oil capacities CHRYSLER CARAVAN 2005 Service Manual
[x] Cancel search | Manufacturer: CHRYSLER, Model Year: 2005, Model line: CARAVAN, Model: CHRYSLER CARAVAN 2005Pages: 2339, PDF Size: 59.69 MB
Page 14 of 2339
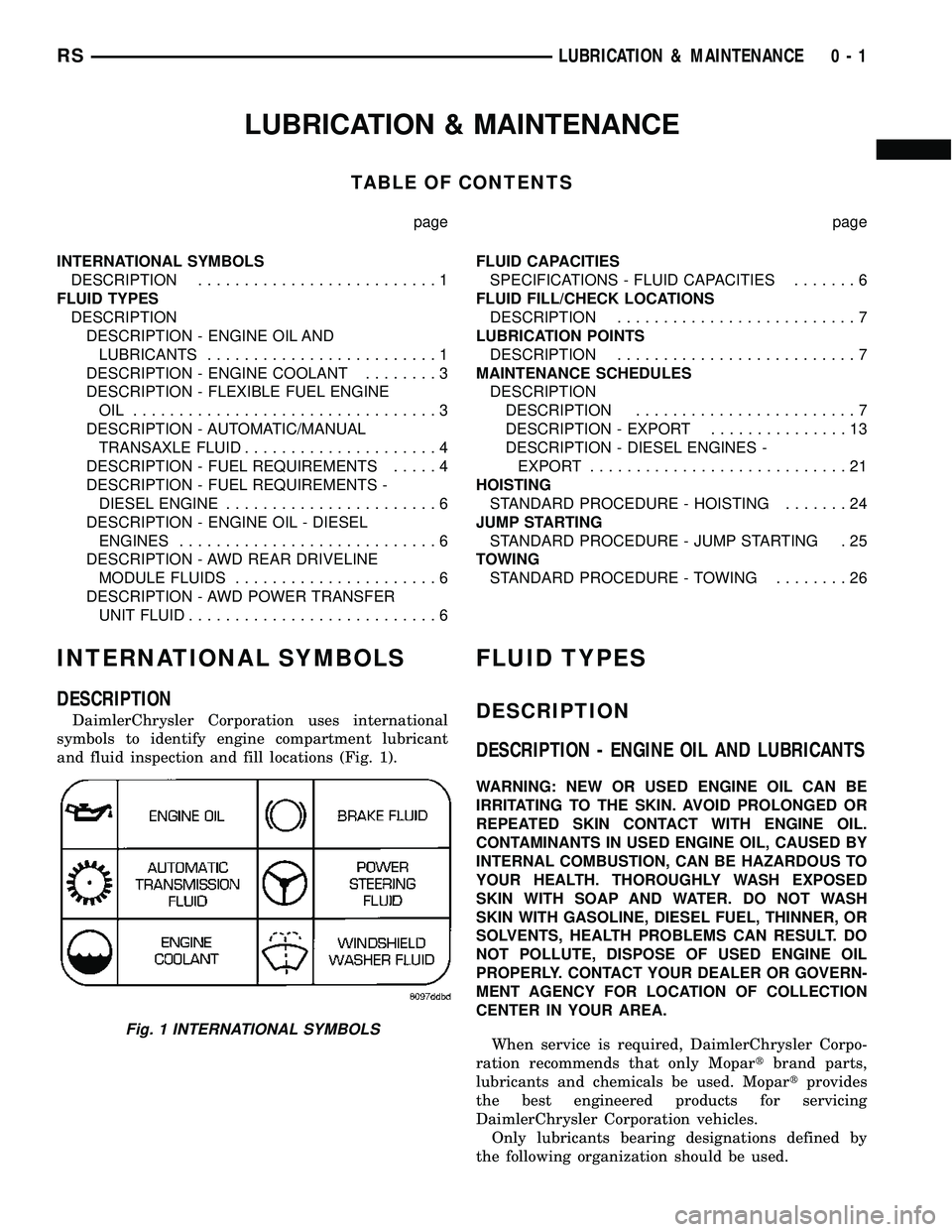
LUBRICATION & MAINTENANCE
TABLE OF CONTENTS
page page
INTERNATIONAL SYMBOLS
DESCRIPTION..........................1
FLUID TYPES
DESCRIPTION
DESCRIPTION - ENGINE OIL AND
LUBRICANTS.........................1
DESCRIPTION - ENGINE COOLANT........3
DESCRIPTION - FLEXIBLE FUEL ENGINE
OIL .................................3
DESCRIPTION - AUTOMATIC/MANUAL
TRANSAXLE FLUID.....................4
DESCRIPTION - FUEL REQUIREMENTS.....4
DESCRIPTION - FUEL REQUIREMENTS -
DIESEL ENGINE.......................6
DESCRIPTION - ENGINE OIL - DIESEL
ENGINES............................6
DESCRIPTION - AWD REAR DRIVELINE
MODULE FLUIDS......................6
DESCRIPTION - AWD POWER TRANSFER
UNIT FLUID...........................6FLUID CAPACITIES
SPECIFICATIONS - FLUID CAPACITIES.......6
FLUID FILL/CHECK LOCATIONS
DESCRIPTION..........................7
LUBRICATION POINTS
DESCRIPTION..........................7
MAINTENANCE SCHEDULES
DESCRIPTION
DESCRIPTION........................7
DESCRIPTION - EXPORT...............13
DESCRIPTION - DIESEL ENGINES -
EXPORT............................21
HOISTING
STANDARD PROCEDURE - HOISTING.......24
JUMP STARTING
STANDARD PROCEDURE - JUMP STARTING . 25
TOWING
STANDARD PROCEDURE - TOWING........26
INTERNATIONAL SYMBOLS
DESCRIPTION
DaimlerChrysler Corporation uses international
symbols to identify engine compartment lubricant
and fluid inspection and fill locations (Fig. 1).
FLUID TYPES
DESCRIPTION
DESCRIPTION - ENGINE OIL AND LUBRICANTS
WARNING: NEW OR USED ENGINE OIL CAN BE
IRRITATING TO THE SKIN. AVOID PROLONGED OR
REPEATED SKIN CONTACT WITH ENGINE OIL.
CONTAMINANTS IN USED ENGINE OIL, CAUSED BY
INTERNAL COMBUSTION, CAN BE HAZARDOUS TO
YOUR HEALTH. THOROUGHLY WASH EXPOSED
SKIN WITH SOAP AND WATER. DO NOT WASH
SKIN WITH GASOLINE, DIESEL FUEL, THINNER, OR
SOLVENTS, HEALTH PROBLEMS CAN RESULT. DO
NOT POLLUTE, DISPOSE OF USED ENGINE OIL
PROPERLY. CONTACT YOUR DEALER OR GOVERN-
MENT AGENCY FOR LOCATION OF COLLECTION
CENTER IN YOUR AREA.
When service is required, DaimlerChrysler Corpo-
ration recommends that only Mopartbrand parts,
lubricants and chemicals be used. Mopartprovides
the best engineered products for servicing
DaimlerChrysler Corporation vehicles.
Only lubricants bearing designations defined by
the following organization should be used.
Fig. 1 INTERNATIONAL SYMBOLS
RSLUBRICATION & MAINTENANCE0-1
Page 19 of 2339
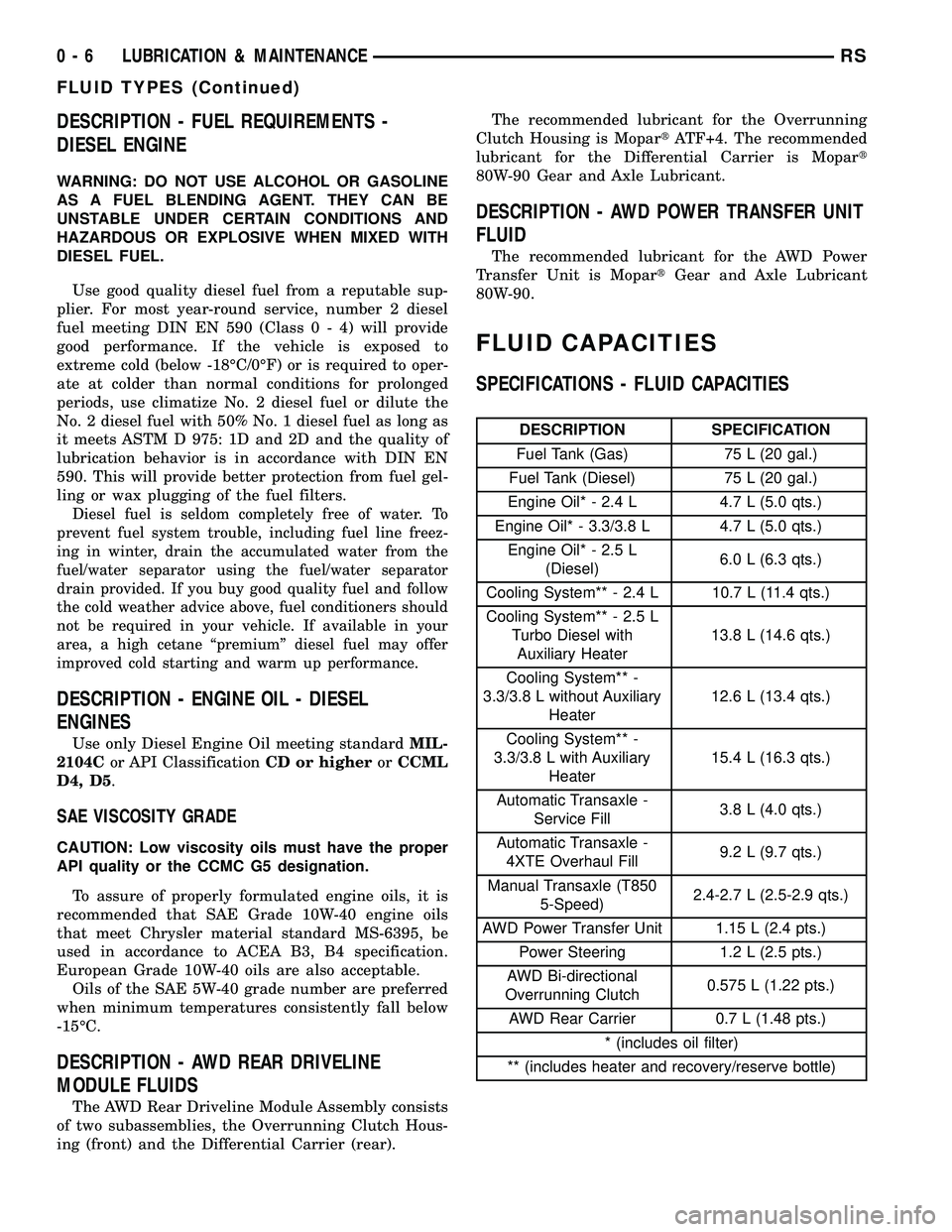
DESCRIPTION - FUEL REQUIREMENTS -
DIESEL ENGINE
WARNING: DO NOT USE ALCOHOL OR GASOLINE
AS A FUEL BLENDING AGENT. THEY CAN BE
UNSTABLE UNDER CERTAIN CONDITIONS AND
HAZARDOUS OR EXPLOSIVE WHEN MIXED WITH
DIESEL FUEL.
Use good quality diesel fuel from a reputable sup-
plier. For most year-round service, number 2 diesel
fuel meeting DIN EN 590 (Class0-4)will provide
good performance. If the vehicle is exposed to
extreme cold (below -18ÉC/0ÉF) or is required to oper-
ate at colder than normal conditions for prolonged
periods, use climatize No. 2 diesel fuel or dilute the
No. 2 diesel fuel with 50% No. 1 diesel fuel as long as
it meets ASTM D 975: 1D and 2D and the quality of
lubrication behavior is in accordance with DIN EN
590. This will provide better protection from fuel gel-
ling or wax plugging of the fuel filters.
Diesel fuel is seldom completely free of water. To
prevent fuel system trouble, including fuel line freez-
ing in winter, drain the accumulated water from the
fuel/water separator using the fuel/water separator
drain provided. If you buy good quality fuel and follow
the cold weather advice above, fuel conditioners should
not be required in your vehicle. If available in your
area, a high cetane ªpremiumº diesel fuel may offer
improved cold starting and warm up performance.
DESCRIPTION - ENGINE OIL - DIESEL
ENGINES
Use only Diesel Engine Oil meeting standardMIL-
2104Cor API ClassificationCD or higherorCCML
D4, D5.
SAE VISCOSITY GRADE
CAUTION: Low viscosity oils must have the proper
API quality or the CCMC G5 designation.
To assure of properly formulated engine oils, it is
recommended that SAE Grade 10W-40 engine oils
that meet Chrysler material standard MS-6395, be
used in accordance to ACEA B3, B4 specification.
European Grade 10W-40 oils are also acceptable.
Oils of the SAE 5W-40 grade number are preferred
when minimum temperatures consistently fall below
-15ÉC.
DESCRIPTION - AWD REAR DRIVELINE
MODULE FLUIDS
The AWD Rear Driveline Module Assembly consists
of two subassemblies, the Overrunning Clutch Hous-
ing (front) and the Differential Carrier (rear).The recommended lubricant for the Overrunning
Clutch Housing is MopartATF+4. The recommended
lubricant for the Differential Carrier is Mopart
80W-90 Gear and Axle Lubricant.
DESCRIPTION - AWD POWER TRANSFER UNIT
FLUID
The recommended lubricant for the AWD Power
Transfer Unit is MopartGear and Axle Lubricant
80W-90.
FLUID CAPACITIES
SPECIFICATIONS - FLUID CAPACITIES
DESCRIPTION SPECIFICATION
Fuel Tank (Gas) 75 L (20 gal.)
Fuel Tank (Diesel) 75 L (20 gal.)
Engine Oil* - 2.4 L 4.7 L (5.0 qts.)
Engine Oil* - 3.3/3.8 L 4.7 L (5.0 qts.)
Engine Oil* - 2.5 L
(Diesel)6.0 L (6.3 qts.)
Cooling System** - 2.4 L 10.7 L (11.4 qts.)
Cooling System** - 2.5 L
Turbo Diesel with
Auxiliary Heater13.8 L (14.6 qts.)
Cooling System** -
3.3/3.8 L without Auxiliary
Heater12.6 L (13.4 qts.)
Cooling System** -
3.3/3.8 L with Auxiliary
Heater15.4 L (16.3 qts.)
Automatic Transaxle -
Service Fill3.8 L (4.0 qts.)
Automatic Transaxle -
4XTE Overhaul Fill9.2 L (9.7 qts.)
Manual Transaxle (T850
5-Speed)2.4-2.7 L (2.5-2.9 qts.)
AWD Power Transfer Unit 1.15 L (2.4 pts.)
Power Steering 1.2 L (2.5 pts.)
AWD Bi-directional
Overrunning Clutch0.575 L (1.22 pts.)
AWD Rear Carrier 0.7 L (1.48 pts.)
* (includes oil filter)
** (includes heater and recovery/reserve bottle)
0 - 6 LUBRICATION & MAINTENANCERS
FLUID TYPES (Continued)
Page 2169 of 2339
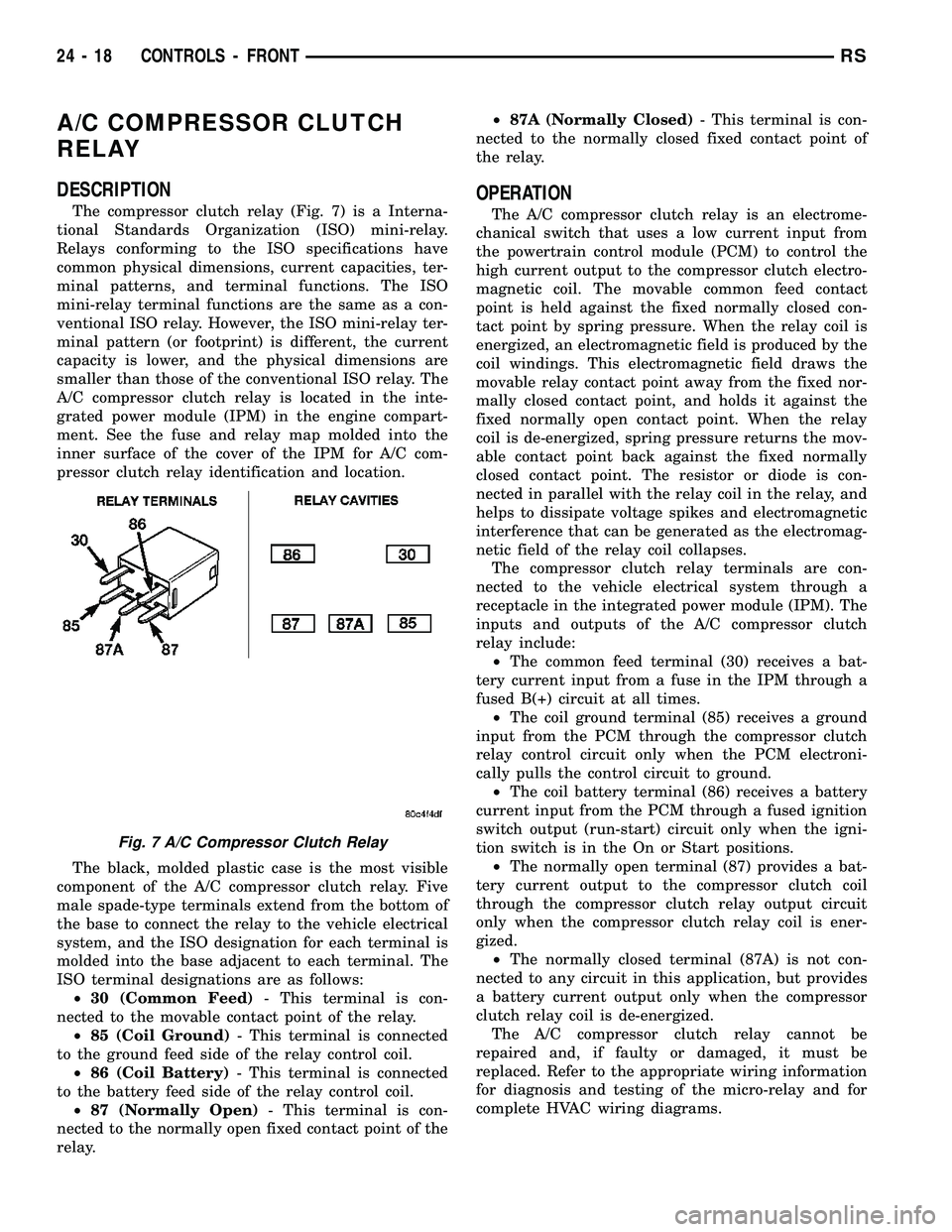
A/C COMPRESSOR CLUTCH
RELAY
DESCRIPTION
The compressor clutch relay (Fig. 7) is a Interna-
tional Standards Organization (ISO) mini-relay.
Relays conforming to the ISO specifications have
common physical dimensions, current capacities, ter-
minal patterns, and terminal functions. The ISO
mini-relay terminal functions are the same as a con-
ventional ISO relay. However, the ISO mini-relay ter-
minal pattern (or footprint) is different, the current
capacity is lower, and the physical dimensions are
smaller than those of the conventional ISO relay. The
A/C compressor clutch relay is located in the inte-
grated power module (IPM) in the engine compart-
ment. See the fuse and relay map molded into the
inner surface of the cover of the IPM for A/C com-
pressor clutch relay identification and location.
The black, molded plastic case is the most visible
component of the A/C compressor clutch relay. Five
male spade-type terminals extend from the bottom of
the base to connect the relay to the vehicle electrical
system, and the ISO designation for each terminal is
molded into the base adjacent to each terminal. The
ISO terminal designations are as follows:
²30 (Common Feed)- This terminal is con-
nected to the movable contact point of the relay.
²85 (Coil Ground)- This terminal is connected
to the ground feed side of the relay control coil.
²86 (Coil Battery)- This terminal is connected
to the battery feed side of the relay control coil.
²87 (Normally Open)- This terminal is con-
nected to the normally open fixed contact point of the
relay.²87A (Normally Closed)- This terminal is con-
nected to the normally closed fixed contact point of
the relay.
OPERATION
The A/C compressor clutch relay is an electrome-
chanical switch that uses a low current input from
the powertrain control module (PCM) to control the
high current output to the compressor clutch electro-
magnetic coil. The movable common feed contact
point is held against the fixed normally closed con-
tact point by spring pressure. When the relay coil is
energized, an electromagnetic field is produced by the
coil windings. This electromagnetic field draws the
movable relay contact point away from the fixed nor-
mally closed contact point, and holds it against the
fixed normally open contact point. When the relay
coil is de-energized, spring pressure returns the mov-
able contact point back against the fixed normally
closed contact point. The resistor or diode is con-
nected in parallel with the relay coil in the relay, and
helps to dissipate voltage spikes and electromagnetic
interference that can be generated as the electromag-
netic field of the relay coil collapses.
The compressor clutch relay terminals are con-
nected to the vehicle electrical system through a
receptacle in the integrated power module (IPM). The
inputs and outputs of the A/C compressor clutch
relay include:
²The common feed terminal (30) receives a bat-
tery current input from a fuse in the IPM through a
fused B(+) circuit at all times.
²The coil ground terminal (85) receives a ground
input from the PCM through the compressor clutch
relay control circuit only when the PCM electroni-
cally pulls the control circuit to ground.
²The coil battery terminal (86) receives a battery
current input from the PCM through a fused ignition
switch output (run-start) circuit only when the igni-
tion switch is in the On or Start positions.
²The normally open terminal (87) provides a bat-
tery current output to the compressor clutch coil
through the compressor clutch relay output circuit
only when the compressor clutch relay coil is ener-
gized.
²The normally closed terminal (87A) is not con-
nected to any circuit in this application, but provides
a battery current output only when the compressor
clutch relay coil is de-energized.
The A/C compressor clutch relay cannot be
repaired and, if faulty or damaged, it must be
replaced. Refer to the appropriate wiring information
for diagnosis and testing of the micro-relay and for
complete HVAC wiring diagrams.
Fig. 7 A/C Compressor Clutch Relay
24 - 18 CONTROLS - FRONTRS
Page 2174 of 2339
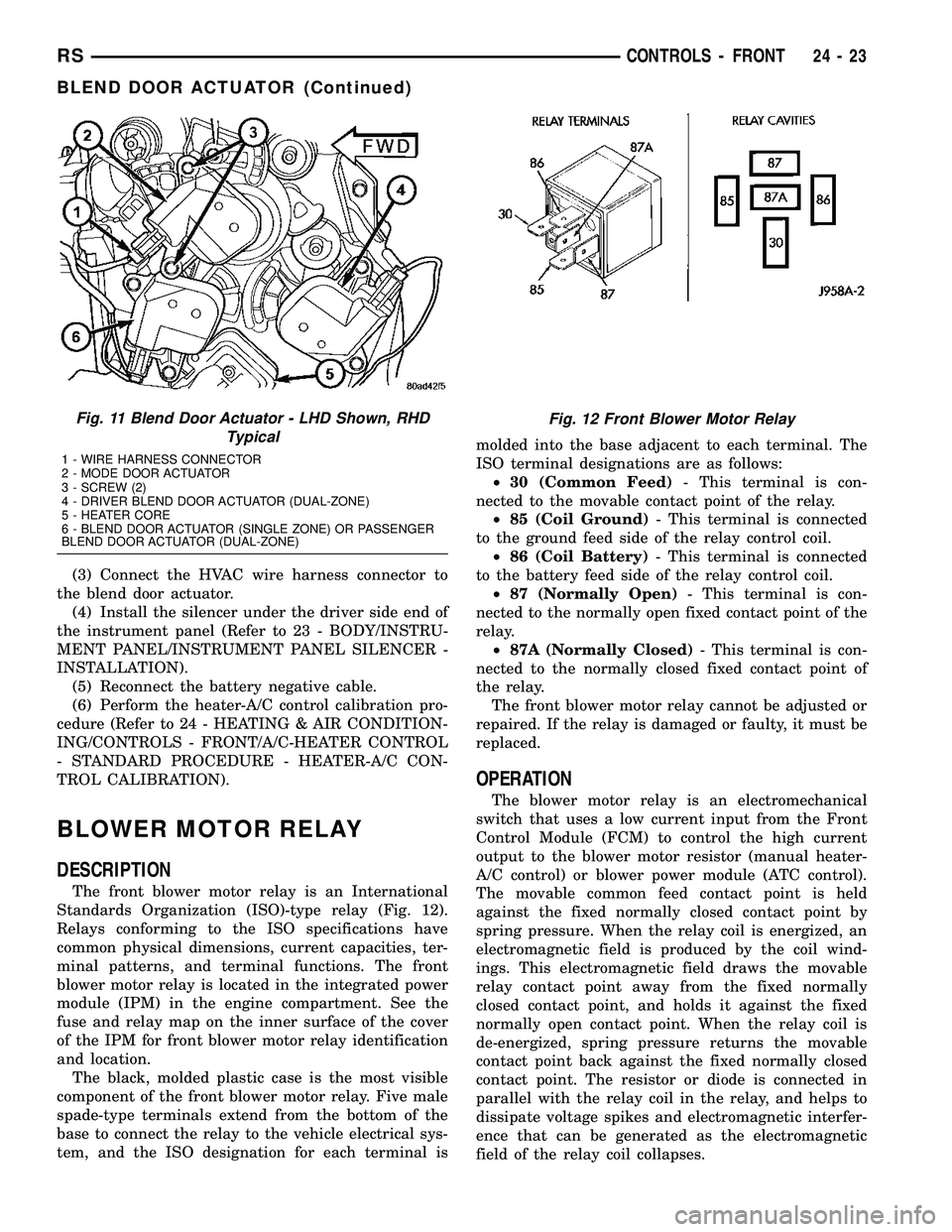
(3) Connect the HVAC wire harness connector to
the blend door actuator.
(4) Install the silencer under the driver side end of
the instrument panel (Refer to 23 - BODY/INSTRU-
MENT PANEL/INSTRUMENT PANEL SILENCER -
INSTALLATION).
(5) Reconnect the battery negative cable.
(6) Perform the heater-A/C control calibration pro-
cedure (Refer to 24 - HEATING & AIR CONDITION-
ING/CONTROLS - FRONT/A/C-HEATER CONTROL
- STANDARD PROCEDURE - HEATER-A/C CON-
TROL CALIBRATION).
BLOWER MOTOR RELAY
DESCRIPTION
The front blower motor relay is an International
Standards Organization (ISO)-type relay (Fig. 12).
Relays conforming to the ISO specifications have
common physical dimensions, current capacities, ter-
minal patterns, and terminal functions. The front
blower motor relay is located in the integrated power
module (IPM) in the engine compartment. See the
fuse and relay map on the inner surface of the cover
of the IPM for front blower motor relay identification
and location.
The black, molded plastic case is the most visible
component of the front blower motor relay. Five male
spade-type terminals extend from the bottom of the
base to connect the relay to the vehicle electrical sys-
tem, and the ISO designation for each terminal ismolded into the base adjacent to each terminal. The
ISO terminal designations are as follows:
²30 (Common Feed)- This terminal is con-
nected to the movable contact point of the relay.
²85 (Coil Ground)- This terminal is connected
to the ground feed side of the relay control coil.
²86 (Coil Battery)- This terminal is connected
to the battery feed side of the relay control coil.
²87 (Normally Open)- This terminal is con-
nected to the normally open fixed contact point of the
relay.
²87A (Normally Closed)- This terminal is con-
nected to the normally closed fixed contact point of
the relay.
The front blower motor relay cannot be adjusted or
repaired. If the relay is damaged or faulty, it must be
replaced.
OPERATION
The blower motor relay is an electromechanical
switch that uses a low current input from the Front
Control Module (FCM) to control the high current
output to the blower motor resistor (manual heater-
A/C control) or blower power module (ATC control).
The movable common feed contact point is held
against the fixed normally closed contact point by
spring pressure. When the relay coil is energized, an
electromagnetic field is produced by the coil wind-
ings. This electromagnetic field draws the movable
relay contact point away from the fixed normally
closed contact point, and holds it against the fixed
normally open contact point. When the relay coil is
de-energized, spring pressure returns the movable
contact point back against the fixed normally closed
contact point. The resistor or diode is connected in
parallel with the relay coil in the relay, and helps to
dissipate voltage spikes and electromagnetic interfer-
ence that can be generated as the electromagnetic
field of the relay coil collapses.
Fig. 11 Blend Door Actuator - LHD Shown, RHD
Typical
1 - WIRE HARNESS CONNECTOR
2 - MODE DOOR ACTUATOR
3 - SCREW (2)
4 - DRIVER BLEND DOOR ACTUATOR (DUAL-ZONE)
5 - HEATER CORE
6 - BLEND DOOR ACTUATOR (SINGLE ZONE) OR PASSENGER
BLEND DOOR ACTUATOR (DUAL-ZONE)
Fig. 12 Front Blower Motor Relay
RSCONTROLS - FRONT24-23
BLEND DOOR ACTUATOR (Continued)
Page 2187 of 2339
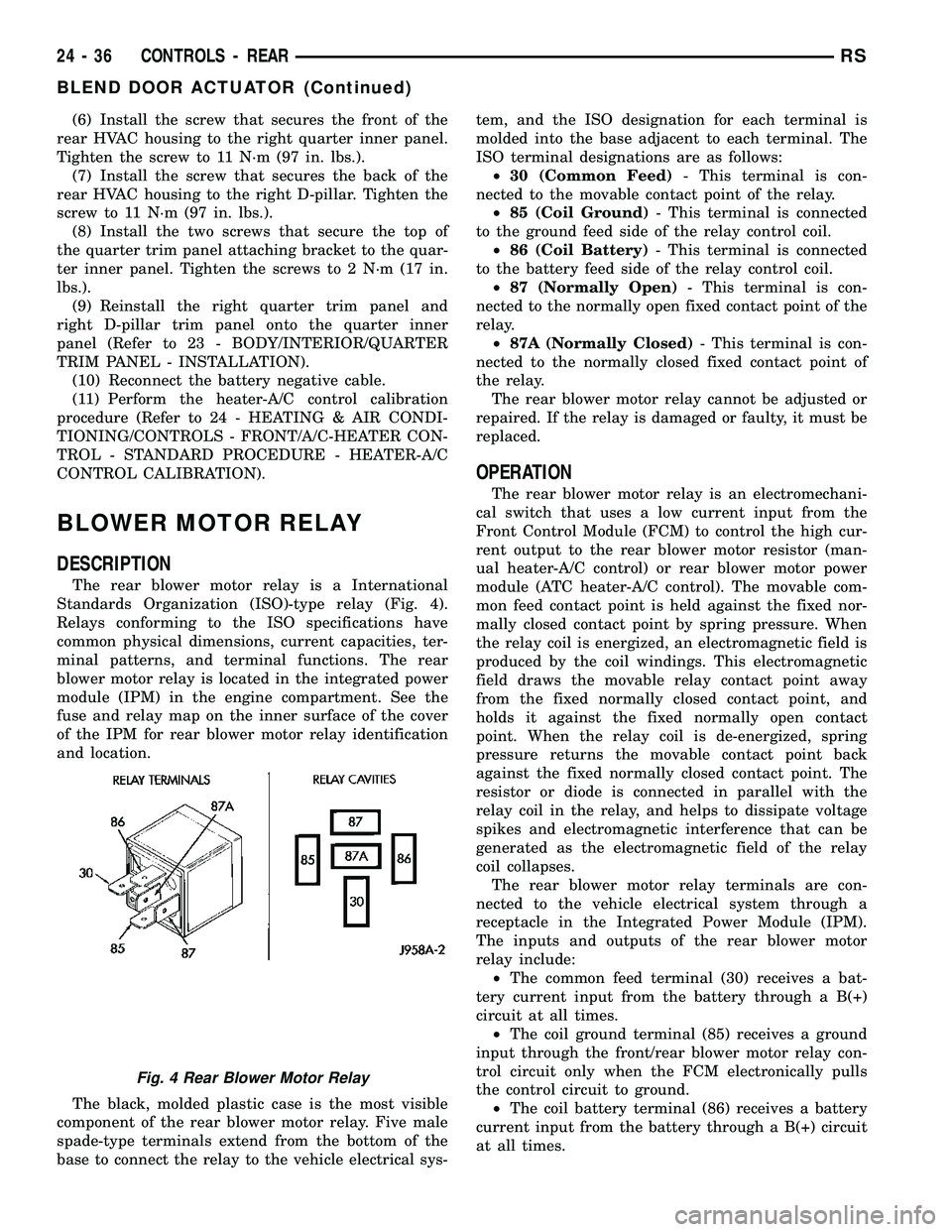
(6) Install the screw that secures the front of the
rear HVAC housing to the right quarter inner panel.
Tighten the screw to 11 N´m (97 in. lbs.).
(7) Install the screw that secures the back of the
rear HVAC housing to the right D-pillar. Tighten the
screw to 11 N´m (97 in. lbs.).
(8) Install the two screws that secure the top of
the quarter trim panel attaching bracket to the quar-
ter inner panel. Tighten the screws to 2 N´m (17 in.
lbs.).
(9) Reinstall the right quarter trim panel and
right D-pillar trim panel onto the quarter inner
panel (Refer to 23 - BODY/INTERIOR/QUARTER
TRIM PANEL - INSTALLATION).
(10) Reconnect the battery negative cable.
(11) Perform the heater-A/C control calibration
procedure (Refer to 24 - HEATING & AIR CONDI-
TIONING/CONTROLS - FRONT/A/C-HEATER CON-
TROL - STANDARD PROCEDURE - HEATER-A/C
CONTROL CALIBRATION).
BLOWER MOTOR RELAY
DESCRIPTION
The rear blower motor relay is a International
Standards Organization (ISO)-type relay (Fig. 4).
Relays conforming to the ISO specifications have
common physical dimensions, current capacities, ter-
minal patterns, and terminal functions. The rear
blower motor relay is located in the integrated power
module (IPM) in the engine compartment. See the
fuse and relay map on the inner surface of the cover
of the IPM for rear blower motor relay identification
and location.
The black, molded plastic case is the most visible
component of the rear blower motor relay. Five male
spade-type terminals extend from the bottom of the
base to connect the relay to the vehicle electrical sys-tem, and the ISO designation for each terminal is
molded into the base adjacent to each terminal. The
ISO terminal designations are as follows:
²30 (Common Feed)- This terminal is con-
nected to the movable contact point of the relay.
²85 (Coil Ground)- This terminal is connected
to the ground feed side of the relay control coil.
²86 (Coil Battery)- This terminal is connected
to the battery feed side of the relay control coil.
²87 (Normally Open)- This terminal is con-
nected to the normally open fixed contact point of the
relay.
²87A (Normally Closed)- This terminal is con-
nected to the normally closed fixed contact point of
the relay.
The rear blower motor relay cannot be adjusted or
repaired. If the relay is damaged or faulty, it must be
replaced.
OPERATION
The rear blower motor relay is an electromechani-
cal switch that uses a low current input from the
Front Control Module (FCM) to control the high cur-
rent output to the rear blower motor resistor (man-
ual heater-A/C control) or rear blower motor power
module (ATC heater-A/C control). The movable com-
mon feed contact point is held against the fixed nor-
mally closed contact point by spring pressure. When
the relay coil is energized, an electromagnetic field is
produced by the coil windings. This electromagnetic
field draws the movable relay contact point away
from the fixed normally closed contact point, and
holds it against the fixed normally open contact
point. When the relay coil is de-energized, spring
pressure returns the movable contact point back
against the fixed normally closed contact point. The
resistor or diode is connected in parallel with the
relay coil in the relay, and helps to dissipate voltage
spikes and electromagnetic interference that can be
generated as the electromagnetic field of the relay
coil collapses.
The rear blower motor relay terminals are con-
nected to the vehicle electrical system through a
receptacle in the Integrated Power Module (IPM).
The inputs and outputs of the rear blower motor
relay include:
²The common feed terminal (30) receives a bat-
tery current input from the battery through a B(+)
circuit at all times.
²The coil ground terminal (85) receives a ground
input through the front/rear blower motor relay con-
trol circuit only when the FCM electronically pulls
the control circuit to ground.
²The coil battery terminal (86) receives a battery
current input from the battery through a B(+) circuit
at all times.
Fig. 4 Rear Blower Motor Relay
24 - 36 CONTROLS - REARRS
BLEND DOOR ACTUATOR (Continued)
Page 2245 of 2339
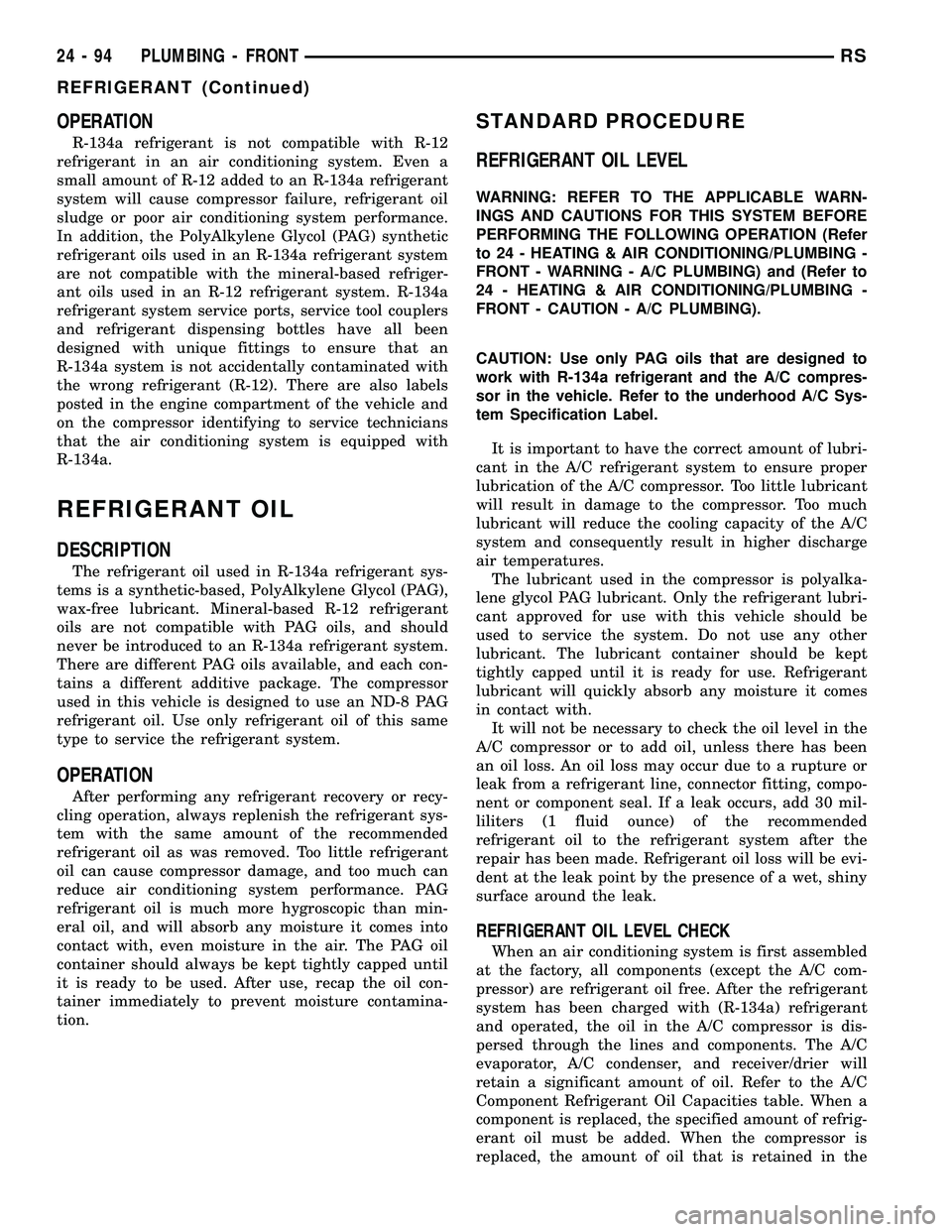
OPERATION
R-134a refrigerant is not compatible with R-12
refrigerant in an air conditioning system. Even a
small amount of R-12 added to an R-134a refrigerant
system will cause compressor failure, refrigerant oil
sludge or poor air conditioning system performance.
In addition, the PolyAlkylene Glycol (PAG) synthetic
refrigerant oils used in an R-134a refrigerant system
are not compatible with the mineral-based refriger-
ant oils used in an R-12 refrigerant system. R-134a
refrigerant system service ports, service tool couplers
and refrigerant dispensing bottles have all been
designed with unique fittings to ensure that an
R-134a system is not accidentally contaminated with
the wrong refrigerant (R-12). There are also labels
posted in the engine compartment of the vehicle and
on the compressor identifying to service technicians
that the air conditioning system is equipped with
R-134a.
REFRIGERANT OIL
DESCRIPTION
The refrigerant oil used in R-134a refrigerant sys-
tems is a synthetic-based, PolyAlkylene Glycol (PAG),
wax-free lubricant. Mineral-based R-12 refrigerant
oils are not compatible with PAG oils, and should
never be introduced to an R-134a refrigerant system.
There are different PAG oils available, and each con-
tains a different additive package. The compressor
used in this vehicle is designed to use an ND-8 PAG
refrigerant oil. Use only refrigerant oil of this same
type to service the refrigerant system.
OPERATION
After performing any refrigerant recovery or recy-
cling operation, always replenish the refrigerant sys-
tem with the same amount of the recommended
refrigerant oil as was removed. Too little refrigerant
oil can cause compressor damage, and too much can
reduce air conditioning system performance. PAG
refrigerant oil is much more hygroscopic than min-
eral oil, and will absorb any moisture it comes into
contact with, even moisture in the air. The PAG oil
container should always be kept tightly capped until
it is ready to be used. After use, recap the oil con-
tainer immediately to prevent moisture contamina-
tion.
STANDARD PROCEDURE
REFRIGERANT OIL LEVEL
WARNING: REFER TO THE APPLICABLE WARN-
INGS AND CAUTIONS FOR THIS SYSTEM BEFORE
PERFORMING THE FOLLOWING OPERATION (Refer
to 24 - HEATING & AIR CONDITIONING/PLUMBING -
FRONT - WARNING - A/C PLUMBING) and (Refer to
24 - HEATING & AIR CONDITIONING/PLUMBING -
FRONT - CAUTION - A/C PLUMBING).
CAUTION: Use only PAG oils that are designed to
work with R-134a refrigerant and the A/C compres-
sor in the vehicle. Refer to the underhood A/C Sys-
tem Specification Label.
It is important to have the correct amount of lubri-
cant in the A/C refrigerant system to ensure proper
lubrication of the A/C compressor. Too little lubricant
will result in damage to the compressor. Too much
lubricant will reduce the cooling capacity of the A/C
system and consequently result in higher discharge
air temperatures.
The lubricant used in the compressor is polyalka-
lene glycol PAG lubricant. Only the refrigerant lubri-
cant approved for use with this vehicle should be
used to service the system. Do not use any other
lubricant. The lubricant container should be kept
tightly capped until it is ready for use. Refrigerant
lubricant will quickly absorb any moisture it comes
in contact with.
It will not be necessary to check the oil level in the
A/C compressor or to add oil, unless there has been
an oil loss. An oil loss may occur due to a rupture or
leak from a refrigerant line, connector fitting, compo-
nent or component seal. If a leak occurs, add 30 mil-
liliters (1 fluid ounce) of the recommended
refrigerant oil to the refrigerant system after the
repair has been made. Refrigerant oil loss will be evi-
dent at the leak point by the presence of a wet, shiny
surface around the leak.
REFRIGERANT OIL LEVEL CHECK
When an air conditioning system is first assembled
at the factory, all components (except the A/C com-
pressor) are refrigerant oil free. After the refrigerant
system has been charged with (R-134a) refrigerant
and operated, the oil in the A/C compressor is dis-
persed through the lines and components. The A/C
evaporator, A/C condenser, and receiver/drier will
retain a significant amount of oil. Refer to the A/C
Component Refrigerant Oil Capacities table. When a
component is replaced, the specified amount of refrig-
erant oil must be added. When the compressor is
replaced, the amount of oil that is retained in the
24 - 94 PLUMBING - FRONTRS
REFRIGERANT (Continued)
Page 2246 of 2339
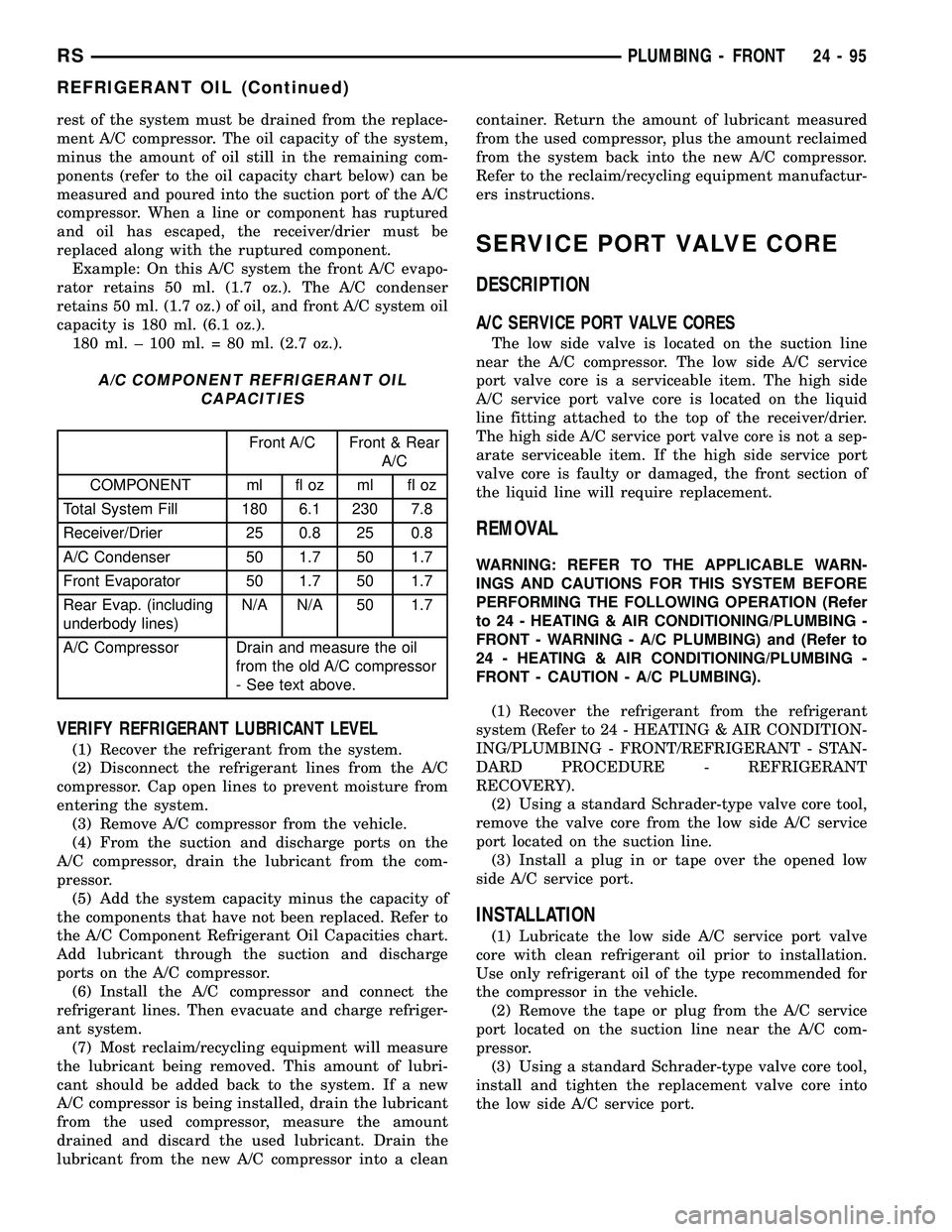
rest of the system must be drained from the replace-
ment A/C compressor. The oil capacity of the system,
minus the amount of oil still in the remaining com-
ponents (refer to the oil capacity chart below) can be
measured and poured into the suction port of the A/C
compressor. When a line or component has ruptured
and oil has escaped, the receiver/drier must be
replaced along with the ruptured component.
Example: On this A/C system the front A/C evapo-
rator retains 50 ml. (1.7 oz.). The A/C condenser
retains 50 ml. (1.7 oz.) of oil, and front A/C system oil
capacity is 180 ml. (6.1 oz.).
180 ml. ± 100 ml. = 80 ml. (2.7 oz.).
A/C COMPONENT REFRIGERANT OIL
CAPACITIES
Front A/C Front & Rear
A/C
COMPONENT ml fl oz ml fl oz
Total System Fill 180 6.1 230 7.8
Receiver/Drier 25 0.8 25 0.8
A/C Condenser 50 1.7 50 1.7
Front Evaporator 50 1.7 50 1.7
Rear Evap. (including
underbody lines)N/A N/A 50 1.7
A/C Compressor Drain and measure the oil
from the old A/C compressor
- See text above.
VERIFY REFRIGERANT LUBRICANT LEVEL
(1) Recover the refrigerant from the system.
(2) Disconnect the refrigerant lines from the A/C
compressor. Cap open lines to prevent moisture from
entering the system.
(3) Remove A/C compressor from the vehicle.
(4) From the suction and discharge ports on the
A/C compressor, drain the lubricant from the com-
pressor.
(5) Add the system capacity minus the capacity of
the components that have not been replaced. Refer to
the A/C Component Refrigerant Oil Capacities chart.
Add lubricant through the suction and discharge
ports on the A/C compressor.
(6) Install the A/C compressor and connect the
refrigerant lines. Then evacuate and charge refriger-
ant system.
(7) Most reclaim/recycling equipment will measure
the lubricant being removed. This amount of lubri-
cant should be added back to the system. If a new
A/C compressor is being installed, drain the lubricant
from the used compressor, measure the amount
drained and discard the used lubricant. Drain the
lubricant from the new A/C compressor into a cleancontainer. Return the amount of lubricant measured
from the used compressor, plus the amount reclaimed
from the system back into the new A/C compressor.
Refer to the reclaim/recycling equipment manufactur-
ers instructions.
SERVICE PORT VALVE CORE
DESCRIPTION
A/C SERVICE PORT VALVE CORES
The low side valve is located on the suction line
near the A/C compressor. The low side A/C service
port valve core is a serviceable item. The high side
A/C service port valve core is located on the liquid
line fitting attached to the top of the receiver/drier.
The high side A/C service port valve core is not a sep-
arate serviceable item. If the high side service port
valve core is faulty or damaged, the front section of
the liquid line will require replacement.
REMOVAL
WARNING: REFER TO THE APPLICABLE WARN-
INGS AND CAUTIONS FOR THIS SYSTEM BEFORE
PERFORMING THE FOLLOWING OPERATION (Refer
to 24 - HEATING & AIR CONDITIONING/PLUMBING -
FRONT - WARNING - A/C PLUMBING) and (Refer to
24 - HEATING & AIR CONDITIONING/PLUMBING -
FRONT - CAUTION - A/C PLUMBING).
(1) Recover the refrigerant from the refrigerant
system (Refer to 24 - HEATING & AIR CONDITION-
ING/PLUMBING - FRONT/REFRIGERANT - STAN-
DARD PROCEDURE - REFRIGERANT
RECOVERY).
(2) Using a standard Schrader-type valve core tool,
remove the valve core from the low side A/C service
port located on the suction line.
(3) Install a plug in or tape over the opened low
side A/C service port.
INSTALLATION
(1) Lubricate the low side A/C service port valve
core with clean refrigerant oil prior to installation.
Use only refrigerant oil of the type recommended for
the compressor in the vehicle.
(2) Remove the tape or plug from the A/C service
port located on the suction line near the A/C com-
pressor.
(3) Using a standard Schrader-type valve core tool,
install and tighten the replacement valve core into
the low side A/C service port.
RSPLUMBING - FRONT24-95
REFRIGERANT OIL (Continued)
Page 2307 of 2339
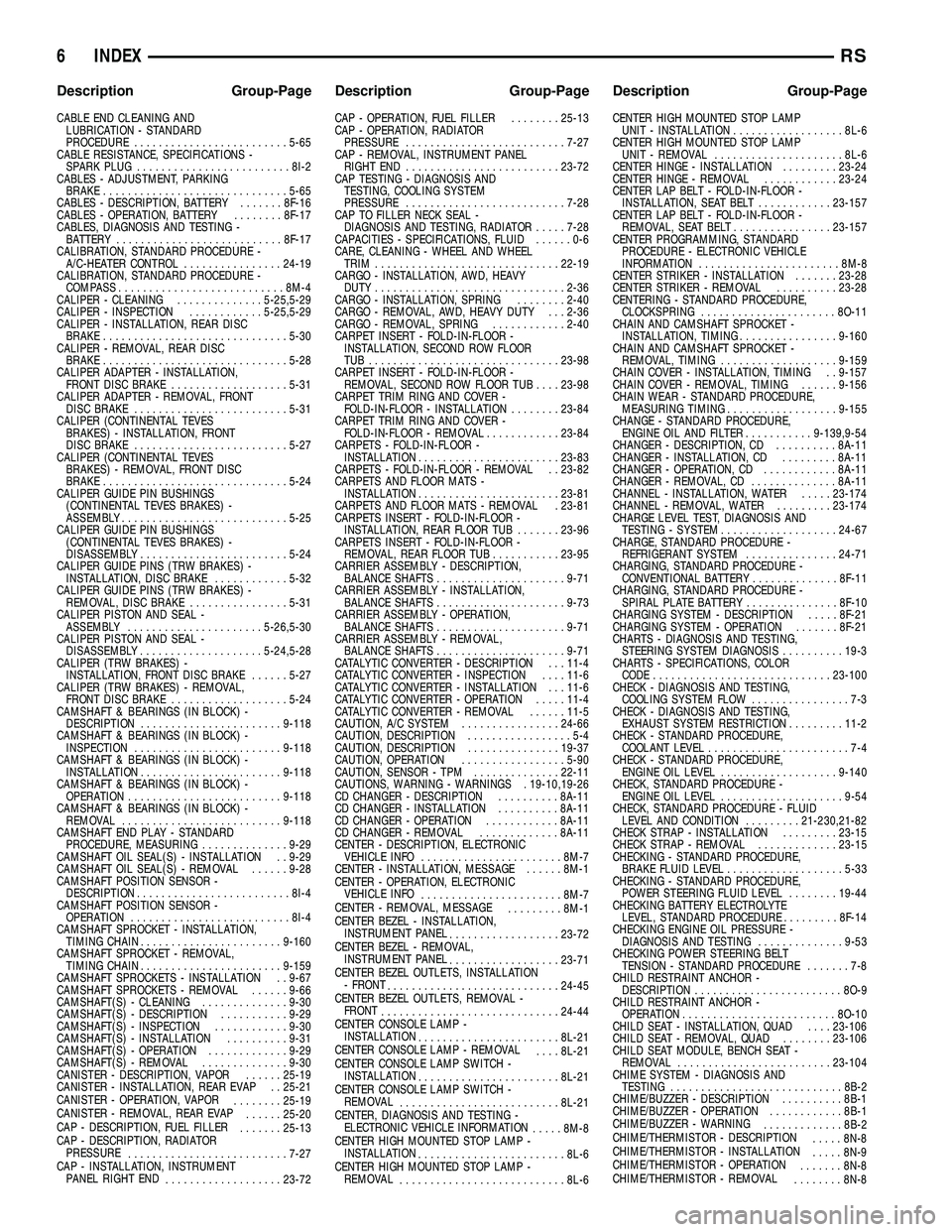
CABLE END CLEANING ANDLUBRICATION - STANDARD
PROCEDURE ......................... 5-65
CABLE RESISTANCE, SPECIFICATIONS - SPARK PLUG ......................... 8I-2
CABLES - ADJUSTMENT, PARKING BRAKE .............................. 5-65
CABLES - DESCRIPTION, BATTERY .......8F-16
CABLES - OPERATION, BATTERY ........8F-17
CABLES, DIAGNOSIS AND TESTING - BATTERY ........................... 8F-17
CALIBRATION, STANDARD PROCEDURE - A/C-HEATER CONTROL ................24-19
CALIBRATION, STANDARD PROCEDURE - COMPASS ........................... 8M-4
CALIPER - CLEANING ..............5-25,5-29
CALIPER - INSPECTION ............5-25,5-29
CALIPER - INSTALLATION, REAR DISC BRAKE .............................. 5-30
CALIPER - REMOVAL, REAR DISC BRAKE .............................. 5-28
CALIPER ADAPTER - INSTALLATION, FRONT DISC BRAKE ................... 5-31
CALIPER ADAPTER - REMOVAL, FRONT DISC BRAKE ......................... 5-31
CALIPER (CONTINENTAL TEVES BRAKES) - INSTALLATION, FRONT
DISC BRAKE ......................... 5-27
CALIPER (CONTINENTAL TEVES BRAKES) - REMOVAL, FRONT DISC
BRAKE .............................. 5-24
CALIPER GUIDE PIN BUSHINGS (CONTINENTAL TEVES BRAKES) -
ASSEMBLY ............................ 5-25
CALIPER GUIDE PIN BUSHINGS (CONTINENTAL TEVES BRAKES) -
DISASSEMBLY ........................ 5-24
CALIPER GUIDE PINS (TRW BRAKES) - INSTALLATION, DISC BRAKE ............5-32
CALIPER GUIDE PINS (TRW BRAKES) - REMOVAL, DISC BRAKE ................5-31
CALIPER PISTON AND SEAL - ASSEMBLY ...................... 5-26,5-30
CALIPER PISTON AND SEAL - DISASSEMBLY .................... 5-24,5-28
CALIPER (TRW BRAKES) - INSTALLATION, FRONT DISC BRAKE ......5-27
CALIPER (TRW BRAKES) - REMOVAL, FRONT DISC BRAKE ................... 5-24
CAMSHAFT & BEARINGS (IN BLOCK) - DESCRIPTION ....................... 9-118
CAMSHAFT & BEARINGS (IN BLOCK) - INSPECTION ........................ 9-118
CAMSHAFT & BEARINGS (IN BLOCK) - INSTALLATION ....................... 9-118
CAMSHAFT & BEARINGS (IN BLOCK) - OPERATION ......................... 9-118
CAMSHAFT & BEARINGS (IN BLOCK) - REMOVAL .......................... 9-118
CAMSHAFT END PLAY - STANDARD PROCEDURE, MEASURING ..............9-29
CAMSHAFT OIL SEAL(S) - INSTALLATION . . 9-29
CAMSHAFT OIL SEAL(S) - REMOVAL ......9-28
CAMSHAFT POSITION SENSOR - DESCRIPTION ......................... 8I-4
CAMSHAFT POSITION SENSOR - OPERATION .......................... 8I-4
CAMSHAFT SPROCKET - INSTALLATION, TIMING CHAIN ....................... 9-160
CAMSHAFT SPROCKET - REMOVAL, TIMING CHAIN ....................... 9-159
CAMSHAFT SPROCKETS - INSTALLATION . . 9-67
CAMSHAFT SPROCKETS - REMOVAL ......9-66
CAMSHAFT(S) - CLEANING ..............9-30
CAMSHAFT(S) - DESCRIPTION ...........9-29
CAMSHAFT(S) - INSPECTION ............9-30
CAMSHAFT(S) - INSTALLATION ..........9-31
CAMSHAFT(S) - OPERATION .............9-29
CAMSHAFT(S) - REMOVAL ..............9-30
CANISTER - DESCRIPTION, VAPOR ......25-19
CANISTER - INSTALLATION, REAR EVAP . . 25-21
CANISTER - OPERATION, VAPOR ........25-19
CANISTER - REMOVAL, REAR EVAP ......25-20
CAP - DESCRIPTION, FUEL FILLER .......25-13
CAP - DESCRIPTION, RADIATOR PRESSURE .......................... 7-27
CAP - INSTALLATION, INSTRUMENT PANEL RIGHT END ................... 23-72CAP - OPERATION, FUEL FILLER
........25-13
CAP - OPERATION, RADIATOR PRESSURE .......................... 7-27
CAP - REMOVAL, INSTRUMENT PANEL RIGHT END ......................... 23-72
CAP TESTING - DIAGNOSIS AND TESTING, COOLING SYSTEM
PRESSURE .......................... 7-28
CAP TO FILLER NECK SEAL - DIAGNOSIS AND TESTING, RADIATOR .....7-28
CAPACITIES - SPECIFICATIONS, FLUID ......0-6
CARE, CLEANING - WHEEL AND WHEEL TRIM .............................. 22-19
CARGO - INSTALLATION, AWD, HEAVY DUTY ............................... 2-36
CARGO - INSTALLATION, SPRING ........2-40
CARGO - REMOVAL, AWD, HEAVY DUTY . . . 2-36
CARGO - REMOVAL, SPRING ............2-40
CARPET INSERT - FOLD-IN-FLOOR - INSTALLATION, SECOND ROW FLOOR
TUB ............................... 23-98
CARPET INSERT - FOLD-IN-FLOOR - REMOVAL, SECOND ROW FLOOR TUB ....23-98
CARPET TRIM RING AND COVER - FOLD-IN-FLOOR - INSTALLATION ........23-84
CARPET TRIM RING AND COVER - FOLD-IN-FLOOR - REMOVAL ............23-84
CARPETS - FOLD-IN-FLOOR - INSTALLATION ....................... 23-83
CARPETS - FOLD-IN-FLOOR - REMOVAL . . 23-82
CARPETS AND FLOOR MATS - INSTALLATION ....................... 23-81
CARPETS AND FLOOR MATS - REMOVAL . 23-81
CARPETS INSERT - FOLD-IN-FLOOR - INSTALLATION, REAR FLOOR TUB .......23-96
CARPETS INSERT - FOLD-IN-FLOOR - REMOVAL, REAR FLOOR TUB ...........23-95
CARRIER ASSEMBLY - DESCRIPTION, BALANCE SHAFTS ..................... 9-71
CARRIER ASSEMBLY - INSTALLATION, BALANCE SHAFTS ..................... 9-73
CARRIER ASSEMBLY - OPERATION, BALANCE SHAFTS ..................... 9-71
CARRIER ASSEMBLY - REMOVAL, BALANCE SHAFTS ..................... 9-71
CATALYTIC CONVERTER - DESCRIPTION . . . 11-4
CATALYTIC CONVERTER - INSPECTION ....11-6
CATALYTIC CONVERTER - INSTALLATION . . . 11-6
CATALYTIC CONVERTER - OPERATION .....11-4
CATALYTIC CONVERTER - REMOVAL ......11-5
CAUTION, A/C SYSTEM ................24-66
CAUTION, DESCRIPTION .................5-4
CAUTION, DESCRIPTION ...............19-37
CAUTION, OPERATION .................5-90
CAUTION, SENSOR - TPM ..............22-11
CAUTIONS, WARNING - WARNINGS . 19-10,19-26
CD CHANGER - DESCRIPTION ..........8A-11
CD CHANGER - INSTALLATION ..........8A-11
CD CHANGER - OPERATION ............8A-11
CD CHANGER - REMOVAL .............8A-11
CENTER - DESCRIPTION, ELECTRONIC VEHICLE INFO ....................... 8M-7
CENTER - INSTALLATION, MESSAGE ......8M-1
CENTER - OPERATION, ELECTRONIC VEHICLE INFO ....................... 8M-7
CENTER - REMOVAL, MESSAGE .........8M-1
CENTER BEZEL - INSTALLATION, INSTRUMENT PANEL .................. 23-72
CENTER BEZEL - REMOVAL, INSTRUMENT PANEL .................. 23-71
CENTER BEZEL OUTLETS, INSTALLATION - FRONT ............................ 24-45
CENTER BEZEL OUTLETS, REMOVAL - FRONT ............................. 24-44
CENTER CONSOLE LAMP - INSTALLATION ....................... 8L-21
CENTER CONSOLE LAMP - REMOVAL ....8L-21
CENTER CONSOLE LAMP SWITCH - INSTALLATION ....................... 8L-21
CENTER CONSOLE LAMP SWITCH - REMOVAL .......................... 8L-21
CENTER, DIAGNOSIS AND TESTING - ELECTRONIC VEHICLE INFORMATION .....8M-8
CENTER HIGH MOUNTED STOP LAMP - INSTALLATION ........................ 8L-6
CENTER HIGH MOUNTED STOP LAMP - REMOVAL ........................... 8L-6CENTER HIGH MOUNTED STOP LAMP
UNIT - INSTALLATION .................. 8L-6
CENTER HIGH MOUNTED STOP LAMP UNIT - REMOVAL ..................... 8L-6
CENTER HINGE - INSTALLATION .........23-24
CENTER HINGE - REMOVAL ............23-24
CENTER LAP BELT - FOLD-IN-FLOOR - INSTALLATION, SEAT BELT ............23-157
CENTER LAP BELT - FOLD-IN-FLOOR - REMOVAL, SEAT BELT ................23-157
CENTER PROGRAMMING, STANDARD PROCEDURE - ELECTRONIC VEHICLE
INFORMATION ....................... 8M-8
CENTER STRIKER - INSTALLATION .......23-28
CENTER STRIKER - REMOVAL ..........23-28
CENTERING - STANDARD PROCEDURE, CLOCKSPRING ...................... 8O-11
CHAIN AND CAMSHAFT SPROCKET - INSTALLATION, TIMING ................9-160
CHAIN AND CAMSHAFT SPROCKET - REMOVAL, TIMING ................... 9-159
CHAIN COVER - INSTALLATION, TIMING . . 9-157
CHAIN COVER - REMOVAL, TIMING ......9-156
CHAIN WEAR - STANDARD PROCEDURE, MEASURING TIMING .................. 9-155
CHANGE - STANDARD PROCEDURE, ENGINE OIL AND FILTER ...........9-139,9-54
CHANGER - DESCRIPTION, CD ..........8A-11
CHANGER - INSTALLATION, CD .........8A-11
CHANGER - OPERATION, CD ............8A-11
CHANGER - REMOVAL, CD ..............8A-11
CHANNEL - INSTALLATION, WATER .....23-174
CHANNEL - REMOVAL, WATER .........23-174
CHARGE LEVEL TEST, DIAGNOSIS AND TESTING - SYSTEM ................... 24-67
CHARGE, STANDARD PROCEDURE - REFRIGERANT SYSTEM ...............24-71
CHARGING, STANDARD PROCEDURE - CONVENTIONAL BATTERY ..............8F-11
CHARGING, STANDARD PROCEDURE - SPIRAL PLATE BATTERY ...............8F-10
CHARGING SYSTEM - DESCRIPTION .....8F-21
CHARGING SYSTEM - OPERATION .......8F-21
CHARTS - DIAGNOSIS AND TESTING, STEERING SYSTEM DIAGNOSIS ..........19-3
CHARTS - SPECIFICATIONS, COLOR CODE ............................. 23-100
CHECK - DIAGNOSIS AND TESTING, COOLING SYSTEM FLOW ................7-3
CHECK - DIAGNOSIS AND TESTING, EXHAUST SYSTEM RESTRICTION .........11-2
CHECK - STANDARD PROCEDURE, COOLANT LEVEL .......................7-4
CHECK - STANDARD PROCEDURE, ENGINE OIL LEVEL ................... 9-140
CHECK, STANDARD PROCEDURE - ENGINE OIL LEVEL .................... 9-54
CHECK, STANDARD PROCEDURE - FLUID LEVEL AND CONDITION .........21-230,21-82
CHECK STRAP - INSTALLATION .........23-15
CHECK STRAP - REMOVAL .............23-15
CHECKING - STANDARD PROCEDURE, BRAKE FLUID LEVEL ................... 5-33
CHECKING - STANDARD PROCEDURE, POWER STEERING FLUID LEVEL ........19-44
CHECKING BATTERY ELECTROLYTE LEVEL, STANDARD PROCEDURE .........8F-14
CHECKING ENGINE OIL PRESSURE - DIAGNOSIS AND TESTING ..............9-53
CHECKING POWER STEERING BELT TENSION - STANDARD PROCEDURE .......7-8
CHILD RESTRAINT ANCHOR - DESCRIPTION ........................ 8O-9
CHILD RESTRAINT ANCHOR - OPERATION ......................... 8O-10
CHILD SEAT - INSTALLATION, QUAD ....23-106
CHILD SEAT - REMOVAL, QUAD ........23-106
CHILD SEAT MODULE, BENCH SEAT - REMOVAL ......................... 23-104
CHIME SYSTEM - DIAGNOSIS AND TESTING ............................ 8B-2
CHIME/BUZZER - DESCRIPTION ..........8B-1
CHIME/BUZZER - OPERATION ............8B-1
CHIME/BUZZER - WARNING .............8B-2
CHIME/THERMISTOR - DESCRIPTION .....8N-8
CHIME/THERMISTOR - INSTALLATION .....8N-9
CHIME/THERMISTOR - OPERATION .......8N-8
CHIME/THERMISTOR - REMOVAL ........8N-8
6 INDEXRS
Description Group-Page Description Group-Page Description Group-Page
Page 2314 of 2339
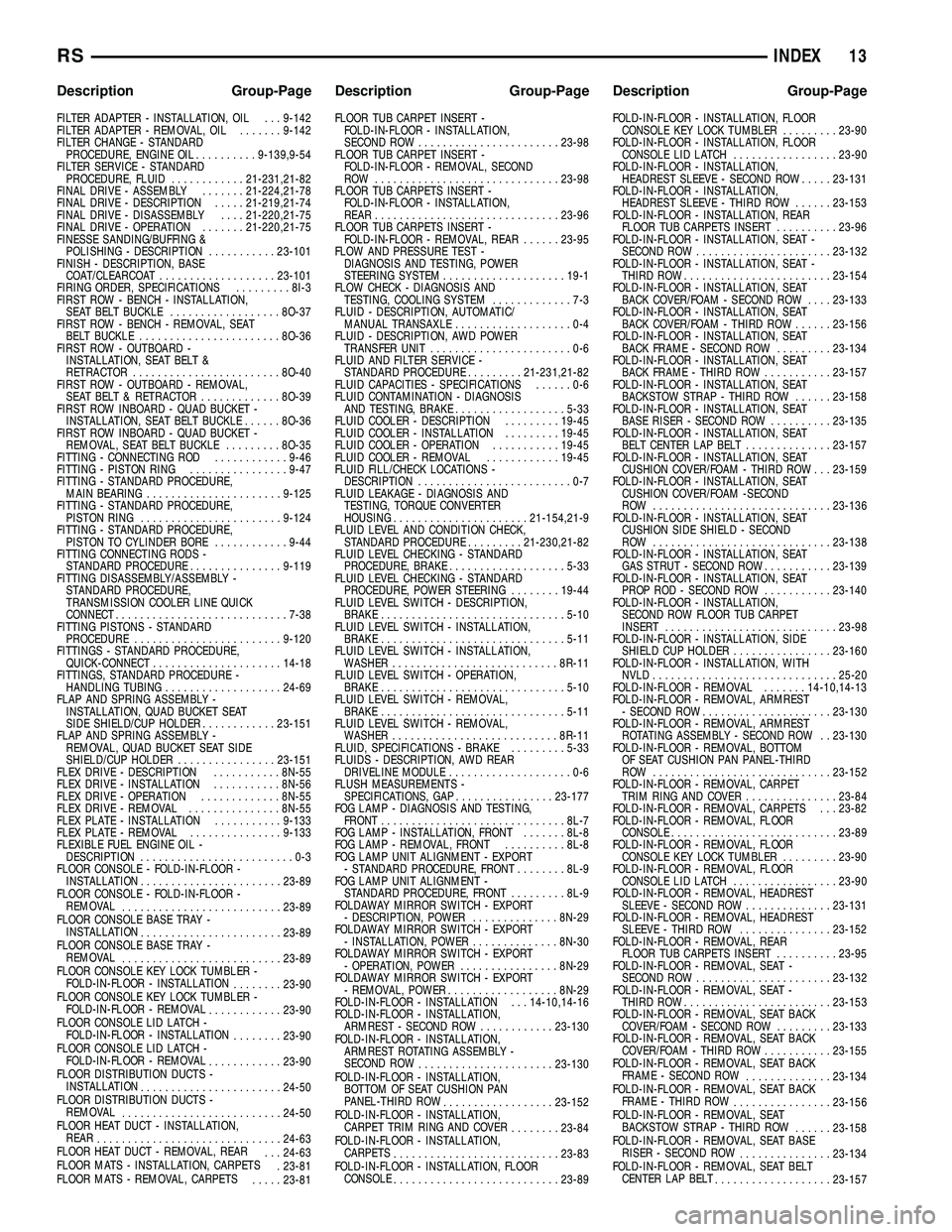
FILTER ADAPTER - INSTALLATION, OIL . . . 9-142
FILTER ADAPTER - REMOVAL, OIL.......9-142
FILTER CHANGE - STANDARD PROCEDURE, ENGINE OIL ..........9-139,9-54
FILTER SERVICE - STANDARD PROCEDURE, FLUID ............21-231,21-82
FINAL DRIVE - ASSEMBLY .......21-224,21-78
FINAL DRIVE - DESCRIPTION .....21-219,21-74
FINAL DRIVE - DISASSEMBLY ....21-220,21-75
FINAL DRIVE - OPERATION .......21-220,21-75
FINESSE SANDING/BUFFING & POLISHING - DESCRIPTION ...........23-101
FINISH - DESCRIPTION, BASE COAT/CLEARCOAT ................... 23-101
FIRING ORDER, SPECIFICATIONS .........8I-3
FIRST ROW - BENCH - INSTALLATION, SEAT BELT BUCKLE .................. 8O-37
FIRST ROW - BENCH - REMOVAL, SEAT BELT BUCKLE ....................... 8O-36
FIRST ROW - OUTBOARD - INSTALLATION, SEAT BELT &
RETRACTOR ........................ 8O-40
FIRST ROW - OUTBOARD - REMOVAL, SEAT BELT & RETRACTOR .............8O-39
FIRST ROW INBOARD - QUAD BUCKET - INSTALLATION, SEAT BELT BUCKLE ......8O-36
FIRST ROW INBOARD - QUAD BUCKET - REMOVAL, SEAT BELT BUCKLE .........8O-35
FITTING - CONNECTING ROD ............9-46
FITTING - PISTON RING ................9-47
FITTING - STANDARD PROCEDURE, MAIN BEARING ...................... 9-125
FITTING - STANDARD PROCEDURE, PISTON RING ....................... 9-124
FITTING - STANDARD PROCEDURE, PISTON TO CYLINDER BORE ............9-44
FITTING CONNECTING RODS - STANDARD PROCEDURE ...............9-119
FITTING DISASSEMBLY/ASSEMBLY - STANDARD PROCEDURE,
TRANSMISSION COOLER LINE QUICK
CONNECT ............................ 7-38
FITTING PISTONS - STANDARD PROCEDURE ........................ 9-120
FITTINGS - STANDARD PROCEDURE, QUICK-CONNECT ..................... 14-18
FITTINGS, STANDARD PROCEDURE - HANDLING TUBING ................... 24-69
FLAP AND SPRING ASSEMBLY - INSTALLATION, QUAD BUCKET SEAT
SIDE SHIELD/CUP HOLDER ............23-151
FLAP AND SPRING ASSEMBLY - REMOVAL, QUAD BUCKET SEAT SIDE
SHIELD/CUP HOLDER ................23-151
FLEX DRIVE - DESCRIPTION ...........8N-55
FLEX DRIVE - INSTALLATION ...........8N-56
FLEX DRIVE - OPERATION .............8N-55
FLEX DRIVE - REMOVAL ...............8N-55
FLEX PLATE - INSTALLATION ...........9-133
FLEX PLATE - REMOVAL ...............9-133
FLEXIBLE FUEL ENGINE OIL - DESCRIPTION .........................0-3
FLOOR CONSOLE - FOLD-IN-FLOOR - INSTALLATION ....................... 23-89
FLOOR CONSOLE - FOLD-IN-FLOOR - REMOVAL .......................... 23-89
FLOOR CONSOLE BASE TRAY - INSTALLATION ....................... 23-89
FLOOR CONSOLE BASE TRAY - REMOVAL .......................... 23-89
FLOOR CONSOLE KEY LOCK TUMBLER - FOLD-IN-FLOOR - INSTALLATION ........23-90
FLOOR CONSOLE KEY LOCK TUMBLER - FOLD-IN-FLOOR - REMOVAL ............23-90
FLOOR CONSOLE LID LATCH - FOLD-IN-FLOOR - INSTALLATION ........23-90
FLOOR CONSOLE LID LATCH - FOLD-IN-FLOOR - REMOVAL ............23-90
FLOOR DISTRIBUTION DUCTS - INSTALLATION ....................... 24-50
FLOOR DISTRIBUTION DUCTS - REMOVAL .......................... 24-50
FLOOR HEAT DUCT - INSTALLATION, REAR .............................. 24-63
FLOOR HEAT DUCT - REMOVAL, REAR . . . 24-63
FLOOR MATS - INSTALLATION, CARPETS . 23-81
FLOOR MATS - REMOVAL, CARPETS .....23-81 FLOOR TUB CARPET INSERT -
FOLD-IN-FLOOR - INSTALLATION,
SECOND ROW ....................... 23-98
FLOOR TUB CARPET INSERT - FOLD-IN-FLOOR - REMOVAL, SECOND
ROW .............................. 23-98
FLOOR TUB CARPETS INSERT - FOLD-IN-FLOOR - INSTALLATION,
REAR .............................. 23-96
FLOOR TUB CARPETS INSERT - FOLD-IN-FLOOR - REMOVAL, REAR ......23-95
FLOW AND PRESSURE TEST - DIAGNOSIS AND TESTING, POWER
STEERING SYSTEM .................... 19-1
FLOW CHECK - DIAGNOSIS AND TESTING, COOLING SYSTEM .............7-3
FLUID - DESCRIPTION, AUTOMATIC/ MANUAL TRANSAXLE ...................0-4
FLUID - DESCRIPTION, AWD POWER TRANSFER UNIT .......................0-6
FLUID AND FILTER SERVICE - STANDARD PROCEDURE .........21-231,21-82
FLUID CAPACITIES - SPECIFICATIONS ......0-6
FLUID CONTAMINATION - DIAGNOSIS AND TESTING, BRAKE .................. 5-33
FLUID COOLER - DESCRIPTION .........19-45
FLUID COOLER - INSTALLATION .........19-45
FLUID COOLER - OPERATION ...........19-45
FLUID COOLER - REMOVAL ............19-45
FLUID FILL/CHECK LOCATIONS - DESCRIPTION .........................0-7
FLUID LEAKAGE - DIAGNOSIS AND TESTING, TORQUE CONVERTER
HOUSING ....................... 21-154,21-9
FLUID LEVEL AND CONDITION CHECK, STANDARD PROCEDURE .........21-230,21-82
FLUID LEVEL CHECKING - STANDARD PROCEDURE, BRAKE ................... 5-33
FLUID LEVEL CHECKING - STANDARD PROCEDURE, POWER STEERING ........19-44
FLUID LEVEL SWITCH - DESCRIPTION, BRAKE .............................. 5-10
FLUID LEVEL SWITCH - INSTALLATION, BRAKE .............................. 5-11
FLUID LEVEL SWITCH - INSTALLATION, WASHER ........................... 8R-11
FLUID LEVEL SWITCH - OPERATION, BRAKE .............................. 5-10
FLUID LEVEL SWITCH - REMOVAL, BRAKE .............................. 5-11
FLUID LEVEL SWITCH - REMOVAL, WASHER ........................... 8R-11
FLUID, SPECIFICATIONS - BRAKE .........5-33
FLUIDS - DESCRIPTION, AWD REAR DRIVELINE MODULE ....................0-6
FLUSH MEASUREMENTS - SPECIFICATIONS, GAP ................23-177
FOG LAMP - DIAGNOSIS AND TESTING, FRONT .............................. 8L-7
FOG LAMP - INSTALLATION, FRONT .......8L-8
FOG LAMP - REMOVAL, FRONT ..........8L-8
FOG LAMP UNIT ALIGNMENT - EXPORT - STANDARD PROCEDURE, FRONT ........8L-9
FOG LAMP UNIT ALIGNMENT - STANDARD PROCEDURE, FRONT .........8L-9
FOLDAWAY MIRROR SWITCH - EXPORT - DESCRIPTION, POWER ..............8N-29
FOLDAWAY MIRROR SWITCH - EXPORT - INSTALLATION, POWER ..............8N-30
FOLDAWAY MIRROR SWITCH - EXPORT - OPERATION, POWER ................8N-29
FOLDAWAY MIRROR SWITCH - EXPORT - REMOVAL, POWER .................. 8N-29
FOLD-IN-FLOOR - INSTALLATION . . . 14-10,14-16
FOLD-IN-FLOOR - INSTALLATION, ARMREST - SECOND ROW ............23-130
FOLD-IN-FLOOR - INSTALLATION, ARMREST ROTATING ASSEMBLY -
SECOND ROW ...................... 23-130
FOLD-IN-FLOOR - INSTALLATION, BOTTOM OF SEAT CUSHION PAN
PANEL-THIRD ROW .................. 23-152
FOLD-IN-FLOOR - INSTALLATION, CARPET TRIM RING AND COVER ........23-84
FOLD-IN-FLOOR - INSTALLATION, CARPETS ........................... 23-83
FOLD-IN-FLOOR - INSTALLATION, FLOOR CONSOLE ........................... 23-89FOLD-IN-FLOOR - INSTALLATION, FLOOR
CONSOLE KEY LOCK TUMBLER .........23-90
FOLD-IN-FLOOR - INSTALLATION, FLOOR CONSOLE LID LATCH .................23-90
FOLD-IN-FLOOR - INSTALLATION, HEADREST SLEEVE - SECOND ROW .....23-131
FOLD-IN-FLOOR - INSTALLATION, HEADREST SLEEVE - THIRD ROW ......23-153
FOLD-IN-FLOOR - INSTALLATION, REAR FLOOR TUB CARPETS INSERT ..........23-96
FOLD-IN-FLOOR - INSTALLATION, SEAT - SECOND ROW ...................... 23-132
FOLD-IN-FLOOR - INSTALLATION, SEAT - THIRD ROW ........................ 23-154
FOLD-IN-FLOOR - INSTALLATION, SEAT BACK COVER/FOAM - SECOND ROW ....23-133
FOLD-IN-FLOOR - INSTALLATION, SEAT BACK COVER/FOAM - THIRD ROW ......23-156
FOLD-IN-FLOOR - INSTALLATION, SEAT BACK FRAME - SECOND ROW .........23-134
FOLD-IN-FLOOR - INSTALLATION, SEAT BACK FRAME - THIRD ROW ...........23-157
FOLD-IN-FLOOR - INSTALLATION, SEAT BACKSTOW STRAP - THIRD ROW ......23-158
FOLD-IN-FLOOR - INSTALLATION, SEAT BASE RISER - SECOND ROW ..........23-135
FOLD-IN-FLOOR - INSTALLATION, SEAT BELT CENTER LAP BELT ..............23-157
FOLD-IN-FLOOR - INSTALLATION, SEAT CUSHION COVER/FOAM - THIRD ROW . . . 23-159
FOLD-IN-FLOOR - INSTALLATION, SEAT CUSHION COVER/FOAM -SECOND
ROW ............................. 23-136
FOLD-IN-FLOOR - INSTALLATION, SEAT CUSHION SIDE SHIELD - SECOND
ROW ............................. 23-138
FOLD-IN-FLOOR - INSTALLATION, SEAT GAS STRUT - SECOND ROW ...........23-139
FOLD-IN-FLOOR - INSTALLATION, SEAT PROP ROD - SECOND ROW ...........23-140
FOLD-IN-FLOOR - INSTALLATION, SECOND ROW FLOOR TUB CARPET
INSERT ............................ 23-98
FOLD-IN-FLOOR - INSTALLATION, SIDE SHIELD CUP HOLDER ................23-160
FOLD-IN-FLOOR - INSTALLATION, WITH NVLD .............................. 25-20
FOLD-IN-FLOOR - REMOVAL .......14-10,14-13
FOLD-IN-FLOOR - REMOVAL, ARMREST - SECOND ROW ..................... 23-130
FOLD-IN-FLOOR - REMOVAL, ARMREST ROTATING ASSEMBLY - SECOND ROW . . 23-130
FOLD-IN-FLOOR - REMOVAL, BOTTOM OF SEAT CUSHION PAN PANEL-THIRD
ROW ............................. 23-152
FOLD-IN-FLOOR - REMOVAL, CARPET TRIM RING AND COVER ...............23-84
FOLD-IN-FLOOR - REMOVAL, CARPETS . . . 23-82
FOLD-IN-FLOOR - REMOVAL, FLOOR CONSOLE ........................... 23-89
FOLD-IN-FLOOR - REMOVAL, FLOOR CONSOLE KEY LOCK TUMBLER .........23-90
FOLD-IN-FLOOR - REMOVAL, FLOOR CONSOLE LID LATCH .................23-90
FOLD-IN-FLOOR - REMOVAL, HEADREST SLEEVE - SECOND ROW ..............23-131
FOLD-IN-FLOOR - REMOVAL, HEADREST SLEEVE - THIRD ROW ...............23-152
FOLD-IN-FLOOR - REMOVAL, REAR FLOOR TUB CARPETS INSERT ..........23-95
FOLD-IN-FLOOR - REMOVAL, SEAT - SECOND ROW ...................... 23-132
FOLD-IN-FLOOR - REMOVAL, SEAT - THIRD ROW ........................ 23-153
FOLD-IN-FLOOR - REMOVAL, SEAT BACK COVER/FOAM - SECOND ROW .........23-133
FOLD-IN-FLOOR - REMOVAL, SEAT BACK COVER/FOAM - THIRD ROW ...........23-155
FOLD-IN-FLOOR - REMOVAL, SEAT BACK FRAME - SECOND ROW ..............23-134
FOLD-IN-FLOOR - REMOVAL, SEAT BACK FRAME - THIRD ROW ................23-156
FOLD-IN-FLOOR - REMOVAL, SEAT BACKSTOW STRAP - THIRD ROW ......23-158
FOLD-IN-FLOOR - REMOVAL, SEAT BASE RISER - SECOND ROW ...............23-134
FOLD-IN-FLOOR - REMOVAL, SEAT BELT CENTER LAP BELT ................... 23-157
RS INDEX13
Description Group-Page Description Group-Page Description Group-Page