light BMW 540i 1998 E39 Owner's Manual
[x] Cancel search | Manufacturer: BMW, Model Year: 1998, Model line: 540i, Model: BMW 540i 1998 E39Pages: 1002
Page 75 of 1002
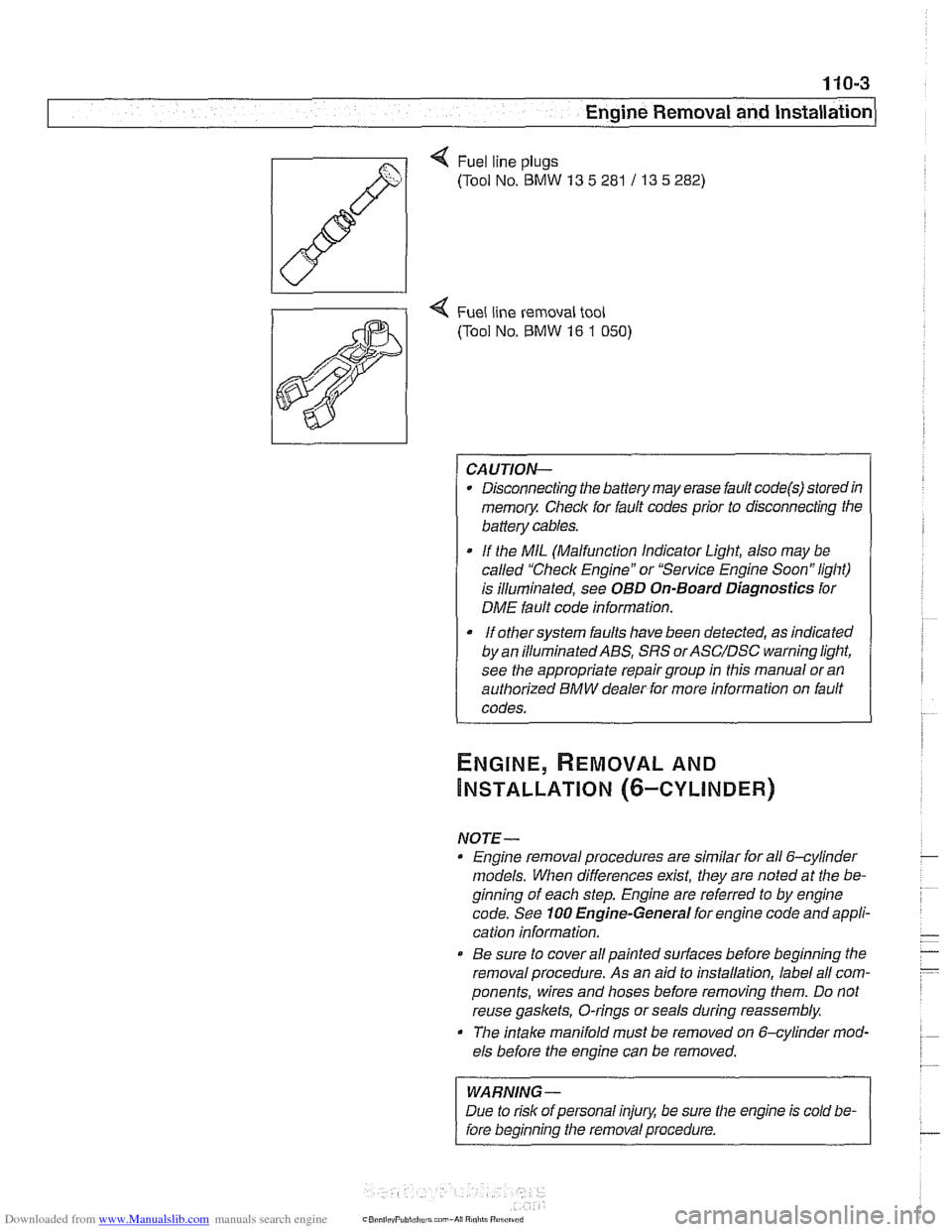
Downloaded from www.Manualslib.com manuals search engine
110-3
Engine Removal and lnstallationl
Q Fuel line plugs
(Tool No.
BMW 13 5 281 / 13 5 282)
4 Fuel line removal tool
(Tool No.
BMW 16 1 050)
CAUTION-
Disconnecting the battery may erase fault code@) storedin
memoiy Check for fault codes prior to disconnecting the
battery cables.
If the MIL (Malfunction Indicator Light, also may be
called "Check Engine" or "Service Engine Soon" light)
is illuminated, see
OBD On-Board Diagnostics for
DME fault code information.
It orhersysrem faults have been detected, as indicated I
by an ~llum~nated ABS, SRS orASC/DSC ~arning light,
see the appropriate repair group in this manual or an
authorized BMW dealer for more information on fault
codes.
NOTE- Engine removal procedures are similar for all 6-cylinder
models. When differences
exist, they are noted at the be-
ginning of each step. Engine are referred to by engine
code. See
100 Engine-General for engine code and appli-
cation information.
@ Be sure to cover all painted surfaces before beginning the
removal procedure. As an aid to installation, label all com-
ponents, wires and hoses before removing them. Do not
reuse
gaskets, O-rings or seals during reassembly.
The
intake manifold must be removed on &cylinder mod-
els before the engine can be removed.
WARNING-
Due to risk of personal injury, be sure the engine is cold be-
fore beginning the removal procedure.
Page 99 of 1002
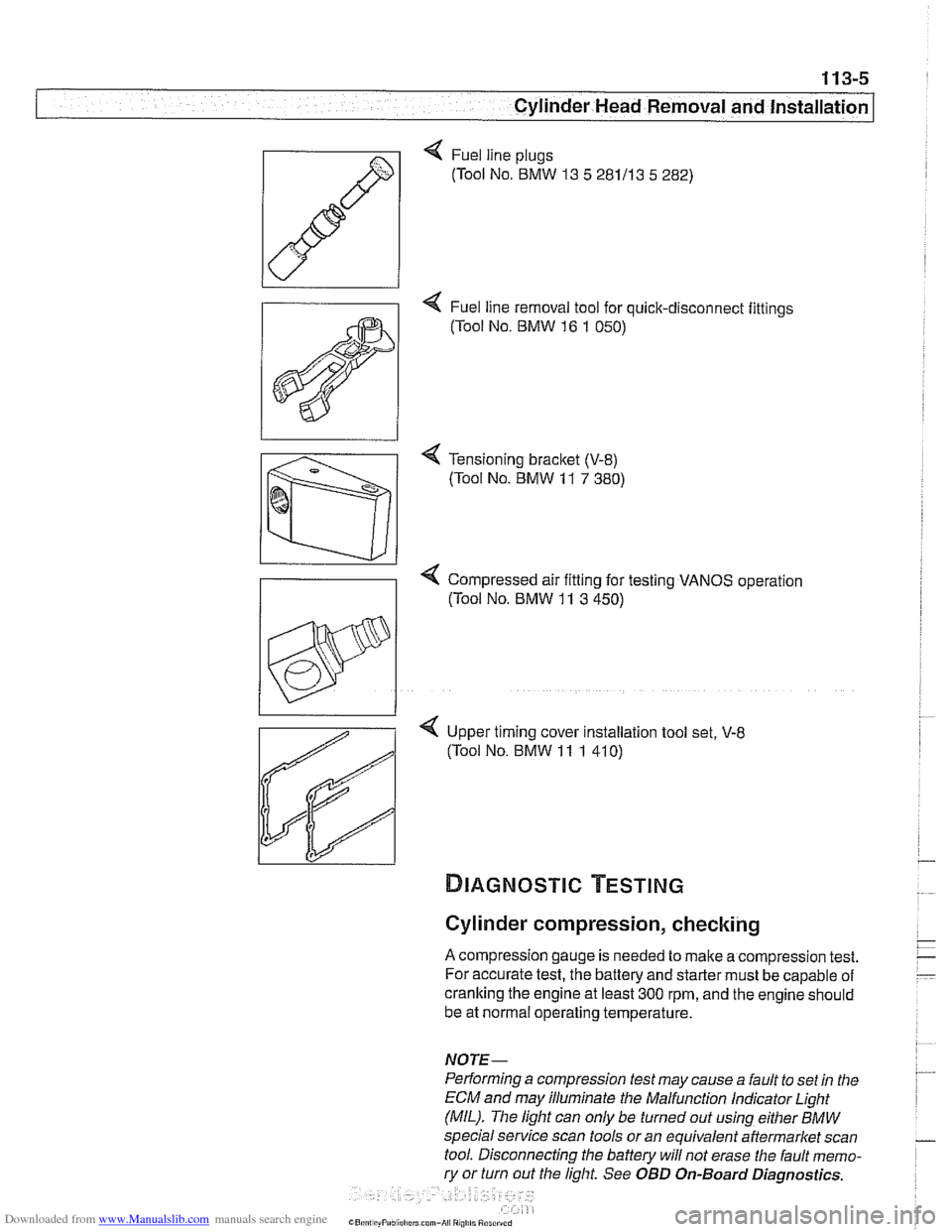
Downloaded from www.Manualslib.com manuals search engine
113-5
Cylinder Head Removal and Installation I
< Fuel line plugs
(Tool No.
BMW 13 5 281113 5 282)
4 Fuel line removal tool for quick-disconnect fittings
(Tool No.
BMW 16 1 050)
< Tensioning bracket (V-8)
(Tool No. BMW 11 7 380)
Compressed air fitting for testing VANOS operation
((Tool No.
BMW 11 3 450)
< Upper timing cover installation tool set, V-8
(Tool No. BMW 11 1 41 0)
Cylinder compression, checking
A compression gauge is needed to make a compression test.
For accurate test, the battery and starter must be capable of
cranking the engine at least
300 rpm, and the engine should
be at normal operating temperature.
NOTE-
Performing a compression test may cause a fault to set in the
ECM and may illuminate the Malfunction
Indicator Light
(MIL). The light can only be turned out using either
BMW
special service scan tools or an equivalent aftermarket scan
tool. Disconnecting the battery will not erase the fault memo-
ry or turn out the light. See OBD On-Board Diagnostics.
Page 112 of 1002
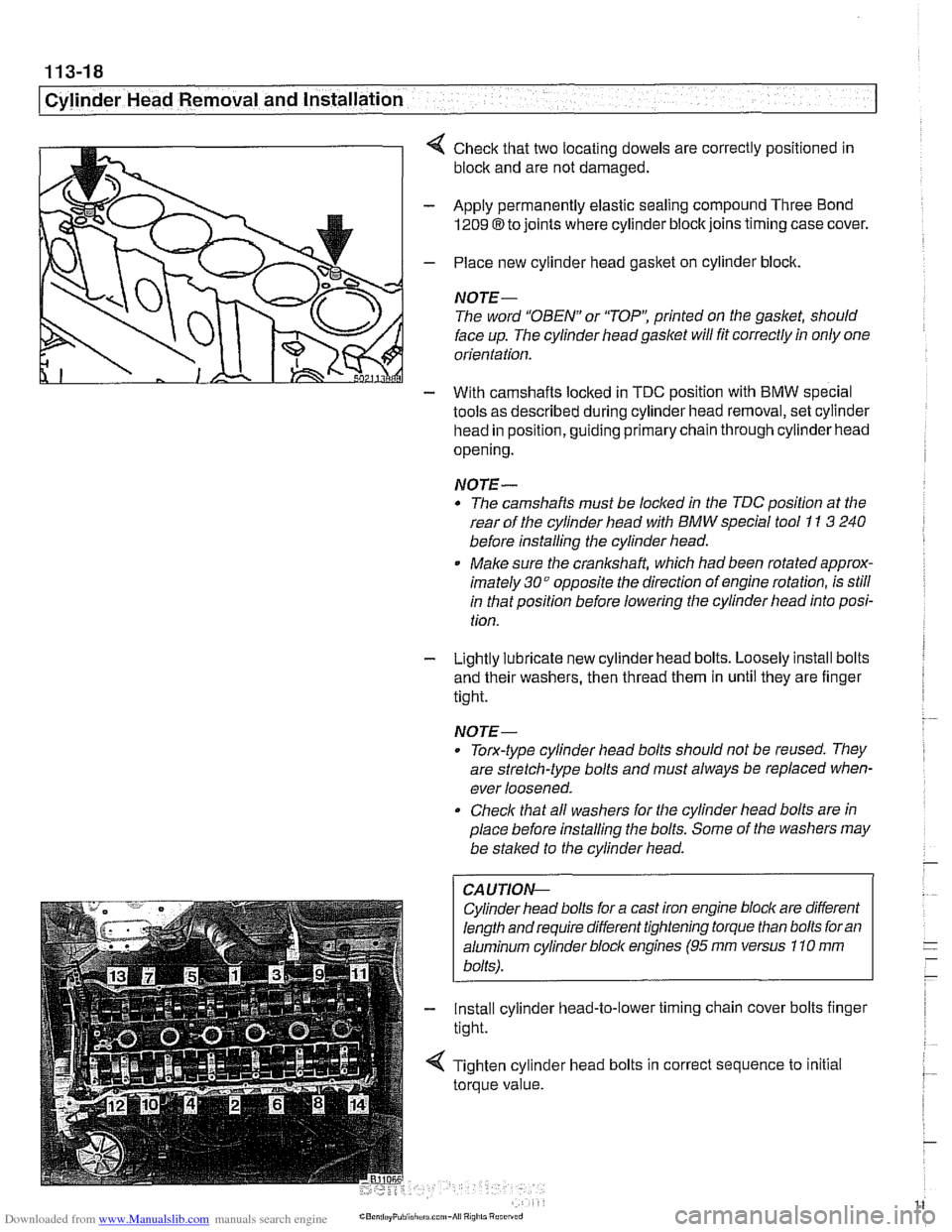
Downloaded from www.Manualslib.com manuals search engine
I Cylinder Head Removal and Installation
4 Check that two locating dowels are correctly positioned in
block and are not damaged.
- Apply permanently elastic sealing compound Three Bond
1209 8 to joints where cylinder block joins timing case cover.
- Place new cylinder head gasket on cylinder block.
NOTE-
The word "OBEN" or 'TOP': printed on the gasket, should
face up. The cylinder head
gasket will fit correctly in only one
orientation.
- With camshafts locked in TDC oosition with BMW soecial
tools as described during cylinder head removal,
seicylinder
head in position, guiding primary chain through cylinder head
opening.
NOTE-
* The camshafts must be locl(ed in the TDC position at the
rear of the cylinder head with
BMW special tool I1 3 240
before installing the cylinder head.
Make sure the
cranksha% which had been rotated approx-
imately
30" opposite the direction of engine rotation, is still
in that position before lowering the cylinder head into posi-
tion.
- Lightly lubricate new cylinder head bolts. Loosely install bolts
and their washers, then thread them in until they are finger
tight.
NOTE-
. Torx-type cylinder head bolts should not be reused. They
are stretch-type bolts and must always be replaced when-
ever loosened.
Check that all washers for the cylinder head bolts are in
place before installing the bolts. Some of the washers may
be
stalced to the cylinder head.
CAUTIOI\C
Cylinder head bolts for a cast iron engine block are different
length and require different tightening torque than bolts for an
aluminum cylinder bloclc engines
(95 rnm versus 110 rnm
bolts).
- Install cylinder head-to-lower timing chain cover bolts finger
tight.
< Tighten cylinder head bolts in correct sequence to initial
torque value.
Page 134 of 1002
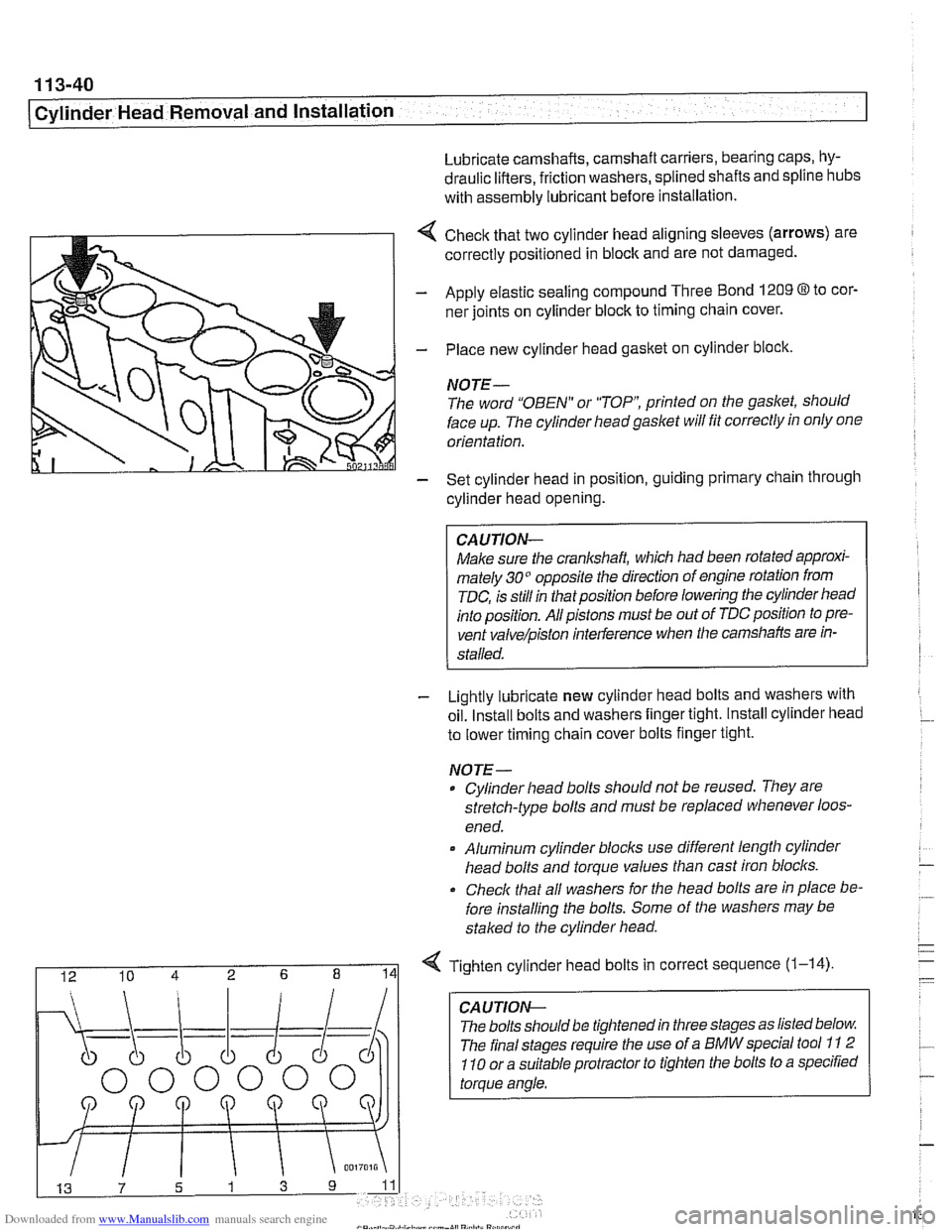
Downloaded from www.Manualslib.com manuals search engine
11 3-40
I Cylinder Head Removal and Installation
Lubricate camshafts, camshaft carriers, bearing caps, hy-
draulic lifters, friction washers, splined shafts and spline hubs
with assembly lubricant before installation.
4 Check that two cylinder head aligning sleeves (arrows) are
correctly positioned in block and are not damaged.
- Apply elastic sealing compound Three Bond 1209 8 to cor-
ner joints on cylinder block to timing chain cover.
- Place new cylinder head gasket on cylinder block.
NOTE-
The word "OBEN" or "TOP printed on the gasket, should
face up. The cylinder headgaslet will fit correctly in only one
orientation.
- Set cylinder head in position, guiding primary chain through
cylinder head opening.
CAUJION-
Make sure the crankshaft, which had been rotated approxi-
mately 30" opposite the direction of engine rotation from
TDC, is still in thatposition before lowering the cylinder head
into position. All pistons must be out of TDC position to pre-
vent
valve/piston interference when the camshafts are in-
stalled.
- Lightly lubricate new cylinder head bolts and washers with
oil. Install bolts and washers finger tight. Install cylinder head
to lower timing chain cover bolts finger tight.
NOJE-
Cylinder head bolts should not be reused. They are
stretch-type bolts and must be replaced whenever loos-
ened.
* Aluminum cylinder blocls use different length cylinder
head bolts and torque values than cast iron blocks.
Check that all washers for
Nle head bolts are in place be-
fore installing the bolts. Some of the washers may be
staked to the cylinder head.
I 12 10 4 2 6 8 141 Tighten cylinder head bolts in correct sequence (1-14)
CA U TIOW-
The bolts should be tightened in three stages as listed below
The final stages require the use of a BMW special tool
11 2
110 or a suitable protractor to tighten the bolts to a specified
torque angle.
Page 138 of 1002

Downloaded from www.Manualslib.com manuals search engine
11 3-44
I Cylinder Head Removal and Installation
4 Secure camshafts in TDC position using BMW special tool
set
11 3 240.
4 In necessary, turn camshaft slightly so that special tools are
squarely seated on cylinder head.
4 Lift timing chain and hold under tension.
Page 151 of 1002
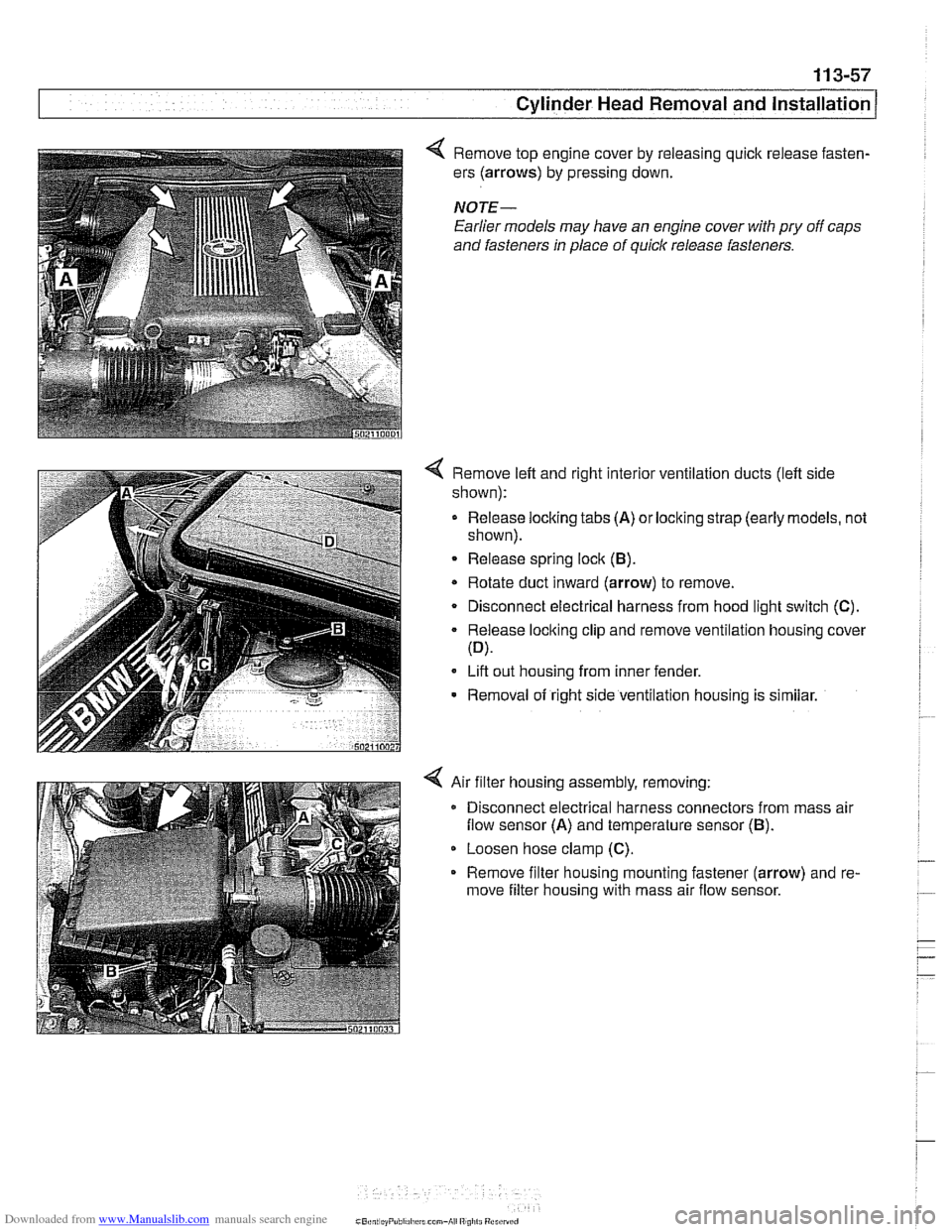
Downloaded from www.Manualslib.com manuals search engine
Cylinder Head Removal and Installation /
4 Remove top engine cover by releasing quick release fasten-
ers (arrows) by pressing down.
NOTE-
Earlier models may have an engine cover with pry off caps
and fasteners
In place of quick release fasteners.
4 Remove left and right interior ventilation ducts (left side
shown):
- Release locking tabs (A) or locking strap (early models, not
shown).
Release spring lock (B).
* Rotate duct inward (arrow) to remove.
Disconnect electrical harness from hood light switch (C).
Release locking clip and remove ventilation housing cover
(D).
Lift out housing from inner fender.
- Removal of right side ventilation housing is similar.
4 Air filter housing assembly, removing:
Disconnect electrical harness connectors from mass air
flow sensor (A) and temperature sensor (B).
Loosen hose clamp (C).
Remove filter housing mounting fastener (arrow) and re-
move filter housing with mass air flow sensor.
Page 186 of 1002
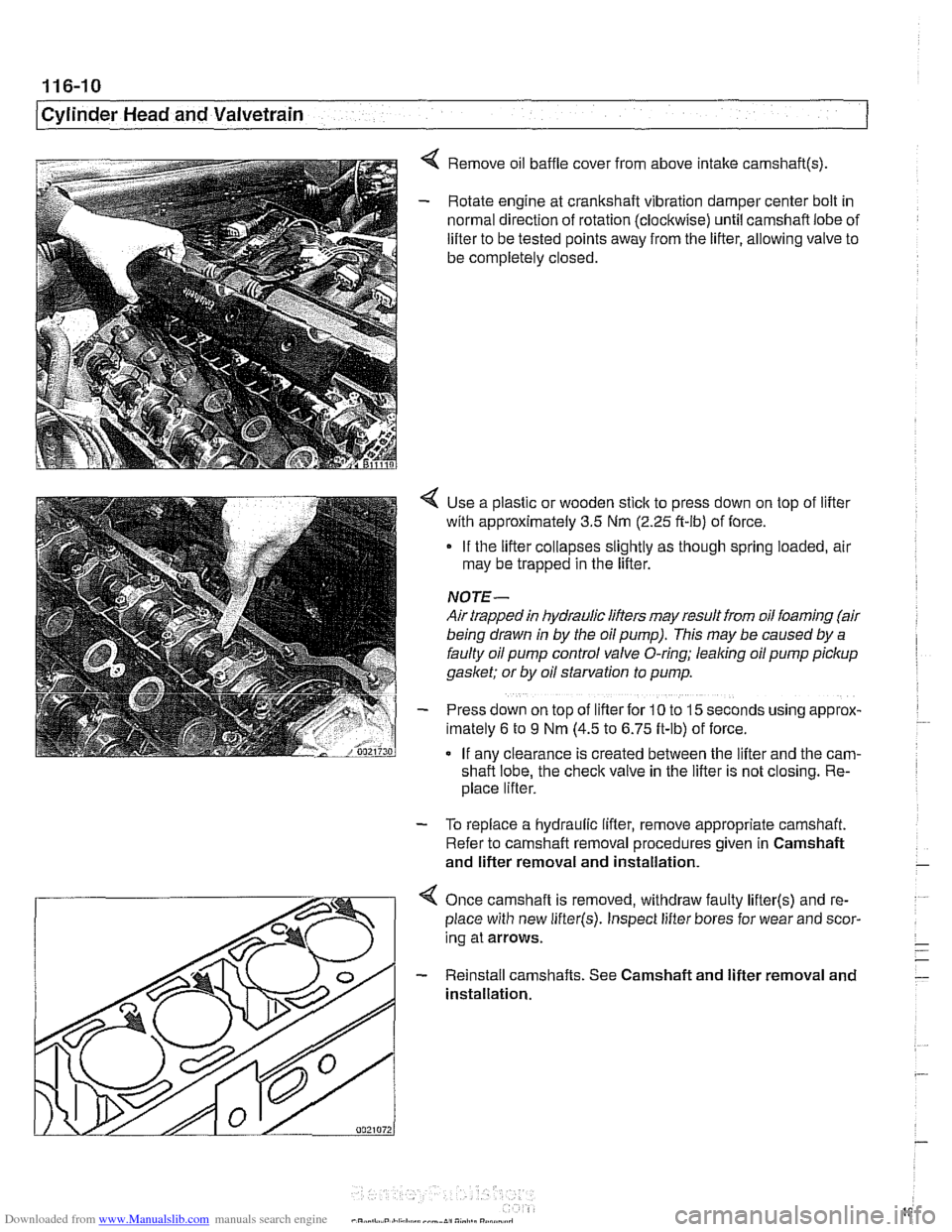
Downloaded from www.Manualslib.com manuals search engine
Cylinder Head and Valvetrain
< Remove oil baffle cover from above intake camshaft(s)
- Rotate engine at crankshaft vibration damper center bolt in
normal direction of rotation (clockwise) until camshaft lobe of
lifter to be tested points away from the lifter, allowing valve to
be completely closed.
Use a plastic or wooden stick to press down on top of lifter
with approximately 3.5 Nm
(2.25 ft-ib) of force.
If the lifter collapses slightly as though spring loaded, air
may be trapped in the lifter.
NOTE-
Air trapped in hydraulic lifters may result from oil foaming (air
being drawn
in by the oil pump). This may be caused by a
faulty oil pump control valve O-ring; leaking oil pump pickup
gaslcet; or by oil starvation to pump.
Press down on top of lifter for
10 to 15 seconds uslng approx-
lmately 6 to 9 Nm (4.5 to 6.75 ft-lb) of force.
If anv clearance is created between the lifter and the
cam-
shafi lobe, the check valve in the lifter is not closing. Re-
place lifter.
- To replace a hydraulic lifter, remove appropriate camshaft.
Refer to camshaft removal procedures given in Camshaft
and lifter removal and installation.
Once camshaft is removed, withdraw faulty
lifter(s) and re-
place with new
lifter(s). Inspect lifter bores for wear and scor-
ing at arrows.
- Reinstall camshafts. See Camshaft and lifter removal and
installation.
Page 294 of 1002
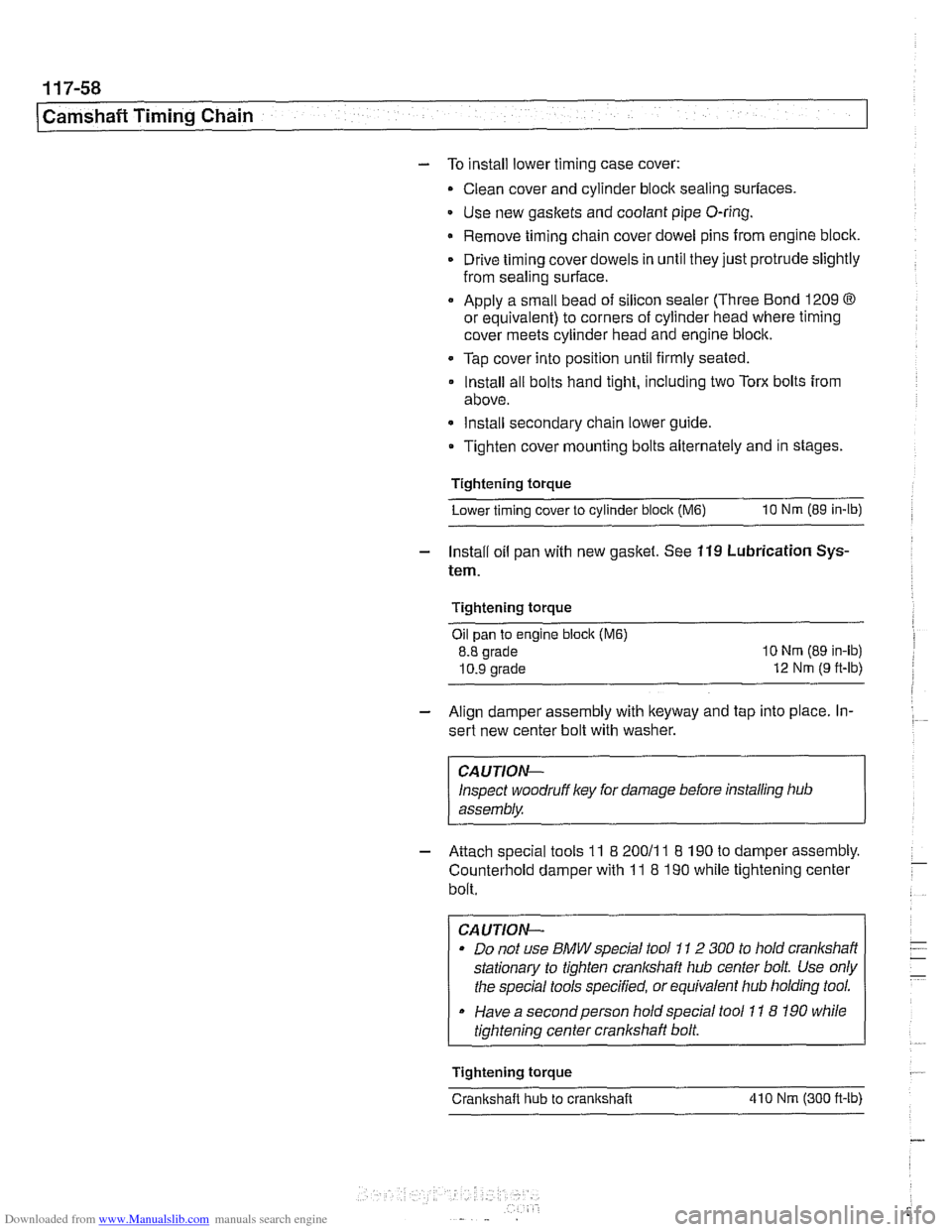
Downloaded from www.Manualslib.com manuals search engine
(camshaft Timing Chain
- To install lower timing case cover:
- Clean cover and cylinder block sealing surfaces
Use new
gaskets and coolant pipe O-ring.
Remove timing chain cover dowel pins from engine block.
Drive timing cover dowels in until they just protrude slightly
from sealing surface.
Apply a small bead of silicon sealer (Three Bond 1209
63
or equivalent) to corners of cylinder head where timing
cover meets cylinder head and engine block.
Tap cover into position until firmly seated.
lnstall all bolts hand tight, including two Torx bolts from
above.
Install secondary chain lower guide.
Tighten cover mounting bolts alternately and in stages.
Tightening torque
Lower timing cover to cylinder
bloclc (M6) 10 Nrn (89 in-lb)
- Install oil pan with new gasket. See 119 Lubrication Sys-
tem.
Tightening torque
Oil pan
to engine bloclc (M6)
8.8 grade
10.9 grade 10 Nrn (89 in-lb)
12 Nm
(9 ft-lb)
- Align damper assembly with lteyway and tap into place. In-
sert new center bolt with washer.
CAUTION-
Inspect woodruff key for damage before installing hub
assembly.
- Attach special tools 11 8 20011 1 8 190 to damper assembly.
Counterhold damper with
11 8 190 while tightening center
bolt.
CAUTION-
Do not use BMW special tool 1 I 2 300 to hold crankshaft
stationary to tighten cranl(shaft hub center bolt. Use only
the special tools specified, or equivalent hub holding tool.
Have a second person hold special tool
11 8 190 while
tightening center crankshaft bolt.
Tightening torque Crankshaft hub to crankshaft 410 Nrn
(300
ft-lb)
Page 323 of 1002
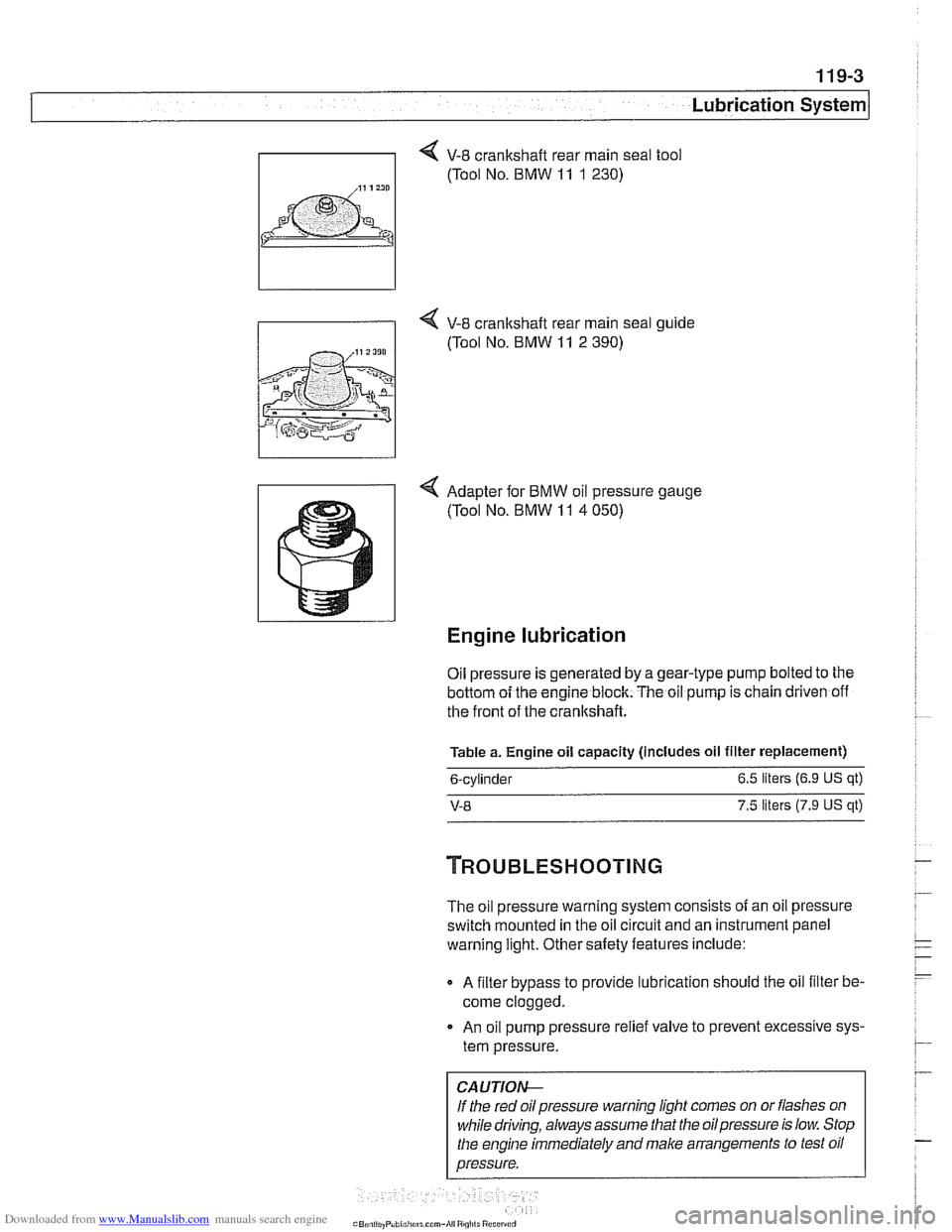
Downloaded from www.Manualslib.com manuals search engine
1 19-3
Lubrication System
V-8 crankshaft rear main seal tool
(Tool No. BMW
11 1 230)
I i 4 V-8 crankshaft rear main seal ouide
4 Adapter for BMW oil pressure gauge
(Tool No. BMW
11 4 050)
Engine lubrication
Oil pressure is generated by a gear-type pump bolted to the
bottom oi the engine block. The oil pump is chain driven off
the front of the crankshaft.
Table a. Engine oil capacity (includes oil filter replacement)
6-cylinder 6.5
liters (6.9
US qt)
V-8 7.5 liters (7.9 US qt)
The oil pressure warning system consists of an oil pressure
switch mounted in the oil circuit and an instrument
panel
warning light. Other saiety features include:
Q A filter bypass to provide lubrication should the oil filter be-
come clogged.
An oil pump pressure relief valve to prevent excessive sys-
tem pressure.
CAUTIOI\C
If the red oil pressure warning light comes on or flashes on
while driving, always assume that the oilpressure is low. Stop
the engine immediately and make arrangements to test oil
pressure.
Page 325 of 1002
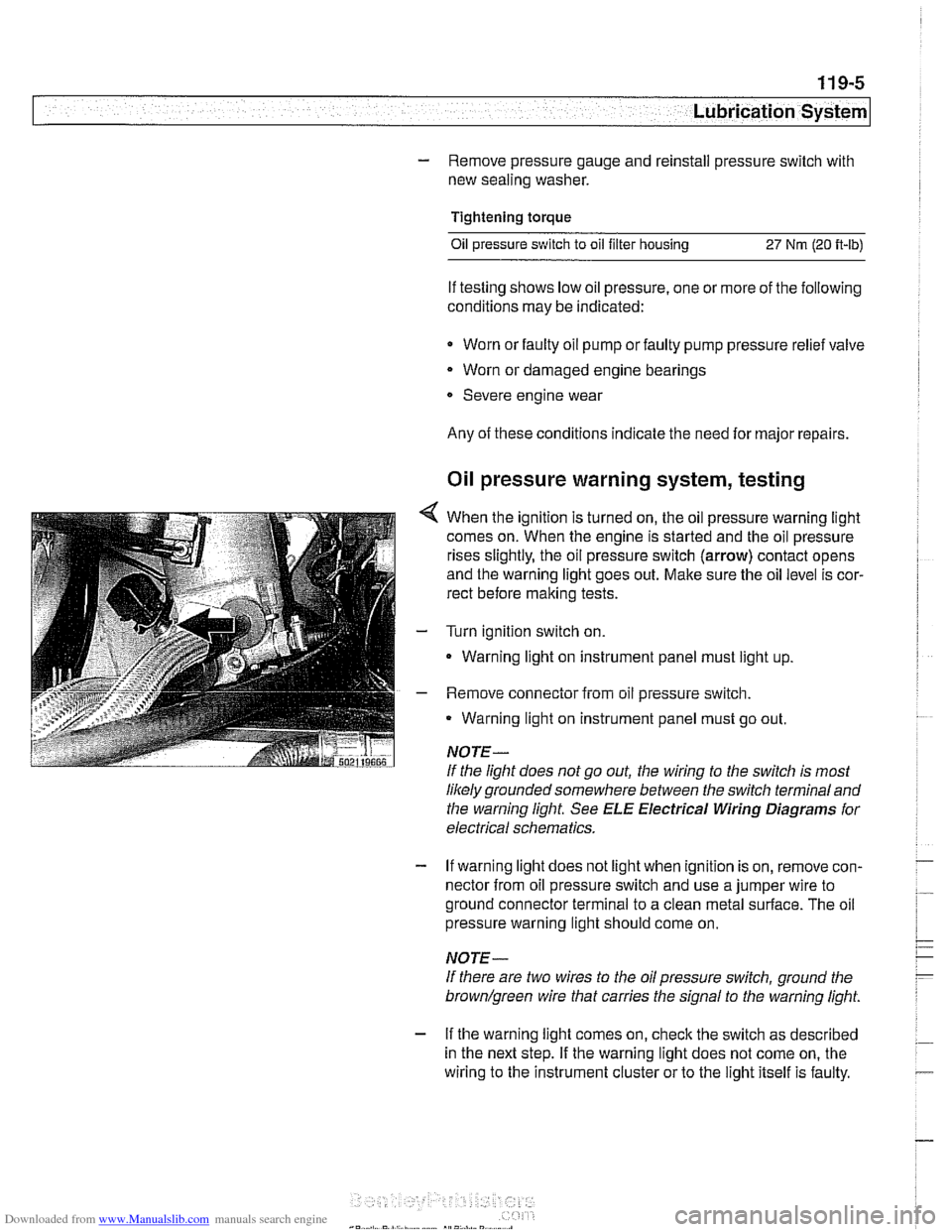
Downloaded from www.Manualslib.com manuals search engine
. .- -
L
- --
- - -. - -- Lubrication ~~stern
- Remove pressure gauge and reinstall pressure switch with
new sealing washer.
Tightening torque
Oil pressure switch to oil filter housing 27 Nm (20 ft-lb)
If testing shows low oil pressure, one or more of the following
conditions may be indicated:
Worn or faulty oil pump or faulty pump pressure relief valve
Worn or damaged engine bearings
Severe engine wear
Any of these conditions indicate the need for major repairs.
Oil pressure warning system, testing
4 When the ignition is turned on, the oil pressure warning light
comes on. When the engine is started and the oil pressure
rises slightly, the oil pressure switch (arrow) contact opens
and the warning light goes out. Make sure the oil level is cor-
rect before making tests.
- Turn ignition switch on.
- Warning light on instrument panel must light up
- Remove connector from oil pressure switch.
Warning light on instrument panel must go out.
NOTE-
If the light does not go out, the wiring to the switch is most
likely grounded somewhere between the switch terminaland
the warning light See
ELE Electrical Wiring Diagrams for
electrical schematics.
- If warning light does not light when ignition is on, remove con-
nector from oil pressure switch and use a jumper wire to
ground connector terminal to a clean metal surface. The oil
pressure warning light should come on.
NOTE-
If there are two wires to the oil pressure switch, ground the
brown/green wire that carries the signal to the warning light.
- If the warning light comes on, check the switch as described
in the next step. If the warning light does not come on, the
wiring to the instrument cluster or to the light itself is faulty.