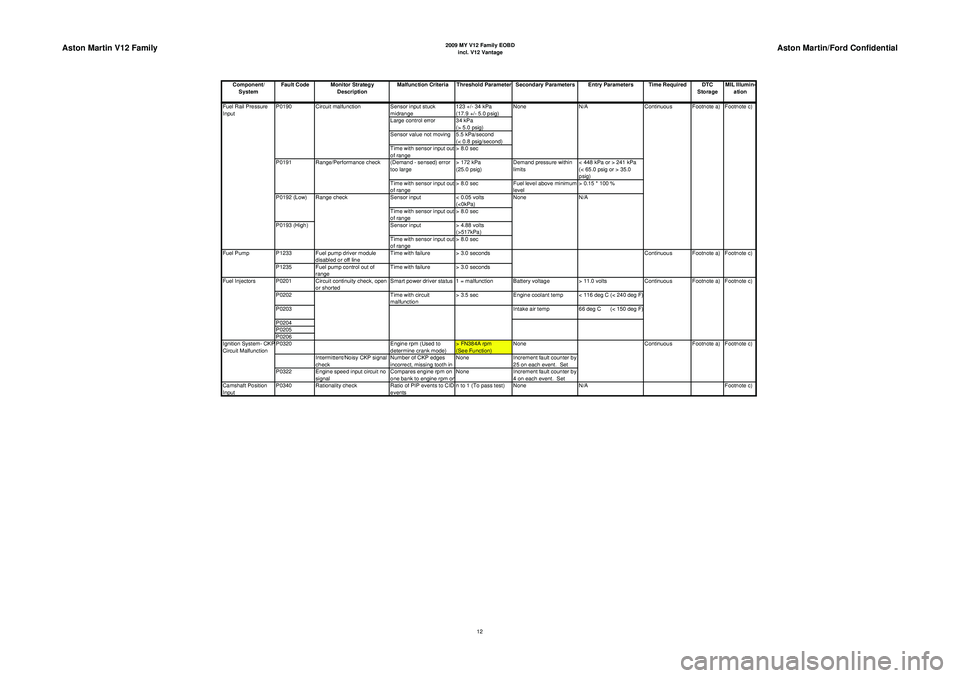
Aston Martin V12 Family
2009 MY V12 Family EOBDincl. V12 Vantage
Aston Martin/Ford Confidential
Component/ System Fault Code Monitor Strategy
Description Malfunction Criteria Threshold Parameter Secondary Parameters Entry Parameters Time Required DTC
StorageMIL Illumin-
ation
Sensor input stuck
midrange 123 +/- 34 kPa
(17.9 +/- 5.0 psig)
Large control error 34 kPa (> 5.0 psig)
Sensor value not moving 5.5 kPa/second (< 0.8 psig/second)
Time with sensor input out
of range > 8.0 sec
(Demand - sensed) error
too large > 172 kPa
(25.0 psig)Demand pressure within
limits < 448 kPa or > 241 kPa
(< 65.0 psig or > 35.0
psig)
Time with sensor input out
of range > 8.0 sec
Fuel level above minimum
level > 0.15 * 100 %
Sensor input < 0.05 volts
(<0kPa)
Time with sensor input out
of range > 8.0 sec
Sensor input > 4.88 volts
(>517kPa)
Time with sensor input out
of range > 8.0 sec
P1233 Fuel pump driver module disabled or off line Time with failure > 3.0 seconds
P1235 Fuel pump control out of range Time with failure > 3.0 seconds
P0201 Circuit continuity check, open or shorted Smart power driver status 1 = malfunction Battery voltage
> 11.0 volts
P0202 Time with circuit
malfunction > 3.5 sec
Engine coolant temp < 116 deg C (< 240 deg F)
P0203 Intake air temp66 deg C (< 150 deg F)
P0204
P0205
P0206
P0320 Engine rpm (Used to
determine crank mode) > FN384A rpm
(See Function)None
Intermittent/Noisy CKP signal
check Number of CKP edges
incorrect, missing tooth in None
Increment fault counter by
25 on each event. Set
P0322 Engine speed input circuit no signal Compares engine rpm on
one bank to engine rpm o
nNone
Increment fault counter by
4 on each event. Set
Camshaft Position
Input P0340 Rationality check
Ratio of PIP events to CID
events n to 1 (To pass test) None
N/A Footnote c)
Footnote c)
Fuel Rail Pressure
Input P0190
P0191
P0192 (Low)
P0193 (High)Range check
Range/Performance check
Fuel Pump Continuous
Circuit malfunction N/A
Continuous Footnote a) Footnote c)
None
None
N/A Footnote a)
Fuel Injectors Footnote c)
Ignition System- CKP
Circuit Malfunction Continuous Footnote a) Footnote c)
Continuous Footnote a)
12
Page 924 of 947
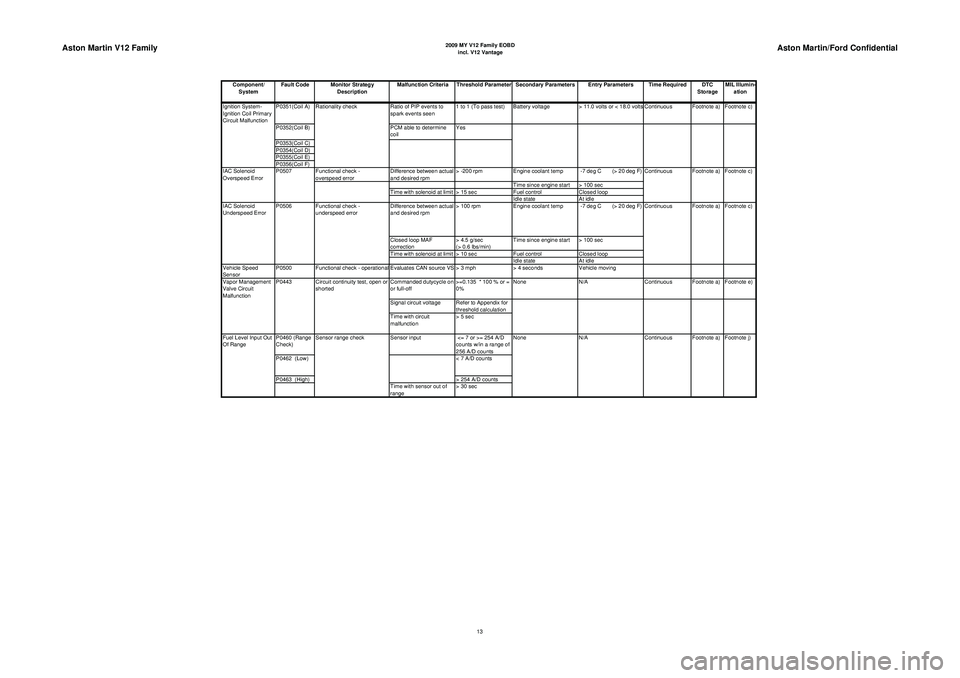
Aston Martin V12 Family
2009 MY V12 Family EOBDincl. V12 Vantage
Aston Martin/Ford Confidential
Component/ System Fault Code Monitor Strategy
Description Malfunction Criteria Threshold Parameter Secondary Parameters Entry Parameters Time Required DTC
StorageMIL Illumin-
ation
P0351(Coil A) Ratio of PIP events to
spark events seen 1 to 1 (To pass test) Battery voltage
> 11.0 volts or < 18.0 volts Continuous Footnote a) Footnote c)
P0352(Coil B) PCM able to determine
coil Yes
P0353(Coil C)
P0354(Coil D)
P0355(Coil E)
P0356(Coil F) Functional check -
overspeed error Difference between actual
and desired rpm> -200 rpm
Engine coolant temp -7 deg C (> 20 deg F)
Time since engine start > 100 sec
Time with solenoid at limit > 15 sec Fuel controlClosed loop
Idle state At idle
Difference between actual
and desired rpm > 100 rpm
Engine coolant temp -7 deg C (> 20 deg F)
Closed loop MAF
correction > 4.5 g/sec
(> 0.6 lbs/min)Time since engine start > 100 sec
Time with solenoid at limit > 10 sec Fuel controlClosed loop
Idle state At idle
Vehicle Speed
Sensor P0500 Functional check - operational Evaluates CAN source VS > 3 mph
> 4 secondsVehicle moving
Commanded dutycycle on
or full-off >=0.135 * 100 % or =
0%None
N/A Continuous Footnote a) Footnote e)
Signal circuit voltage Refer to Appendix for threshold calculation
Time with circuit
malfunction > 5 sec
P0460 (Range
Check) Sensor input
<= 7 or >= 254 A/D
counts w/in a range of
256 A/D counts
P0462 (Low) < 7 A/D counts
P0463 (High) > 254 A/D counts
Time with sensor out of
range > 30 sec N/A
Continuous Footnote a) Footnote j)
Fuel Level Input Out
Of Range Sensor range check
None
Vapor Management
Valve Circuit
Malfunction
P0443 Circuit continuity test, open or
shorted Footnote a) Footnote c)
IAC Solenoid
Underspeed Error P0506 Functional check -
underspeed error Continuous
IAC Solenoid
Overspeed Error
P0507
Continuous Footnote a) Footnote c)
Ignition System-
Ignition Coil Primary
Circuit Malfunction
Rationality check
13
Page 926 of 947
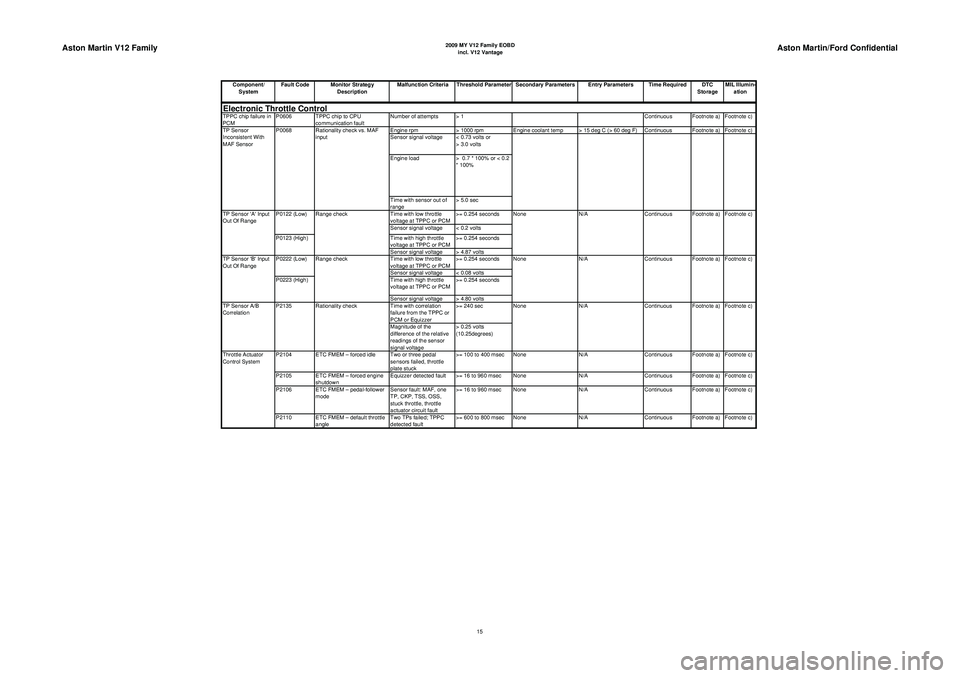
Aston Martin V12 Family
2009 MY V12 Family EOBDincl. V12 Vantage
Aston Martin/Ford Confidential
Component/ System Fault Code Monitor Strategy
Description Malfunction Criteria Threshold Parameter Secondary Parameters Entry Parameters Time Required DTC
StorageMIL Illumin-
ationTPPC chip failure in
PCM P0606 TPPC chip to CPU
communication fault Number of attempts > 1
Continuous Footnote a) Footnote c)
Engine rpm > 1000 rpmEngine coolant temp > 15 deg C (> 60 deg F) Continuous Footnote a) Footnote c)
Sensor signal voltage < 0.73 volts or > 3.0 volts
Engine load > 0.7 * 100% or < 0.2
* 100%
Time with sensor out of
range > 5.0 sec
Time with low throttle
voltage at TPPC or PCM >= 0.254 seconds
Sensor signal voltage < 0.2 volts
Time with high throttle
voltage at TPPC or PCM >= 0.254 seconds
Sensor signal voltage > 4.87 volts
Time with low throttle
voltage at TPPC or PCM >= 0.254 seconds
Sensor signal voltage < 0.08 volts
Time with high throttle
voltage at TPPC or PCM >= 0.254 seconds
Sensor signal voltage > 4.80 volts
Time with correlation
failure from the TPPC or
PCM or Equizzer >= 240 sec
Magnitude of the
difference of the relative
readings of the sensor
signal voltage > 0.25 volts
(10.25degrees)
P2104 ETC FMEM – forced idle Two or three pedal sensors failed, throttle
plate stuck>= 100 to 400 msec None
N/AContinuous Footnote a) Footnote c)
P2105 ETC FMEM – forced engine shutdown Equizzer detected fault >= 16 to 960 msec None
N/AContinuous Footnote a) Footnote c)
P2106 ETC FMEM – pedal-follower mode Sensor fault: MAF, one
TP, CKP, TSS, OSS,
stuck throttle, throttle
actuator circuit fault>= 16 to 960 msec None
N/AContinuous Footnote a) Footnote c)
P2110 ETC FMEM – default throttle angle Two TPs failed; TPPC
detected fault>= 600 to 800 msec None
N/AContinuous Footnote a) Footnote c)
Throttle Actuator
Control SystemElectronic Throttle ControlTP Sensor A/B
Correlation
P2135 Rationality check None N/A Continuous Footnote a) Footnote c) Footnote c)
TP Sensor 'B' Input
Out Of Range P0222 (Low)
P0223 (High)Range check None N/A Continuous Footnote a) Footnote c) None N/A Continuous Footnote a)
TP Sensor 'A' Input
Out Of Range P0122 (Low)
P0123 (High)Range check
TP Sensor
Inconsistent With
MAF Sensor
P0068 Rationality check vs. MAF
input
15
Page 933 of 947
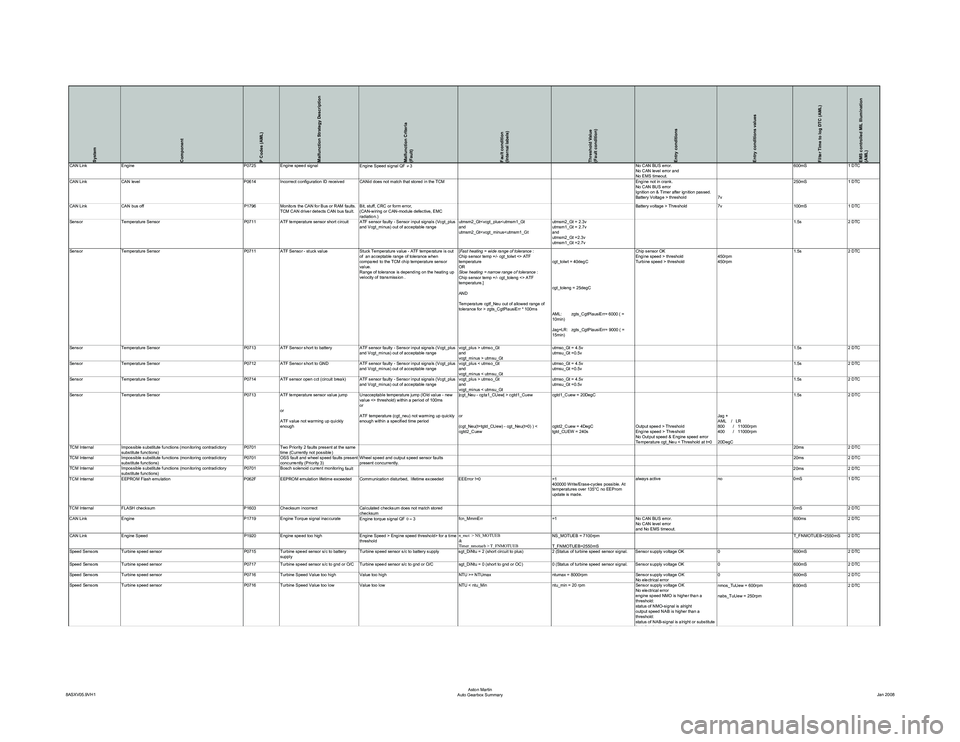
System
Component
P Codes (AML)
Malfunction Strategy Description
Malfunction Criteria
(Fault)
Fault condition
(Internal labels)
Threshold Value
(Fault condition)
Entry conditions
Entry conditions values
Filter Time to log DTC (AML)
EMS controlled MIL Illumination
(AML)
CAN LinkEngine P0725Engine speed signal
Engine Speed signal QF ≠ 3 No CAN BUS error.
No CAN level error and
No EMS timeout.600mS
1 DTC
CAN Link CAN level P0614Incorrect configuration ID received CANid does not match that stored in the TCM Engine not in crank.
No CAN BUS error
Ignition on & Timer after ignition passed.
Battery Voltage > threshold7v250mS
1 DTC
CAN Link CAN bus off P1796Monitors the CAN for Bus or RAM faults.
TCM CAN driver detects CAN bus fault. Bit, stuff, CRC or form error,
(CAN-wiring or CAN-module defective, EMC
radiation.) Battery voltage > Threshold
7v100mS1 DTC
Sensor Temperature Sensor P0711 ATF temperature sensor short circuit ATF sensor faulty - Sensor input signals (Vcgt_plus
and Vcgt_minus) out of acceptable range utmsm2_Gt
utmsm2_Gt
and
utmsm2_Gt =2.3v
utmsm1_Gt =2.7v 1.5s
2 DTC
Sensor Temperature Sensor P0711ATF Sensor - stuck value Stuck Temperature value - ATF temperature is out
of an acceptable range of tolerance when
compared to the TCM chip temperature sensor
value.
Range of tolerance is depending on the heating up
velocity of transmission . [
Fast heating = wide range of tolerance :
Chip sensor temp +/- cgt_tolwt <> ATF
temperature
OR
Slow heating = narrow range of tolerance :
Chip sensor temp +/- cgt_toleng <> ATF
temperature.]
AND
Temperature cgtf_Neu out of allowed range of
tolerance for > zgts_CgtPlausiErr * 100ms cgt_tolwt = 40degC
cgt_toleng = 25degC
AML: zgts_CgtPlausiErr= 6000 ( =
10min)
Jag+LR: zgts_CgtPlausiErr= 9000 ( =
15min)Chip sensor OK
Engine speed > threshold
Turbine speed > threshold
450rpm
450rpm1.5s
2 DTC
Sensor Temperature Sensor P0713ATF Sensor short to battery ATF sensor faulty - Sensor input signals (Vcgt_plus
and Vcgt_minus) out of acceptable range vcgt_plus > utmso_Gt
and
vcgt_minus > utmsu_Gtutmso_Gt = 4.5v
utmsu_Gt =0.5v
1.5s
2 DTC
Sensor Temperature Sensor P0712ATF Sensor short to GND ATF sensor faulty - Sensor input signals (Vcgt_plus
and Vcgt_minus) out of acceptable range vcgt_plus < utmso_Gt
and
vcgt_minus < utmsu_Gtutmso_Gt = 4.5v
utmsu_Gt =0.5v
1.5s
2 DTC
Sensor Temperature Sensor P0714ATF sensor open cct (circuit break) ATF sensor faulty - Sensor input signals (Vcgt_plus
and Vcgt_minus) out of acceptable range vcgt_plus > utmso_Gt
and
vcgt_minus < utmsu_Gtutmso_Gt = 4.5v
utmsu_Gt =0.5v
1.5s
2 DTC
Sensor Temperature Sensor P0713 ATF temperature sensor value jump
or
ATF value not warming up quickly
enough Unacceptable temperature jump (lOld value - new
value <> threshold) within a period of 100ms
or
ATF temperature (cgt_neu) not warming up quickly
enough within a specified time period
|cgt_Neu - cgta1_CUew| > cgtd1_Cuew
or
(cgt_Neu(t=tgtd_CUew) - cgt_Neu(t=0) ) <
cgtd2_Cuewcgtd1_Cuew = 20DegC
cgtd2_Cuew = 4DegC
tgtd_CUEW = 240s
Output speed > Threshold
Engine speed > Threshold
No Output speed & Engine speed error
Temperature cgt_Neu < Threshold at t=0Jag +
AML / LR
800 / 11000rpm
400 / 11000rpm
20DegC1.5s
2 DTC
TCM Internal Impossible substitute functions (monitoring contradictory
substitute functions) P0701
Two Priority 2 faults present at the same
time (Currently not possible) 20ms
2 DTC
TCM Internal Impossible substitute functions (monitoring contradictory
substitute functions) P0701
OSS fault and wheel speed faults present
concurrently (Priority 3) Wheel speed and output speed sensor faults
present concurrently. 20ms
2 DTC
TCM Internal Impossible substitute functions (monitoring contradictory
substitute functions) P0701
Bosch solenoid current monitorin
g fault 20ms 2 DTC
TCM Internal EEPROM Flash emulation P062FEEPROM emulation lifetime exceeded Communication disturbed, lifetime exceeded EEError !=0 =1
400000 Write/Erase-cycles possible. At
temperatures over 135°C no EEProm
update is made.always active
no0mS1 DTC
TCM Internal FLASH checksum P1603Checksum incorrect Calculated checksum does not match stored
checksum 0mS
2 DTC
CAN Link Engine P1719Engine Torque signal inaccurate
Engine torque signal QF 0 = 3 fcn_MmmErr
=1No CAN BUS error.
No CAN level error
and No EMS timeout. 600ms
2 DTC
CAN Link Engine Speed P1920Engine speed too high Engine Speed > Engine speed threshold> for a time
threshold n_mot > NS_MOTUEB
&
Timer_nmotueb > T_FNMOTUEBNS_MOTUEB = 7100rpm
T_FNMOTUEB=2550mS T_FNMOTUEB=2550mS 2 DTC
Speed Sensors Turbine speed sensor P0715Turbine speed sensor s/c to battery
supply Turbine speed sensor s/c to battery supply sgt_DiNtu = 2 (short circuit to plus)
2 (Status of turbine speed sensor signal. Sensor supply voltage OK0600mS2 DTC
Speed Sensors Turbine speed sensor P0717Turbine speed sensor s/c to gnd or O/C Turbine speed sensor s/c to gnd or O/C sgt_DiNtu = 0 (short to gnd or OC)0 (Status of turbine speed sensor signal. Sensor supply voltage OK 0600mS2 DTC
Speed Sensors Turbine speed sensor P0716Turbine Speed Value too high Value too high NTU >= NTUmaxntumax = 8000rpmSensor supply voltage OK
No electrical error 0
600mS2 DTC
Speed Sensors Turbine speed sensor P0716Turbine Speed Value too low Value too low NTU < ntu_Minntu_min = 20 rpmSensor supply voltage OK
No electrical error
engine speed NMO is higher than a
threshold:
status of NMO-signal is alright
output speed NAB is higher than a
threshold:
status of NAB-signal is alright or substitute
fltfl fb Ei t t
nmos_TuUew = 600rpm
nabs_TuUew = 250rpm 600mS
2 DTC
8ASXV05.9VH1 Aston Martin
Auto Gearbox Summary Jan 2008
Page 936 of 947
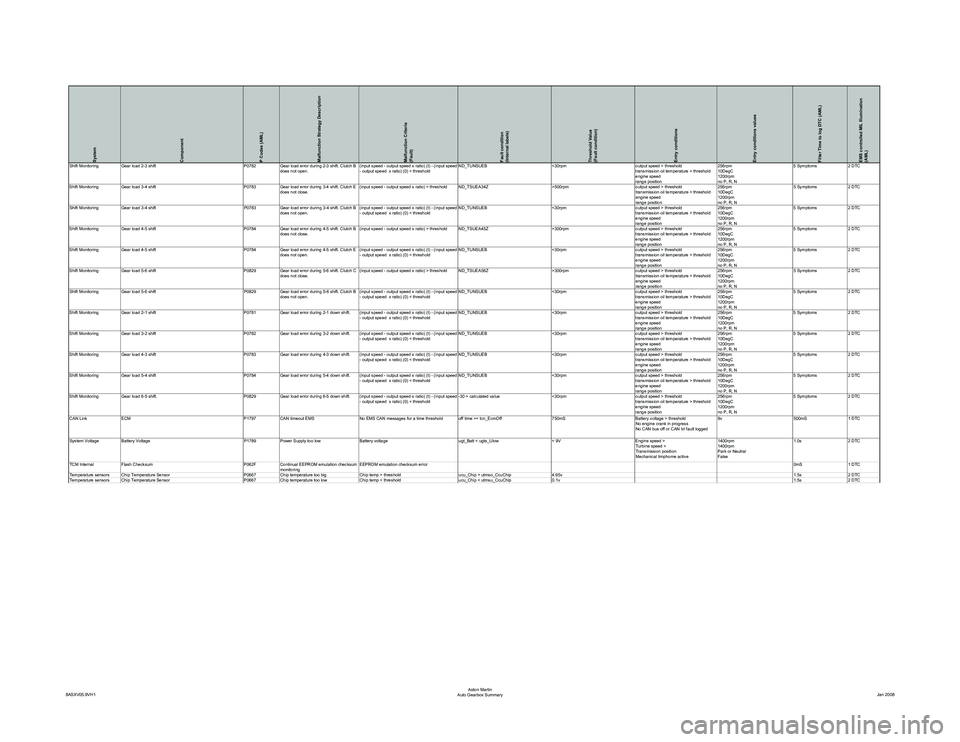
System
Component
P Codes (AML)
Malfunction Strategy Description
Malfunction Criteria
(Fault)
Fault condition
(Internal labels)
Threshold Value
(Fault condition)
Entry conditions
Entry conditions values
Filter Time to log DTC (AML)
EMS controlled MIL Illumination
(AML)
(input speed - output speed x ratio
) (t) - (input speed
- output speed x ratio) (0) < threshold ND_TUNSUEB
<30rpmoutput speed > threshold
transmission oil temperature > threshold
engine speed
range position 256rpm
10DegC
1200rpm
no P, R, N5 Symptoms
2 DTC
Shift Monitoring Gear load 4-5 shift P0784Gear load error during 4-5 shift. Clutch B
does not close. (input speed - output speed x ratio) > threshold ND_TSUEA45Z
>300rpmoutput speed > threshold
transmission oil temperature > threshold
engine speed
range position 256rpm
10DegC
1200rpm
no P, R, N5 Symptoms
2 DTC
Shift Monitoring Gear load 4-5 shift P0784Gear load error during 4-5 shift. Clutch E
does not open.
(input speed - output speed x ratio
) (t) - (input speed
- output speed x ratio) (0) < threshold ND_TUNSUEB
<30rpmoutput speed > threshold
transmission oil temperature > threshold
engine speed
range position 256rpm
10DegC
1200rpm
no P, R, N5 Symptoms
2 DTC
Shift Monitoring Gear load 5-6 shift P0829Gear load error during 5-6 shift. Clutch C
does not close. (input speed - output speed x ratio) > threshold ND_TSUEA56Z
>300rpmoutput speed > threshold
transmission oil temperature > threshold
engine speed
range position 256rpm
10DegC
1200rpm
no P, R, N5 Symptoms
2 DTC
Shift Monitoring Gear load 5-6 shift P0829Gear load error during 5-6 shift. Clutch B
does not open.
(input speed - output speed x ratio
) (t) - (input speed
- output speed x ratio) (0) < threshold ND_TUNSUEB
<30rpmoutput speed > threshold
transmission oil temperature > threshold
engine speed
range position 256rpm
10DegC
1200rpm
no P, R, N5 Symptoms
2 DTC
Shift Monitoring Gear load 2-1 shift P0781Gear load error during 2-1 down shift.
(input speed - output speed x ratio
) (t) - (input speed
- output speed x ratio) (0) < threshold ND_TUNSUEB
<30rpmoutput speed > threshold
transmission oil temperature > threshold
engine speed
range position 256rpm
10DegC
1200rpm
no P, R, N5 Symptoms
2 DTC
Shift Monitoring Gear load 3-2 shift P0782Gear load error during 3-2 down shift.
(input speed - output speed x ratio
) (t) - (input speed
- output speed x ratio) (0) < threshold ND_TUNSUEB
<30rpmoutput speed > threshold
transmission oil temperature > threshold
engine speed
range position 256rpm
10DegC
1200rpm
no P, R, N5 Symptoms
2 DTC
Shift Monitoring Gear load 4-3 shift P0783Gear load error during 4-3 down shift.
(input speed - output speed x ratio
) (t) - (input speed
- output speed x ratio) (0) < threshold ND_TUNSUEB
<30rpmoutput speed > threshold
transmission oil temperature > threshold
engine speed
range position 256rpm
10DegC
1200rpm
no P, R, N5 Symptoms
2 DTC
Shift Monitoring Gear load 5-4 shift P0784Gear load error during 5-4 down shift.
(input speed - output speed x ratio
) (t) - (input speed
- output speed x ratio) (0) < threshold ND_TUNSUEB
<30rpmoutput speed > threshold
transmission oil temperature > threshold
engine speed
range position 256rpm
10DegC
1200rpm
no P, R, N5 Symptoms
2 DTC
Shift Monitoring Gear load 6-5 shift. P0829Gear load error during 6-5 down shift.
(input speed - output speed x ratio
) (t) - (input speed
- output speed x ratio) (0) < threshold -30 > calculated value
<30rpmoutput speed > threshold
transmission oil temperature > threshold
engine speed
range position 256rpm
10DegC
1200rpm
no P, R, N5 Symptoms
2 DTC
CAN Link ECM P1797CAN timeout EMS No EMS CAN messages for a time threshold off time >= tcn_EcmOff 750mSBattery voltage > threshold
No engine crank in progress
No CAN bus off or CAN lvl fault logged 9v
500mS1 DTC
System Voltage Battery Voltage P1789Power Supply too low Battery voltage ugt_Batt < ugts_Ulow< 9VEngine speed >
Turbine speed >
Transmission position
Mechanical limphome active 1400rpm
1400rpm
Park or Neutral
False1.0s
2 DTC
TCM Internal Flash Checksum P062FContinual EEPROM emulation checksum
monitoring EEPROM emulation checksum error
0mS1 DTC
Temperature sensors Chip Temperature Sensor P0667 Chip temperature too big Chip temp > threshold ucu_Chip > utmso_CcuChip4.95v 1.5s2 DTC
Temperature sensors Chip Temperature Sensor P0667 Chip temperature too low Chip temp < threshold ucu_Chip < utmsu_CcuChip0.1v 1.5s2 DTC
8ASXV05.9VH1 Aston Martin
Auto Gearbox Summary Jan 2008