sensor BMW 740IL 1996 E38 Level Control System Manual
[x] Cancel search | Manufacturer: BMW, Model Year: 1996, Model line: 740IL, Model: BMW 740IL 1996 E38Pages: 57, PDF Size: 1.89 MB
Page 3 of 57
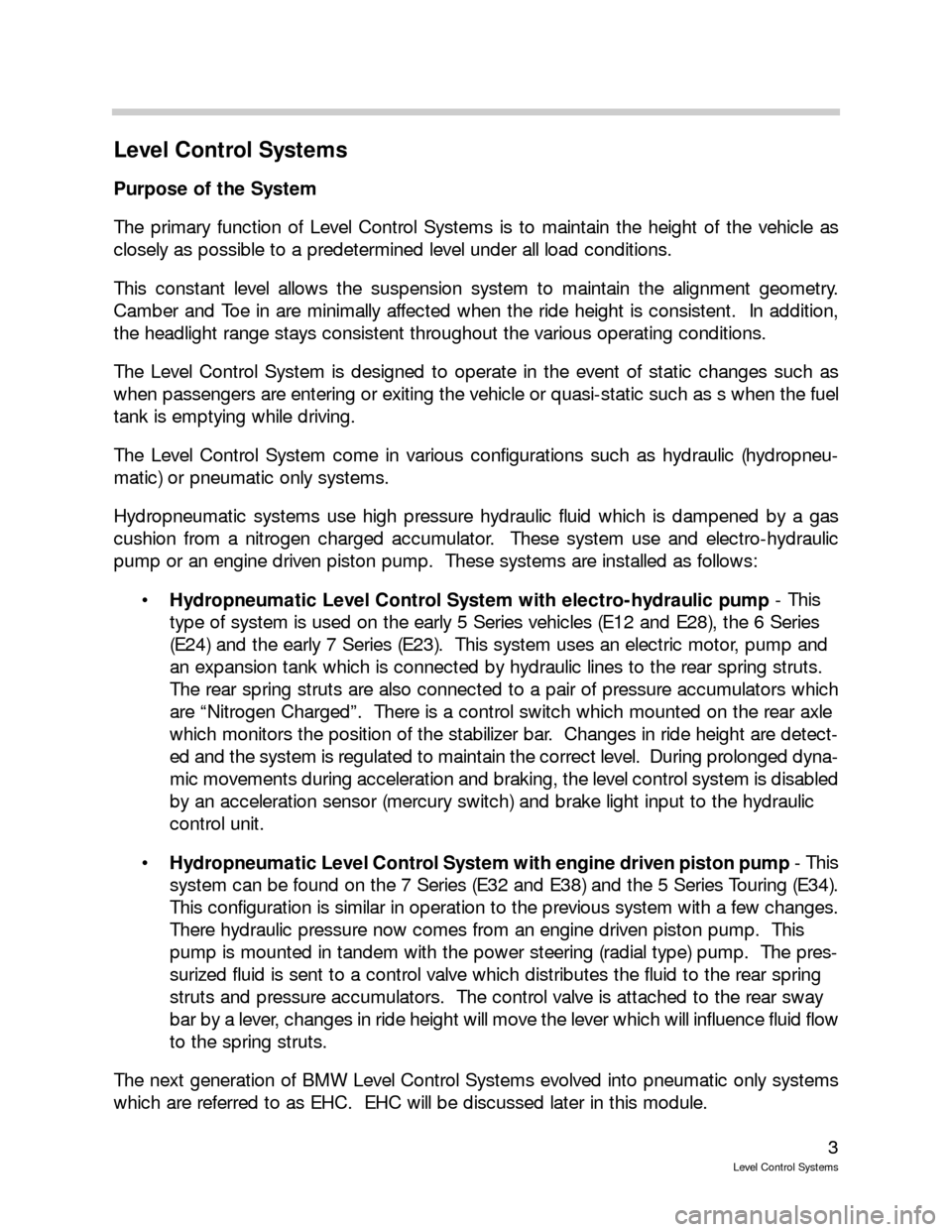
3
Level Control Systems
Level Control Systems
Purpose of the System
The primary function of Level Control Systems is to maintain the height of the vehicle as
closely as possible to a predetermined level under all load conditions.
This constant level allows the suspension system to maintain the alignment geometry.
Camber and Toe in are minimally affected when the ride height is consistent. In addition,
the headlight range stays consistent throughout the various operating conditions.
The Level Control System is designed to operate in the event of static changes such as
when passengers are entering or exiting the vehicle or quasi-static such as s when the fuel
tank is emptying while driving.
The Level Control System come in various configurations such as hydraulic (hydropneu-
matic) or pneumatic only systems.
Hydropneumatic systems use high pressure hydraulic fluid which is dampened by a gas
cushion from a nitrogen charged accumulator. These system use and electro-hydraulic
pump or an engine driven piston pump. These systems are installed as follows:
Hydropneumatic Level Control System with electro-hydraulic pump- This
type of system is used on the early 5 Series vehicles (E12 and E28), the 6 Series
(E24) and the early 7 Series (E23). This system uses an electric motor, pump and
an expansion tank which is connected by hydraulic lines to the rear spring struts.
The rear spring struts are also connected to a pair of pressure accumulators which
are “Nitrogen Charged”. There is a control switch which mounted on the rear axle
which monitors the position of the stabilizer bar. Changes in ride height are detect-
ed and the system is regulated to maintain the correct level. During prolonged dyna-
mic movements during acceleration and braking, the level control system is disabled
by an acceleration sensor (mercury switch) and brake light input to the hydraulic
control unit.
Hydropneumatic Level Control System with engine driven piston pump- This
system can be found on the 7 Series (E32 and E38) and the 5 Series Touring (E34).
This configuration is similar in operation to the previous system with a few changes.
There hydraulic pressure now comes from an engine driven piston pump. This
pump is mounted in tandem with the power steering (radial type) pump. The pres-
surized fluid is sent to a control valve which distributes the fluid to the rear spring
struts and pressure accumulators. The control valve is attached to the rear sway
bar by a lever, changes in ride height will move the lever which will influence fluid flow
to the spring struts.
The next generation of BMW Level Control Systems evolved into pneumatic only systems
which are referred to as EHC. EHC will be discussed later in this module.
Page 14 of 57
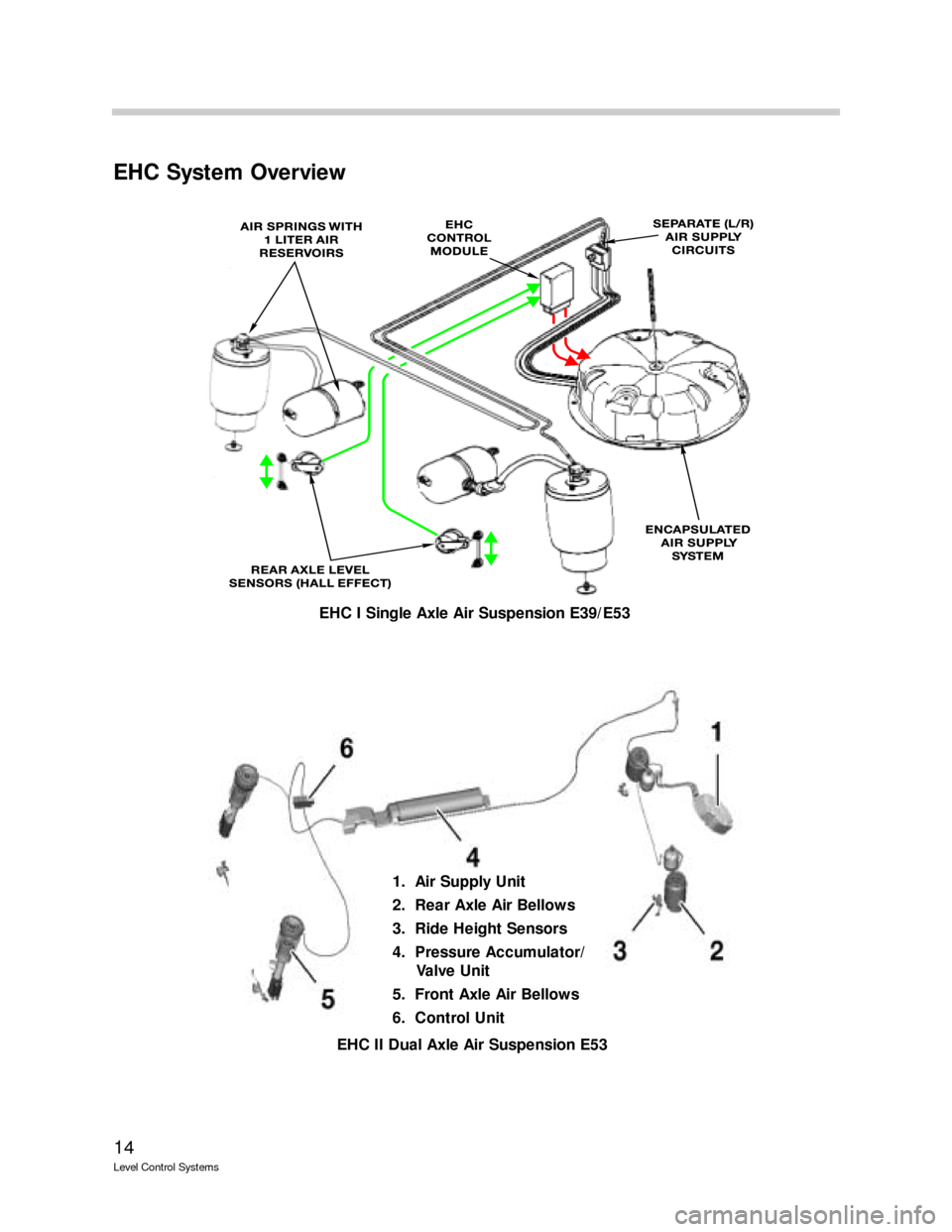
14
Level Control Systems
EHC System Overview
EHC I Single Axle Air Suspension E39/E53
EHC II Dual Axle Air Suspension E53
1. Air Supply Unit
2. Rear Axle Air Bellows
3. Ride Height Sensors
4. Pressure Accumulator/
Valve Unit
5. Front Axle Air Bellows
6. Control Unit
Page 15 of 57
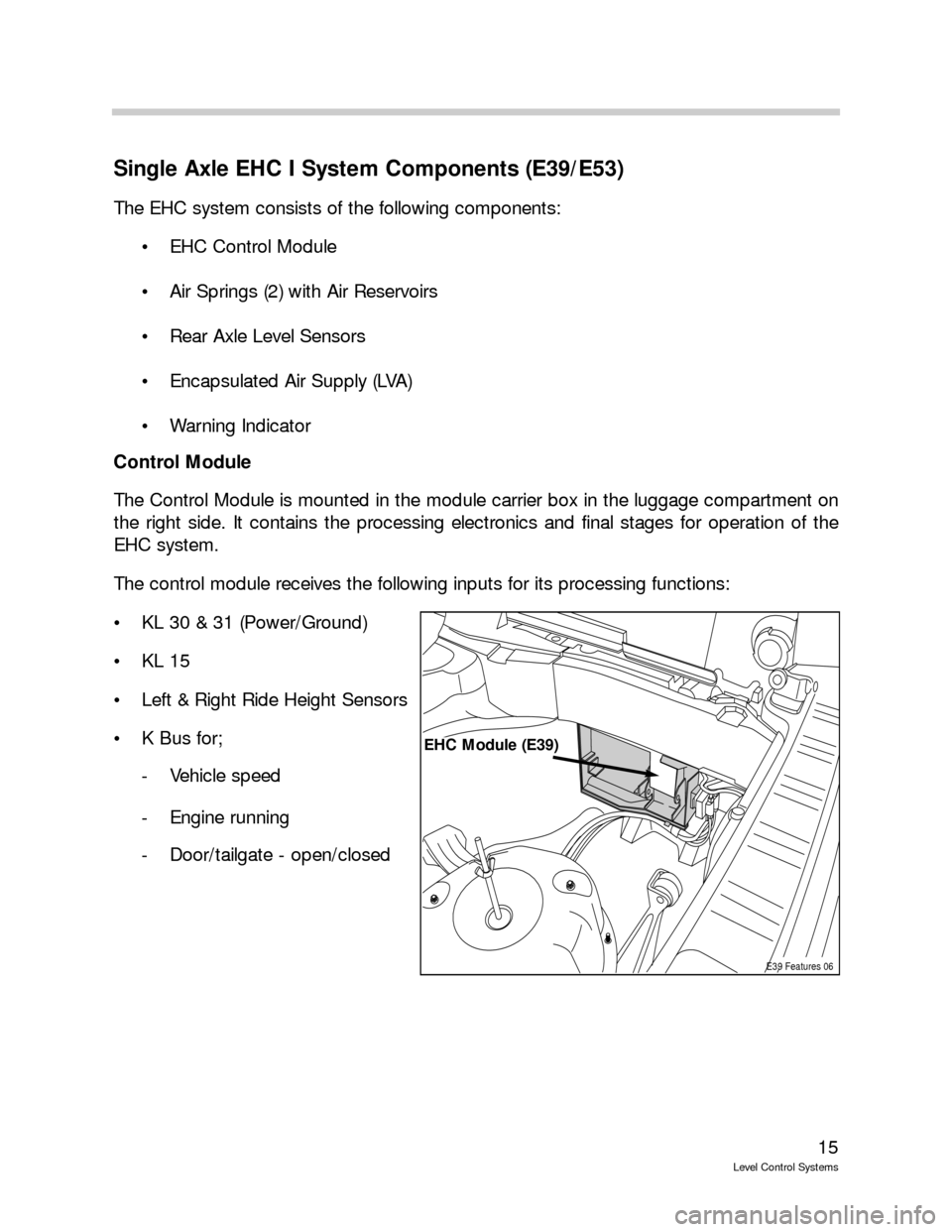
15
Level Control Systems
Single Axle EHC I System Components (E39/E53)
The EHC system consists of the following components:
EHC Control Module
Air Springs (2) with Air Reservoirs
Rear Axle Level Sensors
Encapsulated Air Supply (LVA)
Warning Indicator
Control Module
The Control Module is mounted in the module carrier box in the luggage compartment on
the right side. It contains the processing electronics and final stages for operation of the
EHC system.
The control module receives the following inputs for its processing functions:
KL 30 & 31 (Power/Ground)
KL 15
Left & Right Ride Height Sensors
K Bus for;
- Vehicle speed
- Engine running
- Door/tailgate - open/closed
E39 Features 06
EHC Module (E39)
Page 16 of 57
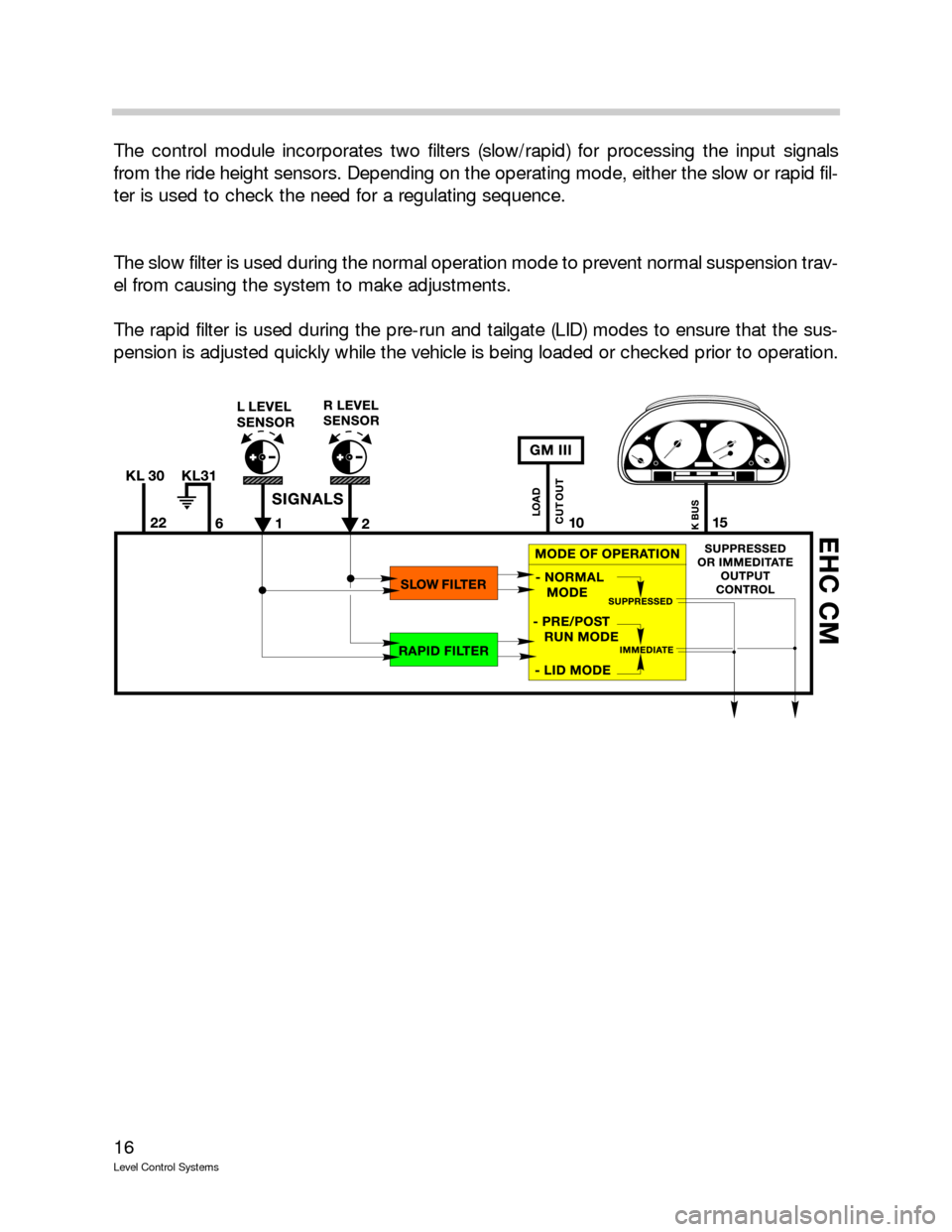
16
Level Control Systems
The control module incorporates two filters (slow/rapid) for processing the input signals
from the ride height sensors. Depending on the operating mode, either the slow or rapid fil-
ter is used to check the need for a regulating sequence.
The slow filter is used during the normal operation mode to prevent normal suspension trav-
el from causing the system to make adjustments.
The rapid filter is used during the pre-run and tailgate (LID) modes to ensure that the sus-
pension is adjusted quickly while the vehicle is being loaded or checked prior to operation.
Page 17 of 57
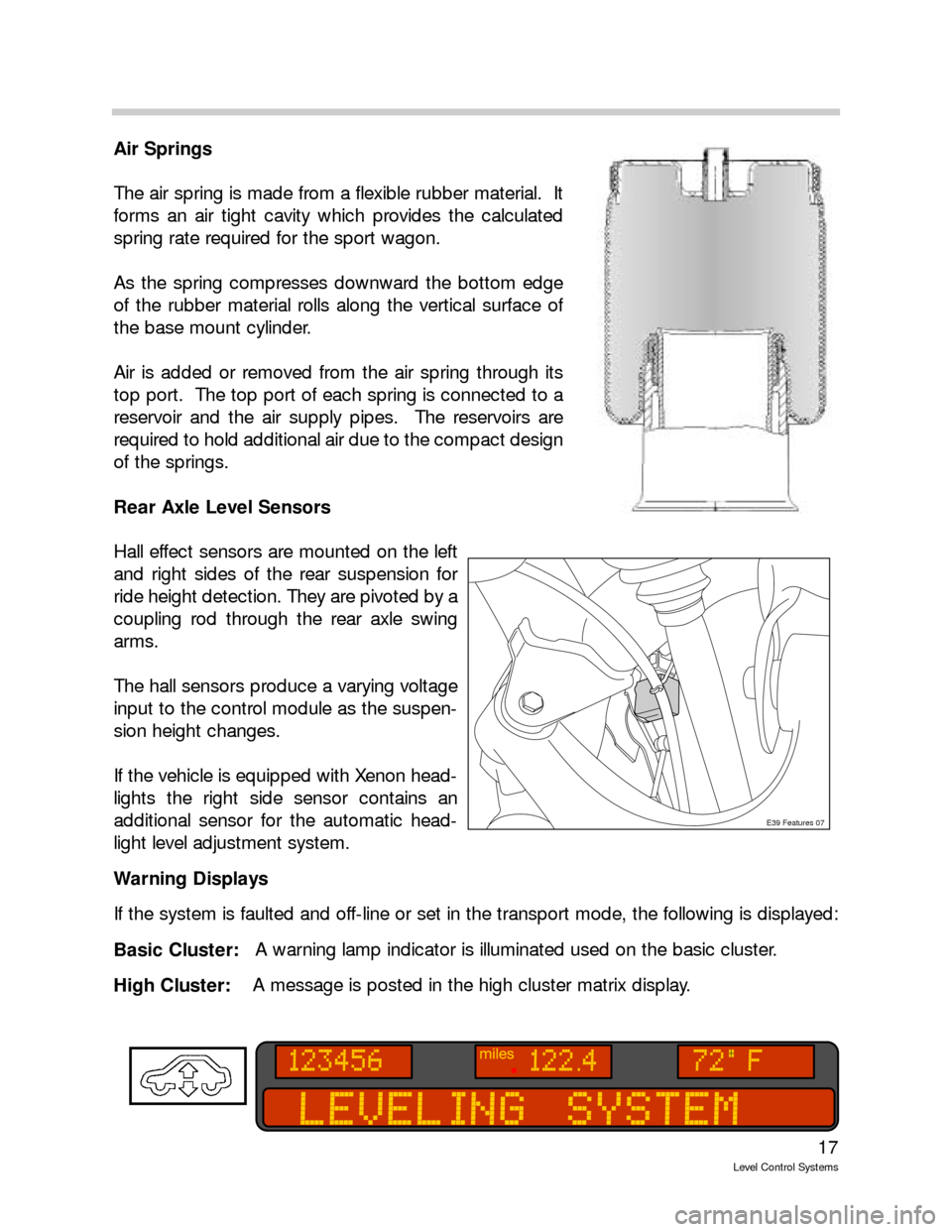
17
Level Control Systems
Air Springs
The air spring is made from a flexible rubber material. It
forms an air tight cavity which provides the calculated
spring rate required for the sport wagon.
As the spring compresses downward the bottom edge
of the rubber material rolls along the vertical surface of
the base mount cylinder.
Air is added or removed from the air spring through its
top port. The top port of each spring is connected to a
reservoir and the air supply pipes. The reservoirs are
required to hold additional air due to the compact design
of the springs.
Rear Axle Level Sensors
Hall effect sensors are mounted on the left
and right sides of the rear suspension for
ride height detection. They are pivoted by a
coupling rod through the rear axle swing
arms.
The hall sensors produce a varying voltage
input to the control module as the suspen-
sion height changes.
If the vehicle is equipped with Xenon head-
lights the right side sensor contains an
additional sensor for the automatic head-
light level adjustment system.
Warning Displays
If the system is faulted and off-line or set in the transport mode, the following is displayed:
Basic Cluster:A warning lamp indicator is illuminated used on the basic cluster.
High Cluster: A message is posted in the high cluster matrix display.
E39 Features 07
Page 21 of 57
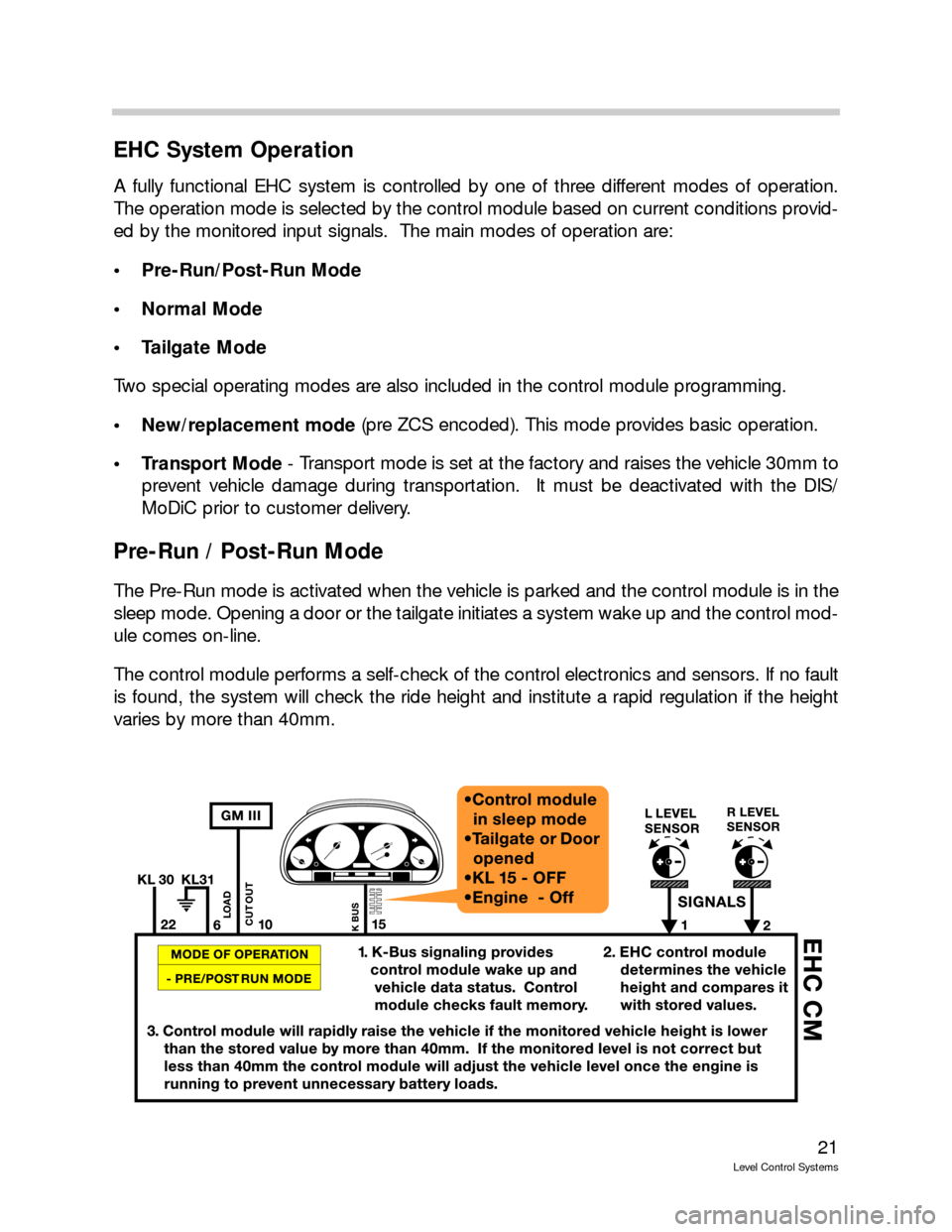
21
Level Control Systems
EHC System Operation
A fully functional EHC system is controlled by one of three different modes of operation.
The operation mode is selected by the control module based on current conditions provid-
ed by the monitored input signals. The main modes of operation are:
• Pre-Run/Post-Run Mode
Normal Mode
Tailgate Mode
Two special operating modes are also included in the control module programming.
New/replacement mode(pre ZCS encoded). This mode provides basic operation.
Transport Mode - Transport mode is set at the factory and raises the vehicle 30mm to
prevent vehicle damage during transportation. It must be deactivated with the DIS/
MoDiC prior to customer delivery.
Pre-Run / Post-Run Mode
The Pre-Run mode is activated when the vehicle is parked and the control module is in the
sleep mode. Opening a door or the tailgate initiates a system wake up and the control mod-
ule comes on-line.
The control module performs a self-check of the control electronics and sensors. If no fault
is found, the system will check the ride height and institute a rapid regulation if the height
varies by more than 40mm.
Page 22 of 57
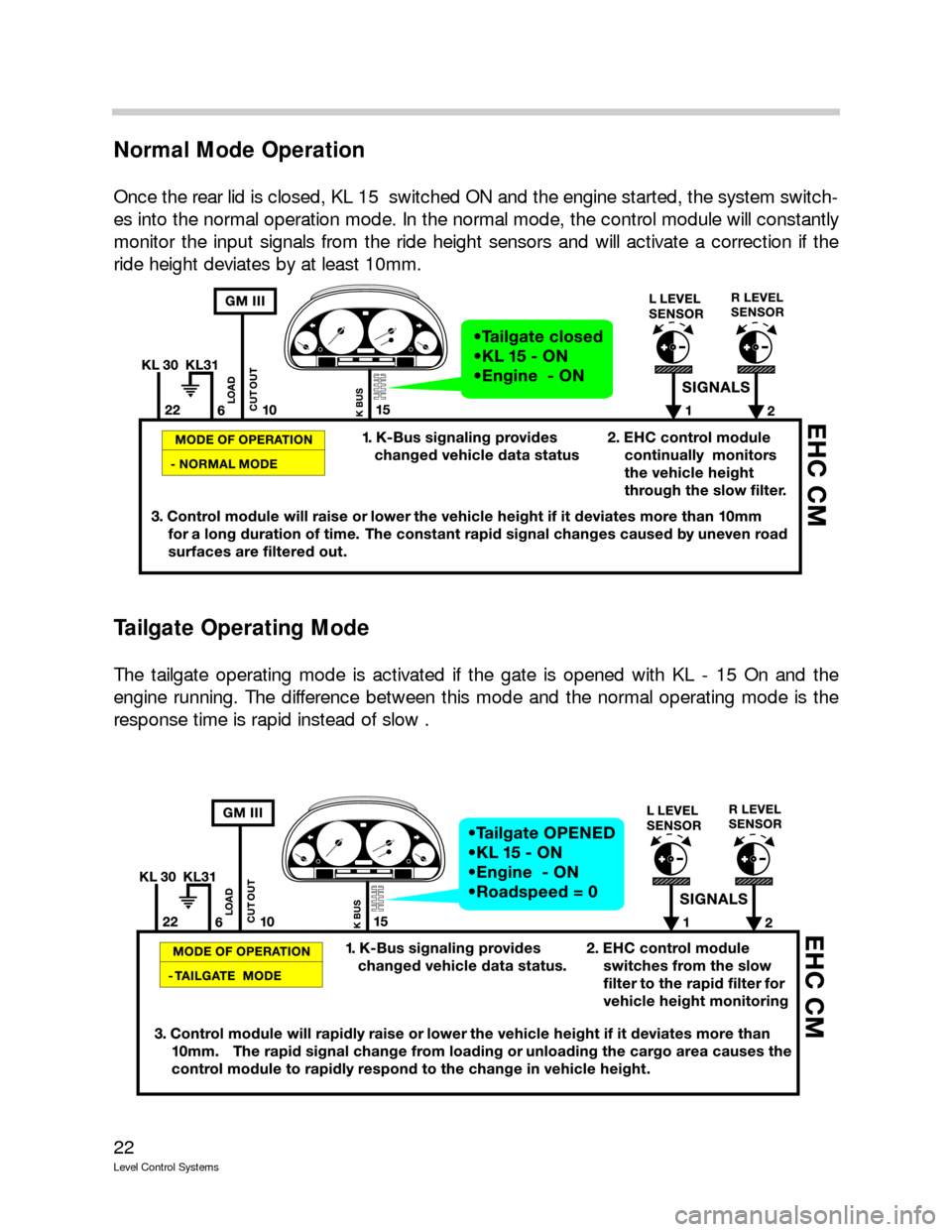
22
Level Control Systems
Normal Mode Operation
Once the rear lid is closed, KL 15 switched ON and the engine started, the system switch-
es into the normal operation mode. In the normal mode, the control module will constantly
monitor the input signals from the ride height sensors and will activate a correction if the
ride height deviates by at least 10mm.
Tailgate Operating Mode
The tailgate operating mode is activated if the gate is opened with KL - 15 On and the
engine running. The difference between this mode and the normal operating mode is the
response time is rapid instead of slow .
Page 23 of 57
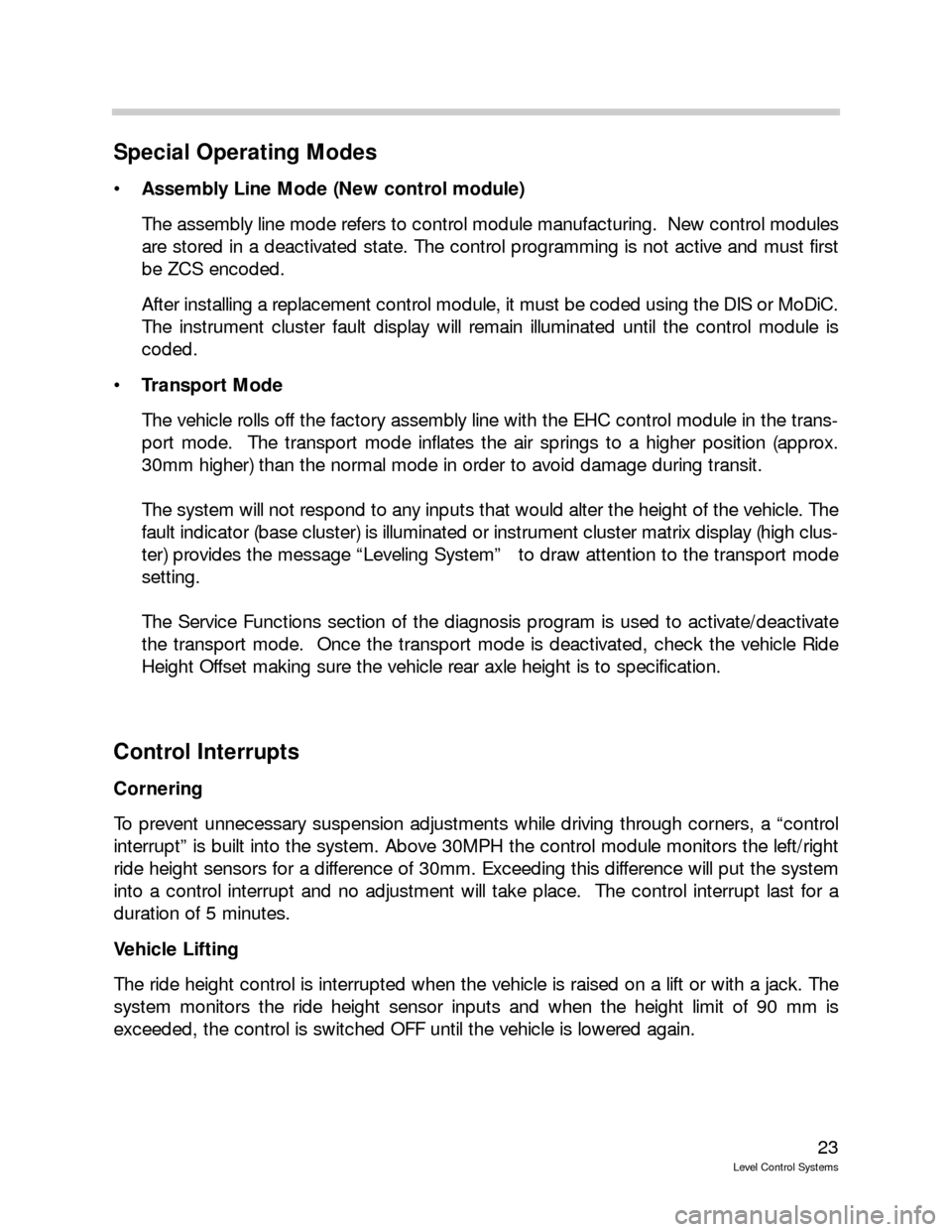
23
Level Control Systems
Special Operating Modes
Assembly Line Mode (New control module)
The assembly line mode refers to control module manufacturing. New control modules
are stored in a deactivated state. The control programming is not active and must first
be ZCS encoded.
After installing a replacement control module, it must be coded using the DIS or MoDiC.
The instrument cluster fault display will remain illuminated until the control module is
coded.
Transport Mode
The vehicle rolls off the factory assembly line with the EHC control module in the trans-
port mode. The transport mode inflates the air springs to a higher position (approx.
30mm higher) than the normal mode in order to avoid damage during transit.
The system will not respond to any inputs that would alter the height of the vehicle. The
fault indicator (base cluster) is illuminated or instrument cluster matrix display (high clus-
ter) provides the message “Leveling System” to draw attention to the transport mode
setting.
The Service Functions section of the diagnosis program is used to activate/deactivate
the transport mode. Once the transport mode is deactivated, check the vehicle Ride
Height Offset making sure the vehicle rear axle height is to specification.
Control Interrupts
Cornering
To prevent unnecessary suspension adjustments while driving through corners, a “control
interrupt” is built into the system. Above 30MPH the control module monitors the left/right
ride height sensors for a difference of 30mm. Exceeding this difference will put the system
into a control interrupt and no adjustment will take place. The control interrupt last for a
duration of 5 minutes.
Vehicle Lifting
The ride height control is interrupted when the vehicle is raised on a lift or with a jack. The
system monitors the ride height sensor inputs and when the height limit of 90 mm is
exceeded, the control is switched OFF until the vehicle is lowered again.
Page 28 of 57
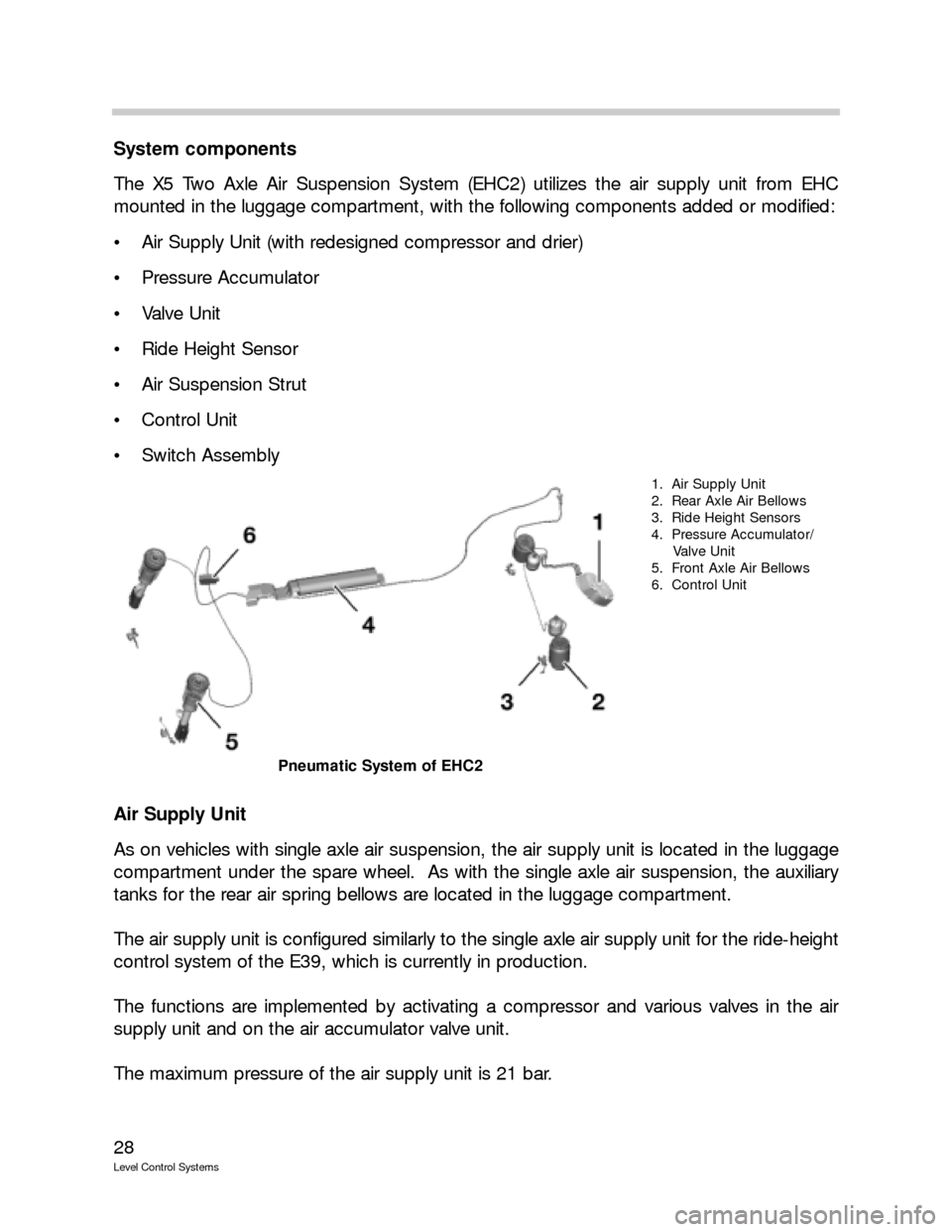
28
Level Control Systems
System components
The X5 Two Axle Air Suspension System (EHC2) utilizes the air supply unit from EHC
mounted in the luggage compartment, with the following components added or modified:
Air Supply Unit (with redesigned compressor and drier)
Pressure Accumulator
Valve Unit
Ride Height Sensor
Air Suspension Strut
Control Unit
Switch Assembly
Air Supply Unit
As on vehicles with single axle air suspension, the air supply unit is located in the luggage
compartment under the spare wheel. As with the single axle air suspension, the auxiliary
tanks for the rear air spring bellows are located in the luggage compartment.
The air supply unit is configured similarly to the single axle air supply unit for the ride-height
control system of the E39, which is currently in production.
The functions are implemented by activating a compressor and various valves in the air
supply unit and on the air accumulator valve unit.
The maximum pressure of the air supply unit is 21 bar.
1. Air Supply Unit
2. Rear Axle Air Bellows
3. Ride Height Sensors
4. Pressure Accumulator/
Valve Unit
5. Front Axle Air Bellows
6. Control Unit
Pneumatic System of EHC2
Page 30 of 57
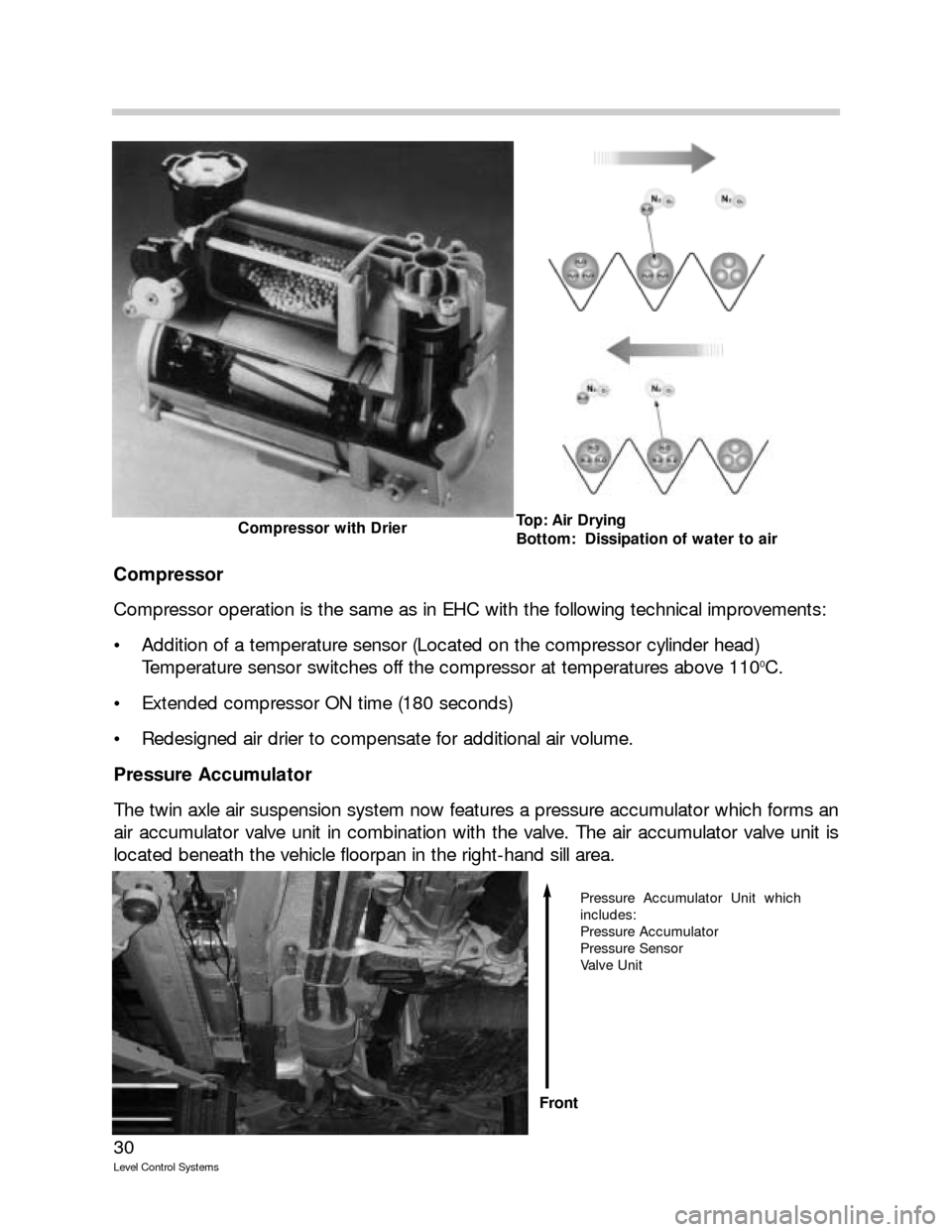
30
Level Control Systems
Compressor
Compressor operation is the same as in EHC with the following technical improvements:
Addition of a temperature sensor (Located on the compressor cylinder head)
Temperature sensor switches off the compressor at temperatures above 110
0C.
Extended compressor ON time (180 seconds)
Redesigned air drier to compensate for additional air volume.
Pressure Accumulator
The twin axle air suspension system now features a pressure accumulator which forms an
air accumulator valve unit in combination with the valve. The air accumulator valve unit is
located beneath the vehicle floorpan in the right-hand sill area.
Top: Air Drying
Bottom: Dissipation of water to airCompressor with Drier
Pressure Accumulator Unit which
includes:
Pressure Accumulator
Pressure Sensor
Valve Unit
Front