table BMW M3 1995 E36 Repair Manual
[x] Cancel search | Manufacturer: BMW, Model Year: 1995, Model line: M3, Model: BMW M3 1995 E36Pages: 759
Page 165 of 759
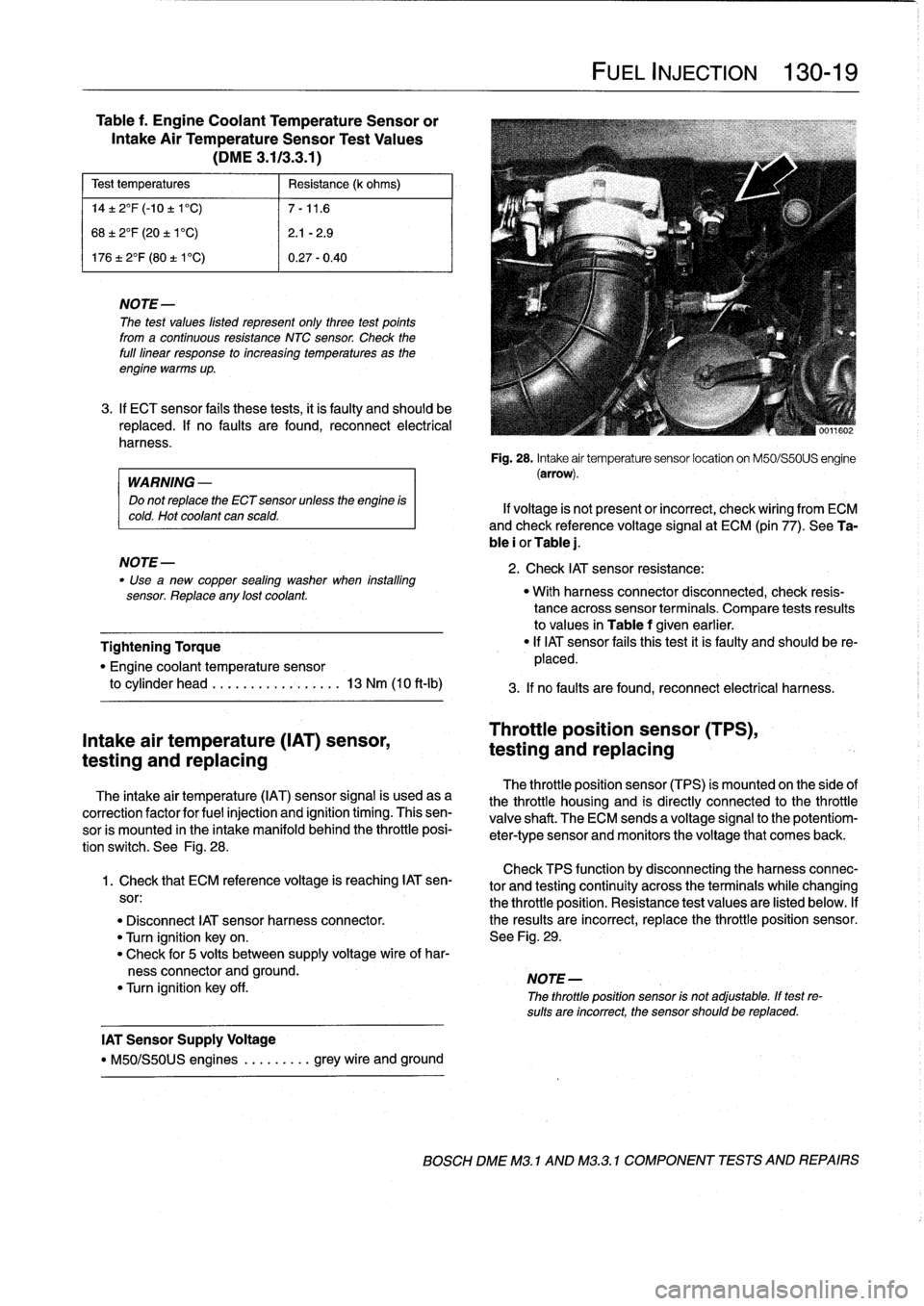
Table
f
.
Engine
Coolant
TemperatureSensor
or
Intake
Air
TemperatureSensor
Test
Values
(DME
3
.113
.3
.1)
Test
temperatures
Resistance
(k
ohms)
14±
2°F
(-10
±
1'C)
7-11
.6
68±
2°F
(20
±
1'C)
2
.1
-2
.9
17612°F
(80
t
V
C)
0
.27-0
.40
NOTE
The
test
values
listed
represent
only
three
test
points
from
a
continuous
resistance
NTC
sensor
.
Check
the
full
linear
response
to
increasing
temperatures
as
the
engine
warms
up
.
3
.
If
ECT
sensor
fails
these
tests,
it
is
faulty
and
should
be
replaced
.
If
no
faults
are
found,
reconnect
electrical
harness
.
WARNING
-
Do
not
replace
the
ECT
sensor
unless
the
engine
is
cold
.
Hot
coolant
can
scald
.
NOTE-
Use
"
a
new
copper
sealing
washer
when
installing
sensor
.
Replace
any
lost
coolant
.
Tightening
Torque
"
Engine
coolant
temperature
sensor
to
cylinder
head
.........
..
.
..
...
13
Nm
(10
ft-lb)
Intake
air
temperature
(IAT)
sensor,
testing
and
replacing
The
intake
air
temperature
(IAT)
sensor
signal
is
usedasa
correction
factor
for
fuel
injection
and
ignition
timing
.
Thissen-
sor
is
mounted
in
the
intake
manifold
behind
the
throttle
posi-
tion
switch
.
See
Fig
.
28
.
Check
TPS
function
by
disconnecting
theharnessconnec-
1
.
Check
that
ECM
reference
voltage
is
reaching
IAT
sen-
tor
and
testing
continuity
across
the
terminalswhile
changing
sor
:
the
throttle
position
.
Resistance
test
values
are
listed
below
.
If
"
Disconnect
IAT
sensor
harness
connector
.
the
resuits
are
incorrect,
replace
the
throttle
position
sensor
.
"
Turn
ignition
keyon
.
See
Fig
.
29
.
"
Check
for
5
volts
between
supply
voltage
wire
of
har-
ness
connector
and
ground
.
NOTE-
"
Turn
ignition
key
off
.
The
throttle
position
sensor
is
not
adjustable
.
If
test
re-
sults
are
incorrect,
the
sensor
should
be
replaced
.
IAT
Sensor
Supply
Voltage
"
M50/S50US
engines
.
........
grey
wire
and
ground
FUEL
INJECTION
130-19
Fig
.
28
.
Intake
air
temperature
sensor
location
on
M50/S50US
engine
(arrow)
.
If
voltage
is
not
present
or
incorrect,
check
wiring
from
ECM
and
check
reference
voltage
signal
at
ECM
(pin
77)
.
See
Ta-
ble
i
or
Table
j
.
2
.
Check
IAT
sensor
resistance
:
"
With
harness
connector
disconnected,
check
resis-
tance
acrosssensor
terminals
.
Compare
tests
resuits
to
values
in
Table
f
given
earlier
.
"
If
IAT
sensor
fafs
thistest
it
is
faulty
and
should
be
re-
placed
.
3
.
If
no
faults
are
found,
reconnect
electrical
harness
.
Throttle
position
sensor
(TPS),
testing
and
replacing
The
throttle
position
sensor
(TPS)
is
mounted
on
the
side
of
the
throttle
housing
and
is
directly
connected
to
the
throttle
valve
shaft
.
The
ECM
sends
a
voltage
signal
to
the
potentiom-
eter-type
sensor
and
monitors
the
voltage
that
comes
back
.
BOSCH
DME
M3
.
1
AND
M32
.1
COMPONENT
TESTS
AND
REPAIRS
Page 166 of 759
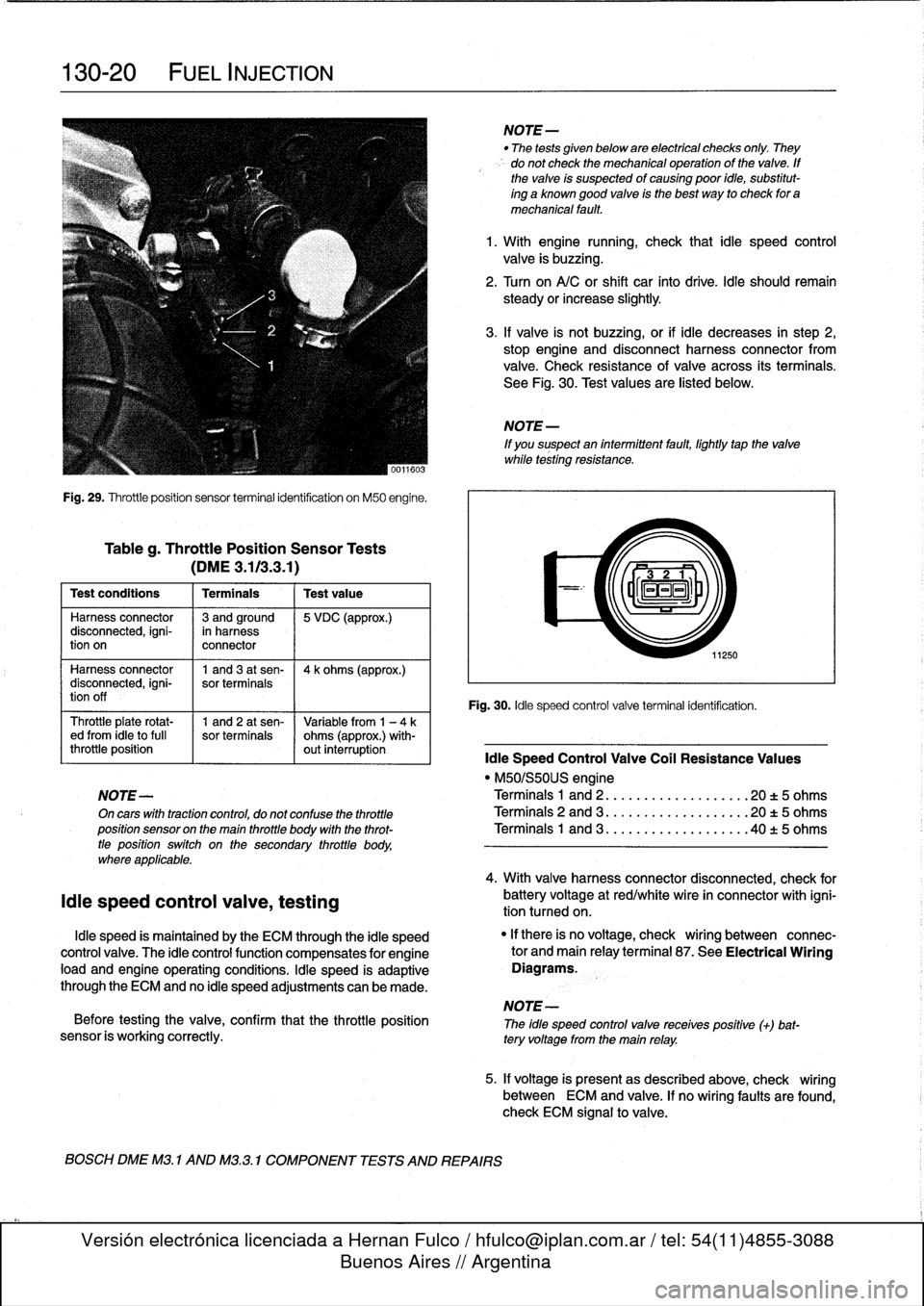
130-20
FUEL
INJECTION
Fig
.
29
.
Throttleposition
sensor
terminal
identification
on
M50
engine
.
Tableg
.
Throttle
Position
Sensor
Tests
(DME3
.113
.3
.1)
Test
conditions
I
Terminals
I
Testvalue
Harness
connector
13
andground
15
VDC
(approx
.)
disconnected,
igni-
in
harness
tion
on
connector
Harness
connector
1
and3
at
sen-
14
k
ohms
(approx
.)
disconnected,
igni-
sor
terminals
tion
off
Throttle
plate
rotat-
1
and
2
at
sen-
Variable
from
1
-
4ked
from
¡dieto
full
sor
terminals
ohms
(approx
.)
with-
throttle
position
out
interruption
¡die
Speed
Control
Valve
Coil
Resistance
Values
"
M50/S50US
engine
NOTE-
Terminals
1
and
2
..
.
................
20
t
5
ohms
On
cars
with
tractioncontrol,
do
not
confuse
the
throttle
Terminals
2
and
3
...................
20
t5
ohms
position
sensor
on
the
main
throttle
body
with
the
throt-
Terminals
1
and
3
..
.
..
:
............
.40
t
5
ohms
tle
positionswitch
on
the
secondary
throttle
body,
where
applicable
.
¡die
speed
control
valve,
testing
¡die
speed
is
maintained
by
the
ECM
through
the
¡die
speed
control
valve
.
The
¡die
controlfunction
compensates
for
engine
load
and
engine
operating
conditions
.
¡die
speed
is
adaptive
through
the
ECM
and
no
¡die
speed
adjustments
can
be
made
.
NOTE-
Before
testing
the
valve,
confirm
that
the
throttle
position
The
idle
speed
controlvalve
receives
positive
(+)
bat-
sensor
is
working
correctly
.
tery
voltage
from
the
main
relay
.
BOSCH
DME
M3
.
1
AND
M3
.3
.1
COMPONENT
TESTS
AND
REPAIRS
NOTE-
"
The
tests
given
below
are
electrical
checks
only
.
They
do
not
check
the
mechanical
operation
of
the
valve
.
If
the
valve
is
suspected
of
causing
poor
idie,
substitut-
ing
a
known
good
valve
is
the
best
way
to
check
for
a
mechanical
fault
.
1
.
With
engine
running,
check
that
¡die
speed
control
valve
is
buzzing
.
2
.
Turn
on
A/C
or
shift
car
finto
drive
.
¡die
should
remain
steady
orincrease
slightly
.
3
.
If
valve
is
not
buzzing,or
if
¡die
decreases
in
step
2,
stop
engine
and
disconnect
harness
connector
from
valve
.
Check
resistance
of
valve
across
its
terminals
.
See
Fig
.
30
.
Test
values
are
listed
below
.
NOTE
-
If
you
suspect
an
intermittent
fault,
lightly
tapthe
valve
while
testing
resistance
.
11250
Fig
.
30
.
¡die
speed
control
valve
terminal
identification
.
4
.
With
valve
harnessconnector
disconnected,
check
for
battery
voltage
at
red/white
wire
in
connector
with
igni-
tion
tumed
on
.
"
If
there
is
no
voltage,
check
wiring
between
connec-
tor
and
main
relayterminal
87
.
See
Electrical
Wiring
Diagrams
.
5
.
If
voltage
is
presentas
described
above,
check
wiring
between
ECM
and
valve
.
If
no
wiring
faults
are
found,
check
ECM
signal
to
valve
.
Page 167 of 759
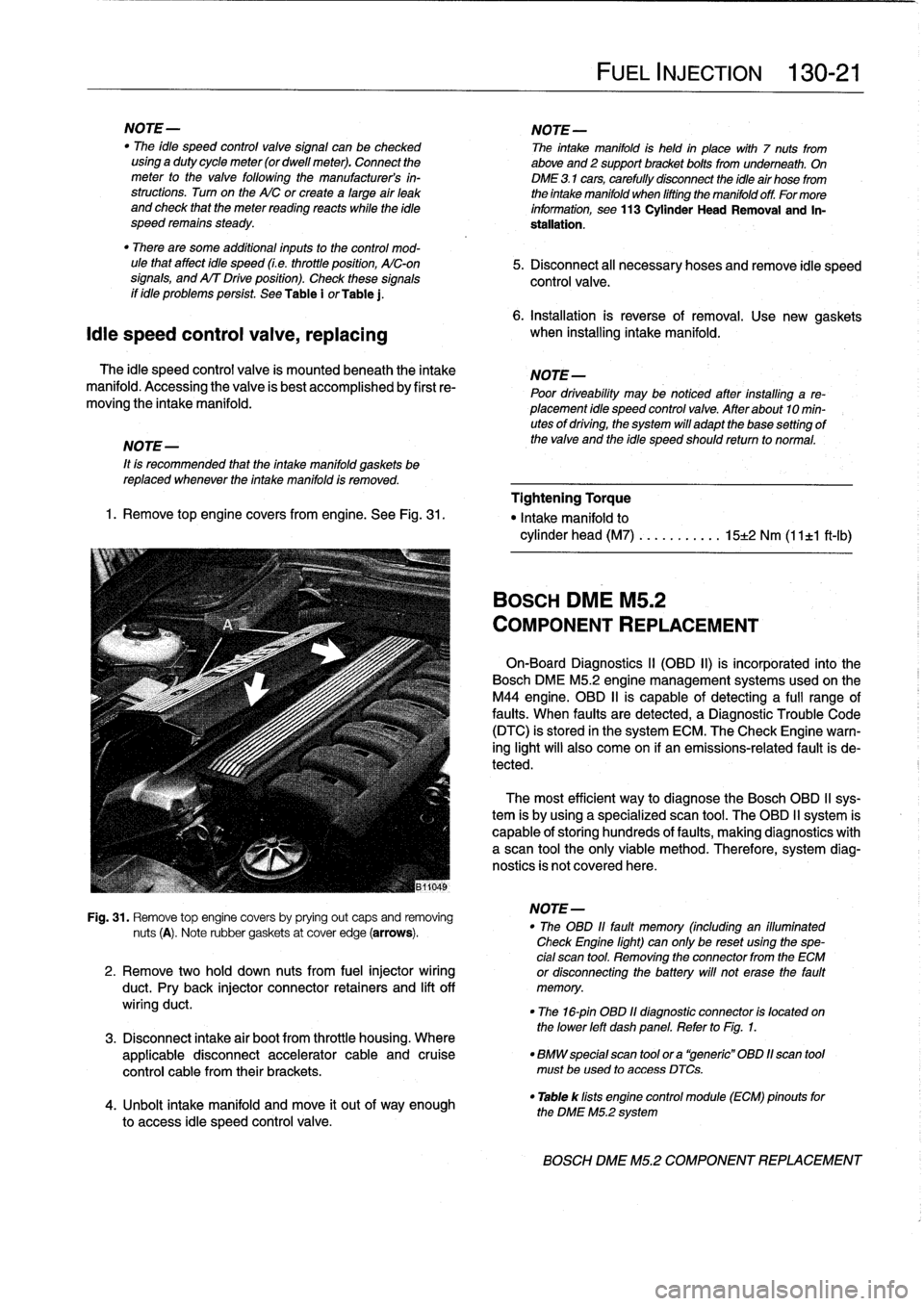
NOTE-
NOTE-
"
The
Ole
speed
control
valve
signal
can
be
checked
The
intake
manifold
is
held
in
place
with
7
nuts
from
using
a
duty
cycle
meter
(or
dwellmeter)
.
Connect
the
above
and
2
support
bracket
bolts
from
undemeath
.
On
meter
to
the
valve
following
the
manufacturer's
in-
DME
3
.1
cars,
carefully
disconnect
the
idleair
hose
from
structions
.
Turn
on
the
WC
or
create
a
larga
air
leak
theintake
manifold
when
lifting
the
manifold
off
.
For
more
and
check
that
the
meter
reading
reacts
while
the
idle
information,
sea
113
Cylinder
HeadRemovaland
In-
speed
remainssteady
.
stallation
.
"
There
are
some
additional
inputs
to
the
control
mod-
ule
that
affect
idle
speed
(Le
.
throttle
position,
AIC-on
5
.
Disconnect
al¡
necessary
hoses
andremove
idle
speed
signals,
andAIT
Drive
position)
.
Check
these
signals
control
valve
.
if
idle
problems
persist
.
See
Tabla
i
orTable
j
.
Idle
speed
control
valva,
replacing
The
idle
speed
control
valve
is
mounted
beneath
the
intake
manifold
.
Accessing
the
valva
is
best
accomplishedby
first
re-
moving
the
intake
manifold
.
NOTE-
¡tis
recommended
that
the
intake
manifold
gaskets
be
replaced
whenever
the
intake
manifold
is
removed
.
1
.
Remove
top
enginecovers
from
engine
.
See
Fig
.
31
.
FUEL
INJECTION
130-21
6
.
Installation
is
reverse
of
Removal
.
Use
new
gaskets
when
installing
intake
manifold
.
NOTE-
Poor
driveability
may
be
noticed
afterinstalling
a
re-
placement
idle
speed
control
valve
.
After
about
10
min-
utes
of
driving,
the
system
will
adapt
the
base
setting
of
the
valva
and
the
idle
speed
should
retum
to
normal
.
Tightening
Torque
"
Intakemanifold
to
cylinder
head
(M7)
........
..
.
15±2
Nm
(11
ti
ft-Ib)
BOSCH
DME
M5
.2
COMPONENT
REPLACEMENT
On-Board
Diagnostics
11
(OBD
II)
is
incorporated
into
the
Bosch
DME
M5
.2
engine
management
systems
used
on
the
M44
engine
.
OBD
II
is
capable
of
detecting
a
full
range
of
faults
.
When
faults
are
detected,
a
Diagnostic
Trouble
Code
(DTC)
is
stored
in
the
system
ECM
.
The
Check
Engine
warn-
ing
light
will
also
come
on
if
an
emissions-relatad
fault
is
de-
tected
.
The
most
efficient
way
to
diagnose
the
Bosch
OBD
II
sys-
tem
is
by
using
a
specialized
scan
tool
.
The
OBD
II
system
is
capable
of
storing
hundreds
of
faults,
making
diagnostics
with
a
scan
tool
the
only
viable
method
.
Therefore,
system
diag-
nostics
is
not
covered
here
.
Fi
31
.
Remove
to
en
ine
covers
b
in
out
caPs
and
removin
NOTE-
nuts
(A)
9
.
P
g
y
Pry
g
g
"
The
OBD
11
fault
memory
(including
an
iiluminated
Note
14
L-te
at
cover
edge
(arrows)
.
Check
Engine
light)
can
only
be
reset
using
the
spe-
cial
scan
tool
.
Removing
the
connector
from
the
ECM
2
.
Remove
two
hold
down
nuts
from
fuel
injector
wiring
or
disconnecting
the
battery
will
not
arase
the
fault
duct
.
Pry
back
injector
connector
retainers
and
lift
off
memory
.
wiring
duct
.
"
The
16-pin
OBD
Il
diagnostic
connector
is
located
on
the
lower
left
dash
panel
.
Refer
to
Fig
.
1
.
3
.
Disconnect
intake
air
bootfrom
throttle
housing
.
Where
applicable
disconnect
accelerator
cable
and
cruise
"
BMW
special
scan
tool
ora
`generic"OBD
II
scan
tool
control
cable
from
their
brackets
.
must
be
used
to
access
DTCs
.
4
.
Unbolt
intake
manifold
and
move
it
out
of
way
enough
to
access
idle
speed
control
valva
.
"
Tablak
lists
engine
control
module
(ECM)
pinouts
for
the
DMEM5
.2
system
BOSCH
DME
M5
.
2
COMPONENT
REPLACEMENT
Page 169 of 759
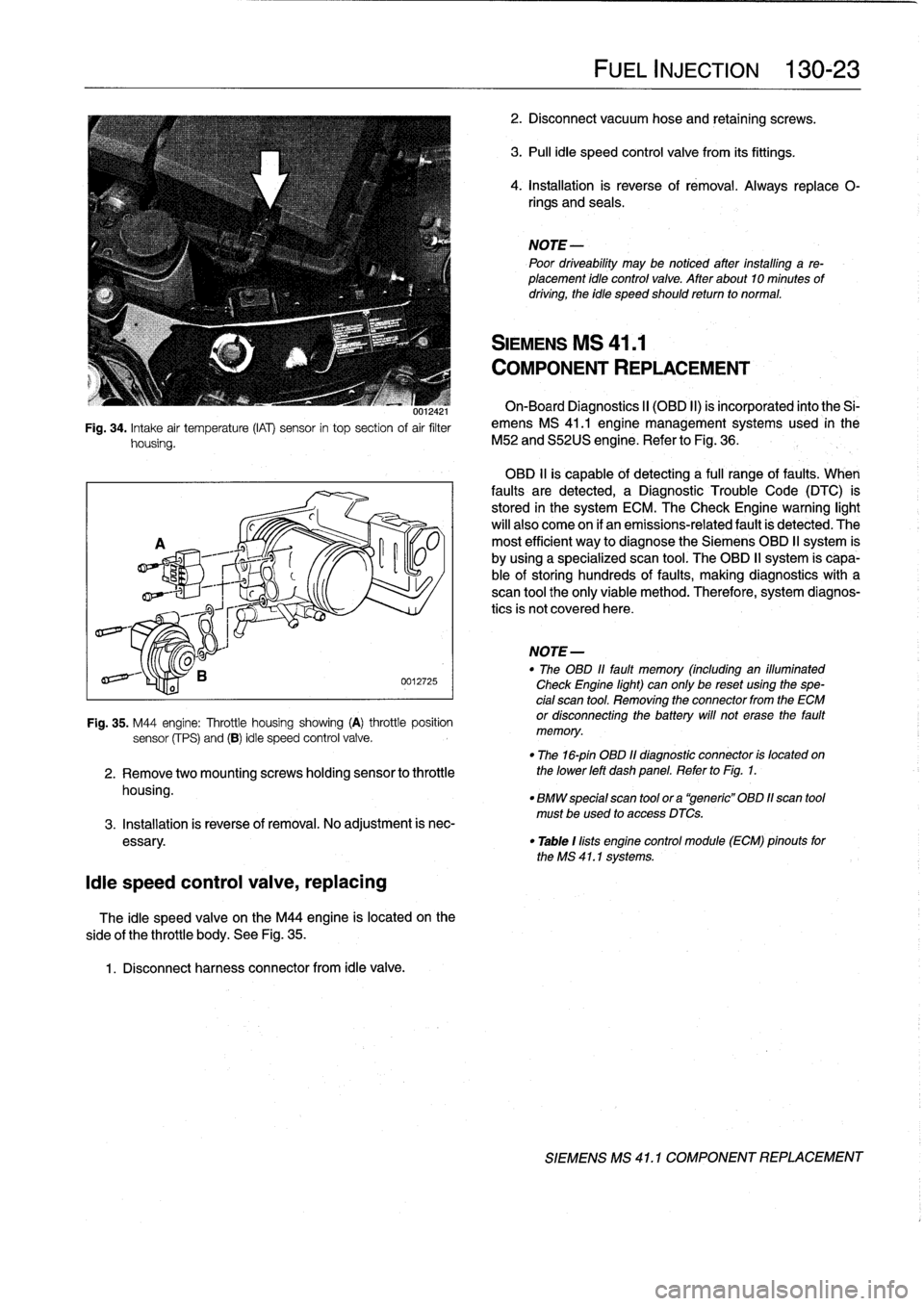
001ía4
i
Fig
.
34
.
Intake
air
temperature
(IAT)
sensor
in
top
section
of
air
filter
housing
.
¡die
speed
control
valve,
replacing
side
of
the
throttle
body
.
See
Fig
.
35
.
1
.
Disconnect
harness
connector
from
¡die
valve
.
0012725
Fig
.
35
.
M44
engine
:
Throttle
housing
showing
(A)
throttle
position
sensor
(fPS)
and
(B)
¡die
speed
control
valve
.
2
.
Remove
twomountingscrews
holding
sensor
to
throttle
housing
.
The
¡die
speed
valve
on
the
M44
engine
is
located
on
the
FUEL
INJECTION
130-23
2
.
Disconnect
vacuum
hose
and
retaining
screws
.
3
.
Pull
¡die
speed
control
valve
from
its
fittings
.
4
.
Installation
is
reverse
of
rémoval
.
Always
replace
0-
rings
and
seals
.
NOTE
Poor
driveability
may
be
notíced
after
installing
a
re-
placement
¡dio
control
valve
.
After
about10
minutes
of
driving,
the
idie
speed
should
retum
to
normal
.
SIEMENS
MS
41
.1
COMPONENT
REPLACEMENT
On-Board
Diagnostics
II
(OBD
II)
is
incorporated
into
the
Si-
emens
MS
41
.1
engine
management
systems
used
in
the
M52
and
S52US
engine
.
Refer
to
Fig
.
36
.
OBD
11
is
capable
of
detecting
a
fui¡
range
offaults
.
When
faults
are
detected,
a
Diagnostic
Trouble
Code
(DTC)
is
stored
in
the
system
ECM
.
The
Check
Engine
warning
light
will
also
come
on
if
an
emissions-related
fault
is
detected
.
The
most
efficient
way
to
diagnose
the
Siemens
OBD
II
system
is
by
using
a
specialized
scan
tool
.
The
OBD
II
system
is
capa-
ble
of
storing
hundreds
of
faults,
making
diagnostics
with
a
scan
tool
the
only
viable
method
.
Therefore,
system
diagnos-
tics
is
not
covered
here
.
NOTE
-
"
The
OBD
11
fault
memory
(including
an
illuminated
Check
Engine
light)
can
only
be
reset
using
the
spe-
cial
scan
tool
.
Removing
the
connector
from
the
ECM
or
disconnecting
the
battery
will
not
erase
the
fault
memory
.
"
The
16-pin
OBD
11
diagnostic
connector
is
located
on
the
lower
left
dash
panel
.
Refer
to
Fig
.
1
.
"
BMW
special
scan
tool
ora
"generic"
OBD
11scan
tool
must
be
used
to
access
DTCs
.
3
.
Installation
is
reverse
of
removal
.
No
adjustment
is
nec
essary
.
"
Table
1
lists
engine
control
module
(ECM)
pinouts
forthe
MS
41
.1
systems
.
SIEMENS
MS
41
.
1
COMPONENT
REPLACEMENT
Page 173 of 759
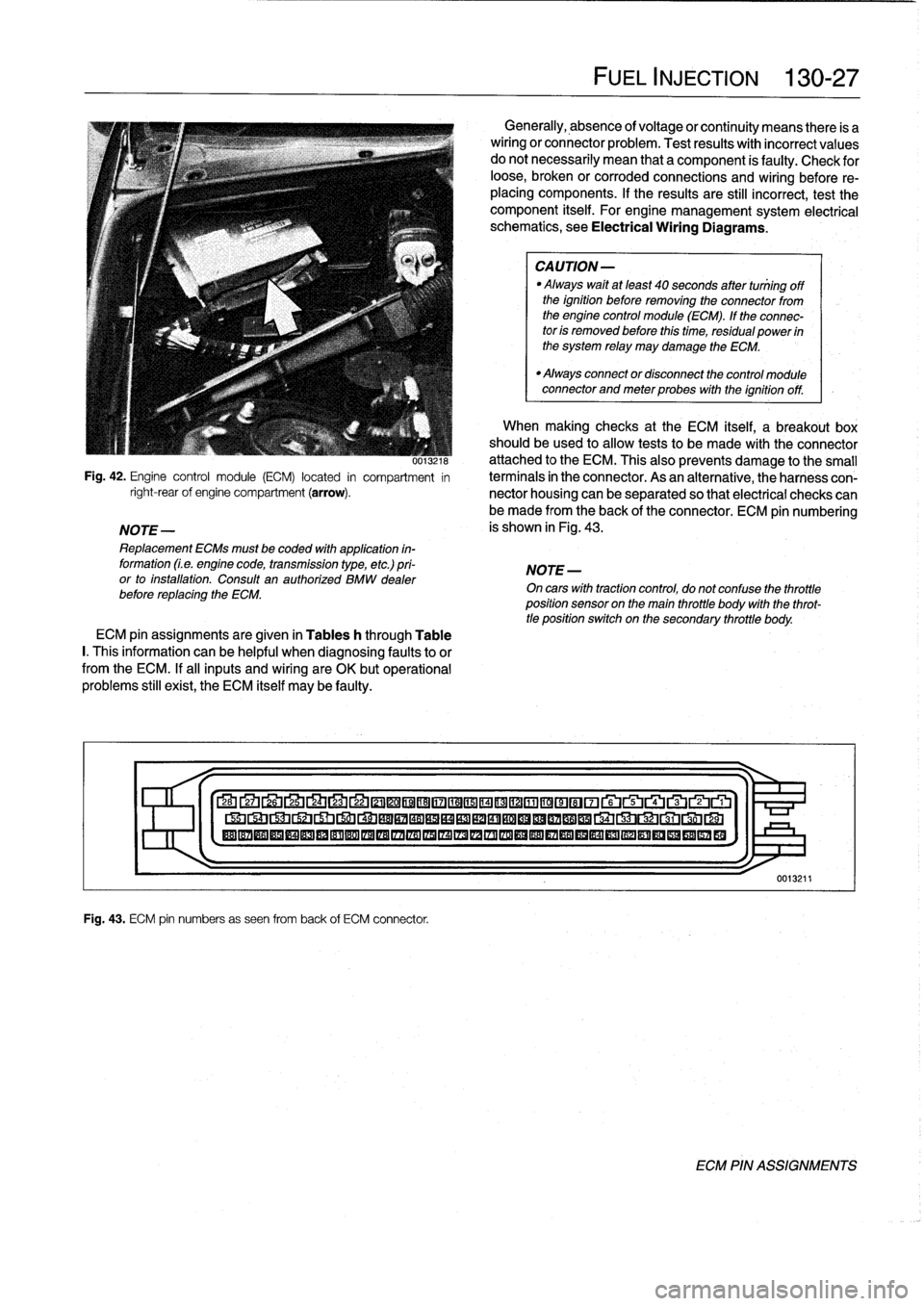
0013ZIM
Fig
.
42
.
Engine
control
module
(ECM)
located
in
compartment
in
right-rearof
engine
compartment
(arrow)
.
NOTE-
Replacement
ECMs
must
be
coded
with
application
in-
formation
(Le
.
engine
code,
transmission
type,
etc
.)
pri-
or
to
installation
.
Consult
an
authorized
BMW
dealer
before
replacing
the
ECM
.
ECM
pin
assignments
are
given
in
Tables
h
through
Table
I.
This
information
can
be
helpful
when
diagnosing
faultsto
or
from
the
ECM
.
If
al¡
inputs
and
wiring
are
OK
butoperational
problems
still
exist,
the
ECM
itself
may
be
faulty
.
Fig
.
43
.
ECM
pin
numbers
as
seen
from
back
of
ECM
connector
.
FUEL
INJECTION
130-
2
7
Generally,
absence
of
voltage
or
continuity
means
there
is
a
wiring
or
connector
problem
.
Test
results
with
incorrect
values
do
notnecessarily
mean
that
a
component
is
faulty
:
Check
for
loose,
broken
or
corroded
connections
and
wiring
before
re-
placing
components
.
If
the
results
are
still
incorrect,
test
the
component
itself
.
For
engine
management
system
electrical
schematics,
see
Electrical
Wiring
Diagrams
.
CAUTION-
Always
waitat
least
40
seconds
after
tuniing
off
the
ignition
before
removing
the
connector
from
the
engine
control
module
(ECM)
.
If
the
connec-
tor
is
removed
before
this
time,
residual
power
in
the
system
relay
may
damage
the
ECM
.
"
Always
connector
disconnect
the
control
module
connector
and
meter
probes
with
the
ignitionoff
.
When
making
checks
at
the
ECM
itself,
a
breakout
box
should
be
used
to
allow
tests
to
be
made
with
the
connector
attached
to
the
ECM
.
This
also
prevents
damage
tothe
small
termínals
in
the
connector
.
As
an
alternative,
theharness
con-
nector
housing
can
be
separated
so
that
electrical
checks
can
be
made
from
the
back
of
the
connector
.
ECM
pin
numbering
is
shown
in
Fig
.
43
.
NOTE
-
On
cars
with
tractioncontrol,
do
not
confuse
the
throttle
position
sensor
on
the
main
throttle
body
with
the
throt-
tle
position
switch
on
the
secondary
throttle
body
.
27
Lb
2L4
LJ
22
©©®®17
©©®©©~©©®©~~rui~~ru
®®®®®®®®®®®®®®®IZA®®®®®®®®®®®®®®®®®
1
>I-
0013211
ECM
PIN
ASSIGNMENTS
Page 174 of 759
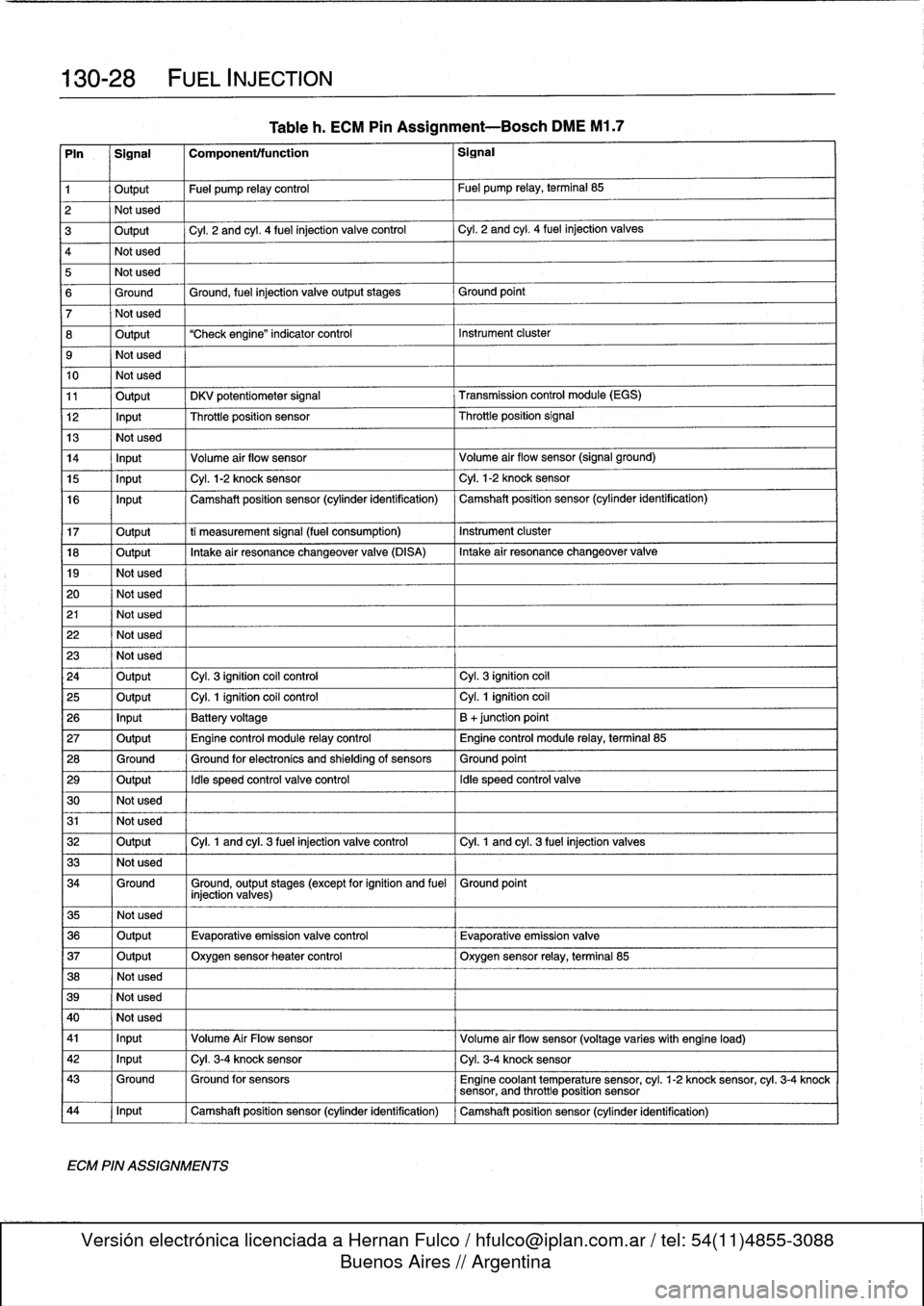
130-
2
8
FUEL
INJECTION
Tableh
.
ECM
Pin
Assignment-Bosch
DME
M1
.7
Pin
Signal
Componenttfunction
Signal
1
Output
Fuel
pump
relay
control
Fuel
pump
relay,
terminal
85
2
Not
used
3
Output
Cyl
.
2
and
cyl
.
4
fuel
injection
valve
control
Cyl
.
2
and
cyl
.
4
fuel
injection
valves
4
Not
used
5
Not
used
6
Ground
Ground,
fuel
injection
valveoutputstages
Ground
point
7
Not
used
8
Output
"Check
engine"
indicator
control
Instrument
cluster
9
Not
used
10
Not
used
11
Output
DKV
potentiometer
signal
Transmission
control
module
(EGS)
12
Input
Throttleposition
sensor
Throttleposition
Signal
13
Not
used
14
Input
Volume
air
flow
sensor
Volume
air
flow
sensor
(signal
ground)
15
Input
Cyl
.
1-2
knock
sensor
Cyl
.
1-2
knock
sensor
16
Input
Camshaft
position
sensor
(cylinder
identification)
Camshaft
position
sensor
(cylinder
identification)
17
Output
ti
measurement
signal
(fuel
consumption)
Instrument
cluster
18
Output
Intakeair
resonance
changeover
valve
(DISA)
Intake
air
resonance
changeover
valve
19
-
Not
used
20
Not
used
21
Not
used
22
Not
used
23
Not
used
24
Output
Cyl
.
3
ignition
coil
control
Cyl
.
3
ignition
coil
25
Output
Cyl
.
1
ignition
coil
control
Cyl
.
1
ignition
coil
26
Input
Battery
voltage
B
+junction
point
27
Output
Engine
control
module
relay
control
Engine
control
module
relay,
terminal
85
28
Ground
Ground
for
electronics
and
shielding
of
sensors
Ground
point
29
Output
Idle
speed
control
valve
control
Idle
speed
control
valve
30
Not
used
31
Not
used
32
Output
Cyl
.
1
and
cyl
.
3
fuel
injection
valve
control
Cyl
.
1
and
cyl
.
3
fuel
injection
valves
33
Not
used
34
Ground
Ground,
output
stages
(except
for
ignition
and
fuel
Ground
point
injection
valves)
35
Not
used
36
Output
Evaporative
emissionvalve
control
Evaporative
emission
valve
37
Output
Oxygen
sensor
heater
control
Oxygen
sensor
relay,
terminal
85
38
Not
used
39
Not
used
40
I
Not
used
41
I
Input
,
Volume
Air
Flow
sensor
Volume
air
flow
sensor
(voltage
varies
with
engine
load)
42
1
Input
1
Cyl
.
3-4
knock
sensor
1
Cyl
.
3-4
knock
sensor
43
Ground
Ground
for
sensors
Engine
coolant
temperature
sensor,
cyl
.
1-2
knock
sensor,
cyl
.
3-4
knock
sensor,
and
throttle
position
sensor
44
1
Input
1
Camshaft
position
sensor
(cylinder
identification)
1
Camshaft
position
sensor
(cylinder
identification)
ECM
PIN
ASSIGNMENTS
Page 175 of 759
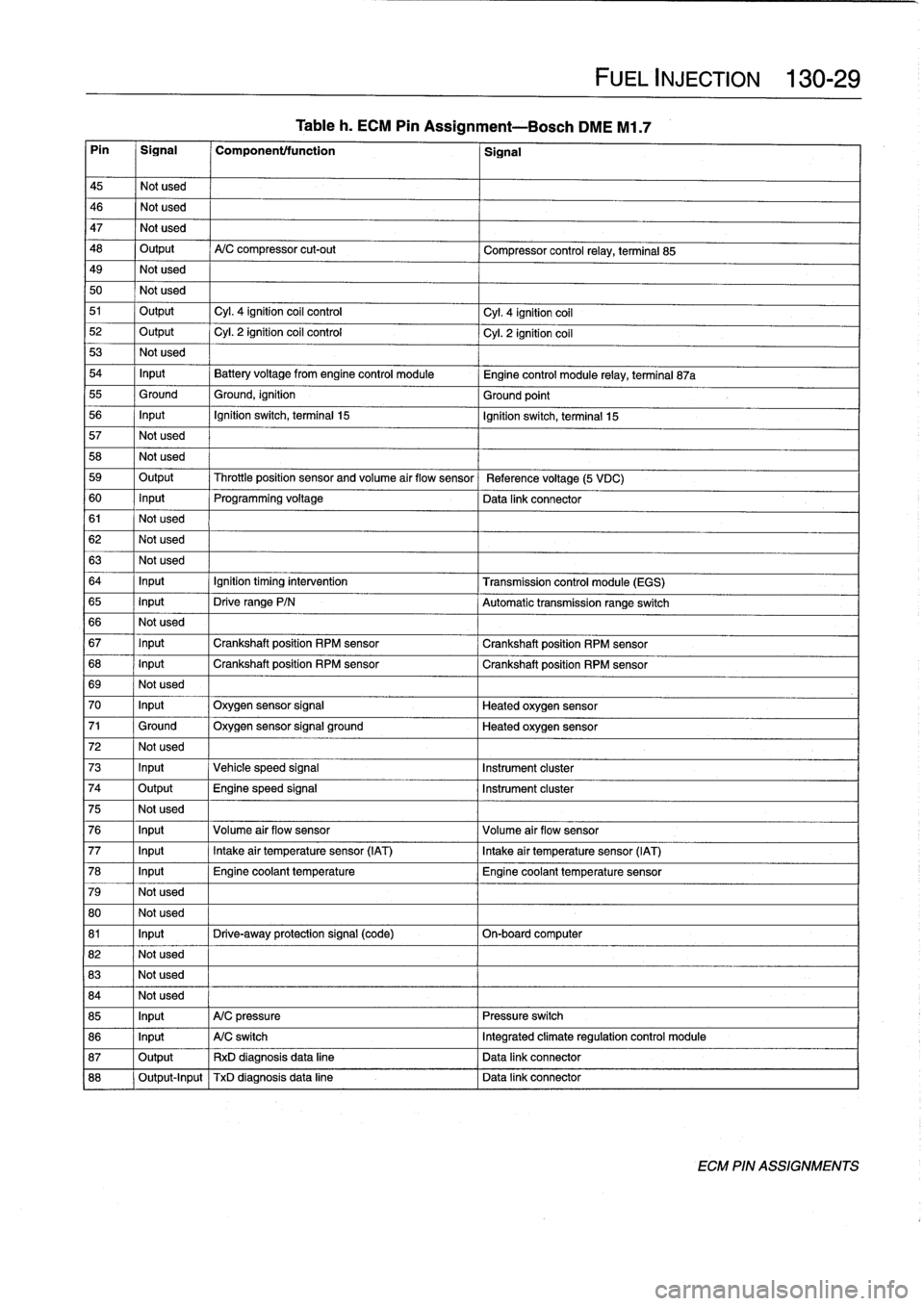
Tableh
.
ECM
Pin
Assignment--Bosch
DME
M1
.7
Pin
1
Signal
1
Component/function
1
Signal
45
Notused
46
Notused
47
Notused
48
Output
A/C
compressor
cut-out
Compressor
control
relay,
terminal
85
49
Notused
50
Notused
51
Output
Cyl
.
4
ignition
coil
control
Cyl
.
4
ignition
coil
52
Output
Cyl
.
2
ignition
coil
control
Cyl
.
2
ignition
coil
53
Not
used
54
Input
Battery
voltage
from
engine
control
module
Engine
control
module
relay,
terminal
87a
55
Ground
Ground,
ignition
Ground
point
56
Input
Ignition
switch,
terminal
15
Ignition
switch,
terminal
15
57
Notused
58
Not
used
59
Output
Throttleposition
sensor
and
volume
air
flow
sensor
Reference
voltage
(5
VDC)
60
Input
Programming
voltage
Data
link
connector
61
Notused
62
Notused
63
Notused
64
Input
Ignition
timing
intervention
Transmission
control
module
(EGS)
65
Input
Drive
range
P/N
Automatic
transmission
range
switch
66
Notused
67
Input
Crankshaft
position
RPM
sensor
Crankshaft
position
RPM
sensor
68
Input
Crankshaft
position
RPM
sensor
Crankshaft
position
RPM
sensor
69
Notused
70
Input
Oxygen
sensor
signal
Heated
oxygen
sensor
71
Ground
Oxygen
sensor
signal
ground
Heated
oxygen
sensor
72
Notused
73
Input
Vehicle
speed
signal
Instrument
cluster
74
Output
Engine
speed
signal
Instrument
cluster
75
Not
used
76
Input
Volume
air
flow
sensor
Volume
air
flow
sensor
77
Input
Intake
air
temperature
sensor
(IAT)
Intake
air
temperature
sensor
(IAT)
78
Input
Engine
coolant
temperature
Engine
coolant
temperature
sensor
79
Notused
80
Not
used
81
Input
Drive-away
protection
signal
(code)
On-boardcomputer
82
Not
used
83
Notused
84
Not
used
85
Input
A/C
pressure
Pressure
switch
86
Input
A/C
switch
Integrated
climate
regulation
control
module
87
Output
RxD
diagnosisdata
line
Data
link
connector
88
Output-Input
TxD
diagnosisdata
line
l
Data
link
connector
FUEL
INJECTION
130-
2
9
ECM
PIN
ASSIGNMENTS
Page 176 of 759
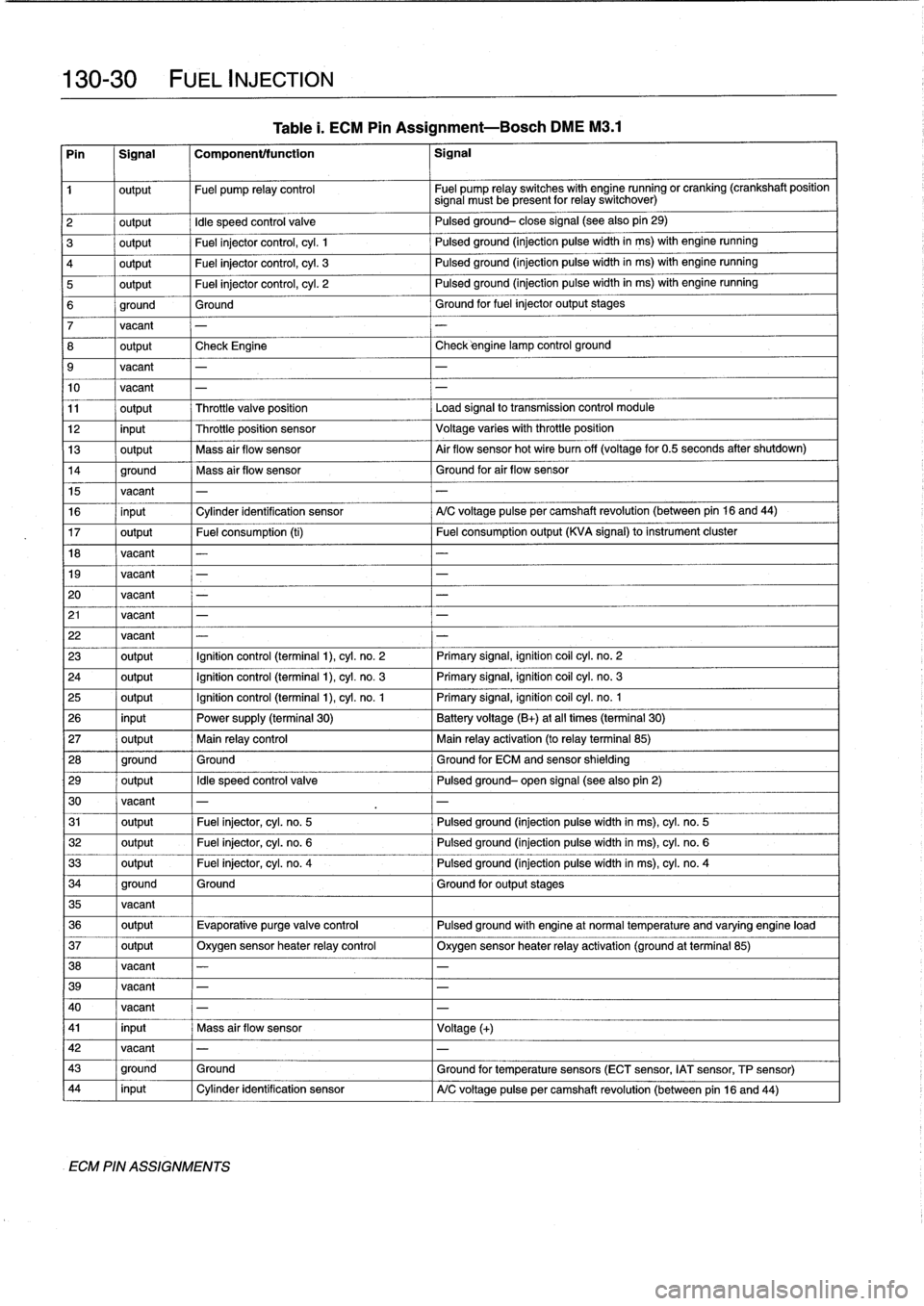
130-
3
0
FUEL
INJECTION
Pin
Signal
Component/function
Signal
ECM
PIN
ASSIGNMENTS
Table
1.
ECM
Pin
Assignment-Bosch
DME
M3
.1
1
output
Fuel
pump
relay
control
Fuel
pump
relay
switches
with
engine
runningor
cranking
(crankshaft
position
Signal
mustbe
present
for
relay
switchover)
2
1
output
1
Idle
speed
control
valve
1
Pulsad
ground-
close
signal
(seealsopin29)
3
output
Fuel
injectorcontrol,
cyl
.
1
Pulsedground
(injection
pulsewidth
in
ms)
with
engine
running
4
output
Fuel
injectorcontrol,
cyl
.
3
Pulsedground
(injection
pulsewidth
in
ms)
with
engine
running
5
output
Fuel
injector
control,
cyl
.
2
Pulsedground
(injection
pulse
width
in
ms)
with
enginerunning
6
ground
Ground
Ground
for
fuel
injector
output
stages
7
vacant
-
-
8
output
Check
Engine
Check
éngine
lamp
control
ground
9
vacant
-
-
10
vacant
-
-
11
output
Throttle
valve
position
Load
signal
to
transmission
control
module
12
input
Throttle
position
sensor
Voltage
varies
with
throttle
position
13
output
Mass
air
flow
sensor
Air
flow
sensor
hotwire
burn
off
(voltage
for
0
.5
seconds
after
shutdown)
14
ground
Mass
air
flow
sensor
Ground
for
air
flow
sensor
15
vacant
-
-
16
input
Cylinder
identification
sensor
A/C
voltage
pulse
per
camshaft
revolution
(between
pin
16
and
44)
17
output
Fuel
consumption
(ti)
Fuel
consumption
output
(KVA
Signal)
to
instrument
cluster
18
vacant
-
-
19
vacant
-
-
20
vacant
-
-
21vacant
-
-
22
vacant
-
-
23
output
Ignition
control
(terminal
1),
cyl
.
no
.
2
Primary
Signal,
ignition
coil
cyl
.
no
.
2
24
output
Ignition
control
(terminal
1),
cyl
.
n
o
.
3
Primary
signal,
ignition
coil
cyl
.
no
.
3
25
output
Ignition
control
(terminal
1),
cyl
.
n
o
.
1
Primary
signal,
ignitioh
coil
cyl
.
no
.
1
26
input
Power
supply
(terminal
30)
Battery
voltage
(B+)
at
al¡
times
(terminal
30)
27
output
Main
relay
control
Main
relay
activation
(to
relay
terminal
85)
28
ground
Ground
Ground
for
ECM
and
sensor
shielding
29
output
Idle
speed
control
valve
Pulsed
ground-
open
signal
(see
also
pin
2)
30
vacant
-
-
31
output
Fuel
injector,cyl
.
no
.
5
Pulsedground
(injection
pulsewidth
in
ms),
cyl
.
no
.
5
32
output
Fuel
injector,cyl
.
no
.
6
Pulsedground
(injection
pulse
width
in
ms),
cyl
.
no
.
6
33
output
Fuel
injector,cyl
.
no
.
4
Pulsedground
(injection
pulsewidth
in
ms),
cyl
.
no
.
4
34
ground
Ground
Ground
for
output
stages
35
vacant
36
output
Evaporative
purgevalve
control
Pulsed
ground
with
engine
at
normal
temperature
and
varying
engine
load
37
output
Oxygen
sensor
heater
relay
control
Oxygen
sensor
heater
relayactivation
(ground
at
terminal
85)
38
vacant
-
-
39
vacant
-
-
40
vacant
-
41
input
Mass
air
flow
sensor
Voltage
(+)
42
vacant
-
-
43
ground
Ground
Ground
for
temperatura
sensors
(ECT
sensor,
IAT
sensor,
TP
sensor)
44
input
Cylinder
identification
sensor
A/C
voltagepulseper
camshaft
revolution
(between
pin
16
and
44)
Page 177 of 759
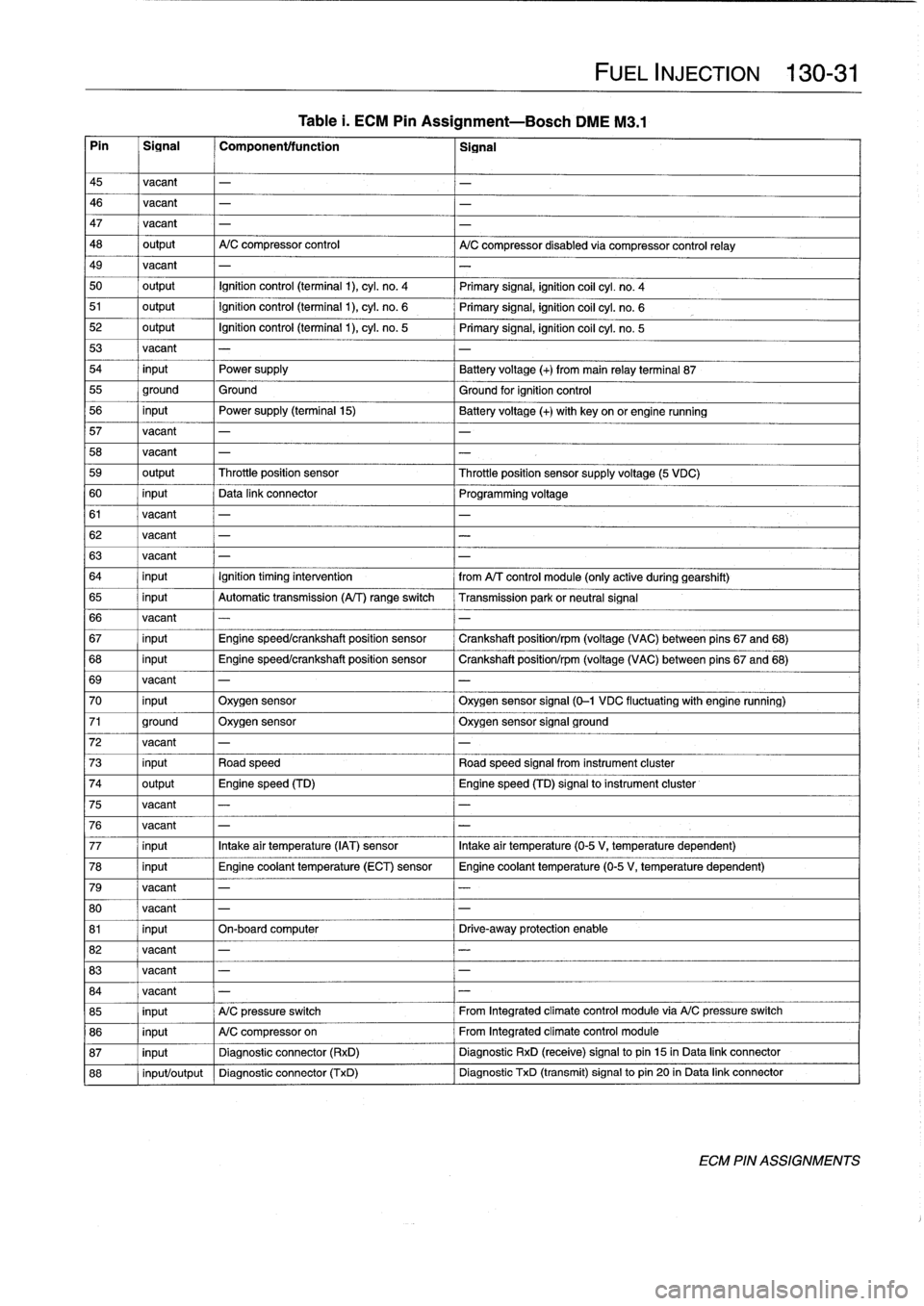
Table
i
.
ECM
Pin
Assignment-Bosch
DME
M3
.1
Pin
Signal
Component/function
2
ignal
FUEL
INJECTION
130-
3
1
45
vacant
-
46
vacant
-
-
47
vacant
-
-
48
output
A/C
compressor
control
A/C
compressor
disabled
via
compressor
control
relay
49
vacant
-
-
50
output
Ignition
control
(terminal
1),cyl
.
n
o
.
4
Primary
signal,
ignition
coil
cyl
.
n
o
.
4
51
output
Ignition
control
(terminal
1),cyl
.
n
o
.
6
Primary
signal,
ignition
coil
cyl
.
no
.
6
52
output
Ignition
control
(terminal
1),cyl
.
n
o
.
5
Primary
signal,
ignitioncoil
cyl
.
no
.
5
53
vacant
-
54
input
Power
supply
Battery
voltage
(+)
from
main
relay
terminal
87
55
ground
Ground
Ground
for
ignition
control
56
input
Power
supply
(terminal
15)
Batteryvoltage
(+)
with
key
on
or
engine
running
57
vacant
-
-
58
vacant
-
-
59
output
Throttleposition
sensor
Throttleposition
sensorsupply
voltage
(5
VDC)
60
input
Data
link
connector
Programming
voltage
61
vacant
-
-
62
vacant
-
-
63
vacant
-
-
64
input
Ignition
timing
intervention
from
A/T
control
module
(only
active
during
gearshift)
65
input
Automatic
transmission
(A/T)
range
switch
Transmission
park
or
neutral
signal
66
vacant
-
-
67
input
Engine
speed/crankshaft
position
sensor
Crankshaft
position/rpm
(voltage
(VAC)
between
pins
67
and
68)
68
input
Engine
speed/crankshaft
position
sensor
Crankshaft
position/rpm
(voltage
(VAC)
between
pins
67
and
68)
69
vacant
-
-
70
input
Oxygen
sensor
Oxygen
sensor
signal
(0-1
VDC
fluctuating
with
engine
running)
71
ground
Oxygen
sensor
Oxygen
sensor
signal
ground
72
vacant
-
-
73
input
Road
speed
Road
speed
signal
from
instrument
cluster
74
output
Engine
speed
(TD)
Engine
speed
(TD)
signalto
instrument
cluster
75
vacant
-
-
76
vacant
-
-
77
input
Intakeair
temperature
(IAT)
sensor
Intake
air
temperature
(0-5
V,
temperaturedependent)
78
input
Engine
coolant
temperature
(ECT)
sensor
Engine
coolant
temperature
(0-5V,
temperature
dependent)
79
vacant
-
-
80
vacant
-
-
81
input
On-boardcomputer
Drive-away
protection
enable
82
vacant
-
-
83
vacant
-
-
84
vacant
-
-
85
input
A/C
pressure
switch
From
Integrated
climate
control
module
via
A/C
pressure
switch
86
input
A/C
compressor
on
From
Integrated
climate
control
module
87
input
Diagnostic
connector
(RxD)
Diagnostic
RxD
(receive)signal
to
pin
15
in
Data
link
connector
88
input/output
Diagnostic
connector
(TxD)
Diagnostic
TxD
(transmit)
signal
to
pin
20
in
Data
link
connector
ECM
PIN
ASSIGNMENTS
Page 178 of 759
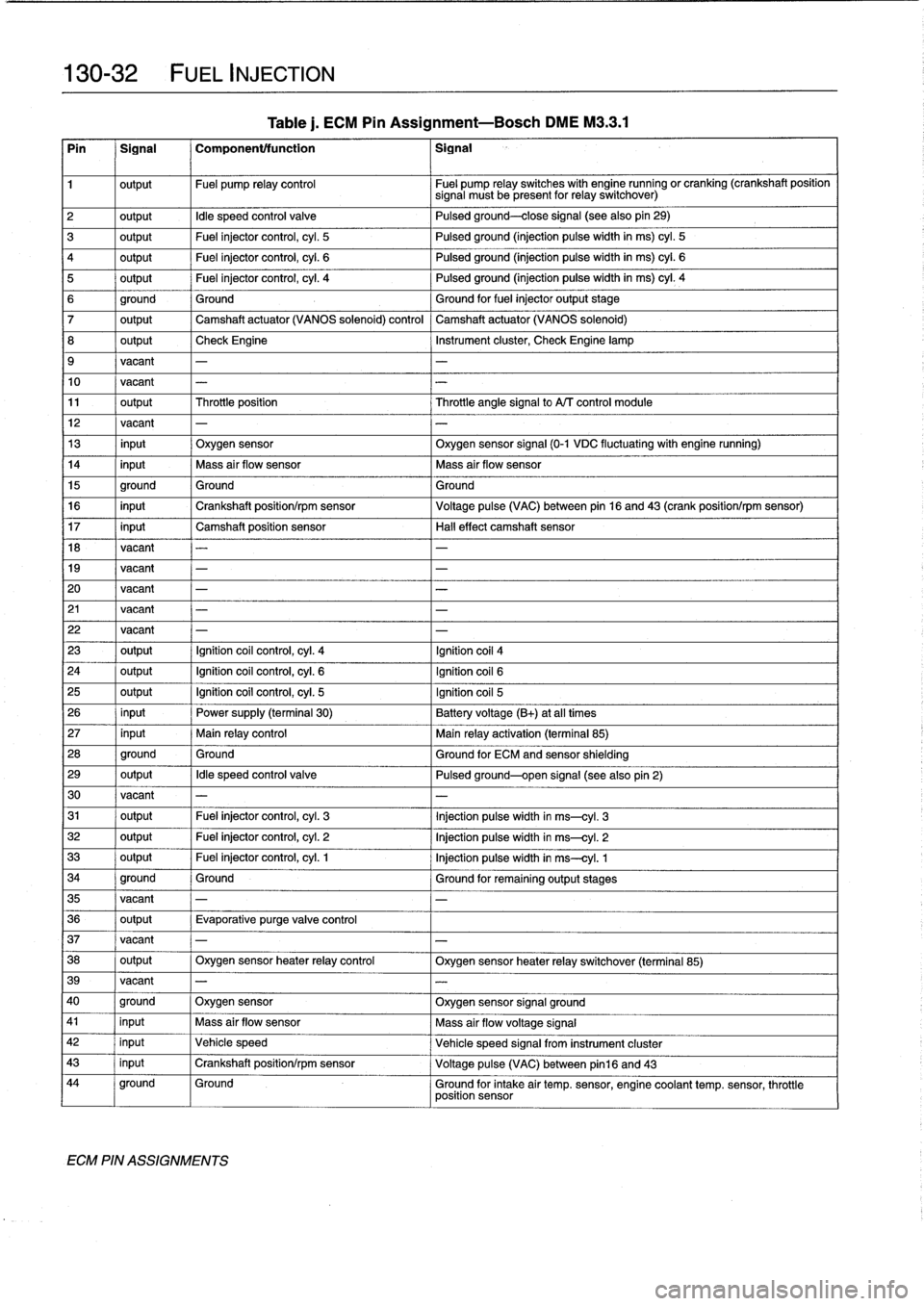
130-
3
2
FUEL
INJECTION
Pin
1
Signal
1
Component/function
1
Signal
1
output
Fuel
pump
relay
control
Fuel
pump
relay
switches
with
engine
running
or
cranking
(crankshaft
position
signal
must
be
present
for
relay
switchover)
2
output
Idle
speed
control
valve
Pulsed
ground-close
signal
(seealso
pin
29)
3
output
Fuel
ínjectorcontrol,
cyl
.
5
Pulsed
ground
(injection
pulsewidth
in
ms)
cyl
.
5
4
output
Fuel
injectorcontrol,
cyl
.
6
Pulsed
ground
(injection
pulsewidth
in
ms)
cyl
.
6
5
output
Fuel
injectorcontrol,
cyl
.
4
Pulsed
ground
(injection
pulsewidth
in
ms)
cyl
.
4
6
ground
Ground
Ground
for
fuel
injector
output
stage
7
output
Camshaft
actuator
(VANOS
solenoid)
control
Camshaft
actuator
(VANOS
solenoid)
8
output
Check
Engine
Instrument
cluster,
Check
Engine
lamp
9
vacant
-
-
10
vacant
-
-
11
output
Throttle
position
Throttle
angle
signal
to
A/T
control
module
12
vacant
-
-
13
input
Oxygen
sensor
Oxygen
sensor
signal
(0-1
VDC
fluctuating
with
engine
running)
14
input
Mass
air
flow
sensor
Mass
air
flow
sensor
15
ground
Ground
Ground
16
input
Crankshaft
position/rpm
sensor
Voltage
pulse
(VAC)
between
pin
16
and
43
(crank
position/rpm
sensor)
17
input
Camshaft
position
sensor
Halleffect
camshaft
sensor
18
vacant
-
-
19
vacant
-
-
20
vacant
-
-
21
vacant
-
-
22
vacant
-
-
23
output
Ignition
coil
control,
cyl
.
4
Ignition
coil
4
24
output
Ignition
coil
control,
cyl
.
6
Ignition
coil
6
25
output
Ignition
coil
control,
cyl
.
5
Ignition
coil
5
26
input
Power
supply
(terminal
30)
Battery
voltage(B+)
at
all
times
27
input
Main
relay
control
Main
relayactivation
(terminal
85)
28
ground
Ground
Ground
for
ECM
and
sensor
shielding
29
output
Idle
speed
control
valve
Pulsed
ground-open
signal
(seealsopin
2)
30
vacant
-
-
31
output
Fuel
injectorcontrol,
cyl
.
3
Injection
pulse
wicith
in
ms-cyl
.
3
32
output
Fuel
injectorcontrol,
cyl
.
2
Injection
pulse
wicith
in
ms-cyl
.
2
33
output
Fuel
injectorcontrol,
cyl
.
1
Injection
pulsewidth
in
ms-cyl
.
1
34
ground
Ground
Ground
for
remaining
output
stages
35
vacant
-
-
36
output
Evaporative
purge
valve
control
37
vacant
-
-
38
output
Oxygen
sensor
heater
relay
control
Oxygen
sensor
heater
relay
switchover
(terminal
85)
39
vacant
-
-
40
ground
Oxygen
sensor
Oxygen
sensor
signal
ground
41
input
Mass
air
flow
sensor
Mass
air
flow
voltage
signal
42
input
Vehicle
speed
Vehicle
speed
signal
from
instrument
cluster
43
input
Crankshaft
position/rpm
sensor
Voltage
pulse
(VAC)
between
pin16
and
43
44
ground
Ground
Ground
for
intake
air
temp
.
sensor,
engine
coolant
temp
.
sensor,
throttle
position
sensor
ECM
PIN
ASSIGNMENTS
Table
j
.
ECM
Pin
Assignment-Bosch
DME
M3
.3
.1