throttle AUDI S4 1998 B5 / 1.G Engine Manual
[x] Cancel search | Manufacturer: AUDI, Model Year: 1998, Model line: S4, Model: AUDI S4 1998 B5 / 1.GPages: 72, PDF Size: 3.25 MB
Page 35 of 72
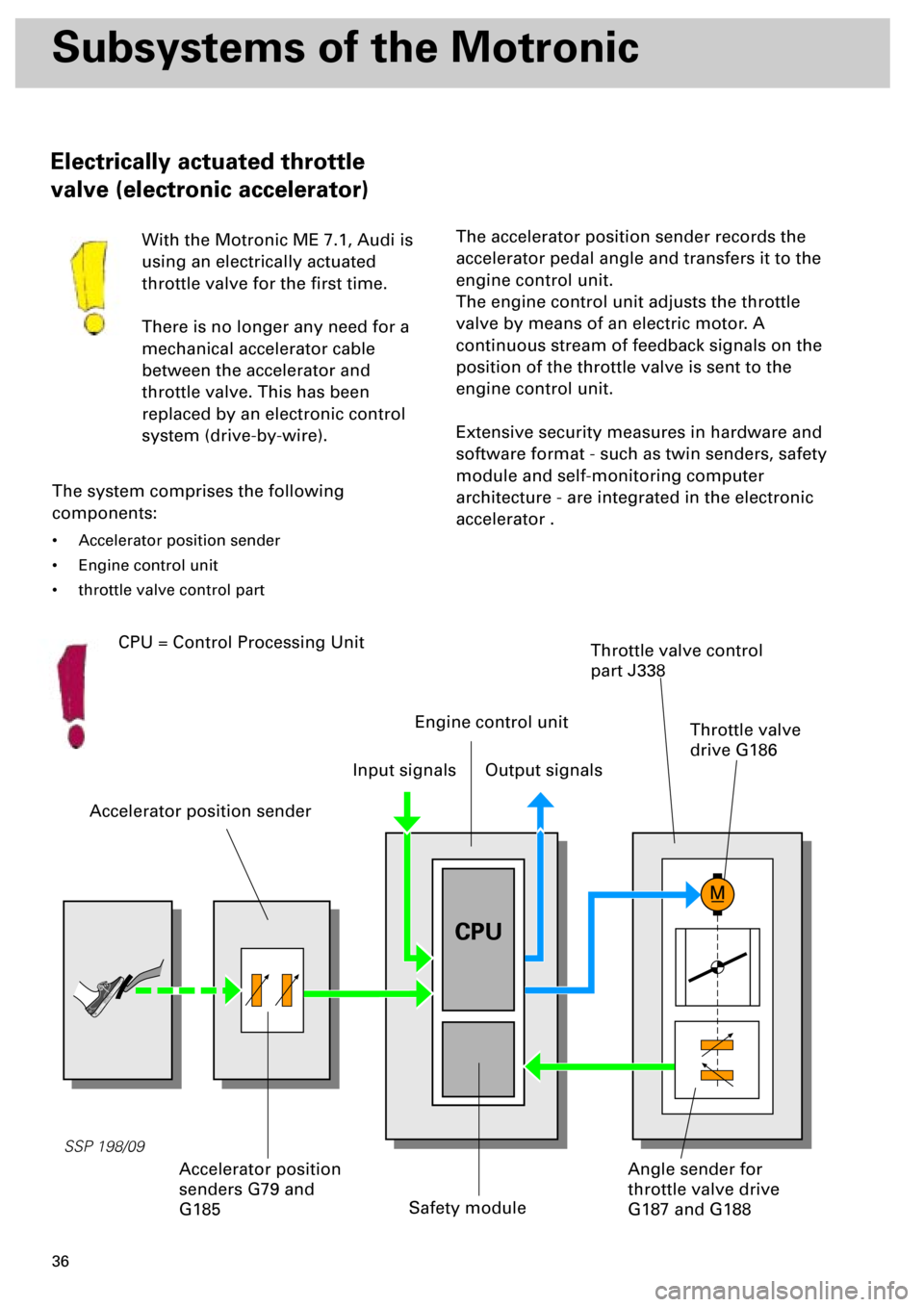
36
SSP 198/09
Subsystems of the Motronic
Electrically actuated throttle
valve (electronic accelerator)
With the Motronic ME 7.1, Audi is
using an electrically actuated
throttle valve for the first time.
There is no longer any need for a
mechanical accelerator cable
between the accelerator and
throttle valve. This has been
replaced by an electronic control
system (drive-by-wire).
The system comprises the following
components:
• Accelerator position sender
• Engine control unit
• throttle valve control part
Accelerator position sender
Safety module
Throttle valve control
part J338
The accelerator position sender records the
accelerator pedal angle and transfers it to the
engine control unit.
The engine control unit adjusts the throttle
valve by means of an electric motor. A
continuous stream of feedback signals on the
position of the throttle valve is sent to the
engine control unit.
Extensive security measures in hardware and
software format - such as twin senders, safety
module and self-monitoring computer
architecture - are integrated in the electronic
accelerator .
Input signalsOutput signals
Angle sender for
throttle valve drive
G187 and G188Accelerator position
senders G79 and
G185
Engine control unit
CPU
CPU = Control Processing Unit
Throttle valve
drive G186
Page 36 of 72
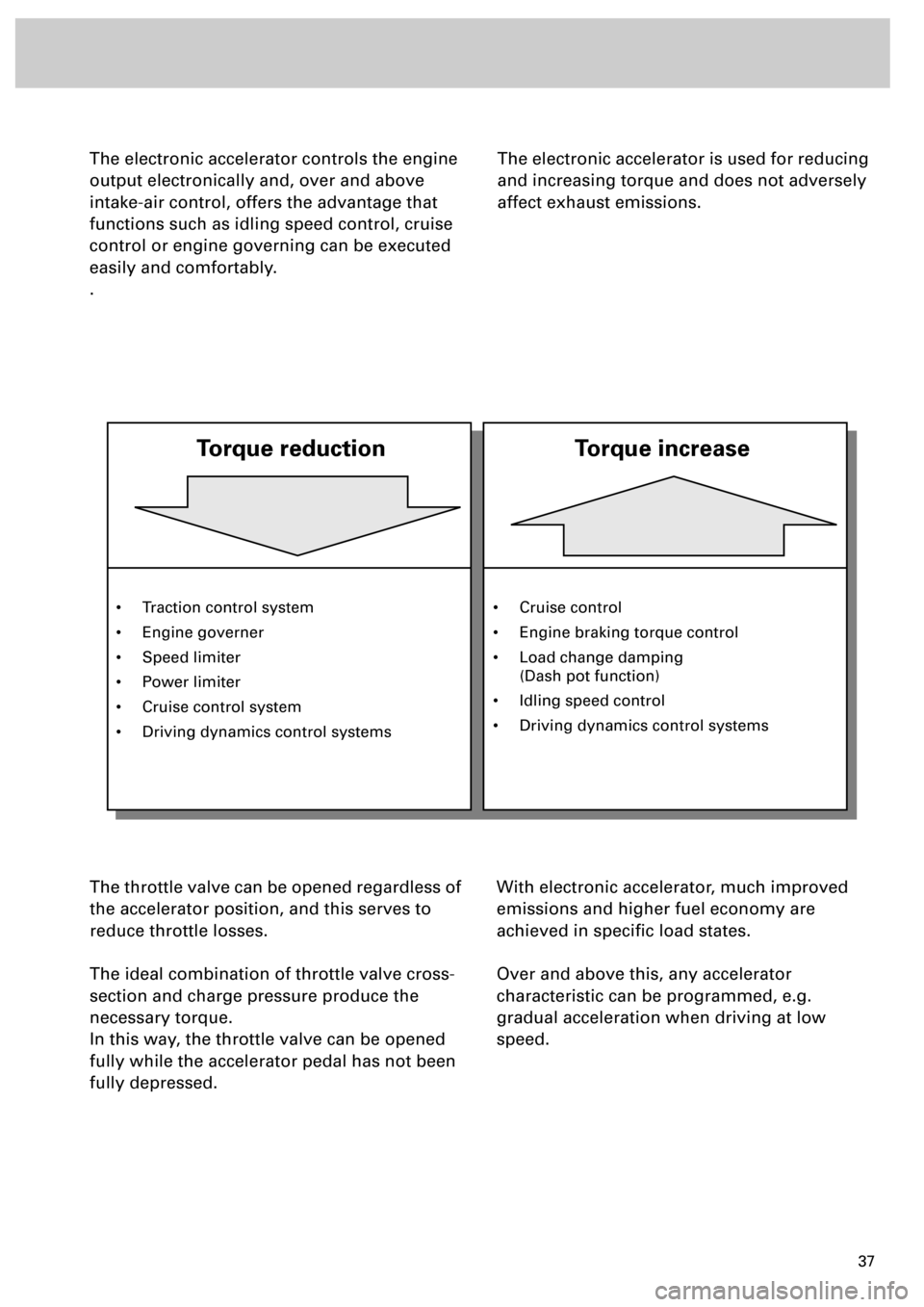
37
The electronic accelerator controls the engine
output electronically and, over and above
intake-air control, offers the advantage that
functions such as idling speed control, cruise
control or engine governing can be executed
easily and comfortably.
.
The throttle valve can be opened regardless of
the accelerator position, and this serves to
reduce throttle losses.
The ideal combination of throttle valve cross-
section and charge pressure produce the
necessary torque.
In this way, the throttle valve can be opened
fully while the accelerator pedal has not been
fully depressed.With electronic accelerator, much improved
emissions and higher fuel economy are
achieved in specific load states.
Over and above this, any accelerator
characteristic can be programmed, e.g.
gradual acceleration when driving at low
speed.
The electronic accelerator is used for reducing
and increasing torque and does not adversely
affect exhaust emissions.
• Traction control system
• Engine governer
• Speed limiter
• Power limiter
• Cruise control system
• Driving dynamics control systems
Torque reduction
Torque increase
• Cruise control
• Engine braking torque control
• Load change damping
(Dash pot function)
• Idling speed control
• Driving dynamics control systems
Page 38 of 72
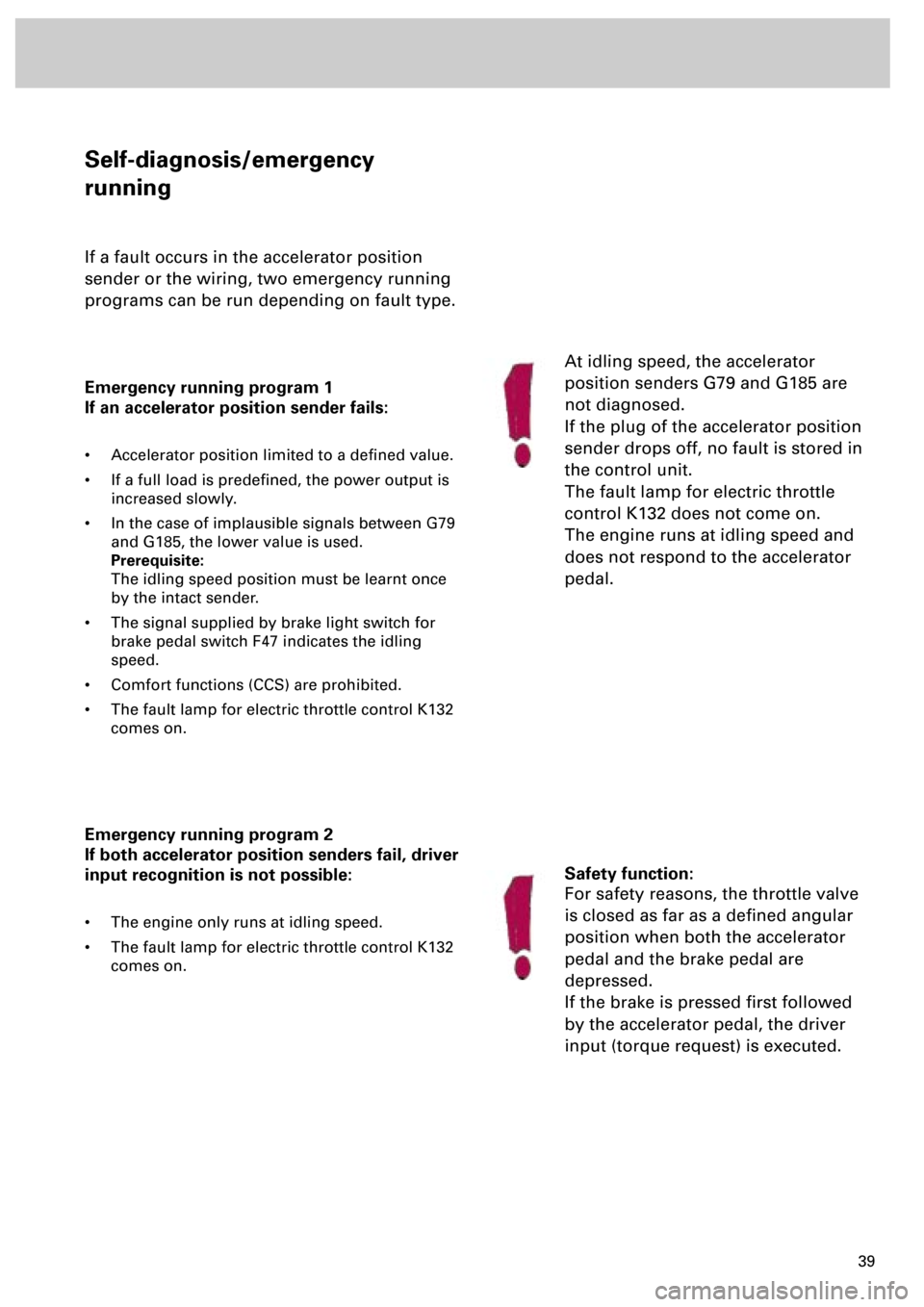
39
Self-diagnosis/emergency
running
If a fault occurs in the accelerator position
sender or the wiring, two emergency running
programs can be run depending on fault type.
Emergency running program 1
If an accelerator position sender fails:
• Accelerator position limited to a defined value.
• If a full load is predefined, the power output is
increased slowly.
• In the case of implausible signals between G79
and G185, the lower value is used.
Prerequisite:
The idling speed position must be learnt once
by the intact sender.
• The signal supplied by brake light switch for
brake pedal switch F47 indicates the idling
speed.
• Comfort functions (CCS) are prohibited.
• The fault lamp for electric throttle control K132
comes on.
Emergency running program 2
If both accelerator position senders fail, driver
input recognition is not possible:
• The engine only runs at idling speed.
• The fault lamp for electric throttle control K132
comes on.
At idling speed, the accelerator
position senders G79 and G185 are
not diagnosed.
If the plug of the accelerator position
sender drops off, no fault is stored in
the control unit.
The fault lamp for electric throttle
control K132 does not come on.
The engine runs at idling speed and
does not respond to the accelerator
pedal.
Safety function:
For safety reasons, the throttle valve
is closed as far as a defined angular
position when both the accelerator
pedal and the brake pedal are
depressed.
If the brake is pressed first followed
by the accelerator pedal, the driver
input (torque request) is executed.
Page 39 of 72
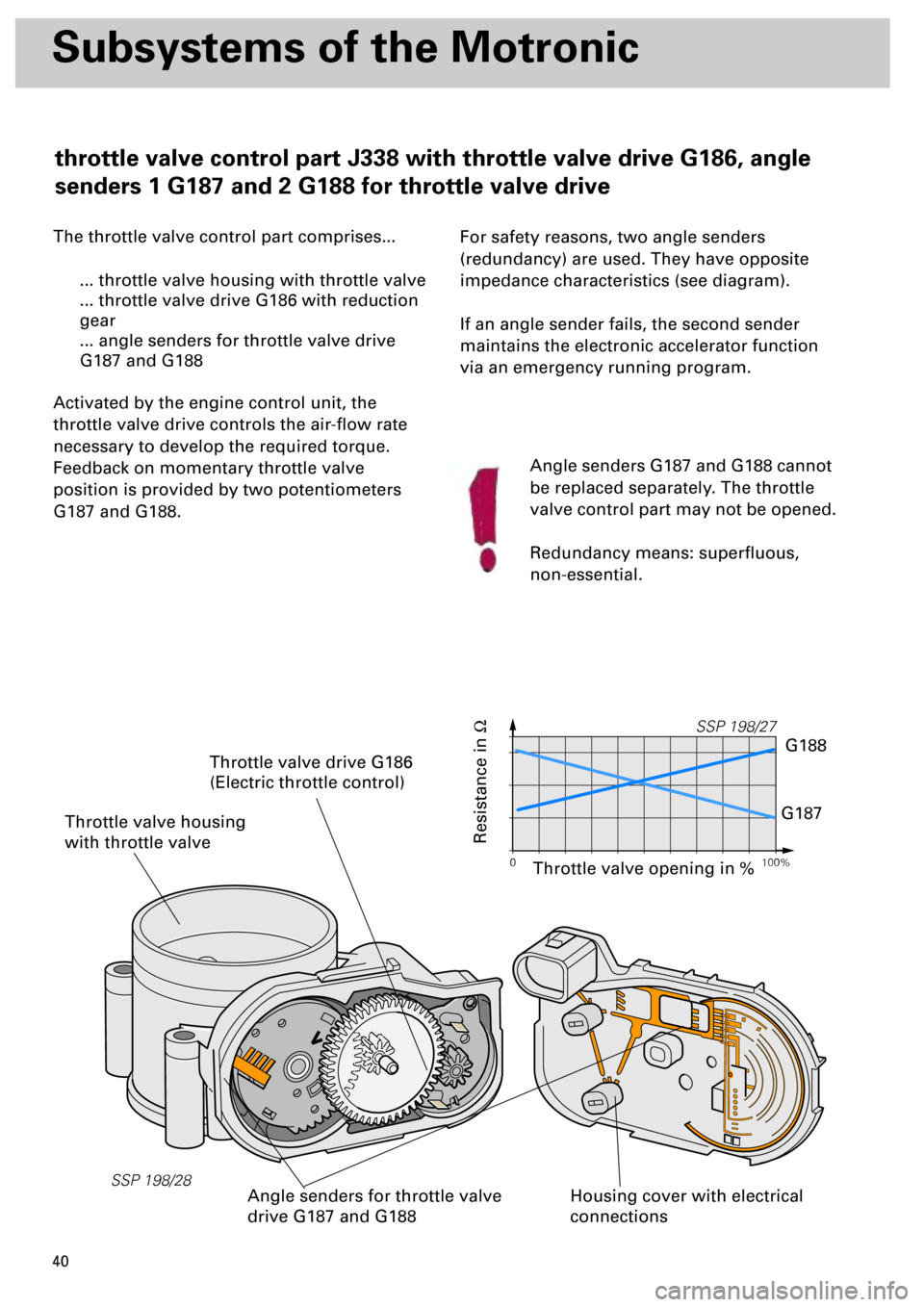
40
SSP 198/28
Subsystems of the Motronic
The throttle valve control part comprises...
... throttle valve housing with throttle valve
... throttle valve drive G186 with reduction
gear
... angle senders for throttle valve drive
G187 and G188
Activated by the engine control unit, the
throttle valve drive controls the air-flow rate
necessary to develop the required torque.
Feedback on momentary throttle valve
position is provided by two potentiometers
G187 and G188.
For safety reasons, two angle senders
(redundancy) are used. They have opposite
impedance characteristics (see diagram).
If an angle sender fails, the second sender
maintains the electronic accelerator function
via an emergency running program.
Throttle valve housing
with throttle valve
Housing cover with electrical
connections
Throttle valve drive G186
(Electric throttle control)
Angle senders for throttle valve
drive G187 and G188
Resistance in
W
Angle senders G187 and G188 cannot
be replaced separately. The throttle
valve control part may not be opened.
Redundancy means: superfluous,
non-essential.
0 100%
SSP 198/27
G188
G187
Throttle valve opening in %
throttle valve control part J338 with throttle valve drive G186, angle
senders 1 G187 and 2 G188 for throttle valve drive
Page 40 of 72
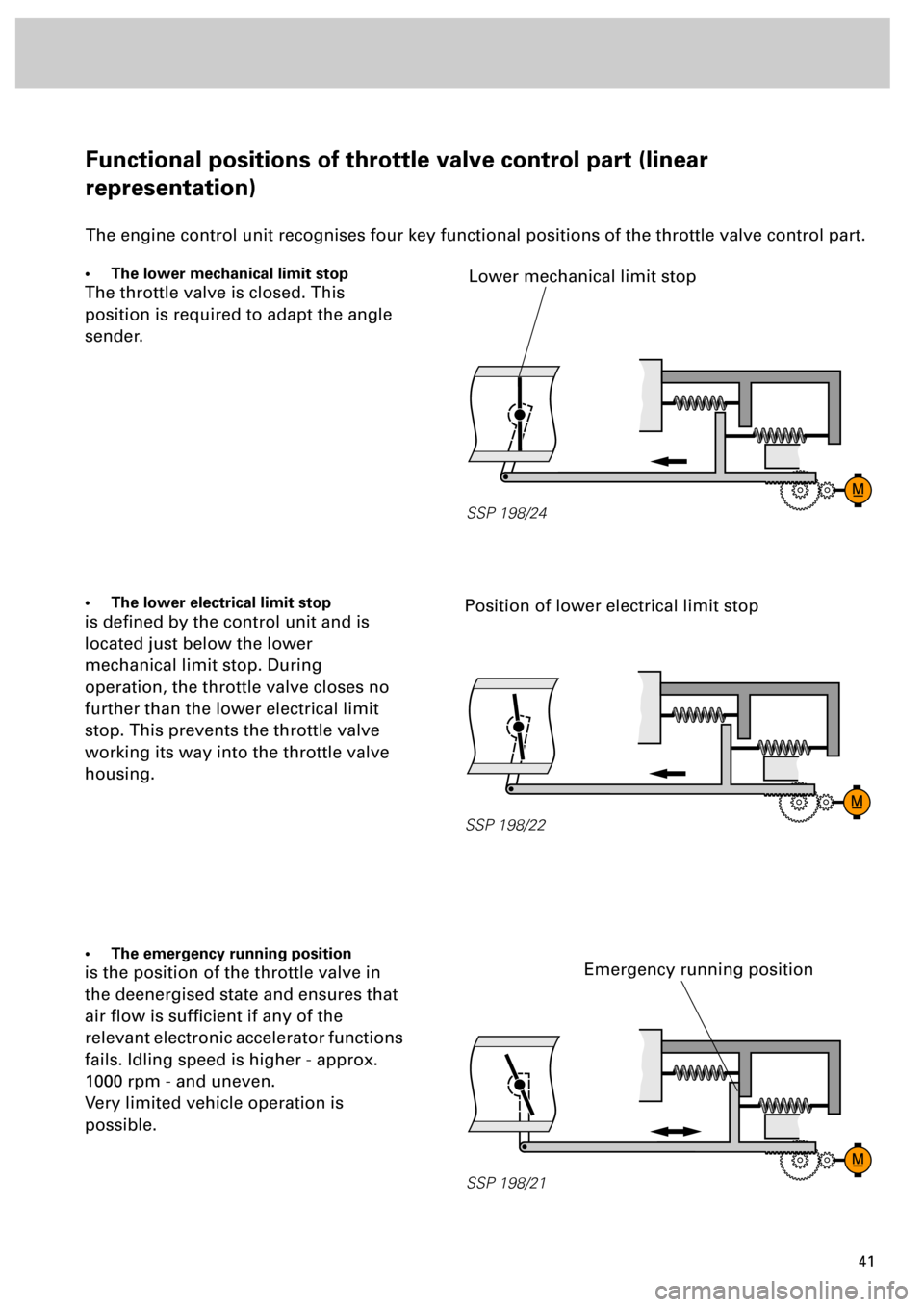
41
Functional positions of throttle valve control part (linear
representation)
The engine control unit recognises four key functional positions of the throttle valve control part.
• The lower mechanical limit stop
The throttle valve is closed. This
position is required to adapt the angle
sender.
• The lower electrical limit stop
is defined by the control unit and is
located just below the lower
mechanical limit stop. During
operation, the throttle valve closes no
further than the lower electrical limit
stop. This prevents the throttle valve
working its way into the throttle valve
housing.
• The emergency running position
is the position of the throttle valve in
the deenergised state and ensures that
air flow is sufficient if any of the
relevant electronic accelerator functions
fails. Idling speed is higher - approx.
1000 rpm - and uneven.
Very limited vehicle operation is
possible.
SSP 198/21
SSP 198/22
SSP 198/24
Position of lower electrical limit stop
Emergency running position
Lower mechanical limit stop
Page 41 of 72
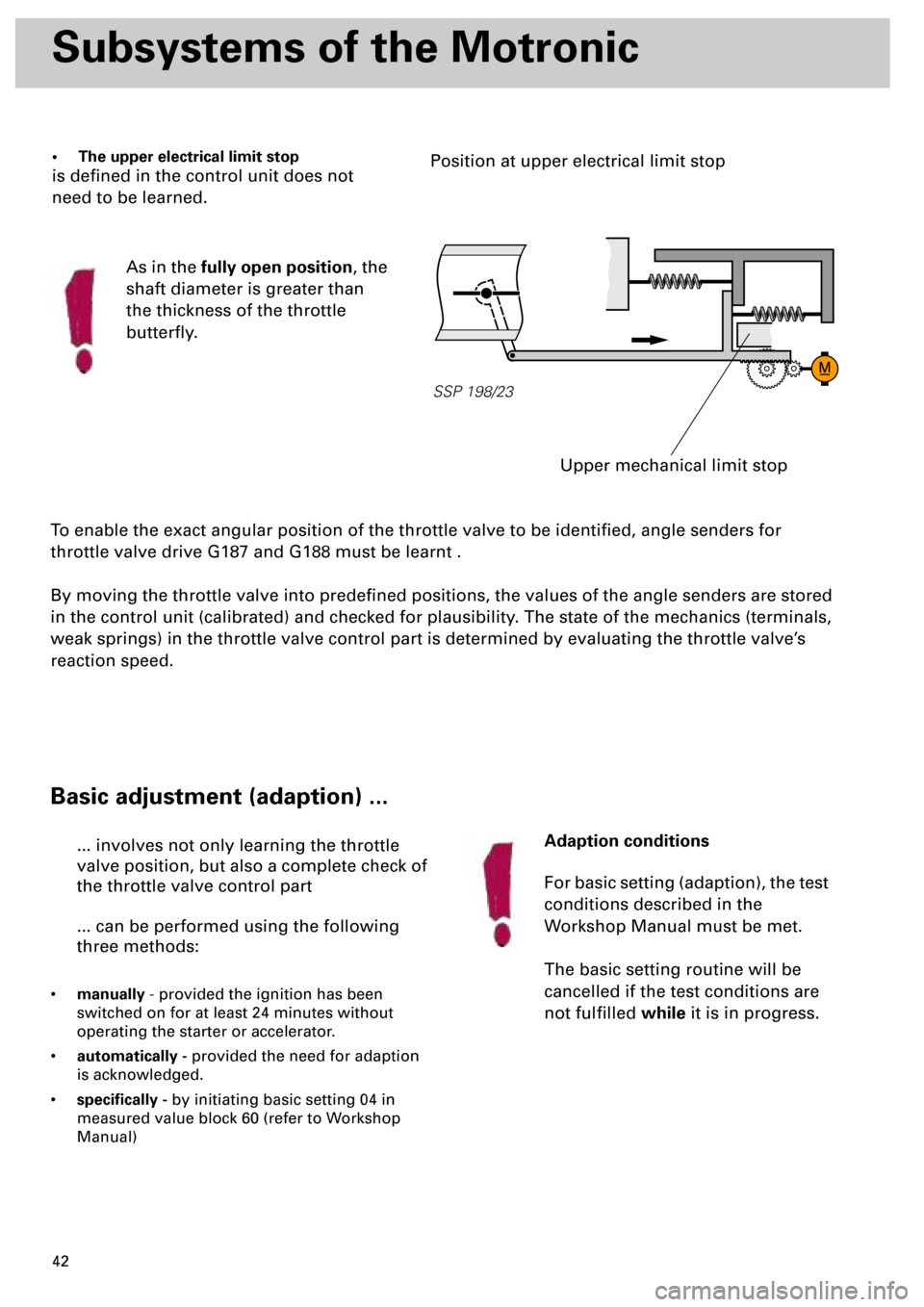
42
Subsystems of the Motronic
To enable the exact angular position of the throttle valve to be identified, angle senders for
throttle valve drive G187 and G188 must be learnt .
By moving the throttle valve into predefined positions, the values of the angle senders are stored
in the control unit (calibrated) and checked for plausibility. The state of the mechanics (terminals,
weak springs) in the throttle valve control part is determined by evaluating the throttle valve’s
reaction speed.
... involves not only learning the throttle
valve position, but also a complete check of
the throttle valve control part
... can be performed using the following
three methods:
•
manually
- provided the ignition has been
switched on for at least 24 minutes without
operating the starter or accelerator.
•
automatically -
provided the need for adaption
is acknowledged.
•
specifically -
by initiating basic setting 04 in
measured value block 60 (refer to Workshop
Manual)
• The upper electrical limit stop
is defined in the control unit does not
need to be learned.
As in the
fully open position
, the
shaft diameter is greater than
the thickness of the throttle
butterfly.
SSP 198/23
Upper mechanical limit stop
Position at upper electrical limit stop
Basic adjustment (adaption) ...
Adaption conditions
For basic setting (adaption), the test
conditions described in the
Workshop Manual must be met.
The basic setting routine will be
cancelled if the test conditions are
not fulfilled
while
it is in progress.
Page 42 of 72
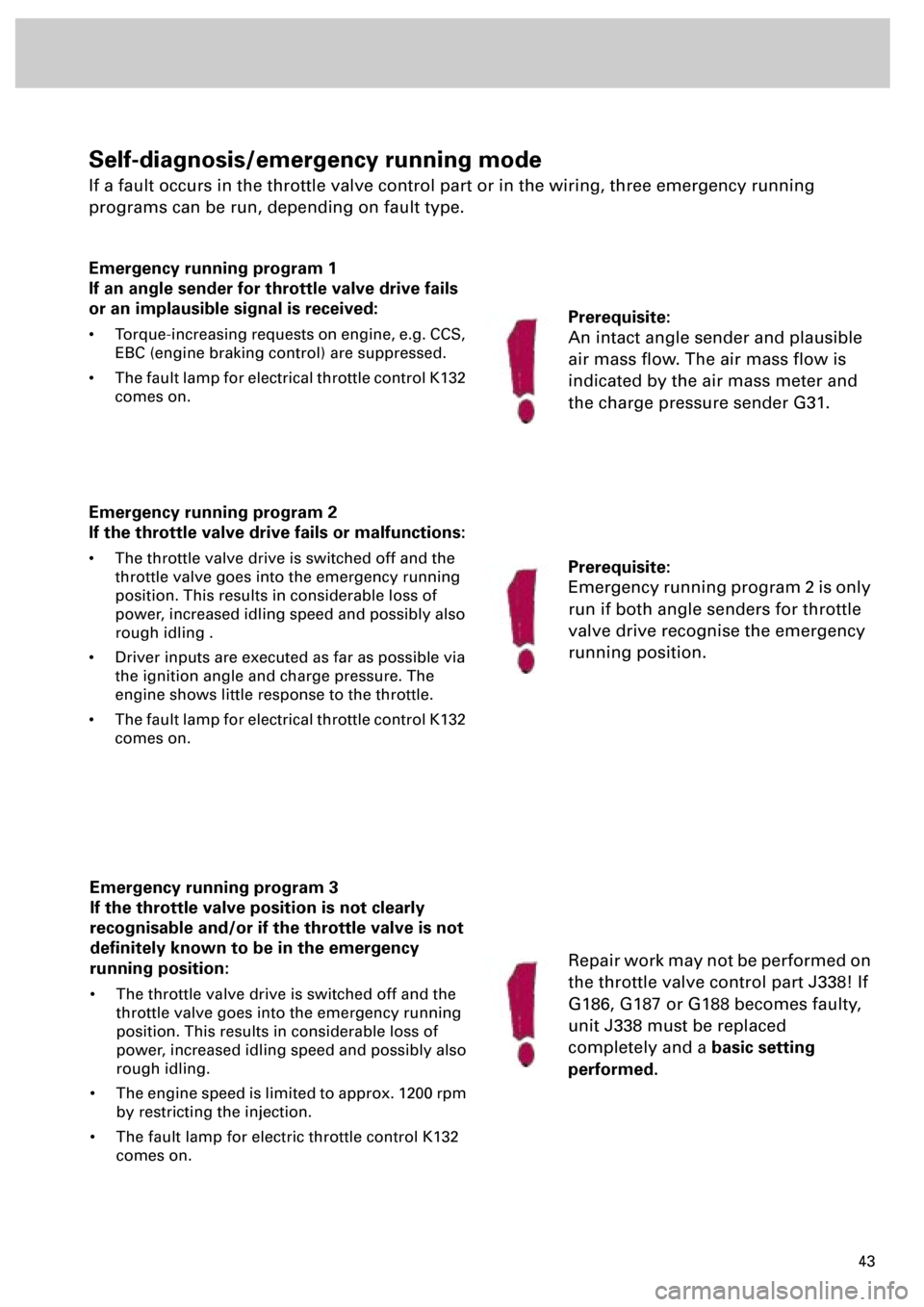
43
Emergency running program 1
If an angle sender for throttle valve drive fails
or an implausible signal is received:
• Torque-increasing requests on engine, e.g. CCS,
EBC (engine braking control) are suppressed.
• The fault lamp for electrical throttle control K132
comes on.
Prerequisite:
An intact angle sender and plausible
air mass flow. The air mass flow is
indicated by the air mass meter and
the charge pressure sender G31.
Self-diagnosis/emergency running mode
If a fault occurs in the throttle valve control part or in the wiring, three emergency running
programs can be run, depending on fault type.
Emergency running program 2
If the throttle valve drive fails or malfunctions:
• The throttle valve drive is switched off and the
throttle valve goes into the emergency running
position. This results in considerable loss of
power, increased idling speed and possibly also
rough idling .
• Driver inputs are executed as far as possible via
the ignition angle and charge pressure. The
engine shows little response to the throttle.
• The fault lamp for electrical throttle control K132
comes on.
Prerequisite:
Emergency running program 2 is only
run if both angle senders for throttle
valve drive recognise the emergency
running position.
Emergency running program 3
If the throttle valve position is not clearly
recognisable and/or if the throttle valve is not
definitely known to be in the emergency
running position:
• The throttle valve drive is switched off and the
throttle valve goes into the emergency running
position. This results in considerable loss of
power, increased idling speed and possibly also
rough idling.
• The engine speed is limited to approx. 1200 rpm
by restricting the injection.
• The fault lamp for electric throttle control K132
comes on.
Repair work may not be performed on
the throttle valve control part J338! If
G186, G187 or G188 becomes faulty,
unit J338 must be replaced
completely and a
basic setting
performed.
Page 43 of 72
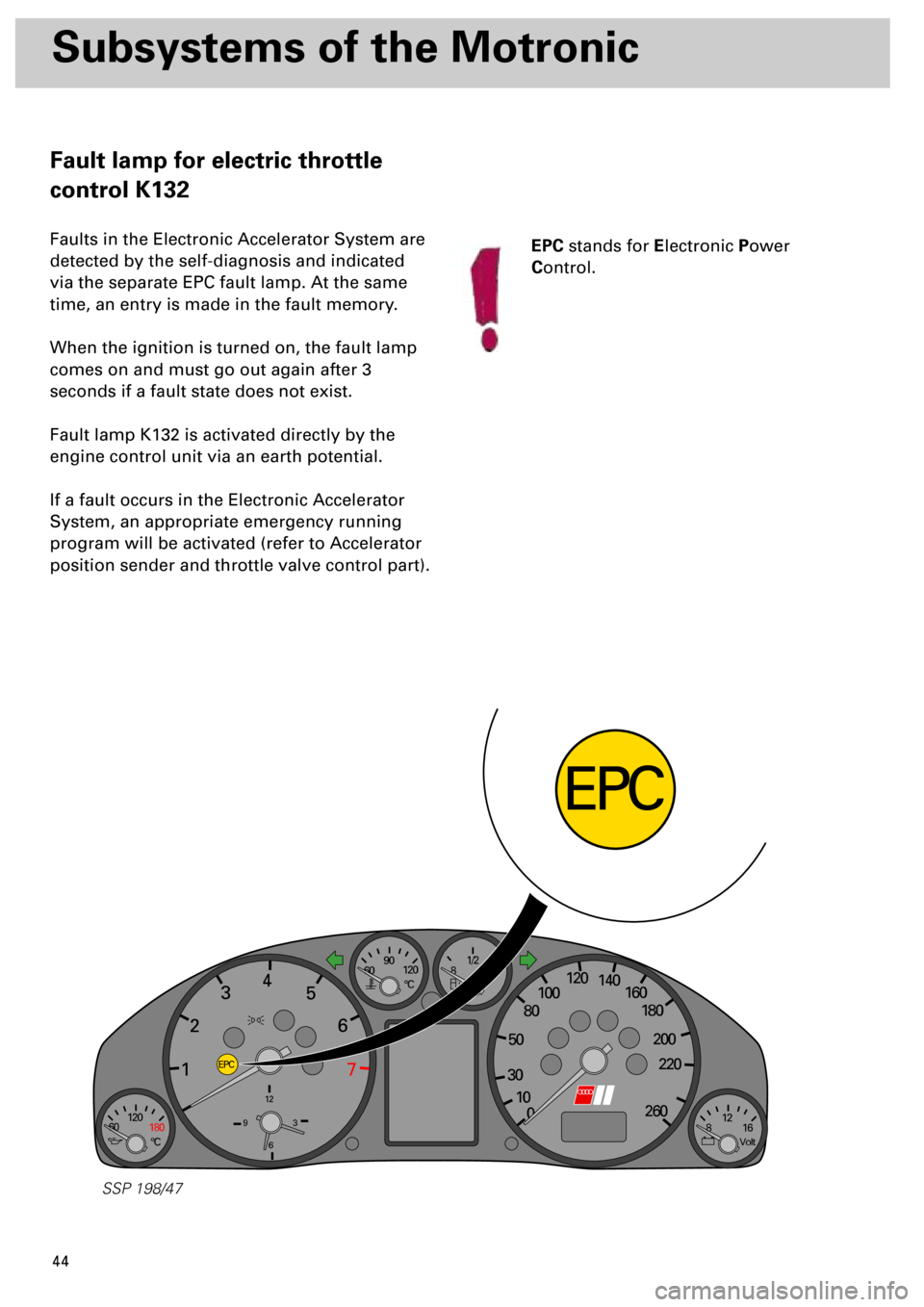
44
Subsystems of the Motronic
120
180
°C 60
90
12
93
6
120
°C 60
12
16
120
100
80
50
30
10140
1234
5
6
7
160
180
200
220
260
Volt8
1/2
1/1
8
0
EPC
EPC
SSP 198/47
Fault lamp for electric throttle
control K132
Faults in the Electronic Accelerator System are
detected by the self-diagnosis and indicated
via the separate EPC fault lamp. At the same
time, an entry is made in the fault memory.
When the ignition is turned on, the fault lamp
comes on and must go out again after 3
seconds if a fault state does not exist.
Fault lamp K132 is activated directly by the
engine control unit via an earth potential.
If a fault occurs in the Electronic Accelerator
System, an appropriate emergency running
program will be activated (refer to Accelerator
position sender and throttle valve control part).
EPC
stands for
E
lectronic
P
ower
C
ontrol.
Page 48 of 72
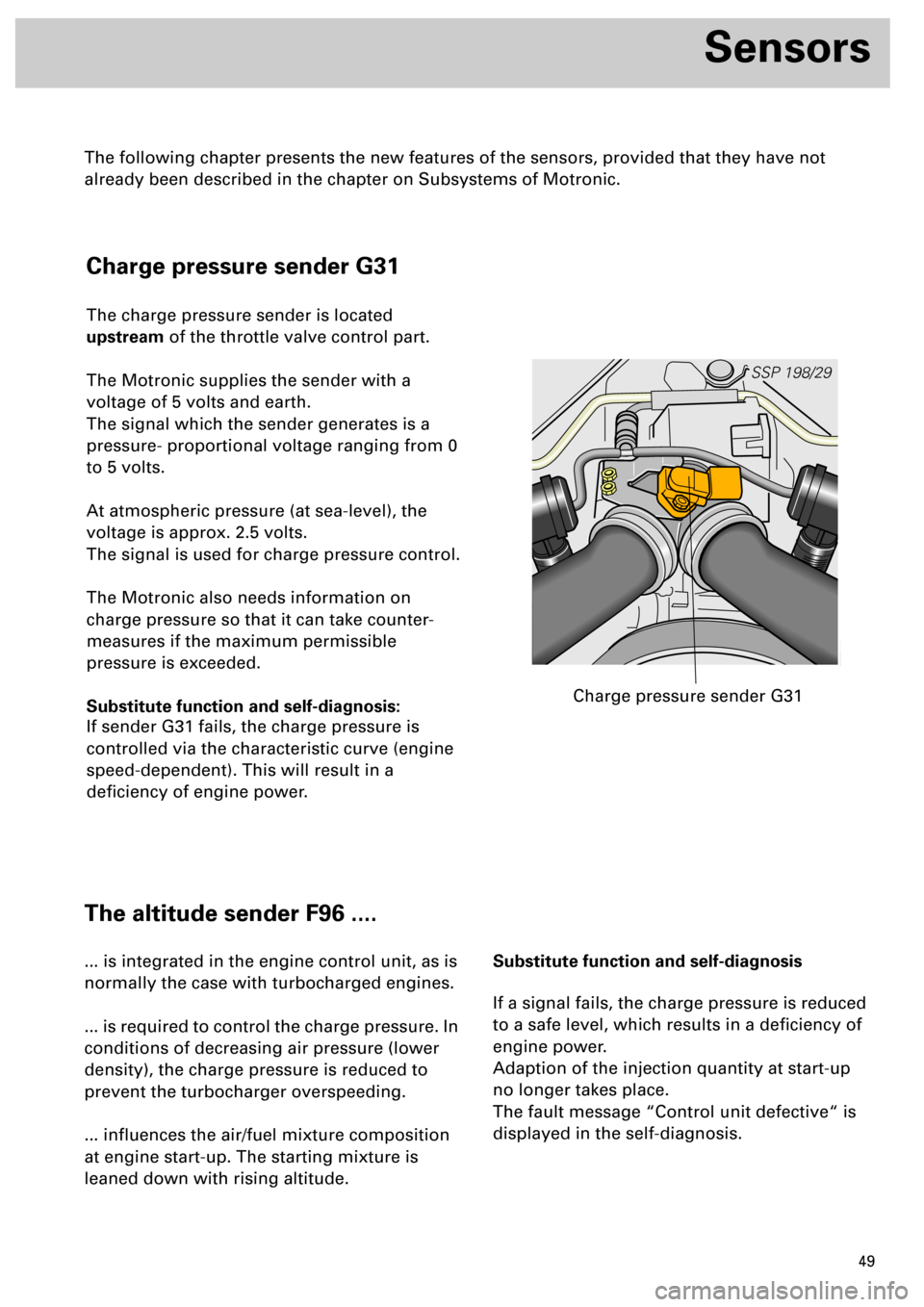
49
Sensors
Charge pressure sender G31
The charge pressure sender is located
upstream of the throttle valve control part.
The Motronic supplies the sender with a
voltage of 5 volts and earth.
The signal which the sender generates is a
pressure- proportional voltage ranging from 0
to 5 volts.
At atmospheric pressure (at sea-level), the
voltage is approx. 2.5 volts.
The signal is used for charge pressure control.
The Motronic also needs information on
charge pressure so that it can take counter-
measures if the maximum permissible
pressure is exceeded.
Substitute function and self-diagnosis:
If sender G31 fails, the charge pressure is
controlled via the characteristic curve (engine
speed-dependent). This will result in a
deficiency of engine power.
SSP 198/29
Charge pressure sender G31
The altitude sender F96 ....
... is integrated in the engine control unit, as is
normally the case with turbocharged engines.
... is required to control the charge pressure. In
conditions of decreasing air pressure (lower
density), the charge pressure is reduced to
prevent the turbocharger overspeeding.
... influences the air/fuel mixture composition
at engine start-up. The starting mixture is
leaned down with rising altitude.Substitute function and self-diagnosis
If a signal fails, the charge pressure is reduced
to a safe level, which results in a deficiency of
engine power.
Adaption of the injection quantity at start-up
no longer takes place.
The fault message “Control unit defective“ is
displayed in the self-diagnosis.
The following chapter presents the new features of the sensors, provided that they have not
already been described in the chapter on Subsystems of Motronic.
Page 49 of 72
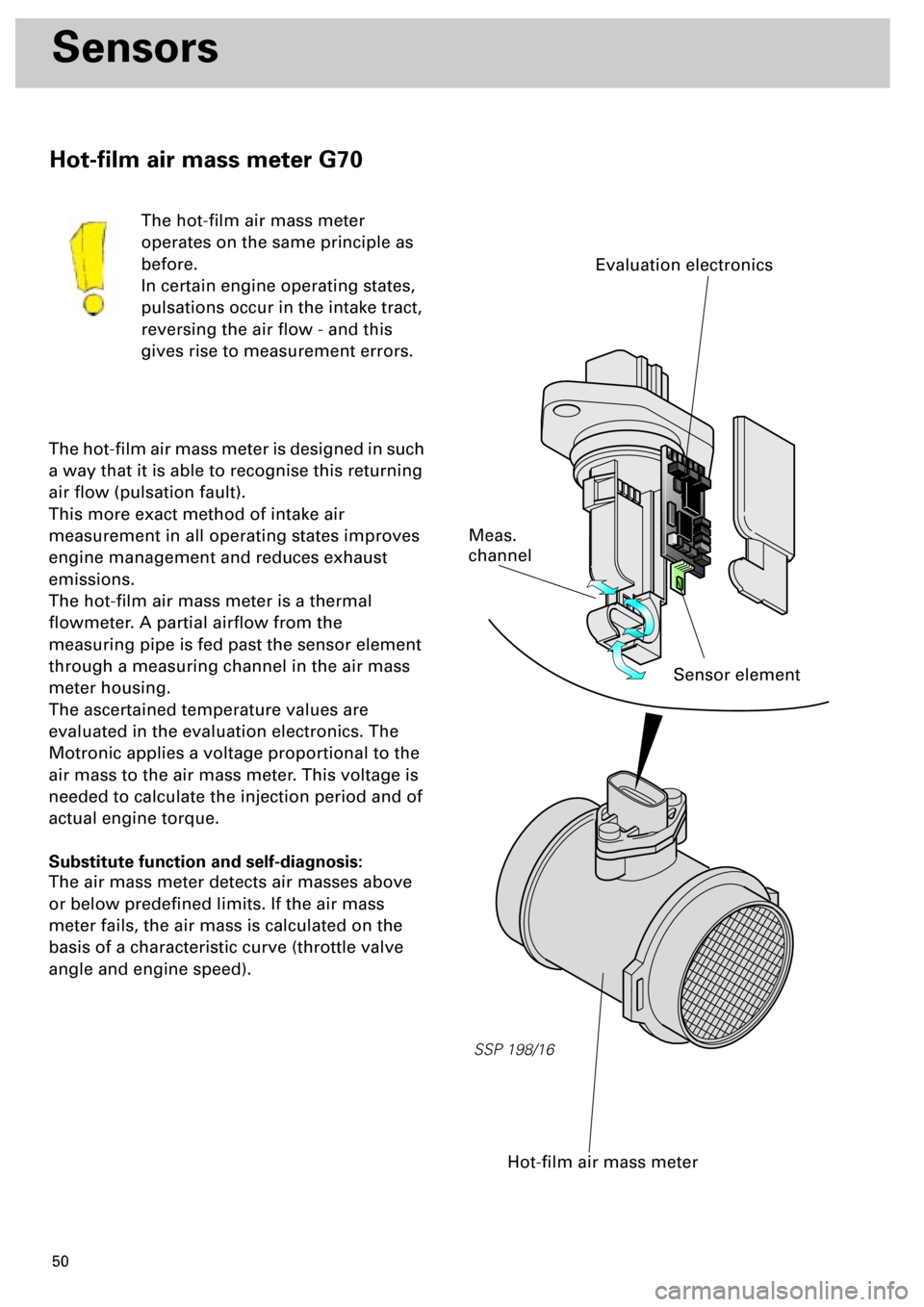
50
SSP 198/16
Sensors
The hot-film air mass meter
operates on the same principle as
before.
In certain engine operating states,
pulsations occur in the intake tract,
reversing the air flow - and this
gives rise to measurement errors.
The hot-film air mass meter is designed in such
a way that it is able to recognise this returning
air flow (pulsation fault).
This more exact method of intake air
measurement in all operating states improves
engine management and reduces exhaust
emissions.
The hot-film air mass meter is a thermal
flowmeter. A partial airflow from the
measuring pipe is fed past the sensor element
through a measuring channel in the air mass
meter housing.
The ascertained temperature values are
evaluated in the evaluation electronics. The
Motronic applies a voltage proportional to the
air mass to the air mass meter. This voltage is
needed to calculate the injection period and of
actual engine torque.
Substitute function and self-diagnosis:
The air mass meter detects air masses above
or below predefined limits. If the air mass
meter fails, the air mass is calculated on the
basis of a characteristic curve (throttle valve
angle and engine speed).
Hot-film air mass meter
Sensor element
Meas.
channel
Evaluation electronics
Hot-film air mass meter G70