fuse CHRYSLER CARAVAN 2003 Service Manual
[x] Cancel search | Manufacturer: CHRYSLER, Model Year: 2003, Model line: CARAVAN, Model: CHRYSLER CARAVAN 2003Pages: 2177, PDF Size: 59.81 MB
Page 1695 of 2177
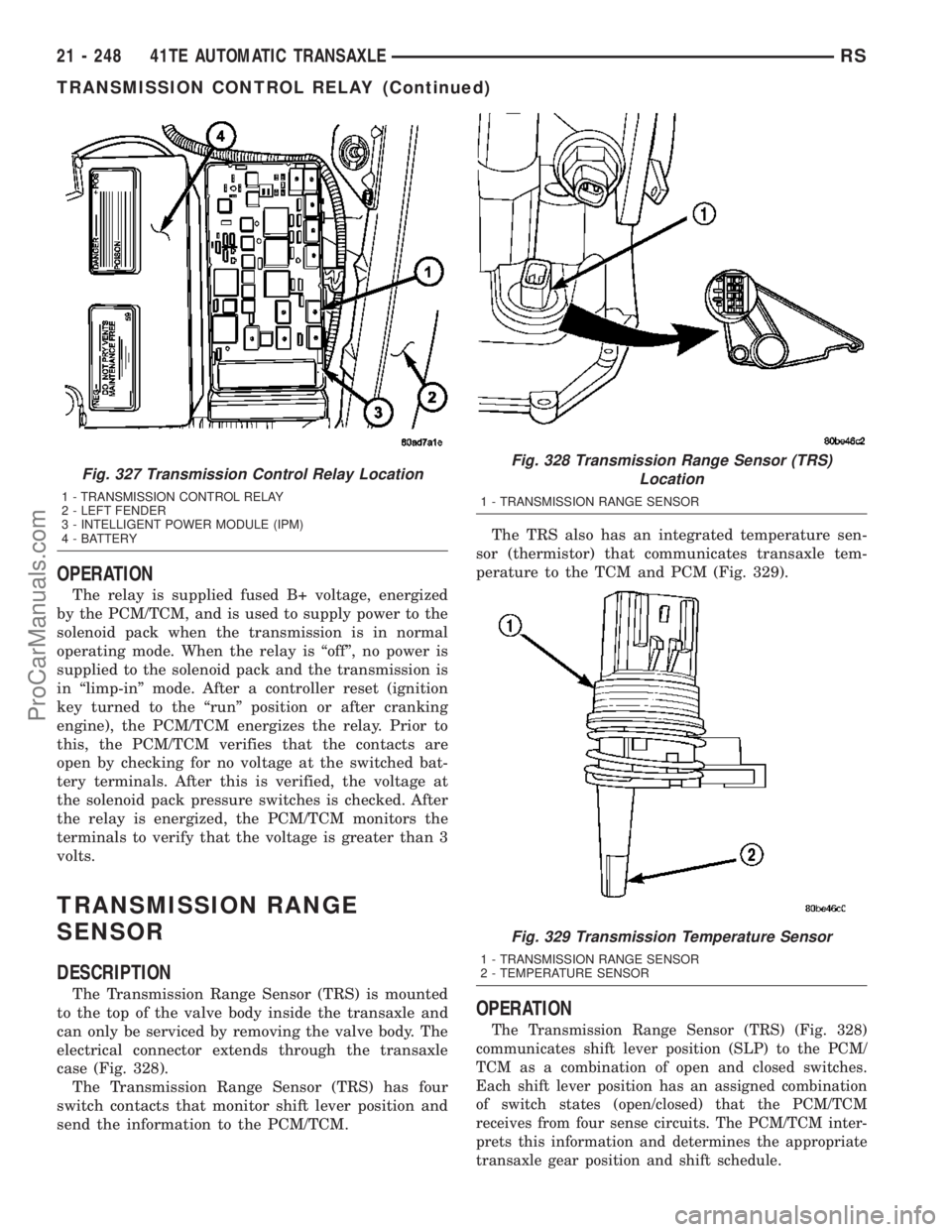
OPERATION
The relay is supplied fused B+ voltage, energized
by the PCM/TCM, and is used to supply power to the
solenoid pack when the transmission is in normal
operating mode. When the relay is ªoffº, no power is
supplied to the solenoid pack and the transmission is
in ªlimp-inº mode. After a controller reset (ignition
key turned to the ªrunº position or after cranking
engine), the PCM/TCM energizes the relay. Prior to
this, the PCM/TCM verifies that the contacts are
open by checking for no voltage at the switched bat-
tery terminals. After this is verified, the voltage at
the solenoid pack pressure switches is checked. After
the relay is energized, the PCM/TCM monitors the
terminals to verify that the voltage is greater than 3
volts.
TRANSMISSION RANGE
SENSOR
DESCRIPTION
The Transmission Range Sensor (TRS) is mounted
to the top of the valve body inside the transaxle and
can only be serviced by removing the valve body. The
electrical connector extends through the transaxle
case (Fig. 328).
The Transmission Range Sensor (TRS) has four
switch contacts that monitor shift lever position and
send the information to the PCM/TCM.The TRS also has an integrated temperature sen-
sor (thermistor) that communicates transaxle tem-
perature to the TCM and PCM (Fig. 329).
OPERATION
The Transmission Range Sensor (TRS) (Fig. 328)
communicates shift lever position (SLP) to the PCM/
TCM as a combination of open and closed switches.
Each shift lever position has an assigned combination
of switch states (open/closed) that the PCM/TCM
receives from four sense circuits. The PCM/TCM inter-
prets this information and determines the appropriate
transaxle gear position and shift schedule.
Fig. 327 Transmission Control Relay Location
1 - TRANSMISSION CONTROL RELAY
2 - LEFT FENDER
3 - INTELLIGENT POWER MODULE (IPM)
4 - BATTERY
Fig. 328 Transmission Range Sensor (TRS)
Location
1 - TRANSMISSION RANGE SENSOR
Fig. 329 Transmission Temperature Sensor
1 - TRANSMISSION RANGE SENSOR
2 - TEMPERATURE SENSOR
21 - 248 41TE AUTOMATIC TRANSAXLERS
TRANSMISSION CONTROL RELAY (Continued)
ProCarManuals.com
Page 2010 of 2177
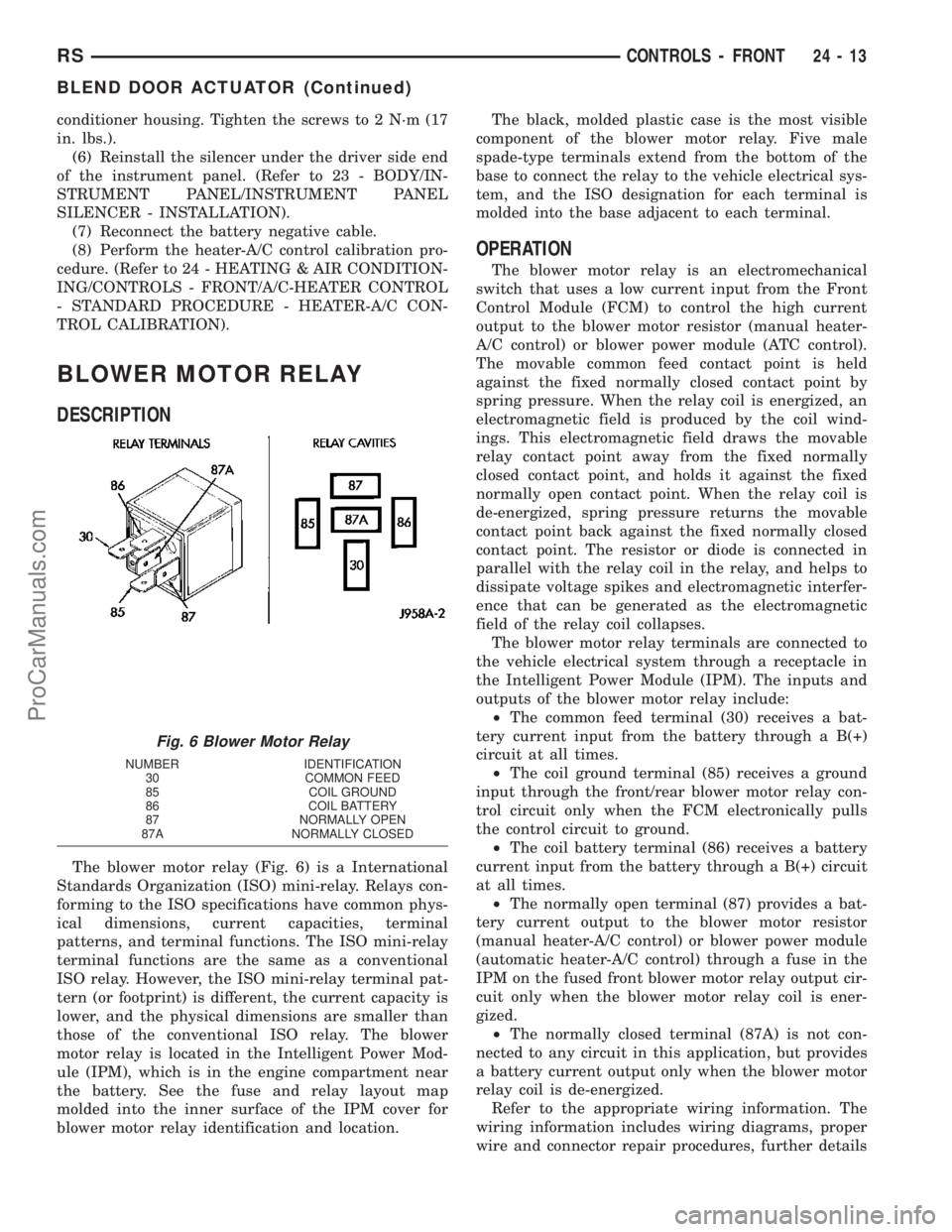
conditioner housing. Tighten the screws to 2 N´m (17
in. lbs.).
(6) Reinstall the silencer under the driver side end
of the instrument panel. (Refer to 23 - BODY/IN-
STRUMENT PANEL/INSTRUMENT PANEL
SILENCER - INSTALLATION).
(7) Reconnect the battery negative cable.
(8) Perform the heater-A/C control calibration pro-
cedure. (Refer to 24 - HEATING & AIR CONDITION-
ING/CONTROLS - FRONT/A/C-HEATER CONTROL
- STANDARD PROCEDURE - HEATER-A/C CON-
TROL CALIBRATION).
BLOWER MOTOR RELAY
DESCRIPTION
The blower motor relay (Fig. 6) is a International
Standards Organization (ISO) mini-relay. Relays con-
forming to the ISO specifications have common phys-
ical dimensions, current capacities, terminal
patterns, and terminal functions. The ISO mini-relay
terminal functions are the same as a conventional
ISO relay. However, the ISO mini-relay terminal pat-
tern (or footprint) is different, the current capacity is
lower, and the physical dimensions are smaller than
those of the conventional ISO relay. The blower
motor relay is located in the Intelligent Power Mod-
ule (IPM), which is in the engine compartment near
the battery. See the fuse and relay layout map
molded into the inner surface of the IPM cover for
blower motor relay identification and location.The black, molded plastic case is the most visible
component of the blower motor relay. Five male
spade-type terminals extend from the bottom of the
base to connect the relay to the vehicle electrical sys-
tem, and the ISO designation for each terminal is
molded into the base adjacent to each terminal.
OPERATION
The blower motor relay is an electromechanical
switch that uses a low current input from the Front
Control Module (FCM) to control the high current
output to the blower motor resistor (manual heater-
A/C control) or blower power module (ATC control).
The movable common feed contact point is held
against the fixed normally closed contact point by
spring pressure. When the relay coil is energized, an
electromagnetic field is produced by the coil wind-
ings. This electromagnetic field draws the movable
relay contact point away from the fixed normally
closed contact point, and holds it against the fixed
normally open contact point. When the relay coil is
de-energized, spring pressure returns the movable
contact point back against the fixed normally closed
contact point. The resistor or diode is connected in
parallel with the relay coil in the relay, and helps to
dissipate voltage spikes and electromagnetic interfer-
ence that can be generated as the electromagnetic
field of the relay coil collapses.
The blower motor relay terminals are connected to
the vehicle electrical system through a receptacle in
the Intelligent Power Module (IPM). The inputs and
outputs of the blower motor relay include:
²The common feed terminal (30) receives a bat-
tery current input from the battery through a B(+)
circuit at all times.
²The coil ground terminal (85) receives a ground
input through the front/rear blower motor relay con-
trol circuit only when the FCM electronically pulls
the control circuit to ground.
²The coil battery terminal (86) receives a battery
current input from the battery through a B(+) circuit
at all times.
²The normally open terminal (87) provides a bat-
tery current output to the blower motor resistor
(manual heater-A/C control) or blower power module
(automatic heater-A/C control) through a fuse in the
IPM on the fused front blower motor relay output cir-
cuit only when the blower motor relay coil is ener-
gized.
²The normally closed terminal (87A) is not con-
nected to any circuit in this application, but provides
a battery current output only when the blower motor
relay coil is de-energized.
Refer to the appropriate wiring information. The
wiring information includes wiring diagrams, proper
wire and connector repair procedures, further details
Fig. 6 Blower Motor Relay
NUMBER IDENTIFICATION
30 COMMON FEED
85 COIL GROUND
86 COIL BATTERY
87 NORMALLY OPEN
87A NORMALLY CLOSED
RSCONTROLS - FRONT24-13
BLEND DOOR ACTUATOR (Continued)
ProCarManuals.com
Page 2011 of 2177
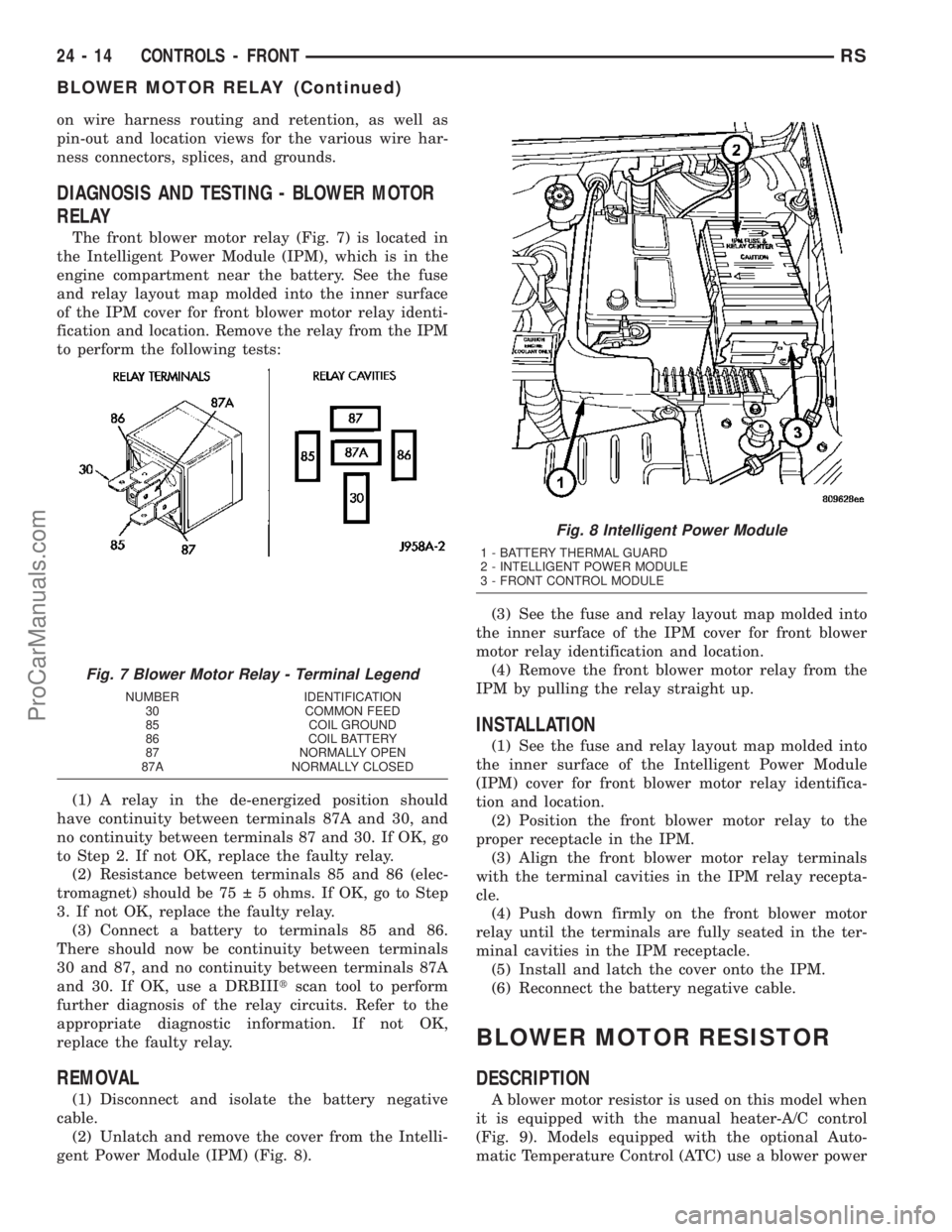
on wire harness routing and retention, as well as
pin-out and location views for the various wire har-
ness connectors, splices, and grounds.
DIAGNOSIS AND TESTING - BLOWER MOTOR
RELAY
The front blower motor relay (Fig. 7) is located in
the Intelligent Power Module (IPM), which is in the
engine compartment near the battery. See the fuse
and relay layout map molded into the inner surface
of the IPM cover for front blower motor relay identi-
fication and location. Remove the relay from the IPM
to perform the following tests:
(1) A relay in the de-energized position should
have continuity between terminals 87A and 30, and
no continuity between terminals 87 and 30. If OK, go
to Step 2. If not OK, replace the faulty relay.
(2) Resistance between terminals 85 and 86 (elec-
tromagnet) should be 75 Â 5 ohms. If OK, go to Step
3. If not OK, replace the faulty relay.
(3) Connect a battery to terminals 85 and 86.
There should now be continuity between terminals
30 and 87, and no continuity between terminals 87A
and 30. If OK, use a DRBIIItscan tool to perform
further diagnosis of the relay circuits. Refer to the
appropriate diagnostic information. If not OK,
replace the faulty relay.
REMOVAL
(1) Disconnect and isolate the battery negative
cable.
(2) Unlatch and remove the cover from the Intelli-
gent Power Module (IPM) (Fig. 8).(3) See the fuse and relay layout map molded into
the inner surface of the IPM cover for front blower
motor relay identification and location.
(4) Remove the front blower motor relay from the
IPM by pulling the relay straight up.
INSTALLATION
(1) See the fuse and relay layout map molded into
the inner surface of the Intelligent Power Module
(IPM) cover for front blower motor relay identifica-
tion and location.
(2) Position the front blower motor relay to the
proper receptacle in the IPM.
(3) Align the front blower motor relay terminals
with the terminal cavities in the IPM relay recepta-
cle.
(4) Push down firmly on the front blower motor
relay until the terminals are fully seated in the ter-
minal cavities in the IPM receptacle.
(5) Install and latch the cover onto the IPM.
(6) Reconnect the battery negative cable.
BLOWER MOTOR RESISTOR
DESCRIPTION
A blower motor resistor is used on this model when
it is equipped with the manual heater-A/C control
(Fig. 9). Models equipped with the optional Auto-
matic Temperature Control (ATC) use a blower power
Fig. 7 Blower Motor Relay - Terminal Legend
NUMBER IDENTIFICATION
30 COMMON FEED
85 COIL GROUND
86 COIL BATTERY
87 NORMALLY OPEN
87A NORMALLY CLOSED
Fig. 8 Intelligent Power Module
1 - BATTERY THERMAL GUARD
2 - INTELLIGENT POWER MODULE
3 - FRONT CONTROL MODULE
24 - 14 CONTROLS - FRONTRS
BLOWER MOTOR RELAY (Continued)
ProCarManuals.com
Page 2018 of 2177
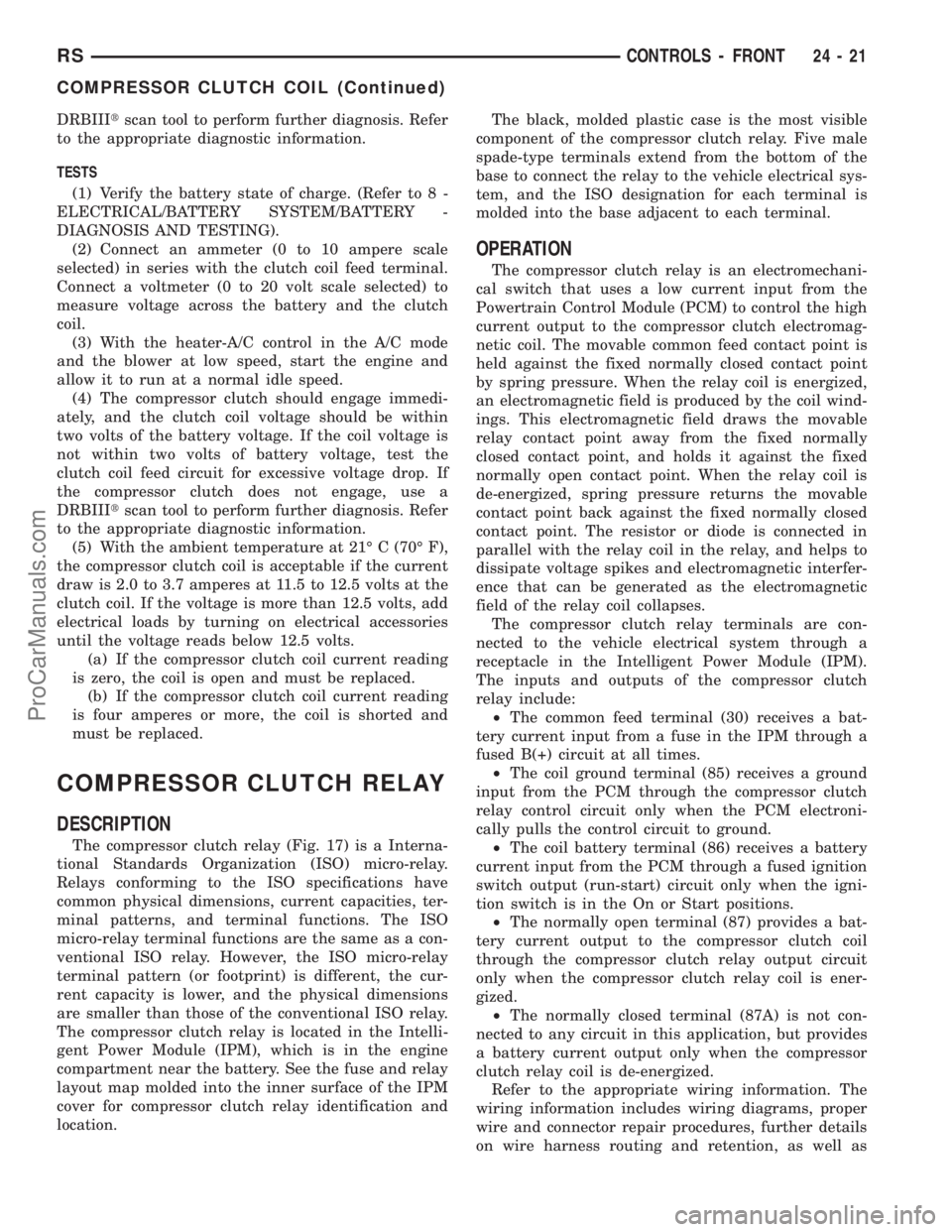
DRBIIItscan tool to perform further diagnosis. Refer
to the appropriate diagnostic information.
TESTS
(1) Verify the battery state of charge. (Refer to 8 -
ELECTRICAL/BATTERY SYSTEM/BATTERY -
DIAGNOSIS AND TESTING).
(2) Connect an ammeter (0 to 10 ampere scale
selected) in series with the clutch coil feed terminal.
Connect a voltmeter (0 to 20 volt scale selected) to
measure voltage across the battery and the clutch
coil.
(3) With the heater-A/C control in the A/C mode
and the blower at low speed, start the engine and
allow it to run at a normal idle speed.
(4) The compressor clutch should engage immedi-
ately, and the clutch coil voltage should be within
two volts of the battery voltage. If the coil voltage is
not within two volts of battery voltage, test the
clutch coil feed circuit for excessive voltage drop. If
the compressor clutch does not engage, use a
DRBIIItscan tool to perform further diagnosis. Refer
to the appropriate diagnostic information.
(5) With the ambient temperature at 21É C (70É F),
the compressor clutch coil is acceptable if the current
draw is 2.0 to 3.7 amperes at 11.5 to 12.5 volts at the
clutch coil. If the voltage is more than 12.5 volts, add
electrical loads by turning on electrical accessories
until the voltage reads below 12.5 volts.
(a) If the compressor clutch coil current reading
is zero, the coil is open and must be replaced.
(b) If the compressor clutch coil current reading
is four amperes or more, the coil is shorted and
must be replaced.
COMPRESSOR CLUTCH RELAY
DESCRIPTION
The compressor clutch relay (Fig. 17) is a Interna-
tional Standards Organization (ISO) micro-relay.
Relays conforming to the ISO specifications have
common physical dimensions, current capacities, ter-
minal patterns, and terminal functions. The ISO
micro-relay terminal functions are the same as a con-
ventional ISO relay. However, the ISO micro-relay
terminal pattern (or footprint) is different, the cur-
rent capacity is lower, and the physical dimensions
are smaller than those of the conventional ISO relay.
The compressor clutch relay is located in the Intelli-
gent Power Module (IPM), which is in the engine
compartment near the battery. See the fuse and relay
layout map molded into the inner surface of the IPM
cover for compressor clutch relay identification and
location.The black, molded plastic case is the most visible
component of the compressor clutch relay. Five male
spade-type terminals extend from the bottom of the
base to connect the relay to the vehicle electrical sys-
tem, and the ISO designation for each terminal is
molded into the base adjacent to each terminal.
OPERATION
The compressor clutch relay is an electromechani-
cal switch that uses a low current input from the
Powertrain Control Module (PCM) to control the high
current output to the compressor clutch electromag-
netic coil. The movable common feed contact point is
held against the fixed normally closed contact point
by spring pressure. When the relay coil is energized,
an electromagnetic field is produced by the coil wind-
ings. This electromagnetic field draws the movable
relay contact point away from the fixed normally
closed contact point, and holds it against the fixed
normally open contact point. When the relay coil is
de-energized, spring pressure returns the movable
contact point back against the fixed normally closed
contact point. The resistor or diode is connected in
parallel with the relay coil in the relay, and helps to
dissipate voltage spikes and electromagnetic interfer-
ence that can be generated as the electromagnetic
field of the relay coil collapses.
The compressor clutch relay terminals are con-
nected to the vehicle electrical system through a
receptacle in the Intelligent Power Module (IPM).
The inputs and outputs of the compressor clutch
relay include:
²The common feed terminal (30) receives a bat-
tery current input from a fuse in the IPM through a
fused B(+) circuit at all times.
²The coil ground terminal (85) receives a ground
input from the PCM through the compressor clutch
relay control circuit only when the PCM electroni-
cally pulls the control circuit to ground.
²The coil battery terminal (86) receives a battery
current input from the PCM through a fused ignition
switch output (run-start) circuit only when the igni-
tion switch is in the On or Start positions.
²The normally open terminal (87) provides a bat-
tery current output to the compressor clutch coil
through the compressor clutch relay output circuit
only when the compressor clutch relay coil is ener-
gized.
²The normally closed terminal (87A) is not con-
nected to any circuit in this application, but provides
a battery current output only when the compressor
clutch relay coil is de-energized.
Refer to the appropriate wiring information. The
wiring information includes wiring diagrams, proper
wire and connector repair procedures, further details
on wire harness routing and retention, as well as
RSCONTROLS - FRONT24-21
COMPRESSOR CLUTCH COIL (Continued)
ProCarManuals.com
Page 2019 of 2177
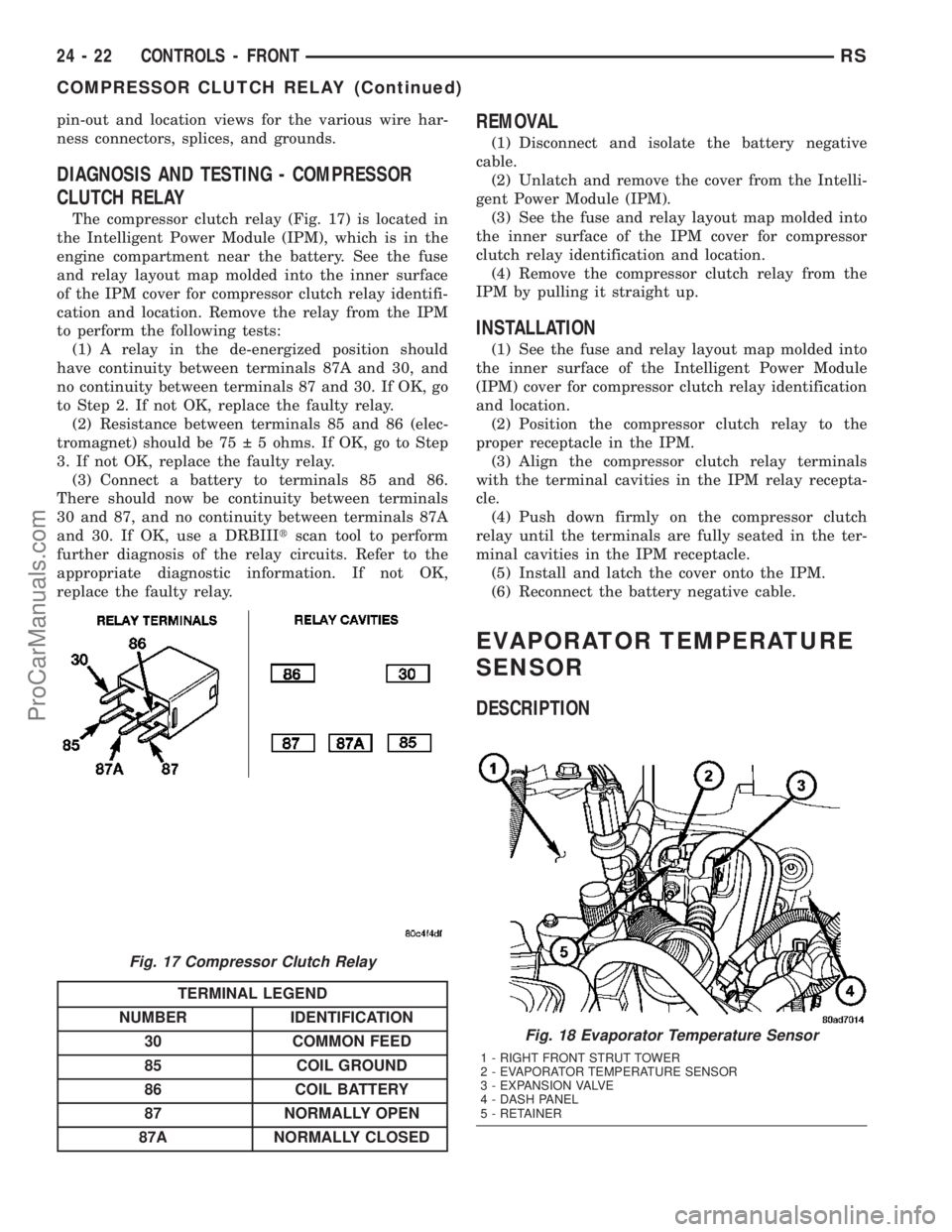
pin-out and location views for the various wire har-
ness connectors, splices, and grounds.
DIAGNOSIS AND TESTING - COMPRESSOR
CLUTCH RELAY
The compressor clutch relay (Fig. 17) is located in
the Intelligent Power Module (IPM), which is in the
engine compartment near the battery. See the fuse
and relay layout map molded into the inner surface
of the IPM cover for compressor clutch relay identifi-
cation and location. Remove the relay from the IPM
to perform the following tests:
(1) A relay in the de-energized position should
have continuity between terminals 87A and 30, and
no continuity between terminals 87 and 30. If OK, go
to Step 2. If not OK, replace the faulty relay.
(2) Resistance between terminals 85 and 86 (elec-
tromagnet) should be 75 Â 5 ohms. If OK, go to Step
3. If not OK, replace the faulty relay.
(3) Connect a battery to terminals 85 and 86.
There should now be continuity between terminals
30 and 87, and no continuity between terminals 87A
and 30. If OK, use a DRBIIItscan tool to perform
further diagnosis of the relay circuits. Refer to the
appropriate diagnostic information. If not OK,
replace the faulty relay.
TERMINAL LEGEND
NUMBER IDENTIFICATION
30 COMMON FEED
85 COIL GROUND
86 COIL BATTERY
87 NORMALLY OPEN
87A NORMALLY CLOSED
REMOVAL
(1) Disconnect and isolate the battery negative
cable.
(2) Unlatch and remove the cover from the Intelli-
gent Power Module (IPM).
(3) See the fuse and relay layout map molded into
the inner surface of the IPM cover for compressor
clutch relay identification and location.
(4) Remove the compressor clutch relay from the
IPM by pulling it straight up.
INSTALLATION
(1) See the fuse and relay layout map molded into
the inner surface of the Intelligent Power Module
(IPM) cover for compressor clutch relay identification
and location.
(2) Position the compressor clutch relay to the
proper receptacle in the IPM.
(3) Align the compressor clutch relay terminals
with the terminal cavities in the IPM relay recepta-
cle.
(4) Push down firmly on the compressor clutch
relay until the terminals are fully seated in the ter-
minal cavities in the IPM receptacle.
(5) Install and latch the cover onto the IPM.
(6) Reconnect the battery negative cable.
EVAPORATOR TEMPERATURE
SENSOR
DESCRIPTION
Fig. 17 Compressor Clutch Relay
Fig. 18 Evaporator Temperature Sensor
1 - RIGHT FRONT STRUT TOWER
2 - EVAPORATOR TEMPERATURE SENSOR
3 - EXPANSION VALVE
4 - DASH PANEL
5 - RETAINER
24 - 22 CONTROLS - FRONTRS
COMPRESSOR CLUTCH RELAY (Continued)
ProCarManuals.com
Page 2029 of 2177
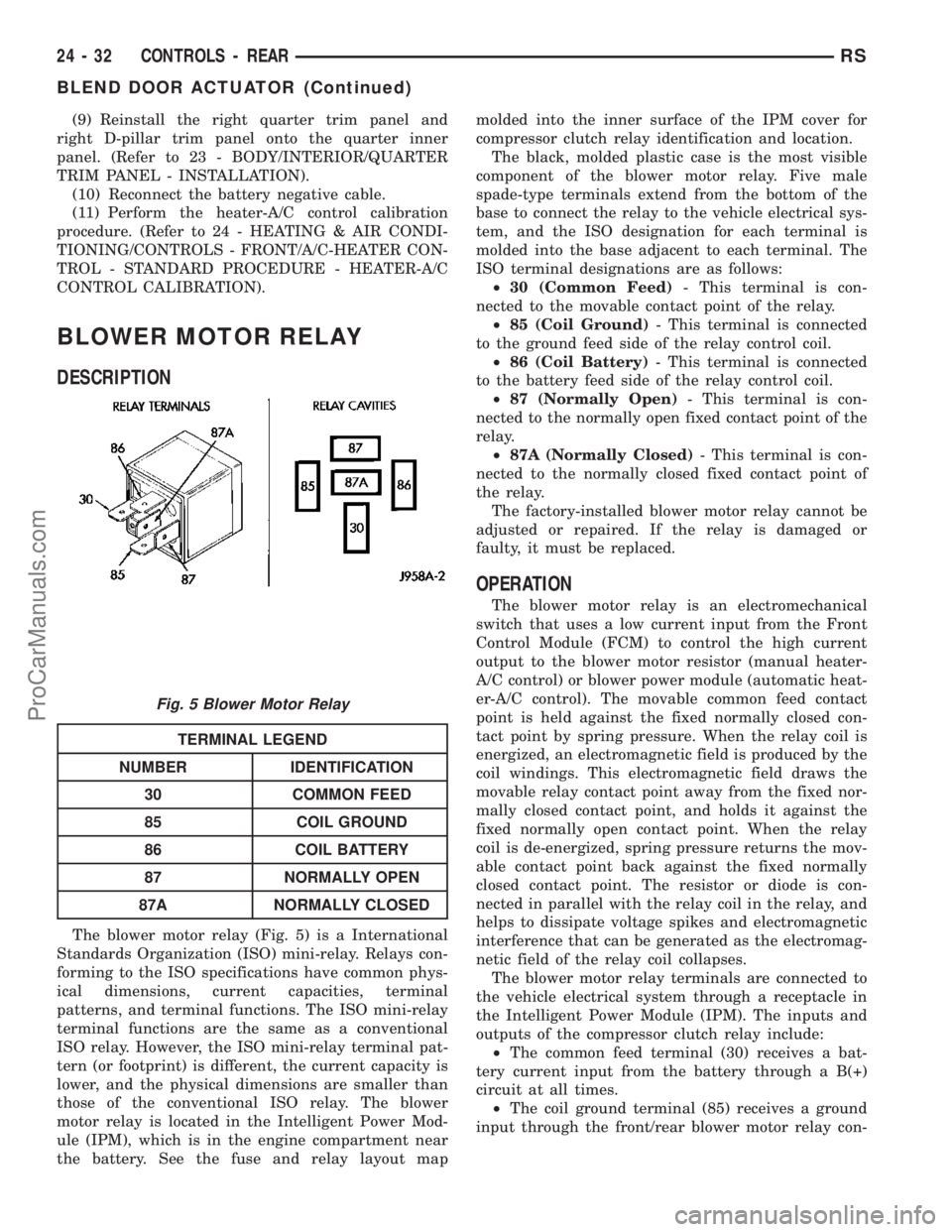
(9) Reinstall the right quarter trim panel and
right D-pillar trim panel onto the quarter inner
panel. (Refer to 23 - BODY/INTERIOR/QUARTER
TRIM PANEL - INSTALLATION).
(10) Reconnect the battery negative cable.
(11) Perform the heater-A/C control calibration
procedure. (Refer to 24 - HEATING & AIR CONDI-
TIONING/CONTROLS - FRONT/A/C-HEATER CON-
TROL - STANDARD PROCEDURE - HEATER-A/C
CONTROL CALIBRATION).
BLOWER MOTOR RELAY
DESCRIPTION
TERMINAL LEGEND
NUMBER IDENTIFICATION
30 COMMON FEED
85 COIL GROUND
86 COIL BATTERY
87 NORMALLY OPEN
87A NORMALLY CLOSED
The blower motor relay (Fig. 5) is a International
Standards Organization (ISO) mini-relay. Relays con-
forming to the ISO specifications have common phys-
ical dimensions, current capacities, terminal
patterns, and terminal functions. The ISO mini-relay
terminal functions are the same as a conventional
ISO relay. However, the ISO mini-relay terminal pat-
tern (or footprint) is different, the current capacity is
lower, and the physical dimensions are smaller than
those of the conventional ISO relay. The blower
motor relay is located in the Intelligent Power Mod-
ule (IPM), which is in the engine compartment near
the battery. See the fuse and relay layout mapmolded into the inner surface of the IPM cover for
compressor clutch relay identification and location.
The black, molded plastic case is the most visible
component of the blower motor relay. Five male
spade-type terminals extend from the bottom of the
base to connect the relay to the vehicle electrical sys-
tem, and the ISO designation for each terminal is
molded into the base adjacent to each terminal. The
ISO terminal designations are as follows:
²30 (Common Feed)- This terminal is con-
nected to the movable contact point of the relay.
²85 (Coil Ground)- This terminal is connected
to the ground feed side of the relay control coil.
²86 (Coil Battery)- This terminal is connected
to the battery feed side of the relay control coil.
²87 (Normally Open)- This terminal is con-
nected to the normally open fixed contact point of the
relay.
²87A (Normally Closed)- This terminal is con-
nected to the normally closed fixed contact point of
the relay.
The factory-installed blower motor relay cannot be
adjusted or repaired. If the relay is damaged or
faulty, it must be replaced.
OPERATION
The blower motor relay is an electromechanical
switch that uses a low current input from the Front
Control Module (FCM) to control the high current
output to the blower motor resistor (manual heater-
A/C control) or blower power module (automatic heat-
er-A/C control). The movable common feed contact
point is held against the fixed normally closed con-
tact point by spring pressure. When the relay coil is
energized, an electromagnetic field is produced by the
coil windings. This electromagnetic field draws the
movable relay contact point away from the fixed nor-
mally closed contact point, and holds it against the
fixed normally open contact point. When the relay
coil is de-energized, spring pressure returns the mov-
able contact point back against the fixed normally
closed contact point. The resistor or diode is con-
nected in parallel with the relay coil in the relay, and
helps to dissipate voltage spikes and electromagnetic
interference that can be generated as the electromag-
netic field of the relay coil collapses.
The blower motor relay terminals are connected to
the vehicle electrical system through a receptacle in
the Intelligent Power Module (IPM). The inputs and
outputs of the compressor clutch relay include:
²The common feed terminal (30) receives a bat-
tery current input from the battery through a B(+)
circuit at all times.
²The coil ground terminal (85) receives a ground
input through the front/rear blower motor relay con-
Fig. 5 Blower Motor Relay
24 - 32 CONTROLS - REARRS
BLEND DOOR ACTUATOR (Continued)
ProCarManuals.com
Page 2030 of 2177
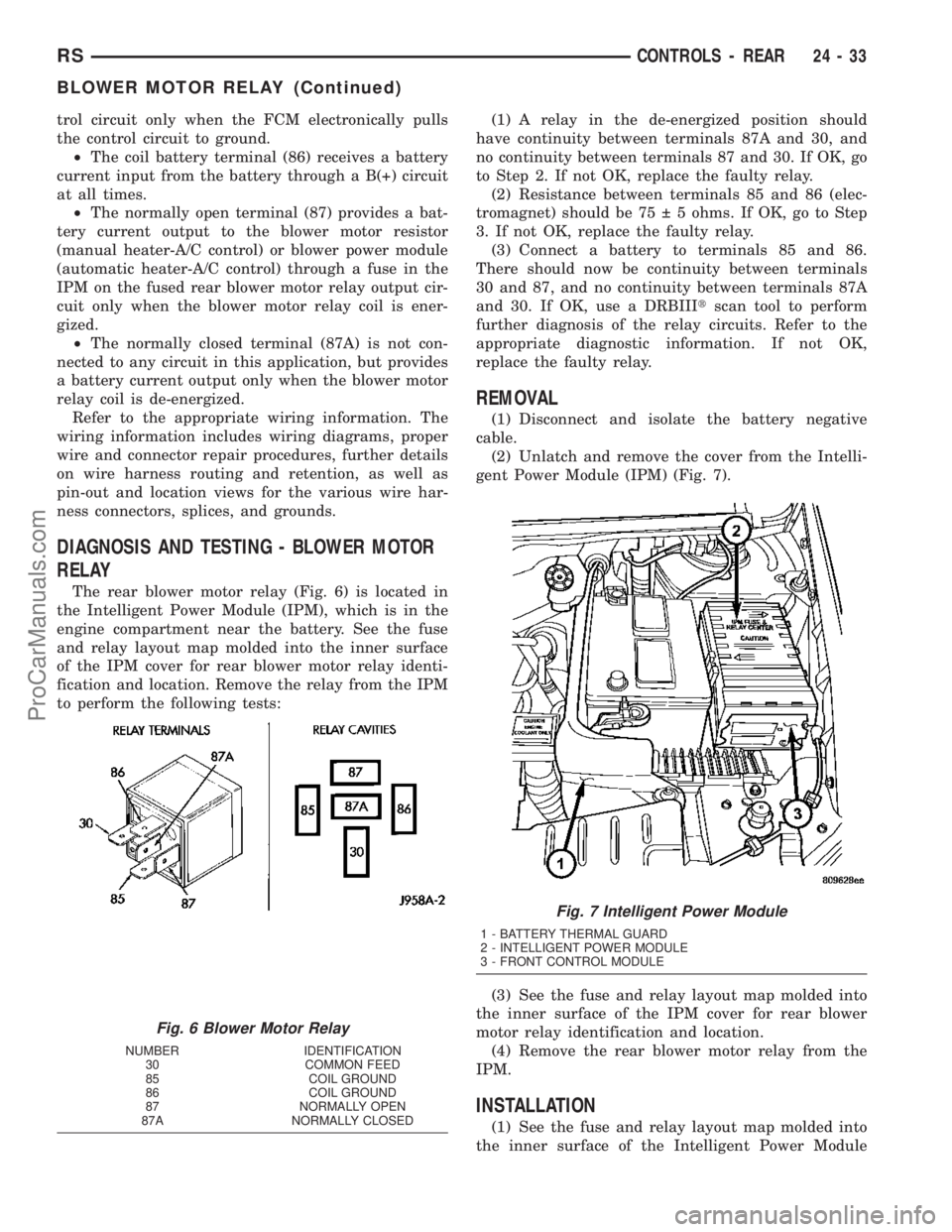
trol circuit only when the FCM electronically pulls
the control circuit to ground.
²The coil battery terminal (86) receives a battery
current input from the battery through a B(+) circuit
at all times.
²The normally open terminal (87) provides a bat-
tery current output to the blower motor resistor
(manual heater-A/C control) or blower power module
(automatic heater-A/C control) through a fuse in the
IPM on the fused rear blower motor relay output cir-
cuit only when the blower motor relay coil is ener-
gized.
²The normally closed terminal (87A) is not con-
nected to any circuit in this application, but provides
a battery current output only when the blower motor
relay coil is de-energized.
Refer to the appropriate wiring information. The
wiring information includes wiring diagrams, proper
wire and connector repair procedures, further details
on wire harness routing and retention, as well as
pin-out and location views for the various wire har-
ness connectors, splices, and grounds.
DIAGNOSIS AND TESTING - BLOWER MOTOR
RELAY
The rear blower motor relay (Fig. 6) is located in
the Intelligent Power Module (IPM), which is in the
engine compartment near the battery. See the fuse
and relay layout map molded into the inner surface
of the IPM cover for rear blower motor relay identi-
fication and location. Remove the relay from the IPM
to perform the following tests:(1) A relay in the de-energized position should
have continuity between terminals 87A and 30, and
no continuity between terminals 87 and 30. If OK, go
to Step 2. If not OK, replace the faulty relay.
(2) Resistance between terminals 85 and 86 (elec-
tromagnet) should be 75 Â 5 ohms. If OK, go to Step
3. If not OK, replace the faulty relay.
(3) Connect a battery to terminals 85 and 86.
There should now be continuity between terminals
30 and 87, and no continuity between terminals 87A
and 30. If OK, use a DRBIIItscan tool to perform
further diagnosis of the relay circuits. Refer to the
appropriate diagnostic information. If not OK,
replace the faulty relay.
REMOVAL
(1) Disconnect and isolate the battery negative
cable.
(2) Unlatch and remove the cover from the Intelli-
gent Power Module (IPM) (Fig. 7).
(3) See the fuse and relay layout map molded into
the inner surface of the IPM cover for rear blower
motor relay identification and location.
(4) Remove the rear blower motor relay from the
IPM.
INSTALLATION
(1) See the fuse and relay layout map molded into
the inner surface of the Intelligent Power Module
Fig. 6 Blower Motor Relay
NUMBER IDENTIFICATION
30 COMMON FEED
85 COIL GROUND
86 COIL GROUND
87 NORMALLY OPEN
87A NORMALLY CLOSED
Fig. 7 Intelligent Power Module
1 - BATTERY THERMAL GUARD
2 - INTELLIGENT POWER MODULE
3 - FRONT CONTROL MODULE
RSCONTROLS - REAR24-33
BLOWER MOTOR RELAY (Continued)
ProCarManuals.com
Page 2040 of 2177
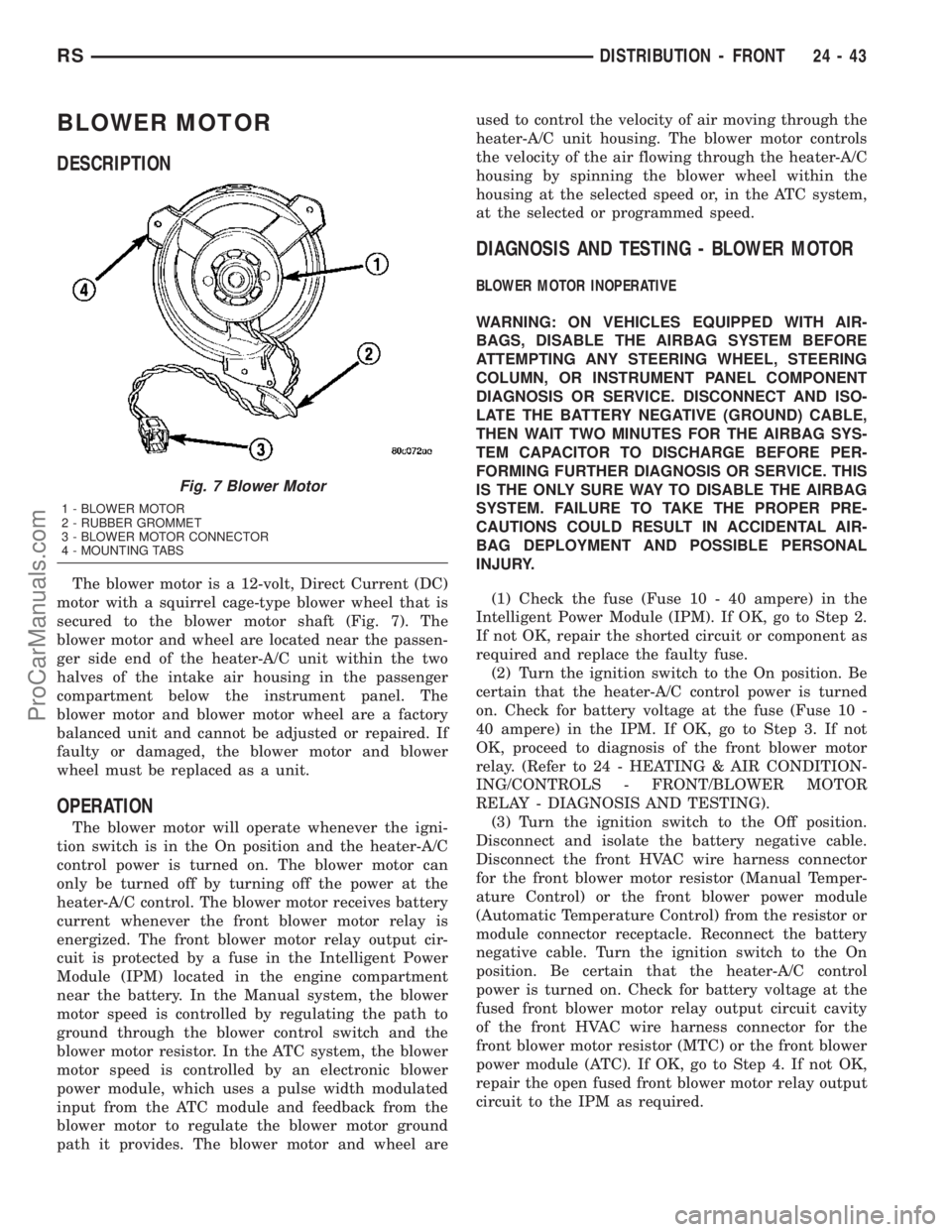
BLOWER MOTOR
DESCRIPTION
The blower motor is a 12-volt, Direct Current (DC)
motor with a squirrel cage-type blower wheel that is
secured to the blower motor shaft (Fig. 7). The
blower motor and wheel are located near the passen-
ger side end of the heater-A/C unit within the two
halves of the intake air housing in the passenger
compartment below the instrument panel. The
blower motor and blower motor wheel are a factory
balanced unit and cannot be adjusted or repaired. If
faulty or damaged, the blower motor and blower
wheel must be replaced as a unit.
OPERATION
The blower motor will operate whenever the igni-
tion switch is in the On position and the heater-A/C
control power is turned on. The blower motor can
only be turned off by turning off the power at the
heater-A/C control. The blower motor receives battery
current whenever the front blower motor relay is
energized. The front blower motor relay output cir-
cuit is protected by a fuse in the Intelligent Power
Module (IPM) located in the engine compartment
near the battery. In the Manual system, the blower
motor speed is controlled by regulating the path to
ground through the blower control switch and the
blower motor resistor. In the ATC system, the blower
motor speed is controlled by an electronic blower
power module, which uses a pulse width modulated
input from the ATC module and feedback from the
blower motor to regulate the blower motor ground
path it provides. The blower motor and wheel areused to control the velocity of air moving through the
heater-A/C unit housing. The blower motor controls
the velocity of the air flowing through the heater-A/C
housing by spinning the blower wheel within the
housing at the selected speed or, in the ATC system,
at the selected or programmed speed.
DIAGNOSIS AND TESTING - BLOWER MOTOR
BLOWER MOTOR INOPERATIVE
WARNING: ON VEHICLES EQUIPPED WITH AIR-
BAGS, DISABLE THE AIRBAG SYSTEM BEFORE
ATTEMPTING ANY STEERING WHEEL, STEERING
COLUMN, OR INSTRUMENT PANEL COMPONENT
DIAGNOSIS OR SERVICE. DISCONNECT AND ISO-
LATE THE BATTERY NEGATIVE (GROUND) CABLE,
THEN WAIT TWO MINUTES FOR THE AIRBAG SYS-
TEM CAPACITOR TO DISCHARGE BEFORE PER-
FORMING FURTHER DIAGNOSIS OR SERVICE. THIS
IS THE ONLY SURE WAY TO DISABLE THE AIRBAG
SYSTEM. FAILURE TO TAKE THE PROPER PRE-
CAUTIONS COULD RESULT IN ACCIDENTAL AIR-
BAG DEPLOYMENT AND POSSIBLE PERSONAL
INJURY.
(1) Check the fuse (Fuse 10 - 40 ampere) in the
Intelligent Power Module (IPM). If OK, go to Step 2.
If not OK, repair the shorted circuit or component as
required and replace the faulty fuse.
(2) Turn the ignition switch to the On position. Be
certain that the heater-A/C control power is turned
on. Check for battery voltage at the fuse (Fuse 10 -
40 ampere) in the IPM. If OK, go to Step 3. If not
OK, proceed to diagnosis of the front blower motor
relay. (Refer to 24 - HEATING & AIR CONDITION-
ING/CONTROLS - FRONT/BLOWER MOTOR
RELAY - DIAGNOSIS AND TESTING).
(3) Turn the ignition switch to the Off position.
Disconnect and isolate the battery negative cable.
Disconnect the front HVAC wire harness connector
for the front blower motor resistor (Manual Temper-
ature Control) or the front blower power module
(Automatic Temperature Control) from the resistor or
module connector receptacle. Reconnect the battery
negative cable. Turn the ignition switch to the On
position. Be certain that the heater-A/C control
power is turned on. Check for battery voltage at the
fused front blower motor relay output circuit cavity
of the front HVAC wire harness connector for the
front blower motor resistor (MTC) or the front blower
power module (ATC). If OK, go to Step 4. If not OK,
repair the open fused front blower motor relay output
circuit to the IPM as required.
Fig. 7 Blower Motor
1 - BLOWER MOTOR
2 - RUBBER GROMMET
3 - BLOWER MOTOR CONNECTOR
4 - MOUNTING TABS
RSDISTRIBUTION - FRONT24-43
ProCarManuals.com
Page 2051 of 2177
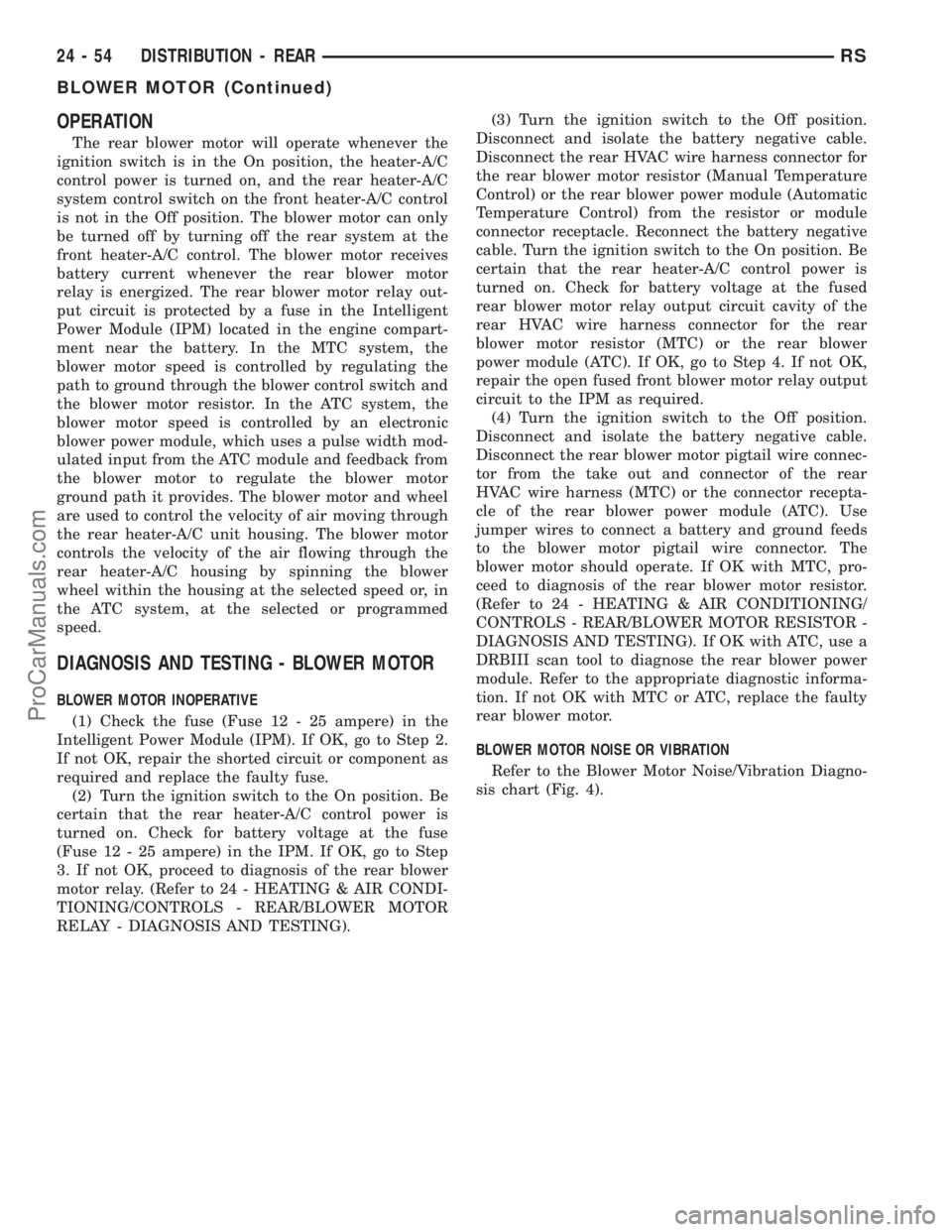
OPERATION
The rear blower motor will operate whenever the
ignition switch is in the On position, the heater-A/C
control power is turned on, and the rear heater-A/C
system control switch on the front heater-A/C control
is not in the Off position. The blower motor can only
be turned off by turning off the rear system at the
front heater-A/C control. The blower motor receives
battery current whenever the rear blower motor
relay is energized. The rear blower motor relay out-
put circuit is protected by a fuse in the Intelligent
Power Module (IPM) located in the engine compart-
ment near the battery. In the MTC system, the
blower motor speed is controlled by regulating the
path to ground through the blower control switch and
the blower motor resistor. In the ATC system, the
blower motor speed is controlled by an electronic
blower power module, which uses a pulse width mod-
ulated input from the ATC module and feedback from
the blower motor to regulate the blower motor
ground path it provides. The blower motor and wheel
are used to control the velocity of air moving through
the rear heater-A/C unit housing. The blower motor
controls the velocity of the air flowing through the
rear heater-A/C housing by spinning the blower
wheel within the housing at the selected speed or, in
the ATC system, at the selected or programmed
speed.
DIAGNOSIS AND TESTING - BLOWER MOTOR
BLOWER MOTOR INOPERATIVE
(1) Check the fuse (Fuse 12 - 25 ampere) in the
Intelligent Power Module (IPM). If OK, go to Step 2.
If not OK, repair the shorted circuit or component as
required and replace the faulty fuse.
(2) Turn the ignition switch to the On position. Be
certain that the rear heater-A/C control power is
turned on. Check for battery voltage at the fuse
(Fuse 12 - 25 ampere) in the IPM. If OK, go to Step
3. If not OK, proceed to diagnosis of the rear blower
motor relay. (Refer to 24 - HEATING & AIR CONDI-
TIONING/CONTROLS - REAR/BLOWER MOTOR
RELAY - DIAGNOSIS AND TESTING).(3) Turn the ignition switch to the Off position.
Disconnect and isolate the battery negative cable.
Disconnect the rear HVAC wire harness connector for
the rear blower motor resistor (Manual Temperature
Control) or the rear blower power module (Automatic
Temperature Control) from the resistor or module
connector receptacle. Reconnect the battery negative
cable. Turn the ignition switch to the On position. Be
certain that the rear heater-A/C control power is
turned on. Check for battery voltage at the fused
rear blower motor relay output circuit cavity of the
rear HVAC wire harness connector for the rear
blower motor resistor (MTC) or the rear blower
power module (ATC). If OK, go to Step 4. If not OK,
repair the open fused front blower motor relay output
circuit to the IPM as required.
(4) Turn the ignition switch to the Off position.
Disconnect and isolate the battery negative cable.
Disconnect the rear blower motor pigtail wire connec-
tor from the take out and connector of the rear
HVAC wire harness (MTC) or the connector recepta-
cle of the rear blower power module (ATC). Use
jumper wires to connect a battery and ground feeds
to the blower motor pigtail wire connector. The
blower motor should operate. If OK with MTC, pro-
ceed to diagnosis of the rear blower motor resistor.
(Refer to 24 - HEATING & AIR CONDITIONING/
CONTROLS - REAR/BLOWER MOTOR RESISTOR -
DIAGNOSIS AND TESTING). If OK with ATC, use a
DRBIII scan tool to diagnose the rear blower power
module. Refer to the appropriate diagnostic informa-
tion. If not OK with MTC or ATC, replace the faulty
rear blower motor.
BLOWER MOTOR NOISE OR VIBRATION
Refer to the Blower Motor Noise/Vibration Diagno-
sis chart (Fig. 4).
24 - 54 DISTRIBUTION - REARRS
BLOWER MOTOR (Continued)
ProCarManuals.com
Page 2153 of 2177
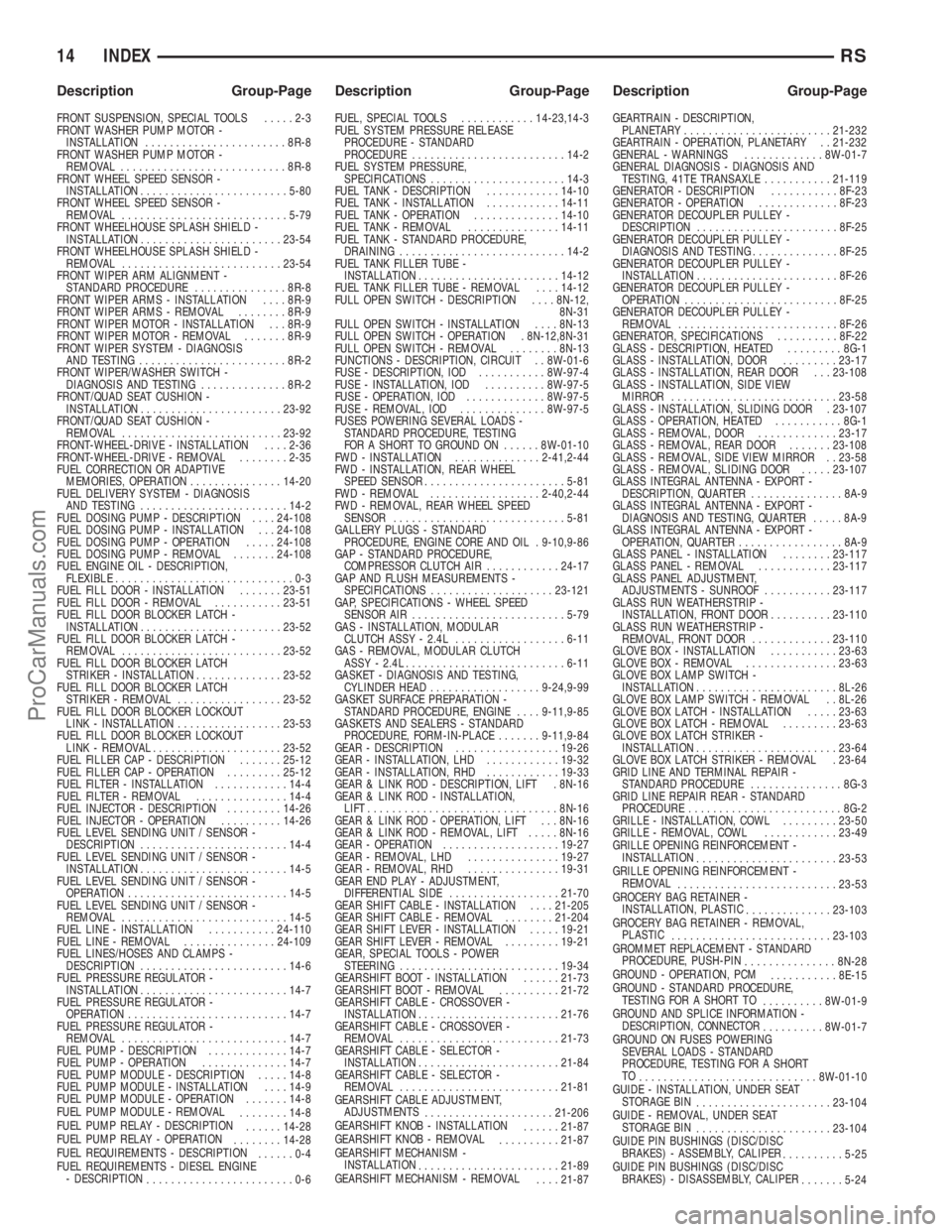
FRONT SUSPENSION, SPECIAL TOOLS.....2-3
FRONT WASHER PUMP MOTOR -
INSTALLATION.......................8R-8
FRONT WASHER PUMP MOTOR -
REMOVAL...........................8R-8
FRONT WHEEL SPEED SENSOR -
INSTALLATION........................5-80
FRONT WHEEL SPEED SENSOR -
REMOVAL...........................5-79
FRONT WHEELHOUSE SPLASH SHIELD -
INSTALLATION.......................23-54
FRONT WHEELHOUSE SPLASH SHIELD -
REMOVAL..........................23-54
FRONT WIPER ARM ALIGNMENT -
STANDARD PROCEDURE...............8R-8
FRONT WIPER ARMS - INSTALLATION....8R-9
FRONT WIPER ARMS - REMOVAL........8R-9
FRONT WIPER MOTOR - INSTALLATION . . . 8R-9
FRONT WIPER MOTOR - REMOVAL.......8R-9
FRONT WIPER SYSTEM - DIAGNOSIS
AND TESTING........................8R-2
FRONT WIPER/WASHER SWITCH -
DIAGNOSIS AND TESTING..............8R-2
FRONT/QUAD SEAT CUSHION -
INSTALLATION.......................23-92
FRONT/QUAD SEAT CUSHION -
REMOVAL..........................23-92
FRONT-WHEEL-DRIVE - INSTALLATION....2-36
FRONT-WHEEL-DRIVE - REMOVAL........2-35
FUEL CORRECTION OR ADAPTIVE
MEMORIES, OPERATION...............14-20
FUEL DELIVERY SYSTEM - DIAGNOSIS
AND TESTING........................14-2
FUEL DOSING PUMP - DESCRIPTION....24-108
FUEL DOSING PUMP - INSTALLATION . . . 24-108
FUEL DOSING PUMP - OPERATION.....24-108
FUEL DOSING PUMP - REMOVAL.......24-108
FUEL ENGINE OIL - DESCRIPTION,
FLEXIBLE.............................0-3
FUEL FILL DOOR - INSTALLATION.......23-51
FUEL FILL DOOR - REMOVAL...........23-51
FUEL FILL DOOR BLOCKER LATCH -
INSTALLATION.......................23-52
FUEL FILL DOOR BLOCKER LATCH -
REMOVAL..........................23-52
FUEL FILL DOOR BLOCKER LATCH
STRIKER - INSTALLATION..............23-52
FUEL FILL DOOR BLOCKER LATCH
STRIKER - REMOVAL.................23-52
FUEL FILL DOOR BLOCKER LOCKOUT
LINK - INSTALLATION.................23-53
FUEL FILL DOOR BLOCKER LOCKOUT
LINK - REMOVAL.....................23-52
FUEL FILLER CAP - DESCRIPTION.......25-12
FUEL FILLER CAP - OPERATION.........25-12
FUEL FILTER - INSTALLATION............14-4
FUEL FILTER - REMOVAL...............14-4
FUEL INJECTOR - DESCRIPTION.........14-26
FUEL INJECTOR - OPERATION..........14-26
FUEL LEVEL SENDING UNIT / SENSOR -
DESCRIPTION........................14-4
FUEL LEVEL SENDING UNIT / SENSOR -
INSTALLATION........................14-5
FUEL LEVEL SENDING UNIT / SENSOR -
OPERATION..........................14-5
FUEL LEVEL SENDING UNIT / SENSOR -
REMOVAL...........................14-5
FUEL LINE - INSTALLATION...........24-110
FUEL LINE - REMOVAL...............24-109
FUEL LINES/HOSES AND CLAMPS -
DESCRIPTION........................14-6
FUEL PRESSURE REGULATOR -
INSTALLATION........................14-7
FUEL PRESSURE REGULATOR -
OPERATION..........................14-7
FUEL PRESSURE REGULATOR -
REMOVAL...........................14-7
FUEL PUMP - DESCRIPTION.............14-7
FUEL PUMP - OPERATION..............14-7
FUEL PUMP MODULE - DESCRIPTION.....14-8
FUEL PUMP MODULE - INSTALLATION....14-9
FUEL PUMP MODULE - OPERATION.......14-8
FUEL PUMP MODULE - REMOVAL
........14-8
FUEL PUMP RELAY - DESCRIPTION
......14-28
FUEL PUMP RELAY - OPERATION
........14-28
FUEL REQUIREMENTS - DESCRIPTION
......0-4
FUEL REQUIREMENTS - DIESEL ENGINE
- DESCRIPTION
........................0-6FUEL, SPECIAL TOOLS............14-23,14-3
FUEL SYSTEM PRESSURE RELEASE
PROCEDURE - STANDARD
PROCEDURE.........................14-2
FUEL SYSTEM PRESSURE,
SPECIFICATIONS......................14-3
FUEL TANK - DESCRIPTION............14-10
FUEL TANK - INSTALLATION............14-11
FUEL TANK - OPERATION..............14-10
FUEL TANK - REMOVAL...............14-11
FUEL TANK - STANDARD PROCEDURE,
DRAINING...........................14-2
FUEL TANK FILLER TUBE -
INSTALLATION.......................14-12
FUEL TANK FILLER TUBE - REMOVAL....14-12
FULL OPEN SWITCH - DESCRIPTION....8N-12,
8N-31
FULL OPEN SWITCH - INSTALLATION....8N-13
FULL OPEN SWITCH - OPERATION . 8N-12,8N-31
FULL OPEN SWITCH - REMOVAL........8N-13
FUNCTIONS - DESCRIPTION, CIRCUIT . . 8W-01-6
FUSE - DESCRIPTION, IOD...........8W-97-4
FUSE - INSTALLATION, IOD..........8W-97-5
FUSE - OPERATION, IOD.............8W-97-5
FUSE - REMOVAL, IOD..............8W-97-5
FUSES POWERING SEVERAL LOADS -
STANDARD PROCEDURE, TESTING
FOR A SHORT TO GROUND ON......8W-01-10
FWD - INSTALLATION..............2-41,2-44
FWD - INSTALLATION, REAR WHEEL
SPEED SENSOR.......................5-81
FWD - REMOVAL..................2-40,2-44
FWD - REMOVAL, REAR WHEEL SPEED
SENSOR............................5-81
GALLERY PLUGS - STANDARD
PROCEDURE, ENGINE CORE AND OIL . 9-10,9-86
GAP - STANDARD PROCEDURE,
COMPRESSOR CLUTCH AIR............24-17
GAP AND FLUSH MEASUREMENTS -
SPECIFICATIONS....................23-121
GAP, SPECIFICATIONS - WHEEL SPEED
SENSOR AIR.........................5-79
GAS - INSTALLATION, MODULAR
CLUTCH ASSY - 2.4L..................6-11
GAS - REMOVAL, MODULAR CLUTCH
ASSY - 2.4L..........................6-11
GASKET - DIAGNOSIS AND TESTING,
CYLINDER HEAD..................9-24,9-99
GASKET SURFACE PREPARATION -
STANDARD PROCEDURE, ENGINE....9-11,9-85
GASKETS AND SEALERS - STANDARD
PROCEDURE, FORM-IN-PLACE.......9-11,9-84
GEAR - DESCRIPTION.................19-26
GEAR - INSTALLATION, LHD............19-32
GEAR - INSTALLATION, RHD............19-33
GEAR & LINK ROD - DESCRIPTION, LIFT . 8N-16
GEAR & LINK ROD - INSTALLATION,
LIFT...............................8N-16
GEAR & LINK ROD - OPERATION, LIFT . . . 8N-16
GEAR & LINK ROD - REMOVAL, LIFT.....8N-16
GEAR - OPERATION...................19-27
GEAR - REMOVAL, LHD...............19-27
GEAR - REMOVAL, RHD...............19-31
GEAR END PLAY - ADJUSTMENT,
DIFFERENTIAL SIDE..................21-70
GEAR SHIFT CABLE - INSTALLATION....21-205
GEAR SHIFT CABLE - REMOVAL........21-204
GEAR SHIFT LEVER - INSTALLATION.....19-21
GEAR SHIFT LEVER - REMOVAL.........19-21
GEAR, SPECIAL TOOLS - POWER
STEERING..........................19-34
GEARSHIFT BOOT - INSTALLATION......21-73
GEARSHIFT BOOT - REMOVAL..........21-72
GEARSHIFT CABLE - CROSSOVER -
INSTALLATION.......................21-76
GEARSHIFT CABLE - CROSSOVER -
REMOVAL..........................21-73
GEARSHIFT CABLE - SELECTOR -
INSTALLATION.......................21-84
GEARSHIFT CABLE - SELECTOR -
REMOVAL..........................21-81
GEARSHIFT CABLE ADJUSTMENT,
ADJUSTMENTS
.....................21-206
GEARSHIFT KNOB - INSTALLATION
......21-87
GEARSHIFT KNOB - REMOVAL
..........21-87
GEARSHIFT MECHANISM -
INSTALLATION
.......................21-89
GEARSHIFT MECHANISM - REMOVAL
....21-87GEARTRAIN - DESCRIPTION,
PLANETARY........................21-232
GEARTRAIN - OPERATION, PLANETARY . . 21-232
GENERAL - WARNINGS.............8W-01-7
GENERAL DIAGNOSIS - DIAGNOSIS AND
TESTING, 41TE TRANSAXLE...........21-119
GENERATOR - DESCRIPTION...........8F-23
GENERATOR - OPERATION.............8F-23
GENERATOR DECOUPLER PULLEY -
DESCRIPTION.......................8F-25
GENERATOR DECOUPLER PULLEY -
DIAGNOSIS AND TESTING..............8F-25
GENERATOR DECOUPLER PULLEY -
INSTALLATION.......................8F-26
GENERATOR DECOUPLER PULLEY -
OPERATION.........................8F-25
GENERATOR DECOUPLER PULLEY -
REMOVAL..........................8F-26
GENERATOR, SPECIFICATIONS..........8F-22
GLASS - DESCRIPTION, HEATED.........8G-1
GLASS - INSTALLATION, DOOR.........23-17
GLASS - INSTALLATION, REAR DOOR . . . 23-108
GLASS - INSTALLATION, SIDE VIEW
MIRROR...........................23-58
GLASS - INSTALLATION, SLIDING DOOR . 23-107
GLASS - OPERATION, HEATED...........8G-1
GLASS - REMOVAL, DOOR.............23-17
GLASS - REMOVAL, REAR DOOR.......23-108
GLASS - REMOVAL, SIDE VIEW MIRROR . . 23-58
GLASS - REMOVAL, SLIDING DOOR.....23-107
GLASS INTEGRAL ANTENNA - EXPORT -
DESCRIPTION, QUARTER...............8A-9
GLASS INTEGRAL ANTENNA - EXPORT -
DIAGNOSIS AND TESTING, QUARTER.....8A-9
GLASS INTEGRAL ANTENNA - EXPORT -
OPERATION, QUARTER.................8A-9
GLASS PANEL - INSTALLATION........23-117
GLASS PANEL - REMOVAL............23-117
GLASS PANEL ADJUSTMENT,
ADJUSTMENTS - SUNROOF...........23-117
GLASS RUN WEATHERSTRIP -
INSTALLATION, FRONT DOOR..........23-110
GLASS RUN WEATHERSTRIP -
REMOVAL, FRONT DOOR.............23-110
GLOVE BOX - INSTALLATION...........23-63
GLOVE BOX - REMOVAL...............23-63
GLOVE BOX LAMP SWITCH -
INSTALLATION.......................8L-26
GLOVE BOX LAMP SWITCH - REMOVAL . . 8L-26
GLOVE BOX LATCH - INSTALLATION.....23-63
GLOVE BOX LATCH - REMOVAL.........23-63
GLOVE BOX LATCH STRIKER -
INSTALLATION.......................23-64
GLOVE BOX LATCH STRIKER - REMOVAL . 23-64
GRID LINE AND TERMINAL REPAIR -
STANDARD PROCEDURE...............8G-3
GRID LINE REPAIR REAR - STANDARD
PROCEDURE.........................8G-2
GRILLE - INSTALLATION, COWL.........23-50
GRILLE - REMOVAL, COWL............23-49
GRILLE OPENING REINFORCEMENT -
INSTALLATION
.......................23-53
GRILLE OPENING REINFORCEMENT -
REMOVAL
..........................23-53
GROCERY BAG RETAINER -
INSTALLATION, PLASTIC
..............23-103
GROCERY BAG RETAINER - REMOVAL,
PLASTIC
..........................23-103
GROMMET REPLACEMENT - STANDARD
PROCEDURE, PUSH-PIN
...............8N-28
GROUND - OPERATION, PCM
...........8E-15
GROUND - STANDARD PROCEDURE,
TESTING FOR A SHORT TO
..........8W-01-9
GROUND AND SPLICE INFORMATION -
DESCRIPTION, CONNECTOR
..........8W-01-7
GROUND ON FUSES POWERING
SEVERAL LOADS - STANDARD
PROCEDURE, TESTING FOR A SHORT
TO
.............................8W-01-10
GUIDE - INSTALLATION, UNDER SEAT
STORAGE BIN
......................23-104
GUIDE - REMOVAL, UNDER SEAT
STORAGE BIN
......................23-104
GUIDE PIN BUSHINGS (DISC/DISC
BRAKES) - ASSEMBLY, CALIPER
..........5-25
GUIDE PIN BUSHINGS (DISC/DISC
BRAKES) - DISASSEMBLY, CALIPER
.......5-24
14 INDEXRS
Description Group-Page Description Group-Page Description Group-Page
ProCarManuals.com