lug pattern CHRYSLER CARAVAN 2005 Service Manual
[x] Cancel search | Manufacturer: CHRYSLER, Model Year: 2005, Model line: CARAVAN, Model: CHRYSLER CARAVAN 2005Pages: 2339, PDF Size: 59.69 MB
Page 1186 of 2339
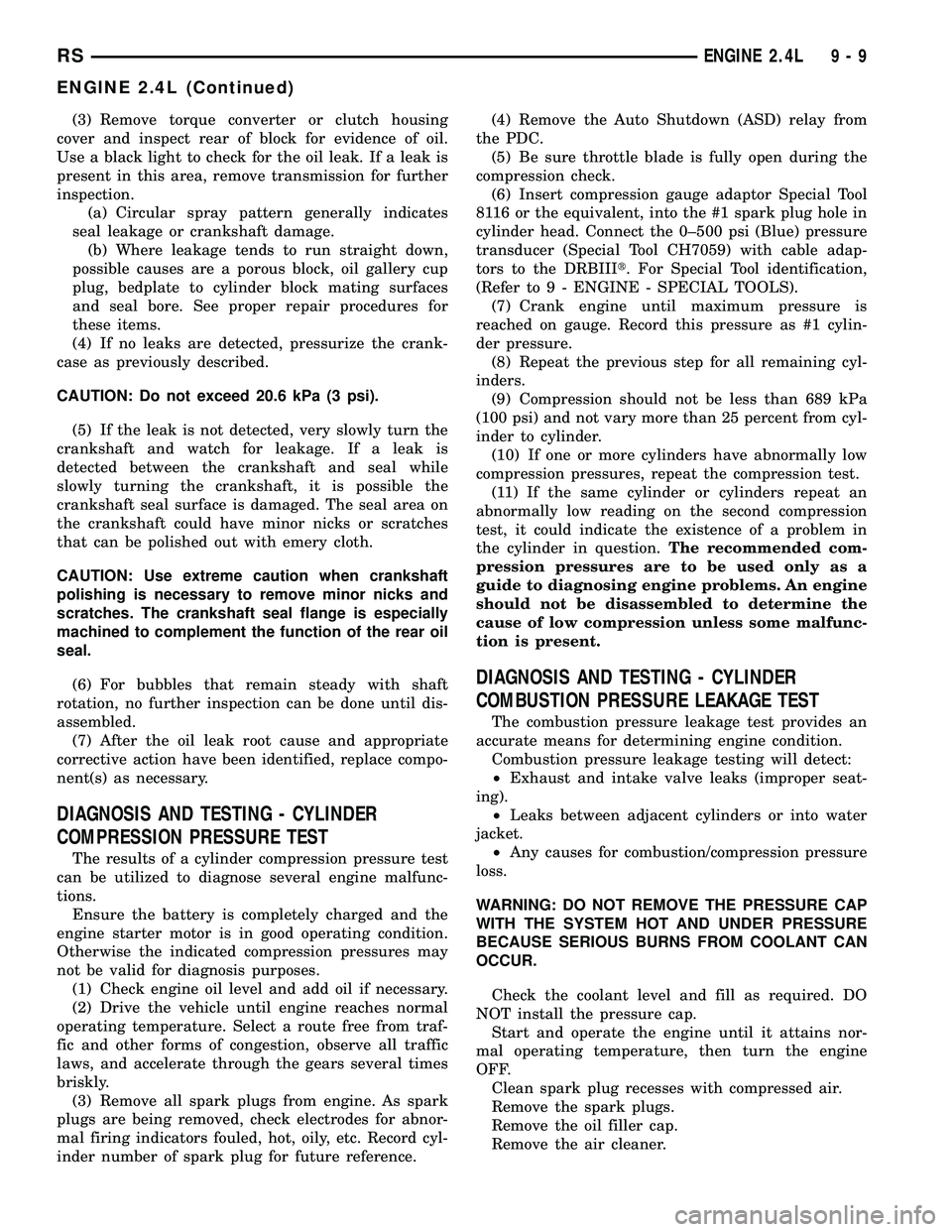
(3) Remove torque converter or clutch housing
cover and inspect rear of block for evidence of oil.
Use a black light to check for the oil leak. If a leak is
present in this area, remove transmission for further
inspection.
(a) Circular spray pattern generally indicates
seal leakage or crankshaft damage.
(b) Where leakage tends to run straight down,
possible causes are a porous block, oil gallery cup
plug, bedplate to cylinder block mating surfaces
and seal bore. See proper repair procedures for
these items.
(4) If no leaks are detected, pressurize the crank-
case as previously described.
CAUTION: Do not exceed 20.6 kPa (3 psi).
(5) If the leak is not detected, very slowly turn the
crankshaft and watch for leakage. If a leak is
detected between the crankshaft and seal while
slowly turning the crankshaft, it is possible the
crankshaft seal surface is damaged. The seal area on
the crankshaft could have minor nicks or scratches
that can be polished out with emery cloth.
CAUTION: Use extreme caution when crankshaft
polishing is necessary to remove minor nicks and
scratches. The crankshaft seal flange is especially
machined to complement the function of the rear oil
seal.
(6) For bubbles that remain steady with shaft
rotation, no further inspection can be done until dis-
assembled.
(7) After the oil leak root cause and appropriate
corrective action have been identified, replace compo-
nent(s) as necessary.
DIAGNOSIS AND TESTING - CYLINDER
COMPRESSION PRESSURE TEST
The results of a cylinder compression pressure test
can be utilized to diagnose several engine malfunc-
tions.
Ensure the battery is completely charged and the
engine starter motor is in good operating condition.
Otherwise the indicated compression pressures may
not be valid for diagnosis purposes.
(1) Check engine oil level and add oil if necessary.
(2) Drive the vehicle until engine reaches normal
operating temperature. Select a route free from traf-
fic and other forms of congestion, observe all traffic
laws, and accelerate through the gears several times
briskly.
(3) Remove all spark plugs from engine. As spark
plugs are being removed, check electrodes for abnor-
mal firing indicators fouled, hot, oily, etc. Record cyl-
inder number of spark plug for future reference.(4) Remove the Auto Shutdown (ASD) relay from
the PDC.
(5) Be sure throttle blade is fully open during the
compression check.
(6) Insert compression gauge adaptor Special Tool
8116 or the equivalent, into the #1 spark plug hole in
cylinder head. Connect the 0±500 psi (Blue) pressure
transducer (Special Tool CH7059) with cable adap-
tors to the DRBIIIt. For Special Tool identification,
(Refer to 9 - ENGINE - SPECIAL TOOLS).
(7) Crank engine until maximum pressure is
reached on gauge. Record this pressure as #1 cylin-
der pressure.
(8) Repeat the previous step for all remaining cyl-
inders.
(9) Compression should not be less than 689 kPa
(100 psi) and not vary more than 25 percent from cyl-
inder to cylinder.
(10) If one or more cylinders have abnormally low
compression pressures, repeat the compression test.
(11) If the same cylinder or cylinders repeat an
abnormally low reading on the second compression
test, it could indicate the existence of a problem in
the cylinder in question.The recommended com-
pression pressures are to be used only as a
guide to diagnosing engine problems. An engine
should not be disassembled to determine the
cause of low compression unless some malfunc-
tion is present.
DIAGNOSIS AND TESTING - CYLINDER
COMBUSTION PRESSURE LEAKAGE TEST
The combustion pressure leakage test provides an
accurate means for determining engine condition.
Combustion pressure leakage testing will detect:
²Exhaust and intake valve leaks (improper seat-
ing).
²Leaks between adjacent cylinders or into water
jacket.
²Any causes for combustion/compression pressure
loss.
WARNING: DO NOT REMOVE THE PRESSURE CAP
WITH THE SYSTEM HOT AND UNDER PRESSURE
BECAUSE SERIOUS BURNS FROM COOLANT CAN
OCCUR.
Check the coolant level and fill as required. DO
NOT install the pressure cap.
Start and operate the engine until it attains nor-
mal operating temperature, then turn the engine
OFF.
Clean spark plug recesses with compressed air.
Remove the spark plugs.
Remove the oil filler cap.
Remove the air cleaner.
RSENGINE 2.4L9-9
ENGINE 2.4L (Continued)
Page 1213 of 2339
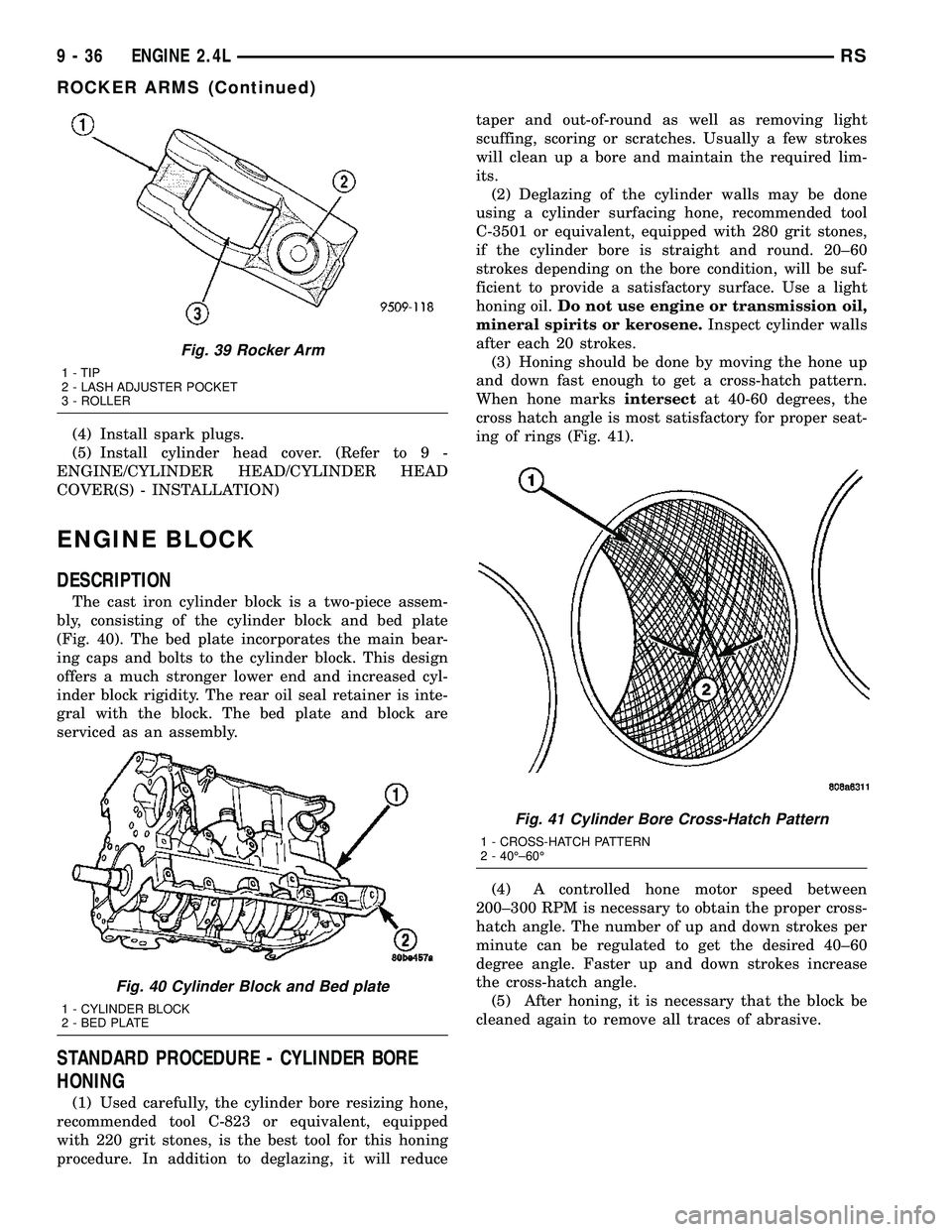
(4) Install spark plugs.
(5) Install cylinder head cover. (Refer to 9 -
ENGINE/CYLINDER HEAD/CYLINDER HEAD
COVER(S) - INSTALLATION)
ENGINE BLOCK
DESCRIPTION
The cast iron cylinder block is a two-piece assem-
bly, consisting of the cylinder block and bed plate
(Fig. 40). The bed plate incorporates the main bear-
ing caps and bolts to the cylinder block. This design
offers a much stronger lower end and increased cyl-
inder block rigidity. The rear oil seal retainer is inte-
gral with the block. The bed plate and block are
serviced as an assembly.
STANDARD PROCEDURE - CYLINDER BORE
HONING
(1) Used carefully, the cylinder bore resizing hone,
recommended tool C-823 or equivalent, equipped
with 220 grit stones, is the best tool for this honing
procedure. In addition to deglazing, it will reducetaper and out-of-round as well as removing light
scuffing, scoring or scratches. Usually a few strokes
will clean up a bore and maintain the required lim-
its.
(2) Deglazing of the cylinder walls may be done
using a cylinder surfacing hone, recommended tool
C-3501 or equivalent, equipped with 280 grit stones,
if the cylinder bore is straight and round. 20±60
strokes depending on the bore condition, will be suf-
ficient to provide a satisfactory surface. Use a light
honing oil.Do not use engine or transmission oil,
mineral spirits or kerosene.Inspect cylinder walls
after each 20 strokes.
(3) Honing should be done by moving the hone up
and down fast enough to get a cross-hatch pattern.
When hone marksintersectat 40-60 degrees, the
cross hatch angle is most satisfactory for proper seat-
ing of rings (Fig. 41).
(4) A controlled hone motor speed between
200±300 RPM is necessary to obtain the proper cross-
hatch angle. The number of up and down strokes per
minute can be regulated to get the desired 40±60
degree angle. Faster up and down strokes increase
the cross-hatch angle.
(5) After honing, it is necessary that the block be
cleaned again to remove all traces of abrasive.
Fig. 39 Rocker Arm
1 - TIP
2 - LASH ADJUSTER POCKET
3 - ROLLER
Fig. 40 Cylinder Block and Bed plate
1 - CYLINDER BLOCK
2 - BED PLATE
Fig. 41 Cylinder Bore Cross-Hatch Pattern
1 - CROSS-HATCH PATTERN
2 - 40ɱ60É
9 - 36 ENGINE 2.4LRS
ROCKER ARMS (Continued)
Page 1262 of 2339
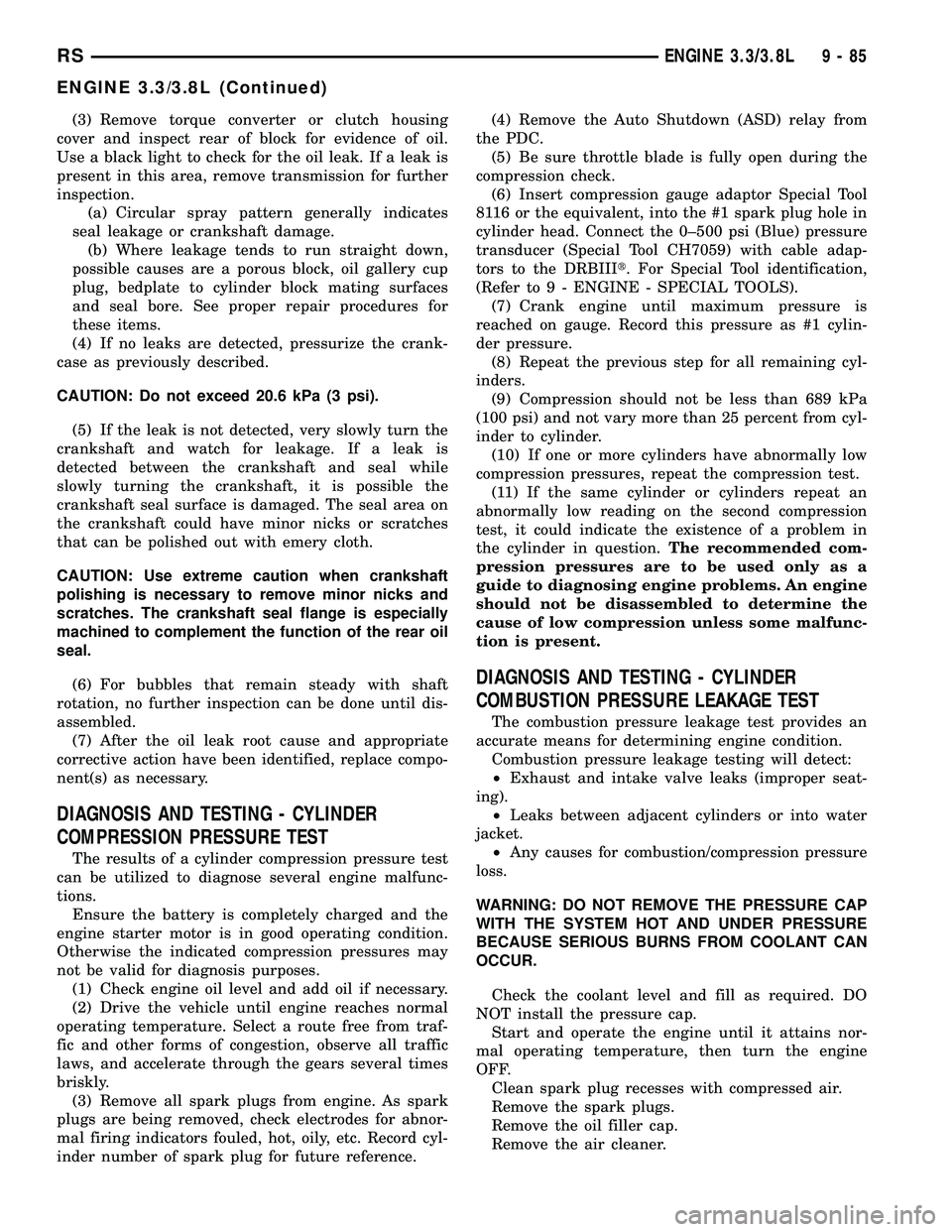
(3) Remove torque converter or clutch housing
cover and inspect rear of block for evidence of oil.
Use a black light to check for the oil leak. If a leak is
present in this area, remove transmission for further
inspection.
(a) Circular spray pattern generally indicates
seal leakage or crankshaft damage.
(b) Where leakage tends to run straight down,
possible causes are a porous block, oil gallery cup
plug, bedplate to cylinder block mating surfaces
and seal bore. See proper repair procedures for
these items.
(4) If no leaks are detected, pressurize the crank-
case as previously described.
CAUTION: Do not exceed 20.6 kPa (3 psi).
(5) If the leak is not detected, very slowly turn the
crankshaft and watch for leakage. If a leak is
detected between the crankshaft and seal while
slowly turning the crankshaft, it is possible the
crankshaft seal surface is damaged. The seal area on
the crankshaft could have minor nicks or scratches
that can be polished out with emery cloth.
CAUTION: Use extreme caution when crankshaft
polishing is necessary to remove minor nicks and
scratches. The crankshaft seal flange is especially
machined to complement the function of the rear oil
seal.
(6) For bubbles that remain steady with shaft
rotation, no further inspection can be done until dis-
assembled.
(7) After the oil leak root cause and appropriate
corrective action have been identified, replace compo-
nent(s) as necessary.
DIAGNOSIS AND TESTING - CYLINDER
COMPRESSION PRESSURE TEST
The results of a cylinder compression pressure test
can be utilized to diagnose several engine malfunc-
tions.
Ensure the battery is completely charged and the
engine starter motor is in good operating condition.
Otherwise the indicated compression pressures may
not be valid for diagnosis purposes.
(1) Check engine oil level and add oil if necessary.
(2) Drive the vehicle until engine reaches normal
operating temperature. Select a route free from traf-
fic and other forms of congestion, observe all traffic
laws, and accelerate through the gears several times
briskly.
(3) Remove all spark plugs from engine. As spark
plugs are being removed, check electrodes for abnor-
mal firing indicators fouled, hot, oily, etc. Record cyl-
inder number of spark plug for future reference.(4) Remove the Auto Shutdown (ASD) relay from
the PDC.
(5) Be sure throttle blade is fully open during the
compression check.
(6) Insert compression gauge adaptor Special Tool
8116 or the equivalent, into the #1 spark plug hole in
cylinder head. Connect the 0±500 psi (Blue) pressure
transducer (Special Tool CH7059) with cable adap-
tors to the DRBIIIt. For Special Tool identification,
(Refer to 9 - ENGINE - SPECIAL TOOLS).
(7) Crank engine until maximum pressure is
reached on gauge. Record this pressure as #1 cylin-
der pressure.
(8) Repeat the previous step for all remaining cyl-
inders.
(9) Compression should not be less than 689 kPa
(100 psi) and not vary more than 25 percent from cyl-
inder to cylinder.
(10) If one or more cylinders have abnormally low
compression pressures, repeat the compression test.
(11) If the same cylinder or cylinders repeat an
abnormally low reading on the second compression
test, it could indicate the existence of a problem in
the cylinder in question.The recommended com-
pression pressures are to be used only as a
guide to diagnosing engine problems. An engine
should not be disassembled to determine the
cause of low compression unless some malfunc-
tion is present.
DIAGNOSIS AND TESTING - CYLINDER
COMBUSTION PRESSURE LEAKAGE TEST
The combustion pressure leakage test provides an
accurate means for determining engine condition.
Combustion pressure leakage testing will detect:
²Exhaust and intake valve leaks (improper seat-
ing).
²Leaks between adjacent cylinders or into water
jacket.
²Any causes for combustion/compression pressure
loss.
WARNING: DO NOT REMOVE THE PRESSURE CAP
WITH THE SYSTEM HOT AND UNDER PRESSURE
BECAUSE SERIOUS BURNS FROM COOLANT CAN
OCCUR.
Check the coolant level and fill as required. DO
NOT install the pressure cap.
Start and operate the engine until it attains nor-
mal operating temperature, then turn the engine
OFF.
Clean spark plug recesses with compressed air.
Remove the spark plugs.
Remove the oil filler cap.
Remove the air cleaner.
RSENGINE 3.3/3.8L9-85
ENGINE 3.3/3.8L (Continued)
Page 1292 of 2339
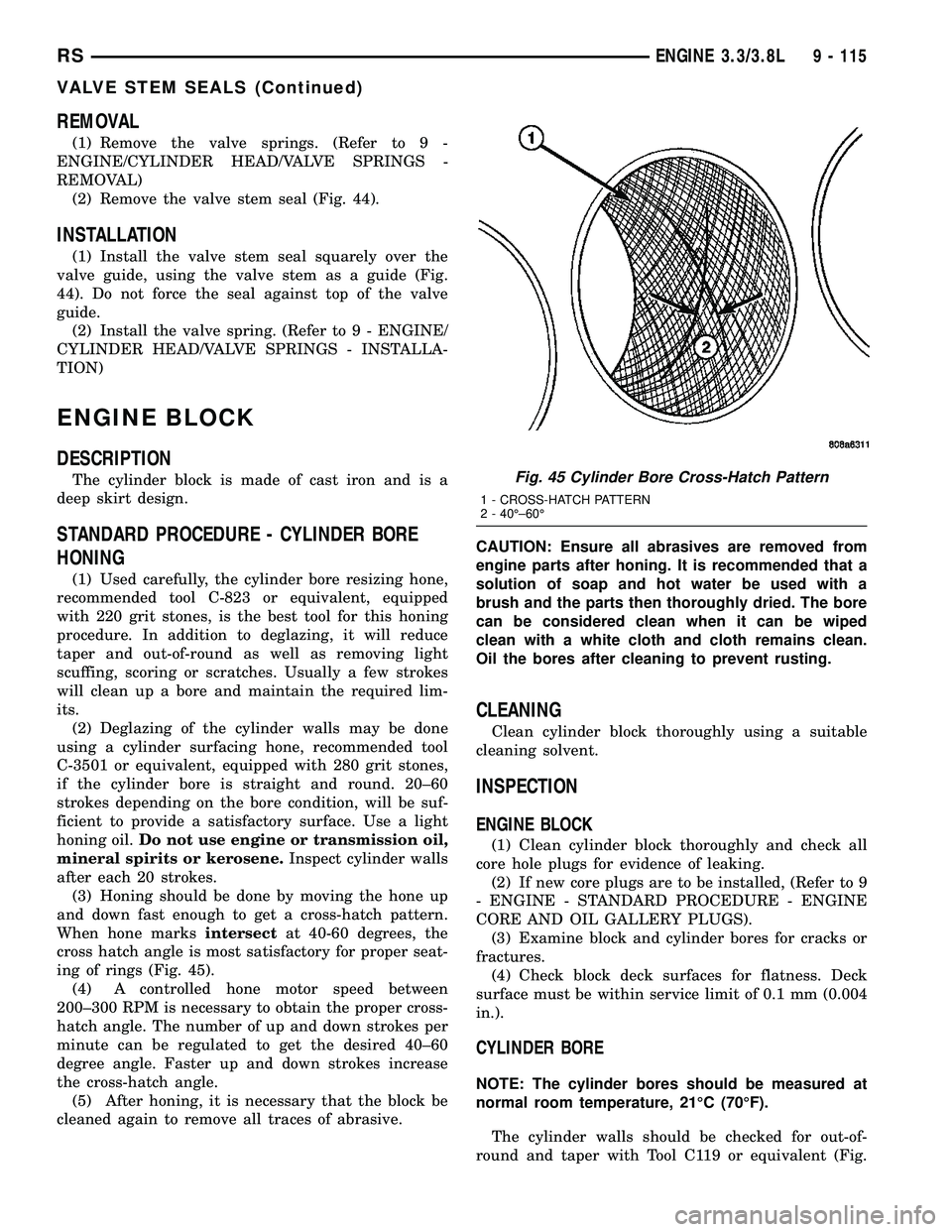
REMOVAL
(1) Remove the valve springs. (Refer to 9 -
ENGINE/CYLINDER HEAD/VALVE SPRINGS -
REMOVAL)
(2) Remove the valve stem seal (Fig. 44).
INSTALLATION
(1) Install the valve stem seal squarely over the
valve guide, using the valve stem as a guide (Fig.
44). Do not force the seal against top of the valve
guide.
(2) Install the valve spring. (Refer to 9 - ENGINE/
CYLINDER HEAD/VALVE SPRINGS - INSTALLA-
TION)
ENGINE BLOCK
DESCRIPTION
The cylinder block is made of cast iron and is a
deep skirt design.
STANDARD PROCEDURE - CYLINDER BORE
HONING
(1) Used carefully, the cylinder bore resizing hone,
recommended tool C-823 or equivalent, equipped
with 220 grit stones, is the best tool for this honing
procedure. In addition to deglazing, it will reduce
taper and out-of-round as well as removing light
scuffing, scoring or scratches. Usually a few strokes
will clean up a bore and maintain the required lim-
its.
(2) Deglazing of the cylinder walls may be done
using a cylinder surfacing hone, recommended tool
C-3501 or equivalent, equipped with 280 grit stones,
if the cylinder bore is straight and round. 20±60
strokes depending on the bore condition, will be suf-
ficient to provide a satisfactory surface. Use a light
honing oil.Do not use engine or transmission oil,
mineral spirits or kerosene.Inspect cylinder walls
after each 20 strokes.
(3) Honing should be done by moving the hone up
and down fast enough to get a cross-hatch pattern.
When hone marksintersectat 40-60 degrees, the
cross hatch angle is most satisfactory for proper seat-
ing of rings (Fig. 45).
(4) A controlled hone motor speed between
200±300 RPM is necessary to obtain the proper cross-
hatch angle. The number of up and down strokes per
minute can be regulated to get the desired 40±60
degree angle. Faster up and down strokes increase
the cross-hatch angle.
(5) After honing, it is necessary that the block be
cleaned again to remove all traces of abrasive.CAUTION: Ensure all abrasives are removed from
engine parts after honing. It is recommended that a
solution of soap and hot water be used with a
brush and the parts then thoroughly dried. The bore
can be considered clean when it can be wiped
clean with a white cloth and cloth remains clean.
Oil the bores after cleaning to prevent rusting.
CLEANING
Clean cylinder block thoroughly using a suitable
cleaning solvent.
INSPECTION
ENGINE BLOCK
(1) Clean cylinder block thoroughly and check all
core hole plugs for evidence of leaking.
(2) If new core plugs are to be installed, (Refer to 9
- ENGINE - STANDARD PROCEDURE - ENGINE
CORE AND OIL GALLERY PLUGS).
(3) Examine block and cylinder bores for cracks or
fractures.
(4) Check block deck surfaces for flatness. Deck
surface must be within service limit of 0.1 mm (0.004
in.).
CYLINDER BORE
NOTE: The cylinder bores should be measured at
normal room temperature, 21ÉC (70ÉF).
The cylinder walls should be checked for out-of-
round and taper with Tool C119 or equivalent (Fig.
Fig. 45 Cylinder Bore Cross-Hatch Pattern
1 - CROSS-HATCH PATTERN
2 - 40ɱ60É
RSENGINE 3.3/3.8L9 - 115
VALVE STEM SEALS (Continued)
Page 2324 of 2339
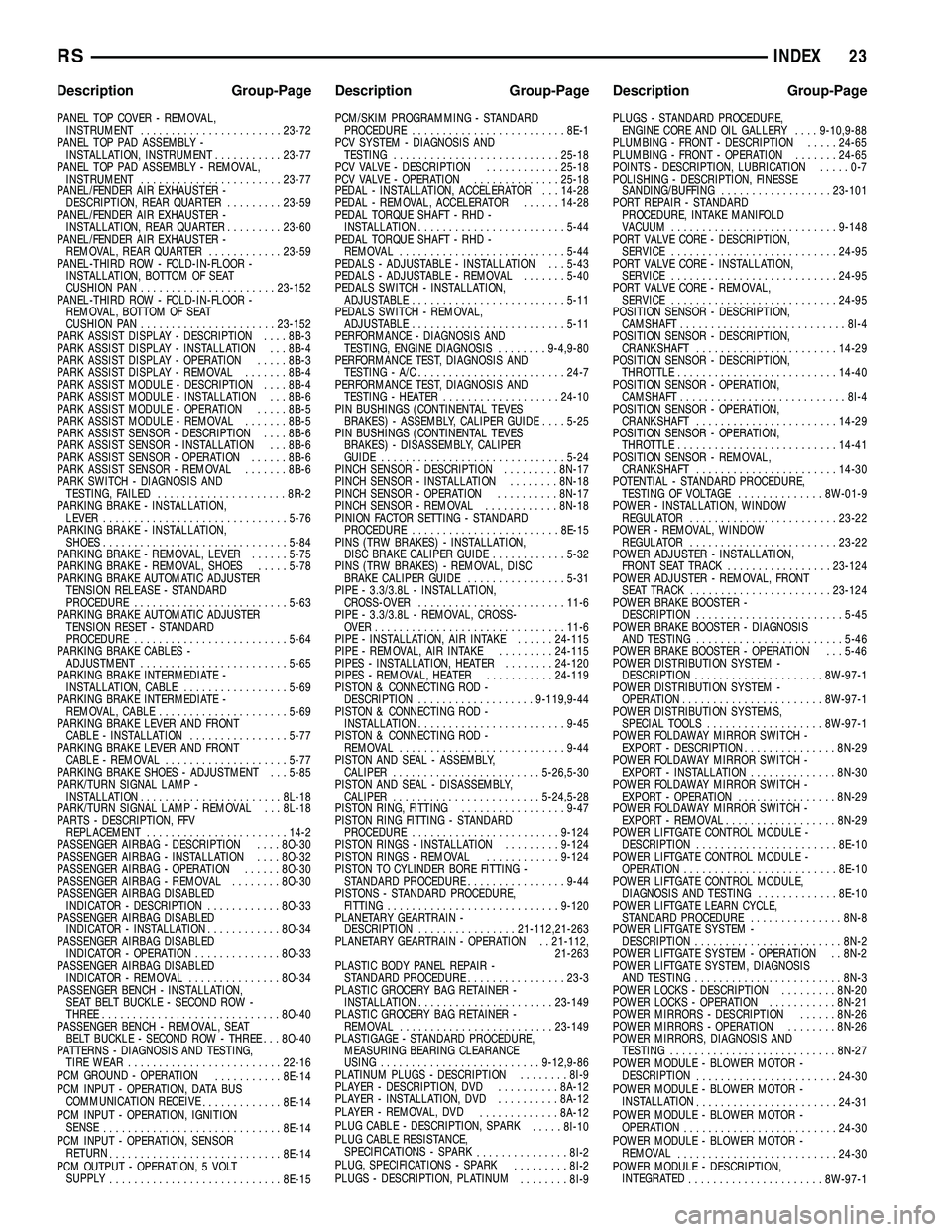
PANEL TOP COVER - REMOVAL,INSTRUMENT ....................... 23-72
PANEL TOP PAD ASSEMBLY - INSTALLATION, INSTRUMENT ...........23-77
PANEL TOP PAD ASSEMBLY - REMOVAL, INSTRUMENT ....................... 23-77
PANEL/FENDER AIR EXHAUSTER - DESCRIPTION, REAR QUARTER .........23-59
PANEL/FENDER AIR EXHAUSTER - INSTALLATION, REAR QUARTER .........23-60
PANEL/FENDER AIR EXHAUSTER - REMOVAL, REAR QUARTER ............23-59
PANEL-THIRD ROW - FOLD-IN-FLOOR - INSTALLATION, BOTTOM OF SEAT
CUSHION PAN ...................... 23-152
PANEL-THIRD ROW - FOLD-IN-FLOOR - REMOVAL, BOTTOM OF SEAT
CUSHION PAN ...................... 23-152
PARK ASSIST DISPLAY - DESCRIPTION ....8B-3
PARK ASSIST DISPLAY - INSTALLATION . . . 8B-4
PARK ASSIST DISPLAY - OPERATION .....8B-3
PARK ASSIST DISPLAY - REMOVAL .......8B-4
PARK ASSIST MODULE - DESCRIPTION ....8B-4
PARK ASSIST MODULE - INSTALLATION . . . 8B-6
PARK ASSIST MODULE - OPERATION .....8B-5
PARK ASSIST MODULE - REMOVAL .......8B-5
PARK ASSIST SENSOR - DESCRIPTION ....8B-6
PARK ASSIST SENSOR - INSTALLATION . . . 8B-6
PARK ASSIST SENSOR - OPERATION ......8B-6
PARK ASSIST SENSOR - REMOVAL .......8B-6
PARK SWITCH - DIAGNOSIS AND TESTING, FAILED ..................... 8R-2
PARKING BRAKE - INSTALLATION, LEVER .............................. 5-76
PARKING BRAKE - INSTALLATION, SHOES .............................. 5-84
PARKING BRAKE - REMOVAL, LEVER ......5-75
PARKING BRAKE - REMOVAL, SHOES .....5-78
PARKING BRAKE AUTOMATIC ADJUSTER TENSION RELEASE - STANDARD
PROCEDURE ......................... 5-63
PARKING BRAKE AUTOMATIC ADJUSTER TENSION RESET - STANDARD
PROCEDURE ......................... 5-64
PARKING BRAKE CABLES - ADJUSTMENT ........................ 5-65
PARKING BRAKE INTERMEDIATE - INSTALLATION, CABLE .................5-69
PARKING BRAKE INTERMEDIATE - REMOVAL, CABLE ..................... 5-69
PARKING BRAKE LEVER AND FRONT CABLE - INSTALLATION ................5-77
PARKING BRAKE LEVER AND FRONT CABLE - REMOVAL .................... 5-77
PARKING BRAKE SHOES - ADJUSTMENT . . . 5-85
PARK/TURN SIGNAL LAMP - INSTALLATION ....................... 8L-18
PARK/TURN SIGNAL LAMP - REMOVAL . . . 8L-18
PARTS - DESCRIPTION, FFV REPLACEMENT ....................... 14-2
PASSENGER AIRBAG - DESCRIPTION ....8O-30
PASSENGER AIRBAG - INSTALLATION ....8O-32
PASSENGER AIRBAG - OPERATION ......8O-30
PASSENGER AIRBAG - REMOVAL ........8O-30
PASSENGER AIRBAG DISABLED INDICATOR - DESCRIPTION ............8O-33
PASSENGER AIRBAG DISABLED INDICATOR - INSTALLATION ............8O-34
PASSENGER AIRBAG DISABLED INDICATOR - OPERATION ..............8O-33
PASSENGER AIRBAG DISABLED INDICATOR - REMOVAL ...............8O-34
PASSENGER BENCH - INSTALLATION, SEAT BELT BUCKLE - SECOND ROW -
THREE ............................. 8O-40
PASSENGER BENCH - REMOVAL, SEAT BELT BUCKLE - SECOND ROW - THREE . . . 8O-40
PATTERNS - DIAGNOSIS AND TESTING, TIRE WEAR ......................... 22-16
PCM GROUND - OPERATION ...........8E-14
PCM INPUT - OPERATION, DATA BUS COMMUNICATION RECEIVE .............8E-14
PCM INPUT - OPERATION, IGNITION SENSE ............................. 8E-14
PCM INPUT - OPERATION, SENSOR RETURN ............................ 8E-14
PCM OUTPUT - OPERATION, 5 VOLT SUPPLY ............................ 8E-15PCM/SKIM PROGRAMMING - STANDARD
PROCEDURE ......................... 8E-1
PCV SYSTEM - DIAGNOSIS AND TESTING ........................... 25-18
PCV VALVE - DESCRIPTION ............25-18
PCV VALVE - OPERATION ..............25-18
PEDAL - INSTALLATION, ACCELERATOR . . . 14-28
PEDAL - REMOVAL, ACCELERATOR ......14-28
PEDAL TORQUE SHAFT - RHD - INSTALLATION ........................ 5-44
PEDAL TORQUE SHAFT - RHD - REMOVAL ........................... 5-44
PEDALS - ADJUSTABLE - INSTALLATION . . . 5-43
PEDALS - ADJUSTABLE - REMOVAL .......5-40
PEDALS SWITCH - INSTALLATION, ADJUSTABLE ......................... 5-11
PEDALS SWITCH - REMOVAL, ADJUSTABLE ......................... 5-11
PERFORMANCE - DIAGNOSIS AND TESTING, ENGINE DIAGNOSIS ........9-4,9-80
PERFORMANCE TEST, DIAGNOSIS AND TESTING - A/C ........................ 24-7
PERFORMANCE TEST, DIAGNOSIS AND TESTING - HEATER ................... 24-10
PIN BUSHINGS (CONTINENTAL TEVES BRAKES) - ASSEMBLY, CALIPER GUIDE ....5-25
PIN BUSHINGS (CONTINENTAL TEVES BRAKES) - DISASSEMBLY, CALIPER
GUIDE .............................. 5-24
PINCH SENSOR - DESCRIPTION .........8N-17
PINCH SENSOR - INSTALLATION ........8N-18
PINCH SENSOR - OPERATION ..........8N-17
PINCH SENSOR - REMOVAL ............8N-18
PINION FACTOR SETTING - STANDARD PROCEDURE ........................ 8E-15
PINS (TRW BRAKES) - INSTALLATION, DISC BRAKE CALIPER GUIDE ............5-32
PINS (TRW BRAKES) - REMOVAL, DISC BRAKE CALIPER GUIDE ................5-31
PIPE - 3.3/3.8L - INSTALLATION, CROSS-OVER ........................ 11-6
PIPE - 3.3/3.8L - REMOVAL, CROSS- OVER ............................... 11-6
PIPE - INSTALLATION, AIR INTAKE ......24-115
PIPE - REMOVAL, AIR INTAKE .........24-115
PIPES - INSTALLATION, HEATER ........24-120
PIPES - REMOVAL, HEATER ...........24-119
PISTON & CONNECTING ROD - DESCRIPTION ................... 9-119,9-44
PISTON & CONNECTING ROD - INSTALLATION ........................ 9-45
PISTON & CONNECTING ROD - REMOVAL ........................... 9-44
PISTON AND SEAL - ASSEMBLY, CALIPER ........................ 5-26,5-30
PISTON AND SEAL - DISASSEMBLY, CALIPER ........................ 5-24,5-28
PISTON RING, FITTING .................9-47
PISTON RING FITTING - STANDARD PROCEDURE ........................ 9-124
PISTON RINGS - INSTALLATION .........9-124
PISTON RINGS - REMOVAL ............9-124
PISTON TO CYLINDER BORE FITTING - STANDARD PROCEDURE ................9-44
PISTONS - STANDARD PROCEDURE, FITTING ............................ 9-120
PLANETARY GEARTRAIN - DESCRIPTION ................ 21-112,21-263
PLANETARY GEARTRAIN - OPERATION . . 21-112, 21-263
PLASTIC BODY PANEL REPAIR - STANDARD PROCEDURE ................23-3
PLASTIC GROCERY BAG RETAINER - INSTALLATION ...................... 23-149
PLASTIC GROCERY BAG RETAINER - REMOVAL ......................... 23-149
PLASTIGAGE - STANDARD PROCEDURE, MEASURING BEARING CLEARANCE
USING .......................... 9-12,9-86
PLATINUM PLUGS - DESCRIPTION ........8I-9
PLAYER - DESCRIPTION, DVD ..........8A-12
PLAYER - INSTALLATION, DVD ..........8A-12
PLAYER - REMOVAL, DVD .............8A-12
PLUG CABLE - DESCRIPTION, SPARK .....8I-10
PLUG CABLE RESISTANCE, SPECIFICATIONS - SPARK ...............8I-2
PLUG, SPECIFICATIONS - SPARK .........8I-2
PLUGS - DESCRIPTION, PLATINUM ........8I-9PLUGS - STANDARD PROCEDURE,
ENGINE CORE AND OIL GALLERY ....9-10,9-88
PLUMBING - FRONT - DESCRIPTION .....24-65
PLUMBING - FRONT - OPERATION .......24-65
POINTS - DESCRIPTION, LUBRICATION .....0-7
POLISHING - DESCRIPTION, FINESSE SANDING/BUFFING .................. 23-101
PORT REPAIR - STANDARD PROCEDURE, INTAKE MANIFOLD
VACUUM ........................... 9-148
PORT VALVE CORE - DESCRIPTION, SERVICE ........................... 24-95
PORT VALVE CORE - INSTALLATION, SERVICE ........................... 24-95
PORT VALVE CORE - REMOVAL, SERVICE ........................... 24-95
POSITION SENSOR - DESCRIPTION, CAMSHAFT ........................... 8I-4
POSITION SENSOR - DESCRIPTION, CRANKSHAFT ....................... 14-29
POSITION SENSOR - DESCRIPTION, THROTTLE .......................... 14-40
POSITION SENSOR - OPERATION, CAMSHAFT ........................... 8I-4
POSITION SENSOR - OPERATION, CRANKSHAFT ....................... 14-29
POSITION SENSOR - OPERATION, THROTTLE .......................... 14-41
POSITION SENSOR - REMOVAL, CRANKSHAFT ....................... 14-30
POTENTIAL - STANDARD PROCEDURE, TESTING OF VOLTAGE ..............8W-01-9
POWER - INSTALLATION, WINDOW REGULATOR ........................ 23-22
POWER - REMOVAL, WINDOW REGULATOR ........................ 23-22
POWER ADJUSTER - INSTALLATION, FRONT SEAT TRACK .................23-124
POWER ADJUSTER - REMOVAL, FRONT SEAT TRACK ....................... 23-124
POWER BRAKE BOOSTER - DESCRIPTION ........................ 5-45
POWER BRAKE BOOSTER - DIAGNOSIS AND TESTING ........................ 5-46
POWER BRAKE BOOSTER - OPERATION . . . 5-46
POWER DISTRIBUTION SYSTEM - DESCRIPTION .....................8W -97-1
POWER DISTRIBUTION SYSTEM - OPERATION .......................8W -97-1
POWER DISTRIBUTION SYSTEMS, SPECIAL TOOLS ...................8W -97-1
POWER FOLDAWAY MIRROR SWITCH - EXPORT - DESCRIPTION ...............8N-29
POWER FOLDAWAY MIRROR SWITCH - EXPORT - INSTALLATION ..............8N-30
POWER FOLDAWAY MIRROR SWITCH - EXPORT - OPERATION ................8N-29
POWER FOLDAWAY MIRROR SWITCH - EXPORT - REMOVAL .................. 8N-29
POWER LIFTGATE CONTROL MODULE - DESCRIPTION ....................... 8E-10
POWER LIFTGATE CONTROL MODULE - OPERATION ......................... 8E-10
POWER LIFTGATE CONTROL MODULE, DIAGNOSIS AND TESTING .............8E-10
POWER LIFTGATE LEARN CYCLE, STANDARD PROCEDURE ...............8N-8
POWER LIFTGATE SYSTEM - DESCRIPTION ........................ 8N-2
POWER LIFTGATE SYSTEM - OPERATION . . 8N-2
POWER LIFTGATE SYSTEM, DIAGNOSIS AND TESTING ........................ 8N-3
POWER LOCKS - DESCRIPTION .........8N-20
POWER LOCKS - OPERATION ...........8N-21
POWER MIRRORS - DESCRIPTION ......8N-26
POWER MIRRORS - OPERATION ........8N-26
POWER MIRRORS, DIAGNOSIS AND TESTING ........................... 8N-27
POWER MODULE - BLOWER MOTOR - DESCRIPTION ....................... 24-30
POWER MODULE - BLOWER MOTOR - INSTALLATION ....................... 24-31
POWER MODULE - BLOWER MOTOR - OPERATION ......................... 24-30
POWER MODULE - BLOWER MOTOR - REMOVAL .......................... 24-30
POWER MODULE - DESCRIPTION, INTEGRATED ......................8W -97-1
RS INDEX23
Description Group-Page Description Group-Page Description Group-Page