CHEVROLET PLYMOUTH ACCLAIM 1993 Service Manual
Manufacturer: CHEVROLET, Model Year: 1993, Model line: PLYMOUTH ACCLAIM, Model: CHEVROLET PLYMOUTH ACCLAIM 1993Pages: 2438, PDF Size: 74.98 MB
Page 181 of 2438
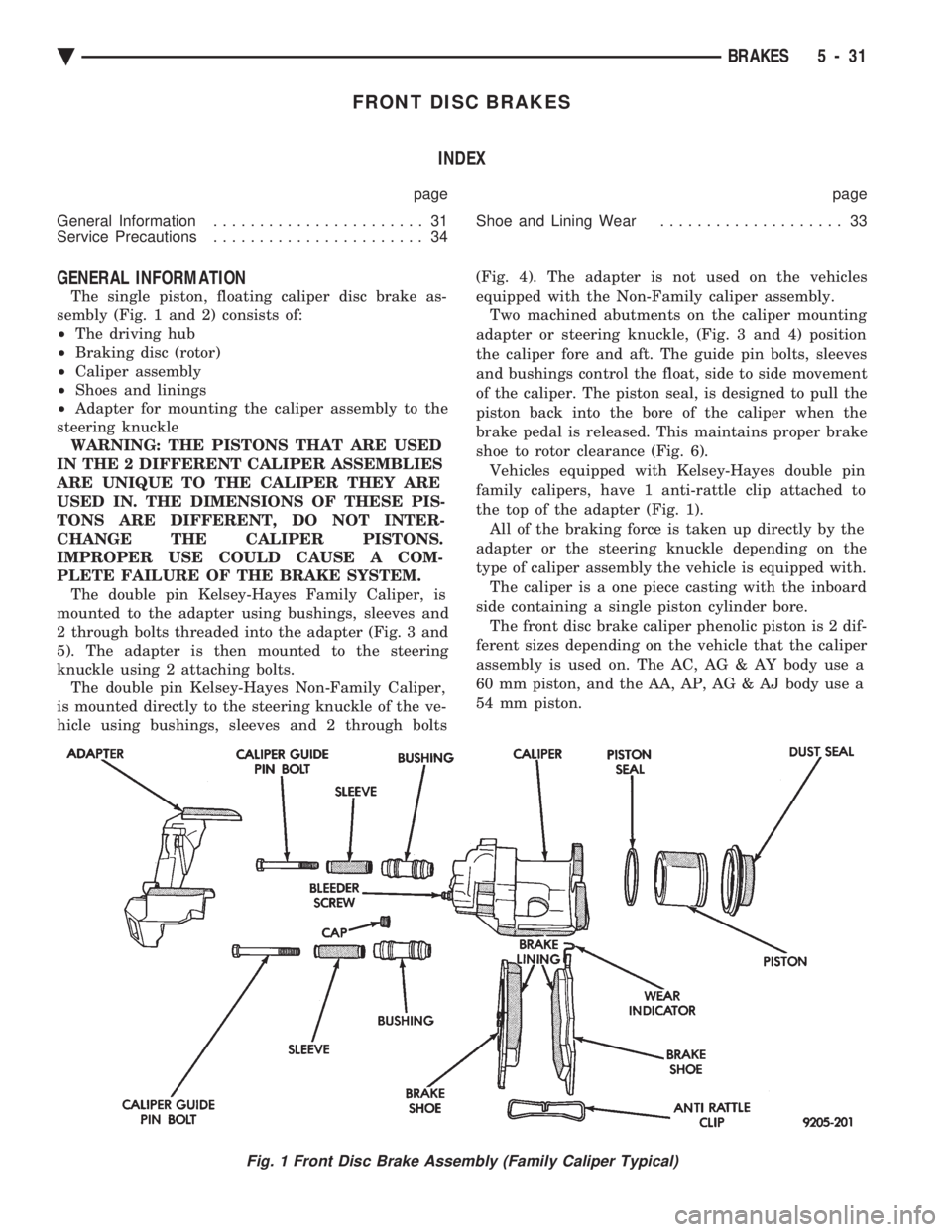
FRONT DISC BRAKES INDEX
page page
General Information ....................... 31
Service Precautions ....................... 34 Shoe and Lining Wear
.................... 33
GENERAL INFORMATION
The single piston, floating caliper disc brake as-
sembly (Fig. 1 and 2) consists of:
² The driving hub
² Braking disc (rotor)
² Caliper assembly
² Shoes and linings
² Adapter for mounting the caliper assembly to the
steering knuckle WARNING: THE PISTONS THAT ARE USED
IN THE 2 DIFFERENT CALIPER ASSEMBLIES
ARE UNIQUE TO THE CALIPER THEY ARE
USED IN. THE DIMENSIONS OF THESE PIS-
TONS ARE DIFFERENT, DO NOT INTER-
CHANGE THE CALIPER PISTONS.
IMPROPER USE COULD CAUSE A COM-
PLETE FAILURE OF THE BRAKE SYSTEM. The double pin Kelsey-Hayes Family Caliper, is
mounted to the adapter using bushings, sleeves and
2 through bolts threaded into the adapter (Fig. 3 and
5). The adapter is then mounted to the steering
knuckle using 2 attaching bolts. The double pin Kelsey-Hayes Non-Family Caliper,
is mounted directly to the steering knuckle of the ve-
hicle using bushings, sleeves and 2 through bolts (Fig. 4). The adapter is not used on the vehicles
equipped with the Non-Family caliper assembly.
Two machined abutments on the caliper mounting
adapter or steering knuckle, (Fig. 3 and 4) position
the caliper fore and aft. The guide pin bolts, sleeves
and bushings control the float, side to side movement
of the caliper. The piston seal, is designed to pull the
piston back into the bore of the caliper when the
brake pedal is released. This maintains proper brake
shoe to rotor clearance (Fig. 6). Vehicles equipped with Kelsey-Hayes double pin
family calipers, have 1 anti-rattle clip attached to
the top of the adapter (Fig. 1). All of the braking force is taken up directly by the
adapter or the steering knuckle depending on the
type of caliper assembly the vehicle is equipped with. The caliper is a one piece casting with the inboard
side containing a single piston cylinder bore. The front disc brake caliper phenolic piston is 2 dif-
ferent sizes depending on the vehicle that the caliper
assembly is used on. The AC, AG & AY body use a
60 mm piston, and the AA, AP, AG & AJ body use a
54 mm piston.
Fig. 1 Front Disc Brake Assembly (Family Caliper Typical)
Ä BRAKES 5 - 31
Page 182 of 2438
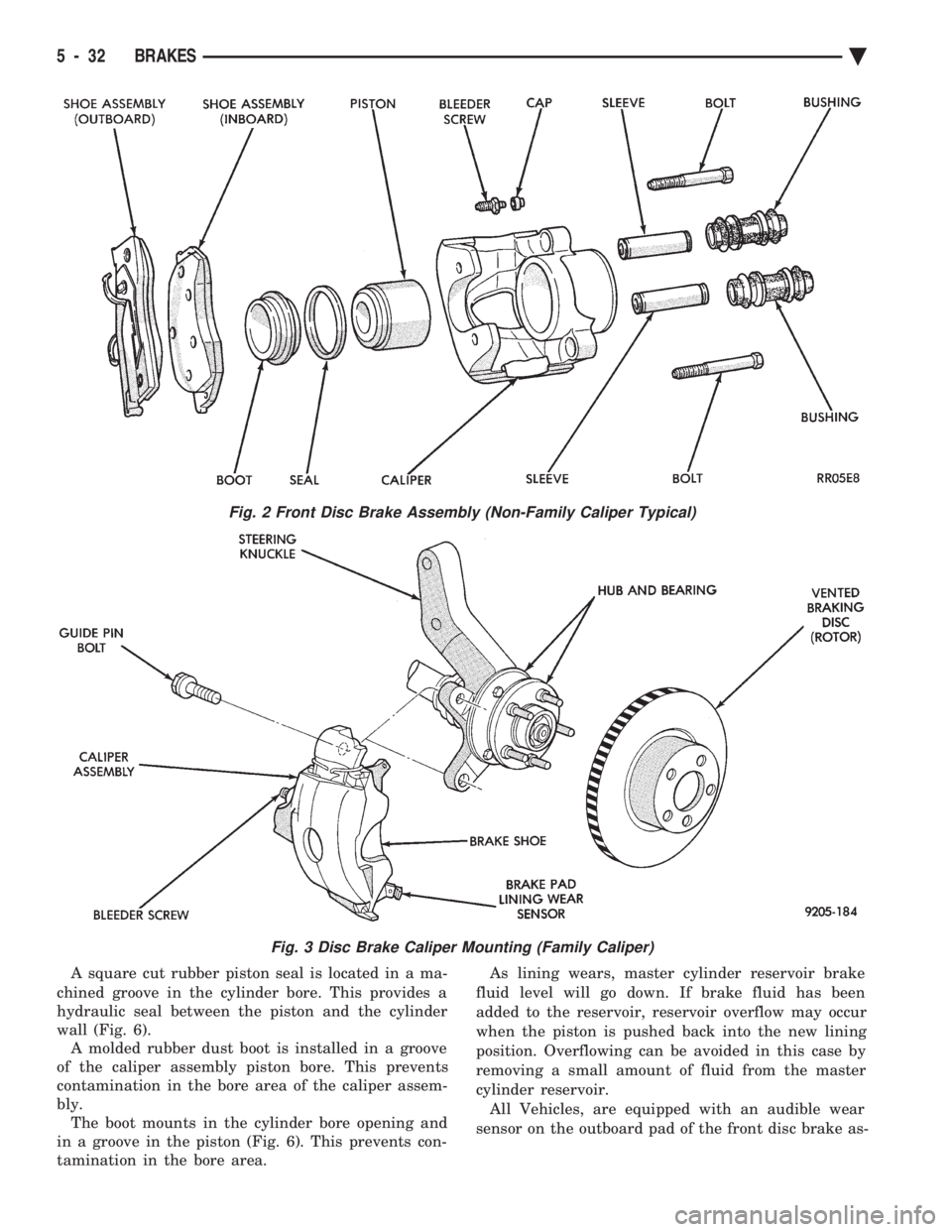
A square cut rubber piston seal is located in a ma-
chined groove in the cylinder bore. This provides a
hydraulic seal between the piston and the cylinder
wall (Fig. 6). A molded rubber dust boot is installed in a groove
of the caliper assembly piston bore. This prevents
contamination in the bore area of the caliper assem-
bly. The boot mounts in the cylinder bore opening and
in a groove in the piston (Fig. 6). This prevents con-
tamination in the bore area. As lining wears, master cylinder reservoir brake
fluid level will go down. If brake fluid has been
added to the reservoir, reservoir overflow may occur
when the piston is pushed back into the new lining
position. Overflowing can be avoided in this case by
removing a small amount of fluid from the master
cylinder reservoir. All Vehicles, are equipped with an audible wear
sensor on the outboard pad of the front disc brake as-
Fig. 2 Front Disc Brake Assembly (Non-Family Caliper Typical)
Fig. 3 Disc Brake Caliper Mounting (Family Caliper)
5 - 32 BRAKES Ä
Page 183 of 2438

semblies. This sensor when emitting a sound signals
that brake lining may need inspection and/or re-
placement.
SHOE AND LINING WEAR
If a visual inspection does not adequately deter-
mine the condition of the lining, a physical check
will be necessary. To check the amount of lining
wear, remove the wheel and tire assemblies, and the
calipers. Remove the shoe and lining assemblies. (See Brake
Shoe Removal paragraph). Combined shoe and lining thickness should be
measured at the thinnest part of the assembly. When a shoe and lining assembly is worn to a
thickness of approximately 7.95 mm (5/16 inch) it
should be replaced. Replace bothshoe assemblies (inboard and out-
board) on the front wheels. It is necessary that both
front wheel sets be replaced whenever shoe assem-
blies on either side are replaced. If a shoe assembly does not require replacement.
Reinstall, the shoe assemblies making sure each shoe
assembly is returned to the original position. (See
Brake Shoe Installation).
Fig. 4 Disc Brake Caliper Mounting (Non-Family Caliper)
Fig. 5 Disc Brake Caliper Mounting (Typical)
Fig. 6 Piston Seal Function for Automatic Adjustment
Ä BRAKES 5 - 33
Page 184 of 2438
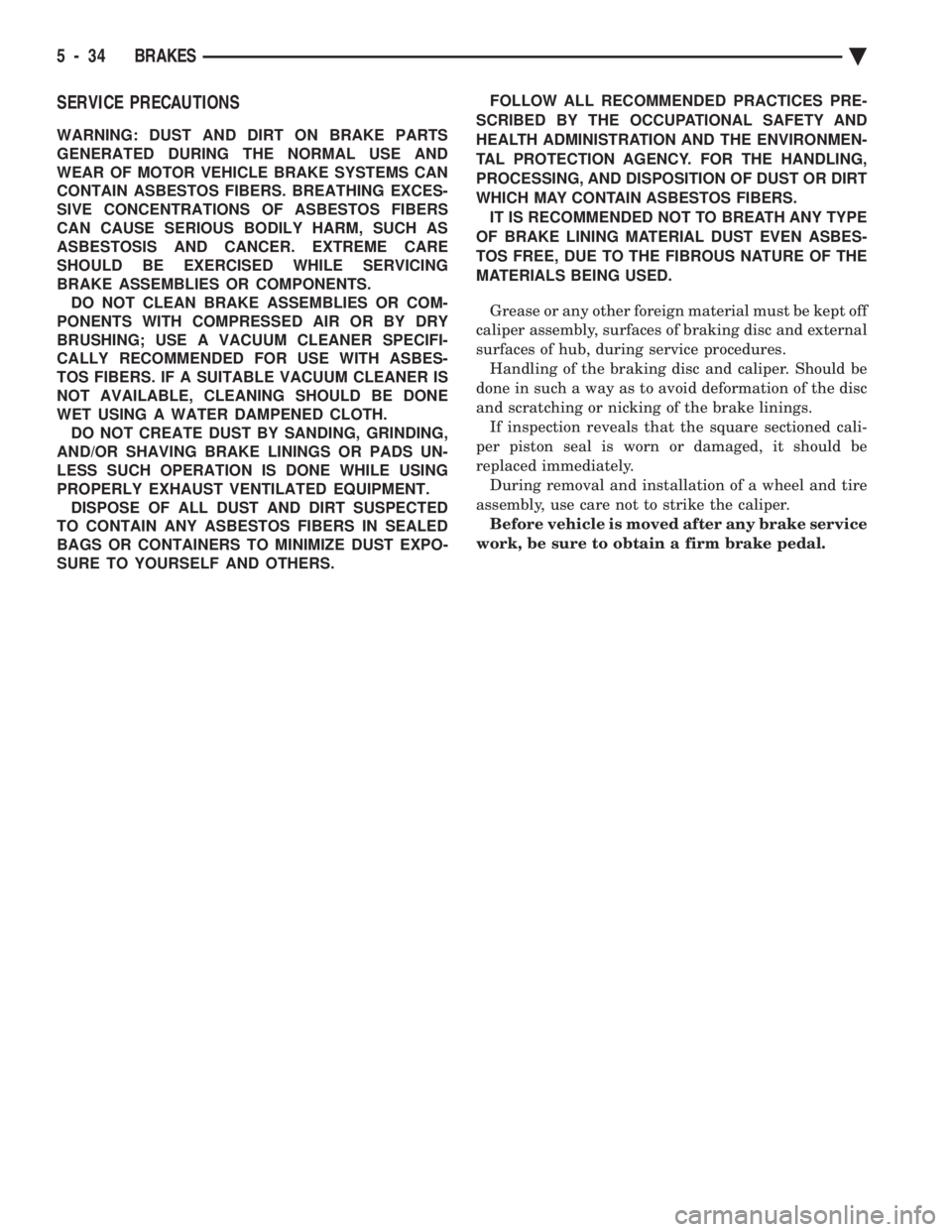
SERVICE PRECAUTIONS
WARNING: DUST AND DIRT ON BRAKE PARTS
GENERATED DURING THE NORMAL USE AND
WEAR OF MOTOR VEHICLE BRAKE SYSTEMS CAN
CONTAIN ASBESTOS FIBERS. BREATHING EXCES-
SIVE CONCENTRATIONS OF ASBESTOS FIBERS
CAN CAUSE SERIOUS BODILY HARM, SUCH AS
ASBESTOSIS AND CANCER. EXTREME CARE
SHOULD BE EXERCISED WHILE SERVICING
BRAKE ASSEMBLIES OR COMPONENTS. DO NOT CLEAN BRAKE ASSEMBLIES OR COM-
PONENTS WITH COMPRESSED AIR OR BY DRY
BRUSHING; USE A VACUUM CLEANER SPECIFI-
CALLY RECOMMENDED FOR USE WITH ASBES-
TOS FIBERS. IF A SUITABLE VACUUM CLEANER IS
NOT AVAILABLE, CLEANING SHOULD BE DONE
WET USING A WATER DAMPENED CLOTH. DO NOT CREATE DUST BY SANDING, GRINDING,
AND/OR SHAVING BRAKE LININGS OR PADS UN-
LESS SUCH OPERATION IS DONE WHILE USING
PROPERLY EXHAUST VENTILATED EQUIPMENT. DISPOSE OF ALL DUST AND DIRT SUSPECTED
TO CONTAIN ANY ASBESTOS FIBERS IN SEALED
BAGS OR CONTAINERS TO MINIMIZE DUST EXPO-
SURE TO YOURSELF AND OTHERS. FOLLOW ALL RECOMMENDED PRACTICES PRE-
SCRIBED BY THE OCCUPATIONAL SAFETY AND
HEALTH ADMINISTRATION AND THE ENVIRONMEN-
TAL PROTECTION AGENCY. FOR THE HANDLING,
PROCESSING, AND DISPOSITION OF DUST OR DIRT
WHICH MAY CONTAIN ASBESTOS FIBERS. IT IS RECOMMENDED NOT TO BREATH ANY TYPE
OF BRAKE LINING MATERIAL DUST EVEN ASBES-
TOS FREE, DUE TO THE FIBROUS NATURE OF THE
MATERIALS BEING USED.
Grease or any other foreign material must be kept off
caliper assembly, surfaces of braking disc and external
surfaces of hub, during service procedures. Handling of the braking disc and caliper. Should be
done in such a way as to avoid deformation of the disc
and scratching or nicking of the brake linings. If inspection reveals that the square sectioned cali-
per piston seal is worn or damaged, it should be
replaced immediately. During removal and installation of a wheel and tire
assembly, use care not to strike the caliper. Before vehicle is moved after any brake service
work, be sure to obtain a firm brake pedal.
5 - 34 BRAKES Ä
Page 185 of 2438
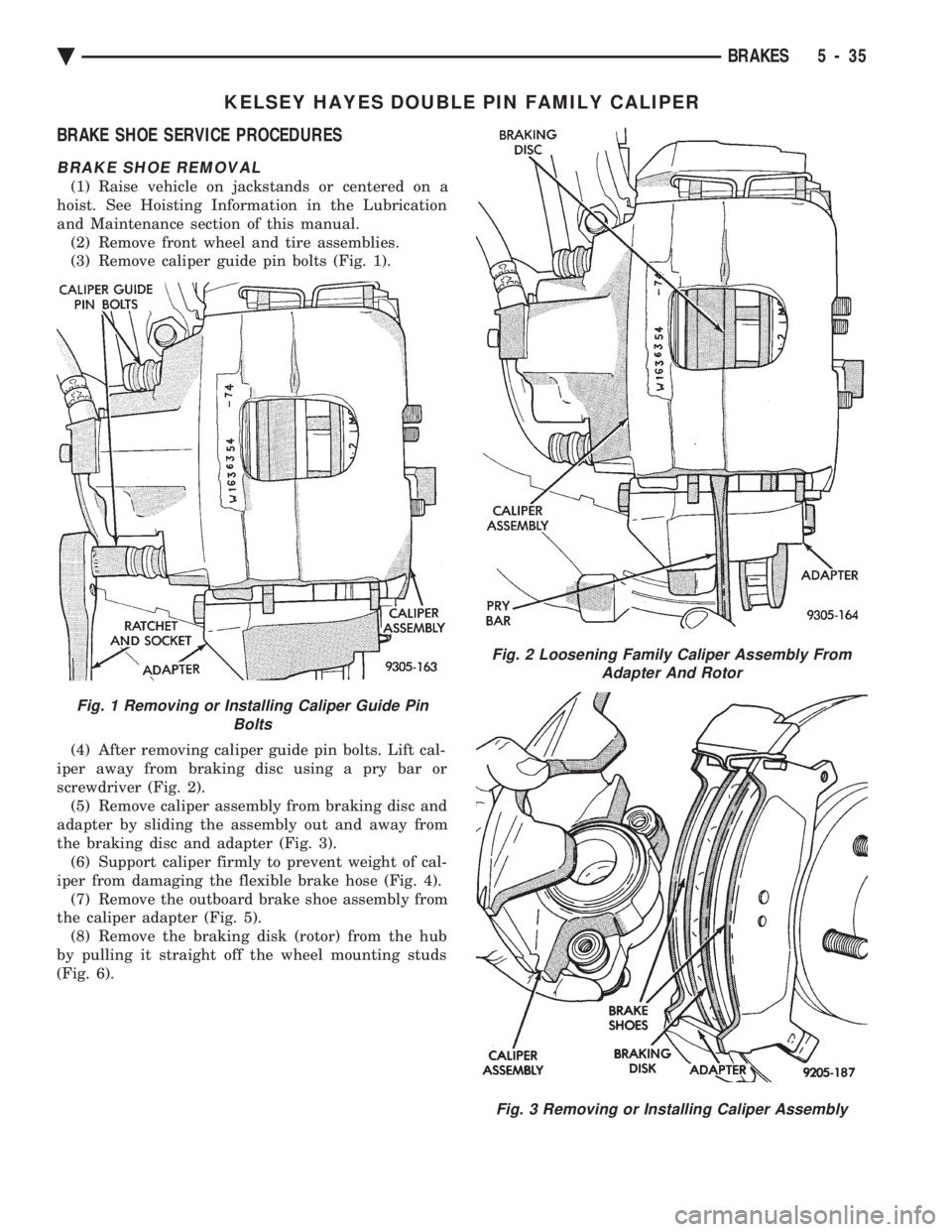
KELSEY HAYES DOUBLE PIN FAMILY CALIPER
BRAKE SHOE SERVICE PROCEDURES
BRAKE SHOE REMOVAL
(1) Raise vehicle on jackstands or centered on a
hoist. See Hoisting Information in the Lubrication
and Maintenance section of this manual. (2) Remove front wheel and tire assemblies.
(3) Remove caliper guide pin bolts (Fig. 1).
(4) After removing caliper guide pin bolts. Lift cal-
iper away from braking disc using a pry bar or
screwdriver (Fig. 2). (5) Remove caliper assembly from braking disc and
adapter by sliding the assembly out and away from
the braking disc and adapter (Fig. 3). (6) Support caliper firmly to prevent weight of cal-
iper from damaging the flexible brake hose (Fig. 4). (7) Remove the outboard brake shoe assembly from
the caliper adapter (Fig. 5). (8) Remove the braking disk (rotor) from the hub
by pulling it straight off the wheel mounting studs
(Fig. 6).
Fig. 1 Removing or Installing Caliper Guide Pin Bolts
Fig. 2 Loosening Family Caliper Assembly FromAdapter And Rotor
Fig. 3 Removing or Installing Caliper Assembly
Ä BRAKES 5 - 35
Page 186 of 2438
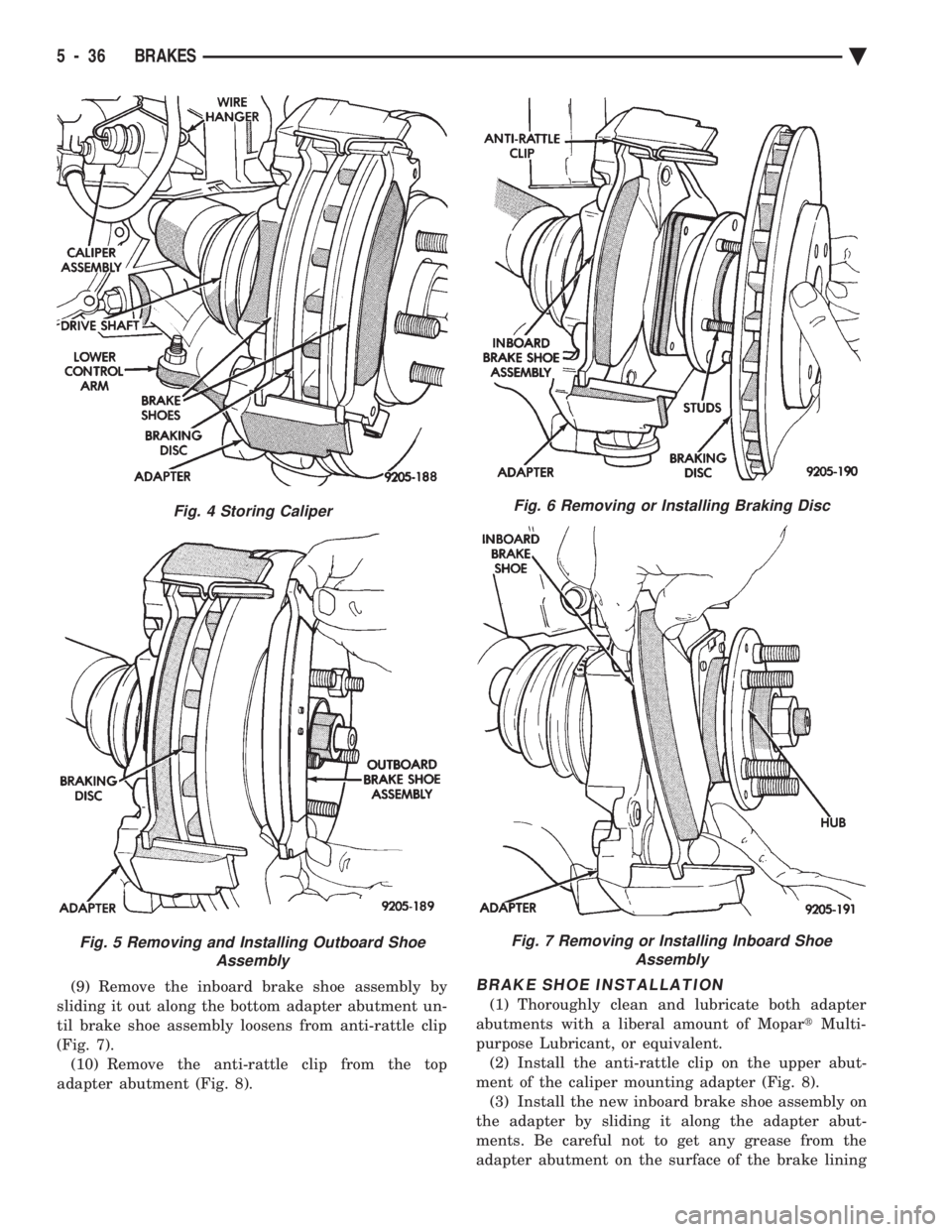
(9) Remove the inboard brake shoe assembly by
sliding it out along the bottom adapter abutment un-
til brake shoe assembly loosens from anti-rattle clip
(Fig. 7). (10) Remove the anti-rattle clip from the top
adapter abutment (Fig. 8).BRAKE SHOE INSTALLATION
(1) Thoroughly clean and lubricate both adapter
abutments with a liberal amount of Mopar tMulti-
purpose Lubricant, or equivalent. (2) Install the anti-rattle clip on the upper abut-
ment of the caliper mounting adapter (Fig. 8). (3) Install the new inboard brake shoe assembly on
the adapter by sliding it along the adapter abut-
ments. Be careful not to get any grease from the
adapter abutment on the surface of the brake lining
Fig. 4 Storing Caliper
Fig. 5 Removing and Installing Outboard Shoe Assembly
Fig. 6 Removing or Installing Braking Disc
Fig. 7 Removing or Installing Inboard ShoeAssembly
5 - 36 BRAKES Ä
Page 187 of 2438
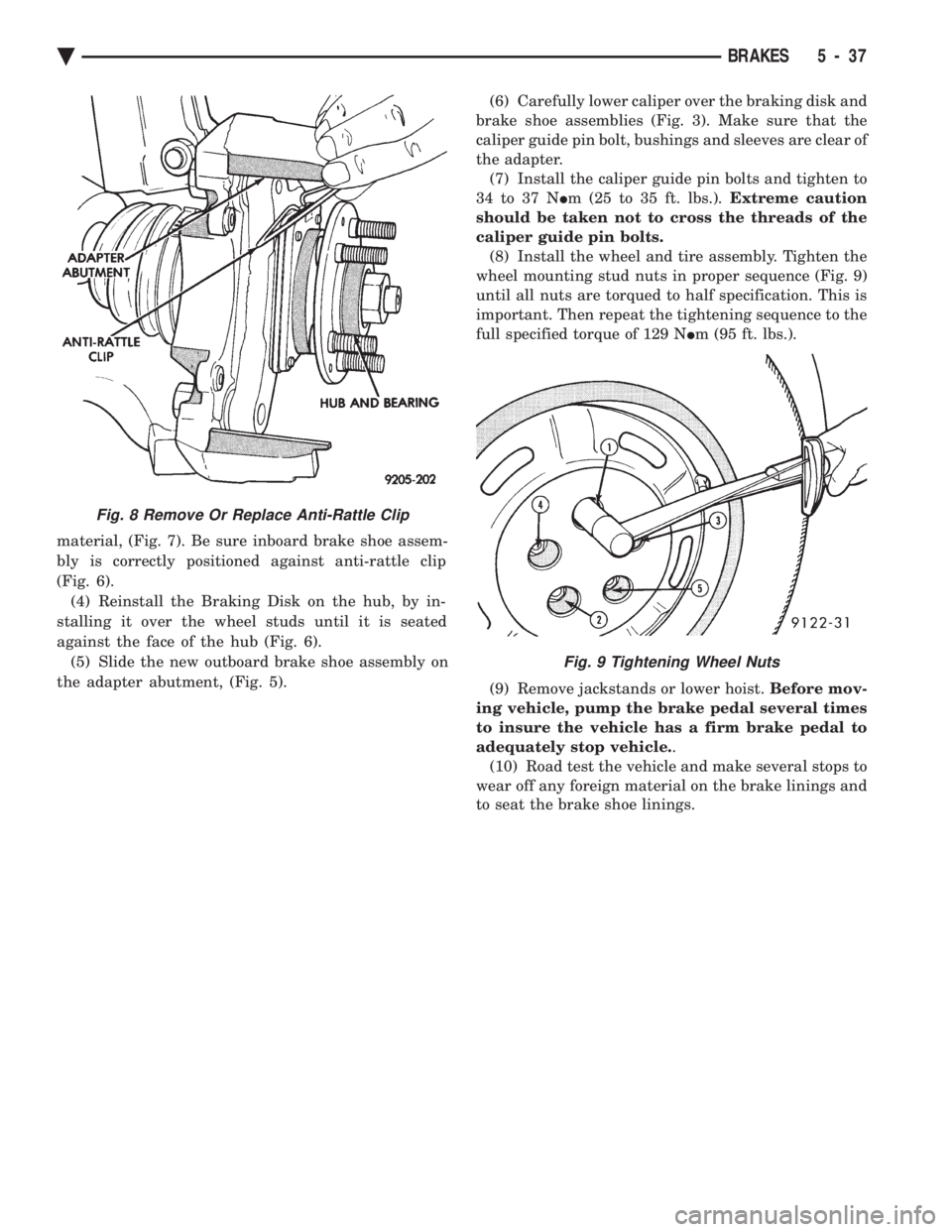
material, (Fig. 7). Be sure inboard brake shoe assem-
bly is correctly positioned against anti-rattle clip
(Fig. 6). (4) Reinstall the Braking Disk on the hub, by in-
stalling it over the wheel studs until it is seated
against the face of the hub (Fig. 6). (5) Slide the new outboard brake shoe assembly on
the adapter abutment, (Fig. 5). (6) Carefully lower caliper over the braking disk and
brake shoe assemblies (Fig. 3). Make sure that the
caliper guide pin bolt, bushings and sleeves are clear of
the adapter. (7) Install the caliper guide pin bolts and tighten to
34 to 37 N Im (25 to 35 ft. lbs.). Extreme caution
should be taken not to cross the threads of the
caliper guide pin bolts. (8) Install the wheel and tire assembly. Tighten the
wheel mounting stud nuts in proper sequence (Fig. 9)
until all nuts are torqued to half specification. This is
important. Then repeat the tightening sequence to the
full specified torque of 129 N Im (95 ft. lbs.).
(9) Remove jackstands or lower hoist. Before mov-
ing vehicle, pump the brake pedal several times
to insure the vehicle has a firm brake pedal to
adequately stop vehicle. .
(10) Road test the vehicle and make several stops to
wear off any foreign material on the brake linings and
to seat the brake shoe linings.
Fig. 8 Remove Or Replace Anti-Rattle Clip
Fig. 9 Tightening Wheel Nuts
Ä BRAKES 5 - 37
Page 188 of 2438
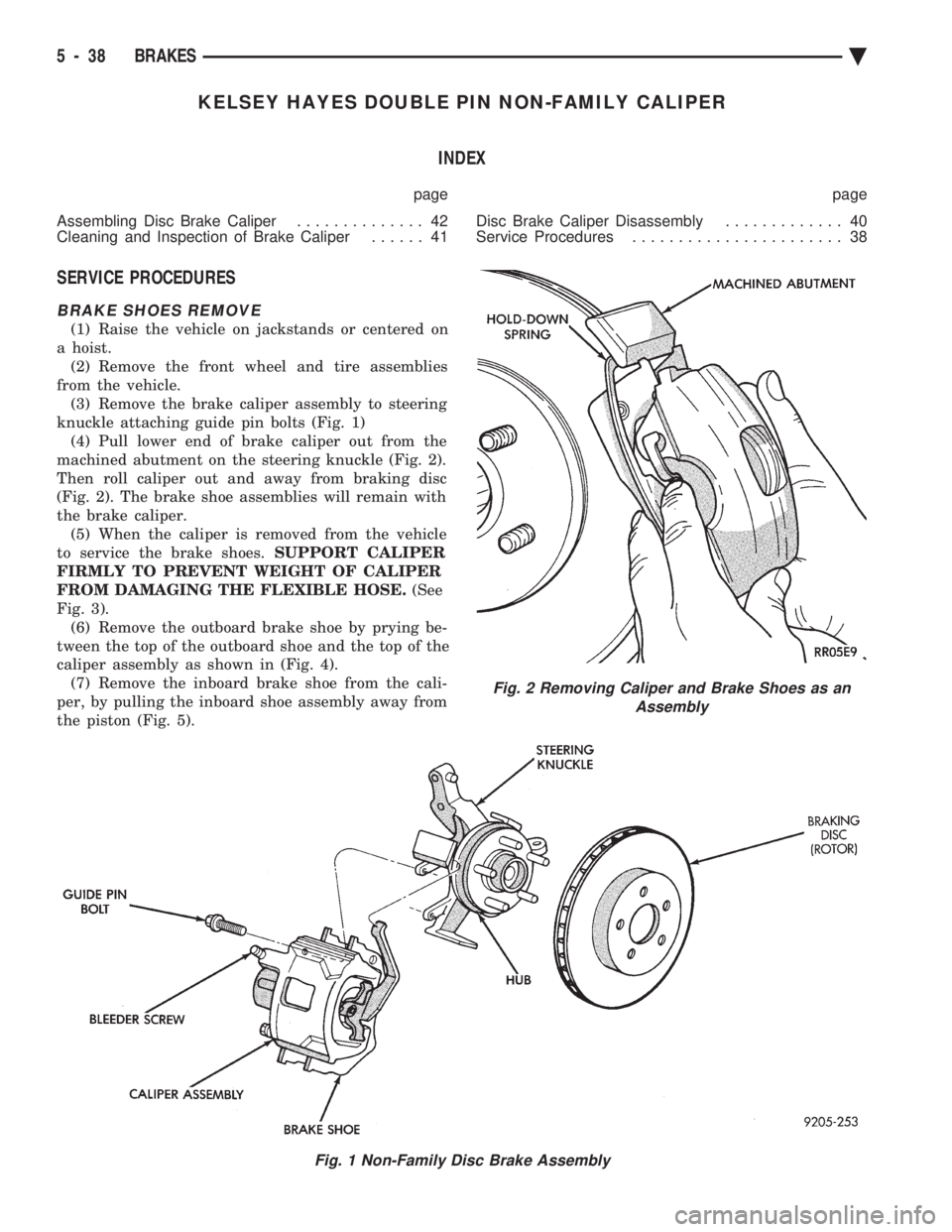
KELSEY HAYES DOUBLE PIN NON-FAMILY CALIPER INDEX
page page
Assembling Disc Brake Caliper .............. 42
Cleaning and Inspection of Brake Caliper ...... 41 Disc Brake Caliper Disassembly
............. 40
Service Procedures ....................... 38
SERVICE PROCEDURES
BRAKE SHOES REMOVE
(1) Raise the vehicle on jackstands or centered on
a hoist. (2) Remove the front wheel and tire assemblies
from the vehicle. (3) Remove the brake caliper assembly to steering
knuckle attaching guide pin bolts (Fig. 1) (4) Pull lower end of brake caliper out from the
machined abutment on the steering knuckle (Fig. 2).
Then roll caliper out and away from braking disc
(Fig. 2). The brake shoe assemblies will remain with
the brake caliper. (5) When the caliper is removed from the vehicle
to service the brake shoes. SUPPORT CALIPER
FIRMLY TO PREVENT WEIGHT OF CALIPER
FROM DAMAGING THE FLEXIBLE HOSE. (See
Fig. 3). (6) Remove the outboard brake shoe by prying be-
tween the top of the outboard shoe and the top of the
caliper assembly as shown in (Fig. 4). (7) Remove the inboard brake shoe from the cali-
per, by pulling the inboard shoe assembly away from
the piston (Fig. 5).
Fig. 1 Non-Family Disc Brake Assembly
Fig. 2 Removing Caliper and Brake Shoes as an Assembly
5 - 38 BRAKES Ä
Page 189 of 2438
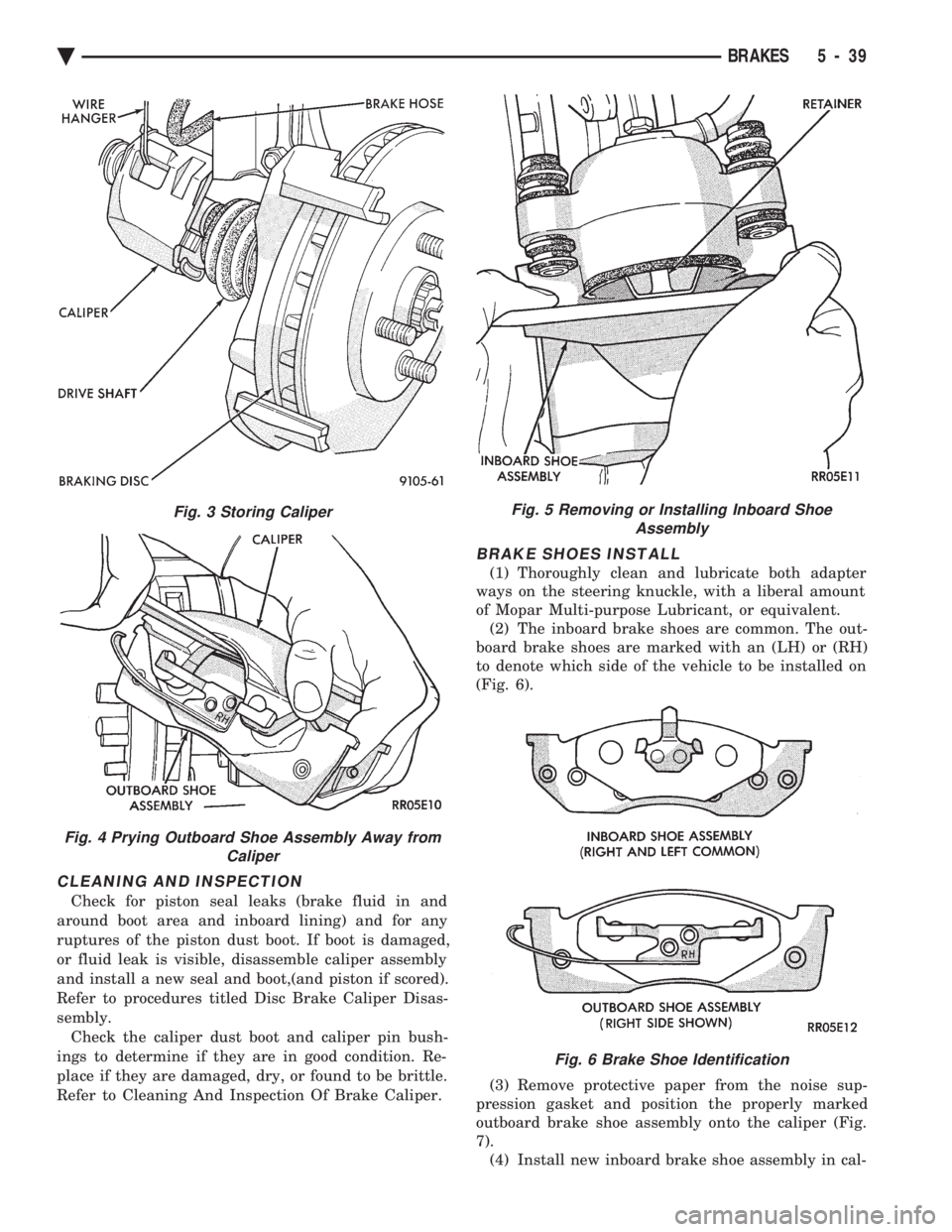
CLEANING AND INSPECTION
Check for piston seal leaks (brake fluid in and
around boot area and inboard lining) and for any
ruptures of the piston dust boot. If boot is damaged,
or fluid leak is visible, disassemble caliper assembly
and install a new seal and boot,(and piston if scored).
Refer to procedures titled Disc Brake Caliper Disas-
sembly. Check the caliper dust boot and caliper pin bush-
ings to determine if they are in good condition. Re-
place if they are damaged, dry, or found to be brittle.
Refer to Cleaning And Inspection Of Brake Caliper.
BRAKE SHOES INSTALL
(1) Thoroughly clean and lubricate both adapter
ways on the steering knuckle, with a liberal amount
of Mopar Multi-purpose Lubricant, or equivalent. (2) The inboard brake shoes are common. The out-
board brake shoes are marked with an (LH) or (RH)
to denote which side of the vehicle to be installed on
(Fig. 6).
(3) Remove protective paper from the noise sup-
pression gasket and position the properly marked
outboard brake shoe assembly onto the caliper (Fig.
7). (4) Install new inboard brake shoe assembly in cal-
Fig. 3 Storing Caliper
Fig. 4 Prying Outboard Shoe Assembly Away from Caliper
Fig. 5 Removing or Installing Inboard ShoeAssembly
Fig. 6 Brake Shoe Identification
Ä BRAKES 5 - 39
Page 190 of 2438
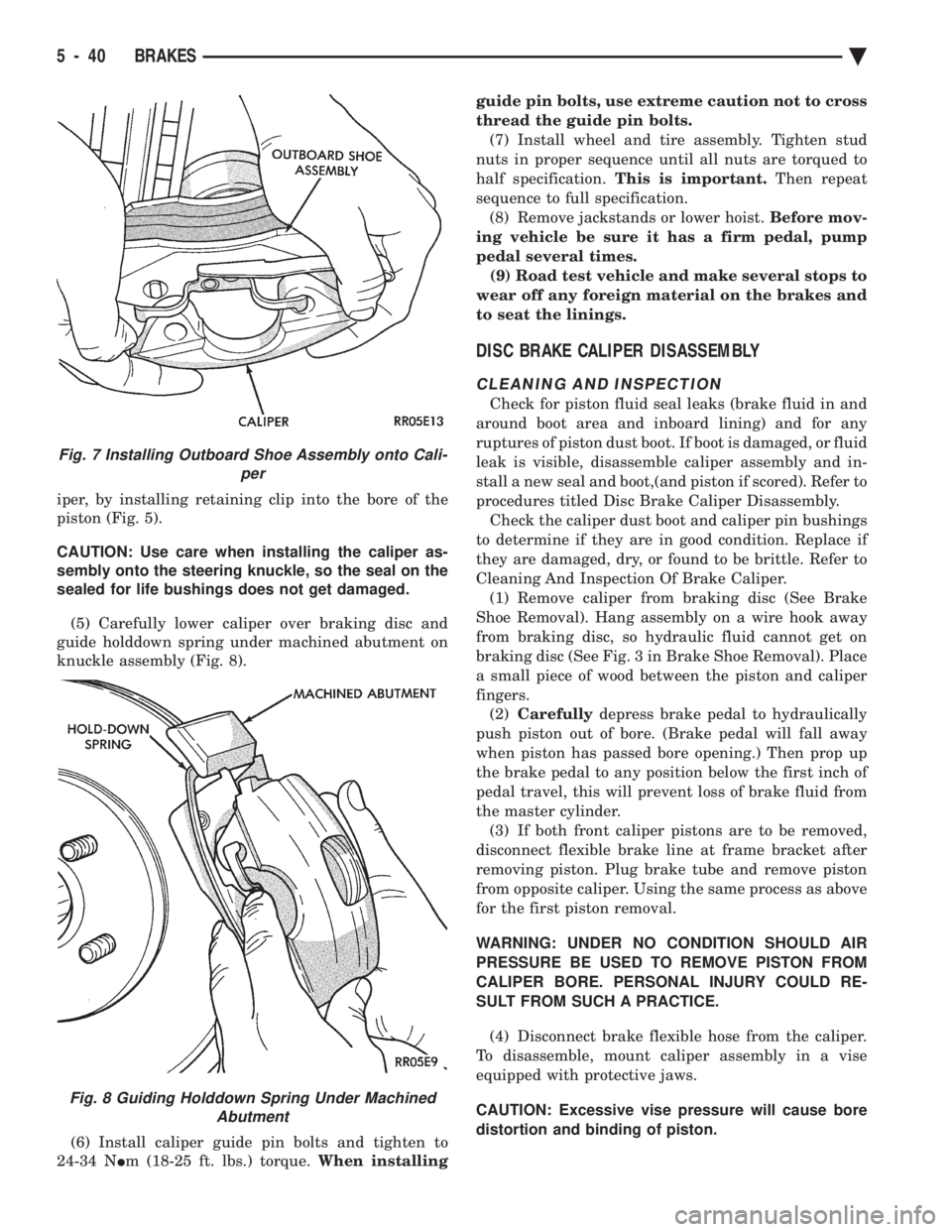
iper, by installing retaining clip into the bore of the
piston (Fig. 5).
CAUTION: Use care when installing the caliper as-
sembly onto the steering knuckle, so the seal on the
sealed for life bushings does not get damaged.
(5) Carefully lower caliper over braking disc and
guide holddown spring under machined abutment on
knuckle assembly (Fig. 8).
(6) Install caliper guide pin bolts and tighten to
24-34 N Im (18-25 ft. lbs.) torque. When installing guide pin bolts, use extreme caution not to cross
thread the guide pin bolts.
(7) Install wheel and tire assembly. Tighten stud
nuts in proper sequence until all nuts are torqued to
half specification. This is important. Then repeat
sequence to full specification. (8) Remove jackstands or lower hoist. Before mov-
ing vehicle be sure it has a firm pedal, pump
pedal several times. (9) Road test vehicle and make several stops to
wear off any foreign material on the brakes and
to seat the linings.
DISC BRAKE CALIPER DISASSEMBLY
CLEANING AND INSPECTION
Check for piston fluid seal leaks (brake fluid in and
around boot area and inboard lining) and for any
ruptures of piston dust boot. If boot is damaged, or fluid
leak is visible, disassemble caliper assembly and in-
stall a new seal and boot,(and piston if scored). Refer to
procedures titled Disc Brake Caliper Disassembly. Check the caliper dust boot and caliper pin bushings
to determine if they are in good condition. Replace if
they are damaged, dry, or found to be brittle. Refer to
Cleaning And Inspection Of Brake Caliper. (1) Remove caliper from braking disc (See Brake
Shoe Removal). Hang assembly on a wire hook away
from braking disc, so hydraulic fluid cannot get on
braking disc (See Fig. 3 in Brake Shoe Removal). Place
a small piece of wood between the piston and caliper
fingers. (2) Carefully depress brake pedal to hydraulically
push piston out of bore. (Brake pedal will fall away
when piston has passed bore opening.) Then prop up
the brake pedal to any position below the first inch of
pedal travel, this will prevent loss of brake fluid from
the master cylinder. (3) If both front caliper pistons are to be removed,
disconnect flexible brake line at frame bracket after
removing piston. Plug brake tube and remove piston
from opposite caliper. Using the same process as above
for the first piston removal.
WARNING: UNDER NO CONDITION SHOULD AIR
PRESSURE BE USED TO REMOVE PISTON FROM
CALIPER BORE. PERSONAL INJURY COULD RE-
SULT FROM SUCH A PRACTICE.
(4) Disconnect brake flexible hose from the caliper.
To disassemble, mount caliper assembly in a vise
equipped with protective jaws.
CAUTION: Excessive vise pressure will cause bore
distortion and binding of piston.
Fig. 7 Installing Outboard Shoe Assembly onto Cali- per
Fig. 8 Guiding Holddown Spring Under MachinedAbutment
5 - 40 BRAKES Ä