torque BMW X5 2004 E53 DSC System Workshop Manual
[x] Cancel search | Manufacturer: BMW, Model Year: 2004, Model line: X5, Model: BMW X5 2004 E53Pages: 24, PDF Size: 1.77 MB
Page 3 of 24

3
TRACTION CONTROL SYSTEM OVERVIEW (ASC)
THEORY OF TRACTION CONTROL
Traction Control Systems are referred to as Automatic Stability Control (ASC), Automatic
Stability + Traction Control (ASC+T), Dynamic Stability Control (DSC) or All Season Traction
(marketing term). The traction control system has gone through several changes since its
introduction in Model Year 1988. While each new version offered new innovations, the prin-
ciple of traction control remains the same for any of these versions.
The link between the vehicle and its driving environment is established by the frictional con-
tact between the tires and the road surface. The ability to control the vehicle while driving,
is lost as a result of excessive wheel spin or slip if either rear tire exceeds its ability to:
• Maintain traction
• Accept side forces to maintain directional control (lateral locating forces)
The primary function of the traction control system is to maintain traction and stability of the
vehicle regardless of the road surface condition. This is achieved by reducing the drive
torque applied to the rear wheels or pulsing the rear wheel brakes to eliminate wheel slip
depending on the version of traction control installed.
The electronics for traction control operation are incorporated in the ABS control module
and share many of the same components and sensors. The module determines the speed
of the vehicle through a calculated average of the four wheel speed sensor inputs. Wheel
slip/spin is then recognized by comparing the speed of the driven wheels to the front
wheels.
A critical slip ratio of greater than 5% between the wheels will cause the traction control regu-
lation to begin. This slip ratio is established when the control module detects a wheel speed
difference of 2 MPH or higher.
Page 7 of 24
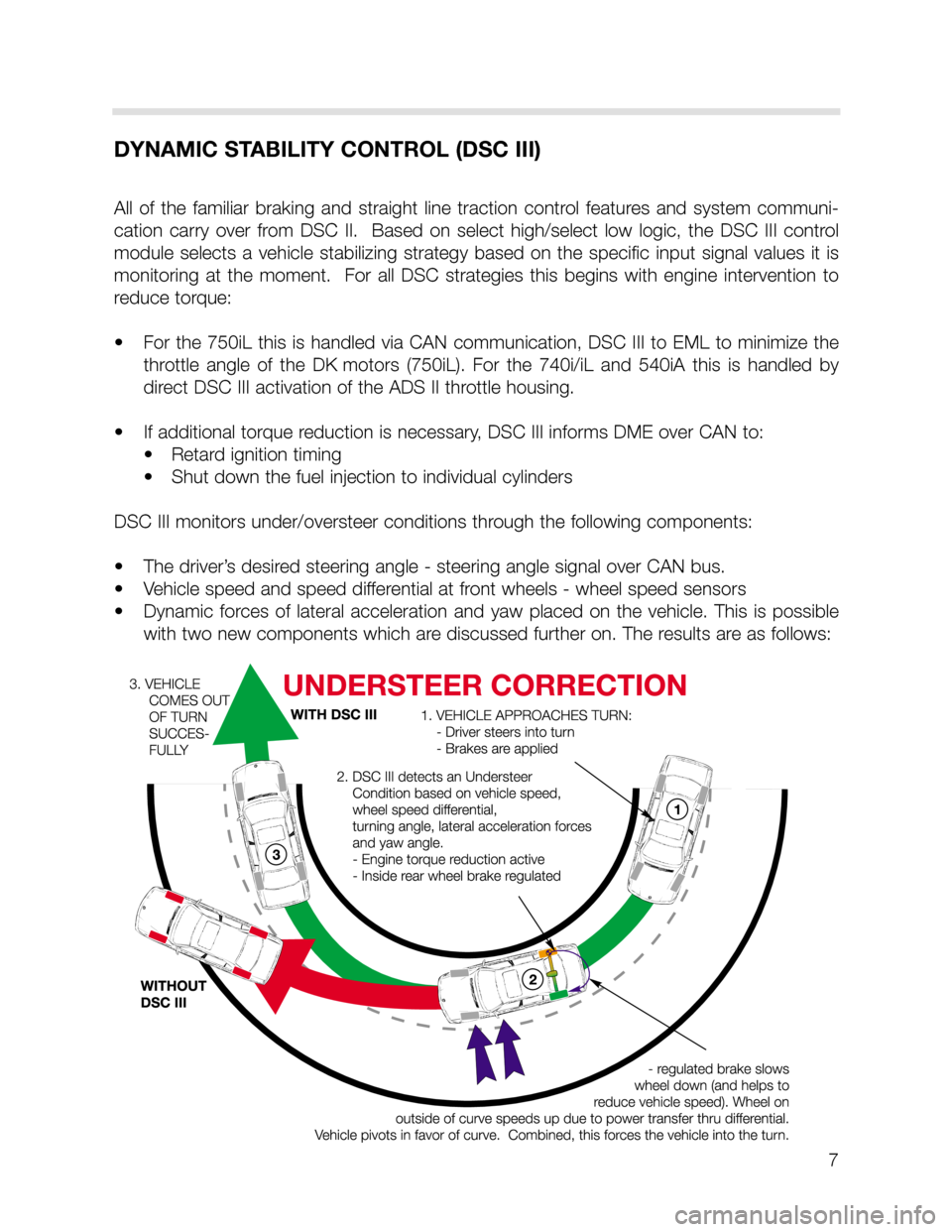
7
DYNAMIC STABILITY CONTROL (DSC III)
All of the familiar braking and straight line traction control features and system communi-
cation carry over from DSC II. Based on select high/select low logic, the DSC III control
module selects a vehicle stabilizing strategy based on the specific input signal values it is
monitoring at the moment. For all DSC strategies this begins with engine intervention to
reduce torque:
•For the 750iL this is handled via CAN communication, DSC III to EML to minimize the
throttle angle of the DK motors (750iL). For the 740i/iL and 540iA this is handled by
direct DSC III activation of the ADS II throttle housing.
• If additional torque reduction is necessary, DSC III informs DME over CAN to:
• Retard ignition timing
• Shut down the fuel injection to individual cylinders
DSC III monitors under/oversteer conditions through the following components:
• The driver’s desired steering angle - steering angle signal over CAN bus.
• Vehicle speed and speed differential at front wheels - wheel speed sensors
• Dynamic forces of lateral acceleration and yaw placed on the vehicle. This is possible
with two new components which are discussed further on. The results are as follows:
Page 13 of 24
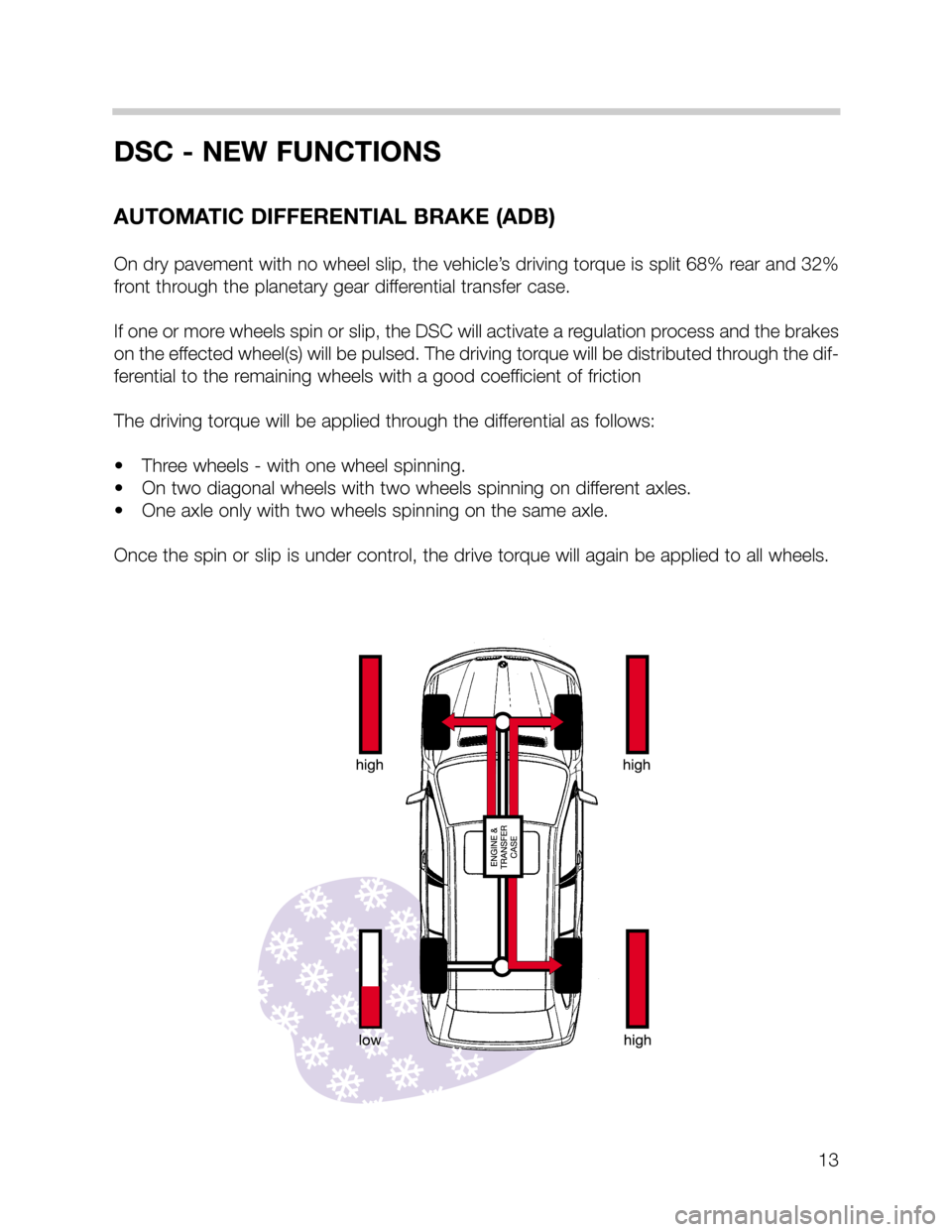
13
DSC - NEW FUNCTIONS
AUTOMATIC DIFFERENTIAL BRAKE (ADB)
On dry pavement with no wheel slip, the vehicle’s driving torque is split 68% rear and 32%
front through the planetary gear differential transfer case.
If one or more wheels spin or slip, the DSC will activate a regulation process and the brakes
on the effected wheel(s) will be pulsed. The driving torque will be distributed through the dif-
ferential to the remaining wheels with a good coefficient of friction
The driving torque will be applied through the differential as follows:
• Three wheels - with one wheel spinning.
• On two diagonal wheels with two wheels spinning on different axles.
• One axle only with two wheels spinning on the same axle.
Once the spin or slip is under control, the drive torque will again be applied to all wheels.