CHEVROLET PLYMOUTH ACCLAIM 1993 Service Manual
Manufacturer: CHEVROLET, Model Year: 1993, Model line: PLYMOUTH ACCLAIM, Model: CHEVROLET PLYMOUTH ACCLAIM 1993Pages: 2438, PDF Size: 74.98 MB
Page 161 of 2438
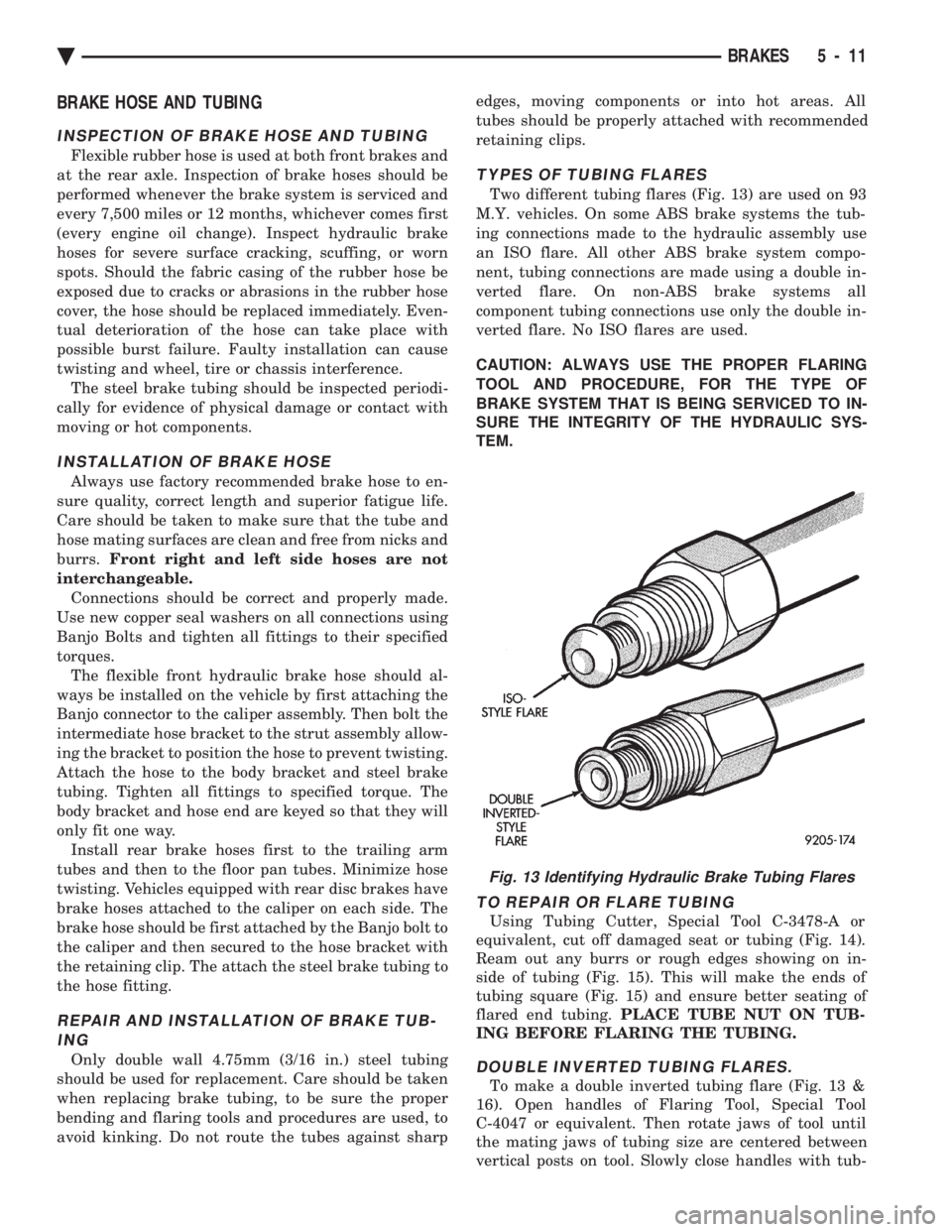
BRAKE HOSE AND TUBING
INSPECTION OF BRAKE HOSE AND TUBING
Flexible rubber hose is used at both front brakes and
at the rear axle. Inspection of brake hoses should be
performed whenever the brake system is serviced and
every 7,500 miles or 12 months, whichever comes first
(every engine oil change). Inspect hydraulic brake
hoses for severe surface cracking, scuffing, or worn
spots. Should the fabric casing of the rubber hose be
exposed due to cracks or abrasions in the rubber hose
cover, the hose should be replaced immediately. Even-
tual deterioration of the hose can take place with
possible burst failure. Faulty installation can cause
twisting and wheel, tire or chassis interference. The steel brake tubing should be inspected periodi-
cally for evidence of physical damage or contact with
moving or hot components.
INSTALLATION OF BRAKE HOSE
Always use factory recommended brake hose to en-
sure quality, correct length and superior fatigue life.
Care should be taken to make sure that the tube and
hose mating surfaces are clean and free from nicks and
burrs. Front right and left side hoses are not
interchangeable. Connections should be correct and properly made.
Use new copper seal washers on all connections using
Banjo Bolts and tighten all fittings to their specified
torques. The flexible front hydraulic brake hose should al-
ways be installed on the vehicle by first attaching the
Banjo connector to the caliper assembly. Then bolt the
intermediate hose bracket to the strut assembly allow-
ing the bracket to position the hose to prevent twisting.
Attach the hose to the body bracket and steel brake
tubing. Tighten all fittings to specified torque. The
body bracket and hose end are keyed so that they will
only fit one way. Install rear brake hoses first to the trailing arm
tubes and then to the floor pan tubes. Minimize hose
twisting. Vehicles equipped with rear disc brakes have
brake hoses attached to the caliper on each side. The
brake hose should be first attached by the Banjo bolt to
the caliper and then secured to the hose bracket with
the retaining clip. The attach the steel brake tubing to
the hose fitting.
REPAIR AND INSTALLATION OF BRAKE TUB- ING
Only double wall 4.75mm (3/16 in.) steel tubing
should be used for replacement. Care should be taken
when replacing brake tubing, to be sure the proper
bending and flaring tools and procedures are used, to
avoid kinking. Do not route the tubes against sharp edges, moving components or into hot areas. All
tubes should be properly attached with recommended
retaining clips.
TYPES OF TUBING FLARES
Two different tubing flares (Fig. 13) are used on 93
M.Y. vehicles. On some ABS brake systems the tub-
ing connections made to the hydraulic assembly use
an ISO flare. All other ABS brake system compo-
nent, tubing connections are made using a double in-
verted flare. On non-ABS brake systems all
component tubing connections use only the double in-
verted flare. No ISO flares are used.
CAUTION: ALWAYS USE THE PROPER FLARING
TOOL AND PROCEDURE, FOR THE TYPE OF
BRAKE SYSTEM THAT IS BEING SERVICED TO IN-
SURE THE INTEGRITY OF THE HYDRAULIC SYS-
TEM.
TO REPAIR OR FLARE TUBING
Using Tubing Cutter, Special Tool C-3478-A or
equivalent, cut off damaged seat or tubing (Fig. 14).
Ream out any burrs or rough edges showing on in-
side of tubing (Fig. 15). This will make the ends of
tubing square (Fig. 15) and ensure better seating of
flared end tubing. PLACE TUBE NUT ON TUB-
ING BEFORE FLARING THE TUBING.
DOUBLE INVERTED TUBING FLARES.
To make a double inverted tubing flare (Fig. 13 &
16). Open handles of Flaring Tool, Special Tool
C-4047 or equivalent. Then rotate jaws of tool until
the mating jaws of tubing size are centered between
vertical posts on tool. Slowly close handles with tub-
Fig. 13 Identifying Hydraulic Brake Tubing Flares
Ä BRAKES 5 - 11
Page 162 of 2438
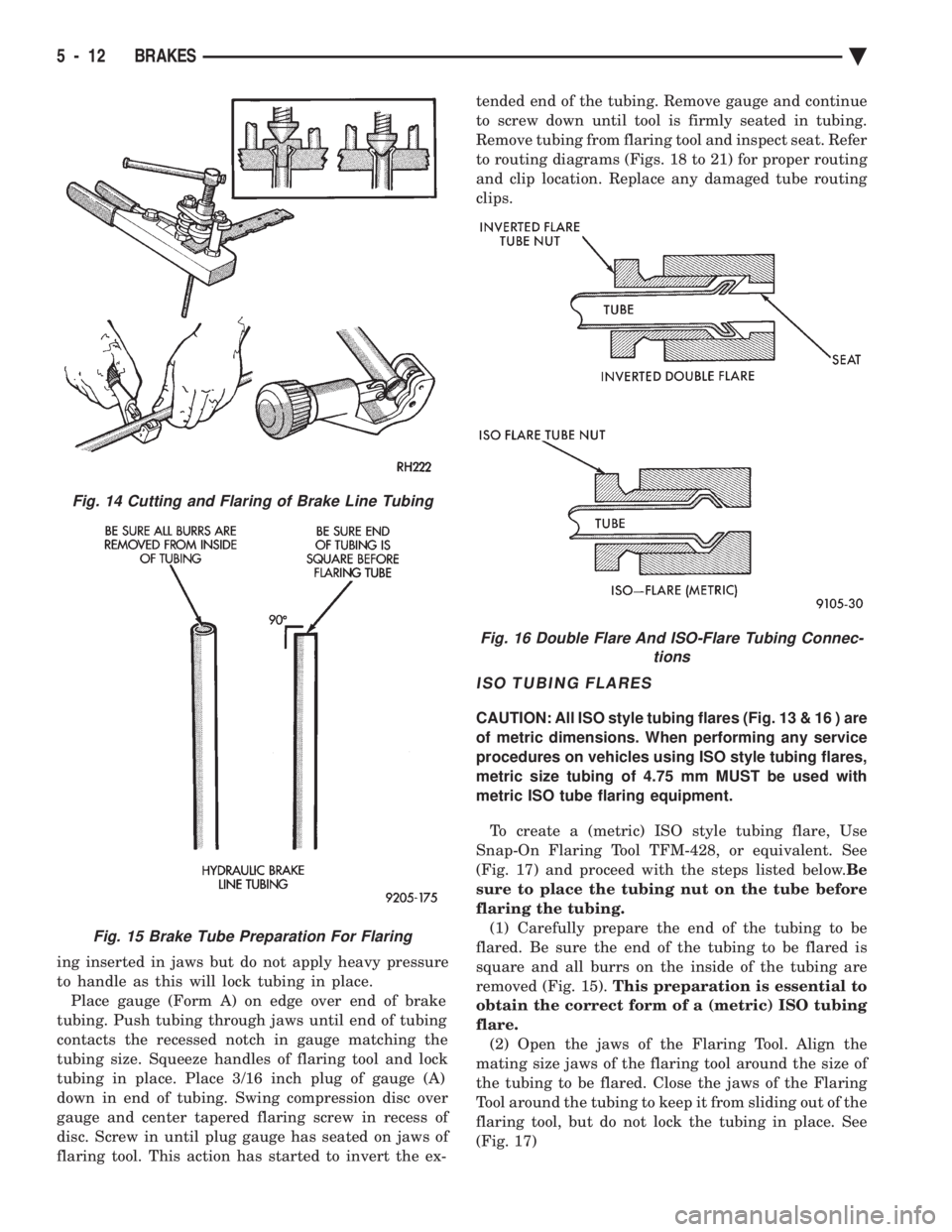
ing inserted in jaws but do not apply heavy pressure
to handle as this will lock tubing in place.Place gauge (Form A) on edge over end of brake
tubing. Push tubing through jaws until end of tubing
contacts the recessed notch in gauge matching the
tubing size. Squeeze handles of flaring tool and lock
tubing in place. Place 3/16 inch plug of gauge (A)
down in end of tubing. Swing compression disc over
gauge and center tapered flaring screw in recess of
disc. Screw in until plug gauge has seated on jaws of
flaring tool. This action has started to invert the ex- tended end of the tubing. Remove gauge and continue
to screw down until tool is firmly seated in tubing.
Remove tubing from flaring tool and inspect seat. Refer
to routing diagrams (Figs. 18 to 21) for proper routing
and clip location. Replace any damaged tube routing
clips.
ISO TUBING FLARES
CAUTION: All ISO style tubing flares (Fig. 13 & 16 ) are
of metric dimensions. When performing any service
procedures on vehicles using ISO style tubing flares,
metric size tubing of 4.75 mm MUST be used with
metric ISO tube flaring equipment.
To create a (metric) ISO style tubing flare, Use
Snap-On Flaring Tool TFM-428, or equivalent. See
(Fig. 17) and proceed with the steps listed below. Be
sure to place the tubing nut on the tube before
flaring the tubing. (1) Carefully prepare the end of the tubing to be
flared. Be sure the end of the tubing to be flared is
square and all burrs on the inside of the tubing are
removed (Fig. 15). This preparation is essential to
obtain the correct form of a (metric) ISO tubing
flare. (2) Open the jaws of the Flaring Tool. Align the
mating size jaws of the flaring tool around the size of
the tubing to be flared. Close the jaws of the Flaring
Tool around the tubing to keep it from sliding out of the
flaring tool, but do not lock the tubing in place. See
(Fig. 17)
Fig. 14 Cutting and Flaring of Brake Line Tubing
Fig. 15 Brake Tube Preparation For Flaring
Fig. 16 Double Flare And ISO-Flare Tubing Connec- tions
5 - 12 BRAKES Ä
Page 163 of 2438
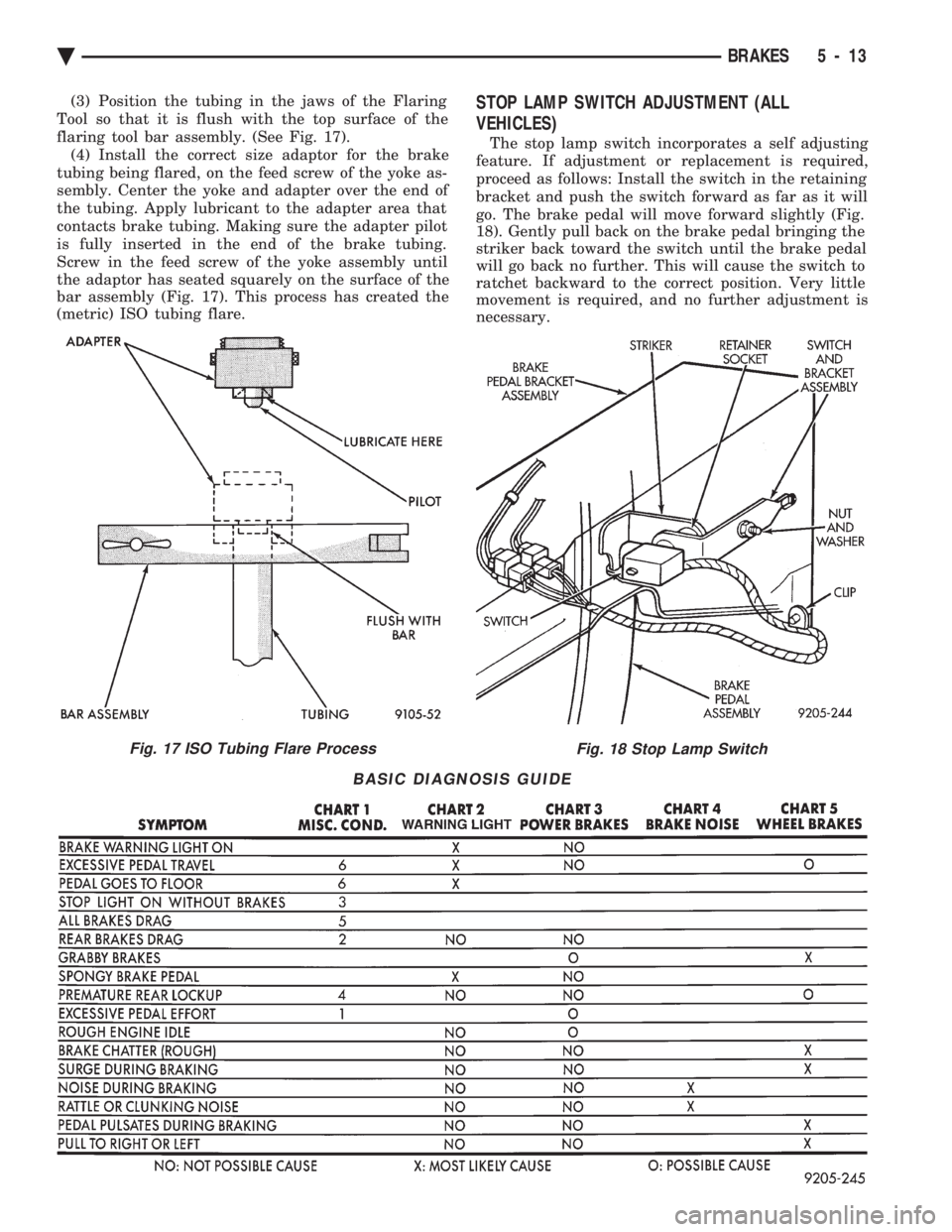
(3) Position the tubing in the jaws of the Flaring
Tool so that it is flush with the top surface of the
flaring tool bar assembly. (See Fig. 17). (4) Install the correct size adaptor for the brake
tubing being flared, on the feed screw of the yoke as-
sembly. Center the yoke and adapter over the end of
the tubing. Apply lubricant to the adapter area that
contacts brake tubing. Making sure the adapter pilot
is fully inserted in the end of the brake tubing.
Screw in the feed screw of the yoke assembly until
the adaptor has seated squarely on the surface of the
bar assembly (Fig. 17). This process has created the
(metric) ISO tubing flare.STOP LAMP SWITCH ADJUSTMENT (ALL
VEHICLES)
The stop lamp switch incorporates a self adjusting
feature. If adjustment or replacement is required,
proceed as follows: Install the switch in the retaining
bracket and push the switch forward as far as it will
go. The brake pedal will move forward slightly (Fig.
18). Gently pull back on the brake pedal bringing the
striker back toward the switch until the brake pedal
will go back no further. This will cause the switch to
ratchet backward to the correct position. Very little
movement is required, and no further adjustment is
necessary.
Fig. 17 ISO Tubing Flare ProcessFig. 18 Stop Lamp Switch
BASIC DIAGNOSIS GUIDE
Ä BRAKES 5 - 13
Page 164 of 2438
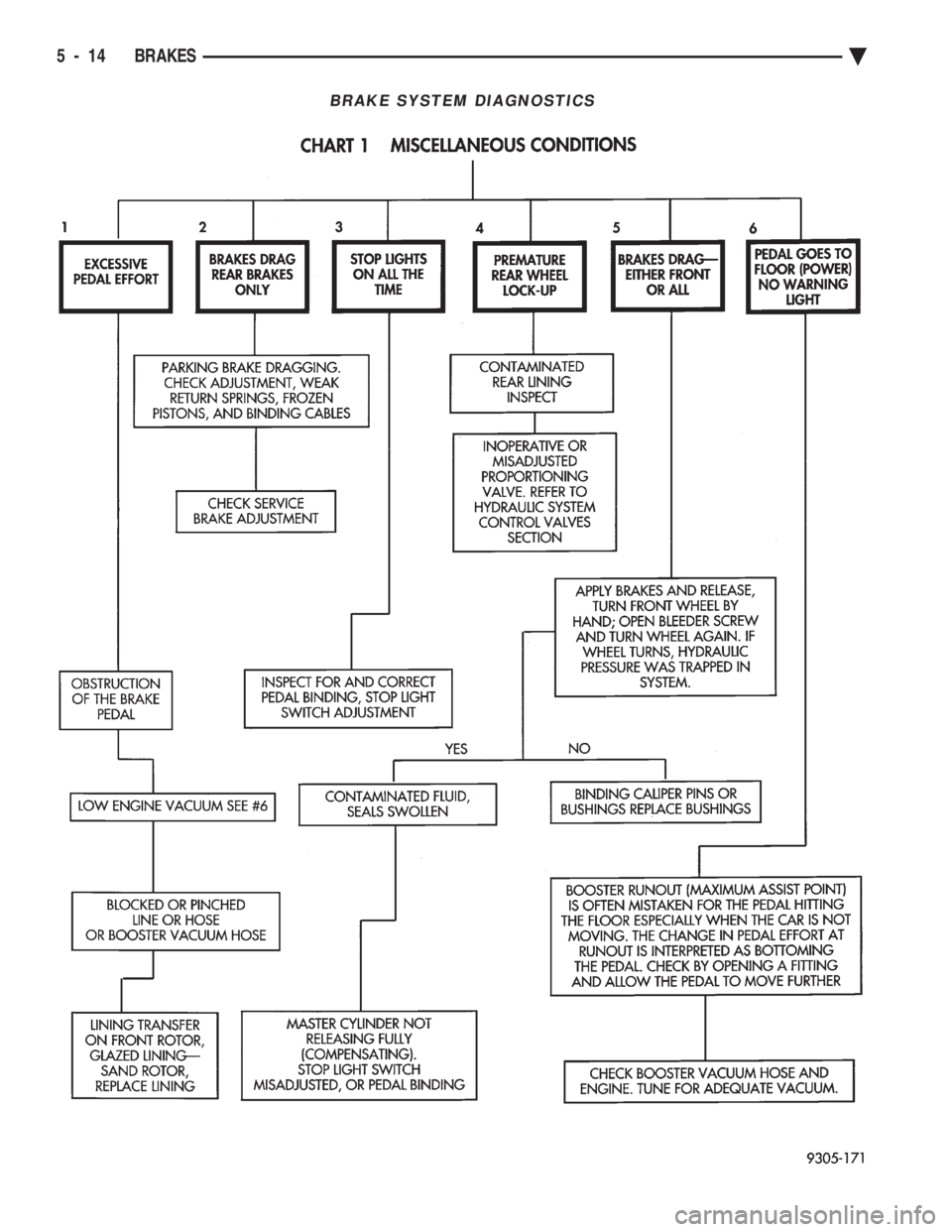
BRAKE SYSTEM DIAGNOSTICS
5 - 14 BRAKES Ä
Page 165 of 2438
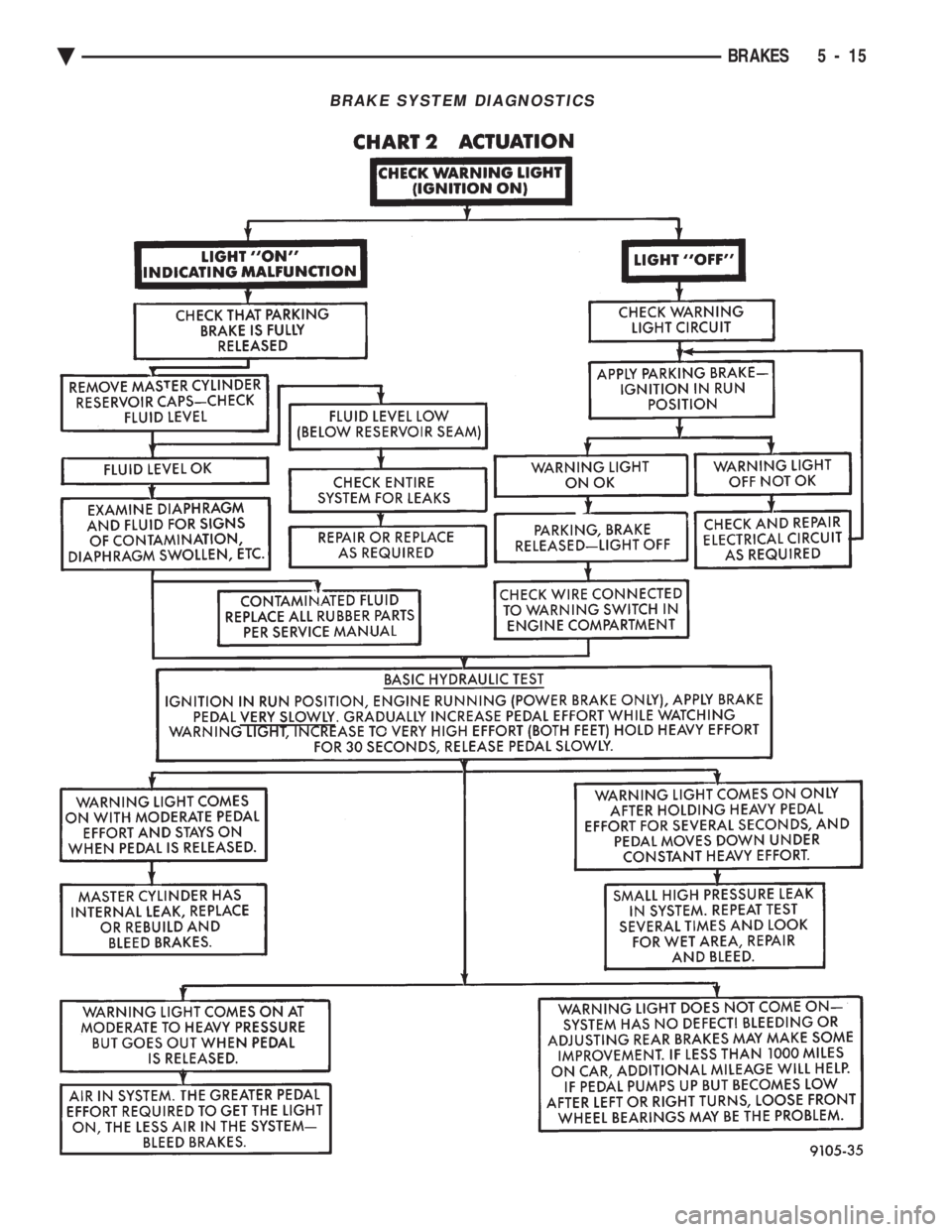
BRAKE SYSTEM DIAGNOSTICS
Ä BRAKES 5 - 15
Page 166 of 2438
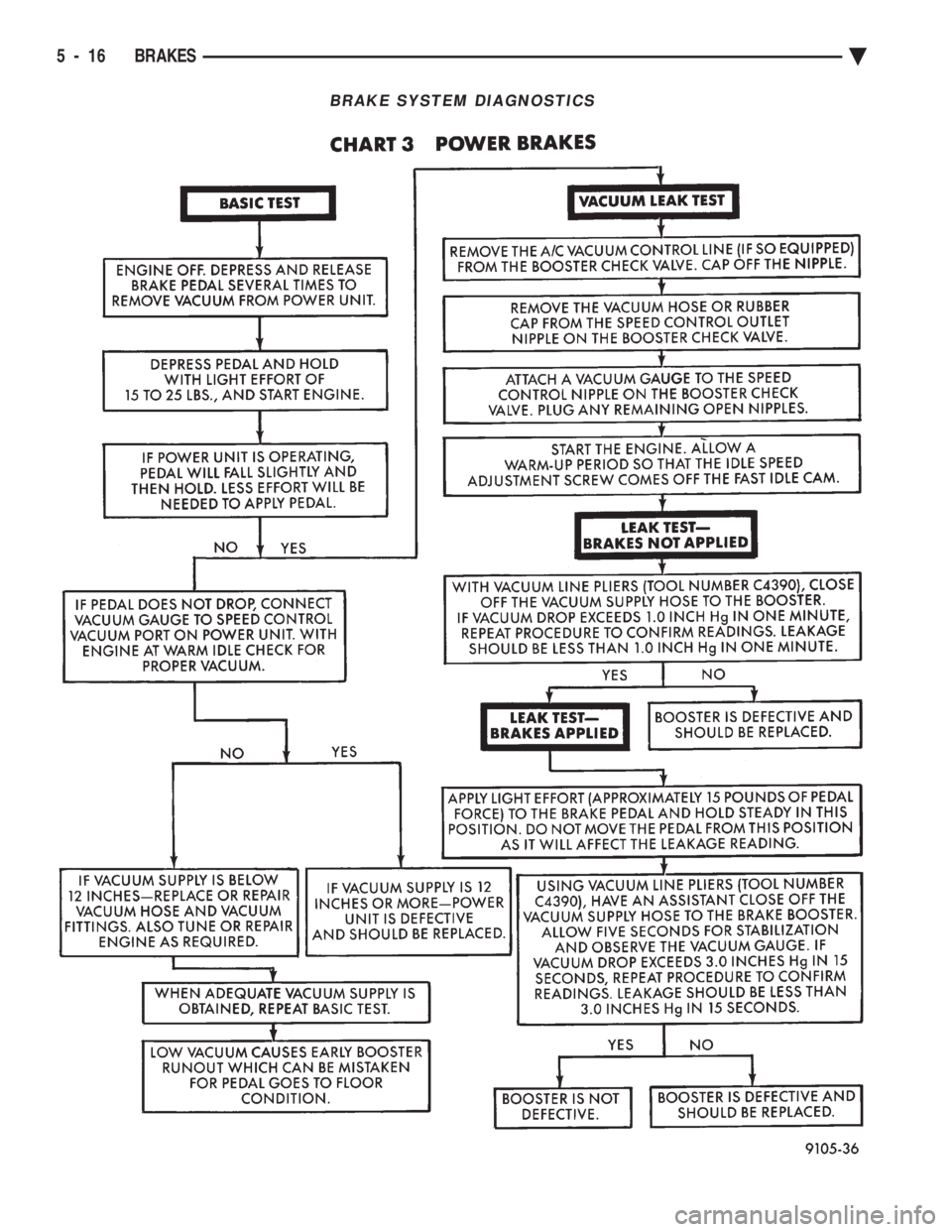
BRAKE SYSTEM DIAGNOSTICS
5 - 16 BRAKES Ä
Page 167 of 2438
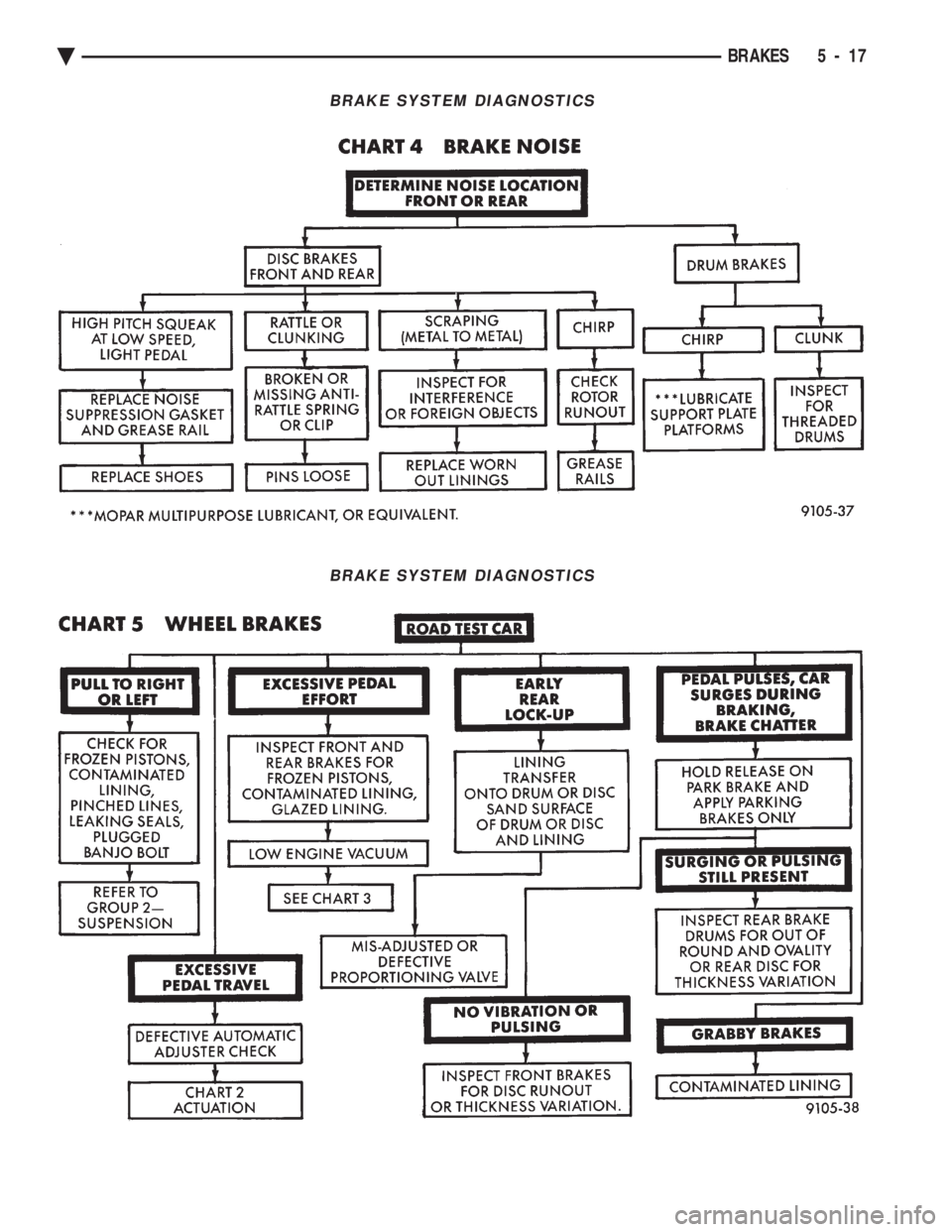
BRAKE SYSTEM DIAGNOSTICS
BRAKE SYSTEM DIAGNOSTICS
Ä BRAKES 5 - 17
Page 168 of 2438
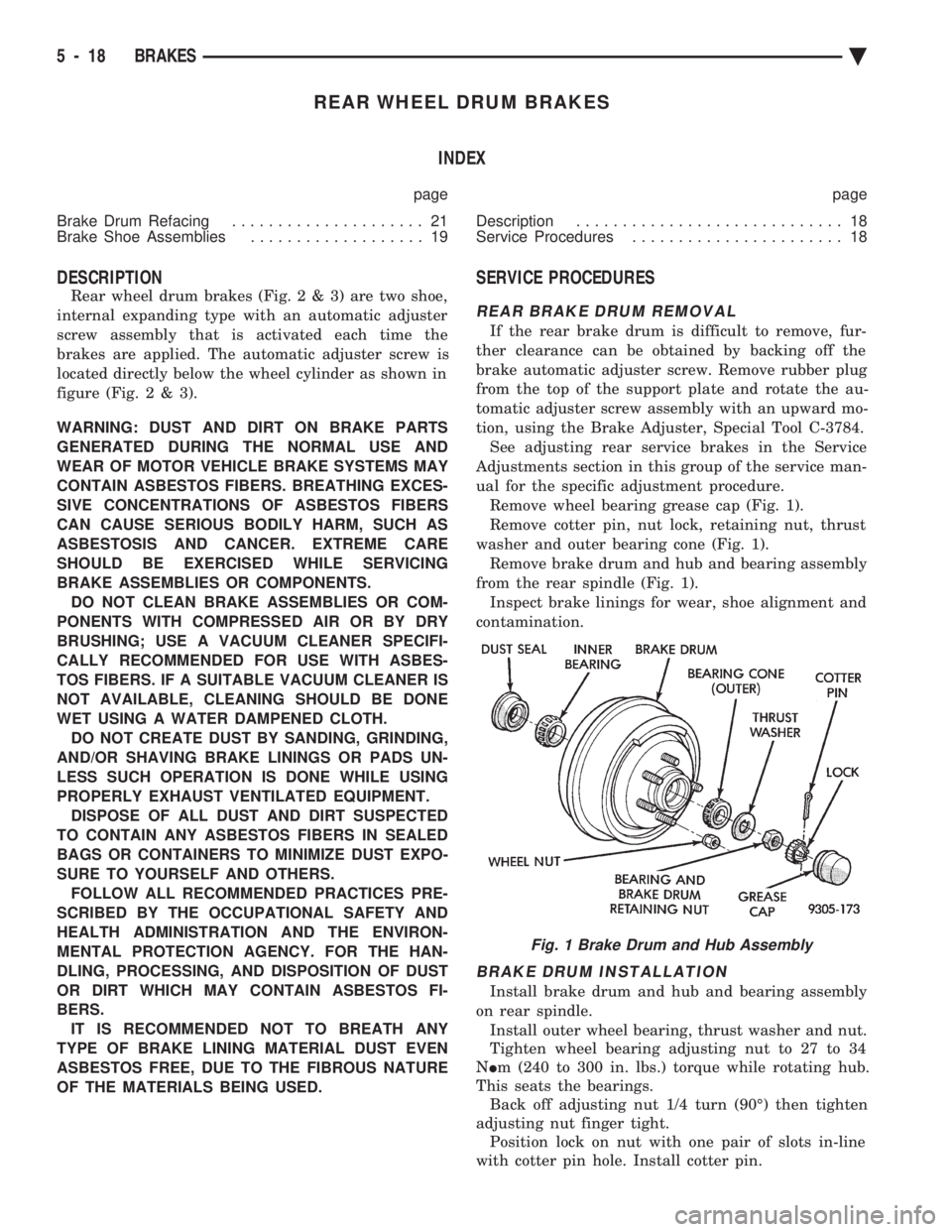
REAR WHEEL DRUM BRAKES INDEX
page page
Brake Drum Refacing ..................... 21
Brake Shoe Assemblies ................... 19 Description
............................. 18
Service Procedures ....................... 18
DESCRIPTION
Rear wheel drum brakes (Fig .2&3)aretwoshoe,
internal expanding type with an automatic adjuster
screw assembly that is activated each time the
brakes are applied. The automatic adjuster screw is
located directly below the wheel cylinder as shown in
figure (Fig .2&3).
WARNING: DUST AND DIRT ON BRAKE PARTS
GENERATED DURING THE NORMAL USE AND
WEAR OF MOTOR VEHICLE BRAKE SYSTEMS MAY
CONTAIN ASBESTOS FIBERS. BREATHING EXCES-
SIVE CONCENTRATIONS OF ASBESTOS FIBERS
CAN CAUSE SERIOUS BODILY HARM, SUCH AS
ASBESTOSIS AND CANCER. EXTREME CARE
SHOULD BE EXERCISED WHILE SERVICING
BRAKE ASSEMBLIES OR COMPONENTS. DO NOT CLEAN BRAKE ASSEMBLIES OR COM-
PONENTS WITH COMPRESSED AIR OR BY DRY
BRUSHING; USE A VACUUM CLEANER SPECIFI-
CALLY RECOMMENDED FOR USE WITH ASBES-
TOS FIBERS. IF A SUITABLE VACUUM CLEANER IS
NOT AVAILABLE, CLEANING SHOULD BE DONE
WET USING A WATER DAMPENED CLOTH. DO NOT CREATE DUST BY SANDING, GRINDING,
AND/OR SHAVING BRAKE LININGS OR PADS UN-
LESS SUCH OPERATION IS DONE WHILE USING
PROPERLY EXHAUST VENTILATED EQUIPMENT. DISPOSE OF ALL DUST AND DIRT SUSPECTED
TO CONTAIN ANY ASBESTOS FIBERS IN SEALED
BAGS OR CONTAINERS TO MINIMIZE DUST EXPO-
SURE TO YOURSELF AND OTHERS. FOLLOW ALL RECOMMENDED PRACTICES PRE-
SCRIBED BY THE OCCUPATIONAL SAFETY AND
HEALTH ADMINISTRATION AND THE ENVIRON-
MENTAL PROTECTION AGENCY. FOR THE HAN-
DLING, PROCESSING, AND DISPOSITION OF DUST
OR DIRT WHICH MAY CONTAIN ASBESTOS FI-
BERS. IT IS RECOMMENDED NOT TO BREATH ANY
TYPE OF BRAKE LINING MATERIAL DUST EVEN
ASBESTOS FREE, DUE TO THE FIBROUS NATURE
OF THE MATERIALS BEING USED.
SERVICE PROCEDURES
REAR BRAKE DRUM REMOVAL
If the rear brake drum is difficult to remove, fur-
ther clearance can be obtained by backing off the
brake automatic adjuster screw. Remove rubber plug
from the top of the support plate and rotate the au-
tomatic adjuster screw assembly with an upward mo-
tion, using the Brake Adjuster, Special Tool C-3784. See adjusting rear service brakes in the Service
Adjustments section in this group of the service man-
ual for the specific adjustment procedure. Remove wheel bearing grease cap (Fig. 1).
Remove cotter pin, nut lock, retaining nut, thrust
washer and outer bearing cone (Fig. 1). Remove brake drum and hub and bearing assembly
from the rear spindle (Fig. 1). Inspect brake linings for wear, shoe alignment and
contamination.
BRAKE DRUM INSTALLATION
Install brake drum and hub and bearing assembly
on rear spindle. Install outer wheel bearing, thrust washer and nut.
Tighten wheel bearing adjusting nut to 27 to 34
N Im (240 to 300 in. lbs.) torque while rotating hub.
This seats the bearings. Back off adjusting nut 1/4 turn (90É) then tighten
adjusting nut finger tight. Position lock on nut with one pair of slots in-line
with cotter pin hole. Install cotter pin.
Fig. 1 Brake Drum and Hub Assembly
5 - 18 BRAKES Ä
Page 169 of 2438
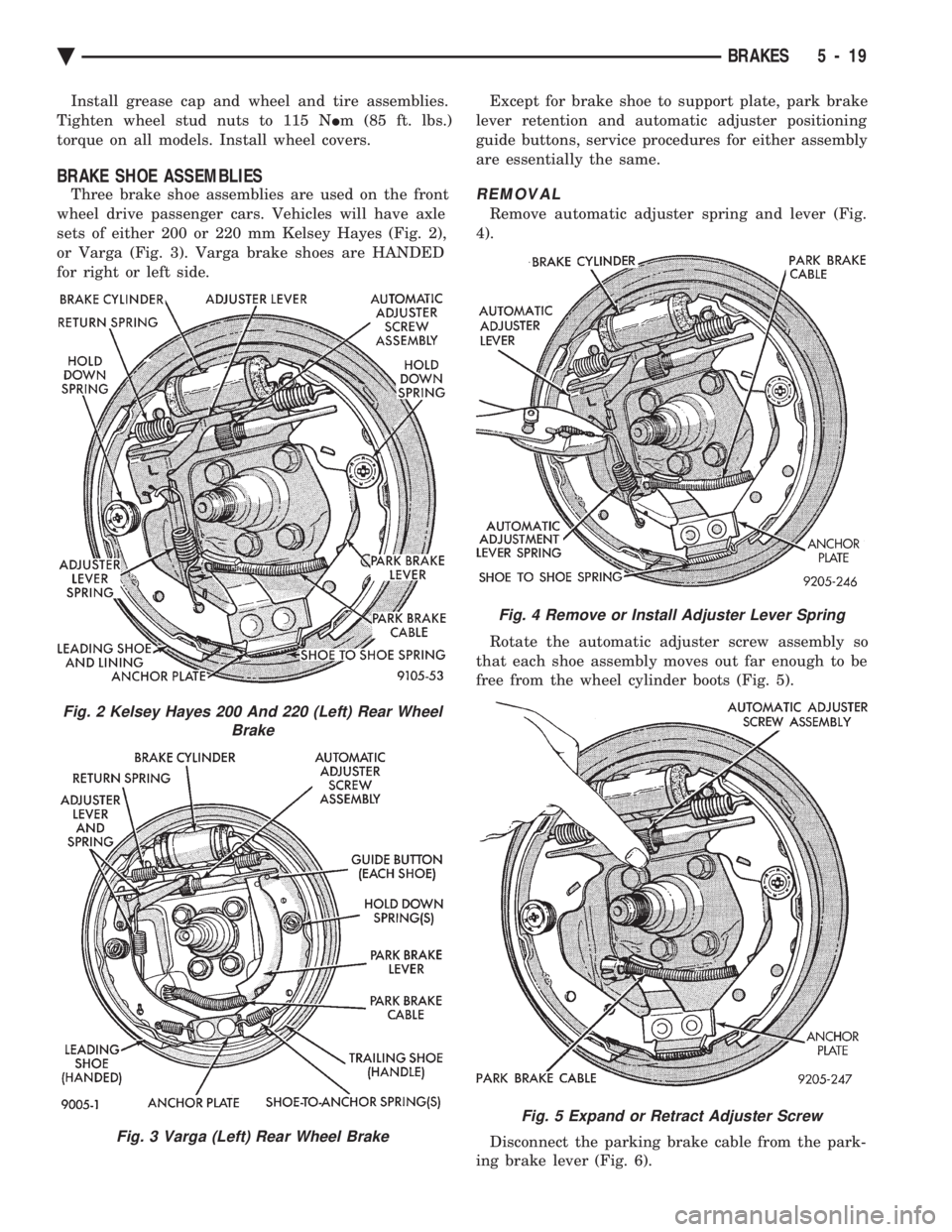
Install grease cap and wheel and tire assemblies.
Tighten wheel stud nuts to 115 N Im (85 ft. lbs.)
torque on all models. Install wheel covers.
BRAKE SHOE ASSEMBLIES
Three brake shoe assemblies are used on the front
wheel drive passenger cars. Vehicles will have axle
sets of either 200 or 220 mm Kelsey Hayes (Fig. 2),
or Varga (Fig. 3). Varga brake shoes are HANDED
for right or left side. Except for brake shoe to support plate, park brake
lever retention and automatic adjuster positioning
guide buttons, service procedures for either assembly
are essentially the same.REMOVAL
Remove automatic adjuster spring and lever (Fig.
4).
Rotate the automatic adjuster screw assembly so
that each shoe assembly moves out far enough to be
free from the wheel cylinder boots (Fig. 5).
Disconnect the parking brake cable from the park-
ing brake lever (Fig. 6).
Fig. 2 Kelsey Hayes 200 And 220 (Left) Rear Wheel Brake
Fig. 3 Varga (Left) Rear Wheel Brake
Fig. 4 Remove or Install Adjuster Lever Spring
Fig. 5 Expand or Retract Adjuster Screw
Ä BRAKES 5 - 19
Page 170 of 2438
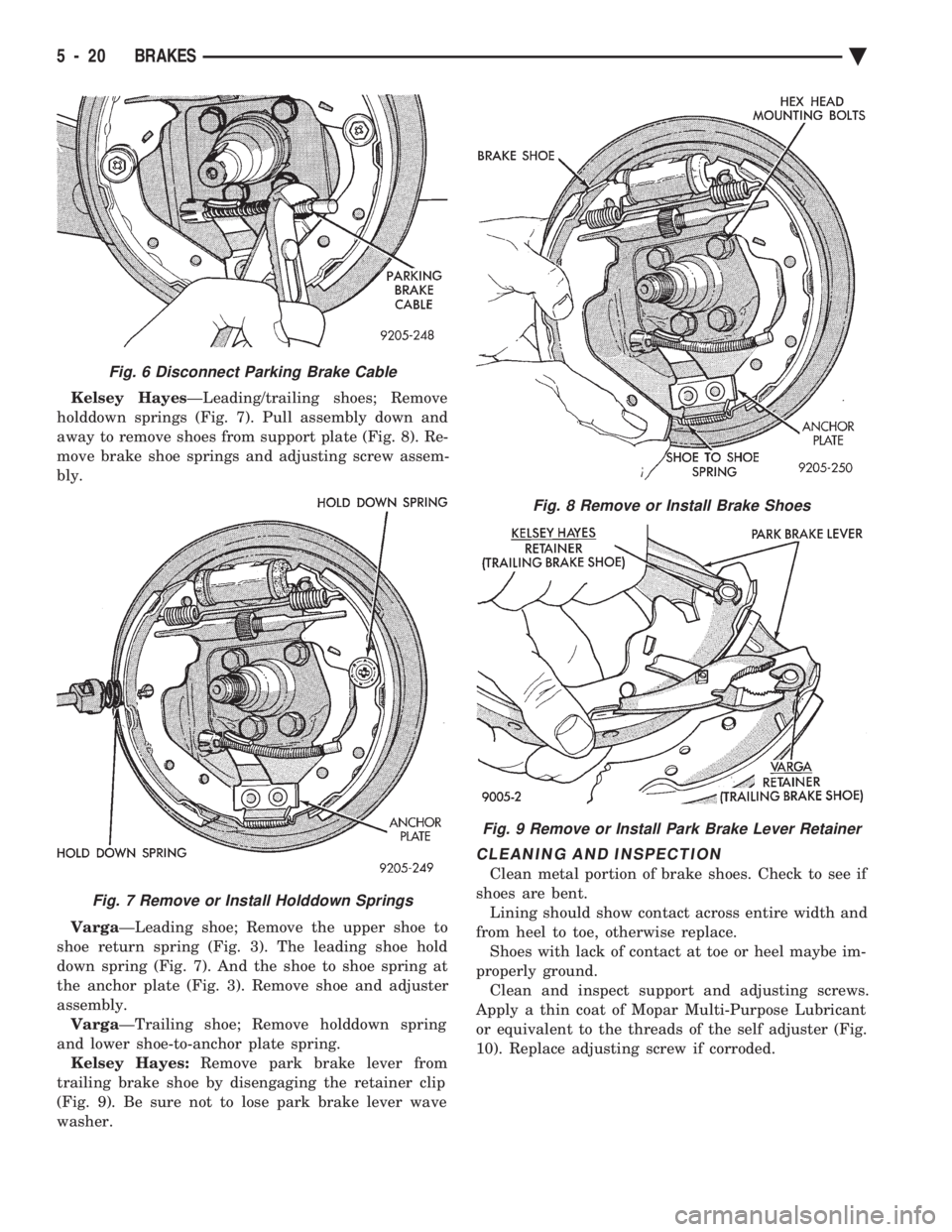
Kelsey Hayes ÐLeading/trailing shoes; Remove
holddown springs (Fig. 7). Pull assembly down and
away to remove shoes from support plate (Fig. 8). Re-
move brake shoe springs and adjusting screw assem-
bly.
Varga ÐLeading shoe; Remove the upper shoe to
shoe return spring (Fig. 3). The leading shoe hold
down spring (Fig. 7). And the shoe to shoe spring at
the anchor plate (Fig. 3). Remove shoe and adjuster
assembly. Varga ÐTrailing shoe; Remove holddown spring
and lower shoe-to-anchor plate spring. Kelsey Hayes: Remove park brake lever from
trailing brake shoe by disengaging the retainer clip
(Fig. 9). Be sure not to lose park brake lever wave
washer.
CLEANING AND INSPECTION
Clean metal portion of brake shoes. Check to see if
shoes are bent. Lining should show contact across entire width and
from heel to toe, otherwise replace. Shoes with lack of contact at toe or heel maybe im-
properly ground. Clean and inspect support and adjusting screws.
Apply a thin coat of Mopar Multi-Purpose Lubricant
or equivalent to the threads of the self adjuster (Fig.
10). Replace adjusting screw if corroded.
Fig. 6 Disconnect Parking Brake Cable
Fig. 7 Remove or Install Holddown Springs
Fig. 8 Remove or Install Brake Shoes
Fig. 9 Remove or Install Park Brake Lever Retainer
5 - 20 BRAKES Ä