BATTERY SUPPLY ASTON MARTIN V8 VANTAGE 2010 Workshop Manual
[x] Cancel search | Manufacturer: ASTON MARTIN, Model Year: 2010, Model line: V8 VANTAGE, Model: ASTON MARTIN V8 VANTAGE 2010Pages: 947, PDF Size: 43.21 MB
Page 3 of 947
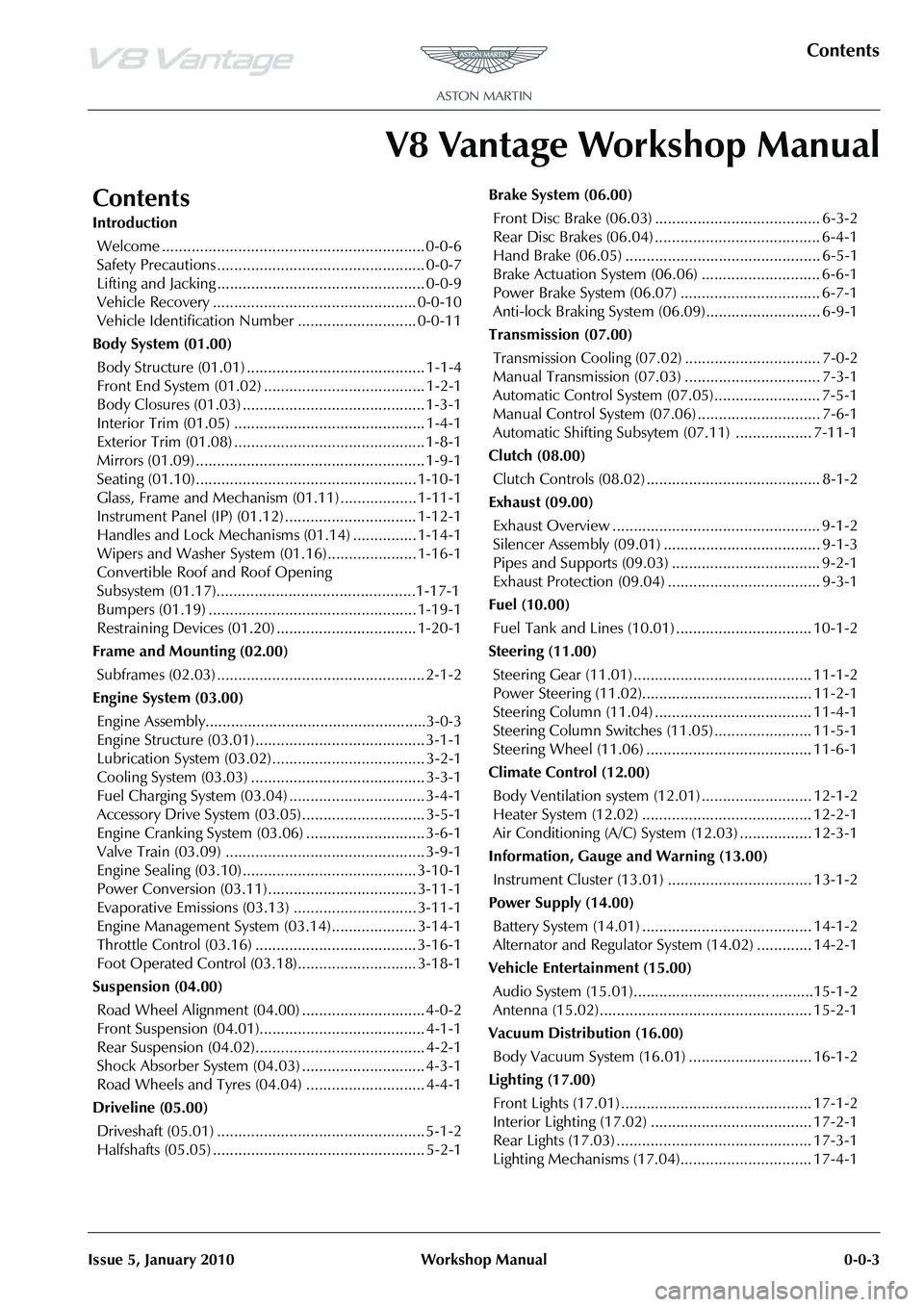
Contents
Issue 5, January 2010 Workshop Manual 0-0-3
V8 Vantage Workshop Manual
Contents
IntroductionWelcome .............................................................. 0-0-6
Safety Precautions ................................................. 0-0-7
Lifting and Jacking ................................................. 0-0-9
Vehicle Recovery ................................................ 0-0-10
Vehicle Identification Number ............................ 0-0-11
Body System (01.00) Body Structure (01.01) .......................................... 1-1-4
Front End System (01.02) ...................................... 1-2-1
Body Closures (01.03) ........................................... 1-3-1
Interior Trim (01.05) ............................................. 1-4-1
Exterior Trim (01.08) ............................................. 1-8-1
Mirrors (01.09) ...................................................... 1-9-1
Seating (01.10).................................................... 1-10-1
Glass, Frame and Mechanism (01.11) .................. 1-11-1
Instrument Panel (IP) (01.12) . .............................. 1-12-1
Handles and Lock Mechanisms (01.14) ............... 1-14-1
Wipers and Washer System (01.16)..................... 1-16-1
Convertible Roof and Roof Opening
Subsystem (01.17)................ ...............................1-17-1
Bumpers (01.19) ................................................. 1-19-1
Restraining Devices (01.20) .... ............................. 1-20-1
Frame and Mounting (02.00) Subframes (02.03) ................................................. 2-1-2
Engine System (03.00) Engine Assembly....................................................3-0-3
Engine Structure (03.01)........................................ 3-1-1
Lubrication System (03.02).................................... 3-2-1
Cooling System (03.03) ......................................... 3-3-1
Fuel Charging System (03.04) ................................ 3-4-1
Accessory Drive System (03.05)............................. 3-5-1
Engine Cranking System (03. 06) ............................ 3-6-1
Valve Train (03.09) ............................................... 3-9-1
Engine Sealing (03.10)......................................... 3-10-1
Power Conversion (03.11)................................... 3-11-1
Evaporative Emissions (03.13) ............................. 3-11-1
Engine Management System (0 3.14).................... 3-14-1
Throttle Control (03.16) ...... ................................ 3-16-1
Foot Operated Control (03.18)............................ 3-18-1
Suspension (04.00) Road Wheel Alignment (04.00) ............................. 4-0-2
Front Suspension (04.01)....................................... 4-1-1
Rear Suspension (04.02)........................................ 4-2-1
Shock Absorber System (04.03) ............................. 4-3-1
Road Wheels and Tyres (04.04) ............................ 4-4-1
Driveline (05.00) Driveshaft (05.01) ................................................. 5-1-2
Halfshafts (05.05) .................................................. 5-2-1 Brake System (06.00)
Front Disc Brake (06.03) ....................................... 6-3-2
Rear Disc Brakes (06.04) ....................................... 6-4-1
Hand Brake (06.05) .............................................. 6-5-1
Brake Actuation System (06.06 ) ............................ 6-6-1
Power Brake System (06.07) ................................. 6-7-1
Anti-lock Braking System (06.09)........................... 6-9-1
Transmission (07.00) Transmission Cooling (07.02) ................................ 7-0-2
Manual Transmission (07.03) ................................ 7-3-1
Automatic Control System (07.05)......................... 7-5-1
Manual Control System (07.06) ............................. 7-6-1
Automatic Shifting Subsytem (07.11) .................. 7-11-1
Clutch (08.00) Clutch Controls (08.02) ......................................... 8-1-2
Exhaust (09.00) Exhaust Overview ................................................. 9-1-2
Silencer Assembly (09.01) ..................................... 9-1-3
Pipes and Supports (09.03) ................................... 9-2-1
Exhaust Protection (09.04) .................................... 9-3-1
Fuel (10.00) Fuel Tank and Lines (10.01) ................................ 10-1-2
Steering (11.00) Steering Gear (11.01) .......................................... 11-1-2
Power Steering (11.02)........................................ 11-2-1
Steering Column (11.04) ..................................... 11-4-1
Steering Column Switches (1 1.05) ....................... 11-5-1
Steering Wheel (11.06) ....................................... 11-6-1
Climate Control (12.00) Body Ventilation system (12.01) .......................... 12-1-2
Heater System (12.02) ........................................ 12-2-1
Air Conditioning (A/C) System (12.03) ................. 12-3-1
Information, Gauge and Warning (13.00) Instrument Cluster (13.01) .................................. 13-1-2
Power Supply (14.00) Battery System (14.01) ........................................ 14-1-2
Alternator and Regulator System (14.02) ............. 14-2-1
Vehicle Entertainment (15.00) Audio System (15.01)................................ ..........15-1-2
Antenna (15.02).................................................. 15-2-1
Vacuum Distribution (16.00) Body Vacuum System (16.01) ............................. 16-1-2
Lighting (17.00) Front Lights (17.01) ............................................. 17-1-2
Interior Lighting (17.02) ...................................... 17-2-1
Rear Lights (17.03) .............................................. 17-3-1
Lighting Mechanisms (17.04). .............................. 17-4-1
Page 465 of 947
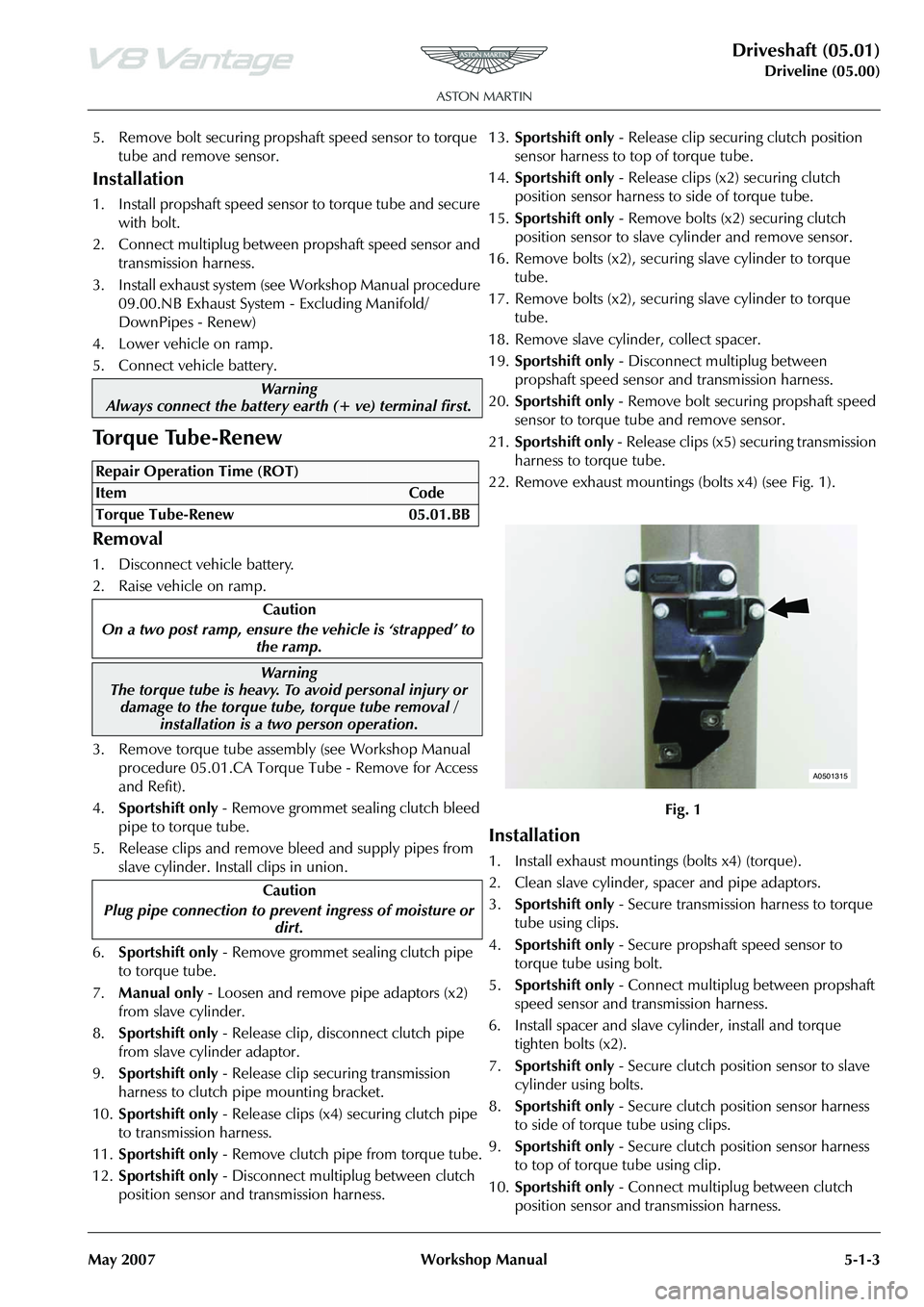
Driveshaft (05.01)
Driveline (05.00)
May 2007 Workshop Manual 5-1-3
5. Remove bolt securing propshaft speed sensor to torque tube and remove sensor.
Installation
1. Install propshaft speed sensor to torque tube and secure with bolt.
2. Connect multiplug between propshaft speed sensor and transmission harness.
3. Install exhaust system (see Workshop Manual procedure 09.00.NB Exhaust System - Excluding Manifold/
DownPipes - Renew)
4. Lower vehicle on ramp.
5. Connect vehicle battery.
To r q u e Tu b e - R e n e w
Removal
1. Disconnect vehicle battery.
2. Raise vehicle on ramp.
3. Remove torque tube assemb ly (see Workshop Manual
procedure 05.01.CA Torque Tube - Remove for Access
and Refit).
4. Sportshift only - Remove grommet sealing clutch bleed
pipe to torque tube.
5. Release clips and remove bleed and supply pipes from slave cylinder. Install clips in union.
6. Sportshift only - Remove grommet sealing clutch pipe
to torque tube.
7. Manual only - Loosen and remove pipe adaptors (x2)
from slave cylinder.
8. Sportshift only - Release clip, disconnect clutch pipe
from slave cylinder adaptor.
9. Sportshift only - Release clip securing transmission
harness to clutch pipe mounting bracket.
10. Sportshift only - Release clips (x4) securing clutch pipe
to transmission harness.
11. Sportshift only - Remove clutch pipe from torque tube.
12. Sportshift only - Disconnect multiplug between clutch
position sensor and transmission harness. 13.
Sportshift only - Release clip securing clutch position
sensor harness to top of torque tube.
14. Sportshift only - Release clips (x2) securing clutch
position sensor harness to side of torque tube.
15. Sportshift only - Remove bolts (x2) securing clutch
position sensor to slave cylinder and remove sensor.
16. Remove bolts (x2), securing slave cylinder to torque tube.
17. Remove bolts (x2), securing slave cylinder to torque tube.
18. Remove slave cylinder, collect spacer.
19. Sportshift only - Disconnect multiplug between
propshaft speed sensor and transmission harness.
20. Sportshift only - Remove bolt securing propshaft speed
sensor to torque tube and remove sensor.
21. Sportshift only - Release clips (x5) securing transmission
harness to torque tube.
22. Remove exhaust mountings (bolts x4) (see Fig. 1).
Installation
1. Install exhaust mounting s (bolts x4) (torque).
2. Clean slave cylinder, spacer and pipe adaptors.
3. Sportshift only - Secure transmission harness to torque
tube using clips.
4. Sportshift only - Secure propshaft speed sensor to
torque tube using bolt.
5. Sportshift only - Connect multiplug between propshaft
speed sensor and transmission harness.
6. Install spacer and slave cylinder, install and torque tighten bolts (x2).
7. Sportshift only - Secure clutch position sensor to slave
cylinder using bolts.
8. Sportshift only - Secure clutch position sensor harness
to side of torque tube using clips.
9. Sportshift only - Secure clutch position sensor harness
to top of torque tube using clip.
10. Sportshift only - Connect multiplug between clutch
position sensor and transmission harness.
Warning
Always connect the battery ea rth (+ ve) terminal first.
Repair Operation Time (ROT)
Warning
The torque tube is heavy. To avoid personal injury or damage to the torque tube, torque tube removal / installation is a two person operation.
Caution
Plug pipe connection to prevent ingress of moisture or dirt.
Fig. 1
$
Page 466 of 947
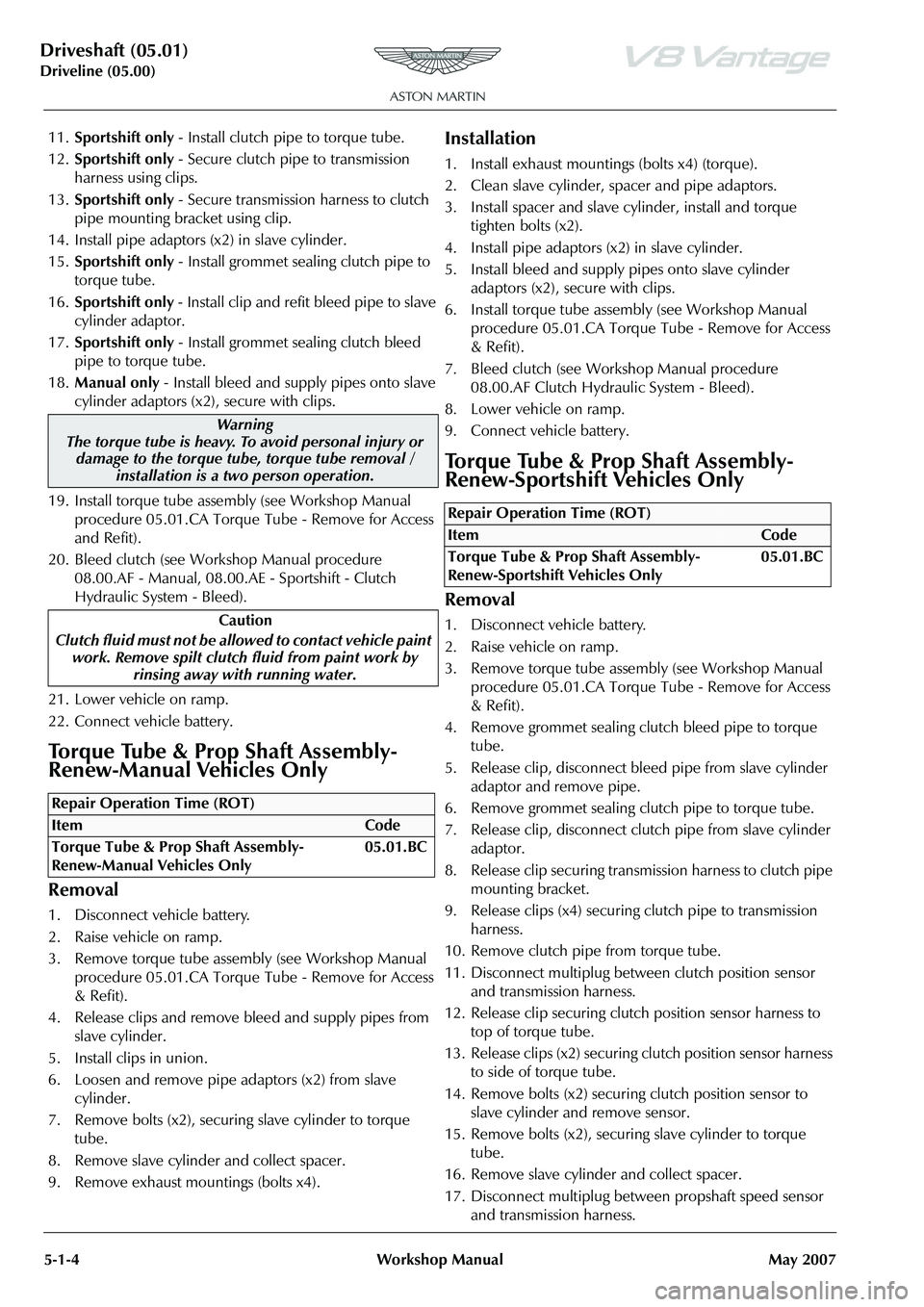
Driveshaft (05.01)
Driveline (05.00)5-1-4 Workshop Manual May 2007
11. Sportshift only - Install clutch pipe to torque tube.
12. Sportshift only - Secure clutch pipe to transmission
harness using clips.
13. Sportshift only - Secure transmission harness to clutch
pipe mounting bracket using clip.
14. Install pipe adaptors (x2) in slave cylinder.
15. Sportshift only - Install grommet sealing clutch pipe to
torque tube.
16. Sportshift only - Install clip and refit bleed pipe to slave
cylinder adaptor.
17. Sportshift only - Install grommet sealing clutch bleed
pipe to torque tube.
18. Manual only - Install bleed and supply pipes onto slave
cylinder adaptors (x2), secure with clips.
19. Install torque tube assembly (see Workshop Manual procedure 05.01.CA Torque Tube - Remove for Access
and Refit).
20. Bleed clutch (see Workshop Manual procedure 08.00.AF - Manual, 08.00.AE - Sportshift - Clutch
Hydraulic System - Bleed).
21. Lower vehicle on ramp.
22. Connect vehicle battery.
Torque Tube & Prop Shaft Assembly-
Renew
-Manual Vehicles Only
Removal
1. Disconnect vehicle battery.
2. Raise vehicle on ramp.
3. Remove torque tube assembly (see Workshop Manual procedure 05.01.CA Torque Tube - Remove for Access
& Refit).
4. Release clips and remove bleed and supply pipes from slave cylinder.
5. Install clips in union.
6. Loosen and remove pipe adaptors (x2) from slave cylinder.
7. Remove bolts (x2), securing slave cylinder to torque
tube.
8. Remove slave cylinder and collect spacer.
9. Remove exhaust mountings (bolts x4).
Installation
1. Install exhaust mountings (bolts x4) (torque).
2. Clean slave cylinder, spacer and pipe adaptors.
3. Install spacer and slave cylinder, install and torque tighten bolts (x2).
4. Install pipe adaptors (x2) in slave cylinder.
5. Install bleed and supply pipes onto slave cylinder adaptors (x2), secure with clips.
6. Install torque tube assembly (see Workshop Manual procedure 05.01.CA Torque Tube - Remove for Access
& Refit).
7. Bleed clutch (see Workshop Manual procedure 08.00.AF Clutch Hydraulic System - Bleed).
8. Lower vehicle on ramp.
9. Connect vehicle battery.
Torque Tube & Prop Shaft Assembly-
Renew
-Sportshift Vehicles Only
Removal
1. Disconnect vehicle battery.
2. Raise vehicle on ramp.
3. Remove torque tube assembly (see Workshop Manual procedure 05.01.CA Torque Tube - Remove for Access
& Refit).
4. Remove grommet sealing clutch bleed pipe to torque tube.
5. Release clip, disconnect bleed pipe from slave cylinder adaptor and remove pipe.
6. Remove grommet sealing clutch pipe to torque tube.
7. Release clip, disconnect clutch pipe from slave cylinder adaptor.
8. Release clip securing transmission harness to clutch pipe mounting bracket.
9. Release clips (x4) securing clutch pipe to transmission harness.
10. Remove clutch pipe from torque tube.
11. Disconnect multiplug betwee n clutch position sensor
and transmission harness.
12. Release clip securing clutch position sensor harness to
top of torque tube.
13. Release clips (x2) securing clutch position sensor harness to side of torque tube.
14. Remove bolts (x2) securing clutch position sensor to slave cylinder and remove sensor.
15. Remove bolts (x2), securing slave cylinder to torque tube.
16. Remove slave cylinder and collect spacer.
17. Disconnect multiplug between propshaft speed sensor and transmission harness.
Warning
The torque tube is heavy. To avoid personal injury or damage to the torque tube, torque tube removal / installation is a two person operation.
Caution
Clutch fluid must not be allowed to contact vehicle paint work. Remove spilt clutch fluid from paint work by
rinsing away with running water.
Repair Operation Time (ROT)
Repair Operation Time (ROT)
ItemCode
Torque Tube & Prop Shaft Assembly-
Renew-Sportshift Vehicles Only 05.01.BC
Page 563 of 947
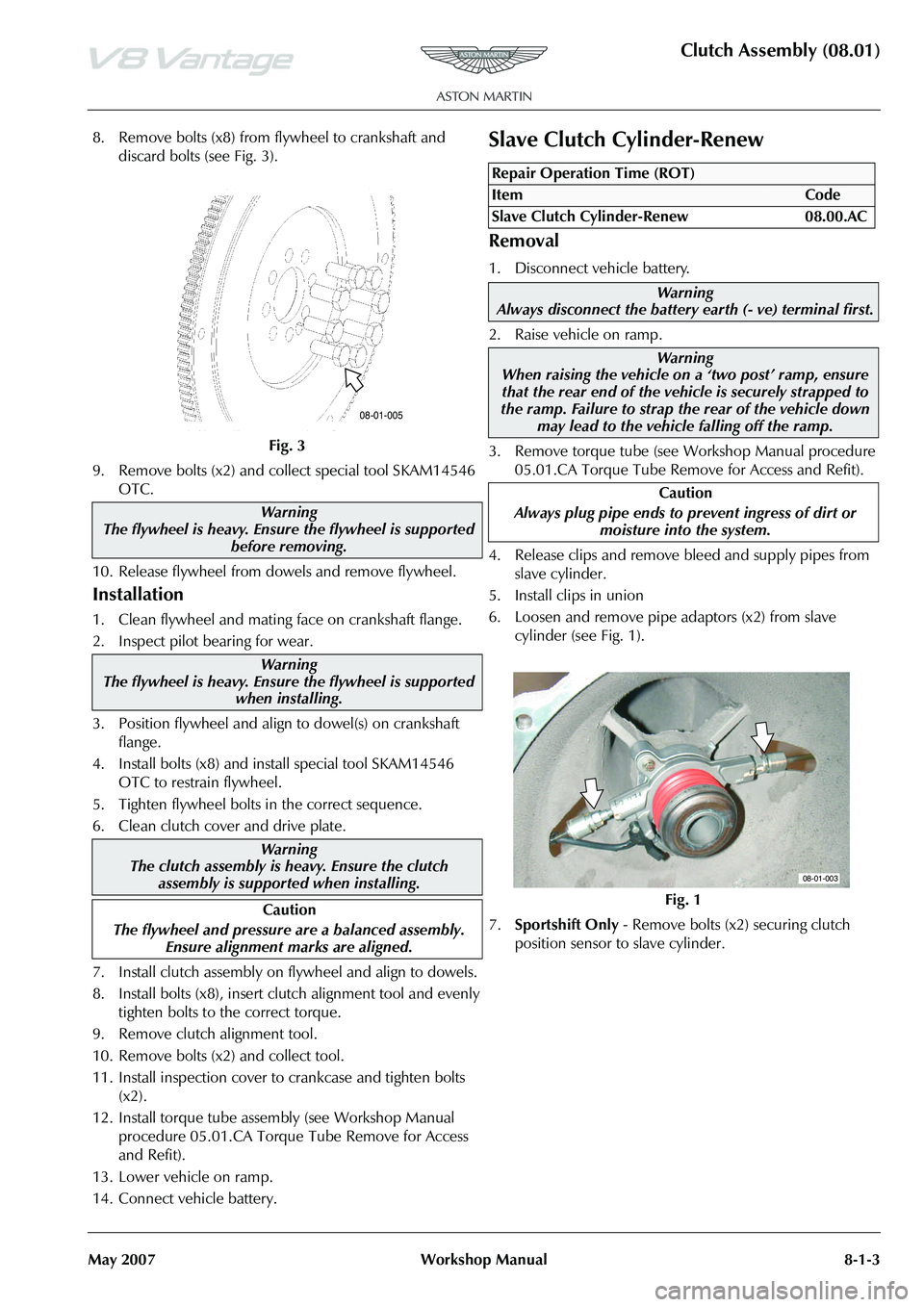
Clutch Assembly (08.01)
May 2007 Workshop Manual 8-1-3
8. Remove bolts (x8) from flywheel to crankshaft and discard bolts (see Fig. 3).
9. Remove bolts (x2) and collect special tool SKAM14546 OTC.
10. Release flywheel from dowels and remove flywheel.
Installation
1. Clean flywheel and mating face on crankshaft flange.
2. Inspect pilot bearing for wear.
3. Position flywheel and align to dowel(s) on crankshaft flange.
4. Install bolts (x8) and install special tool SKAM14546 OTC to restrain flywheel.
5. Tighten flywheel bolts in the correct sequence.
6. Clean clutch cover and drive plate.
7. Install clutch assembly on flywheel and align to dowels.
8. Install bolts (x8), insert clutch alignment tool and evenly tighten bolts to the correct torque.
9. Remove clutch alignment tool.
10. Remove bolts (x2) and collect tool.
11. Install inspection cover to crankcase and tighten bolts (x2).
12. Install torque tube assembly (see Workshop Manual procedure 05.01.CA Torque Tube Remove for Access
and Refit).
13. Lower vehicle on ramp.
14. Connect vehicle battery.
Slave Clutch Cylinder-Renew
08.00.AC
Removal
1. Disconnect vehicle battery.
2. Raise vehicle on ramp.
3. Remove torque tube (see Workshop Manual procedure 05.01.CA Torque Tube Remove for Access and Refit).
4. Release clips and remove bleed and supply pipes from slave cylinder.
5. Install clips in union
6. Loosen and remove pipe adaptors (x2) from slave cylinder (see Fig. 1).
7. Sportshift Only - Remove bolts (x2) securing clutch
position sensor to slave cylinder.
Fig. 3
Warning
The flywheel is heavy. Ensure the flywheel is supported
before removing.
Warning
The flywheel is heavy. Ensure the flywheel is supported
when installing.
Warning
The clutch assembly is heavy. Ensure the clutch
assembly is supporte d when installing.
Caution
The flywheel and pressure are a balanced assembly. Ensure alignment marks are aligned.
Repair Operation Time (ROT)
Warning
Always disconnect the battery earth (- ve) terminal first.
Warning
When raising the vehicle on a ‘two post’ ramp, ensure
that the rear end of the vehicle is securely strapped to
the ramp. Failure to strap the rear of the vehicle down may lead to the vehicl e falling off the ramp.
Caution
Always plug pipe ends to prevent ingress of dirt or moisture into the system.
Fig. 1
Page 564 of 947
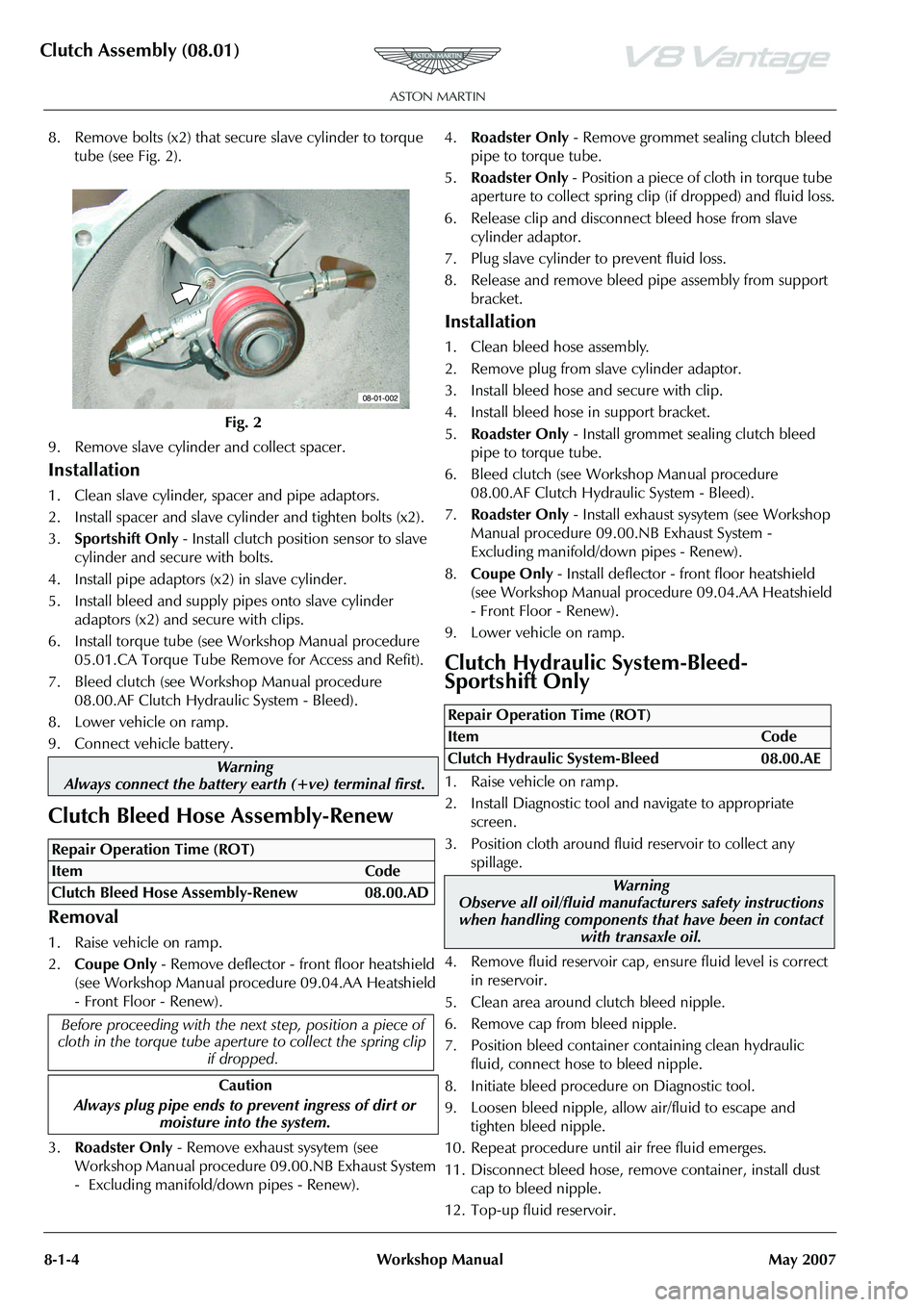
Clutch Assembly (08.01)
8-1-4 Workshop Manual May 2007
8. Remove bolts (x2) that secure slave cylinder to torque tube (see Fig. 2).
9. Remove slave cylinder and collect spacer.
Installation
1. Clean slave cylinder, spacer and pipe adaptors.
2. Install spacer and slave cylinder and tighten bolts (x2).
3. Sportshift Only - Install clutch position sensor to slave
cylinder and secure with bolts.
4. Install pipe adaptors (x2) in slave cylinder.
5. Install bleed and supply pipes onto slave cylinder adaptors (x2) and secure with clips.
6. Install torque tube (see Workshop Manual procedure 05.01.CA Torque Tube Remove for Access and Refit).
7. Bleed clutch (see Workshop Manual procedure 08.00.AF Clutch Hydraulic System - Bleed).
8. Lower vehicle on ramp.
9. Connect vehicle battery.
Clutch Bleed Hose Assembly-Renew
08.00.AD
Removal
1. Raise vehicle on ramp.
2. Coupe Only - Remove deflector - front floor heatshield
(see Workshop Manual proc edure 09.04.AA Heatshield
- Front Floor - Renew).
3. Roadster Only - Remove exhaust sysytem (see
Workshop Manual procedure 09.00.NB Exhaust System
- Excluding manifold/down pipes - Renew). 4.
Roadster Only - Remove grommet sealing clutch bleed
pipe to torque tube.
5. Roadster Only - Position a piece of cloth in torque tube
aperture to collect spring clip (if dropped) and fluid loss.
6. Release clip and disconnect bleed hose from slave cylinder adaptor.
7. Plug slave cylinder to prevent fluid loss.
8. Release and remove bleed pipe assembly from support bracket.
Installation
1. Clean bleed hose assembly.
2. Remove plug from slave cylinder adaptor.
3. Install bleed hose and secure with clip.
4. Install bleed hose in support bracket.
5.Roadster Only - Install grommet sealing clutch bleed
pipe to torque tube.
6. Bleed clutch (see Workshop Manual procedure 08.00.AF Clutch Hydraulic System - Bleed).
7. Roadster Only - Install exhaust sysytem (see Workshop
Manual procedure 09.00.NB Exhaust System -
Excluding manifold/down pipes - Renew).
8. Coupe Only - Install deflector - front floor heatshield
(see Workshop Manual procedure 09.04.AA Heatshield
- Front Floor - Renew).
9. Lower vehicle on ramp.
Clutch Hydraulic System-Bleed-
Sportshift Only
08.00.AE
1. Raise vehicle on ramp.
2. Install Diagnostic tool and navigate to appropriate screen.
3. Position cloth around fluid reservoir to collect any spillage.
4. Remove fluid reservoir cap, en sure fluid level is correct
in reservoir.
5. Clean area around clutch bleed nipple.
6. Remove cap from bleed nipple.
7. Position bleed container containing clean hydraulic fluid, connect hose to bleed nipple.
8. Initiate bleed procedure on Diagnostic tool.
9. Loosen bleed nipple, allow air/fluid to escape and tighten bleed nipple.
10. Repeat procedure until air free fluid emerges.
11. Disconnect bleed hose, remo ve container, install dust
cap to bleed nipple.
12. Top-up fluid reservoir.
Fig. 2Warning
Always connect the battery earth (+ve) terminal first.
Repair Operation Time (ROT)
Before proceeding with the ne xt step, position a piece of
cloth in the torque tu be aperture to collect the spring clip
if dropped.
Caution
Always plug pipe ends to prevent ingress of dirt or moisture into the system.
Repair Operation Time (ROT)
ItemCode
Clutch Hydraulic System-Bleed
Warning
Observe all oil/fluid manufactu rers safety instructions
when handling components th at have been in contact
with transaxle oil.
Page 598 of 947
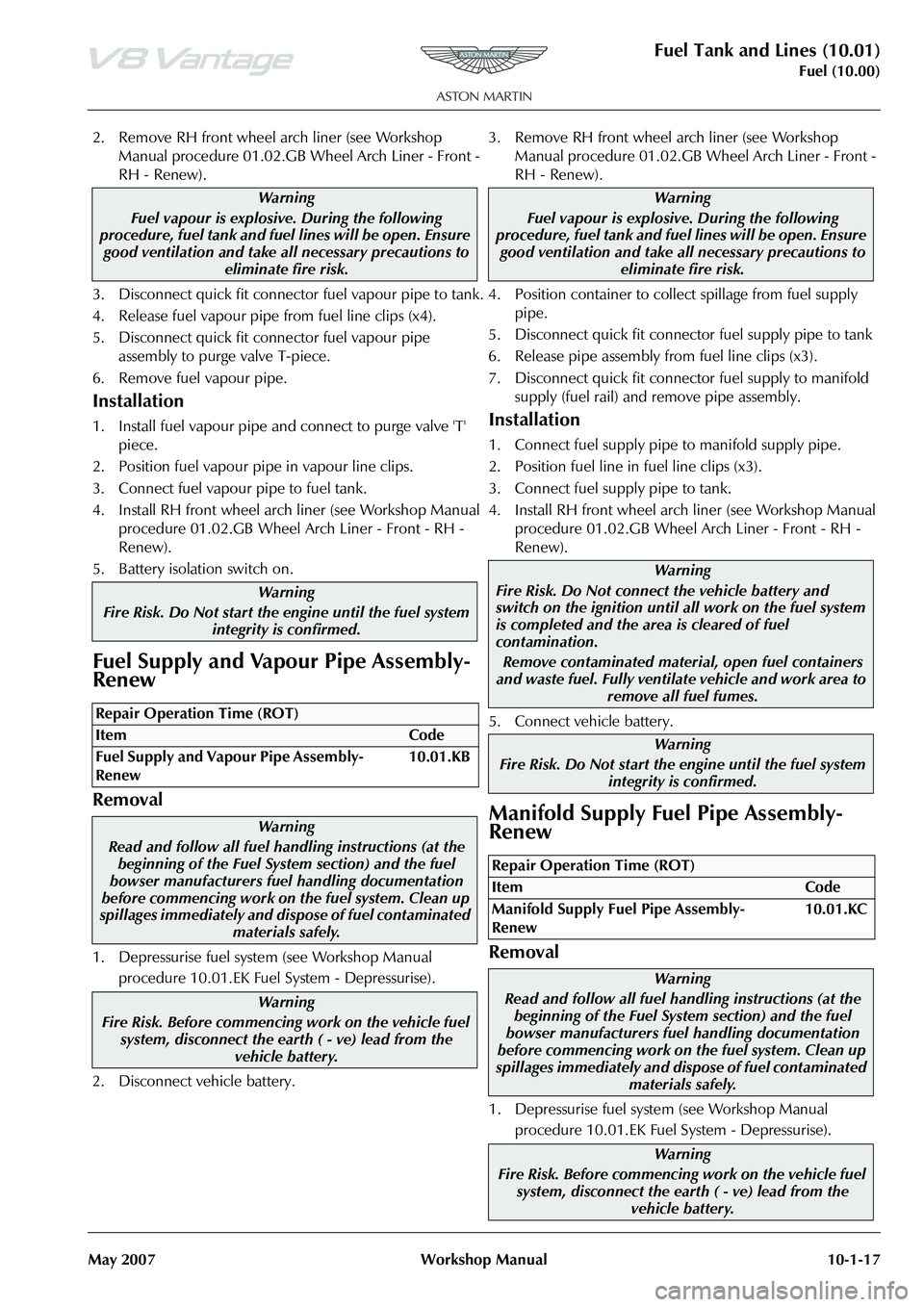
Fuel Tank and Lines (10.01)
Fuel (10.00)
May 2007 Workshop Manual 10-1-17
2. Remove RH front wheel arch liner (see Workshop Manual procedure 01.02.GB Wheel Arch Liner - Front -
RH - Renew).
3. Disconnect quick fit connector fuel vapour pipe to tank.
4. Release fuel vapour pipe from fuel line clips (x4).
5. Disconnect quick fit conne ctor fuel vapour pipe
assembly to purge valve T-piece.
6. Remove fuel vapour pipe.
Installation
1. Install fuel vapour pipe and connect to purge valve 'T' piece.
2. Position fuel vapour pi pe in vapour line clips.
3. Connect fuel vapour pipe to fuel tank.
4. Install RH front wheel arch liner (see Workshop Manual procedure 01.02.GB Wheel Arch Liner - Front - RH -
Renew).
5. Battery isolation switch on.
Fuel Supply and Vapour Pipe Assembly-
Renew
Removal
1. Depressurise fuel system (see Workshop Manual procedure 10.01.EK Fuel System - Depressurise).
2. Disconnect vehicle battery. 3. Remove RH front wheel arch liner (see Workshop
Manual procedure 01.02.GB Wheel Arch Liner - Front -
RH - Renew).
4. Position container to collect spillage from fuel supply pipe.
5. Disconnect quick fit connect or fuel supply pipe to tank
6. Release pipe assembly fr om fuel line clips (x3).
7. Disconnect quick fit connect or fuel supply to manifold
supply (fuel rail) and re move pipe assembly.
Installation
1. Connect fuel supply pipe to manifold supply pipe.
2. Position fuel line in fuel line clips (x3).
3. Connect fuel supply pipe to tank.
4. Install RH front wheel arch liner (see Workshop Manual procedure 01.02.GB Wheel Arch Liner - Front - RH -
Renew).
5. Connect vehicle battery.
Manifold Supply Fuel Pipe Assembly-
Renew
Removal
1. Depressurise fuel system (see Workshop Manual procedure 10.01.EK Fuel System - Depressurise).
Warning
Fuel vapour is explosive. During the following
procedure, fuel tank and fuel lines will be open. Ensure
good ventilation and take all necessary precautions to
eliminate fire risk.
Warning
Fire Risk. Do Not start the en gine until the fuel system
integrity is confirmed.
Repair Operation Time (ROT)
Warning
Read and follow all fuel hand ling instructions (at the
beginning of the Fuel System section) and the fuel
bowser manufacturers fuel handling documentation
before commencing work on the fuel system. Clean up
spillages immediatel y and dispose of fuel contaminated
materials safely.
Warning
Fire Risk. Before commencing work on the vehicle fuel system, disconnect the earth ( - ve) lead from the vehicle battery.
Warning
Fuel vapour is explosiv e. During the following
procedure, fuel tank and fuel lines will be open. Ensure
good ventilation and take all necessary precautions to
eliminate fire risk.
Warning
Fire Risk. Do Not connect the vehicle battery and
switch on the ignition until all work on the fuel system
is completed and the area is cleared of fuel
contamination.
Remove contaminated material, open fuel containers
and waste fuel. Fully ventilate vehicle and work area to remove all fuel fumes.
Warning
Fire Risk. Do Not start the en gine until the fuel system
integrity is confirmed.
Repair Operation Time (ROT)
Warning
Read and follow all fuel hand ling instructions (at the
beginning of the Fuel System section) and the fuel
bowser manufacturers fuel handling documentation
before commencing work on the fuel system. Clean up
spillages immediately and dispose of fuel contaminated materials safely.
Warning
Fire Risk. Before commencing work on the vehicle fuel system, disconnect the earth ( - ve) lead from the vehicle battery.
Page 599 of 947
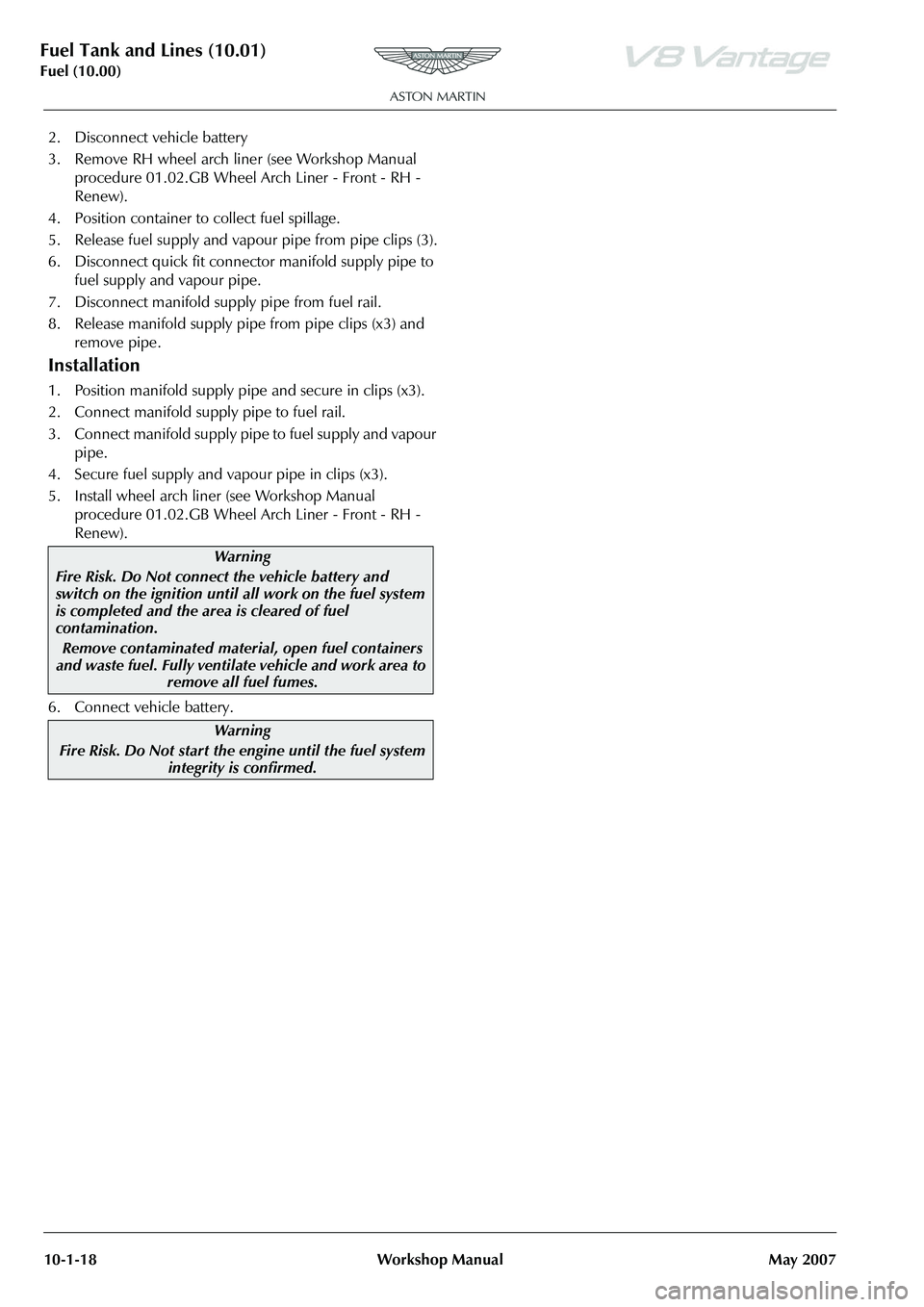
Fuel Tank and Lines (10.01)
Fuel (10.00)10-1-18 Workshop Manual May 2007
2. Disconnect vehicle battery
3. Remove RH wheel arch liner (see Workshop Manual
procedure 01.02.GB Wheel Arch Liner - Front - RH -
Renew).
4. Position container to collect fuel spillage.
5. Release fuel supply and vapour pipe from pipe clips (3).
6. Disconnect quick fit connector manifold supply pipe to fuel supply and vapour pipe.
7. Disconnect manifold supp ly pipe from fuel rail.
8. Release manifold supply pipe from pipe clips (x3) and
remove pipe.
Installation
1. Position manifold supply pipe and secure in clips (x3).
2. Connect manifold supply pipe to fuel rail.
3. Connect manifold supply pipe to fuel supply and vapour
pipe.
4. Secure fuel supply and vapour pipe in clips (x3).
5. Install wheel arch liner (see Workshop Manual procedure 01.02.GB Wheel Arch Liner - Front - RH -
Renew).
6. Connect vehicle battery.
Warning
Fire Risk. Do Not connect the vehicle battery and
switch on the ignition until all work on the fuel system
is completed and the area is cleared of fuel
contamination.
Remove contaminated material, open fuel containers
and waste fuel. Fully ventilat e vehicle and work area to
remove all fuel fumes.
Warning
Fire Risk. Do Not start the en gine until the fuel system
integrity is confirmed.
Page 656 of 947
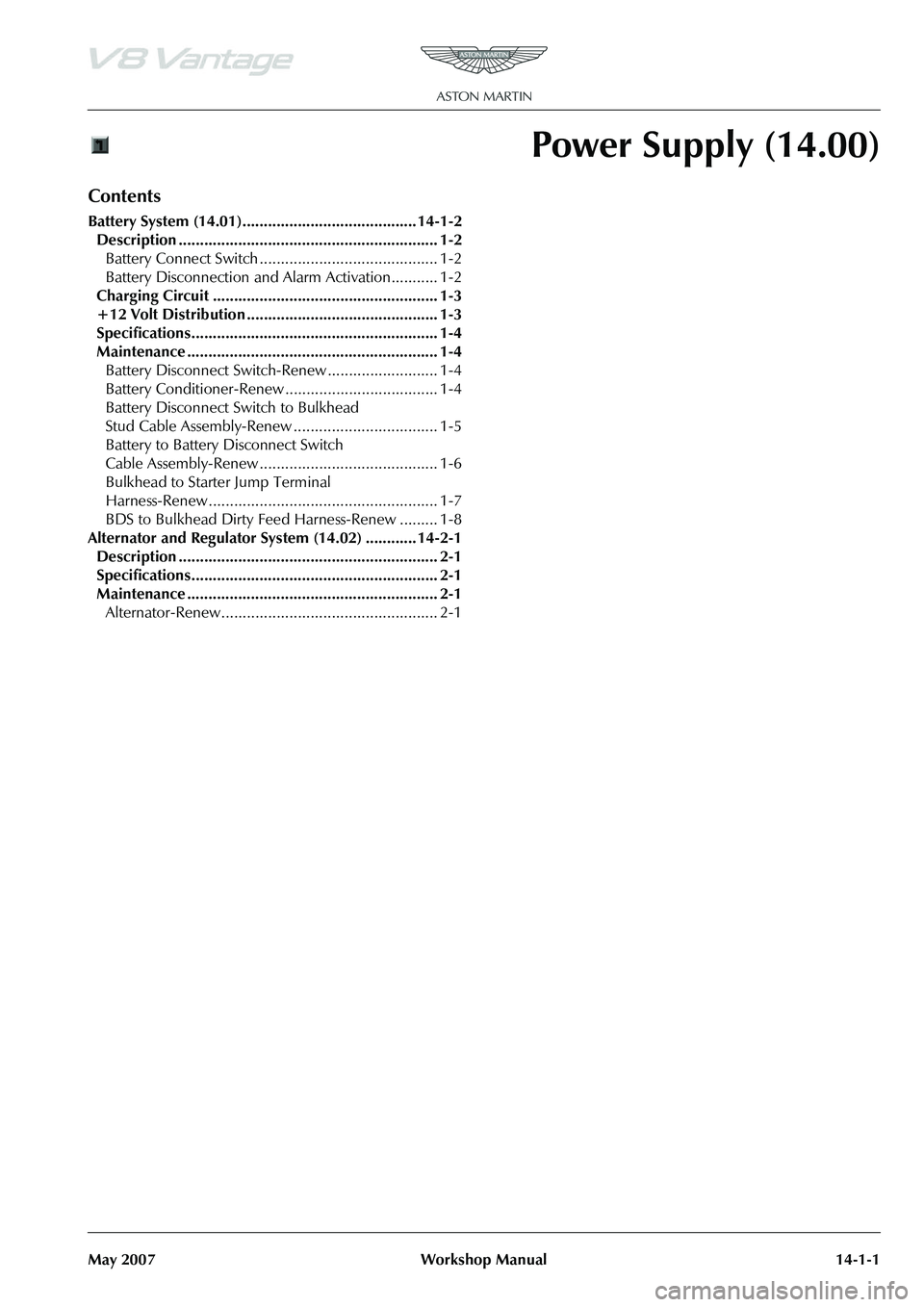
May 2007 Workshop Manual 14-1-1
Power Supply (14.00)
Contents
Battery System (14.01)......................................... 14-1-2Description ............................................................. 1-2 Battery Connect Switch .......................................... 1-2
Battery Disconnection and Alarm Activation........... 1-2
Charging Circuit ..................................................... 1-3
+12 Volt Distribution ............................................. 1-3
Specifications.......................................................... 1-4
Maintenance ........................................................... 1-4 Battery Disconnect Switch-Renew .......................... 1-4
Battery Conditioner-Renew .................................... 1-4
Battery Disconnect Switch to Bulkhead
Stud Cable Assembly-Renew .................................. 1-5
Battery to Battery Disconnect Switch
Cable Assembly-Renew .......................................... 1-6
Bulkhead to Starter Jump Terminal
Harness-Renew ...................................................... 1-7
BDS to Bulkhead Dirty Feed Harness-Renew ......... 1-8
Alternator and Regulator System (14.02) ............ 14-2-1 Description ............................................................. 2-1
Specifications.......................................................... 2-1
Maintenance ........................................................... 2-1 Alternator-Renew................................................... 2-1
Page 657 of 947
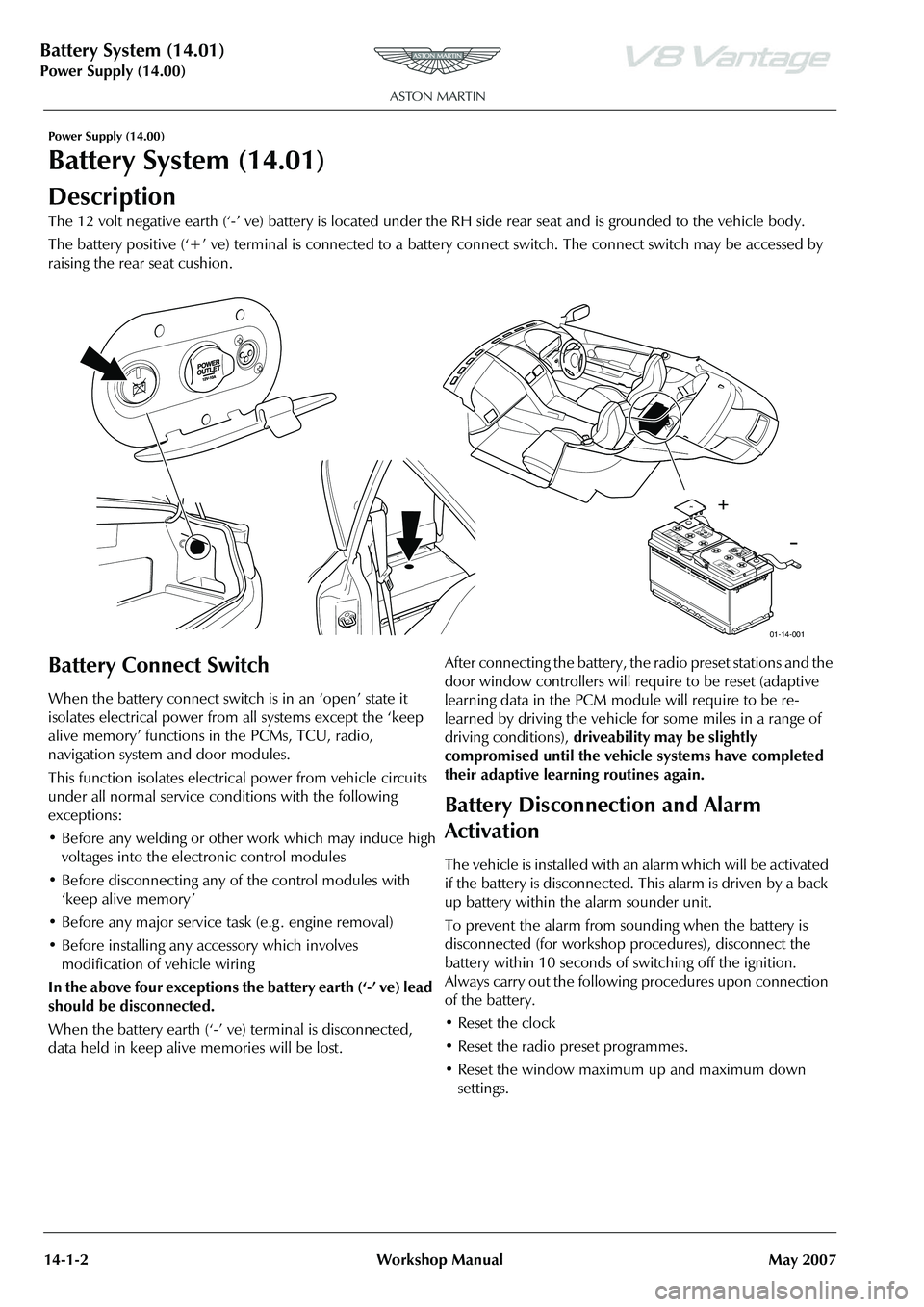
Battery System (14.01)
Power Supply (14.00)14-1-2 Workshop Manual May 2007
Power Supply (14.00)
Battery System (14.01)
Description
The 12 volt negative earth (‘-’ ve) battery is located under the RH side rear seat and is grounded to the vehicle body.
The battery positive (‘+’ ve) terminal is connected to a battery connect switch. The connect switch may be accessed by
raising the rear seat cushion.
Battery Connect Switch
When the battery connect switch is in an ‘open’ state it
isolates electrical power from all systems except the ‘keep
alive memory’ functions in the PCMs, TCU, radio,
navigation system and door modules.
This function isolates electri cal power from vehicle circuits
under all normal service conditions with the following
exceptions:
• Before any welding or other work which may induce high voltages into the electronic control modules
• Before disconnecting any of the control modules with ‘keep alive memory ’
• Before any major service task (e.g . engine removal)
• Before installing any accessory which involves modification of vehicle wiring
In the above four exceptions the battery earth (‘-’ ve) lead
should be disconnected.
When the battery earth (‘-’ ve) terminal is disconnected,
data held in keep alive memories will be lost. After connecting the battery, the radio preset stations and the
door window controllers will require to be reset (adaptive
learning data in the PCM module will require to be re-
learned by driving the vehicle for some miles in a range of
driving conditions),
driveability may be slightly
compromised until the vehicle systems have completed
their adaptive learning routines again.
Battery Disconnection and Alarm
Activation
The vehicle is installed with an alarm which will be activated
if the battery is disconnected. This alarm is driven by a back
up battery within the alarm sounder unit.
To prevent the alarm from so unding when the battery is
disconnected (for workshop procedures), disconnect the
battery within 10 seconds of switching off the ignition.
Always carry out the following procedures upon connection
of the battery.
• Reset the clock
• Reset the radio preset programmes.
• Reset the window maximum up and maximum down settings.
Pb
A
ST O
N
M A
R
TI
N
S H I
E L
D
E YE
S
NO S
U L
F U R
IC
A C I
DF
LU
SH
E
YES
I M
MED IA T
E LY
W IT
H
W A
T
E R
G ET
M ED
IC
AL
H ELP
F A
STSPA
R
KS
F LA
M
ES
S M
OKIN
GD AN G ER / P
OIS
ONEXP L
O S
IV E
G ASE
SC AN
C A
U SE C
A
N C A
U SE
B L
IN DN
ESS
O R
S E
V ER E
B U RNS
B
LI
NDN
ES S
O R
IN JU R
YK EEP
O UT
O F T
HE R
EA C
H O F C H
IL DR
EN D O N
OT
TI P: K EEP
V E
N T C A
PS
T IG HT
A N D L E
VE L!
1
2 V
1
2 V 9
0A
h
9
0A
h
M IN S
M
IN S
( S
AE
)
(
S
AE
)RC
RC6
80 A
M
PS
6
80 A
M
PS2R
83-1
065 5-A
A
2
R
83-1
065 5-A
A170
1 70
01-14-001
Page 658 of 947
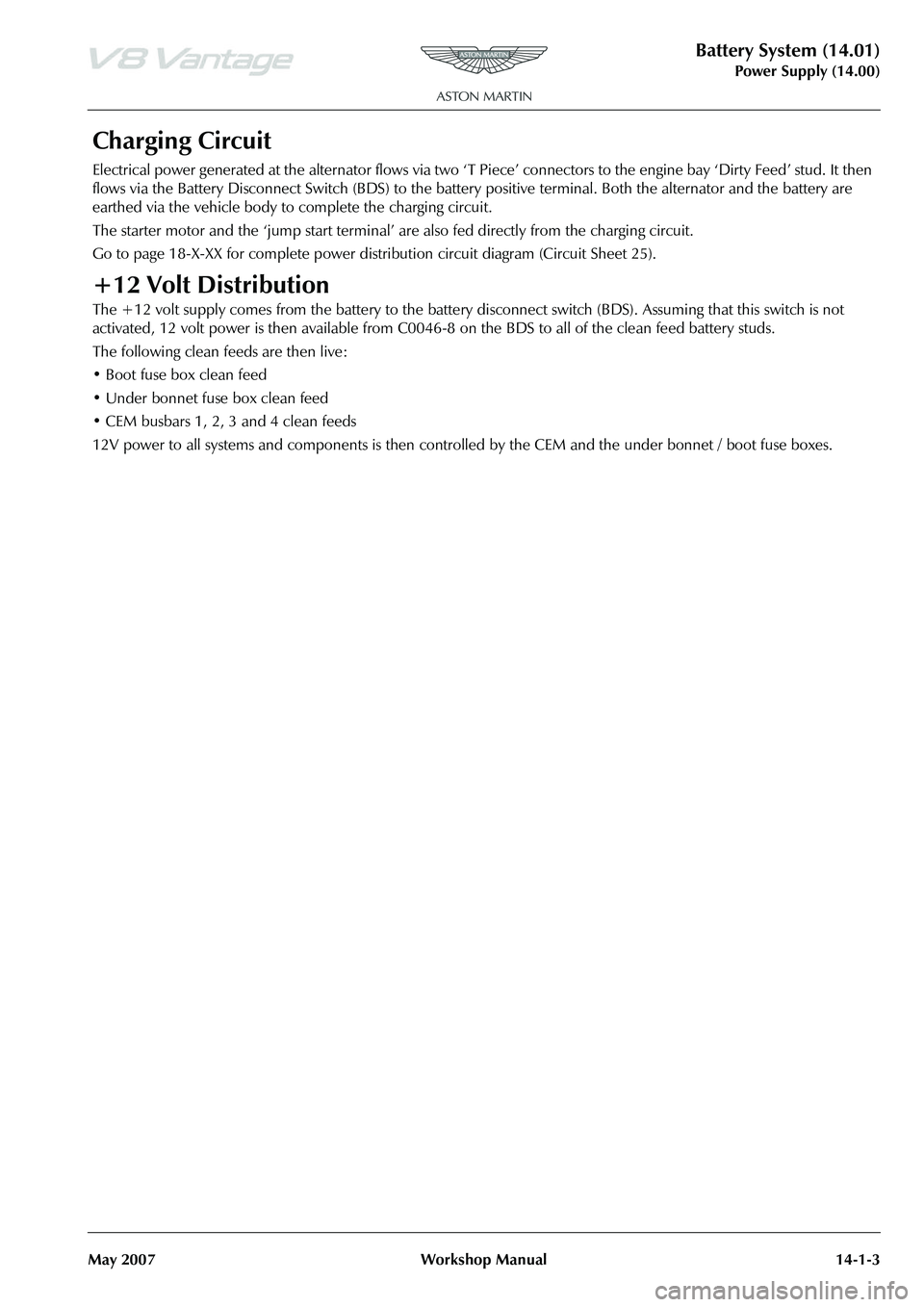
Battery System (14.01)
Power Supply (14.00)
May 2007 Workshop Manual 14-1-3
Charging Circuit
Electrical power generated at the alternator flows via two ‘T Pi ece’ connectors to the engine bay ‘Dirty Feed’ stud. It then
flows via the Battery Disconnect Switch (BDS) to the battery positive terminal. Both the alternator and the battery are
earthed via the vehicle body to complete the charging circuit.
The starter motor and the ‘jump start terminal’ ar e also fed directly from the charging circuit.
Go to page 18-X-XX for complete power dist ribution circuit diagram (Circuit Sheet 25).
+12 Volt Distribution
The +12 volt supply comes from the battery to the battery disc onnect switch (BDS). Assuming that this switch is not
activated, 12 volt power is then available from C0046-8 on the BDS to all of the clean feed battery studs.
The following clean feeds are then live:
• Boot fuse box clean feed
• Under bonnet fuse box clean feed
• CEM busbars 1, 2, 3 and 4 clean feeds
12V power to all systems and components is then controlled by the CEM and the under bonnet / boot fuse boxes.