table BMW M3 1995 E36 Workshop Manual
[x] Cancel search | Manufacturer: BMW, Model Year: 1995, Model line: M3, Model: BMW M3 1995 E36Pages: 759
Page 243 of 759
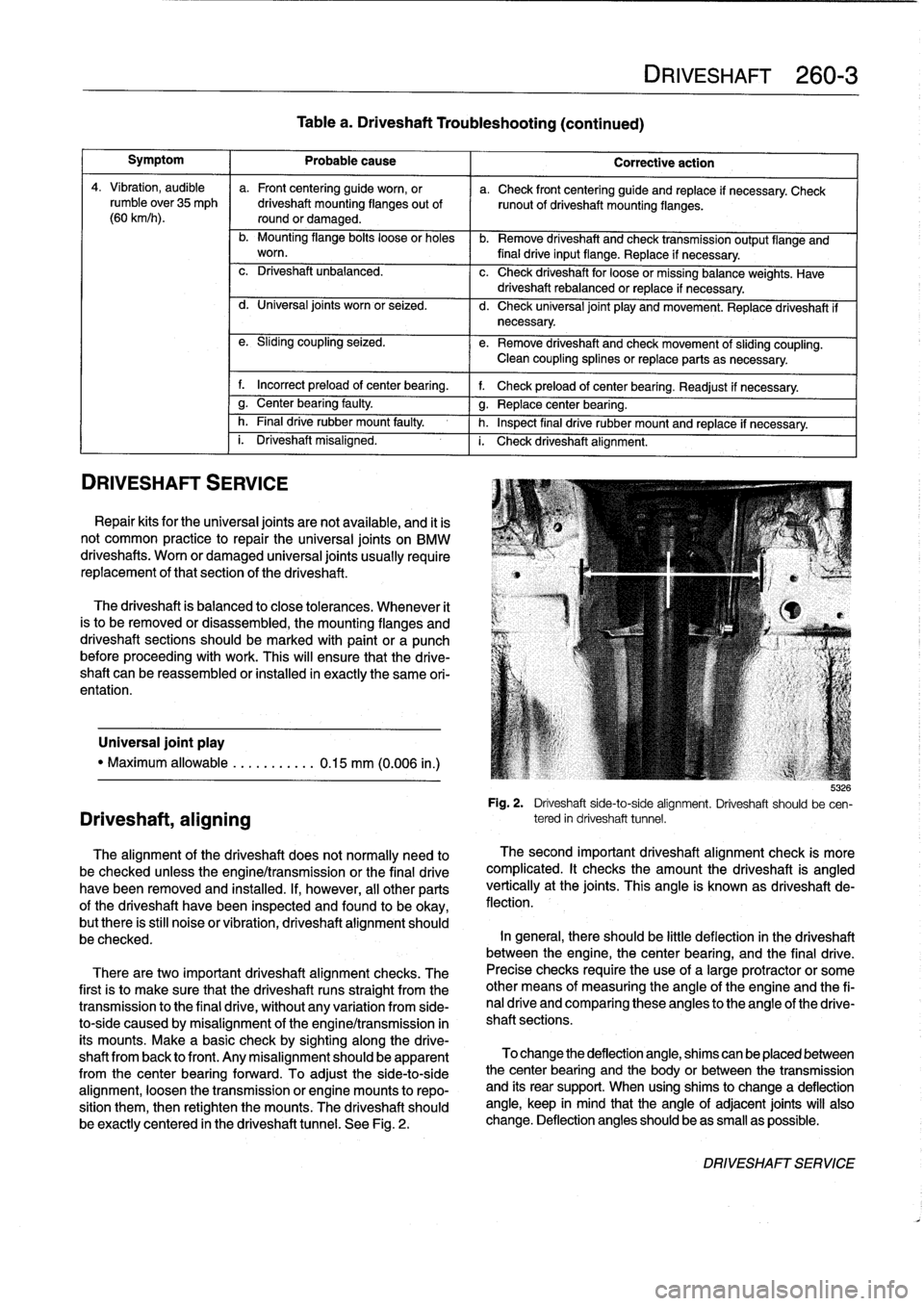
Symptom
1
Probable
cause
4
.
Vibration,
audible
a
.
Front
centering
guide
worn,
or
a
.
Check
front
centering
guide
and
replace
if
necessary
.
Check
rumble
over35
mph
driveshaft
mounting
flanges
out
of
runout
of
driveshaft
mounting
flanges
.
(60
km/h)
.
round
or
damaged
.
b
.
Mounting
flange
bolts
loose
or
holes
b
.
Remove
driveshaft
and
check
transmissionoutput
flange
and
worn
.
final
drive
input
flange
.
Replace
if
necessary
.
c
.
Driveshaft
unbalanced
.
c
.
Check
driveshaft
for
loose
or
missing
balance
weights
.
Have
driveshaft
rebalanced
or
replace
if
necessary
.
DRIVESHAFT
SERVICE
Driveshaft,
aligning
d
.
Universal
joints
worn
or
seized
.
d
.
Check
universal
joint
play
and
movement
.
Replace
driveshaft
if
necessary
.
e
.
Sliding
coupling
seized
.
e
.
Remove
driveshaft
and
check
movement
of
sliding
coupling
.
1
Clean
coupling
splines
or
replace
parts
asnecessary
.
f
.
Incorrect
preload
of
center
bearing
.
f
.
Check
preload
of
center
bearing
.
Readjust
if
necessary
.
g
.
Center
bearing
faulty
.
g
.
Replace
center
bearing
.
h
.
Final
drive
rubber
mount
faulty
h
.
Inspect
final
drive
rubber
mount
and
replace
if
necessary
.i.
Driveshaft
misaligned
.
i.
Check
driveshaft
alignment
.
Repair
kits
for
the
universal
joints
are
not
available,
and
it
is
not
common
practice
to
repair
the
universal
joints
on
BMW
driveshafts
.
Worn
or
damaged
universal
joints
usually
require
replacement
of
that
section
of
the
driveshaft
.
The
driveshaft
is
balanced
to
cose
tolerances
.
Whenever
it
is
to
be
removed
or
disassembied,
the
mounting
flanges
and
driveshaft
sections
should
bemarked
with
paint
or
a
punch
before
proceeding
with
work
.
This
will
ensure
that
the
drive-
shaft
can
be
reassembled
or
installed
in
exactlythe
same
ori-
entation
.
Universal
joint
play
"
Maximum
allowable
...........
0.15
mm
(0.006
in
.)
The
alignment
of
the
driveshaft
does
not
normally
need
to
be
checked
unless
the
engine/transmission
orthe
final
drive
havebeen
removed
and
installed
.
If,
however,
all
other
parts
of
the
driveshaft
havebeen
inspected
and
found
to
be
okay,
butthere
is
still
noise
or
vibration,
driveshaft
alignment
should
be
checked
.
There
aretwo
important
driveshaft
alignment
checks
.
The
first
is
to
make
sure
that
the
driveshaft
runs
straight
from
the
transmission
to
the
final
drive
;
without
any
variation
from
side-
to-side
caused
by
misalignment
ofthe
engine/transmission
in
its
mounts
.
Make
a
basic
check
by
sighting
along
the
drive-
shaft
from
back
lo
front
.
Any
misalignmentshould
be
apparent
from
the
center
bearingforward
.
To
adjustthe
side-to-side
alignment,
loosen
the
transmission
or
engine
mounts
to
repo-
sition
them,
then
retighten
the
mounts
:
The
driveshaft
should
be
exactly
centered
in
the
driveshaft
tunnel
.
See
Fig
.
2
.
Table
a
.
Driveshaft
Troubleshooting
(continued)
DRIVESHAFT
260-3
Corrective
action
b
:izó
Fig
.
2
.
Driveshaft
side-to-side
alignment
.
Driveshaft
should
be
cen-
tered
in
driveshaft
tunnel
.
The
second
important
driveshaft
alignment
check
is
more
complicated
.
It
checks
the
amount
the
driveshaft
is
angled
vertically
at
the
joints
.
This
angle
is
known
as
driveshaft
de-
flection
.
In
general,
there
should
be
little
deflection
in
the
driveshaft
between
the
engine,
thecenter
bearing,
and
the
final
drive
.
Precise
checks
require
theuse
of
a
large
protractor
or
some
other
means
of
measuring
the
angle
of
the
engine
and
the
fi-
nal
drive
and
comparing
these
angles
to
the
angle
of
the
drive-
shaft
sections
.
To
change
the
deflection
angle,
shims
can
be
placed
between
the
center
bearing
and
the
body
or
between
the
transmission
and
íts
rear
support
.
When
using
shims
to
change
a
deflection
angle,
keep
in
mind
that
the
angle
of
adjacent
joints
will
also
change
.
Deflection
anglesshould
beas
small
as
possible
.
DRIVESHAFTSERVICE
Page 249 of 759
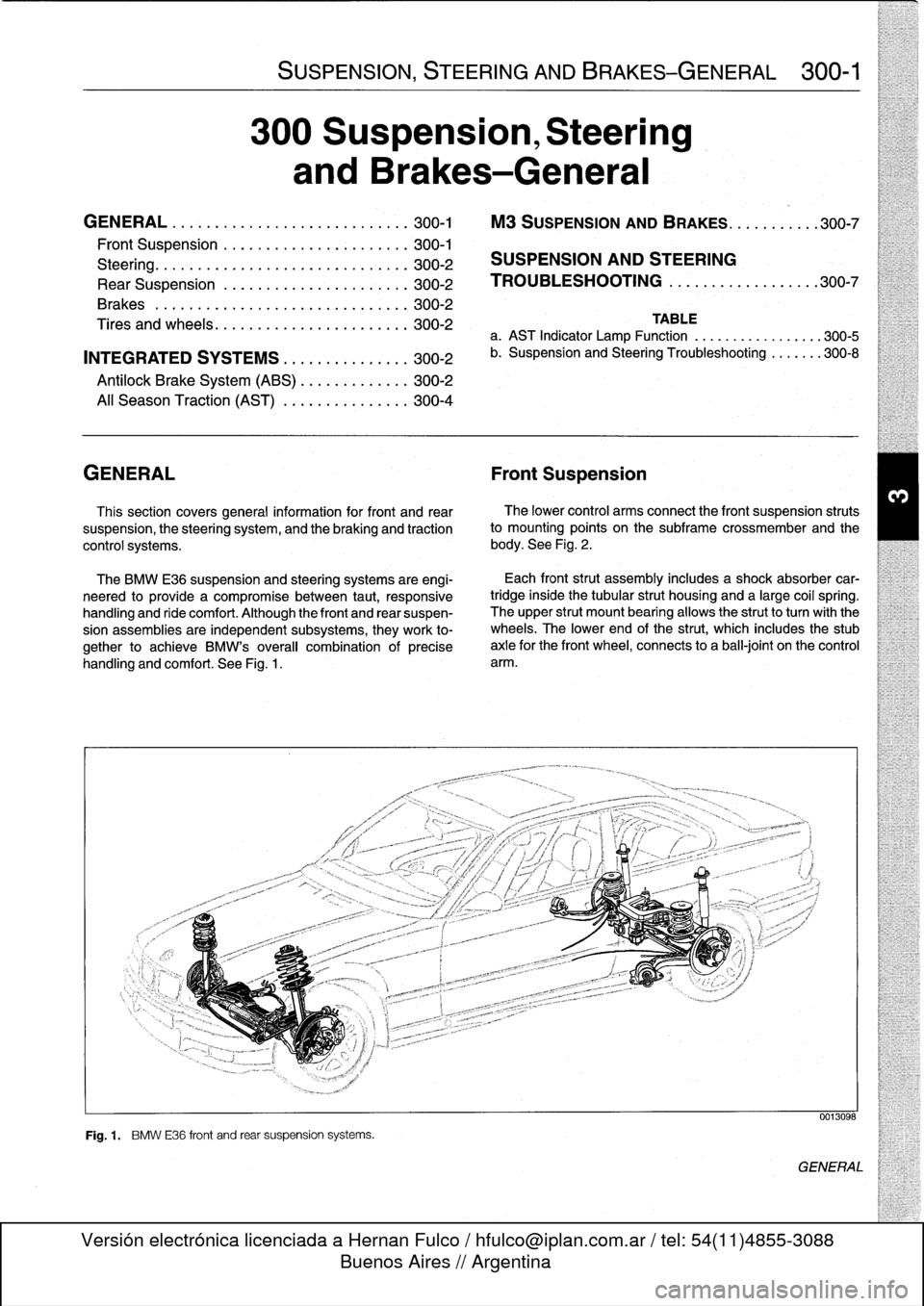
SUSPENSION,
STEERING
ANDBRAKES-GENERAL
300-1
300
Suspension,
Steering
and
Brakes-General
GENERAL
.....
.
....
.
.....
.
.
.
........
.300-1
M3
SUSPENSION
AND
BRAKES
.......
.
...
300-7
Front
Suspension
..........
.
.
.
...
.
.....
300-1
Steering
...
.
.
.
.
.
....
.
.
.
...
.
.
.
...
.
...
.
.
300-2
SUSPENSION
AND
STEERING
Rear
Suspension
....
.
.
.
...
.
.
.
...
.
.....
300-2
TROUBLESHOOTING
..
.
.
.
.............
300-7
Brakes
.
.
.
.
.
.
.
.
....
.
...........
.
.
.
.
.
.
300-2
Tires
and
wheeis
.
................
.
.
.
.
.
.
300-2
TABLE
a
.
AST
Indicator
Lamp
Function
..
..
.
..
.
.........
300-5
INTEGRATED
SYSTEMS
.........
.
.
.
.
.
.
300-2
b
.
Suspension
and
Steering
Troubleshooting
......
.300-8
Antilock
Brake
System
(ABS)
.......
.
.
.
.
.
.
300-2
Al¡
Season
Traction
(AST)
.........
.
.
.
.
.
.
300-4
GENERAL
Front
Suspension
This
section
covers
general
information
for
front
and
rear
The
lower
control
arms
connect
the
front
suspension
struts
suspension,
the
steering
system,
and
the
brakíng
and
traction
to
mounting
points
on
the
subframe
crossmember
and
the
control
systems
.
body
.
See
Fig
.
2
.
The
BMW
E36
suspension
and
steering
systems
are
engi-
neered
to
provide
a
compromise
between
taut,
responsive
handling
and
ride
comfort
.
Although
the
front
and
rear
suspen-
sion
assemblies
are
independent
subsystems,
they
work
to-
gether
to
achieve
BMW's
overall
combination
of
precise
handling
and
comfort
.
See
Fig
.
1
.
Fig
.
1
.
BMW
E36
front
and
rear
suspension
systems
.
Each
front
strut
assembly
includes
a
shock
absorber
car-
tridgeinside
the
tubular
strut
housing
and
a
large
coil
spring
.
The
upper
strut
mount
bearing
allows
the
strutto
turnwith
the
wheels
.
The
lower
end
of
the
strut,
which
includes
the
stub
axle
for
the
front
wheel,
connects
to
a
ball-joint
on
the
control
arm
.
0013098
GENERAL
Page 253 of 759

NOTE-
The
traction
control
system
referred
to
as
AST
(all
sea-
son
traction)
may
also
be
referred
to
as
ASC
(Automat-
ic
Stability
Control)
and
ASC+T
(Automatic
Stability
Control+Traction)
.
The
AST
system
improves
traction
by
electronically
apply-
ing
the
rear
brakes
when
therear
drive
wheels
are
spinning
at
a
faster
rate
than
the
front
wheels
.
The
combined
ABS/AST
control
module,
operating
through
the
ABS
hydraulic
control
unit,
modulates
braking
force
at
therear
wheels
.
In
addition,
AST
uses
retarded
ignition
timing
and
an
auxil-iary
engine
throttle
plate
to
reduceengine
torque
and
maintain
vehicle
stability
.
The
auxiliary
throttle
plate
is
held
open
by
spring
pressure
.
The
AST
system
actívates
the
auxiliary
throttie
position
motor
(ADS)
to
cose
the
AST
throttle
as
needed
.
This
reduces
the
volume
of
engine
intake
air
.
Due
to
the
throttle
closing
very
rapidly
during
AST
operationthe
driver
cannot
increase
theengine
power
output
regardless
of
how
far
theaccelerator
pedal
is
pushed
to
the
floor
.
The
auxiliary
throttle
plate
is
placed
ahead
of
the
conven-
tional
throttle
plate
in
the
throttle
body
.
Traction
control
also
comes
into
operationduringdecelera-
tion
.
Decelerating
on
snowy
or
icy
road
surfaces
can
lead
to
rear
wheel
slip
.
If
a
rear
wheel
startsto
drag
or
lock
up
when
the
throttle
is
closed
rapidly
orduringdownshifting,the
AST
system
can
limit
the
problem
by
advancing
the
ignition
timing
.
A
switch
on
the
center
console
is
used
to
togglethe
AST
on
or
off
.
The
AST
system
is
designed
to
be
maintenance
free
.
There
are
no
adjustments
that
can
be
made
.
Repair
and
trouble-
shooting
of
the
AST
system
requires
special
test
equipment
andknowledgeand
should
be
performed
only
by
an
autho-
rized
BMW
dealer
.
Table
a
lists
theconditions
indicated
by
the
AST
indicator
light
in
the
instrument
cluster
SUSPENSION,
STEERING
AND
BRAKES-GENERAL
300-5
Tablea
.
AST
Indicator
Lamp
Function
Indicator
lamp
1
Condition
1
Comment
Light
on
Normal
AST
start-
Automatic
AST
up
self-test
Light
off
AST
monitoring
Automatic
AST
op-
mode
eration
Press
AST
button,
AST
off
(disabled)
Rocking
the
car
tolight
comes
on
getout
of
snow
or
other
loose
surface
Driving
with
snow
chains
Press
AST
button
:
AST
monitoring
Automatic
AST
op-
light
goes
out
I
mode
eration
Light
flashes
AST
active
mode
I
Normal
AST
oper-
ation
as
it
controls
wheel
speed
Light
stays
on
af-
Defect
in
AST
Consult
BMW
ter
start
up
or
dealer
for
diagno-
comes
on
while
sis/repair
driving
(Vehicle
operation
remains
normal)
WARNING
-
Even
a
car
with
AST
is
subject
to
the
normal
physi-
cal
laws
.
Avoid
excessive
speeds
for
the
road
con-
ditions
encountered
.
CAUTION-
"
If
the
tires
on
the
carare
of
different
makes,
the
AST
system
may
over-react
.
Only
fit
tires
of
the
same
make
and
tread
pattem,
"In
adverse
conditions,
such
as
trying
to
rock
the
car
outof
deep
snow
or
another
soft
surface,
or
when
snow
chainsare
fitted,
it
is
advisable
to
switch
off
AST
and
allow
the
cars
driveline
to
op-
erate
conventionally
.
INTEGRATED
SYSTEMS
Page 255 of 759
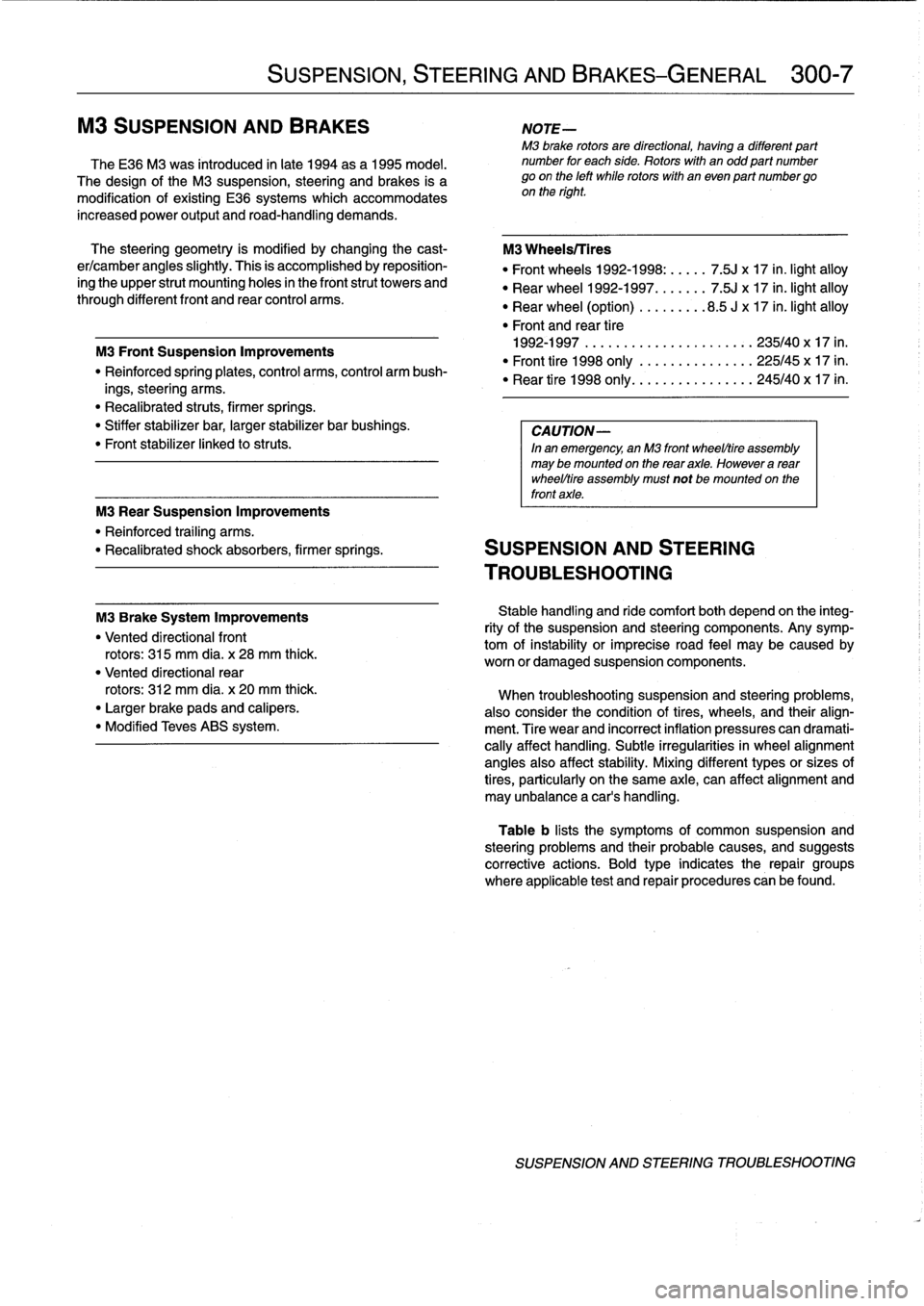
increased
power
output
and
road-handling
demands
.
The
steering
geometry
is
modified
by
changing
the
cast-
er/camber
angles
slightly
.
This
is
accomplishedby
reposition-
ing
the
upper
strut
mounting
holes
in
the
frontstrut
towers
and
through
different
front
and
rear
control
arms
.
M3
Brake
System
Improvements
"
Vented
directionalfront
rotors
:
315
mm
dia
.
x
28
mm
thick
.
"
Vented
directional
rear
rotors
:
312
mm
dia
.
x20
mm
thick
.
"
Larger
brake
pads
and
calipers
.
"
Modified
Teves
ABS
system
.
SUSPENSION,
STEERING
AND
BRAKES-GENERAL
300-
7
M3
SUSPENSION
AND
BRAKES
NOTE-
M3
brake
rotors
are
directional,
having
a
different
part
TheE36
M3
was
introduced
in
late
1994
as
a
1995
model
.
number
for
each
side
.
Rotors
with
an
odd
part
number
The
design
of
the
M3
suspension,
steering
and
brakes
is
a
go
on
the
left
while
rotors
with
en
even
part
numbergo
modification
of
existing
E36
systems
which
accommodates
on
the
right
.
M3
Front
SuspensionImprovements
"
Reinforced
spring
plates,control
arms,
control
arm
bush-
ings,
steering
arms
.
"
Recalibrated
struts,
firmer
springs
.
"
Stiffer
stabilizerbar,
larger
stabilizer
bar
bushings
.
"
Front
stabilizer
linked
to
struts
.
M3
Wheels/Tires
"
Front
wheels
1992-1998
:.....
7
.5J
x
17
in
.
light
alloy
"
Rear
wheel
1992-1997
.......
7
.5J
x17
in
.
light
alloy
"
Rear
wheel
(option)
........
.8
.5
Jx17
in
.
light
alloy
"
Front
and
rear
tire
1992-1997
.............
.
.
.
...
...
235/40
x
17
in
.
"
Front
tire
1998
only
......
...
.
.
.
...
225/45
x
17
in
.
"
Rear
tire
1998
only
.......
.
.
.
...
...
245/40
x
17
in
.
CAUTION-
In
en
emergency,
an
M3
front
wheel/tire
assembly
may
be
mounted
on
the
rearaxle
.
However
a
rear
wheel/tire
assemblymust
not
be
mounted
on
the
front
axle
.
M3
RearSuspensionImprovements
"
Reinforced
trailing
arms
.
"
Recalibrated
shock
absorbers,
firmer
springs
.
SUSPENSION
AND
STEERING
TROUBLESHOOTING
Stable
handling
and
ride
comfort
both
depend
on
the
integ-
rity
of
the
suspension
and
steering
components
.
Any
symp-
tom
of
instability
or
imprecise
road
feel
may
be
caused
by
worn
or
damaged
suspension
components
.
When
troubleshooting
suspension
and
steering
problems,
also
consider
the
condition
of
tires,
wheels,
and
their
align-
ment
.
Tire
wear
and
incorrect
inflation
pressures
can
dramati-
cally
affect
handling
.
Subtie
irregularities
in
wheel
alignment
angles
also
affect
stabílity
.
Mixing
different
types
or
sizes
of
tires,
particularly
on
the
same
axle,
can
affect
alignment
and
may
unbalancea
car's
handling
.
Table
b
lists
the
symptoms
of
common
suspension
and
steering
problems
and
their
probable
causes,
and
suggests
corrective
actions
.
Bold
type
indicates
the
repair
groups
where
applicable
test
and
repair
procedures
can
befound
.
SUSPENSION
AND
STEERING
TROUBLESHOOTING
Page 256 of 759
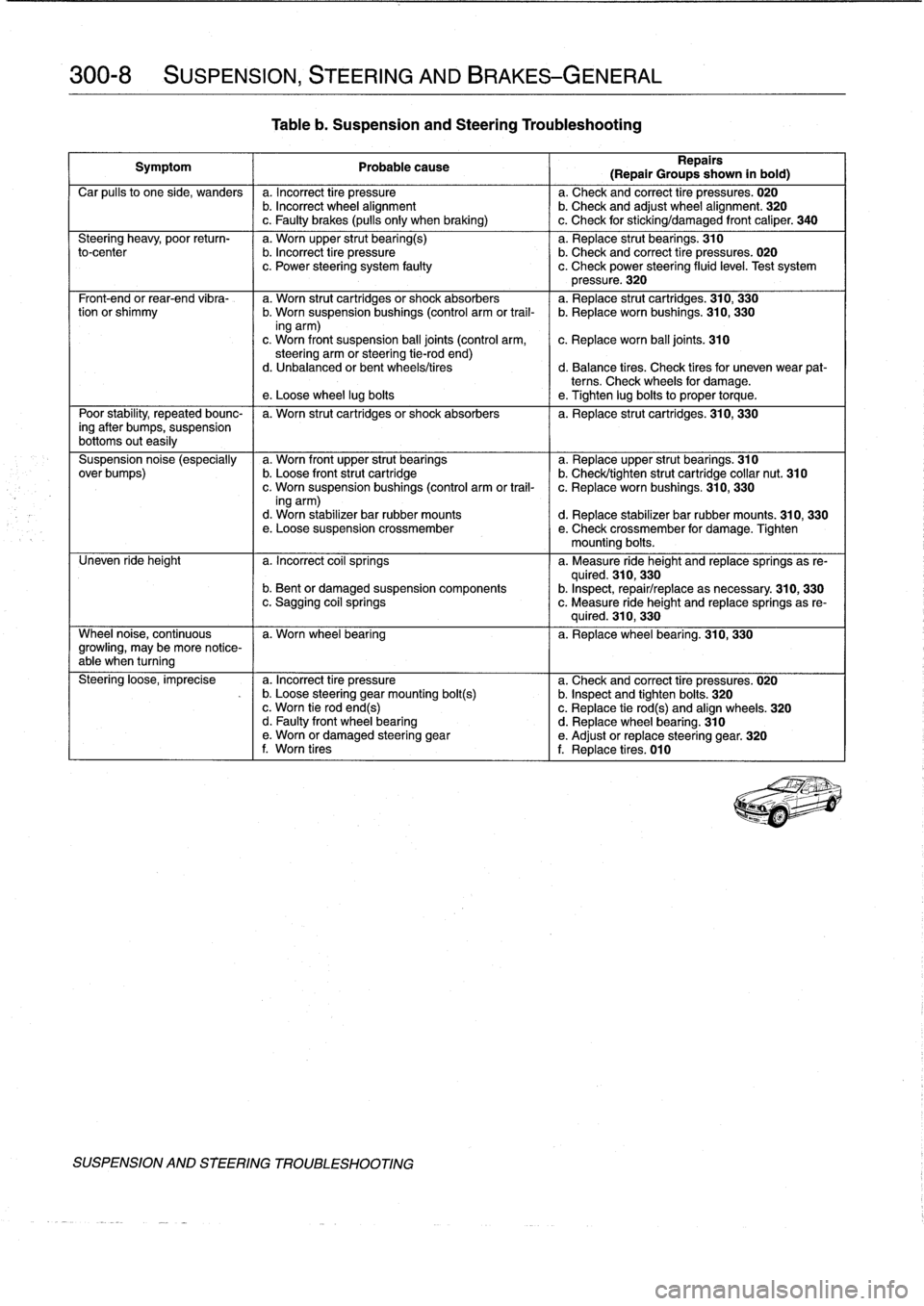
300-8
SUSPENSION,
STEERING
AND
BRAKES-GENERAL
Tableb
.
Suspension
and
Steering
Troubleshooting
Symptom
1
Probable
cause
Repairs
(Repair
Groups
shown
in
bold)
Car
pulís
to
one
side,
wanders
a
.
Incorrect
tire
pressure
a
.
Check
and
correct
tire
pressures
.
020
b
.
Incorrect
wheel
alignment
b
.
Check
and
adjust
wheel
alignment
.
320
c
.
Faulty
brakes
(pulls
only
when
braking)
I
c
.
Check
for
sticking/damaged
front
caliper
.
340
Steering
heavy,
poor
return-
a
.
Worn
upper
strut
bearing(s)
a
.
Replace
strut
bearings
.
310
to-center
b
.
Incorrect
tire
pressure
b
.
Check
and
correct
tire
pressures
.
020
c
.
Power
steering
system
faulty
c
.
Check
power
steering
fluid
level
.
Test
system
pressure
.
320
Front-end
or
rear-end
vibra-
a
.
Worn
strut
cartridgesor
shock
absorbers
a
.
Replace
strut
cartridges
.
310,
330
tion
or
shimmy
b
.
Worn
suspension
bushings
(control
arm
or
trail-
b
.
Replace
worn
bushings
.
310,
330
ing
arm)
c
.
Worn
front
suspension
ball
joints
(control
arm,
c
.
Replace
worn
ball
joints
.
310
steering
arm
orsteering
tie-rod
end)d
.
Unbalanced
or
bent
wheels/tires
d
.
Balance
tires
.
Check
tiresfor
uneven
wear
pat-
terns
.
Check
wheels
for
damage
.
e
.
Loose
wheel
lug
boits
e
.
Tighten
lug
boits
to
proper
torque
.
Poor
stability,
repeated
bounc-
I
a
.
Worn
strut
cartridgesor
shock
absorbers
I
a
.
Replace
strut
cartridges
.
310,
330
ing
after
bumps,
suspension
bottoms
outeasily
Suspension
noise
(especially
a
.
Worn
front
upper
strut
bearings
a
.
Replaceupper
strut
bearings
.
310
over
bumps)
b
.
Loose
front
strut
cartridge
b
.
Check/tighten
strut
cartridge
collar
nut
.
310
c
.
Worn
suspensionbushings
(control
arm
or
trail-
c
.
Replace
worn
bushings
.
310,
330
ing
arm)d
.
Worn
stabilizer
bar
rubber
mounts
d
.
Replace
stabilizer
bar
rubber
mounts
.
310,
330
e
.
Loose
suspension
crossmember
e
.
Check
crossmember
for
damage
.
Tighten
mounting
boits
.
Uneven
ride
height
a
.
Incorrect
coil
springs
a
.
Measure
ride
height
and
replacesprings
as
re-
quired
.
310,
330
b
.
Bent
or
damaged
suspension
components
b
.
Inspect,
repair/replace
asnecessary
.
310,
330
c
.
Sagging
coil
springs
c
.
Measure
ride
height
and
replace
springs
as
re-
quired
.
310,
330
Wheel
noise,
continuous
I
a
.
Worn
wheel
bearing
I
a
.
Replacewheel
bearing
.
310,
330
growling,
may
be
more
notíce-
able
when
turning
Steering
loose,
imprecise
a
.
Incorrect
tire
pressure
a
.
Check
and
correct
tire
pressures
.
020
-
b
.
Loose
steering
gearmounting
bolt(s)
b
.
Inspect
and
tighten
boits
.
320
c
.
Worn
tie
rodend(s)
c
.
Replace
tie
rod(s)
and
align
wheels
.
320
d
.
Faulty
front
wheel
bearing
d
.
Replace
wheel
bearing
.
310
e
.
Worn
or
damaged
steering
gear
e
.
Adjust
or
replace
steering
gear
.
320
f
.
Worn
tires
f
.
Replace
tires
.
010
SUSPENSION
AND
STEERING
TROUBLESHOOTING
Page 257 of 759
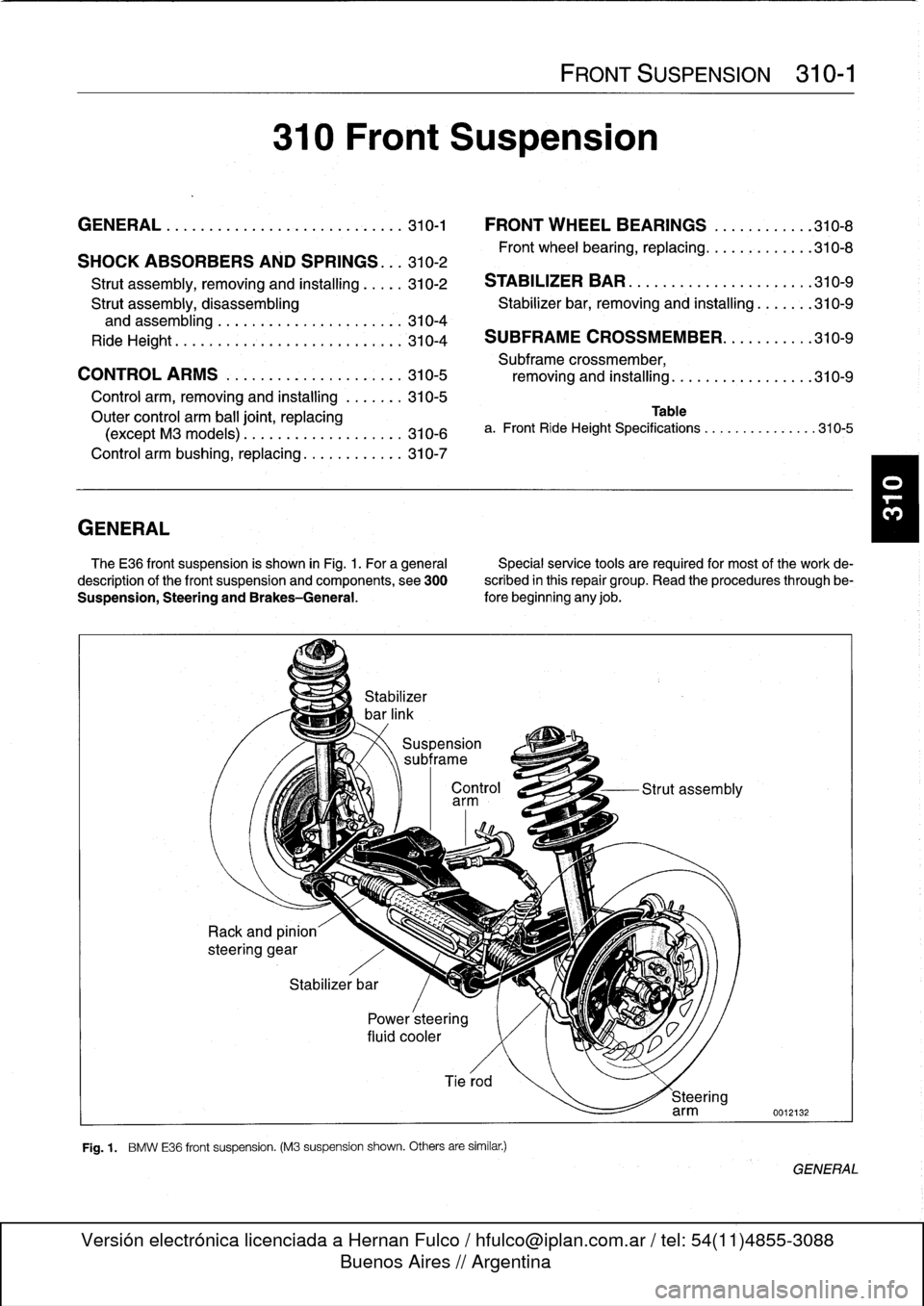
GENERAL
310
Front
Suspension
GENERAL
..
.
.
.
.
.
.
.
.
.
.......
.
........
.
310-1
FRONT
WHEEL
BEARINGS
..
.
.
.
.......
310-8
SHOCK
ABSORBERS
AND
SPRINGS
..
.
310-2
Front
wheel
bearing,
replacing
...
.
.
.
.
.
.
.
...
310-8
Strut
assembly,
removing
and
installing
.....
310-2
STABILIZER
BAR
..........
.
.
.
.
.
.
.
.
.
.
.
.
310-9
Strut
assembly,
disassembling
Stabilizerbar,
removing
and
installing
.
.
.
.
...
310-9
and
assembling
.
.
.
...
.
.....
.
.........
310-4
Ride
Height
.
.
.
.
.
.
.
.
.
.
.
.
.....
.
........
.
310-4
SUBFRAME
CROSSMEMBER
.
.
.
.
.
.
.
.
.
.
.
310-9
Subframe
crossmember,
CONTROL
ARMS
.
.
...
.
.
.
.
.
.
.
...
.
.....
310-5
removing
and
installing
.....
.
.
.
.
.
.
.
.
.
...
310-9
Control
arm,
removing
and
installing
....
..
310-5
Outer
control
arm
ball
joint,
replacing
Table
exce
t
M3
models
310-6
a
.
Front
Ride
Height
Specifications
..
.
.....
..
.
..
..
310-5
Control
arm
bushing,
replacing
.
.
.
...
.
.....
310-7
The
E36
front
suspension
is
shown
in
Fig
.
1
.
For
a
general
Specialservice
tools
arerequired
for
most
of
the
work
de-
description
of
the
front
suspension
and
components,
see
300
scribed
in
this
repair
group
.
Read
the
procedures
through
be-
Suspension,
Steering
and
Brakes-General
.
fore
beginning
any
job
.
Stabilizer
bar
Power
steering
fluid
cooler
Control
Strut
assembly
arm
Tierod
Fig
.
1
.
BMW
E36
front
suspension
.
(M3
suspension
shown
.
Others
are
similar
.)
FRONT
SUSPENSION
310-1
Steering
arm
0012132
GENERAL
Page 260 of 759
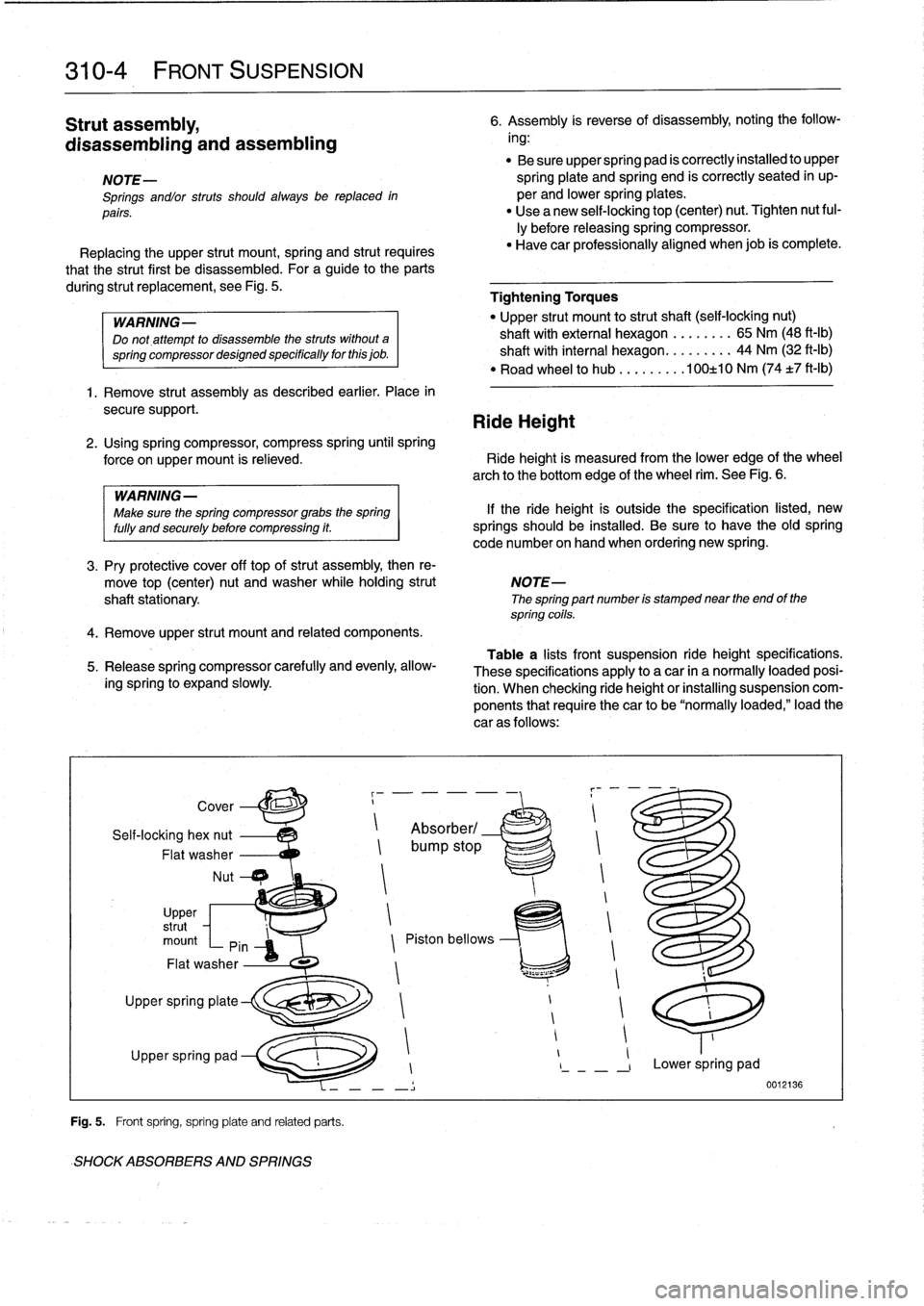
310-
4
FRONT
SUSPENSION
Strut
assembly,
disassembling
and
assembling
-
Be
sure
upper
spring
pad
is
correctly
installed
to
upper
NOTE-
spring
plate
and
spring
end
is
correctly
seated
in
up-
Springs
andlor
struts
should
always
be
replaced
in
per
and
lower
spring
plates
.
pairs
.
"
Use
a
new
self-locking
top
(center)
nut
.
Tighten
nut
fui-
¡y
before
releasing
spring
compressor
.
Replacing
the
upper
strut
mount,
spring
and
strut
requires
"
Have
car
professionally
aligned
when
job
is
complete
.
that
the
strut
first
bedisassembled
.
For
a
guide
to
the
parts
during
strut
replacement,
see
Fig
.
5
.
Tightening
Torques
WARNING-
"
Upper
strut
mount
to
strut
shaft
(seif-locking
nut)
Do
not,attempt
to
disassemble
thestruts
without
a
shaft
with
external
hexagon
......
..
65
Nm
(48
ft-1b)
springcompressordesignedspecificallyforthisjob
.
shaft
with
interna¡
hexagon
.......
..
44
Nm
(32
ft-Ib)
"
Road
wheel
to
hub
........
.100±10
Nm
(74
±7
ft-lb)
1
.
Remove
strut
assembly
as
described
earlier
.
Place
in
secure
support
.
Ride
Height
2
.
Using
spring
compressor,
compress
spring
until
spring
force
onupper
mount
is
relieved
.
Ride
height
is
measured
from
the
lower
edge
of
the
wheel
arch
to
the
bottom
edge
of
the
wheel
rim
.
See
Fig
.
6
.
WARNING
-
Make
sure
the
spring
compressor
grabs
the
spring
lf
the
ride
height
is
outside
the
specification
listed,
new
fully
and
securely
before
compressing
it
.
springs
should
be
installed
.
Be
sure
to
have
theold
spring
code
number
on
hand
when
ordering
new
spring
.
3
.
Pry
protective
cover
off
top
ofstrut
assembly,
then
re-
move
top
(center)
nut
andwasher
whileholding
strut
NOTE-
shaftstationary
The
spring
part
number
is
stamped
near
the
end
of
the
spring
cofls
.
4
.
Remove
upper
strut
mount
and
related
components
.
5
.
Release
spring
compressor
carefully
and
evenly,
allow-
ing
spring
lo
expand
slowly
1
Self-locking
hex
nut
Absorber/
Flat
washer
bump
stop
Nut
Cover
Upper
~
strut
mount
Pin
Z
Piston
bellows
Flat
washer
r
i
t1
~
1
Upper
spring
plate
1
1
1
Upper
spring
pad
I
1
-
,
Lower
spring
pad
-
Í
0012136
Fig
.
5
.
Front
spring,
spring
plate
and
related
parts
.
SHOCKABSORBERS
AND
SPRINGS
6
.
Assembly
is
reverse
of
disassembly,
noting
the
follow-
ing
:
Table
a
lists
front
suspension
ride
height
specifications
.
These
specifications
apply
to
a
car
in
a
normally
loaded
posi-
tion
.
When
checking
ride
height
or
installing
suspension
com-
ponents
that
require
thecar
to
be
"normally
loaded,"load
the
car
as
follows
:
Page 261 of 759
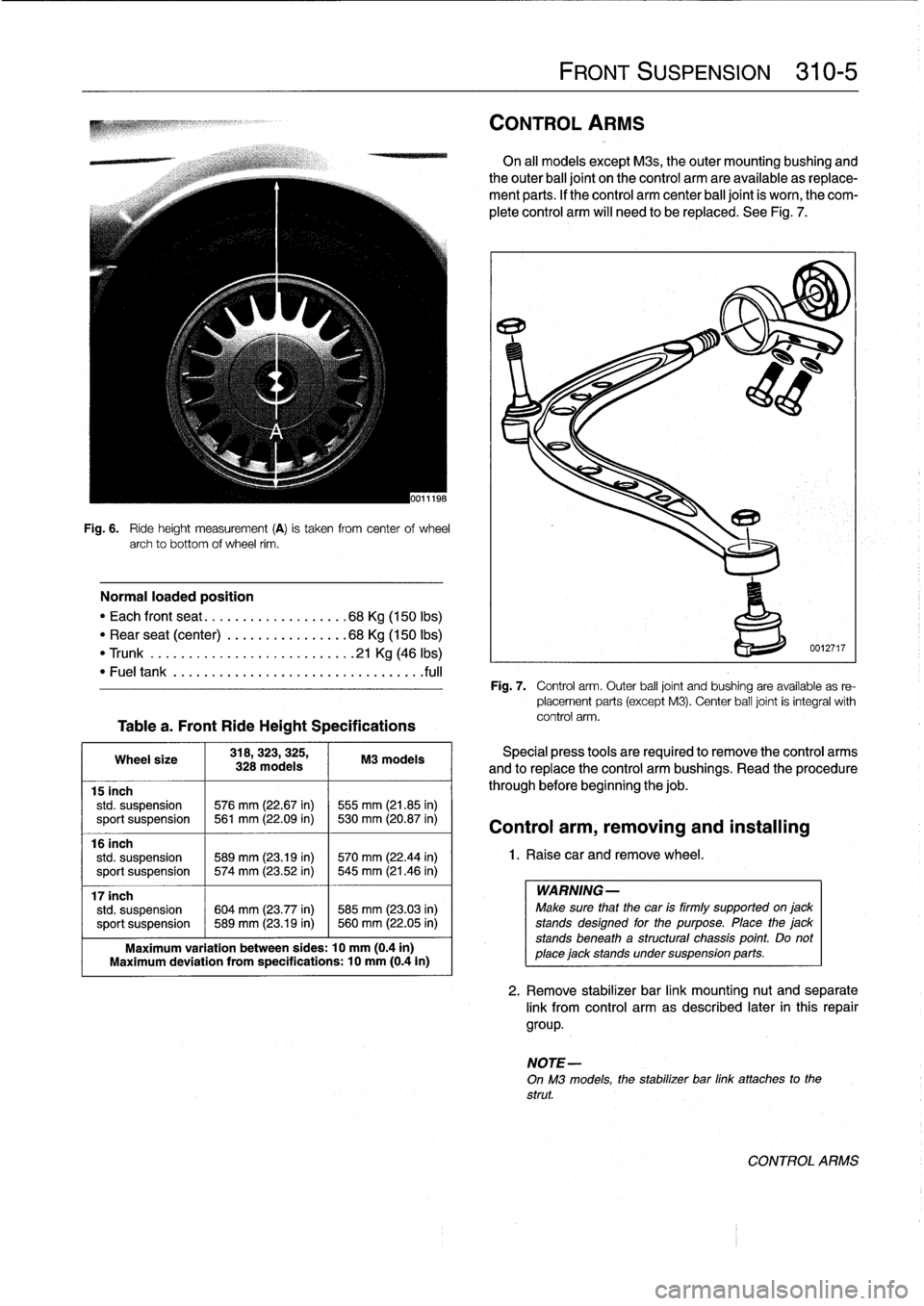
Fig
.
6
.
Ride
height
measurement
(A)
is
taken
from
centerof
wheel
archto
bottom
of
wheel
rim
.
Normal
loaded
position
"
Each
front
seat
...
...
.
..
..........
68Kg
(150
Ibs)
"
Rear
seat
(center)
...
.
.
...........
68Kg
(150
Ibs)
"
Trunk
..........
...
.
.
...........
.21
Kg
(46
lbs)
"
Fuel
tank
...
.
..
....
.
.
....................
.fuf
Tablea
.
Front
RideHeight
Specifications
318,323,325,
Wheel
size
M3
models
328
models
15
inch
std
.
suspension
576
mm
(22.67
in)
1555
mm
(21.85
in)
sport
suspension
~
561
mm
(22.09
in)
530
mm
(20
.87
in)
16
inch
std
.
suspension
589
mm
(23.19
in)
1570
mm
(22
.44
in)
sport
suspensíon
~
574
mm
(23.52
in)
545
mm
(21.46
in)
17
inch
std
.
suspension
604
mm
(23.77
in)
585
mm
(23
.03
in)
sport
suspension
~
589
mm
(23.19
in)
~
560
mm
(22
.05
in)
Maximum
variation
between
sides
:
10
mm
(0.4in)
Maximum
deviation
from
specifications
:
10
mm
(0
.4in)
FRONT
SUSPENSION
310-
5
CONTROL
ARMS
On
al¡
models
except
Mas,
theouter
mounting
bushing
and
theouter
ball
joint
on
the
control
arm
are
available
as
replace-
ment
parts
.
If
the
control
arm
center
ball
joint
is
worn,
the
com-
plete
control
arm
will
need
to
be
replaced
.
See
Fig
.
7
.
Fig
.
7
.
Control
arm
.
Outer
ball
joint
and
bushing
are
available
as
re-
placement
parts
(except
M3)
.
Center
ball
joint
is
integral
with
control
arm
.
Special
press
tools
are
requiredto
remove
the
control
arms
and
to
replace
the
control
arm
bushings
.
Read
the
procedure
through
before
beginning
the
job
.
Control
arm,
removing
and
installing
1
.
Raise
car
and
remove
wheel
.
WARNING-
Make
sure
that
thecar
is
firmly
supportedon
jack
standsdesigned
for
the
purpose
.
Place
the
jack
stands
beneath
a
structural
chassis
point
.
Do
not
place
jack
stands
undersuspension
parts
.
2
.
Remove
stabilizer
bar
link
mounting
nut
and
separate
link
from
control
arm
as
described
later
in
this
repair
group
.
NOTE-
On
M3
models,
the
stabilizer
bar
link
attaches
to
the
strut
.
CONTROL
ARMS
Page 262 of 759
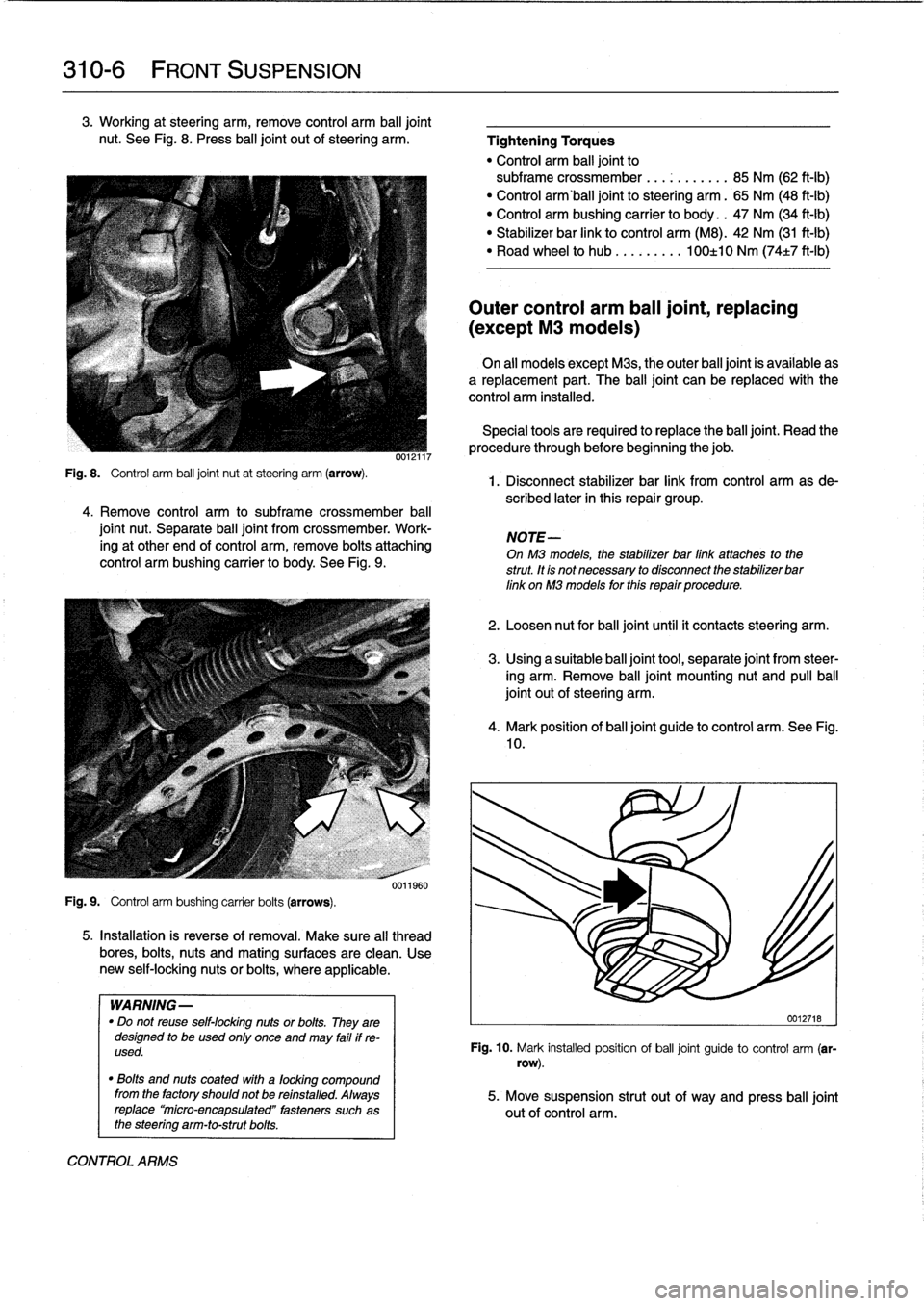
310-
6
FRONT
SUSPENSION
3
.
Working
at
steering
arm,
remove
control
arm
balljoint
nut
.
See
Fig
.
8
.
Press
ball
joint
out
ofsteering
arm
.
Fig
.
8
.
Control
arm
ball
joint
nut
at
steering
arm
(arrow)
.
4
.
Remove
control
arm
to
subframe
crossmember
ball
joint
nut
.
Separate
ball
joint
from
crossmember
.
Work-
ing
at
other
end
of
control
arm,
remove
bolts
attaching
control
arm
bushing
carrier
to
body
.
See
Fig
.
9
.
Fig
.
9
.
Control
arm
bushing
carrier
bolts
(arrows)
.
0012117
0011960
5
.
Installation
is
reverse
of
removal
.
Make
sure
al¡
thread
bores,
bolts,
nuts
and
mating
surfaces
are
clean
.
Use
new
self-locking
nutsor
bolts,
where
applicable
.
WARNING-
"
Do
not
reuse
self-locking
nuts
or
bolts
.
They
are
designed
to
be
used
only
once
and
may
failif
re-
used
.
"
Bolts
and
nuts
coated
with
a
focking
compound
from
the
factory
shouldnot
be
refnstalled
.
Always
replace`micro-encapsulated"
fasteners
such
as
the
steering
arm-to-strutbolts
.
CONTROL
ARMS
Tightening
Torques
"
Control
arm
balljoint
to
subframe
crossmember
.
..
...
...
.
.
85
Nm
(62
ft-Ib)
"
Control
arm'ball
joint
to
steering
arm
.
65
Nm
(48
ft-Ib)
"
Control
arm
bushing
carrier
to
body
.
.
47
Nm
(34
ft-Ib)
"
Stabilizer
bar
link
to
control
arm
(M8)
.
42
Nm
(31
ft-Ib)
"
Road
wheel
to
hub
.
...
...
.
.
100±10
Nm
(74±7
ft-Ib)
Outer
control
arm
ball
joint,
replacing
(except
M3
models)
On
all
models
except
Mas,
the
outer
balljoint
is
available
as
a
replacement
part
.
The
ball
joint
can
be
replaced
with
the
control
arm
installed
.
Special
tools
are
requiredto
replace
the
balljoínt
.
Read
the
procedure
through
before
beginning
thejob
.
1
.
Disconnect
stabilizer
bar
link
from
control
arm
asde-
scribed
later
in
this
repair
group
.
NOTE-
On
M3
models,
the
stabilizer
bar
link
attaches
to
the
strut
.
tt
fs
not
necessary
to
disconnect
the
stabilizer
bar
link
on
M3
models
for
thfs
repair
procedure
.
2
.
Loosen
nut
for
balljointuntil
it
contacts
steering
arm
.
3
.
Using
a
suitable
ball
joint
tool,
separate
joint
from
steer-
íng
arm
.
Remove
ball
joint
mounting
nut
and
pullball
joint
out
of
steering
arm
.
4
.
Mark
position
of
balljoint
guide
to
control
arm
.
See
Fig
.
10
.
0012718
Fig
.
10
.
Mark
installed
position
of
ball
joint
guide
to
control
arm
(sr-
row)
.
5
.
Move
suspension
strut
out
of
way
and
press
ball
joint
out
of
control
arm
.
Page 267 of 759
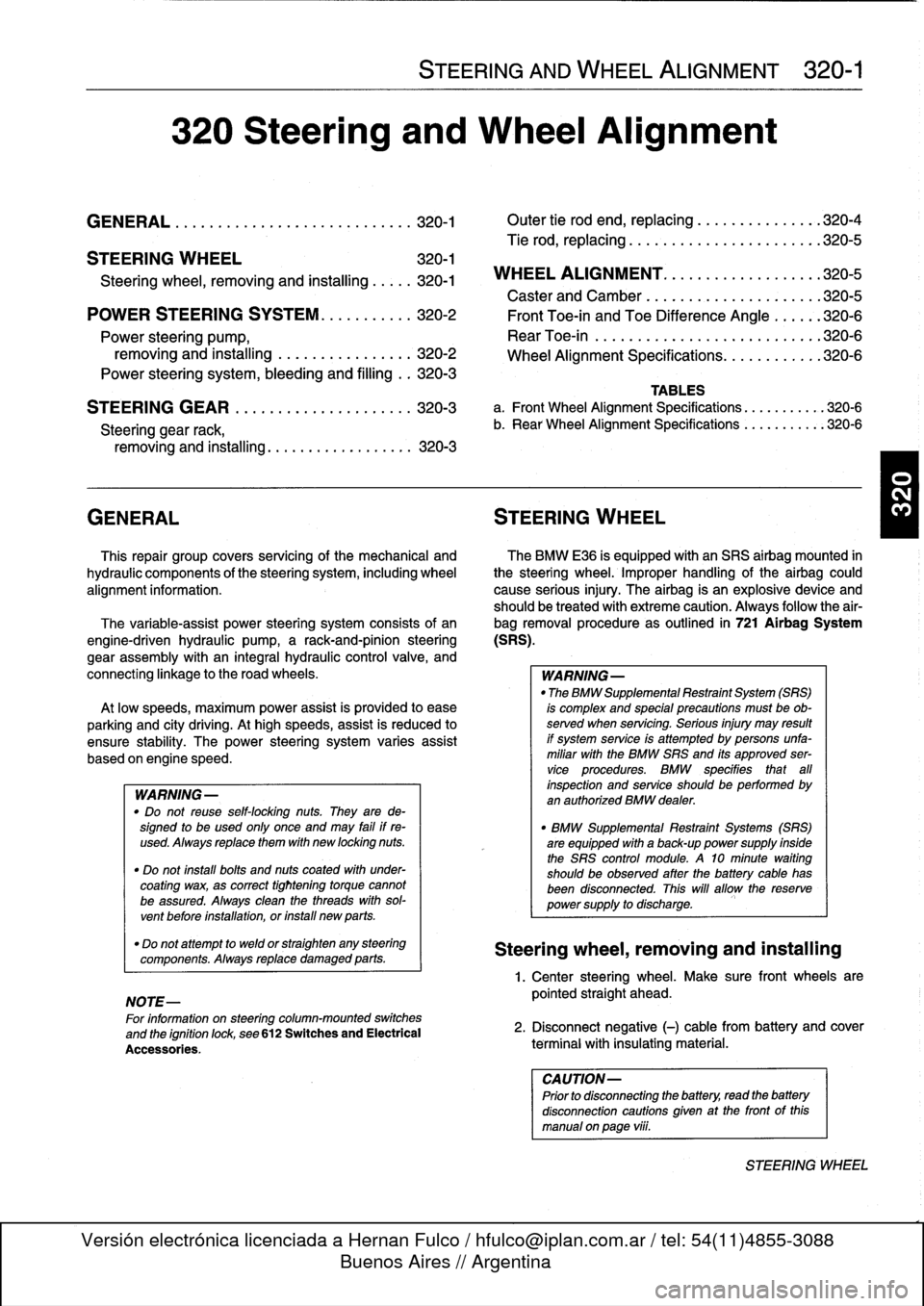
320
Steering
and
Wheel
Alignment
GENERAL
...
.
.
.
...
.
....
.
.
.
.
.
.
.
.
.
...
.
.
320-1
Outer
tie
rod
end,
replacing
.
...
.
.
.
.
.
.
.
...
.
320-4
Tie
rod,
replacing
.
.
.
.
.
.
.
.......
.
.
.
.
.
...
.
320-5
STEERING
WHEEL
320-1
Steering
wheel,
removing
and
installing
.....
320-1
WHEEL
ALIGNMENT
.
.
.
.........
.
.....
.320-5
POWER
STEERING
SYSTEM
.
.
.
.
.
.
.....
320-2
Front
Toe-in
and
Toe
Difference
Angle
.
.
...
.
320-6
Power
steering
pump,
Rear
Toe-in
.
.
.
.
.
.
.
...
.
................
320-6
removing
and
installing
..
.
.
.
.
.
.
.
.
.
.....
320-2
Wheel
Alignment
Specifications
.....
.
......
320-6
Power
steering
system,
bleeding
and
filling
.
.
320-3
STEERING
GEAR
.
.
.
.
...
.
.
.
.
.
.
.
.
.
.....
320-3
Steering
gear
rack,
removing
and
installing
.
...
.
..
.
..
..
..
.
..
.
320-3
GENERAL
STEERING
WHEEL
This
repair
group
covers
servicing
of
the
mechanical
and
The
BMW
E36
is
equipped
with
an
SRS
airbag
mounted
in
hydraulic
components
of
the
steering
system,
including
wheel
the
steering
wheel
.
Improper
handling
of
the
airbag
could
alignment
information
.
cause
serious
injury
.
The
airbag
is
an
explosivedevice
and
should
be
treated
with
extreme
caution
.
Always
follow
the
air-
The
variable-assist
power
steering
system
consistsof
an
bag
removal
procedure
as
outlined
in
721
Airbag
System
engine-driven
hydraulic
pump,
a
rack-and-pinion
steering
(SRS)
.
gear
assembly
with
an
integral
hydraulic
control
valve,
and
connecting
linkage
to
the
road
wheels
.
WARNING-
"
The
BMW
Supplemental
Restraint
System
(SRS)
At
lowspeeds,
maximum
power
assist
is
provided
to
ease
is
complex
and
special
precautions
must
be
ob-
parking
and
city
driving
.
At
high
speeds,
assist
is
reduced
to
served
when
servicing
.
Serious
injury
may
result
ensure
stability
.
The
power
steering
system
varies
assist
if
system
service
is
attempted
by
persons
unfa-
based
on
engine
speed
.
miliar
with
the
BMW
SRS
and
its
approved
ser-
vice
procedures
.
BMW
specifies
that
all
ING-
inspection
and
service
shouldbe
performed
by
WARN
an
authorized
BMW
dealer
.
"
Do
not
reuse
self-locking
nuts
.
They
are
de-signed
to
beused
only
once
and
may
failif
re-
"
BMW
Supplemental
Restraint
Systems
(SRS)
used
.
Always
replace
them
with
new
locking
nuts
.
are
equipped
with
a
back-up
power
supply
inside
the
SRS
control
module
.
A
10minute
waiting
"
Do
not
ínstall
bolts
and
nuts
coated
with
under-
shouldbe
observed
after
the
battery
cable
has
coating
wax,
as
correct
tightening
torque
cannot
been
disconnected
.
This
will
allow
the
reserve
be
assured
.
Always
clean
the
threads
with
sol-
power
supply
to
discharge
.
vent
before
installation,
or
install
new
parts
.
"
Do
not
attempt
to
weldor
straighten
any
steering
components
.
Always
replace
damaged
parts
.
NOTE-
For
information
on
steering
column-mounted
switches
and
the
ignition
lock,
see
612
Switches
and
Electrical
Accessories
.
STEERING
AND
WHEEL
ALIGNMENT
320-1
Caster
and
Camber
.
.
.
.
.
...........
.
....
320-5
TABLES
a
.
Front
Wheel
Alignment
Specifications
.
...
.......
320-6
b
.
Rear
Wheel
Alignment
Specifications
.
...
.......
320-6
Steering
wheel,
removing
and
installing
1
.
Center
steering
wheel
.
Make
sure
front
wheelsare
pointed
straight
ahead
.
2
.
Disconnect
negative
(-)
cable
from
battery
and
cover
terminal
with
insulating
material
.
CAUTION-
Prior
to
disconnectiog
the
battery,
read
the
battery
disconnection
cautions
given
at
the
front
of
this
manual
on
page
viii
.
STEERING
WHEEL