check control BMW 3 SERIES 1985 E30 User Guide
[x] Cancel search | Manufacturer: BMW, Model Year: 1985, Model line: 3 SERIES, Model: BMW 3 SERIES 1985 E30Pages: 228, PDF Size: 7.04 MB
Page 76 of 228
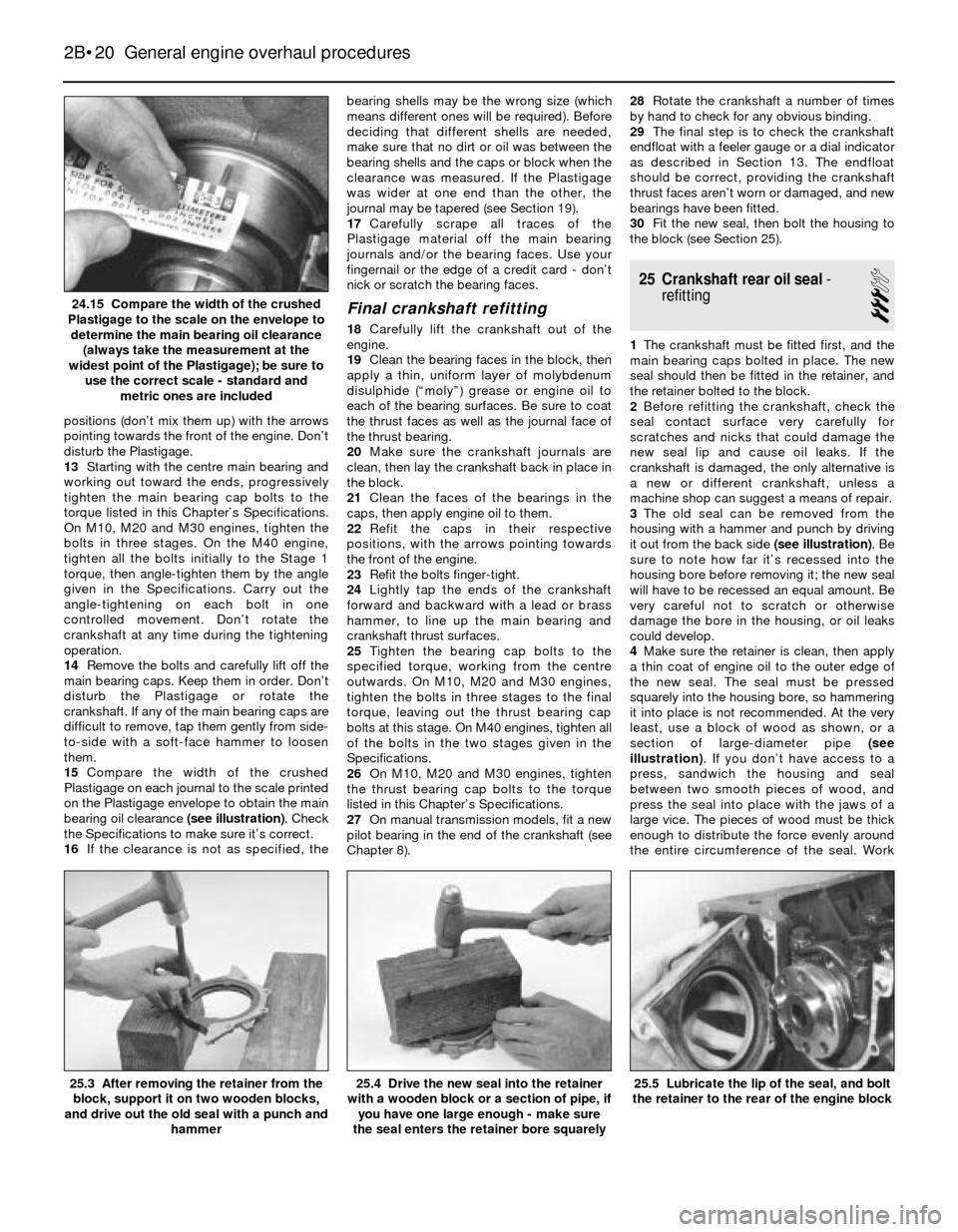
positions (don’t mix them up) with the arrows
pointing towards the front of the engine. Don’t
disturb the Plastigage.
13Starting with the centre main bearing and
working out toward the ends, progressively
tighten the main bearing cap bolts to the
torque listed in this Chapter’s Specifications.
On M10, M20 and M30 engines, tighten the
bolts in three stages. On the M40 engine,
tighten all the bolts initially to the Stage 1
torque, then angle-tighten them by the angle
given in the Specifications. Carry out the
angle-tightening on each bolt in one
controlled movement. Don’t rotate the
crankshaft at any time during the tightening
operation.
14Remove the bolts and carefully lift off the
main bearing caps. Keep them in order. Don’t
disturb the Plastigage or rotate the
crankshaft. If any of the main bearing caps are
difficult to remove, tap them gently from side-
to-side with a soft-face hammer to loosen
them.
15Compare the width of the crushed
Plastigage on each journal to the scale printed
on the Plastigage envelope to obtain the main
bearing oil clearance (see illustration). Check
the Specifications to make sure it’s correct.
16If the clearance is not as specified, thebearing shells may be the wrong size (which
means different ones will be required). Before
deciding that different shells are needed,
make sure that no dirt or oil was between the
bearing shells and the caps or block when the
clearance was measured. If the Plastigage
was wider at one end than the other, the
journal may be tapered (see Section 19).
17Carefully scrape all traces of the
Plastigage material off the main bearing
journals and/or the bearing faces. Use your
fingernail or the edge of a credit card - don’t
nick or scratch the bearing faces.
Final crankshaft refitting
18Carefully lift the crankshaft out of the
engine.
19Clean the bearing faces in the block, then
apply a thin, uniform layer of molybdenum
disulphide (“moly”) grease or engine oil to
each of the bearing surfaces. Be sure to coat
the thrust faces as well as the journal face of
the thrust bearing.
20Make sure the crankshaft journals are
clean, then lay the crankshaft back in place in
the block.
21Clean the faces of the bearings in the
caps, then apply engine oil to them.
22Refit the caps in their respective
positions, with the arrows pointing towards
the front of the engine.
23Refit the bolts finger-tight.
24Lightly tap the ends of the crankshaft
forward and backward with a lead or brass
hammer, to line up the main bearing and
crankshaft thrust surfaces.
25Tighten the bearing cap bolts to the
specified torque, working from the centre
outwards. On M10, M20 and M30 engines,
tighten the bolts in three stages to the final
torque, leaving out the thrust bearing cap
bolts at this stage. On M40 engines, tighten all
of the bolts in the two stages given in the
Specifications.
26On M10, M20 and M30 engines, tighten
the thrust bearing cap bolts to the torque
listed in this Chapter’s Specifications.
27On manual transmission models, fit a new
pilot bearing in the end of the crankshaft (see
Chapter 8).28Rotate the crankshaft a number of times
by hand to check for any obvious binding.
29The final step is to check the crankshaft
endfloat with a feeler gauge or a dial indicator
as described in Section 13. The endfloat
should be correct, providing the crankshaft
thrust faces aren’t worn or damaged, and new
bearings have been fitted.
30Fit the new seal, then bolt the housing to
the block (see Section 25).
25 Crankshaft rear oil seal-
refitting
3
1The crankshaft must be fitted first, and the
main bearing caps bolted in place. The new
seal should then be fitted in the retainer, and
the retainer bolted to the block.
2Before refitting the crankshaft, check the
seal contact surface very carefully for
scratches and nicks that could damage the
new seal lip and cause oil leaks. If the
crankshaft is damaged, the only alternative is
a new or different crankshaft, unless a
machine shop can suggest a means of repair.
3The old seal can be removed from the
housing with a hammer and punch by driving
it out from the back side (see illustration). Be
sure to note how far it’s recessed into the
housing bore before removing it; the new seal
will have to be recessed an equal amount. Be
very careful not to scratch or otherwise
damage the bore in the housing, or oil leaks
could develop.
4Make sure the retainer is clean, then apply
a thin coat of engine oil to the outer edge of
the new seal. The seal must be pressed
squarely into the housing bore, so hammering
it into place is not recommended. At the very
least, use a block of wood as shown, or a
section of large-diameter pipe (see
illustration). If you don’t have access to a
press, sandwich the housing and seal
between two smooth pieces of wood, and
press the seal into place with the jaws of a
large vice. The pieces of wood must be thick
enough to distribute the force evenly around
the entire circumference of the seal. Work
2B•20 General engine overhaul procedures
25.5 Lubricate the lip of the seal, and bolt
the retainer to the rear of the engine block25.4 Drive the new seal into the retainer
with a wooden block or a section of pipe, if
you have one large enough - make sure
the seal enters the retainer bore squarely25.3 After removing the retainer from the
block, support it on two wooden blocks,
and drive out the old seal with a punch and
hammer
24.15 Compare the width of the crushed
Plastigage to the scale on the envelope to
determine the main bearing oil clearance
(always take the measurement at the
widest point of the Plastigage); be sure to
use the correct scale - standard and
metric ones are included
Page 79 of 228
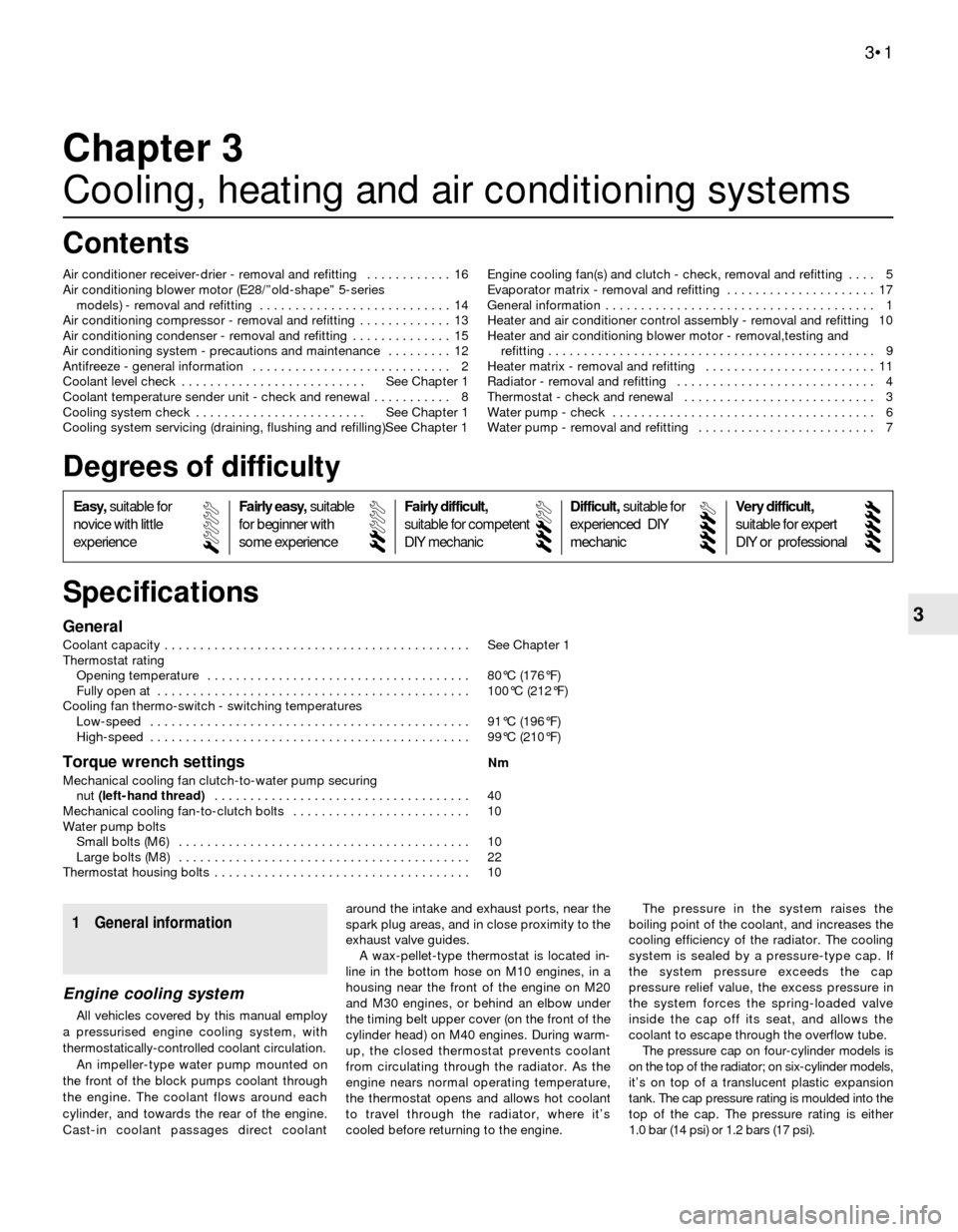
3General
Coolant capacity . . . . . . . . . . . . . . . . . . . . . . . . . . . . . . . . . . . . . . . . . . . See Chapter 1
Thermostat rating
Opening temperature . . . . . . . . . . . . . . . . . . . . . . . . . . . . . . . . . . . . . 80°C (176°F)
Fully open at . . . . . . . . . . . . . . . . . . . . . . . . . . . . . . . . . . . . . . . . . . . . 100°C (212°F)
Cooling fan thermo-switch - switching temperatures
Low-speed . . . . . . . . . . . . . . . . . . . . . . . . . . . . . . . . . . . . . . . . . . . . . 91°C (196°F)
High-speed . . . . . . . . . . . . . . . . . . . . . . . . . . . . . . . . . . . . . . . . . . . . . 99°C (210°F)
Torque wrench settingsNm
Mechanical cooling fan clutch-to-water pump securing
nut (left-hand thread) . . . . . . . . . . . . . . . . . . . . . . . . . . . . . . . . . . . . 40
Mechanical cooling fan-to-clutch bolts . . . . . . . . . . . . . . . . . . . . . . . . . 10
Water pump bolts
Small bolts (M6) . . . . . . . . . . . . . . . . . . . . . . . . . . . . . . . . . . . . . . . . . 10
Large bolts (M8) . . . . . . . . . . . . . . . . . . . . . . . . . . . . . . . . . . . . . . . . . 22
Thermostat housing bolts . . . . . . . . . . . . . . . . . . . . . . . . . . . . . . . . . . . . 10
Chapter 3
Cooling, heating and air conditioning systems
Air conditioner receiver-drier - removal and refitting . . . . . . . . . . . . 16
Air conditioning blower motor (E28/”old-shape” 5-series
models) - removal and refitting . . . . . . . . . . . . . . . . . . . . . . . . . . . 14
Air conditioning compressor - removal and refitting . . . . . . . . . . . . . 13
Air conditioning condenser - removal and refitting . . . . . . . . . . . . . . 15
Air conditioning system - precautions and maintenance . . . . . . . . . 12
Antifreeze - general information . . . . . . . . . . . . . . . . . . . . . . . . . . . . 2
Coolant level check . . . . . . . . . . . . . . . . . . . . . . . . . . See Chapter 1
Coolant temperature sender unit - check and renewal . . . . . . . . . . . 8
Cooling system check . . . . . . . . . . . . . . . . . . . . . . . . See Chapter 1
Cooling system servicing (draining, flushing and refilling)See Chapter 1Engine cooling fan(s) and clutch - check, removal and refitting . . . . 5
Evaporator matrix - removal and refitting . . . . . . . . . . . . . . . . . . . . . 17
General information . . . . . . . . . . . . . . . . . . . . . . . . . . . . . . . . . . . . . . 1
Heater and air conditioner control assembly - removal and refitting 10
Heater and air conditioning blower motor - removal,testing and
refitting . . . . . . . . . . . . . . . . . . . . . . . . . . . . . . . . . . . . . . . . . . . . . . 9
Heater matrix - removal and refitting . . . . . . . . . . . . . . . . . . . . . . . . 11
Radiator - removal and refitting . . . . . . . . . . . . . . . . . . . . . . . . . . . . 4
Thermostat - check and renewal . . . . . . . . . . . . . . . . . . . . . . . . . . . 3
Water pump - check . . . . . . . . . . . . . . . . . . . . . . . . . . . . . . . . . . . . . 6
Water pump - removal and refitting . . . . . . . . . . . . . . . . . . . . . . . . . 7
3•1
Easy,suitable for
novice with little
experienceFairly easy,suitable
for beginner with
some experienceFairly difficult,
suitable for competent
DIY mechanic
Difficult,suitable for
experienced DIY
mechanicVery difficult,
suitable for expert
DIY or professional
Degrees of difficulty
Specifications Contents
1 General information
Engine cooling system
All vehicles covered by this manual employ
a pressurised engine cooling system, with
thermostatically-controlled coolant circulation.
An impeller-type water pump mounted on
the front of the block pumps coolant through
the engine. The coolant flows around each
cylinder, and towards the rear of the engine.
Cast-in coolant passages direct coolantaround the intake and exhaust ports, near the
spark plug areas, and in close proximity to the
exhaust valve guides.
A wax-pellet-type thermostat is located in-
line in the bottom hose on M10 engines, in a
housing near the front of the engine on M20
and M30 engines, or behind an elbow under
the timing belt upper cover (on the front of the
cylinder head) on M40 engines. During warm-
up, the closed thermostat prevents coolant
from circulating through the radiator. As the
engine nears normal operating temperature,
the thermostat opens and allows hot coolant
to travel through the radiator, where it’s
cooled before returning to the engine.The pressure in the system raises the
boiling point of the coolant, and increases the
cooling efficiency of the radiator. The cooling
system is sealed by a pressure-type cap. If
the system pressure exceeds the cap
pressure relief value, the excess pressure in
the system forces the spring-loaded valve
inside the cap off its seat, and allows the
coolant to escape through the overflow tube.
The pressure cap on four-cylinder models is
on the top of the radiator; on six-cylinder models,
it’s on top of a translucent plastic expansion
tank. The cap pressure rating is moulded into the
top of the cap. The pressure rating is either
1.0 bar (14 psi) or 1.2 bars (17 psi).
Page 80 of 228
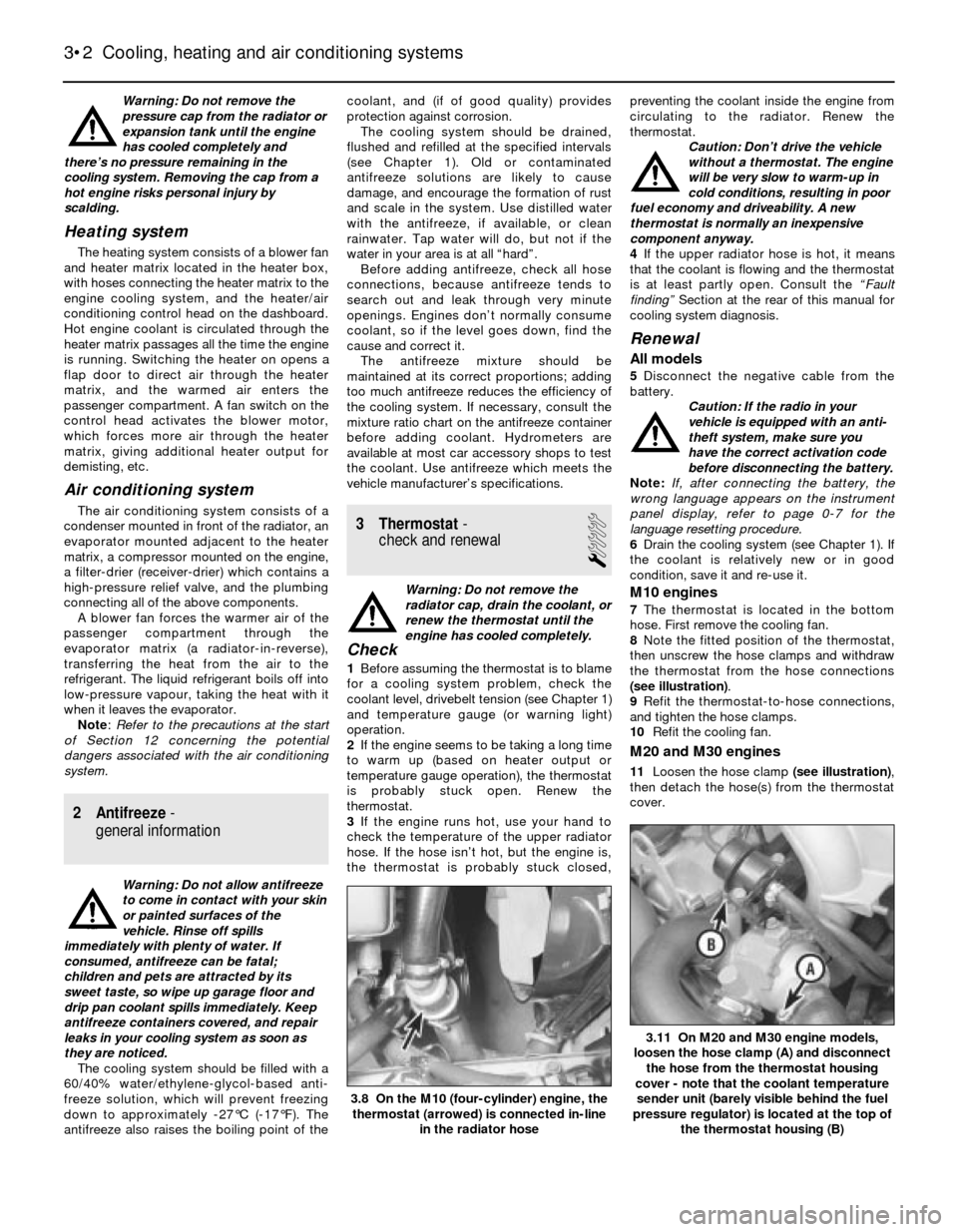
Warning: Do not remove the
pressure cap from the radiator or
expansion tank until the engine
has cooled completely and
there’s no pressure remaining in the
cooling system. Removing the cap from a
hot engine risks personal injury by
scalding.
Heating system
The heating system consists of a blower fan
and heater matrix located in the heater box,
with hoses connecting the heater matrix to the
engine cooling system, and the heater/air
conditioning control head on the dashboard.
Hot engine coolant is circulated through the
heater matrix passages all the time the engine
is running. Switching the heater on opens a
flap door to direct air through the heater
matrix, and the warmed air enters the
passenger compartment. A fan switch on the
control head activates the blower motor,
which forces more air through the heater
matrix, giving additional heater output for
demisting, etc.
Air conditioning system
The air conditioning system consists of a
condenser mounted in front of the radiator, an
evaporator mounted adjacent to the heater
matrix, a compressor mounted on the engine,
a filter-drier (receiver-drier) which contains a
high-pressure relief valve, and the plumbing
connecting all of the above components.
A blower fan forces the warmer air of the
passenger compartment through the
evaporator matrix (a radiator-in-reverse),
transferring the heat from the air to the
refrigerant. The liquid refrigerant boils off into
low-pressure vapour, taking the heat with it
when it leaves the evaporator.
Note: Refer to the precautions at the start
of Section 12 concerning the potential
dangers associated with the air conditioning
system.
2 Antifreeze-
general information
Warning: Do not allow antifreeze
to come in contact with your skin
or painted surfaces of the
vehicle. Rinse off spills
immediately with plenty of water. If
consumed, antifreeze can be fatal;
children and pets are attracted by its
sweet taste, so wipe up garage floor and
drip pan coolant spills immediately. Keep
antifreeze containers covered, and repair
leaks in your cooling system as soon as
they are noticed.
The cooling system should be filled with a
60/40% water/ethylene-glycol-based anti-
freeze solution, which will prevent freezing
down to approximately -27°C (-17°F). The
antifreeze also raises the boiling point of thecoolant, and (if of good quality) provides
protection against corrosion.
The cooling system should be drained,
flushed and refilled at the specified intervals
(see Chapter 1). Old or contaminated
antifreeze solutions are likely to cause
damage, and encourage the formation of rust
and scale in the system. Use distilled water
with the antifreeze, if available, or clean
rainwater. Tap water will do, but not if the
water in your area is at all “hard”.
Before adding antifreeze, check all hose
connections, because antifreeze tends to
search out and leak through very minute
openings. Engines don’t normally consume
coolant, so if the level goes down, find the
cause and correct it.
The antifreeze mixture should be
maintained at its correct proportions; adding
too much antifreeze reduces the efficiency of
the cooling system. If necessary, consult the
mixture ratio chart on the antifreeze container
before adding coolant. Hydrometers are
available at most car accessory shops to test
the coolant. Use antifreeze which meets the
vehicle manufacturer’s specifications.
3 Thermostat-
check and renewal
1
Warning: Do not remove the
radiator cap, drain the coolant, or
renew the thermostat until the
engine has cooled completely.
Check
1Before assuming the thermostat is to blame
for a cooling system problem, check the
coolant level, drivebelt tension (see Chapter 1)
and temperature gauge (or warning light)
operation.
2If the engine seems to be taking a long time
to warm up (based on heater output or
temperature gauge operation), the thermostat
is probably stuck open. Renew the
thermostat.
3If the engine runs hot, use your hand to
check the temperature of the upper radiator
hose. If the hose isn’t hot, but the engine is,
the thermostat is probably stuck closed,preventing the coolant inside the engine from
circulating to the radiator. Renew the
thermostat.
Caution: Don’t drive the vehicle
without a thermostat. The engine
will be very slow to warm-up in
cold conditions, resulting in poor
fuel economy and driveability. A new
thermostat is normally an inexpensive
component anyway.
4If the upper radiator hose is hot, it means
that the coolant is flowing and the thermostat
is at least partly open. Consult the “Fault
finding” Section at the rear of this manual for
cooling system diagnosis.
Renewal
All models
5Disconnect the negative cable from the
battery.
Caution: If the radio in your
vehicle is equipped with an anti-
theft system, make sure you
have the correct activation code
before disconnecting the battery.
Note: If, after connecting the battery, the
wrong language appears on the instrument
panel display, refer to page 0-7 for the
language resetting procedure.
6Drain the cooling system (see Chapter 1). If
the coolant is relatively new or in good
condition, save it and re-use it.
M10 engines
7The thermostat is located in the bottom
hose. First remove the cooling fan.
8Note the fitted position of the thermostat,
then unscrew the hose clamps and withdraw
the thermostat from the hose connections
(see illustration).
9Refit the thermostat-to-hose connections,
and tighten the hose clamps.
10Refit the cooling fan.
M20 and M30 engines
11Loosen the hose clamp (see illustration),
then detach the hose(s) from the thermostat
cover.
3•2 Cooling, heating and air conditioning systems
3.11 On M20 and M30 engine models,
loosen the hose clamp (A) and disconnect
the hose from the thermostat housing
cover - note that the coolant temperature
sender unit (barely visible behind the fuel
pressure regulator) is located at the top of
the thermostat housing (B)
3.8 On the M10 (four-cylinder) engine, the
thermostat (arrowed) is connected in-line
in the radiator hose
Page 82 of 228
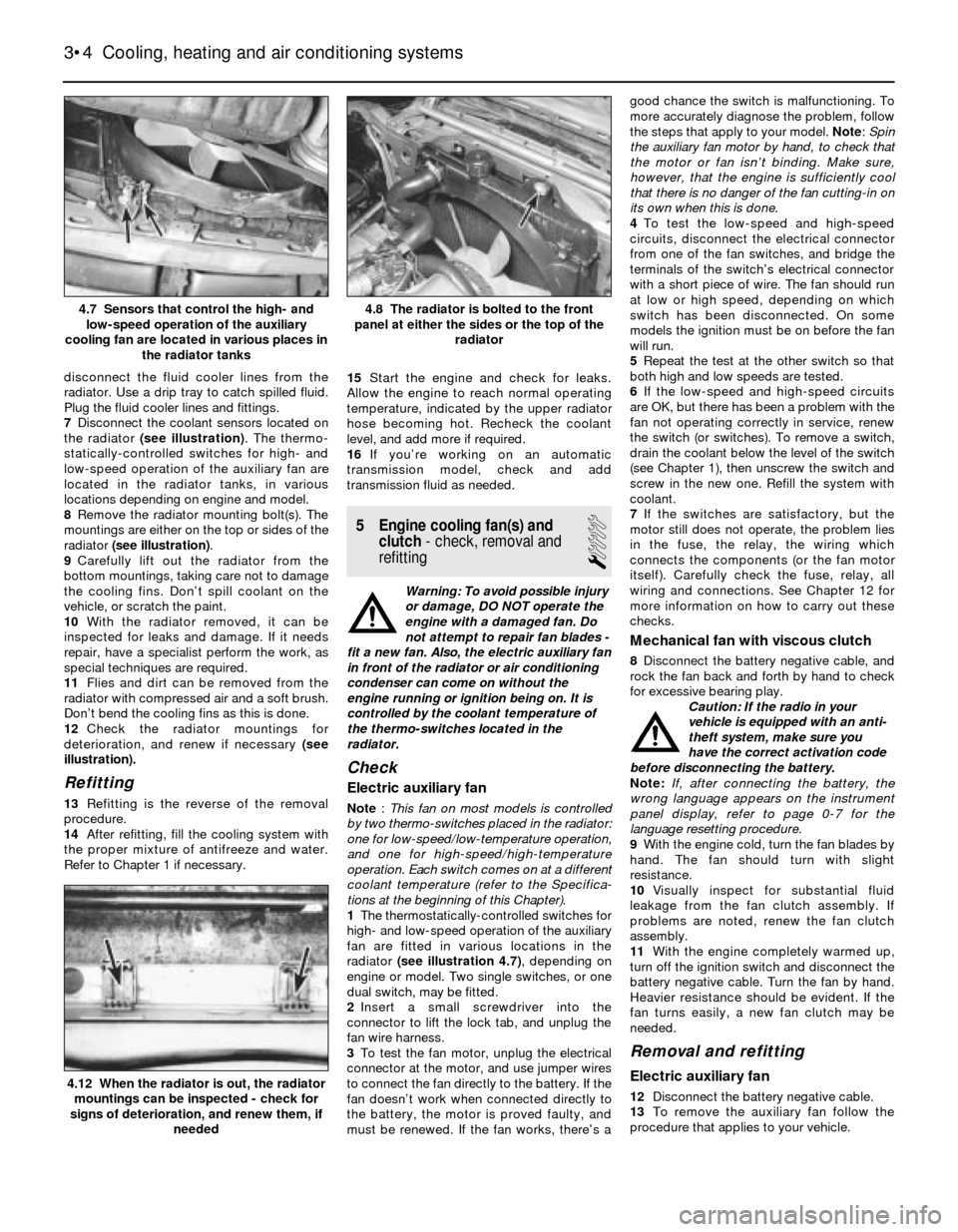
disconnect the fluid cooler lines from the
radiator. Use a drip tray to catch spilled fluid.
Plug the fluid cooler lines and fittings.
7Disconnect the coolant sensors located on
the radiator (see illustration). The thermo-
statically-controlled switches for high- and
low-speed operation of the auxiliary fan are
located in the radiator tanks, in various
locations depending on engine and model.
8Remove the radiator mounting bolt(s). The
mountings are either on the top or sides of the
radiator (see illustration).
9Carefully lift out the radiator from the
bottom mountings, taking care not to damage
the cooling fins. Don’t spill coolant on the
vehicle, or scratch the paint.
10With the radiator removed, it can be
inspected for leaks and damage. If it needs
repair, have a specialist perform the work, as
special techniques are required.
11Flies and dirt can be removed from the
radiator with compressed air and a soft brush.
Don’t bend the cooling fins as this is done.
12Check the radiator mountings for
deterioration, and renew if necessary (see
illustration).
Refitting
13Refitting is the reverse of the removal
procedure.
14After refitting, fill the cooling system with
the proper mixture of antifreeze and water.
Refer to Chapter 1 if necessary.15Start the engine and check for leaks.
Allow the engine to reach normal operating
temperature, indicated by the upper radiator
hose becoming hot. Recheck the coolant
level, and add more if required.
16If you’re working on an automatic
transmission model, check and add
transmission fluid as needed.
5 Engine cooling fan(s) and
clutch- check, removal and
refitting
1
Warning: To avoid possible injury
or damage, DO NOT operate the
engine with a damaged fan. Do
not attempt to repair fan blades -
fit a new fan. Also, the electric auxiliary fan
in front of the radiator or air conditioning
condenser can come on without the
engine running or ignition being on. It is
controlled by the coolant temperature of
the thermo-switches located in the
radiator.
Check
Electric auxiliary fan
Note: This fan on most models is controlled
by two thermo-switches placed in the radiator:
one for low-speed/low-temperature operation,
and one for high-speed/high-temperature
operation. Each switch comes on at a different
coolant temperature (refer to the Specifica-
tions at the beginning of this Chapter).
1The thermostatically-controlled switches for
high- and low-speed operation of the auxiliary
fan are fitted in various locations in the
radiator (see illustration 4.7), depending on
engine or model. Two single switches, or one
dual switch, may be fitted.
2Insert a small screwdriver into the
connector to lift the lock tab, and unplug the
fan wire harness.
3To test the fan motor, unplug the electrical
connector at the motor, and use jumper wires
to connect the fan directly to the battery. If the
fan doesn’t work when connected directly to
the battery, the motor is proved faulty, and
must be renewed. If the fan works, there’s agood chance the switch is malfunctioning. To
more accurately diagnose the problem, follow
the steps that apply to your model. Note: Spin
the auxiliary fan motor by hand, to check that
the motor or fan isn’t binding. Make sure,
however, that the engine is sufficiently cool
that there is no danger of the fan cutting-in on
its own when this is done.
4To test the low-speed and high-speed
circuits, disconnect the electrical connector
from one of the fan switches, and bridge the
terminals of the switch’s electrical connector
with a short piece of wire. The fan should run
at low or high speed, depending on which
switch has been disconnected. On some
models the ignition must be on before the fan
will run.
5Repeat the test at the other switch so that
both high and low speeds are tested.
6If the low-speed and high-speed circuits
are OK, but there has been a problem with the
fan not operating correctly in service, renew
the switch (or switches). To remove a switch,
drain the coolant below the level of the switch
(see Chapter 1), then unscrew the switch and
screw in the new one. Refill the system with
coolant.
7If the switches are satisfactory, but the
motor still does not operate, the problem lies
in the fuse, the relay, the wiring which
connects the components (or the fan motor
itself). Carefully check the fuse, relay, all
wiring and connections. See Chapter 12 for
more information on how to carry out these
checks.
Mechanical fan with viscous clutch
8Disconnect the battery negative cable, and
rock the fan back and forth by hand to check
for excessive bearing play.
Caution: If the radio in your
vehicle is equipped with an anti-
theft system, make sure you
have the correct activation code
before disconnecting the battery.
Note: If, after connecting the battery, the
wrong language appears on the instrument
panel display, refer to page 0-7 for the
language resetting procedure.
9With the engine cold, turn the fan blades by
hand. The fan should turn with slight
resistance.
10Visually inspect for substantial fluid
leakage from the fan clutch assembly. If
problems are noted, renew the fan clutch
assembly.
11With the engine completely warmed up,
turn off the ignition switch and disconnect the
battery negative cable. Turn the fan by hand.
Heavier resistance should be evident. If the
fan turns easily, a new fan clutch may be
needed.
Removal and refitting
Electric auxiliary fan
12Disconnect the battery negative cable.
13To remove the auxiliary fan follow the
procedure that applies to your vehicle.
3•4 Cooling, heating and air conditioning systems
4.12 When the radiator is out, the radiator
mountings can be inspected - check for
signs of deterioration, and renew them, if
needed
4.8 The radiator is bolted to the front
panel at either the sides or the top of the
radiator4.7 Sensors that control the high- and
low-speed operation of the auxiliary
cooling fan are located in various places in
the radiator tanks
Page 85 of 228
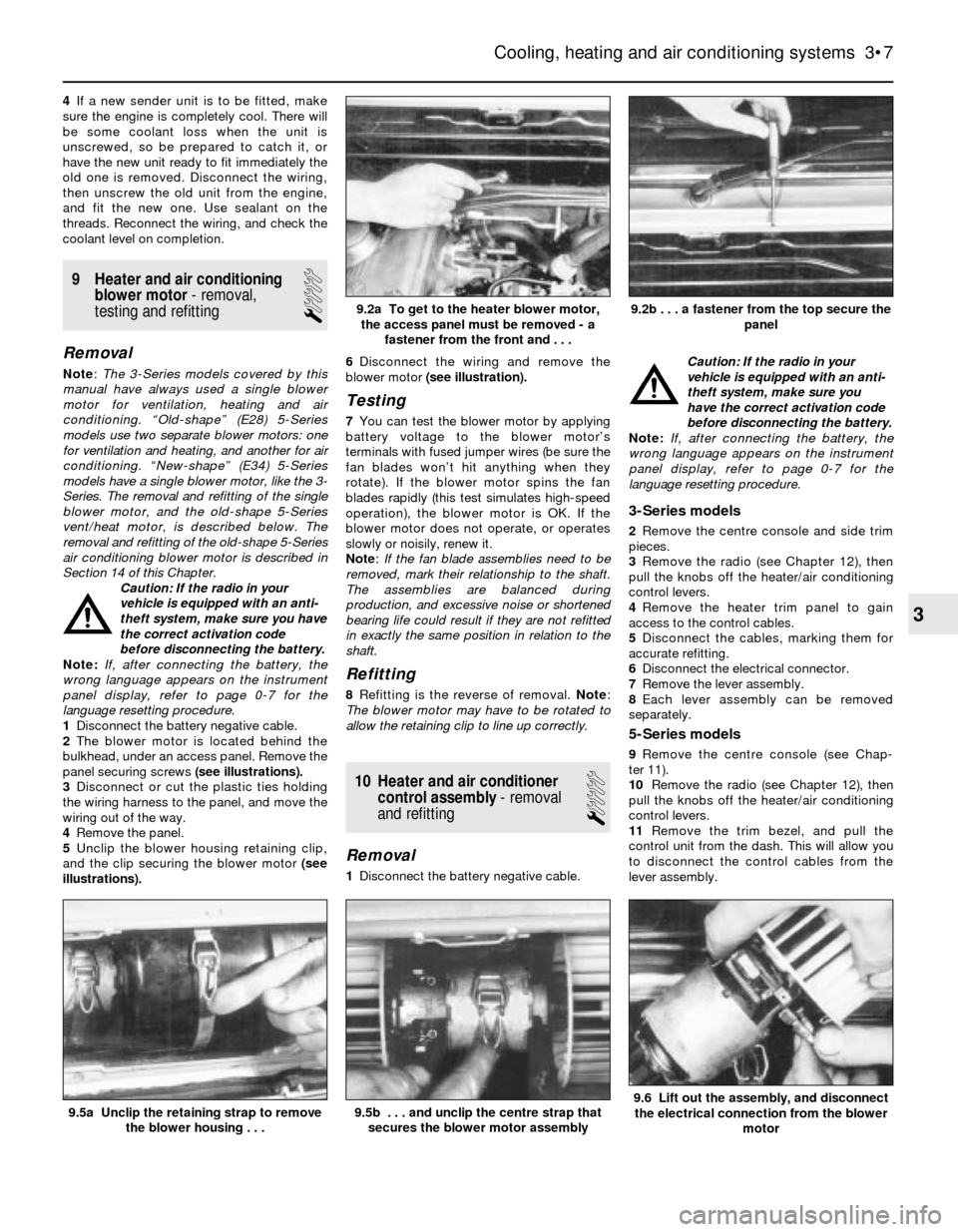
4If a new sender unit is to be fitted, make
sure the engine is completely cool. There will
be some coolant loss when the unit is
unscrewed, so be prepared to catch it, or
have the new unit ready to fit immediately the
old one is removed. Disconnect the wiring,
then unscrew the old unit from the engine,
and fit the new one. Use sealant on the
threads. Reconnect the wiring, and check the
coolant level on completion.
9 Heater and air conditioning
blower motor- removal,
testing and refitting
1
Removal
Note: The 3-Series models covered by this
manual have always used a single blower
motor for ventilation, heating and air
conditioning. “Old-shape” (E28) 5-Series
models use two separate blower motors: one
for ventilation and heating, and another for air
conditioning. “New-shape” (E34) 5-Series
models have a single blower motor, like the 3-
Series. The removal and refitting of the single
blower motor, and the old-shape 5-Series
vent/heat motor, is described below. The
removal and refitting of the old-shape 5-Series
air conditioning blower motor is described in
Section 14 of this Chapter.
Caution: If the radio in your
vehicle is equipped with an anti-
theft system, make sure you have
the correct activation code
before disconnecting the battery.
Note: If, after connecting the battery, the
wrong language appears on the instrument
panel display, refer to page 0-7 for the
language resetting procedure.
1Disconnect the battery negative cable.
2The blower motor is located behind the
bulkhead, under an access panel. Remove the
panel securing screws (see illustrations).
3Disconnect or cut the plastic ties holding
the wiring harness to the panel, and move the
wiring out of the way.
4Remove the panel.
5Unclip the blower housing retaining clip,
and the clip securing the blower motor (see
illustrations).6Disconnect the wiring and remove the
blower motor (see illustration).
Testing
7You can test the blower motor by applying
battery voltage to the blower motor’s
terminals with fused jumper wires (be sure the
fan blades won’t hit anything when they
rotate). If the blower motor spins the fan
blades rapidly (this test simulates high-speed
operation), the blower motor is OK. If the
blower motor does not operate, or operates
slowly or noisily, renew it.
Note: If the fan blade assemblies need to be
removed, mark their relationship to the shaft.
The assemblies are balanced during
production, and excessive noise or shortened
bearing life could result if they are not refitted
in exactly the same position in relation to the
shaft.
Refitting
8Refitting is the reverse of removal. Note:
The blower motor may have to be rotated to
allow the retaining clip to line up correctly.
10 Heater and air conditioner
control assembly- removal
and refitting
1
Removal
1Disconnect the battery negative cable. Caution: If the radio in your
vehicle is equipped with an anti-
theft system, make sure you
have the correct activation code
before disconnecting the battery.
Note: If, after connecting the battery, the
wrong language appears on the instrument
panel display, refer to page 0-7 for the
language resetting procedure.
3-Series models
2Remove the centre console and side trim
pieces.
3Remove the radio (see Chapter 12), then
pull the knobs off the heater/air conditioning
control levers.
4Remove the heater trim panel to gain
access to the control cables.
5Disconnect the cables, marking them for
accurate refitting.
6Disconnect the electrical connector.
7Remove the lever assembly.
8Each lever assembly can be removed
separately.
5-Series models
9Remove the centre console (see Chap-
ter 11).
10Remove the radio (see Chapter 12), then
pull the knobs off the heater/air conditioning
control levers.
11Remove the trim bezel, and pull the
control unit from the dash. This will allow you
to disconnect the control cables from the
lever assembly.
Cooling, heating and air conditioning systems 3•7
9.5a Unclip the retaining strap to remove
the blower housing . . .
9.2b . . . a fastener from the top secure the
panel9.2a To get to the heater blower motor,
the access panel must be removed - a
fastener from the front and . . .
9.6 Lift out the assembly, and disconnect
the electrical connection from the blower
motor9.5b . . . and unclip the centre strap that
secures the blower motor assembly
3
Page 86 of 228
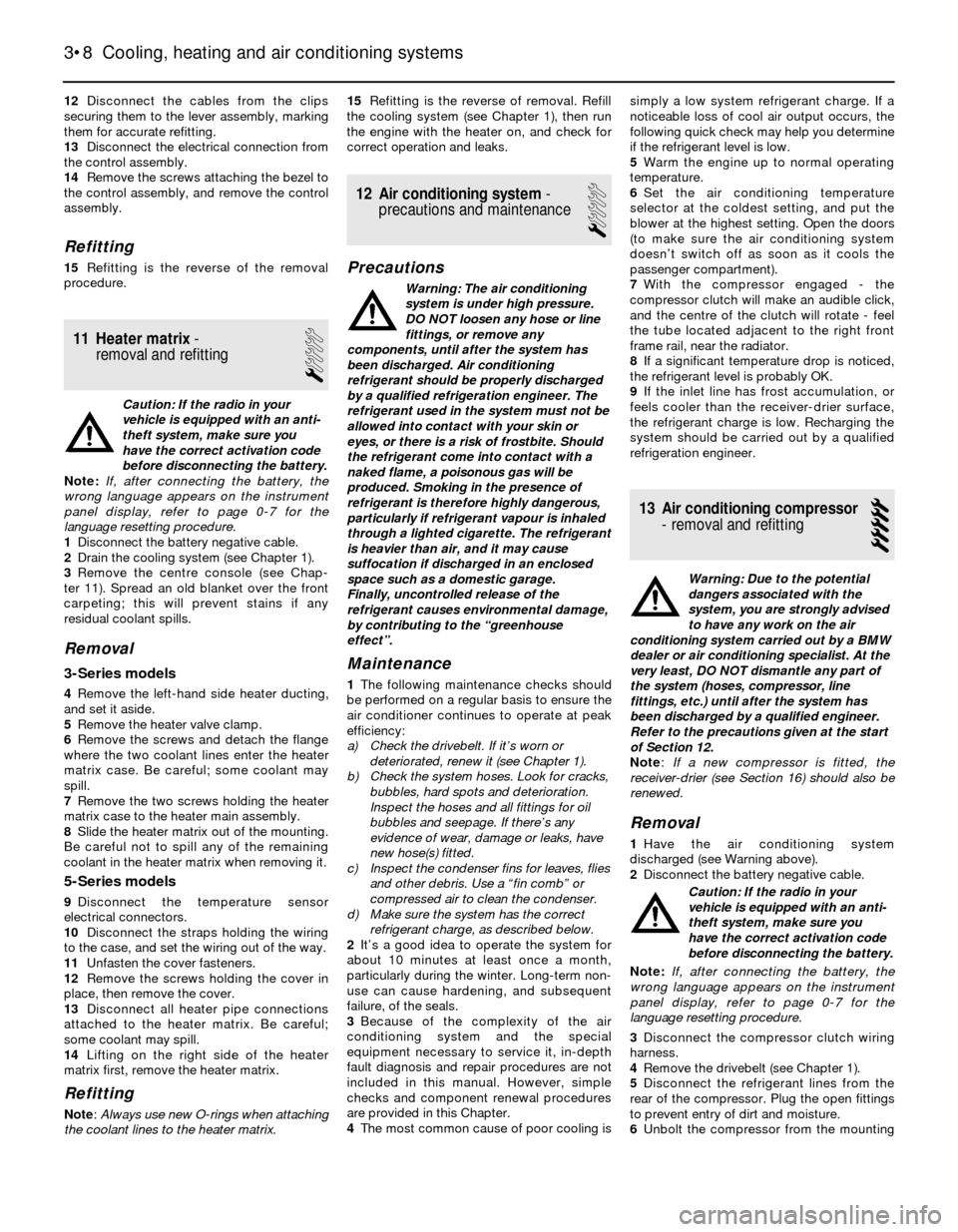
12Disconnect the cables from the clips
securing them to the lever assembly, marking
them for accurate refitting.
13Disconnect the electrical connection from
the control assembly.
14Remove the screws attaching the bezel to
the control assembly, and remove the control
assembly.
Refitting
15Refitting is the reverse of the removal
procedure.
11 Heater matrix-
removal and refitting
1
Caution: If the radio in your
vehicle is equipped with an anti-
theft system, make sure you
have the correct activation code
before disconnecting the battery.
Note: If, after connecting the battery, the
wrong language appears on the instrument
panel display, refer to page 0-7 for the
language resetting procedure.
1Disconnect the battery negative cable.
2Drain the cooling system (see Chapter 1).
3Remove the centre console (see Chap-
ter 11). Spread an old blanket over the front
carpeting; this will prevent stains if any
residual coolant spills.
Removal
3-Series models
4Remove the left-hand side heater ducting,
and set it aside.
5Remove the heater valve clamp.
6Remove the screws and detach the flange
where the two coolant lines enter the heater
matrix case. Be careful; some coolant may
spill.
7Remove the two screws holding the heater
matrix case to the heater main assembly.
8Slide the heater matrix out of the mounting.
Be careful not to spill any of the remaining
coolant in the heater matrix when removing it.
5-Series models
9Disconnect the temperature sensor
electrical connectors.
10Disconnect the straps holding the wiring
to the case, and set the wiring out of the way.
11Unfasten the cover fasteners.
12Remove the screws holding the cover in
place, then remove the cover.
13Disconnect all heater pipe connections
attached to the heater matrix. Be careful;
some coolant may spill.
14Lifting on the right side of the heater
matrix first, remove the heater matrix.
Refitting
Note: Always use new O-rings when attaching
the coolant lines to the heater matrix.15Refitting is the reverse of removal. Refill
the cooling system (see Chapter 1), then run
the engine with the heater on, and check for
correct operation and leaks.
12 Air conditioning system-
precautions and maintenance
1
Precautions
Warning: The air conditioning
system is under high pressure.
DO NOT loosen any hose or line
fittings, or remove any
components, until after the system has
been discharged. Air conditioning
refrigerant should be properly discharged
by a qualified refrigeration engineer. The
refrigerant used in the system must not be
allowed into contact with your skin or
eyes, or there is a risk of frostbite. Should
the refrigerant come into contact with a
naked flame, a poisonous gas will be
produced. Smoking in the presence of
refrigerant is therefore highly dangerous,
particularly if refrigerant vapour is inhaled
through a lighted cigarette. The refrigerant
is heavier than air, and it may cause
suffocation if discharged in an enclosed
space such as a domestic garage.
Finally, uncontrolled release of the
refrigerant causes environmental damage,
by contributing to the “greenhouse
effect”.
Maintenance
1The following maintenance checks should
be performed on a regular basis to ensure the
air conditioner continues to operate at peak
efficiency:
a) Check the drivebelt. If it’s worn or
deteriorated, renew it (see Chapter 1).
b) Check the system hoses. Look for cracks,
bubbles, hard spots and deterioration.
Inspect the hoses and all fittings for oil
bubbles and seepage. If there’s any
evidence of wear, damage or leaks, have
new hose(s) fitted.
c) Inspect the condenser fins for leaves, flies
and other debris. Use a “fin comb” or
compressed air to clean the condenser.
d) Make sure the system has the correct
refrigerant charge, as described below.
2It’s a good idea to operate the system for
about 10 minutes at least once a month,
particularly during the winter. Long-term non-
use can cause hardening, and subsequent
failure, of the seals.
3Because of the complexity of the air
conditioning system and the special
equipment necessary to service it, in-depth
fault diagnosis and repair procedures are not
included in this manual. However, simple
checks and component renewal procedures
are provided in this Chapter.
4The most common cause of poor cooling issimply a low system refrigerant charge. If a
noticeable loss of cool air output occurs, the
following quick check may help you determine
if the refrigerant level is low.
5Warm the engine up to normal operating
temperature.
6Set the air conditioning temperature
selector at the coldest setting, and put the
blower at the highest setting. Open the doors
(to make sure the air conditioning system
doesn’t switch off as soon as it cools the
passenger compartment).
7With the compressor engaged - the
compressor clutch will make an audible click,
and the centre of the clutch will rotate - feel
the tube located adjacent to the right front
frame rail, near the radiator.
8If a significant temperature drop is noticed,
the refrigerant level is probably OK.
9If the inlet line has frost accumulation, or
feels cooler than the receiver-drier surface,
the refrigerant charge is low. Recharging the
system should be carried out by a qualified
refrigeration engineer.
13 Air conditioning compressor
- removal and refitting
5
Warning: Due to the potential
dangers associated with the
system, you are strongly advised
to have any work on the air
conditioning system carried out by a BMW
dealer or air conditioning specialist. At the
very least, DO NOT dismantle any part of
the system (hoses, compressor, line
fittings, etc.) until after the system has
been discharged by a qualified engineer.
Refer to the precautions given at the start
of Section 12.
Note: If a new compressor is fitted, the
receiver-drier (see Section 16) should also be
renewed.
Removal
1Have the air conditioning system
discharged (see Warning above).
2Disconnect the battery negative cable.
Caution: If the radio in your
vehicle is equipped with an anti-
theft system, make sure you
have the correct activation code
before disconnecting the battery.
Note: If, after connecting the battery, the
wrong language appears on the instrument
panel display, refer to page 0-7 for the
language resetting procedure.
3Disconnect the compressor clutch wiring
harness.
4Remove the drivebelt (see Chapter 1).
5Disconnect the refrigerant lines from the
rear of the compressor. Plug the open fittings
to prevent entry of dirt and moisture.
6Unbolt the compressor from the mounting
3•8 Cooling, heating and air conditioning systems
Page 90 of 228
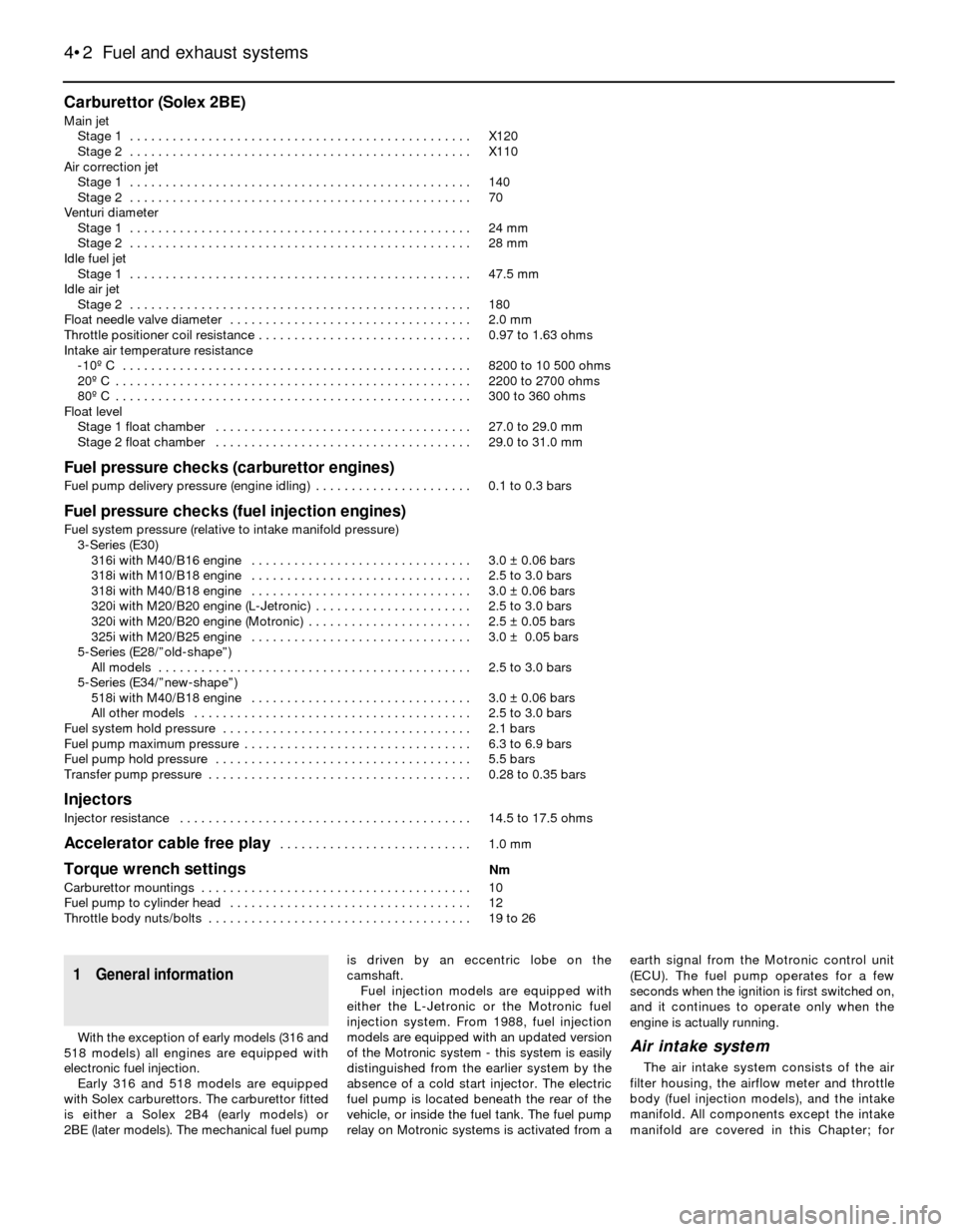
Carburettor (Solex 2BE)
Main jet
Stage 1 . . . . . . . . . . . . . . . . . . . . . . . . . . . . . . . . . . . . . . . . . . . . . . . . X120
Stage 2 . . . . . . . . . . . . . . . . . . . . . . . . . . . . . . . . . . . . . . . . . . . . . . . . X110
Air correction jet
Stage 1 . . . . . . . . . . . . . . . . . . . . . . . . . . . . . . . . . . . . . . . . . . . . . . . . 140
Stage 2 . . . . . . . . . . . . . . . . . . . . . . . . . . . . . . . . . . . . . . . . . . . . . . . . 70
Venturi diameter
Stage 1 . . . . . . . . . . . . . . . . . . . . . . . . . . . . . . . . . . . . . . . . . . . . . . . . 24 mm
Stage 2 . . . . . . . . . . . . . . . . . . . . . . . . . . . . . . . . . . . . . . . . . . . . . . . . 28 mm
Idle fuel jet
Stage 1 . . . . . . . . . . . . . . . . . . . . . . . . . . . . . . . . . . . . . . . . . . . . . . . . 47.5 mm
Idle air jet
Stage 2 . . . . . . . . . . . . . . . . . . . . . . . . . . . . . . . . . . . . . . . . . . . . . . . . 180
Float needle valve diameter . . . . . . . . . . . . . . . . . . . . . . . . . . . . . . . . . . 2.0 mm
Throttle positioner coil resistance . . . . . . . . . . . . . . . . . . . . . . . . . . . . . . 0.97 to 1.63 ohms
Intake air temperature resistance
-10º C . . . . . . . . . . . . . . . . . . . . . . . . . . . . . . . . . . . . . . . . . . . . . . . . . 8200 to 10 500 ohms
20º C . . . . . . . . . . . . . . . . . . . . . . . . . . . . . . . . . . . . . . . . . . . . . . . . . . 2200 to 2700 ohms
80º C . . . . . . . . . . . . . . . . . . . . . . . . . . . . . . . . . . . . . . . . . . . . . . . . . . 300 to 360 ohms
Float level
Stage 1 float chamber . . . . . . . . . . . . . . . . . . . . . . . . . . . . . . . . . . . . 27.0 to 29.0 mm
Stage 2 float chamber . . . . . . . . . . . . . . . . . . . . . . . . . . . . . . . . . . . . 29.0 to 31.0 mm
Fuel pressure checks (carburettor engines)
Fuel pump delivery pressure (engine idling) . . . . . . . . . . . . . . . . . . . . . . 0.1 to 0.3 bars
Fuel pressure checks (fuel injection engines)
Fuel system pressure (relative to intake manifold pressure)
3-Series (E30)
316i with M40/B16 engine . . . . . . . . . . . . . . . . . . . . . . . . . . . . . . . 3.0 ± 0.06 bars
318i with M10/B18 engine . . . . . . . . . . . . . . . . . . . . . . . . . . . . . . . 2.5 to 3.0 bars
318i with M40/B18 engine . . . . . . . . . . . . . . . . . . . . . . . . . . . . . . . 3.0 ± 0.06 bars
320i with M20/B20 engine (L-Jetronic) . . . . . . . . . . . . . . . . . . . . . . 2.5 to 3.0 bars
320i with M20/B20 engine (Motronic) . . . . . . . . . . . . . . . . . . . . . . . 2.5 ± 0.05 bars
325i with M20/B25 engine . . . . . . . . . . . . . . . . . . . . . . . . . . . . . . . 3.0 ± 0.05 bars
5-Series (E28/”old-shape”)
All models . . . . . . . . . . . . . . . . . . . . . . . . . . . . . . . . . . . . . . . . . . . . 2.5 to 3.0 bars
5-Series (E34/”new-shape”)
518i with M40/B18 engine . . . . . . . . . . . . . . . . . . . . . . . . . . . . . . . 3.0 ± 0.06 bars
All other models . . . . . . . . . . . . . . . . . . . . . . . . . . . . . . . . . . . . . . . 2.5 to 3.0 bars
Fuel system hold pressure . . . . . . . . . . . . . . . . . . . . . . . . . . . . . . . . . . . 2.1 bars
Fuel pump maximum pressure . . . . . . . . . . . . . . . . . . . . . . . . . . . . . . . . 6.3 to 6.9 bars
Fuel pump hold pressure . . . . . . . . . . . . . . . . . . . . . . . . . . . . . . . . . . . . 5.5 bars
Transfer pump pressure . . . . . . . . . . . . . . . . . . . . . . . . . . . . . . . . . . . . . 0.28 to 0.35 bars
Injectors
Injector resistance . . . . . . . . . . . . . . . . . . . . . . . . . . . . . . . . . . . . . . . . . 14.5 to 17.5 ohms
Accelerator cable free play . . . . . . . . . . . . . . . . . . . . . . . . . . . 1.0 mm
Torque wrench settingsNm
Carburettor mountings . . . . . . . . . . . . . . . . . . . . . . . . . . . . . . . . . . . . . . 10
Fuel pump to cylinder head . . . . . . . . . . . . . . . . . . . . . . . . . . . . . . . . . . 12
Throttle body nuts/bolts . . . . . . . . . . . . . . . . . . . . . . . . . . . . . . . . . . . . . 19 to 26
4•2 Fuel and exhaust systems
1 General information
With the exception of early models (316 and
518 models) all engines are equipped with
electronic fuel injection.
Early 316 and 518 models are equipped
with Solex carburettors. The carburettor fitted
is either a Solex 2B4 (early models) or
2BE (later models). The mechanical fuel pumpis driven by an eccentric lobe on the
camshaft.
Fuel injection models are equipped with
either the L-Jetronic or the Motronic fuel
injection system. From 1988, fuel injection
models are equipped with an updated version
of the Motronic system - this system is easily
distinguished from the earlier system by the
absence of a cold start injector. The electric
fuel pump is located beneath the rear of the
vehicle, or inside the fuel tank. The fuel pump
relay on Motronic systems is activated from aearth signal from the Motronic control unit
(ECU). The fuel pump operates for a few
seconds when the ignition is first switched on,
and it continues to operate only when the
engine is actually running.Air intake system
The air intake system consists of the air
filter housing, the airflow meter and throttle
body (fuel injection models), and the intake
manifold. All components except the intake
manifold are covered in this Chapter; for
Page 91 of 228
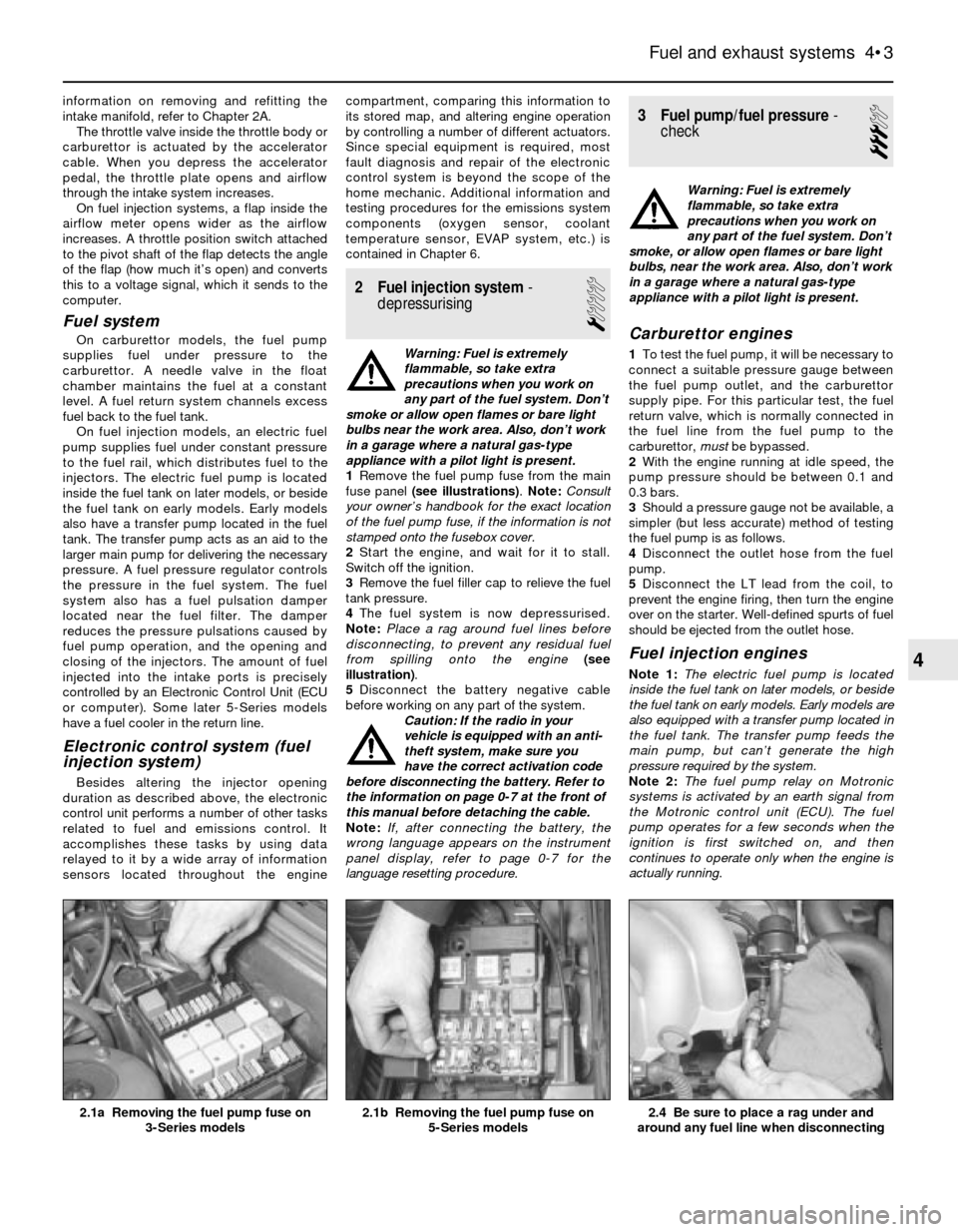
information on removing and refitting the
intake manifold, refer to Chapter 2A.
The throttle valve inside the throttle body or
carburettor is actuated by the accelerator
cable. When you depress the accelerator
pedal, the throttle plate opens and airflow
through the intake system increases.
On fuel injection systems, a flap inside the
airflow meter opens wider as the airflow
increases. A throttle position switch attached
to the pivot shaft of the flap detects the angle
of the flap (how much it’s open) and converts
this to a voltage signal, which it sends to the
computer.
Fuel system
On carburettor models, the fuel pump
supplies fuel under pressure to the
carburettor. A needle valve in the float
chamber maintains the fuel at a constant
level. A fuel return system channels excess
fuel back to the fuel tank.
On fuel injection models, an electric fuel
pump supplies fuel under constant pressure
to the fuel rail, which distributes fuel to the
injectors. The electric fuel pump is located
inside the fuel tank on later models, or beside
the fuel tank on early models. Early models
also have a transfer pump located in the fuel
tank. The transfer pump acts as an aid to the
larger main pump for delivering the necessary
pressure. A fuel pressure regulator controls
the pressure in the fuel system. The fuel
system also has a fuel pulsation damper
located near the fuel filter. The damper
reduces the pressure pulsations caused by
fuel pump operation, and the opening and
closing of the injectors. The amount of fuel
injected into the intake ports is precisely
controlled by an Electronic Control Unit (ECU
or computer). Some later 5-Series models
have a fuel cooler in the return line.
Electronic control system (fuel
injection system)
Besides altering the injector opening
duration as described above, the electronic
control unit performs a number of other tasks
related to fuel and emissions control. It
accomplishes these tasks by using data
relayed to it by a wide array of information
sensors located throughout the enginecompartment, comparing this information to
its stored map, and altering engine operation
by controlling a number of different actuators.
Since special equipment is required, most
fault diagnosis and repair of the electronic
control system is beyond the scope of the
home mechanic. Additional information and
testing procedures for the emissions system
components (oxygen sensor, coolant
temperature sensor, EVAP system, etc.) is
contained in Chapter 6.
2 Fuel injection system-
depressurising
1
Warning: Fuel is extremely
flammable, so take extra
precautions when you work on
any part of the fuel system. Don’t
smoke or allow open flames or bare light
bulbs near the work area. Also, don’t work
in a garage where a natural gas-type
appliance with a pilot light is present.
1Remove the fuel pump fuse from the main
fuse panel (see illustrations). Note:Consult
your owner’s handbook for the exact location
of the fuel pump fuse, if the information is not
stamped onto the fusebox cover.
2Start the engine, and wait for it to stall.
Switch off the ignition.
3Remove the fuel filler cap to relieve the fuel
tank pressure.
4The fuel system is now depressurised.
Note:Place a rag around fuel lines before
disconnecting, to prevent any residual fuel
from spilling onto the engine(see
illustration).
5Disconnect the battery negative cable
before working on any part of the system.
Caution: If the radio in your
vehicle is equipped with an anti-
theft system, make sure you
have the correct activation code
before disconnecting the battery. Refer to
the information on page 0-7 at the front of
this manual before detaching the cable.
Note: If, after connecting the battery, the
wrong language appears on the instrument
panel display, refer to page 0-7 for the
language resetting procedure.
3 Fuel pump/fuel pressure-
check
3
Warning: Fuel is extremely
flammable, so take extra
precautions when you work on
any part of the fuel system. Don’t
smoke, or allow open flames or bare light
bulbs, near the work area. Also, don’t work
in a garage where a natural gas-type
appliance with a pilot light is present.
Carburettor engines
1To test the fuel pump, it will be necessary to
connect a suitable pressure gauge between
the fuel pump outlet, and the carburettor
supply pipe. For this particular test, the fuel
return valve, which is normally connected in
the fuel line from the fuel pump to the
carburettor, mustbe bypassed.
2With the engine running at idle speed, the
pump pressure should be between 0.1 and
0.3 bars.
3Should a pressure gauge not be available, a
simpler (but less accurate) method of testing
the fuel pump is as follows.
4Disconnect the outlet hose from the fuel
pump.
5Disconnect the LT lead from the coil, to
prevent the engine firing, then turn the engine
over on the starter. Well-defined spurts of fuel
should be ejected from the outlet hose.
Fuel injection engines
Note 1:The electric fuel pump is located
inside the fuel tank on later models, or beside
the fuel tank on early models. Early models are
also equipped with a transfer pump located in
the fuel tank. The transfer pump feeds the
main pump, but can’t generate the high
pressure required by the system.
Note 2:The fuel pump relay on Motronic
systems is activated by an earth signal from
the Motronic control unit (ECU). The fuel
pump operates for a few seconds when the
ignition is first switched on, and then
continues to operate only when the engine is
actually running.
Fuel and exhaust systems 4•3
2.4 Be sure to place a rag under and
around any fuel line when disconnecting2.1b Removing the fuel pump fuse on
5-Series models2.1a Removing the fuel pump fuse on
3-Series models
4
Page 101 of 228
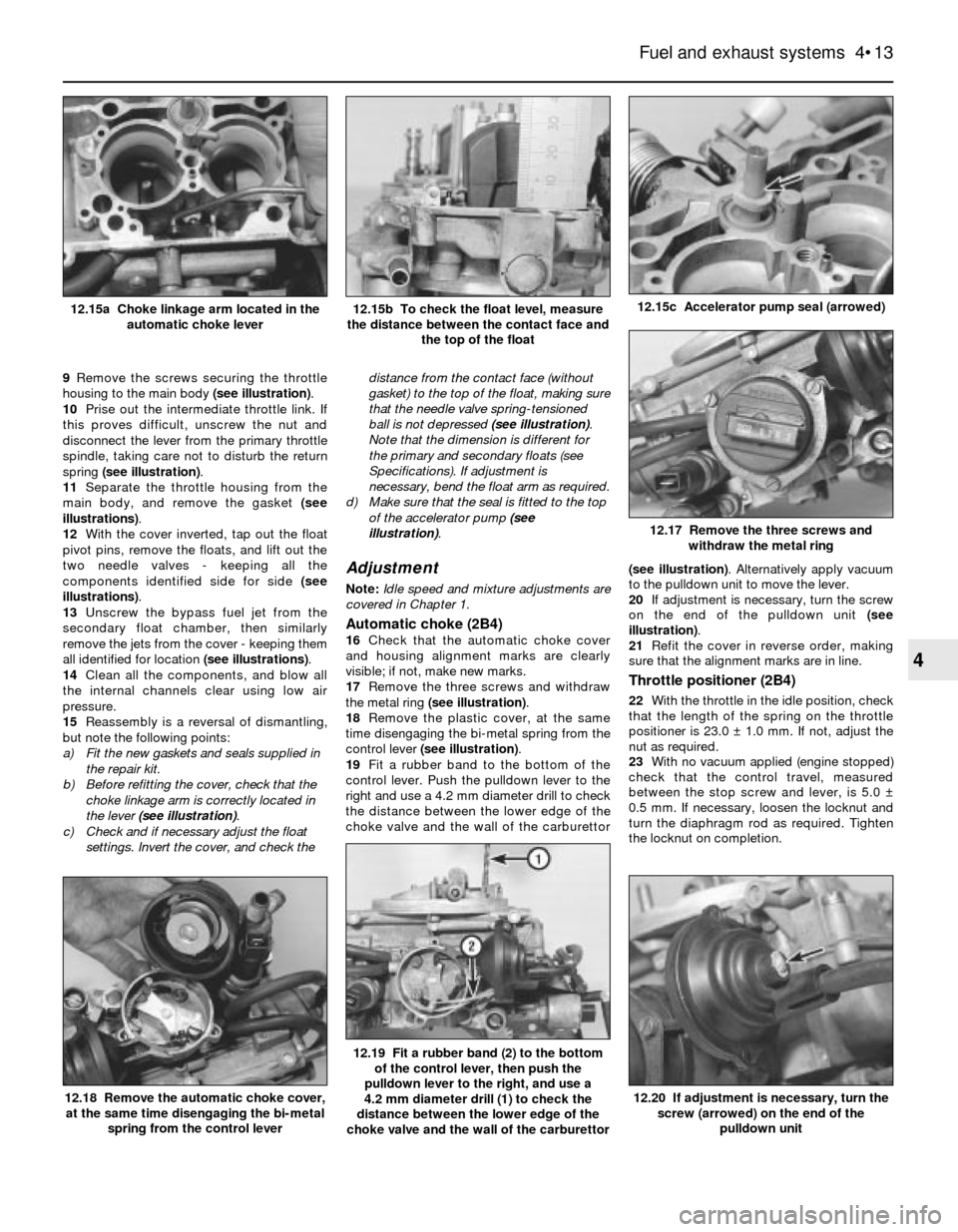
9Remove the screws securing the throttle
housing to the main body (see illustration).
10Prise out the intermediate throttle link. If
this proves difficult, unscrew the nut and
disconnect the lever from the primary throttle
spindle, taking care not to disturb the return
spring (see illustration).
11Separate the throttle housing from the
main body, and remove the gasket (see
illustrations).
12With the cover inverted, tap out the float
pivot pins, remove the floats, and lift out the
two needle valves - keeping all the
components identified side for side (see
illustrations).
13Unscrew the bypass fuel jet from the
secondary float chamber, then similarly
remove the jets from the cover - keeping them
all identified for location (see illustrations).
14Clean all the components, and blow all
the internal channels clear using low air
pressure.
15Reassembly is a reversal of dismantling,
but note the following points:
a) Fit the new gaskets and seals supplied in
the repair kit.
b) Before refitting the cover, check that the
choke linkage arm is correctly located in
the lever (see illustration).
c) Check and if necessary adjust the float
settings. Invert the cover, and check thedistance from the contact face (without
gasket) to the top of the float, making sure
that the needle valve spring-tensioned
ball is not depressed (see illustration).
Note that the dimension is different for
the primary and secondary floats (see
Specifications). If adjustment is
necessary, bend the float arm as required.
d) Make sure that the seal is fitted to the top
of the accelerator pump (see
illustration).
Adjustment
Note:Idle speed and mixture adjustments are
covered in Chapter 1.
Automatic choke (2B4)16Check that the automatic choke cover
and housing alignment marks are clearly
visible; if not, make new marks.
17Remove the three screws and withdraw
the metal ring (see illustration).
18Remove the plastic cover, at the same
time disengaging the bi-metal spring from the
control lever (see illustration).
19Fit a rubber band to the bottom of the
control lever. Push the pulldown lever to the
right and use a 4.2 mm diameter drill to check
the distance between the lower edge of the
choke valve and the wall of the carburettor(see illustration). Alternatively apply vacuum
to the pulldown unit to move the lever.
20If adjustment is necessary, turn the screw
on the end of the pulldown unit (see
illustration).
21Refit the cover in reverse order, making
sure that the alignment marks are in line.
Throttle positioner (2B4)
22With the throttle in the idle position, check
that the length of the spring on the throttle
positioner is 23.0 ± 1.0 mm. If not, adjust the
nut as required.
23With no vacuum applied (engine stopped)
check that the control travel, measured
between the stop screw and lever, is 5.0 ±
0.5 mm. If necessary, loosen the locknut and
turn the diaphragm rod as required. Tighten
the locknut on completion.
Fuel and exhaust systems 4•13
12.15b To check the float level, measure
the distance between the contact face and
the top of the float12.15a Choke linkage arm located in the
automatic choke lever
12.20 If adjustment is necessary, turn the
screw (arrowed) on the end of the
pulldown unit
12.19 Fit a rubber band (2) to the bottom
of the control lever, then push the
pulldown lever to the right, and use a
4.2 mm diameter drill (1) to check the
distance between the lower edge of the
choke valve and the wall of the carburettor
12.17 Remove the three screws and
withdraw the metal ring
12.15c Accelerator pump seal (arrowed)
12.18 Remove the automatic choke cover,
at the same time disengaging the bi-metal
spring from the control lever
4
Page 102 of 228
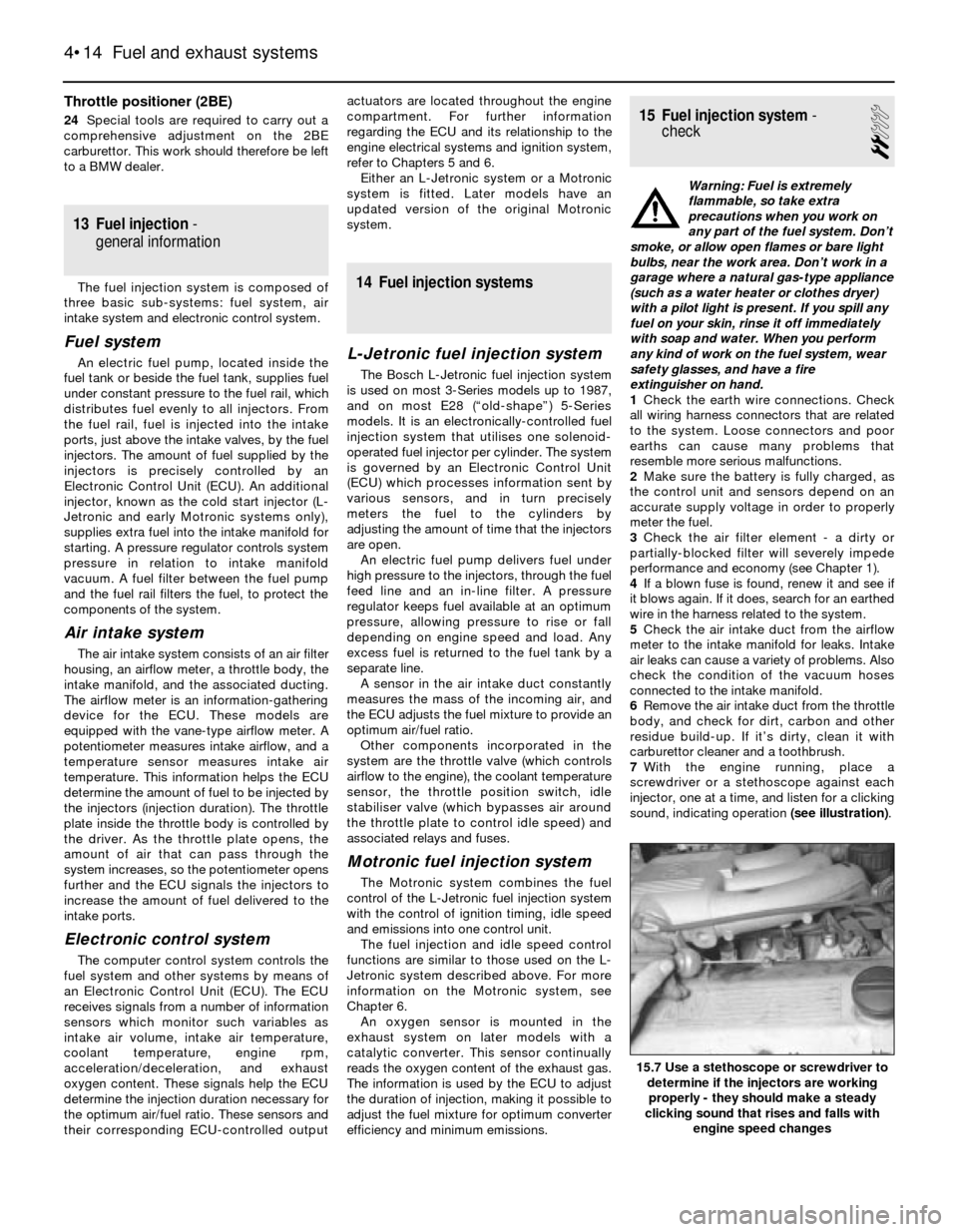
Throttle positioner (2BE)
24Special tools are required to carry out a
comprehensive adjustment on the 2BE
carburettor. This work should therefore be left
to a BMW dealer.
13 Fuel injection -
general information
The fuel injection system is composed of
three basic sub-systems: fuel system, air
intake system and electronic control system.
Fuel system
An electric fuel pump, located inside the
fuel tank or beside the fuel tank, supplies fuel
under constant pressure to the fuel rail, which
distributes fuel evenly to all injectors. From
the fuel rail, fuel is injected into the intake
ports, just above the intake valves, by the fuel
injectors. The amount of fuel supplied by the
injectors is precisely controlled by an
Electronic Control Unit (ECU). An additional
injector, known as the cold start injector (L-
Jetronic and early Motronic systems only),
supplies extra fuel into the intake manifold for
starting. A pressure regulator controls system
pressure in relation to intake manifold
vacuum. A fuel filter between the fuel pump
and the fuel rail filters the fuel, to protect the
components of the system.
Air intake system
The air intake system consists of an air filter
housing, an airflow meter, a throttle body, the
intake manifold, and the associated ducting.
The airflow meter is an information-gathering
device for the ECU. These models are
equipped with the vane-type airflow meter. A
potentiometer measures intake airflow, and a
temperature sensor measures intake air
temperature. This information helps the ECU
determine the amount of fuel to be injected by
the injectors (injection duration). The throttle
plate inside the throttle body is controlled by
the driver. As the throttle plate opens, the
amount of air that can pass through the
system increases, so the potentiometer opens
further and the ECU signals the injectors to
increase the amount of fuel delivered to the
intake ports.
Electronic control system
The computer control system controls the
fuel system and other systems by means of
an Electronic Control Unit (ECU). The ECU
receives signals from a number of information
sensors which monitor such variables as
intake air volume, intake air temperature,
coolant temperature, engine rpm,
acceleration/deceleration, and exhaust
oxygen content. These signals help the ECU
determine the injection duration necessary for
the optimum air/fuel ratio. These sensors and
their corresponding ECU-controlled outputactuators are located throughout the engine
compartment. For further information
regarding the ECU and its relationship to the
engine electrical systems and ignition system,
refer to Chapters 5 and 6.
Either an L-Jetronic system or a Motronic
system is fitted. Later models have an
updated version of the original Motronic
system.
14 Fuel injection systems
L-Jetronic fuel injection system
The Bosch L-Jetronic fuel injection system
is used on most 3-Series models up to 1987,
and on most E28 (“old-shape”) 5-Series
models. It is an electronically-controlled fuel
injection system that utilises one solenoid-
operated fuel injector per cylinder. The system
is governed by an Electronic Control Unit
(ECU) which processes information sent by
various sensors, and in turn precisely
meters the fuel to the cylinders by
adjusting the amount of time that the injectors
are open.
An electric fuel pump delivers fuel under
high pressure to the injectors, through the fuel
feed line and an in-line filter. A pressure
regulator keeps fuel available at an optimum
pressure, allowing pressure to rise or fall
depending on engine speed and load. Any
excess fuel is returned to the fuel tank by a
separate line.
A sensor in the air intake duct constantly
measures the mass of the incoming air, and
the ECU adjusts the fuel mixture to provide an
optimum air/fuel ratio.
Other components incorporated in the
system are the throttle valve (which controls
airflow to the engine), the coolant temperature
sensor, the throttle position switch, idle
stabiliser valve (which bypasses air around
the throttle plate to control idle speed) and
associated relays and fuses.
Motronic fuel injection system
The Motronic system combines the fuel
control of the L-Jetronic fuel injection system
with the control of ignition timing, idle speed
and emissions into one control unit.
The fuel injection and idle speed control
functions are similar to those used on the L-
Jetronic system described above. For more
information on the Motronic system, see
Chapter 6.
An oxygen sensor is mounted in the
exhaust system on later models with a
catalytic converter. This sensor continually
reads the oxygen content of the exhaust gas.
The information is used by the ECU to adjust
the duration of injection, making it possible to
adjust the fuel mixture for optimum converter
efficiency and minimum emissions.
15 Fuel injection system-
check
2
Warning: Fuel is extremely
flammable, so take extra
precautions when you work on
any part of the fuel system. Don’t
smoke, or allow open flames or bare light
bulbs, near the work area. Don’t work in a
garage where a natural gas-type appliance
(such as a water heater or clothes dryer)
with a pilot light is present. If you spill any
fuel on your skin, rinse it off immediately
with soap and water. When you perform
any kind of work on the fuel system, wear
safety glasses, and have a fire
extinguisher on hand.
1Check the earth wire connections. Check
all wiring harness connectors that are related
to the system. Loose connectors and poor
earths can cause many problems that
resemble more serious malfunctions.
2Make sure the battery is fully charged, as
the control unit and sensors depend on an
accurate supply voltage in order to properly
meter the fuel.
3Check the air filter element - a dirty or
partially-blocked filter will severely impede
performance and economy (see Chapter 1).
4If a blown fuse is found, renew it and see if
it blows again. If it does, search for an earthed
wire in the harness related to the system.
5Check the air intake duct from the airflow
meter to the intake manifold for leaks. Intake
air leaks can cause a variety of problems. Also
check the condition of the vacuum hoses
connected to the intake manifold.
6Remove the air intake duct from the throttle
body, and check for dirt, carbon and other
residue build-up. If it’s dirty, clean it with
carburettor cleaner and a toothbrush.
7With the engine running, place a
screwdriver or a stethoscope against each
injector, one at a time, and listen for a clicking
sound, indicating operation (see illustration).
4•14 Fuel and exhaust systems
15.7 Use a stethoscope or screwdriver to
determine if the injectors are working
properly - they should make a steady
clicking sound that rises and falls with
engine speed changes